world,theAround earth.todown 2022-2023 isSustainabilityinourDNA
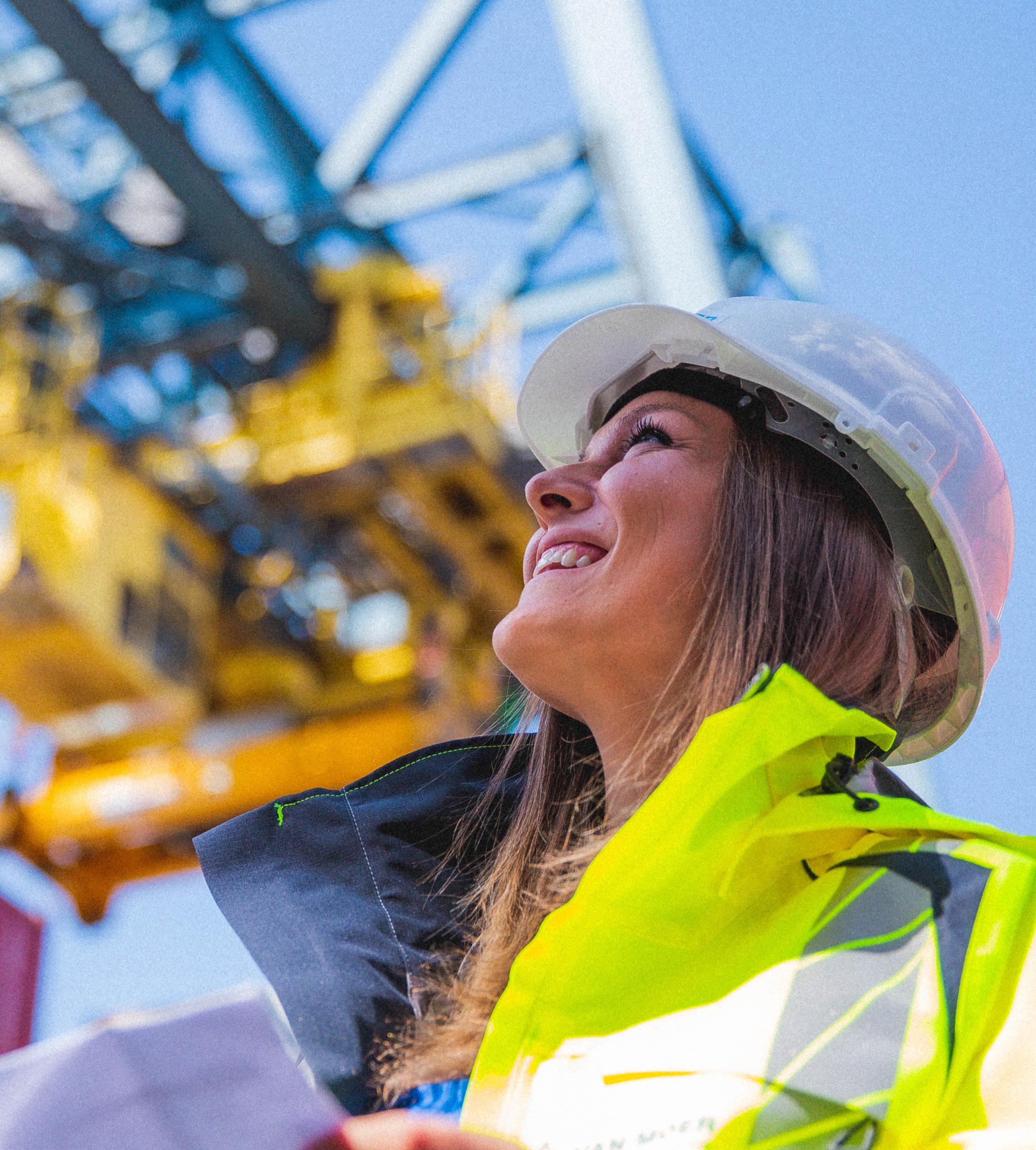
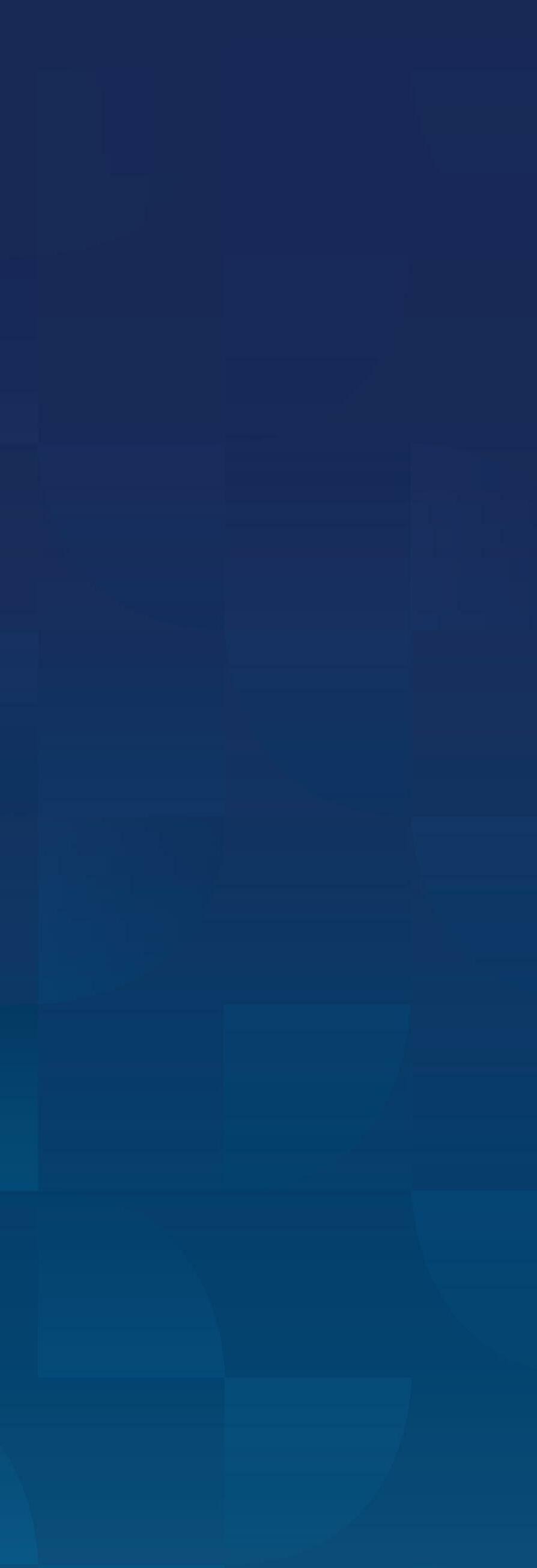
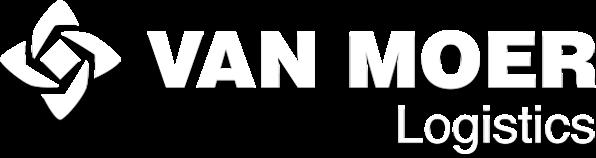
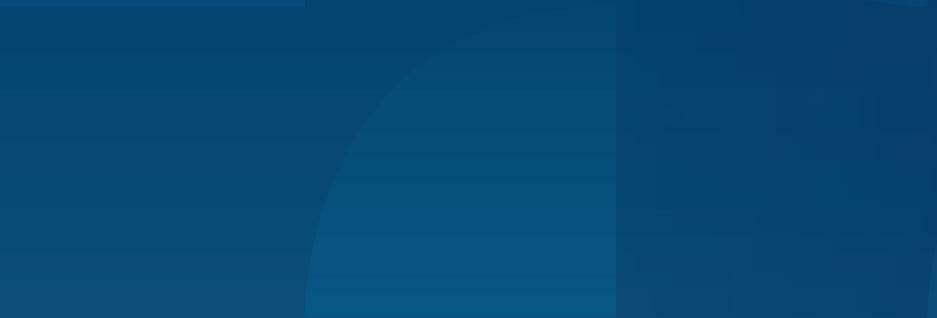
01CONTENT PREFACE 3 02 OUR GROWTH 5 03 KEY FIGURES 6 04 HIGHLIGHTS 2021-2022 8-10 05 OUR ACTIVITIES 10-12 06 EXECUTIVE COMMITTEE 13 07 OUR EXPERTS 14 08 CERTIFICATES 15 09 THE WORLD IS CHANGING 16-19 10 SUSTAINABLE STRATEGY 20-21 Intermodal solutions 22-29 Sustainable and efficient operations 30-47 Commitment to people and safety 48-55 Social responsibility 57-59 11 EVALUATION TARGETS 2021-2022 60 12 OVERVIEW TABLES 61 Overview table SDGs 61 Global Reporting Initiative 62
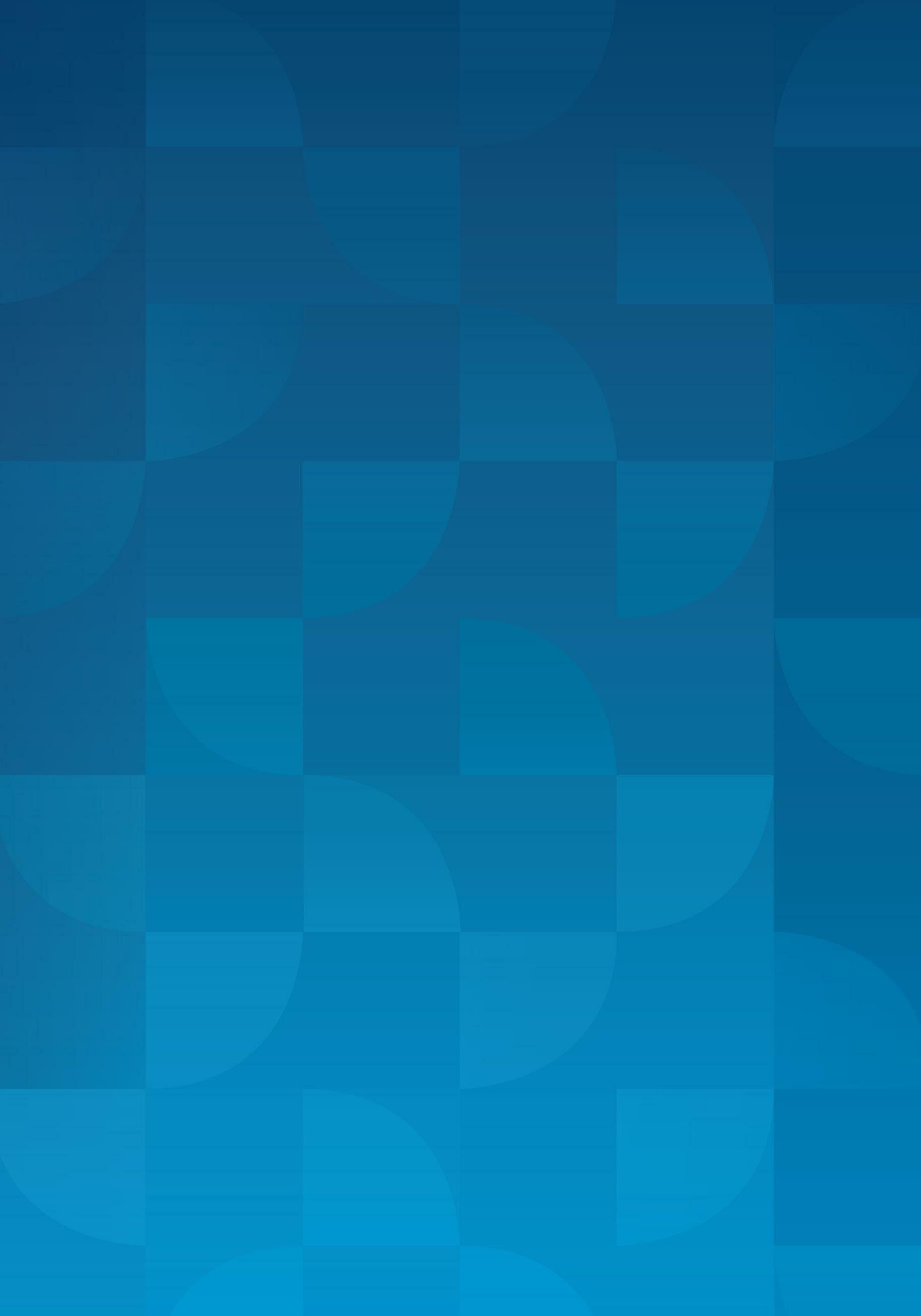

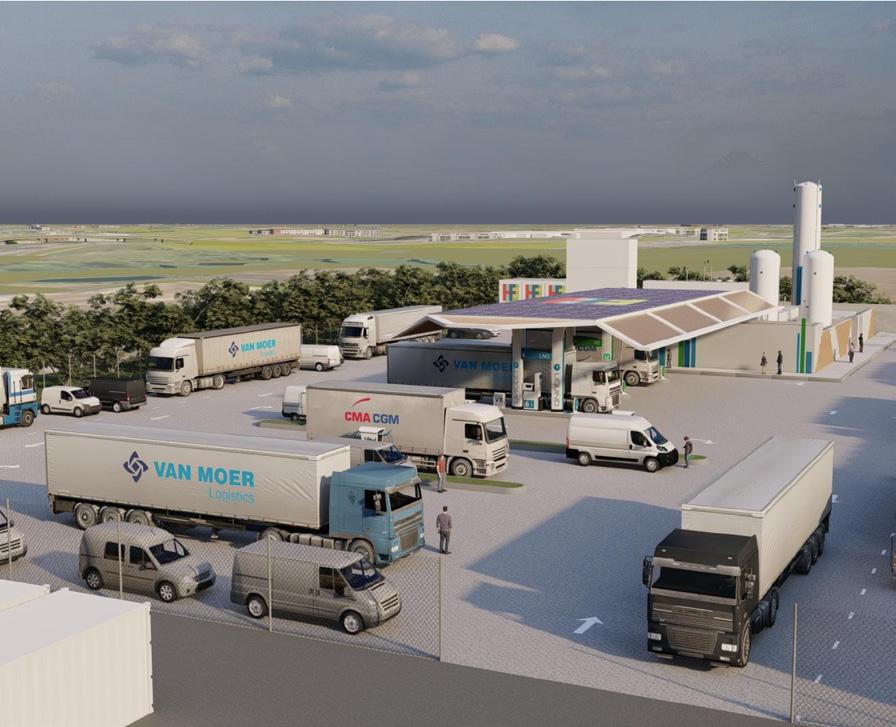
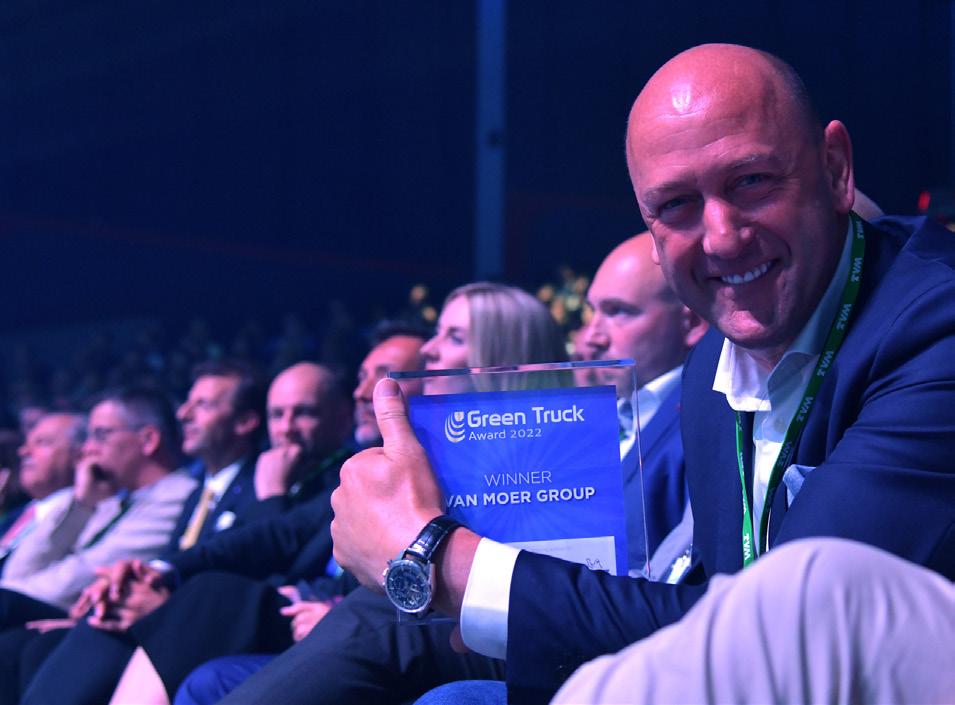
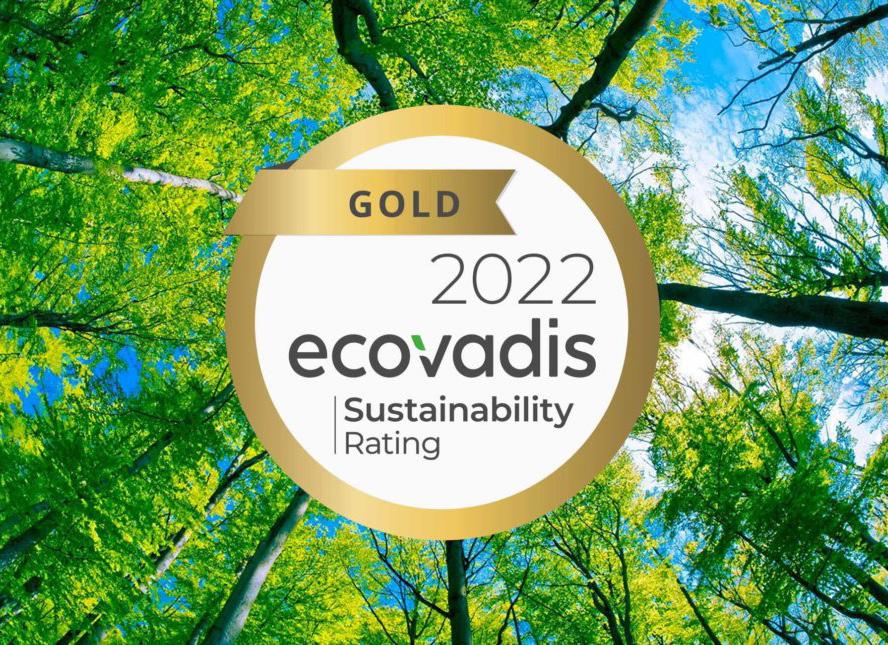
Intermodal solutions Sustainable and efficient operations Commitment to people and safety Social responsibility
This is our second report on our sustainable strategy. In doing so, we have started a tradition. Today, this is still a voluntary commitment, but European regulations will make it compulsory for all companies of our size within a few years. We are already doing this because we believe in the power of cooperation throughout the chains. The positive energy we feel in our many collaborations around intermodality and sustainability confirms that our partners appreciate this as well. Our sustainable strategy, defined in 2021, consists of four pillars that all stem from the ambition to make a difference as a company to customers, the environment, our people and to society in general. The strategy remains unchanged: PREFACE
OUR VISION ON GROWTH Growth is important. Together with all the companies in the port of Antwerp and in Flanders, we must continue to create jobs and prosperity. But this growth must be sustainable. For us, this means that economic growth must be decoupled from the depletion of raw materials and the ecological footprint.
As a partner in sustainable growth, we think creatively and help our customers to continue to achieve this growth in a feasible way. Through our intermodal approach, we ensure that our customers’ complex and circular supply chains can run and grow perfectly with the lowest possible impact on people and the environment. OUR STRATEGYSUSTAINABLE
3Van Moer Logistics
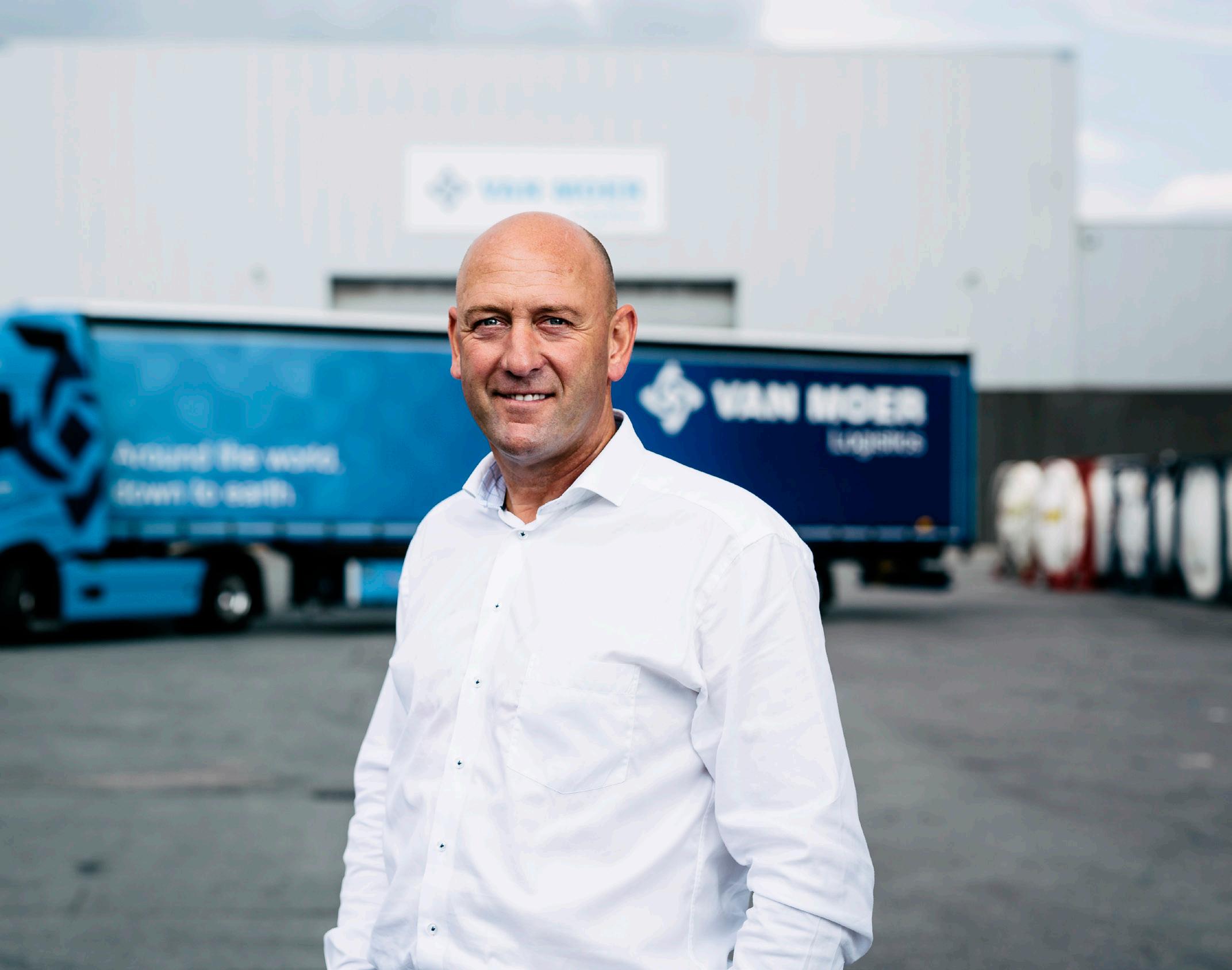




ACKNOWLEDGEMENT
2021 and 2022 were dedicated to sustainable growth. This growth must be supported. That’s why we were looking for a partner with the same long-term vision who could support our ambitious goals. We found it in Ackermans & van Haaren. AvH invested 12.5 million euros and thus acquired 21.74% of the shares of Van Moer Logistics
We have made significant investments in our Bulk & Tank Container Logistics division. We also developed new state-of-the-art sites and warehouses together with partners such as Van Wellen Group and Heylen Warehouses. We established ourselves in Germany through the acquisition of Holtstieger GmbH, just across the border. 2022 is also the year of consolidation for Bulk & Tank Container Logistics. Thanks to the acquisition of Group Van Loon, a fine company with partly identical activities, we can serve our customers on the left and right bank even better.
I am particularly pleased with a number of recognitions that our company received. One was the Green Truck Award, which honoured our broad vision on decarbonisation. We also passed the extensive SQAS audits on our sites with honours. And finally, according to the international sustainability rating agency Ecovadis, we are among the absolute top in Europe for our activities. We achieved three top scores in 2021 and 2022.
All these recognitions are entirely due to our employees, who work hard every day. They go the extra mile for our company, our customers and help achieving our ambitious sustainability goals every day. I am also grateful to our customers and partners who, for years, have been writing a story of sustainable growth with Ius.hope you enjoy reading this report.
Jo Van FounderMoer&CEO We ensure that our customers’ complex and circular supply chains can grow whilst reducing the impact on people and the environment.JoVanMoerFounder&CEO
4 GROWTHSUSTAINABLE
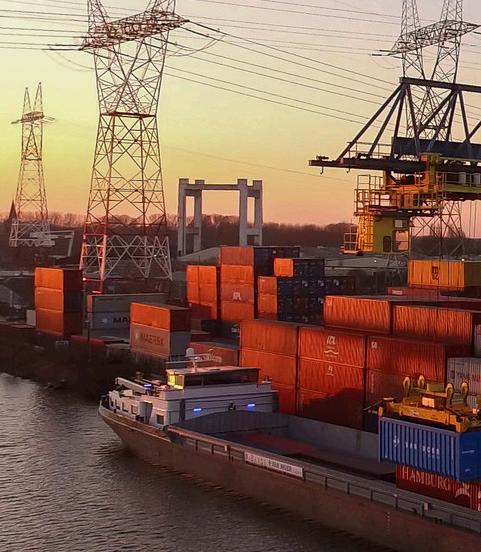
5 OUR GROWTH1990 START OF TRANSPORT 201320112008200419991993 First warehouse in Melsele First activities in the Port of Antwerp First cleaning of tank containers Move to head office in Zwijndrecht First inland terminal in Grimbergen First on-site logistics in Hoboken Start of activities in Ghent Start of inland waterway transport First waterborne port terminal Start of activities in Grobbendonk • Start of activities in Brussels • Start of activities in Germany (acquisition of Holtstieger) • Participation Ackermans & van Haaren Expansion of Bulk & Tank Container Logistics to right bank (acquisition of Group Van Loon) 202220212018201720162015 Van Moer Logistics
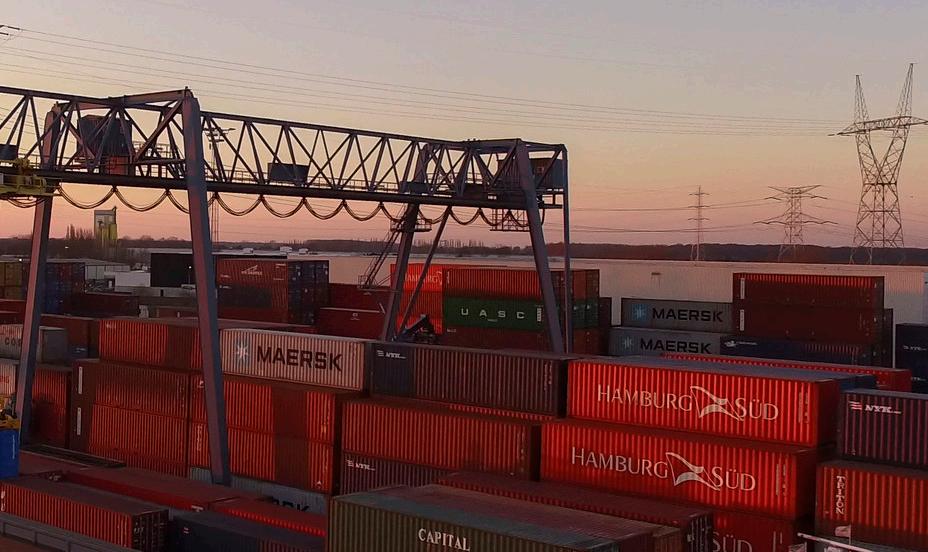
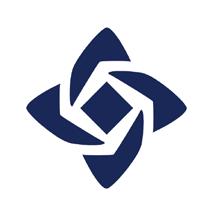
6 KEY FIGURES 2021 2020 2019 Turnover 222,378 186,396 173,430 Margin 46,399 42,870 42,124 Margin % 21.3% 23.6% 24.0% EBITDA 14,520 13,655 15,526 EBITDA % 6.5% 7.3% 9.0% EBIT 3,900 3,798 3,684 Financial expenditure 1,289 1,260 1,573 Extraordinary income 0 0 1,994 Result before tax 2,612 2,538 4,105 * Figures in millions of euros Business Unit Turnover incl. inter company turnover % Turnover excl. inter company turnover % Transport 105,378 41.3% 88,395 39.8% Warehousing 74,626 29.3% 67,901 30.5% Ports & Intermodal 33,882 13.3% 33,012 14.8% Chemicals 18,487 7.2% 18,309 8.2% Forwarding 11,709 4.6% 11,660 5.2% International 10,392 4.3% 2,749 1.2% Other 351 0.2% * Figures in millions of euros 4140 intercompanyIncl. turnover intercompanyExcl. turnover We are throughorganicallyprofitably,growingbothandacquisitions,andcontinuetomaintainastrongcapitalbase. AnnCools CFO 41% 30% 13% 7% 5% 4% 40% 31% 15% 8% 5% 1%
Van Moer Logistics 7
We have great respect for the entrepreneurship of Jo Van Moer and his team. We have noticed that their nononsense approach, characterised by flexibility and enthusiasm in a spirit of partnership, matches with the values of Ackermans & van Haaren. We look forward to supporting the further expansion of Van Moer. This is a unique opportunity for us to invest in sustainable transport and logistics and to strengthen our presence in the Port of Antwerp-Bruges.
TomBamelis CFO,vanAckermans&vanHaaren
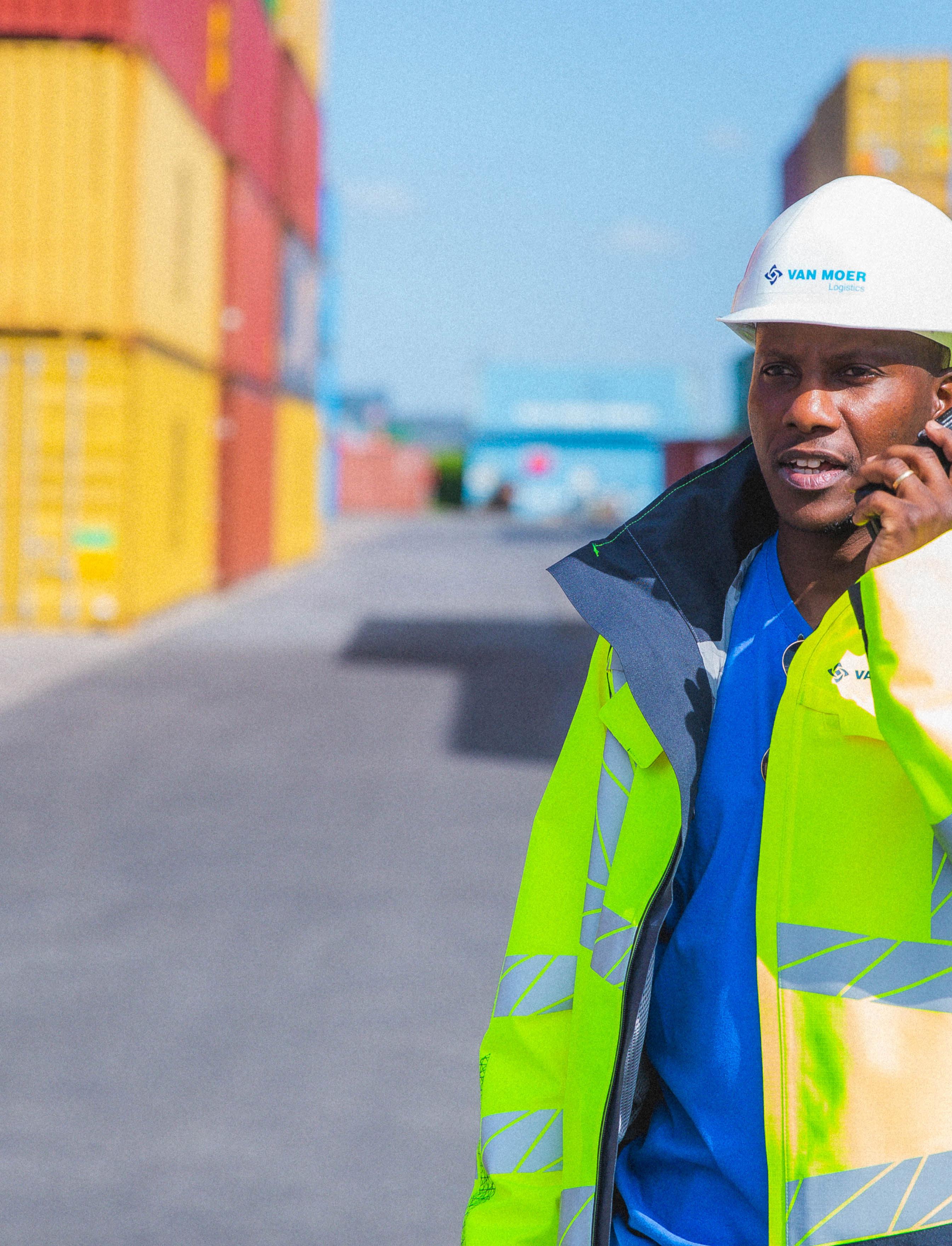
HIGHLIGHTS 2021 - 2022
GROUPACQUISITIONVANLOON
In May 2022, we completed the acquisition of tank container specialist Group Van Loon. Group Van Loon specialises in the transport, cleaning, repair and storage of tank containers on Antwerp’s left and right banks. It employs 130 people and achieved an annual turnover of 20 million euros in 2021. The acquisition fits in with our strategy to expand and strengthen our range of services for companies in the chemical sector. After adding the installations of Group Van Loon, we will do on average 300 cleanings and 275 repairs per day. In recent years, we have invested in the renewal and expansion of our SEVESO site in Zwijndrecht. With the arrival of the new drumming and ADR halls, we further expand our services for the chemical sector. Thanks to the acquisition of Group Van Loon, we are now also doubling our capacity in bulk and tank container logistics. Besides the large capacity, Van Moer Logistics also offers a unique one-stop shop service. The transport, storage, heating, filling, cleaning, checking and repair of the tank containers are done at the same location in Zwijndrecht. These optimisations save our customers a lot of transport costs and tunnel toll charges. The optimisation of these transports also brings significant environmental benefits. It is our ambition to offer the same compre hensive, all-inclusive service on the right bank in the near future, so that our customers can benefit from the one-stop shop principle on both banks of the port of Antwerp.
The family shareholders see Van Moer Logistics as a reliable partner that also has the necessary credibility and resources to continue our work. Additional growth possibilities and opportunities are now created for our employees as well. We have paid a lot of attention to the ‘cultural match’. Van Moer Logistics shares the same values and adheres great importance to a flat organisational structure, an open culture, flexibility and long term relations with all stakeholders.
8
GüntherVanLoon CEO,GroupVanLoon
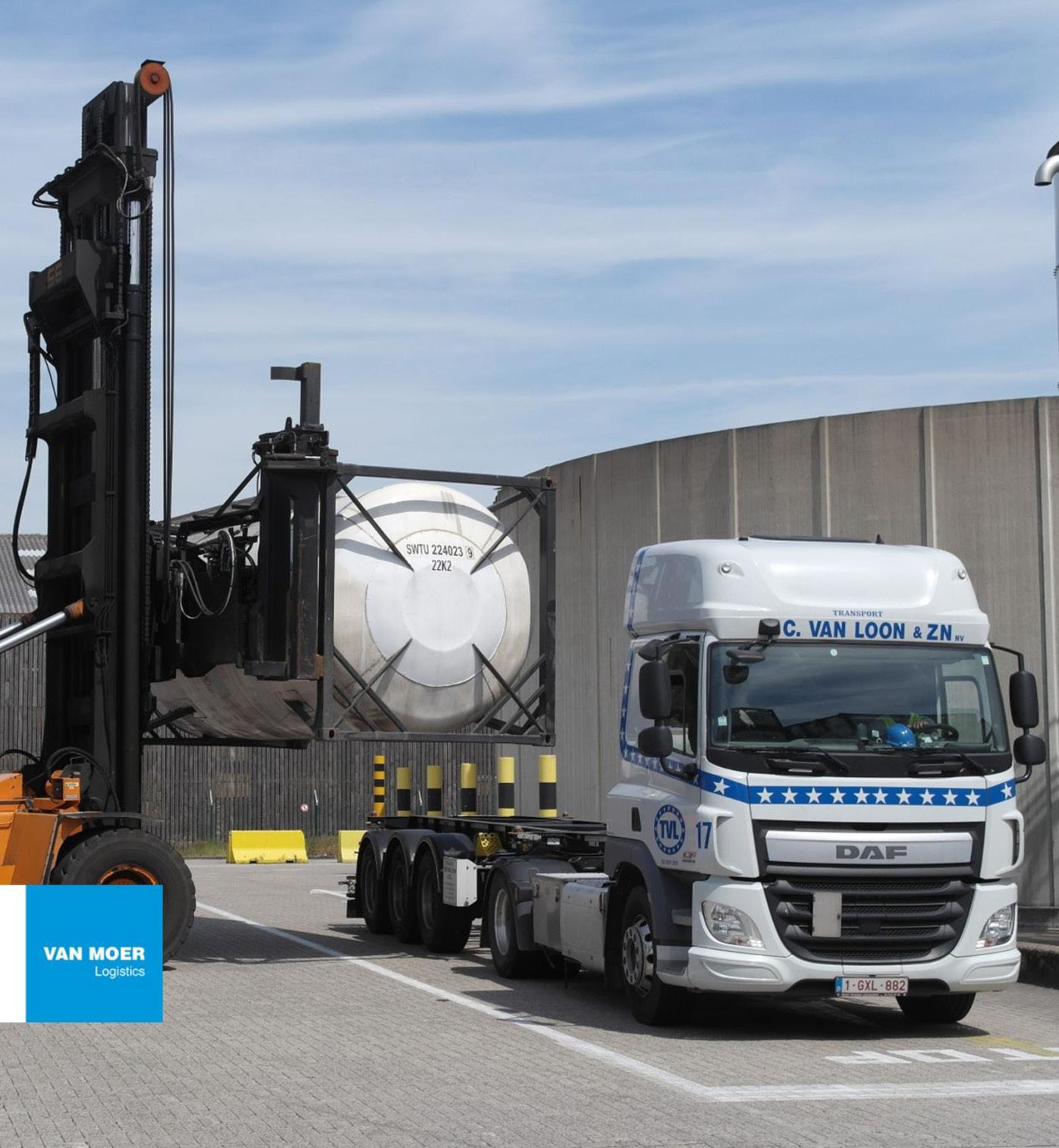
Van Moer Logistics 9
As a result of the acquisition of Spedition Holtstieger in Nettetal (just over the border in Germany near Venlo) we now have a good operating base for further internationalisation. We are thus strengthening our position in what is referred to as the “logistics banana” (Antwerp, Ruhrgebiet, Köln, Mannheim and further south). We now have 110 drivers and almost 80 trucks in Germany.
SPEDITIONACQUISITIONHOLTSTIEGER
DENNIE CONTAINERLOCKEFEERTERMINAL
On the Antwerp East Port site of Heylen Warehouses in Grobbendonk, the first pile of the new logistics development for Van Moer Logistics was drilled in the first week of May 2022. The new distribution and storage warehouse has a surface area of 23,000 m². The seed for this development on the site, which also goes by the name of Antwerp East Port, was sown twelve years ago with the idea of a few entrepreneurs to develop an eastern satellite of the port of Antwerp. Their aim was to strengthen the economic network of the Albert Canal and to keep as many trucks off the road as possible. An inland container terminal was developed, surrounded by a sustainable water-bound logistics business park of approximately forty hectares. The project is led by Van Moer Logistics and Heylen Warehouses and will be supported by De Vlaamse Waterweg. The new distribution and storage warehouse for Van Moer, with a total surface area of 23,000 m², will be equipped with the Building Technologies Platform of Heylen Warehouses, which will allow the capture of some 500 to 600 digital data points from the building and its installations. The building will be completed and ready for use in the first quarter of 2023.

