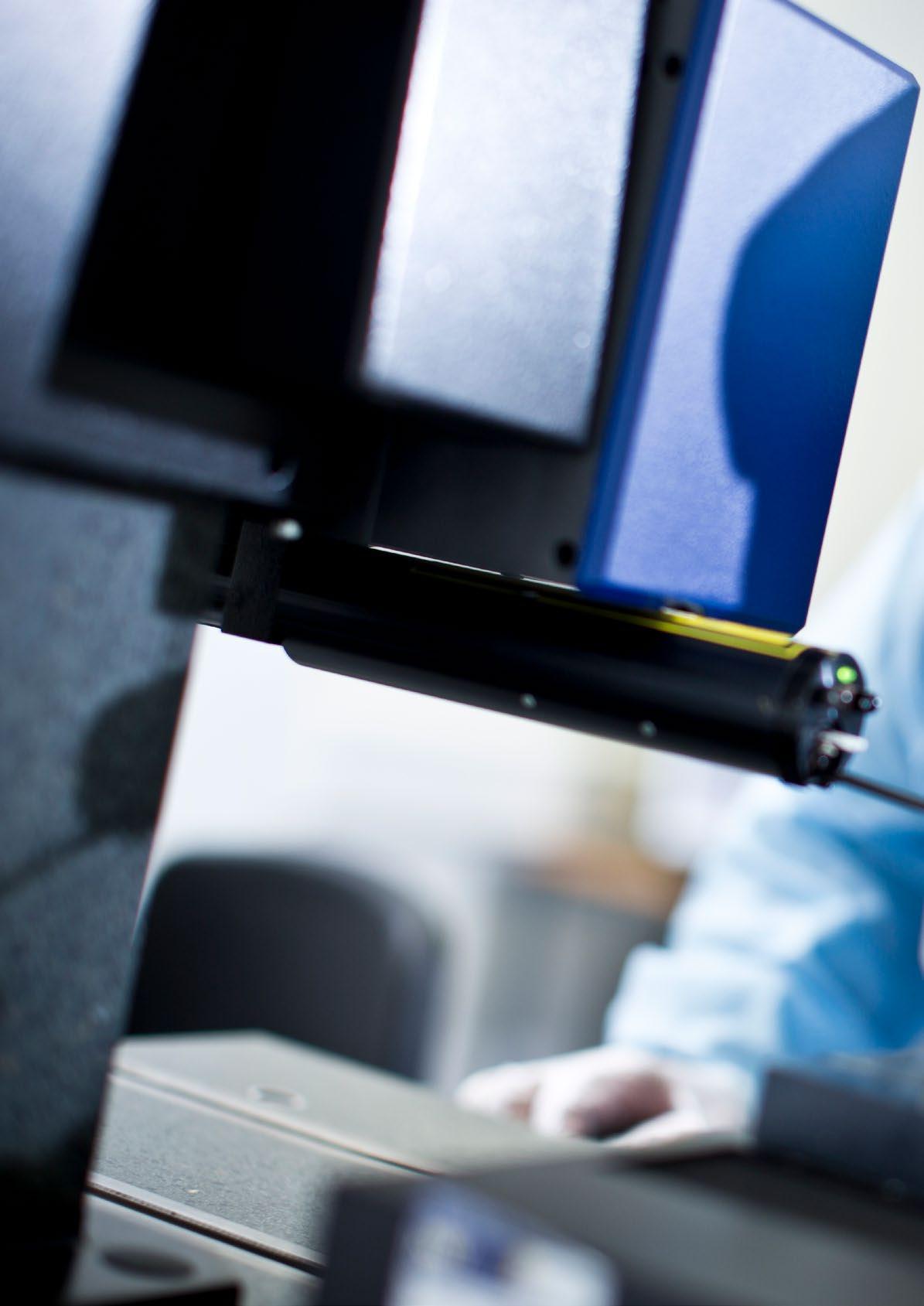
8 minute read
Innovation and Industry
A key priority, as the Hub’s research programme is maturing, is to make sure that research outputs are being applied to deliver meaningful industry impact. This is being achieved through a wide variety of activities including training courses, measurement services work, consultancy, collaborative R&D projects and the commercialisation of new intellectual property. Because of the broad and underpinning nature of metrology, our research team work with a wide variety of industry partners from across many different sectors, and the following pages contain some examples of the work we have been doing with industry over the past year.
