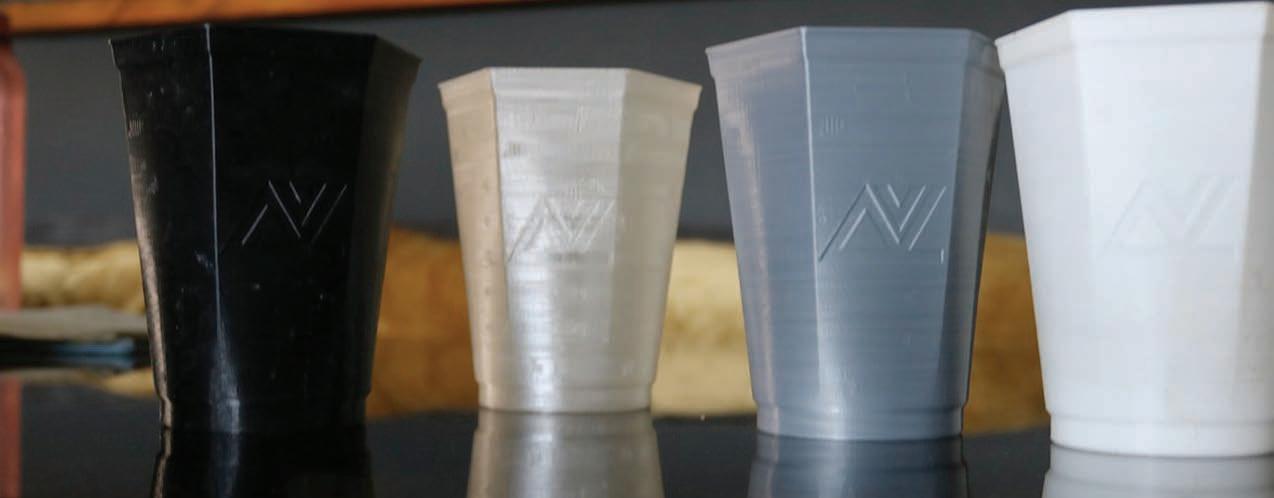
14 minute read
SA entrepreneur saving the planet, one cup at a time
SA entrepreneur uses 3D printing
to help save the planet, one cup at a time
Advertisement
Using 3D printing technology, Red Cup Village started by creating biodegradable drinking cups using polylactide (PLA) filament – a biodegradable polyester derived from sugarcane and corn starch.
Biodegradable drinking cups using PLA filament
AS AN entrepreneur, hobbyist, 3D printing enthusiast, and inventor, Luvuyo Ndiki (30) is the man behind Red Cup Village, a lifestyle brand dedicated to producing high quality and innovative products that help its users make a difference in society.
Ndiki established Red Cup Village in 2014 with a vision to become a leading disruptive 3D printing and 3D scanning company through innovative concepts and premium products. And this vision is steadily coming to fruition thanks to the hard work and dedication of the talented Ndiki and his creative and forwardthinking team.
Using 3D printing technology, Red Cup Village started by creating biodegradable drinking cups using polylactide (PLA) filament – a biodegradable polyester derived from sugarcane and corn starch. Born in Butterworth and raised in Bathhurst, Ndiki says the idea to start the business struck him while studying Design Foundation at the Cape Peninsula University of Technology (CPUT) in 2010.
“The Design Foundation gave me a wide view of the design disciplines, from architecture, interior design, graphic design, product design, surface design and fashion design. I majored in product design, known as 3D dimensional design, in 2011, but could not complete the course due to financial constraints. However, I was determined to graduate, so I enrolled in Public Relation Management, which I completed in 2014,” says Ndiki.
While studying public relations, Ndiki continued to self-teach himself 3D dimensional design and 3D printing technology.
“I fell in love with 3D printing and established Red Cup Village with the idea to make world-class 3D printing and scanning accessible to individuals, organisations and start-ups across various sectors.
“It has been a long journey to where we are today – specialists in manufacturing on-demand consumer products and medical devices using 3D printing and scanning technology in combination with material science. Our platform allows users to construct personalised functional parts and products in a matter of hours, faster than traditional manufacturing processes, using biodegradable raw material derived from corn-starch, sugarcane and recycled plastics,” he explains.
The Red Cup Village 3D printing farm currently holds over 117 highperformance industrial and commercial 3D printers with the capacity for mass volume customisation and personalisation.
