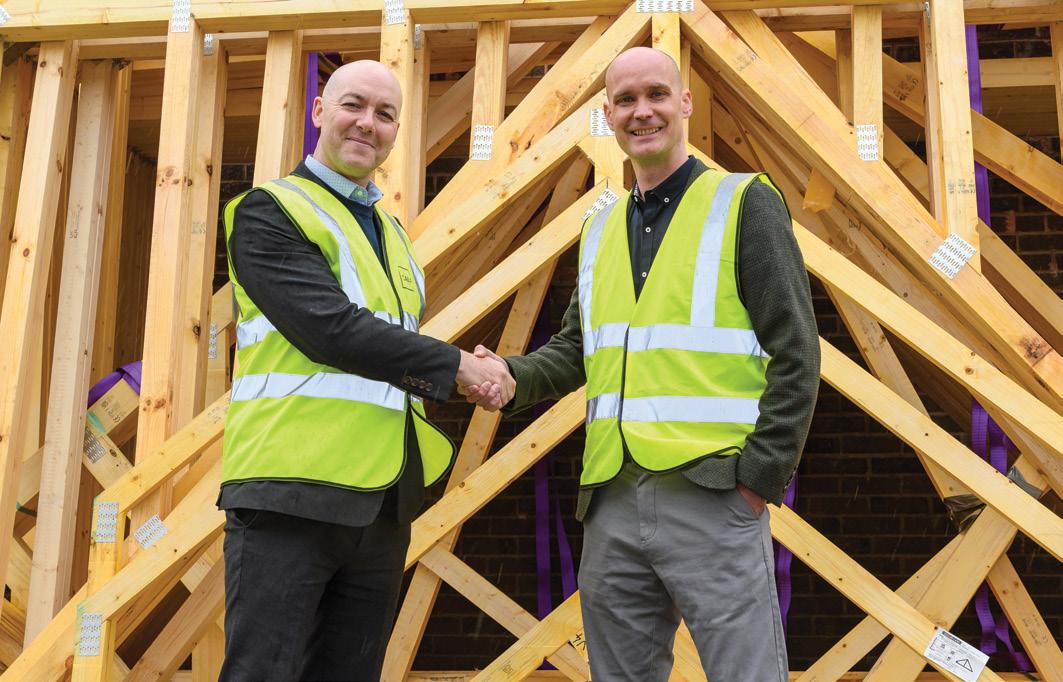
4 minute read
More Options for Zero Carbon Homes
Cala Group, one of the UK’s major homebuilders recently acquired Taylor Lane Timber Frame with the investment reinforcing the homebuilder’s commitment to its climate targets.
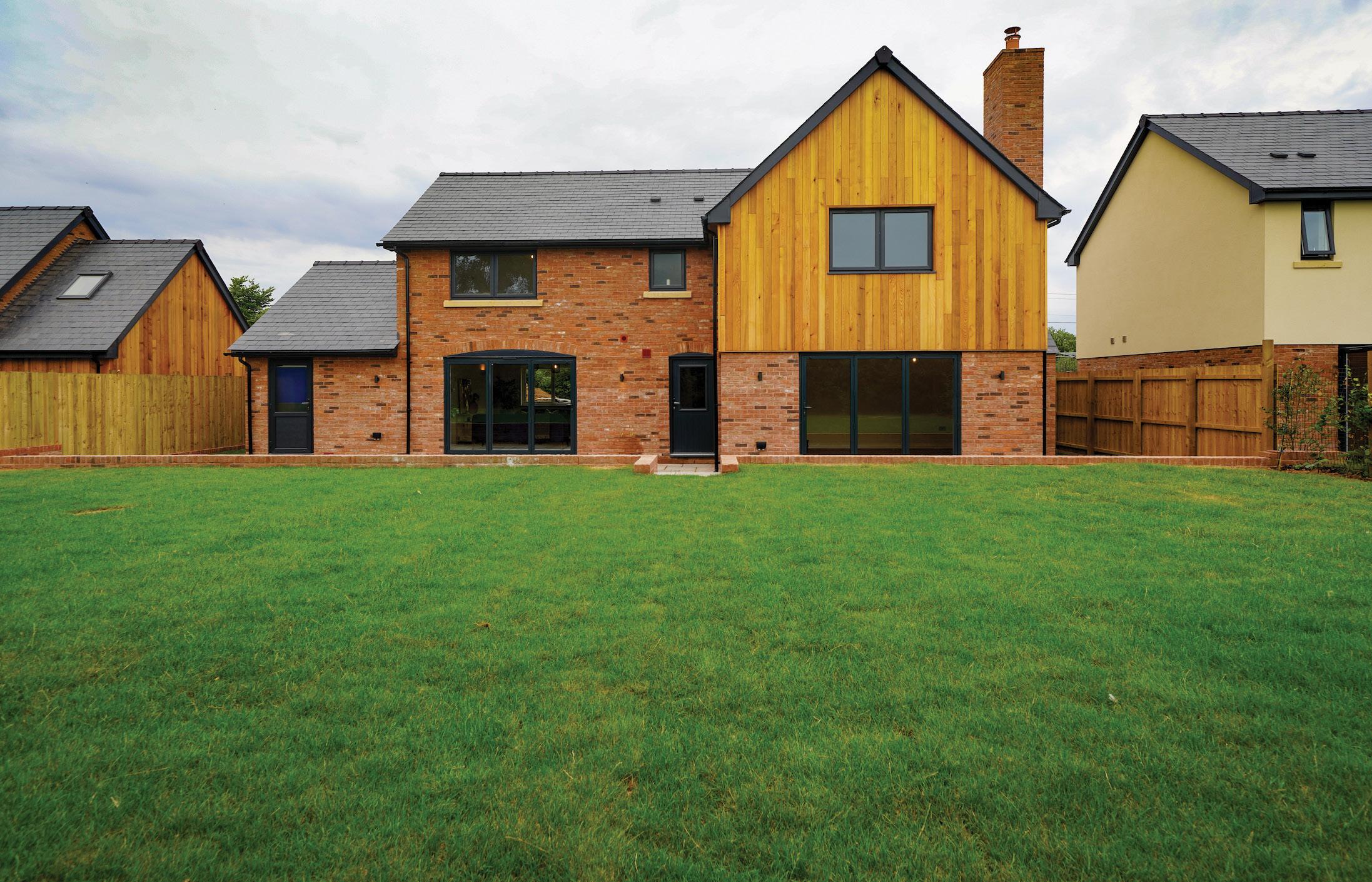
ICala Group announced the 100% acquisition of Taylor Lane Timber Frame Ltd in May with the investment helping drive Cala’s progress towards their sustainability targets and support delivery of the group’s ambitious growth plans in the South of England. Led by an experienced existing management team, Taylor Lane will continue to pursue the vision of their original founders, to deliver high quality products and excellent customer service to scale.
Cala started as the City of Aberdeen Land Association in 1875 and was the first Scottish company listed on the London Stock Market. Today, Cala Group is a subsidiary of Legal & General and comprises the Cala Homes and Legal & General Homes brands. Its carbon reduction strategy sets out their transition to timber frame across all the homes they build in England, where possible.
In Scotland, Cala has been using timber frame construction for over 40 years, and around 80% of Cala’s homes there are built using this method. The investment in Taylor Lane will help Cala to increase the use of timber frame in England to c.1,500 new homes per annum, over the next five years.
Fresh horizons
Taylor Lane Timber Frame was started in 1982 by co-founders Colin Taylor and Barrie Lane and operate from Hereford and a second manufacturing facility in Nantyglo, South Wales. The company produces around 2,000 timber frame units per year and employs over 175 people. Taylor Lane will supply Cala’s five English businesses in the Cotswolds and South of England, while continuing to service existing customers and grow their presence in the wider market.
