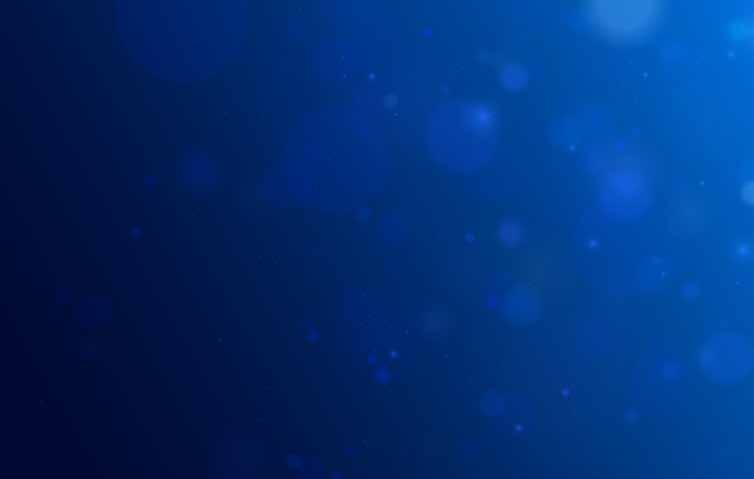
7 minute read
dental implants
accuracy, as layers can be as thin as 20 microns. 35 New technologies are being developed that can print layers as thin as 5 nanometers. This is the currently preferred method for 3D printing of dental objects. Today, resins are available for a multitude of dental purposes including dental models, surgical guides, occlusal guards, orthodontic models and indirect bonding trays, provisional crowns and even long-term objects like dentures and resin restorations. There are several 3D printers on the market today that are designed for dental use such as Formlabs Form3+, SprintRay Pro S and Whip Mix Asiga Pro 4K.
The vast 3D printer market provides dentists with innumerable options beyond those stated previously, but one selection criterium rises above the rest — selecting a 3D printer with dentistry-ready features from the manufacturer allows practitioners to efficiently and predictably print their prepared STL files. Such printers have a user-experience like milling units integrated within CAD/CAM systems, boasting solidified digital processes, lists of approved materials and dental-focused custom settings. For printers that do not have these capabilities, users may need to manually repair STL files, transfer them to the printer, orient the models, experiment with unsupported resins and set print parameters through trial and error.
Resin-based 3D-printed models require finishing steps consisting of removing support structures, washing the print, post-print curing and polishing. While finishing stations can be created from existing dental lab equipment (a fume hood, lab handpiece, curing device, glass containers, ethanol and hand tools), dedicated devices like the Elegoo Mercury or SprintRay Pro Wash/ Dry streamline the process by keeping hazardous materials contained, automating tasks like agitating a model during washing and consolidating equipment into a single device to save space.
Regardless of the type of 3D printer and finishing process used, the National Institute for Occupational Safety and Health (NIOSH) has identified three common work hazards for additive manufacturing: breathing harmful materials, skin contact with harmful materials and flammable materials. During all printing stages, NIOSH recommends proper engineering controls, administrative controls and personal protective equipment. This includes using high-efficiency particulate air (HEPA) filters, introducing safety guidelines for handling and securing volatile materials like resins and solvents and wearing respirators, gloves and safety goggles.36
Surgery Stage
For implant cases where the guide uses existing adjacent teeth for indexing, the guide can simply be placed on the teeth until it seats completely and does not rock. While it is possible to adjust an ill-fitting guide, it indicates an error occurred during the digital workflow, which can result in the implant not being placed in the planned location. The digital planning and guide fabrication steps should be redone with care.
The guide can be used during implant surgery for direct drilling of the osteotomy only (known as half-guided implant placement) or for both drilling the osteotomy and placing the implant through the guide (known as fully guided implant placement). 37 A fully guided approach is more accurate than the partial-guided approach, as distal deviation and angular deviations from the planned position are significantly smaller with the fully guided approach.38
Guided implant placement follows the same principles as freehanded implant placement regarding patient preparation, anesthesia and suturing. While the principles are similar, flap design, osteotomy and implant placement require minor modifications with the guided technique.
Patient preparation involves obtaining informed consent about risks, benefits and alternatives and an appropriate description of the procedure, medications and what to expect. A single preoperative antibiotic dose is sufficient to significantly reduce early implant failure. 39 For local anesthesia, local infiltration using buccal, crestal40 and lingual infiltration is sufficient for most forms of implant placement.
Guided implant placement presents the opportunity for predictable flapless surgery if sufficient keratinized gingiva is present and the underlying bone anatomy allows for it. For this, a biopsy punch drill is used through the guide hole at the implant site until the drill touches bone. The guide is then removed, and the tissue plug at the implant site is removed using suitable instruments such as tissue forceps, periosteal elevators or periodontal knives.
A full thickness flap should be raised for implant placement if the procedure also requires bone removal, simul- taneous ridge grafting or high case difficulty where direct visualization of the bone is needed. Suturing typically aims to limit tissue mobility and aid healing.
