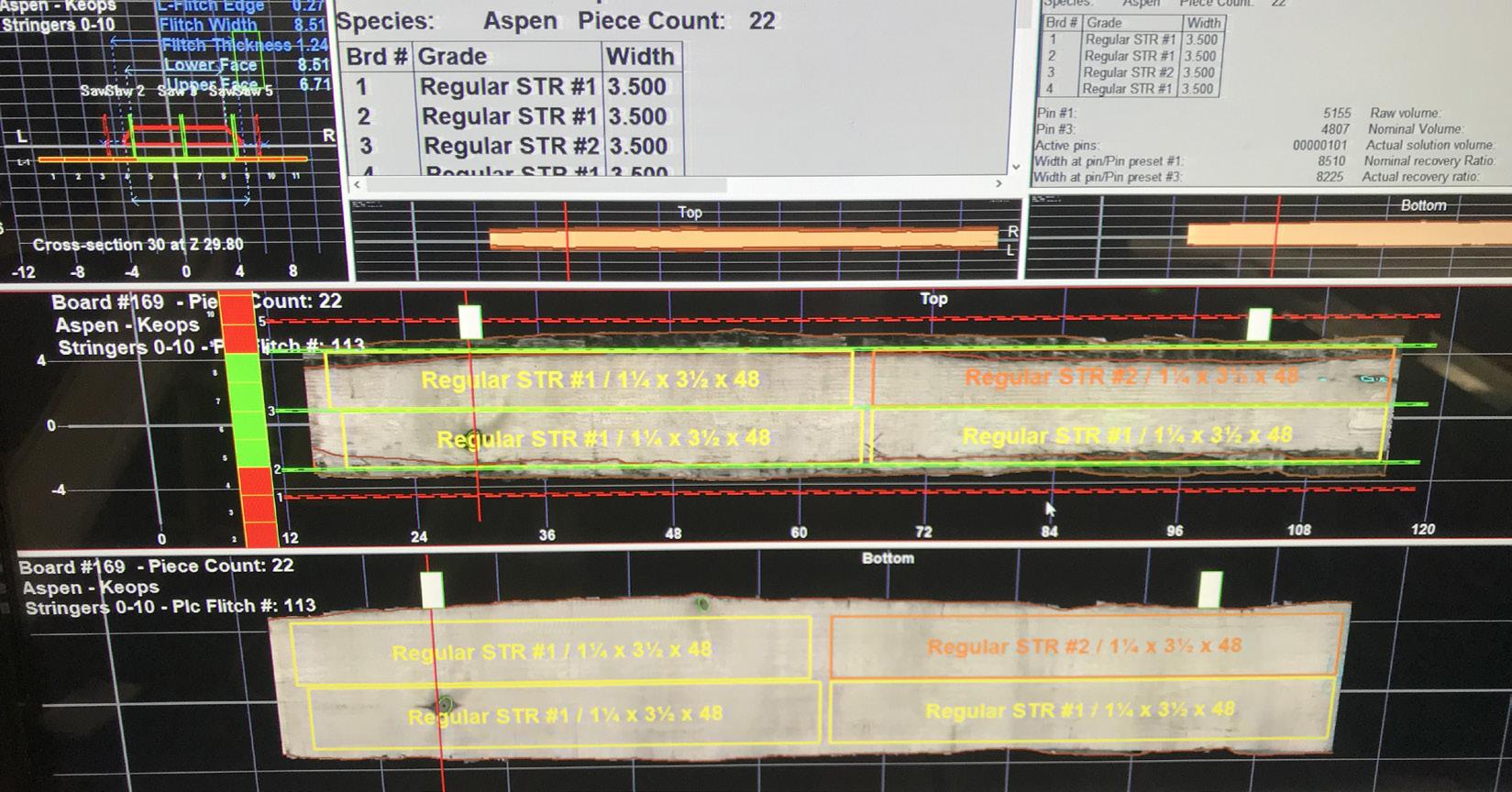
10 minute read
Waipapa Pine − Gaining efficiencies
from Millwide Insider #50
by USNR
Deep Learning
Deep Learning is a subset of machine learning, where neural networks learn from large amounts of data similar to how humans learn from experience. flitch for processing. to highly automated processing. After several months of operation, management responded, “There is still a ways to go to reach targeted capacity, but integration has gone very well. Our staffing level has gone from 16 down to 10 on the production line. We’ve increased our support and maintenance by specializing resources in mechanical, filing room, and electrical engineering.” Management also said, “We’ve increased the range of our products by staying flexible, and our product mix continues to evolve daily.” Mill personnel who were instrumental in the success of the project include Mr. Sébastien Tremblay, project manager, and Mr. Jean-Yves Roussel, financial manager who made it possible to complete the project on schedule. Mill management also This allows for faster start-ups and increasingly accurate grading solutions. USNR has sold over 60 systems to date
Advertisement
Edger vision scanning solutions highlight the benefits of BioVision with Deep Learning technology. Defects are identified highly accurately, and the optimizer fits the highest value board products into the
that use Deep Learning technology. noted, “This was a very good start-up and after-sales service, with good follow-up and communication with a very competent team from USNR.”
