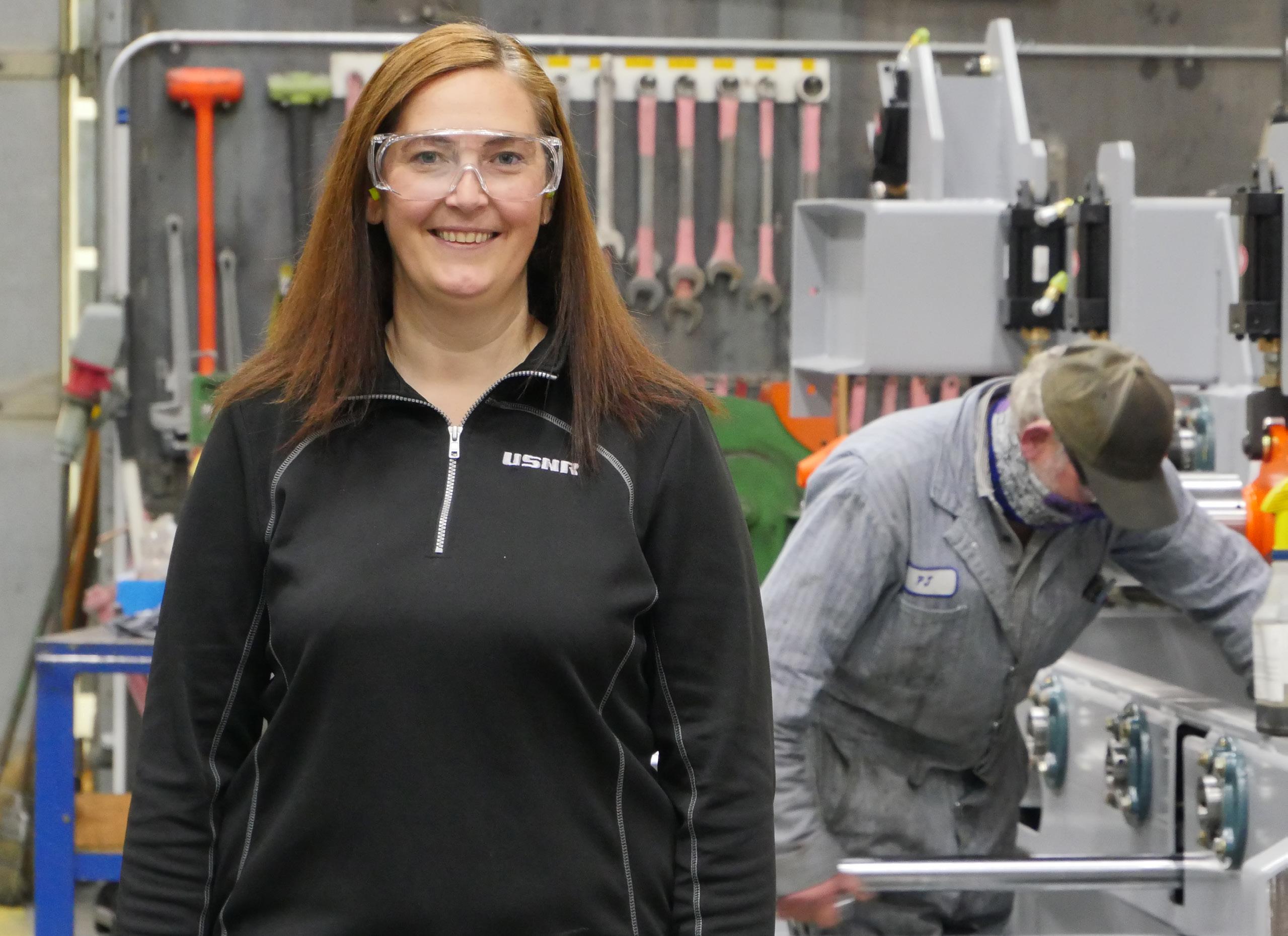
11 minute read
USNR’s Safety Culture − Driving this culture at USNR
from Millwide Insider #50
by USNR
USNR’s Safety Culture
Driving the safety culture at USNR
Advertisement
PROACTIVELY REDUCING RISK AND CULTIVATING SAFE WORK ENVIRONMENTS
Recognizing the importance of health and safety, USNR created a role to elevate this culture within our organization. Meet USNR’s Safety and Training Manager, Adrienne Bootsma. A proactive approach to safety lends to success, especially in morale, productivity, and overall cost. Safety is not a stand-alone initiative, but needs to be integrated into everything that we do.
