SERVICE MANUAL
L213 / L215 / L218 / L220
L223 / L225 / L230
200 Series Skid Steer Loader
C227 / C232 / C238
200 Series Compact Track Loader
Part number 84522361
1st edition English
June 2011
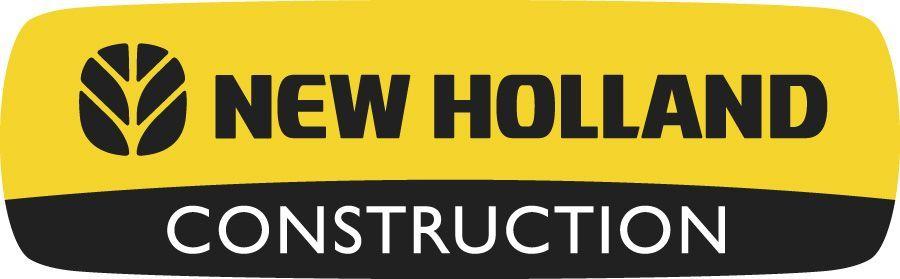
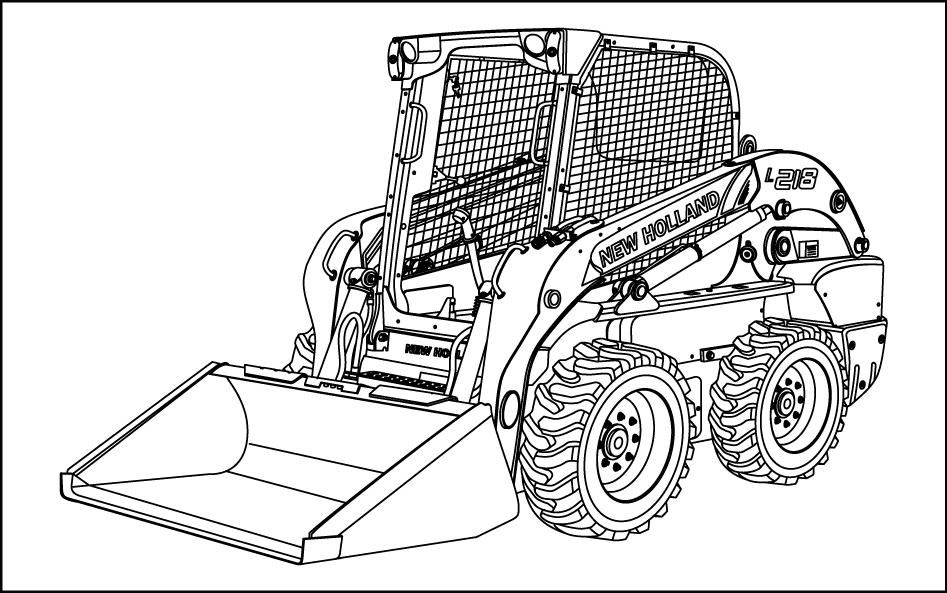
BOOM Lift
ARM T OOL A ACHMENT T ilt
SINGLE ARM Lift
SINGLE ARM T OOL A ACHMENT T ilt
EXCA V A TING AND LANDSCAPING
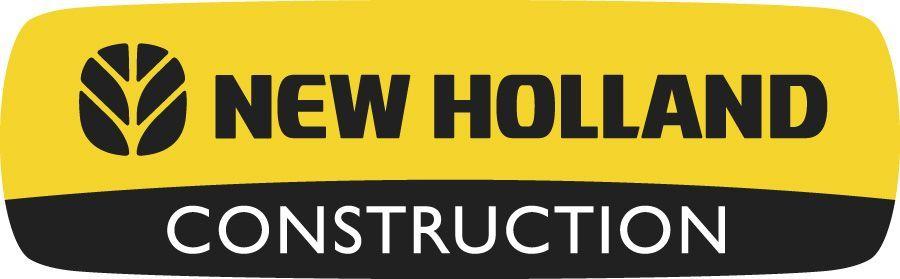
Foreword - Ecology and the environment
When legislation does not yet rule the treatment some the substances which are required advanced technology , sound judgement should govern the use and disposal products a chemical and petrochemical nature.
air , and water are vital factors agriculture and life
NOTICE: The following are recommendations which may
assistance:
• Become acquainted with and ensure that you understand the relative legislation applicable your country
• Where legislation exists, obtain information from suppliers oils, filters, batteries, fuels, antifreeze, cleaning with regard their fect man and nature and how safely use and dispose these
• Agricultural consultants many able help you
HELPFUL HINTS
• A void filling tanks using cans inappropriate pressurized fuel delivery systems which may cause considerable
• avoid skin contact with all
Most them contain substances which may harmful your
• Modern oils contain additives. not burn contaminated fuels and waste oils ordinary heating systems.
• A void spillage when draining f used engine coolant gearbox and hydraulic brake etc. not mix drained brake fluids fuels with lubricants. Store them safely until they can disposed a proper way comply with local legislation and available
• Modern coolant antifreeze and other should replaced every two They should not allowed get into the soil but should collected and disposed properly
• not open the air - conditioning system contains gases which should not released into the mosphere. Y our NEW HOLLAND CONSTRUCTION dealer air conditioning specialist has a special extractor for this purpose and will have recharge the system properly
• Repair any leaks defects the engine cooling hydraulic system immediately .
• not increase the pressure a pressurized circuit this may lead a component
• Protect hoses during welding penetrating weld splatter may burn a hole weaken allowing the loss
Personal safety
This the safety alert used alert you potential personal injury Obey all safety messages that follow this symbol avoid possible death injury
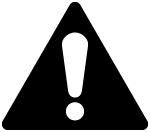
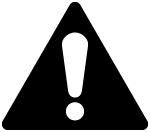
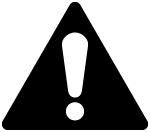
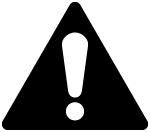
Throughout this manual and machine decals, you will find the signal words DANGER, W ARNING, and CAUTION followed special These precautions are intended for the personal safety you and those working with
Read and understand all the safety messages this manual before you operate service the
DANGER indicates a hazardous situation not will result death serious injury The color associated with DANGER
W ARNING indicates a hazardous situation not could result death serious injury The color associated with W ARNING
CAUTION, used with the safety alert symbol, indicates a hazardous situation which, not avoided, could result minor moderate injury The color associated with CAUTION YELLOW
F AILURE T O FOLLOW DANGER, W ARNING, AND CAUTION MESSAGES COULD RESUL T DEA SERIOUS INJUR Y .
Machine safety
NOTICE: Notice indicates a situation not could result machine property The color associated with Notice
Throughout this manual you will find the signal word Notice followed special instructions prevent machine property The word Notice used address practices not related personal safety
Information
NOTE: Note indicates additional information which clarifies other information this
Throughout this manual you will find the word Note followed additional information about a other information the The word Note not intended address personal safety property
Safety rules - Personal Safety
Carefully study these precautions, and those included the external attachment operators manual, and insist that they followed those working with and for you.
Thoroughly read and understand this manual and the attachment operators manual before operating this any other
Be sure everyone clear the machine before starting. Blow the horn, equipped, three times before starting
Only the operator should the machine when Never allow anyone climb the machine while the machine equipped with Instructors this must only used for training Passengers must not allowed use the Instructors
Keep all shields place. Never work around the machine any the attachments while wearing loose clothing that might catch moving
Observe the following precautions whenever lubricating the machine making adjustments.
• Disengage all clutching levers
• Lower the the ground raise the attachment completely and engage the cylinder safety locks . Completing these actions will prevent the attachment from lowering expectedly
• Engage the parking
• Shut f the engine and remove the key
Always keep the machine gear while going downhill.
The machine should always equipped with suf ficient front rear axle weight for safe
Under some field more weight may required the front rear axle for adequate stability This especially important when operating hilly conditions / when using heavy
Always lower the shut f the set the parking engage the transmission gears and remove the key before leaving the operators
the attachment machine should become obstructed plugged; set the parking shut f the engine and remove the key , engage the transmission gears, wait for all machine attachment motion come a before leaving the operators platform removing the obstruction
1 Never disconnect make any adjustments the hydraulic system unless the machine and / the attachment lowered the ground the safety lock(s) the engaged
Use the flashing lights highly recommended when operating a public
When transporting a road highway , use accessory lights and devices for adequate warning the operators other this check local government V arious safety lights and devices are available from your NEW HOLLAND CONSTRUCTION dealer .
Practice safety 365 days a year
15. Keep all your equipment safe operating condition.
Keep all guards and safety devices
Always set the parking shut f the engine and remove the key , engage the transmission wait for all machine attachment motion come a before leaving the operators platform service the machine and
Remember: A careful operator the best insurance against Extreme care should taken keeping hands and clothing away from moving
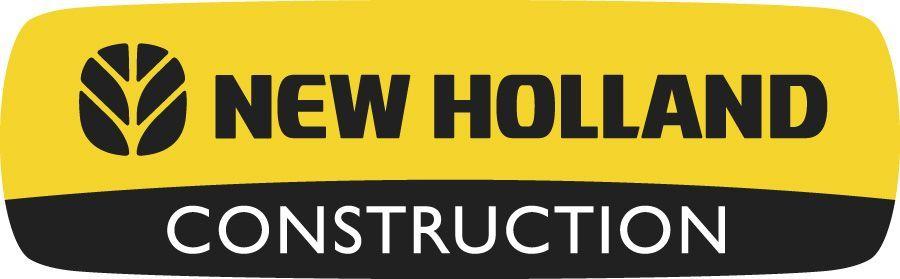
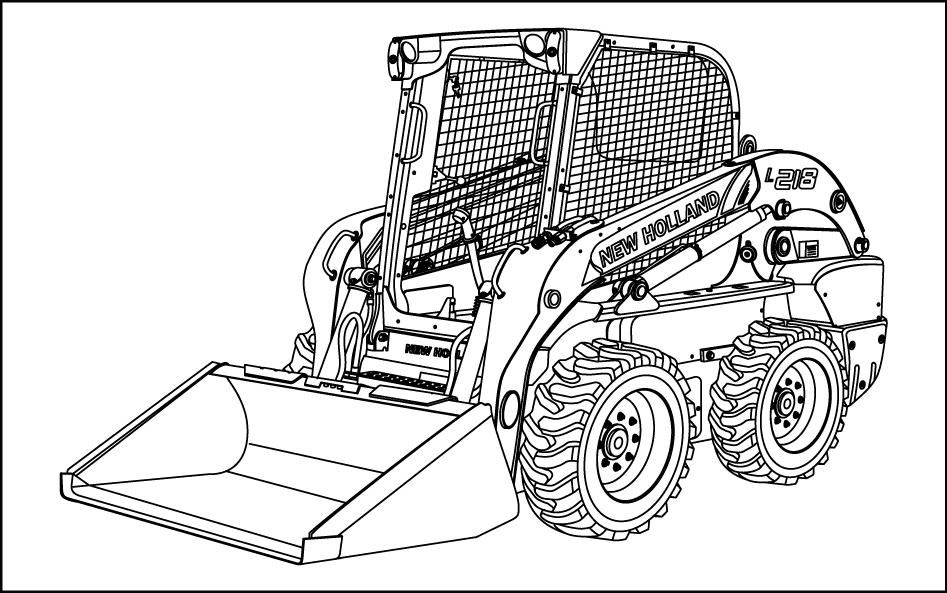
Hydraulic pump - Flow test Loader hydraulic pump
NOTE: T persons are required perform the flowmeter tests for safety avoid possible injury One person must seated the operators seat when the engine The second person control the flowmeter and take the readings.