The mill is enjoying the benefits of advanced technology in its process, and now focused on increasing its capacity. While demand has slowed due to the pandemic, all indications are that it is ramping up once again to respond to a manufacturing climate that is gearing back up.
Waipapa Pine

Gaining efficiencies
SMART INVESTMENTS − SAFER, MORE SATISFIED PERSONNEL
Even when a mill is not capacity-limited, equipment upgrades delivering the latest technologies can bring significant returns, and make the job safer and more satisfying for equipment operators. Waipapa Pine’s chain of successful mill upgrades is proof positive. The results we have seen are outstanding. We’ve seen a 4.2% improvement in sawn recovery, an 8.3% improvement in grade recovery, and a 13% increase in output.
The new supply includes a Revolver Lug Loader fitted with a rotating overhead hold down assembly to facilitate dealing a variety of material thicknesses (above), and a Transverse High Grader and Multi-Track Fence to automate the grading, trimming, and sorting processes (left).
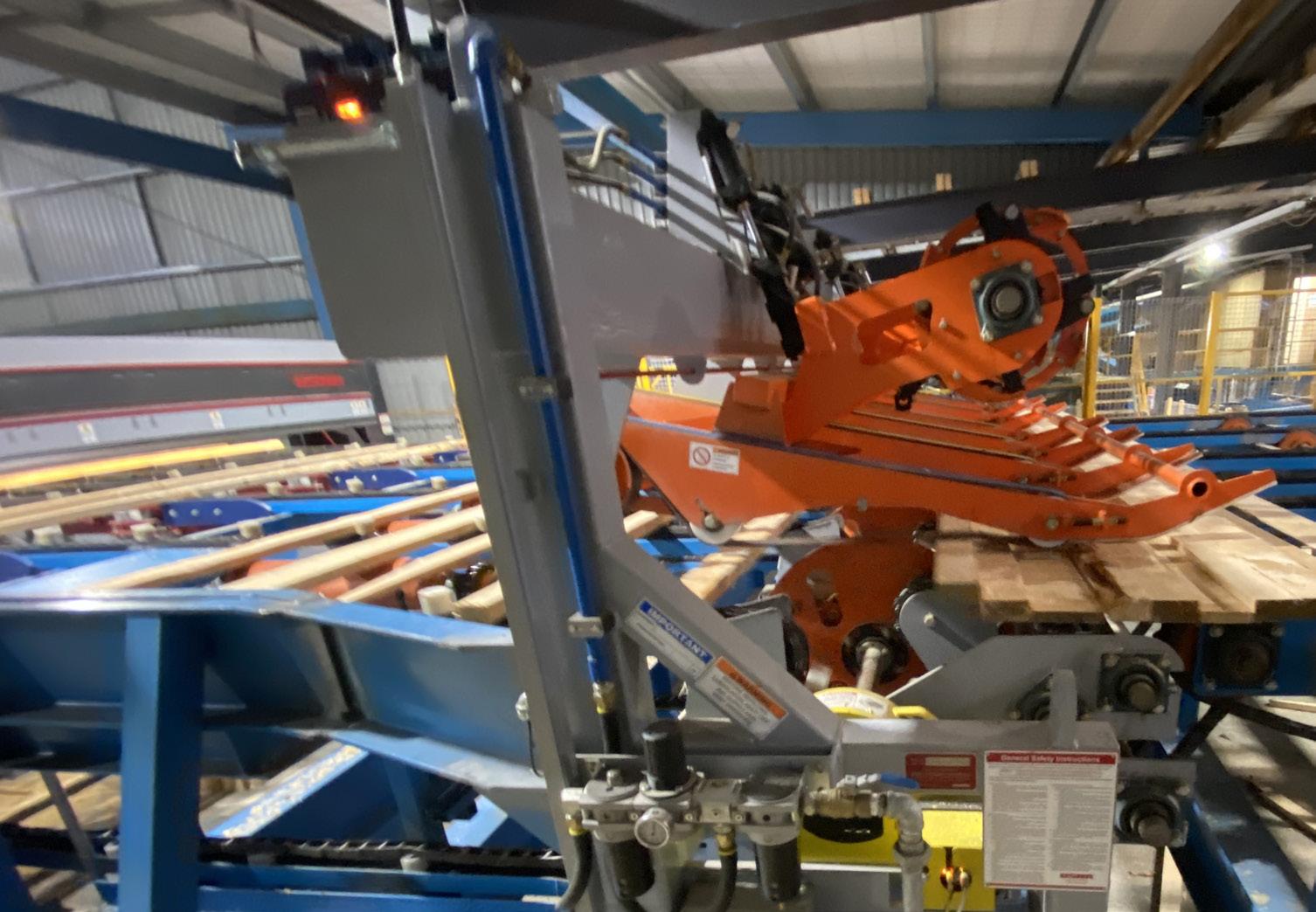
Waipapa Pine’s Kerikeri mill has been upgrading its processes to improve its bottom line, to increase efficiencies, and to move its staff to more challenging and satisfying roles. This latest project succeeds on all fronts.
