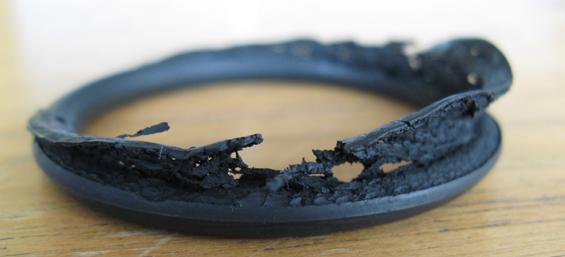
2 minute read
Q&A
In this issue of flow, Philip Clarke, Managing Director of Polymeric Material Failure Consultants, answers readers’ questions related to O-ring failures.
QUESTION: Body to adapter O-ring seals, removed from a gas export line ball valve, show widespread through thickness fracture damage that aligns with the direction of squeeze and yet the valve showed no leakage prior to shut down. Why would this be the case?
PHILIP CLARK: Surprisingly it is often the case that elastomeric sealing components can continue to function effectively despite the presence of considerable material damage (extrusion, RGD, compression set, thermal/chemical ageing). The O-ring damage that you describe is likely to be due to rapid gas decompression (RGD) where high pressure gas absorbed by the seal cannot escape sufficiently quickly when system pressure is reduced, the expanding trapped gas causing internal fracture damage. The phenomenon is often seen as concentric oval fracture features on blisters when opened.
Seal damage can often remain hidden while operating conditions remain static. When temperature, pressure or mechanical loading conditions change during maintenance activities or unintentional plant stoppage, the seal that is no longer pressure energised is disturbed and then challenged when pressure is reapplied.
Steps that can be taken to mitigate the threat of RGD fracture damage in gas valves include careful material selection to match thermal and chemical compatibility requirements with high material tear strength. Optimising seal support using for example higher groove fill, reducing seal section diameter (where design allows) and control of rate and temperature of any controlled blow down event will all help.
QUESTION: How can material identification for O-rings from my used valve be verified against the design/service specification?
PHILIP CLARK: A range of techniques are used for elastomer compound ID. Simple quick measurement of density will help ID generic compound type (e.g. nitriles typically being 1.2-1.3g/cm3 while fluoropolymers tend to be 1.8-1.9g/cm³). Solvent swell response can support initial indications from density with swell response for selected elastomer/solvent combinations being different (e.g. rapid high level swell of nitriles in aromatic hydrocarbon; variable swell of FKM grades in methanol). Air oven ageing can quickly distinguish between NBR and HNBR through subjective stiffness increase).
More complex analytical techniques, such as DSC and TGA, characterise glass transition temperature and thermal decomposition profile while FTIR will use fingerprint identification of chemical functional groups to indicate polymer type. These techniques and others can also be useful when studying material change from service use by comparing used seal condition with a known new reference.
QUESTION: Where seal failure occurs, what information will be required to support an independent failure investigation?
PHILIP CLARK: Seal failure investigation generally involves confirmation of elastomer material type, documentation and characterisation of damage features, gathering of supporting information from the operator with available evidence being bought together to propose a probable root cause.
Seal material condition alone is unlikely to reliably identify the cause of failure. Consideration of the associated engineering hardware and its function is also required.
Requirements from the end user for a typical study include: • Failed components ideally traceable to original location/orientation from planned documented disassembly. • Manufacturers material data sheets. • Unused reference seals. • Process operating conditions (temperature, pressure, fluid, duration). • Historical failure occurrence. • Failure scenario and consequences.
A rigorous investigation is an exercise that can require considerable input from the client to ensure that all possible influences on failure are included.