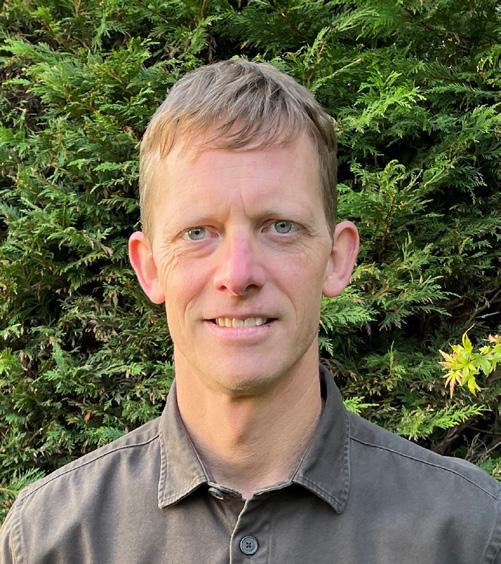
5 minute read
Homes for the Future
Designing and building energy efficient homes is part of what Peter Smith, Passivhaus designer and partner at Roderick James Architects, does every day using green oak and timber technology.

RRoderick James Architects (RJA) has been in existence for many years and was founded in the early 1980s by Roderick James and grew out of his pioneering involvement with the creation of the Centre for Alternative Technology (CAT). The main focus of the practice is to celebrate space and light within its designs and to express the structure of its buildings, using timber frame.
“Coming from a tradition of working with existing oak framed barns, the natural progression for the office was to develop these skills and adapt to using other timbers such as Douglas Fir, Larch and subsequently glulam,” says Peter. “To this day the use of timber as a sustainable building material remains core to our ethos, which can be seen in the wide variety of timber framed designs on our website.”
Green oak and UK timber
The practice specialises in using green oak – which is simply fresh oak that hasn’t been seasoned and dried out. This means it is much easier to work with. “Seasoned oak can be as hard and durable as steel,” says Peter. “As architects, we need to allow for potential movement and shrinkage in the oak frame as it dries. This involves employing some very useful ‘tricks of the trade’, such as separating the structural elements from glazing and plasterboard, creating shadow gaps which allow for the movement in the frame.
“Packers between the oak frame and wall panels allow the plasterboard finishes to sail past the oak and avoid cracks appearing in the plaster if the oak moves. Airtightness membranes are positioned to the outside of these packers and taped back to the wall and roof panels to ensure continuity around the entire building envelope. So provided you know how to deal with it, shrinkage and movement in the oak isn’t necessarily a problem – it adds to the character of the building.”
Homegrown UK timber is regularly used for RJA projects for the structural frames, external cladding and internal lining boards and often specify Douglas fir and larch, and spruce glulam for frames, with oak, ash, beech, pine and spruce amongst the many options for internal finishes and fittings. Peter says: “Our clients often ask for homegrown options, which can be cheaper and lower carbon than imported oak from France or Germany or birch, spruce and pine from Scandinavia or Siberia. Indeed, many of our clients can source their own timber locally, either from their own trees on-site, or from local sawmills and suppliers. Our COP26 House is a prime example of how we can make use of the timber readily available in this country, using clever design and technology to deal with the limitations of structural grading options or durability.”
Energy efficient to the core
Passivhaus design entails a rigorous approach to energy efficiency and is easily achievable from a self-build perspective. According to Peter, its basic tenets are based on five main principles during the design and build process – insulation, airtightness, ventilation with heat recovery, passivhaus windows for solar gain, and the avoidance of thermal bridges.
“Achieving Passivhaus levels is all about paying attention to these principles and taking care during construction that the details are done right,” says Peter. “It is not difficult, but everyone involved in the process needs to be on-board and play their part in achieving the goal. There is time and money associated with the attention to detail and additional materials (thicker walls with more insulation). But the investment pays for itself in the long run through reduced energy costs. Achieving Passivhaus status is also effectively an assurance of build quality, as you cannot achieve it without careful detailing and construction.”
Energy efficiency and an overall better understanding of sustainability has seen an upswing in the interest in timber design commercially, but also within the self-build sector. Of course, when it comes to timber frame projects, this approach has always been far more popular in Scotland than across the rest of the UK. But with volume housebuilders including Barratt Homes adopting more timber for their newbuild homes via Oregon Timber Frame, is this changing?
