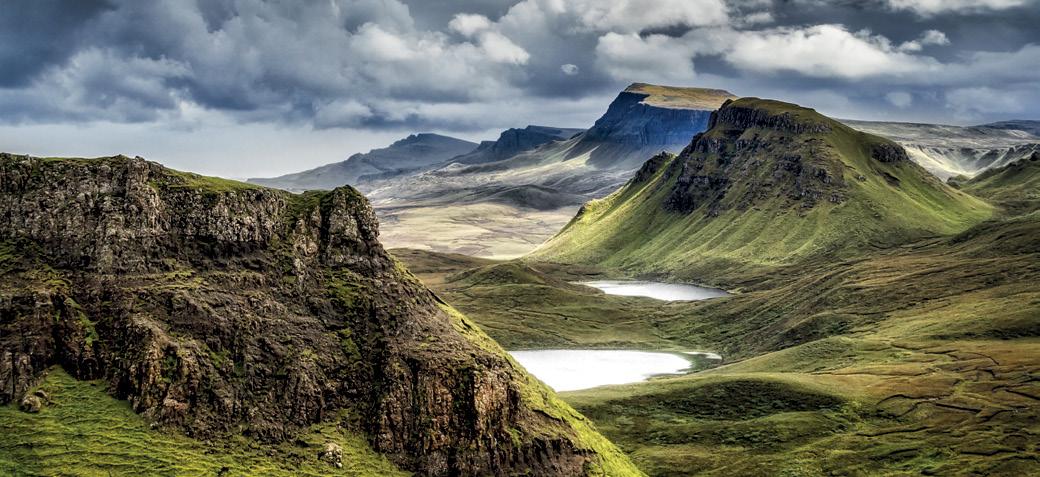
3 minute read
Pump Repairs
failures, and assessing current and future requirements and worn components, companies like Celeros FT that re-engineer parts can provide recommendations for mechanical and material improvements.
For example, rotor dynamics can be optimised to increase asset reliability. This could include improvements to shaft stiffness and wear ring geometry and the addition of swirl brakes.
The materials used for re-engineered parts can include increased corrosion and erosion resistance, which can extend service life and mean time between failure. Or hardened running surfaces can reduce wear and maintain efficiencies for longer, while modern composite materials can mitigate failures.
Bearing life can be extended with an engineering review of current bearing arrangements, appropriate guarding on housings, water in oil monitoring, and using composite materials for line shaft bearings.
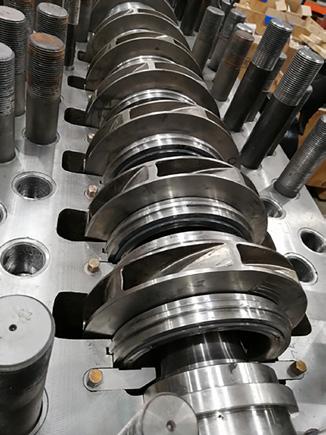
Emission leakage can also be improved with upgrades from gland packing to mechanical seals and from component to cartridge seal assemblies.
RE-RATED PARTS
What if changes to operational performance are desired but have not yet been implemented due to concerns regarding feasibility and any impact on a pump’s health and performance?
Equipment efficiency can be improved to reduce running costs. Material enhancements, particularly of wear parts, can allow tighter running clearances, reducing recirculation losses while hydraulic surfaces can have efficiency coatings applied, reducing friction losses.
A pump’s performance can be aligned to system characteristics to establish the best efficiency point and optimise the reliability curve.
Output can be reduced to suit system or process changes. This may require the rotor to be de-staged or the impeller diameter reduced, or it could also include implementing a variable frequency drive. Similarly, the output can be increased. In either case, a detailed analysis of the impact on the motor and other drive train equipment would be undertaken.
A Rapid And Robust Process
For Celeros FT, the re-engineering process begins with a customer consultation to review the equipment details, operational issues, and performance to determine potential solutions.
Next, laser scanning is used to obtain data on the existing components – not just the parts intended to be replaced, but also mating parts.
Component materials are then analysed to assess potential upgrades and ensure the compatibility of existing and replacement parts.
The data captured at this stage is stored for future reference when there is a demand to supply a part. This methodology facilitates scanning parts when they are available for future requirements.
Based on analysis of all the available data, new components are designed, material grades specified, and manufacturing quality plans are generated. 3D models are created to facilitate CADCAM and additive manufacturing for casting purposes. Computational fluid dynamics and finite element analysis benchmark and validate designs.
Finally, parts are manufactured to stringent quality requirements, rotating components are balanced to applicable grades, pressure-containing parts are hydrotested, and parts are QA/ QC approved before being shipped or incorporated into an overhaul at a Celeros FT Service Centre.
Adding Value
One example where re-engineering added value to a customer of Celeros TF was a UK Oil & Gas operator that required a solution when its (2.5 MW) 12-stage BB3 sea water injection pump failed in service.
The customer consultation defined that the pump, providing seawater injection duty to support field production, required a solution which increased the mean time between failure and optimised its performance.
Celeros FT worked with the customer to improve critical features within the pump, including upgrading the mechanical seals and modifying the existing bearing housings to allow for the provision of bearing isolators.
During a strip inspection, several impellers were shown to be damaged beyond repair. Even with the extensive damage, Celeros FT could re-engineer the hydraulic components appropriately.
Damage to the rotating assembly had resulted in areas within the stationary components that needed repair. The large and heavy top and bottom half pump casings were repaired and machined back to the design intent, re-inspected and hydrotested to the project duty requirements.
3D models of the pump casings were then used as the basis for the mechanical layout. Given the large number of stages, a thorough assessment needed to be completed to ensure full mechanical integration between the mating components, especially when both existing and re-engineered parts were being used.
The shaft was re-engineered and upgraded, and a full rotor dynamic assessment of the pump unit, including a lateral critical speed analysis in accordance with API 610 Latest Edition, was completed.
This assessment, coupled with an in-house performance test at full speed (4000rpm), pressure (>2000m head) and power, gave the customer confidence that the re-engineered and upgraded pump would perform as required.
Conclusion
To ensure critical flow equipment is working to its best, operators need to consistently evaluate equipment behaviour and act quickly to rectify any problems. Reengineering can provide the appropriate engineered solution to overhaul, upgrade, renew or replace older legacy equipment, optimise operation, and simplify spare parts management – irrespective of pump brand – to minimise downtime, reduce total cost of ownership and save the expense and disruption of having to install new systems throughout a plant. chevron-circle-right www.celerosft.com
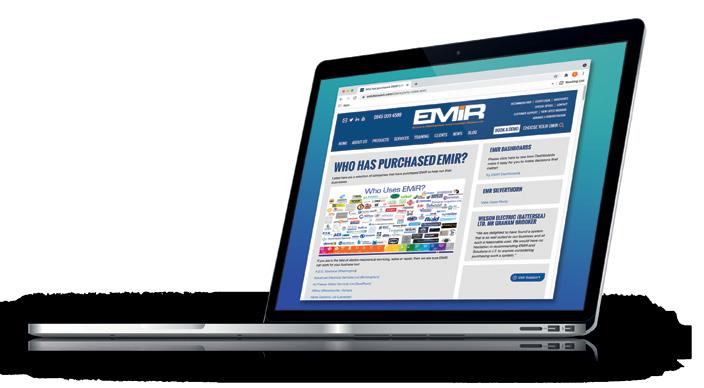