The Waipapa Pine mill in Kerikeri, New Zealand has been in operation processing Radiata Pine into framing timber since 2012. In 2017 the mill installed a USNR Lasar2 scanning system to optimize its carriage operation. The most recent project, completed early in 2020, included major upgrades to the board edger, and green chain/trimline at the plant. Prior to the latest upgrades there were many roles within the mill that required very heavy, manual inputs from the team. The mill’s board edger was manually fed, at 8-10 boards a minute. Clearing the slash decks of rubbish from the board edger and trim line were also hands-on manual processes. Thus mill management decided to invest in new technology to improve these areas. Focus on efficiencies “We are happy with the overall capacity of the mill, so this investment was about moving our focus into gaining efficiencies around this capacity,” said Grant Arnold, Waipapa Pine Operations Director. Log prices in NZ have continued to increase due to export demand, while at the same time New Zealand expects to be experiencing a drop in harvest in this region in coming years. “We wanted to invest in technology that gives us every opportunity to maximize value return on the raw logs we process,” continued Grant. With this goal in mind, Waipapa management looked for improvements that could be made from both sawn recovery and grade recovery perspectives. They were also looking for an opportunity to dramatically change
WAIPAPA PINE — GAINING EFFICIENCIES
The new BioVision Edger system provides dramatic improvements in value recovery by accurately detecting and classifying the defects, far more precise edging, and better grade solutions.
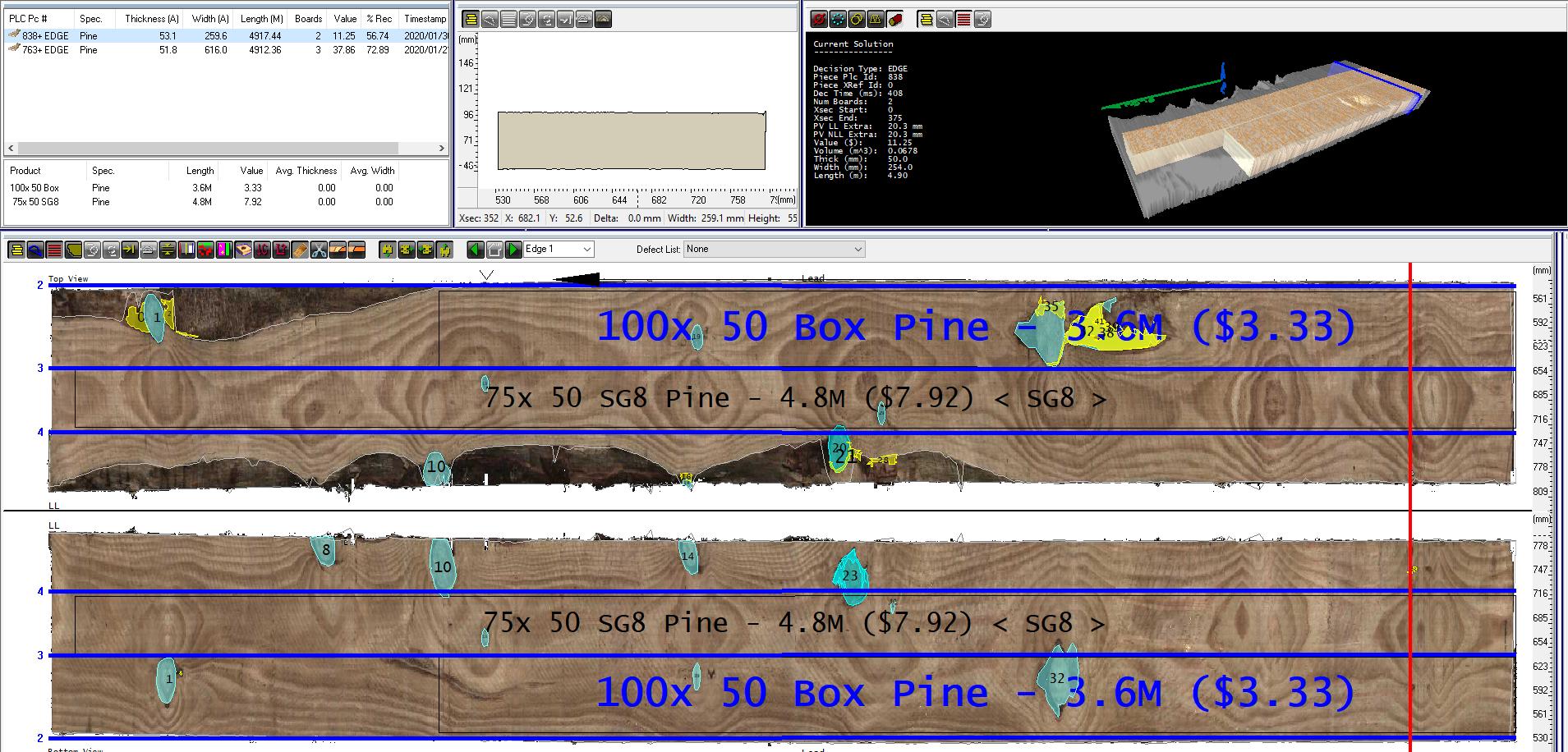
the type of work within the mill, from highly manual to far more automated, providing a safer workplace while increasing the skill level and satisfaction of mill personnel.
