
10 minute read
Embracing Vision of Future, FIA Outlines Areas of Automation for Titanium Forging
By Michael C. Gabriele
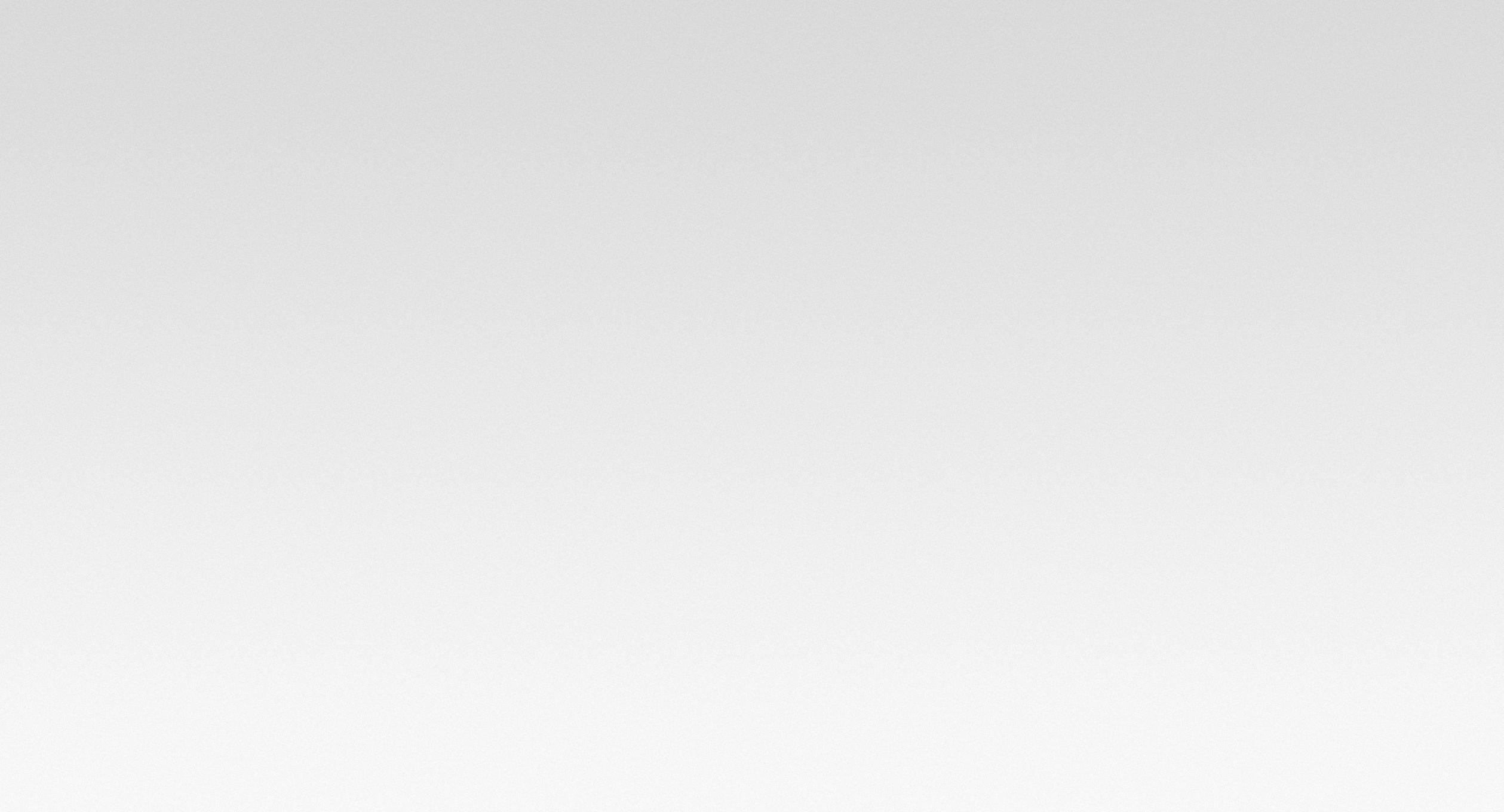
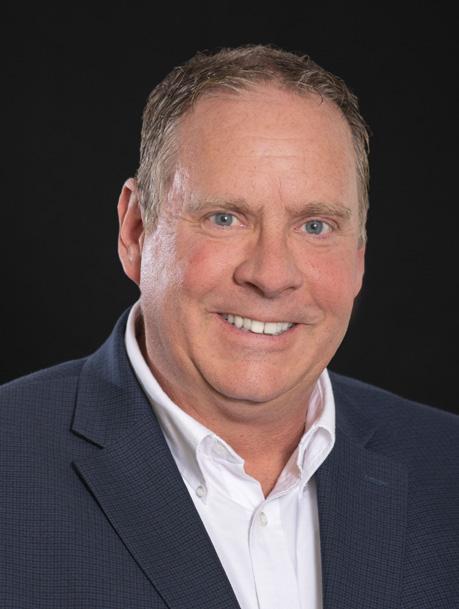
The North American forging industry, including companies operating in the titanium sector, have quietly been investing in an automation renaissance during the last four years—an effort that’s expected to continue through the foreseeable future to modernize the industry’s manufacturing technology. Jim Warren, the president and chief executive officer of the Cleveland-based Forging Industry Association (https://www.forging. org), said this automation renaissance is fulfilling the organization’s outlook filed in a report titled “Vision of the Future—Technology Initiative,” which was published two years ago. That report laid out a technology roadmap for the forging industry to keep pace with competitors in Asia and Europe.