Park the machine a level Lower the loader bucket the floor Stop the Disconnect the hose from the loader pump pressure port (1) T est Point Install a plug the Connect the flowmeter inlet hose the fitting the pressure port (1) the equipped with high flow , disconnect the hose from the high flow pressure port (2) Install a plug the Connect a second flowmeter inlet hose the fitting the pressure port (2) the pump.
NOTE: The first picture for models equipped with a draulic gear pump only The second picture for models equipped with a hydraulic gear pump with high flow
Put the flowmeter outlet hose into the hydraulic voir Use wire fasten the flowmeter outlet hose below the surface the hydraulic
Make sure that the oil level the hydraulic reservoir
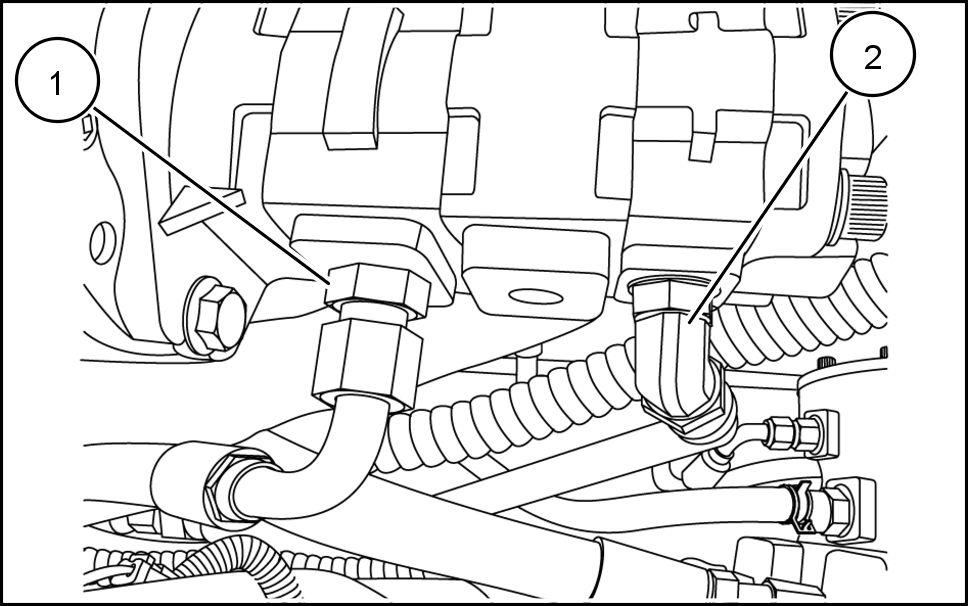
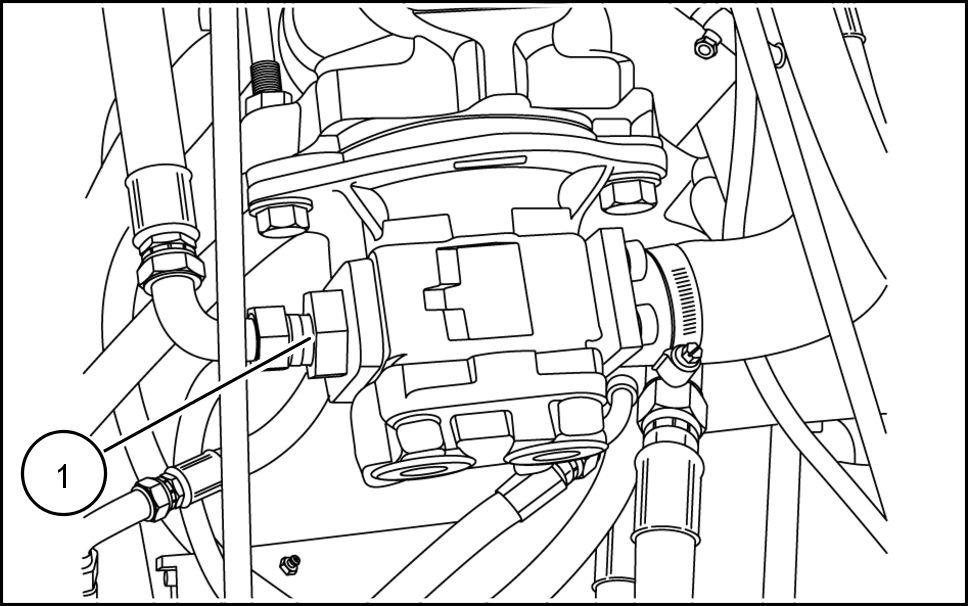
Make sure that the pressure valve the flowmeter opened completely
The oil must operating the oil not operating run the engine full throttle and close the pressure valve the flowmeter until the pressure gauge indicates 103 bar (1500 Continue run the engine full throttle until the temperature the oil 52°C (125°F). Then open the pressure valve completely
Make sure that the pressure valves are opened pletely Adjust the engine speed 2300 r / min (rpm) and read the flow Read the flow and record the reading test number 1 .
Slowly close the pressure valve the flowmeter the loader pump until the pressure gauge indicates bar (1400 Keep the engine running 2300 r / min Read the flow and record the reading test number 2 84522361 15/06/201
Slowly close the pressure valve the flowmeter til the pressure gauge indicates 124 bar (1800
Keep the engine running 2300 r / min Read the flow and record the reading test number
Slowly close the pressure valve the flowmeter til the pressure gauge indicates 152 bar (2200
Keep the engine running 2300 r / min (rpm). Read the flow and record the reading test number
1 Open the pressure valve completely the high flow pump repeat steps 8 thru the high flow Then decrease the engine speed low idle and stop the
NOTE: Understanding the results the tests are outlined the steps below .
12. the output minimum pressure was less than the specification for Gear Pump Flow Loader (Machine Neutral) refer PRIMAR Y -
DRAULIC POWER SYSTEM - General specification (A.10.A) , the problem can a restriction between the reservoir and the gear pump, the problem can a badly worn damaged gear
the output minimum pressure was more than the specification refer PRIMAR Y -
DRAULIC POWER SYSTEM - General specification (A.10.A) , there are problems between the reservoir and the gear However , the gear pump can worn damaged and still have good flow minimum
Loss output 152 bar (2200 psi) indicates that the gear pump worn T o determine the ficiency the gear pump, divide the flow cation from test number 4 the flow indication from test number This answer multiplied 100 the percent ficiency the gear the ficiency the gear pump less than repair replace the gear pump. the ficiency the gear pump more than the pump
Hydraulic pump - Install
NOTE: Before pump apply Molykote G - 4700 / N 86983138) the pump and the coupling Pre - fill the pump with clean hydraulic Inspect O - ring the pump pilot and replace necessary Lubricate the O - ring with clean hydraulic oil.
Hold the pump the mounting location. Rotate the gear pump shaft until aligns with the coupling (1) splines the rear the hydrostatic Shown with call out (X) After the splines are move the pump inward until the mounting flange flush with the mounting surface the hydrostatic pump.