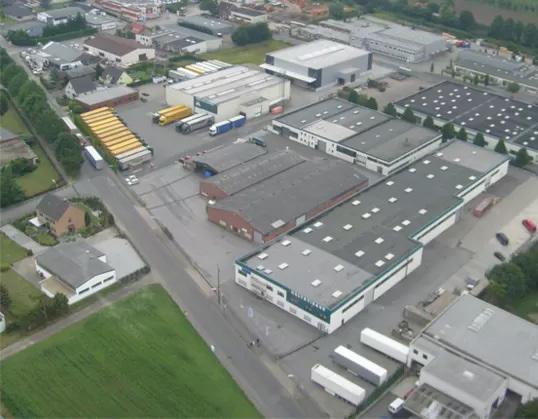
10 1. TRANSPORT & DISTRIBUTION 2. WAREHOUSING & VALUE-ADDED LOGISTICS We offer our customers a whole range of transport solutions and take responsibility for their supply chain. Our planning is optimally aligned with their processes and we can offer drop & swap integrations. We like to think outof-the-box and develop customized services. We offer: • Trailer transport • Container & reefer transport • Tank container transport • Building material transport • Exceptional transport • Transport for retail 24/7 • Breakbulk transport (coils/tubes...) • Class 1 transport • Tipper chassis transport • Silo trailer • Waste transport (national and internatio nal) Ad hoc transports, transportation of damaged equipment from terminal to the quay and to our sites in the port of Antwerp, so that the ne cessary actions can be planned and executed. We specialize in the storage and handling of various commodities. We offer storage for both palletized and bulk goods. Justin-time, full service for your inbound and outbound logistics? Repackaging? Heavy machinery and cargo? We take care of it. We have warehouses at various locations, each specialized in a number of goods flows. Dangerous and/or very valuable products? No problem at all. We are well equipped for it. At several customers, we work next to the production site and the transport from production to storage is automated. We offer: • Indoor & outdoor storage • Temperature-controlled storage • Transfer • Bagging, bulking, compacting, drumming, blending and repackaging • Project cargo • On-site empty container depot • Tailored value-added operations • Consolidation and stripping (split) • Order picking (pallet picking & detail picking) trucks in total* diesel dual-fueltruckstruck (H2) LNG *datadriverscharterstrucksofJune22, 2022 100+435477141577 railway connection (Antwerpen and Brussels) containers per month containers (140.000 TEU) handled in total m2 warehouses in Belgium tons of goods handled 7.5 km 2,000,000580,00080,0006,500 OUR ACTIVITIES
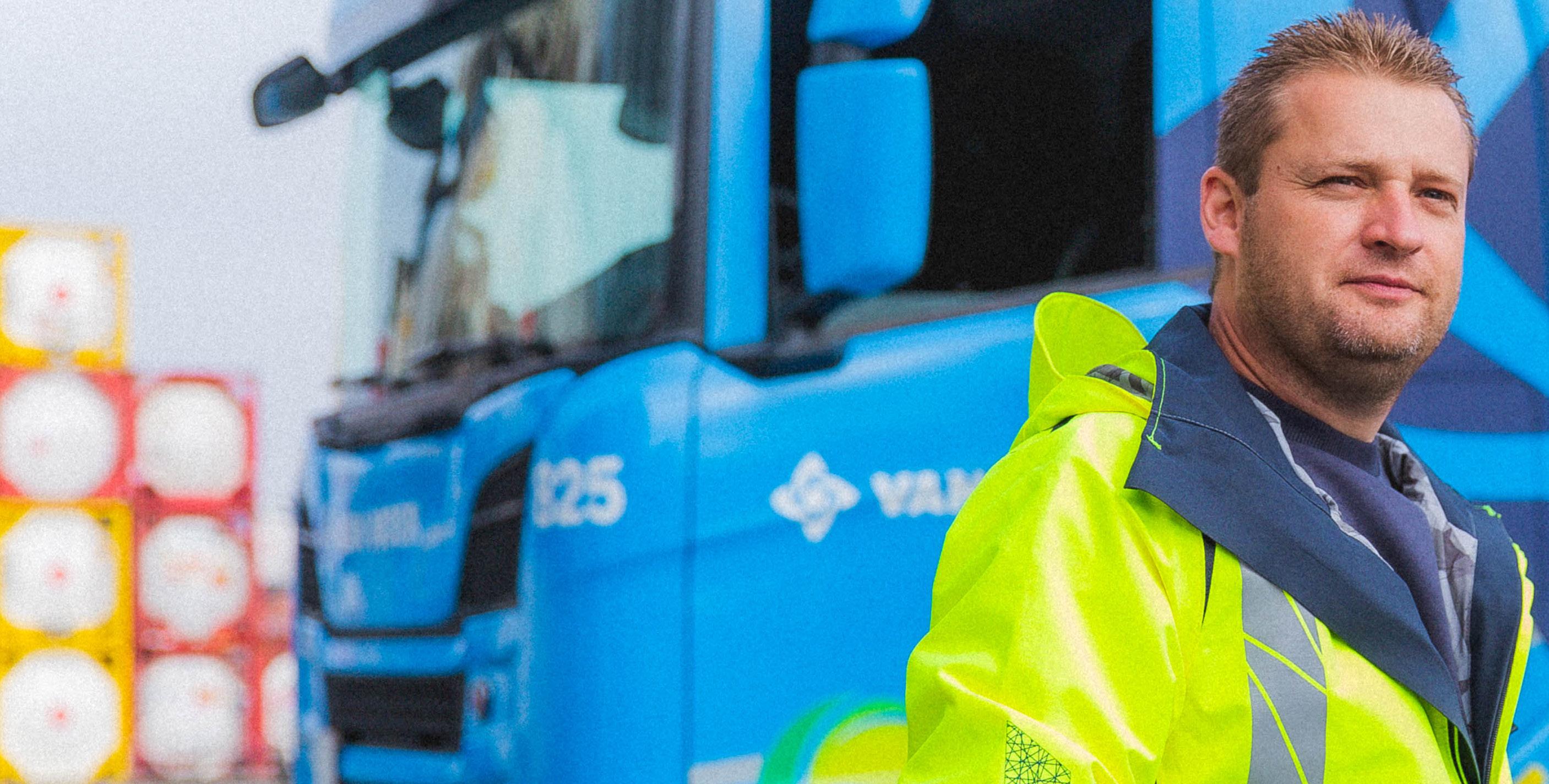

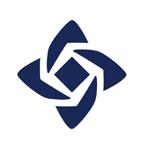
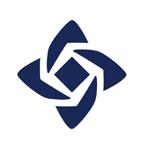
Van Moer Logistics 11 Thanks to our scale and the management of several terminals in strategic locations we can organise multimodal transport with numerous additional services in a cost-effective manner. We offer: • Inland waterway transport • Waterborne port operations • Waterborne inland operations • On-site depot of empty containers • Repair of empty containers • Stuffing and stripping • Fumigation • First & last mile • Inland container terminal operations • Extended gate - Tri-modal solutions - 3PL We offer a depot with integrated services for bulk and container logistics. Everything is efficiently organised on several sites on the left and right banks and tailored to our customers’ various flows of goods. We offer: • Storage / warehousing of empty dirty, cleaned and loaded tanks, ADR & Non Haz • Drumming • Heating up and cooling down / chilling of tank containers and packaged goods • Resin and latex circulation • Repairs / modifications and adaptations of all possible IMO tanks • Cleaning of tank containers and bulk carriers • Nitrogen Dewpoint, PPM, blankets and cleaning of nitrogen in IMO tanks, roadbarrels etc. • Isocyanates (MDI & TDI) cleaning • Liner and flexi bag installations • Transfer of Cryogenics,liquidslining and gas tanks, degassing and recovery Cleaning of chemical tanks ADR, Non Haz, Food, Feed, Halal, Kosher - VAS + Product transfers: tank to tank, from IBC / drum or other possible containers to a tank or vice versa • Heating of barrels, IBC etc. via our hotboxcontainer repairers (including maintenance) tank cleaners flexible heating places (steam, hot water, elec.) TEU storage capacity: 2,750 loaded and 6,250 empty m2 site200,0009,0001402280 TEUbargesvesselsbarge capacity (vessels + terminalreachmobilegantrytransshipmentbarges)terminalscranesharbourcranesstackerstractors3,312898352440 3. PORT & INTERMODAL LOGISTICS 4. BULK & TANK CONTAINER LOGISTICS
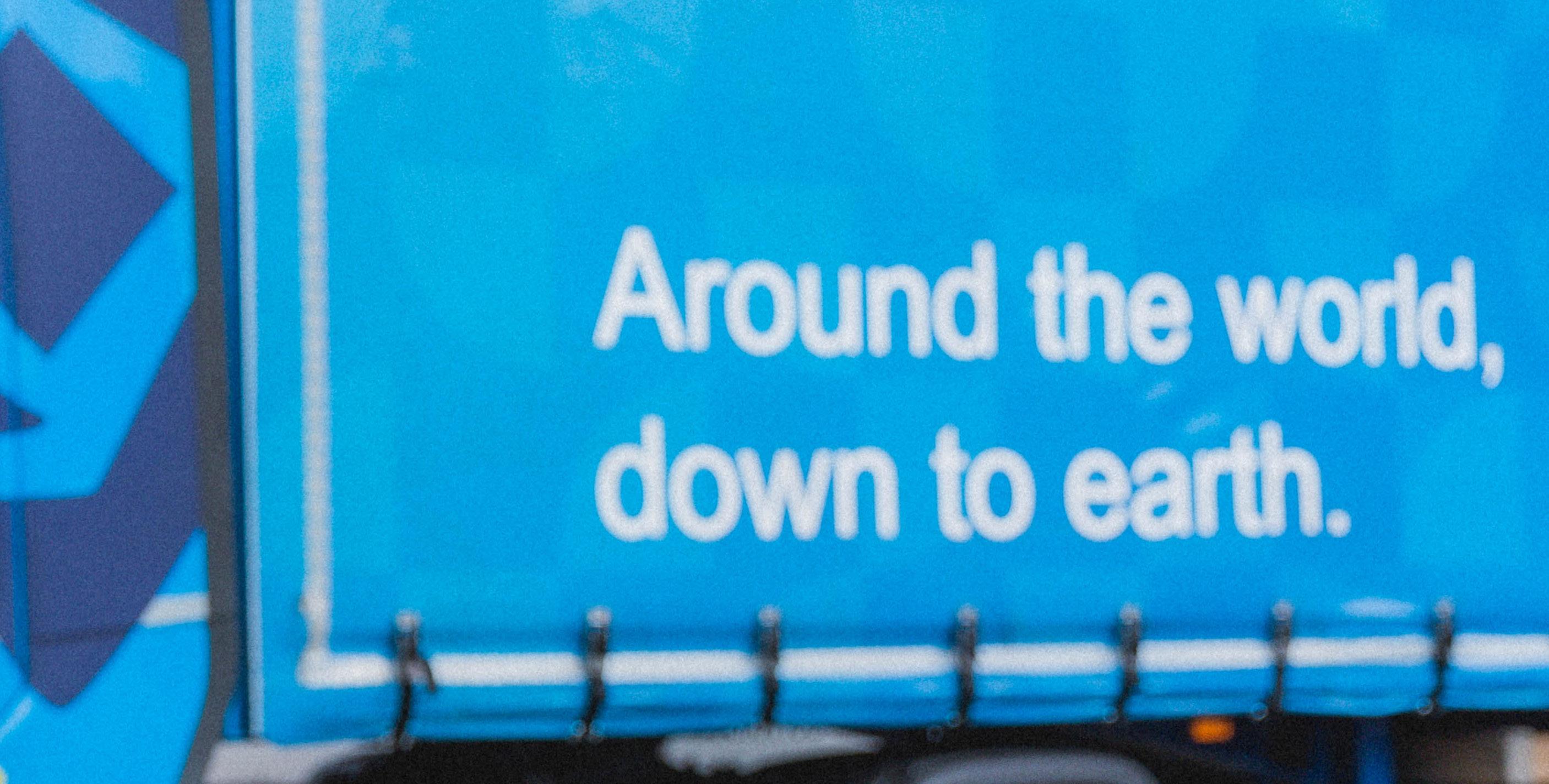

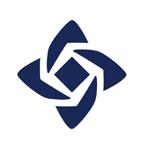
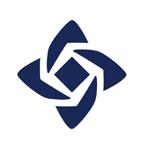
12 Our support teams are at the customer’s disposal with all their expertise in: Forwarding: We find the right customized solutions for shipping, storage and distribution of cargo. Customs: We take care of the legal formalities, arrange inspections, declarations and transits and take care of your administration. On-site logistics: We offer customized solutions to optimize your operations on your site and integrate production, transport and/or distribution. ICT and automatisation: ICT is a business enabler for us. We design or integrate systems to control and analyze your logistics perfectly. Technical advice, engineering and opportunities towards our partners. 5. SUPPORT SERVICES We are a one-stop shop for all logistics challenges. We are strong in thinking and acting in terms of solutions for our customers. New customer requests motivate us to offer customised Carlsolutions.Ghekiere CCO
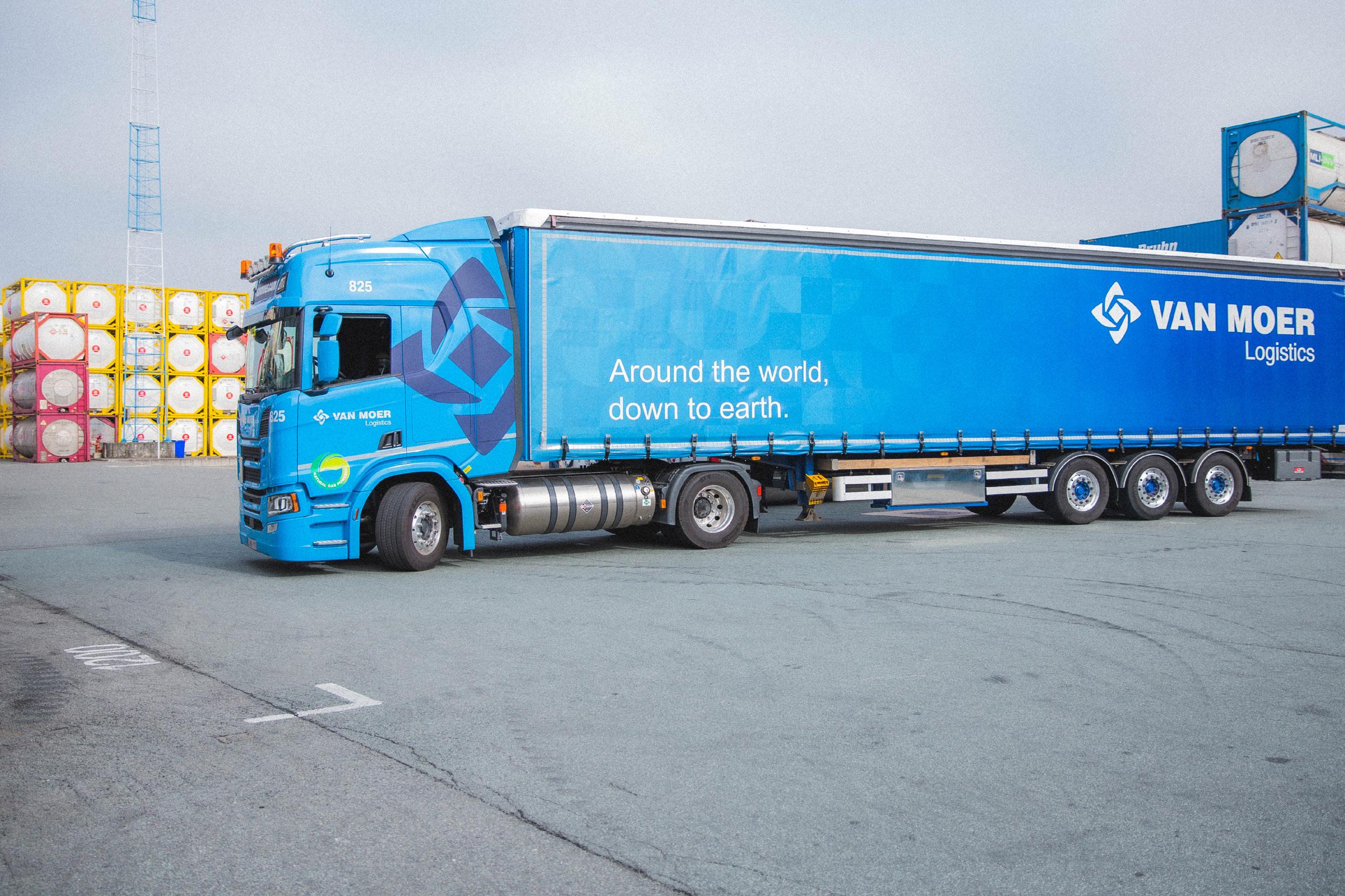






Carl Ghekiere CCO Ann Cools CFO Joris Emanuel IT Director Iwan De Block COO Bulk & Tank Container Logistics
Bert Calluy Legal Counsel Eric Noterman COO Port & Intermodal Logistics
The Board of Directors is the highest governing body. It leads the company and develops its strategic policy. This includes determining a mission and implementing a strategic vision.
GOVERNANCE In terms of governance, we distinguish three major consultative bodies, each with a different task and meeting frequency:
13
In the management committee, the operational results are discussed and an explanation is given by the Q department, the ESH department, the HR department, the Finance department and the Sales department regarding current and/or upcoming projects. The management committee meets quarterly. It consists of the members of the Executive Committee and middle management.
Yves Hebb HR Director
The Board of Directors meets four times a year but can meet more often depending on current projects and/or opportunities. It is composed of Jo Van Moer, Anne Verstraeten, Luc Van Milders, Bernard Moyson and Ann Cools.
The Executive Committee converts the strategic direction into operational objectives and monitors progress. It meets every two weeks. The executive Committee consists of the Founders, the CEO, the CCO, the Legal Counsel, the HR Director, the CFO, the IT Manager, the COO Warehousing & Valueadded Logistics and the COO Bulk & Tank Container Logistics.
Jo Van Moer Founder & CEO Anne Verstraeten Founder Steven Pauwels COO Warehousing & Value-added Logistics
EXECUTIVE COMMITTEE
Van Moer Logistics
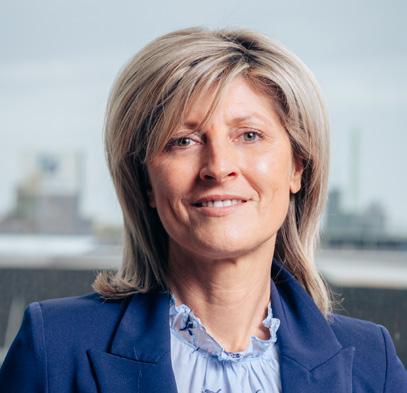
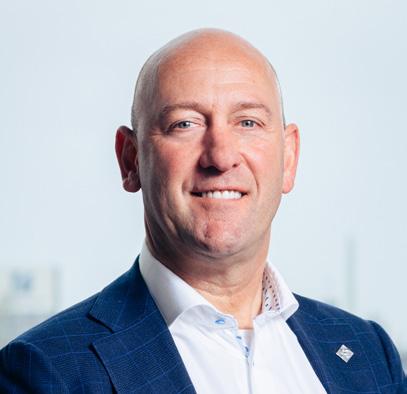
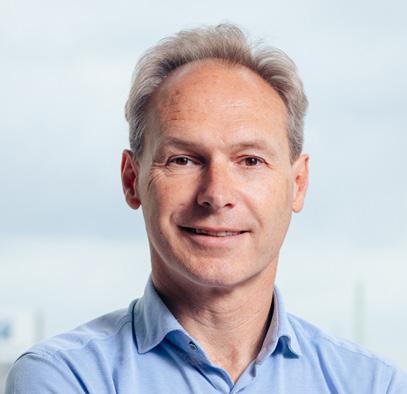
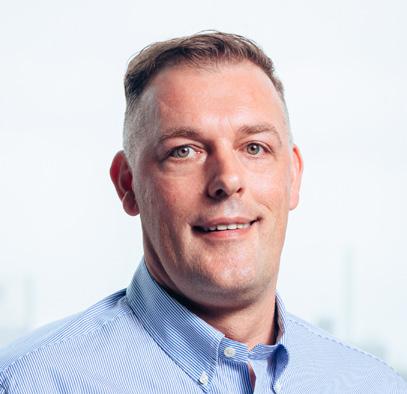

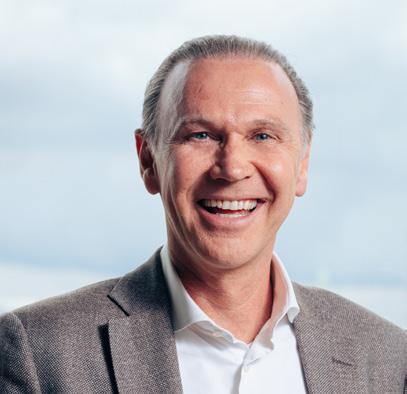
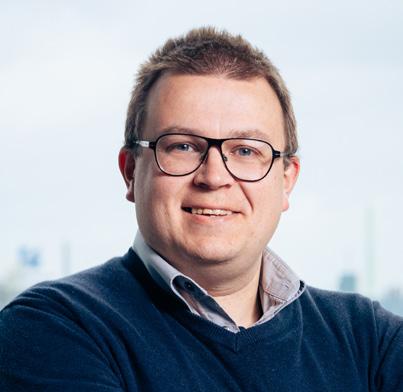
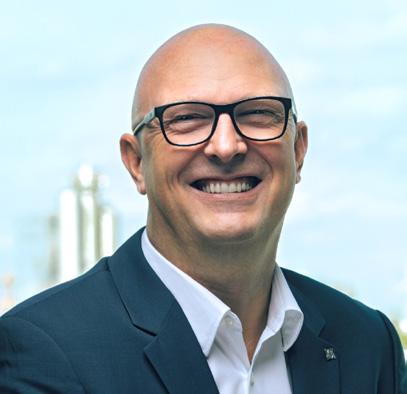
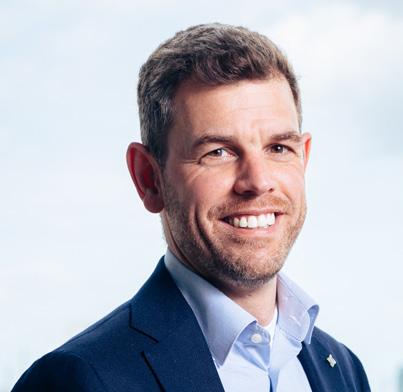
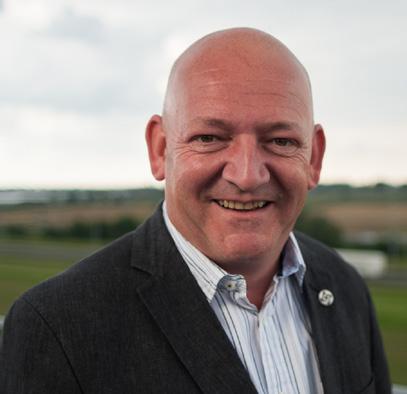
Van Geijt Expert in Forwarding Wim Vandeweghe Expert in Sales Support & Pricing OUR EXPERTS
14
Andy
Bogaerts Expert in Port & Intermodal Logistics Frederick Vermeersch Expert in Transport & Warehousing Ilse Verdonck Expert in ImplementationBusiness
Van Kemseke Expert in Transport & Warehousing Alexander Volders Expert in Transport & Warehousing Werner Cooreman Expert in Transport & Warehousing Anthony De Smet Expert in Value-added Logistics Luc Mertens Expert in Value-added Logistics Maxim Letange Expert in Bulk & Tank Container Logistics
Peggy
Ellen
Wouters Expert in Transport & Warehousing
Frank
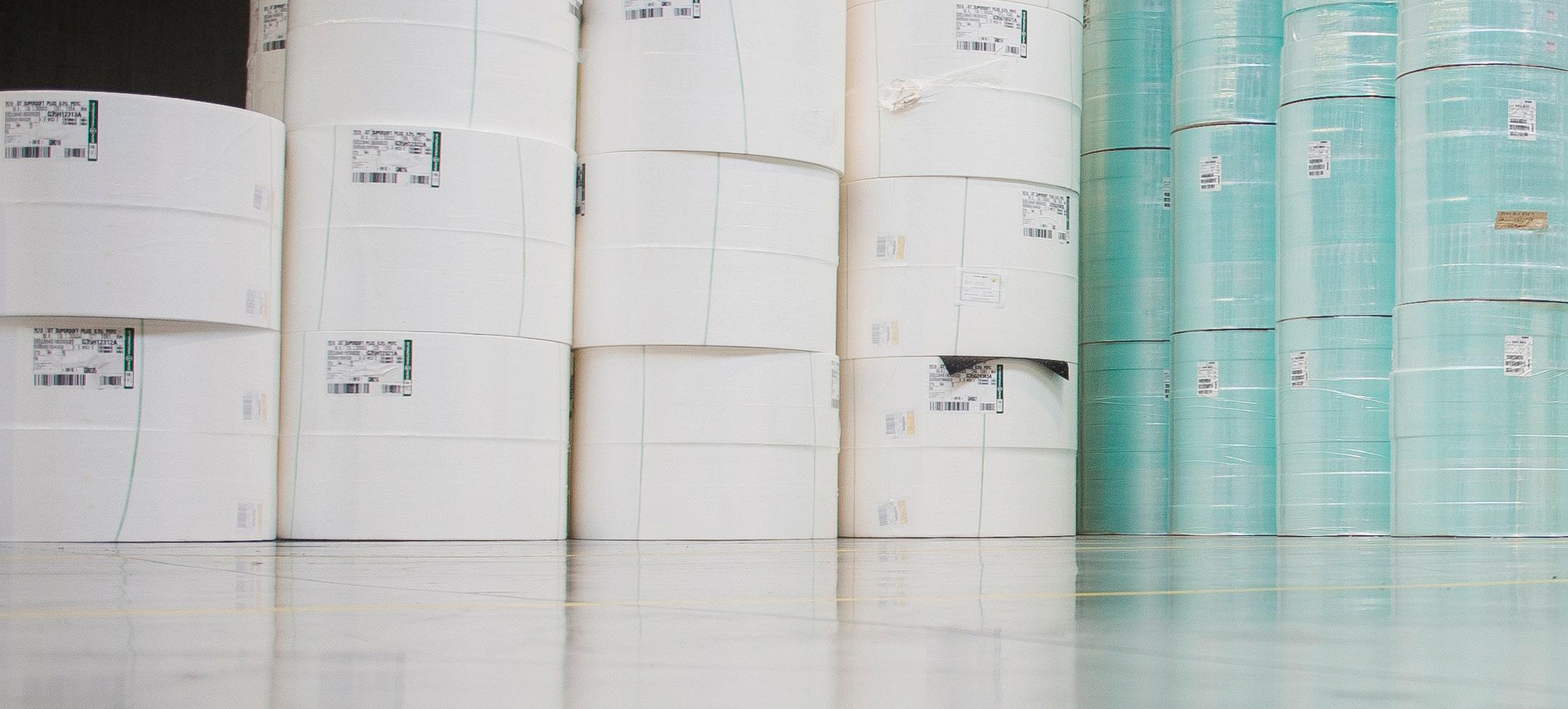
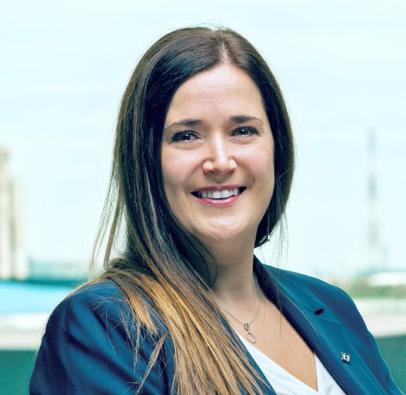
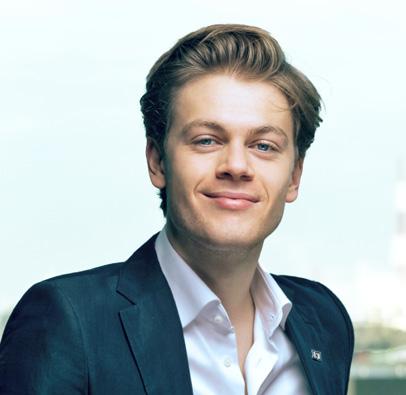
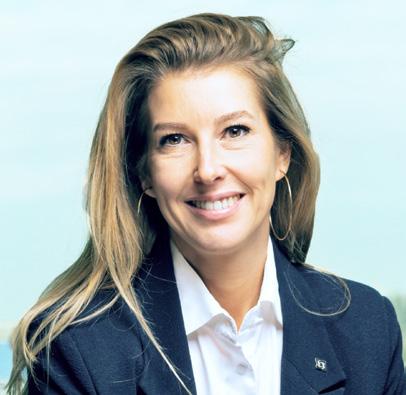
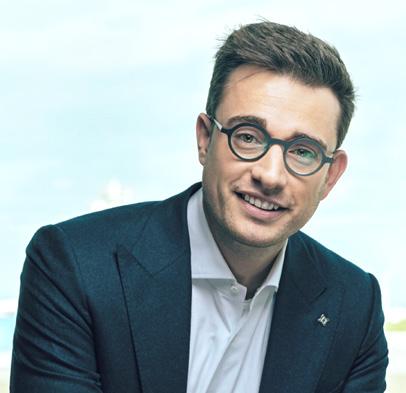
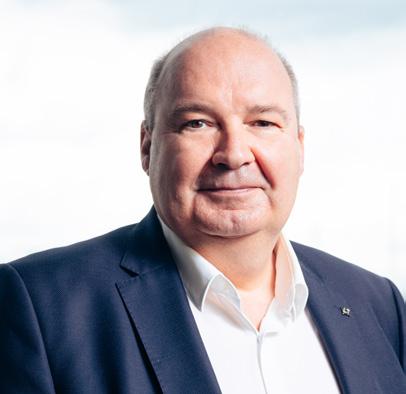
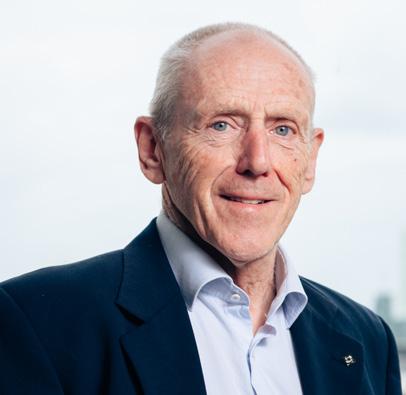

