WHEN SUCCESS IS IMPERATIVE MARCO DELIVERS
COVER LETTER
Dear [Name],
I am writing to express my keen interest in the (Name of Project) and to introduce my company, MARCO, as a potential contractor for this project.
MARCO has over 40 years of experience in providing attention to detail and fast-track construction services for a diverse range of commercial and industrial projects. Our expertise assures you that we can deliver projects on time and to the highest standards of quality.
We have carefully considered every aspect of the project and have developed a comprehensive plan that meets all the requirements outlined in the RFP. We are confident that our proposal will meet your expectations.
At MARCO, we believe that communication and collaboration are integral to the success of any project. We are committed to working closely with you and your team to ensure that we fully understand your vision, goals, and priorities for this project. We will keep you informed at every step of the process, and we will be responsive to your needs and concerns throughout the project lifecycle.
We are excited about the opportunity to work with you on this project and to help you achieve your vision. Thank you for considering MARCO as a potential contractor. We look forward to the opportunity to meet with you to discuss our proposal in more detail.
Sincerely,
Hamad Binyousef CEO
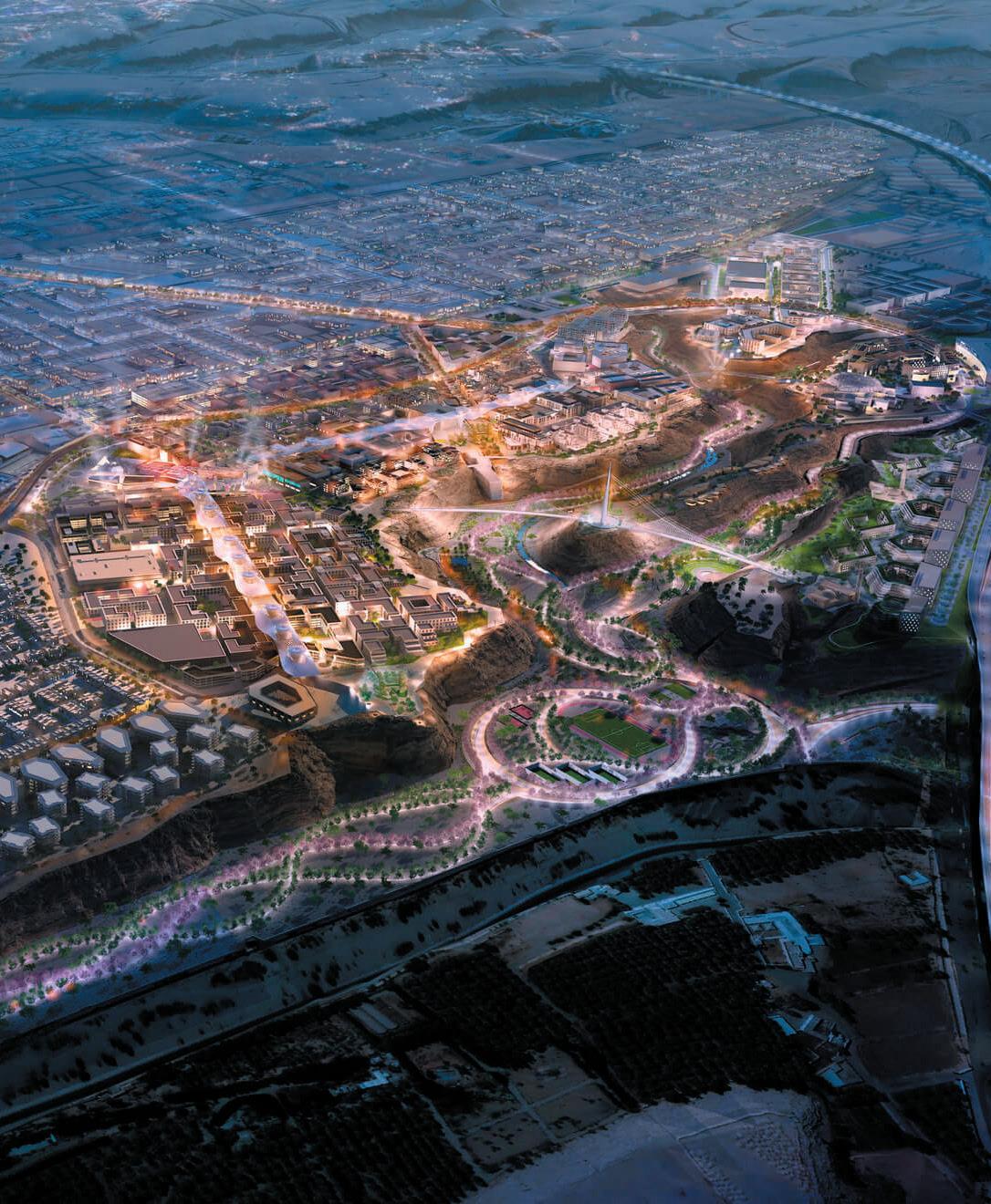
2.0 TENDER CHECKLIST
The following table confirms the receipt of all the below Tender Documents and Contractor’s submission compliance.
3.0 EXECUTIVE SUMMARY
When a successful project is imperative, there’s no room for failure. When you work with MARCO, you get more than just another contractor, you get a handson approach and focused attention to every detail, so you can complete your project with competence and confidence.
The Misk City Company is looking for a Main Contractor who is qualified, approved, and experienced to handle the Al Mishraq Main works according to the employer’s requirements. This includes coordinating and securing all necessary approvals for the project.
MARCO has a successful track record of delivering multistory, mix-use developments throughout the region, with the technical expertise of our teams contributing to our ability to meet the needs and expectations of our clients. That expertise is crucial in meeting clients’ expectations, and our collaborative approach with the employer’s chosen representatives, consultants, and other contractors is an added value to the project. MARCO’s experience in managing and delivering large-scale programs in a collaborative environment is also a significant advantage for this project, where understanding the overall goals of the development is crucial.
Having diligently reviewed the project design and specifications, MARCO’s team is familiar with the project’s requirements and is prepared to work with the employer and engineer to deliver the project to their expectations. This technical proposal contains detailed information that addresses the ITT requirements, clarifies their construction approach, resourcing, and subcontracting strategy. We have also given special attention to the study of the design, scope of work, and logistics, considering the project’s location near other developments and residents. The technical submission also outlines their approach to the management of engineering drawings and coordination with the supervision team to ensure that the technical design is correctly implemented, approvals are expedited to maintain the construction activities’ progress, and digital delivery is considered.
Over 40 years, MARCO has helped to promote growth and innovation by partnering with some of Saudi’s biggest organizations.
Our past client list includes, but is not limited to:
• General Auditing Bureau
• Ministry of Education
• Saudi Electric Company
• Ministry of Interior
• Knowledge Economic City
• Diriyah Gate
• Modon
• NDF
• KAFD
• SIDF
When you partner with MARCO, you get the guarantee of a successfully completed project, made to your specifications, by a contracting company that will serve as your trusted partner throughout the entire process. From the very first site visit through the handoff, you can expect the hands-on and detail-oriented care that our past clients have come to rely on. We understand the unique challenges and opportunities your project provides, and look forward to showing you how MARCO will exceed your expectations and make the process as seamless and efficient as possible.
4.0 COMPANY DOCUMENTATION
Company Documentation is enclosed in Appendix K.
5.0 TENDER ADDENDA - APPENDIX A
Tender Addenda is enclosed in Appendix A.
6.0 CONFIRMATION OF SITE VISIT
Attn: Company Address Address Address
Dear Sir,
This Letter of Tender is provided in reference to the Invitation to Tender letter we received from your company on (date), as well as any additional correspondence issued by yourself or your advisors, and accompanies our Tender in response to your invitation.
All capitalized terms used herein shall have the same meanings accorded to such terms in the ITT.
Mohammed Al Rashid Construction Company hereby confirms that a site visit was undertaken on (date) to verify the condition of the perimeter of the site where the works are to be undertaken, the extent of existing fencing and its condition, the required site access points and all other requirements listed in the ITT document.
Signed,
7.0 AUTHORIZED REPRESENTATIVE & POWER OF ATTORNEY”
Letter is enclosed in Appendix K
8.0 QUALITY POLICY STATEMENT
MARCO is dedicated to delivering construction services of the highest quality and exceeding customer expectations. We do this by following our established quality procedures, and implementing preventive and corrective measures. Our Project Management services provide the resources necessary for adherence to industry best practices.
Our team is guided by our quality procedures documentation, a series of documents and briefs that are used throughout the project life cycle. These documents are part of our Quality Management System (QMS), which is certified with ISO 9001:2015.
These include the:
• MARCO Quality Manual
• MARCO Integrated Management System
• MARCO Code of Ethics
• MARCO Quality Policy
• Procedure for Competency, Awareness, and training
• Procurement Procedure
• Document Control Procedures
• Quality Monitoring
• Quality and Inspection Flowchart
At the mobilization stage and throughout the engineering, material selection, and procurement phases, MARCO’s quality team checks the submission for conformity and document quality before they are submitted to the consultants. Quality checklists are attached to every submission and signed by the quality department representative to ensure that only controlled and approved documents are included.
MARCO’s quality control process includes a two-way inspection procedure that eliminates any quality issues that may arise during work execution. The quality engineers conduct daily site walks to monitor all site activities and implement quality internal inspections in conformance with the required goals. A quality kickoff meeting is held for each new activity to align all team members with the quality requirements and present the approved engineering documents. This proven process ensures the project team’s responsibility and awareness.
MARCO’s quality manager promotes daily huddle discussions with supervision or project management consultant’s representatives to identify any quality risk or issues and to submit official closeout documents along with corrective and preventive actions. To ensure that all activities meet the quality standards, prototypes for all look and feel material are prepared for prior approval as a standard process.
The project quality system is in place from the project award with the submission of the project quality plan, which outlines all the quality system procedures to implement along with MARCO’s and Project Management Consultant’s KPIs’ requirements. This plan includes all activities detailed method statements and inspection procedures for each project execution phase. All of these documents and procedures are used during the project life cycle to maintain the high-quality standards that MARCO is committed to delivering.
All documentation is meticulously organized through identification, segregation, naming, tagging, and unique numbering. These documents are then filed and stored appropriately and saved in our secure online repository, which includes Logs and Registers for efficient document retrieval. Furthermore, all documents are uploaded to Aconex (provided by Misk), ensuring that the Client and Consultant Representatives can access the necessary information at all times.
The Document Management procedures will be further explained after the Main Contract Works award, and will be stored on online data centers with proper redundancy, organized in accordance with Marco’s procedures to prevent disaster risks, and enable quick data recovery in case of any incident.
The section dedicated to the BIM execution plan contains detailed information about the engineering software.
9.0 MEMORANDUM OF PROCEDURE
9.1 MOBILIZATION AND TEMPORARY WORKS
Upon being awarded the project, Marco’s central services will immediately make the necessary arrangements for personnel, labor, and equipment based on the preliminary schedule and resources histograms provided in the proposal.
The Project Director and Project Manager will review these documents, make necessary modifications, and provide further details to ensure the project goals are met. Most of the equipment is currently available for immediate mobilization, and the availability of labor is planned according to the project timeline.
The project’s detailed timeline will include:
• Scheduling For Various Tasks Such As Shop Drawings, Technical Clarifications, and Quality Plans And Procedures
• Manpower And Equipment Assignments
• Sourcing And Procurement
• Material And Equipment Delivery, Construction Works
• Testing And Commissioning
Personnel mobilization arrangements will start together with the mobilization of the site’s temporary facilities, including the:
• Contractor’s Main Office
• Contractor’s Hse Office
• Pmc/Employer Office
• Formwork Workshop
• Steel Rebar Lay Down Area
• Cutting And Bending Areas
• Material Lay Down Area
• Covered Warehouse
• Sample Room
• Mock-Ups Area
• Equipment Maintenance Area
• Parking
Major equipment such as cranes, power generators, and water storage tanks will also be transported to the site to enable staff allocation and the commencement of works.
Data communications will be provided through GSM routers and local cabled network, which is used across all MARCO’s sites to ensure a fast initial setup and reliability of the communication network.
9.1 INTERFACE
Marco will engage various specialist subcontractors, including those for windows, steel structures, metal fabrications, designated LV systems, elevators, landscaping, and other project components. The Project Manager, supported by the Construction Team and the shared services teams of Marco’s head office, will primarily manage the subcontractors. To assist in subcontract management matters, a Sub-Contracts Manager from the shared services team will support the Project Manager and the rest of the Construction Team. During project execution, various departments of the Project Team will work with the appointed specialist subcontractors to ensure timely delivery and expected quality.
This interface with subcontractors will not only be limited to Marco’s own subcontractors but also to other contractors appointed by Misk or its Tenants. The Project Director and Project Manager will manage this interface and coordinate with Misk’s representatives to ensure the work is completed within the given timelines, requirements, and overall coordination of the work. This process is well established in Marco, with extensive experience in delivering commercial turnkey projects, and coordination efforts will be embedded in the team’s routines.
9.2 ENGINEERING
To expedite the project start, MARCO will employ on-site and off-site engineering teams to prioritize engineering drawings and material specifications. This will allow the sourcing and procurement teams to begin during mobilization. This fast-tracking enables the supply chain to be ready and provides the project team with the necessary technical information to start work immediately after mobilization is complete.
To ensure site readiness, MARCO’s surveyors will perform a detailed excavation survey upon the contractor’s appointment. The engineering team will receive support from the appointed BIM consultant, and submission schedules and drawings will be issued for review during mobilization, facilitating alignment with technical requirements and monitoring of engineering submittal performance. The technical manager will regularly meet with consultant representatives to address design clarifications, and work closely with the project manager and QA/QC manager to ensure only approved engineering documents are used on-site.
9.3 SOURCING AND PROCUREMENT
Due to delays in the delivery of construction projects often being attributed to issues with sourcing and procurement processes, MARCO has devoted considerable effort to designing and allocating resources to create an efficient operational workflow. This includes a streamlined process for identifying suppliers and materials to be incorporated in the project, while simultaneously finalizing the engineering details and seeking the necessary initial approvals.
This initial process aims to develop a detailed plan of the procurement activities and set out the procurement strategy for the project, including identifying the long lead items, materials subject to final user approval, and planning of mock-ups.
All of MARCO’s suppliers are subject to both initial and ongoing evaluations to ensure that they possess the capability and suitability to meet each project’s requirements. Our supplier selection criteria is based on several factors, including the supplier’s previous experience and past performance with the product or service to be purchased, the relative sophistication of their quality system, their ability to meet current and potential capacity requirements on the desired delivery schedule, their financial stability, and their technical support availability and support in developing and optimizing processes, among other factors.
Once suppliers have been identified, we will request their approval from the consultant. Communications between the operations, quality, sourcing, and procurement teams are facilitated by a specific procurement software (Precoro), which standardizes the process in conformance with MARCO’s policy and project goals. The purchasing department will only proceed with orders if properly backed by instructions from the project management and quality control teams, specifically regarding final drawings, approved specifications, verified quantities, and delivery schedules.
Upon delivery to the site, a QC engineer inspects the materials internally, using various criteria such as project specifications, applicable international standards, project shop drawings, test certificates, material data sheets, and more, to determine any minor or major defects. If approved, the material is signed off on by the store manager and included in the Material Inspection Request, which is submitted to the consultant for inspection. If rejected, the material is immediately removed from the site and replaced with suitable alternatives.
Additionally, MARCO’s internal auditor prepares a supplier audit schedule utilizing input from purchasing requests, corrective action systems, supplier ratings, and NCR Logs. The auditor will review any potential findings and observations with supplier representatives and summarize the results to the project director for further action as appropriate. A report of the audit must be prepared within 10 days of the exit meeting, unless an extension is approved by the quality manager.
A list of all major items of equipment, plant, materials, and sub-contractors proposed to be used in carrying out the works is included in section 11, with indicative pre-qualification documents of some of the suppliers, manufacturers, or subcontractors that will be engaged for the construction of the project enclosed in Appendix G.
9.4.1
Phasing of construction works
MARCO’s proposal takes into account the logistical complexity of the Al Mishraq construction site, the challenging timeline, and the phasing of both the access and completion dates. The preparation of the proposal is aimed to properly identify and address these challenges, and incorporate necessary contingencies to mitigate them.
The main challenges identified for the project include the congested site, lack of access to work fronts, challenge for concrete pouring, simultaneous work areas with identical access of completion dates, and scope creep which requires additional staff to mitigate.
To tackle these challenges, a construction strategy was developed that consists of phasing the projects into main work packages including Site Setup, logistics and maintenance, Basement, Construction Section A, Construction Section B, and Exteriors. This strategy is further illustrated in a table and plan. The alignment of resources with this strategy is planned and reflected in the Project Organizational chart and the proposed selection of key staff for the project as outlined in sections 9.10 and 10.
9.4.2
High level project risks
Other mitigation actions were also considered, taking into account the high-level risks of the project to establish a framework for the successful delivery of the project.
RISK MITIGATION
Congested Site
Surroundings
Access to work areas
Compressed timeline with almost simultaneous access/ completion dates
Scope creep
Supply chain capacity
Injury of employees
• Traffic control management plan
• Controlled accesses and exits
• Properly sized laydown area
• Night shift for support activities
• Noise and Dust Control
• Traffic control management plans
• Controlled accesses and exits
• Site maintenance
• Concrete stationary pumps and pumping lines
• Night shift for support activities
• Traffic control management plan
• Scope packages – Sections managed by experienced staff Increase number of resources – both management and labor
• Increase number of supervision staff
• Rigorous scheduling and plan ahead
• More than one supplier for the main work packages
• Add commercial and engineering resources to support Consultant and Project Management
• Rigorous scheduling and plan-ahead
• Fast track sourcing
• Select (approve) more than one supplier for each material
• Industry best practices in HSE from induction to day-to-day work monitoring
• Aim to zero harm workplace
Risk management will be a top priority for the project controls team, supporting the project director in the early identification of mitigation actions to implement. Proper records will be maintained and communicated to the project’s consultant representatives in a spirit of mutual collaboration to manage, identify and implement the adequate solutions for each case.
9.4.3
Enabling works
During the site visit, we observed that excavation works were still ongoing by another contractor. As a result, MARCO assumes that the site will be handed over to the Main Works Contractor in a state that is ready for concrete works, with only minor excavation works remaining. This early completion of excavation works allows for the immediate start of surveying and engineering upon appointment as the Main Works Contractor, while the offices, laydown areas, and temporary site works are being set up.
The information gathered from the survey will be incorporated into the overall layout and coordination drawings based on established benchmarks for setting out the works. The consultant will review and validate the information before it is released to the construction personnel for use in construction activities.
To ensure that the project stays on schedule, it is crucial that adequate lifting equipment is available for the distribution of materials, equipment, formwork, steel, etc. The tower cranes proposed in Appendix F will be used for the erection, stripping, and movement of formwork and reinforcement bars, lifting and placement of construction materials, as well as lifting and removal of construction debris.
9.4.4
Concrete structure construction
The contractor faces an initial challenge of accessing the work fronts during the construction of Al Mishraq phase 1. To overcome this challenge, we conducted extensive research with our suppliers to ensure the proper distribution and pouring of concrete. Our proposed solution involves the installation of stationary pumps and temporary concrete pouring lines to deliver ready mix concrete of the required quality to each building element. We will submit detailed information regarding the pouring plan and the location/number of pumps after award. In cases where necessary, concrete pouring using tower or mobile cranes will serve as a complementary method.
Once the drainage and service works within the basement footprint are completed, the construction of the basement will begin. This process will follow the horizontal waterproofing sequence. On-site construction of concrete walls will be done using properly designed formwork for the size and construction loads. Continual verification of proper alignment and levels based on approved project information will be ensured. We will provide adequate cranes, workforce, and equipment to ensure that the programme is met. Following the completion of the concrete works, block walls, MEP works, and some finishing activities will commence according to the sequence detailed in the project time schedules. Vertical waterproofing will be carried out immediately after the completion of the walls, by a specialized sub-contractor in accordance with the approved design and specification.
9.4.5 Building finishes and mpe works
The contractor will follow a specific sequencing of building finishes to ensure quality and avoid damage to completed works. Wet finishes will be completed before dry finishes, and installation will begin from the top and proceed downwards. The work will also proceed linearly over specific areas, with the dry finishes starting before the full completion of the wet finishes. The installation of vertical transportation equipment will be done as soon as possible after the completion of the concrete structure, while the installation of the main MEP equipment will be advanced to allow the completion of the 3rd fix of the MEP installations and the pre-commissioning activities upon finalization of the dry finishes.
To ensure that the works are performed in accordance with the design and specifications, detailed work method statements and related inspection and testing procedures will be issued in advance. Trials and installation mockups will also be executed before the main activities to verify compliance and meet expectations. Hold-points will be identified and approved in a timely manner to ensure that the works are performed as scheduled.
9.4.6
External works
The external works constitute a substantial portion of the project scope and will be carefully synchronized with the advancement of the building construction to ensure uninterrupted access to the work areas. This approach will facilitate an early commencement of the external works to allow timely completion, not only for tenant access but also to meet the overall project delivery schedule for Al Mishraq phase 1.
