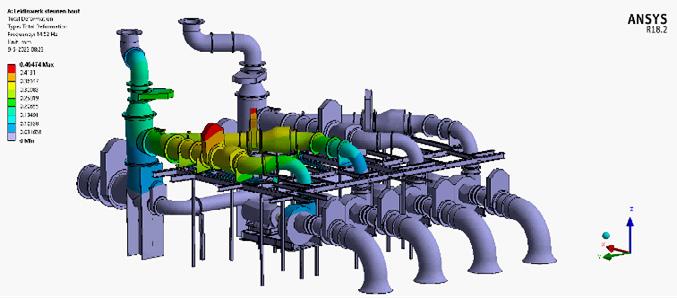
2 minute read
Vibration modelling eliminates Pumping Station’s Critical Resonance Frequencies
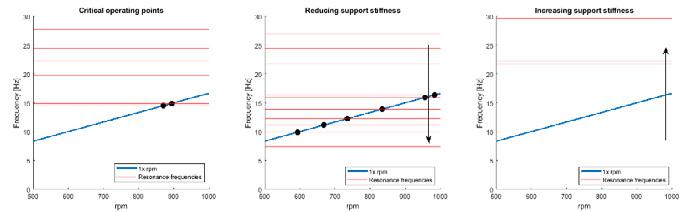
Asset reliability specialist Van Geffen Reliability, which is part of the AES Reliability Group, explains how it used Finite Element Analysis to predict the vibration behaviour of a large sewage pumping station, using the results to optimise the design to reduce the potential for damage to the system once in operation.
Finite Element Analysis (FEA) uses mathematical models to understand and quantify the effects of real-world conditions on an asset.
FEA can be used to model a modification to an existing asset or for a newly developed asset design and is an essential tool when design functionality is absolutely critical.
The analysis carried out on a pumping station design included a numerical modal analysis and harmonic response simulations to predict the vibration behaviour of the pumping station.
A numerical modal analysis is a technique used to determine the mode shapes (vibration patterns) and resonance frequencies of structures and systems. This is done through FEA calculations to simulate and analyse the dynamic behaviour of structures. In numerical modal analysis, the ‘free vibration mode’ is calculated, meaning no external forces are applied to the system.
When carrying out an analysis of the sewage pumping station, in the operating range of the pumps (1x speed range of 5001000 rpm) two critical resonance frequencies were calculated, which will be excited by the first order vibrations of the pumps. These are shown as the two black dots in Figure 1.
A harmonic response simulation is an analysis of the response of a system or structure to an excitation force with a constant frequency. This simulation is used to determine the vibration amplitude and sensitivity to different resonance frequencies, providing insight into preventing harmful vibrations and improving the overall design. A model of this can be seen in Figure 2.
In the operating range of the pumps (1x speed range of 500-1000 rpm) the following load cases were calculated:
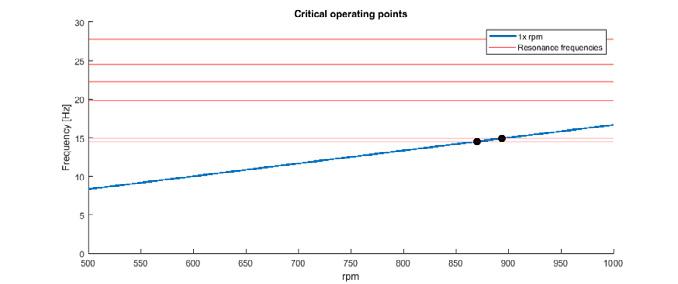
• Imbalance force on all five pumps: equivalent to balance grade 6.3.
• Pressure pulsation on the piping: 1% to 5% of operating point 4 (24.5 mwk = 0.245 MPa Long-Arrow-Alt-Right 0.003 and 0.015 MPa).
A response of 17.8 mm/sec RMS is calculated, which implies a pipework vibration concern factor of 3.0.
THE SOLUTION
To prevent high vibrations, the starting point is to have no resonance frequencies of the main piping system in the operating range of the pumps (1x rpm). The resonance frequencies that have been calculated can be shifted by adjusting the support stiffness. Reducing stiffness will lower the resonance frequencies but risks lowering the current resonance frequencies below the operating range and into the operating range of the pumps. Increasing stiffness will raise the resonance frequencies, with the goal of placing all (main) resonance frequencies of the installation above the operating range of the pumps. chevron-circle-right vgreliability.com
Unbeatable energy efficiency with SynRM motors and drives.
