
11 minute read
Changing the Timber Mindset
Vastern Timber is the largest hardwood saw-milling company in the UK, with the vast majority of its wood bought and sold within one hundred miles of its sawmills. We spoke to managing director, Tom Barnes about homegrown wood, thermal modification and supply and demand.
How has the last 12 months been for the business?
Q: It’s been a rollercoaster but with more ups than downs. Apart from the initial lockdown in March 2020, demand for our timber has been strong and the last nine months have been our busiest ever. As well as general high demand, shortages of imported timber and an increasing focus on supply chains have pushed specifiers and customers towards homegrown timber and we have definitely benefited from that.
Q: The timber market appears to be very busy right now and prices are rising. What is driving this and is it affecting the homegrown market?
The construction sector drives the timber market, and I am surprised by how busy that has been. I think most of us were expecting a recession on the back of the Covid pandemic but it seems the opposite has occurred. High demand in this country has been replicated in the USA, Australia and across Asia, which has created a very competitive environment. At the same time, supply has been constricted by lockdowns and for various reasons large supply countries have reduced felling. The consequence is that prices for some timber products have doubled and availability has halved over the last year. The knock-on effect is that UK softwood log prices have increased by 40% and competition for them is fierce. The hardwood log market is less affected because there are fewer companies able to process them but prices are rising. It’s a good time to own woodland!
Q: What are the reasons for using homegrown timber cladding as opposed to imported species – e.g. Canadian western red cedar?
We grow plenty of species in this country that are suited to exterior timber cladding. Homegrown western red cedar, larch, oak and sweet chestnut are all suitable due to their natural durability and with the help of thermal modification we can now also use native ash, poplar and sycamore. In many cases the homegrown versions are cheaper than imported timber. We do not have enough wood to satisfy the huge demand in this country but recent supply shortages and huge price increases of Canadian cedar and Siberian larch demonstrate that our reliance on importing leaves our plans to build with more wood in jeopardy. I believe that we must aim to be more self-sufficient which means planting more and using more.
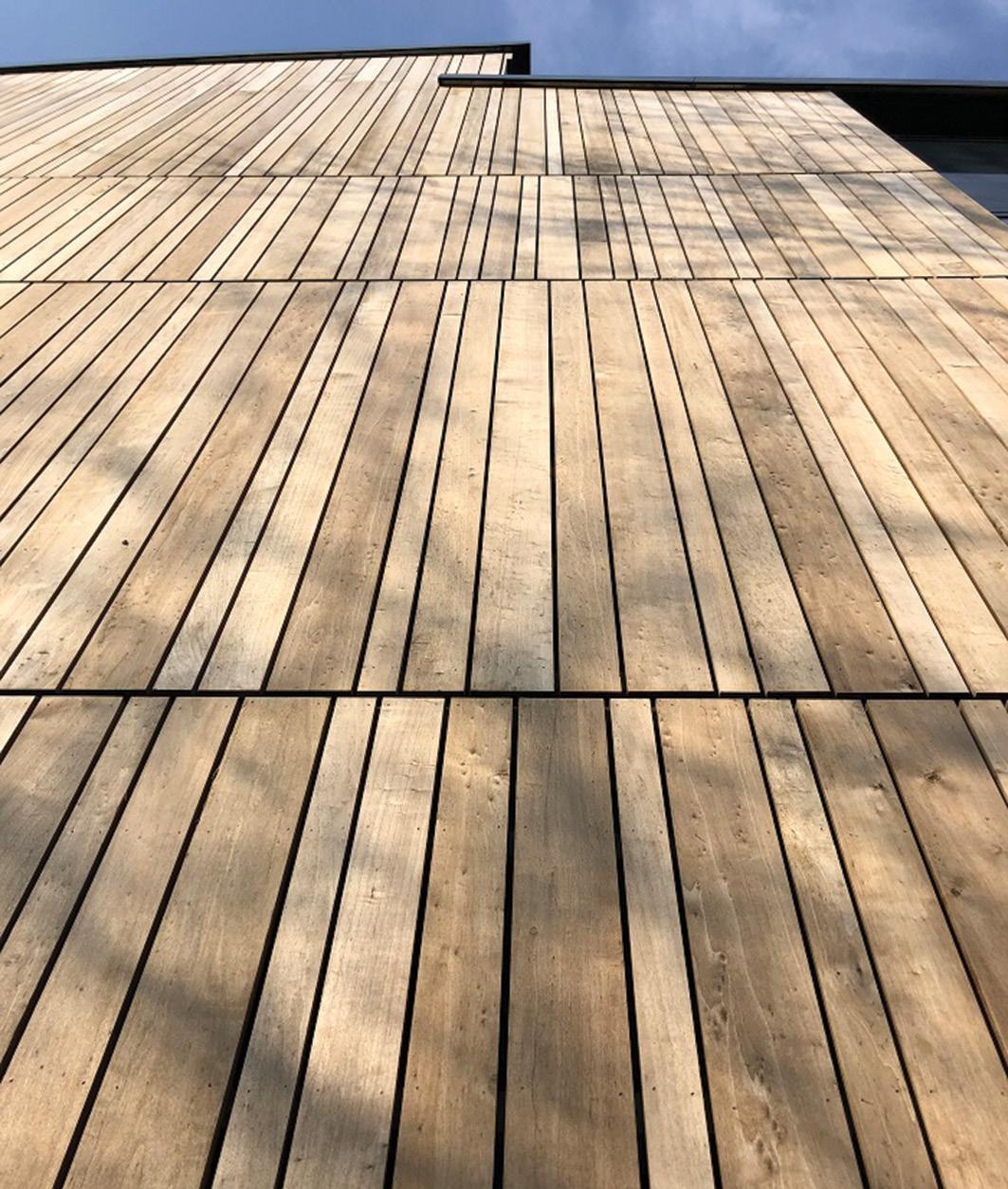
Q: What are the benefits of modified timber above ‘natural’ or un-modified material?