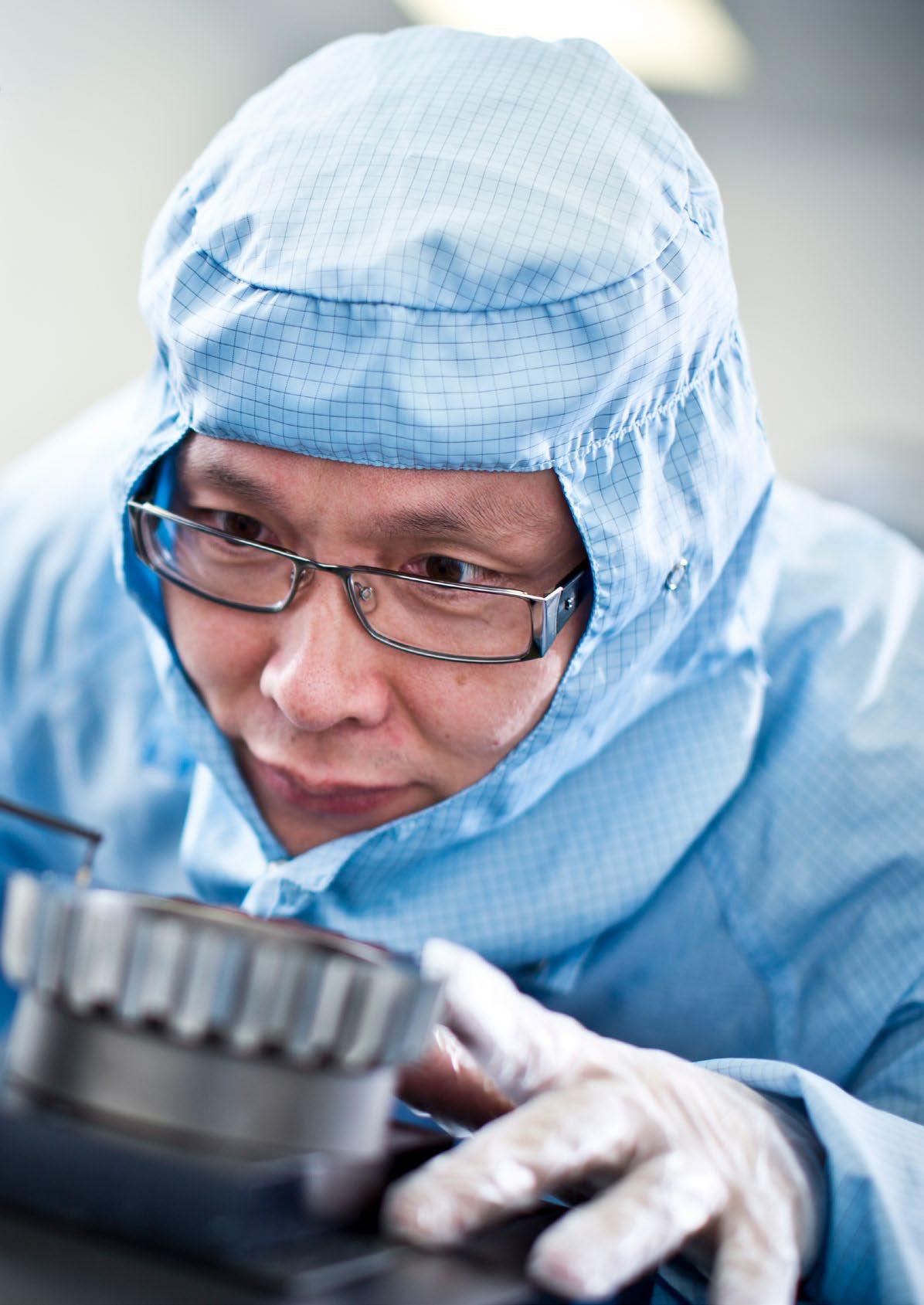
Advertisement
Digital Surf
New collaboration with market leading software company Digital Surf puts the Hub’s mathematics team on the MountainsMap®


Example of surface texture of an additive manufactured part After many years of informal collaboration, including common membership of several ISO standards committees and Working Groups, researchers at Huddersfield have teamed up recently with Digital Surf to develop new state‑of‑the‑art surface analysis solutions.
The Company, which has been developing software for over 30 years, is a market leader in surface analysis where it has a large and diverse user base of instrument manufacturers, manufacturing end‑users and research laboratories. The company delivers solutions based on its Mountains® software platform for profilometry (MountainsMap®), electron microscopy (MountainsSEM®) and scanning probe microscopy (MountainsSPIP®). The Huddersfield team and Digital Surf have both been pioneers in surface metrology, and active contributors at ISO committees for the last 20 years.
