
4 minute read
LOST ART The skinny on your dizzy
from BMW 3-Series
by Thomas Swift
LOST ART by ROB SIEGEL
Sparking the Fire: Prehistoric Ignition 101
Advertisement
n the movie Airplane II, Lloyd Bridges tells Stephen Stucker, “I want
Ito know absolutely everything that’s happened up till now.” “Well, let’s see. First, the earth cooled. And then the dinosaurs came, but they got too big and fat, so they all died and they turned into oil.”
It’s not quite as easy to condense the history of the gasoline-engine ignition system, but I’ll give it a try: Some of the earliest gas engines used what was basically a Bunsen burner and a mechanically sliding window to light the air-fuel mixture. Using a magneto to generate a spark came next—and that method is still used on everything from chain saws to aircraft engines. But as automotive electrical systems became more reliable, battery-powered ignition systems took over and remained the dominant configuration for three-quarters of a century. That setup is charming, but it breaks. Now, everything’s computerized. There. Easy, right?
Every gas engine needs spark to set off combustion, and every spark needs to happen in the right cylinder at the right time. Back in the day, these functions were performed by mechanical contrivances on the engine in which things physically opened, closed, and spun around. You know of this arrangement as the distributor-breaker-point ignition system—and you owe it all to smart guy and eventual GM research head Charles F. Kettering. His eponymous system, first installed on the 1910 Cadillac, had all the elements that remained in automotive ignition through the Seventies.
An ignition coil relies on Faraday’s Law to convert a battery’s 12 volts into the higher voltage needed to produce ignition spark. The distributor times those sparks and sends them to the appropriate cylinder. The distributor is typically a round thing with spark-plug wires attached to the top. Inside, an engine-driven rotor spins, making round-robin contact with electrical tabs on the cap, “distributing” (how about that?) the electrical discharge to those wires, and thus, each spark plug. A contact breaker (or pair of breakers) within the distributor, called points, ride on a lobed shaft. As the engine spins the distributor, the points open and close. When they’re closed, current from the battery flows to the coil. But when the distributor lobe kicks the points open, that stops the current and causes the coil to discharge, creating a sudden jolt of high-voltage electricity. A capacitor, called a condenser, prevents the current from arcing across the point gap, instead forcing it to discharge from the coil. A thick wire connects the coil to the center of the distributor cap—and from there, the jolt is sent to the proper cylinder’s plug, where—bam!—it becomes a spark. With the rotor spinning and the points opening and closing thousands of times a minute, things wear out. The electrical make-and-break causes pits on one side of the point-gap surface and mounds on the other. This wear slightly alters when the plugs fire—and remember, ignition timing needs to be precise. To keep it that way, the points need to be adjusted regularly. Change how close the breakers are to each other and when during the cycle they open—something you can do on almost every set of points—and you change when the spark plug fires. That’s done by measuring something called dwell angle, the number of degrees for each rotation of the distributor that the points are closed. Dwell is adjusted by physically setting the maximum point gap, but that gap is only an approximation of the dwell angle—the angle must be verified by connecting something called a dwell meter to the engine. If the reading on the meter is too high, the points are closed for too many degrees of rotation, and the point gap needs to be increased. (The opposite is true if it’s too low.) This is far easier than it sounds; the dwell meter essentially does all the work, and you simply adjust the points until the meter reading matches what’s specified in your car’s shop manual. While some cars have a little window in the distributor allowing you to adjust the gap while the engine is running, most don’t, making the process one of trial and error.
Neglect dwell adjustments long enough, and eventually the points may not open at all, causing a no-spark condition. Which causes a no-drive condition. In the old days, the low-cost solution was to file the points down to restore their efficiency—and you still can—but replacement is best.
To improve reliability and efficiency, modern cars have dramatically different ignition systems. “Breakerless” electronic ignitions replaced mechanical points in the Sixties and Seventies. The Seventies saw the first digital engine-management systems to map ignition advance and fire the coil at the correct time. The coil still fed a “distributor” of sorts, with a spinning rotor, cap, and individual plug wires, but it did not alter ignition timing. The mid-Nineties heralded the introduction of “stick coils,” thin ignition coils integrated with the spark-plug connector, allowing one coil per spark plug, and thus the deletion of any moving parts or long, highvoltage wires associated with the ignition.
