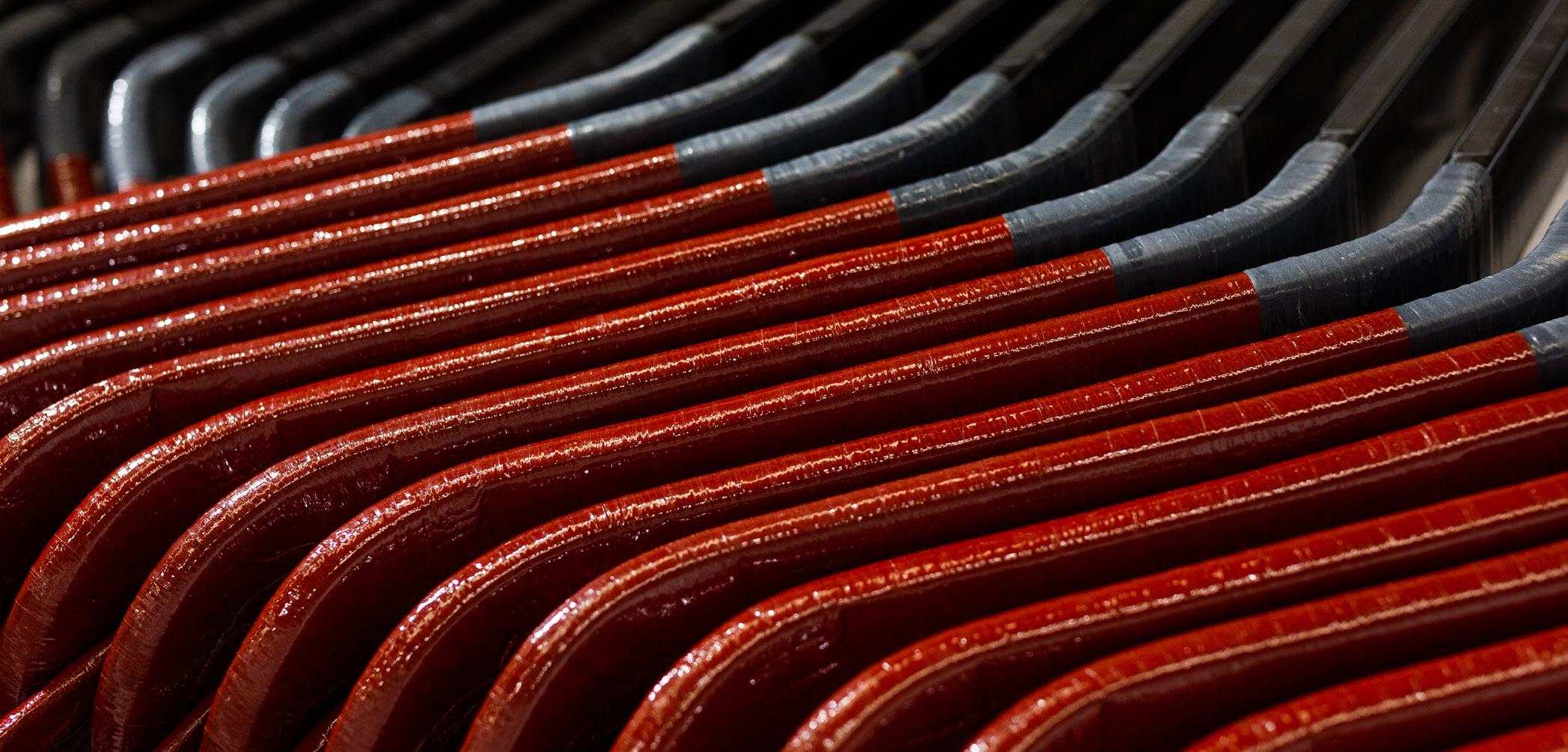
6 minute read
Coil Design
Reducing partial discharge in diamond coils
Preformed Windings, a specialist manufacturer of coils for motors and transformers, explains some of the key factors which go into manufacturing diamond coils which minimise the occurrence of partial discharge and offer longer asset life.
There is a growing awareness in the motor and generator repair industry that partial discharge (PD) levels play a significant role in the life expectancy of MV/HV assets. PD is defined as an electrical discharge occurring between two conducting electrodes without completely bridging the gap. It can significantly reduce asset life due to the energy caused by such discharges deteriorating insulation. The risk of PD occurring is increased considerably above 6kV, and therefore careful consideration should be given when designing and manufacturing components for these machines. Diamond coils should be designed with low PD in mind as this is an effective indicator of the quality and integrity of a coil’s insulation and, therefore, its life expectancy. Preformed Windings, based in Sheffield, UK, has been a thought leader in the manufacture of high-quality diamond coils for over 50 years and is very fortunate to work with leading OEM’s and independent repair facilities across the globe in industries such as hydro, nuclear and oil and gas. In these industries and many others, it is critical to have machines operating reliably even as is often the case, they are expected to last significantly longer than the original design life of the machine.