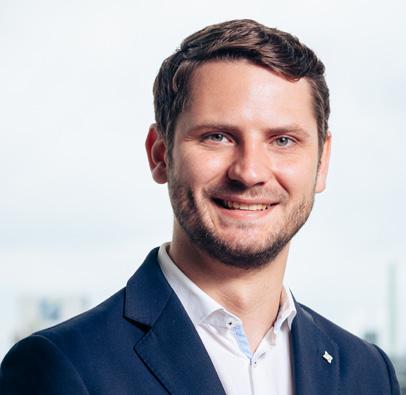
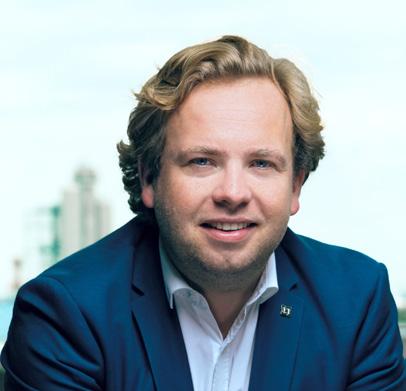
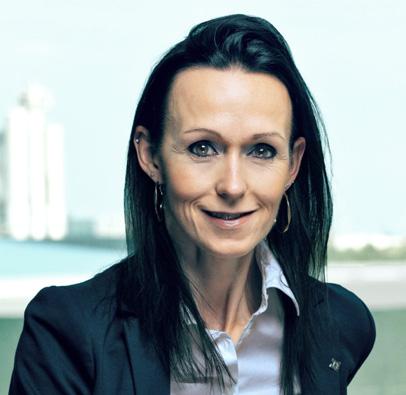

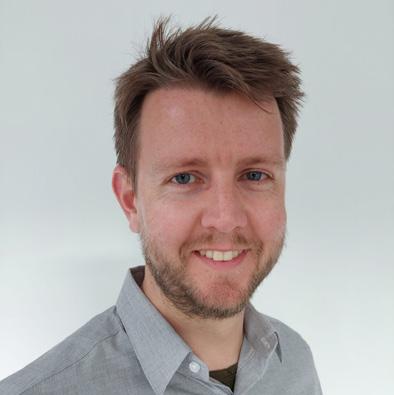
Van Moer Logistics 15 ISO 45001 (safety management) ISO 9001 (quality management) ISO 14001 (environmental management) Ecovadis (environmental and sustainability -audit)Van Moer Cleaning & Repair (73 = gold) Van Moer Transport (64 = silver) Van Moer Stevedoring (66 = gold) AEO (customs) FCA | BIO | NOP | FSSC 22000 | EFTCO FOOD (food products) Excipact | GDP (pharma) SQAS Warehouse | SQAS Tank Cleaning | SQAS Transport (QESSH) CERTIFICATES GOLD MEDALS In 2021, we developed an ambitious sus tainability strategy in cooperation with the specialist consulting firm Sustacon. This strategy has now been awarded. Three business units won a medal. The highest score was for Van Moer Cleaning & Repair, which offers services for bulk and tank container logistics. With a 73% rating, the department recieved gold and is among the top 1% in the sector. The Port & Intermodal Logistics unit, for its part, achieved a score of 66%, also good for gold and among the 3% best companies in the sector. Finally, the transport unit secured a silver medal with a score of 64%. Ecovadis is an ESG (Environmental Social Governance) benchmark that enables companies to assess their sustainability performance. In an Ecovadis assessment, companies are judged on the basis of five pillars: • General policies • Labour & Human Rights • Ethics • Environment • Procurement Van Moer Logistics has the following certifi cates or meets the relevant standard: Our sustainable strategy andtangibledeliversresultsisalsomuchappreciatedinthemarket. HansVerboven ExpertinSustainability
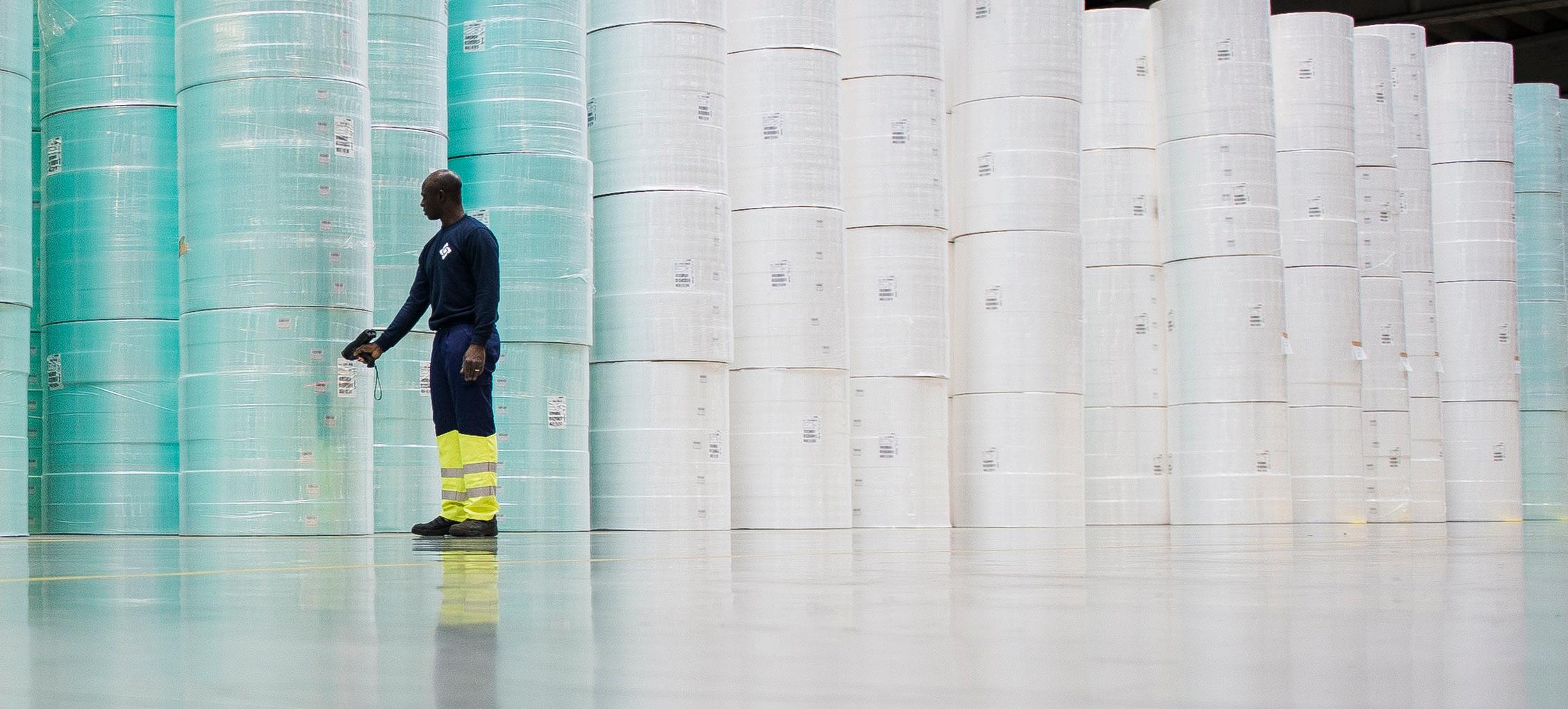






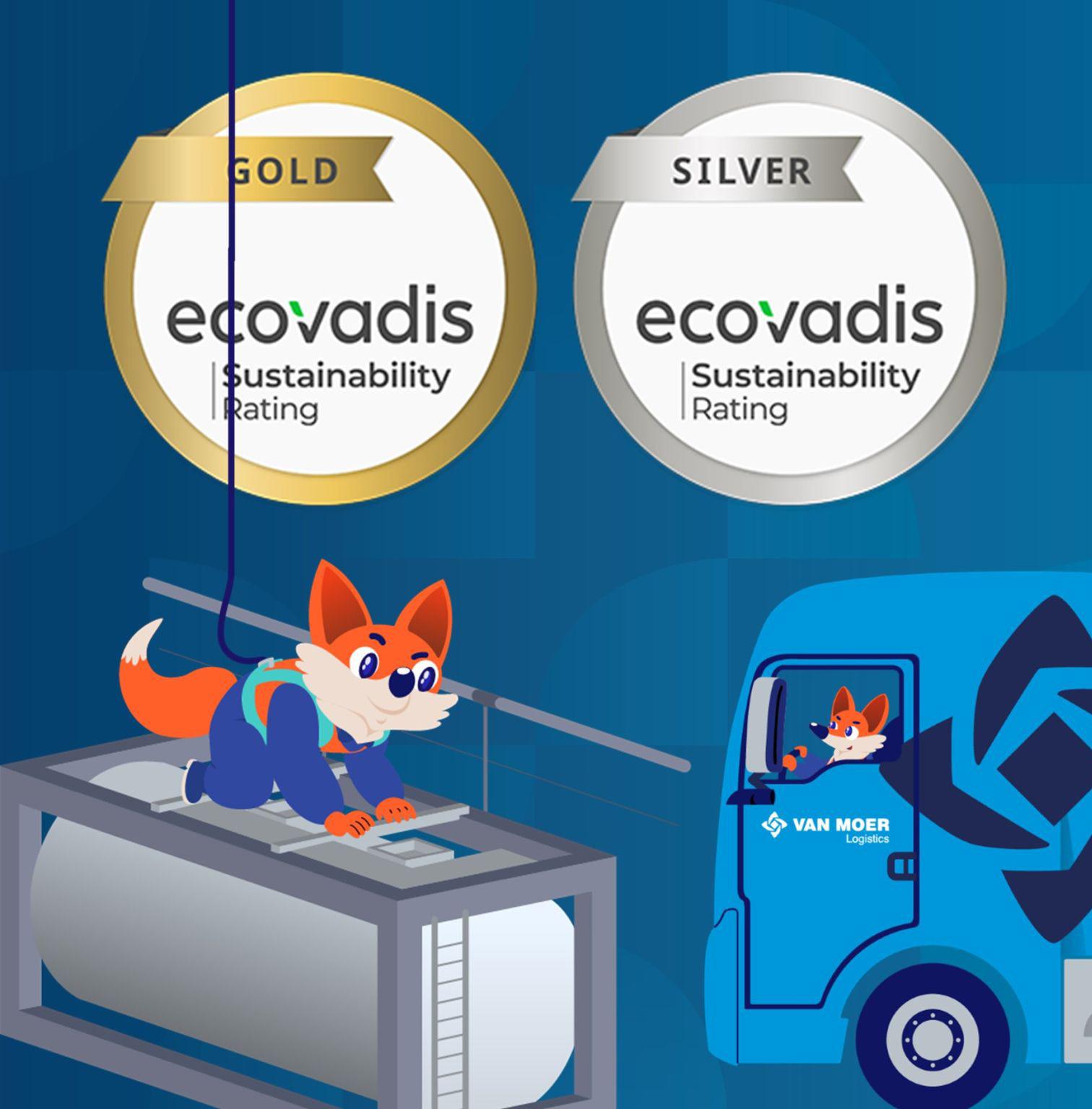
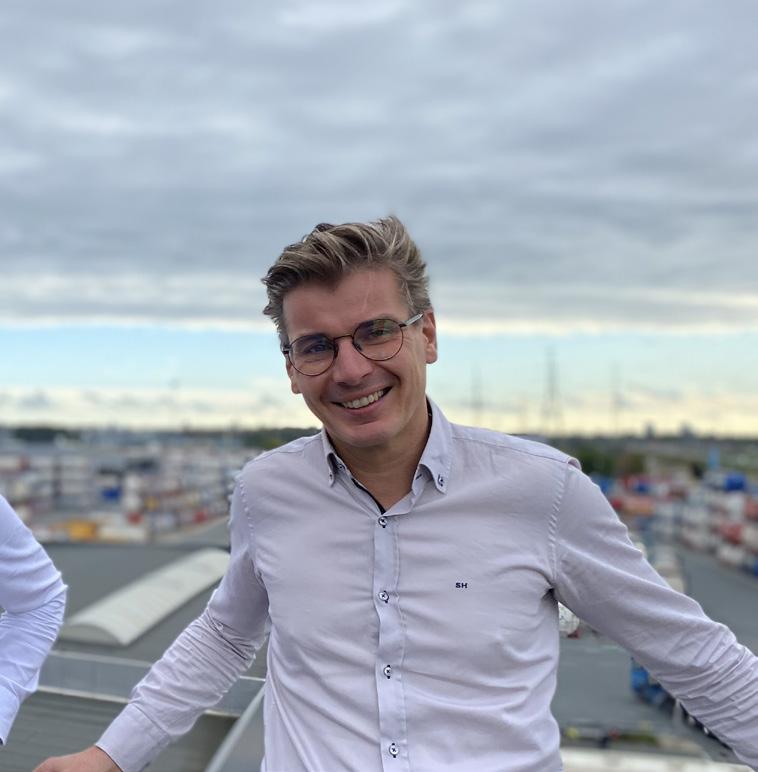
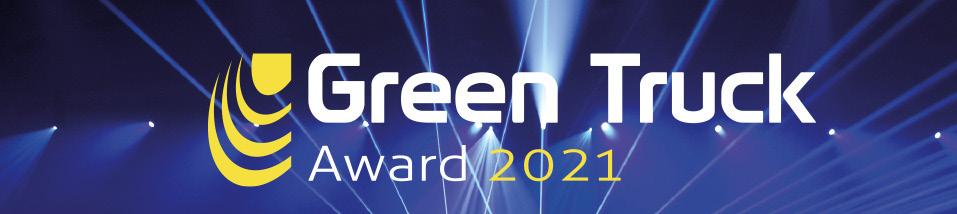
The logistics sector and road traffic in general account for almost a quarter of the green house gases in the European Union, offering a great opportunity for improvement. Almost 75% of all goods in our country are transported by road. By 2030, the need for transport will increase by another 25%. It is unfeasible to transport all of that by road. Our customers also know these challenges. They are increasingly confronted with the constraints of mobility, noise pollution, environmental impacts and the challenges of circular models. They too need to reduce the carbon footprint of their operations while ensuring that goods find their way to users quickly and efficiently. We are there to help within the context of an increasingly complex supply chain and the stricter regulations. We will not achieve much on our own, but through cooperation and partnerships we will get there. We help our customers in the port, in chemistry, in food and many other sectors to carry out their activities efficiently and sustainably. We organise ourselves intermodally, so that we can be the “one-stop shop” for our customers. We realize a positive impact by organising transportation and logistics sustainably for our customers while trying to reduce the environmental impact of our processes. We want to be part of the solution, not the problem. This is how we are preparing for the Green Deal.
16
GREEN DEAL AND THE EU TAXONOMY: WE ARE READY
The Green Deal is the European growth strategy to make the EU a modern, resource-efficient and competitive economy. The European Green Deal aims to drastically reduce CO2 and other greenhouse gas emissions from transport by up to 90% by 2050.
TOGETHER WITH OUR CUSTOMERS AND PARTNERS
The EU taxonomy is a classification system that provides a list of environmentally sustainable economic activities. The classification aims to give investors a reliable compass for making sustainable choices. It also aims to help companies to become more climatefriendly, to reduce market fragmentation and to shift investments to where they are most needed. The taxonomy regulation sets six environmental objectives. Climate change mitigation Adaptation to climate change Sustainable use and protection of water and marine resources The transition to a circular economy Pollution prevention and control Protecting & restoring biodiversity and ecosystems All these frameworks are an opportunity for us, rather than a risk, if we anticipate them now.
THE WORLD IS CHANGING







17 Our Van Moer “blue solutions” are: Working on innovative multimodal transport solutions that unburden Workingcustomerson intelligent systems that optimize routes, loading rates and transport times in a multimodal mix Investing in eco-efficient means of transport and hydrogen technology Monitoring the balance between economic, social and environmental Enforcingcosts safety by working on behaviour, monitoring and technology Building large-scale multimodal infrastructure and efficient warehouse locations 20% Targets for CO2 reduction Compared to 1990 levels 20% Targets for renewable energy % renewable energy 20% Targets for energy efficiency % improvement EU CLIMATE AND ENERGY PLANS UNTIL 2020 32.5%32%55% EU CLIMATE AND ENERGY PLANS UNTIL 2030 EU CLIMATE AND ENERGY PLANS UNTIL EUROPECLIMATE-NEUTRAL2050 We think along with our customers and relieve them of the burden of the increasingly complex supply chain and stricter regulations. AnneVerstraeten Founder Van Moer Logistics
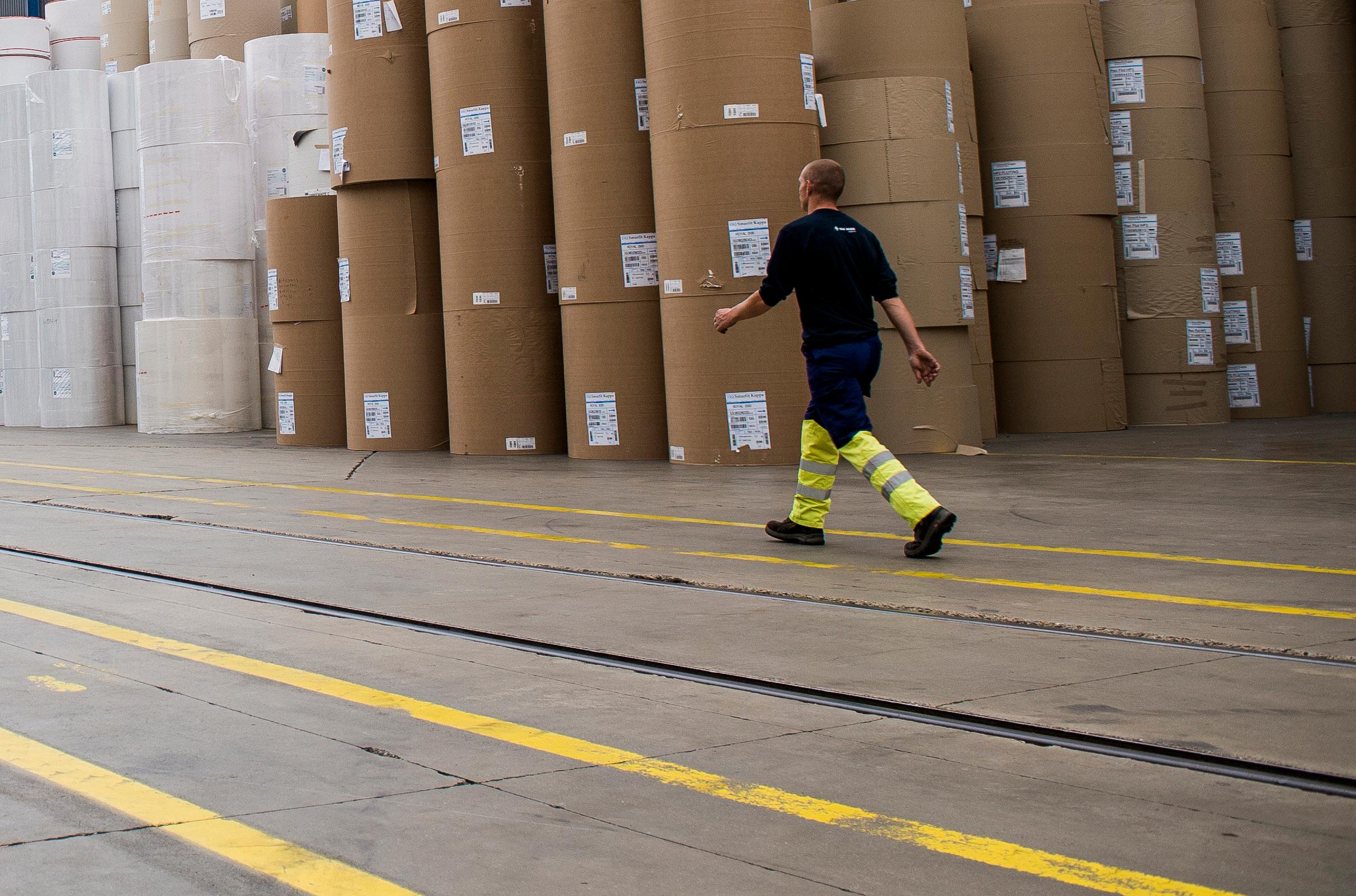






18 MATERIALITY In 2022, we conducted an analysis to identify material ESG topics. Based on input from interactions with customers, employees, banks and investors, civil society organisations and academia, we arrived at a comprehensive list of topics. We have reduced this list to 40. In order to structure it, we assigned the topics to the three ESG pillars. However, it was necessary to add a fourth pillar for the more general topics of an economic nature. This also fits our vision that the sustainability strategy should support the general strategy of the company. The pillars are therefore as follows: • Environmental • Social • Governance • WithinEconomicthesepillars, we have clustered the 40 topics into 10 themes. This is partly a subjective choice, but this way, it is easier to form an overview.
The table on the following page shows the 10 themes and also indicates which topics they cover. In addition, the table makes the connection with our own strategic pillars and themes around which we work and the SDGs. The three figures show how management assesses the ESG subjects. The y-axis shows the impact of the ESG subjects on business operations. The x-axis shows the current extent to which we are prepared for them on the basis of our strategy. The ESG issues in the yellow, orange and red zones are the most dangerous because the control mechanisms may not yet be developed strongly enough.
THEONIMPACT OPERATIONS MediumHigh105 quadrant I quadrant II quadrant IVquadrant III RISK DUE TO INSUFFICIENT MANAGEMENT MECHANISM OR LACK OF STRATEGIC RESPONSE Medium 5 3 0 low 7 9 High 10 4117 510 8 6 2 1 3 ENVIRONMENTAL
The topics within the 10 ESG themes can therefore have an impact on our business operations and long-term strategy. It makes sense to at least monitor them or, even better, to take mitigating measures. For some of the topics we can even have a positive effect through our way of doing business.
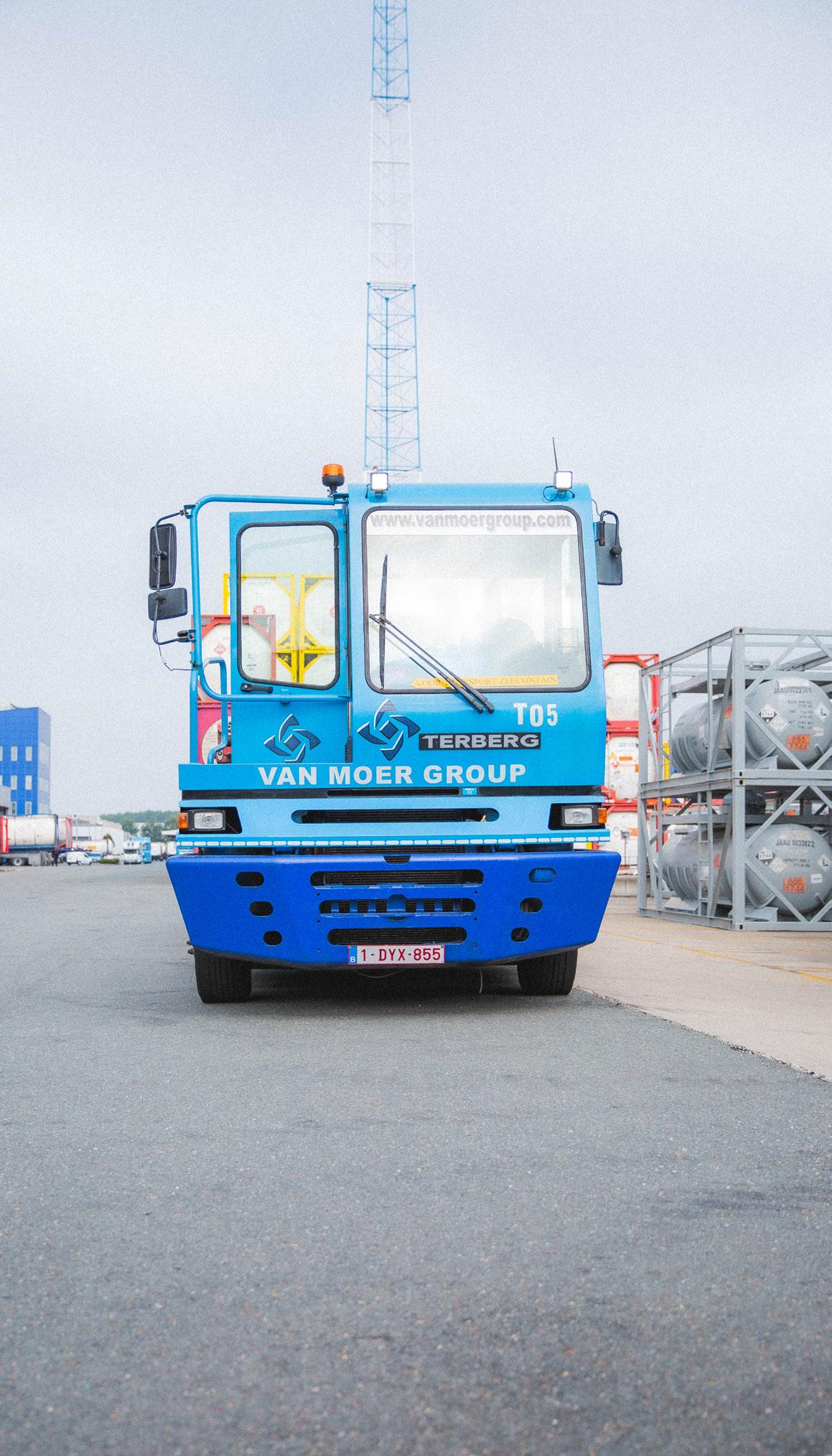
Van Moer Logistics 19 Theme Subject Link with our strategy (see p.20) ENVIRONMENTAL Climate 1. Extreme weather conditions 2. Climate change 3. Building limitations and lack of greenfields for warehousing 4. Environmental impact of mobility 1.3/ - 2.1 - 2.2 1.1/ - 1.3 Pollution 5. Soil pollution 6. Water pollution 7. Hazardous products 8. Waste 9. CO2 emissions 2.12.32.32.32.3 - 2.2 Decarbonisation 10. Renewable energy 11. Decarbonisation fleet 1.3 - 2.1 - 2.2 1.3 - 2.2 SOCIAL Human Capital 12. War for talent / drivers / hands 13. Quality of employment 14. Inclusion and diversity 15. Training and education 16. Safety and well-being 3.2 3.3 3.4 3.5 4.1 4.2 3.3 3.5 3.13.3 Social responsibility 17. Impact logistics sector on mobility 18. Nuisance such as noise, emissions, traffic 19. Stimulating (academic) research 20. Philanthropy 2.31.1 4.2 4.2 GOVERNANCE Good governance and business ethics 21. Expansion of group structure 22. Corporate values 23. Cybersecurity 24. Social dialogue 25. Reputation 26. Risk management / 4.1 // 4.1 4.2 / Anticipation of new regulation 27. Stricter energy and sustainability requirements from customers 28. European regulations on sustainability 29. Transparancy about current sustainability policy and strategy 1.1 - 1.2 - 1.3 - 2.1 - 2.2 - 2.3 1.2 - 1.3 - 2.1 - 2.2 - 2.3 1.2 - 1.3 - 2.1 - 2.2 - 2.3 ECONOMY Operational excellence 30. Operational efficiency 31. Planning risks 32. Quality risks 33. Synergies between departments 2.4 2.5 2.4 2.5 2.4 2.5 / Sustainable growth 34. Multimodal solutions 35. M&A policy /1.1 Economic risks 36. Economic recession 37. Geopolitical tensions and conflicts 38. Disruption of logistics chain 39. Congestion of the road network 40. Price increases /1.1/// THEONIMPACT OPERATIONS High10 12 Medium5 quadrant I quadrant II quadrant IVquadrant III RISK DUE TO INSUFFICIENT MANAGEMENT MECHANISM OR LACK OF STRATEGIC RESPONSE Medium 5 3 0 low 7 191314 20 15 171618 High 10 SOCIAL THEONIMPACT OPERATIONS High10 28 Medium5 quadrant I quadrant II quadrant IVquadrant III RISK DUE TO INSUFFICIENT MANAGEMENT MECHANISM OR LACK OF STRATEGIC RESPONSE Medium 5 3 0 low 7 High 10 232624212729 2225 GOVERNANCE
SUSTAINABLE STRATEGY Our business strategy makes a contributionpositivetotherealisationofthe JoSDGs.VanMoer Founder&CEO 1 SOLUTIONSINTERMODAL • Increasing multimodal traffic • Circularity • Green logistics 2 SUSTAINABLE AND EFFICIENT OPERATIONS • Measure CO2 footprint • Reduce CO2 footprint • Reduce environmental impact • Continuous improvement • Quality 3 COMMITMENT TO PEOPLE AND SAFETY 4 SOCIAL RESPONSIBILITY • Safe work • Open culture and flat structure • Education and training • No-nonsense communication • Diversity • Doing business ethically • Showing involvement
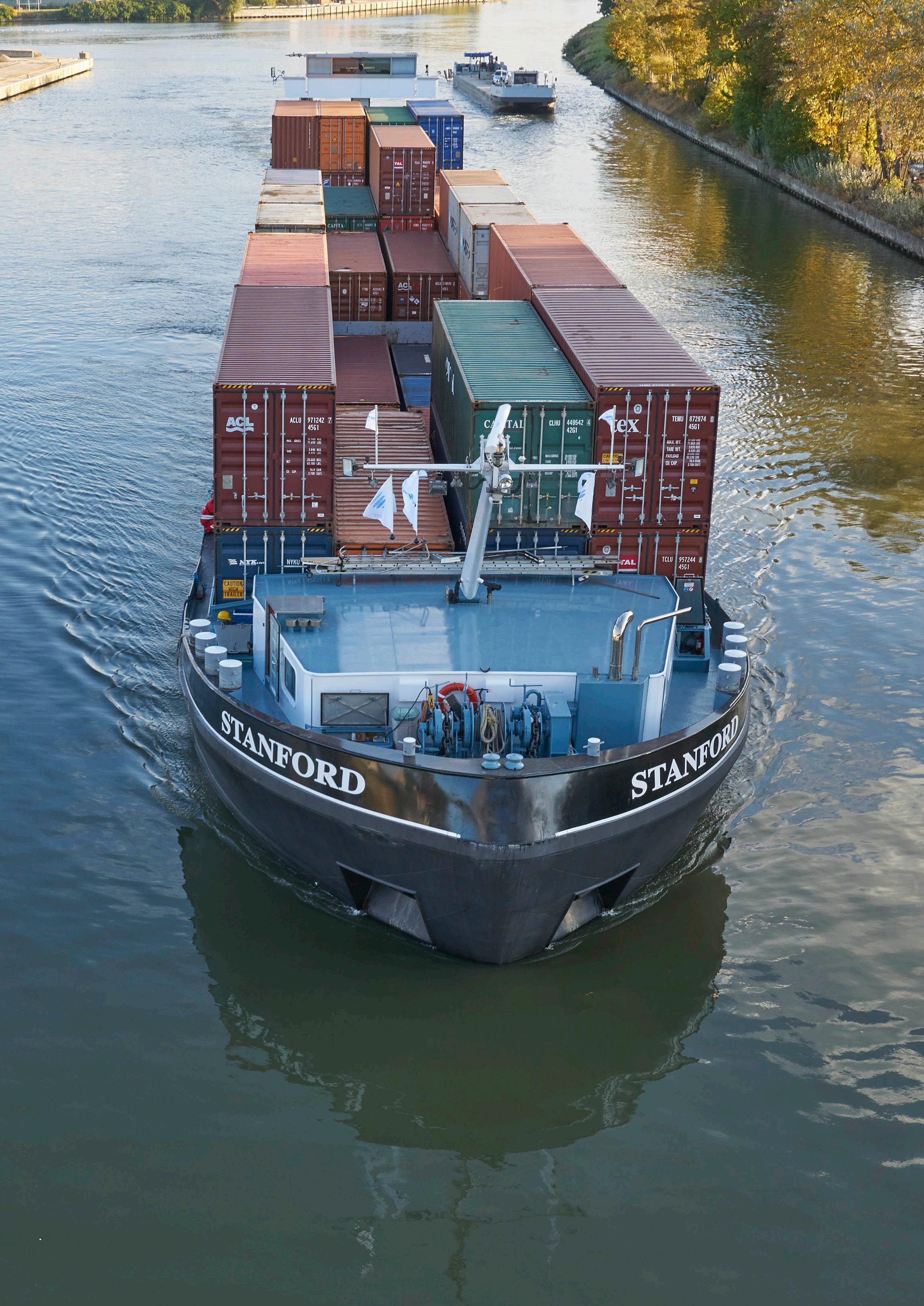




