The mill’s decision The focus of the upgrades involved improving the functionality and level of optimization at the edger and trimmer stations. The mill’s goal was to provide enough speed/capacity to be able to run both green sawn and kiln dried, planed timber at the same time. This project would be the largest completed on site over the last seven years, but it had to be completed with minimal mill downtime. To provide this challenging solution, Waipapa looked to USNR. Waipapa management cited USNR’s high level of capability and focus on supporting the customer, so there was little interest in evaluating another supplier. Grant Arnold explains: “Several years ago, we invested in USNR 3D log scanning on our carriage,” he said. “We saw massive improvements in all measures off the headrig, so it was a no brainer to remain with the USNR platform.” USNR’s solution The new technology involved upgrades to the mill’s USNR 4TA36 edger that the mill bought used for this project, and was updated by USNR. This included adding a fourth shifting saw to the edger sawbox, and installing USNR’s state-of-the-art BioVision optimization system. The edger’s fourth saw accommodates the broad range of material widths the mill processes, ranging from 75mm to 300mm (3” to 12”). The BioVision system utilizes proprietary BioLuma 2900LVG sensors. Its optimization platform takes advantage of Deep Learning technology for enhanced defect recognition and classification. The project also included the conversion of the plant’s existing trimline to a combination line, with the goal to enable processing a random mix of green sawn and kiln dried material, with the addition of the Transverse High Grader (THG). The optimizer provides 3D modeling based on an enhanced optimization platform that is shared across all of USNR’s vision scanning products.
The THG utilizes 4-sided scanning as well as an end-grain scanner to assist in locating the board’s pith. This provides highly accurate defect detection and grade solutions for both green and dry products.