There are benefits both in terms of functionality and long-term availability. Functionally modified woods are altered to enhance a combination of characteristics including durability, stability and consistency. Modern modification processes tend to produce material that is as good as, or better than, the most durable and the most stable natural timbers, without the problems associated with extractives such as tannin or cedar oils. Considering the long term benefits, modification allows us to create high performing timber products without relying on species that take many hundreds of years to grow such as old growth western red cedar, oak or iroko. Because these products are created from pines and quick growing hardwoods that take between 25 and 50 years to grow, we can increase the amount of useful long term timber available in the future, the amount of carbon locked up in the built environment and the percentage from local sources.
Q: What applications are suitable for modified timber – can it be used structurally?
Durability and stability are the two key benefits of modification and as such the most common uses for the material are exterior cladding and semi-structural uses such as decking and external joinery. Modification does not tend to improve the structural qualities of timber and in some cases, such as with thermal modification, the bending strength of the wood is reduced. Unless the structure is external and requires durability, there is no need for modified wood.
Q: The Brimstone range is the only UK grown thermally modified timber – what made you develop this product originally?
Brimstone grew out of a collaboration between partners including Grown in Britain, BRE and industry who joined forces to consider solutions to the poor state of our native broadleaf woodlands. Out of this came the idea that by thermally modifying fast growing white hardwoods we could increase demand for the timber, thereby increasing its value and as a result boost rates of woodland management. As we at Vastern Timber already had all of the capabilities to process the raw timber, it seemed like a logical step to explore the potential for producing thermally modified wood from homegrown hardwoods.

Q: As is widely reported, a healthy UK homegrown timber supply needs more trees to be successful – not just for a healthy construction industry but for hitting zero carbon targets – can the UK forests supply enough raw material to sawmills to satisfy the market?
The simple answer is no. But the data suggests that global forests cannot supply our future needs either. We face the perfect storm of declining domestic supplies caused by a lack of planting and increasing global competition for timber as countries urbanise and attempt to reduce embodied carbon in buildings. Add to this mix the loss of forest due to deforestation, disease and climate change and it is hard to see how we will be able to source enough timber to achieve our ambitions. In April I spoke to the Parliamentary Group on Forestry and Tree Planting, urging them to develop a National Timber Strategy to reconcile our increasing demand for timber and timber-based products with reducing national and international supply. Ultimately, we cannot control international supply but we can take bold steps to boost domestic forestry for the future.
