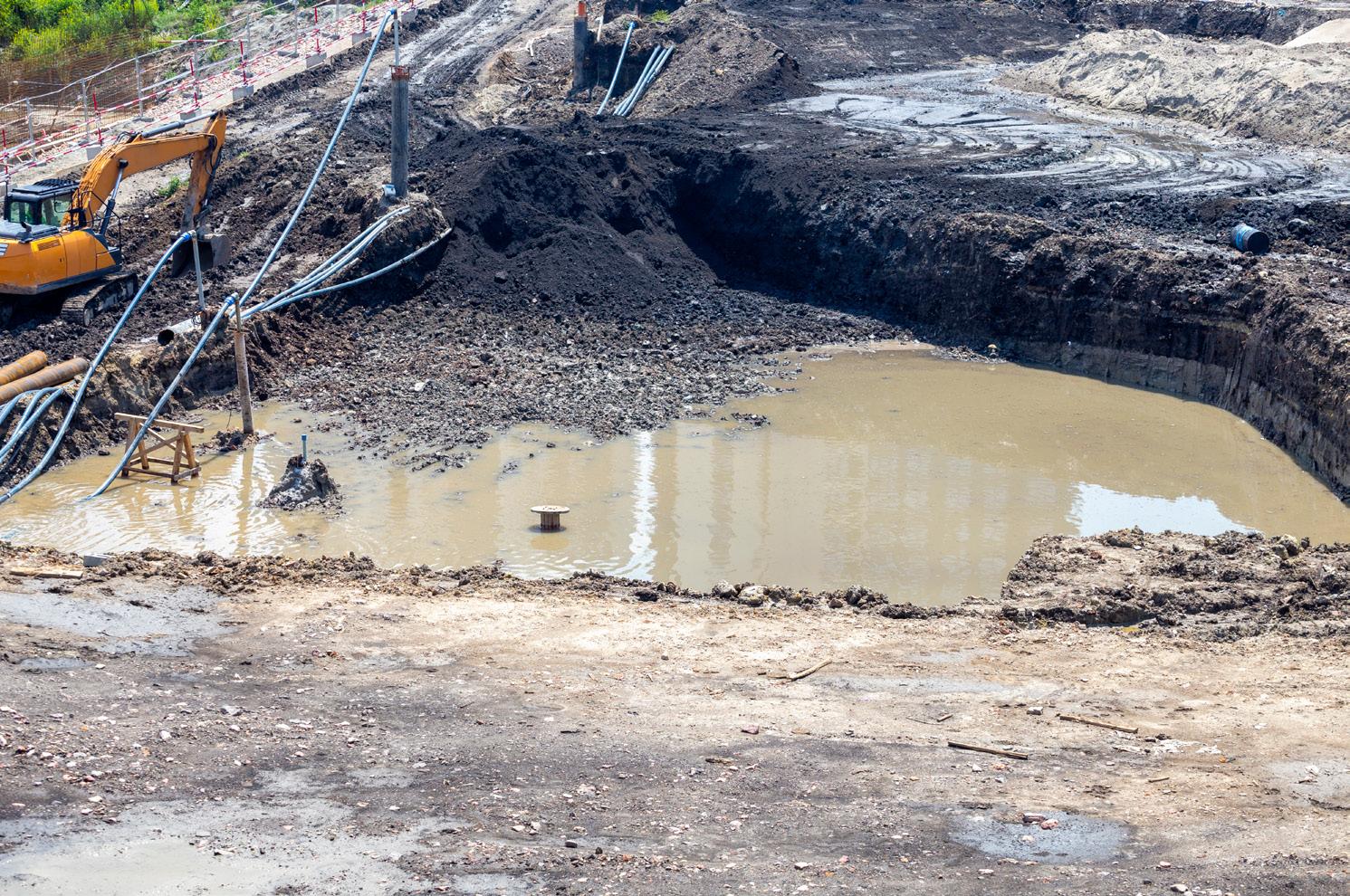
4 minute read
Selecting the right dewatering pump
Suzanne Gill finds out what needs to be considered to help identify the right dewatering pump for an application.
