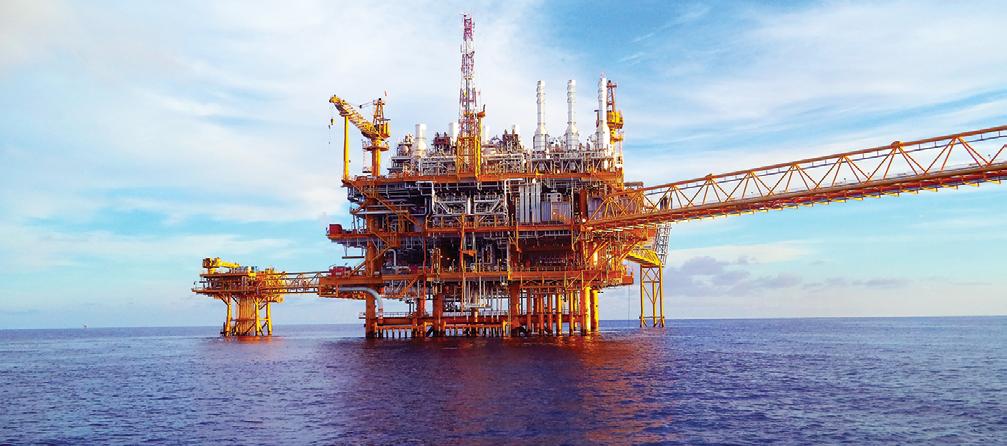
5 minute read
Reliable sealing for carbon capture
As oil and gas companies play their part in the race to meet global net-zero ambitions, an increasing number are working with Carbon Capture, Utilisation and Storage solutions. In this approach, sealing technology has a critical role, as John Crane explains.
According to the most recent report from the United Nation’s Intergovernmental Panel on Climate Change (IPCC), carbon dioxide (CO 2 ) is the main driver of climate change around the globe. In 2020, global CO 2 emissions were estimated by the International Energy Agency (IEA) at 33.4 Gt, and this is forecasted to increase in 2021 as global economies recover from the COVID-19 pandemic. To enable countries to meet their netzero ambitions following the Paris Climate Agreement, large-scale deployment of Carbon Capture, Utilisation and Storage (CCUS) technology and solutions are needed.
For decades, several oil and gas companies have implemented CCUS technology to trap greenhouse gas from natural gas operations, often as pilot or demonstration projects. The captured CO 2 can be compressed and reinjected into geological formations or used for enhanced oil recovery (EOR). However, since 2017, more than 30 CCUS facilities, most of which are large-scale in size, have been planned. Most of these projects are in the United States and Europe, with other projects underway in Australia, China, Korea, the Middle East and New Zealand – all with the potential of capturing more than 130 million tonnes of CO 2 annually.
To safely handle and transport CO 2 into EOR applications or underground storage, centrifugal compressors with non-contacting dry gas seals are typically used. However, as interest in CCUS increases, CO 2 applications face new challenges. Higher operating pressures, temperatures and faster rotational speeds result in increased seal leakage, underscoring how essential the correct sealing system is for successful equipment operation and energy efficiency.
As a result, oil and gas companies must consider several factors when choosing the right sealing system for turbomachinery in CO 2 applications. Selecting an appropriate sealing system will help reduce maintenance time, reduce energy consumption, lower total lifecycle costs and ensure peak performance.
Further, retrofitting CO 2 capture equipment, outlined in the following examples, can extend the lifespans of existing facilities, enhance associated infrastructure and supply chains, and significantly reduce CO 2 emissions.
AUSTRALIAN CCUS DESIGN A SUCCESS
A 2016 joint venture of international oil and gas companies began a CCUS initiative off the Australian coast to address international concerns about greenhouse gases. The 4 MTPA CO 2 injection project would capture CO2 from offshore gas fields and sequester it onshore more than one mile underground. Project engineers found that reliably capturing and storing the
CO 2 presented the greenfield project with considerable compressor sealing challenges, including handling supercritical fluids and volatile temperature and pressure conditions.
Partnering with a well-known compressor manufacturer, seal manufacturer John Crane presented recommendations to address the CCUS challenges, including three CO2 compressor trains – each train equipped with two compressor strings driven by an electric motor and two gearboxes. Four non contacting tandem gas seals per compressor were included in the recommendation to handle the supercritical fluid, as well as seal gas panels that included heating units and other support systems.
Proper seal design was critical. A seal failure could shut down the CO2 injection plant, possibly preventing the operation from meeting the greenhouse gas reduction goals promised to the Australian government. The project injects up to four million tonnes of CO2 each year, reducing greenhouse gas emissions by approximately 40% and contributing 4% to Australia’s carbon reduction target.
The three compressor trains were brought online in sequence – the first in 2019. The tandem gas seals were installed in the compressors by John Crane, and the site’s developers conducted the startup. Engineers from both the CO2 injection site and the compressor manufacturer were familiar with the spiral groove face pattern of the seals as well as their noncontacting design that has been a turbomachinery standard since the 1970s. The seals were built to handle the supercritical CO2 fluid and the high pressure and speeds of the process.
Site engineers expected a long mean time between repair (MTBR) from the seals — the mating and primary rings of seals eliminate wear by maintaining sealing gaps of approximately 5μm/0.0002in during dynamic operation.
Since 2019, when the first compressor train went into operation, there have been no seal failures or repairs on any of the three compressor trains. The LNG operation continues to operate without CO2 seal problems. The high reliability of the seals is helping the operation keep its 40% greenhouse gas emissions reduction commitment – more than 100 million tonnes over the life of the injection project.
FIRST CCUS GETS SEAL OVERHAUL
Operated by a multinational energy company, the world’s first offshore CCUS facility began sequestering CO2 in 1996. The North Sea operation captures and stores approximately one million tonnes of CO2 annually in a sandstone formation one kilometre beneath the ocean floor, using two compressors to pump CO2 into the formation.
Developed to reduce greenhouse gas emissions, the facility also helped the energy company use advanced recovery technology to extract natural gas from hardto-reach pockets. The centrifugal compressors operated at relatively low pressures and were equipped with tandem dry-gas seals.
For the next 16 years, the seals operated reliably and met the expectations of the CCUS managers. The non-contacting seals are designed with a patented spiral groove pattern, maintaining the same sealing gap between the mating and primary rings as the Australian example above.

During planned maintenance in 2012, the tandem seals were refurbished at a John Crane facility to ensure a prolonged working life. The facility was equipped with standardised testing, grooving and spin-test gas seal equipment readily available, including CO2 compression.
Since the overhaul in 2012, the seals have worked without failure or repair – a MTBR record of almost ten years. The seals’ 25-year reliability has helped the energy company sequester more than 25 million tonnes of CO2, the oil and gas platforms work at optimum levels, and the company has avoided millions in potential financial penalties.
CONCLUSION
Even though energy companies have performed enhanced oil recovery with carbon dioxide for decades, the oil and gas industry faces new supercritical CO2 application challenges. However, choosing the right seal technology or retrofitting existing CO2 capture equipment will help reduce maintenance time and costs and ensure peak operational performance.
By accounting for the unique sealing requirements and properties of CO2 at supercritical conditions, oil and gas companies can reliably use CCUS technology to trap millions of tonnes of CO2 from natural gas operations.