
11 minute read
Cover Story – Combilift
Combilift and timber – a perfect combination
Some of the first customers to recognise the benefits of Combilift’s initial product – the C4000 multi-directional forklift – were from the timber industry, and since 1998 the relationship between the Irish manufacturer of handling solutions and this sector has continued to strengthen.
ccording to Combilift’s CEO and co-founder Martin A McVicar, over 40% of the company’s sales are to timber importers, merchants, constructors and related businesses, making it one of the most important industries that relies on Combilift products for safe, space saving and productive materials handling.
Whatever size of operation – large national outlets or smaller individual traders, Combilift’s engineering and technology can make a real difference. Improvements to handling and storage procedures lead to further advantages such as cost savings, higher levels of productivity and efficiency, and enhanced health and safety. Having started with the original C4000 truck, more models of the C-series followed and these are now available with lift capacities from 2.5t to 25t. Combilift became acknowledged as the leading global supplier of long load handling solutions, but its current range goes far beyond this. Its Aisle Master articulated forklifts are designed for narrow aisle operation and handle pallets as well as other loads, as do the CombiCB multidirectional counterbalance design forklifts.
Straddle carriers and mobile gantries cope with extreme oversized loads or containers and last year Combilift introduced its Combi-CSS Container Slip-Sheet, which can complete a full container load cycle in under 6 minutes – a cost-effective solution that is faster and safer when handling rough sawn timber, flat-packed furniture or panel products for example.
For the last few years Combilift has also extended its range of pedestrian operated trucks which are seen as a safer alternative to rideon forklifts when circumstances allow. These naturally operate at slower speeds than ride-on forklifts, and operators have a heightened awareness of their immediate environment as well as good all-round visibility of the load and the forks. Combilift’s pedestrian trucks all feature its unique, patented multi-position tiller arm, which was designed to ensure maximum safety for the operator and other people nearby. This can be turned to the left or right of the truck, allowing the operator to remain in the safest possible position when working in narrow aisles – at the side rather than at the rear, reducing the risk of the operator being crushed or trapped between the truck and racking.
