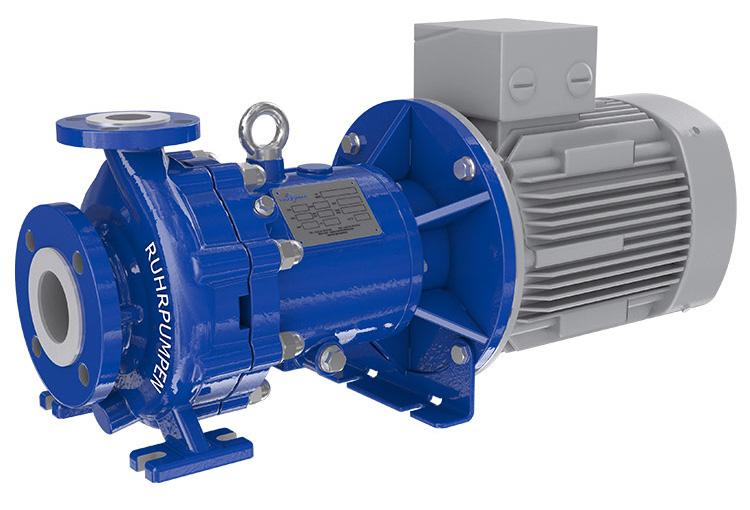
2 minute read
Q&A
In this issue of flow, Shaun Hampson, Vice President of RuhrpPumpen Industrial Europa, answers readers’ pump related questions.
QUESTION: With today’s modern technology, am I best moving to seal-less magnetic drive technology instead of mechanical seals?
SHAUN HAMPSON: A simple answer would be ‘yes’ because of the benefits of safeguarding leakage and emissions with a magnetic drive. When it is important to safeguard the escape of toxic/corrosive/ explosive media, then sealless technology removes the risks of leakage associated with mechanical seal failure and vapour/gas passing the seal faces to the environment. As with single mechanically sealed pumps, magnetic drive machines also need to be protected from dry running and entrained solids controlled. Compared with simple mechanically sealed pumps, the sealless magnetic drive option is generally more expensive. However, costs are balanced firstly when double mechanically sealed Plan 52/53 systems are being employed and secondly when the environmental impact cost would be high. Higher-end magnetic drive pumps also offer ‘double containment’ that seeks to prevent escape even in the event of sealing failure.

QUESTION: What is the simplest way to improve pump efficiency in an old(er) existing continuous process-production facility?
SHAUN HAMPSON: First of all, you should check that the pump is running at its best efficiency point. If the pump duty is to the left of its best efficiency point, because the process requires less flow, then consider trimming the impeller to match the flow & head demand. If the duty is to the right of its best efficiency point, then the pump manufacturer may have a larger impeller to fit with the existing machine and motor. If these options are not possible, or the process is batch/ fluctuating production, then maybe best to install a variable frequency drive. This will, at least, get the best match and power absorbed.
QUESTION: What is the best way to minimise escape of VOC’s to the atmosphere when being pumped?.
SHAUN HAMPSON: Other than opting for gravity feed systems, the main three solutions are:
1. Install seal-less pump technology like a magnetic drive pump with optional secondary control. The secondary control offers protection in the event of containment shell failure.
2. Install canned-motor pump technology.
3. Use double-acting mechanical seals and associated thermosyphon systems.
Generally, the first and second options would be used for cleaner liquids, while the third, with a Plan 53 system, offers protection while pumping liquids with entrained solids.