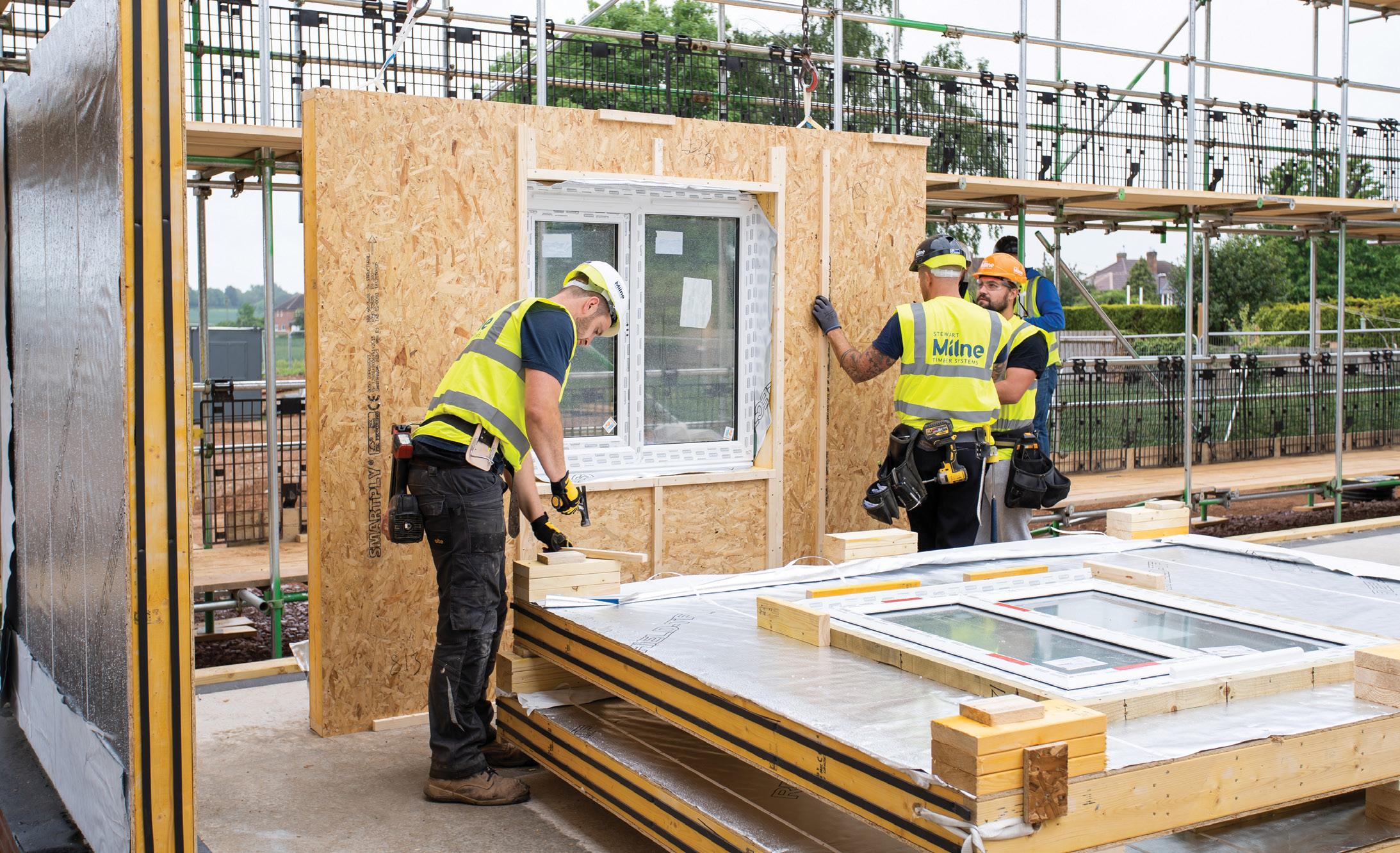
5 minute read
The Key to Net Zero
John Smith, technical director at Stewart Milne Timber Systems (SMTS), highlights why a ‘fit and forget’ and ‘fabric first’ approach is the best solution for the housebuilding industry to become carbon neutral by 2050.
