
14 minute read
Cover Story: Timbermark
The Timber Stamp of Authority
Established in 2004, Timbermark is a marking systems company with a focus on the timber industry. The company pioneered high-resolution inkjet printers for the sector, allowing for sharper detailed images on end-stamps, planed timber and pallet blocks.
Focusing on the timber industry, Timbermark has developed products, applications and engineering solutions for the specific needs of sawmills and pallet factories. It offers dedicated printer installations for moulded timber, sawmill sorting lines, pallet blocks, 2-way bearer pallet lines and 4-way pallet lines. Founder Colin Stewart, had already worked with distributors serving Swedish sawmills and set up the company to offer highresolution inkjet printing to UK sawmills. “We have worked with our customers in the timber industry to understand their demands and developed applications which meet those needs,” says Colin. “We engineer our installations to be robust enough to withstand what can be a pretty rough operating environment, but also to allow the users to get the benefit of an electronics-based system with counting and date functions, or message switching capabilities.”
The latest developments in printing technology allow Timbermark to provide new options for customers. Thermal inkjet (TIJ) printers have found a place as a more efficient alternative to the continuous inkjet system. The printers offered by Timbermark use Hewlett Packard technology in the ink cartridges, which means improved speed, quality and reliability – and all at a lower cost. “What we like about TIJ,” adds Colin “Is that is provides a step-change in terms of inkjet reliability and performance. No more blocked jets, pumps, filters, damaged print heads – all the work is done in the HP cartridge itself. It’s just more efficient. If there’s a problem, just change the cartridge. No waiting for systems to start or engineers to turn up. The result is improved productivity.”
Timbermark’s thermal inkjet printers are supplied by Sojet in China. They are low-cost and the technology is easy to use. Colin says: “The Sojet system is very flexible. You can use up to six heads, so the printing setup can be configured in ways to suit the project. Any repairs are done by simply swapping the module. It is value-engineered in China so that it is the right price, and our customers are often surprised at how little the system costs. It is so simple to set up and install – most plant technicians have the skills required, especially with our guidance. And we can pre-configure the machine to their requirements before shipping. It is realistic to expect zero service costs for this type of printer.”
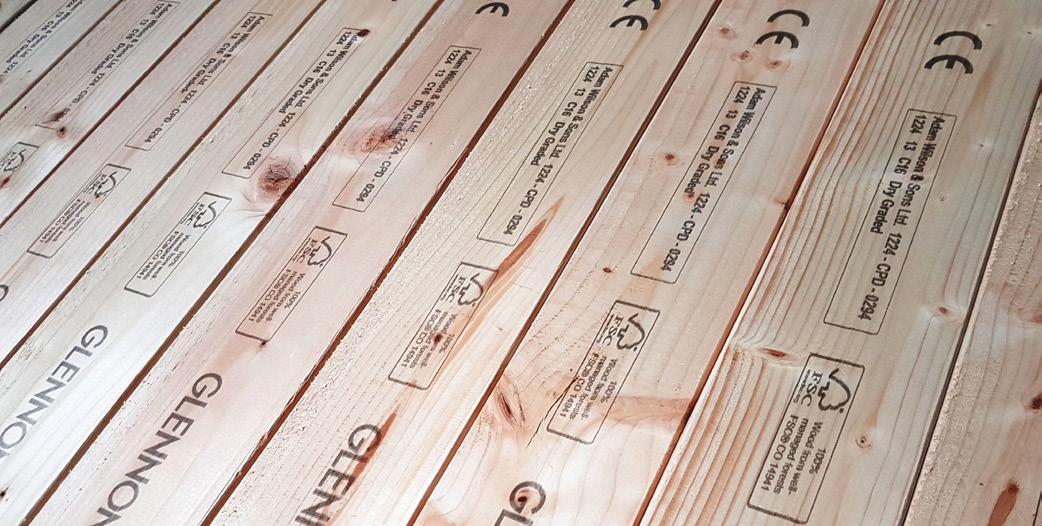
New Products, Development & Innovations High-resolution inkjet printing can be used for a variety of applications such as printing barcodes. This option gives customers a cost-effective alternative to labels, and for sawmill customers, barcodes can be used to identify an individual piece of timber as it transfers between different processes. Using high-resolution print technology, a machine-readable code can be printed onto the top or end of timber on a transverse conveyor. Barcodes can also be scanned to simplify data entry processes. Print quality at 200m/min
High-resolution inkjet printing can be used for printing barcodes.

