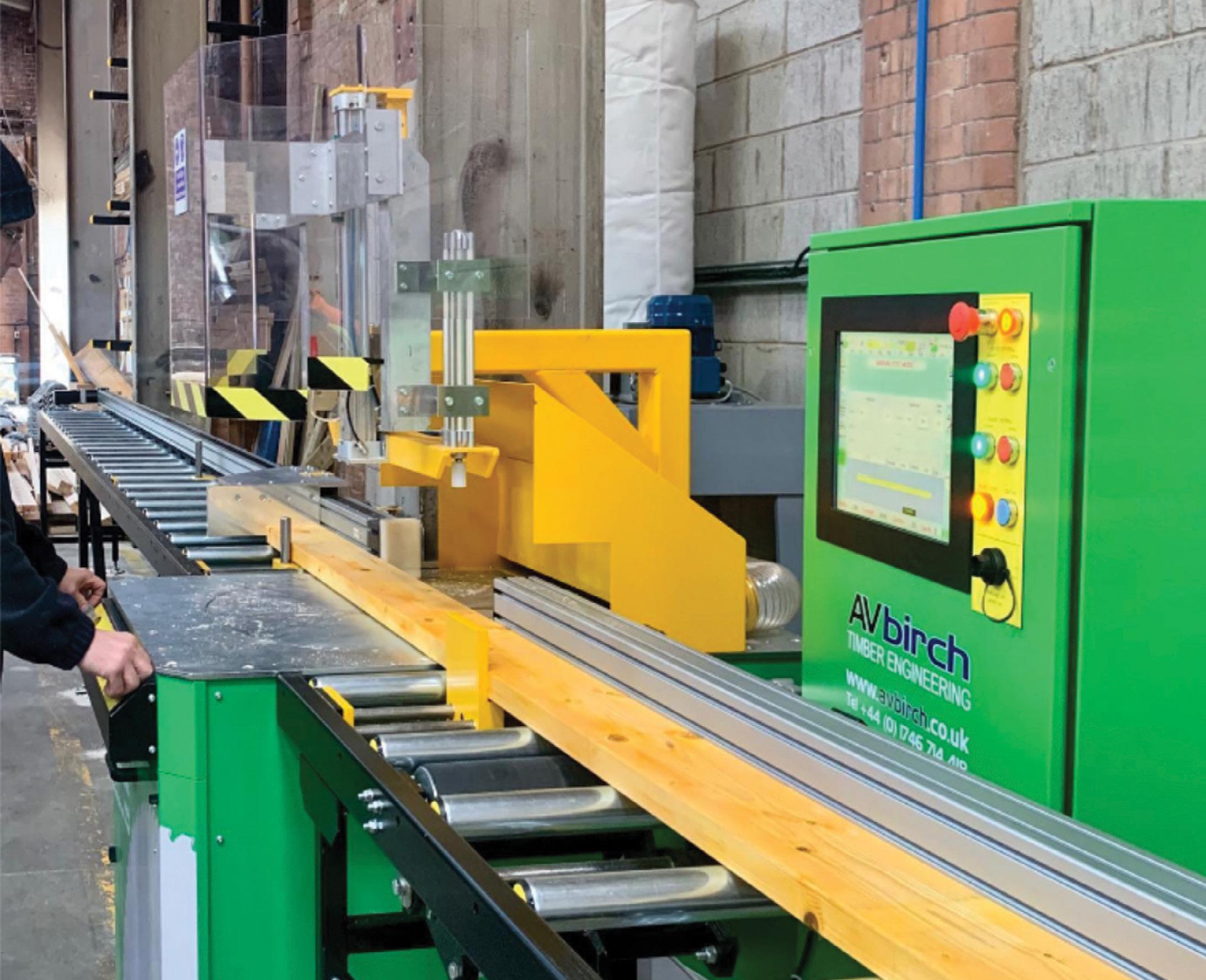
6 minute read
Optimum Timber Performance
Sticx deal in a wide range of timber systems and since 2011 have grown to become a specialist provider of sustainable design and build options. We spoke to co-founder and director John Maddock.
Sticx was founded by two directors that were very experienced in construction, rather than manufacturing. Chris Dermody had 20 years of experience running a company erecting timber frames for other manufacturers and John Maddock had 20 years of main contracting experience. This has served them well over the last 11 years.
