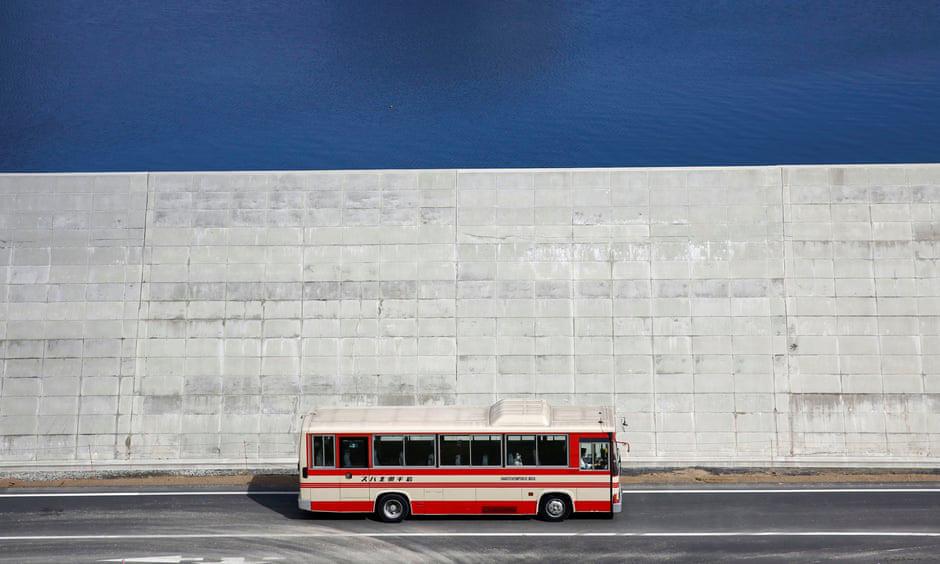
7 minute read
RESEARCH
This workshop explores different ways that the City of Austin and contributing companies are tackling the problem of C02 emissions in the use and production of concrete.
As we know, concrete is a major contributor of greenhouse gases and next to water is the most widely used substance on earth. If concrete were a country, it would be the third largest carbon emitter in the world only next to China and the US. We are seeing an unprecedented growth in cities around the world, in particular Austin, which is projected to grow by 28% in the next 10 years to 3 million residents. How can we continue to expand at such a rapid rate while mitigating the impact of construction on the environment? If we are to meet the goal 2050 goal of the Paris agreement, which is carbon neutrality, there needs to be a complete approach of how governments, companies and individuals participate in building. Because of concrete's qualities and strength, it will continue to be used, the question is how and what we do to use it.
Advertisement
Low-Carbon concrete is quite a broad term. It can be characterized through a multitude of different materials, processes and initiatives.
A seawall in Yamada, Iwate prefecture, Japan, 2018. Photograph: Kim Kyung-Hoon/Reuters
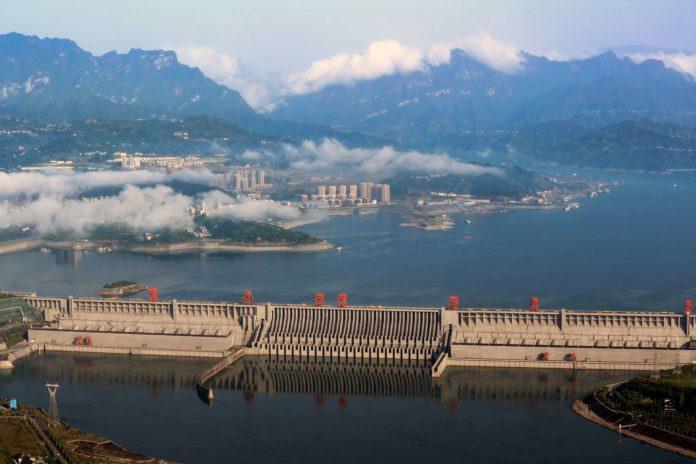
Source: Pixabay
We looked at a collection of different innovative products, methods, and approaches that ask the question of how we reduce our carbon footprint in the construction and building industries.
