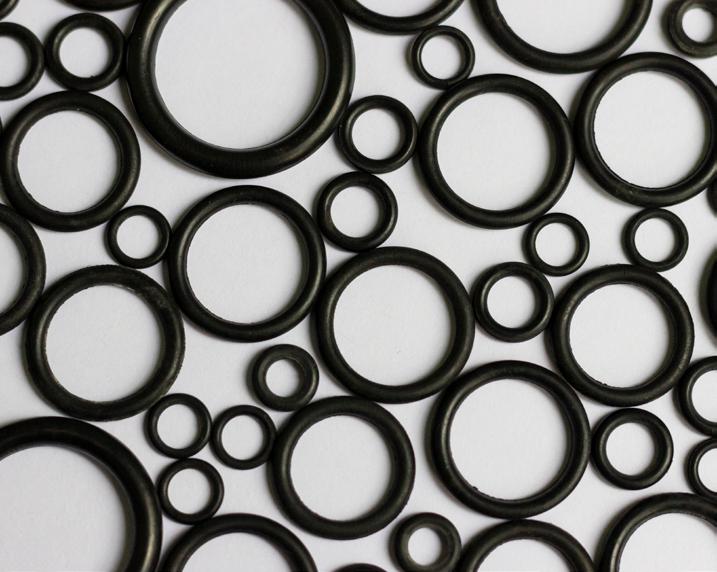
5 minute read
Choose the right O-ring
Selecting the correct O-ring for an application can be critical, but to achieve this many factors need to be considered. To help users make the right choice, fluid sealing product specialist, M Barnwell Services, looks at key aspects of an O-ring’s design.
Elastomers are different compared to any other material used by engineers. For example, plastic or metal components are most likely to be failing when they are visibly deformed. When it comes to an O-ring, for it to function correctly, it must be deformed. An O-ring that is not stretched and squeezed is the wrong O-ring for an application.
An O-ring is a doughnut-shaped article; a closed circle usually made of elastomeric rubber. The O-ring seal’s purpose is to prevent an unwanted leakage or loss of gas or fluid, and it is the most popular form of a seal.
The opposite faces of an O-ring are compressed between the faces of the gland. The consequent zero clearance within the gland guarantees an efficient seal, preventing the fluid or gas from flowing through the gland.
O-RING MANUFACTURING
There are two standard processes for the manufacture of rubber O-rings.
In the compression moulding process, the material is manually placed into a mould before the upper and lower parts of the mould are closed. This process is particularly suitable for larger dimensions and smaller quantities due to it being very time-consuming.
With the injection moulding process, the material is automatically injected into a mould (otherwise known as a tool), which has various O-ring cavities. Injection moulding is a process suitable for small dimensions and large quantities.
ELASTOMERS
Elastomers are polymers, which are described as large molecules (or macromolecules) formed of many sub units. In Greek, polymer means ‘many parts (poly, ‘many’ + mer, ‘parts’). The polymers are linked to each other to compose a network with cross-connections. Consequently, they demonstrate the typical elastic and rubbery features. The raw product is rubber and is either acquired from plants that produce the substance or developed synthetically.
A properly designed sealing system includes some level of initial O-ring squeeze.
When applied to an elastomer, vulcanisation leads to the formation of chemical crosslinks of polymer chains. This is to ensure that after the force is removed, the molecules return to their original shape. This is how an O-ring retains its shape; if it were stretched too much, it would cause the bonds to break.
HOW AN O-RING WORKS
A properly designed sealing system includes some level of initial O-ring squeeze. Only the elasticity of the squeezed O-ring ensures the seal at atmospheric pressure. Nevertheless, the O-ring is pressed against the low-pressure side of the gland as system stress activates the seal. The O-ring fills the diametrical clearance and prevents any additional leakage.
Pressure and many other considerations determine the efficiency of a seal.
DIMENSIONAL CONSIDERATIONS
An O-ring’s inside diameter (ID) must be smaller than the piston groove diameter to offer an efficient seal. This is because an O-ring needs to be slightly stretched so it closely fits the groove. The stretch mentioned above needs to be between 1–5%, with an ideal stretch of 2% in most installations. A stretch of more than 5% is not recommended; the consequent pressure on the seal will reduce the cross-section and contribute to early ageing. In installations where less friction is required and some leakage is allowed, O-rings can sit or ‘float’ in the grooves freely.
To calculate the cross-section (CS) of an O-ring, the size of the gland and the amount of compression must be considered to achieve an effective seal. Diametrical clearance is a gap between two mating surfaces of a gland. Practically all glands have diametrical clearance; therefore, an O-ring’s cross-section must be larger than the gland height. As a result, the compressed O-ring blocks the diametrical gap, consequently preventing leakage.

MATERIAL CONSIDERATIONS
Following the calculation of the correct O-ring size, the correct material must be chosen. Numerous elastomer materials are available with a wide variety of characteristics, including their chemical resistance, temperature suitability and material hardness. All of these factors must be considered before purchasing a seal, and a manufacturer or supplier should be able to advise on the best choice if required.
Resistance of particular rubbers to degradation by exposure to various chemicals is a major consideration for O-ring material selection. It is crucial to match the O-ring material with application chemicals to ensure the best resistance. This should be the first step when choosing an O-ring material.
The temperature range encountered throughout the process/operation must also be taken into account. Measuring temperature in the adjacent O-ring environment, rather than the system temperature, is especially important. Also, the duration of exposure to any high temperature must be considered, regardless of whether it entails short (intermittent) or long (constant) exposure.
Shore A hardness is a measurement of the hardness of a rubber element. The numerical measurements for Shore A hardness go from softer materials (lower-numbered, less than 70) to harder materials (highernumbered, greater than 70). For instance, the standard FKM/FPM (Fluoroelastomer) compound has a hardness of 75 Shore A. This grading technique is intended to operate in the range of ±5 points.
In dynamic (moving) installations, two types of friction can be observed. When experiencing breakout friction – the force needed to start a motion – the intermittent motion of the component can cause excessively high pressures; these pressures can tear sections of the seal that stick to the gland wall, consequently leading to seal failure.
With ongoing running friction, the constant motion of the component can lead to heat building up in the seal material. This results in swelling, which causes even more heat to build up and leads to extrusion and failure.
Different materials will react differently to friction, and so this should also be factored into the selection.
SUMMARY
Correct selection of an O-ring is a direct result of many design considerations to obtain optimal sealing performance. These involve size, compression, stretch, chemical compatibility, and resistance to pressure, temperature and friction. Frequently, various materials could be appropriate for a particular application, therefore it is important to consider a full selection of price and environmental factors. The ultimate choice will be a balance between all of the considerations mentioned above. Of course, if you are in any doubt, you should contact a reputable supplier for advice. chevron-