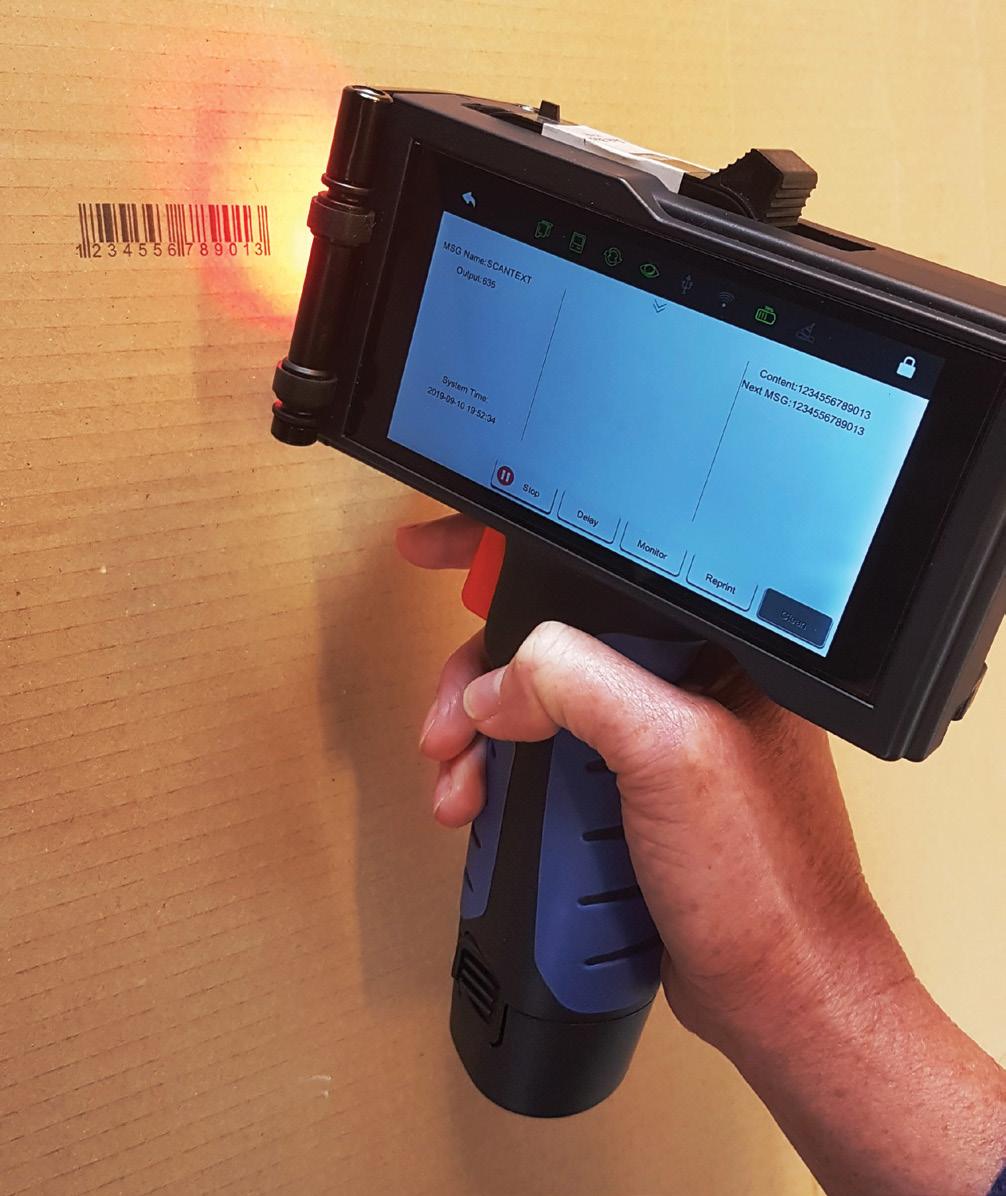
Sojet technology is low-cost and easy to use
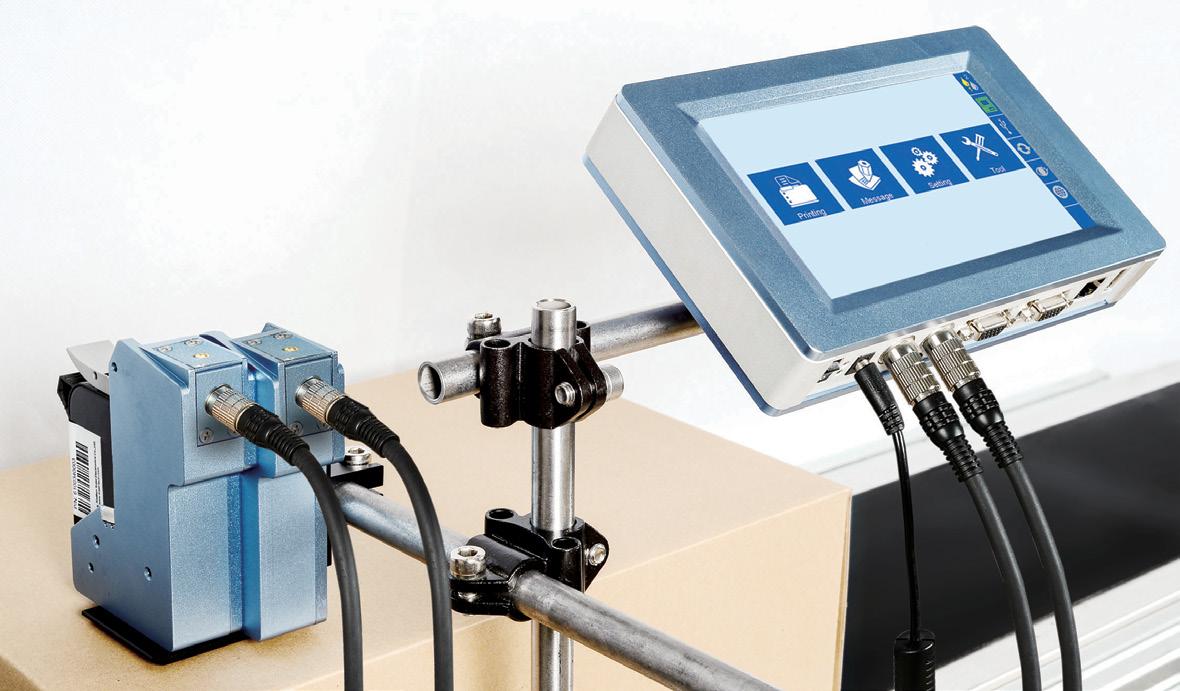
Barcode scanning with Sojet’s handheld Elfin V1H printer
Timbermark offers both low- and highresolution handheld printers with scan-to-print functionality so customers can scan a barcode and reproduce the information it contains in a variety of formats. Fixed position systems can utilise the same protocol for sending and receiving data via a network cable. In this way factory data systems can be used to make external variable data work, without the need to use a more expensive, fully-featured controller. Printing speed is another area where Timbermark is looking to make improvements. Current installations run at a speed of 200m/ min, but Timbermark is looking for opportunities to test at higher speeds. “Our print head and ink supply mounting concept mean we can run a high-resolution head less than 3mm from the substrate and get precise registration between the stitched print heads that make up the design,” adds Colin. “The concept is to arrange two heads to overprint each other, thus doubling the resolution. In this way we can run at low-resolution and higher speed and double-up on the ink deposit to make the stamp opaque enough at high speed.”