“Taylor Lane is a successful business with an experienced management team and talented workforce, who share Cala’s passion for quality and service,” said Kevin Whitaker, CEO at Cala Group. “We look forward to working with the Taylor Lane team, supporting them as they continue to develop and grow their business to achieve the ambition of their original founders to deliver to scale.
“For Cala, this also demonstrates our clear commitment to delivering our climate targets. The investment in Taylor Lane sets out our path to transitioning to timber frame across our English developments, a key element of our sustainability strategy. The positive arguments for timber frame construction have never been more compelling. Generating up to 20% less embodied carbon than a typical masonry build and offering the benefits of speed and efficiency of construction and superior factory-built quality, the advantages of using timber strongly support our decision to invest in timber frame and grow our use in the future.”
The investment illustrates Cala’s confidence in Taylor Lane’s potential and provides a strong platform for continued growth, while ensuring both consistency and stability for Taylor Lane’s employees, customers and operations.
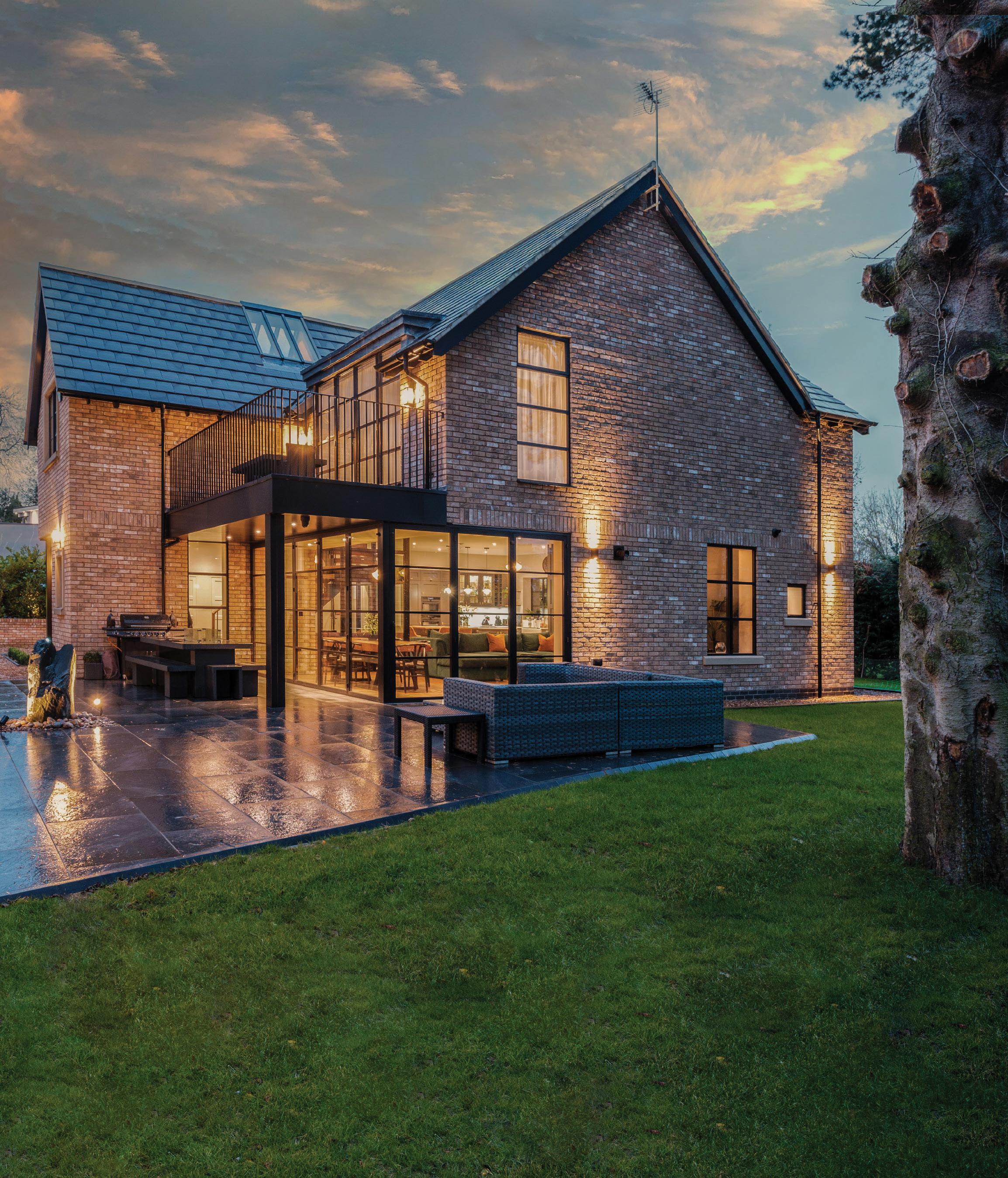
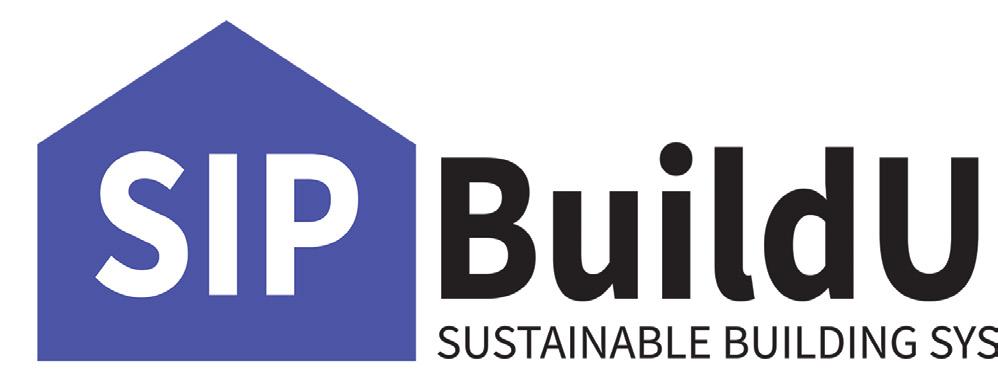
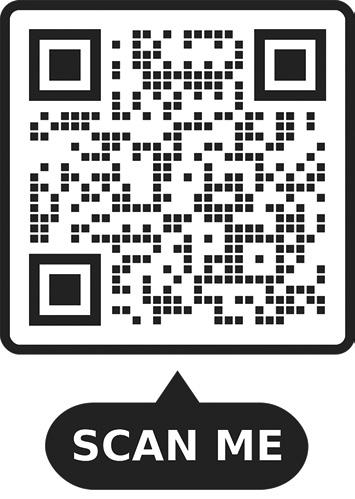
“This marks the start of an exciting new chapter for Taylor Lane and is a fantastic endorsement of our potential from a highly respected UK homebuilder,” adds Jonathan Lane, Managing Director at Taylor Lane. “We are delighted to being moving forward with Cala as our new owners. Over the past 40 years we have successfully grown Taylor Lane to a £30m turnover business delivering around 2,000 timber frame units per year, to a wide variety of sectors. This is testament to the vision of our cofounders, Colin Taylor and Barrie Lane, and the hard work and commitment of our employees alongside the quality of our product and our approach to customer service. We have robust growth plans in place, a loyal customer base and a talented team. We also have the security of Cala’s ownership and a pipeline of additional future growth to come from their transition to timber frame construction in England.”