The safety and training of our employees and our customers are very important to USNR during normal times, and now even more so with the advent of the COVID-19 pandemic. Fortunately we already had an experienced team in place along with the infrastructure to tackle challenges like these.
Safety and Training Manager Adrienne Bootsma holds the role of Corporate Safety and Training Manager. In this role she is responsible for the implementation of a comprehensive safety management system, and leads USNR’s safety and training efforts. Adrienne has a team that encompasses each of our facilities throughout North America and in Sweden, that promotes, monitors, and reports on our safety and training initiatives for our employees working at our facilities, and while visiting customers’ sites.
COVID-19 challenge The COVID-19 pandemic is a unique challenge for USNR as well as for our customers all over the world. But our responses have been swift, efficient, and effective. Adrienne notes, “The COVID-19 pandemic is ever evolving and challenges all decision makers, stakeholders, and health and safety professionals as we navigate uncharted territory.” Adrienne is proud of USNR’s proactive safety culture and says that this positive climate has really helped with the adoption of new processes and procedures. As USNR’s operations and customers are scattered around the globe, part of Adrienne’s job is to remain
USNRintegrates safety into everything we do abreast of trends, recommendations, policy, and law, in jurisdictions around the world. In connection with COVID-19, Adrienne has been leading a management task force to develop and implement safety policy, and actively intervene to maintain the safety of our personnel and stakeholders. Through our response efforts USNR continues to operate all of its manufacturing shops in North America and in Sweden. We also service customer equipment throughout the world on a daily basis. Adrienne says, “Everyday presents a new challenge, and through diligence and protocol we are navigating and succeeding. I am very proud that USNR is committed to the health and safety of all its employees.”
Safety beyond the pandemic Personal protective equipment now includes face coverings, sanitizing spray and wipes, hand sanitizer, and gloves. Adrienne notes that this is the new normal for personal protection. “There is a renewed emphasis on behavior-based safety; individuals are responsible for their behaviors. This proactive approach shifts influence from “having to work safely” to “wanting to work safely”. Wanting to wear a face covering rather than having to wear a face covering.”