Timbermark is also exploring how to print with a pigmented white ink using a UV-curing system. The equipment – from Yeacode in China – produces an incredibly sharp 300-dpi print quality. It allows high-resolution printing onto challenging substrates such as wet-painted surfaces. The TIJ technology is really simple to use, and Timbermark is offering customers the opportunity to self-install. Via its new e-commerce platform at: www.t-mark. co.uk technicians can purchase the printing equipment online and install it themselves without having to rely on expensive service engineers. This potential cost-saving is one of the benefits of the new generation of printers and seems a timely development in the light of the current social distancing policies many companies have adopted to contain the spread of the coronavirus. In its 15 years of trading, Timbermark has developed a customer base across the UK and Europe. It has exhibited at LIGNA in Germany and now has customers in five Eurozone countries. Exporting is still a key part of the company’s growth strategy, a plan that Colin hopes won’t be impacted by Brexit. “We have assured our customers that their costs from us won’t change,” says Colin. “We will pay the import tariffs on goods that we supply. We are committed to ensuring our customer across the UK and Europe continue to enjoy the best possible service from us, whether we’re inside the EU or not.” Printing with a pigmented white ink using a UV-curing system
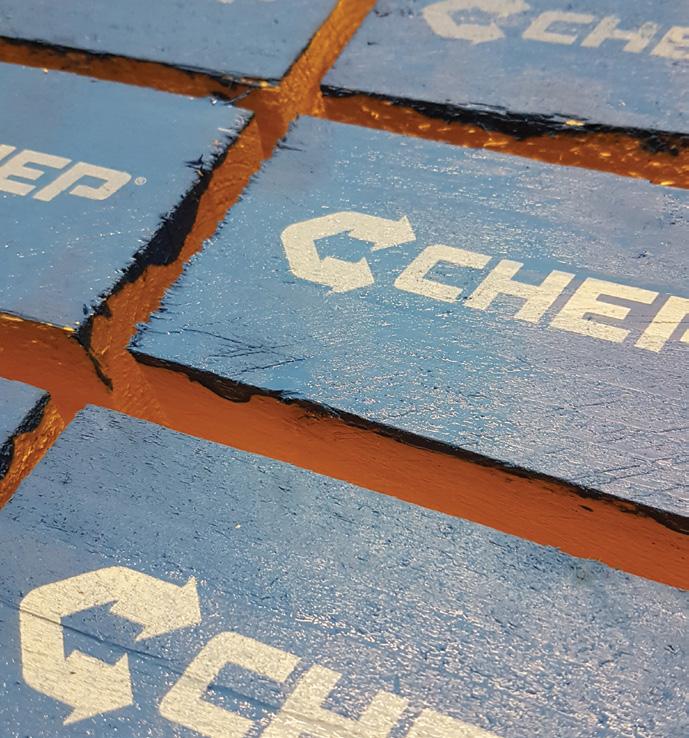
Spruced Up for Customer Care
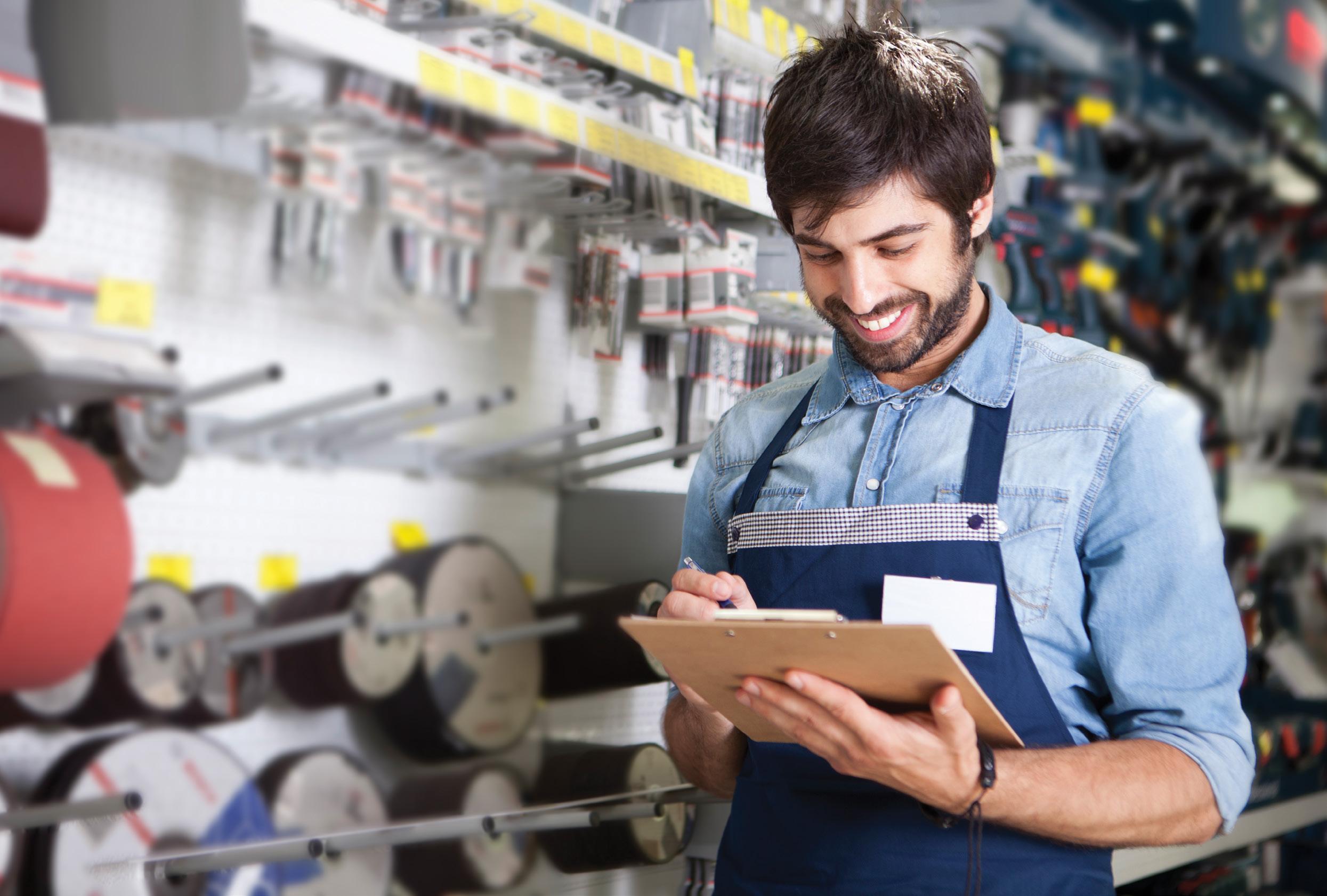
Coomers Timber & Building Supplies has been serving builders, small local developers, landscapers and retail customers since 1956. The introduction of ECI’s ERP software, Spruce gave the team the functionality to be more efficient and deliver improved customer service.
When adding a third site to their portfolio, it became obvious to the Coomers team that new technology was required to ensure minimal disruption for staff and to maintain a high quality customer experience. Selling a wide range of heavy building materials, landscaping, timber and lightside products, the team at Coomers realised they required industry-specific software, designed for the challenges builders merchants face on a day-to-day basis. Understanding customers
The modern customer expects builders’ merchants to understand their needs and even pre-empt their orders. Despite the obvious challenges this brings, the Coomers team were determined to be proactive as well as reactive to their customers, meaning they needed to be able to collect and access customer data at the click of a finger to spot key trends. ECI’s ERP software, Spruce, brings efficiency to customer relationship management. As well as being able to spot key buying trends, it combines a point-ofsale system and information database, making communication simple. With customer records available at the touch of a button, the Coomers staff can print or email documents, providing the information customers require, in their preferred format within minutes.