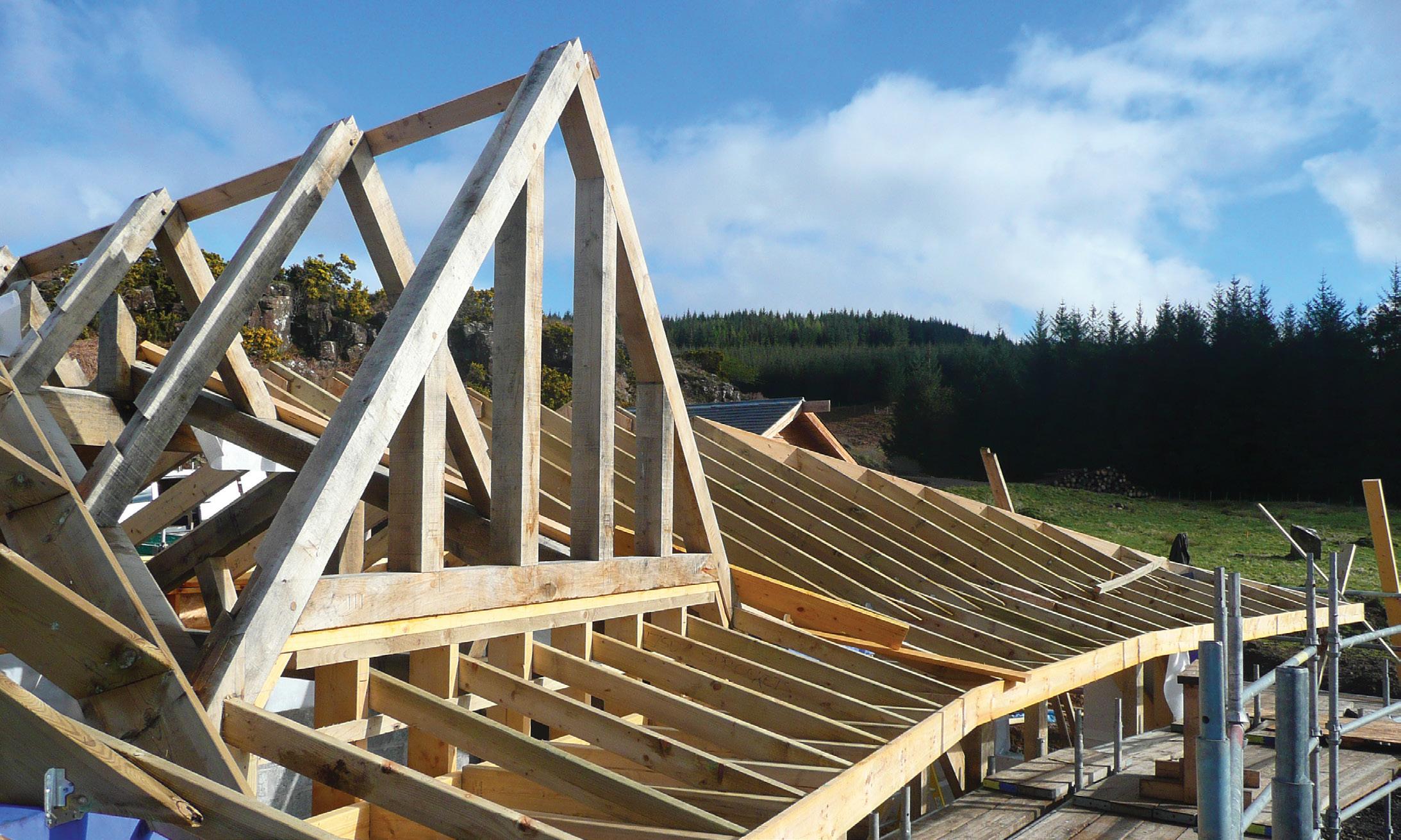
“I’m based in Scotland,” says Peter. “Where we have a strong tradition of building with timber – in fact most of our houses are built with at least a timber internal leaf to the walls, with either blockwork and render or timber cladding to the outside. Internal walls and roofs are predominantly timber construction. According to Wood for Good, 85% of all new homes in Scotland are built using wood. That’s almost three times more than in England and Wales. With recent advances in technology and supply chain issues, coupled with a sharp focus on embodied carbon, we have certainly seen an increase in the use of timber throughout the UK – especially so in our Devon and Salisbury offices. This has not confined itself to the self-build sector, with housing associations and commercial clients across the spectrum of the building industry looking to change to timber for construction.”

Standout schemes
What has been a standout home/scheme that you have been involved in personally and why? “The COP26 House, which itself was an adaptation of many previous RJA house designs (like our BAARN houses and other recent affordable housing projects), is definitely a standout project for me. Mostly because of the learning process we went through, looking in detail at every single component of the building with embodied carbon in mind – and how to reduce it to an absolute minimum. Another aspect of the project which made it special for me was the level of collaboration we achieved between more than 25 different companies who helped to deliver the house in time for COP26, to prove to the world that we can build beautiful zero carbon houses right now, with the materials we have readily available.”
With sustainability and environmental concerns within the built environment so important, RJA has a ‘RJA ZERO’ sustainability policy that is part of the overall aims of achieving the 2050 net zero targets. “RJA ZERO is a natural progression for what we have been doing as a company since our inception nearly 40 years ago,” adds Peter. “We continually push beyond the ‘norm’ of building regulations and common practice, to find better and more efficient ways of designing and constructing our buildings.
“Since I started with RJA in 2010, we have been building with timber of course, using the Fabric First approach of insulation and airtightness, but also insulating with natural, breathable, and recycled materials such as hemp, woodfibre and cellulose. As a Passivhaus designer, I can advise clients on how they can reduce future energy bills to an absolute minimum. We are now also focusing on circular economy and retrofit as ways of reducing embodied carbon in our designs. Achieving net zero as a country by 2050 is certainly attainable, we are aiming for 2030 as a business and also with our designs.”
2023 is looking busy for the practice with projects in store ranging from a tiny 24sqm Bothy in the Cairngorms to a multi-functional commercial project comprising a golf club, aparthotel, café, exhibition spaces and restaurant, as well as several brand new oak framed family homes
More at www.roderickjamesarchitects.com