Leadership Adrienne has had a long career with USNR, and her emergence as a leader in the health and safety arena is an important development for the company. Raised by teachers in a small community, Adrienne has always had a keen interest in continuous learning. Her career began in 1998 as a co-op student placement in USNR’s electrical plant at Salmon Arm, BC. Upon completion of a Computer Automated Systems Technician diploma, she joined the company fulltime. After successive advances, Adrienne became the Electrical Plant Manager. In 2017 she completed an Executive MBA in Health and Safety Leadership, and assumed the role of Environmental Health and Safety Manager. Adrienne has recently moved to USNR’s head office in Woodland, WA and has taken on a dual role leading the company’s
efforts for both safety and internal/external training.
Understand all the hazards and risks involved in the task at hand Seekto eliminate or minimize the hazards and risks Never proceed until an analysis is complete Re-evaluate the hazards and risks if anything changes
Delivers dramatic production increases
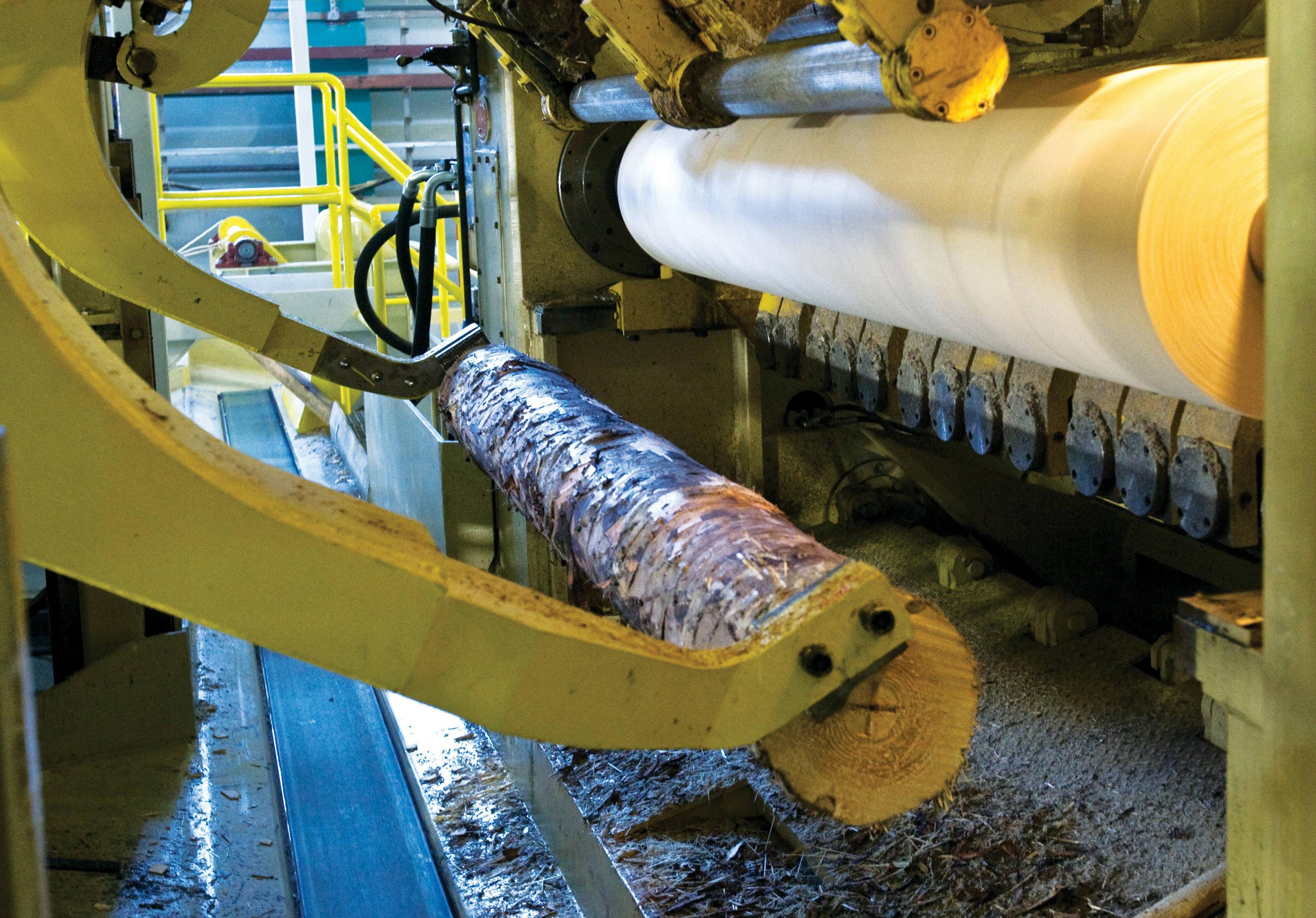
With over 150 years of experience, USNR’s Coebrand veneer lathe systems are known to provide the highest recovery, greatest throughput, and highest quality veneer in the industry.
Designed for both hardwood and softwood applications, our lathe systems accommodate log diameters from 4-1/2” to 60” (115 mm to 1,5 m), and will peel blocks down to 2” (50 mm) diameter cores.
Available in dual or triple spindle models, USNR lathe systems offer versatility and improved recovery. With over 1,200 lathes in operation, over 90% of veneer in North America is peeled on Coe-brand lathes. Contact us to learn more about the benefits of putting this technology to work in your mill.
New Projects
BR-Wood − New Sawmill USNR’s European headquarters, located in Söderhamn, Sweden, has signed a contract with the Belarusian company BR-Wood LLC for the supply of a complete sawmill. BRWood is the largest wood processing company in Belarus. The contract includes all equipment for log handling, debarking, saw line, edger line, lumber sorting, and residuals handling. All optimization and PLC control systems will also be supplied by USNR. Deliveries will begin in 2020, with commissioning in 2021.
Dempsey Wood − Bucking Optimization Dempsey Wood Products at Orangeburg, SC has ordered optimization and controls to automate its bucking line. The mill has been updating its operation for several years, and wants to increase log input to its sawmill, which this project will accomplish. The new optimization and controls systems will automate the line, resulting in much improved throughput as well as far higher recovery from each log. The new bucking system will be configured with 3 scan zones to accommodate the short infeed to the bucking saws, and utilize USNR’s BioLuma lineal laser profile technology to generate the bucking solution. The system will include the MillTrak 3D log gap control system which will monitor and control the gap between pieces to ensure smooth flow and maximize throughput. The installation is scheduled for the fourth quarter of 2020, with full production before the end of 2020.
