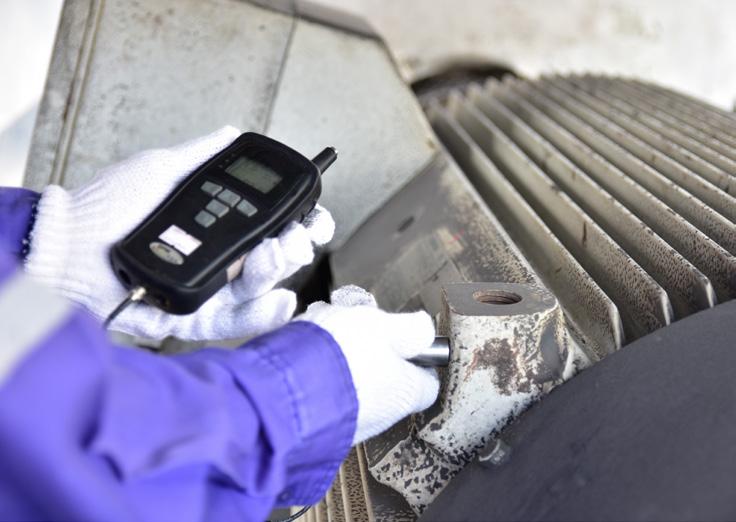
4 minute read
Tackle machine vibration and improve reliability
Wear and tear, unbalance, looseness and misalignment are the most commonly found vibration issues in machines. Timely detection of vibration can help avoid downtime and enhance the lifespan of machines. Machine reliability specialist, Reliability Maintenance Solutions, explains how precision balancing and alignment practices help minimise forces acting on a machine’s bearings and shaft seals, resulting in the improved reliability of these key components.
When looking at the causes of vibration problems, it is always necessary to distinguish between normal operations and emerging issues. Vibration can be symptomatic of a problem, or it can be the cause of a problem. There are times when the machine isn't physically vibrating, and there is a problem. In general, most systems are designed to avoid vibration as opposed to creating it. (Excluding shakers and screens, of course.)
Common Vibration Problems
Vibrating machinery, left unchecked, can speed up the deterioration rate of parts or cause damage to the system that may require key components of a machine to be replaced. There are quite a few reasons why machinery may start vibrating; here are the four most common causes.
Wear
When rotating components like roller or ball bearings, gears, or drive belts start to show signs of wear, the machine vibration patterns and levels change, mostly increasing in vibration.
For example, if a roller bearing race becomes pitted, the bearing rollers generate impacting and frictional vibration. This occurs as the rolling elements travel over the section of the pitted race. Other examples of wear causing vibration include a drive belt breaking down or a heavily worn or chipped gear tooth.
These both generate a different increase and pattern change in the vibration signature.
Unbalance
If a rotating component has what is known as a heavy spot, this can cause machine vibration, which increases exponentially with speed. Unbalance occurs when the shafts' geometric and mass centrelines do not coincide. The reason for this is because the heavy spot will force the mass centreline off the geometric centreline.
Unbalance can be caused by a few different things, such as:
• Maintenance issues: missing balance weights or dirty or deformed fan blades.
• Manufacturing defects, including casting flaws or machining errors.
The effects of an unbalance will become more significant as a machine's speed increases. The biggest concern with unbalance is that it can cause unnecessary vibration and drastically reduce the operational life of bearings.

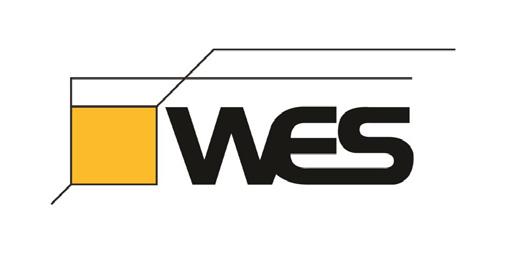
Looseness
Looseness can be rotating or mechanically generated.
