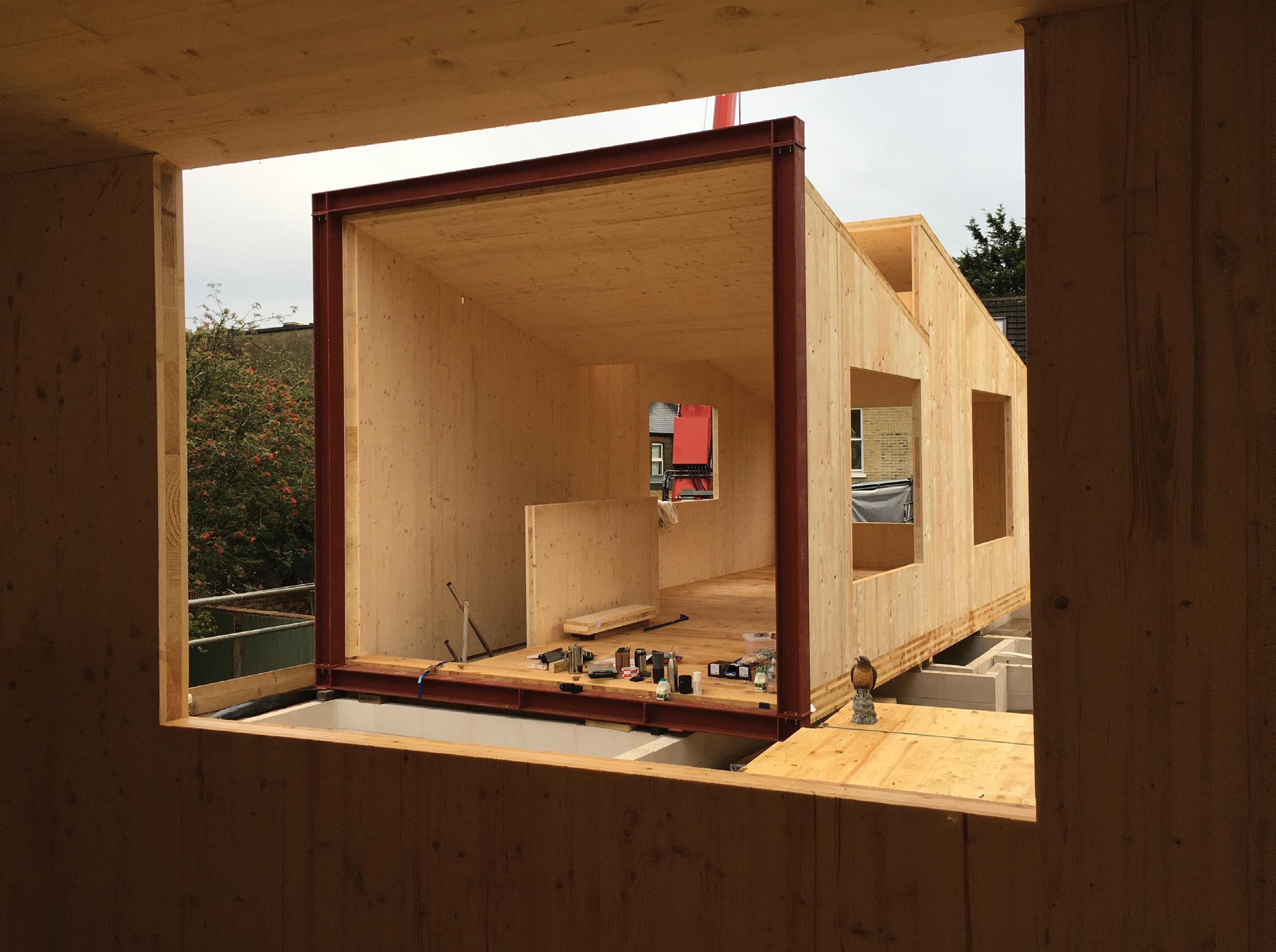
6 minute read
Cover Story: Piveteaubois
Small & Perfectly Formed
Photo © French-Tye
A new development in London will see the transformation of a former builder’s yard into a small but sustainable housing scheme using cross laminated timber (CLT) and offsite manufacture.