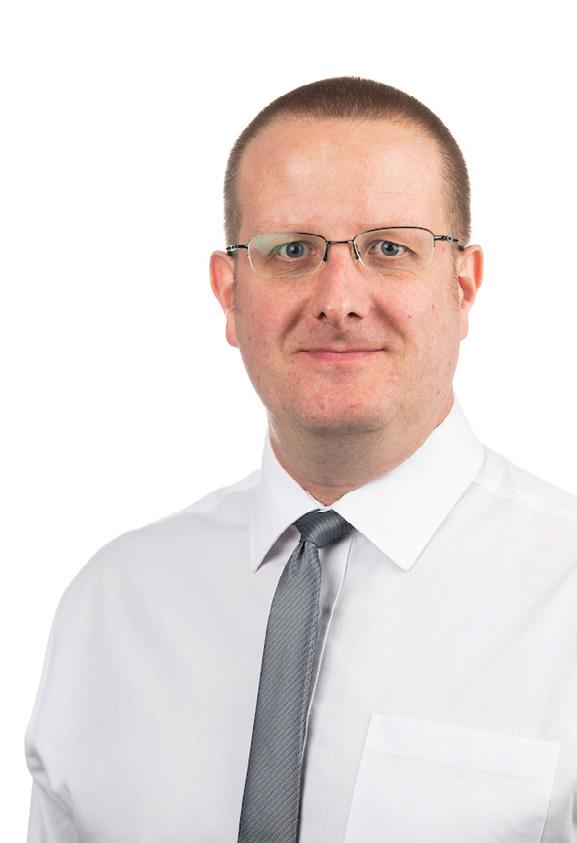
Since 1975, SMTS has promoted the use of a fabric first, fit and forget approach to construction. It is not a new concept, but it is absolutely one which, now more than ever, is crucial in fulfilling the large housing gap and achieving net zero by 2050. Sustainability and eco-friendly practices have moved from being ‘nice-to-have’ to being an essential part of every business across all sectors and, as one of the UK’s largest industries, construction has a key part to play in creating a system where circularity and sustainability take precedence in the supply chain.
Additionally, Covid-19 has impacted significantly on household finances and further highlights the UK’s need for new affordable housing stock to be built quickly and at volume, all while meeting green targets and delivering significant cost savings. Although the pandemic has posed major challenges for the industry, it has also offered opportunities to pause, take stock, and consider the adoption of fresh initiatives that drive better efficiency. And when it comes to efficient building systems, it is hard to beat ‘fit and forget’ timber frame solutions.
By adopting timber frame solutions, the speed of on-site construction increases rapidly, with the possibility for homes to be installed and made watertight in a matter of days, saving costs for housebuilders. A fabric first approach is vital in maintaining the lifelong performance of the building. Energy-saving can be seen from the moment materials are sourced, until they are installed in the final build, and continuously throughout their lifetime. At SMTS we have developed build systems that can provide U-values as low as 0.13W/m2K. So, when it comes to meeting the 2050 net zero target, as well as being commercially viable – there really is no comparison to timber frame solutions.
Structural timber has the lowest overall carbon dioxide footprint of any building material and, on average, replacing just one cubic metre of concrete with timber in construction can save a tonne of CO2
emissions.
Our Sigma® II Build System, developed over 10 years ago as part of the Sigma® home at BRE in Watford, the UK’s first zero carbon home, was an integral part of A2Dominion’s Bicester Eco Village development – the UK’s first eco town – and is the perfect example of the fit and forget approach and all it can do for communities, residents and the planet.
With an aim to deliver the most sustainable living in the UK for its residents, by using this system, 94 homes in the eco-village benefited from greater thermal properties and lower energy consumption, resulting in highly fuel and energy efficient dwellings. Our Sigma® II product takes ‘whole life costing’ into account, as well as risk and homeowner impact. When building with timber frame, a home can be designed as one integrated system with a fabric first approach as energy efficiency is locked into the home’s core; without a reliance on micro-renewable bolt-ons which require regular maintenance and are likely to need replacing during the life of the building.