9.5 DEMOBILIZATION
Following the substantial completion and start of testing and commissioning, as-built drawings and other essential documents for maintenance purposes will be generated. The Project Director will meticulously plan the demobilization of temporary facilities and staff to ensure a seamless handover. Apart from dismantling temporary facilities, this phase involves disconnecting temporary services and connecting permanent ones, conducting general cleaning, and carrying out reinstatement works where necessary.
9.6 HEALTH AND SAFETY
Marco places a high priority on the health and safety of its workers and staff, which is reflected in its management of project sites. As part of this commitment, dedicated offices and teams will be deployed to the Al Mishraq project to oversee and implement comprehensive procedures for training, safety induction, and monitoring systems. These systems will be established in accordance with the best industry practices and recommendations to ensure a safe workplace and a goal of zero harm throughout the duration of the project. Regular audits will be conducted to assess the site’s health and safety conditions, measuring them against project and company standards. Our teams have a proven track record of successfully managing zero harm sites in the Kingdom and will bring this experience to the Al Mishraq project.
9.7 PROJECT ORGANIZATION, DECISION MAKING AND DAY TO DAY OPERATIONAL STRUCTURE
The Project Management team aims to ensure seamless coordination and control of the entire project development and delivery process through a unified organizational structure. This is achieved by carefully selecting qualified key personnel to oversee the construction process, with a focus on maintaining continuity between various phases and activities such as design, sourcing, procurement, and project delivery.
9.8 LIAISON AND TECHNICAL SUBMITTALS REVIEW AND APPROVAL
To ensure compliance with the project’s requirements for material selection, work execution, and knowledge transfer, our team will work closely with the project’s consultants. All project documentation, ranging from product data sheets to shop design and operation manuals, will be shared for review and approval to certify the quality of the works’ design, construction, and performance. Our experienced team expects a smooth review and approval process, given the nature of the works.
9.9 LOGISTICS
9.9.1
Site Set-up
In addition to site logistics, ensuring the safety of the site also requires proper delimitation, access, and circulation. The proposed set-up for the Al Mishraq project, presented in the following lines and drawings in Appendix F, is a preliminary study subject to further review and detailing. Temporary buildings will be installed on the site for both the Contractor’s and the PMC/Employer’s use, with a proposed location shown in the layout plan in Appendix F. These facilities will be situated in an area isolated from the construction site.
The Site facilities will comprise a Contractor’s Main office, Contractor’s HSE office, PMC/Employer office, Formwork workshop, Steel rebar lay down area, cutting and bending areas, Material lay down area, Covered warehouse, Sample room and mock-ups area, Equipment maintenance area, and Parking.
To prevent unauthorized access, the site hoarding will isolate the working areas from the rest of Misk City. The hoarding will allow control of the entry and exit points for workers, materials, and equipment. The site boundary will have a hoarding erected to secure it during the contract period. Access to the site will be through personnel site entrance doors and vehicle entrance gates, and the hoardings will be kept clean and secure throughout the contract duration.
MARCO will assign security officers to ensure site security and keep records of entrance and exit. They will provide appropriate levels of site security for the benefit of the project and all its stakeholders, reducing the potential for theft or accidents. The security team will periodically assess the site to review the need for improvements or changes during the construction process.
Parking areas will be located near the offices and laydown areas. The MARCO site team will discourage parking outside of controlled areas and ensure that site personnel and visitors do not park in unauthorized areas.
9.9.2
Traffic Circulation
The transportation and storage of materials for the project will be arranged and coordinated with outside suppliers and delivered to designated laydown areas within the site boundaries. All materials will be segregated and stored on hard ground at ground level.
The proposed route for access and egress to the site can be found in Appendix E. Routes from the laydown areas to the work areas will be determined in further detail during construction and may be periodically revised due to site containment, especially during the initial basement construction. Once the ground floor slab is completed, circulation routes can be established at that level to the various buildings, always accessed from controlled entry gates.
9.9.3
Pedestrian Routes
To ensure that everyone is aware of the agreed route, site induction and pre-order meetings will be held to communicate with sub-contractors, suppliers, deliveries, and visitors. The traffic plan will provide the ideal route which will be issued to all relevant parties. A Traffic Management Plan will also be put in place, outlining all traffic and pedestrian management measures and displaying necessary signage as per local standards.
As most workers will arrive on buses, a dedicated parking area has been assigned next to the laydown/offices area to control access and egress in an orderly manner. Emergency scenarios will also be taken into account, identifying additional exit points, although this is subject to further evaluation for future works in the surroundings of Al Mishraq.
9.9.4
Unloading Areas and Storage
To ensure that all construction and support activities are confined within the Contractor’s designated areas, warehouses and storage spaces are planned to be located adjacent to the work site for material laydown. The incoming and outgoing traffic will be regulated by the traffic management plan, and the loading and offloading operations will be coordinated by the management, strictly within the assigned boundaries. The plans in Appendix F provide further details on this matter. Mobile cranes and forklifts will be utilized for the loading and unloading of materials at the laydown areas, while the tower cranes will be the primary vehicles for load and unload operations at the work areas.
9.9.5
Pre-assembly Areas
A pre-assembly area will be located adjacent to the laydown area and utilized during various stages of the project, including the structural and finishing phases. During the concrete structure phase, the majority of the area will be designated for formwork and steelwork preparation. An additional space will be allocated for the storage of approved material samples and the assembly of prototypes or mock-ups. The mock-ups area will be utilized for a limited number of mock-ups to aid in the selection of materials and decision-making on the constructability of proposed solutions.
9.9.6 Temporary Water and Power
The site will be powered by diesel generators to meet the necessary loads for both offices and work areas. Sufficient generators will be provided, and their location and capacity will be specified in the power distribution plans, which will also cover cable distribution, panelboard diagrams, and cable sizing. Open-type generators will be used at the work site, while soundproofed generators will be utilized to power the offices to reduce noise levels.
Water will be supplied to the site by water tankers and stored in on-site water storage tanks. Potable water for consumption will undergo regular quality testing to ensure compliance with applicable safety standards.
9.9.7
FOD Plan and Site Maintenance
Marco recognizes the significant risk posed by falling debris on construction sites, which can endanger workers, bystanders, and structures. The Occupational Safety and Health Administration (OSHA) identifies being hit by a falling object as one of the leading causes of death for construction workers. Falling objects can slide, roll, fly, slip, and swing, making it crucial for employers and workers to take necessary precautions to secure all equipment and tools and prevent unnecessary hazards.
To prevent incidents on construction sites, Marco implements the following measures, among others, and will do the same at Al Mishraq:
• Inspect tools, hoists, and cranes to ensure they are in good and safe working condition.
• Use screens, debris nets, guardrails, and toe boards on scaffolds to prevent objects and tools from falling to lower levels from overhead work areas.
• Store materials no closer than two meters from floor openings or hoist ways.
• Provide proper training to workers on the safe operation of power tools and all other tools before use.
• Supply appropriate personal protective equipment (PPE), such as hard hats, goggles, safety glasses, and face shields to prevent injuries from falling or flying objects.
• Ensure that rotating and moving parts on power tools and industrial machinery are guarded when in use.
• Remove tools with splintered, loose, or cracked handles from the site.
• Secure tools and other items to prevent them from falling onto people below.
• Keep areas clear of clutter, and stack and secure materials to prevent them from sliding, even during wind gusts.
The HSE Manager and Supervisors support the implementation of these actions, and the HSE officers and Logistics Engineer will be responsible for ensuring the site remains a safe workplace.
9.10 INTERFACE
Marco will engage various specialist subcontractors, including those for windows, steel structures, metal fabrications, designated LV systems, elevators, landscaping, and other project components. The Project Manager, supported by the Construction Team and the shared services teams of Marco’s head office, will primarily manage the subcontractors. To assist in subcontract management matters, a Sub-Contracts Manager from the shared services team will support the Project Manager and the rest of the Construction Team. During project execution, various departments of the Project Team will work with the appointed specialist subcontractors to ensure timely delivery and expected quality.
This interface with subcontractors will not only be limited to Marco’s own subcontractors but also to other contractors appointed by Misk or its Tenants. The Project Director and Project Manager will manage this interface and coordinate with Misk’s representatives to ensure the work is completed within the given timelines, requirements, and overall coordination of the work. This process is well established in Marco, with extensive experience in delivering commercial turnkey projects, and coordination efforts will be embedded in the team’s routines.
9.11 QUALITY CONTROL
The following table details the tests, trials and the like to be performed by a third-party laboratory during the construction stage.
PROJECT LABORATORY TESTING LIST
No.
1. Geotechnical Investigation (If Required)
1.1 Physical Tests
Grain Size Distribution
Particle Size
Atterberg Limits
Moisture Content
Unconfined Compressive Strength
Chemical Tests
Water Analysis (full)
ASTM D 3080
ASTM D 2216
Sulphate Content Percentage
PH Percentage
Chloride Content
2. Excavation Soil Investigation
2.1 Sieve analysis for granular materials ASTM D 422, 2.2 Plasticity indices ASTM D 4318 method A
2.3 Specific gravity ASTM D 854, 2 Determination of the California Bearing Ratio ASTM D 1883,
Unconsolidated undrained triaxial compression tests on cohesive soils
Chemical and biological analysis of soil and ground water
Calcium carbonate content of soil
ASTM D 2850
PROJECT LABORATORY TESTING LIST
No.
Test Description Standards
Determination of the dry density/ moisture content relationship of soil
Elastic modulus for rocks
Concrete
1 Concrete Trial Mixing
1.1 Water Analysis
1.2 Cement Testing (if Recent Test certificate is not provided)
1.3 Aggregates (if Recent Test certificate is not provided)
ASTM D 1557 /ASTM D
698
ASTM D 7012
B.S. 3148: 1980 OR SASO 701 OR ASTM C 94
ASTM D 75
For Remarks
Free of ron pyrites, coal, mica, shale, alkali, coated grains, or similar laminated materials such as soft and flaky particles, or any material which may attack the reinforcement
1.4
Addmixtures Chemical (if Recent Test certificate is not provided) /Air entraining
1.5 Sulphate expasion
1.6 Cement Content
1.7 Compressive strength
1.8 Slump test
1.9 Temprature test
Fresh concrete
Slump test
Temprature test
Hardned Concrete
Compressive strength 7 & 24 days
ASTM C 494 / C 260
ASTM C452 ≤ 0.045%
ASTM D806 - 19
ASTM C-39/C-31
ASTM C143.
ASTM C 1064
ASTM C143.
ASTM C 1064
ASTM C-39/C-31
Dry Density For Light weight concrete Only
Post Tension Grout
Grout Physical Properties
Grout Compressive Strength
Grout Slump Test
Seven Wires Strands/Physical, Chmical & Mechanical
ASTM C 579
ASTM A416
PROJECT LABORATORY TESTING LIST
No. Test Description
Anchorage BS EN 13391
Concrete unit masonary blocks
Mortar Compressive strength 7 Days 3.10 Mpa / 28 Days 5.17 Mpa
Masonary blocks Compressive strength
Masonary blocks weight
Masonary blocks water absorbtion
Structural Steel Framing
Shop Bolted Connection
Field Bolted Connection
Welded Connection
Stone Cladding
Anchorage Pull out test
Stone Load Test
Fluid Applied Water proofing
Flood Testing
Traffic Epoxy
Flood Testing
Composite Wall Panels
Modified Bituminous Protected Membrane Roofing
Flood Testing
Swimming Pool Flood Test
EPDM Waterproofing Membrane
Air Lance Test
Glazed Aluminum Curtain Wall
Full mockup
Air Infiltration
Water Penetration
Fluid Applied Flooring (resinous Flooring)
Thickness test
Chemical Resistance
Epoxy flooring
Applicable For Remarks
48 Hrs For Leackage
ASTM D 5957,
ASTM E 329
100 MM water for leak 24 hrz
100 mm below the overall depth
Non-Destructive tests as per ASTM D4437
ASTM E 783
ASTM E 1105
Core Test for each 93 M2 3.2 MM Body Coat
ASTM D 543
According to approved Material Check Page 765
Traffic Control Equipment
Electrical & Mechanical test
Trench excavation and backfilling
NETA ATS, Section 7.15
Compaction test (MAX dry density BS 1377: Part 4: Method 3.5/3.6.
PROJECT LABORATORY TESTING LIST
No.
Test Description
Density of compacted
Cone Penetration
Compaction fraction
Asphalt paving
Plant control Testing
a. hot bin gradations of aggregate (sampling)
Density and Thickness (core Test)
Mechanical Analysis
Resistance to Plastic Flow of
Bituminous Mixture
Extraction of Bitumen from Bituminous Paving Mixtures
Bulk Specific Gravity of Compacted
Bituminous Mixtures
Thickness of In Place Pavement
Theoretical Maximum Specific Gravity of bituminous Paving Mixtures
Interlock tiles
Compaction
Concrete Testing
Irrigation 941
Hydrostatic Testing
Concrete Pipes
Hydrostatic Testing
Crushing test
BS 1377: Part 9
Method 2.1 or 2.2
TRL Method or BS 1377
AS per Project specs
31 23 33 - 5
ASTM D 75.
AASHTO T30.
ASTM D 1559.
ASTM D 2172
ASTM D 2726
ASTM D 3459
ASTM D 2041
1-3 Cylinder for each 1-3 Cylinder for each 230 m2
As per project specs
32 84 00 - 7
ASTM C76 or BS 5911
Pin holes for linings electrical spark tester set at a minimum of 20,000 volts
Water Distribution And Fire Fighting HYDROSTATIC TESTING
disinfection and testing of the potable water system
Bacteriological Tests
AWWA C651.
AWWA C651.
Valves, Fire Hydrants, Water Meter And Appurtenances
Gate valves
Sanitary Sewerage
Hydrostatic testing
AWWA C500.
For all types of pipes
PROJECT LABORATORY TESTING LIST
No. Test Description
For Remarks Storm Drainage System
Hydrostatic testing Service Roads, Parking Areas And Footpaths
Compaction tests
In situ density of compacted soils
Cone Penetration
BS 1377: Part 4:
Method 3.5/3.6
BS 1377: Part 9
Method 2.1 or 2.2
TRL Method or BS 1377
9.12 SUSTAINABILITY AND ENVIRONMENT
Please refer to Section 23 and Appendix E.
9.13 HANDING OVER AND DEFECTS LIABILITY PERIOD
Before the handover of the building, the commissioning process is crucial to ensure that the building systems are designed, installed, and tested to operate in accordance with the design intent. This requires a set of operations that align with the building construction to meet the owner’s interests. The handing over procedures are the starting point for smooth operation and easier maintenance. Therefore, MARCO will provide full documentation for each trade, including material, location, supplier and manufacturer identification, spare parts list, maintenance recommendations, and operation guide. Major documents, such as As-Built Drawings, Testing and Commissioning Certificates, Maintenance Defect Liability Period, and Operation and Maintenance Manuals will be handed over to the client.
To achieve a complete integrated process, commissioning plans will be prepared, and pre-commissioning and completion of commissioning of the building systems will be carried out. The commissioning process will be coordinated with the construction manager, design team, and engineer to determine optimal points. An action plan for the construction phase will be implemented, which includes pre-construction kick-off, review of submittal logs, identification of specific forms and backup documentation, tracking, review of shop drawings and material submittals, interpretation of commissioning requirements, verification of installation, functional performance, training, and documentation, and completion of a commissioning report.
The contractor’s team will have experienced professionals in commissioning processes as per requirement fundamental commissioning prerequisite. This includes reviewing owner project requirements and basis of design documents and preparing documentation and compilation of method statements and O&M manual for construction review. The commissioning of systems will be the responsibility of the MEP Manager and specialist equipment suppliers. The MEP Manager will verify that the Owner’s Project Requirements have been met by the project design. System testing, including air balance testing, water pressure testing, and any other functional testing, will be the responsibility of the MEP Manager as part of their commissioning scope. The MEP Manager’s team, with the support of each system supplier, will provide documentation and reviews to meet the commissioning requirements and ensure that the systems function as intended.
The commissioning of the system testing will be performed as per ASHRAE Guideline, including but not limited to chiller start-up and commissioning, chilled water pumping systems, fresh air system commissioning, specialist A/C equipment commissioning, electrical cold testing, lighting control, BMS commissioning, domestic hot water systems and chlorination, and renewable energy systems. The MEP subcontractor(s) will revisit the building within ten months of completion to assist in verifying building operation.
10.1 Organization Chart
Recruitment and
Business Development Manager and Bidding Director
Projects
Business Development
Corporate Planning
Accomodations and Clinics
Administration
Estimation and Bidding Manager
Estimation
Technical Proposals
Commercial Proposals
Methods and Constructability
Project
Construction
Engineering
Quality
Support Staff
Chairman
CEO
General Manager
Procurement and Contracts Manager
Sub-Contract Administration
Sub-Contracts
Spent Analysis
10.2 Schedule of Staff
Appendix H below outlines the staffing requirements for the project, including the current capacity of the company and the proposed number and category of staff to be hired upon project award. The essential functions will be deployed to the site offices as indicated, while certain off-site supporting staff will be added based on project needs to provide technical and strategic expertise. Section 10 and Appendix D provide detailed information about the qualifications of the proposed key staff, and Appendix H contains the staff mobilization timeline.
10.3 Schedule of Labor
With a workforce of over 2,500 experienced workers across various trades, along with the ability to recruit additional resources as needed, Marco has the capacity to successfully complete the Al Mishraq Phase 1 project within the proposed timeline and scale. Additionally, when necessary, Marco collaborates with local subcontractors to enhance their capabilities and meet challenging deadlines, such as those encountered in the Al Mishraq project. For a comprehensive labor schedule, please refer to Appendix H.
10.4 Schedule of Equipment
The Schedule of Equipment enclosed in Appendix H provides a detailed description of each item, including specifications, quantity, and any other relevant details. This information is essential for evaluating the feasibility of the project and determining the necessary resources and budget required for its successful completion.
Furthermore, we have included a detailed timeline for when the equipment will be needed throughout the project, including specific dates and milestones. This timeline ensures that the required equipment is available when needed, thus avoiding any delays or disruptions to the project’s progress.
11.0 PROGRAM
11.1 PROGRAM SUMMARY
The scope of this project is to build the AL MISHRAQ MAIN WORKS, which will be a combination of residential and office buildings with a low-rise structure, typically comprising three floors and a ground level. Additionally, there will be retail spaces distributed across the building complex, featuring a dedicated food court as per the site plan. The project will also involve the construction of a two-level basement, and upon completion, the built-up area is expected to be approximately 145,000 m2 gross floor area (GFA) and 280,000 m2 built-up area (BUA).
11.1.2 Summary of the Proposed Time Schedule
This time schedule has been developed to ensure acceptable planning, and scheduling, and to provide a work plan that is reasonable and executable. The development of this schedule includes the resource allocation required to meet all completion milestones.
MARCO has developed a CPM schedule in Primavera format, in line with the overall time to completion of 586 working days. It is noted that Contract Documents specify 23 Months as the duration to complete the works, a realistic assessment of the scope for the project requirements.
The scope of work consists of Supply, Construction works Installation, Testing, and Commissioning of the construction of the AL MISHRAQ MAIN WORKS.
Stage 1: from LOA - Permitting and Surveying
• Immediate start of the site surveys and permitting documents
• Immediate start of the hoarding mock-up to allow its approval and start at the earliest.
• Issue of the proposal to locate the video cameras.
• Issue proposals for the design and location of the site offices
Stage 2: From NTP - Hoarding and Survey Reports
The above early activities are deemed critical to the successful completion it allows the clearance to move to the next construction stages:
• Hoarding, gates, advertising, and video cameras completion 30 days from NTP
• Site surveys and Investigations completed 30 days from NTP
Stage 3: After Mobilization works
After completion of Mobilization & General requirements, MARCO will immediately start the construction work.
The sequence of work:
• NTP
• Permits
• Site Preparation
• Construction works
• MEP & Finishing work
• Testing & Commissioning
• Handover
Considerations and Assumption in this Schedule.
The calendar used in this Baseline program comprises the following; weekends (Friday only) 8 hours working day. Public and religious holidays have been added to the calendar
1. Considered 6 hrs. Working during Ramzan
2. Considered EID holidays
3. Considered National Holiday & Foundation Day
Major Programme Milestone
(Table-- Pg 52 of MISK tech doc)
Above mentioned milestones were made part of the schedule to easily see and control the important things that the project needs and give alarm to all users of the things that are important to be started and to be finished.
11.1.3 Preliminaries And General Conditions:
1) Mobilization
a) The mobilization plan comprises several key elements including the provision of supervisory staff, transportation for staff and labor, and construction of temporary facilities to house the workforce during the project.
b) It also includes site facilities and preparation works such as sheds for materials, security site fencing, safety barricades, signage, and other relevant items as stipulated in the General Requirement contract.
2) Procurement and Delivery Phase
a) The procurement and delivery phase involves material submittal-approval, visual mock-up, purchase orders, and delivery of materials to the manufacturer for fabrication, and subsequent delivery of the finished product to the site.