Brandon Williams of CarbonCure
CarbonCure has developed a “stackable technology” that can be incorporated into existing workflows, reducing emissions by 5% (new interactions are pushing these reductions closer to 30%). Their process re-purposes carbon dioxide from industrial processes without compromising the overall performance of the concrete, making it a viable option for projects of all scales. Injected CO2 gas is chemically converted into solid mineral carbonates. This simultaneously stores the carbon within the aggregate and increases the strength of the resulting mix. To date, CarbonCure has implemented its technology into 300 operations worldwide and 4 facilities in Austin in collaboration with Lauren Concrete. In the Lake Austin HEB project by LakeFlato, there was an estimated savings of 160,500 lbs of CO2.
Brandon Williams joined us in part-one of the workshop as the Market Development Manager of CarbonCure. He was trained as a Civil Engineer and has nine years of experience in the concrete industry. Generally, the private industry has mostly utilized CarbonCure but Brandon Williams stated “There are instances where we are able to get state approval on our technology, we are trying to get acceptability in the public sector.”
Cory Miller of Lauren Concrete
Lauren Concrete is leading provider of ready-mix concrete in Central Texas. Started by two brothers, Ronnie and Ray in 1986, with one plant and three trucks, the company has grown into 23 plants and over 500 employees. With the introduction of CarbonCure in four of their plants, with plans to expand to more, the ready-mix company has taken on large jobs such as UT Energy and Engineering Building and the HEB at Lake Austin. We were joined by Cory Miller of Lauren Concrete.
Cory is Quality Control Manager where he rigorously tests the strength and quality of the newly implemented CarbonCure in their ready-mix concrete. “We tested CarbonCure with cement and ash to see how reactive it would be. After that, we found our dosage rate,” said Cory. “We are seeing significant strength increases from our standard control mix with CarbonCure, and I’m confident in reducing cement content by 6%. Even with this reduction we are still achieving over-design.”