Busy builders, developers and landscapers also expect the checkout process to be as streamlined as possible. Using the software, the Coomers staff can quickly scan items, enter product codes, or look them up in the catalogue using a range of search terms. Supplementary information is also easy to bring in, including wiring diagrams, COSHH data sheets or photos – often exceeding customer expectations. Managing stock
Being able to easily access live stock levels across the three sites, via a single and fully-integrated system was an absolute must. As Coomers stock more than 7000 items, it was imperative that the sales staff had instant access to the most up-to-date stock level information to avoid customer disappointment. The Coomers team now have access to an automatic stock replenishment feature, which the team heavily relies on to review all purchasing needs on a daily basis. Most suppliers now generate orders based on predetermined stock levels – making the process far simpler. Additionally, instances of over-ordering or running out of certain stock lines have significantly reduced, helping to drive a customer-centric approach, not to mention a far more efficient and cost-effective operation. Modern consumers have grown to expect notifications and updates on their order status. Via ECI’s Spruce system, Coomers can send out automatically generated notifications – ensuring customers are kept updated all the way through the ordering, buying and delivery process.”

Managing a multi-branch operation
Visibility into all areas of the business is important in a multibranch operation employing over 70 members of staff. The Hampshire, Surrey and Sussex branches are now linked via a single system, meaning one branch can see, sell and deliver stock to a customer from a completely different branch – ensuring customer satisfaction and bolstering Coomers’ overall reputation.
Knowing how best to handle credit control can be tricky. This process is now handled professionally and in a consistent manner across every store, providing various levels of controls for the credit controller and giving point-of-sale staff some ‘room for manoeuvre’ with customers while maintaining control in the back office. This also helps with customer communication. Modern consumers have grown to expect notifications and updates on their order status. Via ECI’s Spruce system, Coomers can send out automatically generated notifications – ensuring customers are kept updated all the way through the ordering, buying and delivery process.
Managing change
The introduction of new software can be disruptive, especially if staff are not technologically savvy. Time and revenue lost training staff is an understandable concern for businesses considering a new system. With this in mind, installing an intuitive and easy-to-use ERP system was an absolute