Derome Group − Cambio 500 The Derome Group has signed a contract with USNR for a Cambio 500 for its sawmill in Kinnared. The new debarking machine will be delivered and put into operation at the beginning of next year. The new debarking machine replaces an existing Cambio 500 which has served the company well after service both in Kinnared and at another former sawmill.
Haapajärvi − Cambio 460 The latest in the line of orders for USNR’s Cambio line is a Cambio 460 to be installed at Haapajärven Ha-Sa Oy in Haapajärvi in central Finland. This debarking machine replaces an older Cambio 460 that will remain as a spare machine. The mill also has a Cambio 75 and a CamTrim flare reducer in the sawmill’s debarking line.
Jordan Lumber − LHG update, Deep Learning technology Jordan Lumber of Mt. Gilead, NC installed its Lineal High Grader (LHG) in the early 2000s, and it has been providing accurate defect detection and classification performance. With the advent of USNR’s Deep Learning technology and improved computing capability, the mill is now investing to upgrade its system to take advantage of the latest technology advancements. The upgrade includes moving to the new software platform now shared by all the USNR automated grading systems (BioVision in the green mill, Transverse High Grader in the dry mill, and AddVantage chop and rip optimizer in the value added market). The Deep Learning neural network will enhance knot, pith, bark, and other defect detection and classification, and provide highly accurate grade and trim solutions. The mill’s WinTally sorter management system will receive the latest version release. WinTally works in conjunction with the automated grading system to provide enhanced sorting and product processing.
KyKenKee − Counter-Flow Kiln KyKenKee Inc. of Vance, AL has ordered a new Counter-Flow Kiln to add drying capacity to its operation. The plant has 7 existing kilns, with 6 of those being USNR units. This new kiln will be natural gas-fired, and will utilize the Kiln Boss control system that also controls the other kilns at this site. The Counter-Flow Dry Kiln delivers continuous non-stop production, enabling you to increase kiln production by up to 50%. It uses a staging and loading system to keep packages moving through the kiln continuously and automatically. The Kiln Boss system allows the mill to easily control all important wood drying variables. The system tracks custom drying schedules, provides alerts to potential problems or to system changes, and reports batch and historical statistics for review. This latest kiln will be installed in Q3 and started up in Q4 of this year.
Moelven Notnäs Ransby − Multi-Track Fences Moelven Notnäs Ransby AB has ordered two Multi-Track Fences from USNR. The new units with their fast and precise adjustments will increase both the accuracy and the throughput for the operation. These two are #7 and #8 units sold in Europe (around 160 machines sold worldwide), three of which were also sold to Germany in quick succession.
Paul M Jones Lumber − Double track dry kiln Paul M Jones Lumber of Snow Hill, MD is expanding its kiln capacity with a new double-track dry kiln. The mill produces lumber and heavy timbers, much of which supplies treaters for marine applications. The new supply will more than double its capacity with a 54’ long steam-heated, high temperature batch kiln, and Kiln Boss controls. The existing kiln at this site is a Coebrand kiln, still performing well after decades of production. The Kiln Boss system will control both kilns, and the mill is also installing SCS in-kiln moisture measurement in both kilns. The new kiln is scheduled to be started up in Q4.
Piedmont Hardwood − StickN-Fork Stacker Piedmont Hardwood in Mount Pleasant, NC is updating its sawmill with a new Multi-Track Fence and a Stick-N-Fork stacker from USNR. The mill is looking to improve the accuracy and throughput of its trimmer line, and to gain efficiencies and productivity at its stacker. As part of this project, the control system will be updated to ControlLogix, and a WinTally sorter management system will be added. This project is scheduled to be completed in fourth quarter 2020. WKO − LHG update with Deep Learning technology The Wilkins family owns two mills: WKO at Carson, WA and Mt. Hood at Hood River, OR. Both mills installed USNR’s Lineal High Grader (LHG) a few years ago, and are now updating these systems with the latest technology that provides the benefits of Deep Learning technology for improved lumber grade classification and recovery. The latest platform that USNR provides for all of its grade scanning systems - both green mill and dry mill, includes Deep Learning technology along with other advancements. New vision sensors, computer hardware, and the latest software load will be installed. Deep Learning technology will provide enhanced detection of knots, pith, bark, and more defects. These systems will be upgraded later this year.