The Huddersfield team’s research on freeform surfaces (using triangular mesh) has recently been published and is a landmark for the future of surface metrology. Digital Surf will enable this research, combined with the company’s own developments, to benefit a worldwide audience. The collaboration of the two expert teams is expected to create advanced and innovative metrology tools for the analysis of freeform surfaces. Use of these types of surface in engineering applications is growing alongside the emergence of new process technologies such as additive manufacturing. The collaboration is therefore critical for the next generation of metrology solutions. A first phase of the collaboration, which started last year, allowed the company to provide plugins developed by Huddersfield researchers, to be used with MountainsMap®. Now, phase 2 will see a deeper collaboration of both teams, with a transfer of knowledge focused on surface parameters and form fitting for freeform surfaces. This will allow native calculations within MountainsMap® and better integration for users. The first outcome of this collaboration is expected to be integrated into MountainsMap® in the second half of 2021. Plans are already being discussed to develop a longer‑term research collaboration to address future challenges and opportunities.
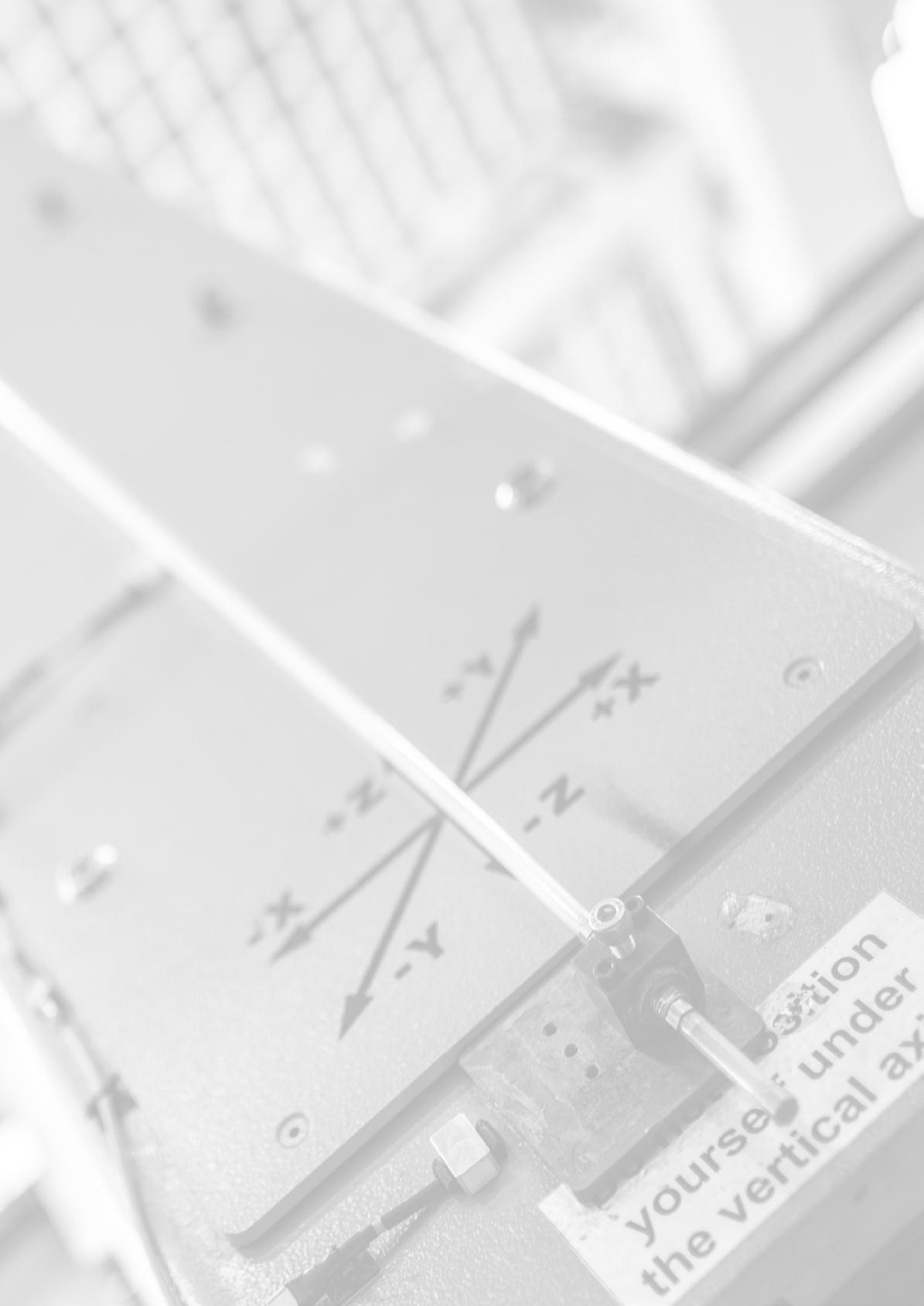
More information on Digital Surf and MountainsMap® can be found at www.digitalsurf.com and on the Hub’s freeform research output in the book Advanced Metrology – Freeform Surfaces. This book discusses methods able to handle the geometry of free‑form surfaces and bridge the knowledge gap between research and practical industrial applications. “We recognise Huddersfield’s continued world‑leading position in surface metrology research and the value that we, as a business, can gain from maintaining a close and mutually beneficial collaboration.”