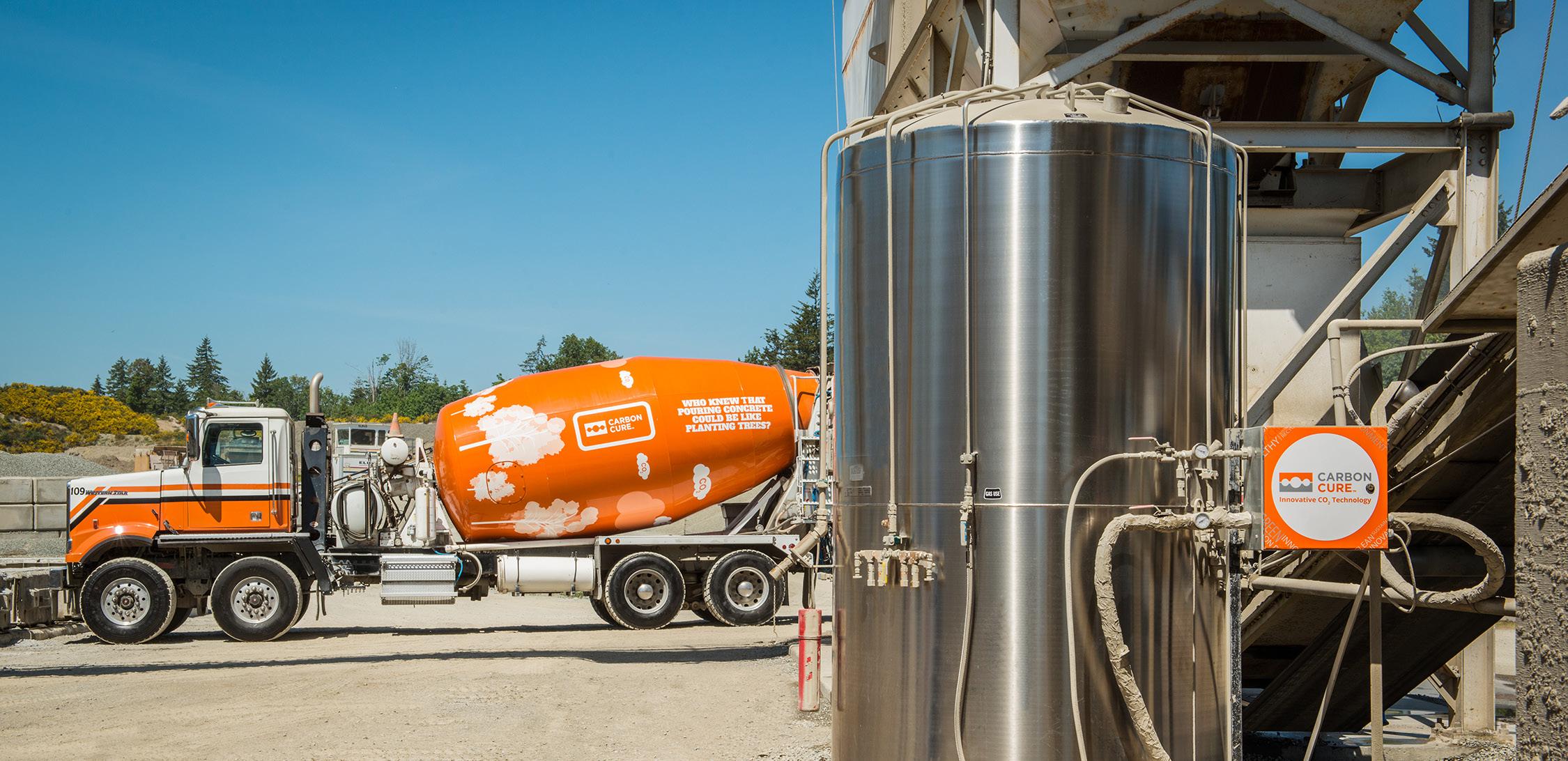
Source: CarbonCure
Tom Ennis of the City of Austin
Tom Ennis is a Sustainability Officer with the Watershed Protection Department at the City of Austin. He was trained as an Environmental Engineer and has been central in bringing CarbonCure to the city of Austin. He continues to push for further innovation as he believes that CarbonCure is only a stepping stone, and not a “cure-all” to the carbon emissions problem in concrete production. “It’s time to reconsider the 100-year old mixes, it’s coming, it’s going to be a decade of change.” Tom helped pass a resolution recommending “supporting the development of pilot programs that utilize Carbon Dioxide Mineralization Concrete for future Austin infrastructure projects.”
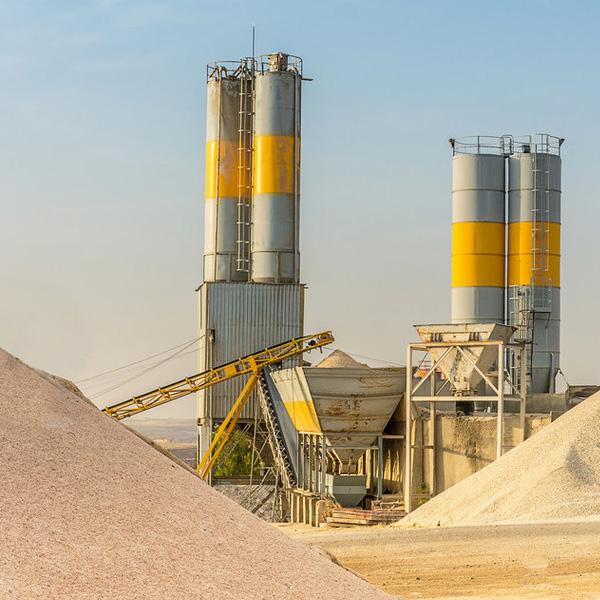
Blue Planet plant
Dougal Heap of Blue Planet
Founded in 2012 by Brent Constanz, Blue Planet’s approach to tackling the carbon emissions issue involves the use of synthetic limestone to permanently encase atmospheric carbon inside their aggregate. This aggregate can then be used to offset the use of natural limestone or even sand, depending on the coarseness of the granules. To date, their largest implementation has been the construction of the San Francisco International Airport. With the implementation of their aggregate, they were able to make each cubic yard of concrete carbon-negative. As the technology becomes more readily available, they hope to make their product the more economically viable alternative for all projects.
Dougal joined us for the second part of the workshop where participants got to physically engage and work with the product that he presented. He is the product manager at the California based Blue Planet LTD. "We are finding an inexhaustible supply of calcium and alkalinity. The current sources will enable the capture of tens of millions of tonnes of CO2, but Blue Planet’s mission is to sequester billions of tonnes of CO2.”