More at www.vastern.co.uk
The installation of Brimstone timber at the Sylva Wood Centre helped transform an old grain store into an exciting new workspace showcasing the best of British timber.
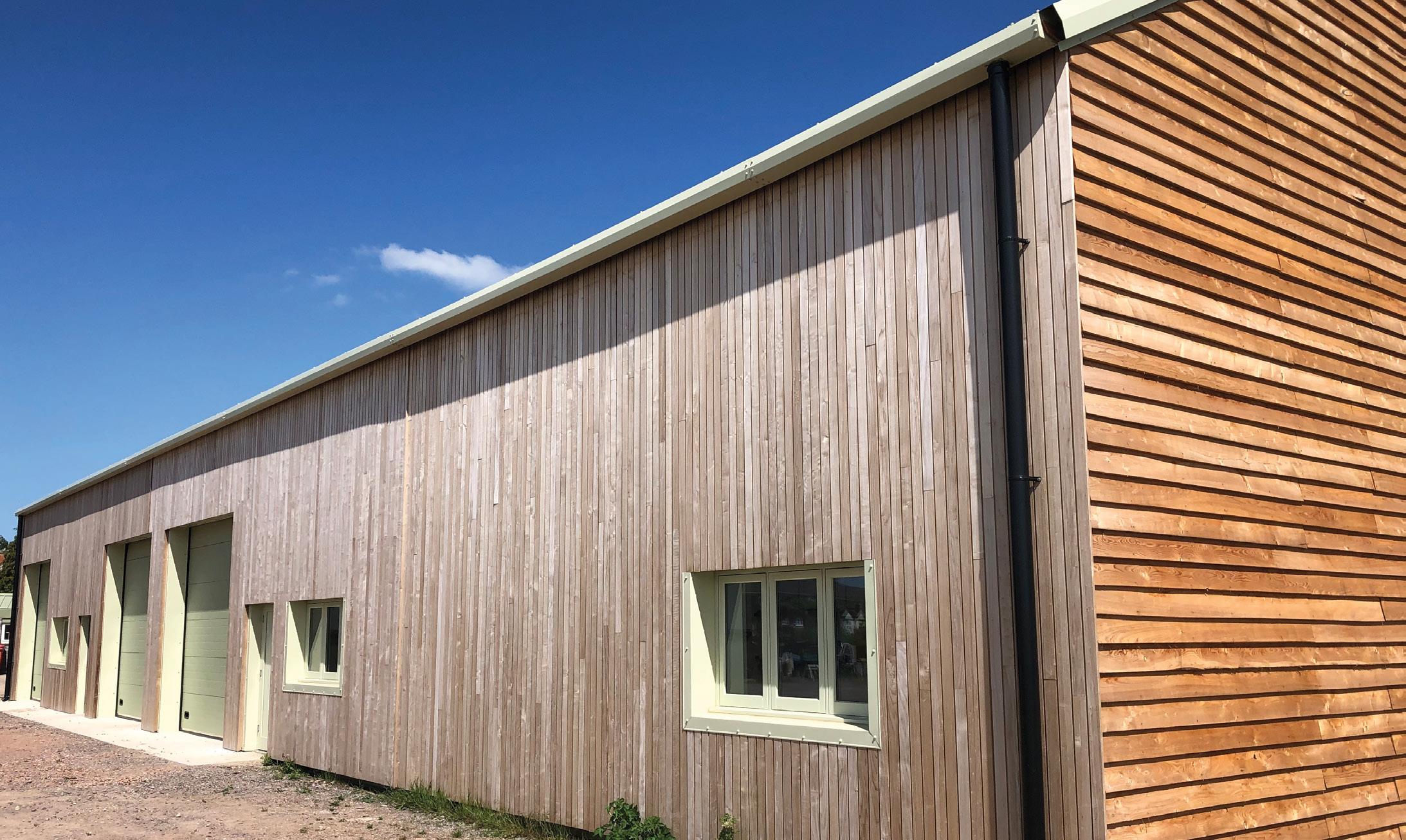
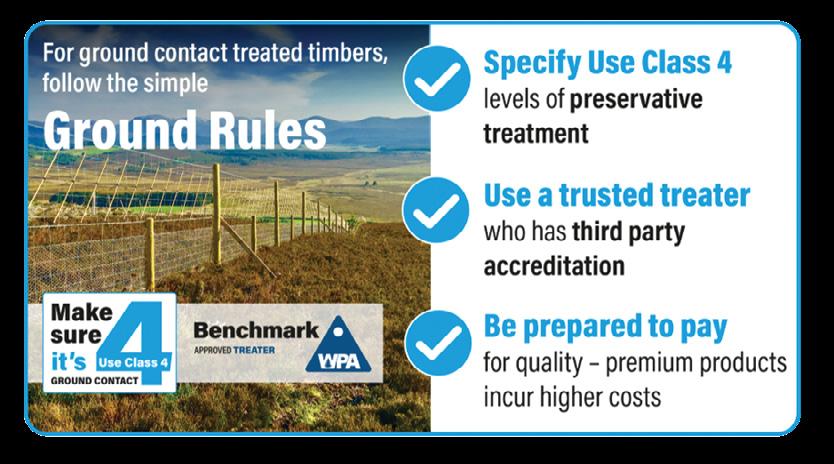