Due to its global presence along with close relationships with the Association of Electrical and Mechanical Trades (AEMT), The Electrical Apparatus
Service Association (EASA), leading insulation manufacturers, repair facilities and PD monitoring companies, Preformed Windings has been approached by several leading OEM’s to carry out significantR&D projects over the past few years, with a focus on reducing PD levels in windings. This research and development has allowed Preformed Windings to assist end-users and repair companies alike to clearly define specifications that reduce PD levels in assets providing the benefit of reduced maintenance costs and long-term reliability.
PARTIAL DISCHARGE IN COILS
There are many quality control considerations when designing and manufacturing diamond coils, but for this introduction, the focus is on the reduction or elimination of voids within coils. Reducing voids or cavities in diamond coils significantly improves PD results. Strictly controlled manufacturing processes allow for significant reduction, or even elimination, of the voids typically found in locations such as between conductors and the mainwall or turn insulation, within the mainwall insulation itself, or between the coils and the stator.
Voids within coils can be eliminated or significantly reduced if they are manufactured with precision and using high-quality materials. Also, attention needs to be paid to proper fitting, and an initial design with a long service life in mind, to avoid voids being introduced during operation from issues such as insulation delaminating due to thermal or electrical stresses. High quality manufacturing of coils, a trusted repair company and extensive testing such as waveform, corona camera, thermal cycle, voltage endurance and tan delta then all become key.
MANUFACTURING CONSIDERATIONS
When manufacturing diamond coils with low PD levels in mind, sourcing only the highest quality materials is always the starting point, along with the correct handling and storage of materials. Careful consideration should then be made at every stage of coil design and manufacture. For example, due to insulation tape being applied under tension, it is vital to ensure that all conductors are parallel to avoid introducing voids between the conductors and the insulation. Therefore, from the first manufacturing stage, which is looping, careful control of back tension of the copper, lay of the conductors, and careful application of turn tape is critical.
“We are often asked why we apply turn tape in-house and why we do not apply mainwall insulation while the coil is a loop rather than after we have shaped the coil. The reason is simply that we want to control the overlap of the insulation very carefully and avoid introducing voids. If the mainwall insulation is applied before shaping, then at every bend the overlap of the insulation is reduced on the outside face of the bend and on the inside, there is a tendency for the insulation to ripple under compression. In high-stress areas, such as the first bend at the end of the slot portions, this would result in undesirable void content and PD levels,” said Martyn Widdowson, Technical Manager at Preformed Windings.
Another key part of high-quality resin-rich coil manufacture is the final pressing stage, where the insulation and resin are pressed into a homogenous mass using the careful application of pressure and heat. Carrying out this final press stage in a factory environment allows extremely tight tolerances and exceptionally low PD results to be achieved.
Les Guthrie, Production Manager at Preformed Windings, explained: “A common question is how long should the final pressing take,? Many coil manufacturers simply press for a standard time for all coils regardless of coil size, number of layers of insulation or thermal mass. Additionally, manufacturers often make the mistake of inserting coils into the press while the press is at curing temperature, which causes the surface to cure very quickly and without allowing air bubbles to escape. Unfortunately, there is no simple answer to this question as to achieve the lowest PD levels, trials of the pressing process must be carried out to ensure that the temperature of the resin is consistent and correct throughout the coil allowing for the correct viscosity to be achieved, and the excess resin to flow from the coil without removing valuable insulation and introducing air bubbles.”
The careful application of high-quality insulation and the subsequent careful shaping and pressing processes ensures that the insulation is void and ripple-free and is less susceptible to delamination. Without this approach, the voids, ripples and delamination would rapidly reduce the life of coils as identified through an extensive thermal cycle and voltage endurance testing with PD testing before and after. Danny Fox, Managing Director at Preformed Windings, said: “It is our experience that carefully manufactured low PD coils can not only survive the rigours of the thermal cycle and voltage endurance testing but also then pass all standard electrical tests while still returning results mirroring a brand-new coil.”
THE FUTURE
Currently, there is a hunger in the HV repair market for low PD coils, but there is a lack of clear specification or guide to best practices. For this reason, Preformed Windings continues to work with well-respected partners to carry out extensive R&D activity related to reducing PD in coils and rewound stators.
James Stevens, Global Sales and Marketing Director at Preformed Windings, said: “Preformed Windings is well positioned and willing to help end-users and repair companies alike to raise the expectation of service life in rotating electrical machinery by sharing knowledge and expertise. We have successfully developed low PD coils that have been extensively tested both internally and independently, exceeding industry standard tests such as thermal cycle and voltage endurance many times. As a result, it is now possible to have much longer warranties such as five or ten years with confidence that the machines will run consistently and efficiently.”