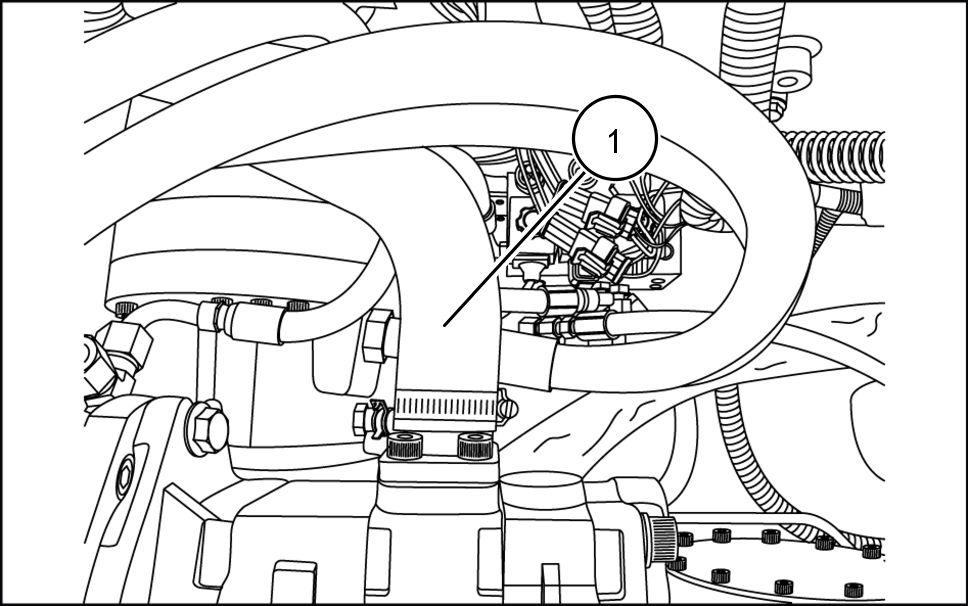
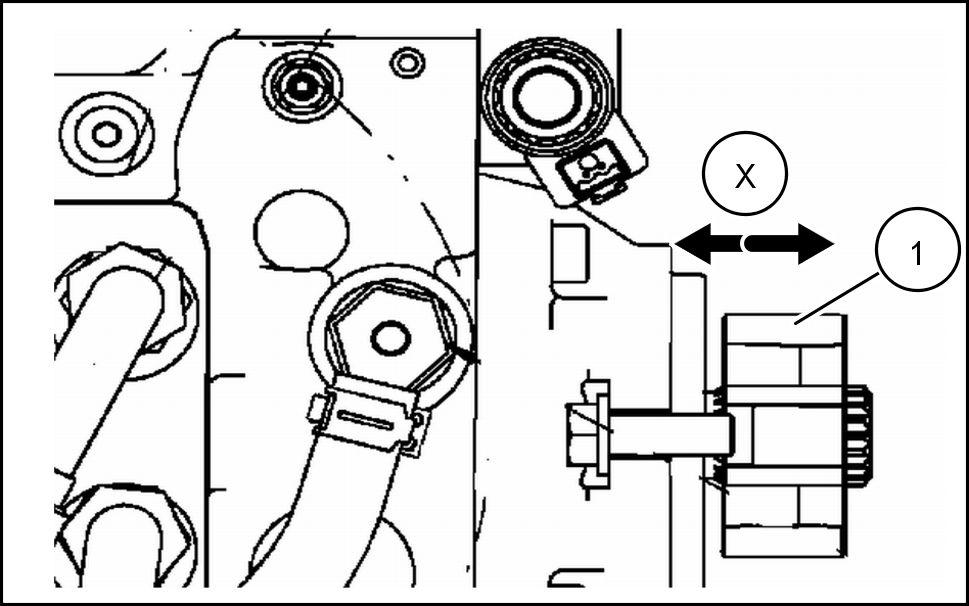
Apply Loctite 243 the pump mounting bolts (4) stall washers the bolts and install the bolts into the pump mounting T ighten the mounting bolts
Connect gear pump hydraulic hoses (A) and (B) ,
Connect the gear pump supply hose (1) and tighten hose
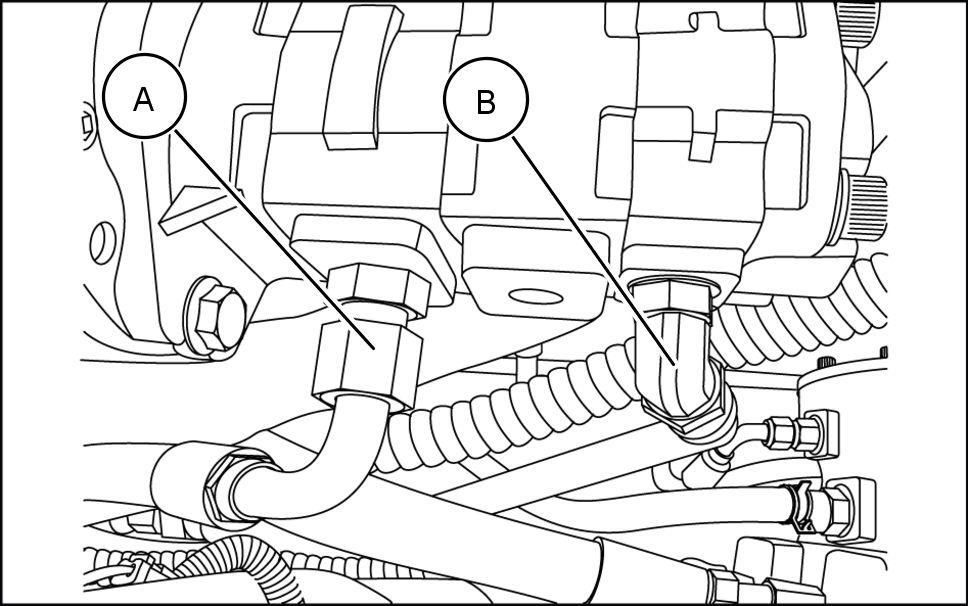
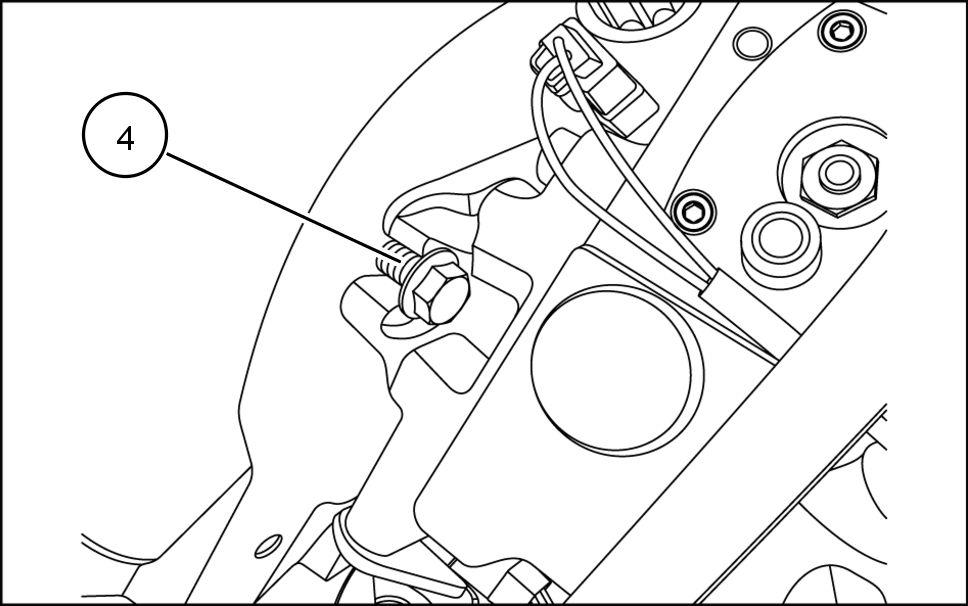
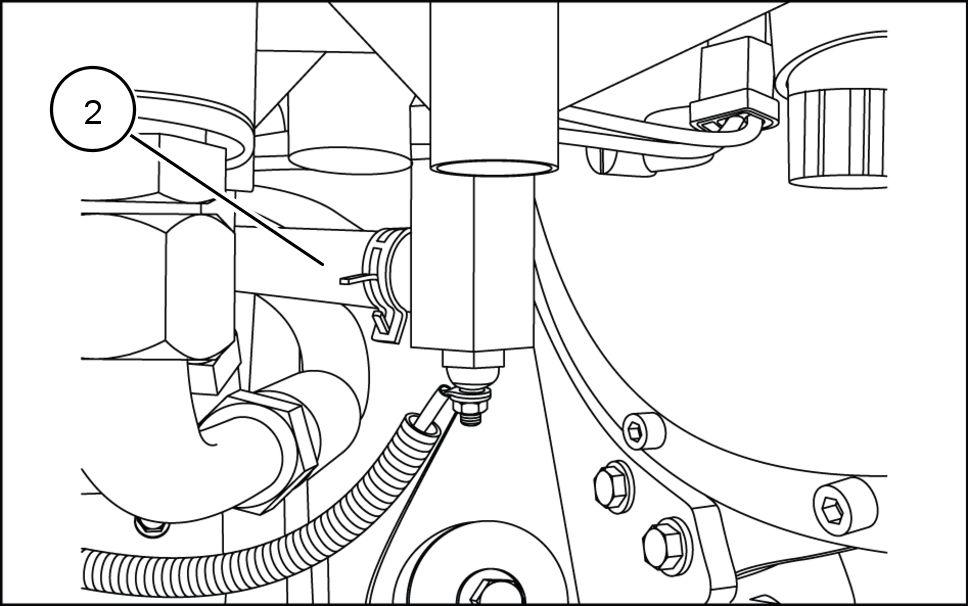
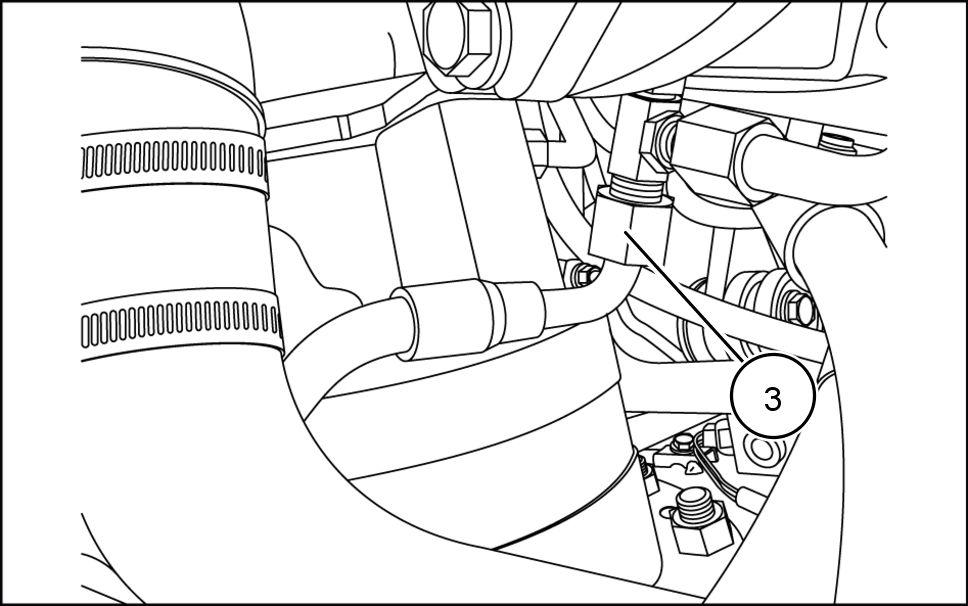
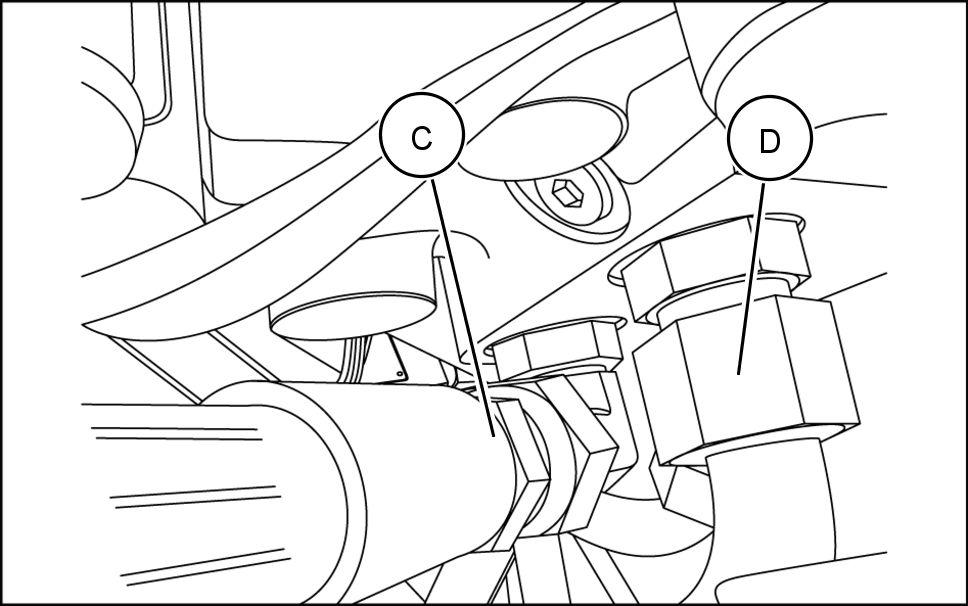
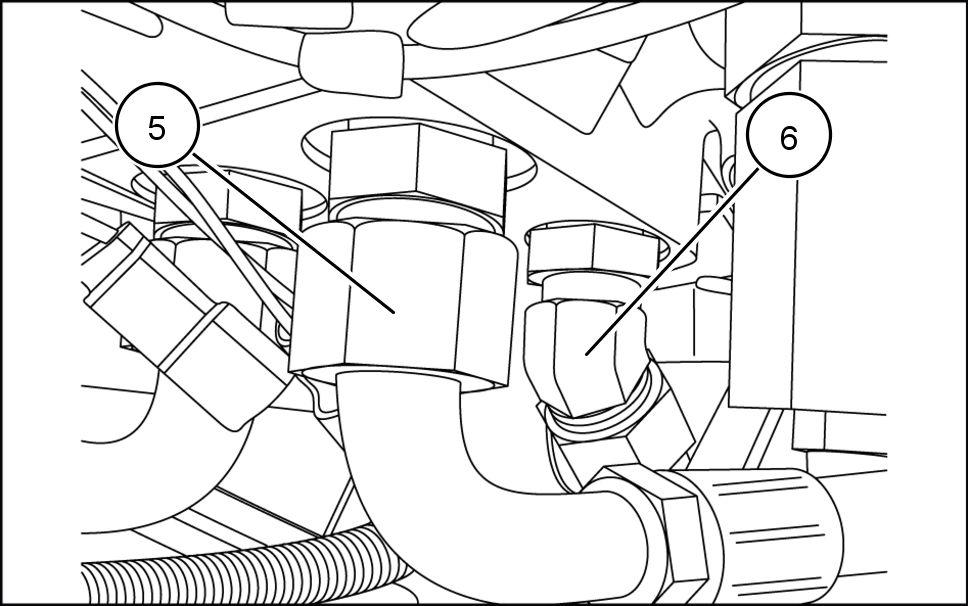

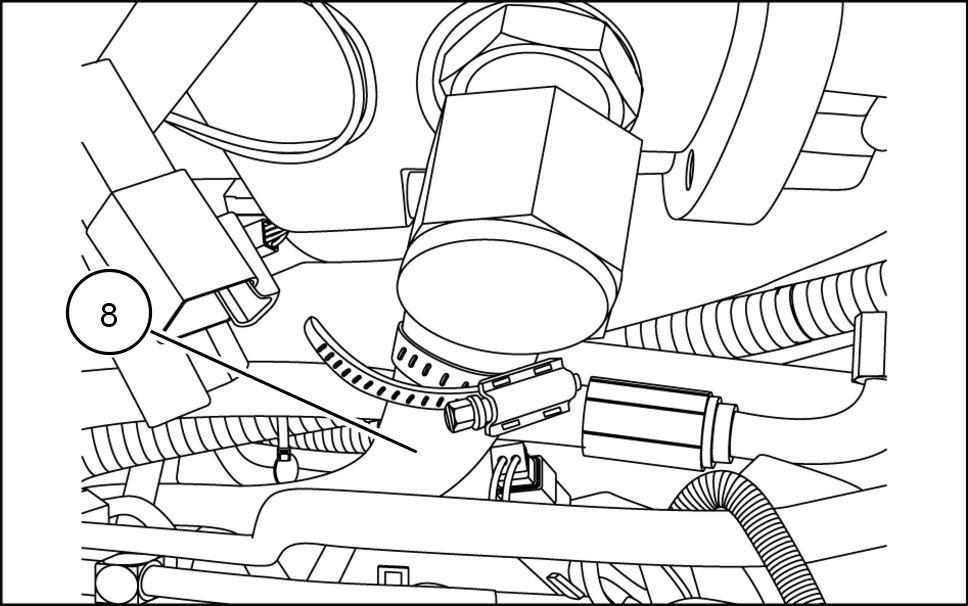
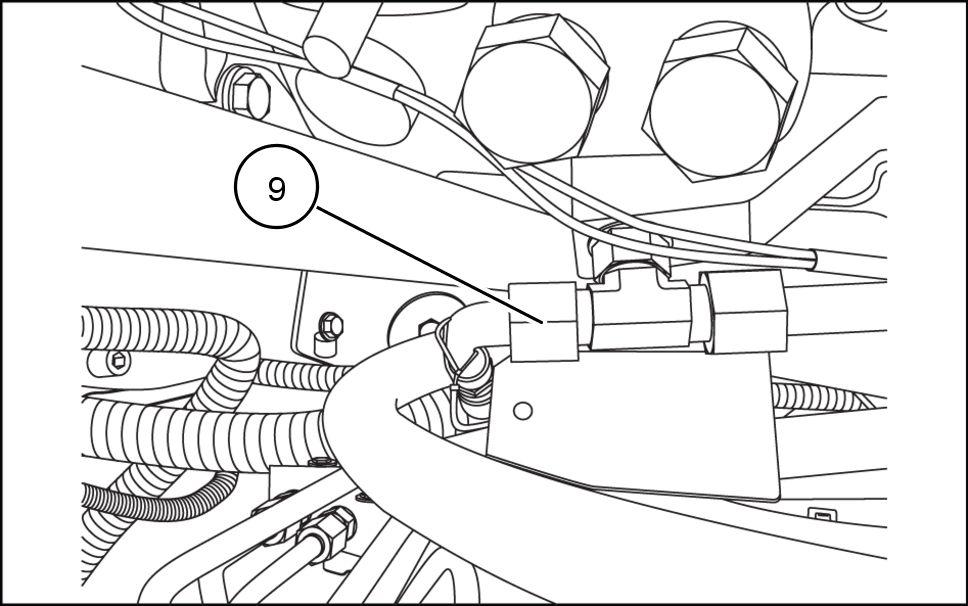
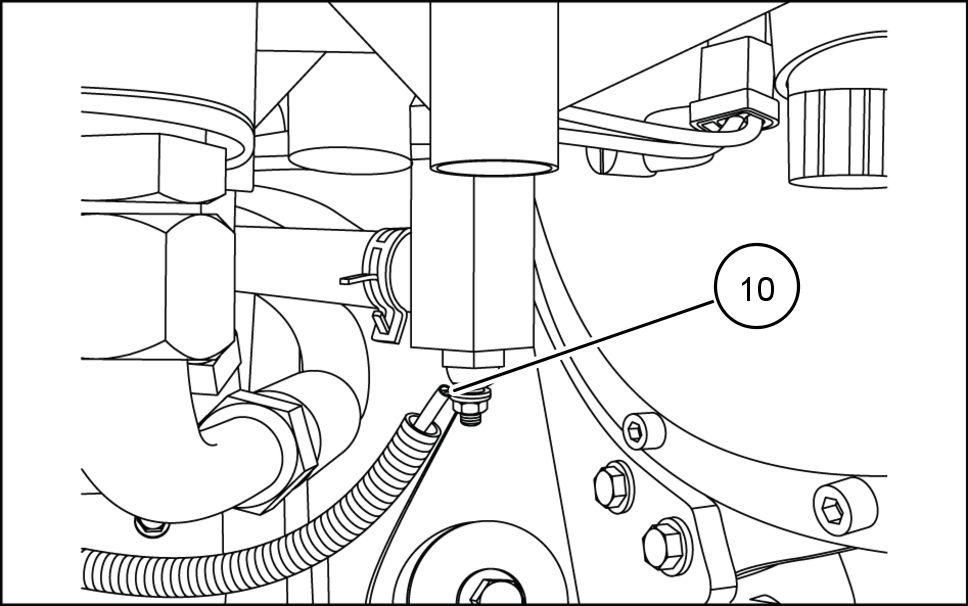
13. Connect the right hand side back alarm tions
14. Connect the left hand side back alarm tions (12)
Connect the control wires (E) and (F) located the bottom
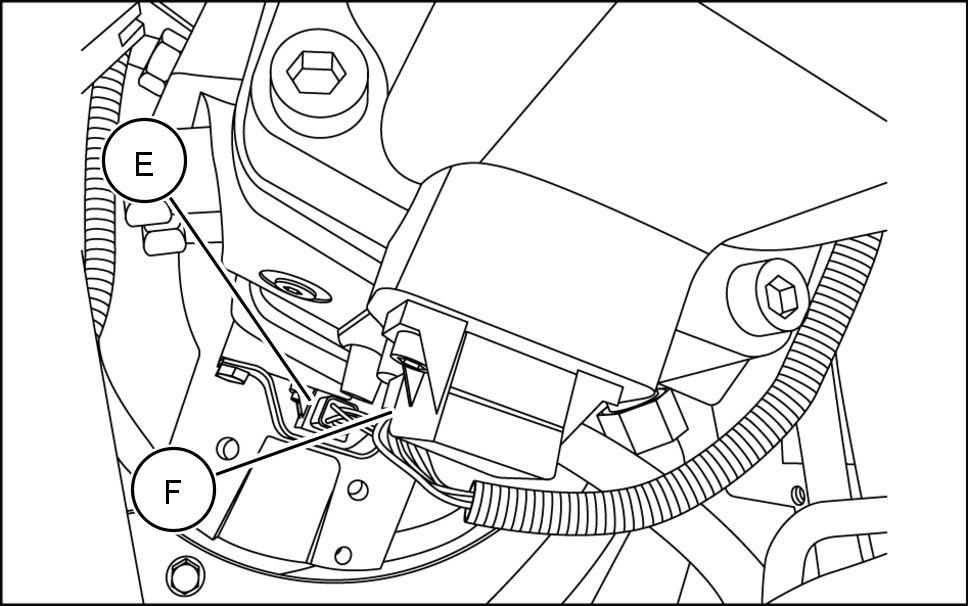

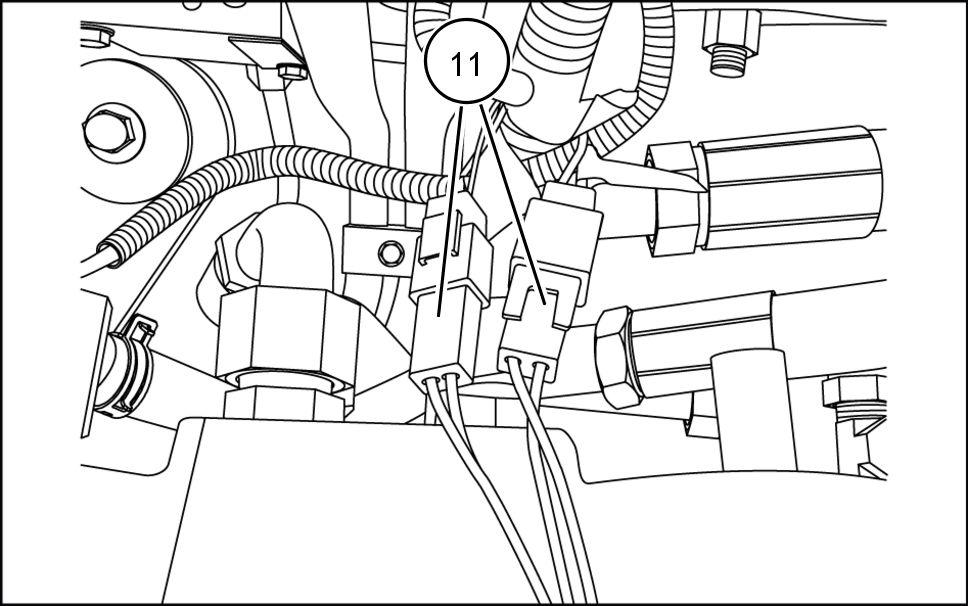
Charge pump - Pressure test
T esting the low - pressure charge system safer and usually more informative than going into the high - pressure test T o obtain much system information charge pressure readings must taken neutral well working the system both the forward and reverse
With the system only charge pressure present the closed this the leakage from the system the least and the charge pressure the the system the leakage from the system will increase and the charge pump flow will make for this With more the charge pump oil flowing the closed less oil will flow across the charge pressure relief and therefore the pressure will slightly less. the leakage from the system excessive, the charge pressure will drop f more. This slight drop charge pressure between the system neutral and with the system under load indicates the condition the closed loop system
Raise and securely block the unit f the
Remove the brake release lines from the tee fitting that connects the B port (1) the brake valve (2) and cap

Cap the tee fitting that connects the B port the brake
Connect a kPa (41 bar) (600 psi) pressure gauge the charge pressure test Remove the hose from the tee fitting and install a kPa(600 psi) pressure gauge.
