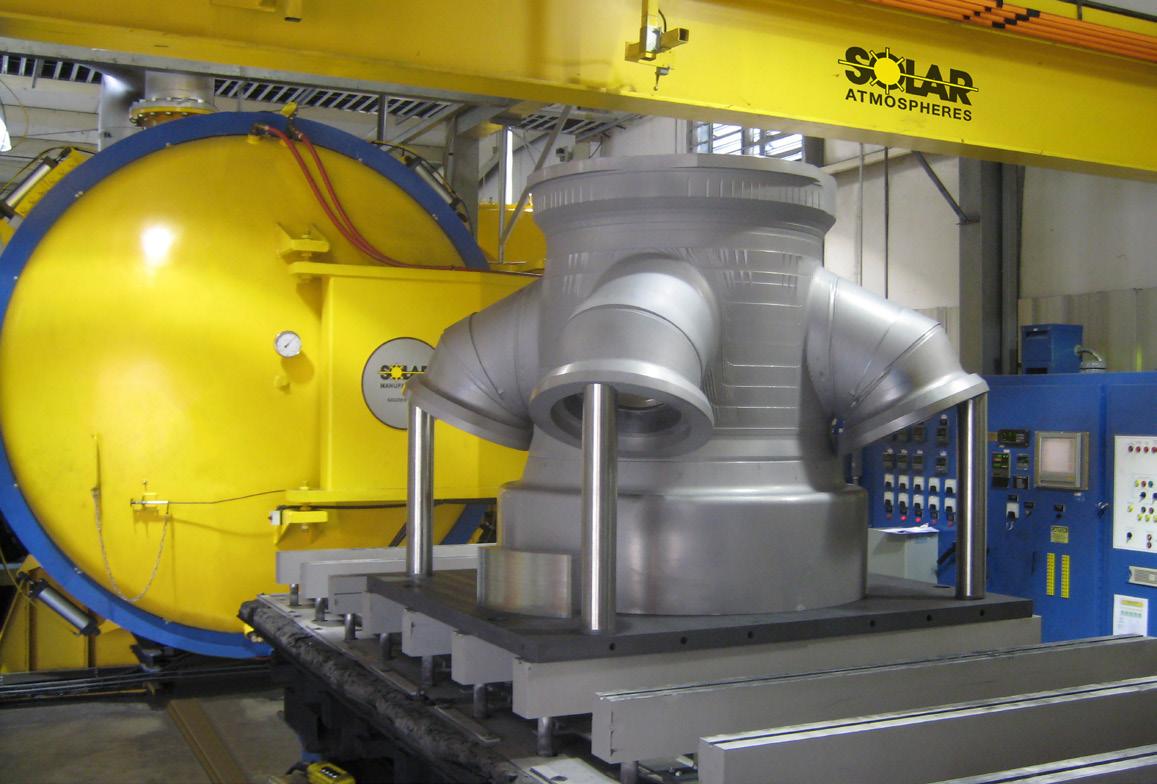
10 minute read
Aerospace Vacuum Heat Treating Services
Advantages
• Bright, clean, scale-free surfaces with minimal distortion
• Furnace capacities up to 48 feet long and 150,000 lbs
• Full line of major aerospace approvals
• Titanium and high nickel alloys titanium aerostructures across programs of record: higher titanium content in current generation aero platforms; demanding operating environments; affordability pressures driving demand for cost effective materials/parts and improvements in manufacturing productivity. “Product and process innovations are aiding growth in titanium optimized structures and high-temperature alloys.”
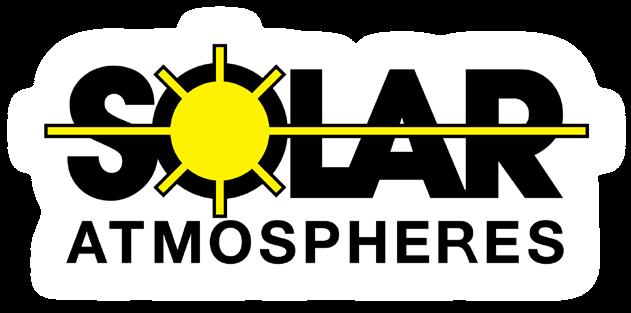
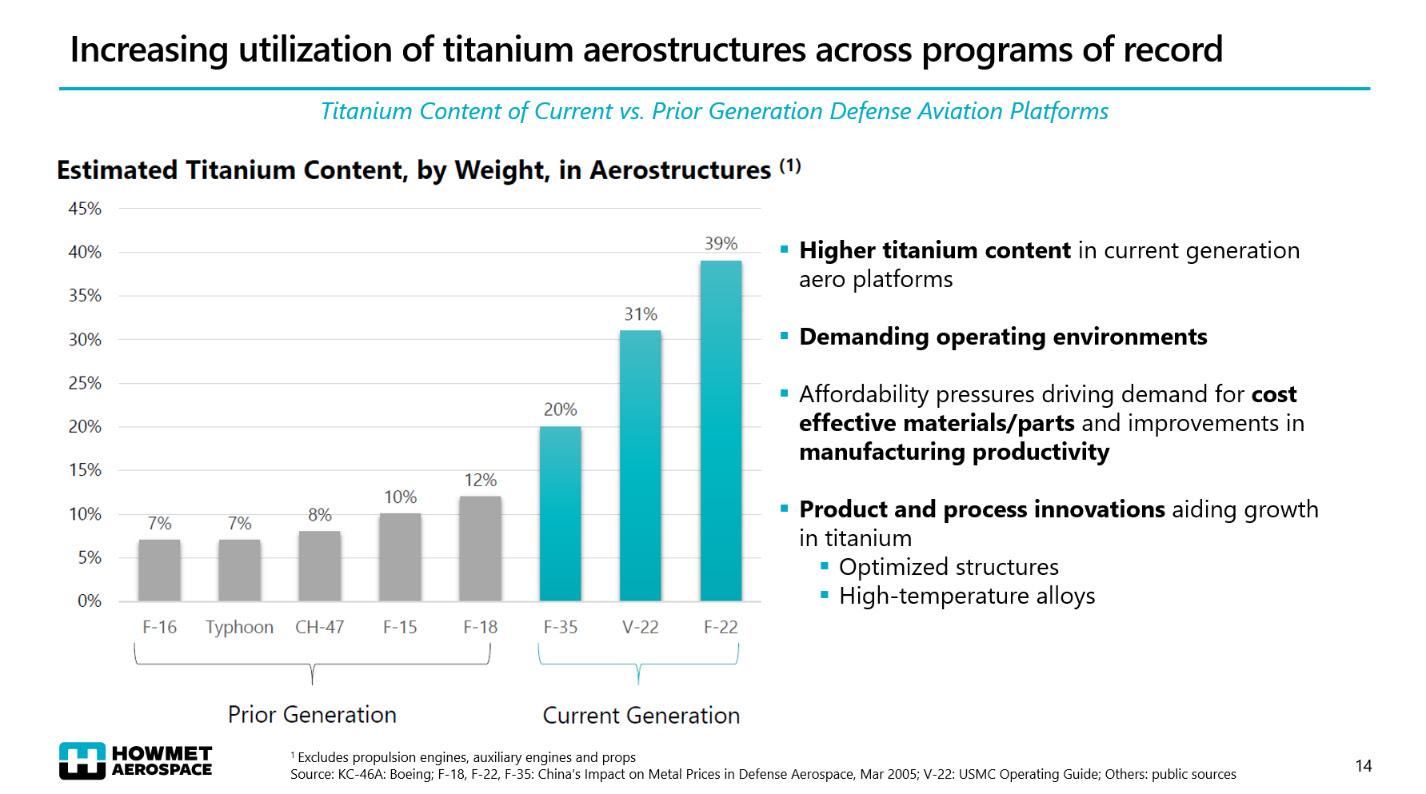
He described titanium-intensive F-35 jets as being increasingly popular among NATO member countries. Volumes remain fully funded by U.S. government and supported by increased foreign military sales to Canada, Finland, Switzerland, Germany, Czech Republic, and Greece, more anticipated. Overall for NATO, there’s been the replacement of legacy long-range precision fire systems, radar, and air and missile defense systems; significant investments in air superiority programs, like F-35; and increasing focus on critical materials supply chains, with an industrial base policy focused on “on-shoring, re-shoring, and friend-shoring.”
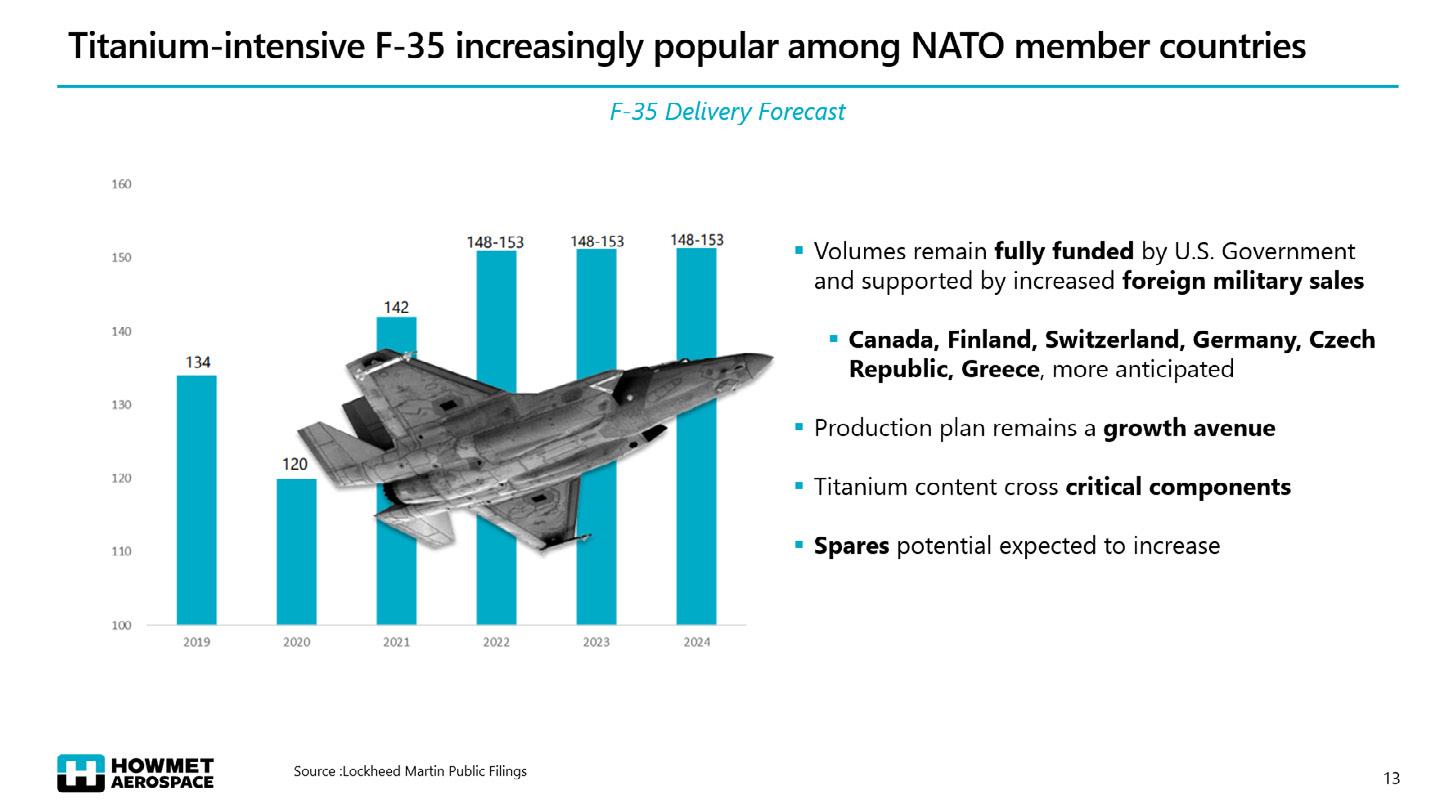
Titanium Sponge Outlook
Takeshi Nakashima, Toho Titanium Co. Ltd., discussed titanium sponge demand outlook for the near term. Nakashima said titanium sponge demand is recovering from Covid-19 and keeps increasing. “Air passenger recovery and growth helps aerospace demand increase. Industrial demand for commodity sponge has already recovered and demand for high-end products is also recovering. Global titanium sponge demand in 2021 exceeded prepandemic demand level due to the increasing demand in China. At the moment, a shortage of titanium scrap requires more sponge consumption in melting.”