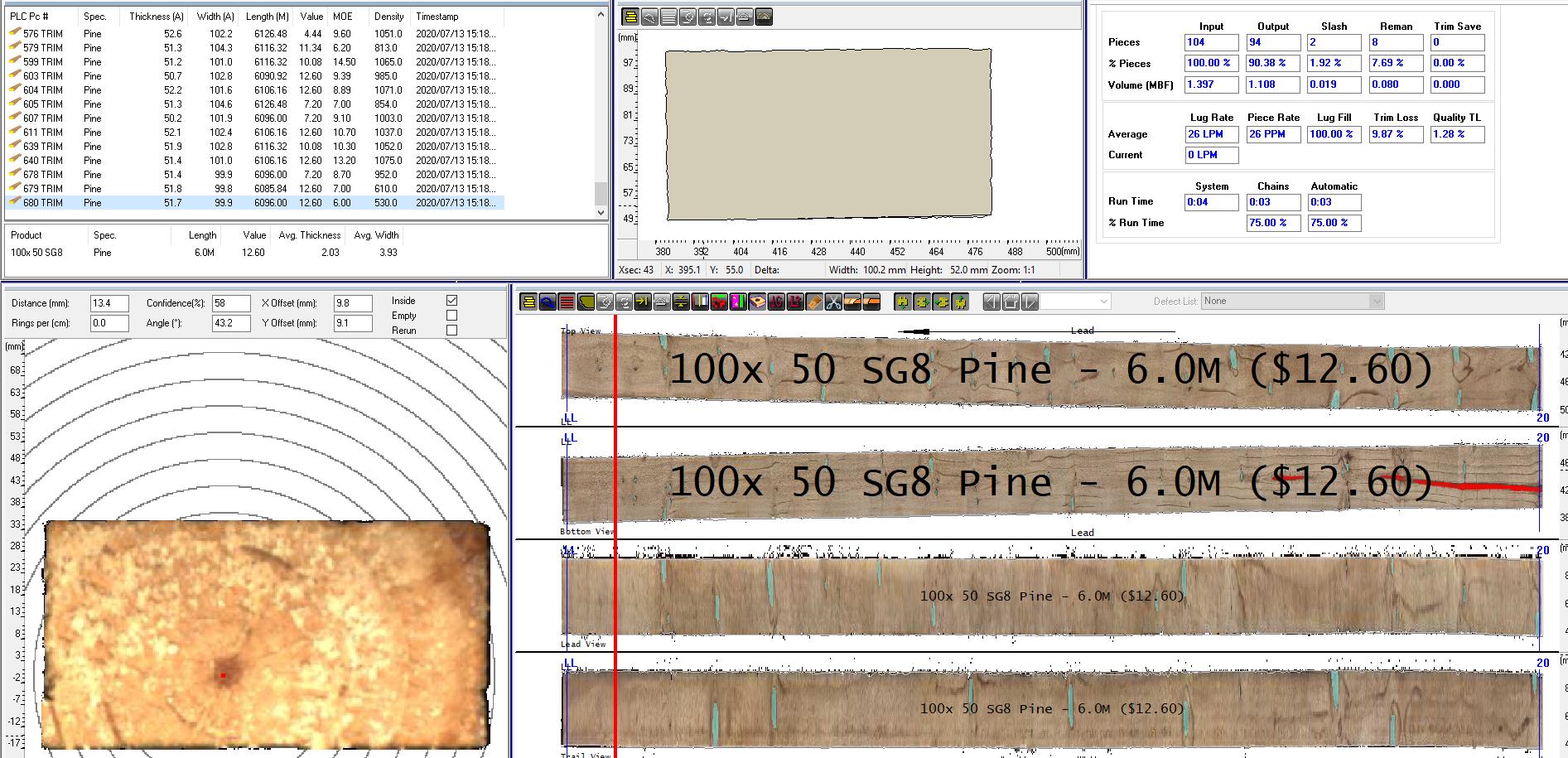
These systems are also now enhanced with the benefits of Deep Learning technology. Also included in the project were installation of a new Revolver Lug Loader and Multi-Track Fence. Both are instrumental in providing increased processing capacity, and maintaining efficiencies and trimming accuracy at the speeds that the mill targeted. The Revolver was chosen to efficiently handle the variation of product thicknesses, from 25mm to 105mm (1” to 4”), and green as well as kiln dried product. The Revolver is fitted with a rotating overhead hold down assembly that assists the feeding process for mixed thickness products. We wanted to invest in technology that gives us every opportunity to maximize value return on the raw logs we process.