4. SOCIAL RESPONSIBILITY
1. INTERMODAL SOLUTIONS
21 Our sustainable strategy consists of four pillars that all stem from the ambition to make a difference as a company to customers, to our environment, to our people and society in general. Long-term sustainable business is in the DNA of our family business. For our values, it provides a compass to the future. Through our business operations, we can also have a positive impact on the realisation of several Sustainable Development Goals.
We are a family business where, despite growth, people are not just numbers. We talk to each other and help each other. This vision is at the heart of our HR policy. In a sector that is often in the news because of unsafe or poorly paid jobs, we try to set the example. Safety and involvement come first for us. We create a pleasant and stimulating work environment, guarantee equal opportunities and continuous learning and development opportunities and contribute to workable work for everyone.
Our corporate responsibility also extends far beyond our employees, customers and business partners. We are part of the whole community. We have all been given many opportunities and where we can, we give these back. We also support many great initiatives that contribute to a better society for the benefit of all. Our engagement in the local community was further intensified in 2021 and 2022. In recent months, we have invested heavily in dialogue with a number of stakeholders and have noticed that this leads to meaningful insights and sometimes cooperation!
For our customers, we are a full-range partner in transport and logistics, offering added value and taking care of everything from A to Z. We manage the complexity of multimodal transport. We can quickly, flexibly and efficiently help our customers solve their transport and logistics challenges. We want to be a key facilitator in the transition to a circular economy. Digital platforms and measurement systems provide us with insight and overview in this regard. Our investments and acquisitions result from our vision of integrating all elements of intermodal transport into our operations. Through our systemic thinking and intermodal solutions, we contribute to sustainable economic growth, innovation and investment in infrastructure, the development of sustainable cities and communities, and reduce the social and environmental aspects of transportation and Inlogistics.2021and 2022, the new acquisitions will further improve our multimodal network and allow us to use our economies of scale to deli ver more added value with less environmental impact. Through our broad network of termi nals, warehouses and logistics hubs and our scale, we can unburden our customers as a one-stop shop intermodal provider.
2. SUSTAINABLE AND EFFICIENT OPERATIONS We are focused on efficiency and try to reduce our environmental impact in everything we do. Thanks to our focus on quality and efficiency, we realise maximum value for our customer with a minimum waste of raw materials, time, resources and talent. The expansion of our activities on multiple sites through investments and acquisitions of companies with complementary services, ensures that we can serve our customers even better. We invest in the latest technologies aiming for a maximum reduction of our carbon footprint. In this way, we are preparing ourselves for the European Green Deal and are helping to battle climate change. We have a long-term horizon and do not shy away from major investments. In the past year, we have experimented strongly with hydrogen technology and bi-fuel trucks. We are involved in several research projects to enable the transition to green logistics. We have reached a point where our size offers many economies of scale to have a real impact. So it’s time to put even more pressure on the accelerator to achieve the climate objectives more quickly.
A good atmosphere at work is important. But work can also be fun after hours. We take advantage of the regained freedom to connect our people through sport and fun after work.
Van Moer Logistics
3. COMMITMENT TO PEOPLE AND SAFETY
GREENCIRCULARITYTRAFFICLOGISTICSGOAL2025
Inland ports can be an “extended gate” where no intermediate customs checks need to take place. In this way, the transport time is Our goal: As a director of a multimodal logistics chain, we want to fully relieve our customers in their increasingly complex and circular supply chain. In doing so, we strive for a balance between economic, ecological and social considerations. We are committed to collaborating with various partners to realize the multimodal shift together. We have three clear commitments to this end:INCREASING MULTIMODAL
22 1. INTERMODAL
Certain optimizations only come with size. We are horizontally anchored broadly enough and have the volumes and capacity to achieve economies of scale. In addition, through our acquisition policy, we have vertically integrated part of the chain. New acquisitions and expansions at our strategic locations, including Germany since 2022, ensure that we can expand our customers’ business. Our direct access to maritime transport, our inland terminals and regional hubs, warehouses with rail connections, unloading quays, transhipment sites, inland barges and our fleet of nine ships, eight barges and 477 trucks, enable us to create an integrated multimodal approach. This enables us to optimise transport and logistics from our director’s role.
Inland ports are essential in the transition to a greener supply chain. They can serve as the end and starting point for maritime transport.
• Making infrastructure and capacity available for inland navigation and road transport;
• Optimal use of each modal form;
50% increase in TEU transported by water by 2025 compared to 2021 SOLUTIONS
INCREASING MULTIMODAL TRAFFIC We believe in inland logistics: transport of goods from the hinterland to the seaports or vice versa. This can be done by rail, barge and road transport The way transports are controlled, or better, directed, has a major effect on the environmental impact through the greenhouse gases CO2, CH4, NOx and particulate matter. Our contribution lies mainly in:
• Optimizing the energy efficiency of each modal form; • Offering a mix that balances economic, social and environmental parameters.
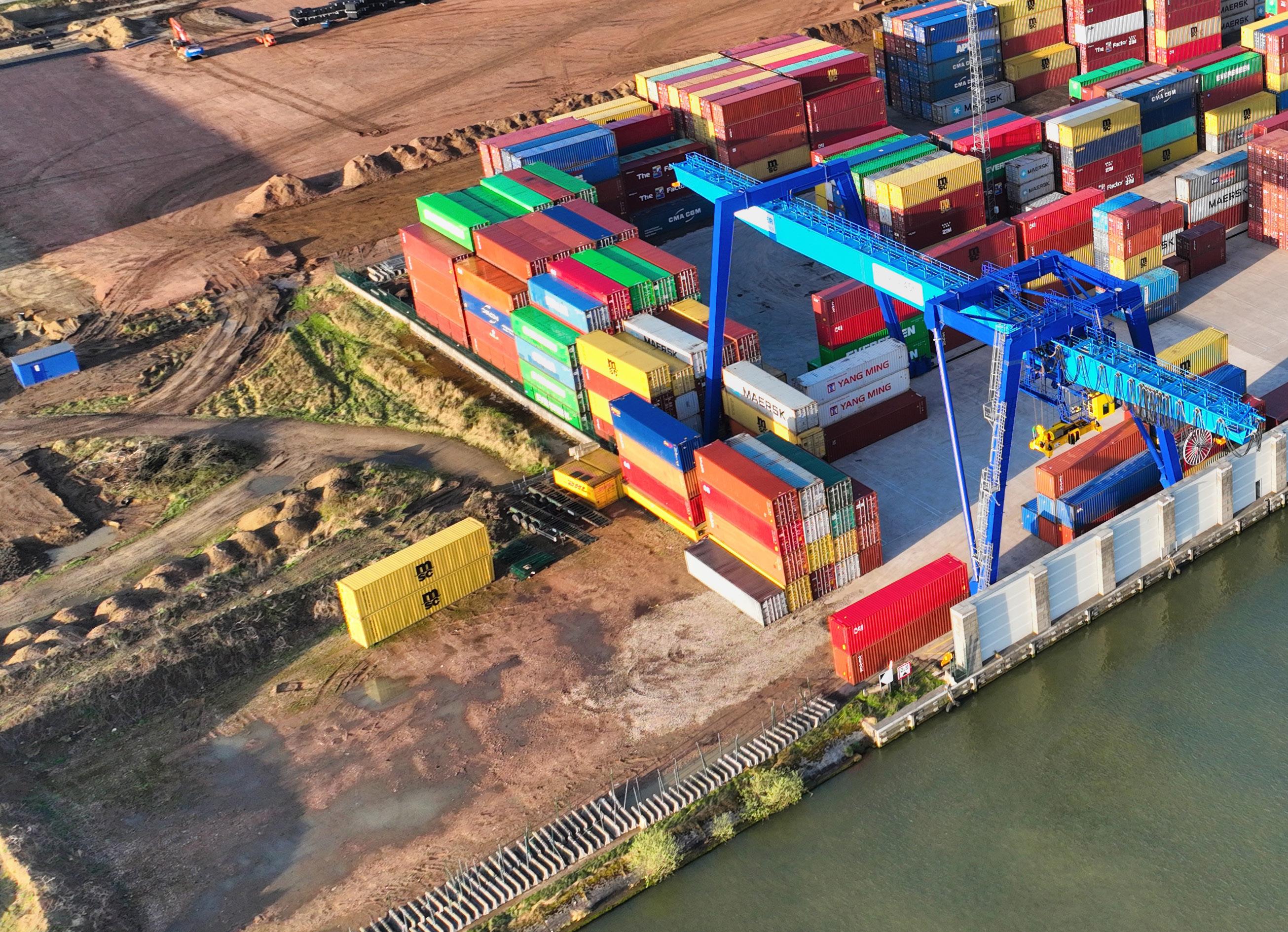
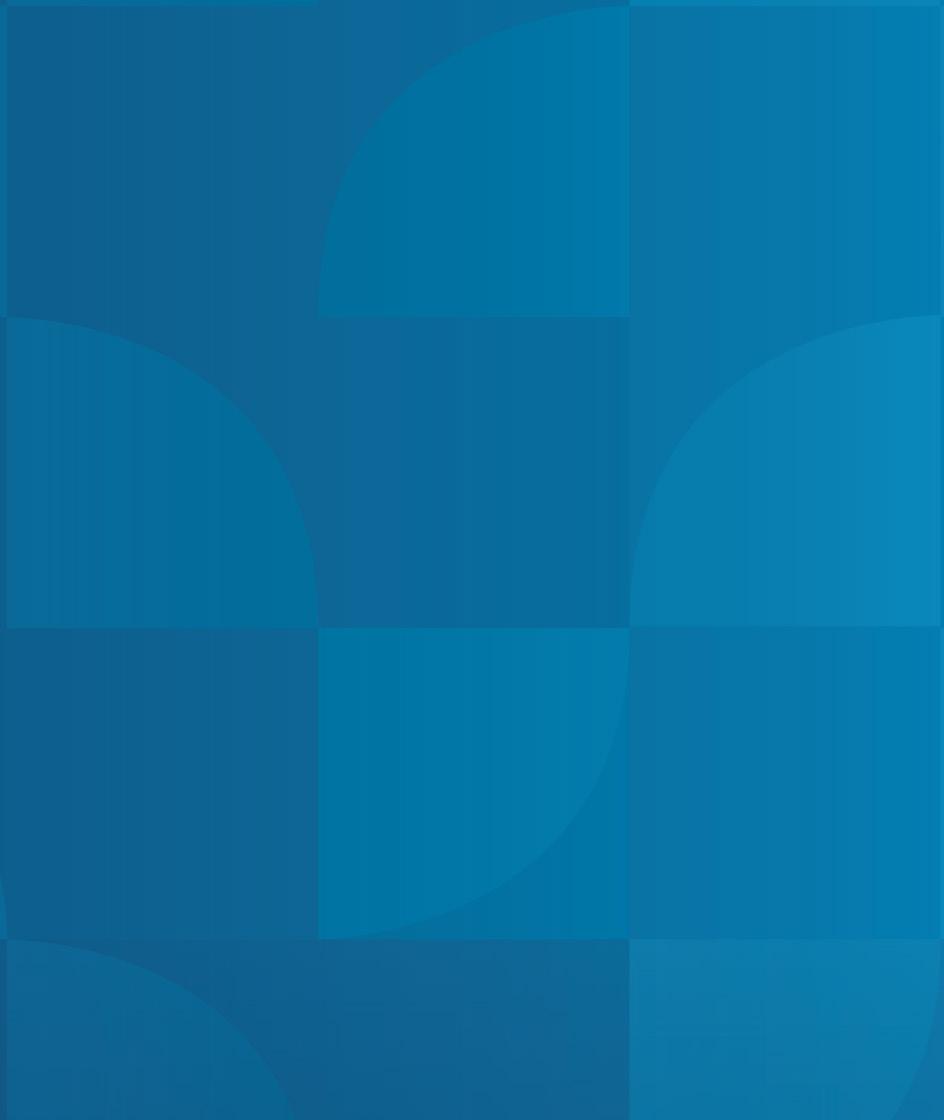



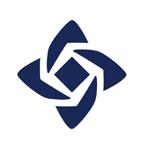
23Van Moer Logistics - 1. Intermodal solutions optimized. Today we have eight terminals along Flemish and Brussels waterways. Some were constructed in partnership to suit a customer or specific traffic. Others are open to a broad container flow and are considered as fully-fledged regional hubs because of the framework. You find the idea of partnerships in our warehouses as well. Some warehouses serve as a hub for a particular customer or specialize in a certain type of goods (chemicals, paper, granulates, food, etc.). Other warehouses even have a direct connection with the client’s production hall. And still others are storage and transshipment hubs for a multitude of Fromgoods. the port of Antwerp, we work in three directions: Brussels, Leuven and Grobbendonk. Strengthened by the merger of the ports of Antwerp and Zeebrugge (Port of Antwerp-Bruges), we also direct our attention to Zeebrugge. 2020 2021 Increase Increase in % Waterborne transport 312,479 385,018 72,539 19% Road transport 473,888 548,809 74,921 14% Total 786,367 933,827 147,460 33% % Barge 40% 41% % Road 60% 59% 385,018 TEU transpor ted by water within the port in 2021 19% increase in waterborne transport compa red to 2020
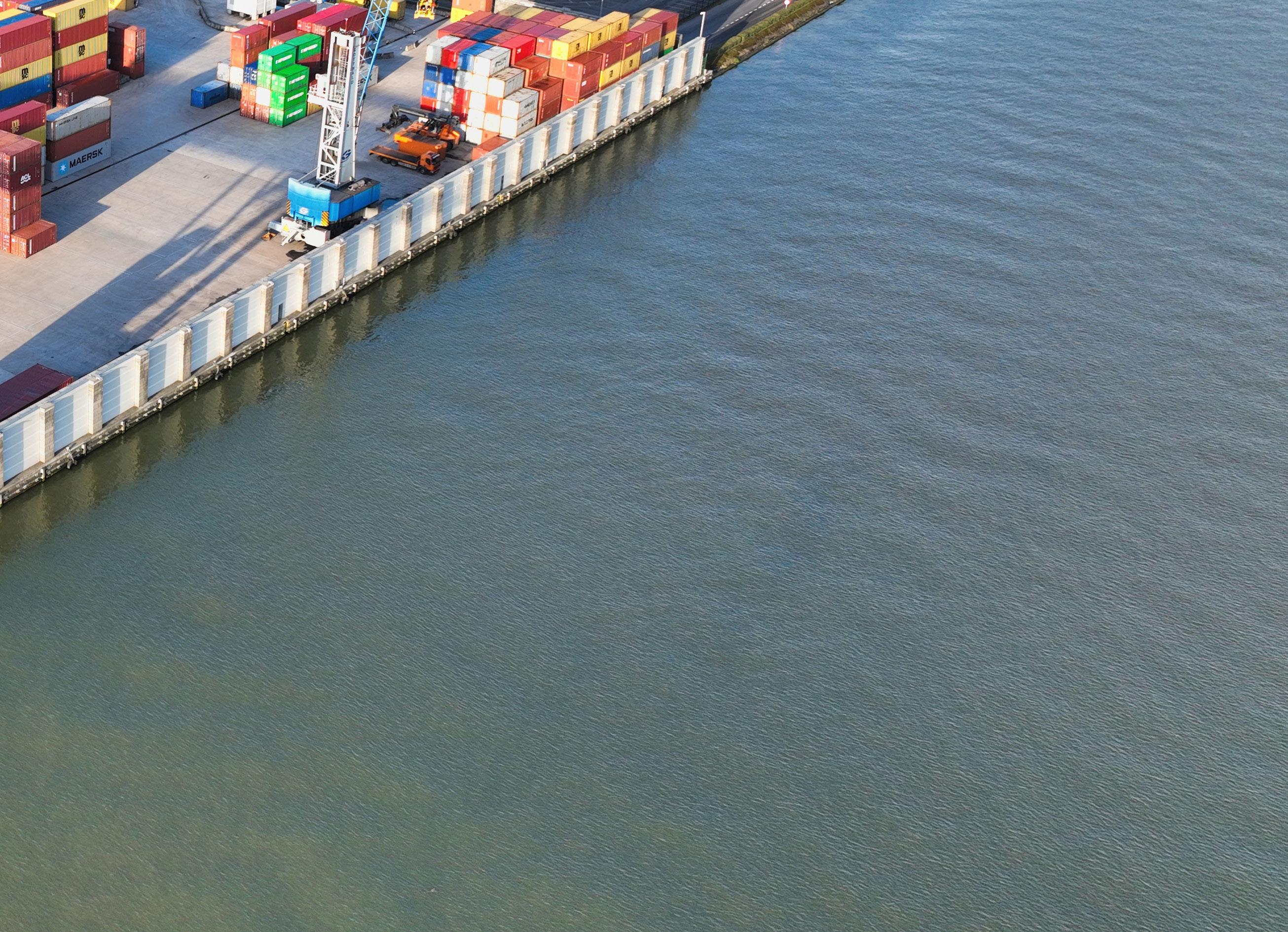


505,000 TEU transpor ted by ATO via water within the port in 2021 DID YOU KNOW? A barge is a ship without propulsion. It cannot sail by itself. Call it a kind of trailer, but in front or alongside a ship. It always needs a ship or a pusher tug. By taking the pusher tug with our other ships, the capacity in TEU doubles. So it is economically viable and almost halves the CO2 emissions per TEU transported. 220 metres quay wall 42,871.5 TEU transported in 2021 on TTB 37,095(Brussels)TEU transported in 2021 on CTC (Grim 2bergen)traintracks
44,766 TEU via DLCT in 2021 27,979 trucks off the road
Dennie Lockefeer Container Terminal In early 2019, we acquired the former Antwerp East Terminal on the Albert Canal in Grobbendonk. A large part of the accumulated volume had meanwhile ended up back on the road, a phenomenon known as “reverse modal shift”. We renamed the terminal Dennie Lockefeer Container Terminal (DLCT) and took up the challenge to recover the traffic and to drastically reduce the noise pollution for the local residents. By 2020, the inland terminal kept 21,693 trucks off the road. We use the site as a transport hub to Limburg and Liege. In 2021, the inland terminal kept 27,979 trucks off the road. Today we have two ships sailing there, which means we can now offer four departures per week. In this way, the terminal offers a larger capacity and a more flexible service. The Antwerp deep-sea terminals are served daily and a connection to Zeebrugge is also possible from Grobbendonk. The modal shift revolves around cooperation. That is why external transporters can also drop off their export containers at DLCT. The expansion by 23,000 m2 of warehouses will enable us to achieve strong growth here.
ATO is a joint venture between Boortmalt and Van Moer Logistics. The terminal in the port of Antwerp has 1,130 running meters of quay, a water depth of 16 meters and is 275,000 sqm in size. ATO has a reliable and fast connection by rail and barge to all deep-sea quays in Antwerp, Zeebrugge and Rotterdam. ATO is fully integrated into the inland terminal network on the Antwerp, Brussels and Leuven axes.
Associated Terminal Operators
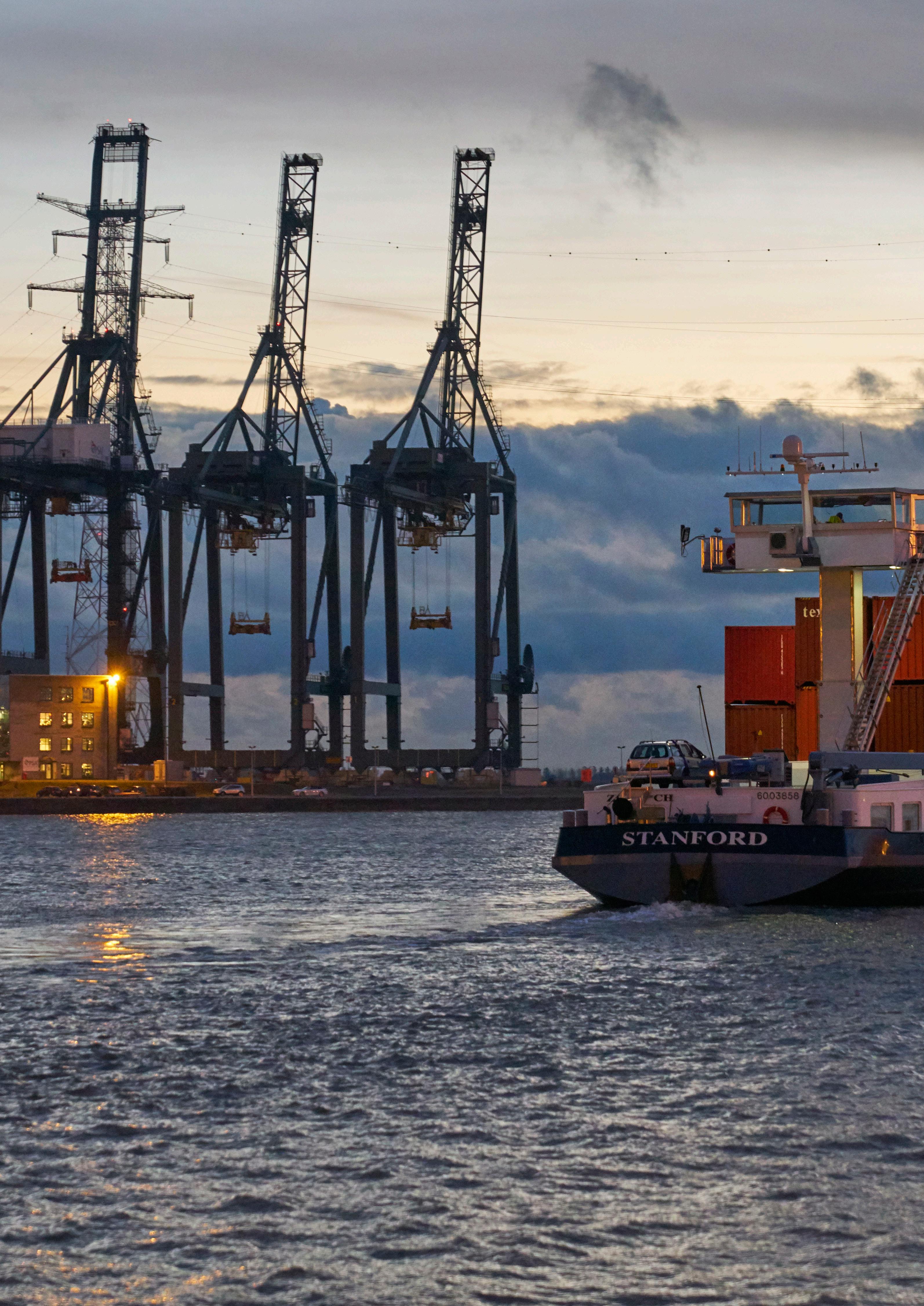







Bornem For Wienerberger, we take care of the consolidation of pallets of bricks for export at the quay in Bornem. With our mobile installations, we are well equipped to unload the bricks from the production site of Beerse in Bornem and to load them afterwards consolidated on coasters. After unloading the stones in Bornem, the barges continue to Grimbergen, where they load non-contaminated soil from infrastructure works in Brussels. This soil is returned to the plant in Beerse to fill up the old clay pits. The latter is done in the context of landscape restoration. In this way, a water-bound transport loop has been created between Beerse, Bornem and Grimbergen. This results in an annual saving of approximately 6,000 freight trips. WeBarge Under the banner of iBarge, we have invested in our own barges since 2016, transporting containers between the two banks of the Scheldt. In 2019, iBarge acquired the assets of APS and continued to sail as WeBarge. We now have nine vessels and eight barges. Our focus is on the efficient organisation and safe execution of container shipments, both within the Port of Antwerp and beyond. The sailing schedule allows our modern and extensive fleet to call at all of Antwerp’s container terminals on a daily basis. In 2022, we will replace three vessels, providing an opportunity to switch to more environmentally friendly hybrid stage 5 marine engines (electricity and marine diesel oil). We also have an estuary ship on order to sail to Zeebrugge. Terminal Hoboken
Trimodal Terminal Brussels (TTB) and Container Terminal Cargovil (CTC) In March 2021, we acquired TTB. Because TTB and our terminal at Cargovil in Grimbergen are close to each other, we will create new synergies. Thanks to the extra terminal capacity, our barges will be able to be deployed more efficiently. We also see opportunities here for other water-bound urban distribution. And we will contribute to the further sustainable development of the Brussels port area and the creation of employment opportunities. In April 2021, we already added a warehouse capacity of 20,000 sqm. Together with Port of Brussels, we are currently developing an investment and growth programme. In time, this will result in even more storage space, an extra crane and the activation of the railway lines so that we can make this terminal trimodal. Today, we are also exploring the possibilities of facilitating green urban distribution from the terminal. Terminal Wilsele On the Leuven-Dijle canal, we operate a terminal in Wilsele that has been specifically set up to transport household waste from a large part of Flemish Brabant to the waste treatment company Indaver in Antwerp. Every year, approximately 60,000 tons of household waste are transported by inland waterway, thus avoiding some 3,864 truck trips. 73.5% savings of CO2 compared to road 3,864transportjourneys saved Van Moer
Logistics - 1. Intermodal solutions
Umicore partnered with us to achieve the modal shift in Hoboken. Every year, Umicore processes some 350,000 tons of raw materials such as electronic waste, automotive catalysts, industrial catalysts and by-products from other metalworking companies. To drastically reduce road transport, we commissioned a new quay along the Scheldt. We take care of the supply of containers by ship and the traction from the quay to the unloading place. In this way, approximately 8,500 trucks are taken off the road each year.
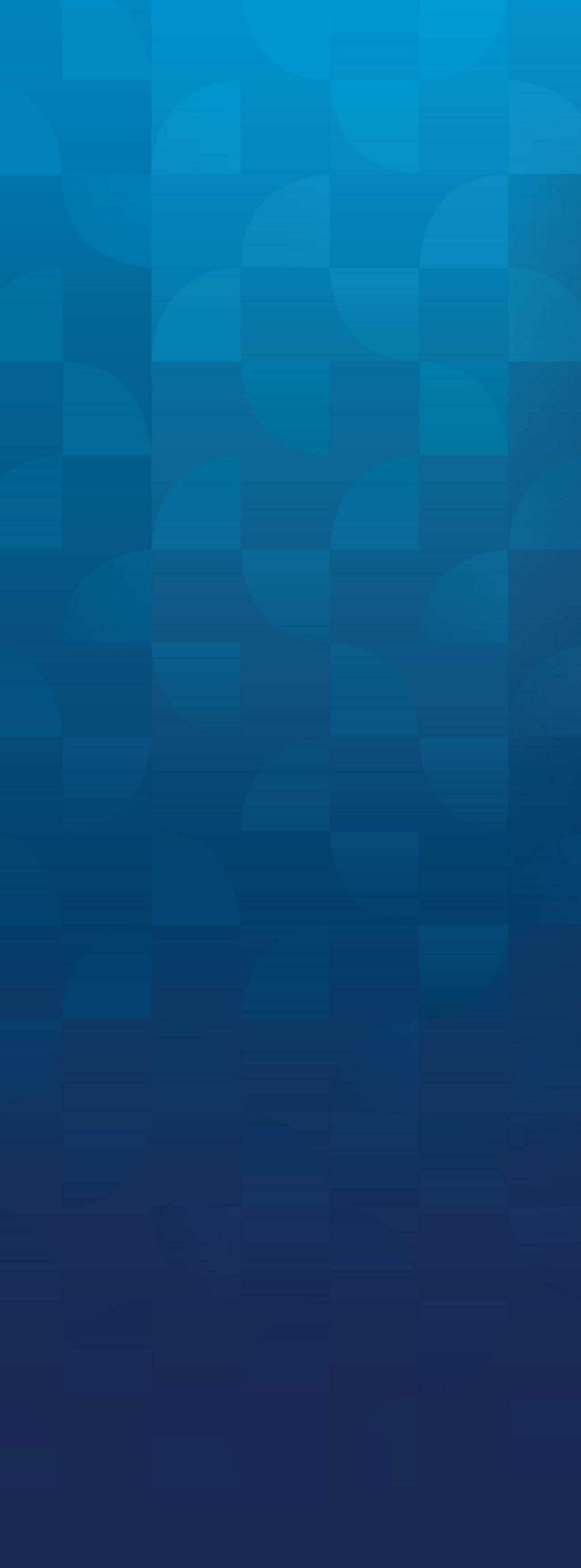
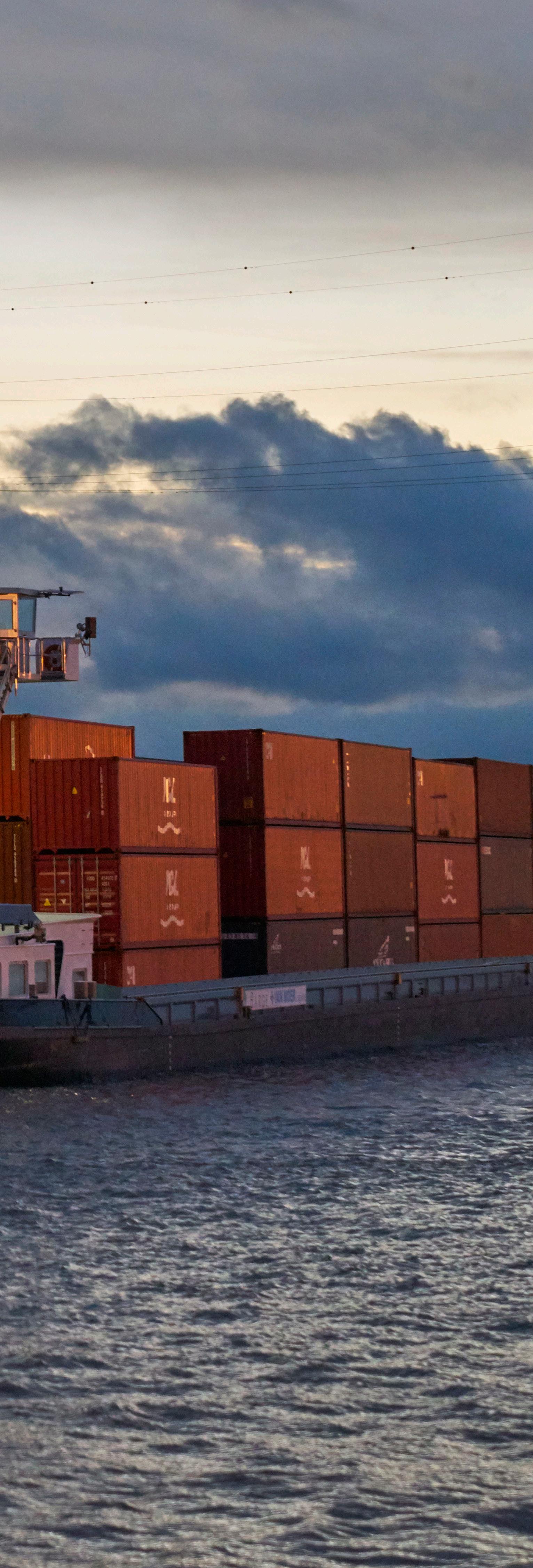


Van Moer Logistics supports its customers in designing, shaping and rolling out circular models and value chains. In this process, we fully assume our role as a value-adding circular logistics partner. All this requires the right expertise in chain management, but also the means to work efficiently on a large scale. Through our investments in hubs, infrastructure and our fleet, we have the assets to materially accelerate the transition and fully relieve customers of the burden. Our extensive network of terminals in convenient locations for recycling and chemistry in Flanders ensures that we can make the circular models work efficiently with minimal environmental impact.
GOAL 2025 Five circular projects with on-site value-adding logistics where we take the lead by 2025
Efficiency: the cost of collecting materials should not outweigh the benefits of reuse. An efficient logistics chain and the right people in the right place are needed here.
The Port of Antwerp-Bruges will make a crucial contribution to the circular economy through its chemical cluster. New value chains are emerging based on renewable and circular raw materials. We are ready to relieve the chemical industry of its logistical circular challenges. As an external chain director, we look at the whole picture from a broader perspective. Today we already have several partnerships running and offer on-site logistics solutions for reverse logistics and waste processing. We are further working on partnerships for value-adding circular logistics. The future is circular... With circularity, we mean an economic system of closed cycles in which raw materials, components and products lose their value as little as possible, renewable energy sources are used and systems thinking is central. The transition to a circular economy is not easy. To organise the circular model feasibly, companies are best to work with an experienced logistics partner who is committed to:
Environmental cost: the environmental impact of collection may not exceed the benefits of recycling our multimodal approach, and the optimizations to planning and fleet management reduce the CO2 impact per TEU transported per kilometer. Focus on core business: petrochemical companies’ sites are often not suited for these specific types of logistics, and expertise in chain management is required. We manage the complete material flows, have our own sites and are familiar with all types of optimizations within the value chain.
We want to be a key facilitator in the transi tion to a circular economy.
26 CIRCULARITY
Effectiveness: to be economically viable, sufficient volume and scale must be generated. We focus on industry and large volumes where economies of scale are achieved.
The transition to a circular economy will require smart logistics, capable of setting up integrated circular supply chains and managing reverse logistics. A very important role here is reserved for the supply chain director, who is responsible for the efficient matching of supply and demand of materials and raw materials for use and reuse.
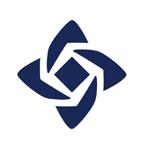