Inspired by Africa
Ndiki recalls how Red Cup Village was inspired by his grandmother’s story about an immensely enlightened African
Using 3D printing, Red Cup created biodegradable drinking cups using polylactide (PLA) filament – derived from sugarcane & corn starch
Hexcel showcases carbon fibre prepreg capability for UAV applications
THE successful maiden flight of a lightweight camera drone, developed using Hexcel HexPly® carbon fibre prepregs, has highlighted the capability of carbon fibre prepregs for Unmanned Aerial Vehicles (UAV) applications. The composite drone was developed by a team of students from the University of Applied Sciences Upper Austria in Wels with composite materials supplied by Hexcel Neumarkt in Austria.
A team of six students in the university’s lightweight construction and composite materials course was responsible for the complete design, engineering, and manufacture of the camera drone over a period of 18 months. Hexcel materials and optimization of the composite engineering enabled the team to reduce the composite structural mass by an impressive 42% compared to similar drones.
Hexcel Neumarkt was one of eight
Ndiki established Red Cup Village with the idea to make world-class 3D printing and scanning accessible to individuals, organisations and start-ups across various sectors
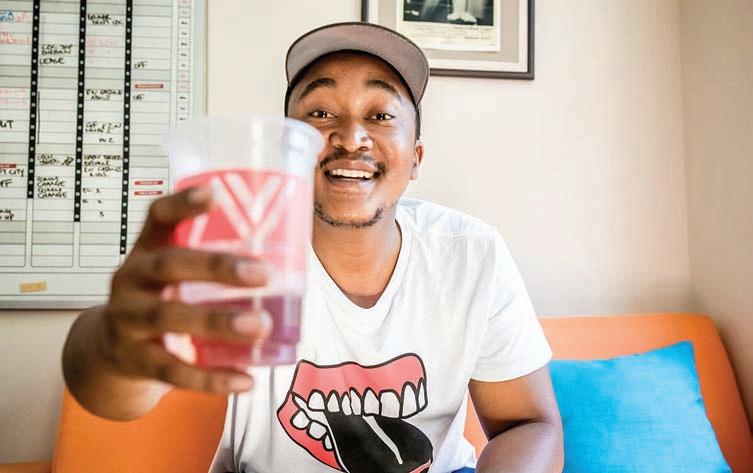
woman in the 13th Century.
“She united two rival kings by inviting them to a social gathering, where she made them drink from the same wooden cup. The two rival kings ended up not only sharing the cup but, belief systems and cultural backgrounds, which created social cohesion and united them and their villages.”
As such, the Red Cup Village name is a combination of his grandmother’s story and the disposable red cups popular in the hip-hop community. Even the brand’s logo, an upside-down R & V, makes reference to the ancient wooden cup shared by the rival kings, with the V-shaped vessel allowing users to pour their drinks from both sides.
Ndiki shares that his brand story has always been about bringing people from different cultures together. “It’s not just a cup, but a lifestyle. We are building a global lifestyle brand through the best quality products using raw and locallygrown materials and ethical sourcing practices.” “As a company, we look towards creating sustainable products for the environment and stimulate green economic growth in the country by producing local products from recycled plastics pallets. We also aim to empower young people to a lifestyle of unity, friendship and discovery,” he says.
“We want Red Cup Village to be a hub for innovative people from diverse cultures. We want South Africans to come together and drink from the same cup as one, united nation,” Ndiki adds.
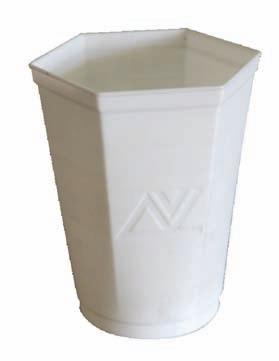
www.redcupvillage.com
industrial partners supporting the university team throughout the project, providing all carbon fibre prepreg materials used for the drone’s landing gear as well as the fuselage. The ultra-lightweight 32g landing gear was laid up and cured in the press, whereas the fuselage was autoclave cured by the student team using Hexcel HexPly M901 and HexPly M78.1 prepreg
www.hexcel.com
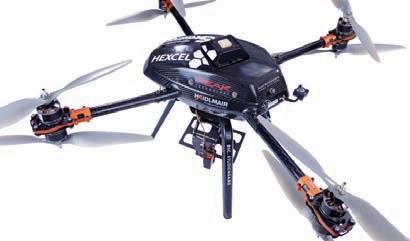
resin systems with a combination of woven and unidirectional carbon fibre reinforcements.