Optimum Performance: why treated wood works
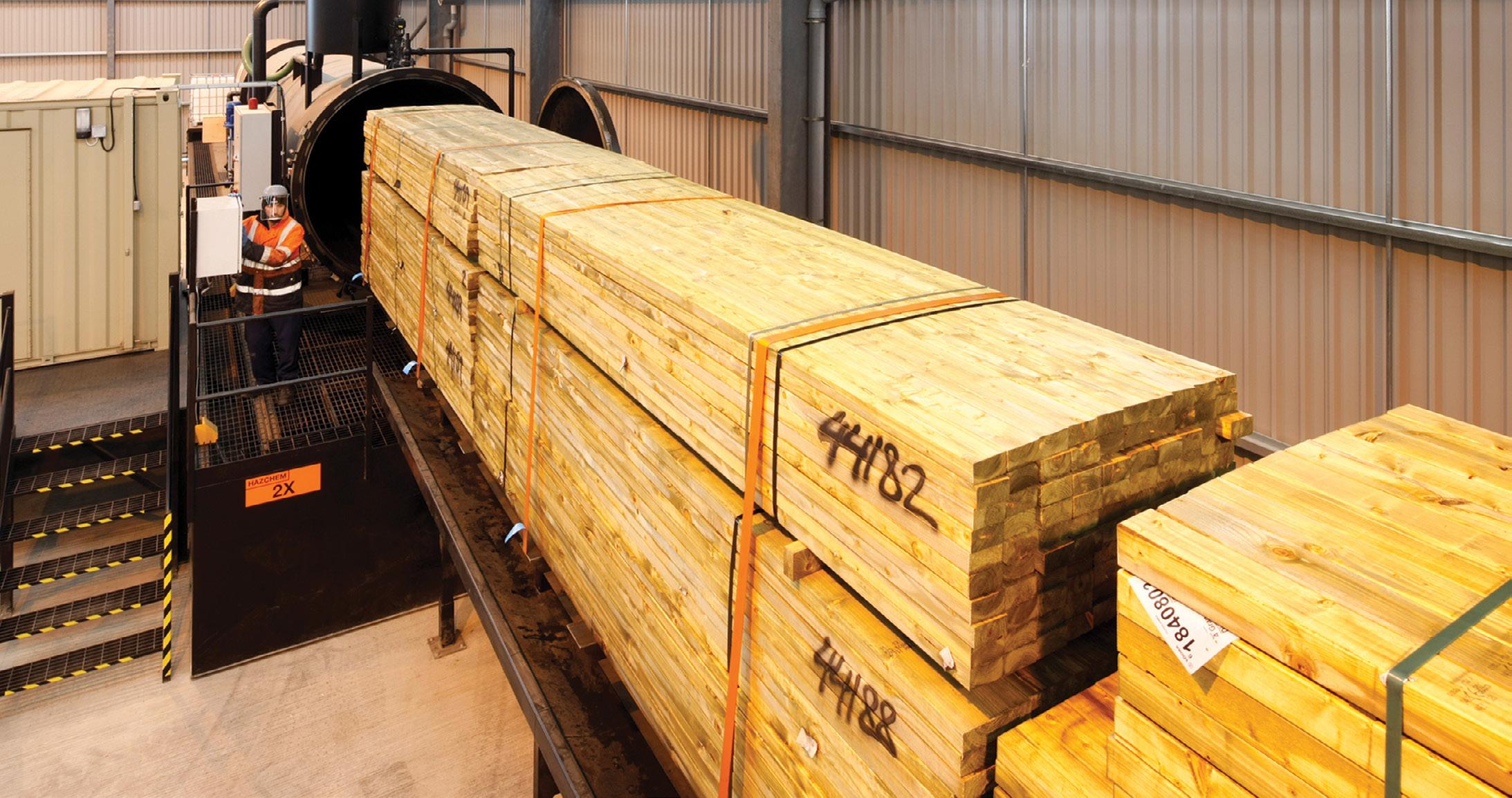
As trade associations unite in a campaign to grow demand for preservative treated wood, Gordon Ewbank, CEO at the Wood Protection Association, highlights why using the right product in the right place is so important.