Cala progresses towards carbon reduction targets
Taylor Lane and Cala Homes ensures that all timber sourced is either PEFC or FSC certified, promoting sustainable forest management via timber certification and Cala is also making positive progress towards achieving its targets of building homes for its customers that are operationally net zero carbon enabled from 2030, and reaching net zero total greenhouse gas emissions by 2045. Cala’s Carbon reduction data for the year ending 31 December 2022 shows absolute operational carbon emissions of 9,175t CO2e, down 8% against 2021. This reduction was achieved despite a 4% increase in the number of new homes completed in the year. The homebuilder also confirmed their Science Based Target (SBT), of achieving a 42% absolute reduction in Scope 1 and 2 emissions by 2030, has been formally ratified. Being owned by Legal and General, Cala’s SBT falls under the Legal and General target. In 2022, Cala made strong headway, with an absolute reduction of 16% in scopes 1 and 2 (against a 2021 baseline).
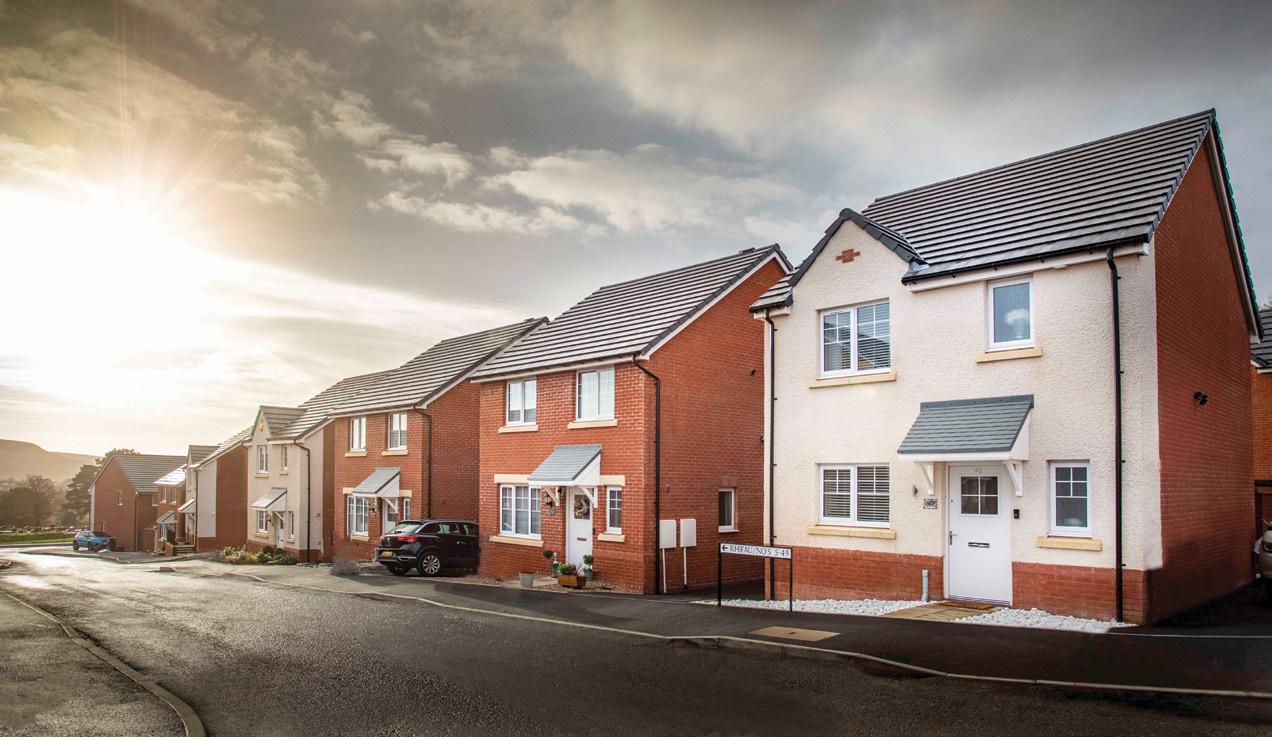
Building regulations, environmental impact and rising fuel prices have driven the demand for a genuine fabric first approach to low energy buildings. In response, Timber Innovations has launched a new innovative, systemised proposition – The Larsen ‘Kit of Parts’. This technical manual will assist anybody engaged in the design or procurement of low energy buildings and is available as an e-book.