The ethos behind all of these innovative products, designed and manufactured in Monaghan, Ireland and exported to over 85 countries, is the ability to “do more with less” as Martin McVicar puts it. The majority of Combilifts can replace a combination of other types of machines, making them versatile, multi-tasking machines. This saves on capital expenditure, lowers fleet running costs and maintenance overheads as well as reducing the carbon footprint. The ability to work in confined spaces and narrower aisles than conventional trucks also enables best use of that very valuable commodity – space – and can avoid the need for hiring costly additional storage or relocation if businesses grow.
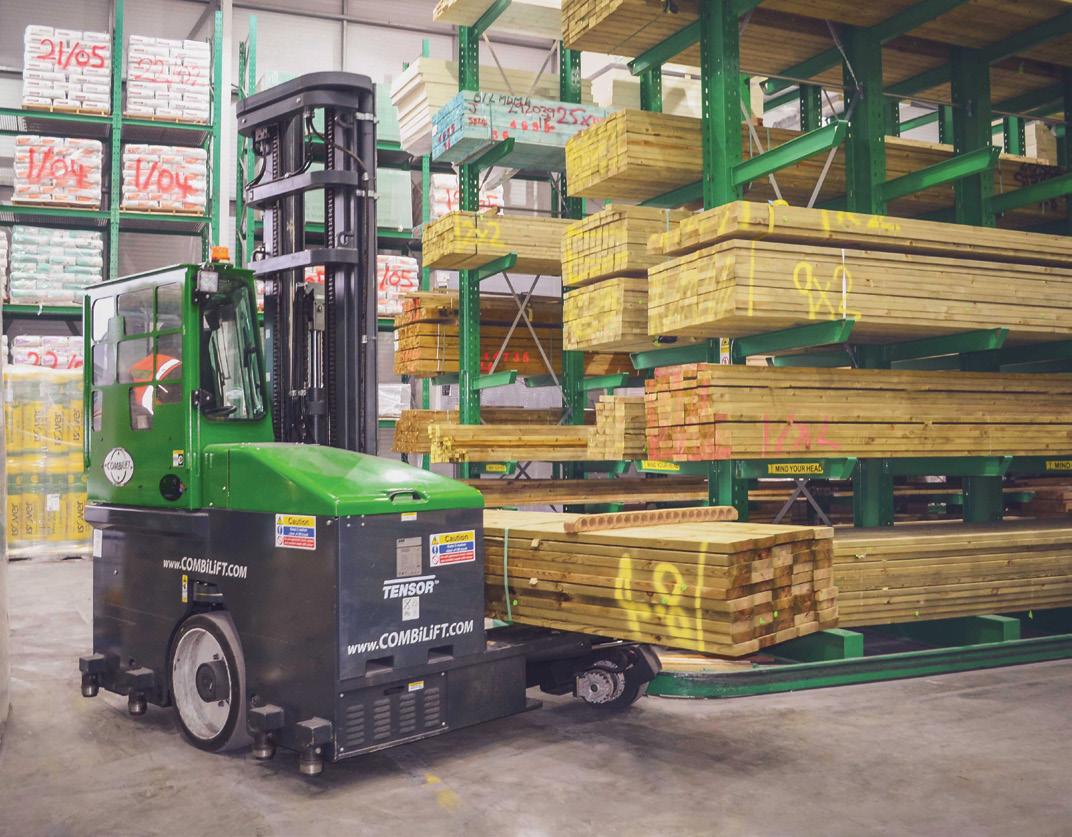
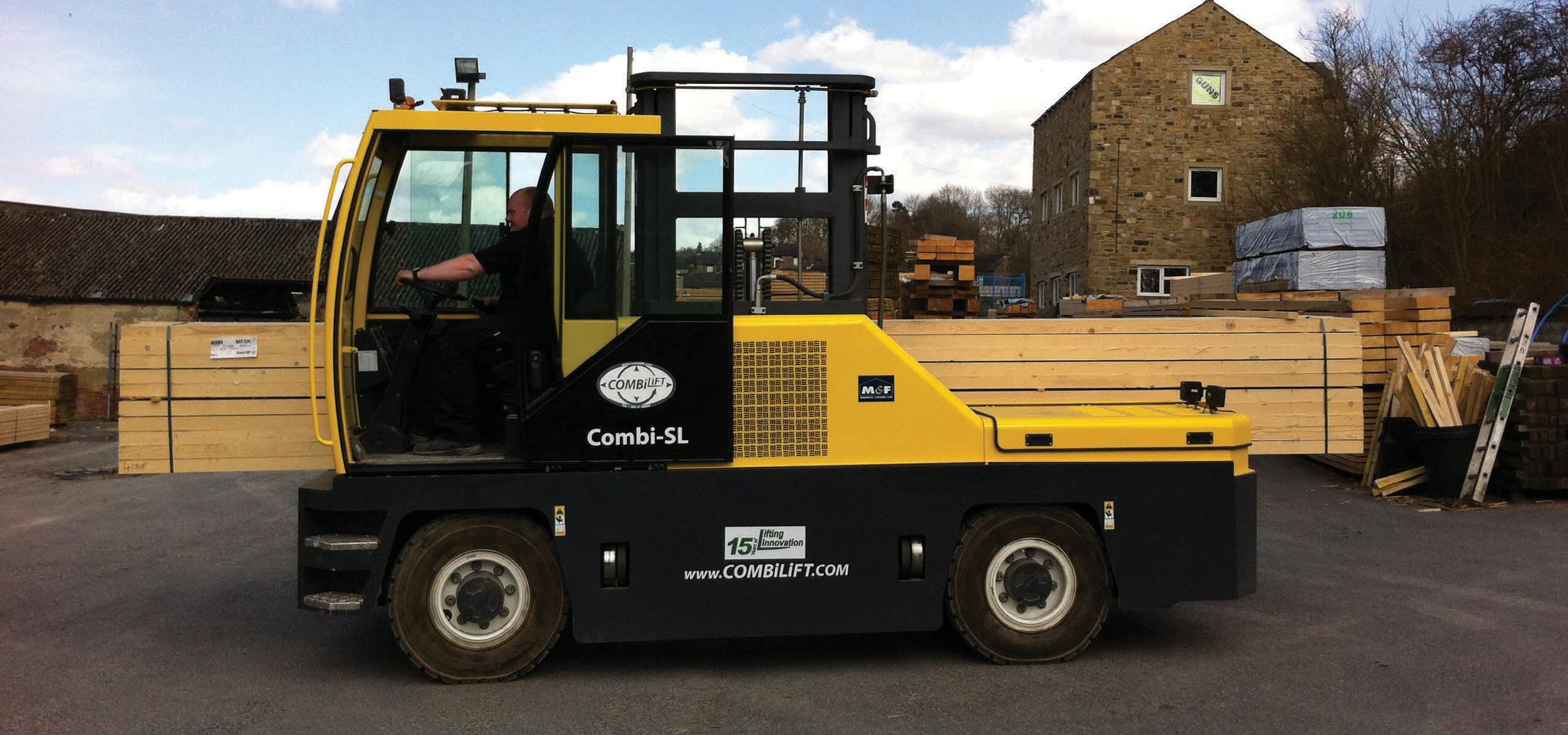
One long-term user of Combilift’s products is Lawsons Timber, which saw the potential of the C4000 model not long after its launch on the market. Around 35 C-Series trucks are now in operation at its 17 sites in and around London, and their ability to replace a combination of counterbalance and sideloader models is a major benefit when handling long products in tight spaces. Group Transport Manager David Harvey explains: “Most of our branches are in built up areas such as Camden, Acton and Wandsworth, where expansion of sites is nigh on impossible – due to cost issues or the density of surrounding buildings. We can only ‘go up not out’ with our storage, so packing as much stock into any given area is crucial. Being able to configure aisles widths according to the depth of the Combilifts and going up to racking heights of 7.5m means we can optimise space and cope with growth.”
Lawsons is also capitalising on Combilift’s expansion of its electric range. Most recent additions are two C4000Es at the Merton branch and numerous STEs (stand on models) at Whetstone and Camden. “We are keen to keep emissions as low as we can for the good of the environment,” adds David Harvey. “Also to keep noise levels to a minimum for our neighbours in residential areas. These electric models tick the boxes on both counts. Electric power is definitely the way forward for us and our drivers also like the quiet operation they offer.” For Cumbria-based RH Wilson (Lakes) Ltd, space saving was also an issue, but a major priority for Ann and Rodney Dalton when they took over the business was to improve overall efficiency and stock location procedures. The company specialises in grading timber for specific end use, whether it be redwood and hardwood for joineries making doors and windows, or whitewood for pallet and packaging manufacturers. Packs of products were previously block stacked and moved around with 2-directional sideloaders or counterbalance trucks.