The Timber Trade Federation (TTF) is making third-party quality assurance mandatory for members producing treated wood products by July next year. In the meantime, in partnership with the Wood Protection Association (WPA), an educational campaign to raise supply chain knowledge about how to specify and use treated wood correctly has just been launched and the campaign’s first advertisements are appearing now in key trade magazines.
The Confederation of Forest Industries (Confor) and the Timber Decking & Cladding Association (TDCA) have joined forces with the TTF and WPA to drive the campaign’s educational messages into the supply chain to help improve buyer understanding and change perceptions about the performance of preservative wood protection.
The TTF Action Plan
The TTF treated wood action plan has been developed in close collaboration with WPA and is designed to build confidence in the choice of preservative treated wood for ground contact applications, so creating the conditions required to grow demand for added value wood products. The key elements of the 3-point plan are:
• Preservative treated wood must be accurately and unambiguously specified/purchased, for use or resale, and is clearly identified at all points of the chain as fit for the intended purpose • Customers purchasing treated products from TTF members must be provided with adequate information and, where appropriate, training to be able to use and install those products safely and effectively • Preservative treated wood must be produced by or purchased, directly or indirectly, from a treatment provider whose operation has been assessed and approved under an independent and reputable accreditation scheme (by July 2022).
“Using the right product in the right place – and actively making sure the wrong product does not go into a project – is a responsibility which runs right throughout the supply chain,” says David Hopkins, TTF CEO. “This means labelling the goods properly so they can be clearly identified by customers and making sure an accurate product description is carried all the way through the supply chain – from the treatment plant through to merchants, to builders to architects, and others. Using the right product in the right place is a responsibility which runs right throughout the supply chain and something that we must get right. It is only by working together that we can achieve this.”
The Code for Construction Product Information
This campaign also connects into the development of the Code for Construction Product Information (CCPI). The CCPI arises from the issues across construction first crystallized the Hackitt Review, which was followed by two further reports from the Competency Steering Group for Building a Safer Future, including ‘Setting the Bar’. The Construction Products Association (CPA) is launching an industrywide consultation into the new CCPI, to gather the views before it is formally launched later this year. The Hackitt report confirmed radical change was needed for construction products, particularly in the areas of testing and marketing, and the need for a sector-wide approach to providing clear, accurate and unambiguous product information.
While the Grenfell tragedy may not have involved timber products, it has impacted the commercial landscape for all building materials and claims for performance right through the supply chain. This links very directly into the first element of the TTF Action Plan for treated wood, namely ‘treated wood must be accurately and unambiguously specified and be clearly identified at all points of the chain’. This message is proving very timely and gives an added focus and impetus to this initiative.
Share in the WPA’s passion for treated wood
WPA is delighted that major timber trade associations are collaborating closely to help the UK market for treated wood grow. We are happy to talk with any other organisation who shares our passion for wood protection technology and the industry’s mission to realise the full potential of wood as a sustainable, low environmental impact construction and landscaping material.
With timber increasingly being recognised as our ‘go to’ construction material of the future, it’s crucial that it is specified correctly. Ensuring that the timber has been sourced from sustainably managed forests is paramount, as is checking that it is treated correctly to the specified Use Class.
ndependent bodies, including
Ithe Committee on Climate Change, have reported that favouring timber over high carbon materials such as concrete and steel is one of the most effective ways to reduce carbon emissions. This is where timber treatment really comes to the forefront; providing long term protection against fungal decay and insect attack to one of the most sustainable building materials.