“New knowledge must be developed and applied industrywide through specific research and development that focuses on bulk deformation sciences and engineering technologies so that more cost efficient and higher performing products and processes are developed,” the report stated. “Partnerships between the forging industry, federal laboratories, universities, and vendor companies must be formed to share information on integrated computational tools, advanced modeling, and automation techniques. Advancements in computer modeling, sensors and controls, and technology for intelligent manufacturing are other areas in which developments could be applied to benefit the forging industry as well as several other vision industries.” Warren underlined three key areas of automation being adopted by the forging industry. The most forward-thinking of these is the use of a “digital twin,” a technology that runs parallel with a factory floor forging operation. He said this digital twin can track the manufacturing operation in real time and anticipate potential system disruptions before they occur.
A Jan. 28 online article posted by Forbes.com (“How To Reinvent Continuous Improvement With Intelligent Digital Twins In Manufacturing”) explained that the unfolding “fourth wave” of a global industrial revolution is being realized “through the use of various technologies, including intelligent digital twins that
allow for real-time monitoring of a machine’s condition, artificial intelligence that can analyze large amounts of data to produce actionable insights, and connected devices that provide live status updates.” “Intelligent digital twins are software models that closely resemble the real-life counterpart they are based on,” Forbes reported. “The twin is fed information Jim Warren from various sources, including sensors, monitoring equipment, and software programs. This digital twin constantly learns to provide the latest updates on the physical machine’s health based on observed conditions. As intelligent factories become a reality, they will enable
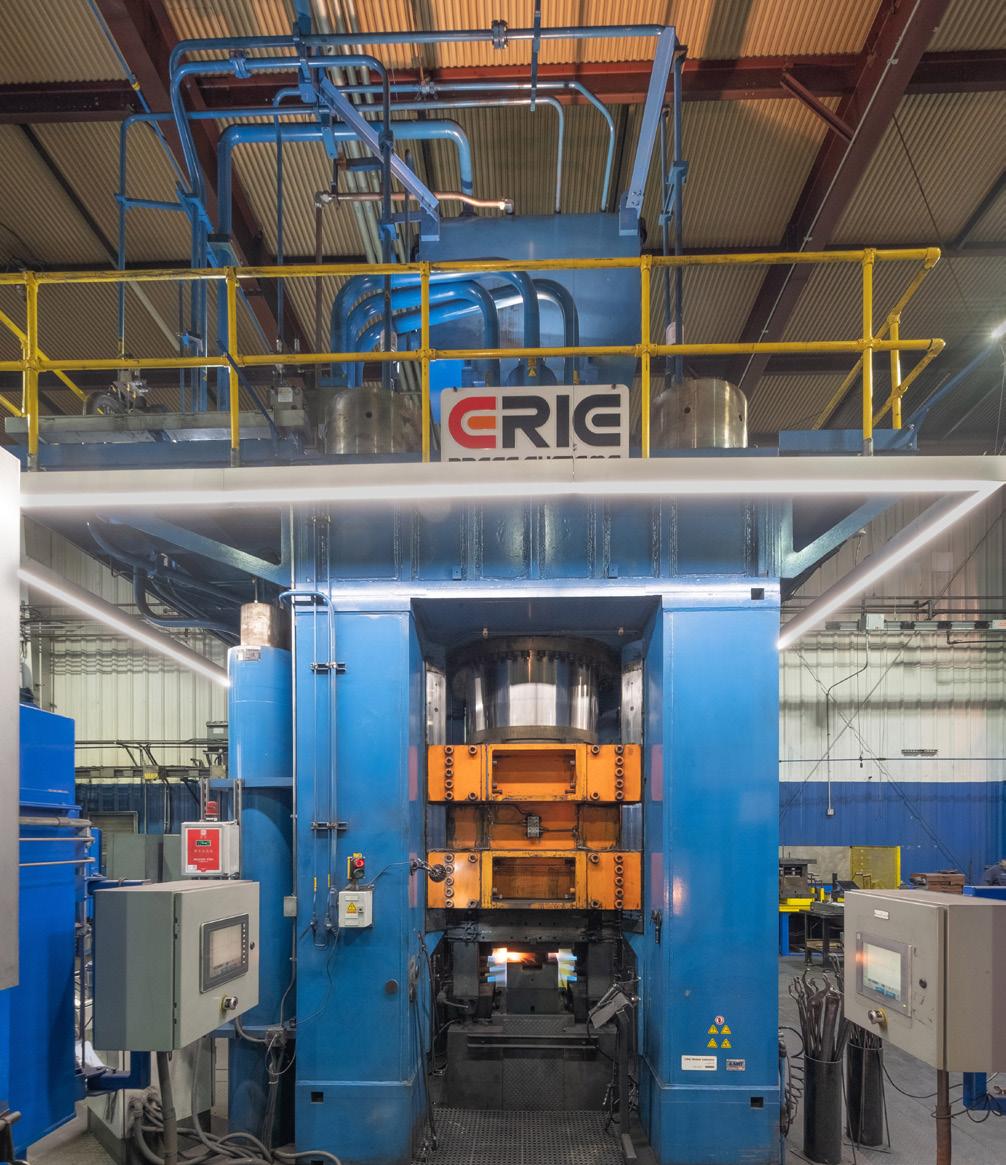
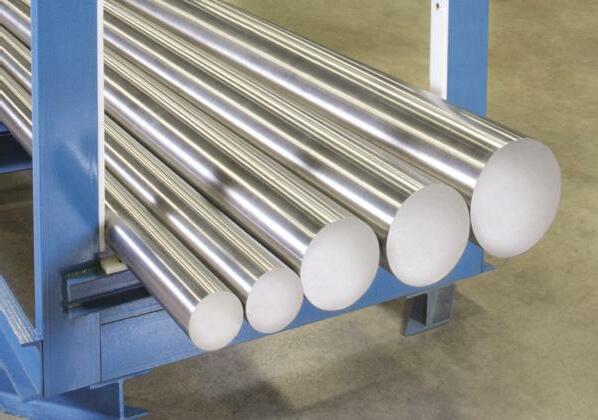
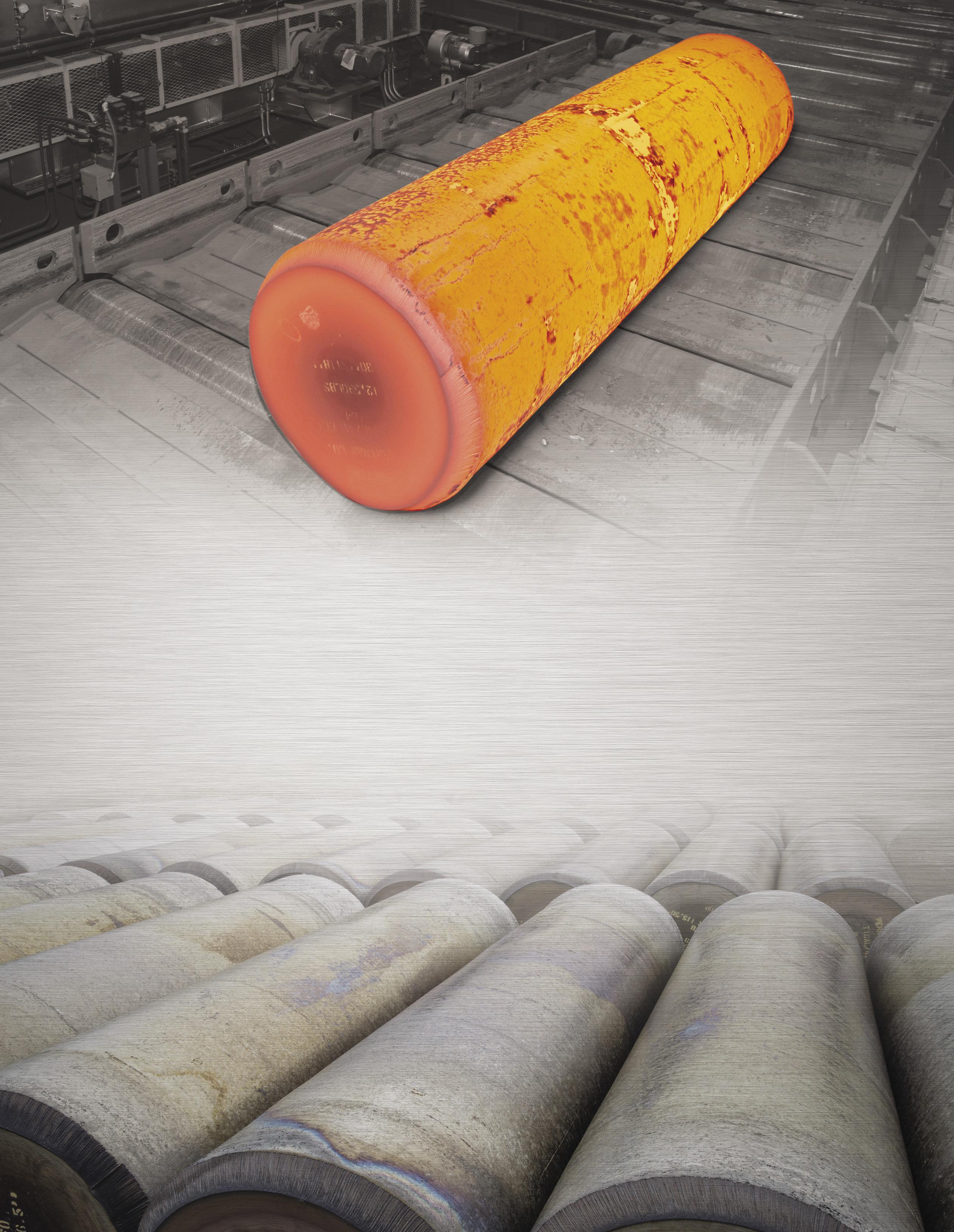
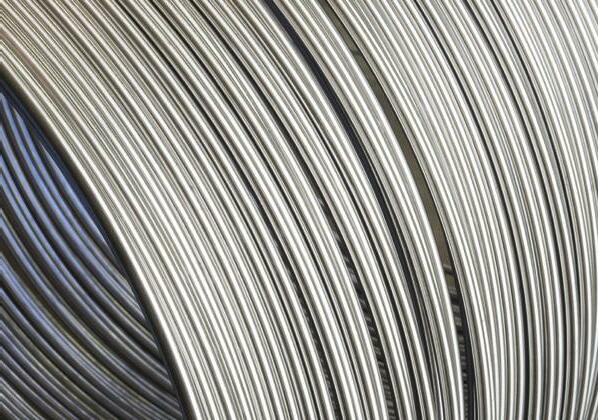
Positioned to Respond.
Our continued investment and expansion has us in the right place to meet your needs.
Our capacities and resources are aligned. We are prepared and well positioned to supply a full range of products including ingot, centerless ground bar, precision coil, additive wire, premium fine wire and shapes – all at competitive lead-times. We are expertly equipped to address the growing demands of the aerospace, medical, recreation, infrastructure, and industrial markets worldwide. We understand the ever-changing factors of the industries we serve and are committed to supporting the growth of your business.