“We did a detailed study of how long it was taking us to retrieve a specific pack and were alarmed at the figures,” says Rodney. “We were spending a substantial amount of time a day moving packs around and needed at least two employees to do this so it really added up in terms of hours and manpower. My first thought was out with free stacking, in with as much racking as possible and then find a manoeuvrable forklift capable of working in tight spaces.”
Since the latest C4000 has been on site the results have been impressive according to Rodney: “The time saving has been enormous – we are down to five minutes per pack – or four minutes 23 seconds to Combilift’s sideloader range is also a popular choice for the timber sector. Following the introduction of the 3-wheel multi-directional sideloaders 15 years ago, the 4-wheel, two directional model now gives an extra element of choice for customers.
be precise. This makes a huge difference when dealing with the four to seven artics a day that we typically load or unload. Quick stock location enables us to adhere to just-in-time delivery schedules. A knock-on bonus is that we now only need 30 minutes for the monthly stocktake compared to around two and a half hours previously.”
Combilift’s sideloader range is also a popular choice for the timber sector. Following the introduction of the 3-wheel multi-directional sideloaders 15 years ago, the 4-wheel, two directional model now gives an extra element of choice for customers. It is also engineered to be very suitable for prolonged long distance travel at high speeds, eliminating any concern of overheating that can be an issue in other sideloader brands. Merritt and Fryers in Skipton was one of the first companies to take delivery of this model, which replaced an old sideloader that had been in service for around twenty years. The versatility of the 5t capacity truck enables it to be used in the relatively narrow confines between racking in the warehouse, in the sales yard as well as in the large timber import area. Its tight tuning circle – “very impressive for its size,” says driver Howard Baker – and is of great benefit for precise manoeuvring with long loads around customers’ parked cars and other obstacles.