the hydraulic oil not operating temperature, run the engine full throttle and hold the bucket trol lever the ROLLBACK position for Then return the bucket control lever NEUTRAL for Repeat this cycle until the temperature the oil least 52°C (125°F).
Continue run the engine full Read the pressure gauge and record the Charge Pressure Stop the
The pressure reading must - bar (362 - 410 psi) the relief valve must adjusted with the pressure step the sure not loosen the cap the hydraulic reservoir Remove the and poppet for the charge pressure relief
Inspect the parts the charge relief the parts are add shim(s) from the shim refer parts manual, and repeat steps 5 through 9 until the pressure
NOTICE: For the following test the machine MUST raised supports until the tires are above the floor . This a safety procedure the hydraulic parking brakes fail 84522361 15/06/201
10. After you get the correct charge pressure the following steps:
Start and run the engine low Increase the engine speed full equipped with 2 shift into transport (high) Slowly move one the direction control levers FOR W ARD load the hydrostatic piston pump and drive tor without decreasing the engine NOT Lug the Reduced engine speed causes creased charge pump flow , which will fect the sure readings. Repeat for the opposite side (only move one lever a
Read the pressure The pressure must within 138 kPa bar) (20 psi) the pressure step
Repeat Steps A and B with the direction control levers
Interpretation the results:
Once the charge pressure meets specifications with the levers the neutral compare the sure readings under load with the neutral The readings should highest with the levers the NEUTRAL for this when the direct ing charge relief has handle the greatest amount oil flow The maximum dif ference charge sure readings between the system neutral and the system loaded both directions must not greater than 138 kPa bar) (20 Any dif ence greater than 138 kPa (1.5 bar) (20 psi) indicates excessive leakage from the closed which will require repair
NOTE: The charge pressure drop indicates internal age from the system with the system under This caused less oil flowing over the charge relief and fore, the lower pressure. Excessive leakage (greater than 138 kPa bar) (20 psi) will result slower drive speed that side the but depending what aged the the leakage may only show under heavy load
NOTE: T o determine the problem the pump the motor the following:
1 the side (left right) that the charge pressure dropped more than 138kPa bar) cap the two high - pressure lines that supply the drive motor The lines can capped either the pump the motor , which ever
NOTE: The charge pressure drop indicates internal leakage from the system with the system under This caused less oil flowing over the charge relief and the lower Excessive leakage (greater than 138 kPa bar) (20 psi) will result slower drive speed that side the but depending what damaged the the leakage may only show under heavy load
With the lines capped the drive motor , start and run the engine low idle. Increase the engine speed full Slowly move the direction control lever that being tested FOR W ARD load the drostatic piston pump without decreasing the engine NOT Lug the Reduced engine speed causes decreased charge pump flow , which will fect the pressure
NOTE: The charge pressure drop indicates internal leakage from the system with the system under This caused less oil flowing over the charge relief and the lower Excessive leakage (greater than 138 kPa bar) (20 psi) will result slower drive speed that side the but depending what damaged the the leakage may only show under heavy load
Read the pressure The pressure must within 138 kPa (1.5 bar) (20 psi) the pressure step
NOTE: The charge pressure drop indicates internal leakage from the system with the system under This caused less oil flowing over the charge relief and therefore, the lower pressure. Excessive leakage (greater than 138 kPa bar) (20 psi) will result slower drive speed that side the but depending what damaged the the leakage may only show under heavy load
Repeat Steps 1 1 and with the direction control levers
Interpretation the results with the two high - pressure lines capped the drive motors: the charge pressure drops more than 138 kPa bar) (20 psi) the pressure step the leakage the pump.
Remember that this a closed loop hydrostatic one component the debris will sent directly the mating component and cause this damage contamination will return the reservoir through the case drain system. the very least once a failure has the ing component the hydrostatic system must spected for any contamination has been returned the reservoir , tear down and inspection both complete closed loop systems necessary since the same charge pump feeds cause the hydraulic system shares the reservoir with the hydrostatic all and components must thoroughly cleaned prevent contamination from reentering the repaired system.
NOTE: The charge pressure drop indicates internal leakage from the system with the system under load. This caused less oil flowing over the charge relief and the lower Excessive leakage (greater than 138 kPa bar) (20 psi) will result slower drive speed that side the but depending what damaged the the leakage may only show under heavy load
Charge pump - Pressure test (Machines Equipped with Controls)
Connect a kPa (41 bar) (600 psi) pressure gauge test (1) see next
NOTICE: For the following test the machine MUST raised supports until the tires are above the floor This a safety procedure the parking brakes fail
NOTE: Y will need two people perform this The operator seat must the raised position gain access the hydrostatic
the hydraulic oil not operating temperature run the engine full throttle and hold the bucket trol lever the ROLLBACK position for Then return the bucket control lever NEUTRAL for seconds. Repeat this cycle until the temperature the oil least 52°C (125°F).
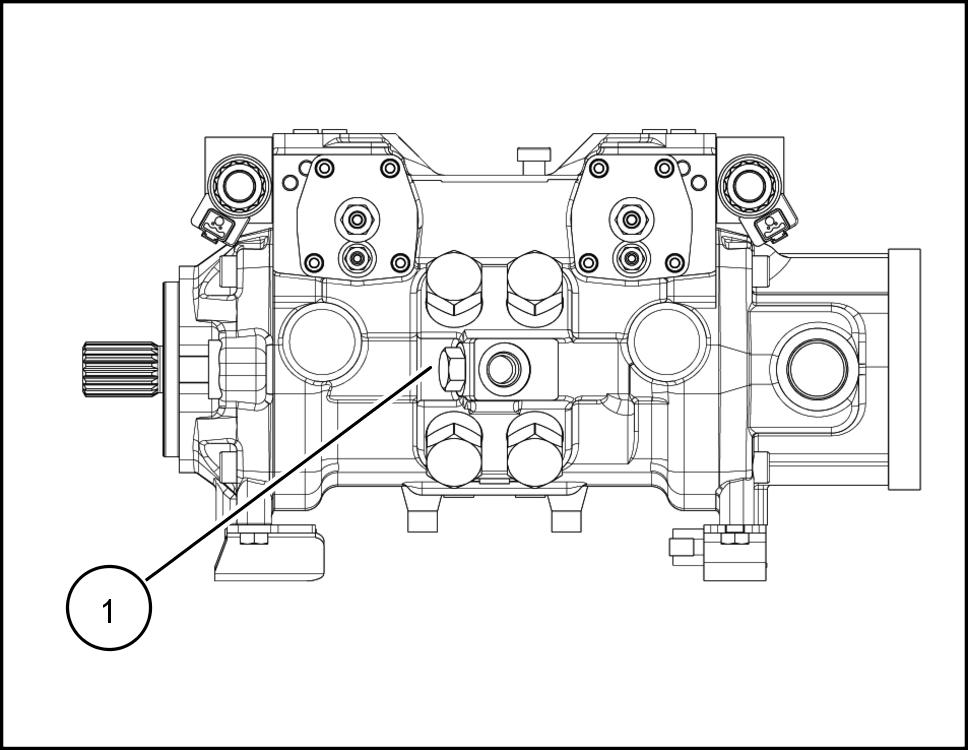
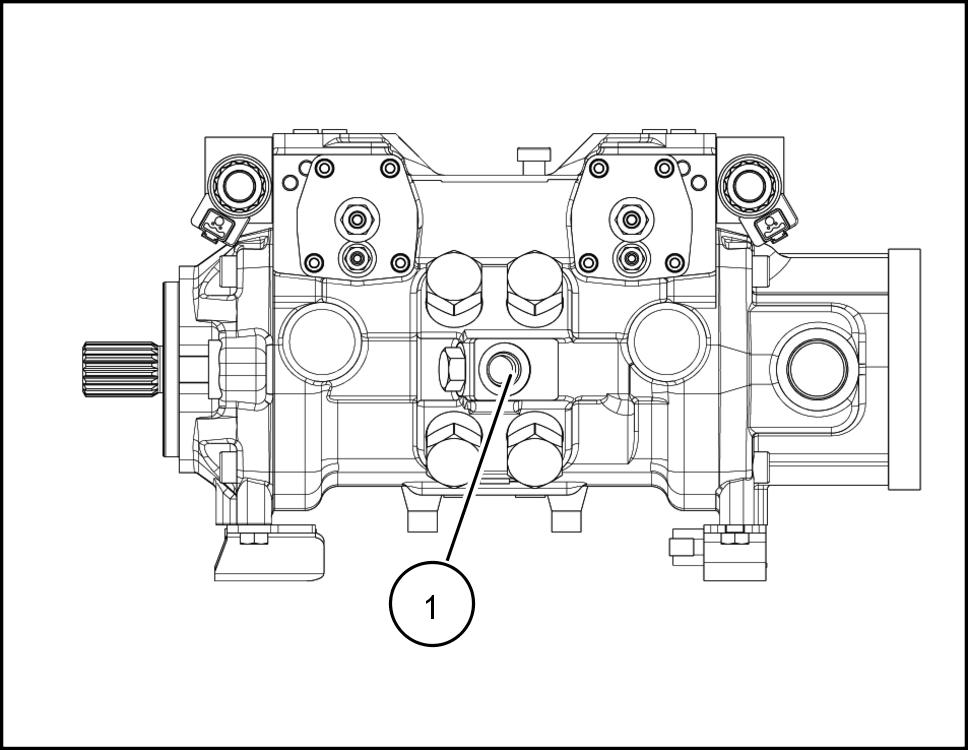
Continue run the engine full Read the pressure gauge and record the Charge Pressure reading. Stop the engine.