The bio-composite outer cladding and steel substructure of the Ermerweg underpass engineered by Solico, and the newly refurbished Valsteeg viaduct with composite handrail.
Composite elements for viaduct
DUTCH composite engineering specialist Solico has partnered with composites systems integrator Advantage Composite BV to engineer the composite elements of the 3 Phase N34 reconstruction project in the Netherlands.
The project includes the extensive reconstruction of multiple viaducts and underpasses along the N34, a provincial dual carriageway road linking the Dutch provinces of Drenthe and Overijssel. Advantage Composite BV manufactured composite elements engineered by Solico for the project.
Solico’s scope of work covered the detailed engineering of various infrastructure elements including steel support structures, composite claddings, railings, and handrails used throughout the project. In addition, Solico’s in-house test laboratory supported Advantage Composite BV with an extensive material testing and characterisation programme, enabling the finite element analysis of components using a novel bio-based material with a wood finish aesthetic.
One such example is the bio-based material used on the Valsteeg viaduct cladding in Phase 1, which combines the striking visual aesthetic of weathered steel with the durability and weight reduction of a composite material.
www.solico.nl
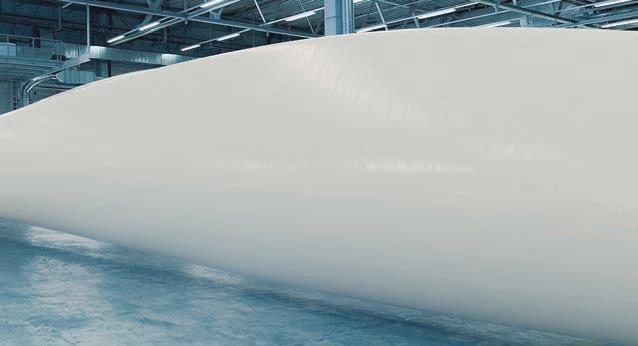
OCT / NOV 2021 38
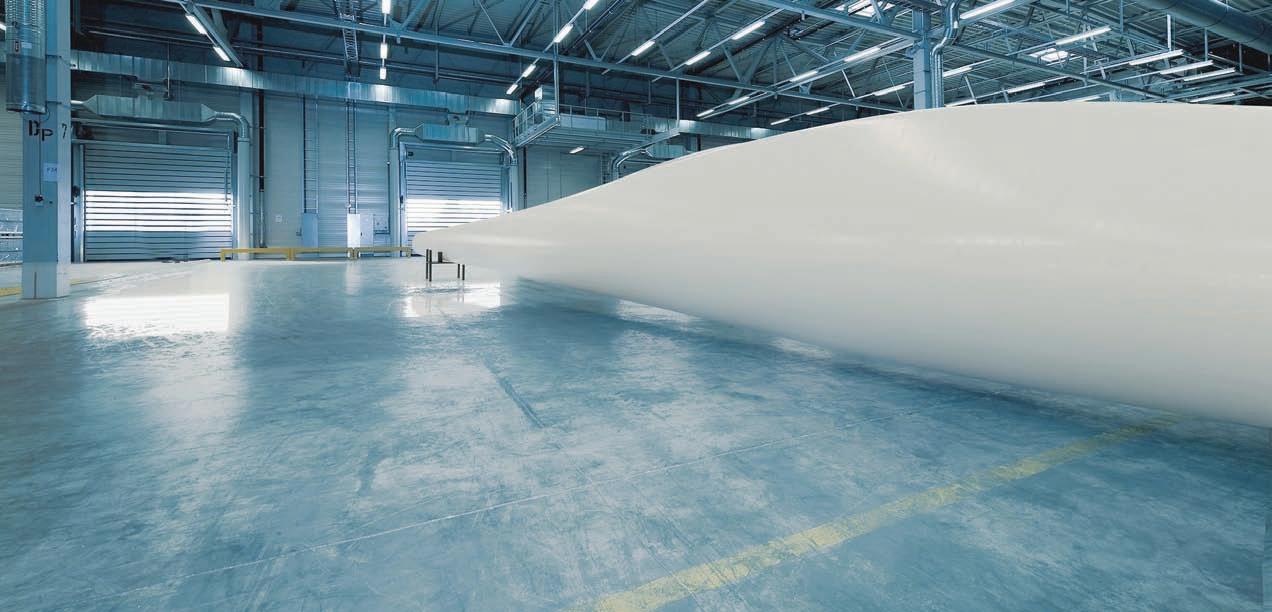
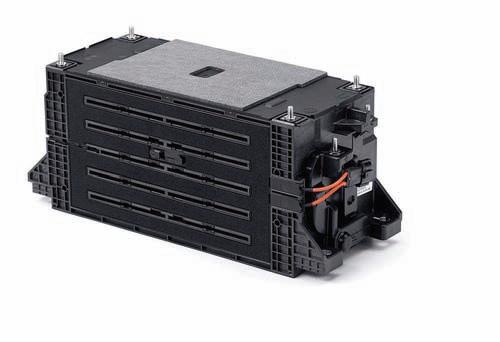
Hexcel’s surface technology revolutionises the blade surface finishing process
HEXCEL has launched its latest HexPly® XF surface technology that significantly reduces shell manufacturing time within the wind blade surface finishing process. HexPly XF increases overall blade manufacturing efficiency by reducing time in the mould by up to two hours and by banishing surface defects that require rework before painting.
As the surge in wind energy continues, wind turbine manufacturers are under increasing pressure to reduce costs, increase quality, and optimize productivity. Hexcel’s HexPly XF surface technology has been formulated to address the limitations of current blade shell surfacing techniques whereby pinholes and other surface defects have to be repaired by hand to achieve the perfectly smooth surface required for painting.