François Blateyron, Vice President, Research & Metrology, Digital Surf
Advanced Machinery and Productivity Institute
Working with NPL and a West Yorkshire and Greater Manchester consortium to develop a major new Advanced Machinery initiative.
“AMPI is not about UK industry imitating machinery already available, it’s about working collaboratively to leapfrog current technologies. We want to develop the smart and connected machinery needed to manufacture a whole new generation of products that address industrial and societal challenges such as net‑zero carbon.”
The Advanced Machinery and Productivity Institute (AMPI) is an industry led initiative to drive innovation for the UK’s advanced machinery manufacturers. Its aim is to build economic growth through the design, development and manufacture of advanced intelligent machinery, robotics, and cooperative systems which are needed to make a step change in productivity and to support emerging sectors. Fundamental to the programme is embedded metrology and its critical role in the control of the next generation of machines. Centred around existing capabilities and research excellence across the North of England, AMPI will be a partnership between industry, local government, higher education institutions, further education colleges and NPL.
A team from the Hub have been working closely with the consortium to build momentum for this initiative, which has successfully secured seed‑corn funding from the Government’s Strength in Places Fund to develop a full business case for AMPI. With strong support from Local Enterprise Partnerships in West Yorkshire and Greater Manchester, and a commitment from Rochdale Development Agency to build a landmark facility as a long‑term home for AMPI, plans are being developed for a series of research, innovation and skills development programmes.

The Hub team, working closely with NPL and several of our industry partners, are heavily involved in designing these initial anchor projects, some of which will be ideal vehicles for accelerating impact from the Hub’s core research programme. The programme will also draw in expertise from research groups across the Universities of Leeds, Manchester, and Salford, expanding the Hub’s network of academic collaborations.
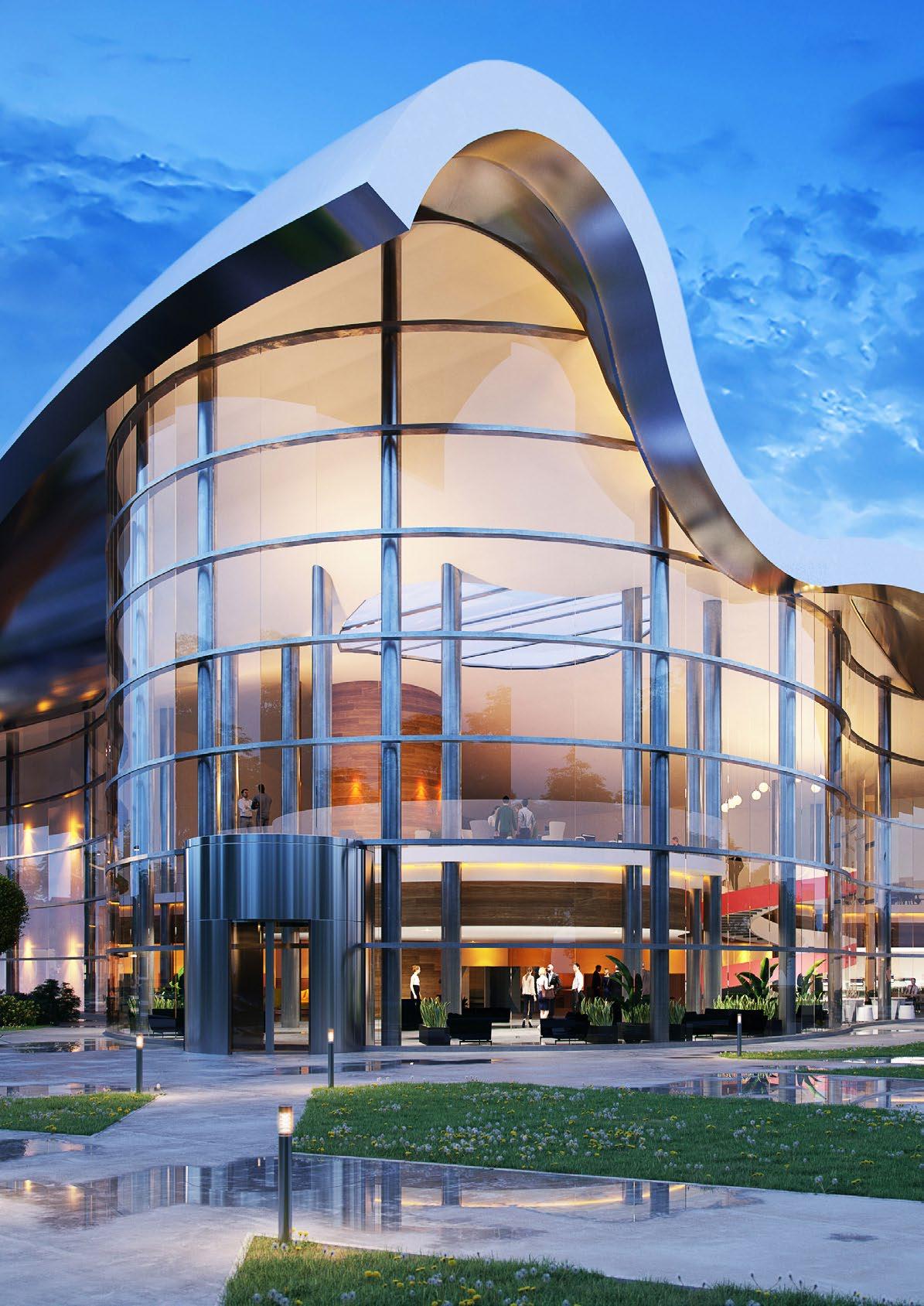
Cubit Precision Measurement Ltd