Much of the sideloader’s time is spent in the timber import section, which it accesses easily in spite of a very steep gradient from the main site. This is where joists which can measure 600 x 600 x 13.8m are stored. Offloading, loading and moving these extreme loads requires a robust and powerful truck, and the single hydrostatic drive motor coupled with a JCB differential axle ensures optimum performance. Howard Baker says: “The tilting carriage makes it very easy to get the forks under the packs and the full glazing on the front of the cab enables you to look directly down onto the load, and I also like the fact that you can tilt the steering column when getting in and out.”
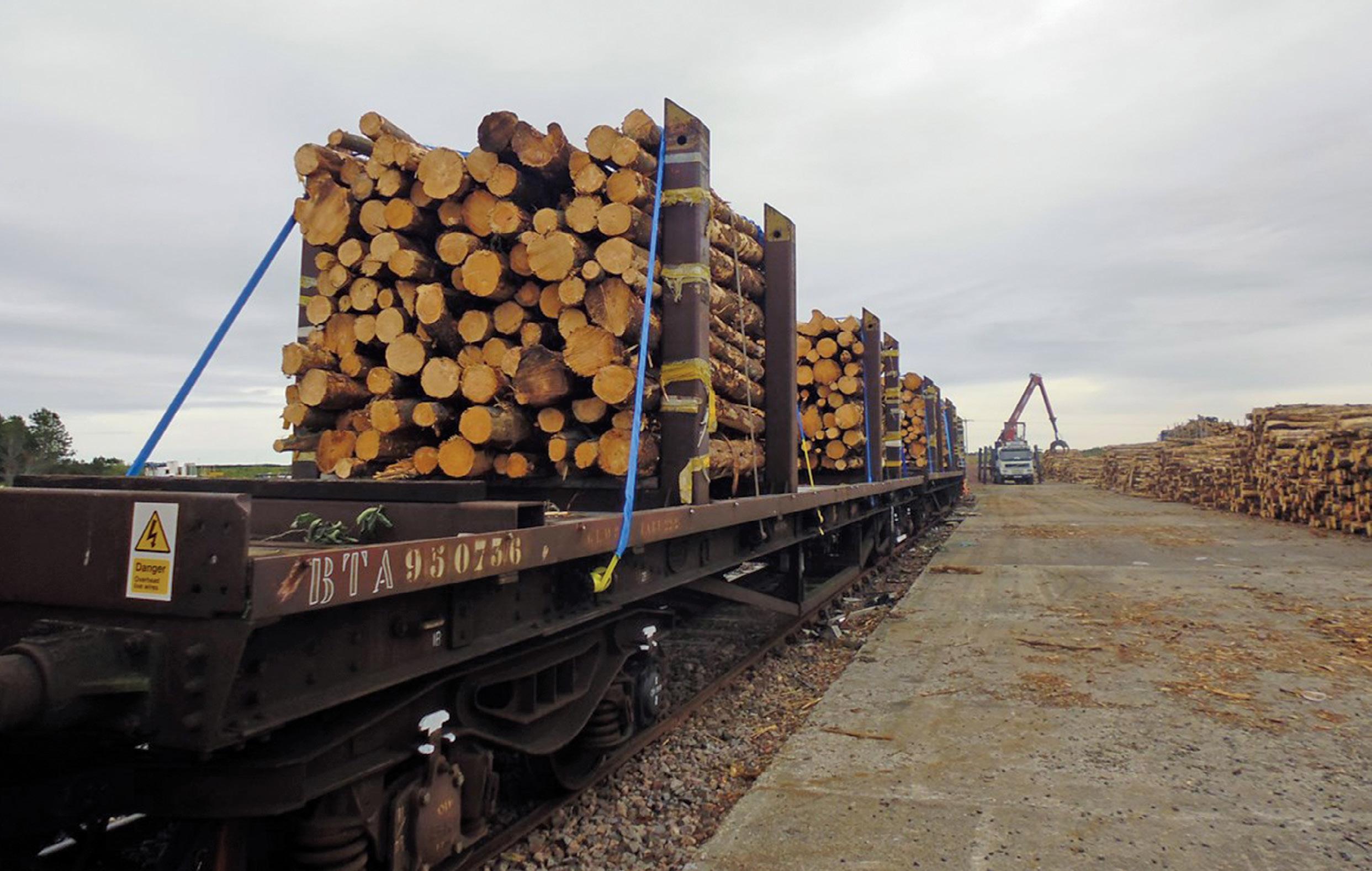
Road to rail options
The road network is the most important means of timber transport in the UK with over 90% of all timber delivered to processing plants by lorry – but a recent trial in the Scottish Highlands may be part of a change to use more rail and help reduce transport carbon emissions.