HexPly XF surface technology satisfies the most challenging surface quality requirements by introducing a new material format as the surface finishing layer, eliminating the need for a traditional in-mould gel coating process. HexPly XF for infused rotor blades, is a lightweight non-woven semi-preg construction, comprising an epoxy resin matrix, that co-cures with standard epoxy infusion systems. The product has a successful track record in prepreg blades and has now been adapted for infusion processes.
Easy to handle and supplied in a ready to use roll form, HexPly XF can be quickly applied by hand or with semiautomated layup equipment. It features one self-adhesive, surface finishing side - indicated by a removable protective foil. This side of the prepreg is placed against a release agent treated mould surface. Once the material has been positioned, the lay-up of the blade shell structure can start immediately, and the laminate can be infused. After curing, the blade is de-moulded with the manufacturer benefitting from a pinhole-free surface that needs minimal preparation before painting.
HexPly XF material is less than half the weight of a typical gel coat per square metre, reducing the overall weight of the blade. Additionally, the consistent areal weight and thickness of the prepreg film provide a completely uniform surface coating, ensuring blade weight distribution and balance are maintained, which is critical as rotor diameters continue to increase. With no need to handle or mix liquid chemicals as in the gel coat process, HexPly XF also improves the health and safety working conditions on the shop floor.
The material has a shelf life of six weeks at ambient temperature, which also minimizes cold storage requirements and helps to reduce scrap.
Lanxess, INFAC develop composite battery module housing
SPECIALTY chemicals company Lanxess (Cologne, Germany) and Korean auto parts specialist INFAC (Seoul), which specializes in automotive control cables, actuators, antennas, and battery packs, have together developed a battery module housing for electric vehicles (EVs).
The battery housing uses Durethan BKV30FN04 from Lanxess to satisfy stringent mechanical and chemical property requirements for latest EV components. The halogen-free, flame-retardant and glass fibrereinforced polyamide 6 (PA6) is characterised by its optimized flame-retardant and electrical properties. Lanxess notes that the material is highly processable and enables the integration of complex functions required for housing components, resulting in a smaller number of parts and a simplified assembly process as well as lighter weight.
The new battery housing part has also been adopted by series production of EV models launched by a Korean OEM this year.