L
ocated at the edge of Wanstead Flats in London, Forest Houses – including a three-bedroom family home and two smaller two-bedroom homes – will also see the remodelling and extension of a former end-of-terrace shop that straddles the entrance to the site, to create another onebedroom home. The project showcases what can be done on a small site to create desirable low carbon living.
To transform his family’s old premises, client Spencer Seaton, enlisted Dallas-Pierce-Quintero (DPQ) architects to create a clever design to maximise the available space. The plan was to build the ground floor of the three newbuild homes in white cement block and place open-plan CLT living areas/kitchens on top. In addition to this the floors, walls and roofs of the space were made from CLT with a huge picture window, encased in a steel frame, overlooking the heath.
Tucked into a corner of the site, DPQ’s design for the newbuild homes is based on ‘upside-down’ living – moving bedrooms to the ground floor and positioning the kitchen and living spaces on the projecting first floor. This simple re-arrangement gives living spaces elevated views during the day, and a more secluded feel to the bedroom spaces beneath. In a nod to the site’s industrial history, the upper floors of each home feature a sawtooth roof profile, sensitively designed to avoid the appearance of an overly dominating development. Here the first floors are orientated north – allowing large, principal windows to frame stunning views over Wanstead Flats, while also sensitively protecting the privacy of the surrounding properties. The glazing reflects the natural surroundings and roots the scheme into its local surroundings. At ground floor level, a carefully considered jigsaw arrangement lends itself to the irregular