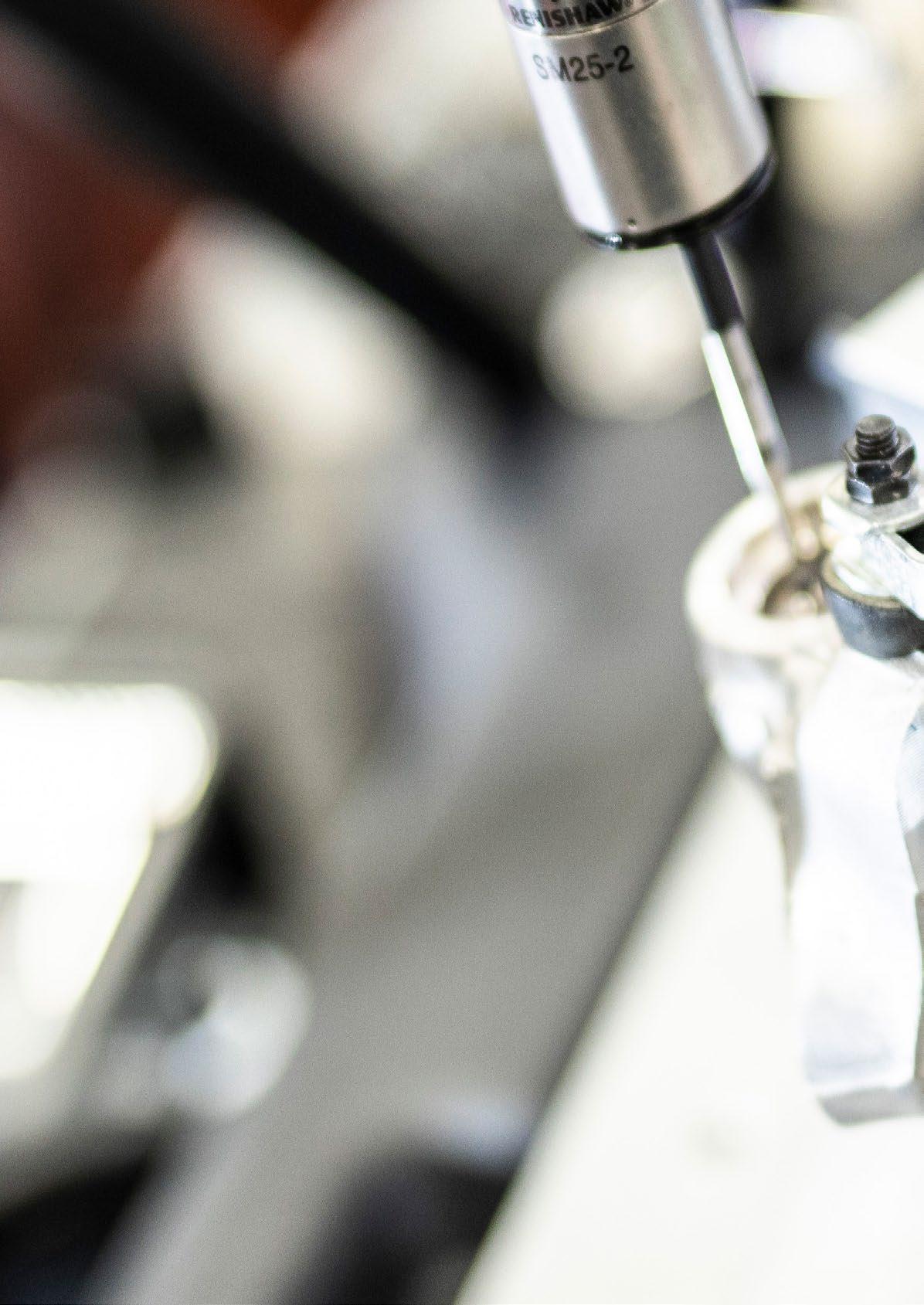
16 minute read
Research Highlights
The Hub research programme comprises several work packages which each address individual challenges and can broadly be separated into three categories: Sensor development, Data analytics, and Metrology assisted manufacture.
As the programme progresses, linkages between the categories will be developed into future work packages to deliver industry ready solutions.