The procurement schedule is aligned with the construction schedule and includes the following cycle:
i) request for quotations
ii) receiving and analyzing quotations
iii) material submittal and approval
iv) placing purchase orders
v) fabrication, transportation
vi) delivery to the site.
Due to the long lead items, delivery dates are strictly monitored to avoid any delays in construction activities.
3) Construction Phase
a) Due to the criticality and time constraints of the project, effective execution and management of the construction phase are vital. The construction works are divided into sections based on the Work Breakdown Structure, including:
i) Enabling Works
ii) Structure to Complete
iii) Finishes
iv) MEP Works
v) Equipment Installation
vi) External Works
vii) Testing & Commissioning, Snagging
viii) Completion & Handover
A zone-wise high-level construction sequence for the project is outlined to facilitate effective monitoring and control.
Working Hours/Calendar Considered in the Programme:
Calendars have been assigned to each activity according to one of the conditions as stated below:
During Normal Days:
• Work Calendar: this is the default calendar, used to represent a normal week and Normal weather conditions covering 6 days with one shift per day with (8) hours per shift.
During Ramadan
• 6-Working Hours for Muslim workers & 8-Working Hours for Non-Muslim workers
During Summer
• 8-Working Hours have been considered during summer days
4) Time Schedule, Milestones Schedule, Engineering, Procurement and Construction Programme, and Critical Path
Please refer to the documents enclosed in the Appendix I, containing:
• Time Schedule Summary
• Milestones
• Engineering, Procurement, and Construction Time Schedule
• Critical Path
5) Long Lead Items Procurement Strategy
Material Submittal will be done 5-6 months earlier from the installation so that any technical issues will be anticipated and resolved within the given period and to prevent any delays.
Some of the material will be submitted for approval earlier as possible in order to expedite procurement and delivery, so that there is no effect on construction-related activities.
6) WBS Breakdown
Project Schedule:
The project schedule has been prepared using Primavera Version 20, encompassing all our scope, quantities, and required resources for various trades.
The following settings have been assigned to all activities:
• Activity Type: Task Dependent
• Duration Type: Fixed Duration & Units
• Percent Complete Type: Physical
Critical Path Activities:
The critical path represents the longest path from the project start to its completion, considering all tasks and their durations. It provides a clear overview of the project’s actual schedule. In this report, the critical activities are defined as those with total float equal to or less than zero. The filtered activities that fall along the critical path of the project are enclosed in an XER format file.
Measuring Progress:
All proposed progress measurement systems, standard milestones, breakdown of progressive elements, and the methodology for tracking progress will be based on an earned value approach. These measures will be reviewed and approved by the Supervising Consultant before implementation.
12. KEY PERSONNEL
The table below presents information regarding the essential personnel intended for employment on the Al Mishraq Main Works project. This information encompasses their qualifications, years of experience, and the suggested positions. The provided names are tentative and will be confirmed upon the contract being awarded.
The CVs of the proposed key personnel are attached in Appendix D.
Sham Warale Project Director
Emad Abdeljawad Project Manager
Youssef Ghazali Construction Manager
Suhaib Waled Construction Manager
Qais Jayyousi Asad Construction Manager
Ahmed Gbril MEP Manager
Ahmad Samir QA/QC Manager
Ahmed Selim QA/QC Manager
Aktar Shabir HSE Manager
Harikrishnan HSE Manager
Mohammed Gama Technical Manager
Mohammed Abdel Technical Manager
Engineer Project Director 30
Manager 25
Project Manager 25
Engineer Project Manager 17
Engineer Project Manager 12
Manager 14
Manager 13
in Science HSE Manager 16
Eng. HSE Manager 17
Eng. Tech. Manager 20
Eng. Tech. Manager 20
Ayman Alrajab Commercial Manager Civil Engineer, MBA Com. Manager 12
Abdallah Gazaleh Project Controls Manager Civil Engineer New Hire 17
Mohammed Rizwan Planning Manager Civil Engineer Planning Manager 18
13. PROPOSED DOMESTIC SUBCONTRACTORS AND SUPPLIERS
As part of our commitment to delivering a successful project, we have carefully selected suppliers and subcontractors based on a number of factors, including project design, specifications, and duration, as well as the durability, ease of operation, and reliability of maintenance operations. Most of our suppliers and manufacturers have a long-standing commercial relationship with us, which ensures the dependability and capacity required for the successful completion of the project.
To give you an idea of the suppliers and subcontractors we plan to work with, we have included an uncomprehensive list of the main materials, equipment, and subcontractors in the following tables. Please note that this list is subject to further material selection and approvals from the Consultant’s representatives.
We believe that having these long-term relationships with our suppliers and subcontractors will facilitate the management of project requirements and construction operations, as well as enable a smoother continuity into facility management once the project is completed.
In addition to the specification of the manufacturers of the materials and equipment for the project, please refer to Appendix G for pre-qualification documents for some of these vendors. If you require any further information or have any questions, please do not hesitate to contact us.
14. HEALTH, SAFETY & ENVIRONMENTAL POLICIES
14.1 HSE POLICY
MARCO (Mohammed M. Al Rashid Co.) is dedicated to safeguarding the health and safety of its employees, clients, visitors, and the wider community, as well as protecting the physical environment in which the company operates. MARCO is committed to complying with OHSAS 18001/45000 & 14001, ILO OSH-200, ISO 45001, and the Saudi Labor Law (SLL) along with its associated Royal Decrees and decisions.
The management and staff of MARCO pledge to:
• Ensure that our services meet the standards and expectations of our clients while ensuring the safety and well-being of our staff and the protection of our assets.
• Prevent any adverse impacts on the environment resulting from our actions.
• Continuously review and improve health and safety performance under top management’s supervision.
• Comply with relevant health, safety, and environmental laws and regulations, both national and international, that apply to our operations.
• Establish zero injuries and accidents as project objectives and targets.
• Prevent accidents and work-related injuries and illnesses.
• Identify hazards, assess risks, and effectively manage them.
• Maintain work equipment in a safe condition and provide a safe system of work and working environment for employees and all individuals working on our behalf.
These commitments will be achieved through:
• Establishing and maintaining a documented Health, Safety, and Environmental Management System (HSEMS) that aligns with national standards such as the Labor Law (Royal Decree No. M/51, 27.09.2005) and Ministerial Decision No. 10/X/W/A/DF, 23.10.1989), as well as international standards (OHSAS 18001, OSHA 1926 CFR, ISO 9001, and ISO 45001).
• Implementing procedures, programs, and guidelines to support the HSEMS.
• Providing the necessary resources for the successful implementation of the management system.
• Communicating the company’s HSE policy and objectives to relevant parties, including employees and clients, and ensuring that line management is committed to the HSEMS.
Hamad Al-Yousef General Manager
14.2 ENVIRONMENTAL POLICY
We strive for continuous improvement in our environmental quality system by practicing responsible procurement, reducing and controlling various forms of waste, preventing pollution, protecting environmentally sensitive areas and natural habitats, and conserving natural resources. To achieve this, we maintain an effective environmental management system that aligns with the requirements of the General Environmental Law, General Authority of Meteorology and Environmental Protection (GAME&P), Saudi Labor Law Section 8, ISO 9001, and Wild de Protected Areas Regulation BS EN ISO 14001:2015.
This framework supports our environmental goals and objectives, including:
• Cultivating a corporate culture of environmental stewardship
• Implementing and developing an environmental quality system
• Conducting environmental risk assessments and preparing project-specific environmental control plans as required
• Ensuring compliance with relevant environmental legislation, regulations, government environmental laws, best practices, and other applicable environmental standards
• Considering and evaluating the environmental impact of planning and operational decision making at MARCO
• Integrating environmental protection into all activities to prevent or mitigate adverse environmental effects
• Providing appropriate environmental information and guidance to employees
• Ensuring awareness of MARCO’s environmental policy among all employees
• Ensuring subcontractors and their employees are aware of and adhere to MARCO’s environmental policy and procedures
• Taking necessary measures to prevent environmental incidents, maximize recycling to reduce waste and discharge, and conserve resources through efficient energy use, emission reduction, waste elimination, and practical recycling
• Pursuing continual improvement in our environmental policy and environmental management system
This policy will be communicated to all stakeholders, employees, and individuals working on our behalf. It is the responsibility of each person to fully comply with the requirements outlined in this policy, particularly by cooperating and conducting their work in a manner that does not jeopardize the environment. To continuously enhance our environmental management system, we will regularly review this policy and its contents to ensure effective implementation.
Hamad Al-Yousef General Manager
14.3 SUSTAINABILITY POLICY
MARCO holds the responsibility of mitigating societal and environmental impacts during the construction and management of facilities. Our commitment lies in conducting our activities in a sustainable manner, adhering to best practices and employing a comprehensive set of subject-specific policies and sustainability codes.
The following are our overarching sustainability objectives:
1. Foster career development, provide opportunities for lifelong learning, and support diverse, engaged, motivated, and competent teams.
2. Create safe, welcoming, and accessible environments for all employees and stakeholders.
3. Encourage internal and supply chain innovation and ideas that generate sustainable value for key stakeholders.
4. Cultivate an inclusive working environment where everyone feels valued and respected.
5. Ensure that our economic sustainability practices meet community expectations.
6. Implement sustainability-focused procurement processes, evaluations, and contractual requirements, incorporating sustainable materials, products, and considerations in project decision-making.
7. Comply with environmental legislation, regulations, and approvals.
8. Minimize waste, impacts on natural and cultural heritage areas, sensitive receptors, water, air, and land, while also reducing resource consumption, including energy and water.
9. Recognize that sustainability leads to economic prosperity and creates value for shareholders, society, customers, and employees.
This policy will be effectively communicated to all employees and individuals working on our behalf. It is the responsibility of each individual to fully comply with the requirements outlined in this policy. We are dedicated to continuously improving our sustainability framework, and therefore, this policy and its contents will be reviewed periodically to ensure effective implementation.
15. EXTERNAL MANAGEMENT AND TECHNICAL ASSISTANCE
For the delivery of the Misk Al Mishraq Main Construction works, MARCO will appoint specialist consultants to provide Engineering and Laboratory services for the following:
• BIM implementation, execution and delivery of models and information assets.
• Third Party Laboratory Testing agents.
This technical submission includes information on additional site temporary facilities, and the following paragraphs provide an overview of the temporary works that will be involved. These works will include the following elements: site offices, warehouses, scaffolding, temporary hoarding and accesses, temporary power and water distribution, temporary lighting, temporary air exhaust, and concrete distribution and stationary pumps.
16. JOINT VENTURE AGREEMENTS
Not Applicable
17. ALTERNATIVE TENDER OPTIONS
Not Applicable
18. TEMPORARY WORKS
This technical submission includes information on additional site temporary facilities, and the following paragraphs provide an overview of the temporary works that will be involved. These works will include the following elements: site offices, warehouses, scaffolding, temporary hoarding and accesses, temporary power and water distribution, temporary lighting, temporary air exhaust, and concrete distribution and stationary pumps.
18.1 Site Office and Accommodations
The site offices proposed for the project are situated east of the project site, adjacent to the laydown area. Detailed plans for the offices and other temporary facilities are provided in Appendix F. The design of these facilities has been based on the ITT requirements and anticipated project needs. Apart from the site offices, the logistics areas will also include open storage areas, warehouses, mock-up and pre-assembly zones, a local equipment maintenance workshop, and ample parking spaces.
As MARCO already owns labor accommodation facilities nearby, with a capacity of over 1,500 people, there will be no need for additional site accommodation facilities. Moreover, a new labor camp capable of accommodating 800 people is currently under construction and is expected to become operational in the second half of 2023. These facilities are located within a 30 km distance from the Misk City Project site, with an estimated travel time of 40 to 50 minutes each way.
18.2 Temporary Water and Power Supply
Detailed plans will be submitted on award of the project, based on the preliminary proposal for the site layout arrangement enclosed in the Appendix F.
19. PRE-QUALIFICATION OF SUB-CONTRACTORS
Enclosed in Appendix G are indicative pre-qualification documents or some of the suppliers, subcontractors, and manufacturers that will be appointed (subject to further selection and approval) for the Al Mishraq Main Works.
20. CONFLICT OF INTEREST
Letter is enclosed in Appendix K.
21. LETTER FROM BANK
Letter is enclosed in Appendix K.
22. STAMPED TENDER DOCUMENTS
Documents enclosed in Appendix B.
23. CONSTRUCTION SUSTAINABILITY PLAN
Marco recognizes and shares the commitment of Misk City to enhance construction sustainability in the Kingdom. Keeping this objective in mind and to further showcase our capability and involvement in this endeavor, we have identified the requirements outlined in the ITT. Although the LEED certification is not currently intended, we aspire to achieve a certification-ready construction.
Both the project team and the Construction implementation plans will address the following requirements, which are further detailed in Appendix E:
1. Construction Activity Pollution Prevention:
• Develop and implement a plan to control erosion and sedimentation.
2. Construction and Demolition Waste:
• Commit to divert at least 50% of construction and demolition waste through reuse and recycling, either within the project or by third-party off-site utilization.
3. Protect or Restore Habitat:
• Consider natural areas in the construction’s mobilization and storage strategy.
4. Water Efficiency:
• Explore the adoption of smart water meters to monitor 100% of water consumption.
5. Smart Energy Systems:
• Consider installing smart energy meters to cover 100% of power connections.
6. Materials and Resources:
• Ensure that a minimum of 25% of materials, based on cost, meet one of the following criteria:
• Purchased from a manufacturer participating in an extended producer responsibility program.
• Bio-based materials meeting the Sustainable Agriculture Network’s Sustainable Agriculture Standard.
• FSC certified wood products.
• Reused materials.
• Materials with recycled content.
7. Solid Waste Management:
• Develop a solid waste management plan, employing separate bins for different types of waste to facilitate reuse, recycling, or sustainable off-site disposal.
8. Organic Waste Treatment:
• Establish a dedicated organic waste management plan to handle organic waste during the construction phase. Compost bins will be used to support the landscaping aspect of the project.
9. Indoor Environmental Quality:
• Low-Emitting Materials:
• Utilize building interior materials (excluding the waterproofing membrane) that meet
the low-emitting criteria based on the CDPH Standard Method.
• Construction Indoor Air Quality Management Plan:
• Implement an indoor air quality (IAQ) management plan for both the construction and preoccupancy phases of the building.
10. Soil and Materials:
• Implement appropriate measures for hazardous waste, materials, lubricants, and fuels, including the creation of bounded areas and ensuring proper disposal of cleanup materials.
11. Air Quality:
• Utilize well-maintained equipment.
• Perform regular maintenance to ensure proper functioning.
• Strictly adhere to appropriate community site speed limits and monitor compliance.
12. Water Quality:
• Develop a plan to address sedimentation and erosion.
• Store hazardous and non-hazardous materials with primary and secondary containment.
• Ensure proper disposal of materials.
13. Noise:
• Use equipment with exhaust sound reduction features.
• Employ low-noise engines and sound enclosures.
• Regularly maintain equipment to minimize noise.
• Provide advance notification when noisy activities are anticipated.
14. Waste Management and Hazardous Materials:
• Designate specific areas for storing fuels, oils, chemicals, or other hazardous liquids.
• Implement spill protection measures.
• Maintain tidy work areas.
• Select materials considering their Material Safety Data Sheets and adhering to OSHA safety requirements for storage and disposal.
15. Traffic and Transportation:
• Regulate traffic, access, and regress, limiting access to working areas and transporting oversized equipment.
• Regulate on-site idle time.
• Control transport of debris.
• Promote safe and defensive driving practices.
• Provide route maps and implement traffic control measures.
• Designate safe areas for pedestrians.
16. Social and Community:
• Provide appropriate personal protective equipment (PPE) for all personnel and ensure adequate training.
• Offer cultural orientation to promote understanding and respect.
17. Monitoring and Reporting Phases:
• Monitor and report on the following aspects:
• Land management and site clearing.
• Soils.
• Equipment and vehicles.
• Water quality.
• Air quality.
• Noise.
Marco recognizes and shares the commitment of Misk City to enhance construction sustainability in the Kingdom. Keeping this objective in mind and to further showcase our capability and involvement in this endeavor, we have identified the requirements outlined in the ITT. Although the LEED certification is not currently intended, we aspire to achieve a certification-ready construction.
Both the project team and the Construction implementation plans will address the following requirements, which are further detailed in Appendix E:
1. Construction Activity Pollution Prevention:
• Develop and implement a plan to control erosion and sedimentation.
2. Construction and Demolition Waste:
• Commit to divert at least 50% of construction and demolition waste through reuse and recycling, either within the project or by third-party off-site utilization.
3. Protect or Restore Habitat:
• Consider natural areas in the construction’s mobilization and storage strategy.
4. Water Efficiency:
• Explore the adoption of smart water meters to monitor 100% of water consumption.
5. Smart Energy Systems:
• Consider installing smart energy meters to cover 100% of power connections.
6. Materials and Resources:
• Ensure that a minimum of 25% of materials, based on cost, meet one of the following criteria:
• Purchased from a manufacturer participating in an extended producer responsibility program.
• Bio-based materials meeting the Sustainable Agriculture Network’s Sustainable Agriculture Standard.
• FSC certified wood products.
• Reused materials.
• Materials with recycled content.
7. Solid Waste Management:
• Develop a solid waste management plan, employing separate bins for different types of waste to facilitate reuse, recycling, or sustainable off-site disposal.
8. Organic Waste Treatment:
• Establish a dedicated organic waste management plan to handle organic waste during the construction phase. Compost bins will be used to support the landscaping aspect of the project.
9. Indoor Environmental Quality:
• Low-Emitting Materials:
• Utilize building interior materials (excluding the waterproofing membrane) that meet the low-emitting criteria based on the CDPH Standard Method.
• Construction Indoor Air Quality Management Plan:
• Implement an indoor air quality (IAQ) management plan for both the construction and preoccupancy phases of the building.
10. Soil and Materials:
• Implement appropriate measures for hazardous waste, materials, lubricants, and fuels, including the creation of bounded areas and ensuring proper disposal of cleanup materials.
11. Air Quality:
• Utilize well-maintained equipment.
• Perform regular maintenance to ensure proper functioning.
• Strictly adhere to appropriate community site speed limits and monitor compliance.
12. Water Quality:
• Develop a plan to address sedimentation and erosion.
• Store hazardous and non-hazardous materials with primary and secondary containment.
• Ensure proper disposal of materials.
13. Noise:
• Use equipment with exhaust sound reduction features.
• Employ low-noise engines and sound enclosures.
• Regularly maintain equipment to minimize noise.
• Provide advance notification when noisy activities are anticipated.
14. Waste Management and Hazardous Materials:
• Designate specific areas for storing fuels, oils, chemicals, or other hazardous liquids.
• Implement spill protection measures.
• Maintain tidy work areas.
• Select materials considering their Material Safety Data Sheets and adhering to OSHA safety requirements for storage and disposal.
15. Traffic and Transportation:
• Regulate traffic, access, and regress, limiting access to working areas and transporting oversized equipment.
• Regulate on-site idle time.
• Control transport of debris.
• Promote safe and defensive driving practices.
• Provide route maps and implement traffic control measures.
• Designate safe areas for pedestrians.
16. Social and Community:
• Provide appropriate personal protective equipment (PPE) for all personnel and ensure adequate training.
• Offer cultural orientation to promote understanding and respect.
17. Monitoring and Reporting Phases:
• Monitor and report on the following aspects:
• Land management and site clearing.
• Soils.
• Equipment and vehicles.
• Water quality.
• Air quality.
• Noise.
24. BIM IMPLEMENTATION PLAN
24.1 FORWORD
The purpose of this section is to establish the strategy of the BIM Execution Plan for the Misk City Development – Al Mishraq main construction works. This document is prepared in accordance with international standard requirements, addressing the EIR and the project goals for collaboration and information modelling. Moreover, it provides details on how the deliverables stated in the EIR are to be achieved and the responsibility assignment and allocation of said deliverables according to discipline and specialty. The Contractor’s team will update this document upon contract appointment to include additional details explaining how to meet each deliverable requirement.
Since the Contractor proposes a specialist Consultant for the delivery of the EIR requirements, this document further intents to demonstrate and ensure that the appointed party develops the project and its phases (Construction and handover) in line with the project needs.
24.2 APPLIED STANDARDS AND DOCUMENTS
To establish a consistent approach to collaboration, the Contractor confirms the compliance with the guidance as described in the Project’s EIR, and the below listed recognized standards and best practice documents will be followed and implemented during all stages of the project.
Used Standards table:
BS EN 19650-1
BS EN 19650-2
RIBA Plan of work
NBS BIM Object Standards
24.3 PROPOSED PROJECT TEAM AND ORGANIZATIONAL CHART
The Contractor and Specialist Consultant will assign to the project (either on-site or offsite) several experienced professionals that will ensure the achievement of the BIM goals, project deliverables and warrant the establishment of the correct workflows, procedures, and communication protocols.