For the osteotomy with a conventional kit, a key specific for each drill is placed into the guide, and the drill passes through the key. For the osteotomy with a guided kit, each drill is passed directly through the guide. Each drill has a drill stop that reaches the predetermined length (the implant length + tissue thickness + guide thickness) that was programmed into the guide. The osteotomy should follow the manufacturer’s protocol using a surgical drill with high rpm, low torque, copious irrigation, low pressure and, if needed, a straight up-and-down pumping motion to prevent thermal damage to the bone.
Implant placement should also follow manufacturers’ protocols, typically using very low speed (< 20 rpm) and a defined torque (often 30 Ncm to 50 Ncm) that provides sufficient stability without inducing pressure necrosis. For maximum benefit and fully guided surgery, the implant should also be placed through the guide to minimize placement errors. If the implant is placed freehanded after using the guide for the osteotomy, angulation errors may be introduced and some of the benefits of fully guided surgery will be lost. At each osteotomy and implant placement step, the clinician must check if the placement matches what was planned and if the placement is appropriate for the given site.
Pitfalls of Using Guides
For posterior areas, using a surgical guide on a dentate patient may be difficult, as the acrylic and added implant drill length may prevent the operator from using the guide, especially in individuals with limited mouth opening.
“For maximum benefit and fully guided surgery, the implant should also be placed through the guide to minimize placement errors.”
While fully guided implant surgery can result in improved placement accuracy, placement errors are still possible stemming from inaccuracies in the CBCT acquisition, 3D scanning, guide planning, 3D printing, positioning of the guide during surgery and short guide sleeve length.41 It is also possible that a clinician may need to forgo using a t
Dental Implants

surgical guide as consequence of unanticipated complications encountered during surgery, such as insufficient implant stability at the planned insertion depth, closer than expected proximity to vital structures, encountering a bone dehiscence or a poorly fitting guide.42 While low-cost 3D printers can produce acceptable guides, 43 accuracy of the guide is dependent on the manufacturing process and size of the guide, with small guides having better fit.44
Dynamically Guided Surgery
The previously described method using a surgical guide fitted over the adjacent teeth describes static guided surgery, which is the more common guided surgery approach. Dynamically guided implant placement was introduced to dentistry in the year 2000, where motion tracking of the patient and handpiece provides the clini- cian instant feedback about the planned implant position within the context of CBCT data. More recent availability of in-office CBCT machines, reduced cost and improved designs to facilitate use of these systems in a dental office have led to greater interest in this technology, as it may result in a simpler implant planning workflow.45 Currently, two dynamically guided implant systems have received FDA 510(k) clearance and are available in the U.S. (i.e., Navident ClaroNav, X-Nav X-Guide Dynamic 3D Navigation). 6,47 With these systems, cameras mounted in the operatory record optic markers placed on the handpiece and the patient and a computer system provides the operator feedback on a screen whether the implant motor is positioned at the correct angle and position. As another approach in dynamically guided implant placement, robotics was introduced to implant dentistry in 2017 with the development of an autonomous robot implant placement system in China and FDA clearance of a robotic system that assists placement of implants.48 The FDA- cleared system is available as the Neocis YOMI system where a handpiece is mounted on a robotic arm that provides the operator haptic feedback on the correct angulation and position.49 Currently, this system has been developed for use in fully and partially edentulous arches, but requires sufficient teeth or bone to stably hold a splint in place.50 A drawback of the robotic approach is that this system is still quite expensive and is still undergoing development for wider applications.
Digital Restoration
Once the implant is integrated and ready to be restored, a conventional implant-level impression can be taken to have the restoration fabricated. However, the digital workflow can continue with an intraoral scan of the implant to reap the maximum benefits from digital dentistry.
To use an intraoral scanner for an implant restoration, a scan body is required. A scan body is equivalent to the impression coping (FIGURE 16) in the conventional method. Each scan body is unique to each implant platform, as with an impression coping, so this needs to be ordered from the implant distributor prior to the intraoral scan appointment. The scan body is used in the same way as an impression coping. The healing abutment is removed, the scan body seated and hand-tightened and a radiograph taken to verify complete seating. Once fully seated, an intraoral scan is taken in lieu of an impression, taking care to capture all the notches of the scan body in detail (Fig. 17).
The lab uses the scan body image to determine the exact implant position and to design the abutment and restoration accordingly. The lab can print a model and fabricate the restoration conventionally, or it can design and mill the restoration digitally.
Conclusion
Digital implant workflows hold the promise for dentists to plan and execute implant placement with great accuracy, reliability and predictability, leading to potentially simpler and more predictable restoration. The key requirements for implementing digital implant dentistry are to use a CBCT machine and an intraoral scanner to create a 3D model of bone, teeth and overlying soft tissue and to use this model to plan implant placement for guided surgery.
Reprinted with permission from the California Dental Association, copyright September 2022
The corresponding author, Tobias Boehm, DDS, PhD, can be reached at tboehm@westernu.edu.