The outlook, according to Nakashima, is that global sponge capacity can cover total sponge demand. “Chinese suppliers are eager to expand sponge capacity.” The Ukrainian war reduces CIS (Commonwealth of Independent States) titanium sponge/products supply for aerospace in 2022 and

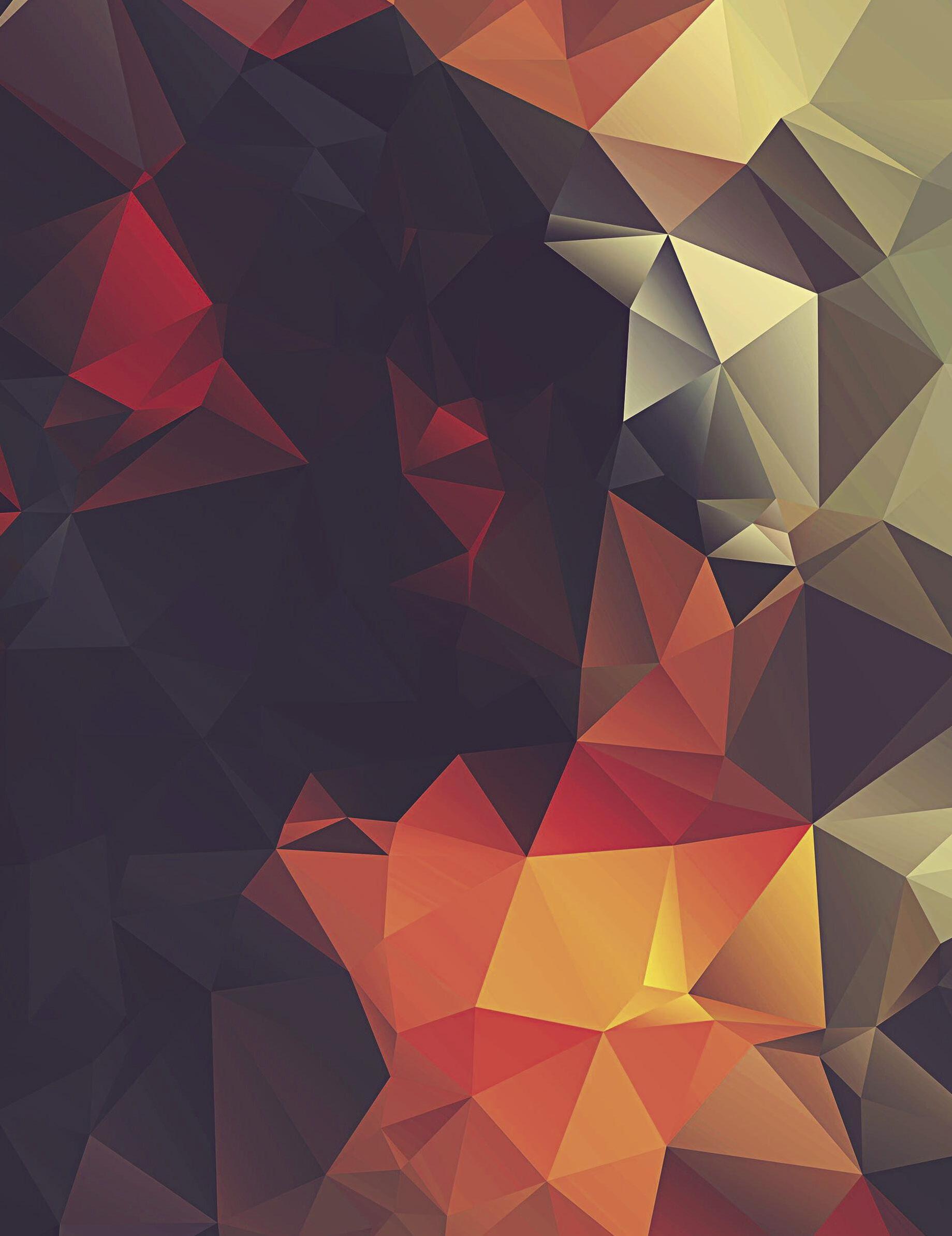
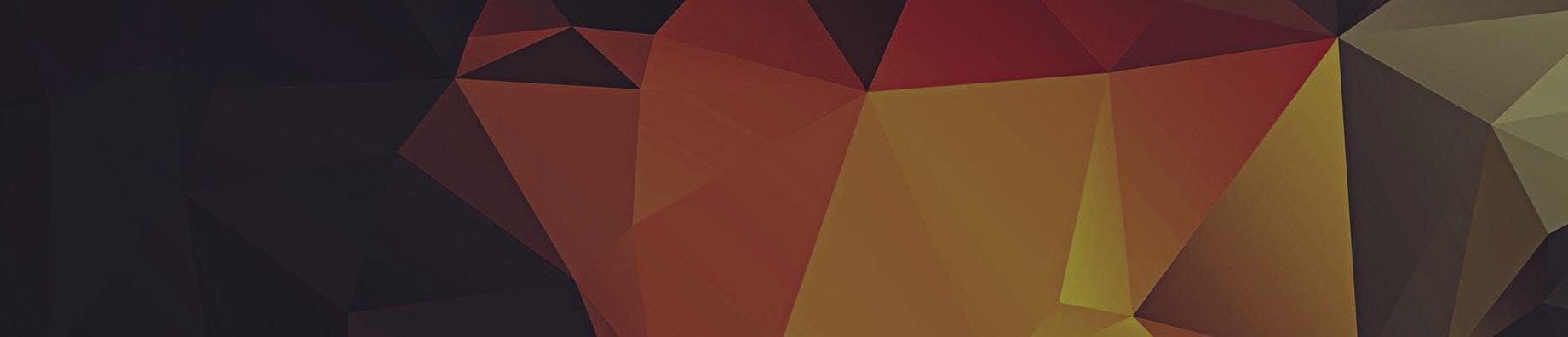
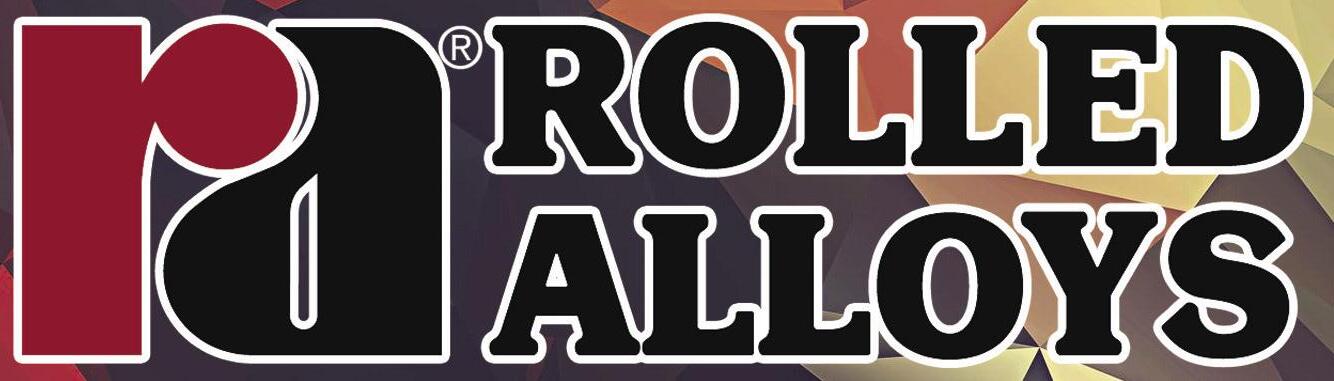
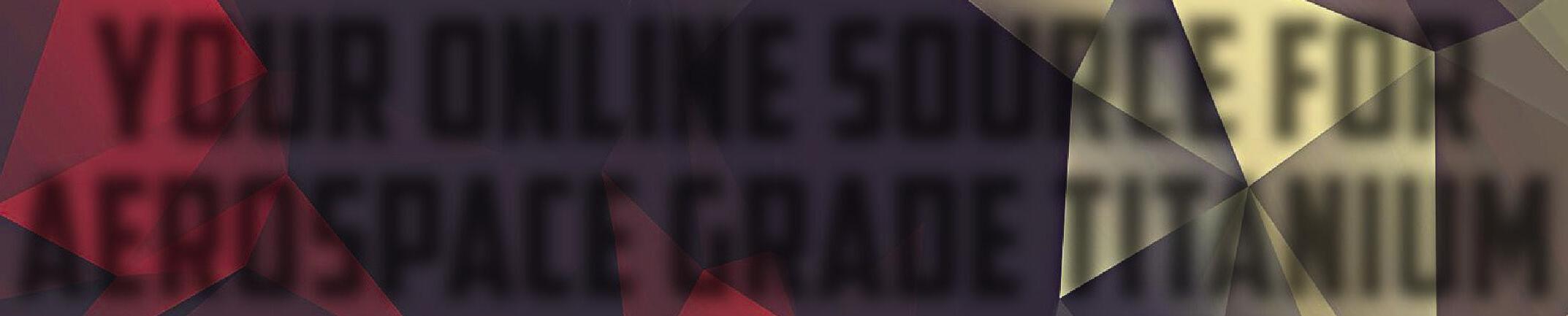
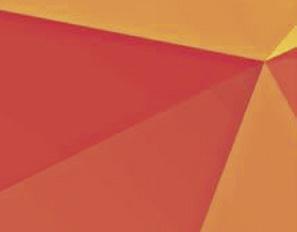
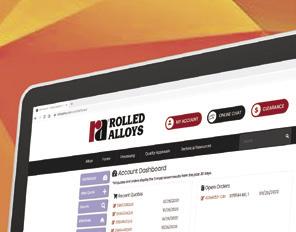
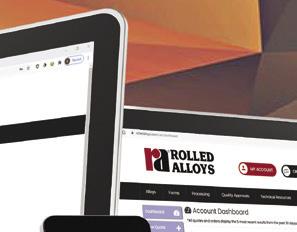
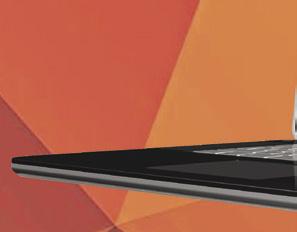
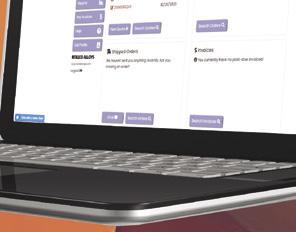
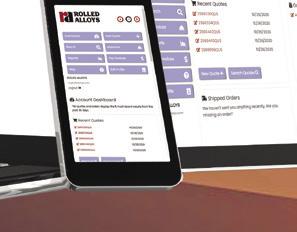
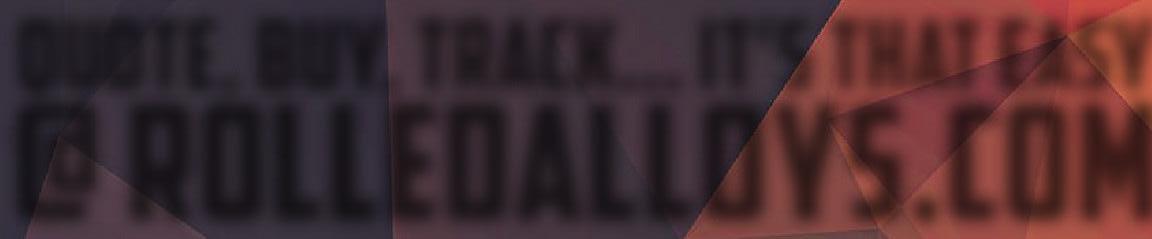

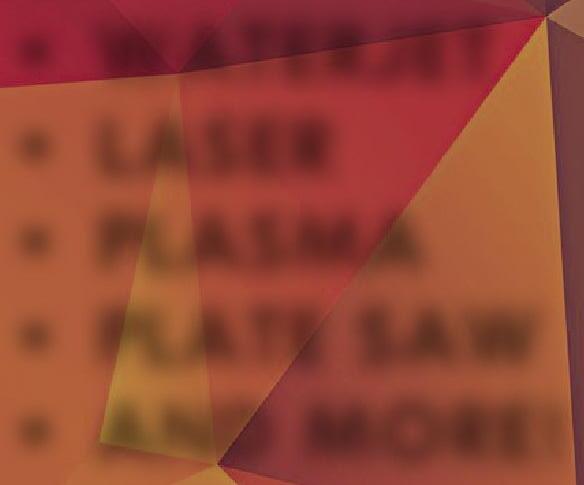
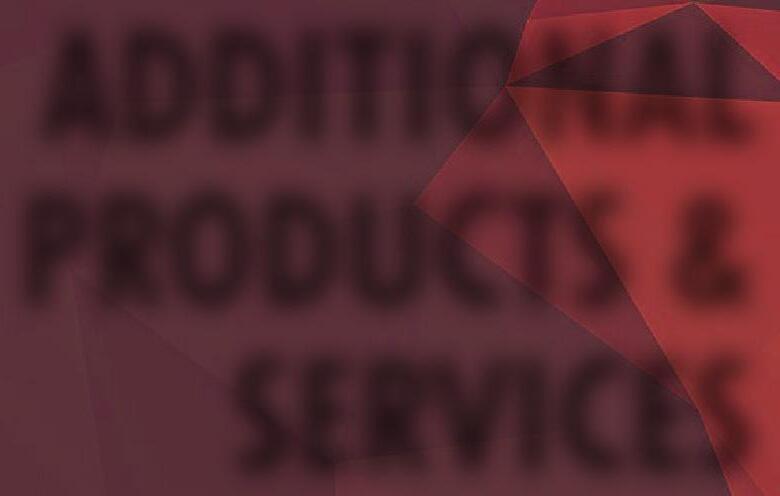
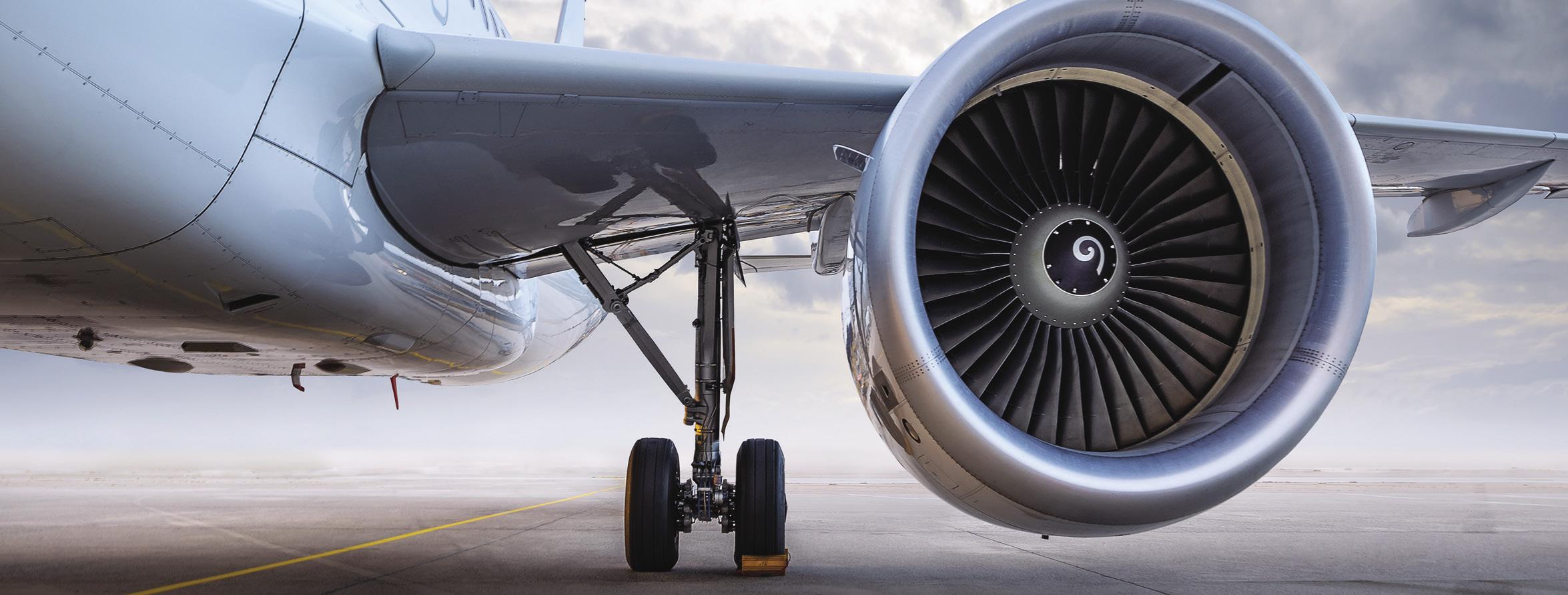