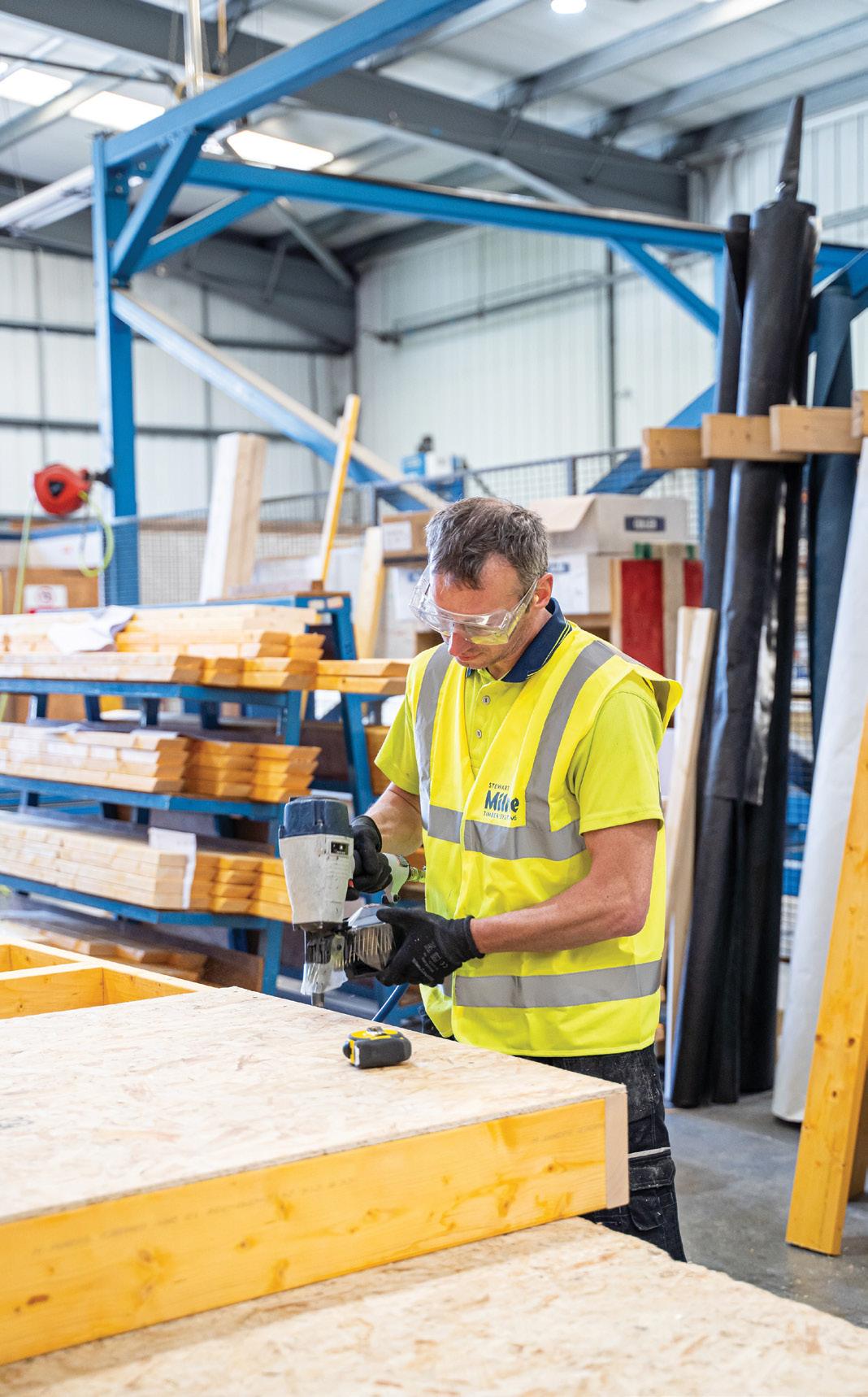
Bicester Eco Town
A2Dominion’s development in North West Bicester is a 393home project, aiming to deliver the most sustainable living in the UK for its residents. With the homes designed to achieve true zero carbon rating, delivering energy efficient, good quality affordable housing is crucial to the success of the project.
Ultimately, a fabric first approach will save the homeowners money and give them peace of mind that their home will deliver the designed energy performance. As we know, timber has superior energy efficiency and low embodied carbon, meaning homes are naturally warm in winter and yet still cool in summer, allowing residents to enjoy the benefits of better energy efficiency, air quality and exacting fabric quality which is built to last.
As well as the benefits of a fabric first approach to energy efficient homes, utilising an offsite manufactured timber frame build solution also provides homeowners with confidence in the quality of the building fabric, and that the energy performance of the home will be in-line with the design intent. By considering the whole life costing and the environmental impact of home building, alongside our development partners involved in Bicester Eco Village, we were able to design one of the most exciting, high quality and sustainable villages in the UK.
As an industry, we know that changes must be made to play our part in creating a better world and to counter the impact of global warming in a more meaningful way, and the most effective way to do this is from the outset, with a fabric first mentality that addresses the whole-life issues head on. Timber frame solutions developed through offsite construction are one of the few processes within the industry right now that couples true energy efficiency throughout its value chain with financial benefits for suppliers and consumers which will aid in making a true and significant contribution towards the construction industry achieving the 2050 net zero goal.