24.3.1
Organizational Chart
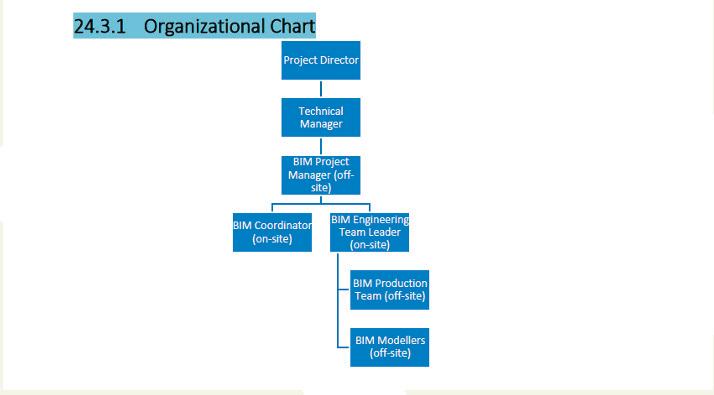
24.3.2 Organizational Roles and Responsibilities
BIM Project Manager
• Prepare the (BEP).
• Pre-model Setup.
• Establish standards and methodology.
• Develop server requirements and resolve conflicts to ensure successful integration for all BIM Model contributors.
• Verify BIM capabilities of the Contractor’s team.
• Develop processes for transferring and accessing Model files
• Establish access rights.
• Negotiating, developing and enforcing the Project Protocol.
• Prepare BIM protocols, establish Standards and BIM procedures for Contractor, Employer, Employers Representative and Assistant contribution and access to models, their security & stability and getting revisions incorporated.
• Create BIM file set-up and management.
• Provide template Files.
• Clearly define a protocol for file transfer and handling.
• Establish and maintain a process for change documentation and communicating the change.
• Provide a method and format for identifying clashes, documenting, resolving and revisions to the BIM model.
• Establish standards for, coordinate and ensure the quality of contributions to the BIM models by other parties, including by the Employers Representative and the Contractor.
BIM Coordinator
• Enforce the BEP.
• Create, maintain and manage a single point central database that hosts all models and their content in direct control of the BIM Management.
• Receive and manage the construction phase information provided by the contractor’s BIM models.
• Enforce reliability of the BIM Model’s information so that it is an accurate representation of as built construction.
• Regularly audit, integration and validate information to ensure BIM model is robust.
• Manage quality and quantity model information.
• Manage model updates.
• Provide clash detection.
• Ensure the Contractor delivered models have standardized properties.
• Manage the health of the files and provide periodic file stability and integrity checks.
• Maintain a data base of all BIM elements, standards, families and 2D / 3D content.
• Coordinate submission and exchange of Models.
• Manage access rights.
• Facilitate extracts & exports.
BIM Engineering Team Leader
• Set up Model according to the BIM Execution Plan.
• Create components not provided by others.
• Provide content, families & annotations as required for each Level of Development.
• Provide 2D drafting details.
• Establish, create and maintain drawing sheets & visibility settings.
• After review and approval incorporate all updates, change, revisions, clash detections and BIM requests for information into the models.
• Integrate Contractor models into the BIM model.
• Maintain model storage and security.
• Regularly back up Model and maintain back up in a secure and independent location from the model storage.
• Collect incoming Models.
• Log incoming Models.
• Validate that files are complete and usable and in compliance with applicable protocols.
• Maintain record copy of each file received.
• Collect Model files and make available for viewing.
• Perform clash detection in accordance with established protocols and issue periodic clash detection reports.
• Maintain Model archives and backups.
BIM Production Team
• Suggest and Nominate Coding, Naming, Numbering for BIM Platforms and Work sets.
• Develop shared data and relationships between models e.g. grids, floor levels, shared project coordinates.
• Ensure that all the procedures for Information Exchange are defined and implemented.
• Confirm that all the project team members are following BIM Execution Plan.
• Arranging QC/QA meetings and agendas.
• Pre-Planning each BIM creation considering model content, level of details, format and party responsible for updates plus the distribution of the model and data to various parties.
• Participating in all major BIM activities as required by the team.
• Certify that the project is based on a company Protocols & Standards.
24.4 MAIN OBJECTIVES
S/N Objective
BIM Process/Use mapped
1 Use BIM to inform the design & construction program and to review the design at key project phases to ensure complinace to program. Construction system design
2 Vendor information to be prsent in BIM, subject to vendor contractual obligations. As built modelling, CObie and Asset handover
3 Management of all project information, procedures and correspondences through BIM environment using models and CDE. Construction system design
4 Use appropriate tools and methods to address clash control and omitting it. 3D coordination
5 BIM to inform design & construction progress. Construction system design
6 Verify Quantities for costing purposes. BOQ extraction
7 Fabrication and drawings approval using BIM extractions and CDE gates. Shop drawing
8 LOD 500 at the end of project - Project handover to FM. As built modeling
9 Facilitate decision making process for any changes or major issues. Construction system design
10 Clash rnditions and discrepencies to be fast highlighted and resolved. 3D coordination
11 Facilitate quantity extraction/validation and drawings production. BOQ extraction
12 Virtual models for all project disciplines and facilities. Construction system design
13 To enable the transfer of project data into data management during operation. As built modeling, COBie and Asset coordination
14 Better collaboration and communication using CDE among all project stakeholders. Construction system design, 3D coordination
15 Better quality for extracted data which facilitate all project works & activities. Phase planning (4D modelling)
16 Visualization for all required data like anlysis and constructability. Construction system design, 3D coordination
24.5 SOFTWARE TOOLS AND INTEROPERABILITY
24.5.1 Software Tools
The following software tools will be used in delivering the EIR requirements:
BIM Use
Architectural modeling
Structural modeling
MEP modeling
Infrastructure modeling
Software
Autodesk Revit
Autodesk Revit
Autodesk Revit
Autodesk Civil 3D
4D modeling Navisworks
3D coordination Navisworks
Clash detection Navisworks
To establish a consistent approach to collaboration, the project team will keep consistent communication and collaboration between all discipline by sharing BIM models regularly in various file formats (Native, NWC and IFC) and notify team members of any change.
3D coordination shall be using Navisworks software in which model review will be held as well as coordination review and clash detection reporting.
24.5.2 Workflows and Procedures
The proposed workflow for the delivery of the BIM requirements is presented in the following diagram:
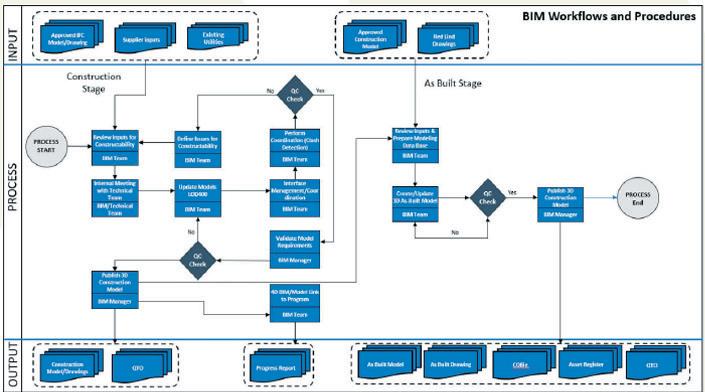
24.5.3 Interoperability
The Contractor will comply with the information exchange format requirement, mentioned in the EIR and commit to the OpenBIM™ standards, providing all BIM submissions in three formats: the native format, which depends on the agreed tool selected by the author of the information, Naviswork format (NWC/NWD) and the IFC format.
24.6 BIM COLLABORATION
MISK will provide the CDE (Aconex) to its project team members as needed. The Common Data Environment (CDE) is the place where to hold all project information, data, processes, and procedures. It acts as single sources of truth at any time of project, it enables to control and monitor data changes, history, and revisions.
The CDE will contain:
• Graphical Data (models, drawings, IFC, photographs, video, etc.)
• Non-graphical Data (schedules, databases, COBie, etc.)
• Documents (contracts, minutes, RFI’s, brief, specifications, reports, BOQ, inspection plans, commissioning certificates, product data sheets, user manuals, etc.)
Using the agreed CDE (Aconex) for sharing the project information and deliverables, gives the Employer, PMC, and Supervision Consultants the ability for e-view and e-review models and BIM uses.
Meetings will be conducted periodically and whenever needed. Below are some of the proposed meetings:
Meeting Name Occurance
BIM Initiation Meeting (Kick off) Once
BEP Demonstration As requested
BIM Workshop Meeting
BIM Coordination Meeting
BIM Validation Meeting
BIM Initiation Meeting:
As requested
B-monthly
As requested
The purpose if this meeting is to establish the principles of the BIM adoption, scope and ambition of the project, setup of the BEP, and to agree when future meetings will be held.
BIM Execution Plan Demonstration:
After the initial kick-off meeting, the team shall clearly understand who will be responsible for the defined tasks, and in what sequences the BIM Uses will be executed. The responsible parties for the Level One map shall clearly document and distribute it to the project team for review prior to the following meeting. Each responsible party for the specified BIM Uses shall also draft their workflow prior to the Design BIM Project Execution Process meeting.
BIM Workgroup Meeting:
Meeting to track the progress of BIM implementation on the project in the context of the BEP. This meeting shall be used as a mechanism to identify forthcoming challenges and agree a proactive solution. Proposed Agenda would be as follows:
• BIM process
• Data requirements within the project model requirements within the project CDE requirements
• Models
• Common Data Environment
BIM Coordination Meeting:
After the Design BIM Project Execution Process meeting, the team must focus on developing the information exchanges. Each responsible party for an exchange shall take the lead in developing the information exchanges. The authors of the information exchange will need to coordinate with the information receivers to ensure that they have developed consistent information exchanges with minimal inconsistencies to discuss. The team members shall also prepare for the discussions regarding infrastructure requirements which will occur in Meeting Three. Team members shall compile examples of typical methods that they have used or wish to use on the project to share with the team.
Once the meetings are complete, the BIM Project Execution Plan shall be distributed to all parties and approved as appropriate for the project and contracting structure. Team members shall ensure that the plan monitoring and updating procedure is implemented into the project controls system.
BIM Validation Meeting:
Meeting to review and discuss deficiencies in model geometry and data identified during the model validation checks undertaken by the BIM Validator. Agenda:
• Modelling progress, where everyone is and what they have been doing in terms of modelling • Go through outstanding actions from previous minutes
• Collaboration, things we are working on together as a team
• Technical, dealing with any technical issues the team are experiencing
• Scopes and contracts, finalizing and reviewing progress against the BXP
• Validation goes through checks and assign responsibility and timescales to resolve issues
• Ascertaining whether the design teams need any additional support going forward to help them compete required tasks
24.7 DATA PLANNING AND DOCUMENTATION
24.7.1 Responsibility matrix
Marco confirms its commitment confirms to manage, co-ordinate and deliver offsite manufacturing and onsite Construction in accordance with the Construction Programme and resolution of Project Queries from site as they arise, and to furnish information as set out in the Responsibility Matrix incorporating Information exchanges in accordance with Project Programme. Liaise with Project Teams as required.
The scope will include the delivery of the BIM uses as follows:
• Cost estimation
• 4D Modelling (BIM+Programme)
• 3D Coordination
• Logistics Planning
• Construction System Design
• Ownership of Asset Register
• Cost Control and Monitoring
24.7.2 Master Information Delivery Plan (MIDP)
The Master Information Delivery Plan (MIDP) is a primary plan which is used to manage the delivery information during the project lifecycle. It will be developed by the project delivery manager in collaboration with the task team managers and then used by the project delivery manager to assist in the delivery of project information during the project. It shall be addressed on the BIM Execution Plan.
Information deliverables which may be listed in the MIDP include (but are not limited to):
• Models
• Drawings or renditions
• Specifications
• Equipment schedules
• Room data sheets
• Procurement packages
• Reports
• Schedules
24.7.3 Task Information Delivery Plan (TIDP)
The Task Information Delivery Plan (TIDP), is federated lists of information deliverables by each task, including format, date and responsibilities. It is the responsibility of each task team manager to compile their own TIDP which then assist in the development of the MIDP. Each task shall have a corresponding milestone that aligns to the overall design and construction program, taking into consideration any sequencing requirements to produce the information.
Each task shall also detail the responsibility of each supplier’s information and show the responsibility for the preparation of project documents transfer from one team to another.
24.7.4 Levels of development (LOD)
Marco will follow MISK’s Element level of detail catalogue (MC-PH01-SIW-00005-MSKPLNBIM-000009) in accordance with the following:
Stage
Construction
As Built
LOD
Once
LOD500 Model elements with actual size, shape, location and orientation required for construction representation. Space reservations and/or clearance required for installation, operation and maintenance identified. Final details, such as fixtures, connections, placeholders or supports and temporary works required for site installation and fabrication are captured. Onsite assembly / construction for bespoke items cptured.
24.8 DELIVERABLES
24.8.1 List of deliverables
The delivery of project BIM uses will be performed as per MISK requirements as follows:
• Cost estimation.
• 4D Modelling (BIM+Programme).
• 3D Coordination.
• Logistics Planning.
• Construction System Design.
• As-Built Modeling.
• COBie and Asset Handover.
Detailed list of deliverables will be submitted in the appropriate section of the postappointment BEP.
24.8.2 Project Information Model (PIM) delivery strategy
The project information model (PIM) supports the delivery of the project and contributes to the Asset Information Model (AIM) to support asset management activities. A PIM should also be stored to provide a long-term archive of the project and for auditing purposes.
The project team will establish processes and procedures to cover the following aspects of creating and maintaining the PIM for:
• Requirements for information and data maintenance, including version control, integrity checks, validation against the PIR (Project Information Requirements).
• Requirements for information and data maintenance in accordance with the EIR (Employer Exchange Requirement).
24.8.3 Assets Information Model (AIM) delivery strategy
The asset information model (AIM) supports the strategic and day-to-day asset management processes established for the project. The project team will establish processes and procedures to cover the following aspects of maintaining the AIM:
• Requirements for information and data maintenance, including version control, integrity checks, validation against the AIR (Asset Information Requirements) and other assurance activities.
• Requirements for the generation, capture or importing of the identified maintainable assets information and data.
• Requirements for the storage of information and data according to integrity, security and confidentiality requirements.
24.9 STANDARD METHODS AND PROCEDURES (SMP)
24.9.1 Volume strategy
The main purpose of segregating models is driven by performance; therefore, the BIM execution team party will divide the models by building, levels and disciplines in accordance with project size and complexity to keep the models accessible and maintainable.
24.9.2 PIM origin & orientation
The project execution team will use the following in terms of measurements and coordinate system:
• Coordinate System:
• Zone:
• Horizontal Units of Measure:
• Vertical Units of Measure:
• Horizontal Datum:
• Vertical Datum:
24.9.3 Naming conventions
All shared and published project information file container naming will comply with project’s naming convention standards and to be as follows:
• CAD file naming convention:
• BIM file naming convention:
24.9.4 Exchange format
For each of the project deliverables, the lead appointed party will deliver information in the formats listed in the table below:
Type
Documents
2D Drawings
3D models
Quantity takeoff
Project Control
Site management mode
Example
BEP
Format
Docx, PDF Reports Docx, PDF, Xlsx
Shop Drawings
Illustrations and sketches
Construction model
Asset model
Federated model
Coordination model
Construction Qty model
Native file format, PDFm DWFx, .dwg
Native file format, PDFm DWFx, NWX, NWD, IFC
Native file format, TBA Schedules Xlxs
4D model
5D model
Logistics planning
Crane movement
Native file format, TBA
Native file format, TBA
Native file format, TBA
Native file format, TBA
25. SIGNED LETTER OF ACCEPTANCE OF VOLUME 2 – FORM OF CONTRACT
To:
Mr. Paul Mincher Misk City Company
Riyadh, KSA
Date: 25-10-2022
Dear Sir,
We the Undersigned, having examined the tender documentation, accept the terms and conditions in the Form of Contract enclosed in Volume Two without qualification.
Yours faithfully,
(Deputy Bidding Manager)
Duly authorized to sign on behalf of:
Messrs Mohammad M. Al Rashid for Trading & Contracting Co. Ltd. MARCO
KEY PERSONNEL EXPERIENCE
Name: Ahmed Samir Abdullah
Nationality: Egyptian
Mother tongue (other languages): Arabic (Fluent), English (Fluent)
Areas of Expertise, with years of experience in each area (also identify years of post-graduate experience):
14-years’ experience in different civil & fit out fields that include concrete works & Royal finishing. full knowledge of ISO 9001: 2015 Quality standards, full experience that QA/QC engineer needs to know about building systems development (ISO Certified Lead Auditor 9001:2015).
Year of Birth: 1987
Academic Qualifications:
Academic Qualification Date Certified
Qualification 2009
B.sc Civil Engineering
• Introduction of ISO 9001:2015
• IRCA ISO 9001:2015 qualified LEAD auditor
• CAD program (AUTOCAD). 2D
• Sap, E-Tabs, safe
Professional Registration (including jurisdiction)/ Affiliations/licenses
Current role and years in such role:
Saudi Council of engineering
QA/QC Manager, 4 Years
Role Proposed on this Project: QA/QC Manager
List of Employers (current and previous; time period employed at each firm):
Name of Institution (country)
Shoubra Faculty of Engineering, Banha University, Egypt
Key Relevant Experience (minimum 5 projects):
Employers
MARCO
DEPA Interiors
Location Years
Riyadh, Saudi Arabia Oct 2019 to present
Riyadh, Saudi Arabia Sept 2017 to Aug 2019
Al-Arrab Contracting Co. Riyadh, Saudi Arabia Aug. 2015 to Aug 2017
Al Mayal Construction Co. Riyadh, Saudi Arabia April 2011 to July 2015
Hassan Allam Co.
MARCO - QA/QC Manager
Start From: 10/2019 to Present Job Responsibilities
Cairo, Egypt
Dec.2009 to April 2011
• Initiate quality manual for the company, Initiating the IMS for the company.
• set up and maintain controls and documentation procedures.
• Preparing PQPs for ongoing project, Manage and assist all sites QC teams.
• Publishing and maintain the quality forms, Perform Quality Audits and create audit reports
Key Relevant Experience (minimum 5 projects):
Depa Interiors MOI Head quarter Jeddah
Job Title: Senior QA/QC Engineer (Acting Manager)
Start From: Sept 2017 To Oct. 2019.
Job Responsibilities:
• In charge of all project quality documentation, standards and implementation
• Supervision of All my company scope in Royal finishing such as veneer wood panels installation, Marble installation wall and floor, Acoustic and fire-resistant door installation, Special paint finishes, mosaic tile installation, Mirrors, upholstery panels, carpets, decorative false ceiling and Precast cladding.
• Work execution as per PQP, WMS.
Al-Arrab Contracting Company: (KAP-4) project
Job Title: QA/QC Engineer
Start From: 8/2015 To 8/2017
• Ensure all site works as per method of statement.
• Responsible of quality implementation in building for all executed works steel rebar’s , Concrete works , wooden form work for casting, water isolation execution, concrete frames, concrete pouring, masonry works, plaster works, decorative wooden works, marble flooring, precast cladding and Paintings.
Al Mayal Construction Company
Job Title: (QA/QC Engineer)
Start from: 4/2011 to 7/2015.
Ensure all site works according to WMS&ITP, Micro tunneling procedure and inspections, Responsible for general onsite technical and engineering matters.
Make Look ahead schedule for the work.
Hassan Allam Sons, Egypt
Job Title: civil Site Engineer for The village mall project from (12/2009 – 4/2011)
• Responsible for general onsite technical and engineering matters. Responsible for steel arrangement, shutters and concrete
EXPERIENCE AT CURRENT EMPLOYER
Project Name and Location:
Specific responsibilities of Employee on each Project:
MARCO (Head office) Manage all ongoing projects quality Projects locations (Diriyah, KAFD, KACST).
• Initiating the IMS for the company.
• set up and maintain controls and documentation procedures.
• Preparing PQPs for ongoing projects. Manage and assist all sites QC teams.
• Publishing and maintain the quality forms. Internal audit schedule.
• Perform Quality Audits and create audit reports
• Issuing CAR’s for the concerned departments and following to close it.
• Follow all projects MS & ITP’s Look ahead.
• Adhere with quality standard and with company policy to achieve quality objectives
APPENDIX C - MARCO INTERGRATED MANAGEMENT SYSTEM
Project Cost Management
Project cost management includes the process involved in estimating, budgeting, and controlling costs so that the project can be completed within the approved budget.
1. Estimate costs: the process of developing an approximation of the monetary resources needed to complete the project activities.
2. Determine budget: the process of aggregating the estimated cost of individual activities or works package to establish an authorized cost base line.
3. Control costs: the process of monitoring the status of the project to update the project budget and managing changes to the cost base line.
Project cost control includes:
• Influencing factors that impact changes to the authorized cost baseline.
• Ensuring prompt action on all change requests.
• Managing actual changes as they occur.
• Preventing cost expenditures from exceeding authorized funding, both on a per-period and overall project basis.
• Monitoring cost performance to identify and analyze variances from the approved cost baseline.
• Monitoring work performance in relation to funds expended.
• Excluding unapproved changes from reported cost or resource usage.
• Communicating approved changes and associated costs to relevant stakeholders.
• Taking action to mitigate expected cost overruns and bring them within acceptable limits.