Timber Innovations originally developed their low energy ‘Larsen System’ for relatively niche clients building Passivhaus certified houses but over the last couple of years the market for such has rapidly evolved. David Himmons, managing director of Timber Innovations said: “Clients have a greater understanding and need for buildings to perform. The spectrum of market sectors now demanding and understanding efficient building envelopes is such that it really is the new norm.”
A flagship project for the Larsen System is the new innovative Museum of Land Speed on Pendine Seafront. Together with the Caban, an affordable 14 room hotel which was also built using the Larsen System, they are part of the brand-new Tourism Attractor facility at Pendine Seafront, Carmarthenshire.
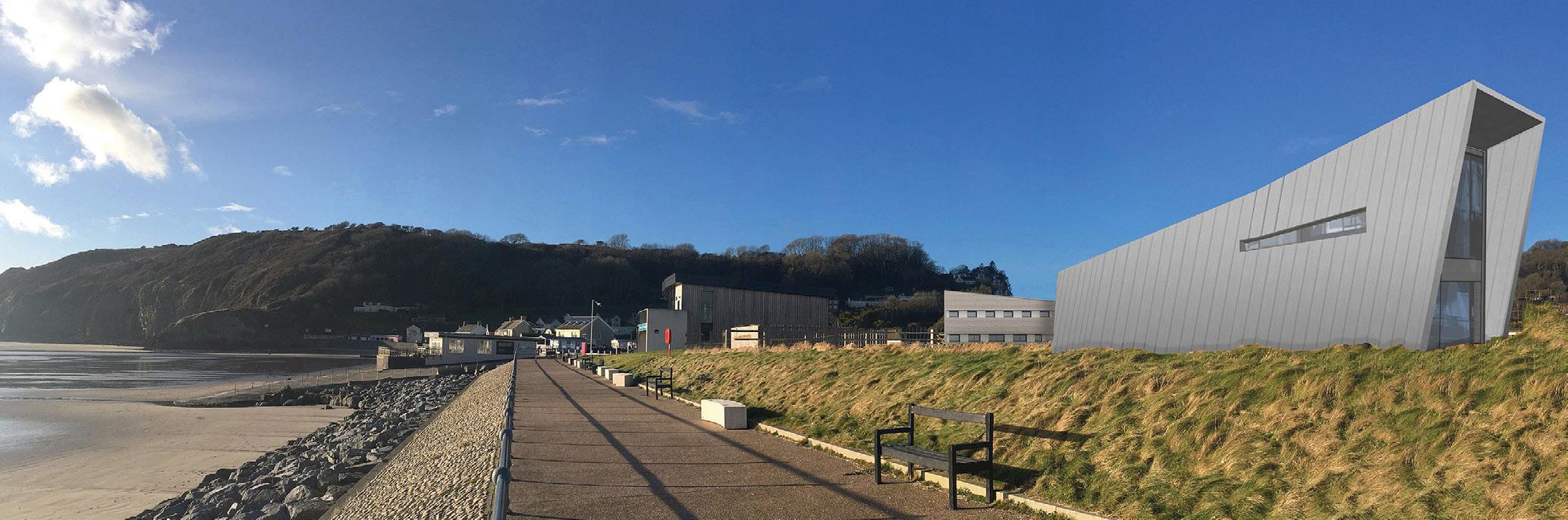
The Larsen system has a unique twin stud design to virtually eliminate cold bridging through the envelope and is flexible to achieve almost any required U value with a wide choice of insulation materials. “What we’ve done is harness all of our experience from many years of low energy and Passiv projects to develop a systemised approach for our clients so they can eliminate common pitfalls and build with confidence.” comments Gareth Lloyd, technical director.