According to Lanxess, Durethan BKV30FN04 is not only mechanically robust, but also boasts high-voltage insulation, is resistant to up to 800 volts and effectively blocking high-voltage current, characteristics that are critical to protect the battery from external shock. In addition to maintaining high strength and stiffness when in contact with electrolyte or cooling media, and enabling chemical resistance to suppress chemicallyinduced damage, the material’s flame-retardant properties help prevent or delay flames from spreading in case of a fire. Lanxess claims glass fibre-reinforced Durethan BKV30FN04’s durability to mechanical loads is also superior to unfilled PA6.
www.lanxess.com

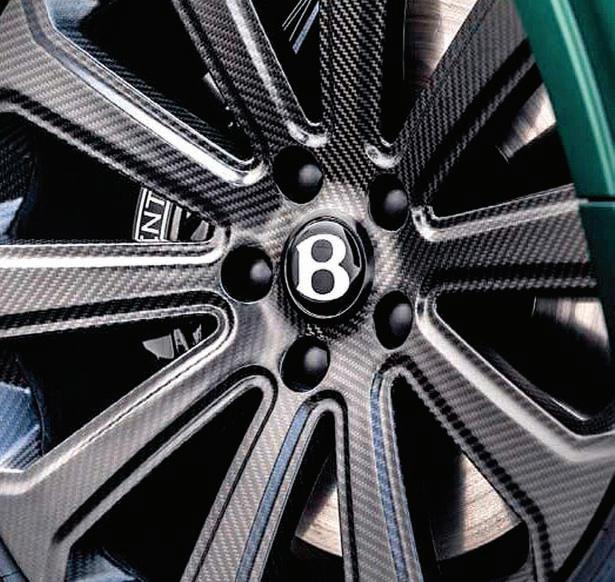
Bentley reveal new carbon fibre rim
A weight saving of 6kg per wheel
COMING from the ‘Carbon Valley’ of the Emilia Romagna region, the innovative full carbon car wheel that the prestigious British car manufacturer Bentley recently revealed for its Bentayga SUV is developed by Bucci Composites.
The 22” carbon wheel, the largest ever made in carbon, guarantees an innovative design and excellent performance, as well as a weight saving of 6kg per wheel.
All the benefits of using the ultralight carbon fibre wheel are directly linked to the reduced weight of the wheel: a lighter component design means less rotational inertia, which translates into greater acceleration, shorter braking distance and better vehicle handling.
Furthermore, less un-sprung mass means improved grip between the tyre and road thus ensuring excellent road holding characteristics.
A further key benefit of the Bucci Composites wheel is the hub-wheel coupling system which allows the wheel to be fixed to the hub in the traditional way, eliminating the risk of wheel bolt torque loss. This assembly system provides all the advantages of a conventional wheel fixing system but with the significant added weight reduction.
The carbon fibre rim has undergone rigorous testing as part of this process and Bucci Composites is the only manufacturer globally to have passed the new TUV standard (German testing body for the certification of automotive components) for non-metallic rims, a standard that was not in existence when the project started.
Bucci Composites has also invested in new innovative production technology (High Pressure RTM – HP-RTM), which will enable them to continue developing new carbon fibre wheel models for the automotive sector.
www.bucci-composites.com
Lambo goes retro with hybridised, carbon fibre-intensive LPI 800-4 supercar
ASK any automotive designer about classic vehicle designs and you’re likely to hear ‘Lamborghini Countach’, a vehicle that rolled out of Sant’Agata Bolognese, Italy in 1974 and had iterations until 1990.
As the Italian builder of supersport cars transitions to an electric future, it is paying tribute to the Countach with the LPI 800-4, which has a hybridised 6.5-litre V12 with a system output of 802 horsepower.
And to make the four-wheel-drive car light for high performance, the engineers went carbon fibre intensive.
The LPI 800-4 features a carbon fibre monocoque with aluminium front and rear frames. All of the exterior body panels – hood, doors, quarter panels, etc – are carbon fibre, with the exception of the roof, which is a photochromatic material that changes from solid to transparent with a pushbutton.
The front splitter, wind surrounds, side mirror caps, engine cover air intakes, rocker panels and rear splitter are also carbon fibre. Even the brakes are carbon fibre ceramic discs with aluminum calipers.