A spin‑out to provide innovative in‑process metrology products and consultation services for real‑time surface precision measurement and characterisation.
Earlier this year, Dr Hussam Muhamedsalih, senior research fellow in the Hub, established a new spin‑out company, Cubit Precision Measurement Ltd. This is the first spin‑out created by the Hub and will be used as a vehicle to commercialise optical surface metrology products.
Dr Muhamedsalih successfully completed his Royal Academy of Engineering (RAEng) Enterprise Fellowship, featured in last year’s annual report, which was a key driver to setting up the spin‑out. It also resulted in a new multi‑wavelength polarising interferometer, one of the first pipeline products that Cubit aims to commercialise. This technology is currently being validated by the Centre for Process Innovation (CPI), a High Value Manufacturing Catapult Centre, on large‑scale roll‑to‑roll coating equipment, thanks to funding via the EPSRC Researcher in Residence programme. More funding success has continued this year for Dr Muhamedsalih, resulting in the award of a RAEng Industrial Fellowship. This Fellowship will develop a novel metrological measurement sensor for a two‑dimensional material manufacturing process in conjunction with Paragraf, a new Hub industrial partner who develop and deliver game‑changing, commercial‑quality, graphene‑based electronic devices. This collaboration is expected to lead to the creation of a demonstrator that will validate the new metrology sensor in a real environment, and create a new pipeline product.

This is an exciting new opportunity, not only for the Hub, but for Dr Muhamedsalih, who is the new Managing Director of the spin‑out. Cubit Precision Measurement will provide the Hub with an innovative way to commercialise new products and services ensuring that our metrology research is having real word benefit and impact.

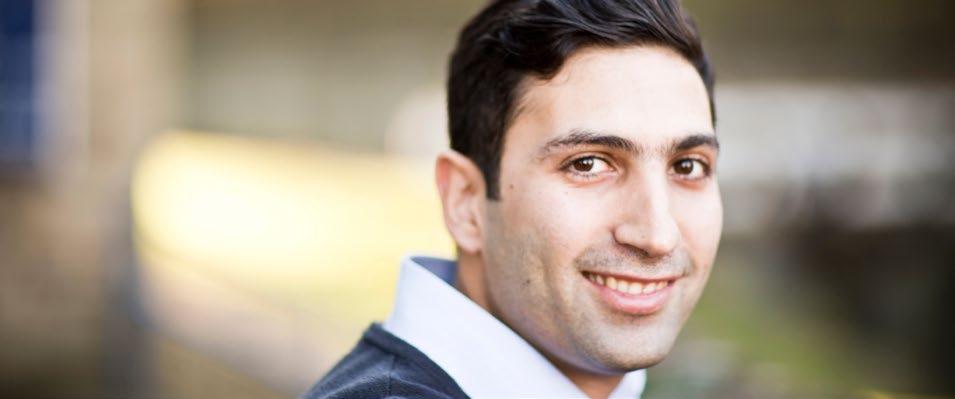
“Cubit Precision Measurement is a recent high‑tech start‑up company whose area of business operation is developing solutions for in‑process surface metrology. Cubit has grown out of the University of Huddersfield’s Future Metrology Hub and will work together on developing and translating novel technologies to industry. It is our belief that measurement and manufacturing on the same machine can add value to the clients, making them more globally competitive.”