2023. Ukrainian titanium feedstock supply has been reduced since the war, which results in titanium sponge production decrease in CIS countries that relied on Ukrainian feedstock supply. Japanese sponge suppliers, who mainly supply titanium sponge for aerospace, have suffered from titanium sponge’s low profitability. At the moment, the sponge price for industrial customers appears to be more attractive than for aerospace.”
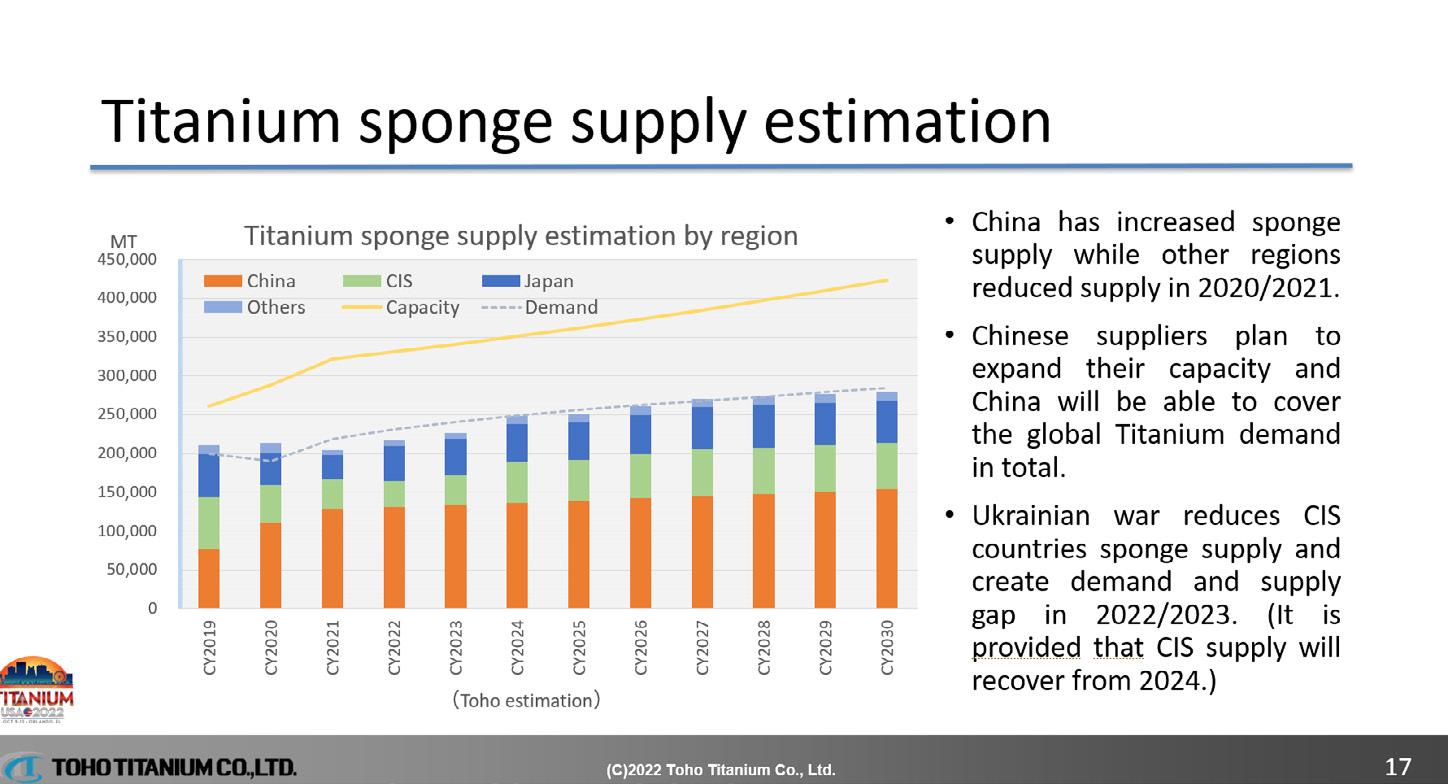

Regarding the sponge production cost outlook, titanium sponge production cost is increasing. “The increasing demand for titanium dioxide, which occupies 90 percent of titanium feedstock usage, and the shortage of titanium feedstock supply, keeps pushing feedstock prices up. Titanium sponge production consumes a lot of electricity. The hike in (the cost of electricity) influences sponge production. Other material costs like coke and magnesium also are rising.”