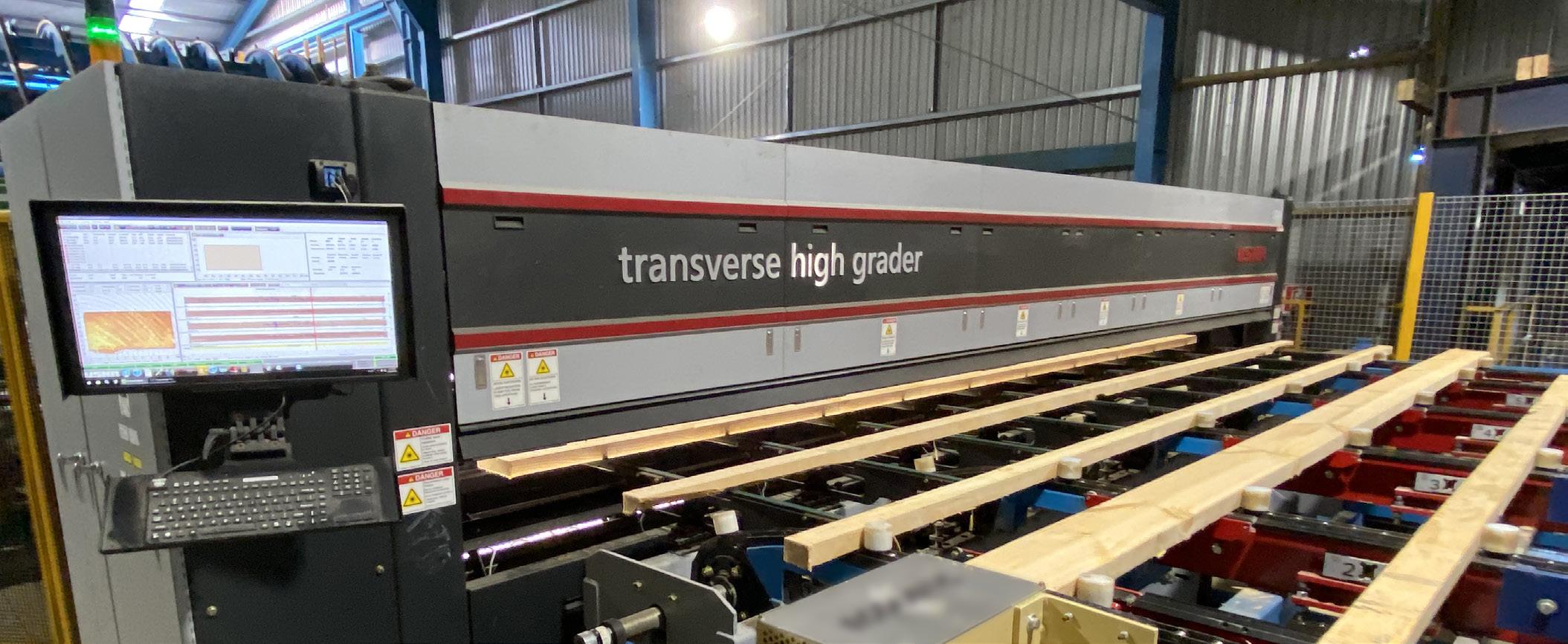
WAIPAPA PINE — GAINING EFFICIENCIES
The green trim line from the Revolver Lug Loader through the THG, Multi-Track Fence, and trimmer, to the incline to the sorter.
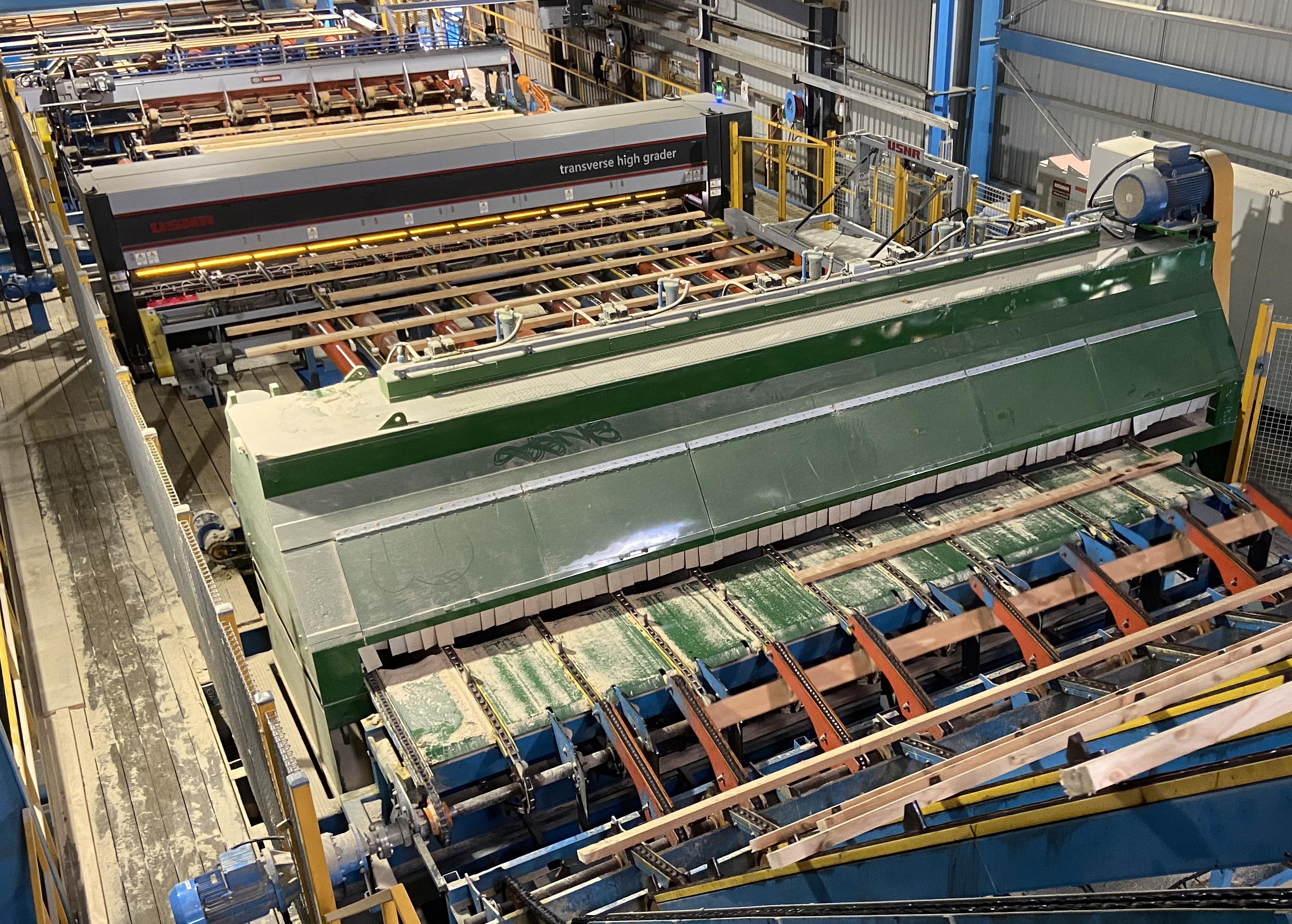
We effectively had two weeks to have everything mechanically completed so that electrical and controls could be installed. Dry line integration The planer outfeed is designed to feed directly to the green trimline on a separate landing deck. The mill plans to install a moisture meter after the Revolver Lug Loader to identify green vs dry material. This will allow the mill to run green and dry material through the green trimline simultaneously. This component of the project has been delayed due to COVID-19. In the meantime, with a wide range of product sorts the initial process employed is running dry material in batches through the trimmer line to take advantage of the grading accuracy of the THG. With the very attractive payback being seen, the mill is eager to implement this additional capability.
The installation The plant upgrades were clearly a team effort. USNR and Skookum Technology (USNR’s agent in the region) worked closely on engineering and project management, and mechanical integration of the new mill hardware was provided by Skookum. The groups coordinated closely with mill personnel to ensure a very successful result.
The project needed to be completed during the four-week downtime window over the plant’s Christmas shutdown. To prepare for the installation a lot of equipment needed to be constructed within the mill but offline, while the mill operated at full capacity. Other equipment needed to be assembled outside of the mill and readied for moving into place once the back end of the sawmill building was demolished. “Needless to say, planning and execution of the project was critical,” said Grant. “We effectively had two weeks to have everything mechanically completed so that electrical and controls could be installed.” “The USNR team