Fully Integrated Titanium Manufacturing
724.746.9390 | www.perrymanco.com
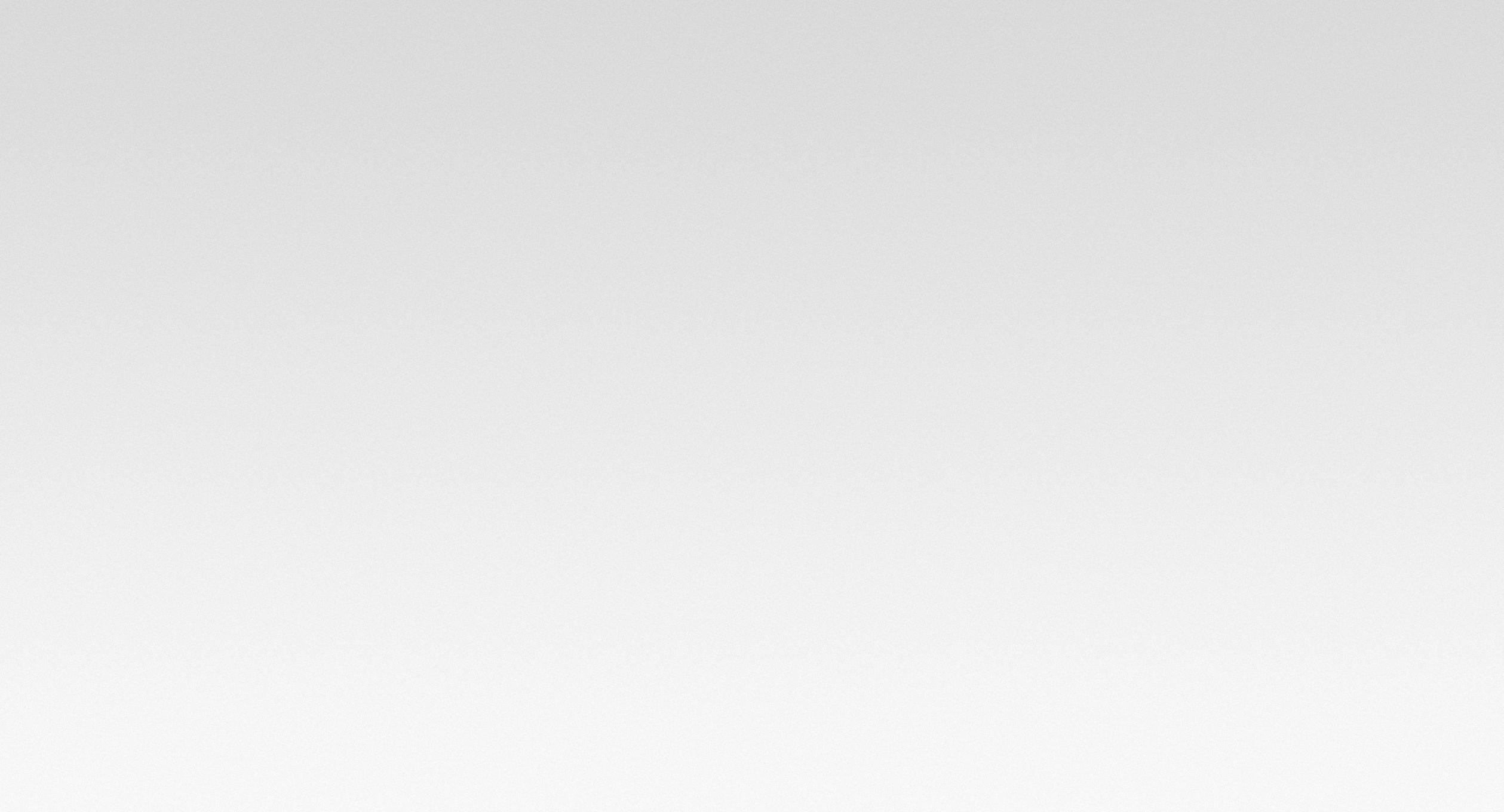
the manufacturing industry to shorten delivery cycles, reduce the cost of production and improve product quality through real-time insights.”
A second area of automation involves improvements in nextgeneration digital forging simulation systems, used off-line at the front end of the manufacturing process. Simulation systems can predict how a titanium billet is likely to flow inside a forging die, based on factors such as the die design, time, temperature and pressure. Warren said simulation systems can help streamline the forging process, as well as offer a guide to extend the life of a die. These systems also can simulate the heat treating process, which is especially significant to maximize the quality and integrity of forged titanium parts.
Warren said a third area of forging automation can be found in the incremental upgrades to factory floor material handling systems, enhancing the accuracy, safety and repeatability of robotic and conveyor equipment in transporting a heated titanium billet to the forging press. In addition, the forging industry is migrating to induction electrical heating systems, gaining the benefits of more precise heating control of billets, compared with more traditional gas-fired furnaces.
While commercial aerospace remains a dominant market for titanium forgings for the production of landing gear, advanced engines and aero structures, opportunities continue to emerge in military applications. Aside from military aircraft, the Defense Logistics Agency of the Department of Defense is focused on light-weighting weapons and military equipment. For example, The New York Times, in a pageone, May 23 story, reported that American-made M777 howitzers are being shipped to support Ukraine.
The lethal American howitzers “are chunky machines of steel and titanium swathed in hydraulic hoses and perched on four braces that fold up and down.” The lightweight weapons are appreciated on the battlefield for their maneuverability, but also from the perspective of strategic military logistics—the ability to transport and deliver the equipment via long-distance cargo planes. Warren acknowledged that the U.S. forging industry, compared with global competitors, has “legacy” issues, given its heavy level of investment in older Bharat Screw Presses equipment. “China has a fully automated forging industry. Europe changes out its forging equipment more often than the United States.” The Forging Industry Association’s “Vision of the Future” document outlined these challenges and charted a road Jim Warren, the president and chief executive officer of the Forging Industry Association, underlined key areas of automation being adopted by the forging industry. The most forwardthinking of these is the use of a “digital twin,” a technology that runs parallel with a factory floor forging operation. He said this digital twin can track the manufacturing operation in real time and anticipate potential system disruptions before they occur.