shape of the site, as the three units efficiently interlock layouts around a series of lightwells and courtyards, to optimise the number of family homes on the site. These draw natural light and sunshine deep within the floorplan, creating private outdoor spaces and tranquil views from all the bedrooms. Windows have been arranged so that hallways look across the courtyards, creating a sense that all routes are connected to the outside.
“For us, every project focuses on the experience of the people using the buildings we create,” says Jonathan Dallas, from DPQ. “Tailoring these to their needs, and designing homes that enable people to get the most out of the spaces they live in. By embracing the often forgotten ‘spaces in-between’, we’re always seeking to develop innovative designs that make the most of each site’s potential and harness its unique features throughout the building, such as the striking views of the neighbouring grassland at Forest Houses. A commitment to sustainability – and in particular, a passion for materiality – informs our approach at every stage, as we celebrate the warm and tactile qualities of responsibly-sourced, natural materials to create a healthy home for the long-term.”
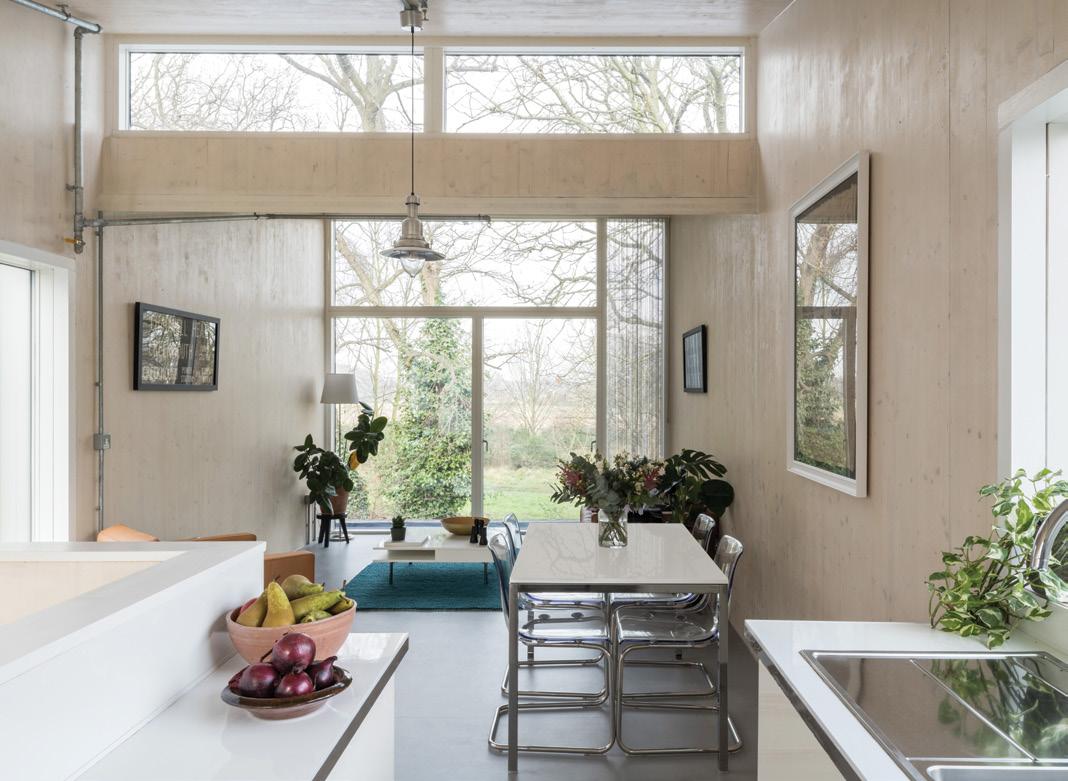
Photo © French-Tye
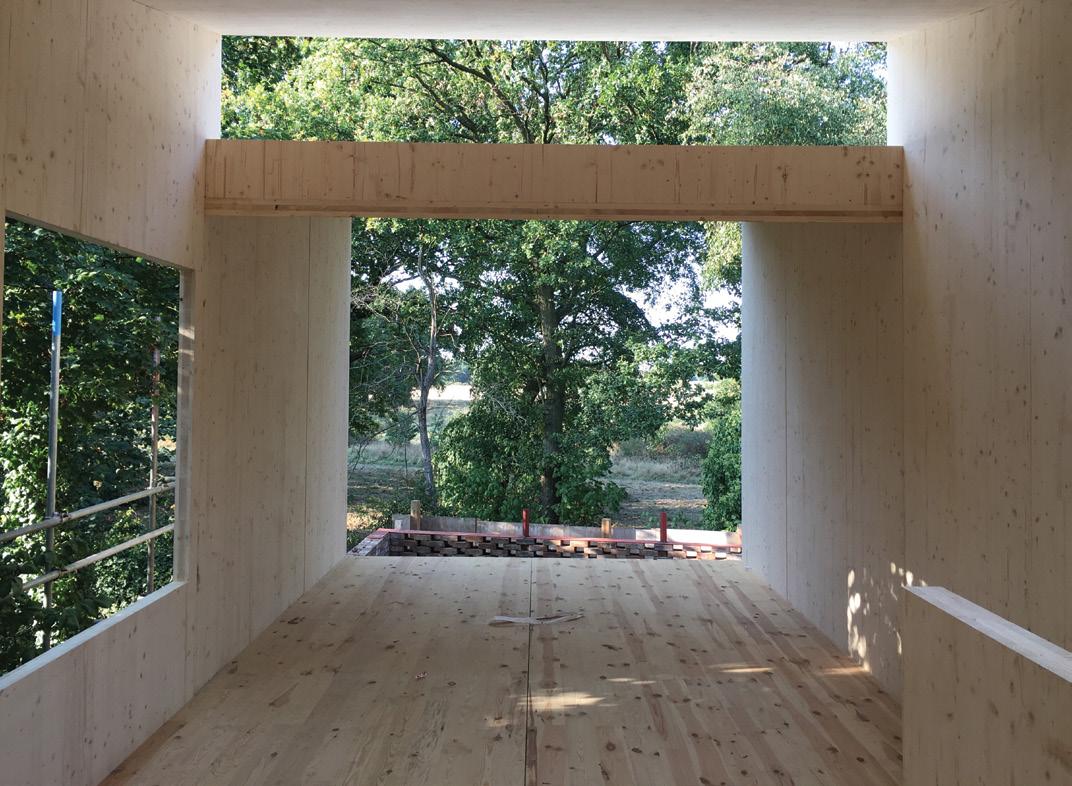
The timber elements were supplied by leading French timber supplier PIVETEAUBOIS and included 25m3 of non-visible Pine CLT for the floor panels, with 33m3 of visible Spruce for the walls and the roof. The CLT panels were CNC-manufactured in a precision factory environment at the company’s main production site in Sainte-Florence, France, with all timber sourced from responsibly managed PEFCcertified forests guaranteeing the material as legal and sustainable.