More at www.timberframe.co.uk
The Larsen Kit of Parts can be found at online.fliphtml5.com/ywlrr/maws/#p=1
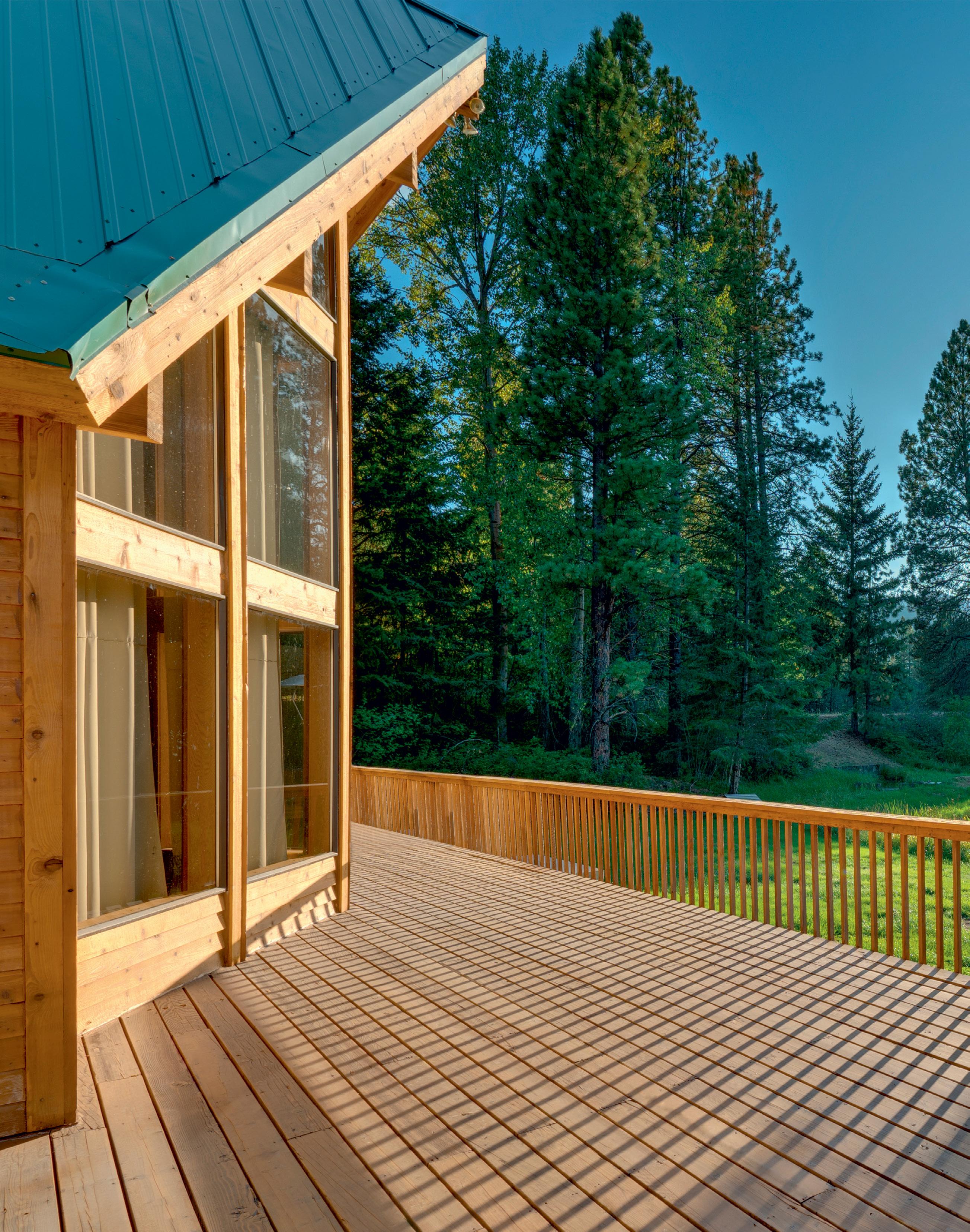