he volume of timber produced each year from UK T forests is forecast to rise from the current 11.5 million cubic metres to 13 million cubic metres by 2030. Developing a safe and efficient timber transport system is therefore essential to the continued success of the forest industry. As the latest updated 2020 edition of the Timber Transport Forum’s Code of Practice states: “Timber transport contributes a substantial part of our industry’s raw material costs and carbon emissions and has a major influence on the sector’s overall competitiveness.
“Road haulage will remain the dominant form of timber transport. Even for rail, waterway and marine modes of transport, the first leg of the journey out of the forest will normally need to be by lorry. In recent years we have removed many of the barriers to timber transport but continued investment in infrastructure and other improvements will be required.”
As a part of that investment and need for improvements – and to try and start a move away from the reliance on road transport – 6,000 tonnes of timber were recently transported by rail in a six-week trial in the Highlands, taking around 250 lorries totalling 55,000 lorry miles away from Scotland’s roads. The Scottish Government allocated £195,000 to Victa Railfreight to carry out the trial through the Scottish Strategic Rail Freight Fund and was the first time timber had been moved by rail in Scotland for more than 10 years. Timber from forestry in Caithness was loaded at Georgemas Junction near Halkirk and taken to Inverness, where long term plans could see logs unloaded at a new siding at Dalcross near Inverness Airport and taken to the nearby Norbord factory, to provide the raw material for a wide range of panel products including OSB. Operated by Victa Railfreight, partners included Transport Scotland, Network Rail, Hitrans and Scottish Forestry. The project took heavy duty timber lorries of the A99 and A9.
Scottish cabinet secretary for Transport, Infrastructure & Connectivity Michael Matheson said: “We have worked closely with the timber and rail freight industry to explore opportunities for modal shift. The trial will help to demonstrate that the movement of timber in Scotland by rail is possible as well as efficient and it will provide confidence to both the timber and rail freight industries, to develop permanent and sustainable solutions to meet market needs. This type of collaboration can support a sustainable green economic recovery from the current health crisis. It is good news for the timber and rail freight industry, for the Scottish economy and for the environment.”
Neil Sime, Victa Railfreight’s Managing Director said: “Victa is delighted that the Scottish Government has provided substantial funding so that we could bring together rail freight and timber industry partners to enable this collaborative trial of moving timber by rail to happen. We hope that it will lead to further movements of timber by rail across Scotland, providing greener solutions and reducing damage to sensitive rural roads.” The trains operated from Georgemas to the Inverness Millburn Yard for onward delivery to Norbord at Dalcross and James Jones at Mosstodloch. The trial was due to finish by the end of September and once it has been assessed, the findings will help shape future policies
in how timber is transported to market. Timber has been supplied from Munro Harvesting and Kelpie Woodlands with Georgemas Energy and Logistics Park providing access to the terminal. Jamie Farquhar, national manager for Scotland for forestry at Confor, said: “This is most welcome news, particularly as rail may be the only way to get some otherwise landlocked timber to market. Confor has worked hard for many years with the Timber Transport Forum to minimise the carbon footprint and impact of timber transport on rural communities – and rail can provide another effective option to do this, and to supply timber to our wood processing industry.”