Advertisement
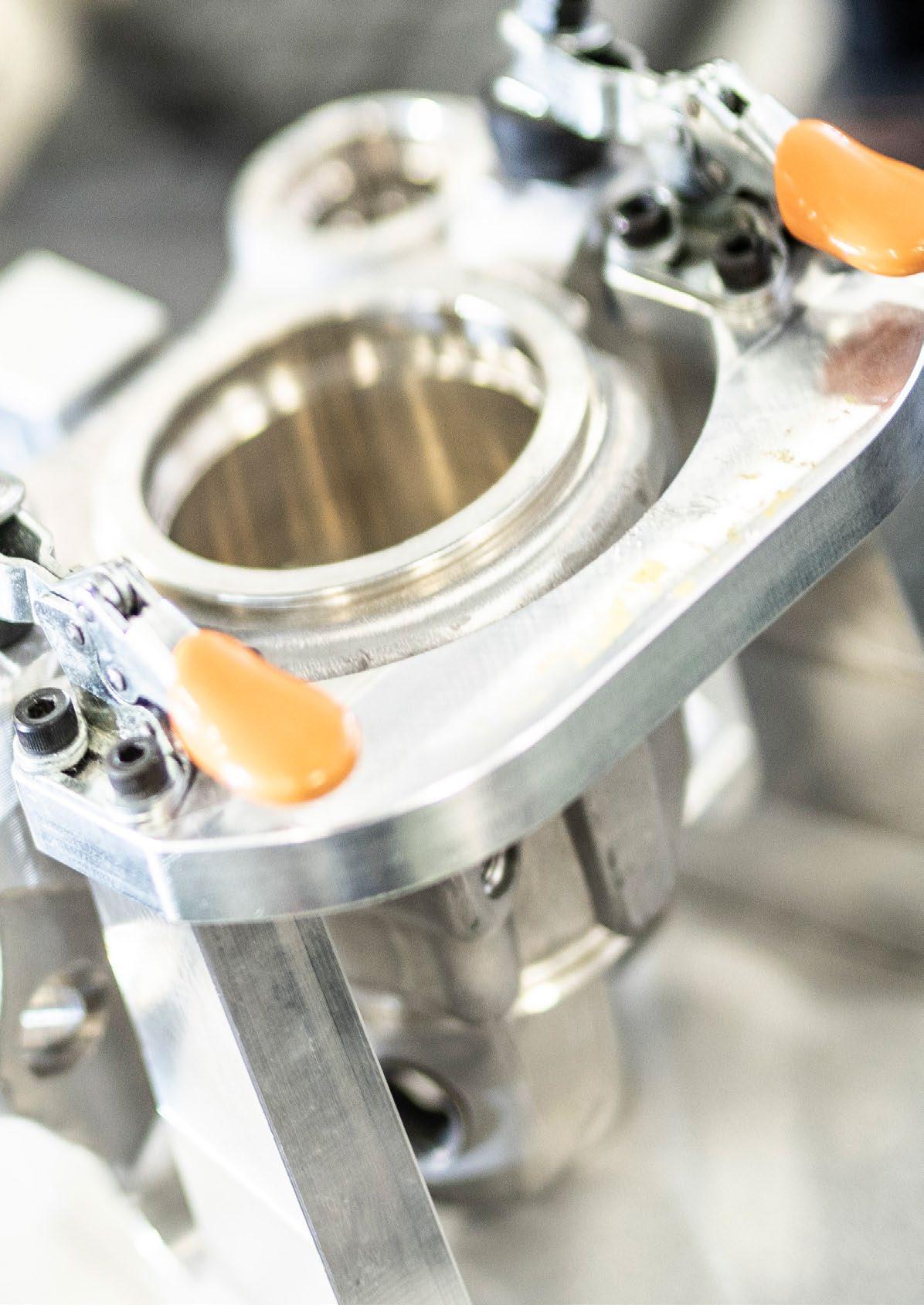
New Sensor Technologies for On‑machine Metrology
A team at the University of Huddersfield is working to develop new sensor technologies suitable for embedded metrology. On‑machine metrology is advantageous as it allows measurement of surfaces in a manufacturing environment.
Measurement in‑situ is challenging and some applications with limited space require a small volume probe with remote interrogation apparatus. Dispersed Reference Interferometry (DRI) seeks to solve this problem and provide a high dynamic range probe in a small package which is capable of measurement rates of 5000 Hz or more.
