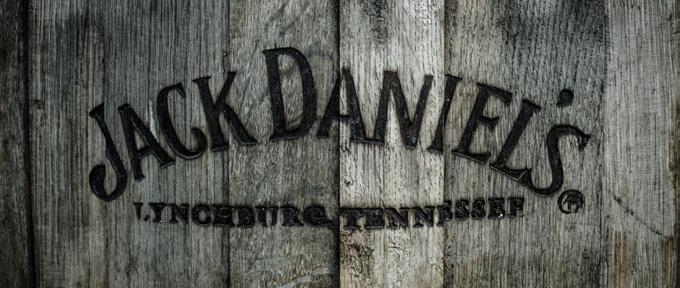
2 minute read
Connected reliability drives efficiency and productivity
With support from Fluke Reliability, Jack Daniel’s cooperage is supporting its barrel manufacturing with predictive maintenance, as Renew found out.
The Jack Daniel Cooperage, where barrels or casks are made, creates barrels for Jack Daniel’s and other brands within Brown-Forman, producing thousands per week.
Such a facility requires a well-trained team to track and analyse maintenance needs to increase productivity and ensure a smooth production process.
Martin Nelson, a maintenance and engineering manager at Jack Daniel Cooperage, and his team of repair and preventative maintenance technicians are responsible for just that. Nelson and his team use the eMaint computerised maintenance management system (CMMS) software and two types of vibration sensors from Fluke Reliability to keep the facility up and running.
The Jack Daniel Cooperage team can automatically generate work orders when their equipment exceeds temperature and vibration thresholds by connecting condition monitoring sensors with the maintenance software. As a result, they have improved their preventative maintenance (PM) and moved into predictive maintenance.
While the whiskey is made with Jack Daniel’s time-honoured and time-consuming process, the cooperage uses state-of-the-art technology to make its barrels. “The number one cost that goes into a whiskey is the barrel,” Martin Nelson explained.
To meet Jack Daniel’s exacting standards, Martin’s team needed to test and prove the value of various prototypes of custom barrel-making equipment for different parts of the process. In addition to the machinery used to make the barrels themselves, the cooperage has an extensive dust collection system which needed to be taken into account. All of it requires strong attention to detail and a firm commitment to an asset management strategy.
Working With A Cmms
Every technician on the team is now using eMaint. The features they rely on most are work orders and inventory management. They have customised PMs to include pictures with captions explaining what needs to be done.
“I have several PM reports that autogenerate to me and give me the status of open PMs, overdue PMs, and PM completion percentage, which is huge,” Martin added. “We are slated to have 100% PM completion every week.”
The work order system in eMaint has been a crucial tool for the cooperage in helping to plan and prioritise the work that gets done. “One of the nice things about eMaint is I can differentiate work orders,” Martin continued. “I segregate all the project stuff out versus what’s going on in real time.”
Martin uses several different categories of work orders, including RCCA (root cause and corrective action), safety work, corrective maintenance, TPM (total productive maintenance), and emergency maintenance. Identifying what’s most urgent, for example, or what will require specialised parts or labour, helps the team ensure they have the resources they need when and where they need them.
Enhancing The Benefits
In addition to using eMaint, the cooperage also uses two types of vibration monitoring sensors from Fluke Reliability. The sensors and software work together to keep the maintenance team updated on how the equipment is operating. “I like the way that it does the reporting and auto-generates the work orders when it’s out of its threshold –over the temperature or vibration,” Martin went on to say.
VibGuard vibration sensors offer advanced alarm tools to monitor for specific failures. They collect several different types of data. The cooperage also uses other Fluke vibration sensors. Maintenance teams can advance their connected reliability journey with access to real-time machine health data in their CMMS. Connected reliability is about centralising data from different systems and tools to make it readily accessible and actionable. Pairing sensors and software makes a more holistic approach possible, where teams can plan rather than just react.
Approximately 31 staves – narrow lengths of wood – go into making each barrel. The staves are precisely shaped on all sides with the cooperage’s specialised equipment. Thousands of barrel staves are processed each shift.
Due to this, the cooperage now also uses vibration sensors on the gearboxes, blowers, bearings, and motors which are part of the dust collection system to ensure a holistic maintenance strategy.
Looking To The Future
With a focus on continuous improvement and connected reliability utilising Fluke Reliability’s solutions, the Jack Daniel’s cooperage has overhauled its maintenance practices, and its strategies are being adopted throughout Brown-Forman. TIMES-CIRCLE