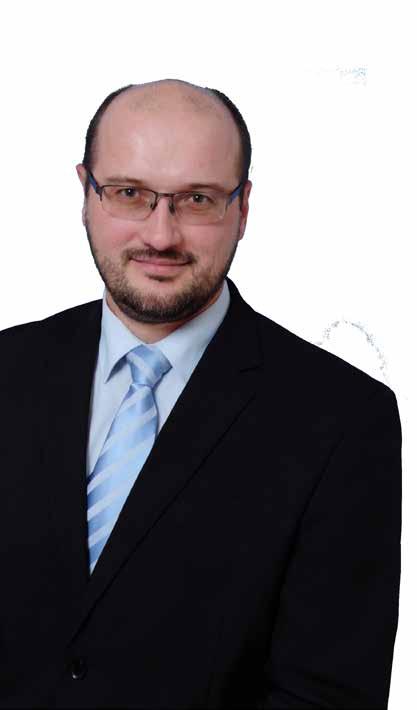
6 minute read
To mas Rais, Head- Logistics
tomas rai s
How are you reacting and responding to the pandemic? The current situation faced by the world has almost no equivalent. Of course, there have been unwanted events witnessed in the past, but the current level of measures to control the spread of the disease is unprecedented.
Advertisement
With the relaxation offered for indus tries to operate, we have to cautiously weigh our options to continue with pro longed pause, or to step in and set new standards of operations where life and livelihood have equal priorities. Together
with our medical team, we have setup a 60 point detailed SOP which defines our new way of operations - with built in social distancing, hygiene measures and a strict protocol to keep track of anyone who might display any symptoms of the disease. We are also ensuring there is lot of awareness that is communicated to everyone we are working with including the employees of our suppliers as that is the key to a rapid reset.
Not only auto industry but other business ventures too are still holding on to see what will be the long-term re percussions of this pandemic. One cannot just assume that things will get back to normal suddenly in 2021. The auto industry had started witnessing a de cline since 2018, and over the next few months, we have to continue to watch out for signs of recovery.
What are the practical challenges you are facing with right now and what have you adopted as the correct solutions to keep sales strong during tough times? Challenges like business continuity, liquidity, cost overruns, shrinking market demand are putting pressure on reve nue. From a logistics perspective, we cannot permit interruption of supplies to ensure continuity of produc tion. This means planning material dispatches with suppliers in ad vance to take into account delays that may be faced due to en-route checks or interstate travel re strictions. Working to get better visibility to supplier performance can be very beneficial to predicting potential supply disruptions and working proactively to alleviate the impact. Companies that aren’t electronically connected to key direct suppliers and don’t have real time data on the inbound flow of products and materials, should move quickly to implement programs to access data and enhance management and decision making capabilities. Tomas Rais, He ad of
Lo gist ics , Škoda Auto Volkswagen
India in an exclusive interview with Ritika Arora Bhola , talks about reorienting programming to rapidly support firm capacity, supply chain linkages, and ensure production continuity.
As an industry, the only way to stay relevant in the business is to be agile to the changes and be prepared to be flexi ble in response to whatever new situation that we may come to face. We also had to review investment decision, redrafted contracts with providers, prioritised spending, and checked the entire value chain and costs to look for optimisation.
What do you make of the stimulus package announced by the government? Any other measures you think the government should implement to strengthen the Indian auto industry?
The stimulus package announced by the government is a welcome move as it will give right boost to demand and growth of the economy. While it’s primarily a mix of fiscal and monetary support, the overall sentiment towards Ease of Doing Business processes and fundamental reforms is the highlight of the work done by the government.
Continued support by the govern ment will only ensure that the right skills and technology will benefit in the development of a stronger component ecosystem which is less dependent on import. While that will not happen over night, the critical volume required for such an industry to flourish is available in India and hopefully we will see more fulfillment in that direction. How helpful has been the modernisation of Skoda’s manufacturing with inclusion of advanced robotics and automation? We employ high level of automation in production, ensuring an adequate bal ance of modernisation of the manufacturing and logistics processes without taking away the critical human touch necessary for optimal quality. We have rolled out the Volkswagen Audi Seat Skoda (VASS) communication standard in our shops that allow for easy mainte nance, standardised communication protocols and interfaces. High precision processes like welded and glued joints are over 60 per cent automated as this allows stable production process, more uniform and symmetrical dimensions of car bodies. We have also increased auto mation in the paint shop in both sealing and panting areas that significantly re duces material consumption thus bringing environmental benefits.
By collecting data from automated stations we have the opportunity to analyse potential risks in part noncon formities, monitor material consumption, keep data for every vehicle manufactured, apply predictive maintenance of our equipment, and potentially re duce the requirements for ad hoc transportation of extra parts or spares.
Do you think technology helps in reducing significant turnaround time and freight cost? What are the key initiatives that Skoda has spearheaded as part of the larger industry?
Non-availability of information and data blindness were major factors affecting turnaround time. This leads to ineffi ciencies in value chain thus increasing the freight cost. Technology has helped improve the efficiency of maritime and
air traffic turnaround time which has helped reduce the freight cost for global supply chains.
Electronic exchange of information has infused transparency, better visibil ity and reliability in supply chain. Combined with tracking technologies such as GPS, resource planning has become more precise and thus improved overall efficiency of supply chains, benefits of which reflects in terms of turnaround time and freight cost.
Automation of processes in mate rial flow chain is also increasing production efficiency and helping us reduce costs. Use of non-conventional energy driven vehicles for transporta tion are being evaluated to reduce carbon foot print and fulfill our operational vision of achieving carbon neutrality by 2025.
With the pandemic situation in purview, how are you looking to reskill people to fill up the key roles? We have made sure that the skillset of our employees are updated and upgrad ed amidst the pandemic. Our HR has taken many initiatives like online train ing, skill development sessions, technological support to help our employees’ practice remote working. Technology has helped improve the efficiency of maritime and air traffic turnaround time which has helped reduce the freight cost for global supply chains.

The need is to be continuously skilled, and it is a key framework for all our employees.
How have you forged a supply chain that can withstand and recover from severe shocks with little insight on proactively developing resiliency? Over the last two decades, global supply chain has matured and has become lean er. While the main drivers of disruptions are known, supply chain design has mea sures in place to keep business afloat. We are able to tap into a complex global net work of suppliers to cater to the best quality products, while offering ourselves the cost benefit of volume sourcing.
While pandemic as the current one can affect our manufacturing opera tions, a geo singular event can impact supply chain and hence the advantage is to retain a plan ‘B’ for every scenario. This has been our approach to ensure production continuity and while we also practice high-level of localisation going up to 95 per cent for the upcoming MQB A0 products as part of the India 2.0 proj ect, as supply chain experts, we have provision for a wide range of contin gency, including accepting disruptions as a part of business temporarily and devise ways to minimise it.