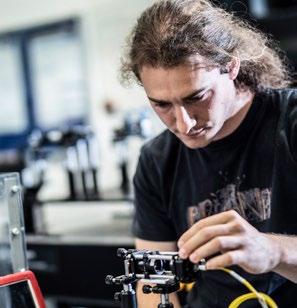
Dr James Williamson is working on reducing the size of the interrogation unit and Dr Wenhan Zeng is working to improve the signal processing speed and accuracy. This will lead to increased measurement rate and demonstrate increased stability through reduction in size and use of improved materials. Design, alignment and calibration have been carried out on a test bed in the Hub’s state‑of‑the‑art optics lab at the University of Huddersfield. With help from Dr Wenbin Zhong, a member of the ultra‑precision manufacturing group, a prototype device has been installed on a Nanoform 250 single point diamond turning machine to carry out physical, on machine trials.
On‑machine measurement at 5000 Hz has been achieved and further work to verify new algorithms and calibrate the prototype instrument is continuing. Delivery of a device ready for industrial evaluation and testing is imminent.
This research has generated significant interest from industry and is additionally supported by funding from the ProSurf EU 2020 project. In particular, Hub partner Renishaw has agreed to provide the use of their facilities and substantial expertise to help evaluate the metrological performance of the DRI in a range of application‑specific contexts. The aim is to assess the commercial potential for DRI and establish potential application areas. The refined second‑generation DRI prototype, incorporating signal processing advances and reduced size will be delivered to Renishaw next year. After initial commissioning, the Renishaw technical team will evaluate the prototype instrument and feedback to the Huddersfield team on areas for further optimisation.
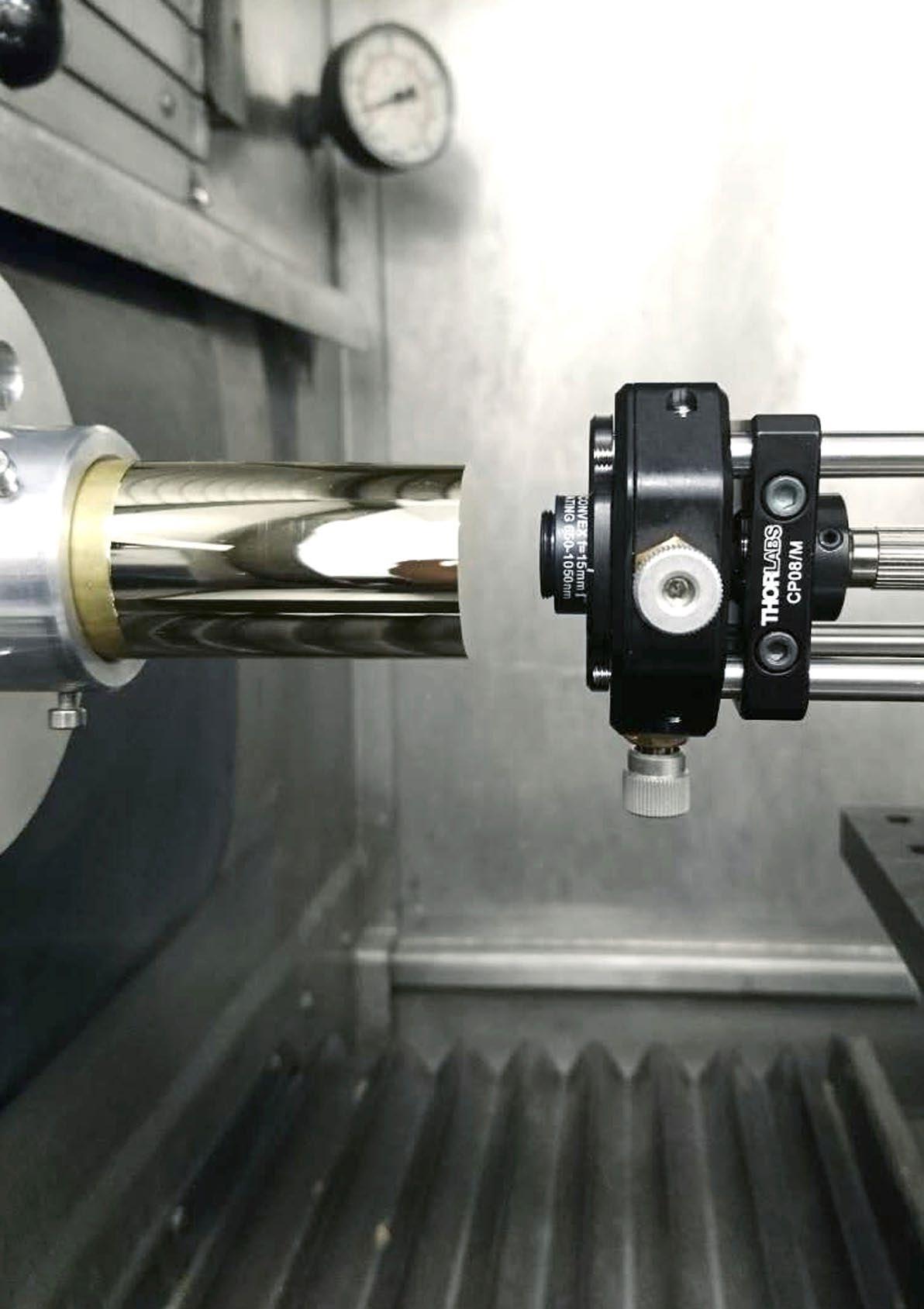
Active System Machining – Metrology embedded precision machining

Serial robotic arms are a highly flexible solution to the challenge of multi‑axis machining in large volume spaces.