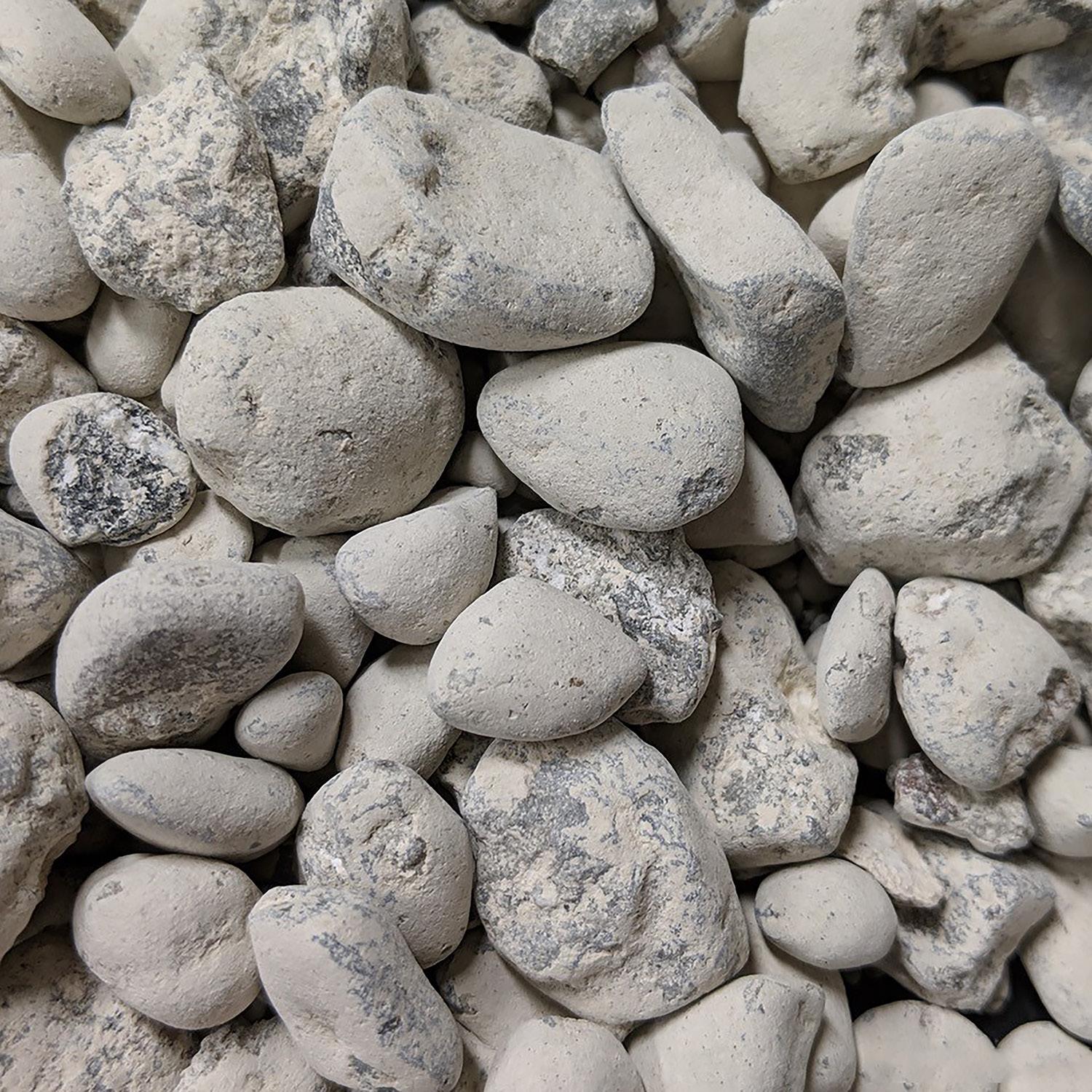
Coated Blue Planet Aggregate
Concrete Canvas
Our last featured material was from Concrete Canvas. We explained to participants how the material could be used and then allowed them to experiment outside of the workshop.
Concrete Canvas is a flexible, concrete-impregnated fabric that hardens when hydrated to form a thin, durable, waterproof and fire resistant concrete shell. It is made up of three layers; the top is a fibrous material that enhances hydration and encourages plant growth. The middle is composed of a 3D fiber matrix filled with dry cement. It is backed with a PVC coating. The canvas allows for construction without the need for plant or mixing equipment. Concrete Canvas can be laid at a rate of 200 m2 per hour by a three man team. Overall, it uses 95% less material than conventional concrete applications. The company got its start making inflatable concrete structures that were used as shelter. Today, the canvas is often used to prevent erosion near bodies of water.

The original product was invented as an emergency shelter. Source: National Geographic Section of Concrete Canvas Source: Titan Environment

The following products and innovations were researched by the Materials Lab and show the scope of lowcarbon concrete and how it is being incorporated into building and construction.