Van Moer Logistics - 1. Intermodal solutions
On-site logistics at JBF Global Europe
The Blue Gate Antwerp site also has a logistics zone. This zone consists of a terminal on the Scheldt and an area behind it for logistics activities. We operate the terminal and take care of the supply and removal of soil and building materials for the site itself. In time, the terminal will serve as a transshipment center for construction materials, a so-called Circular Construction Consolidation Center (CCCC). Transport flows to and from the city will be carried out there as efficiently and sustainably as possible. Smart urban distribution is a fact.
For the next five years, we will be respon sible for the loading, unloading and pack aging of palletised goods, the planning and operational functioning of the stora ge batteries (silos), and the administrative handling of incoming and outgoing goods.
The PET factory of JBF Global Europe in Laakdal recently started marketing an innovative technology of chemical recycling to meet the new European directives on plastic recycling. By 2029, the member states must achieve a collection percentage of 90% and by 2025, at least 25% of PET bottles must consist of recycled material. The factory in Laakdal can process up to 150 tons of postconsumer PET flakes daily. That’s more than 200,000 tons on an annual basis.
And more importantly: the new products - under the name APE RE25 - already contain 25% of recycled material, while remaining of equal quality. The recycled PET can therefore be directly reused for food and beverage packaging.
Van Moer Stevedoring Blue Gate Antwerp Petroleum South was once the heart of Antwerp’s petroleum industry. Today this site is ready for a new chapter: Blue Gate Antwerp. The climate-neutral business park is reserved for innovative companies that want to grow sustainably, thanks to circular models.
In March 2022, we acquired the on-site activities of JBF Global Europe (Laakdal). A pool of 30 employees provides logistical support to the production unit of the inter national polyester (PET) producer.
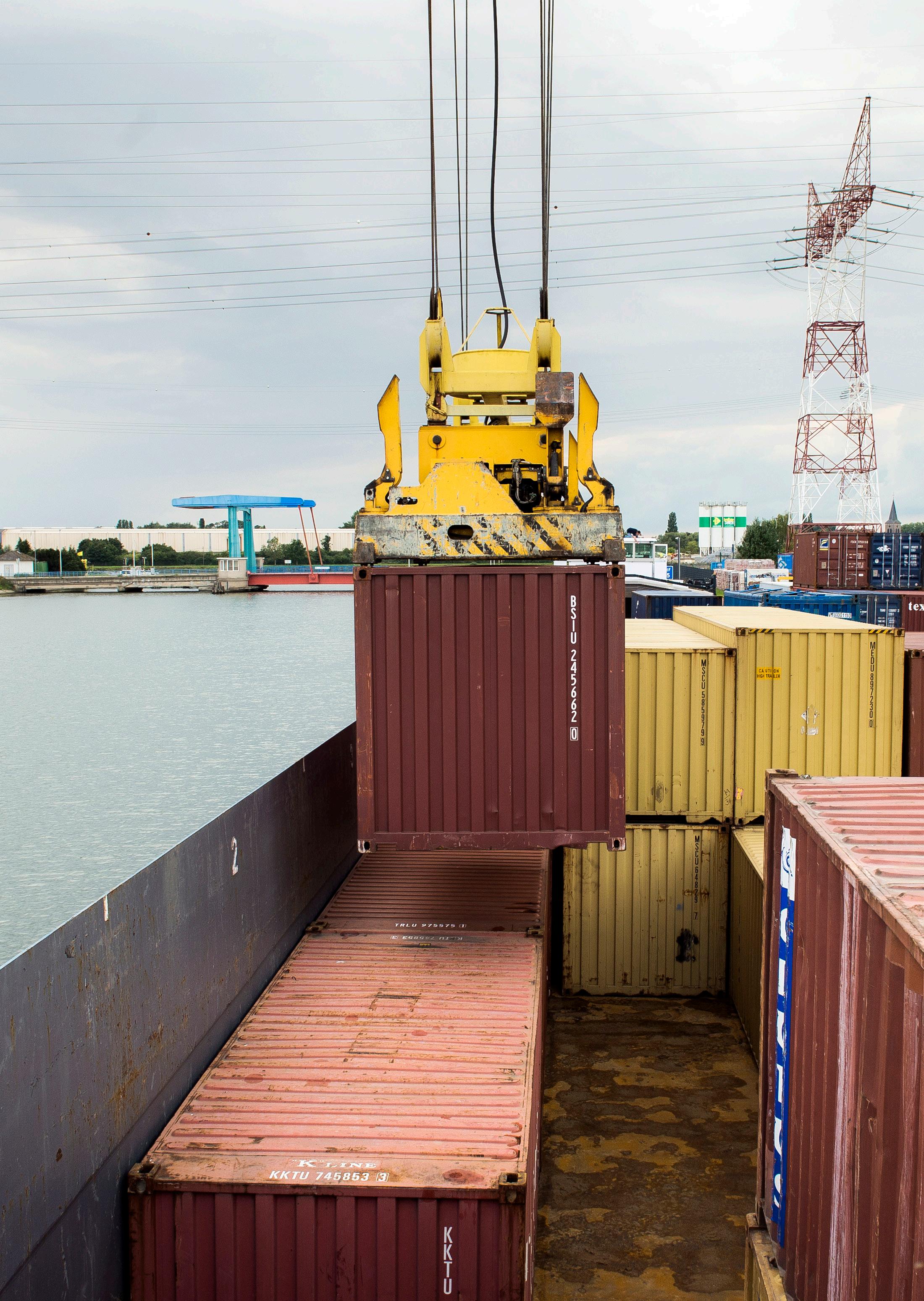
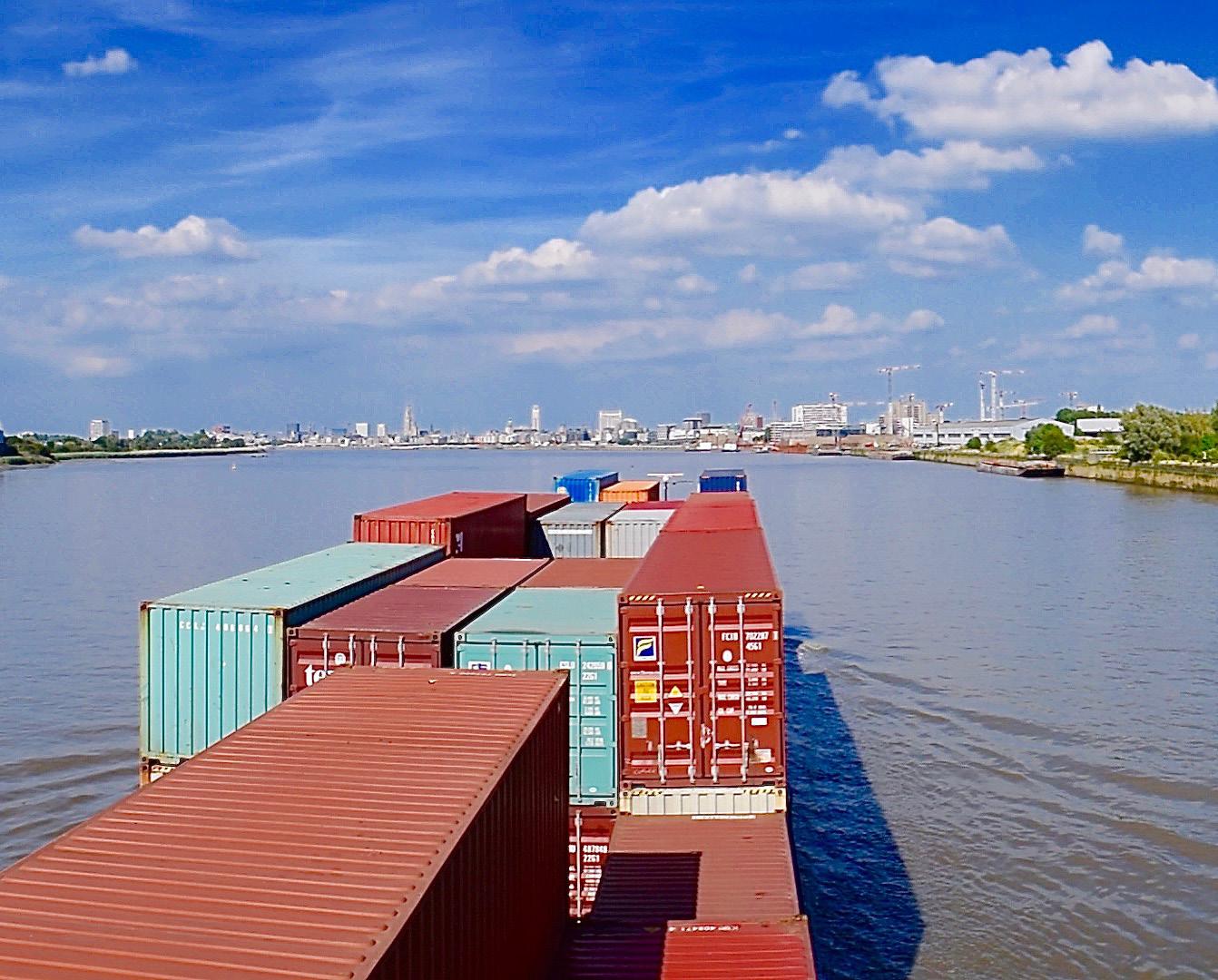
28 remains the optimal way to transport goods. We are constantly working on making our transports more efficient. We do this by mo dernizing the fleet, by smarter loading and routes, by monitoring and rewarding good driving behaviour and above all with intelligent logistics. We like to offer our customers total solutions and develop our services to suit their needs. We think in the long term and dare to invest on the customers’ behalf. Digitalization Both at the terminals and in our road transport, smart planning software ensures that everything runs as efficiently as possible. Every truck that runs empty on a route is a waste. Every container that we have to move to reach another represents a cost. We closely monitor the efficiency of our operations. Our load factor in freight transport is peaking just above 90% for some time now. We put all our expertise at the disposal of our customers. This enables them to optimize their logistics flows with us. We also optimize the flows of empty and full containers, avoiding extra trips to and waiting times at the busy Antwerp terminals and depots. CO2 impact Just like us, our customers are working on mapping and reducing the CO2 impact of their business activities. More and more, we receive requests from clients to map the specific CO2 impact of the flows we perform. Thanks to our own CO2 dashboard, we can do this relatively easily. We also like to discuss alternatives with a lower CO2 impact.
GOAL 2022-2023 Achieve a nearly CO2 neutral supply chain by 2023 (= 80% less emissions than regular transport)
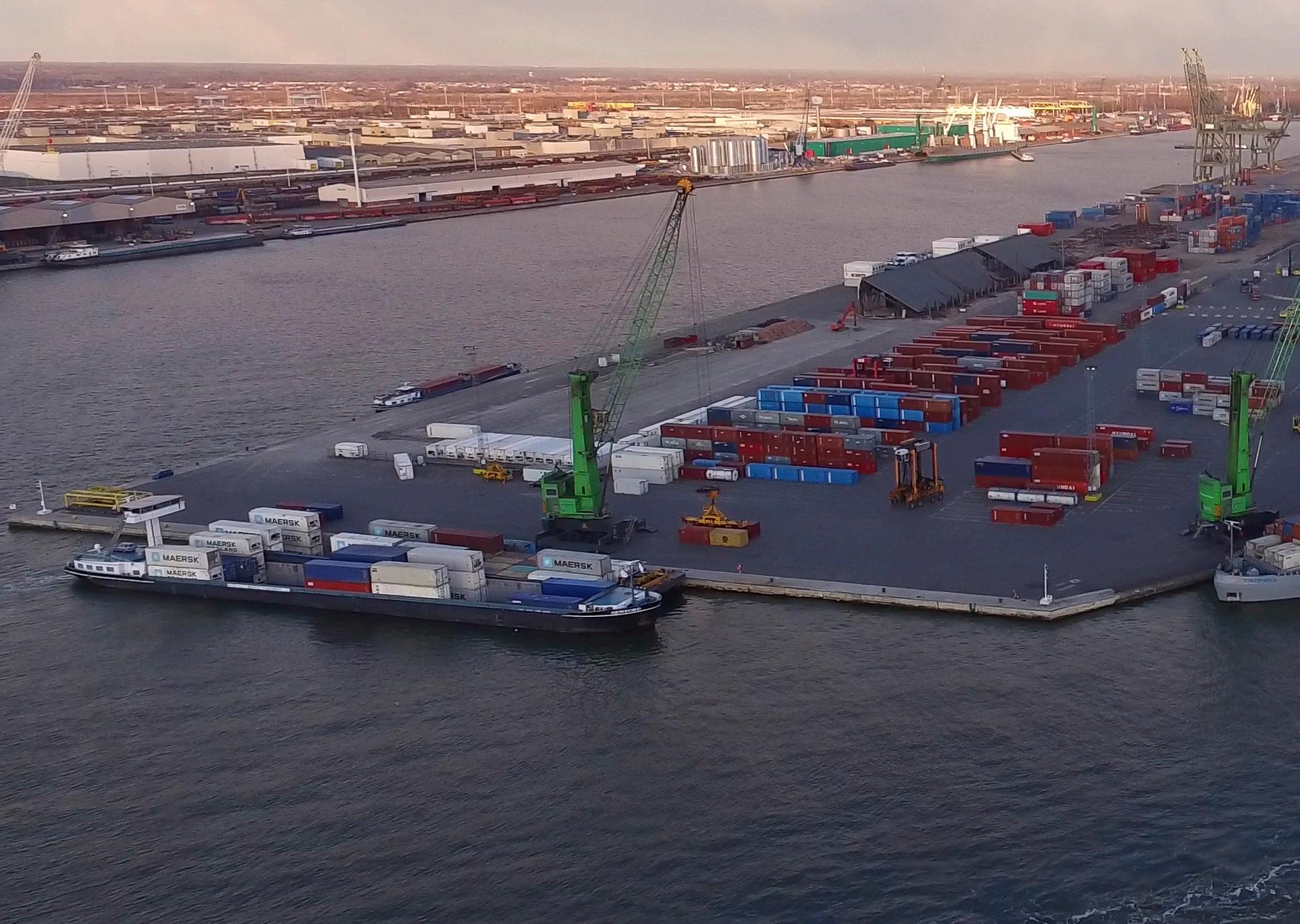
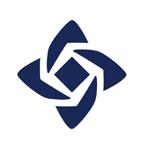
29 FACTS & FIGURES Our total transport in 2021 amounted to 933,827 TEU of which 385,018 were intra-portal and intermodal. We therefore organised 41% of our traffic by water. The purely intermodal routes accounted for 84,553 saved trips in 2021 on the fol lowingAntwerp-Brussels:routes: 75.3% less CO2 emitted and 28,205 trucks off the road Antwerp-Grimbergen: 75.7% less CO2 emitted and 21,197 trucks off the road Antwerp-Grobbendonk: 81.3% less CO2 emitted and 27,979 trucks off the Antwerp-Hoboken:road 80.8% less CO2 emitted and 4,596 trucks off the road Antwerp-Wilsele: 73.3% less CO2 emitted and 2,576 trucks off the road Route TEU Saved trips Saved KM COtransportfromemissionsTheoreticalroad2kg/year Effective fromemissionswater borne traffic CO2 kg / year COtransportparedsavedEmissionscomtoroad2kg/year Effective savings as ofpercentageawaterbor ne traffic (Brussels)TTB 42,871 28,205 2,068,350 5,141,011 1,270,933 3,870,078 75.3% (Grimbergen)CTC 37,095 21,197 1,472,024 4,199,152 1,021,297 3,177,855 75.7% (Grobbendonk)DLCT 44,766 27,979 1,709,841 4,062,435 761,074 3,301,361 81.3% (Hoboken)Umicore 5,606 4,596 142,958 419,848 80,732 339,116 80.8% Wilsele 3,864 2,576 186,044 256,284 68,338 187,946 73.3% Total 134,202 84,553 5,579,217 14,078,730 3,202,374 10,571,156 Van Moer Logistics - 1. Intermodal solutions
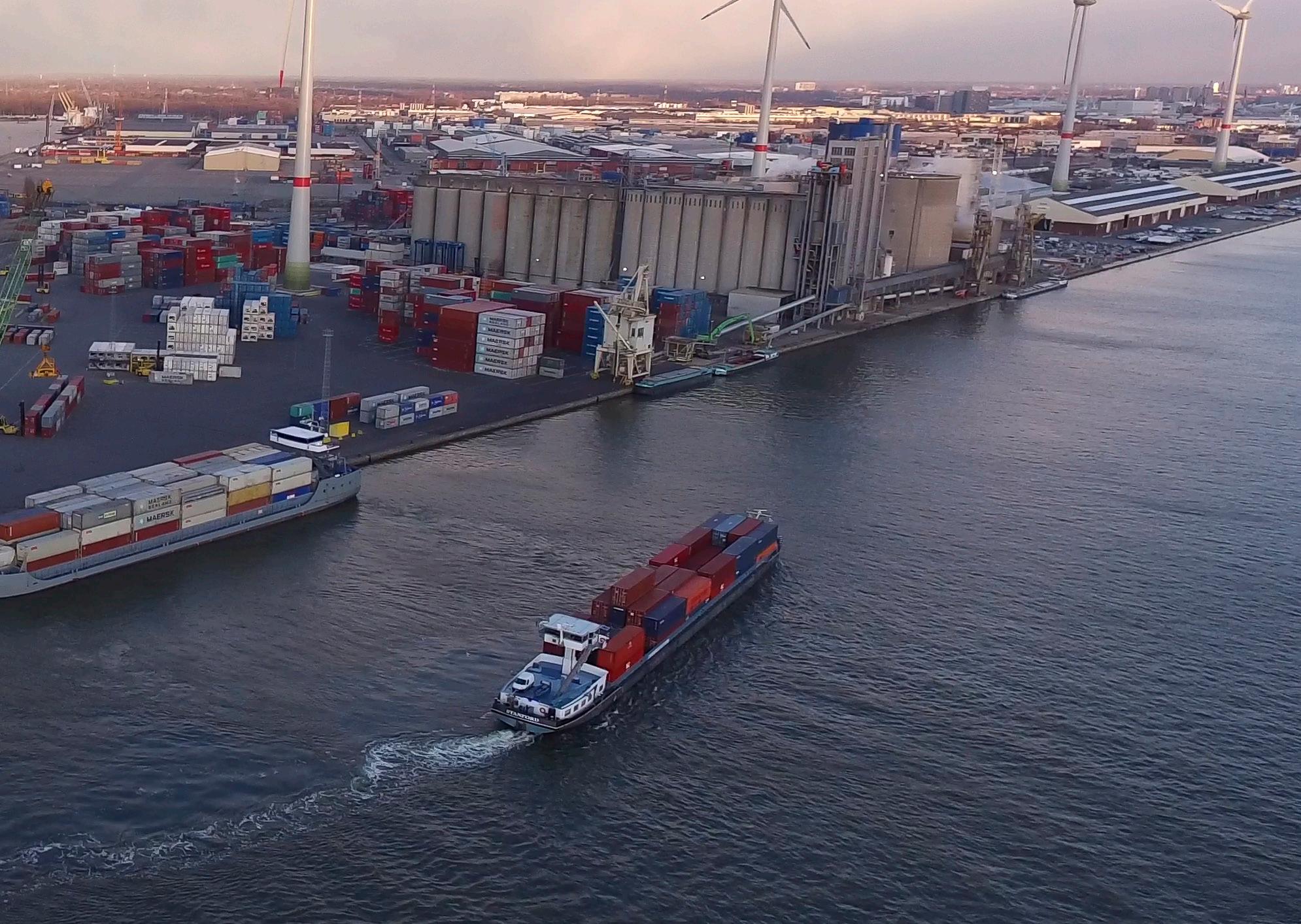





MEASURE CO2 FOOTPRINT Our goal: to do better than the EU Green Deal. We believe it is important to know our carbon footprint. Only then are we able to take tar geted measures to reduce our CO2 impact. We notice that many of our stakeholders and customers appreciate this as well. In the autumn of 2021, we started a very ex tensive exercise to map the impact of all our activities on all sites in scope 1 and scope 2. We used the calendar year 2020 as the base line and now also have the complete data for As2021.a company, we want to be part of the solution and not part of the problem. The refore, we have developed a reduction plan for our own operations. Optimisations in our services, our intermodal approach and vertical integration ensure that our custo mers’ operations will also become greener.
30
` MEASURE CO2 FOOTPRINT REDUCE CO2 FOOTPRINT REDUCE ENVIRONMENTAL CONTINUOUSIMPACT IMPROVEMENT QUALITY 2. SUSTAINABLE & EFFICIENT OPERATIONSGOAL2022-2023 • Plan for the decarbonisationfleet • Set up CO2governance system • CO2 measurement at acquired companies
Our Sustainabilitygoal: is at the core of our daily operations. As we have grown, we have naturally begun to think in a more structured way about how we can operate efficiently and sustainably. The motto here is to create as much value as possible for our customers and other stakeholders with a minimum waste of time, resources, money and non-renewable raw materials.

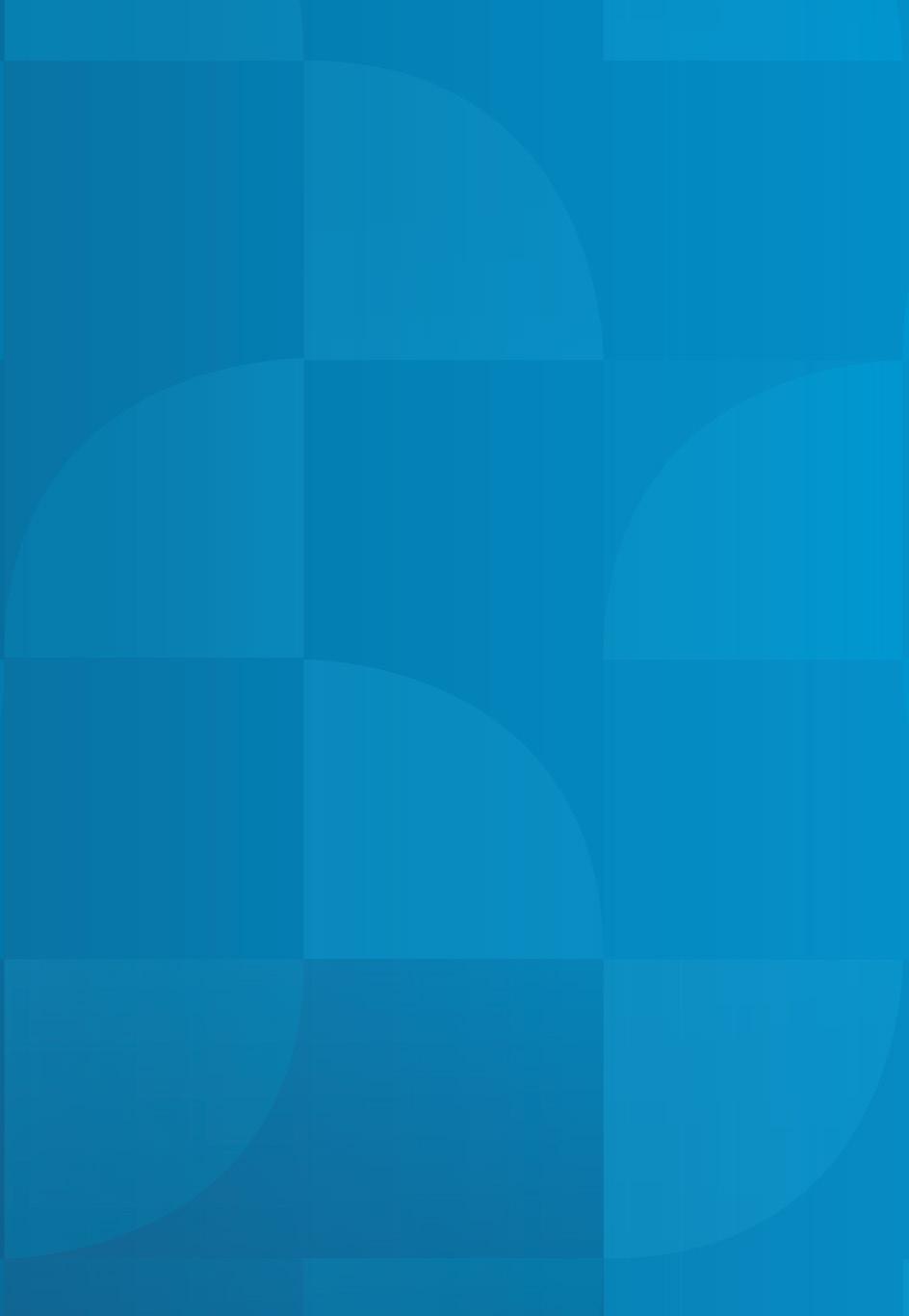
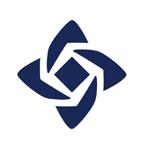