members were great,” said Grant. “Everyone had their job to do and completed it without any issues at all. Communication between the USNR team and our project guys was excellent from start to finish. It was also great to have such highly skilled and knowledgeable USNR staff on site so we could learn from them.” Grant also noted that the Skookum design team did a great job, while Skookum engineers supported the Waipapa Pine team very well on site. On the Waipapa side, Phillip Crawley, Engineering Manager, completed an outstanding job managing the delivery of a complex project within the confines of a very small timing window to install and commission the plant upgrade. Processing Managers Jody Mitchell and Dan Spake also worked hard to ensure successful commissioning of the lines, and optimization of the outputs. Training of mill personnel was done at USNR’s facility in Salmon Arm, BC, and was also held on site in New Zealand during start-up and commissioning.
Results “The results we have seen are outstanding, across all key measures within the business,” said Grant. “We’ve seen a 4.2% improvement in sawn recovery, an 8.3% improvement in grade recovery, and a 13% increase in output.” Raw log input costs have reduced, and overall value return has been improved. This project has had a large impact on how the mill operates and the type of roles/work that staff members perform. Now, 95% of the operational jobs within the mill are very “hands off”. Health and safety stats have improved, and the company has been able to take its manual graders and train them in the new technology, which has given them a great boost from both a job satisfaction and skills perspective.
Prepared for the future “We are experiencing some very uncertain times, with unpredictable long-term economic impact,” said Grant. “This investment will provide us the opportunity to maximize efficiencies across our complete processing footprint, while being able to respond nimbly to any changing landscape we have in front of us.”