Self-Healing Concrete
Developed by Henk Jonkers and a team at Delft University of Technology, self-healing concrete utilizes dormant bacteria and food starch to fix cracking in concrete. When a crack appears, water seeps in and reactivates the bacteria, adding to concrete longevity and structural integrity. More here.

MineralBuilt
From our very own Cisco Gomes at the University of Texas, these CMU blocks are designed with the strength of masonry but flexibility of wood framing. Using standard CMU molds, these blocks can be made 50% faster and can fit 33% more on a standard shipping pallet. More here.
Knit Candela
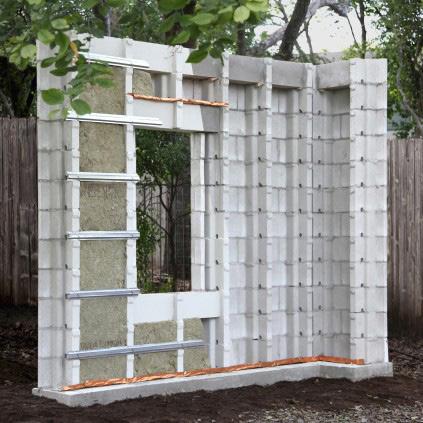
From the office of Zaha Hadid and ETH, Knit Candela is a thin concrete shell that utilizes a lightweight waterproof knit formwork that can be left in place after the concrete cures. More here.
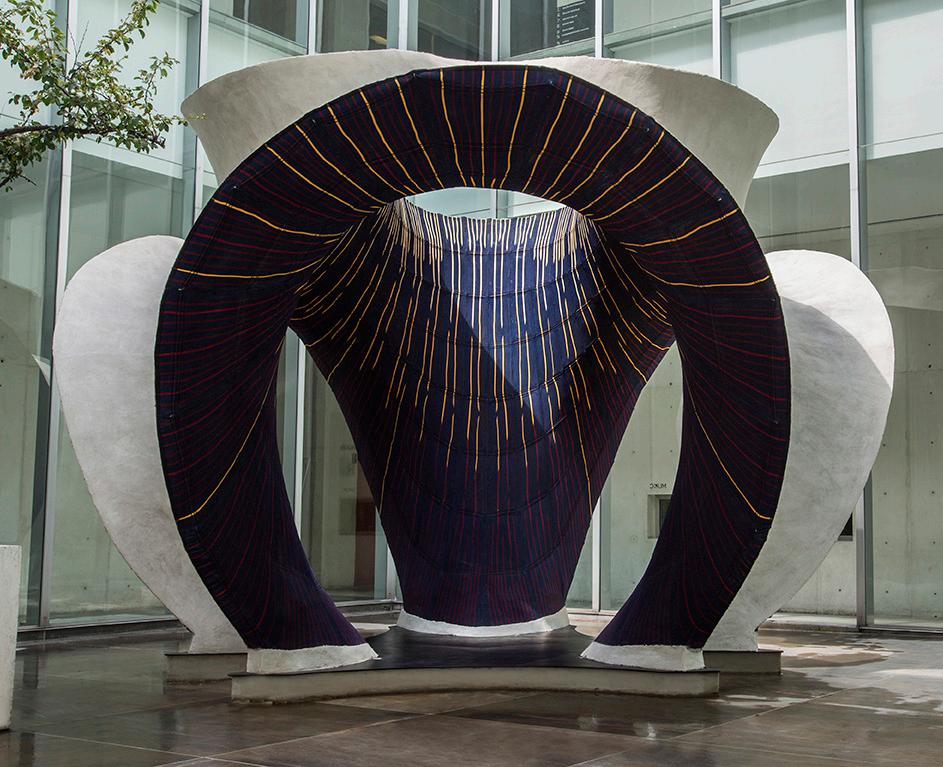
CarbiCrete
This company eliminates the need for cement by using ground steel slag which is a by-product of the steel manufacturing process. Similar to CarbonCure, the blocks are then cured using C02, giving the concrete it’s strength. More here.

U.S. Lawmakers Take a Concrete Step To Battle Emissions
The New Carbon Architecture: Building to Cool the Climate
Concrete: the most destructive material on Earth
CarbonCure
Lauren Concrete
City of Austin watershed protection
Blue Planet
Concrete Canvas