•
•
• Fuel consumption subcontractors (charters)
Sustainable
31
• Generation of own electricity through solar panels Heating Fuel consumption trucks Fuel consumption passenger cars
• Elecricity from the grid
Methodology We mapped our carbon footprint for the calendar years 2020 and 2021. In order to do this, we looked at scope 1 and scope 2 according to the Greenhouse Gas Protocol (GHG), which is the most widely used protocol worldwide to calculate greenhouse gas emissions. The GHG has three scopes:
•
• Forwarding SCOPE 1 SCOPE 2 SCOPE 3 Direct CO2 emissions, caused by own sour ces within the organisation. This concerns emissions from own building-, transport- and production-related activities. Indirect CO2 emissions, through the genera tion of purchased and consumed electricity or Indirectheat. emissions of CO2 caused by the busi ness activities of another organisation. The se are emissions from sources that are not owned by the organisation and over which it has no direct influence. Moer Logistics - 2. and efficient operations
For our calculation, we included all scope 1 and scope 2 consumptions. However, we made a small exception for business travel (air travel = scope 3) and we also included the CO2 impact of the chartered trucks (third party = scope 3) in our calculation. We find it important to gain insight into the charters as they contribute to our core business. We calculate the impact of fuels according to the Tank to Wheel (TTW) standard. This looks at the direct emissions of the activity. It does not include the CO2 impact from fuel extraction and production. In the scope of our measurement are the energy consumption and revenues related to:
•
Van
• Fuel consumption business travel (air travel) Fuel consumption refrigerants
• Fuel consumption inland shipping Fuel consumption industrial rolling stock
•
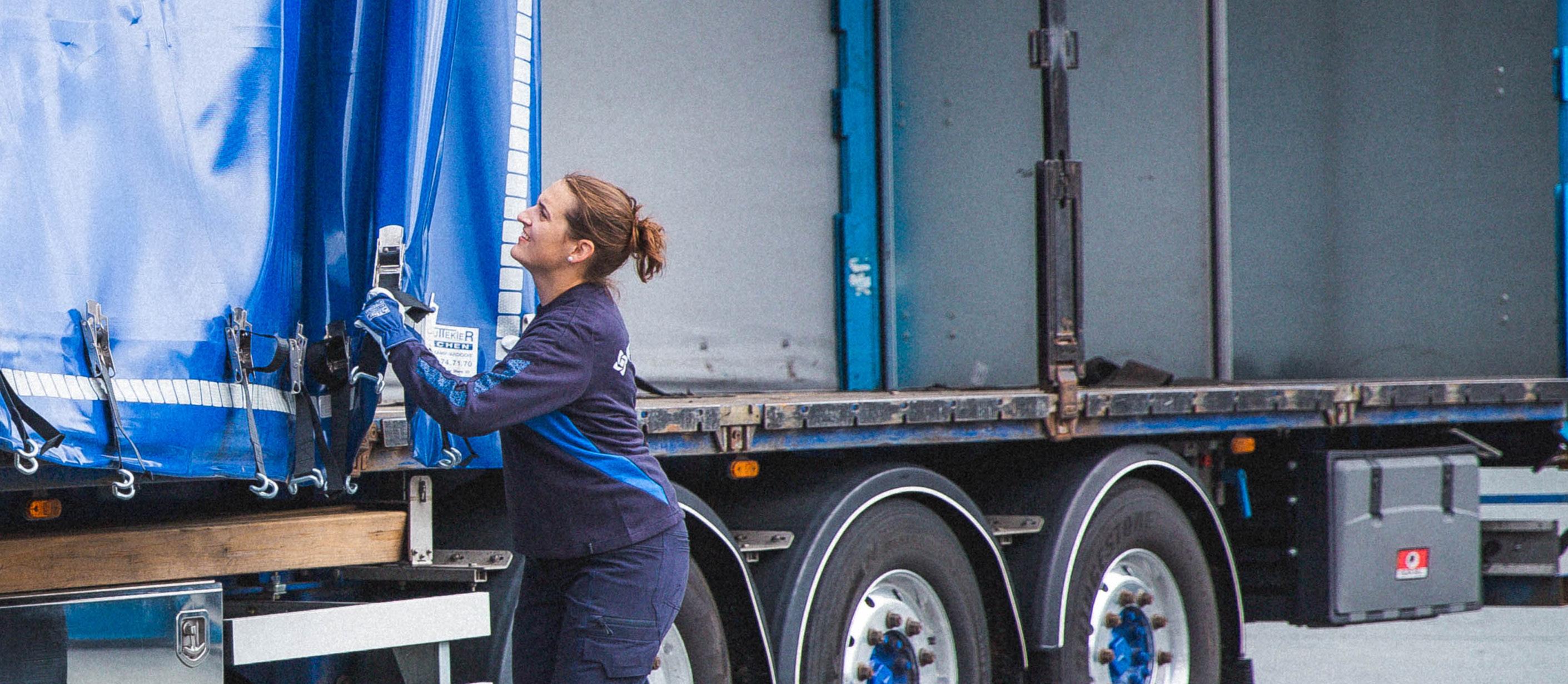
91 +5 +4 +E SCOPE 1, 2 & 3 Fuel (scope 1 + scope 3)* 38,617 tons Heating (scope 1) 1,875 tons (cleaning & repair processes) Electricity (scope 2) 1,658 tons Business travel (scope 3) 30 tons Forwarding (scope 3) 12 tons Heating (scope 1) 7 tonstonsTOTAL42,199CO2 91% 5% 4% * Fuel scope 1 = 32,024 tons Fuel scope 3 (charters) = 6,592 tons ** Due to rounding off, there is a difference of 1 tonne in the sum 2020 2021 Fuel (scope 1) tCO2 32,977 32,024 Diesel (litres) 11,864,912 11,329,821 LNG (kg) 386,691 539,346 MDO (litres) 754,419* 754,419 Petrol (litres) 39,006 40,542 Fuel (scope 3) 6,357 6,592 Diesel (litres) 2,530,370 2,623,772 Heating (scope 1) tCO2 1,874 1,875 Natural gas (kWh) 10,234,056** 10,234,308 Electricity (scope 2) tCO2 1,422 1,658 Grey electricity (kWh) 8,416,562 9,809,264 Green purchased electricity (kWh) 9,431 11,727 Green self-generated electricity (kWh) 1,027,012 703,618 Total emissions CO2 (tons) 42,667 42,199 Turnover (mio €) 186,396 222,378 Absolute reduction -1.1% Tons CO2 / mio € 228,905 189,762 Relative reduction -17.1% * The quantities for 2020 could not be fully established for this item. We have therefore taken the figures for 2021 as an assumption. ** This marginal difference between 2020 and 2021 does not mean that there is hardly any evolution. The activities for which natural gas is used (cleaning and repair) and the number of sites that are heated with gas have indeed increased.
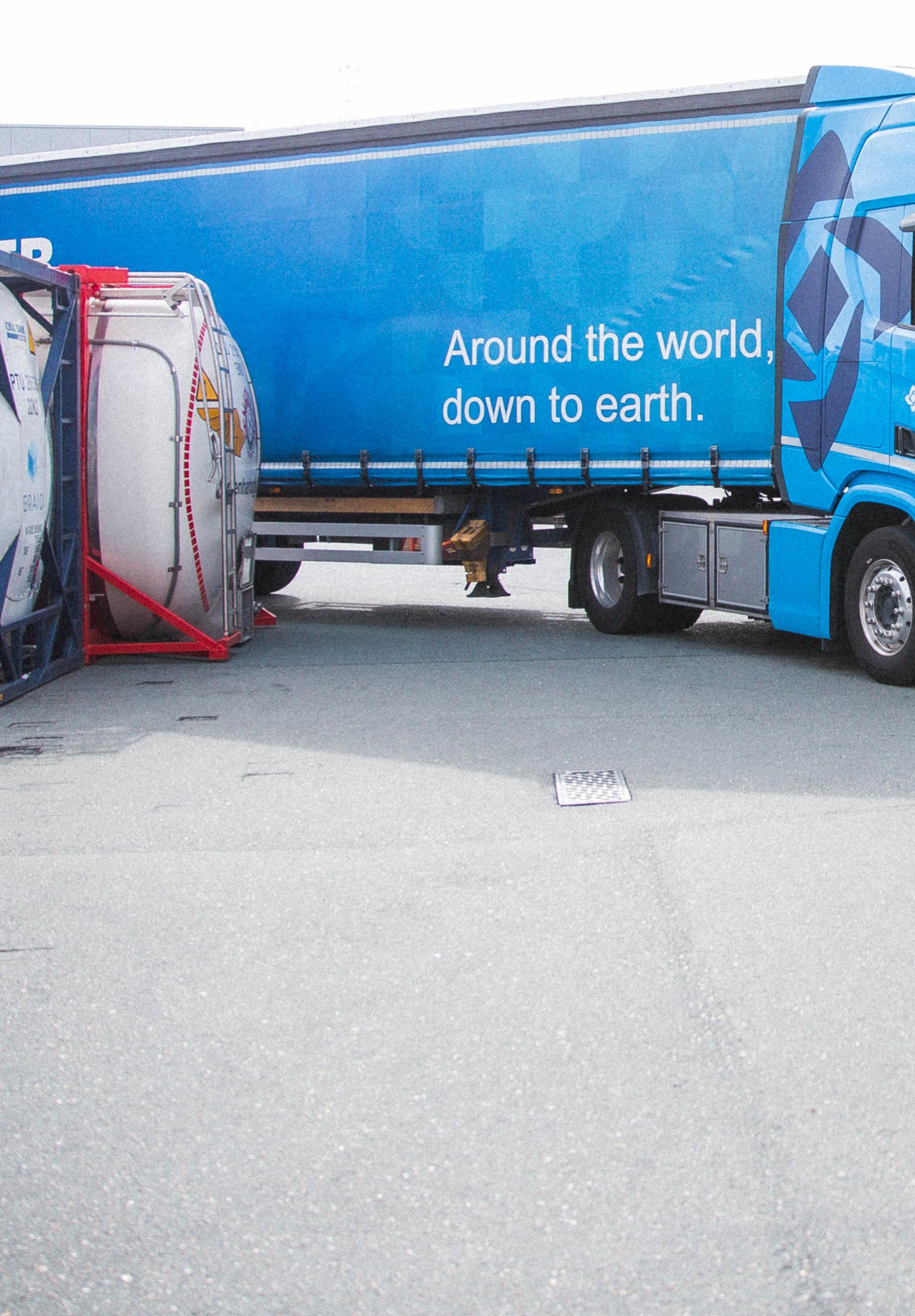
89 100 100 Diesel 11,329,821 ltres LNG 539,346 kg Marine Diesel Oil (MDO) 754,419 litres Petrol 40,542 litres Grey purchased electricity 9,809,264 kWh Green self-generated electricity 703,618 kWh Green purchased electricity 11,727 kWh *no CO2 footprint for green electricity tonstons32,024CO21,658CO21,875tonsCO2 Natural gas 10,234,308 kWh 89% 4% 7% 100% 100% Fuel (scope 1) Heating (scope 1) Electricity (scope 2) Van Moer Logistics - 2. Sustainable and efficient operations In units: In units: In units:
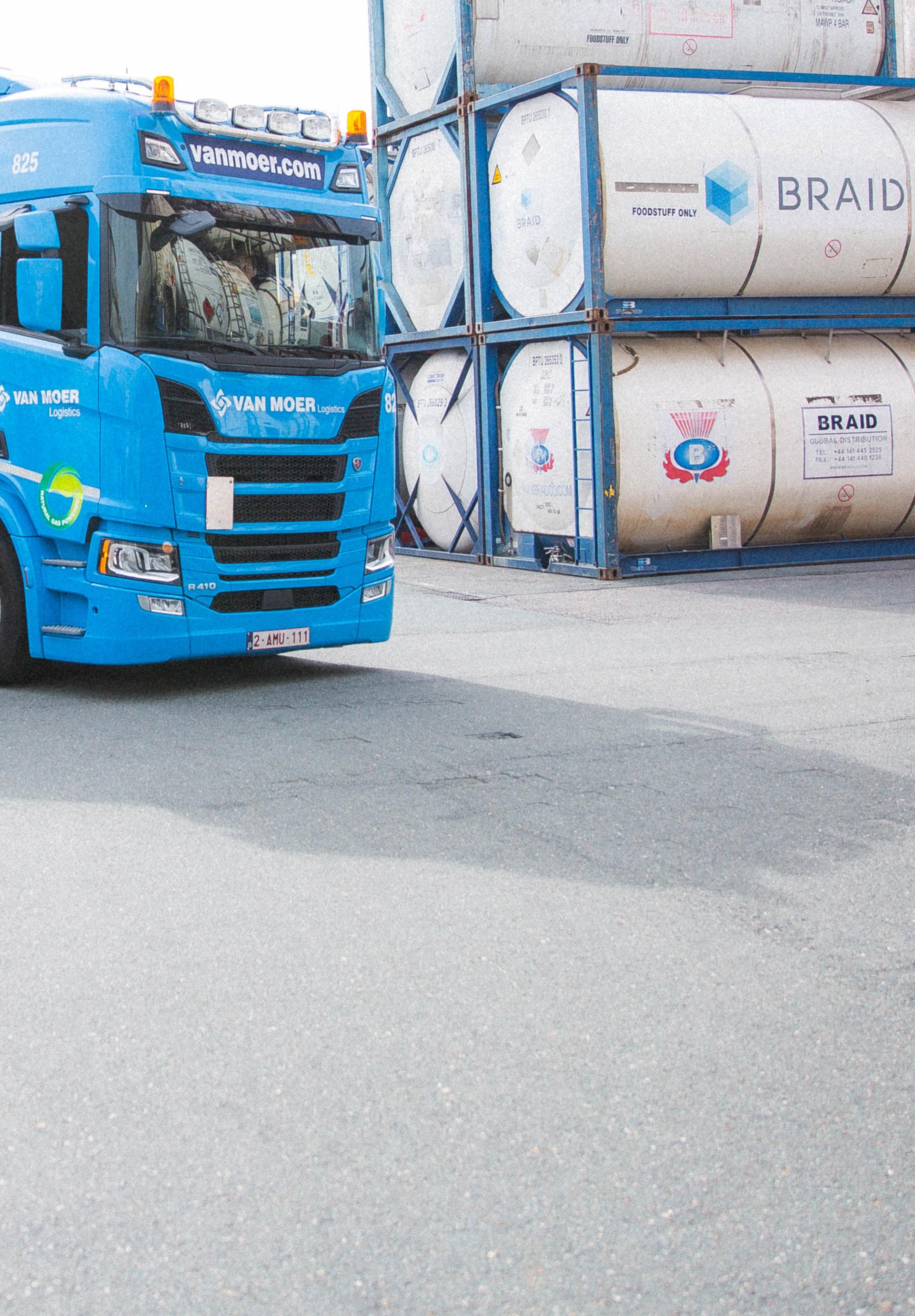
34
Methodological restraints Although the data has been compiled with particular accuracy, this does not guarantee absolute completeness nor correctness. After all, some data are missing for a number of consumption items. Here we have made realistic estimates. This was the case for some data on fuel consumption of trucks in 2020 and the electricity of hybrid cars charged at public and private charging stations. For the third party trucks we use a conversion that assumes 30 litres of diesel per 100 kilometres driven. Because we only have a 50% interest in Antwerp Terminal Operator (ATO), we have also only included 50% of its total CO2 emissions. We will treat other participations in the same way in the future. Despite some limitations and necessary assumptions with regard to the distribution key of the consumption, we can give a wellfounded overview of the total carbon footprint of the business activities of Van Moer Logistics.
The total emission of Van Moer Logistics amounts to 42,199 tons of CO2 equivalents in 2021. We have compared these emissions, by approximation, with the following figures to put this into perspective: 5,024 times annual CO2 emissions of the average European 19,812 return flights from Brussels to New York 4,368 times around the globe by car 3,517 hectares of forest are needed to offset these CO2 emissions
An additional point of attention is the setting up of a central CO2 governance structure. At present, the data is widely dispersed, which makes data collection a time-consuming and difficult task.
Conclusion The fuel consumption of trucks (including charters), industrial rolling stock, cranes and ships accounts for approximately 90% of the total consumption. It is obvious that any investment here can have a major impact. We want to focus on alternative fuels for the trucks to reduce diesel consumption. The focus is therefore on an investment programme to convert the entire fleet to more renewable fuels as quickly as possible.
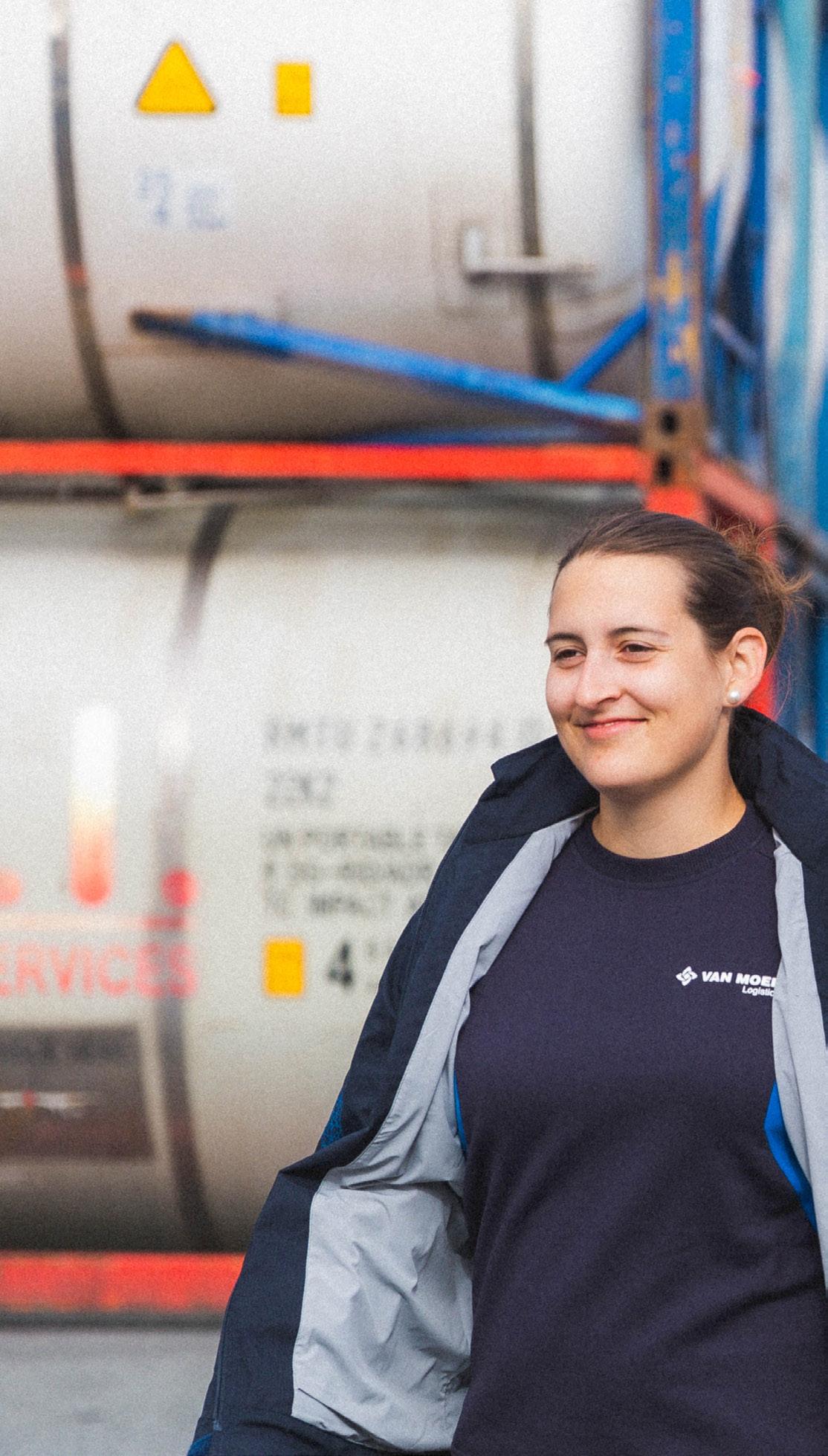




REDUCE CO2 FOOTPRINT Today we are maximally focused on efficiency and reducing our energy consumption. This is how we are getting ready for the European Green Deal.
GOAL 2030 65% CO2 reduction in relative terms by 2030 (reference year 2020)*
* We are currently using turnover as a measure of our total footprint. This can give a distorted picture when inflation occurs. Furthermore, the relative growth of less CO2-in tensive activities (such as warehousing) could distort the overall picture. In the future, we will also compare the sub-activities on the basis of TEU transported by road and water, cleared containers, etc. Moer Logistics - 2. Sustainable and efficient operations
Van
The Green Deal targets for 2030 are achievable through continuous improvement, behavioral change, technological evolution and smart chain management. To become climateneutral in 2050, a lot will have to be done and a real breakthrough will have to be forced. Hydrogen may be the solution. In November 2021, we launched a first pilot project with a dual-fuel hydrogen truck for delivery to Delhaize supermarkets. The truck aims to reduce CO2 emissions by up to 80%. After the 12-month test phase, we will see how the technology developed by CMB.TECH can be rolled out across our entire truck fleet.
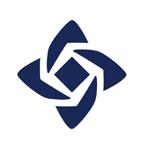
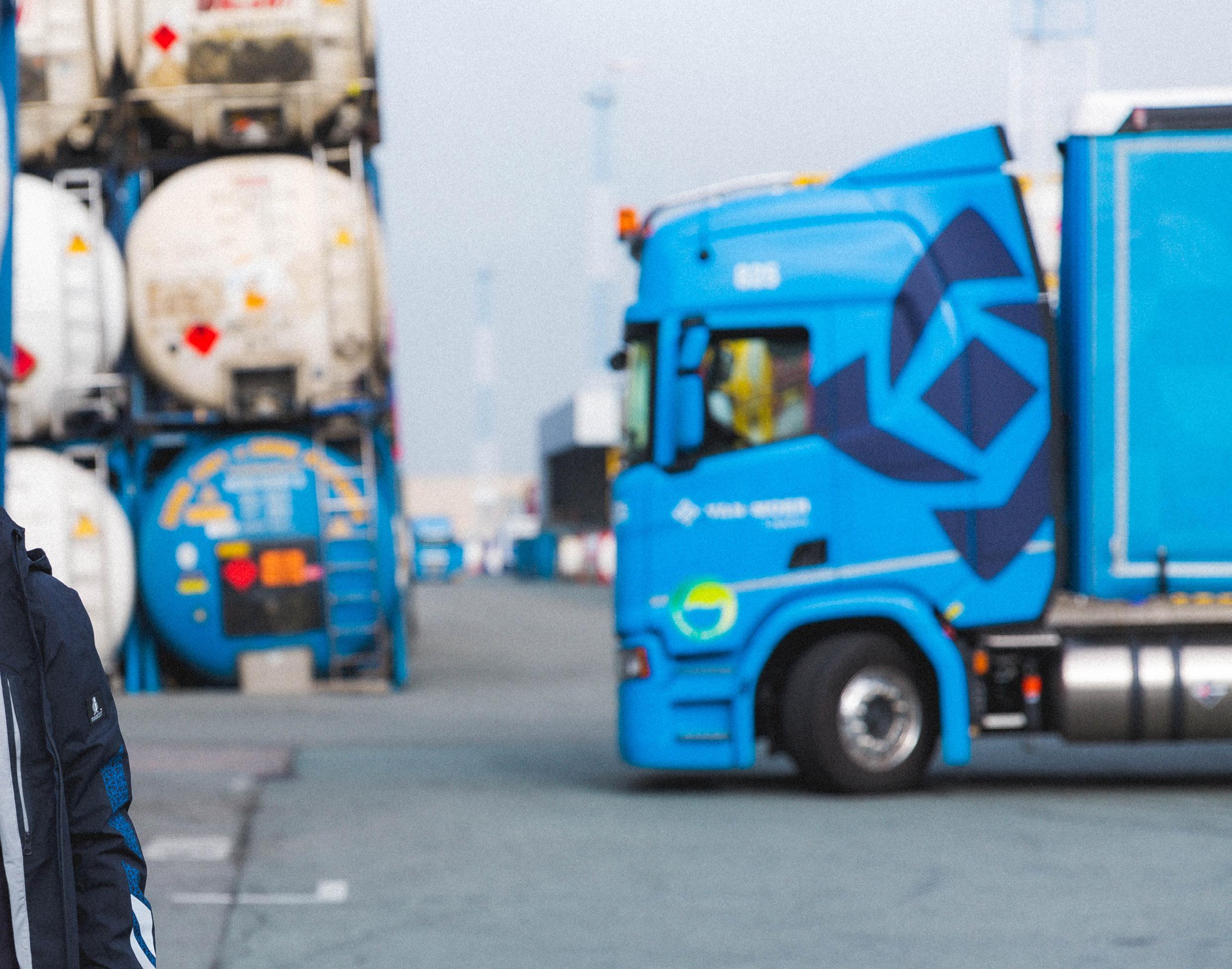
COOBulk&TankContainerLogistics
Green energy To date, we have had a total of just over 11,000 sqm of solar panels installed on the roofs of our warehouses, generating 1,500 MWh per year. About half of the power generated is for our own use, the rest is fed into the grid. In total, 15% of our electricity use is selfgenerated. In addition, we use solar energy from installations on rented warehouses. New investments are currently being planned. With today’s energy prices, this will certainly pay off. In January 2022, we switched 16 sites to green energy contracts. Energy savings We are systematically investing in the energy efficiency of our buildings, warehouses and installations. For example, we are changing all our warehouses to LED lights with motion sensors. This project is 75% finished. We use a lot of appliances with batteries. We can charge these with our own green electricity. For our electric forklift trucks, we have double battery packs. These allow us to drive on battery power in all shifts. Investments in sustainable growth In 2021 we invested a total of 3.4 million euros in our cleaning, heating, repair and storage department. It was expanded and renewed with improved capacity for five chemical, one food and two bulk lanes. A circulation unit for cleaning resins, resins and latex will also be provided. The heating system will have additional connections through a capacity increase of 40 additional fixed positions.
The tanks were already heated by hot water, steam or electricity, and this will soon be supplemented by high-pressure steam (up to 7 bar at 160°C). The heating of ADR and non-ADR products in drums, IBCs or other packaging has recently been made possible thanks to the development of an on-site hot box installation. This is how we respond to the changing expectations and needs of our customers.
Our investments are focused on increasedefficiencyenergyand sustainable technologies: a win-win. IwanDeBlock

37Van Moer Logistics Site Total sqm solar panels kWp MWh / year Property 1054 11,100 1,660 1,500 Our property 1994 14,087 821 781 Rental property 1167 9,580 264 233.1 Rental property Ghent 2 11,778 constructionUnder constructionUnder Rental property Ghent 3 4,516 860.62 33,080.16 Rental property Grobbendonk 14,315 517 493.5 Rental property Brussels 7,850 1,036 936 Rental property GREEN ENERGY DASHBOARD Overview of current and planned investments and initiatives (not exhaustive) • Conversion to green energy contracts at 16 sites (completed) • Energy renovation of the Brussels site and extension of the site with BREEAM certification Very Good • Study for replacement of cooling installation at HAZOP 1167 • Installation of solar panels at site 1793 to cover heating and cooling consumption. Expected power: 1,727.5 kWp • Installation of solar panels at NNRC • Replacement of skylights on site 1143 • Recuperation of condensation heat in the Cleaning & Repair Department • Purchase of electric sweepers • Replacement of three ships by ships with stage 5 hybrid engines • Order for an estuary vessel with hybrid engine • Order for 19 additional bi-fuel trucks (H2 and diesel) • Option taken on 30 full H2 trucks • Switching fleet policy to hybrid and electric cars • Research on own hydrogen filling station at the Zwijndrecht site • Participation in research consortium for hydrogen in Brussels • Bicycle policy (200 bicycles bought already) • Preparation for installation of solar panels at 3 additional locations • New ADR warehouse with BREEAM standard Van Moer Logistics - 2. Sustainable and efficient operations 37
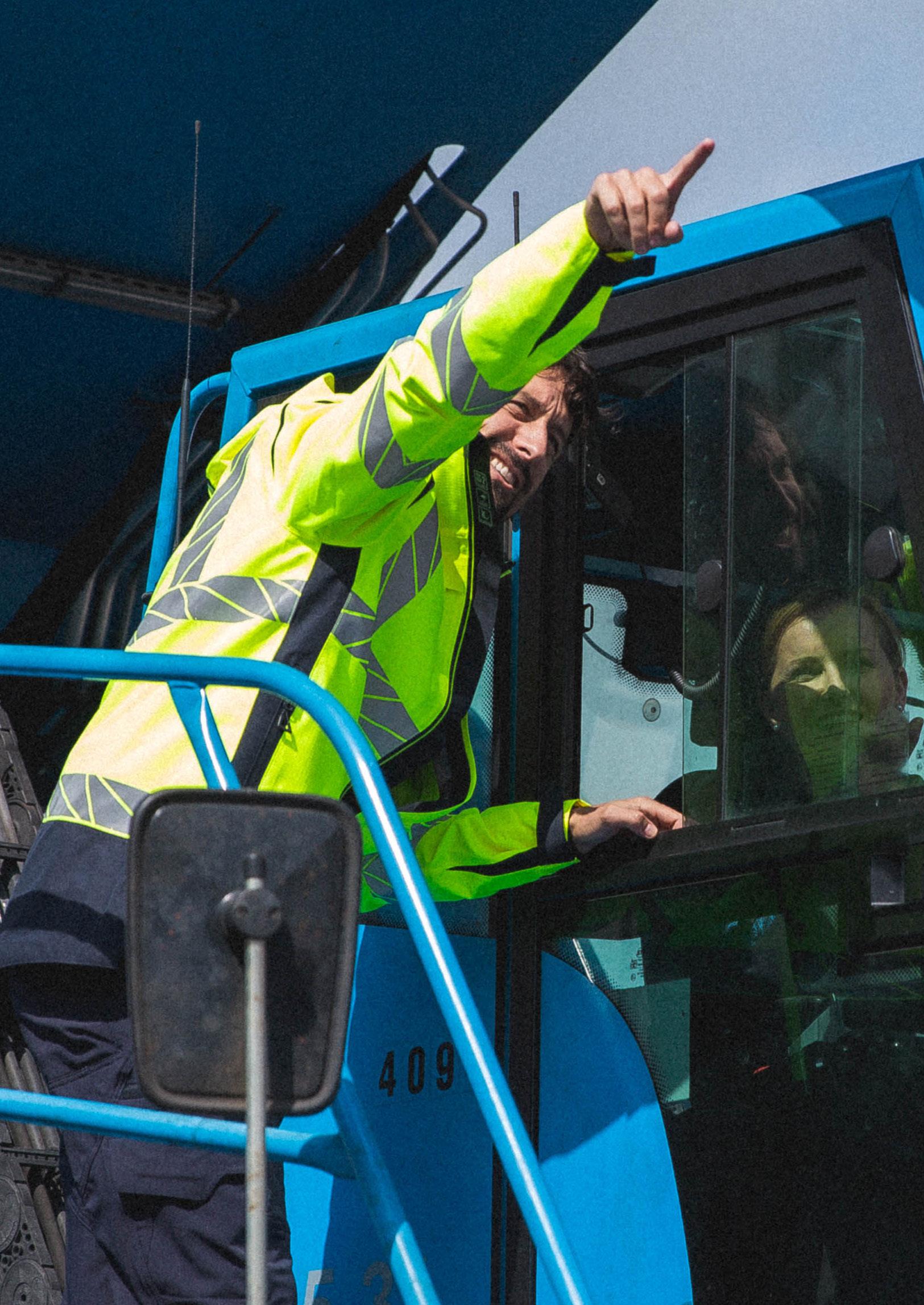
38
CMB.TECH owns a multimodal hydrogen filling station in Antwerp and introduced its prototype hydrogen truck. Thanks to its dual-fuel technology, the truck has several advantages over full hydrogen trucks. The truck has a longer range, is much cheaper to buy and has no loss of cargo space in the Thetrailer.dual-fuel hydrogen truck can add hydrogen as fuel in its converted diesel engine to consume less diesel and produce less CO2. If necessary, the engine can also run completely on diesel. In addition to CO2, NOX emissions are also reduced, by up to -70 per cent, but given the very ecological after-treatment on new diesel engines, this also results in a reduction in AdBlue consumption. By using the existing diesel engine and drive train, we can reduce the investment cost of this truck to 1/3rd of a zero-emission alternative. The dual-fuel functionality is what makes this truck so interesting. The goal is to run 100 per cent on hydrogen, but in daily life on the road, one has to take into account unpredictable factors such as traffic jams and waiting hours. Thanks to the diesel reserve, we don’t have to worry about the truck running out of fuel in the middle of its journey.
The dual-fuel truck In November 2021, we took our first dualfuel truck into service. After the 12-month test phase, we will see how the technology developed by CMB.TECH can be further rolled out across our fleet. The testing of this dual-fuel hydrogen truck is the first step towards a rapid scale-up and roll-out of more similar trucks on European roads in 2022. In the meantime, we have already ordered 19 new trucks of this type.

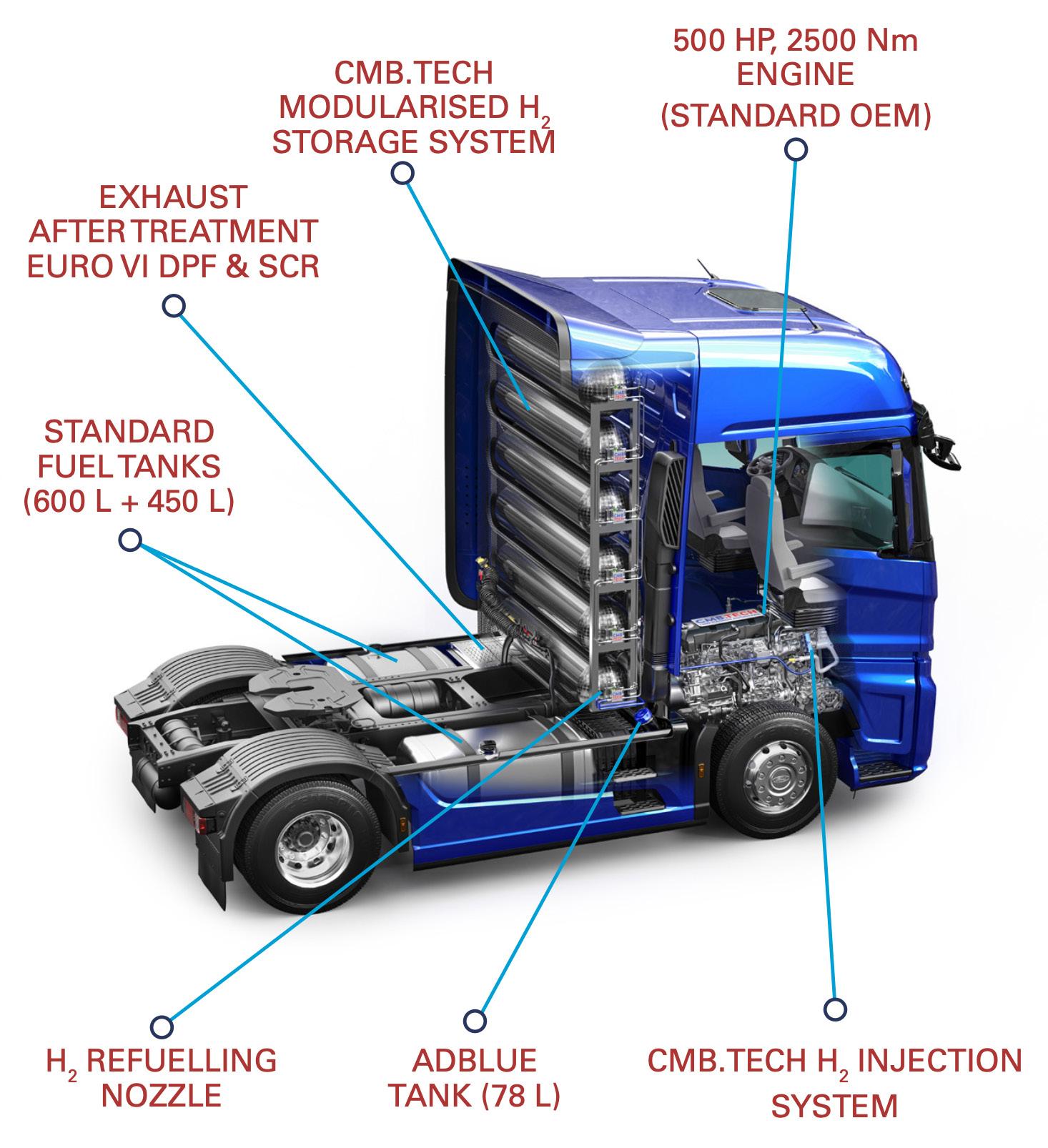
Our dream: our own H2 filling station Together with various partners, we are currently examining the practical, technological and economic feasibility of switching to hydrogen for the most part in the coming years. In this way, we can become the partner of choice for CO2-neutral supply chains and distribution. We want to evaluate whether we can supply our own green hydrogen. Therefore, together with some partners, we launched a lowcarbon multi-fuel Energy Hub concept that will supply all three fuels from the same "station".
The first focus in this project is on H2 trucks. We are looking for an "on depot" electrolyser solution to refuel the 20-30 H2 trucks. The second focus lies on the rest of the truck fleet, converting the LNG trucks to biogas/bioLNG/ landfill gas. The University of Antwerp is monitoring the project. In concrete terms, this project could result in a filling station at our site in Zwijndrecht, where green hydrogen, green electricity and biogas can be generated. Its realisation depends on the granting of European subsidies.
Fingers crossed! Van Moer Logistics - 2. Sustainable and efficient operations
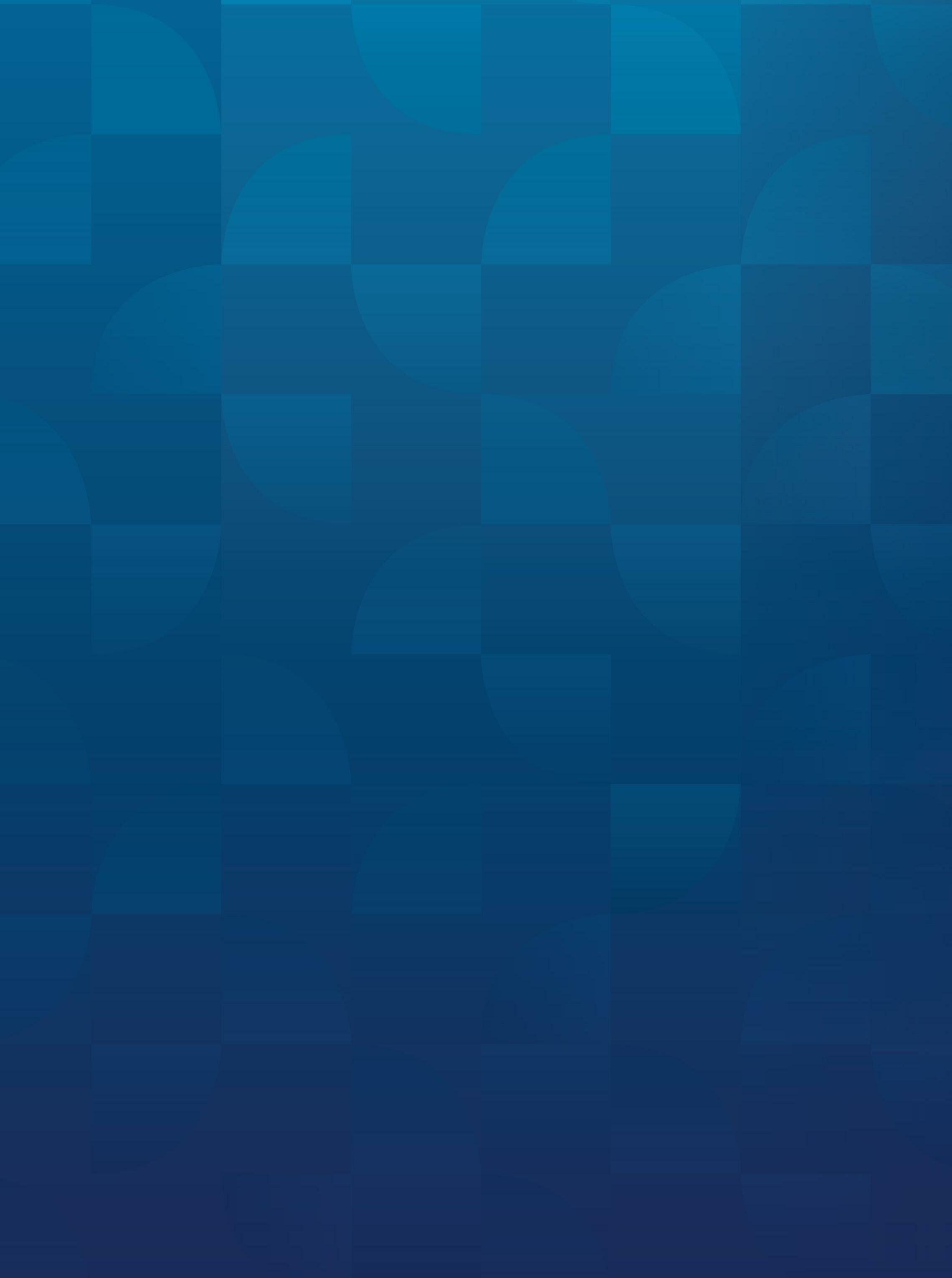