USNR and Bosch Rexroth are providing a solution for obsolete and long leadtime valves. We offer a highly flexible replacement/upgrade path to the more efficient series-4X valve, giving you options that minimize the New, Remanufactured, or Rebuilt? Yes! The program provides flexible options for sourcing series-2X, -3X, and -4X valves to keep your mill running smoothly while you plan an overall transition Bosch Rexroth Valve Exchange Program NEW! impact on your operation. to the series-4X valve platform. Options for new, remanufactured, and repair/exchanges allow you to avoid downtime during this industry-wide transition.
Valve Service Options
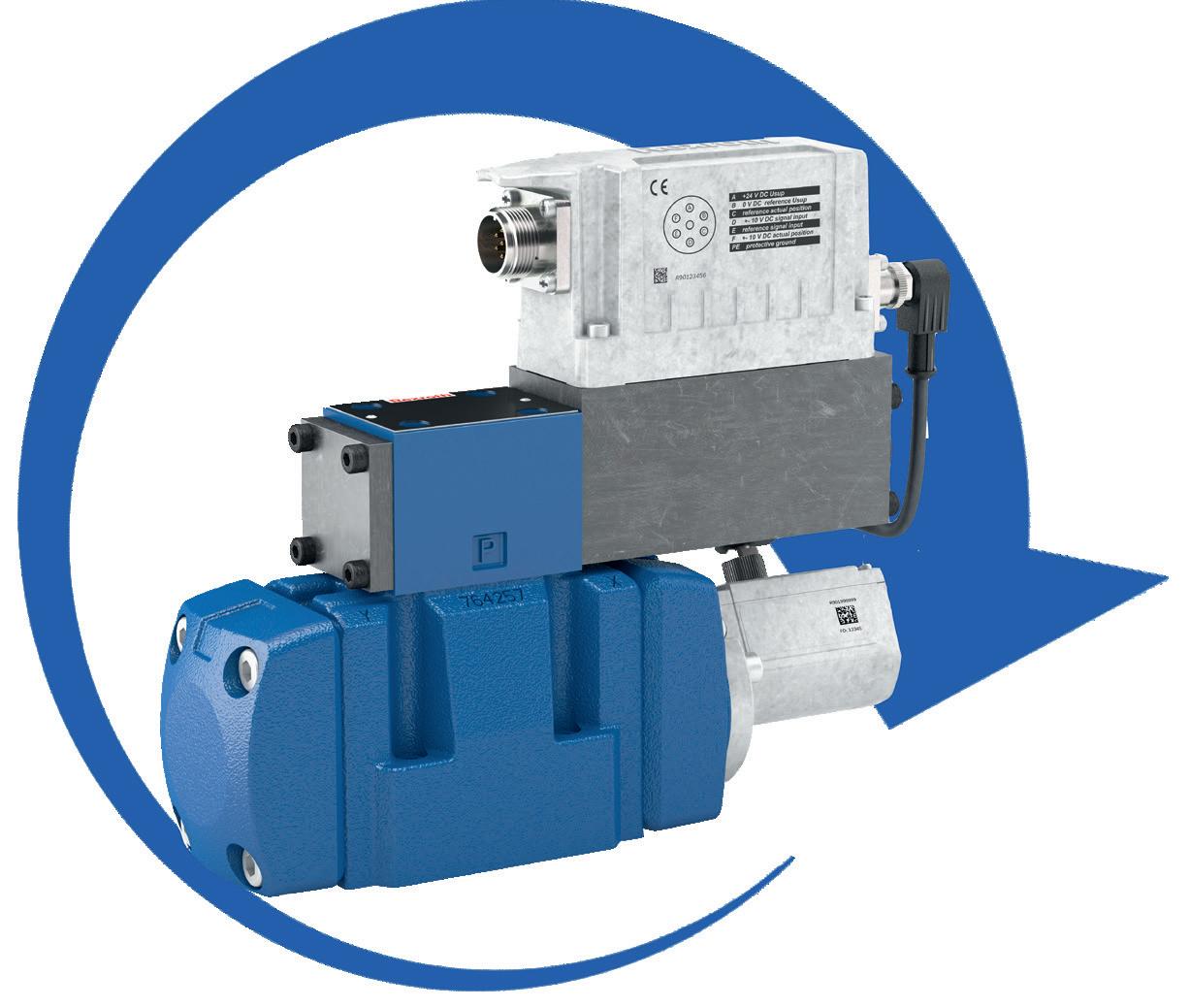
Purchase a lower-priced remanufactured valve and get a full 2-year warranty (from date of shipping). Requires a valve core return, core credit applied. Return series-2X, -3X, and -4X valves for rebuild. The 3-week standard turn around time drops to 2 weeks when shipped priority.
