
7 minute read
Fast & Flexible Living
Beattie Passive, a leading provider of Passivhaus homes in the UK, are preparing to revolutionise housebuilding with their new range of modular, zero carbon homes.
The first company in the UK to combine offsite construction methods with a Passivhaus Institute certified complete build system, are set to deliver a new range of homes from cosy one-bedroom pocket homes to sprawling three-storey apartment blocks, Beattie Passive stands ready to deliver the highest quality, Passivhaus standard homes at a scale and pace never seen before in the industry.
Beattie Passive are taking timber construction to a whole new level. Developing on their signature Haus4one, a fully modular, Passivhaus standard one-person home built to turnkey, Beattie Passive have pioneered a whole new range of high quality, energy efficient modular homes of various designs, including one-, two- and three-bedroom homes and apartments. Designed for councils, housing associations and developers, the new modular range offers a large variety of products and styles that can be delivered quickly and can fit with the client’s needs and aesthetic requirements, whilst delivering the highest quality of housing. With the homes able to be built quickly in their modular factory, Beattie Passive are currently the only company in the UK able to deliver net zero, Passivhaus standard homes at a scale and pace never seen before in the industry.
As with every other home built by Beattie Passive, the new modular homes are built using the innovative Beattie Passive build system, a fabric-first approach to building that is designed from the ground up to deliver Passivhaus as standard. Whereas traditional construction methods involve numerous joints between floors, walls and roofs (each joint experiencing inevitable heat and air loss), the Beattie Passive build system incorporates a continuous insulation system within a treated timber frame structure delivering a complete build system from foundation beams, ground floor, walls and ceiling.
Once in place, high performance insulation material is injected into the cavities, creating one continuous insulated layer all around the property, with no joints and no leaks. As standard the Beattie Passive system provides the following benefits:
• Thermal bridge free ≤0.01 W/(mK) • High thermal efficiency (U-Values) • Walls - ≤0.11 W/(m²K) • Roof ≤0.11 W/(m²K) • Ground Floor ≤0.12 W/(m²K) • Airtightness below 1m³/hm²(@50pa) • Triple glazed Passivhaus windows.
This greatly increases the energy efficiency of Beattie Passive homes and means that their homes reach Passivhaus standards every time. With the easy addition of renewable energy sources such as solar panels and air source heat pumps, these homes can effortlessly reach net zero carbon and achieve official Passivhaus certification.
One of Beattie Passive’s current developments is their biggest project to date, a modular development of 48 homes comprising a variety of one-, two- and three-bedroom apartments for Cardiff Council. Currently under construction in the Beattie Passive modular factory, the apartments are being transported to and finished on site, and once the apartment blocks are assembled, solar panels will be fitted. This means the development upon completion will be net zero carbon and will achieve Passivhaus Plus certification.
Cabinet Member for Housing and Communities, Councillor Lynda Thorne, said: “The Council is extremely pleased to be working with Beattie Passive to provide innovative and sustainable solutions to help tackle housing need in the city. We’ve made excellent progress in supporting people who’ve been homeless over the last few months and our vision for services for the future is now taking shape very quickly. Beattie Passive’s modular solutions provide a fast and effective response for our plans. The flexibility of this fully demountable system means they can be moved elsewhere in the future if required, enabling us to respond to changing housing need over time.”
Ron Beattie, Managing Director of Beattie Passive, added: “We are very excited to be launching our new range of modular housing. These are the first fully modular homes that are able to achieve net zero carbon and reach Passivhaus certification on the market and have all the same benefits as every other Beattie Passive build. These can be built and delivered much quicker than a traditional build for a comparable price, and we believe this offers a real opportunity to revolutionise housebuilding in the UK.”
Panel Decision
The use of flame retardant panels in construction is far from a new idea, but the innovation in manufacture and performance in panels has been significant, if little understood. In fact, some very traditional FR panels have found themselves the perfect solution for a very modern problem! Stuart Devoil, Group Head of Marketing at James Latham brings some of that innovation to light.