Upgrades will make your stacker run like new
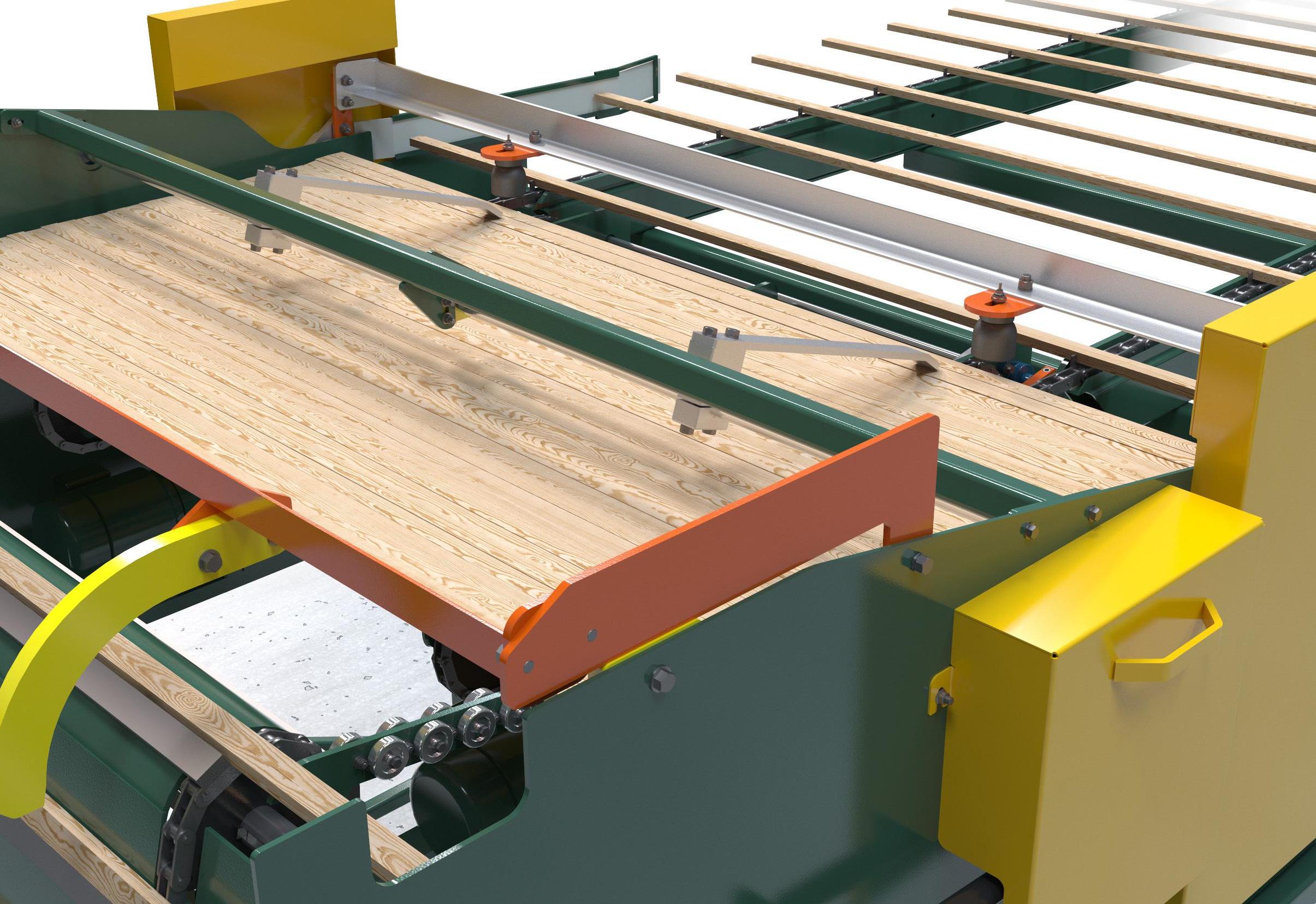
USNR offers three upgrades that will transform your existing stacker into a feature-rich, user-friendly design that provides excellent stick alignment and smooth, continuous operation at high speeds, all at a fraction of the cost of a new system.
The Stick Lifter upgrade replaces all lifters with the nextgeneration Direct Lift design that enables you to run at higher speeds without affecting lift position.
The Stick Feeder upgrade adjusts feeder timing to match the distribution lug chain-speed timing for smooth stick transfers even at the highest chain speeds.
The Rake Off Assembly upgrade converts your system from hydraulic to electric, for a smooth operation (up to 20 cycles per min.) while maintaining the ability to retract forks, even if boards are out of position, without damaging the Rake Off. Contact us to learn more.