Matt Schmink of AmeriTi Manufacturing, offered thoughts on the outlook for titanium scrap. “We are facing a volatile market for titanium scrap in the near to medium term. Regional imbalances and logistics bottlenecks will either sharpen or soften the peaks and troughs. On a macro level, the market should remain relatively stable; from a micro-view, however, we could see substantial instability.” The global titanium scrap availability forecast indicates that scrap levels will exceed 240,000 metric tons by the year 2025.

Nicholas D. Corby, III, vice president, Titanium Products and Services, for ELG Utica Alloys, also addressed titanium scrap trends. ELG Utica Alloys processes, sources and supplies high-performance alloys and metals for our customers across the globe. According to Corby, using scrap as the primary source of raw materials for the production of titanium ingots will reduce the energy consumption and related carbon dioxide emissions by 95.4 percent.
“Most of the melting capacity for titanium scrap is concentrated in the North America (largest capacity worldwide) with new projects in
The project funded by Innovate UK
Epoch Wires is pleased to announce their involvement in an Innovate UK research project as part of the “NATEP helping SMEs innovate in aerospace - Autumn 2021” competition. The project entitled “NanoTi - Grain refinement of Ti-6Al-4V wire to enable Aerospace DED AM” is led by Epoch Wires and supported by TWI.
The project aims to design novel-alloy wire chemistry to minimise the grain growth in Ti6Al4V alloys deposited by Additive Manufacturing. In this work, Epoch Wires will produce new wires with a nanoparticle injection, forming equiaxed grains to enhance the mechanical properties of Ti6Al4V alloys. TWI will be depositing the wires using laser, plasma, and electron-beam additive manufacturing techniques. Epoch Wires will be utilising it’s proprietary technology of producing metal-cored wires using continuous laser-seam welding technology, designed for titanium alloys.
The NanoTi project has received funding from Innovate UK under grant agreement No. 10030392.
Nano Ti Wires
Innovative and cost-effective titanium wires for the aerospace industry
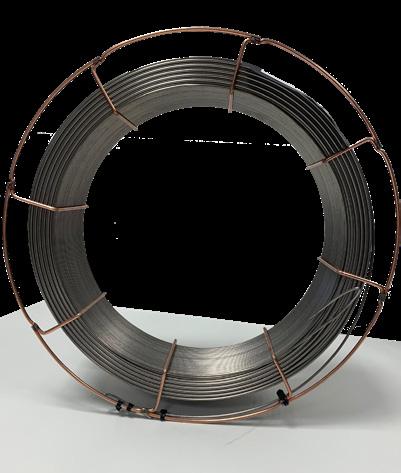
Laser-seam welded Ti6Al4V wire
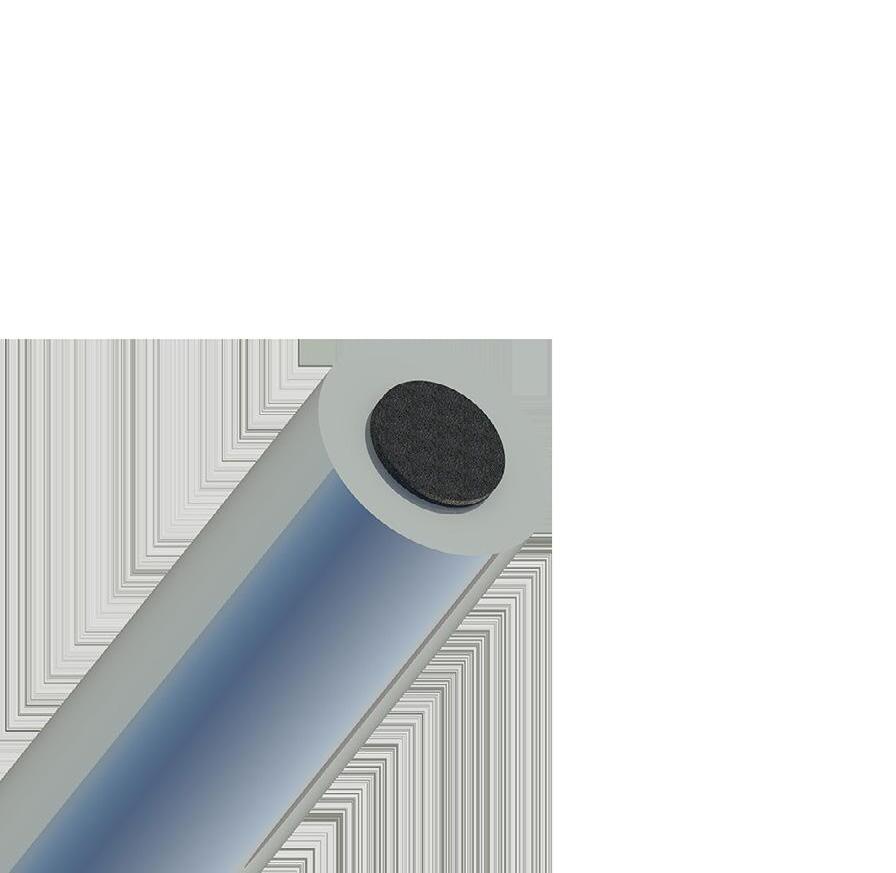
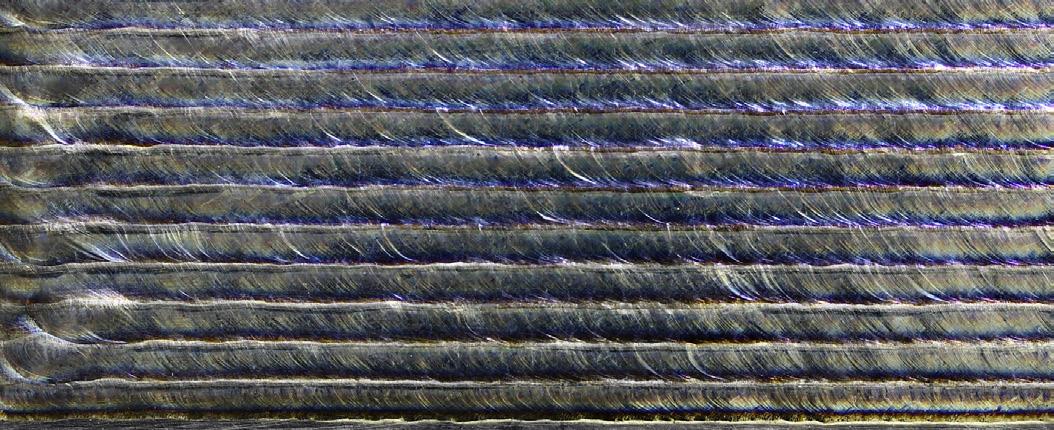

Ti6Al4V material deposited using Nano Ti wires, with laser additive manufacturing technology (image courtesy of TWI)
Contact
Serdar Atamert (CEO) serdar.atamert@epochwires.com
+44 (0) 7414 866801
Epochwires.com info@epochwires.com
Unit 8, Burlington Park, Cambridge, CB22 6SA, UK
Europe, Japan and China,” Corby said. “Scrap has to be sourced globally but supplied locally. Sophisticated logistic solutions are needed to secure scrap volumes generated emerging manufacturing clusters
Vanadium Trends
Terry Perles of TTP Squared Inc. reported that the global use of molybdenum in the first quarter of 2022 rose 9 percent to 153.8 million pounds when compared to the previous quarter, but fell 2 percent compared to the same quarter of the previous year. Global production of molybdenum was 581.4 million pounds in 2021, a 3-percent decline from 602.4 million pounds in 2020, according to figures released by the International Molybdenum Association (IMOA). Global usage in 2021 rose 14 percent to 614.3 million pounds from 539.7 million pounds the previous year. Figures released by the IMOA show that the global production of molybdenum fell by 4 percent to 138.4 million pounds the first quarter of 2022 when compared to the previous quarter—a fall of 7 percent when compared to the same quarter of the previous year.