priority. Alongside a thorough implementation period there is also extensive online help available. This has ensured that whatever screen or part of the system a user is in, there is always a help button to ensure the user feels fully-supported and has access to hints and tips. So much so that Coomers require less than half an hour to set up and train each new Spruce user.
Significant expansion
Having worked tirelessly to build a reputation for outstanding customer service, the Coomers team are determined to stay ahead of the game. For Coomers, the introduction of a new ERP not only facilitates a more streamlined way of working, but also allows for expansion of the operation and increasing profits, while facilitating strong customer relationships and overall satisfaction.
Vacsol Flex protectionThe most for your Construction Timbers COMING SOON...
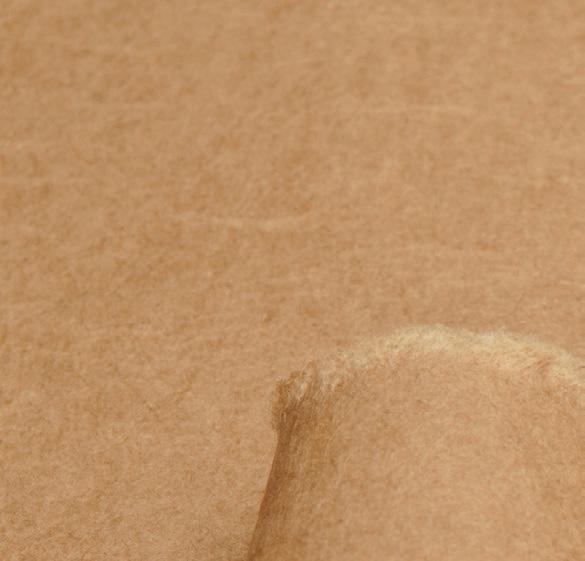




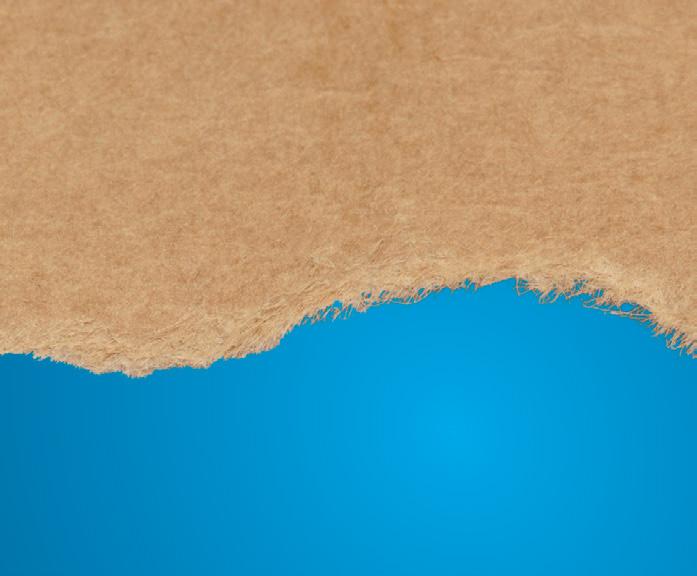


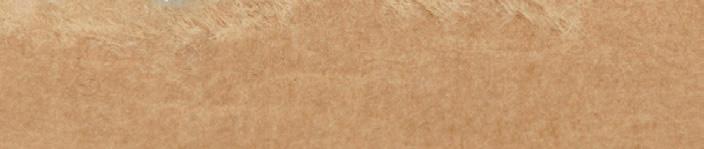
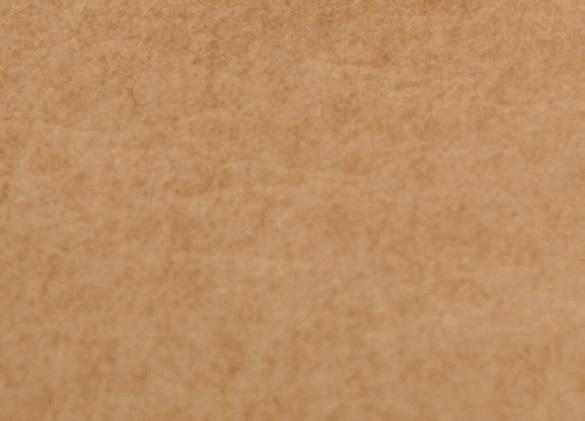
www.lonzawoodprotection.com/eu
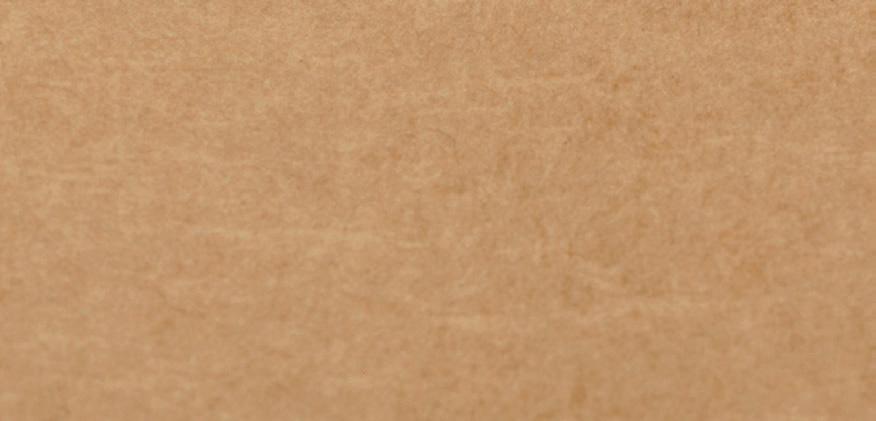
Changing the industry –one log at a time
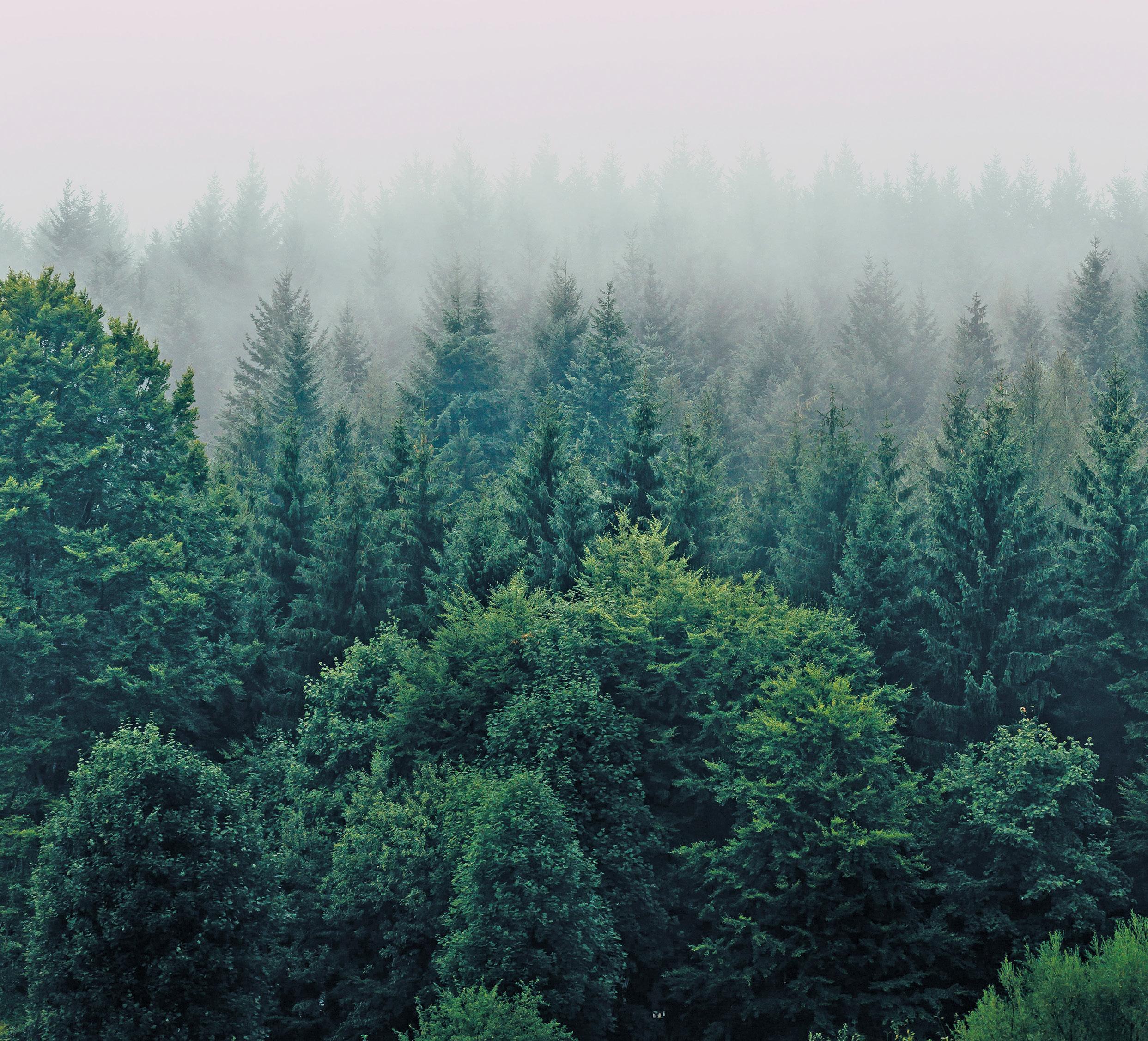
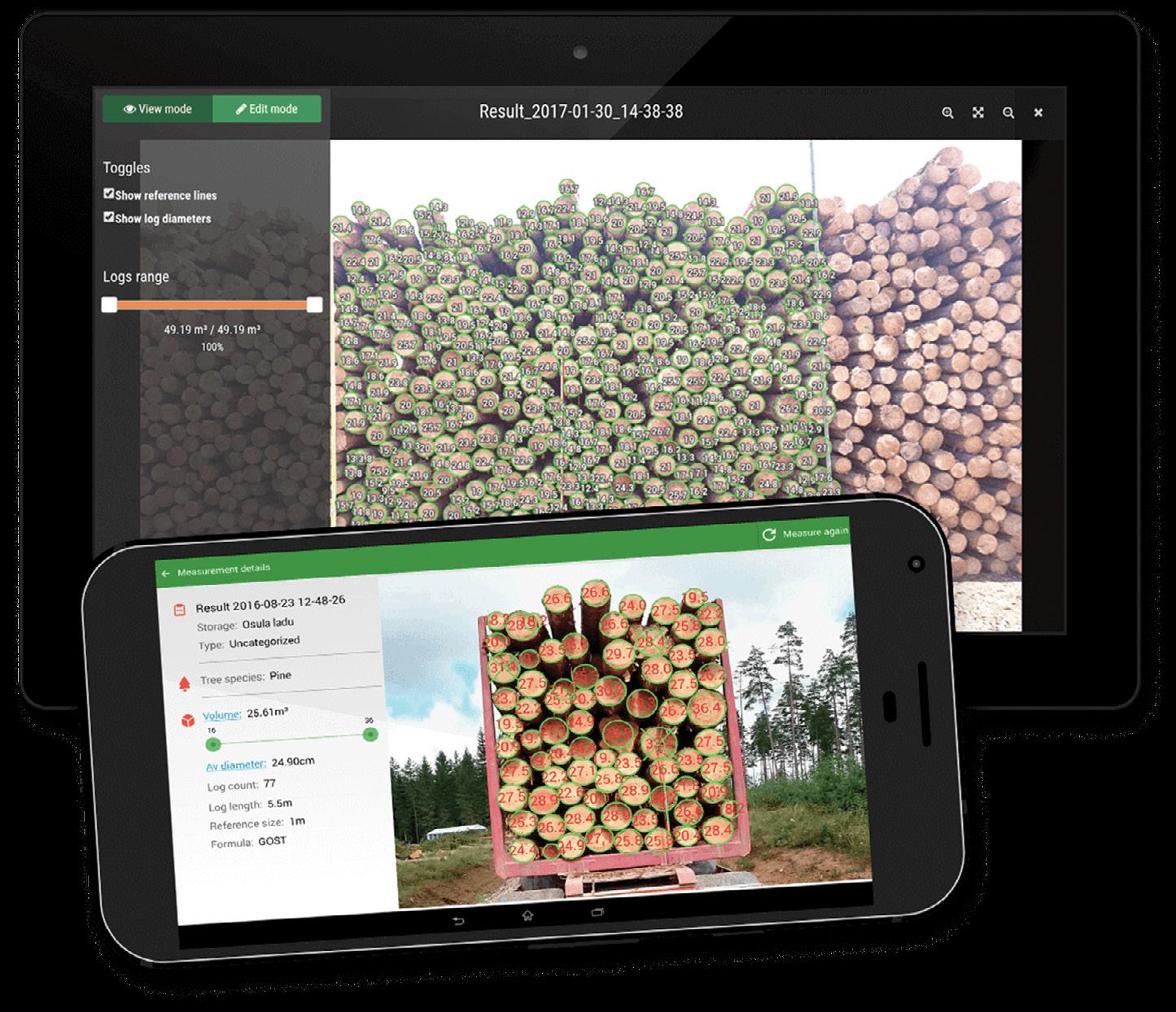
In an effort to make the forestry sector more profitable, efficient and transparent, an innovative mobile-device-based solution is providing accurate measurement of timber in a variety of settings.