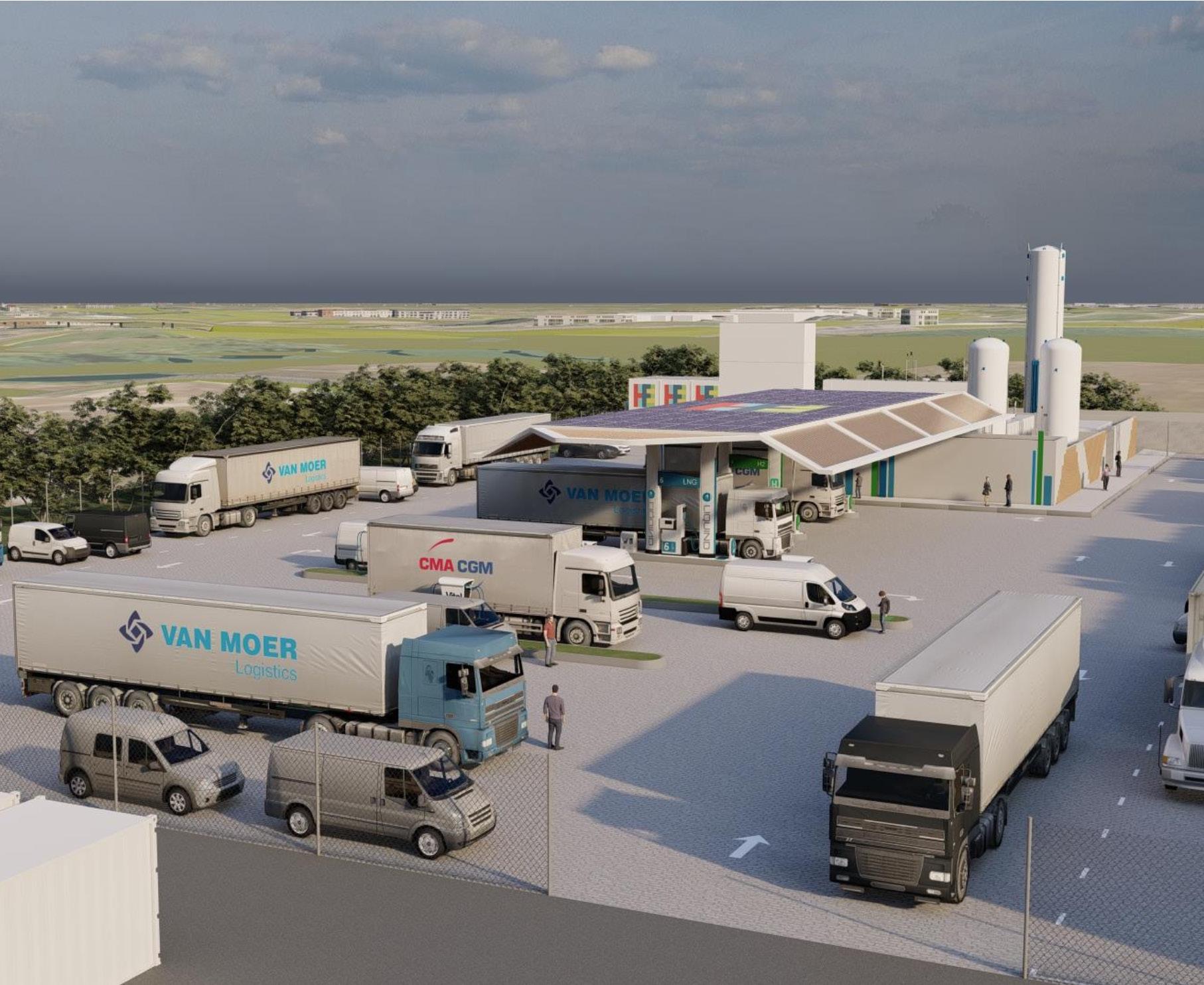
GOAL
Extend the companiestomanagementenvironmentalsystemthenewlyacquiredandsites
More sustainable fleet We are continually investing in our fleet. All our trucks have a EURO 6 engine, which is mainly reflected in less NOx and fine dust. Of course, we take fuel consumption into account when making our investment decision. There are considerable differences between the various manufacturers. Our fleet now comprises 41 LNG trucks and 1 dual-fuel hydrogen truck. We monitor the fuel consumption of our fleet very carefully. By monitoring several parameters, we can make our drivers aware of the impact of their driving behaviour on actual fuel consumption. The measuring equipment installed in the trucks keeps track of data on cruise control, average speed, hard braking, idling and of course average consumption. We are also trying to make the industrial rolling material in our warehouses or on our sites more sustainable, to continue the trend towards green energy. Today, 80% of our fleet of industrial rolling material is electric. We always choose ‘A’ brands for our rolling material, which are often already much more sustainable than ‘B’ brands. Besides consumption and performance, the quality of the machines and the after-sales service are very important to us. We divide our entire fleet of industrial rolling material (+300 forklifts) between a handful of ‘A’ brands. When buying, we always ask for input from both unit managers and forklift drivers. It is important that they are satisfied with the vehicles they drive. 2023-2024

We have an ISO 14001 certified environ mental management system. Our focus is on monitoring and evaluating environ mental performance, proactively informing employees about the company’s environmental policy to encourage them to pay attention to it, and freeing up budgets to make investments that reduce the environ mental impact of business activities.
• Sewage screens to filter out plastics
• Site fence with cast jerseys to keep plastic on site
• Contract for monthly sweeping by a specialised company
REDUCE ENVIRONMENTAL IMPACT
• Toolboxes to make employees aware of processes and procedures
• Pallet turners to replace damaged bags without loss
• Permanent maintenance teams appointed for maintenance, order and tidiness
The Port of Antwerp is one of the main production and logistics centers for plastics in Europe. Unfortunately, small plastic pellets sometimes end up in nature during production, storage, transport or processing. To combat this, Port of Antwerp together with Plastics Europe, Essenscia and Voka Alfaport launched the Zero Pellet Loss platform. The platform serves to support clean-up activities in the port area, exchange best practices and give substance to the concrete action plan to combat the loss of pellets. Operation Clean Sweep is an international program to prevent the loss of plastic pellets and their release into the environment (pellets, flakes and powders) during treatment by the various entities in the plastic value chain. We have signed the charter. This means that we are committed to the working group and that we take measures at our sites. Some of our actions and/or investments inclu de:
• Purchase of electric sweepers on various sites
• Sensor loading systems that prevent product from overflowing manholes
Van Moer Logistics - 2. Sustainable and efficient operations
• Procedures in which loaded trucks are completely blown clean to keep plastic granules on site
Zero pellet loss
• Repaving to smooth surface = better to control and easier to clean up pellets
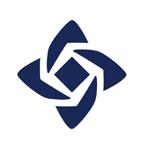
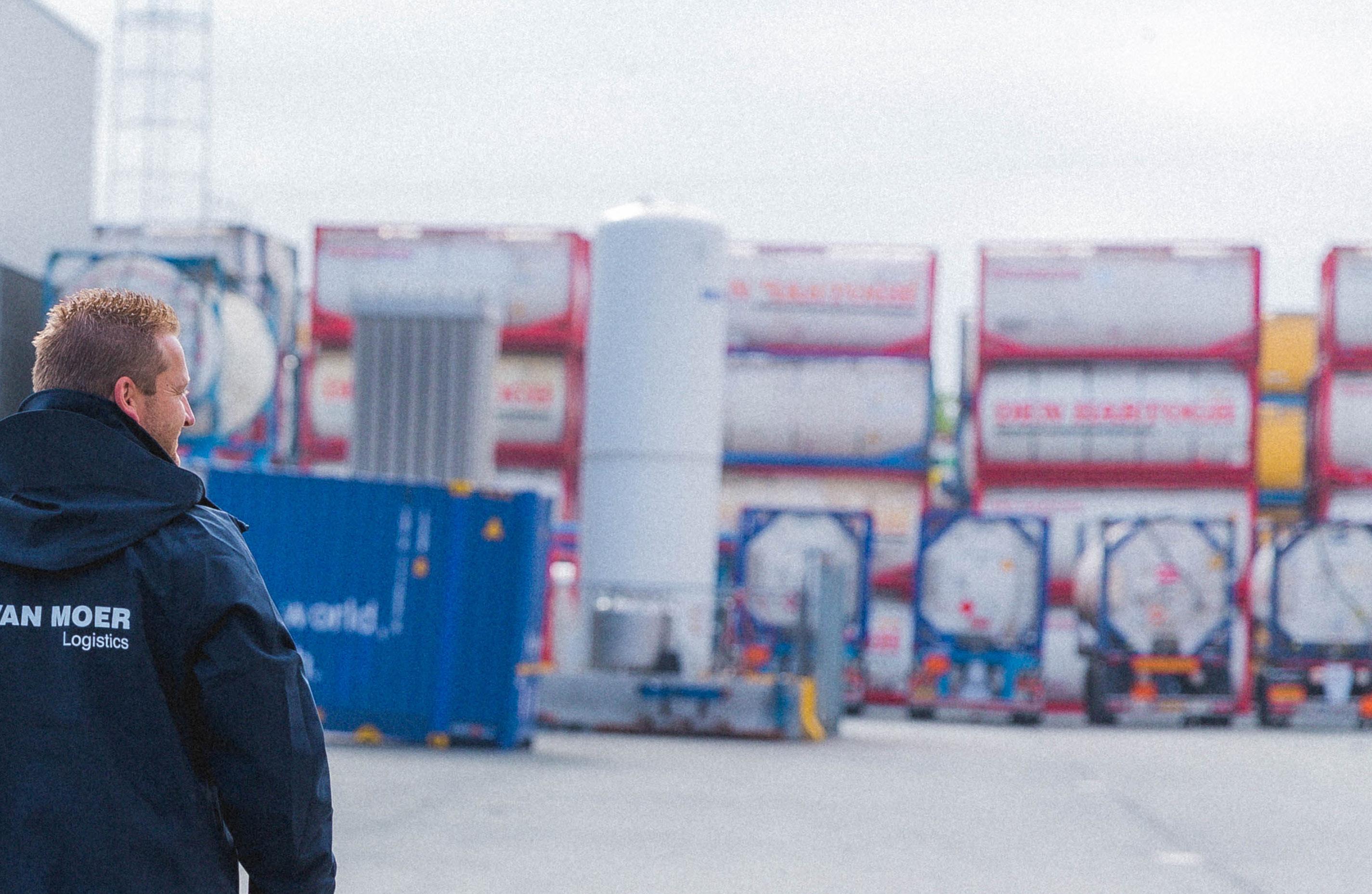
All activities related to the facilities of our sites are monitored centrally. Due to rapid growth and many acquisitions, the priority today is the standardization of contracts, maintenance and working methods. Within our ISO 14001 environmental management system, there is also a waste policy for all our sites. With re gard to cleaning, in 2021 the focus was on more organic and ‘green’ products. We like to keep it clean Several times a year we clean up the compa ny surroundings. Despite the many trash cans and facilities for truck drivers along the roads in our neighbourhood, there is still too much littering. By cleaning, we ensure that fauna and flora, and in particular the many birds, rabbits and toads, are not impacted. In this way, we contribute to biodiversity in our highly industrialized environment. Minimizing nuisance
Water treatment At our site in Zwijndrecht, we clean chemical containers. Because of this, our site is also recognized as a Seveso site. This implies a whole series of obligations that we follow up on meticulously. We guarantee that all our wastewater is fully treated and returned to nature. We have invested in a VISOP water treatment system that works by flotation. Facility management
Recycling We are strongly committed to recycling in order to recover as much lashing material as possible. The material removed from import containers is reused for the export of goods. We reuse airbags, straps, buckles, wooden plates and pallets. Last year, we set a target to reduce nonseparated waste by 10%. In 2020, the total amount of commercial/sorting waste was 386,58 tons. In 2021, the total amount of commercial/sorting waste was 345,082 tons. This is a decrease in absolute figures of about 12% due to better sorting. The fact that we achieved this in a year in which we again grew strongly makes us feel satisfied. It is our people who do their best every day to sort well that have achieved this result. Our neigbourhood is pleasant again to live, relax and sleep in. We are impressed by the constructive feedback, the initiative and the shortterm adaptability of Van Moer Logistics. We would therefore like to thank them sincerely for their efforts and we hope that other transporters will follow.
We are aware that transport and logistics can cause inconveniences. We try to deal with this in the best possible way. An example is the Dennie Lockefeer Container Terminal in Grobbendonk. The site was not without controversy because of noise pollution for local residents. At one point the terminal was even shut down for this reason. When we took over the site, we got in touch with the neighbourhood committee. Our CEO Jo Van Moer himself goes to the meetings. We believe that economic activity can happen in harmony with all stakeholders. In situations like this, we put ourselves in the shoes of the person sitting at the consultation table with us. In this way, we understand and do everything possible to reconcile seemingly conflicting Weinterests.have done several investments and optimizations at DLCT Grobbendonk and are also working on the awareness and behaviour of people on the site to reduce noise pollution. The next step is the construction of an embankment with a noise barrier. This screen must ensure that the noise pollution caused by the loading and unloading of containers remains within the legal norms.
G.R.Localresident
42
Van Moer Logistics - 2. Sustainable and efficient operations
Thanks to several counts by local residents, it was established that a large number of the lorries were from our company. It concerns a flow of containers between a distribution centre in Grimbergen and the Cargovil site in Vilvoorde. A resident sent a personal e-mail to Jo Van Moer. We contacted Unfortunately,him.we were unaware of the si tuation and did not hesitate a second to enter into dialogue. In consultation with them, we put the problem on the table of our local department and our partner in Grimbergen. We believe it is very important to build and maintain a good relationship with all our stakeholders. For us, this is also an element of sustainable business. Since October 2021, our trucks have been following a new route to transport the con tainers to and from the distribution centre.
In collaboration with a customer, Van Moer Logistics has mapped out a new route to reduce traffic nuisance in Grimbergen. To the great satisfaction of the local residents ... Since the end of 2020, the inhabitants of Groot Grimbergen have experienced inconvenience caused by freight traffic in their neighbourhood. 612 families signed a petition with an explicit request for slower and safer goods transport in Groot Grimbergen. Some residents also contacted the local government to raise the problem, but unfortunately those discussions led to nothing.
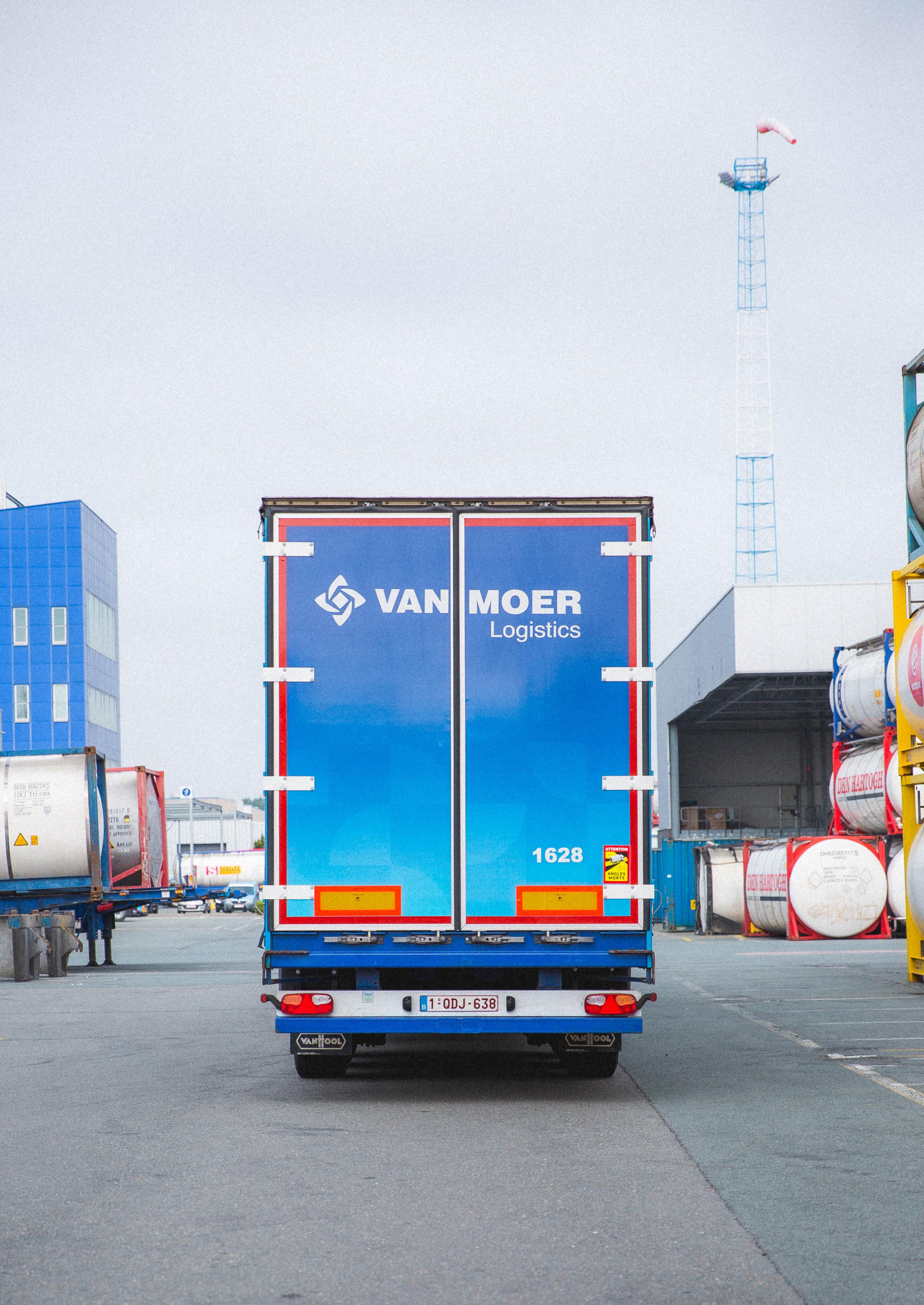
44 our processes. We can use them to guarantee our service levels and learn a lot from them. Drop & Swap services An example of a process improvement are the shuttle services. At several hubs, we already work with a shuttle system. Here, drivers can simply pick up their trailer and immediately take another one with them. In this way, they do not have to queue up to load or unload and they can do what they like best: driving. Our warehouse staff can also control their planning better and work more efficiently, because the work no longer comes in waves, but always at the same pace. GOAL 2022-2023 • Van Moer goes paperless: 50% fewer companywideprintsper year • 10 vertical integrationsstakeholderby2023
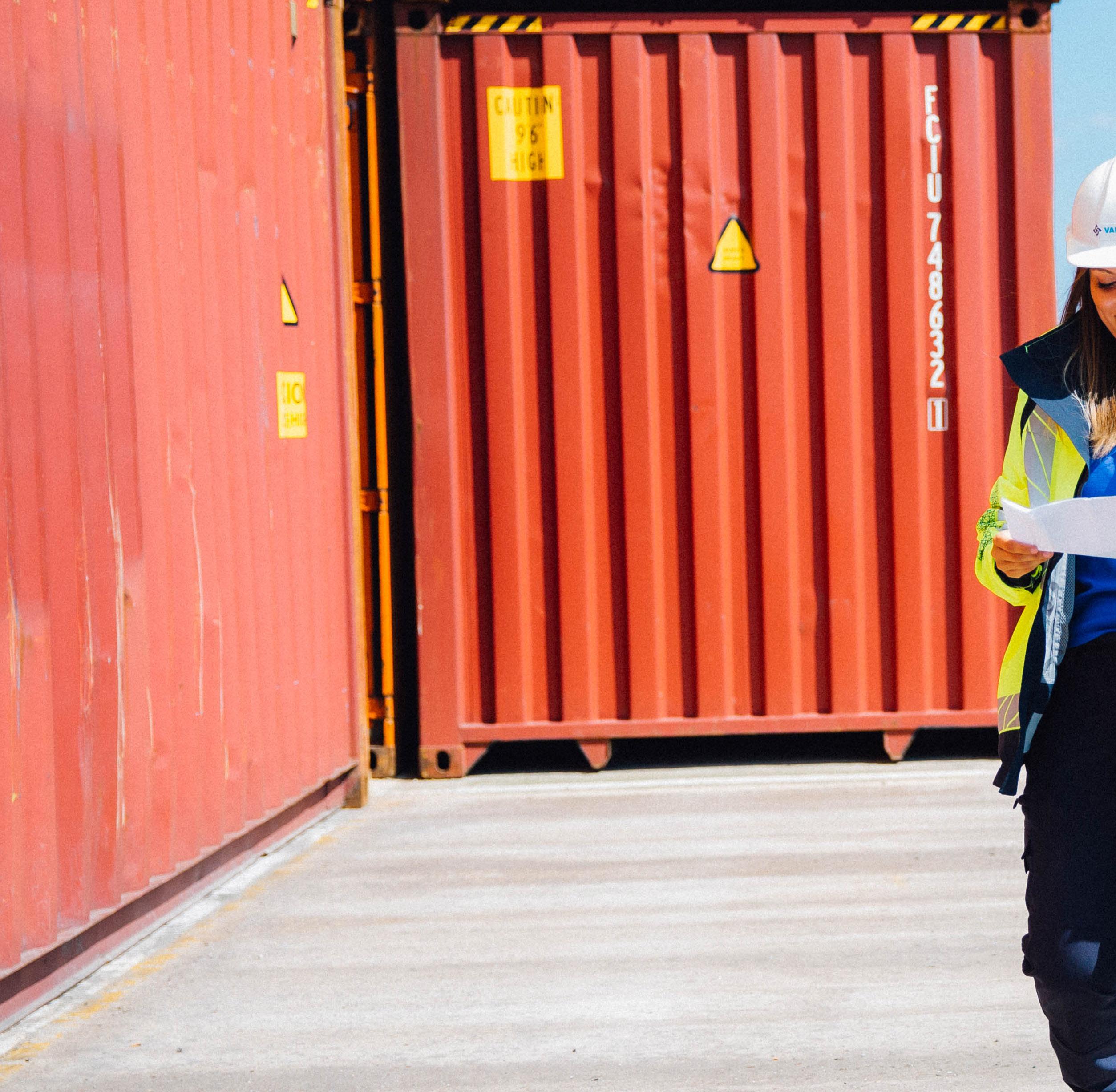
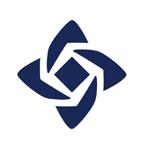
operations
operations
is
operations
45 We have streamlined our waste policy and now work with a select group of partners at our various sites. The decisive factor in choosing the partners was the guarantee that our streams would be recycled to the maximum
partnerships. We also offer
processes.
questions
our customers
Dannyextent.Cleymans Preventionadvisor At the end of 2021, we were one of the first companies to take part in the SQAS audit under the new standard. Our CO2 measurement and reduction plans and the Operation Clean Sweep initiatives received special praise.
to really
solutions
Van Moer Logistics - 2. Sustainable
DID YOU KNOW We continue to strengthen our quality services and encourage the
ShannaStuer Qualitycoordinator team approach as advisors and help optimise This highly appreciated in the close tailor-made to who have about the carbon footprint and sustainability of the we carry out specifically for them. and efficient
customers
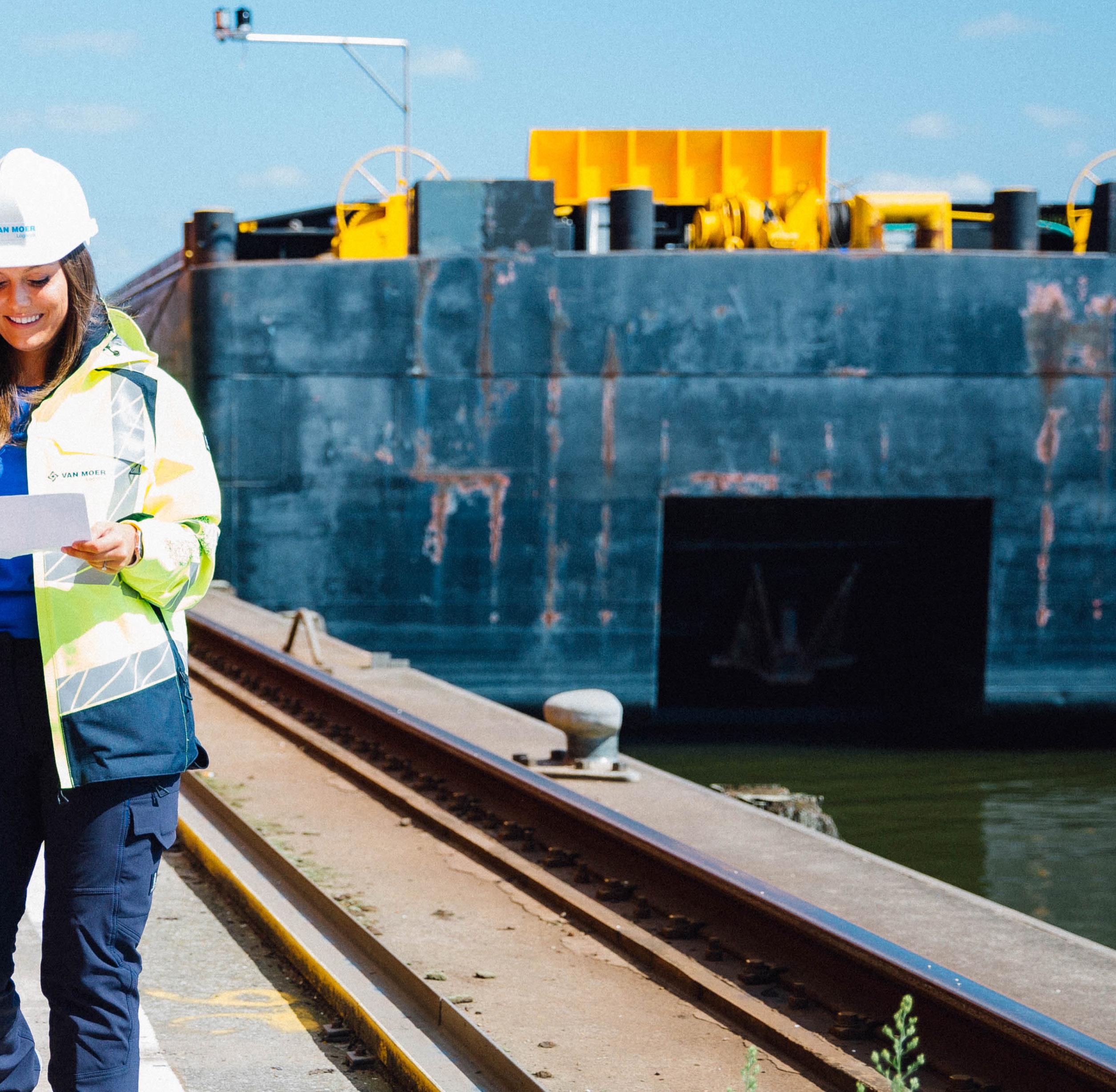
GOAL
Strive for departmentsmonitoringmonthlyofallthrough QESSHCustomer-dashboards focused Decision-makingFlexibleIntegratedapproachprocessbasedonfactsActionPartnership Communication Motivate * The 8 building blocks of our vision of quality
46
QUALITY With us, quality is more than a department, it’s an attitude. We ensure that customers are satisfied, we want to exceed their expectations and prevent future complaints. Our quality department is closely linked to the daily operations. By quality, we mean the delivery of products and services according to the expectations of the supplier and customer and according to the requirements of the sector, and this to the satisfaction of the customer. To ensure that the desired quality, both in terms of method and services or products delivered, is also achieved, we have a quality management system. This system is ISO 9001 certified. Our quality department is at the heart of the business-to-business and is also the customer’s guide. It participates in the preliminary process to ensure that we can keep our promise of value-added logistics. Monitoring and data analysis are essential here. We use KPI dashboards that are drawn up together with the customer. As a result, we see a significant improvement in performance and tracking. In many cases, we go through these dashboards with the customer on a monthly basis and together we look for the reason for certain fluctuations. Where possible, we adjust procedures. In this way, quality becomes a form of partnership. Quality must also motivate. That is why we use a dashboard to monitor checks that are linked to JO-ker points for our employees. In those checks, quality and safety are measured together. The JO-ker points can be saved up and exchanged for nice rewards. 2022-2023
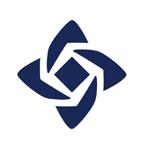
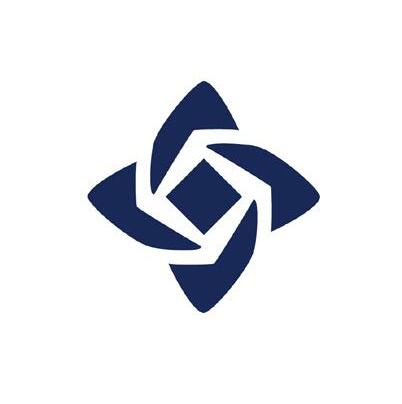
QESSH DASHBOARD month 1 month 2 month 3 Number of tours made by prevention officers l l l Objective: 2 tours per month Number of 5S checks per supervisor l l l Objective: 1 tour per month Mystery topic l l l Objective: topic dependent Frequency rate (FG) l l l Objective: 0 Severity rate (EG) l l l Objective: 0 Number of unsafe situations reported + near misses l l l Objective: based on FG+EG last month HSE action management l l l Objective: max 15% open actions with expired or no deadlines Traceability l l l Objective: 100% of goods at correct location Action management Q l l l Objective: max 15% open actions with expired or no deadlines Average score KPI customer dashboards l l l Objective: Completeness>75%of checklists l l l Objective: 10 checklists completed correctly Our quality level is one of the most important aspects by which we can distinguish ourselves from our competitors in the sector. It is therefore of great importance that there is a critical focus within the group on measuring and evaluating these parameters. In this way, we can respond proactively and continuously improve so that we can build a stable partnership with customers.our JonasFiers QESSHManager l l l l Extra JO-kers through Blue Diamond appreciation policy Can be improved Insufficient On hold Van Moer Logistics - 2. Sustainable and efficient operations