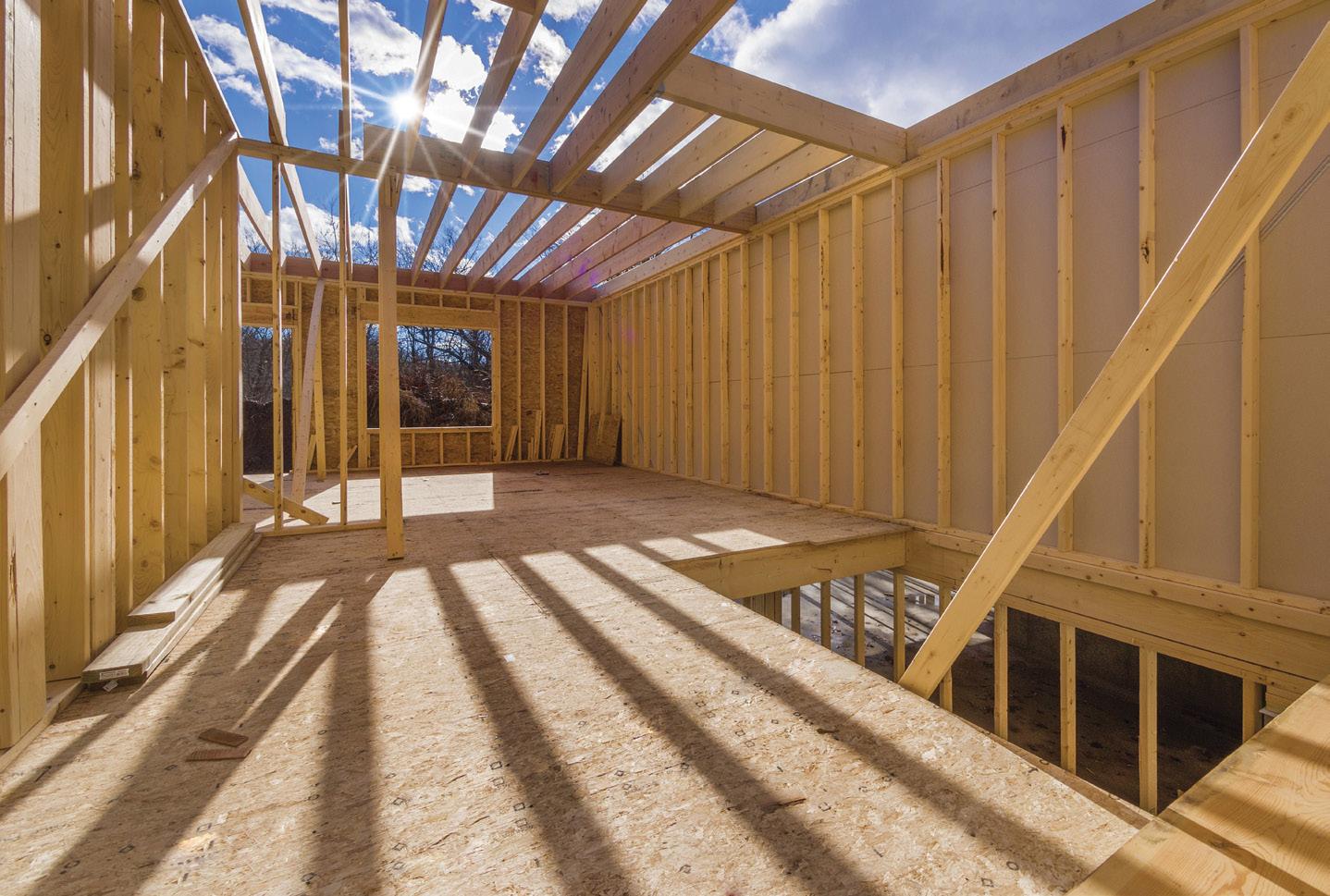
A new water-based low pressure preservative treatment
To help meet the evolving needs of construction timber product specification, Lonza Wood Protection has recently launched VACSOL Aqua 6118 which can be used to treat timbers in Use Class 1, 2 and 3 (coated). More commonly known as VACSOL 6118, this new water-based low-pressure preservative treatment is both metal and VOC-free.