Project Cost Management Overview B-Estimate cost
1-Inputs
1.1 Scope base line
1.2 Project schedule
1.3 Risk register
1.4 Organizational process assets
2-Tools & technique
2.1 Expert judgment.
2.2 Project management estimating software.
2.3 Vendor bid analysis.
2.4 Other methods for estimating like analogous, three points, parametric, contingency allowances.
3-Outputs
3.1 Activity cost estimates
3.2 Basis of estimates
3.3 Project documents update
1-Inputs 1.1 Activity cost estimates
1.2 Basis of estimates
2-Tools & technique
2.1 Cost aggregation
2.2 Reserve analysis
2.3 Expert judgment
2.4 Funding limit reconciliation
1-Inputs 1.1 Project management plan
1.2 Cost performance base line
1.3 Project funding requirement
1.4 Organizational process assets
2-Tools & technique
2.1 Earned value management.
2.2 Forecasting
2.3 To complete performance index ( TCPI )
2.4 Performance review
2.5 Variance analysis
2.6 Project management soft ware
3-Outputs
3.1 Activity cost estimates
3.2 Basis of estimates
3.3 Project documents update
3-Outputs
3.1 Work Performance measurement
3.2 Budget Forecast
3.3 Organizational process assets update
3.4 Change request
3.5 Project management plan update
3.6 Project documents update
Quality Control Program
1) QUALITY POLICY
• The company is committed to meeting project specification requirements and assumes responsibility for compliance with these requirements. The Quality Control Program outlines the quality system and aims to establish effective practices and procedures for the project. Its ultimate goal is to ensure that the items and services provided meet the client›s needs, satisfy specified quality requirements, and adhere to contractual and legislative commitments.
• All company personnel, including management, are required to read and understand this Quality Program and fully commit to delivering the required quality through the application of the quality assurance system. Any issues or disagreements related to the implementation of this QC program within the organization will be referred to the project manager for final resolution, ensuring alignment with specified requirements.
• This Construction Quality Control Program (CQCP) will be implemented to ensure that remedial and construction procedures are performed in accordance with the plans and specifications outlined in the contract. The CQCP serves as a mechanism to maintain effective quality control at the O&M Projects Site.
• The quality control measures outlined in this program encompass the quality control organization, methods for performing, documenting, and enforcing quality control operations for both the primary Contractor and Subcontractors (including inspection and testing), inspections to be conducted, and protocols for implementing corrective actions.
• The overall management of the CQCP will be entrusted to the Contractor›s Quality Control Manager (QCM). The QCM will possess the authority to oversee all construction quality control (CQC) matters and will be responsible for ensuring that all materials and work conform to the contract specification requirements. Inspection and testing firms will be available to support the QCM in verifying the conformity of all work aspects with the contract requirements. Any deviations from the CQCP will be promptly reported by the QCM to the On-site Project Manager.
2) PURPOSE
• The Construction Quality Control Program (CQCP) serves the purpose of providing an comprehensive overview of the Company›s Quality System and outlining the structure and implementation of the Quality Control System. Establishing and implementing effective Quality Control Systems on any project is crucial to ensure the control, inspection, testing, and documentation of all aspects related to procurement, fabrication, and installation in accordance with the Contract Drawings and Specifications. These systematic procedures, applied in a logical construction sequence, guarantee that the products or services meet the required quality standards.
• The objective of this Quality Control Program is to meet all system requirements of International Standards and the Client Guideline Specification for Construction Quality Control. It encompasses the establishment, documentation, and maintenance of policies, procedures, practices, and associated methods. Additionally, it defines responsibilities and authorities to achieve three specific objectives:
• To serve as a roadmap that provides direction and meaning to our mission, specifically the project objective for the final turnover to the Client.
• To reflect our Statement of Quality Commitment.
• To maintain a documented Quality Control Plan that enables periodic assessments and continual improvement.
Health and Safety Management Programs
(1) Management programs are established and maintained to achieve all the objectives and targets of MOHAMMED ALRASHID TRADING & CONTRACTING CO.
(2) This management program shall include;
a) Designation of responsibility for achieving the objectives and targets at each function and level of the organization.
b) Methodology and time/frame when they are to be achieved.
(3) The management program(s) shall be reviewed at regular intervals as scheduled and updated. Where applicable for specific projects, the program(s) shall be incorporated as per the project requirements.
(4) Project Manager has responsibility to establish the management program to achieve the project objectives and targets.
(5) Project HSE Manager shall check and monitor timely the performance of the management program established within each discipline of the project organization.
Environmental System
(1) Project manager shall establish and maintain a set of procedures to protect the environment from adverse effects resulting from activities performed under the project requirements.
(2) Project Manager shall undertake an environmental review in relation to the works to identify, evaluate, recommend, and apply mitigation measures to deal with the adverse consequences of any environmental impact resulting from customer or vendors/ subcontractors’ permanent and temporary activities during the works.
(3) Engineering Manager shall identify the potential environmental effect and impact of specific processes at design phase based on the contract requirements. This result shall be incorporated into the design activities such as EIA (Environmental Impact Assessment), ENVID(Environmental Impact Identification) and noise protection studies with noise map etc.
(4) The Site Manager shall identify the environmental effects and impacts on the construction site. This result shall be incorporated into the construction site activities such as incidents and potential emergency situations, potential impact on local communities, waste management including waste stream, construction camps and lay down areas including subcontractors’ compounds, handling hazardous materials and the like.
(5) Environmental management shall be documented to ensure that its documents and records are identified, verified, up-to-date and available at point of use to support the active work as part of the safety case.
(6) The process to identify the significant environmental effects and impacts in association with the activities at operating units includes;
• Emissions to air
• Discharges into water
• Waste management including disposal of fluids from drilling activities.
• Contamination of soil
• Noise Protection with Noise Map
• Hazardous Materials
• Use of energy and natural resources
• Acoustic Job Specification
• Equipment Noise Control and Abatement
• Vegetation Clearance
• Redirection of water flow
• Re-instatement and Commissioning
• Impact on local communities including other issues.
(7) Significant environmental effects and impacts are determined by a combination of several criteria;
• Frequency
• Consequence to the environment (with sensitivity of surroundings)
• Operational management
• Compliance with local laws and regulations
Risk Assessment
Purpose
This procedure is to identify the expected risks during project execution, estimate the severity level, and provide the systematic and standard method for hedge plan.
Application
This procedure is applicable to identify, analyze, report and manage the risks on MOHAMMED ALRASHID TRADING & CONTRACTING CO. project site.
Responsibilities
4.1 Site Manager
Site Manager has the final responsibility to ensuring that risk assessment is carried out for each activity on the project as per this procedure and is done without endangering health and safety in accordance with the local legislation, client’s requirements and stipulations laid down in the HSE management system document.
4.2
Site HSE Manager
The Site HSE Manager shall be responsible for monitoring the application of this procedure by regular HSE Audits.
He shall further provide support in the acquisition of suitable training courses and material.
4.3
Field Construction Manager/ Field Engineer
The Field Construction Managers/ Field Engineer shall be responsible for the implementation of this procedure and for ensuring and reviewing that all necessary risk assessment are undertaken by the relevant sections on the project and that all actions arising from the risk assessment are fully implemented. He shall be responsible for ensuring that personnel who are required to undertake risk assessments have received the required training.
4.4 Site HSE Supervisor
He shall ensure that all risk assessments are adequately coordinated, documented, filed, reviewed and followedup. All of these sub-activities are essential elements of the risk management process.
The responsible persons for the relevant sections shall be responsible for establishing a plan and scope for risk assessment to be carried out within the area of responsibility.
Shall ensure that all supervisors and HSE personnel at site shall contribute to the risk assessment performance within their area of responsibility and ensure that any follow-up and lessons learned are passed to the
workforce via safety meeting and toolbox talks. All supervisory staff will be informed of the findings of any risk assessments which have been carried out on them, their work, equipment they may use and activities they may be involved in. Instructions for any subsequent correction actions shall be advised and implemented.
4.5
Subcontractor Site Manager
The Subcontractor Site Manager shall be responsible for the preparation of risk assessment and for ensuring all actions arising from the risk assessment are fully implemented.
He shall be responsible for ensuring that personnel who are required to undertake risk assessments have received the required training.
Definitions
5.1 Risk
Risk is the measure both of the likelihood and the severity of a specified untoward event caused by an identified hazard.
5.2 Hazard
A hazard is a situation which poses a level of threat to life, health, property or environment. Most hazards are dormant or potential, with only a theoretical risk of harm, however, once a hazard becomes ‹active›, it can create an emergency situation.
5.3 Risk assessment.
A task that assesses risk in terms of both severity and probability
Procedure
6.1
Identification of Hazards
6.1.1 The following procedure shall be kept to identify the risks most effectively and consistently within limited time and budget:
(1) To make check list by investigation of risks in the project.
(2) To classify and express systematically the risk factor with consistent criteria.
(3) To summarize the risk, which shall be deeply considered at the risk analysis stage, and decide the major risk parameter, which shall be used for set-up risk analysis model.
6.1.2 The check list for comprehensive risk factor shall be made by not only investigation for risk occurrence case at past similar project but also reflection of subjective decision and experienced acknowledgement at working level, hearing of expert opinion on the field, and survey of opinion in the related team.
6.2 Evaluation of Risks
6.2.1 Hazards identified for each task subject to risk assessment will be analyzed to determine the risk value and level which should be controlled accordingly. Definition of the terminology associated with risk assessment is as follows.
1) Severity: The outcome of an event especially as relative to an individual, asset, reputation, or environment.
PROJECT REFERENCE SHEETS
Madinah Gate
Details:
Owner: Madinah Gate Real Estate Development Co.
Consultant: Khatib & Alami
Location: Madinah
Built Up Area: 83,900 M2
Project Brief:
This is a turnkey project that incorporates a basement area, retail, and hotel for an approximate 83,900 sqm built-up area, including two basements, ground, plus 20 floors and bus station. Works include the construction of all retail, offices, administration offices, 325 hotel rooms, and a restaurant. This takes in all civil, architectural, finishes, and MEP, plus external hard landscaping.
Imam Saud University: Supporting Academic Area and Car Parking
Details:
Owner: Ministry of Higher Education – Imam University
Consultant: TYPSA
Location: Riyadh
Built Up Area: 321,899 M2
Project Brief:
The Supporting Academic Area and Car Parking consist of a rectangular building with six floors above ground level and three underground levels. The first two floors above the ground level are designed to accommodate general purpose areas while the four remaining upper levels are designed to house offices and administration areas, supporting deaneries, scientific centers, and societies.
The gross floor area of the resulting multi-story building is 321,899.16 m2 and is conceived as a collection of eight independent buildings working as a whole and linked together by circulation areas surrounded by on singular facade
Samhan Heritage Hotel
The Details:
Owner: Diriyah Company
Consultant: Currie Brown
Location: Riyadh
Built Up Area: 31,200 M2
Project Brief:
The Samhan Heritage Hotel is being built in Samhan District, Ad-Diriyah, on around 14,000 sqm. The lot is located in the Buffer Zone of a UNESCO Site within a prestigious site in Riyadh.
The project will consist of approximately 31,200 sqm of0 built-up area, composed of 13 buildings and a cluster of Mud houses, including 142 Hotel guest rooms, food and beverage outlets, health club and spa facilities, Meeting facilities, retail, landscaping, car parking and a Mosque.
Diriyah Art Futures
Details:
Owner: Diriyah Company
Consultant: Faithful+Gould / Saudi Consulting
Location: Riyadh
Built Up Area: 13,000 M2
Project Brief:
The Scope of Work consists of supply, construction, installation, startup testing and commissioning of the Addiriyah Art Centre including the demolition and excavation works, procurement and supply of all materials, provide all equipment, labor and materials necessary to perform and coordinate all shop and coordination drawings, temporary works (including design), fabrication, delivery, installation and erection, construction support (including obtaining all required trade specific permits), testing, start-up and performing the activities necessary to complete the Work.
Green Riyadh: Landscape of a Neighborhood Olaisha and Middle Uraija
Details:
Owner: Royal Commission For Riyadh City
Consultant: Parsons Co.
Location: Riyadh
Built Up Area: Olaisha: 2.22 KM2 Al Uraijah: 8.07 KM2
Project Brief:
The project involved site preparation, including rubbish clearance, vegetation removal,
and tree protection. Earthwork included excavation for tree pits and shrubs, with soil preparation for landscaping. Soft landscaping involved precise planting of trees, shrubs, and ground cover. Hardscape works included installing pavers, curb stones, ramps, and stairs. Electrical works covered LV cables, controllers, and a SCADA system. Water supply infrastructure included construction of tanks and a pump station for plant watering during construction. The project successfully transformed the site into a functional and visually appealing space through meticulous site preparation, earthwork, soft landscaping, hardscape installations, electrical works, and water supply provision.
Misk: District 5 and Lower Wadi Sport Pavilion
Details:
Owner: MISK City
Consultant: Consultancy Group (CG)
Location: Riyadh
Designer & PMC: ARCADIS/ JLL
Project Brief:
The proposed area underwent comprehensive infrastructure development for the master plan. This involved installing utilities, corridor lines, and accessories such as irrigation, stormwater, wastewater, potable water, gas, LV/MV systems, street lighting, and telecom networks. Grading activities achieved the desired rough grading level, while hardscape pavements were constructed with precast pavers, curb stones, and asphaltic roads. Specialty works included street lighting, package substations, and signage. The construction of the Lower Wadi Sport Pavilion followed stages of earthworks, substructure, ground floor slab, superstructure with the roof and finishes, MEP systems, and an underground water tank with a pump room. These developments created functional and aesthetically pleasing spaces, meeting the area’s needs and contributing to overall progress.
KAFD Parcel 3.01, 3.02, and 3.06 Car Parking, Retail, Supermarket, and Cinema
The Details:
Owner: King Abdullah Financial District
Consultant: Parsons
Location: King Abdullah Financial District Riyadh
Total Area: 160,300 M
Project Brief:
The project calls for the design & build of 3 parcels 3.01, 3.02 & 3.06. Its main purpose is having additional 2,350 car park lots at KAFD, including roof recreational area, supermarket, retail, cinema, and atrium.
Parcel 3.01: 11 levels (4 basements & 7 floors) of car parking offering 1,940 lots and offering spaces for retail, supermarket, cinemas & atrium.
Parcel 3.02 & 3.06 and roof of 3.11: 5 levels car parking offering additional 410 lots and offering spaces for recreational area, gym, swimming pool, landscape & hardscape.
Student Lobby in Male Academic Area
The Details:
Owner: Ministry of Higher Education – Imam University
Consultant: TYPSA
Location: Riyadh
Built Up Area: 35,000 M2
The students’ lobby in Male Academic area is an artistically unique solid star shaped building pentagon-shaped; thus, its five sides are partitioned into five main areas in addition to a central region and the garden rises from the basement towards the upper floors and appears dramatically illuminated by means of a translucent skylight.
Project Designed PTFE fabric tensioned membrane- tensile structural roofing including supporting frame, the substructure and superstructure for students to socialize and thrive in their extracurricular activities with the Facility of Auditorium, Main Restaurant and Café, Gymnasium, Theater, Health club, Shops and kiosks ,Exhibitions and events area & all kind of services specially tailored for the students (ATM, travel agency, bank, barbershop, Super-market, pharmacy) which blends outwards with the commercial mall and a central garden.
Fit-out Works for Parcel 3.04 in KAFD (Phase 1 & 2)- SIDF HQ
The Details:
Owner: Saudi Industrial Development Fund - SIDF
Consultant: Q Design
Value: 185,079,399 SAR
Location: Riyadh
Built Up Area: 26,000 M2
Project Brief:
MARCO was hired to fit out parcel 3.04 Saudi industrial & Development Funds (SIDF) headquarters, includes the architectural finishes work, mechanical, electrical and communication work in the following main divisions:
Demolition work, Masonry work, Metal work, Wood & plastics
Thermal & moisture protection, Openings, Finishing, Specialties
Furnishings, Fire suppression, Plumbing, HVAC, Integrated Automation
Electrical , Communication, Electronic safety & security.
The 32-story tower is divided into 4 major groups namely group A, group B, group C & group D based on the functions of the floors.
General Auditing Bureau Headquarters in Riyadh
Owner: General Auditing Bureau
Consultant: Arch Center
Location: Riyadh
Built Up Area: 74,500 M2
Project Brief:
This project consists of an urban building comprising a tower that will make it a landmark in the Malaz area at Jamea Street, Riyadh. The building consists of 18 floors and includes 3 basements for parking and 15 office floors. The total built-up area of the building is 40,000 sqm. Project consists of 7 No of Floors with total built up area of project is 34,500 m2, Basement 1 to 4 is Car parking (No. of Parking = 426) with Auditorium with capacity of 484 seats in ground floor, there is a multipurpose hall and a restaurant for approx. 100 people.
WADI Public Realm Completion Works
Details:
Owner: King Abdullah Financial District (KAFD)
Consultant: Ashbelya Consulting Engineering
Location: Riyadh
Built Up Area: 34,500 M2
Project Brief:
The scope of works comprises the completion of the water features, pump rooms, trellis, elevators, escalators, drainage channel, electro-mechanical works, and landscaping and irrigation works associated with packages 1 & 2 of the Wadi. This includes the construction of complete stairway No. 5 and water feature No. 5, located between parcel 1.11 and the Arch Bridge.
Construction of Ready-Built Factories (58 Units)
The Details:
Owner: MODON
Consultant: JASARA
Location: Sudair
Built-Up Area: 26,100 M2
Project Brief:
The project consists of 58 RBF units of 450 m2 each. These pre-engineered buildings have a main factory area (gable steel frame) of 1,800 m2 for Type 1 and 900 m2 for Type 2. There are 14 blocks of Type 1 and 1 block of Type 2. Total Steel Structure = 26,100 m2.
32. PROJECT REFERENCE LIST
33. LIST OF MANPOWER
34 LIST OF EQUIPMENT
36 QUALITY CONTROL PROGRAM NARRATION
TABLE OF CONTENTS
1. INTRODUCTION OF CONSTRUCTION QUALITY CONTROL PROGRAM (CQCP)
a) Quality Policy
b) Purpose
2. GENERAL QUALITY CONTROL REQUITEMENTS
a) Testing & Inspection Standards
b) Work Performance
3. MANAGEMENT RESPONSIBILTY
a) Scope
b) Personnel, Responsibilities and Authority
c) Organization Chart
d) Verification Resources and Personnel
e) Management Review
4. QUALITY SYSTEM
a) Scope
b) Responsibilities
c) General
d) Control of Quality Control Program / Procedures
e) Implementation
f) Quality Control Reports
5. MATERIAL APPROVAL AND PROCUREMENT PROCESSES
a) Scope
b) Submittals
c) Procurement
6. DOCUMENT CONTROL
a) Scope
b) Responsibilities
c) General
d) Control of Records
e) Control of Drawings
7. CONTROL OF NON-CONFORMACE REPORT
a) Scope
b) Responsibilities
c) General
d) Identification & Segregation
e) Disposition and Implementation
8. CORRECTIVE ACTION
a) Scope
b) Responsibilities
c) General
9. CONTROL OF INSPECTION AND TESTING
a) Scope
b) Responsibilities
c) Construction Inspection & Testing
d) Receiving Inspection & Testing
10. INSPECTION, MEASURING AND TEST EQUIPMENT
a) Scope
b) Responsibilities
c) Control of Equipment
11. INSPECTION AND TEST STATUS
a) Scope
b) Responsibilities
c) General
d) Inspection Procedures
e) Field Testing Procedures
f) Sub-Contractor / Supplier Inspection
g) Pre-Installation Quality Control
h) Installation Quality Control
12. CONTROL OF MOCK-UP CONSTRUCTION
a) Scope
b) Procedures
13. QUALITY RECORD CONTROL
a) Scope
b) Responsibilities
c) General
d) Collection / Filling
14. MATERIAL AND EQUIPMENT STORAGE
a) Scope
b) Responsibilities
c) General
d) Procedures
15. TRADING & CONTRACTING COMPANY
a) Employment of Agency
b) Organization and Management of Agency
c) Human Resource
d) Quality Service
e) Test Capabilities
16. INTERNAL AUDIT
a) Scope
b) Responsibilities
c) Scheduling
17. SUMMARY OF QUALITY STANDARD FORMS
A. Organization Chart
B. Daily Reports (Manpower), B1: Daily Report (Equipment’s), B2: Daily Report (Activities)
C. Material Submittal, C1: Submittal form (Client / Consultant)
D. Submittal Master Log
E. Technical Query
F. Technical Query Log
G. Drawing Submittal
H. Drawing Master Log
I. Non-Conformance Report
J. NCR Log
K. Equipment Calibration Tracking Log
L. Request for Inspection (RFI)
M. Hold Point released (HPR)
N. Material Inspection Request (MIR)
O. Material Storage
P. Periodic Inspection Log
1. INTRODUCTION OF CONSTRUCTION QUALITY CONTROL PROGRAM (CQCP)
a) QUALITY POLICY
• It is the quality policy of the company to meet the project specification requirements by taking responsibility in compliance with the project requirements. The Ultimate purpose of this Quality Control Program which describes the quality system is to identify quality practices and procedures that will be applied to this project; that will ensure that the Items and services provided satisfy the client’s needs, meet specified quality requirements and are in accordance with contractual and legislative commitments.