However, this flexibility comes at the cost of reduced stiffness when compared to conventional machining systems and can lead to machining forces causing chatter and creating surface irregularities. Changes in pose of the robotic arm and moving the tool to another plane also affect the accuracy of the machining. This means that using the serial robot’s own internal control systems does not provide the level of accuracy necessary for precision machining.
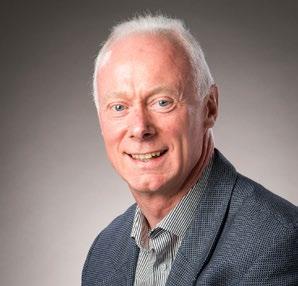
Professor Patrick Keogh leads a team of researchers at the University of Bath working to develop a system to solve accuracy problems in both the dynamic and path planning actions of serial robots.
The team has adapted a laser tracking system to control the position of the robot which uses a reflector placed close to the machining head. By closely monitoring the actual position of the arm and comparing this to a nominal path generated by the robot’s control system, it is possible to map and compensate for motion errors to within 10 microns.
To control the dynamic effected created by the high frequency of the machining process, an active system has been developed which can be attached to the machine tool. Accelerometers are used to measure accelerations in the X, Y, Z directions and the vibration signals are used in a feedback loop. These are then processed by a controller to activate the inertial actuators, minimising vibration. The control strategy is based on H_infinity optimal synthesis in which model uncertainty is accounted for in the minimisation of a cost function that represents a metric for the machine tool vibration. Edge trimming trials have shown the control to be effective in eliminating machine tool chatter. With this active control system machining errors can be reduced by 90%.
As work progresses on this project, the team aim to make the device retrofittable to existing robot arms and carry out trials in a real production environment.
The technology developed in this project will enable serial robots to be used as machining tools, providing a cost‑effective option for manufacturing large volume, complex components in industries within, for example, aerospace and automotive sectors. The technology will also enable smaller manufacturing companies to operate competitively in these markets. Additional work is also being carried out on the positioning of multiple robots in relation to each other and collaboration between robots carrying out a range of tasks in the same manufacturing environment, for example cleaning around the item being manufactured. However, to cover the whole working volume of multiple robots, the system will become too complex for existing controllers to run in real‑time. To solve this problem, the team are investigating an AI approach to teach the robot to control different points in the working volume. This work will build on existing Hub research packages whilst also bringing in new partners.