“A framer’s performance at site level may only account for 20% of what they do, but it is almost entirely what they are judged on by clients,” says John. “Sticx has grown organically with a long list of repeat clients who know that we understand that the proven benefits of timber frame construction. Our ability to prefabricate open or closed panels is matched by our considered approach to delivery. We can erect prefabricated panels, stick build frames where access is limited, fabricate floor cassettes on or offsite and other options that are selected to suit site requirements.
“We moved from Bootle to larger premises on the Wirral in 2016 and have continued to grow, despite the recent challenges of Covid and timber price instability. We took the decision a few years ago that the advantages of metal-web joists were so significant that they would be our standard offering, so we set up Joistz Ltd to fabricate them for all our projects and to create a second line of sales to builders and other framers.”
Supply chain pressures
The timber material supply chain has been under real pressure for some time and the Ukrainian conflict has added to this – and does seem to be stabilising – but still has created a number of business pressure points. “Timber pricing went through a crazy period as Covid finished,” says John. “We buy directly from the importers and prices, that had been relatively stable for many years, suddenly went up around 250%. Given that the construction industry over the last 30 years has all but forgotten about inflation and clients expect extended fixed price periods, it has been a challenge.
“Fortunately, prices have dropped back down but the concern we have about this is that it reflects a reduction in demand, which is a result of a cooling market. The good thing as far as we’re concerned is that cementitious products and masonry all require high energy expenditure in production and this is now giving us an advantage that it’s difficult to see us losing.”
Not all about housing
With continual discussion over the quality and quantity of housing required across the UK, timber frame is in a perfect position to capitalise on the requirement for quicker and more sustainable homes. But is housing still the main sector driving timber frame specification – or have others started to catch up such as education and retail?
“Unusually, we have come the other way,” says John. “Most of our work was in education and student accommodation, until we made the decision to take our experience to clients who were interested in saving money through design improvement. We have clients now who are more willing to invest in design, to standardise details and to save money through
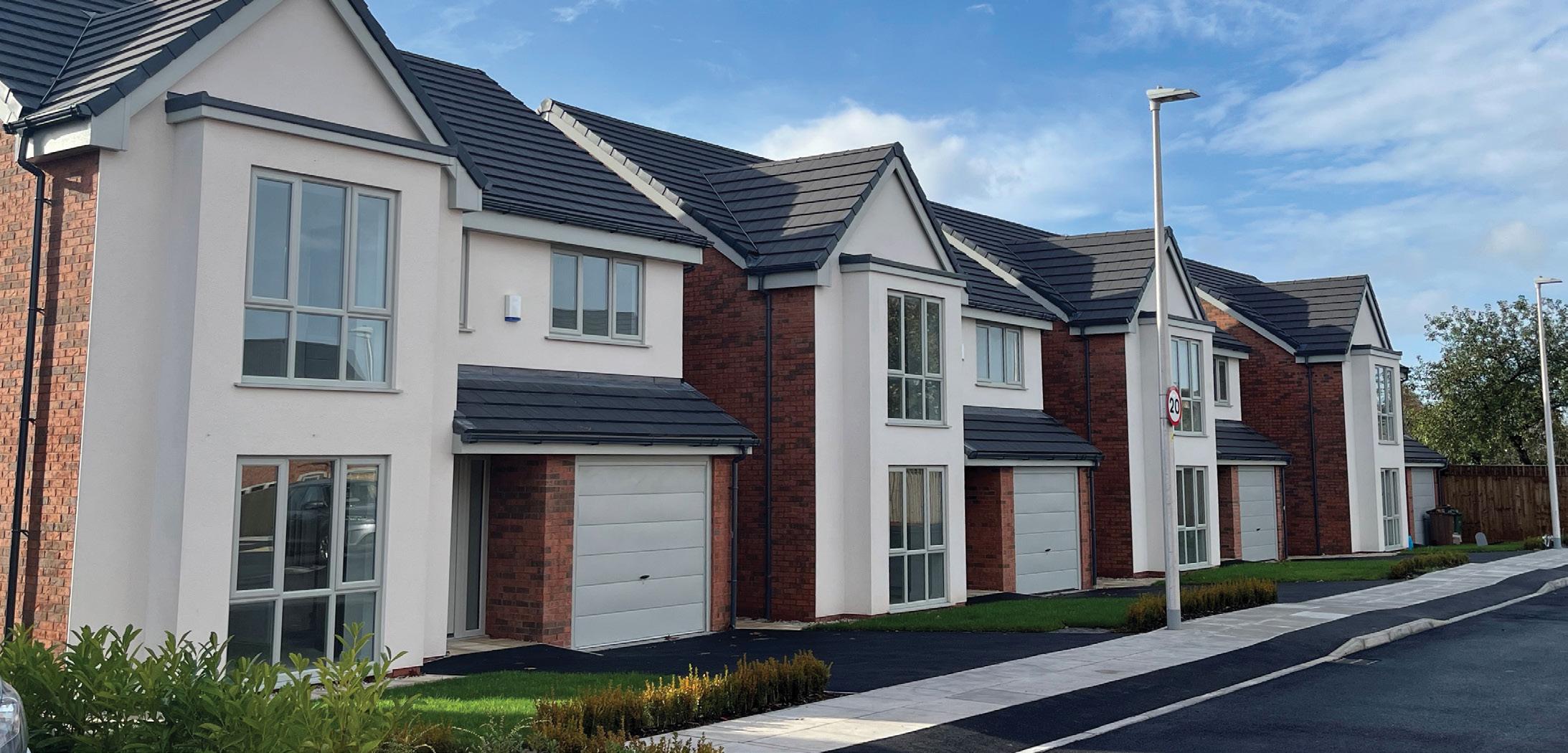
the elimination of waste. Whilst everyone is concerned about material price hikes, the real issue that is coming down the road is the skill shortages in traditional trades. Partnering with a specialist framing contractor, secures clients ability to deliver projects that they may struggle to deliver otherwise. Long-term relationships de-risk so much of the work, clients are really cottoning on to this.”
There has been a big uptake and interest in engineered timber – CLT and glulam – in recent years above the classic timber frame/panel systems? But questions surround whether CLT/ glulam is suitable for smaller development – is it cost-effective? “To find the optimum solution for a project, it’s important to have all the tricks at your disposal. Early involvement of a timber frame specialist allows architects and engineers access to the best solution for any particular project. It’s unlikely that CLT will be the best value solution for social housing any time soon, but it will start to sneak into projects where there are architectural imperatives, and as this happens it will be selected more by architects and engineers who know where to go to get the design support they need.”