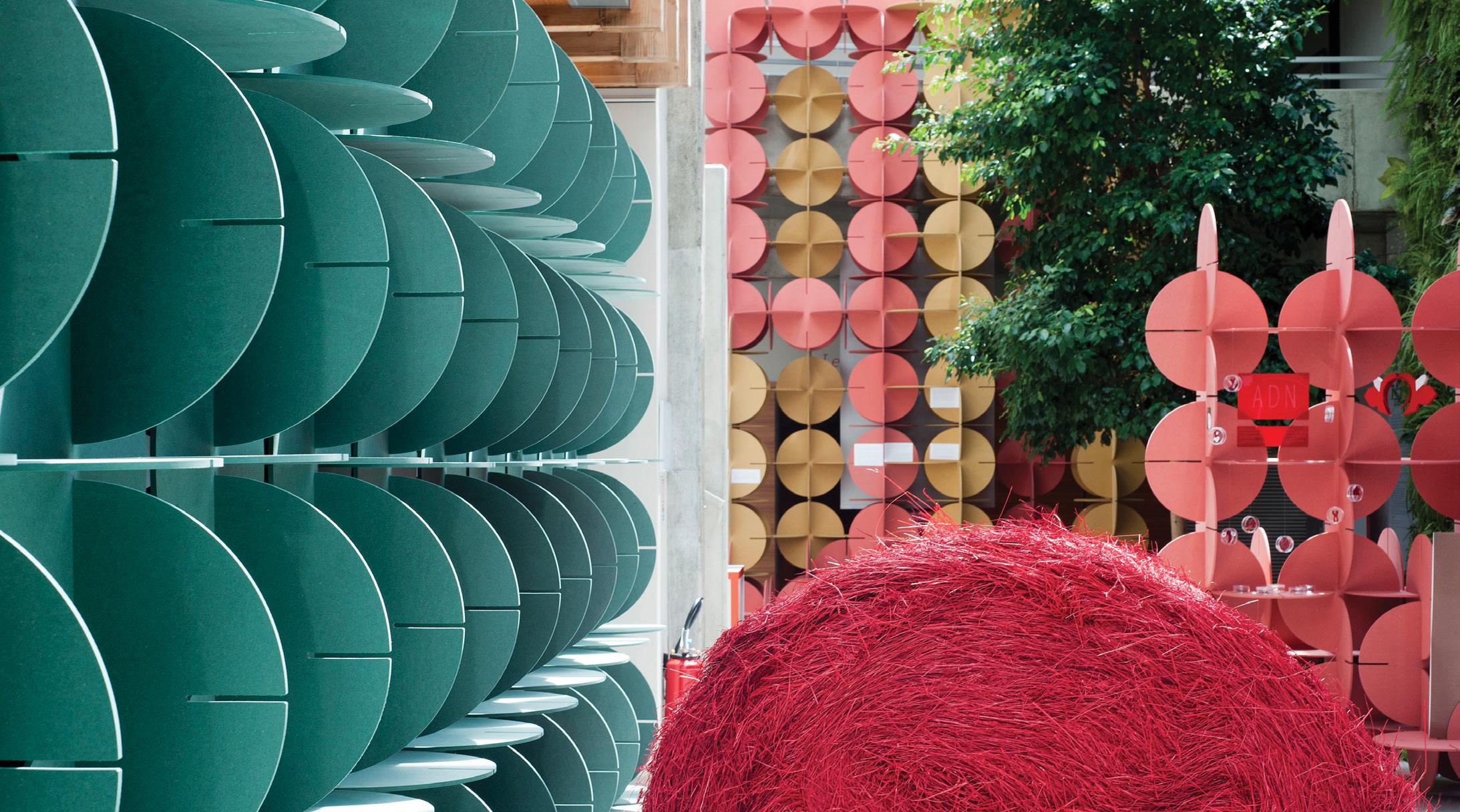
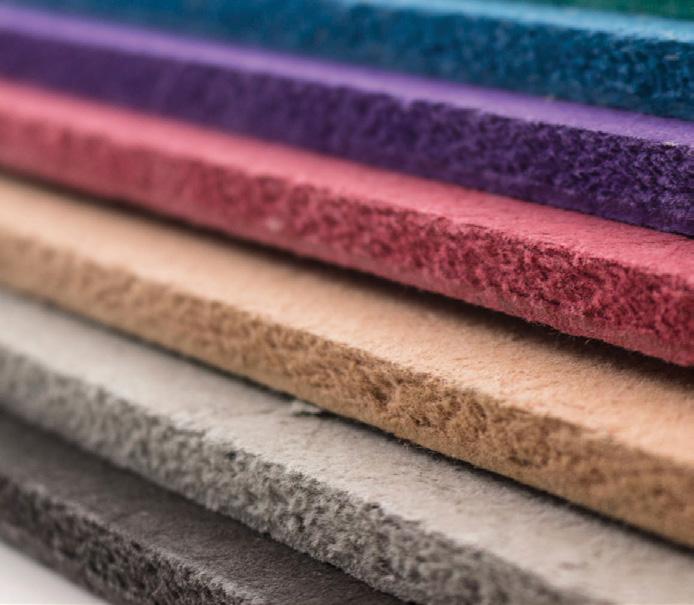
J
ames Latham was founded in 1757, when it first imported hardwoods into Liverpool, but much like construction panels, the company has progressively moved forward to remain at the cutting edge of panel materials technology. In fact, Lathams has always been ahead of the panels game, being the first UK importer to set up a panels business in the early 1900’s, being the first stockist to take delivery of MEDITE MDF in the UK, and being the first importer to stock TRP plywood from Weyerhauser. It’s safe to say that with a history like this, and the experience learned from these firsts, Lathams leads the way when it comes to panels.