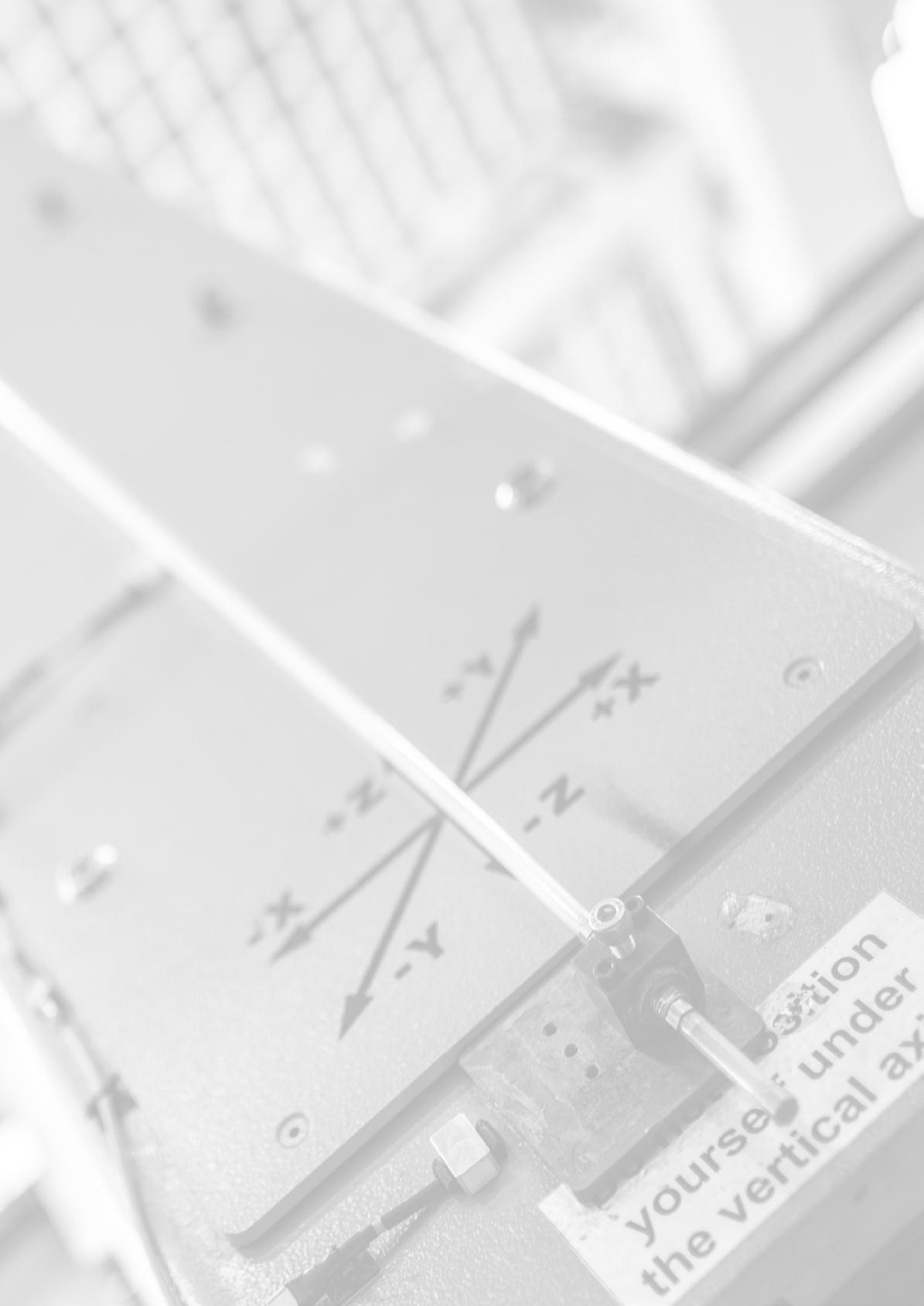
Dr Hussam Muhamedsalih
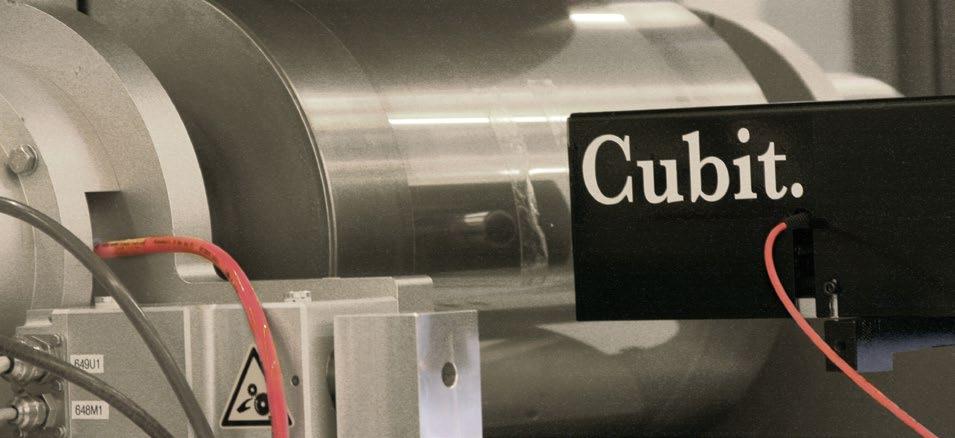
Gyrotricity
A new relationship to develop a sustainable, cost‑effective solution for fast charging electric vehicles.
Professor Patrick Keogh and PhD student Gauthier Fieux at the University of Bath are working with Gyrotricity Ltd on the design and manufacture of magnetic bearings for deployment in Gyrotricity’s innovative kinetic energy storage system.
As electric vehicles become more common, there is a similar rise in the need for charging stations. Fast charging is particularly suitable for areas such as service station forecourts. However, installing fast charging stations is currently a very costly and time‑consuming process as it requires substantial upgrades to the existing grid supply.