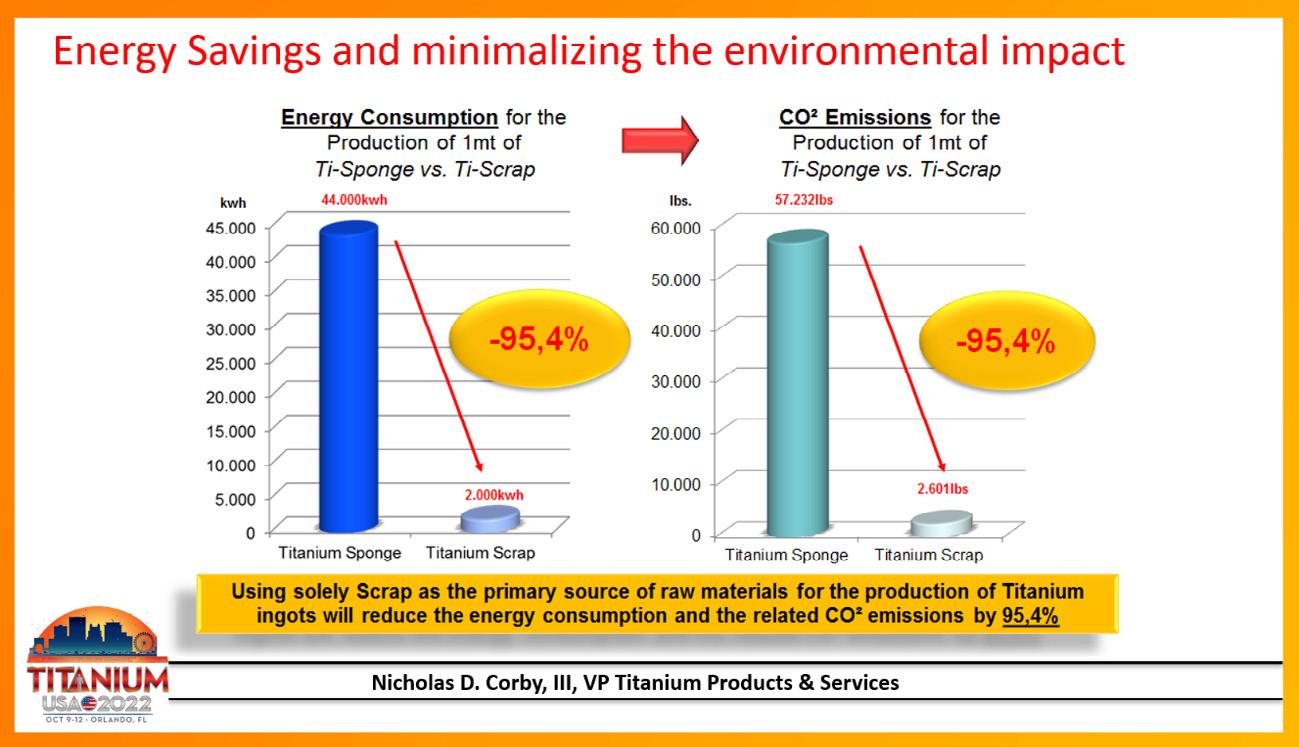
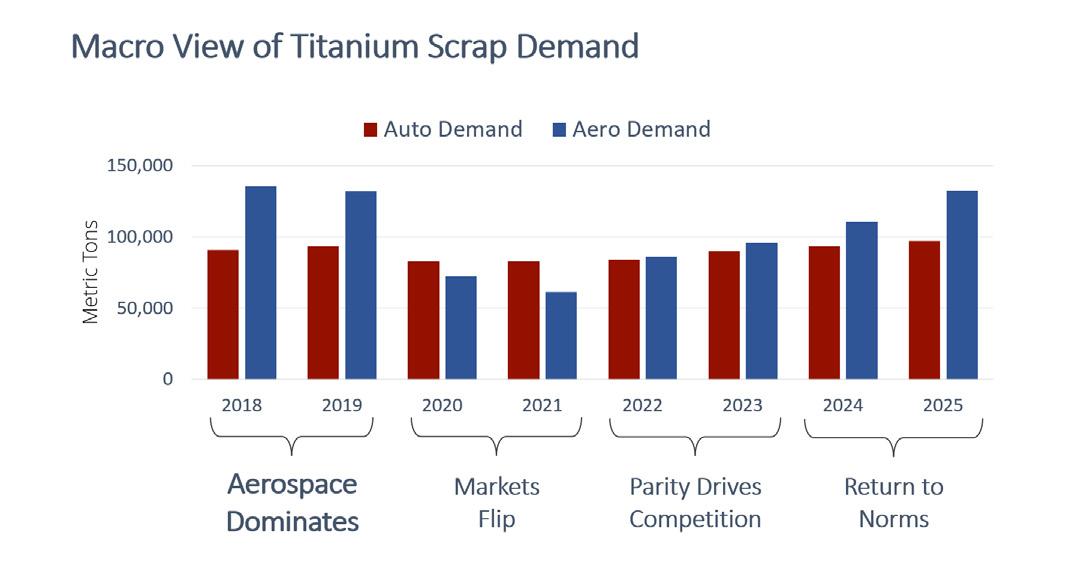
In a guest article earlier this year, published by
TITANIUM TODAY, Perles wrote that global vanadium production and consumption have shown high rates of growth in recent years. From 2016 to 2021 consumption of vanadium globally grew from 71,700 metric tons pure vanadium (MTV) to 120,375 MTV for a compound annual growth rate (CAGR) of 10.2percent. Vanadium production over this period has grown from 76,530 MTV in 2016 to 115,667 MTV in 2021 for a CAGR of 8.6 percent. Pre-Covid-19 titanium alloy production consumed approximately 4 percent of the vanadium produced each year. During Covid-19, production of titanium alloys was drastically affected and in recent months production of titanium alloys as started to recover and we expect that by 2023 titanium alloy production will return to pre-Covid-19 levels.
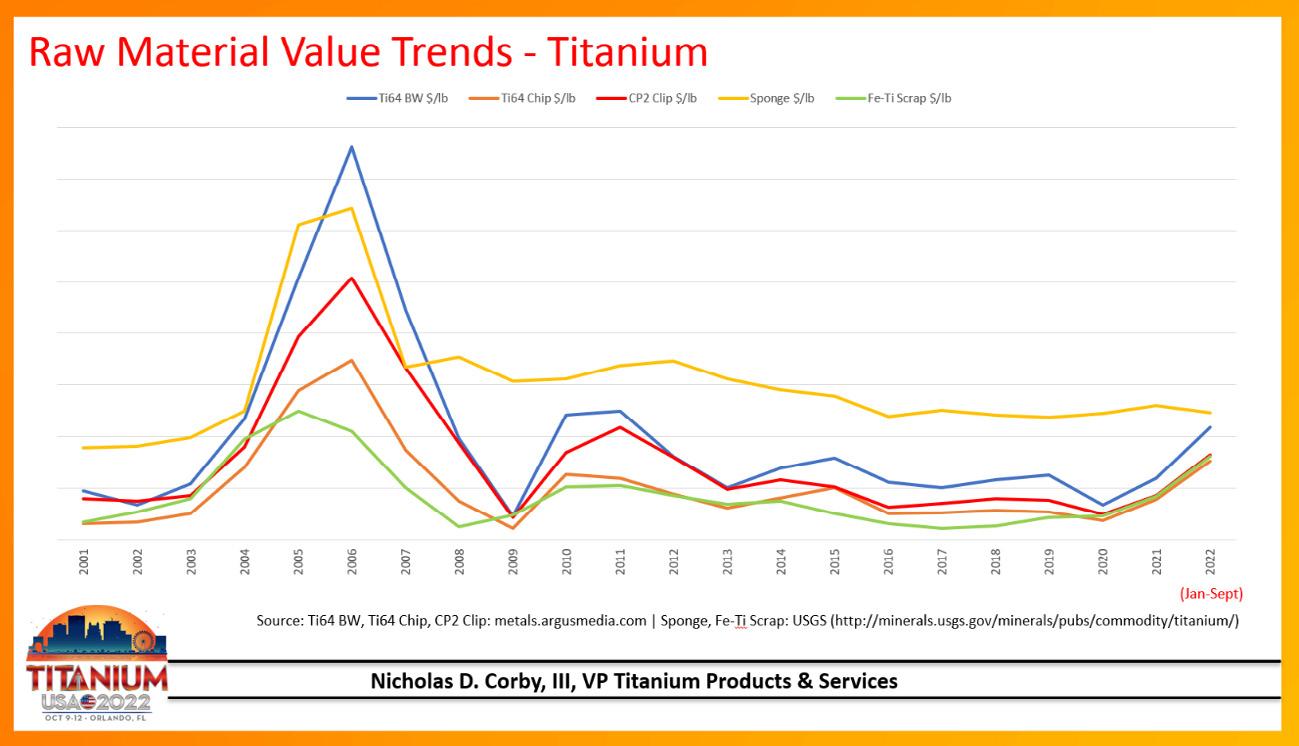
“Vanadium has been classified as a critical mineral by the European Union, the United States and other jurisdictions,” Perles wrote. “High-purity vanadium is critical for various national defense applications including jet engines, airframes, ballistic missiles, and as a coating for night vision goggles. Vanadium is critical in the production of many basic chemicals and petrochemicals and as a pollution control catalyst. Vanadium consumption in these critical applications will continue to grow in the coming years and the supply of high-purity vanadium for these applications will continue to be important from a defense and economic development standpoint.”

Titanium Mill Products: Sheet, Plate, Bar,Pipe,Tube,Fittings, Fasteners, Expanded Sheet & Ti Clad Copper or Steel.
Titanium Forgings and Billet: Staged intermediate ingot & billet to deliver swift supply of high quality forgings in all forms and sizes including: rounds, shafts, bars, sleeves, rings, discs, custom shapes, and rectangular blocks.
Titanium, Zirconium, Tantalum & High-Alloy Fabrication & Field Repair Services: Vessels, Columns, Heat Exchangers, Piping, Anodes, Custom Fabrications, Field & In-House Reactive-Metal Welding & Equipment Repair Services Available 24/7.

Plate Heat Exchangers: Plate Heat Exchangers to ASME VIII Div 1 Design, Ports from 1” through 20” with Stainless Steel, Titanium and Special Metals, Plate Heat Exchanger Refurbishing Services & Spare Parts.
Two Service Centers & Fabrication Facilities in Ohio & Texas with Capabilities in: Waterjet, Welding, Machining, Sawing, Plasma Cutting & Forming.
Serving a Wide Variety of Industries: Chemical Processing, Mining, Pulp & Paper, Plating, Aerospace, Power and others.


A Postcard from Japan
Takashi Hirose, the chairman of the Japan Titanium Society and the representative director and executive vice president of Nippon Steel Corp., offered insights on current titanium trends in Japan. “Japanese sponge producers have increased their shipments of sponge since 2013,” Hirose said. “The shipments of sponge temporarily decreased in 2020 due to Covid-19, and shortly bottomed out because of the titanium demand recovery. “Hirose noted that Japan accounted for 16 percent of global titanium sponge production in 2021, but that China has been expanding its production for 14 years and represents 61 percent of the market share.