Timber haulage is central to the forestry lifecycle and it is now hugely important to pursue opportunities to reduce the environmental damage it can create. Anne MacKenzie, senior route freight manager for Network Rail Scotland, added: “We are confident that this trial will demonstrate that rail is a viable and environmentally sustainable way to transport timber and are
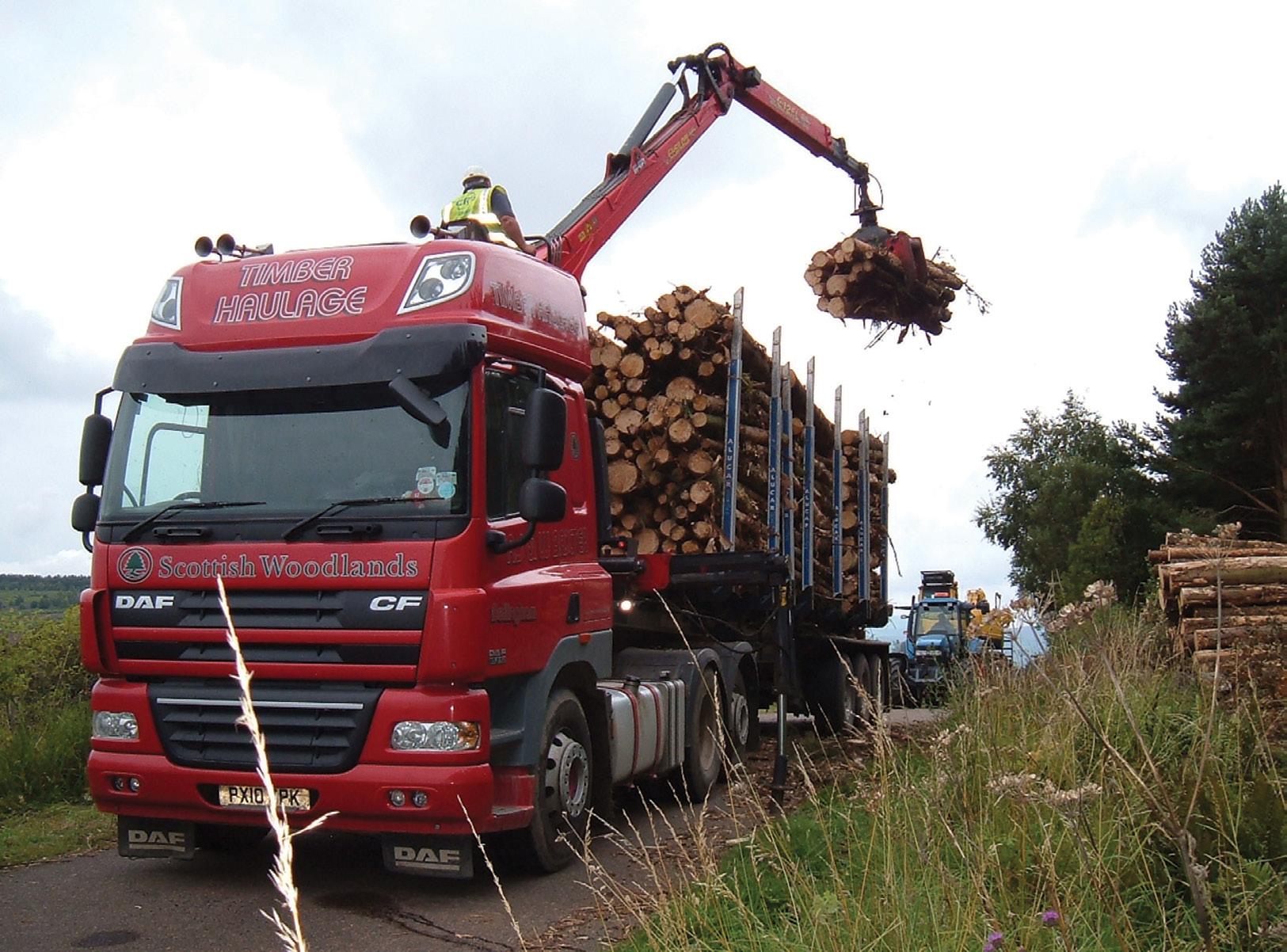
delighted to have worked closely with our rail freight industry partners in supporting this co-operative venture.”
