
5 minute read
Scott Barnes
Learning the Language of Sealants Choosing the right concrete coating depends on the project
SCOTT BARNES
Advertisement
In our business we often hear phrases that use the word “seal” in relation to concrete decks. Coming from property owners, condo board members and property managers, the word has so many meanings and far-reaching implications that we usually stop the conversation right there and start asking questions to narrow down what it is that they want to achieve. Ask 10 people what “sealing the concrete” means to them and you will likely get 11 answers!
As a rule of thumb, “sealing” to a licensed concrete coating contractor means either installing a waterproof coating, decorative coating or penetrating coating, or maybe a combination of coatings depending on the structure.
To further complicate things, each of these coating types has sub-categories, grouped by material, application and finished appearance. There are even some waterproofing coatings that still “breathe.”
Understanding the language used in concrete coatings also is important so both client and contractor are on the same page. Words you might hear or come across in a proposal or in researching coatings include elastomeric, solvent-based, water-based, cementitious, penetrating, on-grade, above-grade or elevated, primer coat, base coat, wear coat, texture coat, top coat and clear coat.
As an estimator, I usually start by asking whether the structure to be coated is elevated or on-grade? This is key, and depending on the answers to the next few questions there could be multiple options. Or maybe just one.
My next question usually is about traffic—is it vehicular or pedestrian?
At this point I am narrowing down the options available and starting to formulate additional questions that will ultimately give me one or two recommendations.
Next question: Are you trying to protect the concrete or change its appearance, or both?
Next I ask the client what they want to see as a finished project. What do they expect the coating to do or solve? How long do they expect it to last, and what is their expected level of maintenance?
I usually get asked about coatings for four basic types of structures: parking decks, pool decks, walkways/lanais and planters.
Parking decks and walkways are usually the easiest to provide recommendations for, because by their very nature they are “elevated” and should be waterproofed. Typically, that waterproofing type is the multi-layer elastomeric coating. They start with a primer

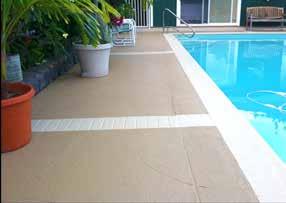
and base coat to seal the concrete in a non-breathable “rubber” coating. The rubber coating of course needs to be protected so additional layers of material are added on top of the primer and base coat. For vehicles, it is usually two wear coats in driving lanes and a single coat in parking stalls.
Elevated deck waterproofing usually involves coating the whole concrete slab on every elevated floor, but there are some parking decks that only receive the coating at the parking stalls that are open to the environment (rain). This is less costly than coating the whole structure, but in my opinion does not fully consider wind-swept water being moved into the driving lanes, causing wheel spin and sliding by cars and pedestrians moving across wet floors.
In cases like this, maybe the parking stalls should be coated with an elastomeric, and critical known areas of pedestrian traffic or vehicle turns
can have an epoxy coating application for the added traction. Typically, epoxy coatings wear like iron and very rarely need repair or refreshes, or need to be removed and reapplied like the elastomeric coating that can rip, bubble and tear over time. Epoxy coatings are typically installed out of direct sunlight and would be considered the premium of coatings.
One point that needs to be clarified here is that the waterproof coating only gets applied to the horizontal surfaces of the elevated concrete deck and if possible, the edges. The coating does not get applied to the underside of the deck (the ceiling of the deck below.) If it was applied on all sides of a deck it would totally encapsulate the slab and prevent the “breathing” that is necessary to longevity in concrete.
The breathing of concrete is necessary to allow moisture to flow in and out of the concrete continuously. You might not think that solid concrete is “wet,” but a recent survey of a pool deck at a major hotel being prepared for a new coating revealed a relative humidity rate in some areas above 90%. This kind of moisture is problematic for coatings but it is not impossible; it just requires additional moisture mitigation work.
The next most requested structure are pool decks. Again, the right product requires knowing if the pool deck is on-grade or elevated. Elevated pool decks have a choice of coating types. Because they are elevated and need protection, they can receive an elastomeric coating. Or if a more pleasing appearance is required, they can receive a cementitious coating as long as there is a waterproofing membrane incorporated into the cementitious product and not an underlying one already there under a topping slab.
With the waterproofing component, cementitious coatings are perfect for elevated pool decks, rec decks, walkways and lanais. Cementitious coatings feel great on bare feet. They have at least three texture finishes and have multiple color choices, custom stains, custom patterns and borders, and can be repaired easily and usually imperceptibly.
Cementitious coatings are by definition using a cement base. Cement is put down with a hand trowel by skilled masons, which is different than the elastomeric which is usually put down by a roller. The cement is mixed with polymer to provide a thinness not capable with standard concrete.
Typically, elastomeric coating costs less than cementitious coatings.
On-grade pool decks, walkways and lanais should not receive a waterproofing coating, only a breathable coating, which typically shifts the coating choices back to the cementitious coating.
With planters, usually they are leaking by the time I get called. Typical solutions for leaking planters range from simple crack repair to full removal of contents, concrete spall repair and then recoating with a waterproofing that could be full epoxy to elastomeric.
The last two coatings that I want to talk about are epoxy coatings for interior decks/floors and penetrating sealers. Epoxy coatings are excellent as industrial coatings for warehouses and custom epoxies are incredibly decorative finishes for homes, churches, showrooms etc. If you want protection and/or a totally custom finish on an interior floor, I suggest looking at epoxy floor offerings. ❖
Scott Barnes is a concrete specialistestimator with Central Pacific Specialty Contractors. He has over 10 years of experience in concrete restoration, concrete repairs, epoxy injections, concrete coatings, decorative concrete coatings, waterproofing and pools. His specialty is the repair and maintenance of concrete for the owners and managers of low-rise apartment building walk-ups. Reach him at 255-1794 or scott.b@cpschawaii.com.