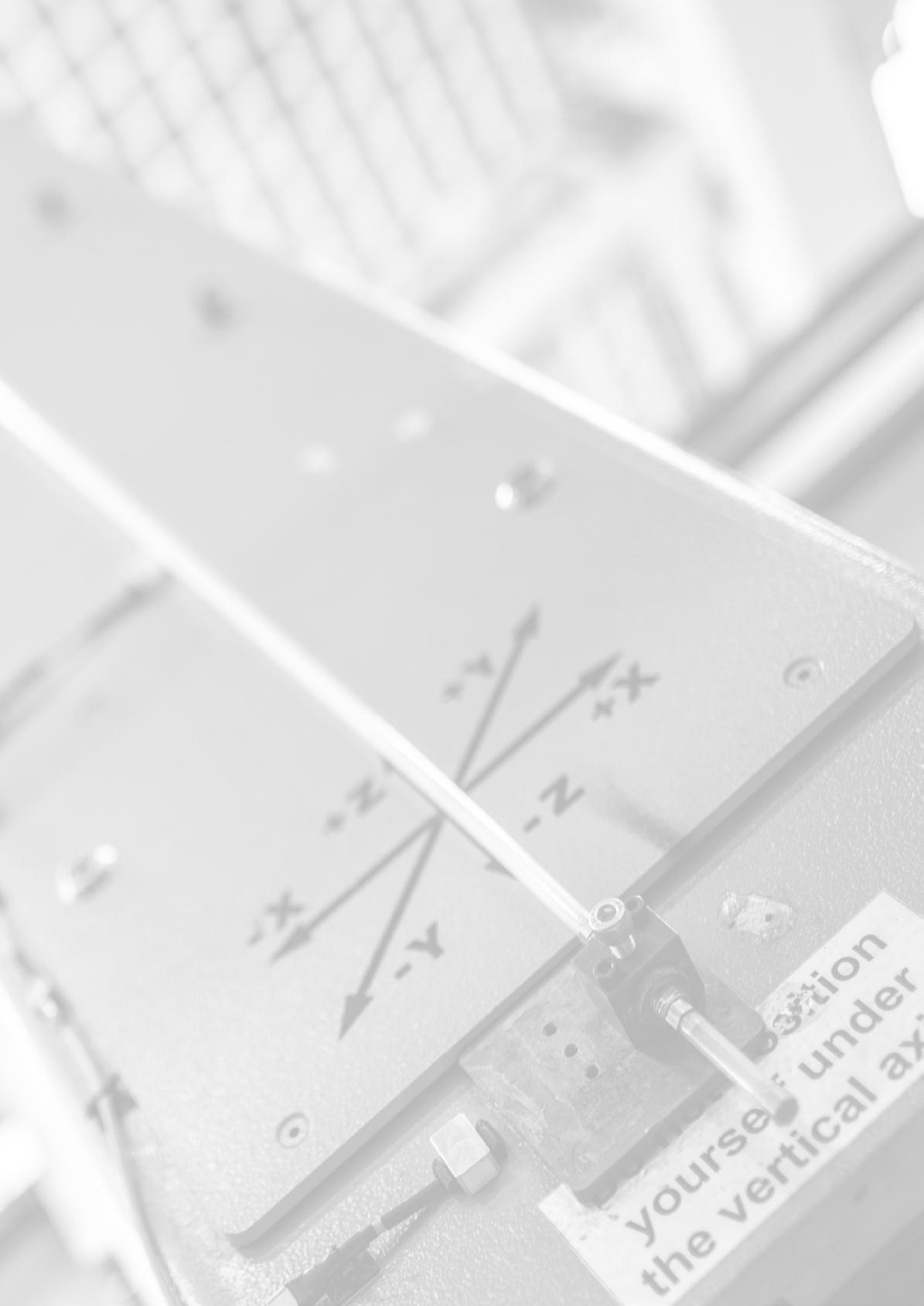
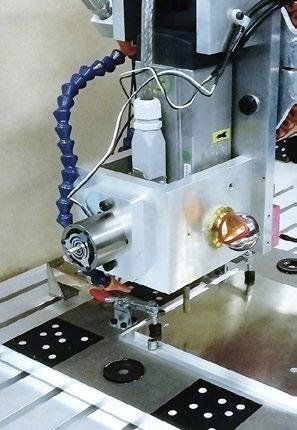
Data Engineering
Increases in the capability of embedded metrology technology such as integrated networks of sensors, bring with them new challenges in terms of data management and information extraction.