“This scheme was fantastic to see develop,” says Elisabeth PiveteauBoley, director UK & Ireland. “The team worked together extremely well to bring together all the elements on a small development site. The first floor CLT ‘pods’ were delivered as panels before erection and the assembly was done very easily. The use of timber has created several stylish homes and shows what a dynamic and flexible material it is.” The lightweight first floor is all clad in the same galvanised metal sheets to create a highly textured and unified external envelope that flows between the walls and the roofs. The interior structural elements are left undressed with the white, exposed blockwork complemented by the tactile and natural feel of the CLT structure, building a connection with the surrounding tree canopies.
To create a sense of cohesion across the scheme, the use of CLT was also mirrored in the refurbishment of the existing end-of-terrace shop, where it features in the roof of the new extension. All materials were responsibly sourced and chosen for their longevity, recycling capabilities and ability to provide a healthy, toxin-free home. Celebrating simplicity in materials and innovation in construction, this super-insulated project
French Engineered Timber
PIVETEAUBOIS is a leading French softwood sawmiller and manufacturer of timber products for the construction, landscaping and energy sectors. Its passion for wood has always driven the family mission – to build a durable and sustainable world by making the most of every tree. Construction accounts for 60% of PIVETEAU’s sawn production with an annual production of glulam, glued solid timber and fingerjointed timber of 50,000m3, cladding production of 1,000,000m2 and an annual CLT production capacity of 350,000m2. PIVETEAUBOIS uses material from local French PEFC-certified forests and the fully automated 10,000m² production facility at its Sainte-Florence headquarters is the first industrial site producing CLT panels in French wood of any significant scale.
Photo © French-Tye
fuses traditional and offsite manufacture to create truly sustainable and energy efficient homes.
“It’s always great to work on such innovative design and for such an experienced client,” said Will Bateman, design director at specialist timber framing company, Wooden House. “The team as always, worked really hard and even though there were a few nervous moments, owing to high winds and Covid-19 restrictions, we still managed to complete the job in just five days.”
The tight space of the site with a narrow entrance saw the timber craned in and unloaded, with the CLT floors fitted in place to create much needed room to work in. The steel frames were then bolted together, lifted into place and secured. Each unit was then built one after the other working backwards from the frame with the roofs of all newbuilds going on last.
For Spencer Seaton, the development has lived up to all his expectations, saying: “I am amazed how quick everything came together on-site and I haven’t got enough praise or thanks for the boys at DPQ and Wooden House for helping me turn this disused yard into such beautiful properties.”
The scheme shows how structural timber can provide a speedy and sustainable solution to create energy efficient and attractive homes. The site was small and constrained but the use of CLT timber panels fitted together as ‘pods’ delivers a design-driven way to create small but desirable homes.
More at www.piveteaubois.com/en www.woodenhouse.ltd www.d-p-q.uk
The HEXAPLI CLT range consists of panels ranging from 60mm to 360mm thick made from sawn timber classified at C18 or C24 and in max length panels of 16m by 3.5m in Pine, Spruce or Douglas Fir. All panels can be coated with our translucent UC2 water repellent PARKA to protect the panels from water ingress and staining during transit and erection and from decay. In the drive to popularise CLT for low-carbon construction, PIVETEAUBOIS will be launching its new HEXAKIT product at Carrefour du Bois (1-3 June 2022). HEXAKIT offers a range of standard size CLT panels with optimised lengths for two or three support spans for floor, wall, roofs and flat roofs for homes and offices. HEXAPLI and HEXAKIT CLT products are EPD-verified construction products and therefore provide credit for building certification applications (LEED, BREAM, HQE).