Gyrotricity Ltd have developed a unique solution to this problem which uses a fail‑safe flywheel of a simple and low‑cost steel construction. This device builds up a store of energy from the existing grid infrastructure which can then be discharged to deliver a fast charge.
Off‑the shelf options exist for some of the parts necessary for the fly wheel but these are prohibitively expensive and would make the system commercially unviable. The team at Bath is working on more cost‑effective solutions for the bearing sensors and actuators that must operate in a vacuum. Gauthier’s role in the project is the design and manufacture of a hybrid magnetic bearing system and associated position sensors. The bearing control system has an inherent condition monitoring function that can provide early warning of any impending fault in the high‑speed rotating components and keep the flywheel operating efficiently and safely.
The project and the working relationship between the University of Bath and Gyrotricity has proved mutually beneficial. Gauthier has been able to bring his metrology expertise and the skills developed as part of his PhD studies to Gyrotricity to overcome a challenge in the manufacture of their system while gaining technical and project management skills in an industrial setting.
Based on the success of the initial work, it is expected that the Future Metrology Hub will continue to support Gyrotricity in bringing this sustainable technology to market. Gauthier Fieux


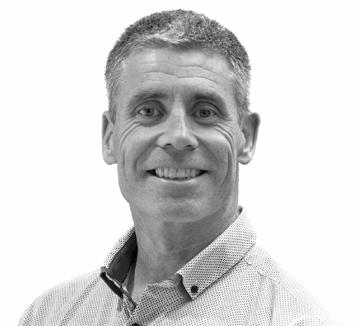
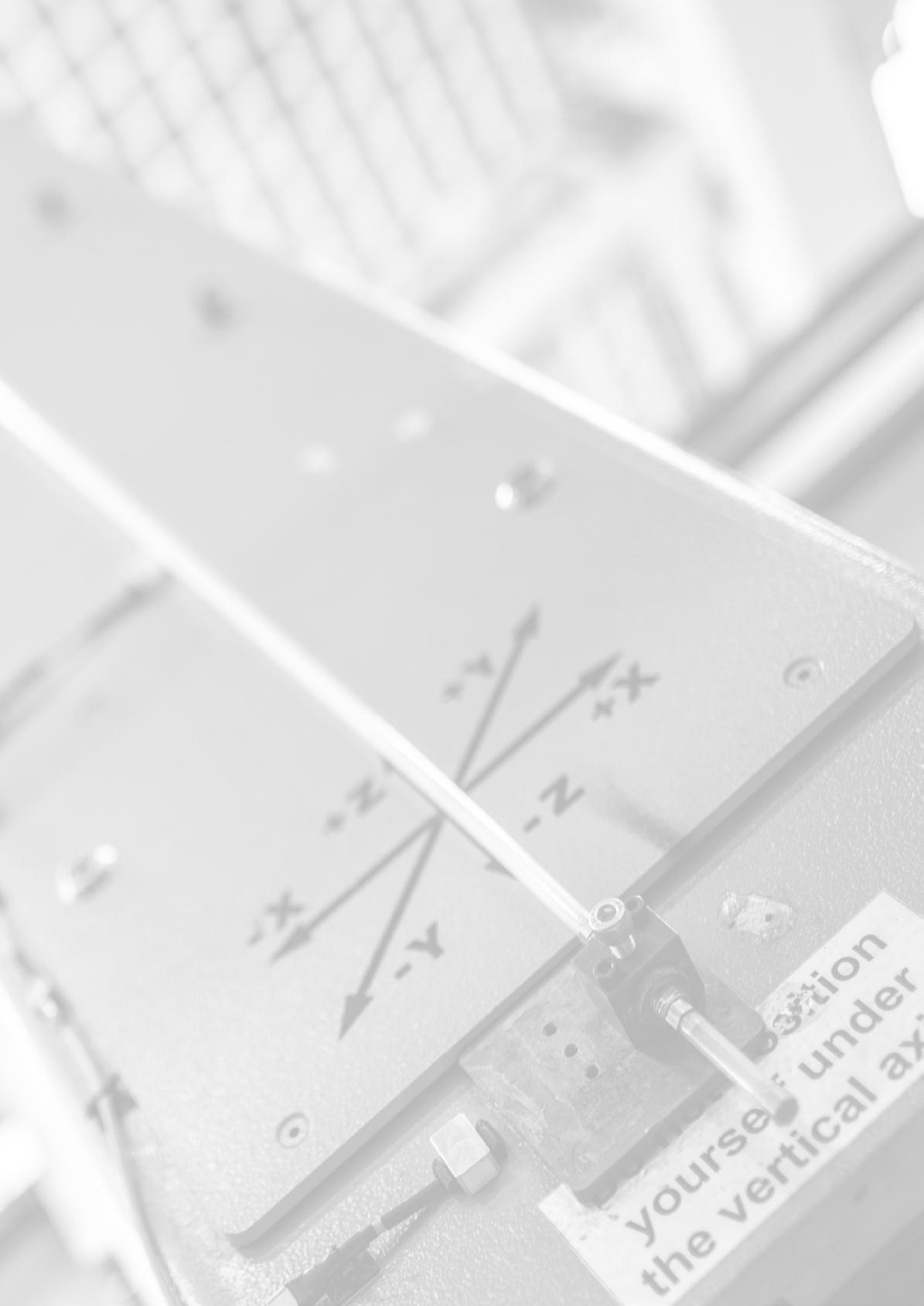
Gyrotricity Flywheel “Gauthier and the team at Bath have been key in advancing our flywheel technology and the collaboration demonstrates the value of business working with universities. I look forward to developing the relationship with the Hub further”
Matt Journee, CEO – Gyrotricity
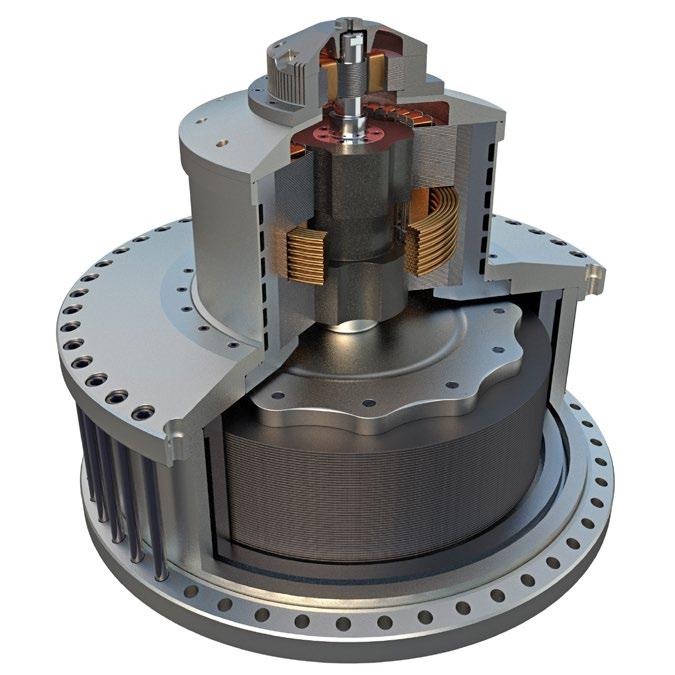