The supply chain from forest to merchant is a complex one. One forest-tech company has been working hard to improve that chain for both log buyers and sellers and is doing it using specialist digital software and a pioneering algorithm. This collected digital data on timber – from logs to containerised shipments can be used for management of the entire supply chain. All the required data (volume, number of logs, log diameters, location) are available in digital form, reducing human error and enabling quick reporting and data processing.
Timbeter was created by a sawmill owner who was facing the problem of measuring logs manually every day and thought that if smartphones could recognise human faces, they could also recognise logs from a photo. “The idea for Timbeter came during a 48-hour hackathon that really helped us to look at the problem from a different angle and question the traditional methods and habits of the forestry sector,” says Martin Kambla, co-Founder and Chief Technology Officer. “It is a digital timber measurement solution that uses machine learning technology and artificial intelligence for accurate log detection.” How is it done? A simple photo taken using the dedicated Timbeter app of the timber, whether in a pile, on a truck or in a container can be analysed. This provides a wealth of accurate and reliable information for anyone dealing with timber log measurement from forest owners, sawmills to manufacturers and transport companies. Only an Android or iOS smart device (mobile phone or tablet) is required to run the software and it can run on any computer or browser.



has dropped significantly. Previously, since the measurements were done manually and there were claims regarding quality and volume, many shipments were not accepted. Now, with the availability of the data digitally, the authorities receive the necessary information beforehand and approval can happen in real-time.
So as the new decade begins, there are some exciting and busy times ahead for the Estonian-based forest-tech pioneer. What does the next 18 months hold for the company? “Measurements are just the beginning,” says Martin. “The majority of our future developments are focusing on reporting, logistics, and sales to help companies and governments reduce their administrative burden. We will continue developing more features and applications for our AI, automatic defect detection, creating 3D models. Last month we launched a new feature to detect duplicates measurements to help companies control the sub-contractors and single high-value log measurement.”
Timbeter serves clients in 61 countries around the world and is available in 11 languages with over 10,000 users, measuring more than 10 million cbm annually. Each pile of logs can be measured for pile density, log diameters, and the number of logs in minutes, to save the measurer time and obtain accurate data. Users can filter the diameters to see how many logs are in the specific range. Every pile is geo-tagged making the tracking of the timber’s origins easier. This can also be used as a key step in maintaining forest chain of custody and combating illegal logging.
Every measurement is stored in the cloud providing a real-time overview of measurements related to their species and qualities and every pile can be re-measured in the web if required. Timbeter’s storage enables users to analyse and share your measurements quickly, view inventories, active storage statuses and create instant reports in a few taps of a button, aiding managers and accountants to remain informed and up-to-date.
Timbeter allows users to have a greater control over their measurements, as all the information can be easily audited and controlled. This digital data can then be shared between customers and business locations to create a totally transparent and easily understood flow of information.
The introduction of digital technology across the construction industry is having a profound effect globally. But the forestry and timber sectors have been seen as slow and reluctant to modernise and adopt new technology. “Technology is only one part of the adoption process,” adds Martin. “Precision forestry is still relatively new. The sector also tends to love heavy machinery and paper, so in that sense, adopting smart devices in their daily processes is a big change. What we have seen is that it really depends on the mindset of the people in a company and how willing they are to change old habits and procedures. There are still many opportunities for artificial intelligence (AI) to make a big impact in solving forestry’s big issues. For example, illegal logging, reducing the administrative burden related to reporting and control for both companies and governments, and to make sure each tree that has been cut in a sustainable way reaches its maximum value.” For the merchant sector and timber supply chain the benefits are potentially massive. Smart and quick digital solutions that can be used by large manufacturers and small private forest owners, that is affordable and accessible for everyone, helps to increase transparency, secure fair trade and boost productivity levels.
“We have had cases where customers get a 200 EUR win with their first measurement by having a more accurate result,” says Martin. “It is really all about the transparency, efficiency of operations and safety of the people during the measurement process. Some exporters using Timbeter have told us the number of claims coming from China Precision forestry is still relatively new. The sector also tends to love heavy machinery and paper, so in that sense, adopting smart devices in their daily processes is a big change.”