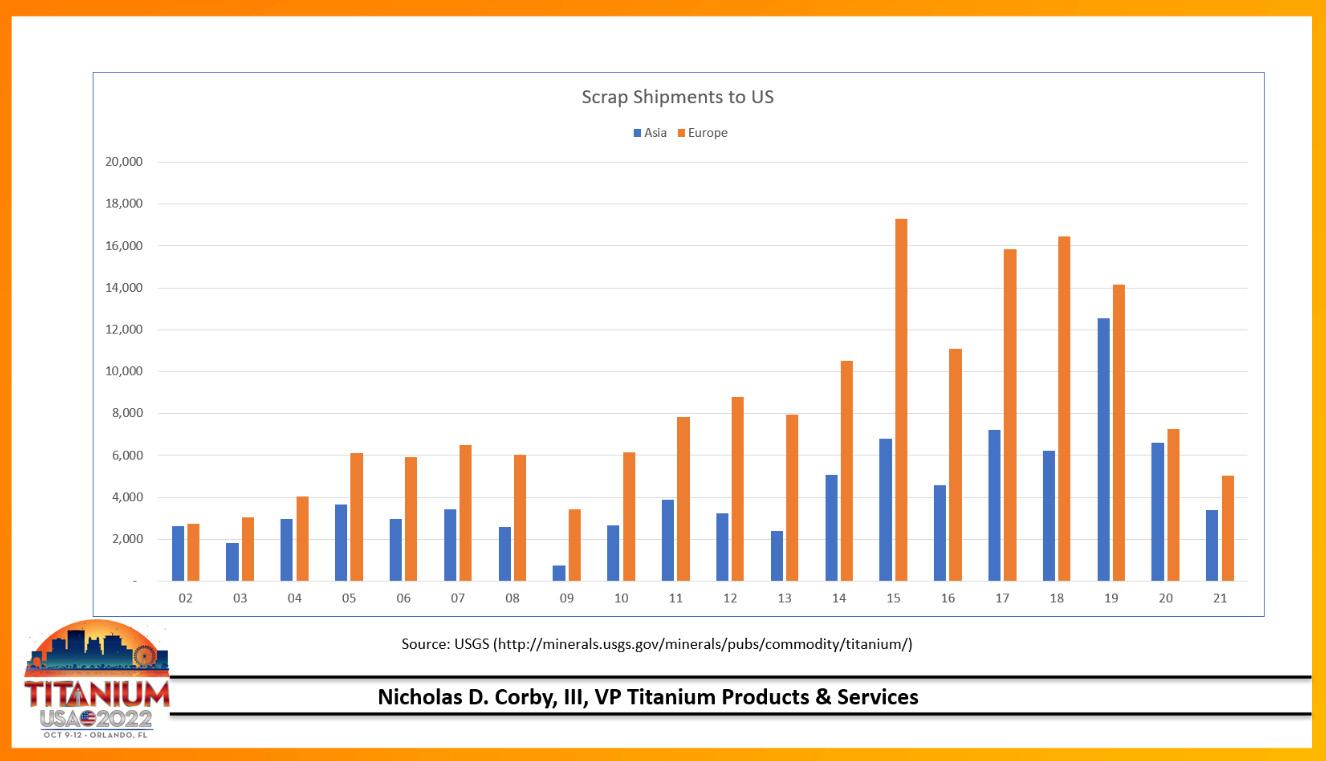
Hirose said Japan titanium mill product shipments have decreased since 2019, but shipments will increase this year owing to titanium demand recovery.
The Japan Titanium Society, founded in 1952, contributes to the development of the titanium industry in Japan, and is celebrating its 70th anniversary in 2022. The society organizes meetings and trains young researchers and engineers. It also subsidies to develop new titanium applications and contributes grants for technology research program. “The Japan Titanium Society continues to work to promote expansion of new applications in titanium and help nurture the next generation of leaders of our industry,” Hirose said. “We believe that these activities will contribute to expanding titanium demand and developing the titanium industry.”
Manufacturing Technologies
Ron Adams, business development director for QuesTek Innovations LLC, discussed the concept of
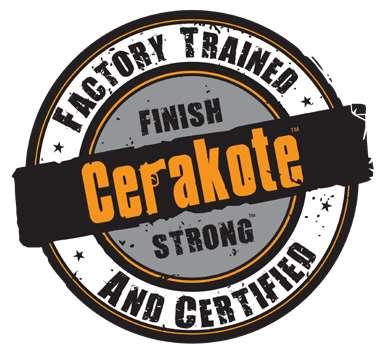
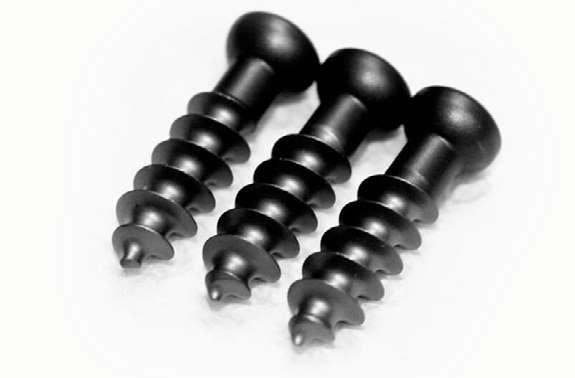
“Materials by Design®; Leveraging Integrated Computational Materials Engineering (ICME) Technologies for Development of Improved Performance Titanium Alloys.” He said it takes too much time and too high cost to develop and deploy novel materials and alloys. The QuesTek solution involves technology (software and methodologies) proven to reduce the time and cost, and increase the performance of novel materials.
The goal is to utilize “predictive capability” to assure qualification of minimum design properties for specified performance. Accelerated Insertion of Materials (AIM) methodologies and Integrated Computational Materials Engineering
(ICME) technologies are the keys for addressing the goal. Predictive software links process microstructure and property performance. This involves Alloy Qualification Tools (AQT) using ICME, leveraging ICME technologies for the development of improved performance titanium alloys.
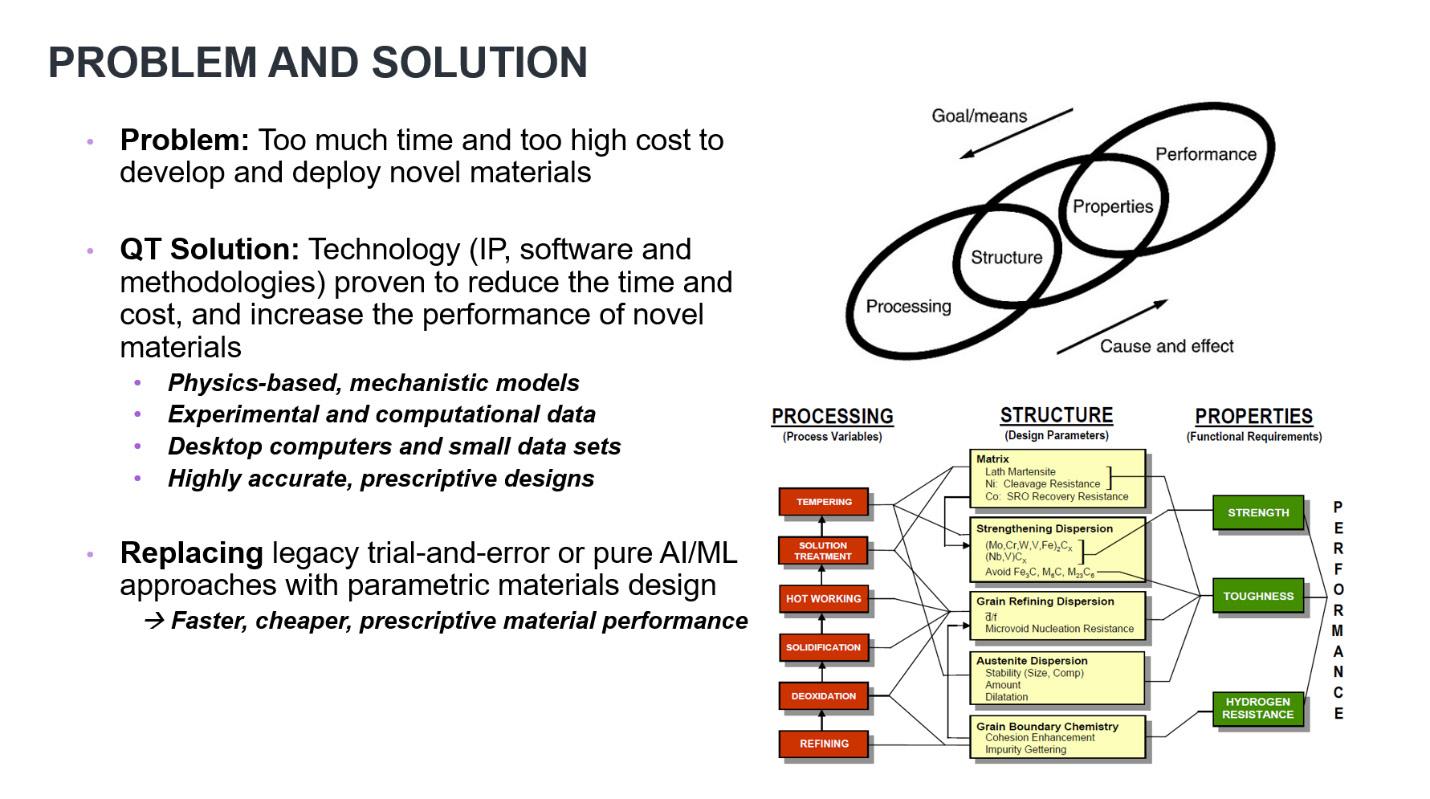
Adams said that QuesTek takes a holistic approach to fatigue modeling, with separate models to consider various length and time scales, and models combined for total life predictions. “While this application emphasizes AM (additive manufacturing), it can effectively extend beyond to the qualification of various other manufacturing applications. The technology delivers robust, accurate properties predictions with varying processing and test conditions (temperatures, orientations and surface finish, according to Adams.
QuesTek Technology is the “2020 Air Force AM Challenge” award winner as “First Place Top Performer,” and the “AM BENCH 2022 Challenge” as the first place awardee for best modeling results.
Joe Grohowski, the president of Praxis Technology, provided an update on “The State of the Art: Titanium Metal Injection Molding.” Grohowski said Praxis’ TiMIM technology represents years of investment and development, a titanium-only production facility, custom feedstock that limits binder contamination, and follows ASTM F2885 and F2989 and FDA master file guidelines.