We have a lot to contend with as we navigate the post-Covid recovery, fight climate change and consider political and economic changes which will inevitably impact our industry. However, making changes now, from the ground up, will future-proof construction businesses, provide a commercial advantage and develop a better world for communities throughout the UK.
More at www.stewartmilnetimbersystems.com
Timber systems were therefore an ideal fit for the priorities of the ambitious task at hand.
The project at Bicester was the UK’s first eco town, designed to achieve high standards of environmental sustainability. SMTS worked with A2Dominion and Willmott Dixon, the main contractor, to provide its Sigma® II Build System for 94 of the first 393 homes as part of the ‘Exemplar’ phase of the project.
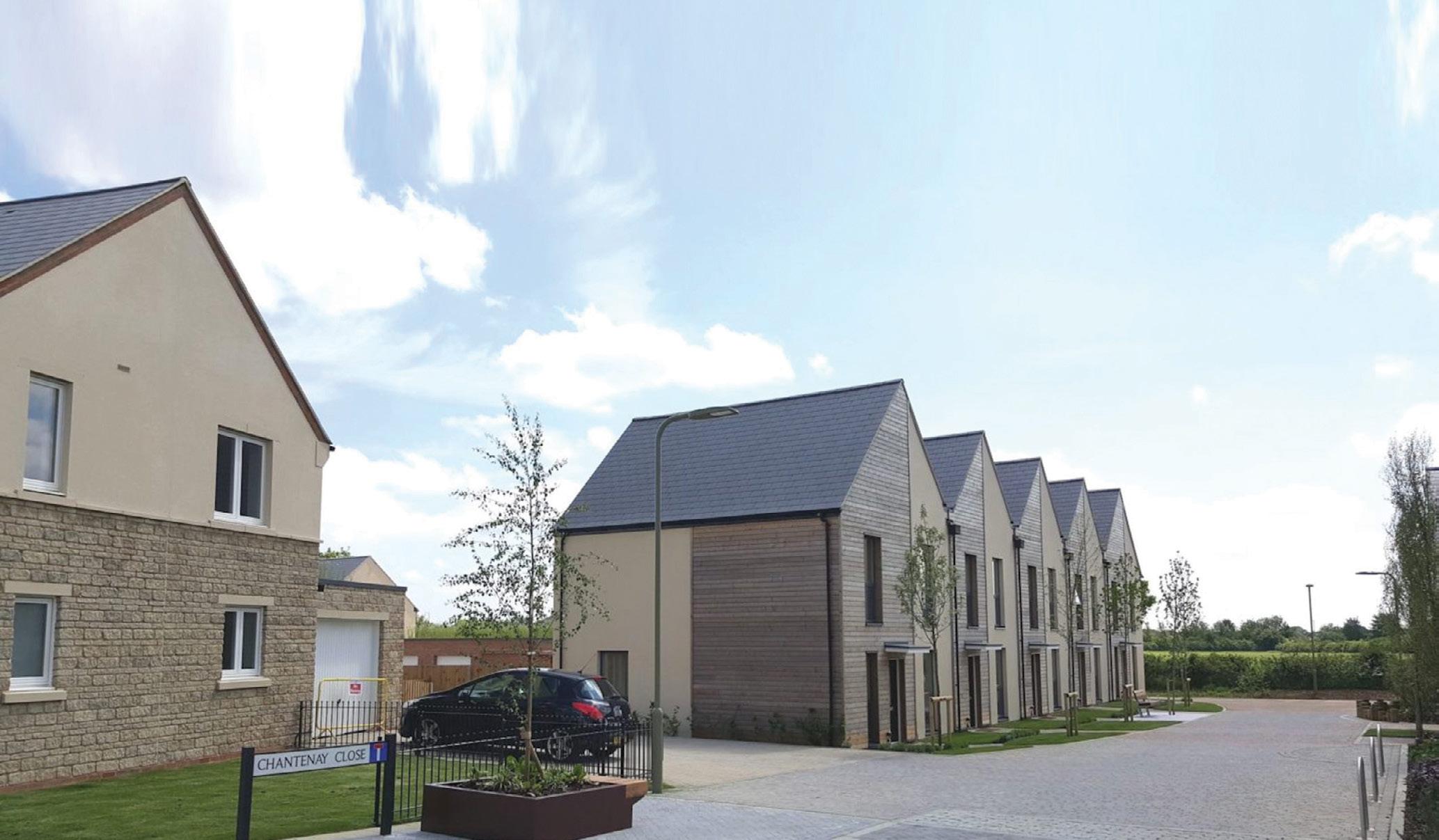