Purchase new in-stock valves and receive a core credit with the return of a replacement valve core.
Note: Upgrading the 4WRLE-3X series valve to a series-4X requires scheduling a service call for valve tuning at installation. Series-3X valve core return credit honored for a limited time.
PO Box 310 Woodland, WA 98674
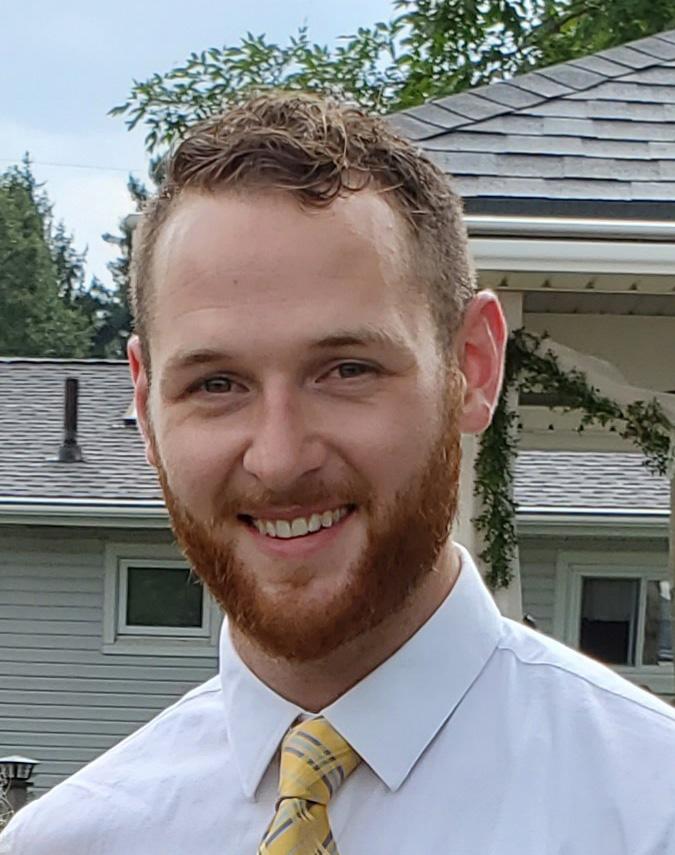
Profile
Upcoming Events 2020−2021
Clayton Paratore is an Account Manager, working in our engineered products division. He joined USNR in January 2019. The product lines Clayton is most associated with are large multiopening column presses for the manufacture of fiberboard, OSB, and other composite materials. He also promotes modern designs of presses for the rubber industry. A mechanical engineer by trade, Clayton earned his degree at Cleveland State University. His background includes the aerospace industry and with integrating automated systems for a broad range of industries. During that time he came to realize that he most enjoyed helping customers formulate solutions for their issues, rather than day-to-day engineering responsibilities. Clayton says, “When an opportunity came to join the sales team at USNR I seized it.” Clayton has especially enjoyed learning about USNR press products, and is awed at their longevity. “It is rewarding to see products like OSB siding distributed in applications across North America, and knowing that it was almost certainly made on a USNR press. Traveling to rural communities that have grown around plants with our reliable, long-life systems has shown me the importance of supplying quality equipment.” He also notes how eager the USNR engineering team members are to help him get his feet wet in a new industry. Clayton practices Brazilian Jui Jitsu as well as several forms of mixed martial arts. He and his fiancé, Jordyn, enjoy cooking together and entertaining guests with their culinary pursuits. He says, “We are nutrition nerds!” He applies his mechanical engineering talents to work on his ATV and truck, and is also avid helping others achieve their fitness goals.
2020 Events:
SEPTEMBER 15−18: Woodworking, Minsk, Belarus
SEPT. 30−OCT. 2: ExpoDrev Russia, Krasnoyarsk, Russia
OCTOBER 14−15: OptiSaw (Virtual) 14−English, 15−French 2021 Events:
MARCH 23−25: Montreal Wood Convention, Montreal, Quebec
MARCH 30−APRIL 1: Mass Timber Conference, Portland, OR
MAY 21−22: Expo Richmond, Richmond, VA
MAY 10−14: Ligna, Hannover, Germany