More at www.transport.gov.scot
Wide Range of LPG
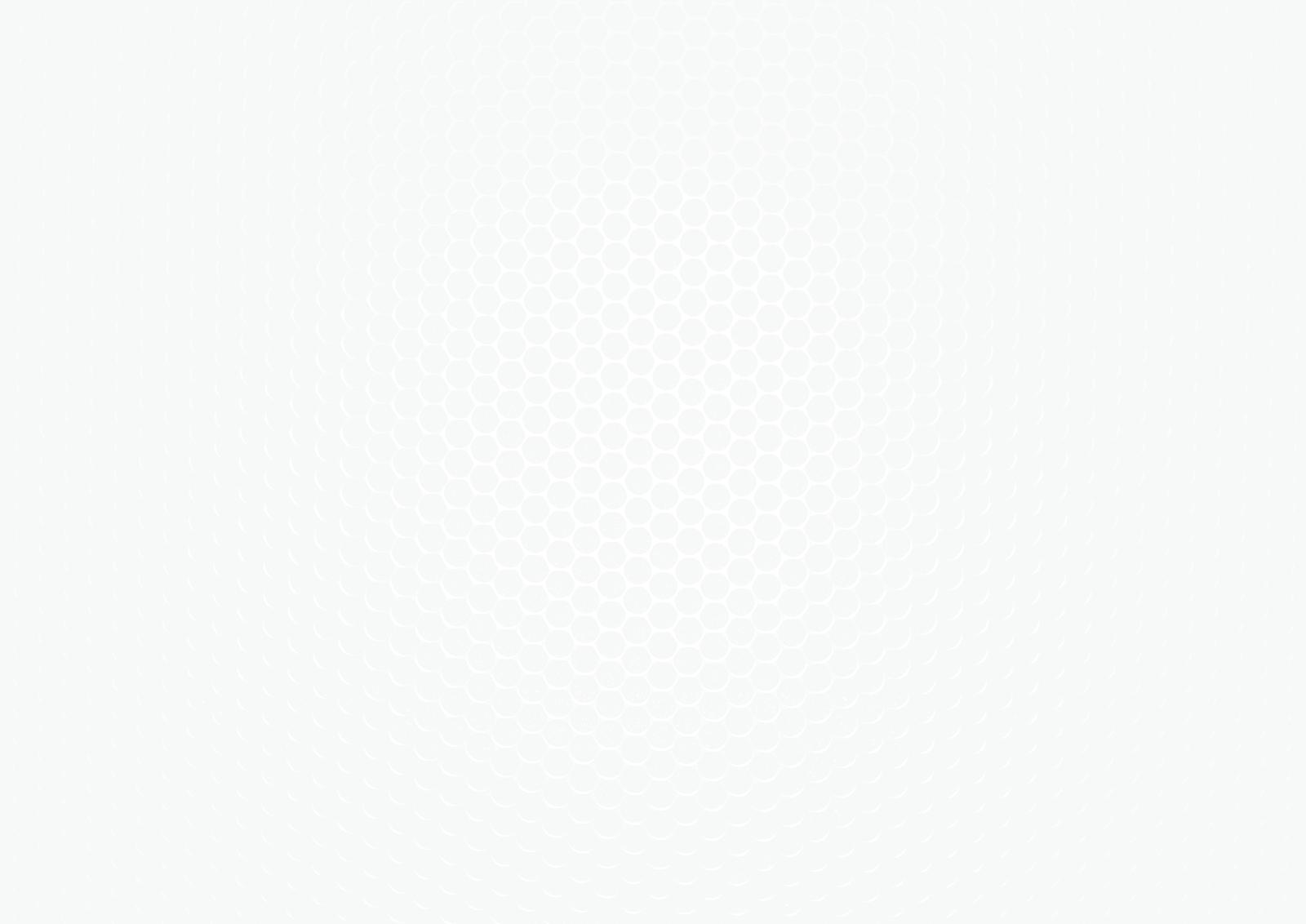
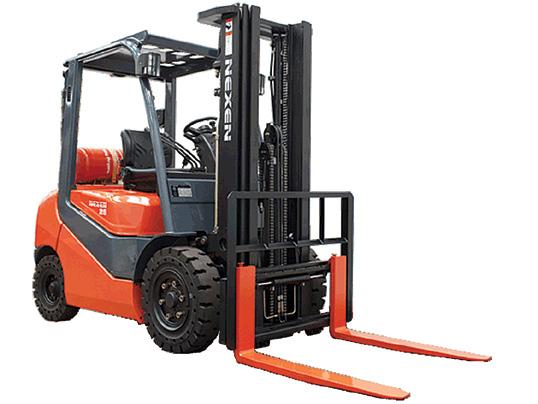
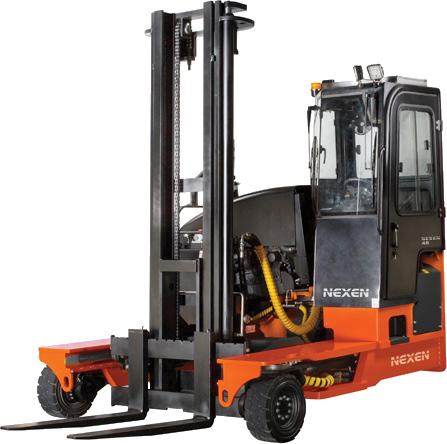