Starting with something a little familiar, Irish OSB manufacturer SMARTPLY has introduced a new structural product which offers outstanding fire performance in the form of SMARTPLY MAX FR B. What makes this product unique is the manufacturing process. Individual flakes (or strands) of wood are treated with a water-based FR solution before the panel is manufactured, meaning the fire protection is maintained all the way through the panel allowing it to be cut or machined without losing any of the fire performance. The boards are then produced using ContiRoll® technology, meaning panels of practically any length are achievable. Much like rolling out pastry, the OSB panel goes under rollers on a continuous conveyor, allowing the panels to be cut only when the desired panel length is achieved. Panels up to 2.8 x 7.5m are achievable, making them ideal for Modern Methods of Construction. A structural, moisture resistant, flame retardant Euroclass B panel, up to 7.5m long! What more could the sector ask for? Well maybe something that offers fire protection, but good looks too? Valchromat is a High Density Fibreboard (HDF) that acts like a moisture resistant MDF. Available in eleven colours, the boards are ‘through coloured’, with the dye continuing right through the panel. This means you can take advantage of all those machining benefits a high-density product brings: crisp edges, clean CNC cuts, dense core and uniform surface, but without exposing a different coloured centre. Perfect for projects where you need that little extra design flair, but still require high performance and dependability. Whilst the standard Valchromat is suitable for kitchens, bathrooms, furniture and many other interior applications, the Euroclass B-s2,d0 Flame Retardant version is perfect for commercial fit outs, retail and hospitality environments, exhibitions, museums, and even schools.
And while we’re talking education, one product in particular has undergone a very interesting evolution in recent months. Sundeala must be one of the most recognised names in fibre panels. First manufactured back in 1898, it’s used for noticeboards, pinboards and signage the world over. It’s 100% recycled, 100% recyclable, and comes in a wide range of colours. But the really interesting thing is about its FR performance. Or more precisely, the performance of its FR version. Because firstly, Sundeala FR is the only UK manufactured Euroclass B pin board to meet building regulations for use in circulation areas and protected fire escape routes as laid out in Approved Document B2 and the BB100. Moreover, in ISO 17025 compliant laboratory tests, it was found to be highly resistant to coronavirus and was 100% virus free just five minutes after infection. This means Sundeala now has a new lease of life as the perfect product to help in the fight against a global pandemic. From touch plates to social distancing screens, walkway partitions, screening and protective wall cladding, the applications are pretty much endless.
So there we are, a trip through the world of panels which, possibly, has breathed a little life back into a subject that many may see as ‘commodity’. Like Lathams, the panel industry doesn’t stand still and has adapted very well to market demands. Products listed here are available throughout Lathams’ network of 12 depots in the UK & Ireland.
For more information, please visit or email www.lathamtimber.co.uk/products/panels info@lathams.co.uk
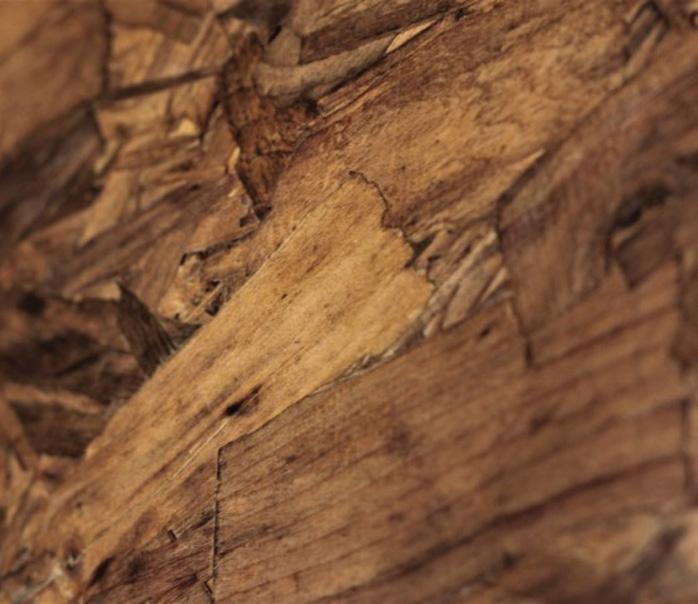