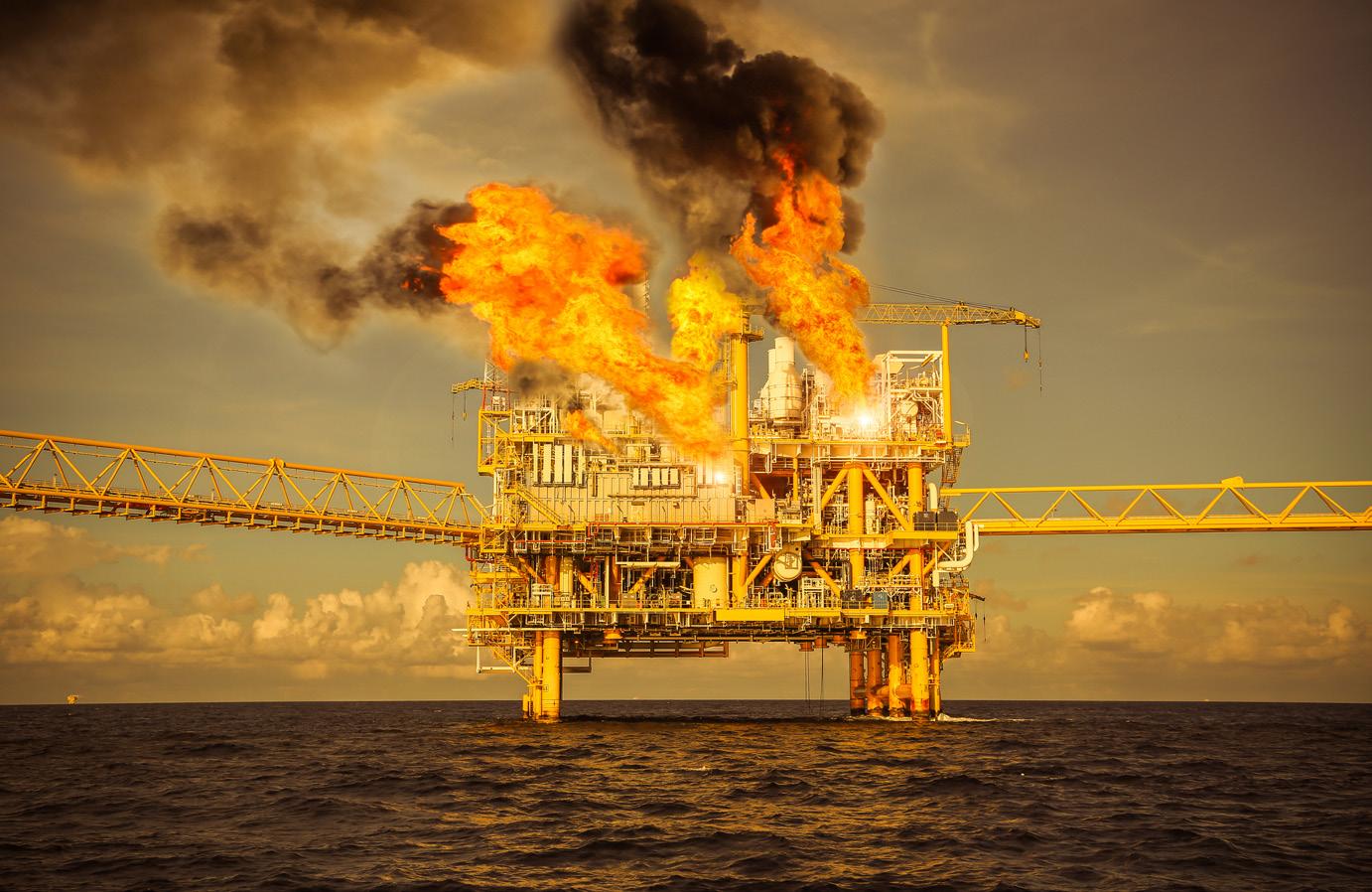
4 minute read
Hazardous Areas
Are you documenting Ex repairs?
Wherever there are gaseous atmospheres and dust, there is the potential for explosions with disastrous results. It is easy to see why legislation relating to hazardous areas and ensuring it is followed is important. When repairing electromechanical equipment used in hazardous areas, correct documentation is key to demonstrating compliance, and in turn, safety, as Karl Metcalfe, Technical Support at the AEMT, explains.
The responsibility for ensuring compliance and safety in hazardous environments sits squarely with the user of the equipment.This means that if you commission the repair of Ex rated equipment, the responsibility for ensuring the repair maintains the equipment’s compliance with the ATEX directive is yours. The AEMT Ex Register is a list of AEMT members who have met the requirements to be listed as an Ex registered member with the expertise and ability to repair hazardous area Ex equipment, but ensuring they do is the user’s responsibility.
The situation can be likened to repairing a car. A garage will fix it, but you are still responsible for that car being roadworthy when you drive it afterwards. The garage will give you a piece of paperwork to say what has been done, and you will keep that piece of paper as a record of that work. Looking after Ex equipment is relatively similar, if somewhat more involved.
The Ex repair standard (BS EN IEC 60079-19:2019), which has been developed to ensure the safe repair, maintenance and overhaul of equipment used in hazardous areas, states that: “The user is the organisation or person which is the owner, or operator, of the equipment, and they are primarily responsible for repairing it; not the equipment manufacturer or repairer”. It also says: “The user should consider whether sufficient facilities and competencies are available to undertake the repair or overhaul of such equipment by the user or whether it should be contracted to specialist repair and overhaul service providers”.
In situations where equipment is to be repaired by a specialist service provider, the standard goes on to state that: “The user has to ascertain that the service facility concerned can demonstrate compliance with the relevant stipulations of this document [the standard] and any regulatory requirements”.
If you don’t ask the repairer for evidence that their practices and the work they have carried out meet required standards, they do not have to give that to you. But it remains your responsibility that the item you have had repaired is still safe for use. If an incident happens, you will have to explain why you have fitted a piece of equipment in a hazardous environment without knowing the specification of that piece of equipment.
In addition, it is the user’s responsibility to be aware of any relevant legislation regarding periodic inspection and verification to ensure equipment remains fit for purpose. Plus, the user should be aware that sufficient information must be provided to third-party service facilities and installers to meet occupational health and safety obligations.
DOCUMENTATION
To meet these requirements, the user and repairer should work together, and the documentation of all stages of a repair is essential. The service facility needs to assess the equipment’s status and agree on the expected status of the equipment after repair and the scope of work with the user. This should be done in writing so that if there is a problem at a later date, there is a paper trail to evidence the circumstances – something which can protect both the user and the repairer.
The service facility should also ask the user to provide all necessary information and data related to the equipment being repaired, including previous repairs, overhauls, or modifications. To do this, the user must gather and keep this information when previous repairs have been carried out.
After a repair, the user should be given written details of all the faults detected, full details of the repair or overhaul, a list of replaced or reclaimed parts, plus the results of all checks and tests. And this information should be in sufficient detail to be useful to the next repairer.
In addition, a copy of the user contract or order, along with a comparison of the results against the criteria that have been used to determine compliance, and a recapitulation of the marking applied should also be kept.
The repair standard says that the service facility must keep all documentation, including any drawings, electrical and mechanical measurements and readings, and all agreements in writing between the user and repairer for ten years. The equipment user should do so as well.
A repairer listed on the AEMT Ex repair register will have been assessed as meeting the requirements needed to repair hazardous area Ex equipment, so this is an excellent place to start when a repair is required. But any end-users needing guidance on safely repairing Ex equipment can also contact the AEMT directly.