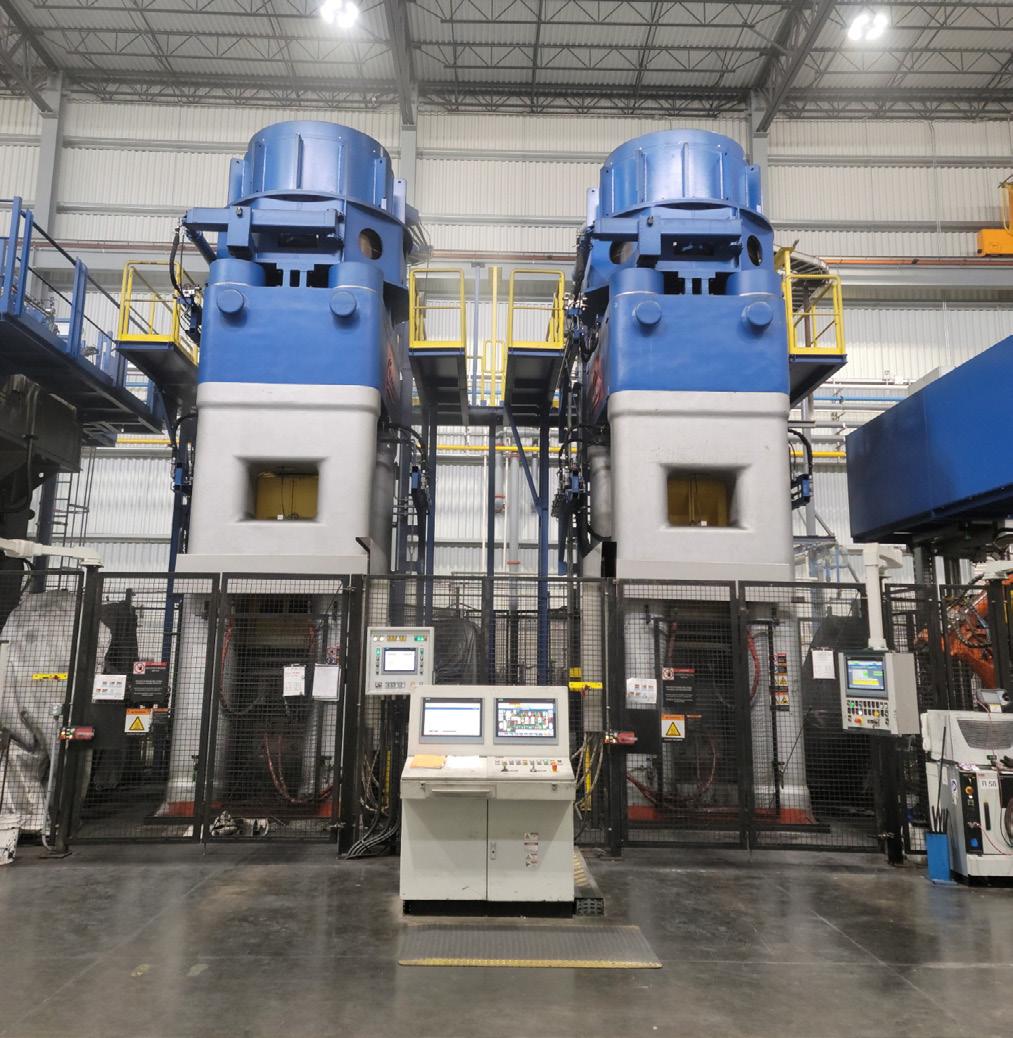
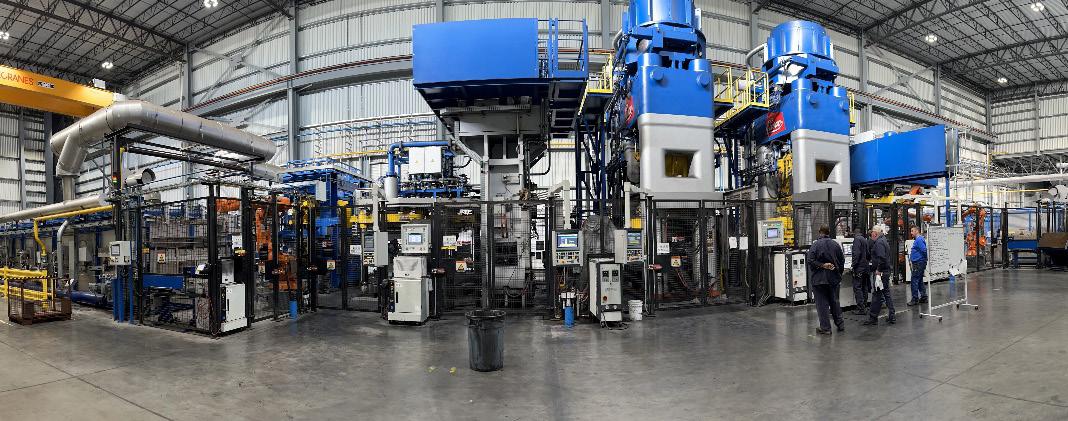
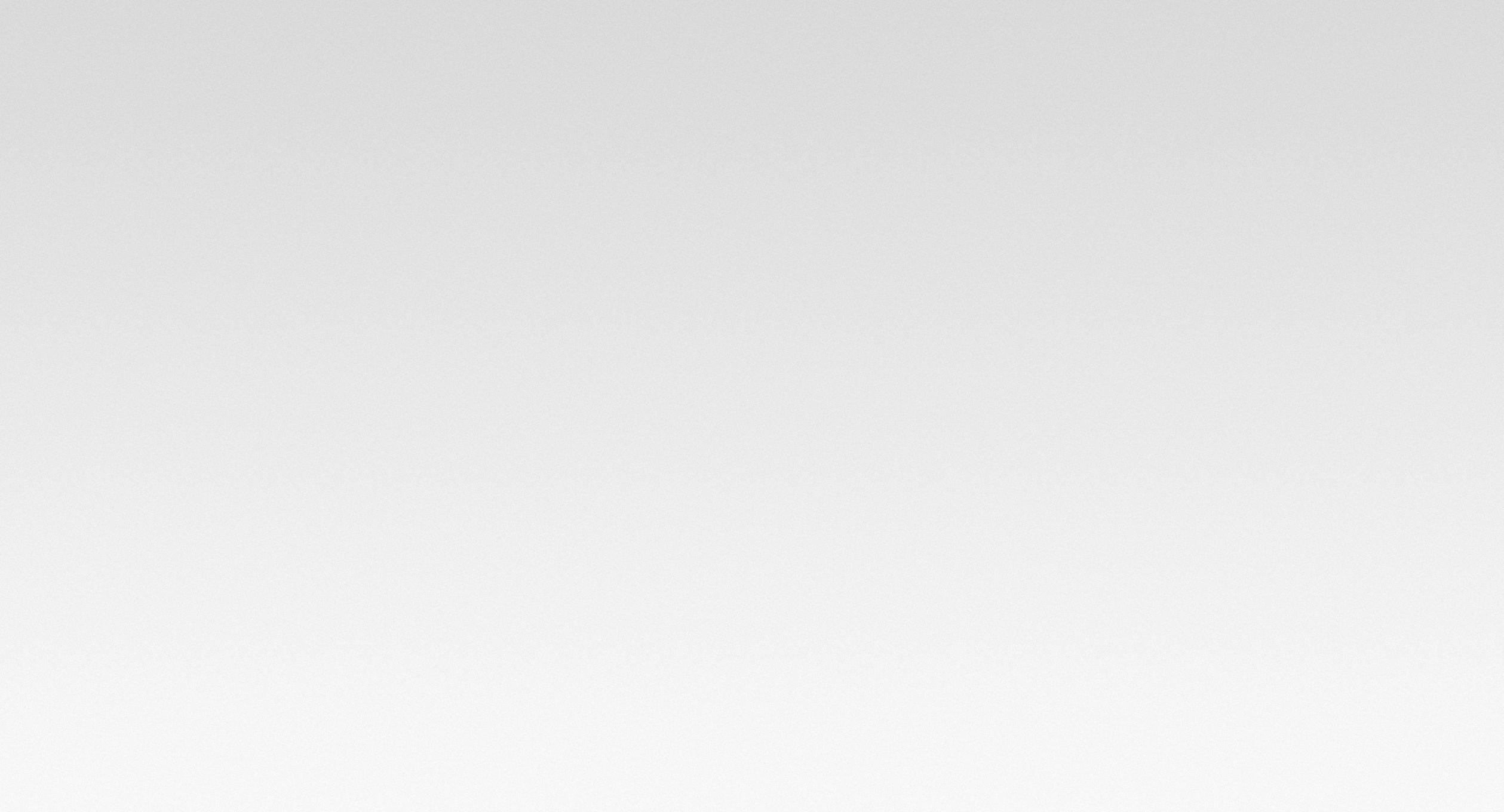
Factory Floor Panorama with Bharat Presses
map for this industrial group. “The forging industry is a key link between critical manufacturing segments— metal suppliers (both ferrous and nonferrous) and end user industries. Forgings, which appear in 20 percent of the products representing the gross domestic product of the United States, are essential to the U.S. industrial economy, its society, and its national security. In recent years the U.S. forging industry has undergone significant shrinkage associated with intense global competition, technological changes, and environmental and economic factors. Those companies that survived the industry downsizing emerged stronger and better equipped to face the competitive challenges of manufacturing today.” The document identified major U.S. industries that depend on forgings, a list that included automotive and truck; agricultural machinery and equipment; valves, fittings, and petrochemical applications; hand tools and hardware; off-highway and railroad equipment; general industrial equipment; ordnance and marine; and aerospace.
“Impediments to collaborative, pre-competitive research must be eliminated, advocating programs that reward performance rather than specific methods of regulatory compliance. Cost, benefits, and relative risk of cooperative ventures must be given greater consideration. Forging companies must work with U.S. and international governments and standards organizations to harmonize standards for nomenclature, documentation, quality, and testing. The industry needs to improve the efficiency of logistics by developing new methods for working more effectively with suppliers, sponsoring efforts to shape information technology and standards to meet the manufacturing needs of the forging industry.” n (Editor’s note: All photos courtesy of the Forging Industry Association.)