The pressure must a minimum 2,413 kPa (24 bar) (350 psi) full
the pressure correct step the pressure not correct loosen the cap the hydraulic voir Remove the and poppet for the charge relief See figure below
Inspect the parts the charge relief valve (1) the parts are good, add shim(s) from the shim kit and repeat steps 1 through 4 until the pressure
After you get the correct charge pressure the following
NOTICE: For the following test the machine MUST raised supports until the tires are above the floor This a safety procedure the parking brakes fail hold.
(A.) Start and run the engine low idle. Engage the parking equipped with 2 shift into transport (high)
Increase the engine speed full Slowly move the ground drive control lever FOR W ARD load the hydraulic piston pumps without decreasing the engine
(C.) Read the pressure The pressure must within 138 kPa bar) (20 psi) the pressure step
(D.) Repeat Steps B and C with the ground drive control lever REVERSE
Interpretation the results:
Once the charge pressure meets specifications with the levers the neutral compare the pressure readings under load with the neutral The readings should highest with the levers the NEUTRAL for this when the direct ing charge relief has handle the greatest amount oil flow The maximum dif ference charge sure readings between the system neutral and the system loaded both directions must not greater than 138 kPa bar) (20 Any dif ence greater than 138 kPa (1.5 bar) (20 psi) indicates excessive leakage from the closed which will require repair
NOTE: The charge pressure drop indicates internal age from the system with the system under This caused less oil flowing over the charge relief and fore, the lower pressure. Excessive leakage (greater than 138 kPa bar) (20 psi) will result slower drive speed that side the but depending what aged the the leakage may only show under heavy load
NOTE: T o determine the problem the pump the motor the following:
the side (left right) that the charge pressure dropped more than 138kPa bar) cap the two high - pressure lines that supply the drive motor The lines can capped either the pump the motor , which ever
NOTE: The charge pressure drop indicates internal leakage from the system with the system under This caused less oil flowing over the charge relief and the lower Excessive leakage (greater than 138 kPa bar) (20 psi) will result slower drive speed that side the but depending what damaged the the leakage may only show under heavy load
With the lines capped the drive motor , start and run the engine low idle. Increase the engine speed full Slowly move the direction control lever that being tested FOR W ARD load the drostatic piston pump without decreasing the engine NOT Lug the Reduced engine speed causes decreased charge pump flow , which will fect the pressure
NOTE: The charge pressure drop indicates internal leakage from the system with the system under This caused less oil flowing over the charge relief and the lower Excessive leakage (greater than 138 kPa bar) (20 psi) will result slower drive speed that side the but depending what damaged the the leakage may only show under heavy load
84522361 15/06/201 1
1 Read the pressure The pressure must within 138 kPa bar) (20 psi) the pressure step
NOTE: The charge pressure drop indicates internal leakage from the system with the system under This caused less oil flowing over the charge relief and the lower Excessive leakage (greater than 138 kPa (1.5 bar) (20 psi) will result slower drive speed that side the machine, but depending what damaged the the leakage may only show under heavy load
Repeat Steps 9 and with the direction control levers
Interpretation the results with the two highsure lines capped the drive motors: the charge pressure drops more than 138 kPa bar) (20 psi) the pressure step the leakage the
Remember that this a closed loop hydrostatic one component the debris will sent directly the mating component and cause this damage contamination will return the reservoir through the case drain the very least once a failure has occurred, the ing component the hydrostatic system must spected for any contamination has been returned the reservoir , tear down and inspection both complete closed loop systems necessary since the same charge pump feeds them. Also, cause the hydraulic system shares the reservoir with the hydrostatic all and components must thoroughly cleaned prevent tion from reentering the repaired
NOTE: The charge pressure drop indicates internal leakage from the system with the system under This caused less oil flowing over the charge relief and therefore, the lower pressure. Excessive leakage (greater than 138 kPa bar) (20 psi) will result slower drive speed that side the but depending what damaged the the leakage may only show under heavy load
Reservoir - Apply vacuum
Remove the cap from the hydraulic reservoir
Install adapter cap CAS1871 the filler
Connect the vacuum pump CAS10193 the adapter .
Start the vacuum
Reservoir - Filling
Lower the loader lift arms the ground and shut f the engine.
Clean the reservoir filler cap and the area around the filler cap with cleaning
T urn the filler cap 1 / 2 turn relieve air pressure from the reservoir not remove the filler cap from the reservoir until the pressure relieved.
Remove the filler cap from the reservoir
Add the correct CNH T3509 , the reservoir until the proper oil level the reservoir
Fill the reservoir until the oil level the midpoint the sight Install the reservoir
Start and run the engine and operate the Lower the loader lift arms the Stop the engine and check the oil level the reservoir Add oil
Reservoir - V isual inspection
Check the reservoir for wear , and pair required.
NOTICE: not modify the strainer , any material that gets past the strainer can directly the gear control and auxiliary hydraulic attachment and cause major damage these
Inspect the strainer Remove and replace the strainer dirty
Inspect the return line and suction line for cracks and debris buildup. Repair required.
Thank you very much for your reading. Please Click Here. Then Get COMPLETE MANUAL.NOWAITING
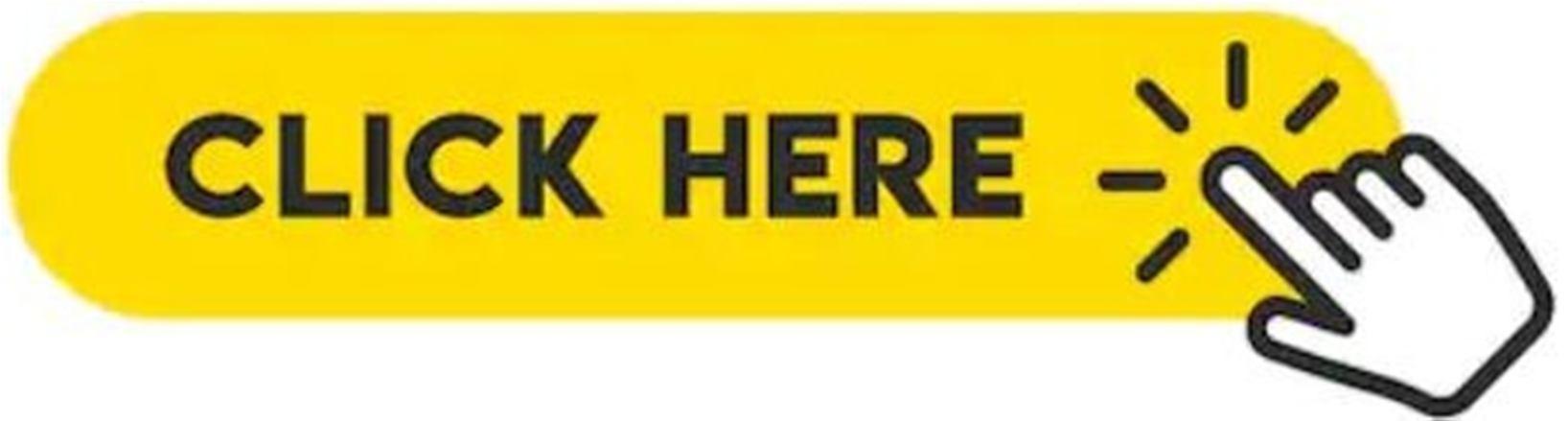
NOTE:
If there is no response to click on the link above, please download the PDF document first and then clickonit.
Filter - Remove
Prior operation:
Reservoir - Apply vacuum (A.10.A)
The filter base can removed opening the rear door and lifting the rear engine hood. Loosen and remove the filter element (1) from the filter
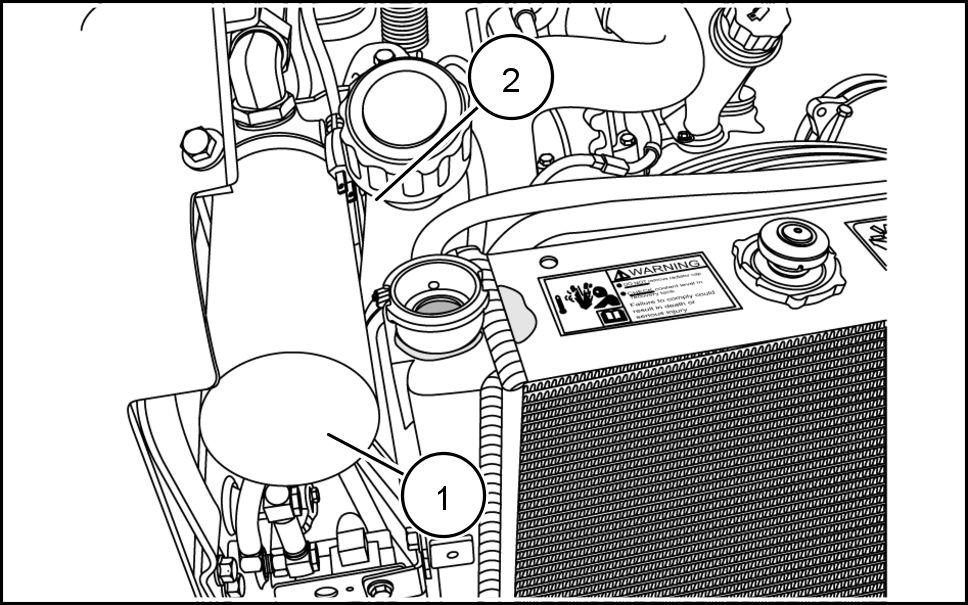
Remove the ground wire (2)
Remove the (3) , and (4) , oil lines and cap prevent loss oil.