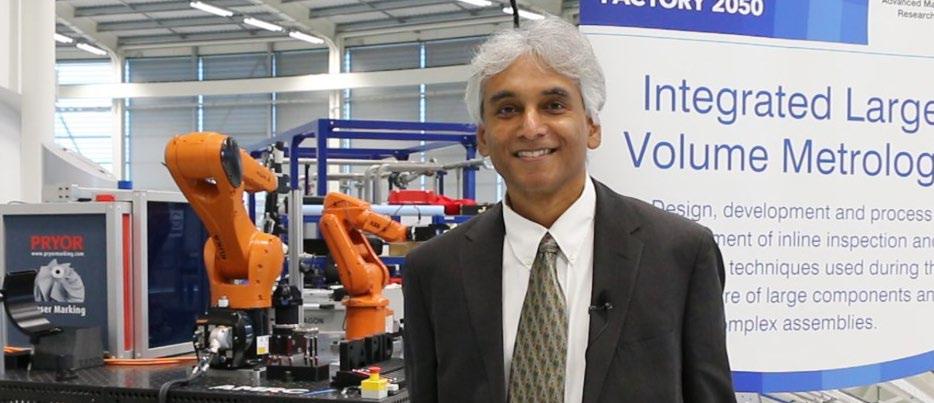

Professor Visakan Kadirkamanathan leads a team of researchers at the University of Sheffield who are working with the Advanced Manufacturing Research Centre (AMRC) team led by Ben Morgan to develop a host of novel solutions. Building on the vision of Industry 4.0, this work aims to use informatics‑based decisions to improve each stage of the manufacturing process. To develop the systems needed, rather than focussing on building the whole system, which would be a massive project in itself, the Sheffield team is building a set of case studies which can be used as exemplars of different aspects of informatics to support manufacturing decisions. The first case study has focussed on the production of a set of bearing housing parts at the AMRC facilities. Using a design of experiments process, the initial material conditions were set by varied heat treatment and then the part was manufactured using 19 separate processes. For each of these processes, parameters such as feed‑rate and spindle speed were varied between artefacts, while features such as tool cutting force and vibration were continually monitored. In order to determine the impact of the variable processes, each part was subjected to intensive measurement of key features, using a variety of techniques such as CMM measurement for dimensionality or optical measurement for surface characterisation.
The ultimate aim of this case study was to demonstrate that if a predictive model could be built using artificial intelligence and Bayesian methods, and the manufacturing processes were capable of consistent, repeatable and predictable performance, it would then be possible to create a data driven ‘Virtual CMM’. This would enable process parameters to be gathered to carry out a virtual inspection of the finished part, effectively eliminating the need for a time consuming and costly additional physical procedure.
One of the key challenges faced throughout this process was the discrepancy between the large amount of high frequency data which was gathered during manufacturing and the low number of parts manufactured which yielded data points for validation. To overcome this challenge a combination of neural network, feature extraction and fuzzy logic approaches was applied. High frequency analytics is still in its infancy. However, if this approach proves successful, it will be possible to monitor processes throughout all the manufacturing stages and predict what the outcomes will be. Ultimately, the faster you can process the data from each of the manufacturing stages, the earlier you can make decisions which impact on the final product quality. This in turn can lead to reduced waste with more parts being manufactured to conformance. This work fundamentally underpins several aspects of the Hub research programme. For instance, Professor Andrew Longstaff’s work on AI control of manufacturing systems relies heavily on the ability the process large amounts of disparate data in real time. In addition to the metrology applications that have risen from the ability to process real time data at higher frequencies, the advances made by the Sheffield team have the potential to impact on a wide range of fields.
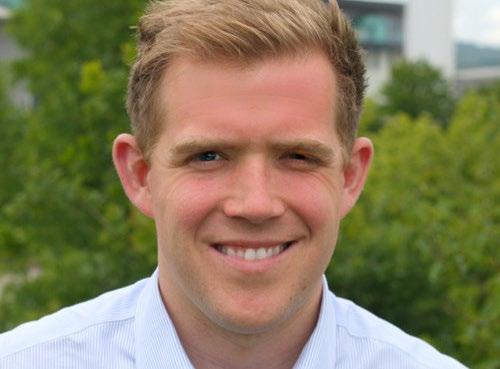
Ben Morgan, AMRC
UK Metrology Research Roadmap
The Hub recently published its UK Metrology Research Roadmap policy report detailing the findings of our first roadmapping event which took place in early 2020.
The event was facilitated by the Institute for Manufacturing, based at the University of Cambridge, and held over a full day at Loughborough University. Taking part were delegates from across the Hub consortium along with representatives from the High Value Manufacturing Catapult (HMVC) Centres, other Manufacturing Hubs, the National Physical Laboratory (NPL) and from across the UK Academic community. In total, 20 external organisations were represented. External delegates were invited based on their specialist knowledge or experience working in metrology research or in a related manufacturing field with unique metrology challenges.