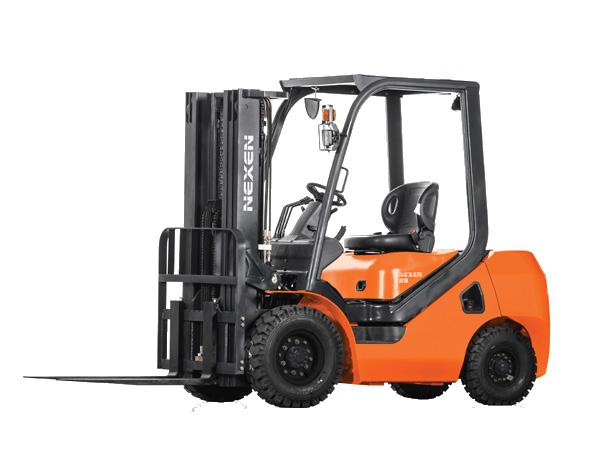
Wide Range of Diesel
Loadmaster® Sideloaders Rough Terrain Compact 4WD
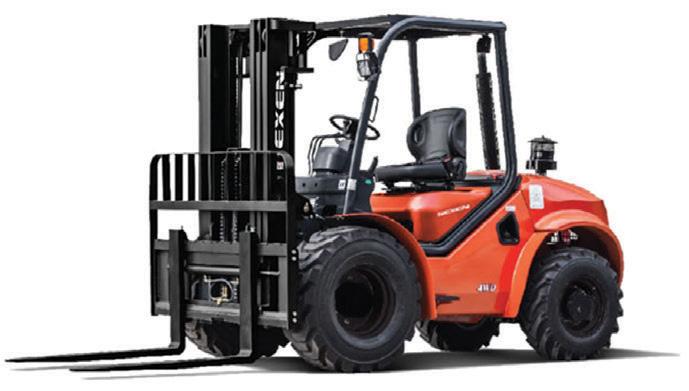
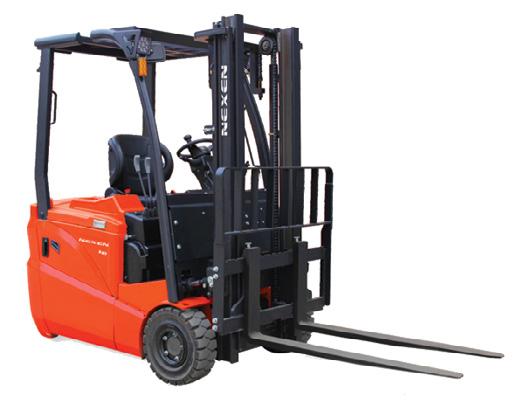