The timber sector has been historically slow in the uptake of digital technology – is that true and how are you using the latest architectural and building design software?
“I think we’d argue that the timber frame sector has not been slow with digital technology,” adds John “Design is a large part of what we do. Practical and accurate design leads to waste reduction and successful projects and I would say somewhere around a third of our overhead covers our design costs. I think generally the industry needs to reverse the trend we’ve seen since the wholesale introduction of design and build contracting and invest in project designers.
“The main obstacle to the adoption of BIM and better use of the technology is the commercial approach of risk aversion. Clients not wanting to procure traditionally because they think they’d rather divest themselves of the design and measurement risk. It has lead us down a path where the people best placed to design out waste don’t believe it’s in their interest to do so because they aren’t paid a sufficient fee. Waste in the industry is hidden but there is so much abortive work and wasted, repeated effort. We can do so much more with the technology we have, but the procurement method must align itself with a progressive approach.”
Green and lean
The construction industry is under huge pressure to provide zero carbon design and adopt a more circular approach – how is Sticx ensuring high levels of sustainability, certification and streamlined offsite production processes? “We’re firm believers that panelised systems are the way forward. We think that there is a huge amount of wasted effort going into volumetric solutions where the concept is basically flawed. Timber is the only sustainable construction material. All of our material is PEFC-certified. Timber frame promotes better insulation detailing and the extra attention to design reduces wasted material and just as importantly wasted effort.
“We have partnered with the Sovini Group on Merseyside, who have a pipeline of 1000 new units to build. We are helping them to standardise their designs, to make the small adjustments that reduce wasted effort from following trades, to take the lessons learnt from site and feed them back into the designs for the next project. The partnership allows us to work as a team with our partners and the success of the relationship is a continuously improving outcomes for all of our partners. The entirety of this arrangement is the definition of sustainable building.”
How do you see the timber sector developing over the next 18 months and what plans has Sticx for 2023? “The rise of timber frame is inexorable. The climate emergency demands the use of sustainable materials – the skills shortage in traditional trades drives the need for more offsite fabrication and generally we think we’re riding that trend. We’re obviously mindful of the macro economic climate going into 2023: rising costs, lack of available money and a general slowdown in activity. We believe that timber frame will continue to grow its market share. The price of timber has dropped back to normal levels whilst cementitious products and steel, with the cost of energy in their production, will still be inflated over the next year. We see more clients adopting timber frame because of this and we expect to continue to grow.”