Like many things on vintage cars, old ignition has its charms. In modern cars, a complex and exacting procedure has been swapped for a handful of sensors and algorithms and processors. While I often replace the points and condenser on my old cars with a compact electronic ignition unit for reliability, I miss the process of setting the timing. Many modern repair shops don’t even know what the tools are, let alone how to use them.
Surely you think that’s silly. (And to cap things off with another Airplane! reference, you say, “Of course I do, and don’t call me Shirley.”)
Rob Siegel (robsiegel.com) is a renaissance wrench from Boston.
BUILDING PERFORMANCE
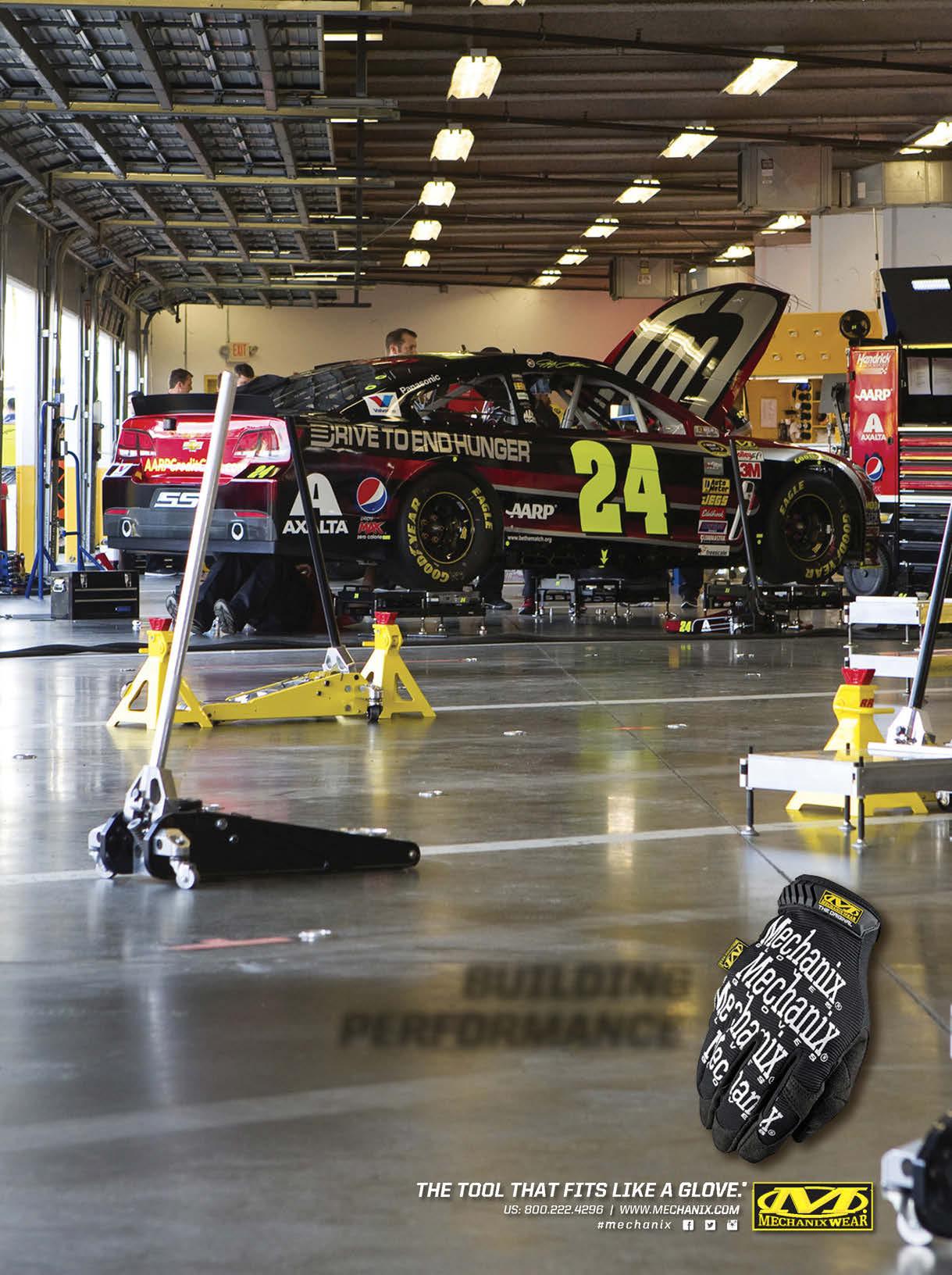