There are three types of mechanical looseness to consider: Rotating looseness, structural looseness (foundation flexibility) and non-rotating looseness. Rotating looseness can occur due to wear in a bearing.
The problem with looseness is that, irrespective of what caused it, looseness can cause damage such as fatigue and wear in equipment mounts and further bearing wear. It can become very dangerous and destructive if a vibrating component is either loosely attached to its mounts or has loose bearings.
MISALIGNMENT/ SHAFT RUNOUT
A common cause of vibration is when the machine shafts are out of line. Misalignment is the root cause of many machine breakdowns, bearing failures, and damaged seals, shafts and couplings. It is widely believed that over 50% of machine failures are due to misalignment.
Misalignment does not have a single cause but can be a combination of reasons. It can happen:
• By developing over time (wear)
• During the assembly process
• Not considering thermal expansion during the alignment process
• Not being reassembled properly after maintenance
• Because of shifting components (structural issues)
Not practising precision alignment will cause premature wear and tear of components, increase unscheduled downtime and increase maintenance costs due to unexpected repairs or the replacement of parts.
As we have already mentioned, machine vibration can create time-consuming and expensive problems. For example, vibration consumes excess power, forces equipment to be taken out of service for unscheduled downtime, and expedites machine wear, increasing overall asset life costs.
There are also secondary safety issues to consider, as well as reduced operational uptime.
Measuring and analysing vibration can give asset owners an indication of a machine's health condition and hence reliability. When this data is analysed correctly it can help with preventive and reactive maintenance actions.
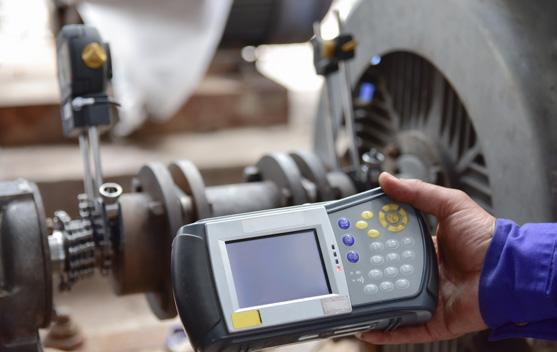
It can improve preventive maintenance by enabling the maintenance team to stay ahead of potential problems. It can help with corrective maintenance to ensure that everything which needs repairing – or replacing – is done the first time so there are no unpleasant surprises later on.
Technicians need to understand the difference between abnormal and normal vibration in machine components. With this understanding and the right tools, a technician can reliably, effectively, and quickly find vibration-related issues and then determine whether or not the component(s) can be repaired, serviced, or if they need to be replaced.
Corrective Methods
When it comes to machine vibration problems, the good news is that practically all issues can be corrected in place. That is, of course, provided the vibration-related issues are found early enough.
There are a few ways to treat vibration problems correctly; these include:
1. Precision balancing.
2. Bearing replacement.
3. Identifying any additional bad parts and having them sourced and then replaced.
4. Precision alignment.
5. Precision lubrication. That is, ensuring the correct lubricant is in the correct volume at the right time.
6. Dissemble, inspect visually, clean, and then reassemble. This can help to fix some of the more elusive problems. However, be aware of introducing new defects due to human error on intrusive maintenance like this.
7. Stiffening and mass loading to reduce measured vibration. This should lower motion; however, it will increase local stresses on the bearings if the cause of the machine vibration is not eliminated and this will cause bearings to wear at a faster rate.
On a final note, some machines do have excessive vibration. In these cases, where the machine function is still being fulfilled, and there is no deterioration, it may not be worth doing anything as long as the machine is carrying out its primary function with no apparent anomalies.
If the vibration amplitude is stable, then, in most cases, it's safe for the machine to continue operating. The advantage of this is that it will avoid additional downtime and the unnecessary cost of repairs. As long as you monitor and assess your machinery with vibration analysis, you should be able to plan, operate your machines for longer with less wear and tear, and reduce the risk of machine failure. TIMES-CIRCLE