Forging Industry Association Offers Guidelines for Forging of Titanium
The Forging Industry Association provides basic information on the forging of titanium on its website (https:// www.forging.org/forging/ design/46-titanium-alloys.html). Titanium alloys are selected for applications requiring high strength, low weight, high operating temperature or high corrosion resistance. Specific strength is high compared with steel. Densities are approximately 55 percent those of steel and 60 percent greater than aluminum alloys. The properties and cost of titanium alloys make them the choice in applications where a premium can be justified for high performance, such as aerospace, chemical processing and prosthetic devices. The
designation system indicates the type and amount of the major alloying constituents. For example Ti-6Al-4V contains 6 percent aluminum and 4 percent vanadium.
As with other forging alloys, the mechanical properties of titanium alloys are affected by forging and thermal processes as well as alloy content. However, when die filling is optimized, there is only a moderate change in tensile properties with grain direction, and comparable strengths and ductility are obtainable in both thick and thin sections. The processing of titanium alloys through the forging and subsequent thermal processes is a highly developed technology.
Titanium alloys are more difficult to forge than most steels. The metallurgical behavior of the alloys imposes some limitations and controls on forging operations, and influences all of the steps in the manufacturing operation. Special care is exercised throughout all processing steps to minimize surface contamination by oxygen, carbon or nitrogen. These contaminants can severely impair ductility, impact toughness, and the overall quality of a titanium forging if left on the surfaces.
Hydrogen can also be absorbed by titanium alloys and can cause problems if levels exceed specified amounts. Hydrogen absorption, unlike that of oxygen, is not always confined to the surface.