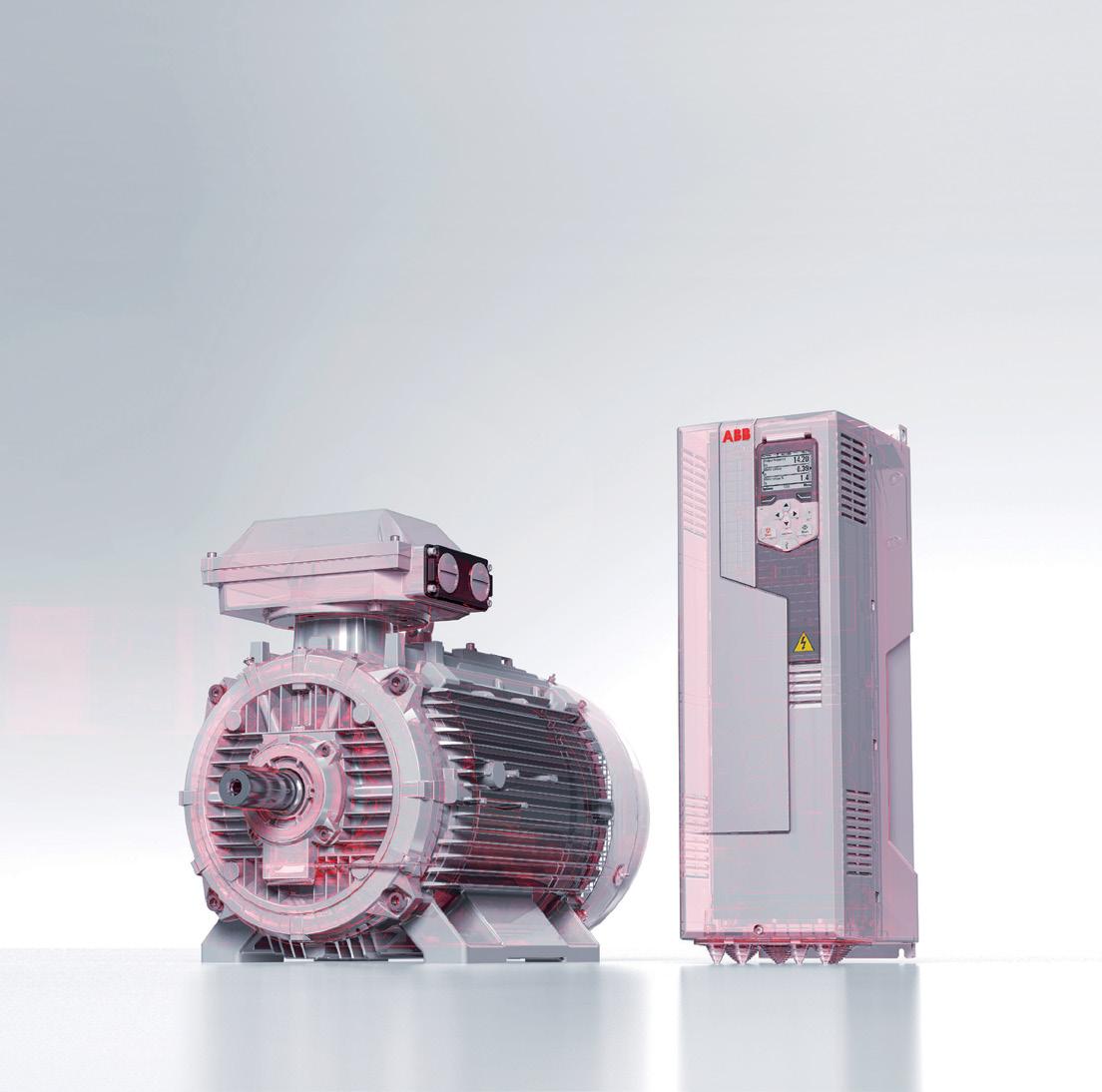
Safe, smart and sustainable solutions across the water cycle.
If you’re looking for world-leading efficiency, ABB has the perfect motor and drive combination for water and wastewater applications, helping you to save energy, spend less and produce more.
To find out more, search for “ABB IE5 SynRM”