VACSOL 6118 is a Biocidal Products Regulation (BPR) authorised product. At Lonza we commit to obtaining full BPR authorisation for products that we are planning to launch to market. This process is a substantial investment and involves passing stringent risk assessments, as well as generating extensive data and studies to prove that the wood preservative is effective against wood destroying fungi and/or insects. The BPR requires data on the possible exposure and toxicity to humans such as reproduction toxicity, carcinogenicity, or endocrine disruption etc., as well as data on environmental impacts such as accumulation in soil or ecological toxicity.
A focus on environmental impact
Investment in BPR authorisation allows Lonza Wood Protection to confidently assure the market that timbers treated with VACSOL 6118 are non-hazardous to human and animal health, and to the environment. And, with an increased focus on the circular economy, timber treated with VACSOL 6118 can be recycled or reused at end of life.
In addition, to help timber treaters reduce their carbon footprint VACSOL 6118 has been designed as an easy-to-use concentrate that is diluted on-site to meet individual business requirements. against fungal and insect attack around general building timbers and joinery components. For Use Classes 1 and 2 it can deliver the desired service life of 60 years.
As VACSOL 6118 leaves the timbers virtually unchanged in their appearance, Lonza Wood Protection offer a range of colour options to help treatment companies confirm to their end customers that the timbers have been preservative treated. These TREATMENT MARKERS are a range of short-term (dye based) and medium-term (pigment based) colour options that provide an initial colour strike purely to indicate a preservative treatment has been added.
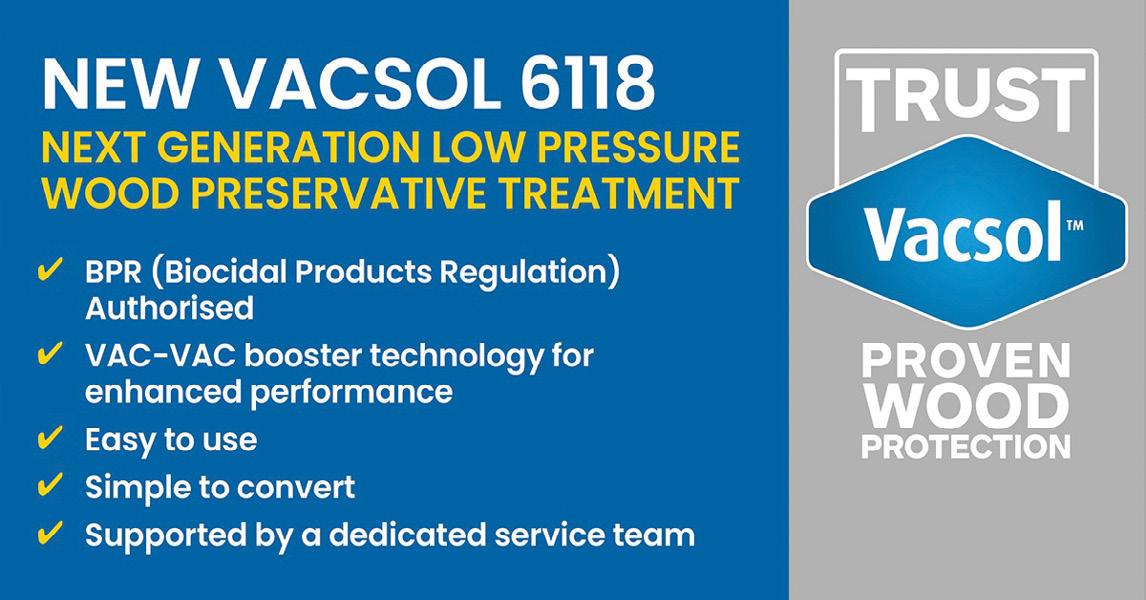
Tried, Tested and Trusted Wood Protection
With VAC-VAC booster technology for enhanced performance, VACSOL 6118 provides an effective ‘envelope’ of long-term protection

VACSOL Aqua 6118 is a BPR authorised product. Use wood preservatives safely. Always read the label and product information before use.