Titanium alloys can be forged to precision tolerances. However, excessive die wear, the need for expensive tooling, and problems with microstructure control and contamination may make the cost of close tolerance (not machined) forging prohibitive except for simple shapes like compressor fan blades for turbo-fan engines.
Close tolerance forgings in moderately large sizes are currently being developed using hot die and isothermal forging techniques. Hot die and conventional forging of the Ti-10V-2Fe-3Al alloy, which has a relatively low forging temperature, has been demonstrated to be very successful with dies made from heat resistant alloys and heat treated to over 650°C (1200°F).
Glass coatings are commonly used to protect the titanium forgings from excessive oxidation and to provide some lubrication as well as serving as a release compound to prevent die galling (pressure welding).
There are three basic types of titanium forging alloys: alpha alloys, alpha-beta alloys, and beta alloys. The alpha alloys are designed for resistance to creep at elevated temperatures, exceeding 535°C (1000°F) in some cases. They are not heat treatable in the conventional sense but they are annealed after forging to relieve stresses. The microstructure of alpha is essentially all alpha phase.
The alpha-beta alloys are those that include a mixture of alpha and transformed beta microstructures at room temperatures. They are heat treatable to very high strengths with a solution treatment and an age cycle. The widely used Ti-6Al-4V alloy is also the most common forging alloy.
The beta alloys are those containing sufficient alloy content to retain the beta phase to room temperature. Alloys include the more common Ti-10V2Fe3Al as well as some more highly alloyed grades such as Ti-13V-11Cr-3Al. These alloys are treatable to high strengths exceeding those achievable with Ti6Al-4V. The alloy Ti-13V-11Cr-3Al has been largely superseded by the 10-2-3 grade for forgings. In all three groups, the forging practices have a profound influence on the resulting properties. Forging suppliers should be contacted for their experiences in forging and heat treating these families of titanium alloys. n
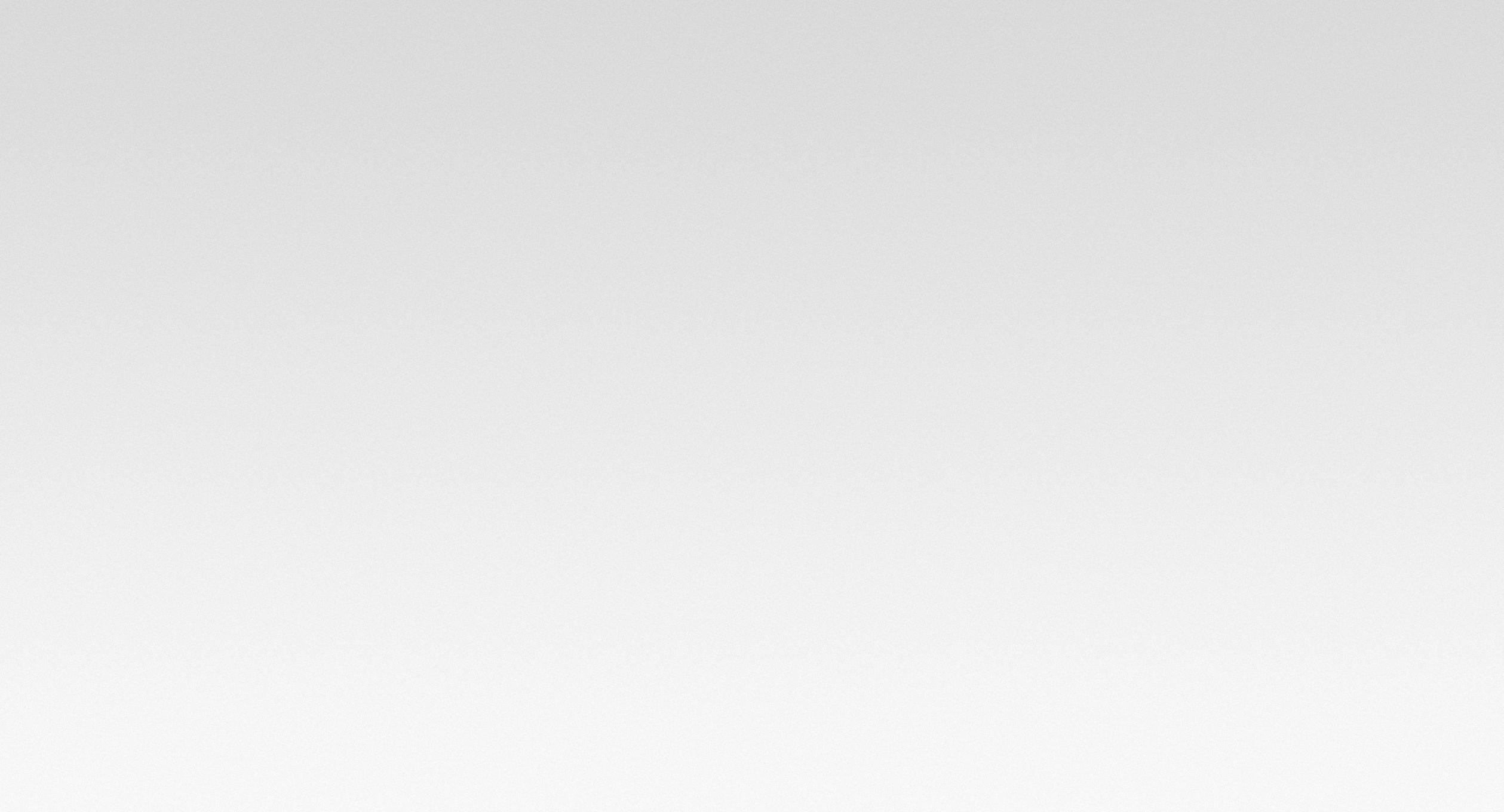
tricormetals.com astrolite.com tricoralloys.com
Titanium Mill Products:
Sheet, Plate, Bar,Pipe,Tube,Fittings, Fasteners, Expanded Sheet & Ti Clad Copper or Steel.