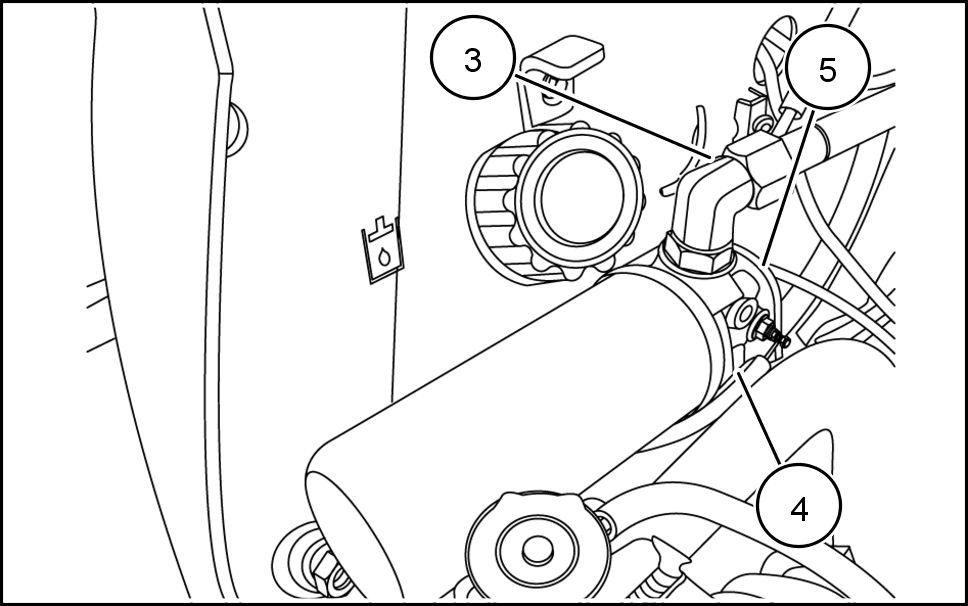
Stop vacuum
Loosen and remove the filter base mounting bolts (5)
Remove the filter base assembly from the
Filter - Install
Prior operation: Reservoir - Apply vacuum (A.10.A)
Reinstall the filter base with the hardware previously removed (1) . T orque the mounting hardware
Reinstall the hydraulic lines (2) and (3) and tighten the lines seat line fittings; loosen andtorque.
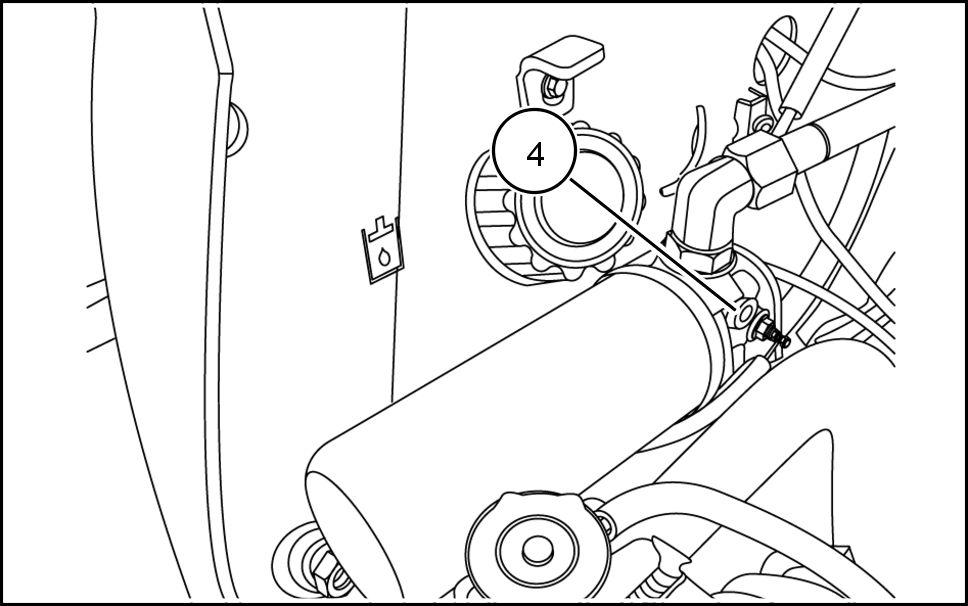
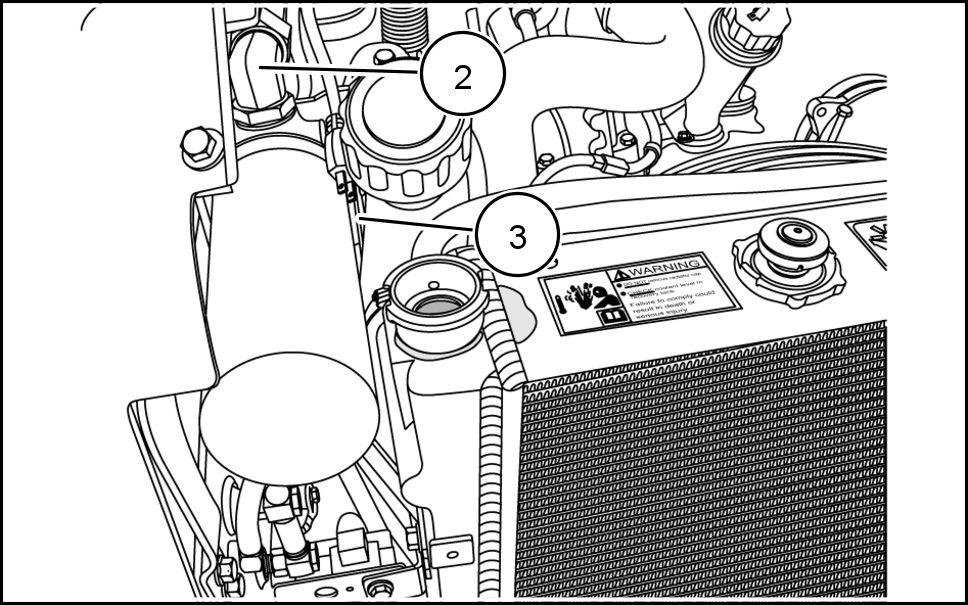
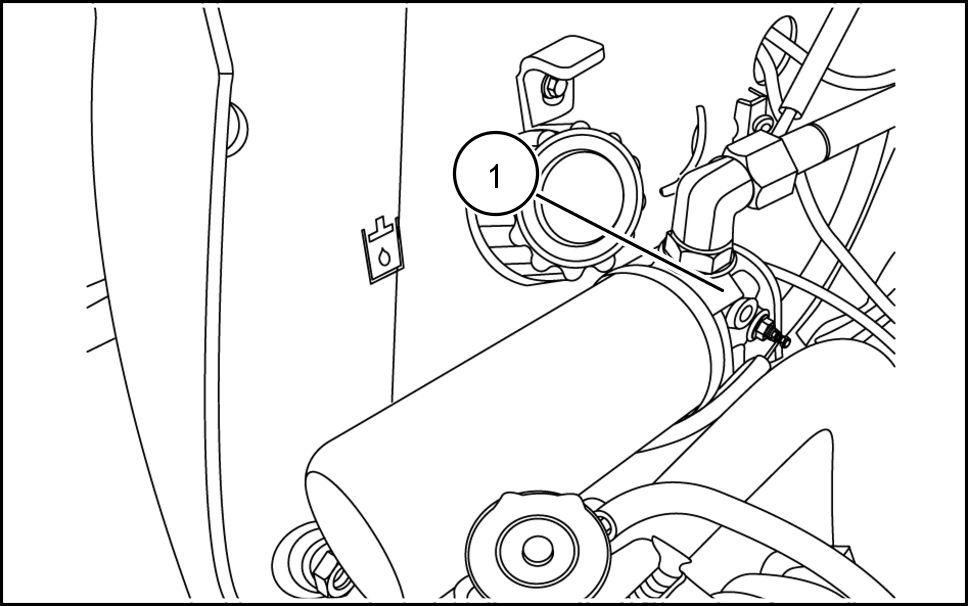
Stop vacuum pump. Connect the ground wire (4) the filter sensor .
Coat the seal ring a new filter element with clean 10W - and tighten the new filter element hand tight 23.017.6 ( - ) .