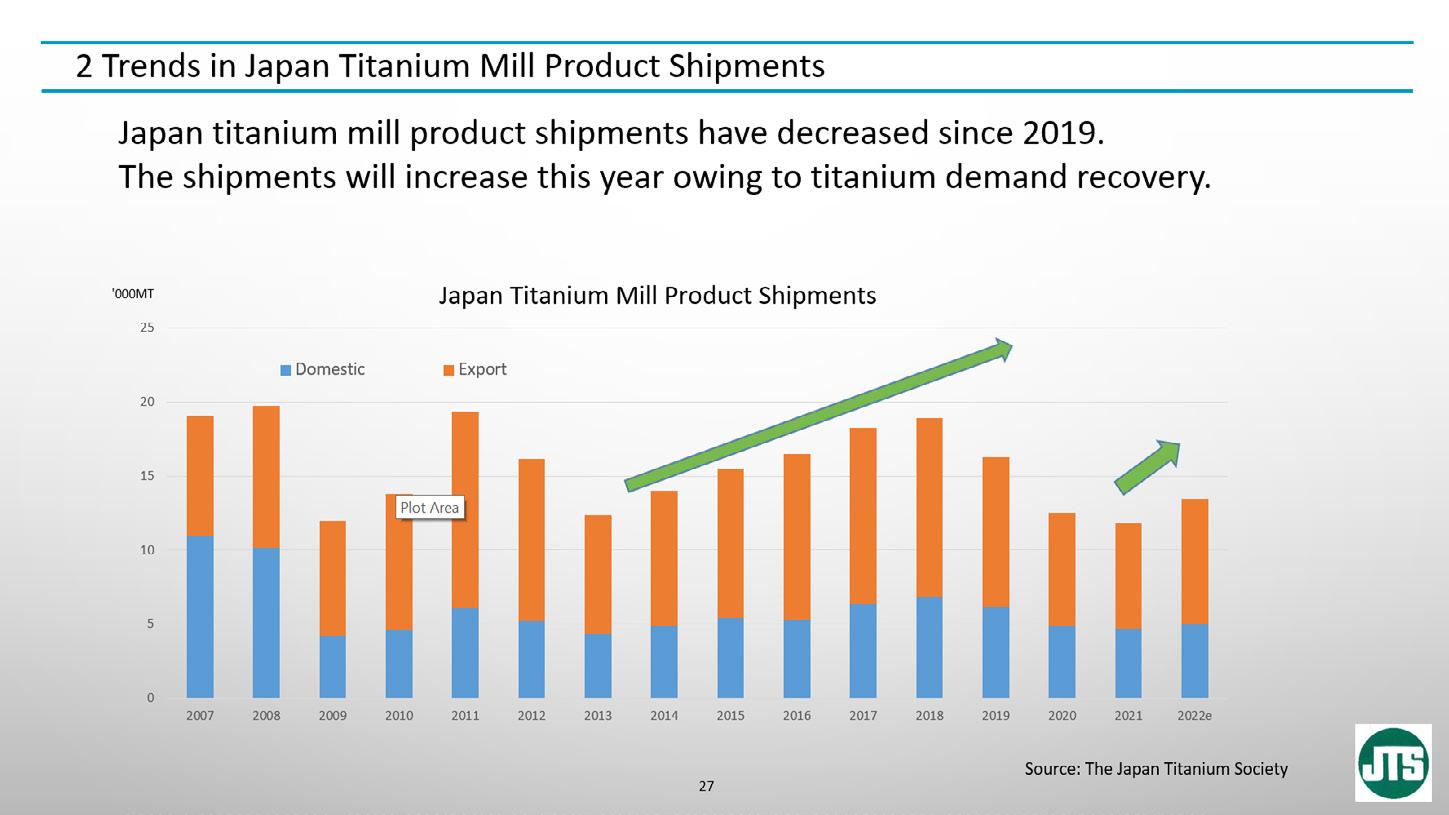
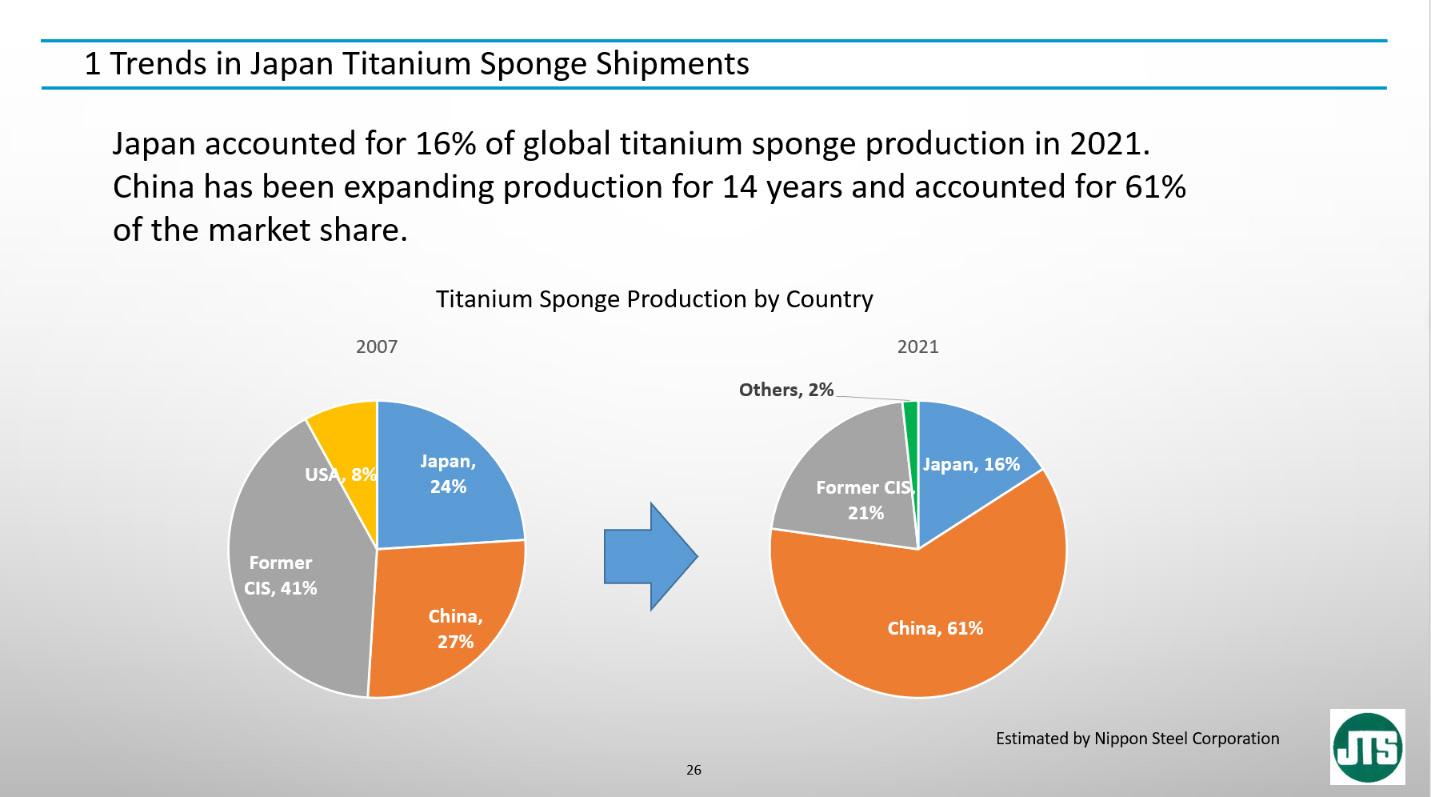
Advantages of metal injection molding (MIM) parts, according to Grohowski, are smooth fillet radii inside and outside, no machining burrs or sharp edges, no residual stresses, added complexity at no extra cost, molded-in positional indication and identification features, compound/complex curvatures, and the ability to combine assemblies. The challenges for MIM are that titanium is extremely sensitive to contamination; titanium powder is especially reactive, along with adoption challenges for regulated industries.
Professor Martin Jackson of the Henry Royce Institute at the University of Sheffield in the United Kingdom outlined the “Fast Forge of Titanium Alloy Waste for Future Low-Cost Components” being reviewed at his institute. Jackson said the Royce vision for metals involves the advanced metals processing theme, which aims to build on the UK’s strength in metals processing and provide UK academia and industry with advanced facilities, collaboration opportunities, holistic support and expertise, all of which are needed to deliver innovative metals processing technologies and novel alloy solutions.
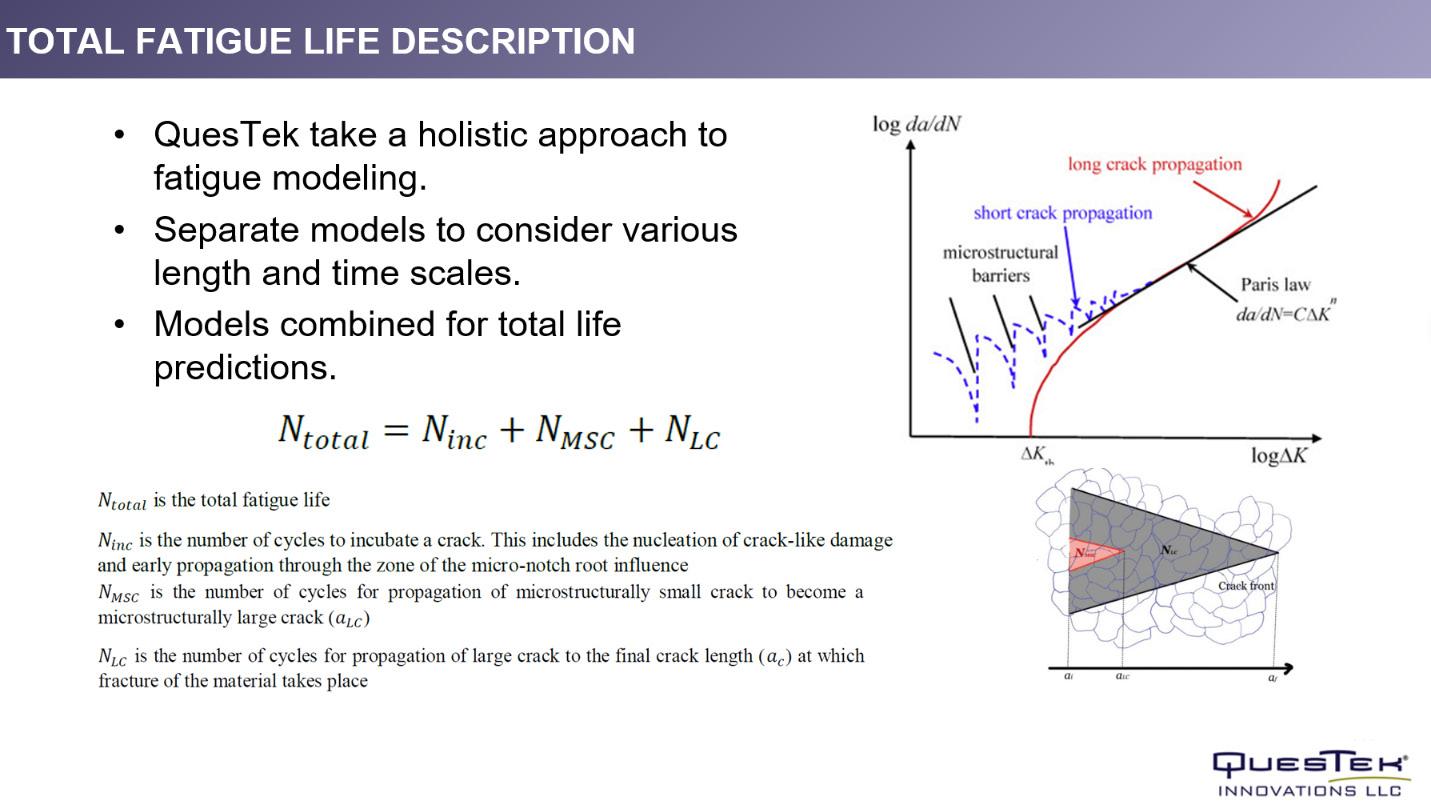

“We need to treat swarf (machine scrap waste) as a valuable feedstock,” he said. High-value alloyed titanium swarf is used as a feedstock for the FAST and FAST-forge process, which has the potential for generating near-net shape components in high strength and good fatigue life applications. Jackson said production volumes and cost levels of swarf could find applications in automotive industry and other markets, and would lead to the development of a new UK titanium supply chain. Jackson said the FAST process involves closed-die forging of FAST billets; forging trials prior to committing to batch FAST process tooling; confirmation of simulation analysis before committing to FAST process tooling; confirmation of FAST process tooling design; confirmation of forging tooling design, all of which would ensure material flow is as expected.