Much work has taken place recently around developing roadmaps for metrology, especially in the fields of advanced manufacturing and industry. The HMVC Centres are currently working on a roadmap for UK manufacturing while a recent report published by HVMC investigated a systematic approach to integrated measurement and control for advanced manufacturing over a 10–year period. These exercises have generally covered the whole spectrum of metrology but have focussed on identifying the key challenges facing industry and the associated metrology applications and techniques which can be used to address them.

To build on the existing body of work, the Hub decided to focus our roadmapping event very specifically on the research landscape to determine the best ways in which the research community, comprising of Academia, Industrial R&D and Policymakers and Funding Bodies, could meet the needs that have been previously identified. Landscape
This table opposite is a condensed version of the overall landscape which outlines the highest priority areas identified on the day. The landscape consists of:
Trends & Drivers Goals for the development or refinement of new and existing technologies
Research Themes The highest priority areas to focus research activities
Capabilities & Enablers The practical and strategic resources which can be drawn upon to deliver the identified research programmes
Industry trends and drivers Including market, technology & business trends & drivers, product and service programmes (Including Industrial Strategy) Understanding and improving tolerancing (Aca & Ind)
Tracability (Aca & Ind)
Industry needs In‑process Metrology Portable metrology (Ind) Reduced lead times and cost, faster more efficient manufacturing processes (Ind & Pol)
Digital Metrology In process measurement (Aca & Ind) Embedded Sensors (Aca & Ind)
Metrology for Non‑controlled Environments Smart products processes and big data and analytics (Aca & Ind)
Sensornets (Aca & Ind)
Other Non contact measurement of light absorbing materials e.g. carbon fibre (Aca & Ind)
New Science Quantum, Photonics etc. Increased automation for global competitiveness (Ind & Pol)
Research themes Optical Technology (Aca & Ind)
Error Mapping and compensation of multi cooperating platforms (Aca & Ind)
Technology Product technology i.e. related to delivery of product functionalities New Sensor Technology (e.g. Miniturisation, Low Cost, Uncontrolled Environments, Challenging Materials) Miniaturisation of devices Automation, metrology system for assisted machining and assembly (Aca & Ind)
XCT (Aca & Ind)
Materials Technology, e.g. Nano materials, Hybrid materials Meta‑materials measurement and photonic integration
Enabling technology Portable metrology systems (in‑situ analysis) Real Time Systems (Measurement, Uncertainty, Analytics) Adaptive control Artificial intelligence
Manufacturing Production process technologies In‑process metrology system integration and calibration In‑process measurement of surface/subsurface geometry and other characteristics Modelling & Simulation (e.g. Digital Twin) (Aca & Ind)
Machine Learning & AI (inc. Category Semantic Language) (Aca, Ind & Pol)
Design for Verification
System engineering/ integration competencies
E.g. training, academia‑ industry engagement
Capabilities and enablers
Skills
Infrastructure (e.g. Asset/ facility requirements, etc. Process monitoring
Automatic defect recognition (NDT)
Measurement system integration to machine (accuracy vs machine and in‑process environment)
Skills and proficiency standard for metrology
Metrology Community Current Hub Consortium (Hub/Spokes, Feasibility Partners, NPL, HVM Catapult, Industry R&D,) including international collaboration
Wider Metrology Community (New relationships required to enhance research and delivery performance) National and/or regional metrology centres (e.g. Hub, NPL, Metrology Institutes, HVM Catapults) (Aca & Pol)
World class optical sensor research base (Aca, Ind & Pol)
Technology developers working with metrology institutes (Aca, Ind & Pol)
End users working with metrology institutes (Aca, Ind & Pol)
World class data science research base (Aca, Ind & Pol)
Industrial partnerships and industry engagement (Aca, Ind & Pol) True digital twin
Sensor integration into manufacturing process Closed loop control from process inspection
Rapid 3D surface mapping for comparison at micron scale (Aca & Ind)
Software tool to predict errors prior to manufacturing (Aca & Ind)
Infrastructure technology for AM GDT, design manufacture, metrology (Aca & Ind) Community education measurement/metrology (Aca, Ind & Pol)
Accoustic NDT (Aca & Ind)
High speed secure and robust communications networks (e.g. 5G) (Aca, Ind & Pol)
AI and autonomous technology (Aca, Ind & Pol) Real time error compensation during manufacturing (Aca & Ind)
Real time metrology (Aca & Ind)
Key Themes and Messages
Over the course of the event, several key themes and messages emerged which encapsulated multiple topics and covered broadly similar ideas across the prioritised research landscape. Highlights of these are given below and a more complete examination can be found in the full report, available on the Future Metrology Hub website.