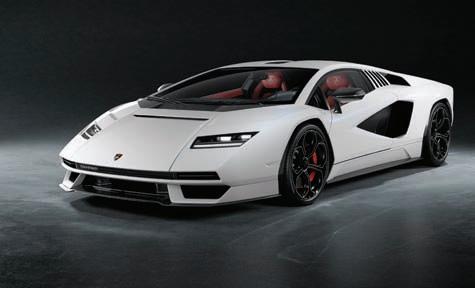
YCOM composite all-electric race scooter
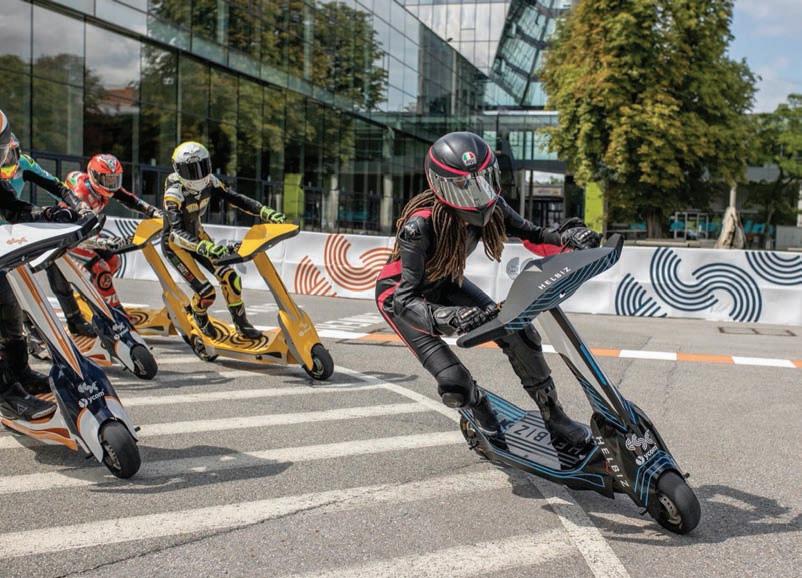
YCOM (Stradella, Lombardy, Italy), a company that specialises in motorsports engineering and lightweight composite design, has completed the official delivery and testing of its high-performance composite S1-X eSkootr for the eSkootr Championship (eSC), a new racing series that highlights e-mobility and frontier innovation. Supplied to all eSC competitors, the S1-X Skootr is YCOM’s first full-electric vehicle and can reach speeds of up to 100 kilometres per hour.
With expertise in designing and manufacturing technology for motorsport – including Formula 1 and FIA World Endurance Championship winners – as well as experience in the launch of multiple new race series, YCOM says it was well-positioned to develop, build and supply eSkootrs to the eSC.
YCOM’s agile approach also enabled it to accelerate the S1-X’s development, taking the initial prototype to a productionready design within less than four months. Not only that, but 10 race-ready eSkootrs have been delivered, YCOM notes, just five months after the partnership with eSC began.
In a collective test with 16 different riders, the S1-X was initially limited to 40% power, increasing to 70% by the end of testing. Even at this output, YCOM says, many riders were fatigued by the physical demands of such speeds and lean angles of up to 55°. With improved physical conditioning and additional practice in October testing, it is hoped that the riders will be able to use 100% power as well as the additional 20% temporary boost function in the first race.
Formed in 2020, the eSC is the world’s first micromobility racing series. Following exhibition events in 2021, its opening season in 2022 will see fierce racing between 30 competitors on specially designed circuits from 400 to 800 metres long. Intended to raise awareness of e-mobility and promote the rapid advancement of sustainable transportation solutions, the eSC marks a new chapter in motorsport history.
Raising the bar for protective performance with ultra-light Formula E racing suit
TEIJIN Aramid has helped engineer a new protective motor racing suit that will be worn for the first time at the Berlin Formula E ‘E-Prix’. The ultra-light suit harnesses the superior protective qualities of Teijinconex neo for professional motor racing.
Based on Teijinconex neo fibres, the professional racing suit is the latest product to emerge from Teijin Aramid’s longstanding collaboration with OMP Racing, a market-leading producer of premium motorsport safety equipment. The new suit has been custom-made for Envision Virgin Racing, one of 12 teams competing in the Formula E World Championship, the world’s premier electric racing competition.
The suit contains innovative features designed to maximize both the safety and comfort of drivers during competition. The outer layer of the garment consists of an ultra-light fabric made with Teijinconex®, resists temperatures of up to 400°C and does not burn or melt when exposed to extreme heat. Because of these superior protective qualities, the suit contains just two layers, one less than most standard racing suits. This allows the wearer greater flexibility and a more tailored, comfortable fit. The suit is also up to 10% lighter than the previous racing wear worn by the Envision Virgin Racing Formula E Team, further enabling the movement and performance of drivers.
OCT / NOV 2021 41