• This Quality Program shall be read and understood by all concerned company personnel including management who shall be fully committed to providing the required quality, through the application of the quality assurance system. Any problems or difference of opinion between the organizations within the company regarding the application of this QC program shall be brought to the project manager for final resolution and such resolution shall be consistent with specified requirements.
• This Construction Quality Control Program (CQCP) will be implemented to ensure remedial and construction procedures that performed in compliance with the plans and specification under this contract. This CQCP will provide a means to maintain effective quality control at the O & M Projects Site.
• The quality control measures as presented herein include quality control organization; methods of performing, documenting, and enforcing quality control operations of both the primary Contractor and Subcontractors (Including inspection and testing); inspections to be performed and protocol describing corrective actions.
• Overall management of the CQCP will be the responsibility of the Contractor’s Quality Control Manager (QCM). The QCM will have the authority to act in all construction quality control CQC matters and will be responsible for ensuring that all materials and work comply with the contract specification requirements. All inspection and testing firms will be at the disposal of the QCM to ensure that all aspects of the work conform to the contract requirement. The QCM will report any deviation from the CQCP independently to the On-site Project Manager.
b) PURPOSE
• The purpose of this Construction Quality Control Program (CQCP) is to provide an overview of the Company’s Quality System operation and describe the structure and implementation of the Quality Control System. The development and implementation of functional Quality Control Systems on any project is essential to control, inspect, test and keep records of all aspects of procurement, fabrication and installation of the project, in conformance with the Contract Drawings and Specifications. These systematic procedures shall be applied in logical construction sequences which will ensure that the product or service will satisfy a given requirement of quality.
• The purpose of this Quality Control Program is to comply with all system requirements of International Standard and the Client Guideline Specification for Construction Quality Control Program will fine, document & maintain policies, procedures, practices, and related methods. It also covers responsibilities and authorities that help in achieving three
(3) specific objectives:
1) To serve as a road map that gives direction and meaning to our mission (Project objective for Final Turn over to Client)
2) To mirror the Statement of Quality Commitment.
3) To have a documented Quality Control Plan that helps us in periodical assessment and continual enhancement.
2. GENERAL QUALITY CONTROL REQUIREMENTS
a) TESTING AND INSPECTION STANDARDS
• Conducting Test and Inspection in the most basic requirements of a certain project and it will be in accordance and comply with the applicable standards given in this contract specification and Contract Drawing requirements.
• Quality Control procedures will conform to and satisfy all applicable technical requirements providing the same degree of quality as tests and other quality control procedures specified in this contract.
• All records and reports will be documented, arranged, and maintained to ensure traceability between material, fabrication, and test records.
• All test equipment will follow applied standards and will be available on the site in complete and calibrated condition.
b) WORK PERFORMANCE
• All work to be performed will be in accordance with and conform to the quality requirements specified in the individual Specification Sections. Where quality level is not indicated, work of quality customary in similar types of work shall be performed.
• Where codes, laws, or regulations require work of higher quality or performance, work complying with those codes, laws, and regulations shall be provided.
• In the case of two or more quality provisions of the Contract Documents conflict, the most stringent requirement shall be complied with. Where requirements are different but equal and where it is uncertain which requirement is most stringent, clarification from the Client shall be obtained before proceeding.
• The work shall comply with the manufacturer’s instructions and recommendations. A record of instructions and recommendations, which supplement or conflict with the manufacturer’s written instructions, shall be kept.
• When manufacturer’s instructions and recommendation conflict with the Contract Documents, clarification shall be obtained from the Clients before proceeding.
3. MANAGEMENT RESPONSIBILITY
a) SCOPE
• This section describes the company organization responsibility for the implementation of the quality system. The specific responsibilities and interface control between organizations are defined in each section of this QC program.
• This Quality Control Plans includes procedures, instructions, and reports to be used to provide adequate coverage for all quality control activities required by this Contract, and to ensure that all quality construction and services in accordance and conform with the available plans and specifications standard.
• The Contractor’s key personnel assigned to this project should possess a broad range of remedial action experience and skills.
• The functional responsibilities of key technical personnel are summarized as follows.
b) PERSONNELS, AUTHORITIES AND RESPOSIBLITIES
1. On-Site Project Manager (PM)
• The Contractor’s On-site Project Manager will be the primary contact person at the site with whom Consultant Engineers will interact daily under this contract.
• The Contractor’s On-site Project Manager has the responsibility and authority as a contractor Representative for the construction quality policy, directions, strategy, and operation including delegation of the authority to Quality Control Manager for control over activities affecting quality.
• The Contractor’s On-site Project Manager will ensure that:
• Appropriate resources are allocated to the project and balanced to ensure best value of Client.
• Contract Management Procedures.
• All tasks are conducted in accordance with the available plan and project specifications.
• The Contractor’s on-site Project Manager will become and remain personally involved until each problem is resolved and appropriate corrective measures are implemented. They will typically communicate at least once daily on the progress of the project.
• The Project Manager will be on the jobsite, to ensure that the project is progressing as per scheduled.
• The On-site Project Manager is responsible for implementation and support of the Contractor’s CQCP and will oversee all aspects of work under this contract for remediation at the site, including:
• All procurements.
• Qualified Contractor and subcontractor resources are assigned to the project and balanced to ensure jobs are aligned with project needs and requirements.
• The Site is maintained and secure.
• All tasks are conducted safely and in compliance with project specifications.
• Contractor or Sub-contractor coordination.
• Maintaining charge of all field operations.
• Provide overall guidelines & directions for the Company.
• Directs, controls senior Functional Heads to achieve desired results, and drives customer focus, continual and organization improvements.
2. Quality Control Manager (OCM)
• The Quality Control Organization shall be led by a Quality Control Manager, who will report directly to the onsite Project Manager. And shall have the authority and responsibility to instruct removal and replacement of any defective work. The QCM is required to be on site during execution of work to facilitate and monitor every stage of the project.
• The Quality Control Manager will report directly to the On-site Project Manager on matters concerning quality control. He will have both the authority and the duty to halt any operation appearing to be out of compliance with contract specification and Drawing requirement.
• The QCM is responsible for keeping and maintaining all records related to personnel, supplies, equipment use, and equipment calibration and sampling. His function will be to ensure compliance with the contract plans and specifications.
• QCM responsibilities include:
• Performing and documenting field inspections.
• Preparing daily Quality Control Reports.
• Scheduling, reviewing, certifying, and managing project submittals.
• Maintaining the Submittal Register
• Providing coordination of required quality control testing, reviewing results, and submitting.
• Coordinating, documenting, and tracking preparatory, initial, and final inspections.
• Tracking construction deficiencies and ensuring timely corrective action.
• Coordinating field sampling activities (as required).
• Reviewing calibration of test equipment (as necessary).
• Preparing addenda to the CQCP as necessary when additional phases of work are added.
• Maintenance of as-built drawings.
• Coordinating responses to vendors’ requests for information and technical issues.
• Serving as main point of contact at the site for Client clarification and discussions on quality and technical issues.
• Delegating duties to QC Engineers and notifying Client to whom what duties have been delegated.
• The QCM or QC Engineers will be on-site when work is being performed to ensure that all works and test conducted @ site follow the applicable standards and Client specification requirement.
3. Quality Control Engineer
• He shall work under the supervision of QCM which had given him the authority to inspect material, equipment’s, and work craftsmanship & support personnel to perform the duties described in the Quality Control Plan.
• He shall remain on site during the execution of work with complete authority to take any action necessary to ensure compliance with respect to all contract specification and Drawing requirement as per Quality Control Plan.
• The Quality Control Engineer shall be well trained in the methods and skills required to performs his daily task as per enumerated under hereof:
• The proper operation of instrument tools and equipment they must use or supervise.
• He shall be familiar with reading and understanding the documentation provided.
• The relation of his duties to quality and safety on site be capable of performing the following required functions:
• Check materials at the work site to ensure consistency with contract specifications and the approved material submittals.
• Prepare and maintain current records of all quality control operations to include those of subcontractors.
• Witnessing every Test performed with the aid of an independent approved Testing Laboratory and ensuring that all test results will follow the contract specification requirement.
• He shall be in control of non-conformance reports wherein he needs to establish and maintain the procedures to identify and correct non conformances found during the construction of the work, receipt or storage of materials and equipment, fabrication, installation, or testing.
• Non-Conformance items shall be reported to QCM and must be controlled and documented using Non-Conformance Report (NCR). The controls and related responsibilities and authorities for dealing with non-conformances will be defined in a documented procedure and official receiving file copies are kept at site.
• The Quality Control Engineer responsible for verifying the activities on site, though audit, surveillance inspection, test, witness and monitoring for the production, construction and servicing process, reviewing the nonconforming products, and reporting the quality matters to Quality Control Manager.
4. Contractor – Superintendent
• The Project Superintendent will be responsible for supervising all field activities. His duties include supervision of the craft labor (Equipment operators, truck driver, and laborers). Technical staff (Survey crew), and all subcontractors.
• The designated Superintendent is also responsible for the maintenance of all on-site construction equipment.
c) ORGANIZATION CHART (SEE ATTACHED APPENDIX – A)
• The organization chart of the project is attached in this section. These charts include all separate departments and functions responsible for quality tasks.
• The individual(s) or organization(s) responsible for establishing and executing a quality system under this QC program may delegate any or all the work to others but shall retain responsibility, therefore.
• The company may subcontract, upon Employer’s agreement, with another organization to carry out any of work on the construction activities, but shall retain overall responsibilities, therefore.
d) VERIFICATION RESOURCES AND PERSONNEL
• Adequate resources for verification activities shall be provided by each responsible superintendent and the personnel who perform verification activities shall be trained as specified of this QC program. The inspection personnel for the special process shall be separately qualified and organized in the Dept.
• Verification activities shall include checking, auditing, inspection, test and monitoring of the field design change, production, construction, and servicing processed and/or product.
• The assigned qualified inspection / verification / audit personnel shall have the authority to:
• Initiate action to prevent the occurrence of product nonconformity.
• Identify and record any product quality problems.
• Initiate, recommend, or provide solutions through designated channels.
• Verify the implementation of solutions.
• Control further processing, delivery, or construction of nonconforming product until the deficiency or unsatisfactory condition has been corrected.
e) MANAGEMENT REVIEW
• The construction manager shall review the quality system at appropriate intervals to ensure continuing suitability and effectiveness. The QC manager is responsible for reporting the quality implementation to the Construction manager.
• The responsible level shall take necessary corrective actions with respect to the quality systems, resources, or personnel based on the results of the management review.
4. QUALITY SYSTEM
a) SCOPE
• This section describes the establishment and maintenance of the documented Quality Control Program for ensuring that stated quality policy and objectives are effectively accomplished.
• The CQCP will be implemented to ensure compliance with the specifications for remedial action construction as detailed in the contract specifications.
• The basis of the CQCP is nationally recognized standards published by the American Society for Testing and Materials (ASTM) and the Project Specifications.
• In addition, procedures utilized within the CQCP should reflect the experience gained by MOHAMMED AL-RASHID TRADING & CONTRACTING CO. in completing construction projects like the O & M Center Project.
• Quality control measures will extend to field sampling procedures; staffing; types of material and equipment to be used; and methods of performing, documenting, and enforcing quality control operations of both the contractor and subcontractors (including inspection and testing).
b) RESPONSIBILITIES
• The Quality Control Manager has authority and responsibility for the development and maintenance of the Quality Control Program, and the coordination and monitoring of its effective implementation.
c) GENERAL
• The documented Quality Control Program shall be established in compliance with the requirements of the client.
• Quality assurance shall be operated strictly in accordance with this QC program and Procedure with provides the management tool and identifies the major elements of quality assurance requirements.
• For effective implementation of quality assurance, detailed quality assurance documents which become a part of this QA/QC program shall be established.
d) CONTROL OF QUALITY CONTROL PROGRAM / PROCEDURES
• The Quality Control Manager is responsible for preparing, distributing, and maintaining the QC Program / Procedures in accordance with the Quality system control.
• Controlled QC Program / Procedures shall be maintained and updated by the latest revision. The original QC Program shall be kept on file by the QC Department.
• The QC Program / Procedure to be controlled shall be maintained currently with the latest authorized changes.
• The QC Program shall be revised and controlled by volume.
• Only controlled copies of QC Program / Procedures shall be distributed for use within the organization.
• The revised areas of QC Program / Procedures expect for the typographical correction shall be identified using a vertical line with revision triangle in the righthand margin of each page.
• Superintends are responsible for preparing the work procedures for the major and or special activities which cannot be covered by the project specifications.
The relevant procedures are to be developed later at site and referenced in each relevant chapter of this Quality Control Program.
• As previously stated, maintenance of the CQCP will be the responsibility of the QCM. The QCM will be responsible for ensuring that all materials and work comply with the contract specifications.
• The QCM may have a field engineer of QC Engineer at his disposal to assist him with the on-site inspections.
• Testing firms will be at the disposal of the QCM to ensure contract compliance in all aspects of work. All reports from testing firms will be forwarded to the QCM for his review and approval.
e) IMPLEMENTATION
• The QCM will be responsible for implementing the CQC Plan by ensuring that quality materials and supplies are provided for the proposed project, and that good workmanship is provided in all aspects of this contract.
• The QCM will report directly to the On-site Project Manager and will complete daily site inspection to ensure compliance with the quality control specifications.
• Daily reports will be completed listing all field testing and sampling activities. These reports will be submitted to the CLIENT representative daily.
• The QCM will be responsible for ensuring that all materials and work comply with the contract plans and specifications, and that all performance standards are met.
• It is anticipated that the CLIENT representative and the Contractor’s QCM will meet frequently to forecast and/or prevent any potential problems from arising.
f) QUALITY CONTROL REPORTS
• Quality Control Reports with enclosed Inspection and Test Plan (ITP) are necessary to keep the client informed about the QC activities taking place on site and for the improvement of the Quality System. QC Reports on a daily, weekly, and monthly basis will be prepared and submitted to the CLIENT.
a) Daily Quality Control Report
• The “Daily Quality Control Report” (Manpower & Equipment) is the report used to record and monitor daily inspection activities. Using the suggested format (SEE ATTACHED APPENDIX-B, B1 &B2). This report will be submitted to the CLIENT Field Engineer early in the morning for the following day. This report will include:
1) Name of the QC Site Personnel involved in inspection activities.
2) Item of work inspected, finding and action taken.
3) Materials and Equipment received and inspected, finding action taken.
4) Samples taken, tests made, and results received including action taken for failing tests.
5) Nonconformance found and/or corrected.
6) Quality instructions received from CLIENT Personnel.
7) Offsite inspection of materials and equipment.
b) Monthly Quality Control Report
• As part of the Quality Control Report to the Quality Control System, MOHAMMED AL-RASHID TRADING & CONTRACTING CO. will prepare a Monthly Quality Control Report will be submitted to CLIENT every 1st Day of Hijra Month.
• The monthly Control report will summarize the following:
1) Summary of all Testing conducting for the month
2) Summary of all Inspection Conducting for the month.
3) Summary of all activities accomplished for the month.
4) Progress photo’s showing the accomplishment gained for the month.
5) Proposed Quality Control Program Improvements.
6) Revision to Frequency of Testing (if Any)
7) Work Recommended for Acceptance.
8) Summary of all Test results conducted by the 3rd Party for the month.
9) Non-conformances found and/or recommended / corrected. (If Any)
• The report along with the Test Certificate will be handed over to the CLIENT.
5. MATERIALS APPROVAL & PROCUEMENT PROCESS
a) SCOPE
• This section describes the process and standard procedures in taking approval to CLIENT for the materials to be use and the procurement processes after the material was being approved.
• The section should be in conformity to the quality policy in this program for ensuring Quality Control Program and objectively accomplished.
b) SUBMITTALS
• The QCM will follow standard procedures concerning submittals, including the use of the CLIENT standard transmittal form. (SEE ATTACHED APPENDIX – C & C1)
• A “Specification Comparison Sheet” will be attached to each submittal to compare what is being proposed directly with specification requirements,’ including applicable codes and standards, such that compliance or deviations are clearly stated.
• A submittal register Long listing of all submittals record will be prepared by MOHAMMED AL-RASHID TRADING & CONTRACTING CO. (SEE ATTACHED APPENDIX-D).
• The register will be prepared in conjunction with the anticipated progress schedule.
• The QCM will be responsible for the review and approval of submittals prior to submitting to the CLIENT representative. This includes reviews of materials and suppliers’ catalog cuts, as well as subcontractor submittals.
• The QCM will review the submittal for completeness and compliance with the contract specifications. Variations to a submittal will be noted on the submittal comparison sheet.
• The QCM will actively participate during procurement activities to ensure purchase orders and subcontracts comply with the contract.
• MOHAMMED AL-RASHID TRADING & CONTRACTING CO. will not proceed to the purchasing stage of the material unless CLIENT will approve the material submittal.
• All submittals having code 3 statuses or disapproved will be resubmitted again complying or conforming of what the comments are given by the CLIENT to get code 1 to proceed with the work.
• After the preparation of the submittal by the Technical Office, QC Manager will review it and sign the “Specification Comparison Sheet” when the submittal will be returned from CLIENT either, approved or rejected the QC Dept. will keep a copy of it in its office.
• On arrival of approved submittal, the QCM will inform the relevant QC Personnel what has been approved, so that they will be aware of what they must inspect on site. Also, QCM will inform section heads of other departments so that the Engineers are aware of the approved materials or equipment.
• If MOHAMMED AL-RASHID TRADING & CONTRACTING CO having any technical queries, or they need technical clarification from CLIENT by official standard form (SEE ATTACHED APPENDIX- E&F)
c) PROCUREMENT
• The materials and equipment required for the Project will be procured from approved manufacturers / suppliers from the in-Kingdom or from out-of-kingdom market. Very special care must be given to such procurements in order to avoid non-conformities.
• Hence, an organization will be established for the purchase or order of the materials and equipment, either from National or International market.
Procured and Fabricated Material inside the Kingdom
• Prior for purchasing any item or materials MOHAMMED AL-RASHID TRADING & CONTRACTING CO. will make material submittal to be submitted to CLIENT for approval. We will gather all technical data for the product from the supplier/ manufacturer for supporting documents for the submittal.
This data includes:
a) Product Technical data and specification
b) Material test Report and Certificate
c) Production or Fabrication Specification
d) Methods / Ways of Production or Fabrication
e) Dates of production or Fabrication Including any other Technical Data related to the Product item.
f) Welding procurement specification (if required)
g) Certification of welders (if required)
• With all these information MOHAMMED AL-RASHID TRADING & CONTRACTING CO. will prepare a technical submittal using the CLIENT standard form (Submittal Comparison sheet) showing the specification requirement of the product versus the available specification of the material proposed to be used to the project and submit to CLIENT.
• This submittal will be reviewed and signed by the QCM wither the proposed materials conform or comply with the CLIENT requirement before submitting to CLIENT.
• Procurement stage of the material will not be process until CLIENT approves and accept the technical Submittal for the proposed material.
• If the proposed material will be rejected by CLIENT having a status code of CODE3, MOHAMMED AL-RASHID TRADING & CONTRACTING CO. will not be process for procurement for the said item, instead we will rectify and comply with all the given comments and resubmit it again to CLIENT for approval.
• MOHAMMED AL-RASHID TRADING & CONTRACTING CO. will submit an alternative submittal as an option for the said item meeting the CLIENT specification requirement.
• During the delivery of the materials procured, that material(s) of equipment on site will be inspected by CLIENT Manager / Engineer ensuring that all technical information data
and specification of the material must be comply and conform to the technical submittal approved by CLIENT.
• A material Inspection Request will be forwarded to CLIENT to conduct join inspection together with the contractor QC for the materials/equipment revised @ site. The request form must be closed by CLIENT prior to fixing the said material @ working site.
• If ever CLIENT shall ask for a visit to a manufacture plant or show room, then MOHAMMED AL-RASHID TRADING & CONTRACTING CO. will arrange the date and time for visiting and informing both parties (CLIENT AND MANUFACTURER/SUPPLIER) the agreed time and date of visit.
Procured and Fabricated Material / Equipment Outside in the Kingdom
• MOHAMMED AL-RASHID TRADING & CONTRACTING CO. will procure the said long lead items by the aid of our valuable different manufacturers/ Suppliers (3rd Party) to which they are dealing to us for so many completed projects by CLIENT.
• The following details and information will be gathered.
a) Complete Product Specifications
b) Ways/methods of production
c) Quality of materials
d) Delivery Time Confirmation
e) Testing certificates
f) Available of spare parts
• With all these information MOHAMMED AL-RASHID TRADING & CONTRACTING CO. will prepare a technical submittal showing the proposed materials and submit it to CLIENT for approval.
• If the CLIENT approves the proposal, then the company will proceed for procurement stage of the said material or equipment. If the CLIENT does not approve the proposal, then the whole procedure has to be repeated with another manufacturer until we have the official approval from the CLIENT to the said item prior proceeding.