Metrology as an enabling technology
Metrology has long been recognised as an enabling technology for engineering innovation, but this has generally been focussed on the ability to manufacture with greater degrees of accuracy and precision. Currently, significant interest is being paid to the potential for metrology to drive productivity improvements through reduced waste and scrappage and also as a key component of new technologies such as Additive Manufacture.

Growing metrology skills gap
Engineers and technicians rarely learn anything more than the most basic principles of metrology and it is only when they specialise that concepts such as repeatability, traceability and uncertainty are introduced. However, understand these concepts will be increasingly important as metrology becomes embedded throughout the manufacturing process. Metrology as a fundamental aspect of simulation, and by extension the design process
Using improved metrology to quantify all the variables in the manufacturing process unlocks the potential to accurately model and simulate the process from start to finish. This is fundamental to facilitating agile manufacture, optimally choosing the right machine and process within a set of given performance constraints. Companies engaged in the low volume/ one off manufacture of extremely high value components, where there is a need to get it ‘right first time’ will find this highly beneficial.
Metrology as a key component of sustainable manufacture
Sustainable manufacture is a topic of great interest to society however the impact that metrology can play is often overlooked. Improving metrology capability improves production efficiency which in terns leads to reduced energy and material costs. Novel technologies or approaches necessary to create the next generation of sensors/systems
Developing the next generation of metrology sensors and associated technologies is crucial to achieving true in‑process metrology. This can be achieved by drawing on cutting edge research in the fields of physics, data science and artificial intelligence to create novel solutions to the challenges of developing rugged miniaturised sensors and real time decision making using significant quantities of data.
KEY MESSAGES
Policymakers
Metrology is a crucial element of all scientific, manufacturing and industrial processes. Breakthroughs in these areas are often closely related to developments in metrology technology and techniques though the role of metrology is often significantly less visible.
An increased ability to quantify and evaluate various aspects of the manufacturing process can help companies achieve significant gains in efficiency. However, developing and adopting new metrology technologies and techniques is capital intensive and few companies have access to world leading knowledge and expertise in the field.
The true impact of the skills gap is not fully understood and could be significantly hampering the growth of high value manufacturing capacity in the UK. Meanwhile, the lack of a recognised framework for metrology training hampers both academia and industry in developing a strategic approach to addressing the skills gap.
Industry
Industry can often be reluctant to move away from established technology and tends to “stick with what they know”. Meanwhile, translating novel approaches to metrology from lab based experiments into industry ready solutions is often as challenging as the fundamental science. Building strong links with academia should enable much more rapid access to cutting edge technology and yield a competitive advantage.
The ability to accurately simulate and predict the outcome of machine/ workpiece interactions presents a substantial opportunity for manufacturers. Embracing this technology will enable more efficient, agile manufacture to reduce waste, cost and lead times.
The degree to which gains in efficiency can be made is often limited by the metrology technology available within a company. Building links with the metrology community can help to identify more appropriate or more capable systems and techniques which could have wide ranging impacts across the whole production environment.
The previous model of having a select few individuals, typically a QA department, trained in good metrology theory and practice will no longer be efficient or effective as in‑process systems become more widespread. Knowledge and understanding of metrology will need to be a core element of a production/manufacturing engineer’s training.
Academia
The field of metrology offers a wealth of opportunities to deploy novel science or technology into real world applications. Researchers in metrology should stay abreast of developments in scientific fields and actively recruit researchers from a diverse range of subjects by maintaining a broad network of connections.
Developing true digital twin systems presents a significant challenge due to the vast number of processes, materials and environmental conditions which must be understood. Crucial to achieving this is the ability to gather real world data from a broad range of manufacturing environments. Universities must build strong partnerships with industry where both parties have a willingness to share data and have close interaction if this is to be possible.
Training in good metrology practice is uncommon for undergraduate students. Typically, students and researchers are only trained in metrology when they encounter a specific issue. By incorporating metrology more broadly into the syllabus, graduates will gain a highly valuable skill and the pool of talent which the metrology community can draw upon to find talented researchers will be expanded.