Oil cooler - Remove for models equipped with ISM engine
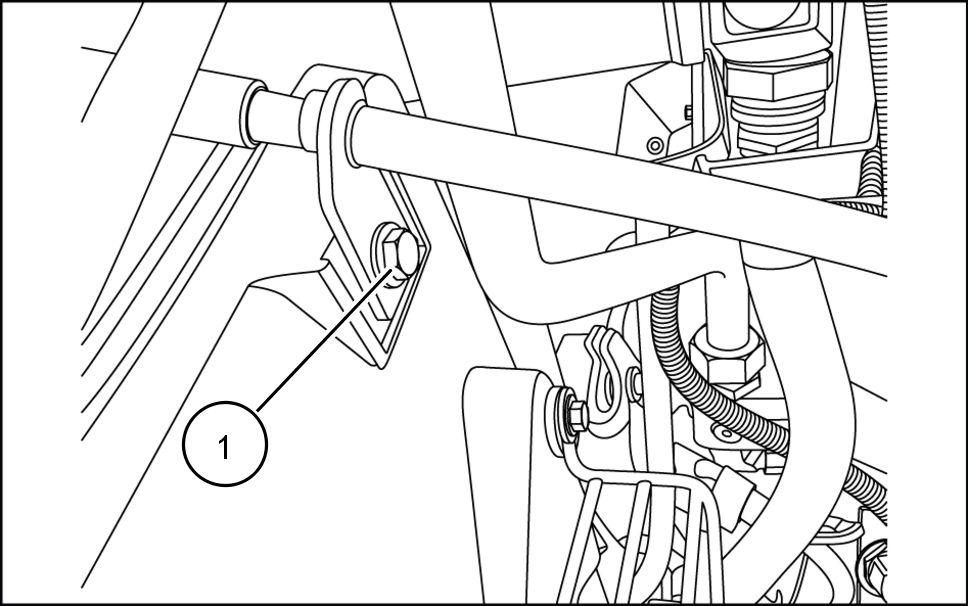

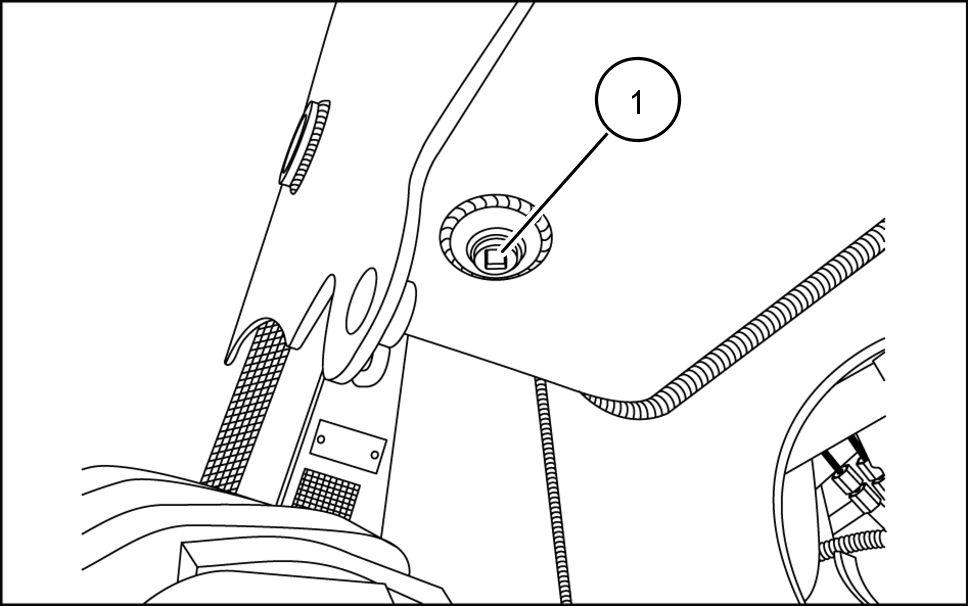
Remove coolant overflow hose (1) and tank bracket
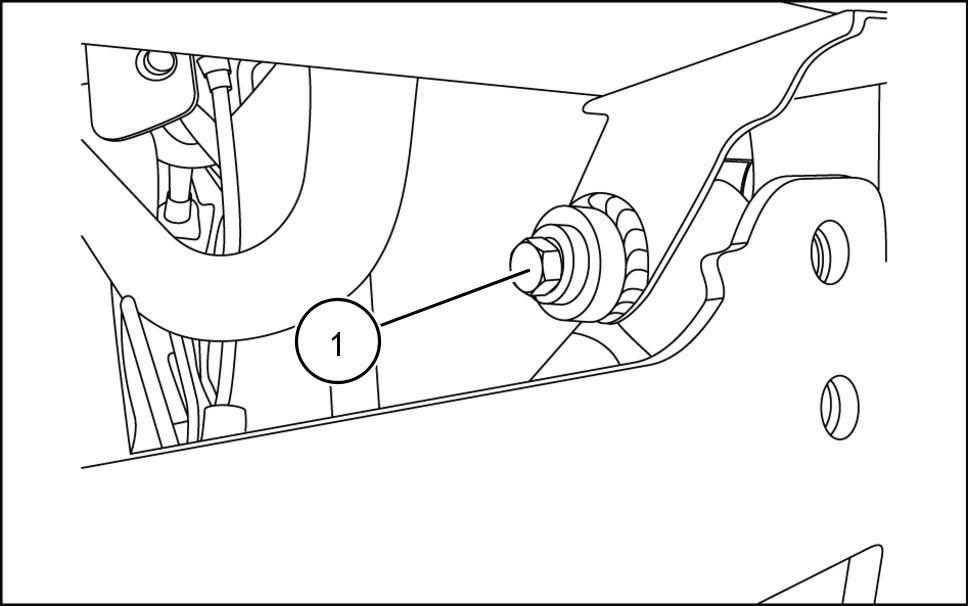
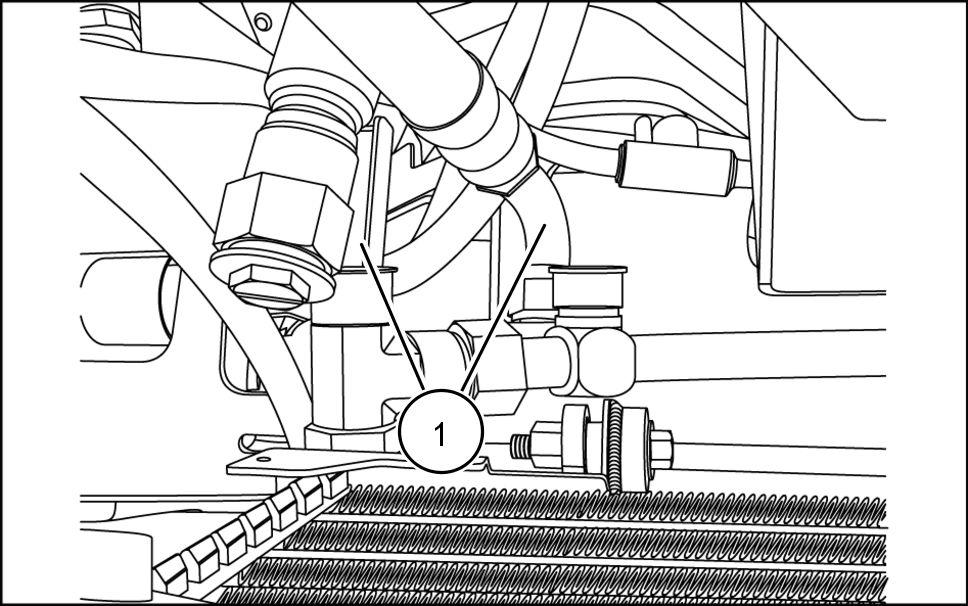
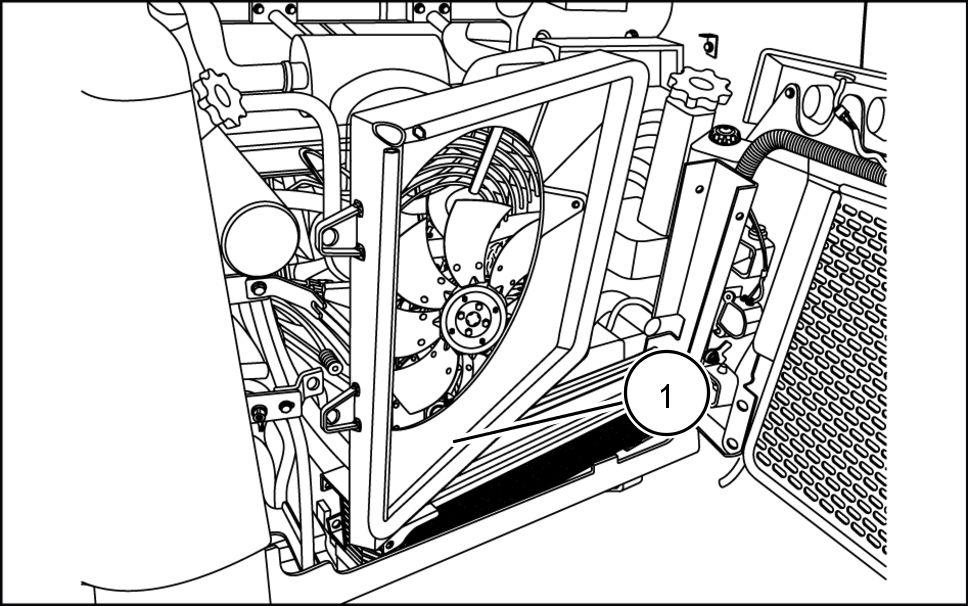
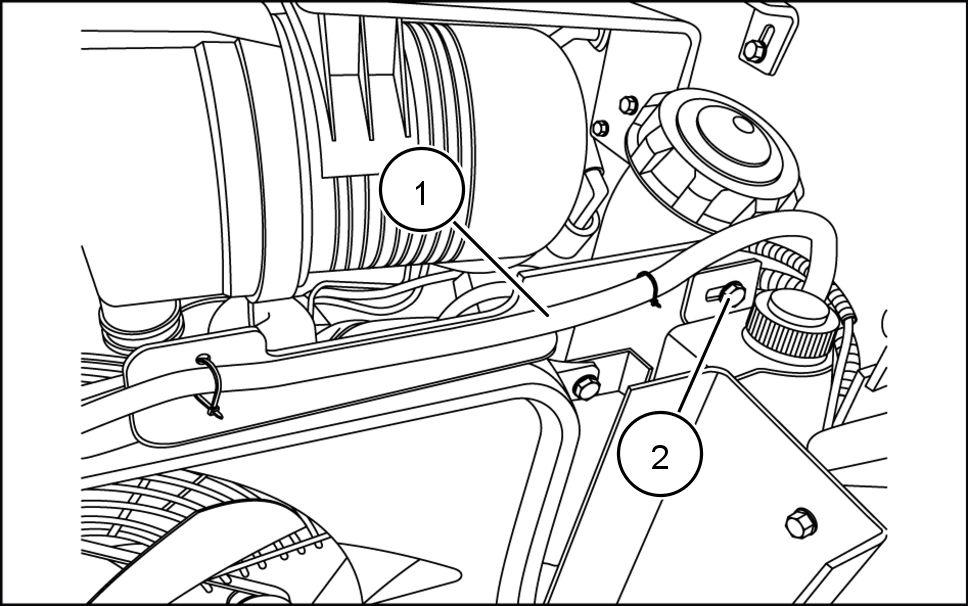
Remove oil cooler (1) from the machine.
Next operation: Oil cooler - Install for machines equipped with ISM engine
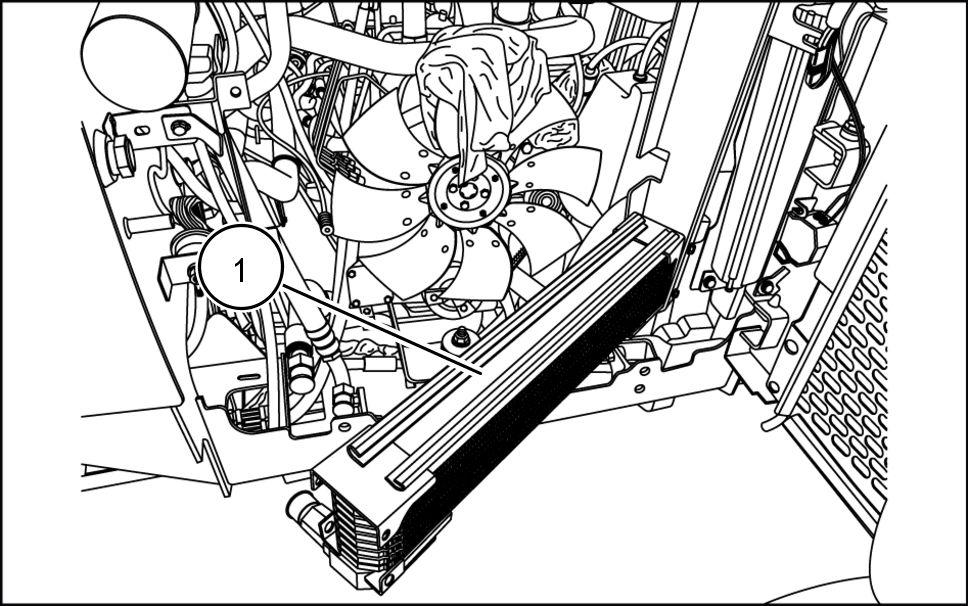