• During the delivery of the materials procured, that material(s) of equipment on site will be inspected by CLIENT Manager / Engineer ensuring that all technical information data and specification of the material must be comply and conform to the technical submittal approved by CLIENT.
• A material Inspection Request will be forwarded to CLIENT to conduct join inspection together with the contractor QC for the materials/equipment revised @ site. The request form must be closed by CLIENT prior to fixing the said material @ working site.
• All the escorting documents and certificates of the products will be handed over to CLIENT proving that the imported products are according to the contract specification.
6. DOCUMENT CONTROL
a) SCOPE
• This section describes the requirements, and control system for the preparation, review, approval, distribution and change of the documents to be used by the relevant department at site.
b) RESPONSIBILITIES
• The Field Control Manager is responsible for establishing the document control procedure and assigning the document controller to control the site documents.
• Each superintendent is responsible for implementing the control requirements of controlled documents at site.
c) GENERAL
• The preparation, review, approval, distribution and change of documents that specify quality requirements or prescribe activities affecting quality shall be controlled to assure that the correct documents are being used.
• All documents including their revisions shall be legible, dated, clean and readily identifiable and maintained in an orderly manner.
• The type of documents which shall be controlled are as follows, but not limited to:
• Project QC Program
• Quality Procedures
• Work Procedures
• Drawings
• Employer Documents
• Project Specifications and standards
• Instructions
• Vendor Data Books
• Codes & standards
• Procedures, Drawings, Specifications, and Instructions shall be established by the responsible department respectively and controlled in accordance with this section.
• The QCM/ QC Engineer will record project activities in a daily quality control report always maintained on site.
• All site activities, site inspections, and field testing of materials will be recorded daily, along with any unacceptable site occurrences or deficiencies and their associated corrective action.
• Each daily entry into the report will be signed by the QCN. QC reports will be submitted daily during all field construction activities.
• MOHAMMED AL-RASHID TRADING & CONTRACTING CO. maintains a documented quality system to ensure that all products and services conform to the specified requirements. The quality system is structured with four levels of documentation.
• The company has designed and implemented a Document Control Procedure to
serve the purpose of controlling and monitoring of documents such as creation, review, approval for adequacy, issuance and distribution and revision of documents pertaining to MOHAMMED AL-RASHID TRADING & CONTRACTING CO. QC Program.
d) CONTROL OF RECORDS
• The company has designed & implemented a Records Control Procedure. The purpose is to:
1) Create a companywide uniform method of Quality records control.
2) Demonstrate effective operation CQCP and maintain evidence of practices.
3) Records shall remain legible, readily, identifiable, and retrievable. A documented procedure shall be established to define the control needed for the identification, storage, protection, retrieval, retention time and disposition of records.
4) All Quality Control Records shall be kept in a centralized area and filed in chronological order by pay item when possible.
5) The filing of records shall be kept current and open to review by the CLIENT.
6) All Quality Control Records shall be easily identified and traceable to specific requirements in the specifications and drawings.
7) The Quality Control Records packaged for each pay item and indexed for ease or reference shall be turned over to the CLIENT prior to initial acceptance.
8) A record shall be established and maintained to provide evidence of conformity to requirements and of the effective operation of the Quality Control System.
e) CONTROL OF DRAWINGS
i) Drawing Management System
• A central easily accessible master drawing register Log that records the latest revision of all documents in the drawing management system. (SEE ATTACHED APPENDIX – G&H).
• As drawings are revised, the superseded versions are automatically archived to our drawing management history file, thereby maintaining an audit trail.
• All drawings, specifications, procedures, project plans, etc. can now are easily found through a single access point.
• Drawings should be stamped or otherwise marked to clearly indicate that the drawing is controlled.
• Drawing indexes should be readily available and maintained current to allow quick verification of drawings for use.
• Controls should be established for distribution and updating of drawing files.
• Drawings that are posted at various locations on the planet should also be controlled.
• Drawings that are not part of the controlled drawing system should be considered uncontrolled and clearly identified as such.
• Maintenance procedures should indicate how controlled and uncontrolled drawings are identified so that personnel can readily determine the status of drawings.
• Uncontrolled drawings should not be used for the performance or planning of maintenance work activities.
ii) Drawing Control System
• A master drawing register must be maintained and should hold the latest revision of all project documents and drawings.
• Generate transmittals and submittals and maintain an audit trail for drawing control purposes.
• Drawing control should focus on managing revisions to drawing with a drawing history being automatically maintained.
• The latest revisions of a drawing must be sent to those who have not received them.
• A drawing control system must maintain a review process both internal and external parties.
• Alerts must be expedited to ensure a response to documents and drawing issues.
iii) Practical Steps to Drawing Control
• Incoming and internal drawings need to be processed.
• A drawing register of the latest drawings must be maintained.
• Distribution of drawings in the drawing control system must take place via transmittals to staff and other parties who need them.
• An audit trail of the drawings in the drawing control system must be maintained to ensure that there is tracking of who got what, when and why.
• The managing of revised documents and their distribution and archiving superseded drawings as part of the drawing control process.
• MOHAMMED AL-RASHID TRADING & CONTRACTING CO. will always maintain and assure that all drawings available at site is that the latest issued drawing (IFC Drawing) by CLIENT. The QCM will always update the CLIENT for any revision and changes pertaining to all drawings available at site.
• MOHAMMED AL-RASHID TRADING & CONTRACTING CO. will provide a copy of complete set of Drawing in relation to all discipline. Set of IFC Drawings and As-Built Drawings will be always available at site.
• As-Built Drawing should always be updated from time to time to ensure that all changes and revision from IFC Drawing will be reflected as earlier phase of the project.
• A drawing control system shall be established and maintained to provide revised drawings and ensure continuous removal of obsolete drawings from work areas. Changes involving interface with other work areas, or affecting materials controlled by others shall be controlled by the Contractor.
• Drawing changes shall be clearly annotated, implemented changes shall be attached and clearly identified and associated drawings shall be revised accordingly.
• Drawings that have been approved, or approved as noted, by CLIENT shall be used for fabrication, installation, and inspection.
7. CONTROL OF NON-CONFORMANCE REPORT
a) SCOPE
• This section describes the requirements for the control of construction and fabrication conforms to the specified requirements.
• The purpose of this section is to establish a procedure to identify and correct nonconformances found during construction phase of the project, receipt or storage of material and equipment, fabrication, installation, or testing.
• As MOHAMMED AL-RASHID TRADING & CONTRACTING CO. is fully responsible for the quality of his work and shall produce work with a quality conforming to professional standards identified in the contract documents.
• MOHAMMED AL-RASHID TRADING & CONTRACTING CO. will establish and maintain the procedures to identify and correct non-conformances found during construction of the work, receipt or storage of materials and equipment’s, fabrication, installation, or testing.
• Any part of the construction, works had been done, materials and equipment to which does not conform to the requirements of the Technical Specifications, approved Submittals or Design Drawings will be issued NCR for non-conformity of the requirement.
b) RESPONSIBILITIES
• The QC Manager has the responsibility for the identification, investigation, and documentation, when practical, of the non-conformance and for verifications of proper implementation of the correction according to the disposition and for notification to the client.
• The assigned inspector is responsible for identification of non-conformance, initiating nonconformance document, proposal for correction, if possible and verifying implementation result of correction.
c) GENERAL
• Construction and fabrication that do not conform to the specified requirements shall be identified and held until proper disposition has been made for construction.
d) IDENTIFICATION AND SEGREGATION
• Nonconforming materials shall be identified and notified to the relevant organization for the prevention of further processing and their nonconforming condition shall be described by the assigned QC Engineer.
• When any personnel other than the responsible personnel find any nonconforming materials, he will immediately notify the QC Department. Designated hold area until the appropriate disposition is made.
• When segregation is impractical or impossible on site due to physical conditions, such as size, weight or access limitations, the nonconforming materials or associated area shall be clearly identified by marking, ropes or other distinguishable means. When the nonconformance is found at the receiving stage, the products shall be segregated and documented.
• All non-conforming items will be documented using a Non-conformance Report (NCR). Using the standard format of the NCR from CLIENT (SEE ATTACHED APPENDIX – I). By filling up this format, official and identified NCR can be issued and will be documented and complied together with the Quality Control Documentation.
• When a certain NCR is issued, no further work shall take place until the nonconformance has been corrected.
e) DISPOSITION AND IMPLEMENTATION
• The appropriate disposition of nonconforming material and construction shall be done based on one of following:
a) Rework
• The process by which a non-conforming item is changed to make it conform to specified requirements by further work, e.g., re machining, re-welding, re assembling, replacement of parts, or other means.
b) Repair
• The process of restoring non-conforming characteristics to a condition acceptable to the CLIENT, though that item still may not conform to the original requirement.
c) Reject
• The action taken to eliminate a non-conforming item from its specified use.
d) Use As Is
• The action taken to obtain the CLIENT’s approval to accept an otherwise unacceptable item.
• After the non-conformance is corrected, it shall be subject for inspection, verification, and approval by CLIENT.
• As specified in the project specification, the proposed use as it is or repair of product which does not conform to specified requirements shall be reported for concession to the CLIENT. The description of nonconformity that has been accepted, and of repairs, shall be recorded to donate the actual condition.
• Repaired and reworked portions shall be re-inspected, and the records shall be maintained.
• MOHAMMED AL-RASHID TRADING & CONTRACTING CO. will avoid and minimize NCR if possible. But if ever happen, if any NCR was being issued, MOHAMMED AL-RASHID TRADING & CONTRACTING CO. will discuss to the CLIENT immediately the cause of the non-conformity of the work or materials resulting from receiving NCR.
• MOHAMMED AL-RASHID TRADING & CONTRACTING CO. will take prescribed corrective action pertaining to the subject that does not have conformity from the contract specification and drawing requirement.
• MOHAMMED AL-RASHID TRADING & CONTRACTING CO. will propose appropriate corrective action to eliminate the cause of non-conformities to prevent Recurrence. The approval of the proposed corrective action shall be obtained from the CLIENT before any correction begins.
• Corrective actions shall be appropriate to the effects of the non-conformities encountered.
• The correction shall be any one of the following:
• MOHAMMED AL-RASHID TRADING & CONTRACTING CO. will prepare a log to control NCRs from issue to closeout for monitoring and follow-up for all issued NCR.
• Suggested NCR log from by CLIENT; (SEE ATTACHED APPENDIX – J)
• All NCR’s corrected by “Repair” or by “Use as Is” will be included and reflected in the “As-Built” drawing documents for reference.
8. CORRECTIVE ACTION
a) SCOPE
• This section describes the requirements for the corrective action taken to prevent recurrence of significant conditions adverse to quality.
b) RESPONSIBILITIES
• The QC Manager is responsible for determining the need for corrective action and each superintendent is responsible for the implementation of corrective actions.
• The QC Manager shall identify the significant conditions adverse to quality based on:
a) Investigation the cause of all nonconformance and the corrective action needed to prevent recurrence.
b) Analyzing all processes, operations, quality records, Employer complaints, etc. to detect and eliminate potential causes of nonconformance.
c) Initiating preventative actions to deal with problems to a level corresponding to the risks encountered.
d) Implementing and recording changes in procedures resulting from corrective action.
e) The superintendent for implementing the corrective action shall establish and organize the necessary resources such as personnel, equipment, tools, or facilities for the action to be taken.
c) GENERAL
• When a significant condition adverse to quality is identified, corrective action shall be initiated and documented to prevent recurrence.
• The responsible superintendent for corrective action shall respond by documenting the cause, corrective action to be taken to preclude recurrence and estimated date for completion of the corrective actions.
• When the corrective action to be taken requires the changes to the current quality system, the documented corrective action shall be transmitted to QC department for review.
• The QC personnel shall verify the implementation of the corrective action.
9. CONTROL OF INSPECTION AND TESTING
a) SCOPE
• This section describes the control system for inspection and testing to ensure that the materials and construction conform to the specified requirements.
b) RESPONSIBILITIES
• The QC Manager is responsible for ensuring that inspection and testing are performed in accordance with the general Inspection & Testing procedure (ITP) and are conducted by the inspection personnel.
• The assigned inspector is responsible for performing the inspection activities and for witnessing the tests.
• The project ITP of CLIENT shall be followed.
c) CONSTRUCTION INSPECTION
• QC Inspectors are responsible for the inspection of the construction in progress and upon completion according to the ITP’s.
d) RECEIVING INSPECTION AND TESTING
• Receiving inspection shall be performed by the QC Department and warehouse man.
• The collected materials from client product shall not be used until it has been inspected as conforming to specified requirements or drawings.
• Receiving inspection shall be performed by visual inspection for dimension, damage, deterioration, etc.
10. INSPECTION, MEASURING AND TEST EQUIPMENT
a) SCOPE
• This section describes the methods for control and calibration of inspection, measuring and test equipment to be used for demonstrating the conformance of the materials and construction to the specified requirements.
b) RESPONSIBILITIES
• The QC Manager is responsible for calibration of Equipment. The calibrated equipment shall be documented by a tracking log form system. (SEE ATTACHED APPENDIXK).
c) CONTROL OF EQUIPMENT
• Equipment shall be used in a manner which ensures that measurement uncertainly is known and is consistent with the required measurement capability.
• All equipment shall be checked and recalibrated at prescribed intervals. The equipment shall be identified with a suitable indicator to show calibration status.
• If out of calibration performance, the investigation shall be made of the validity of previous inspection or test performed using those Equipment.
• Environmental conditions shall be suitable for the calibration, measurements and tests being conducted.
11. INSPECTION AND TEST STATUS
a) SCOPE
• This section describes the requirements for inspection and test status to assure that the required inspection and tests are performed and to assure that the materials and workmanship which have not passed the required inspections and tests are not inadvertently used or accepted.
b) RESPONSIBILITIES
• The QC Manager is responsible for the identification of inspection and test status during fabrication and construction.
c) GENERAL
• The status of inspection and test activities shall be identified throughout construction.
• The result of all required Testing and Inspection shall be recorded by the inspection.
d) INSPECTION PROCEDURE
• To ensure that all construction and remedial activities comply with the project specifications, the QCM will complete, in conjunction with the subcontractors, three stages of site inspections for each feature of work.
These inspections will include the following:
1). STAGE I – PREPARATORY INSPECTION
• In this stage an Internal coordination meeting will be conducted by the QC Department and attended by the Site Manager, relevant Site Superintendent, other applicable QC personnel, and other key participants in the new phase of work.
• The applicable workers will be instructed as to the performance required to meet the requirements of the contract for this phase of work.
• Specification topics for review at this meeting include:
• Review of each paragraph of applicable specification and contract drawings.
• Ensure that all submittals and permits have been approved.
• Review inspection and/or testing criteria.
• Examination of the work area to assure that preliminary work has been completed satisfactorily.
• Examination of required materials and equipment are on hand, safely stored, and ready for use.
• Review the activity hazard analysis to assure safety requirements are met.
• Ensure that site personnel have been trained in required classes for safety and security.
• Check to ensure that provisions have been made to provide required field quality control testing.
• Examine the work area to ascertain that all preliminary work has been completed.
• Verify all field dimensions and advise CLIENT, of any discrepancies.
• Perform a physical examination of materials and equipment to assure that they conform to approved shop drawings or submittal data and that all required materials and/or equipment are on hand and comply with the Contract requirements.
• After the preparatory inspection and prior to commencement of work, MOHAMMED AL-RASHID TRADING & CONTRACTING CO. will instruct each applicable worker on the level of workmanship required to meet contract specification.
2). STAGE II – INITIAL INSPECTION
• Initial phase inspections will be performed as soon as a representative portion of the feature of work has been accomplished.
• Initial inspections include, but are not limited to, examination of the quality of workmanship; review of control testing for compliance with control requirements; and identification of defective or damaged materials, omissions, and dimensional requirements.
• After the Initial Inspection has been performed, and all identified defect or damaged materials have been rectified, a Request for Inspection (RFI) will be sent to CLIENT addressing the specific item to be inspected and the time thereof of inspection.
• Using the standard format from CLIENT for RFI, (SEE ATTACHED APPENDIX – L), MOHAMMED AL-RASHID TRADING & CONTRACTING CO. will send this request to CLIENT 24Hrs. before the desired date of inspection through fax or by E- mail.
• During the inspection time, MOHAMMED AL-RASHID TRADING & CONTRACTING CO. representative, QC Engineer will go along with CLIENT representative to conduct inspection for the said item to be inspected.
• If CLIENT accepted the work, a RFI and Hold Point Released (HPR) (SEE ATTACHED APPENDIX – M), must be closed out and signed. And then work will proceed to the next activities.
• If ever CLIENT will not accept the work done, written comments must be filled in the RFI provided, and that comments, remarks or recommendation is subjected to MOHAMMED AL-RASHID TRADING & CONTRACTING CO. rectification and lead to go to next phase of Inspection, Final Inspection.
3). STAGE III – FINAL INSPECTIONS
• MOHAMMED AL-RASHID TRADING & CONTRACTING CO. will conduct inspection internally by the aid of the Quality Department whether all comments or remarks given from CLIENT during initial inspection are all done and rectified, and everything is ready for Final Inspection.
• The same process will be followed as we request for inspection during the Initial Inspection.
• MOHAMMED AL-RASHID TRADING & CONTRACTING CO. will not proceed to the work until such inspection will be closed out and “HOLD POINT RELEASED” will signed by CLIENT.
• All inspection documents will be filed and kept @ the site QC office for reference at any time needed.
e) FIELD TESTING PROCEDURE
• MOHAMMED AL-RASHID TRADING & CONTRACTING CO. will conduct field-testing to verify that control measures are adequate to provide a product that conforms to contract requirements.
• Field testing will be conducted under the authority of the QCM, and he or his designee shall:
a) Arrange for, or conduct, field testing in accordance with applicable test parameters (ASTM, etc.) or required standard for CLIENT.
b) Verify that facilities and testing equipment are available and comply with testing standards and ensure that testing facilities are approved by CLIENT and are validated.
c) Check test equipment calibration data against certified standards.
d) Verify that all tests are documented and submitted as part of quality control system reporting.
e) Review all test documentation prior to submittal.
f) SUB-CONTRACTOR / SUPPLIER INSPECTION PLAN
• It is where in the procedure of controlling procurement sources coming from dependable Subcontractor / Suppliers where in to ensure that each purchase conforms to the specified quality requirement.
• MOHAMMED AL-RASHID TRADING & CONTRACTING CO. will evaluate and select sources base on their ability to supply material and equipment in accordance with the project requirements and will perform quality control operations at the source, location of Manufacturer, fabrication, and assembly of items to be incorporated in the work.
• MOHAMMED AL-RASHID TRADING & CONTRACTING CO. Quality Control representative shall be responsible for the approval and release of materials and components for the shipment and control the quality of purchased material and equipment to the site.
• MOHAMMED AL-RASHID TRADING & CONTRACTING CO. will submit certified copies of the supplier’s quality control procedures, where applicable, that the supplier uses to assure manufacturing to uniform quality of products, including color, dimensions, and materials and shall keep the quality records received from the suppliers, manufacturers, fabricators and the like to ensure availability of data for assessment of quality.
• MOHAMMED AL-RASHID TRADING & CONTRACTING CO. will submit to CLIENT a vendor approval for certain suppliers containing their complete information about their company background, previous projects completed. Testing, and Technical Specification of their product.
g) PRE-INSTALLATION QUALITY CONTROL
• As standard practices requirements, prior to installation of a certain portion of the work, pre-installation will be conducted prior to the start of the new activity. The inspection requirement will cover the following.
a) Surface condition for the work to be performed must be ready to start the new application.
b) Work coordination to the other trade of the construction (Mechanical and Electrical works) if needed, must be fixed first prior to proceeding.
• No work will be started until all preparation of the surfaces and materials required prior to proceeding will be closed out.
h) INSTALLATION QUALITY CONTROL
• MOHAMMED AL-RASHID TRADING & CONTRACTING CO. will perform works with the quality control guidelines and procedures as per CLIENT requirements and contract specification.
• The following guidelines are included.
a) Checking all materials to be used on the execution is as per approved Technical/ Material Submittal and on the Materials Inspection, Request approved by CLIENT for the item during the time of delivery.
b) Ensuring to control and monitor the quality performance over suppliers and manufacturers, products, services, site conditions, and workmanship, to produce work of specified quality base on contract specification and drawing requirements and comply with the manufacturer’s applicable instruction and recommendations for installation based on the approved technical submittal.
c) Compliance with required contract specification and Drawing requirement.
d) Only qualified personnel that are capable or have expertise for the item are allowed to perform the job.
e) All materials to be used or to be installed are as per approved materials by CLIENT.
f) Compliance with manufacturer’s tolerances.
g) Clarification to CLIENT will be raised if ever there’s conflict between the manufacture’s standard with the Contract Document and specification prior to proceeding.
h) All work dimensions and measurements will be reviewed prior to proceeding.