At some point in their operational lives, mines and quarries will certainly need a dewatering pump. With construction managers and engineers increasingly coming under pressure to improve efficiencies across their sites, the correct choice of dewatering pump can contribute by offering both cost and efficiency benefits.
Hrishikesh Kulkarni, Product Marketing Manager, Pumps, at Atlas Copco Power and Flow, says that the first consideration should be the nature of the liquid being pumped as this will have a significant impact on the type of pump needed. “Important factors to consider include general composition, the concentration and size of suspended particles, as well as the liquid’s pH level, temperature, and chemical content,” he said. “Consider, for example, whether the water will contain fine particles or a much thicker fluid, and how aggressive the media might be.”

Where high concentrations of solids are present, Hrishikesh advises using slurry pumps, as they are designed to handle corrosive and abrasive media. “If the liquid is particularly aggressive, ensure the pump is robust and designed with protection features such as hardened, clog-free impellers, and wearresistance,” he said.
According to Hrishikesh, one of the most critical performance considerations relating to a dewatering pump will be the flow requirement – how much liquid needs to be moved and how quickly? For example, a pump with a maximum flow rate of 138m 3 /hr might remove water from a pool that is 36m 3 in 15 minutes, while a pump with a flow rate of 350m 3 /hr would empty the pool in just six minutes.
For the best value and efficiencies, the pump selected should handle the flow requirements with enough capacity to cope with fluctuations in water level. A pump that is over-specified and can handle a much higher flow capacity will be more costly and will not provide the most cost-effective solution. On the other hand, a pump that has been under-specified will struggle to transport the media and is likely to wear out more quickly, resulting in a shorter life span.
The height to which the fluid needs to be pumped and how far it needs to travel are other considerations that will impact the pressure that the pump needs to deliver to ensure it can pump efficiently and reliably. The greater the distance the water needs to be pumped, the more friction is created, which results in pressure loss from the pump. Pumps need to overcome gravity resistance as well as friction losses.
Hrishikesh advises that if the suction lift required for dewatering with a surface pump is more than around 7m, a submersible pump should be considered. “These units are designed to be totally submerged, using the proximity and pressure of the surrounding water to aid fluid movement through the hose, which means that less energy is needed to move the water,” he said.
UNDERSTANDING NPSH
Weir Minerals has highlighted the importance of understanding net positive suction head (NPSH). The available NPSH (NPSHa) is the static pressure available in a system to force the water into the pump. This, says the company, will largely determine which model within a style of pump is suitable for an application.
NPSH can be affected by several variables, including the static differentiation between a pump’s suction and the water level, the length of the suction pipeline and the pump’s elevation above sea level. Other factors, including temperature and specific gravity, play a role.
Every pump will have a minimum NPSH requirement to ensure continuous flow, which depends on its operating duty point. So the net positive suction head available (NPSHa) needs to be compared to the net positive suction head required (NPSHr) to select a dewatering pump.
NPSHa must always be more than NPSHr – typically with a 1-1.5m safety margin to prevent suction cavitation, advises Weir Minerals.
POWERING YOUR PUMP
If mains electricity is available, electric pumps are considered to offer the best and most efficient choice. Electric submersible pumps are considered by many to be the simplest, most energy-efficient and economical approach.
If the site is remote and prone to a fluctuating mains supply, consider a pump whose motor and starter are equipped with inbuilt electrical protection against varying voltage, phase failure and human error.
Diesel is used mainly in mobile dewatering pumps, such as those operating at the bottom of a mine pit, which require frequent relocation alongside the mine’s sumps as the mine develops. In such applications, a manually primedcentrifugal pump would result in a timeconsuming exercise each time it was moved – the advice here would be to look closely at the benefits that self-priming pumps can offer.
CONCLUSION
When specifying dewatering pumps, do give careful consideration to the liquid being pumped, together with the physical demands of the application – such as flow, elevation and distance the fluid travels. Selecting the most appropriate pump for the task will go a long way towards helping engineers meet the efficiency and productivity demands that are increasingly being placed on them.