Titanium Forgings and Billet:
Staged intermediate ingot & billet to deliver swift supply of high quality forgings in all forms and sizes including: rounds, shafts, bars, sleeves, rings, discs, custom shapes, and rectangular blocks.
Titanium, Zirconium, Tantalum & High-Alloy Fabrication & Field Repair Services:
Vessels, Columns, Heat Exchangers, Piping, Anodes, Custom Fabrications, Field & In-House Reactive-Metal Welding & Equipment Repair Services Available 24/7.
Plate Heat Exchangers:
Plate Heat Exchangers to ASME VIII Div 1 Design, Ports from 1” through 20” with Stainless Steel, Titanium and Special Metals, Plate Heat Exchanger Refurbishing Services & Spare Parts.
Two Service Centers & Fabrication Facilities in Ohio & Texas with Capabilities in:
Waterjet, Welding, Machining, Sawing, Plasma Cutting & Forming.
Serving a Wide Variety of Industries:
Chemical Processing, Mining, Pulp & Paper, Plating, Aerospace, Power and others.
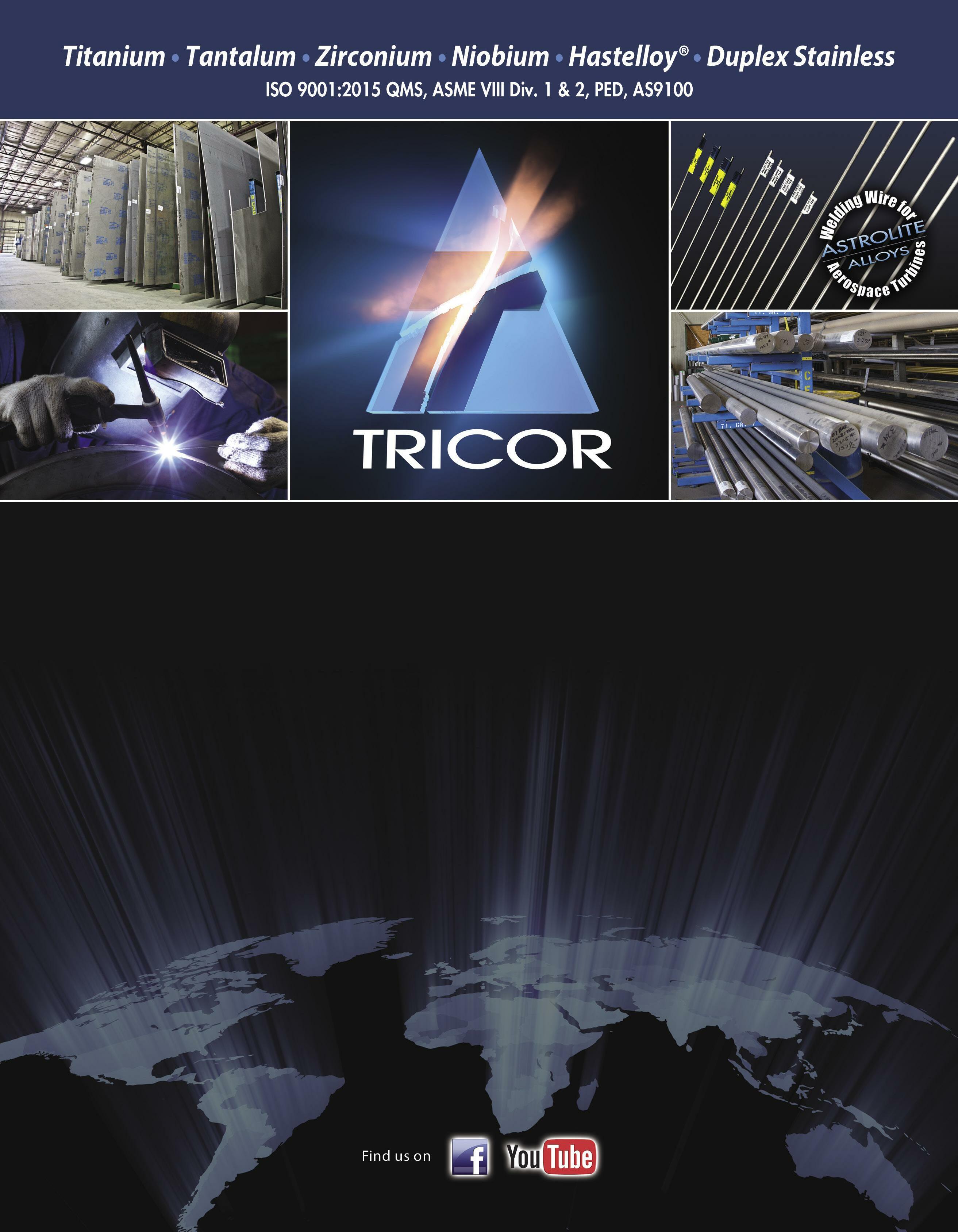
Ti sheet, plate, bar, & forgings 6/4,6/4ELI, CP Ti, Welding Wire, & Fabrications
Tricor Metals, Ohio Division 3225 W. Old Lincoln Way Wooster, Ohio 44691 Phone: 330-264-3299 Fax: 330-264-1181
Tricor Metals, Texas Division 3517 North Loop 336 West Conroe, Texas 77304 Phone: 936-273-2661 Fax: 936-273-2669
Tricor Metals, Michigan Division 44696 Helm St. Plymouth, MI 48170 Phone: 734-454-3485 Fax: 734-454-7110
Astrolite Alloys California Division 201 Bernoulli Circle, Units B & C Oxnard, CA 93030 Phone: 805-487-7131 Fax: 805-487-9694