12. CONTROL OF MOCK-UP CONSTRUCTION
a) SCOPE
• This Section describes the requirements making a “Mockup Sample” to a certain job to which it is required by Client as per specification requirement.
b) PROCEDURE
• Prior to constructing any Mock-up samples for certain activity that is in need.
MOHAMMED AL-RASHID TRADING & CONTRACTING CO. will make a Method of Statement for the certain activity mentioning the sequence of activity on how to perform and complete the certain job.
• This Method of Statement will be submitted to CLIENT for approval.
• After CLIENT approves the Method of Statement, Mock-Up construction will be followed at site.
• Mock-Up construction includes the following:
• Construction will be built as per the desired finish requirement, using all finish materials specified in IFC Drawing and Contract Specification for the complete work.
• Install a mock-up using acceptable products and manufacture approved installation methods.
• Maintain mock-up during construction for workmanship comparison.
• Incorporate mock-up into final construction upon the Client approval.
• Obtain the CLIENT acceptance of finish color, texture and pattern, and workmanship standard.
• All locations, sizes and dimensions of the Mock-ups sample is as per indicated in the respective product Specification Section, drawing requirement or as directed by the CLIENT.
• Test specimen and assemblies will be provided if required for that activity.
• The CLIENT approval of the mock-ups shall be obtained before starting work, fabrication, or construction.
• The accepted mock-up will be the construction standard of the works until the entire activity is completed.
• Remove and legally dispose of mock-up when no longer required.
13. QUALITY RECORD CONTROL
a) SCOPE
• This Section describes the control system for identification, collection, indexing, filling, storage, maintenance, and disposition of the quality records.
b) RESPONSIBILITIES
• The QC Manager is responsible for collecting and maintaining all the QC records generated throughout all the construction phases.
• He is responsible for the control of quality records which are generated in his organization and maintenance of quality records.
c) GENERAL
• All quality records must be legible and identifiable to the specific product involved. The quality records shall be maintained to demonstrate achievement of the required quality and the effective operation of the quality system.
• Pertinent subcontractor quality records shall be included in the quality record.
d) COLLECTION / FILING
• The responsible QC Engineer shall collect the identified quality records.
• The quality records shall be stored and maintained in such a way that they are readily retrievable in facilities that provide a suitable environment to minimize deterioration or damage and to prevent loss.
• The quality records shall not be removed from the storage facility without the permission of the QC Manager.
• The quality records are maintained in copies.
• Quality records shall be made available for evaluation by the CLIENT.
• As control of records in concern, MOHAMMED AL-RASHID TRADING & CONTRACTING CO. Provides a separate room (Documents Control Room) to protect and secure all Quality related documents in project in order that all records are updated and traceable.
14. MATERIAL AND EQUIPMENT STORAGE
a) SCOPE
• This Material Controller is responsible for providing secure storage areas or stock rooms for the transportation of products to prevent damage, loss, or deterioration.
B) RESPONSIBILITIES
• This Material Controller is responsible for providing a secure storage area or stock room to prevent damage or deterioration of product, pending use or delivery, and the condition of product in stock shall be assessed at appropriate intervals.
• The QC Manager is responsible for verifying that all Equipment / Materials are in good condition.
c) GENERAL
• Handling, storage, packaging, and transportation of products shall be performed in a safe manner.
• Handling of products shall be conducted using suitable means in order to prevent.
d) PROCEDURES
• MOHAMMED AL-RASHID TRADING & CONTRACTING CO. will prepare procedures and shall be established at site to control receipt, handling, storage, and preservation of material and equipment in accordance with all applicable specifications, manufacturer recommendation and standards.
• All materials delivered to construction site should be as per approved technical or material submittal by CLIENT.
• Any delivered material that does not comply with and conform to the requirement will not be accepted and will be rejected and returned to the sender otherwise an NCR will be issued.
• Prior for requesting for material inspection for the delivered materials, MOHAMMED AL- RASHID TRADING & CONTRACTING CO. will conduct an internal inspection to the said material whether it conform to the baseline requirement.
• All materials or equipment delivered at site is subject to CLIENT inspection and approval. Using the standard format from CLIENT for material inspection (MIR) (SEE ATTACHED APPENDIX – N). This process will be conducted and with the presence of Client representative.
• MOHAMMED AL-RASHID TRADING & CONTRACTING CO. will provide specific area (store) separate by every discipline (Civil, Electrical, Mechanical) to have a good and secure storage of the materials. Company provides one (1) person in-charge for every department as storekeeper for the security purposes and monitoring as well.
• The procedure for the inspection of receipt and storage of permanent material and equipment shall include the following:
• Material Receipt and Storage Requirement, using the Client standard format and filling up all the data required. (SEE ATTACHED APPENDIX – O), completed for each item of permanent plant material and equipment. After Stored the Materials / Equipment’s MOHAMMED AL-RASHID TRADING & CONTRACTING CO. will perform periodically inspect the Materials / Equipment using the standard form of CLIENT (SEE ATTACHED APPENDIX – P)
• In case that there is some material or equipment that does not conform to contract specification and drawing requirement it will be rejected and not accepted and to be returned to the supplier or manufacturer otherwise an NCR will be issued for the item.
• All documents are compiled in file boxes with specially designated names and filled on a one cabinet shelf in a manner that can be easily traced.
• Cabinet’s shelves are divided and categorized by discipline (Civil, Mech & Elect.) and all Quality Control Reports and documents.
15. TRADING & CONTRACTING COMPANY a) EMPLOYMENT OF AGENCY
• MOHAMMED AL-RASHID TRADING & CONTRACTING CO. will provide an Independent Testing Laboratory with Sub-contractors / Suppliers (3rd Party) for all test required to the project according to contract specification and Contract documents requirements. This third party is the person responsible for all testing conducted at site or at their office thereof.
• MOHAMMED AL-RASHID TRADING & CONTRACTING CO. will prepare the PreQualification documents of the said independent laboratory agency and to be submitted to CLIENT for approval.
• MOHAMMED AL-RASHID TRADING & CONTRACTING CO. documents includes:
• Organization
• Human Resources
• Quality of Services
• Test capabilities
b) ORGANIZATION AND MANAGEMENT OF AGENCY
• Organization includes the following.
• Admin and Account section
This unit is overall responsible for administration of MOHAMMED AL-RASHID TRADING & CONTRACTING CO. including:
• Arranging visas and hiring of personnel
• Maintenance of accounts and invoicing
• Follow-up with different related Government offices.
• Material Testing Section
The Material Testing Unit conducts all business relating to testing of materials both in the field and in laboratory coordinate with Sub-Contractor/Suppliers. This unit also arranges to supply the on-site quality control / quality assurance crew’s and on-site / field laboratories as and when required by clients.
• Logistic Support & Procurement Section
This Unit provides all logistic support to the Geotechnical, Materials testing and Survey units.
• Reproduction Section
This section is responsible for drafting, typing and reproduction of geotechnical and material testing reports. This section also runs computer programs.
• Surveying Section
This section is responsible for staking and surveying test locations for coordinated and ground elevations for a geotechnical or material testing study before starting the project.
• Maintenance and Garage Section
This section keeps in stock the spare for all rig/equipment and carries out the day-today maintenance of the machinery. Check and maintain all the equipment/vehicle in good condition is the responsibility of this section. This section is supervised by the Procurement Department.
c) Human Resource
• MOHAMMED AL-RASHID TRADING & CONTRACTING CO. employees highly qualified and experienced Project Managers, Dept. Managers, Engineers, Supervisors, Mechanics, Electricians, Administrative staffs, Procurement staffs, Secretaries.
• MOHAMMED AL-RASHID TRADING & CONTRACTING CO. directly recruits the workforce from different countries include but not limited to India, Pakistan, Philippines, Bangladesh, Egypt, Jordon, etc.
• The personnel organization structure represents the following:
• Board of Director
• He is the overall in-charge of MOHAMMED AL-RASHID TRADING & CONTRACTING CO. and function as Technical & Administrative Head of the group.
• He participates in the preparation of the Bid proposals, undertakes the business promotion, attends negotiation and meetings, and reviews some important reports & decisions.
• He is a B.E from University of Texas, Austin. In Civil Engineering and has 37 years’ experience that included Ministry of Transportation, Ministry of Finance, Road & Infrastructure Companies, Ministry of Higher Education, Defense, GOSI, etc. projects in the Kingdom.
• General Manager
• He is the overall in charge for Technical Operations head of the group.
• He participates in the preparation of the Bid proposals, undertakes the business promotion, attends negotiation and meetings, and reviews some important reports & decisions. He takes care of all the projects.
• Deputy General Manager
• Project Managers
• Department Managers
• Bidding Manager
• Human Resource Manager
• Cost Control Manager
• Planning & Materials Manager
• Procurement Manager
• Chief Executive Officer
• He is the overall in charge of Accounts & Finance head of the group.
• He participates in the preparation of the Bid proposals, undertakes the business promotion, attends negotiation and meetings, and reviews some important reports & decisions.
• Chief Finance Officer
• Government Relation Officer
d) Quality Services
• To maintain the high standard of accuracy the following procedure will be followed:
• MOHAMMED AL-RASHID TRADING & CONTRACTING CO. will get and then analyze the Profile as well as Samples from the Sub-contractors/ Suppliers before submitting the products/material to the CLIENT.
e) Test Capabilities
• To maintain the high standard of accuracy the following procedure will be followed:
• MOHAMMED AL-RASHID TRADING & CONTRACTING CO. will get and then analyze Factory Test Certificate & Routine test reports the Sub-contractors/ Suppliers before submitting the products/material to the CLIENT.
• After approved by the CLIENT, MOHAMMED AL-RASHID TRADING & CONTRACTING CO. will perform standard test, strength test, special test coordinate with Sub-contractors/ Suppliers (Electromechanical Materials) on Site.
16. INTERNAL QUALITY AUDIT
a) SCOPE
• This section describes the system for planned and documented internal quality audits to verify whether the site quality activities comply with the planned QC program arrangements and to determine the effectiveness of the site quality system.
b) RESPONSIBILITIES
• The project QC Manager has the overall responsibilities for establishment of audit schedule and audit plan, performance of audit and monitoring the effectiveness of the quality system.
c)
• He is responsible for planning, performing audits and recording audit results.
• He has the responsibilities for qualification of audit personnel.
SCHEDULING
• Internal quality audits shall be scheduled at a frequency commensurate with the status and importance of activities and performed at least once annually.
• The Audit schedules shall be approved by the QC Manager and issued for review by the Project Manager.
• The QC Manager shall review the Audit Schedule periodically and revise as necessary to assure that coverage is maintained current.
• The Quality control program is subject to CLIENT’s audit to evaluate the performance and implementation of the program whether conforming to the requirements.
• The audit will be conducted as per CLIENT standard period of the project will be completed.
• Specific period of projects that is subject to audit is as follows.
• 25%
• 50%
• 75%
• And Final.
TEMPERATURE: CONTRACTOR DAILY SCHEDULE
MAXIMIMUM: MINIMUM:
CONSTRUCTION OF:
DATE: DAY:
CONTRACTOR:
CERTIFICATE:
I CERTIFY
SUPERVISING COMPANY REMARKS:
Appendix - B2
DATE:
Submittal No:
SUBMITTAL INFORMATION SHEET
Date of Submittal:
Manufacturer: Item Description:
Supplier: Location: Building:
Specifications Details: BOQ Detail: Page No: Item No:
Brand Name: Items Submitted:
Model No:
Capacity:
Elect./Mech. Characteristic:
General Information:
Engineer’s Comments:
Contractors
Date: Date:
Certificates
Specifications Manufacture Data
Drawings
Inst. Procedure
Samples
Catalog Cuts
SUBMITTAL INFORMATION SHEET (CLIENT/CONSULTANT)
Submittal No:
Early Required Date of Material:
Submittal No:
Specification Ref:
Late Required Date of Material: BOQ Ref:
Subject:
Manufacture Name and Address: Local Agent or Supplier: Attachments:
Technical Brochure
Certificate
Manufacturers Dir. & Specs.
Shop Drawings
Samples
O & M Manuals
Material Description:
Estimated Delivery Time to Site:
Contractors Comments: Local Supplier:
Spare Parts Lists
Warranty As Built Drawings
Others
Engineer’s Comments:
From Consultants to Client:
The above submittal was received and studied according to the relevant documents and our comments are as follows:
Conclusion:
Approved
Date:
Approved As Noted
Client’s Representative:
Rejected for Reasons Stated Above
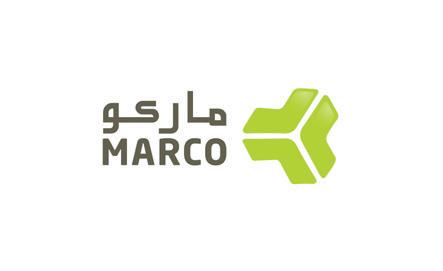

To:
TECHNICAL QUERY Appendix - E FOR CONTRACTORS USE
From:
Project No: TQ No:
Late Required Date of Material: BOQ Ref:
Problem: Please identify all relevant drawings / specifications. To be filled in by the originator.
Signature:
Position:
FOR CONSULTANT CONSTRUCTION TEAM USE
Proposed Solution: (If Applicable) To be filled in by the Consultant construction team
Date:
Signature: Position:
Actions to Consultant Main Office for Reply: Yes No
Approved by Consultant (Construction)
FOR CONSULTANT TECHNICAL SERVICES USE
Date:
Date:
Proposed Solution:
Signature:
Approved by HOTS:
Distribution:
Construction Team Project Master File
Resident Engineer
Position:
Date:
Date:
Architect
Electrical Engineer
Mechanical Engineer
Project Title:
TECHNICAL QUERY STATUS LOG SHEET Appendix - F
Project Number:
Technical Query No: Technical Query Description Issued by: Issued to: Directed to ZFP Office Response Yes No Due Received
Project Title: Location:
DRAWING SUBMITTAL
New Submittal
Resubmittal
Submittal No:
Previous Submittal No:
MOHAMMED AL-RASHID CO. (MARCO)
Project Number:
Submittal Date: / /
Previous Submittal Date: / /
PURPOSE OF SUBMITTAL: For Information For comments For Approval
CIVIL ARCHITECTURAL STRUCTURAL PLUMBING ELECTRICAL OTHERS
TYPE OF DRAWING: SHOP DRAWING AS BUILT DRAWING CLIENT DRAWING
DRAWINGS: NOTE: PLEASE USE THE ATTACHMENT IN CASE ITEMS ARE MORE THAN THE PROVIDED
S
Contractor’s Remarks:
CONTRACTOR ENG:
CONTRACTOR PROJECT MANAGER: Name: Name: Signature: Date: Signature: Date:
Consultant Comments:
CONSULTANT ENG:
Approval Status
Name: Signature: Date: Approved Approved As Noted Resubmittal is Required
CONSULTANT PROJECT MANAGER RECEIVED BY CONSULTANT RECEIVED BY CONTRACTOR
Name: Signature: Date: Date: Date:
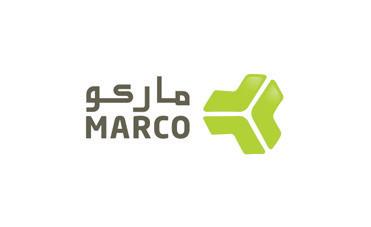
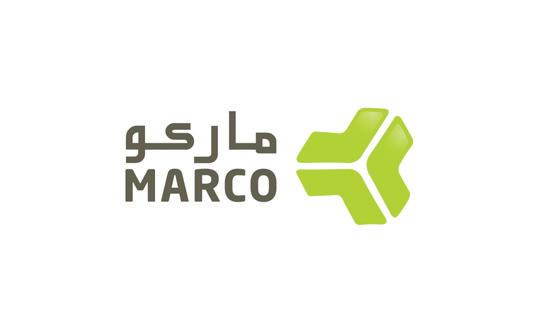
NON-CONFORMANCE REPORT
NCR NO: CONTRACTOR NAME: Page of:
CONTRACT NO: LOCATION: PAY ITEM INFO:
DRAWING / SPECIFICATION / ITEM NUMBER REV
NON-CONFORMING CONDITION RESCRIPTION:
REPORTED
DISPOSITION: Rework Repair Use as Reject
Disposition By: Contractor QC Manager Approval:
CLIENT APPROVAL REQUIRED: Yes No (Client Approval for all Repair or Use-As-Is Disposition)
CLIENT DISPOSITION: Rework Repair Use as Reject
PE CONCURRENCE: DATE: DESIGN CHANGE REQUIRED: Yes No
DRAWING / SPECIFICATION NUMBER: REV: DCN NUMBER:
PPE CONCURRENCE:
REINSPECTED BY CONTRACTOR:
Cause of Non-Conformance
Action Taken to Prevent Reoccurence
Acceptance of Corrective Action: Contractor QC Manager
CLIENT Acceptance for Final Closure:
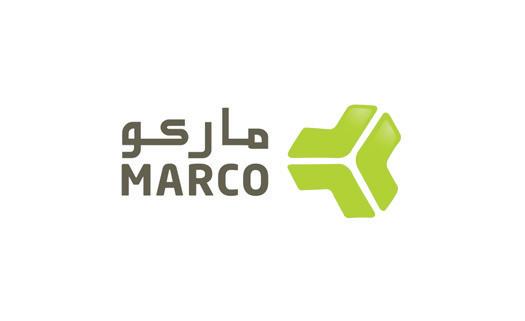
DATE:
CONTRACTOR:
CONTRACTOR NO:
CONTRACTOR TITLE:
LOCATION:
PREPARED BY:
CHECKED BY:
CONTRACTOR ENGINEER CLIENT ENGINEER
REQUEST FOR INSPECTION OF WORK RFI NO: #
PROJECT:
DATE:
The following section(s) of the works has (have) been completed and we respectfully request that you inspect and approve the work.
BUILDING SECTION:
1. Required Checking Point:
2. Required Checking Date:
3. Drawing Reference:
Appreciate your kindness and awaiting the favor of your prompt response.
Attached: Location Plan Date:
SIGNATURE OF ENGINEER IN-CHARGE:
Recipient Signature:
CLIENT COMMENTS:
CLIENT DEPARTMENT
CIVIL ARCH ELECT MECH
SIGNATURE OF PROJECT MANAGER:
SIGNATURE OF APPROVAL
RECEIPT
DATE
MOHAMMED AL-RASHID CO. (MARCO)
INSPECTION / TESTING HOLD POINT
1 WORK AREA / LOCATION:
2 DOCUMENTS / DRAWING NO:
3 DESCRIPTIONS OF ACTIVITY / WORK:
HPR No.
DATE:
Testing (Required or Not, Procedures, Kind of Test)
CIVIL MECHANICAL
ELECTRICAL
PAY ITEM:
WORK: 1) May Proceed: 2) May Not Proceed: Date of Inspection: Time of Inspection:
REMARKS: HOLD POINT RELEASED BY:
Date: Time:
Date: Time:
ATTN: CLIENT LEAD FIELD ENGINEER
Permission to proceed does not constitute Final Acceptance or Resolution of Quantities for unit price work. Calculations, Analysis or other Contractors furnished backup attached to this “Hold Point Release Form” serve as Contractor’s preliminary support documentation subject to final reconciliation by CLIENT and the Contractor.
MOHAMMED AL-RASHID CO. (MARCO)
MATERIAL INSPECTION REQUEST (MIR) Appendix -
MIR No.
DATE:
SUBMITTAL NO:
LOCATION:
DRAWING NO:
DESCRIPTION OF MATERIAL:
PAY ITEM (S):
Permission to proceed does not constitute Final Acceptance or Resolution of Quantities for unit price work. Calculations, Analysis or other Contractors furnished backup attached to this “Hold Point Release Form” serve as Contractor’s preliminary support documentation subject to final reconciliation by CLIENT and the Contractor.
REMARKS:
INSPECTION BY Q.C DEPARTMENT (MARCO)
MATERIAL INSPECTION RELEASE BY CLIENT ENGINEER
QC ENGINEER: NAME:
SIGNATURE:
SIGNATURE:
QC MANAGER: DATE
SIGNATURE:
MATERIAL / EQUIPMENT AND STORGE REQUIREMENT
CONTRACT NO:
DESCRIPTION OF MATERIAL / EQUIPMENT:
Pay Item No: Supplier:
Receiving Inspection Procedure:
Documentation Requirements:
STORAGE AND MAINTENANCE REQUIREMENTS: DATE RECEIVED
DATE:
CONTRACTOR:
PREPARED BY:
CHECKED BY:
CONTRACTOR ENGINEER CLIENT ENGINEER
PERIODIC INSPECTION LOG FOR THE STORED MATERIALS AND EQUIPMENT
PERIOD OF INSPECTION: EVERY 30 DAYS (MONTHLY)
DISCIPLINE:
CIVIL
ELECTRICAL
MECHANICAL
DATE OF INSPECTION:
DATE OF LAST INSPECTION:
STORAGE AND MAINTENANCE REQUIREMENTS:
PREPARED BY:
CONTRACTOR ENGINEER
CHECKED BY:
CLIENT ENGINEER
LOST TIME INCIDENT REPORT
Lost Time Injuries are the sum of fatalities, permanent total disabilities, permanent partial disabilities and lost workday cases.