In a 2020 online technical journal (www.mdpi.com/20754701/10/2/296), Jackson wrote that forged titanium billets used in the aerospace industry, after being machined, create substantial levels of swarf. “The quantity of waste titanium swarf generated is increasing as aircraft orders, and the titanium components contained within them, are increasing. Cleaned Ti-6Al-4V swarf was fully consolidated using the FAST process at sub-transus and super-transus temperatures, followed by hot forging at sub-transus temperatures at different strain rates. It was demonstrated that swarfderived Ti-6Al-4V FAST billets have equivalent hot forging flow behavior and resultant microstructures when directly compared to equivalently processed conventional expensive hydride–dehydride powder, and previously reported Kroll-derived melt-wrought material. This demonstrates that titanium swarf is a good quality feedstock for downstream processing.”
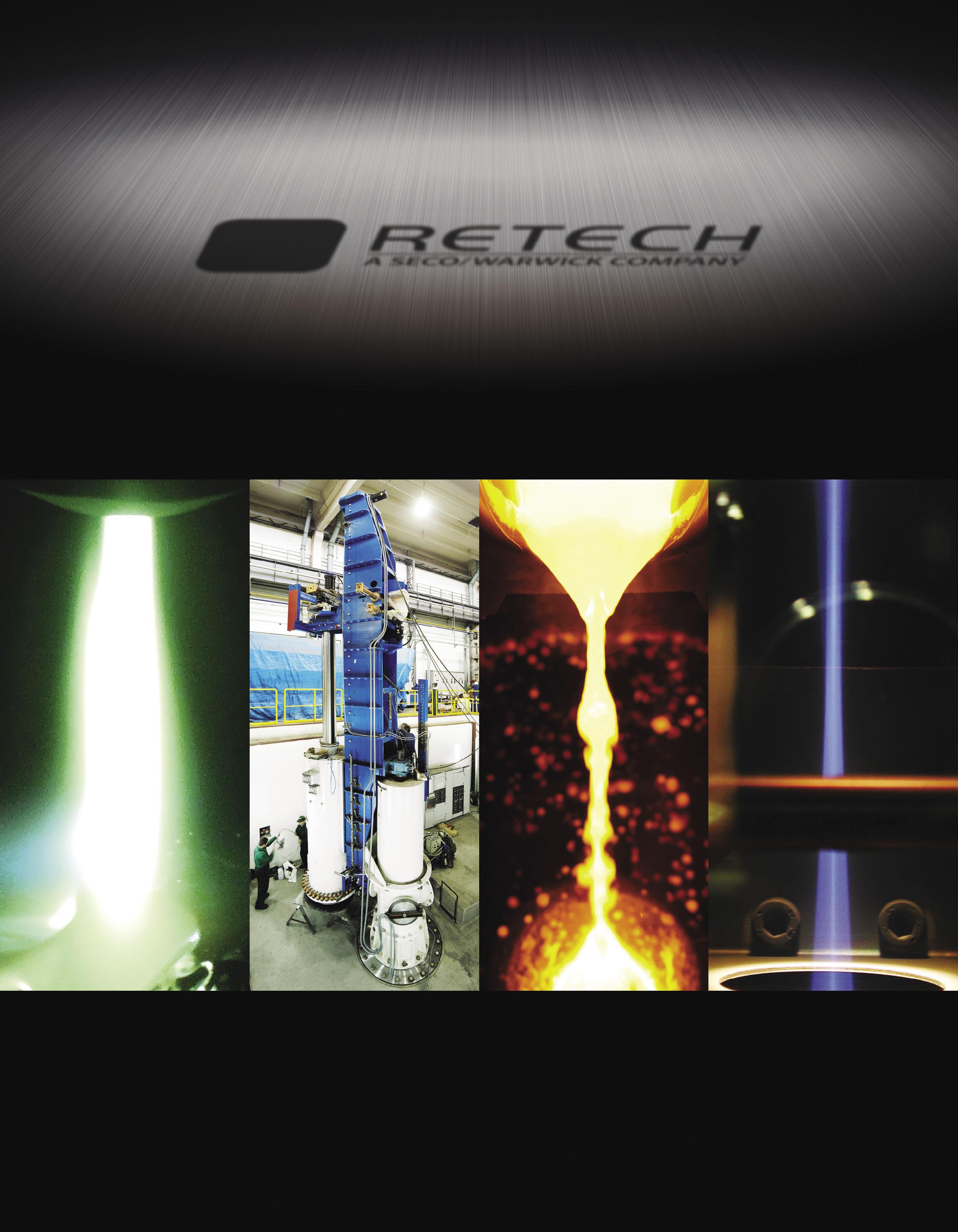
Maximilian A. Kaiser, chair of lightweight automotive design for the department of mechanical engineering, Paderborn University, Germany, examined the “Heat Transfer Coefficient Investigation for Hot-Die Quenching Process of Ti 6 AL4V Alloy.” Kaiser said a new, efficient and resource-saving process for sheet metal forming of Ti-6AL-4V is needed. One solution is TISTRAQ: Titanium Solution Treatment and Rapid Quenching, a combination of short-time quenching and forming process with additional annealing.
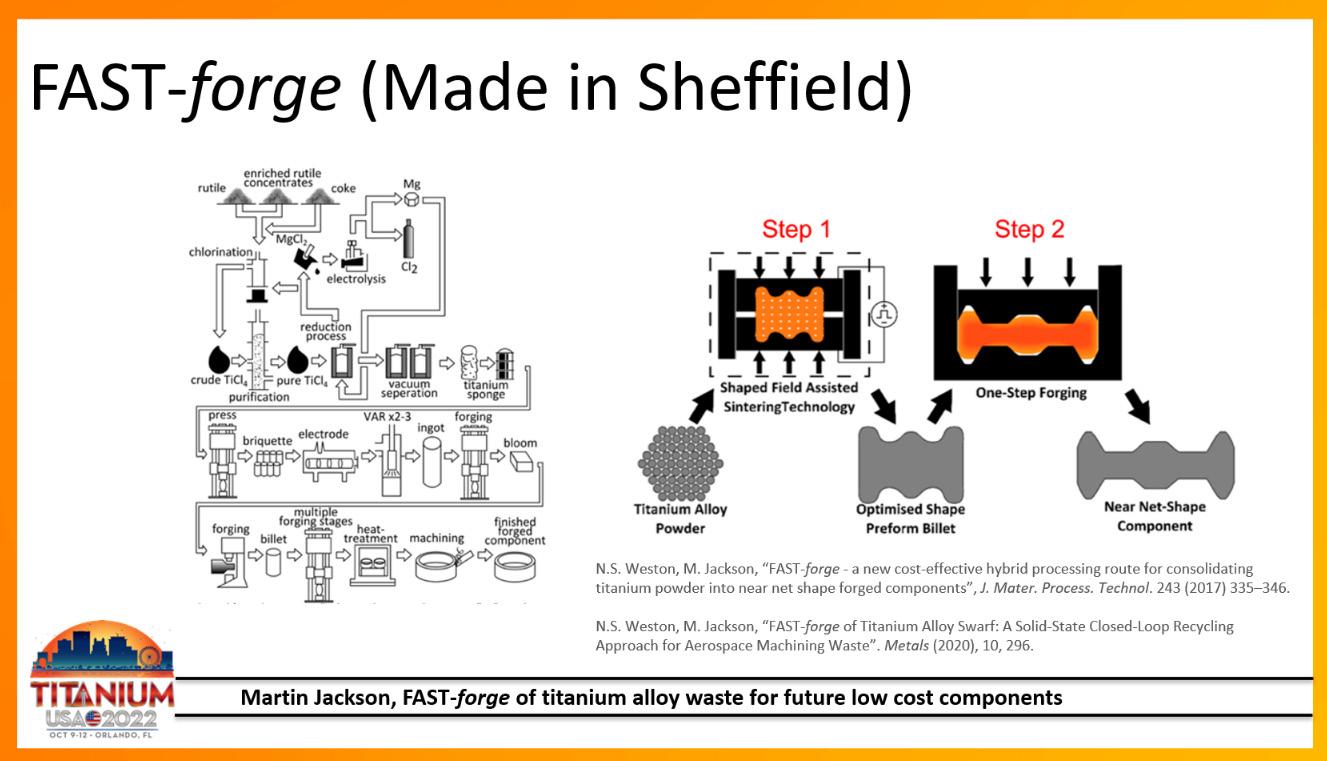
An online technical paper (https:// www.heggemann.com/news/2020/ aeronautical-research-new-publiclyfunded-joint-project-launched) explained that TISTRAQ is intended to avoid the formation of an oxygenenriched brittle edge layer (Alpha Case). “This process route offers great potential for increasing the efficiency for the production of aviation parts.”
The paper stated that “the main objective of the TISTRAQ joint project is the development of a new forming process for the energyand material-efficient production of sheet metal parts made of α+β titanium alloys with enhanced mechanical properties through process-integrated heat treatment. The project is funded by the German federal government in the context of the aeronautical research program and it was launched in July 2020. For the first time, the titanium alloys shall be heated very quickly and then quenched with tempered forming tools. The process-integrated heat treatment increases the potential