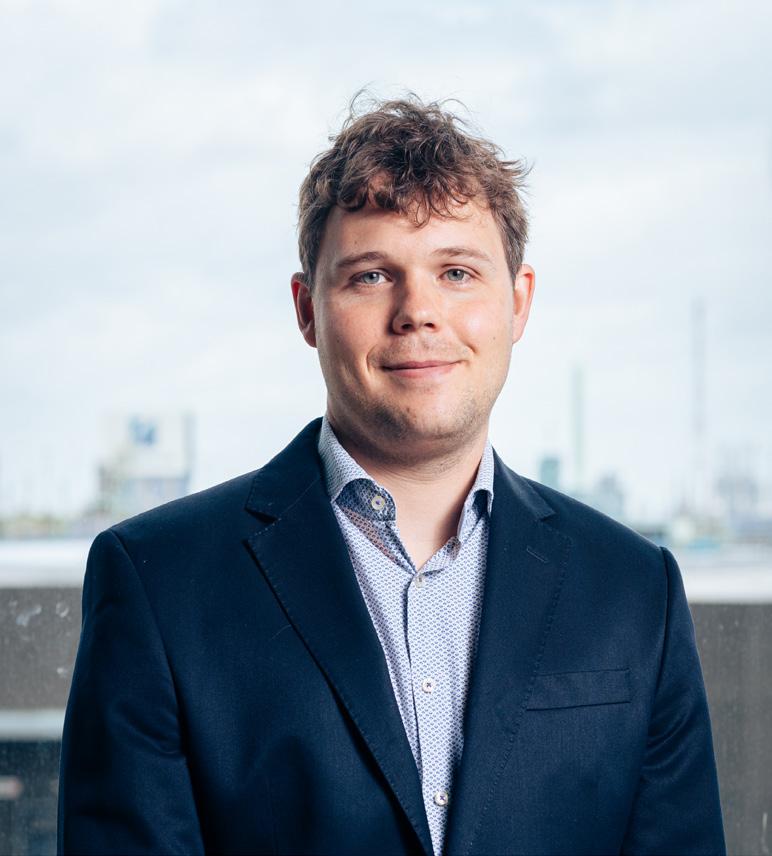
• Achievement of the targets set for frequen cy rate and severity rate in 2022 (see page 50) • Evolution to level 4 on the safety ladder for all departments in 2025
*Data available on July 4th 2022
48
AND
EDUCATIONSTRUCTUREAND TRAINING DIVERSITYCOMMUNICATIONNO-NONSENSE 3. COMMITMENT
SAFE
SAFE WORK Safety is a prerequisite to work. However, safety is also a verb. We must work on it every day. Our safety department consists of prevention advisers who are actively involved in operations. They ensure that everything is done according to legal standards, they check whether inspections are in order and they make sure that everyone always has the necessary training to operate the equipment used or to drive vehicles. The diversity of our sites, activities and employees makes this a particularly challenging task. Since 2019, our processes in the area of safety have been ISO 45001 certified. With the Antwerp port companies and the employer organisation CEPA, we have signed the Safety and Health Charter. We commit to making the necessary measurable efforts to avoid fatal occupational accidents and to re duce the frequency rate and severity rate of accidents. We commit to: • Cultivate safety awareness in our company; • Create a safe and healthy work environment; • Actively participate in safety initiatives of the Antwerp port companies and the CEPA employers’ organisation. Our goal: We are a family business and a fa mily of employees. Our people are our most important asset. We care for each other and want to provide a safe and pleasant work environment. In doing so, we make five commitments: WORK OPEN CULTURE FLAT TO PEOPLE AND SAFETY GOAL 2022-2025
-
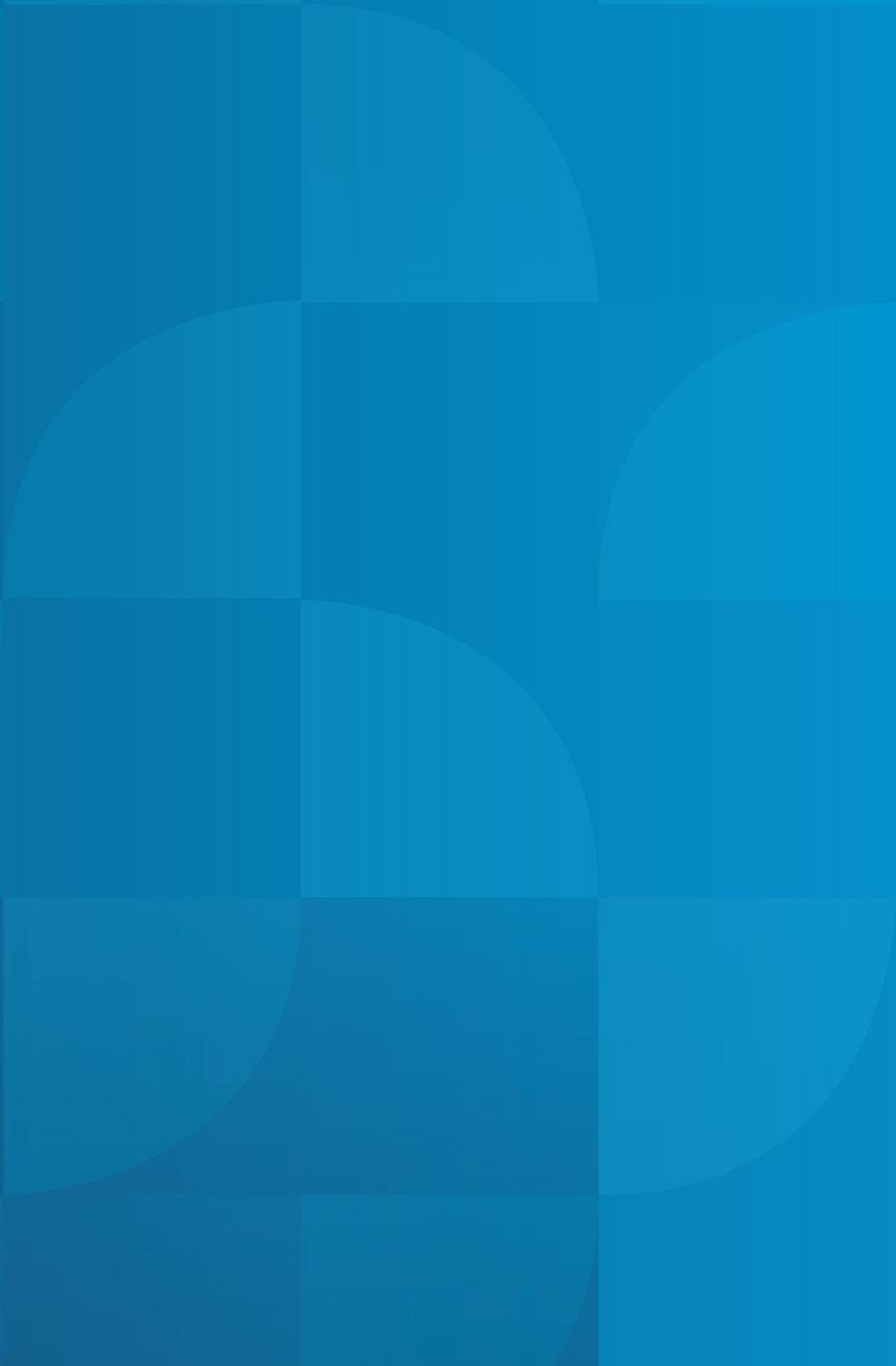
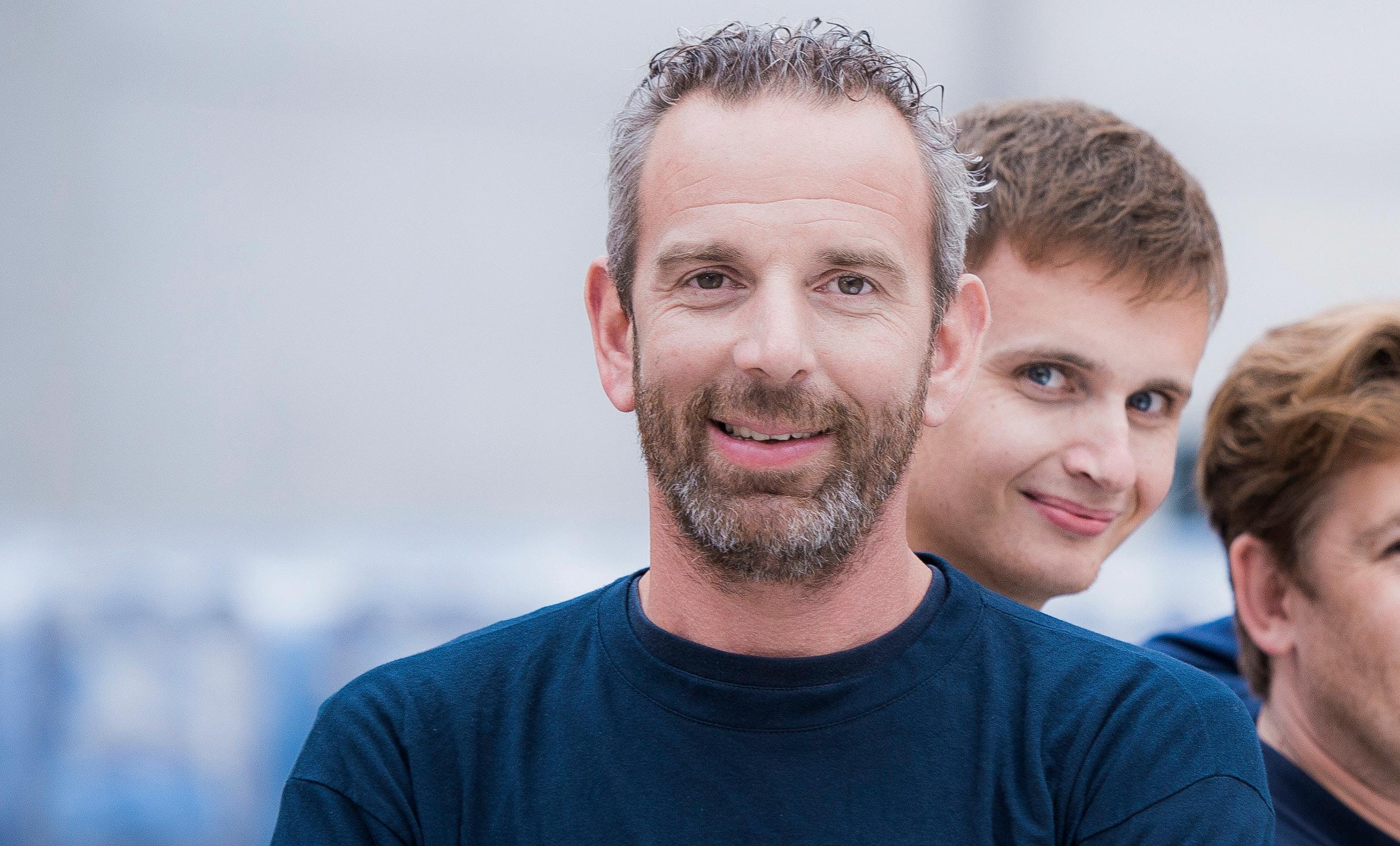





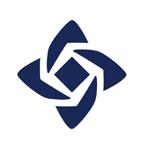
CALCULATING We have systems in place to manage known risks and hazards. Safety gets a lot of attention. We proactively look at what we can still improve. PROGRESSIVE We do it safely or we don’t do it at all. Safety is fully integrated into every process. Level 1 Level 2 Level 3 Level 5 Van Moer Logistics - 3. Commitment to people and safety Anticrash alarm To ensure maximum safety, we equip all our forklifts with anticrash alarm systems. In this way, we hope to reduce the number of accidents to a minimum. In the Antwerp port area, there have been three serious accidents involving forklift trucks in the last twelve months, two of which resulted in fatalities. We still have too many accidents, even though we are one of the best performers in the port. But every accident is one too many and we need to do something about it. Six years ago, we had a fatal accident with a forklift truck and we don't want that to happen again. That's why we're equipping our 335 forklift trucks at ten sites with a digital system that will warn them if a hazard or collision is imminent. You can compare it to the display and alarm when you park your car. At the same time, the 600 employees in the warehouses are given a smart bracelet that starts to vibrate when a forklift gets too close or threatens to hit Thethem.system, made by the Belgian company Rombit, also registers the driving style, so that we can provide feedback to the drivers. They will never again be able to get into a machine without training. The investment involved is EUR 2 million. We are not saving costs on safety.
Safety Jack Safety Jack is our mascot. It refers to the legendary fox Reinaert that once haunted the Waasland region. Safety Jack is cunning and smart. Safety Jack is always on his guard, thinks about every situation and always uses the right PPE. Safety Jack is everywhere. Safety culture In 2020, we started a comprehensive process to improve our safety culture. We are trying to make safety a genuine attitude among our employees. They have to organise themselves daily, help each other and ensure correct com pliance with regulations. In 2021, we adjusted our organisation and expanded the core de partment on safety. We now have a contact person per business unit for safety, environ ment and quality. We have not yet succeeded in reaching the extra step on the safety ladder in all our de partments, but we are working on it. PATHOLOGICAL Ignorance is bliss. REACTIVE When something happens, changes are made ad hoc, but the impact is short-lived.

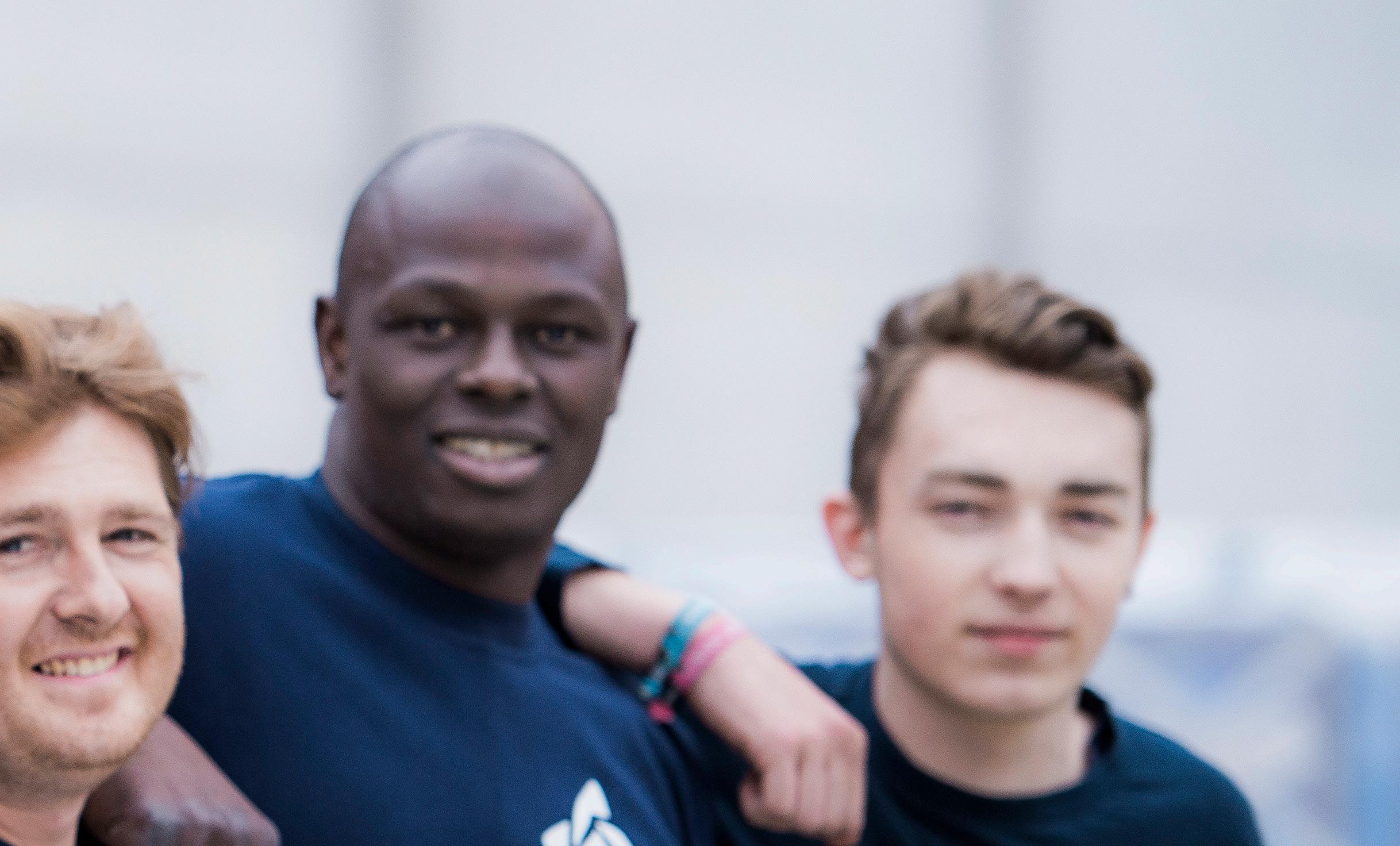
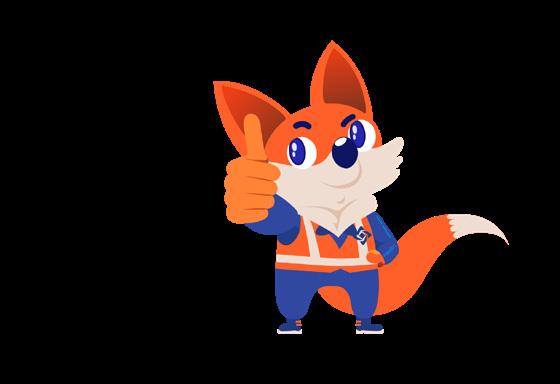
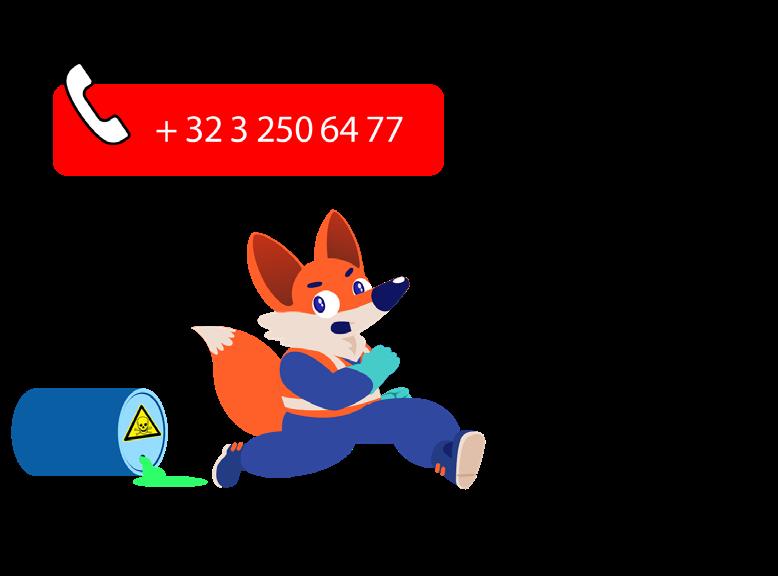
Bulk & Tank Container 3.36 0.7 0.27 P&I 0.52 0.69 0.25 Warehousing 1.15 0.55 1.07 Transport 1.56 0.5 0.52
Our drivers are our ambassadors on the road. They have a great responsibility. New drivers receive training from us and are assisted by a driving instructor. We help them through the driver’s manual, which is also available through the internal communication app. Even after their start-up period, we continue to guide them intensively. On their behalf, we organise the blue driver challenge (control marathons at frequent intervals once every two months) and frequent driver meetings where they meet to discuss daily matters and safety. More than 80% of our trucks are equipped with intelligent sensors and measuring systems. This allows us to provide monthly individual driving style reports to our drivers with some basic parameters, an overview of damage, fines, braking behaviour, speed and idling. Depending on the trip profile, we can thus see whether a driver is exhibiting inefficient or careless driving behaviour. Good behaviour will also be rewarded with JO-kers. Since recently, the drivers can also see the earned JO-kers in the communication app. We hope that this will stimulate them even more to set a good example. 2021FR 2022Target May 31, 2022) 2021SR 2022Target May 31, 2022)
To be able to work in a structured way on our safety, we have developed a system that is motivating. Our reward system with JO-kers (a pun on the first name of our CEO Jo Van Moer) rewards the team effort with a form of competition between managers and workers. With the JO-kers, you can order products such as toys or kitchen appliances. The follow-up of this system is done through dashboards that contain specific criteria for all departments.
BU
Current si tuation 2022 (until
If I have any doubts about safety, I seek advice first. I always set a good example. I think for another and speak to them about their unsafe behaviour. I always wear the correct personal protective equipment. If it cannot be done safely, then we do not do it.
We have eight basic rules for safety. It is very simple: if it is not safe, we don’t do it. I only drive a machine if I have the proper certificates and attestations. A safe vehicle is placed in service, inspected and visually in order. I have the right and duty to stop an unsafe situation.
Bulk & Tank Container 73.60 18 28.58 P&I 83.92 23 53.10 Warehousing 48.22 27.06 34.98 Transport 98.58 22.31 10.74 Frequentiegraad van ongevallen Frequency rate of accidents Severity rate of accidents BU
Monitoring safety efforts
8 basic rules
Current si tuation 2022 (until
Monitoring of our drivers
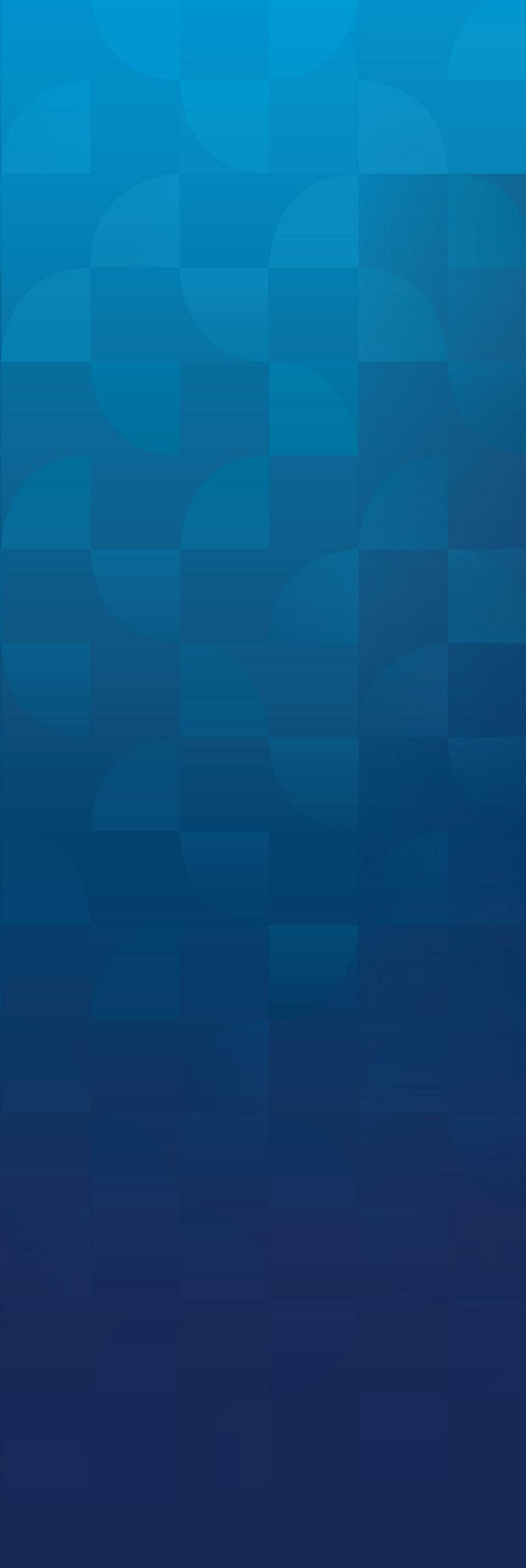









GOAL 2022-2023 Pro-actively stimulating internal developmentcareerpaths with a minimum of 5 per year It is our people who make the difference and ensure that we live up to our reputation as a reliable,logisticsvalue-addingplayer. Our flexibility and the nononsense mentality to deliver results is highly appreciated by our customers.
OPEN CULTURE AND FLAT STRUCTURE We have an open culture and a flat structure, where everyone is accessible and approachable. We offer every employee who is able and willing to do so the opportunity to grow in expertise, roles and tasks. We are careful to maintain our flat and agile organisational structure. In this way, everyone is approachable and we keep in touch with each other. By not creating too many levels, we remain a very agile and flexible organisation. There is an open atmosphere and a culture of trust. Initiative and entrepreneurship are always appreciated. A flat organisational structure also means that there are few management layers. As a growth company, everyone helps to create the opportunities and promotion possibilities of tomorrow. This means that some people evolve spontaneously into more managerial roles. We see the growth of our people primarily as a combination of personal development, the focus on specific projects and the gradual assumption of other roles within the same or other services or business units. All our vacancies are made available internally. We speak to every internal applicant. After all, by applying, they are indicating that they want to grow or do something else. Sometimes there is no match with the job, but these interviews often lead to other opportunities within the company. In this way, we ensure internal mobility throughout the organisation.
Van
StevenPauwels COO Warehousing& Value-addedLogistics Moer Logistics Commitment to people and safety
- 3.
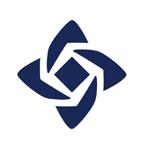
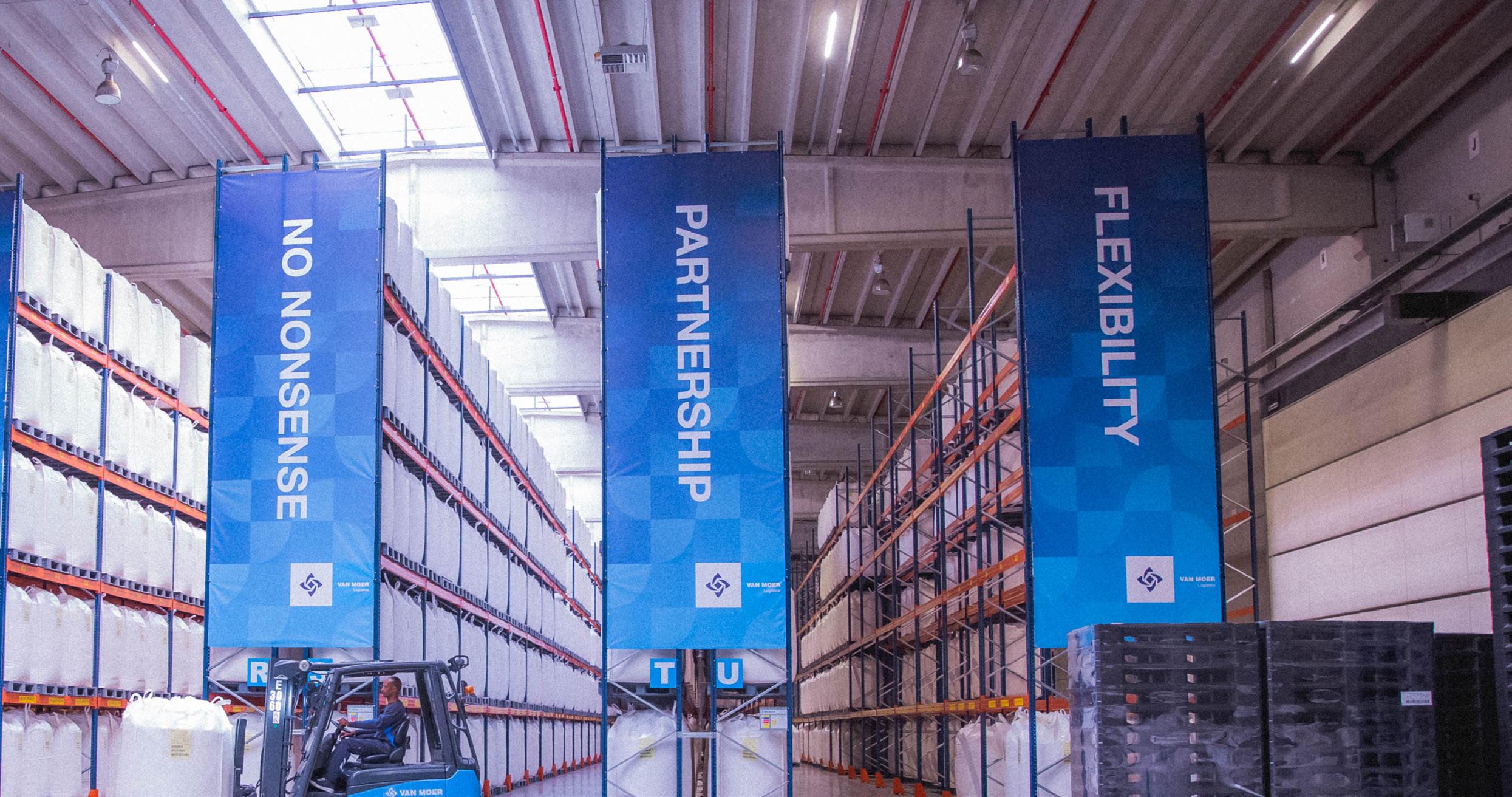
• No-nonsense: what you see is what you get. Our horizontal and open organisational structure keeps us with both feet on the ground.
• Flexible: we like to think out-of-the-box. We offer a wide range of solutions and always look for the perfect fit for each customer.
80% of our employees do not work at a desk. They too must feel involved. That is why we invested in a communication platform that is accessible to everyone via an app. This way, everyone is informed just as quickly and in a clear and uniform way.
Values are central We don’t put our values on the wall, but we live by them. They are the core of our DNA
• Enthusiasm: enthusiasm is contagious and our enthusiastic employees are our best ambassadors. Our employees take initiative.
• Partnership: our goal is to build sustainable long-term relationships with our customers and employees.
• Make a difference: we never give up. Where others walk away, we just battle on. That’s why we invest in the talents of our employees, so they can meet any challenge.
FelienVanOost Marketing &Communication Manager






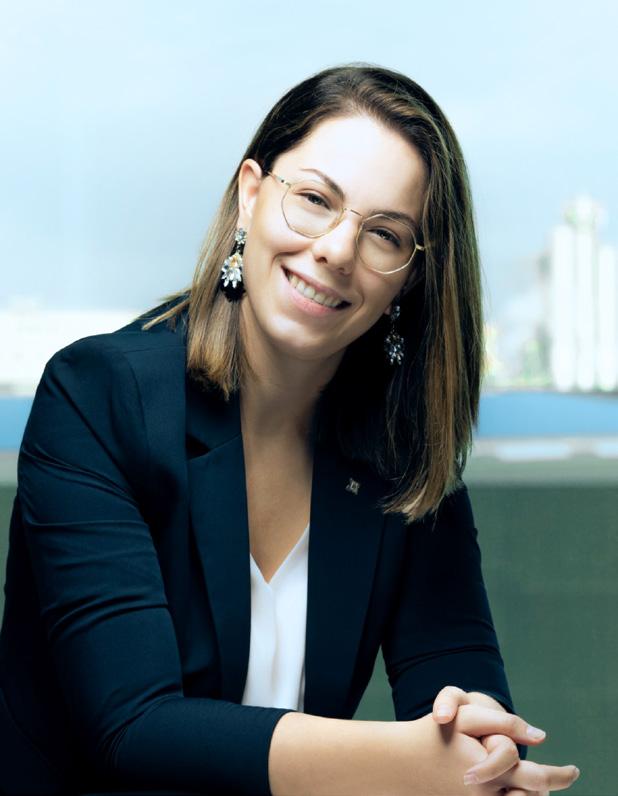
Our family is growing. The number of branches is increasing. Therefore it is extremely important to let the Van Moer Logistics culture and identity live in the same way everywhere. Communication is the absolute priority here. We communicate with our stakeholders through multiple channels. Our approach is no-nonsense and together leads to a win-win. Because we are growing in many places, our communication is becoming more complex. In the future, we want to communicate in an even more structured way in the form of a stakeholder Communicationdialogue.with our employees is a top priority. After all, well-informed employees are engaged and motivated employees. With Van Moer Connect, we have found an alternative for the classical way of internal communication, such as mail traffic and intranet. It concerns a digital platform that can link existing systems (such as mail, leave requests, reward system, order platform for work clothes, ...) and groups them under one platform. Our employees now receive all communications through a single app on their cell phones. Of course, we can also send the communication to specific departments, site locations, people, etc. Interaction is also possible. The recipients can send feedback or reading confirmations. This makes communication both bottom-up and top-down.
EDUCATION AND TRAINING
GOAL 2022-2023
Until recently, training was still fragmented and mainly focused on what was needed within the legal standards. Because we are growing, we had to do things differently. We have prepared carefully to get where we want to be: 2022 is the year of birth of the Van Moer Academy a virtual campus containing the complete training offer for our employees. We have hired a dedicated training coordinator for this purpose. We want to map out a number of functional and personal growth paths, which our people can follow when their changing role or function requires it. In this way, we are evolving towards a culture of lifelong learning. In a company like Van Moer Logistics, standing still is not an option: everyone must continue to invest in their own growth.
GOAL 2022-2023
COMMUNICATIONNO-NONSENSE
53
Our industry is changing and our company is growing. Our people need to grow with us. That’s why a structured policy on education and training is a top priority.
Development of training catalogue Van Moer Academy
Integrate the online learning platform of the Van Moer Academy in the Van Moer Connect app Van Moer Logistics - 3. Commitment to people and safety
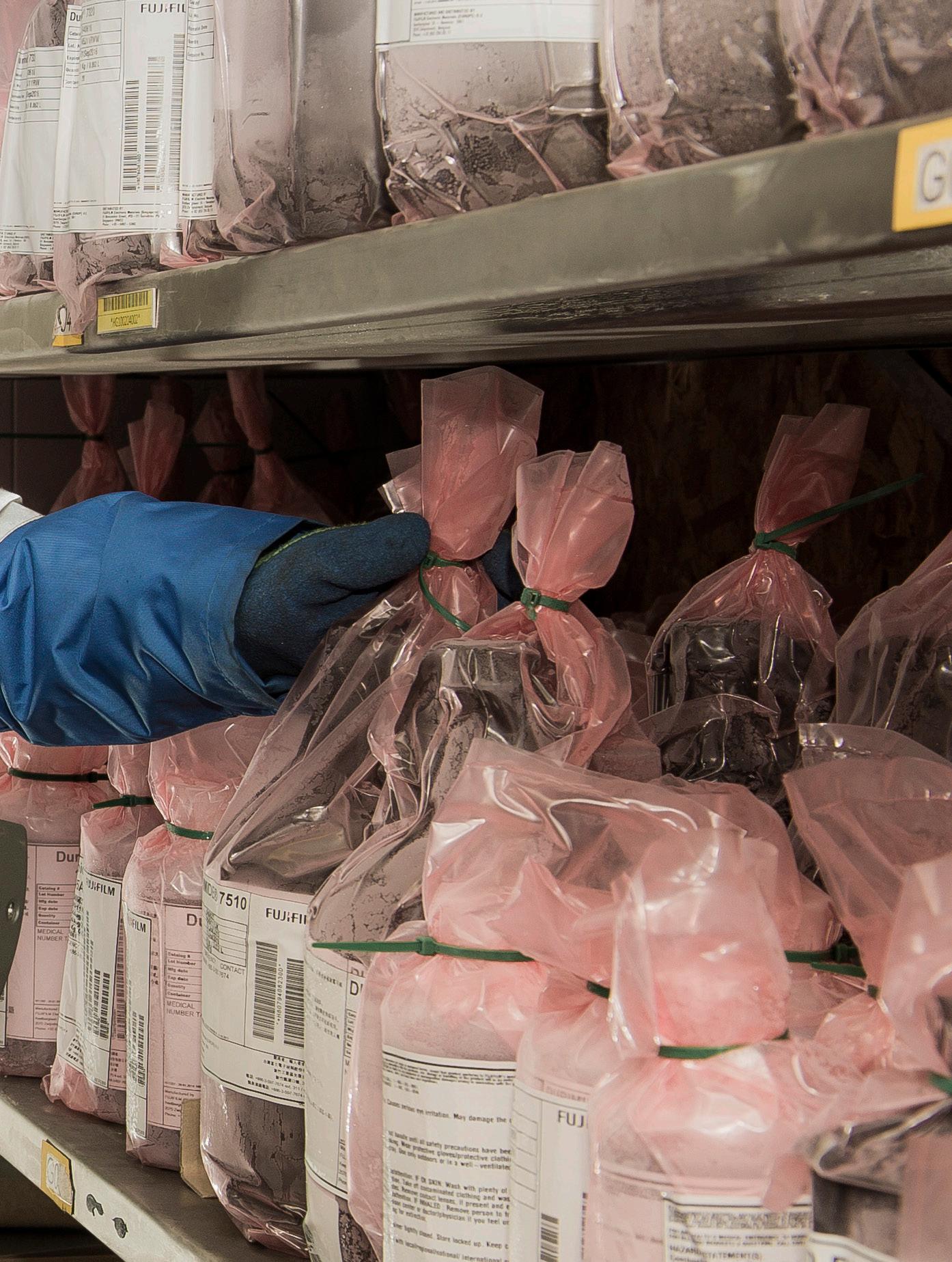
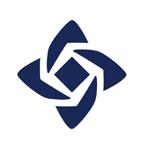
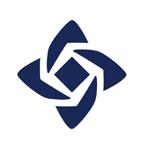
DIVERSITY As a company, we also want to be a reflection of society and offer the same opportunities to anyone who wants to seize them. Our port and logistics are a gateway to the world. We also like to let the world itself in through our company gates. Diversity is an opportunity to make us even more creative and agile. Gender, origin or age play no role in Todaythis.we have almost 50 nationalities working for us. Although our profession is still very much a male stronghold, we do everything we can to attract female employees as well. When it comes to recruitment and selection, we try to be flexible in terms of language requirements, as long as it does not compromise safety and good operational practice. We translate our safety instructions into several languages and closely monitor other nationalities who do not speak Dutch and sometimes English. In this way, they too can grow.
YvesHebbHRDirector 54
GOAL 2023 80% of participateexecutivesintraining on inclusive leadership and dealing with other cultures We expect everyone to be practical and hands-on. We like to roll up our sleeves and have an informal style of working. With us, a good result is more important than hierarchy. We think in terms of solutions and come up with out-of-the-box solutions when necessary.
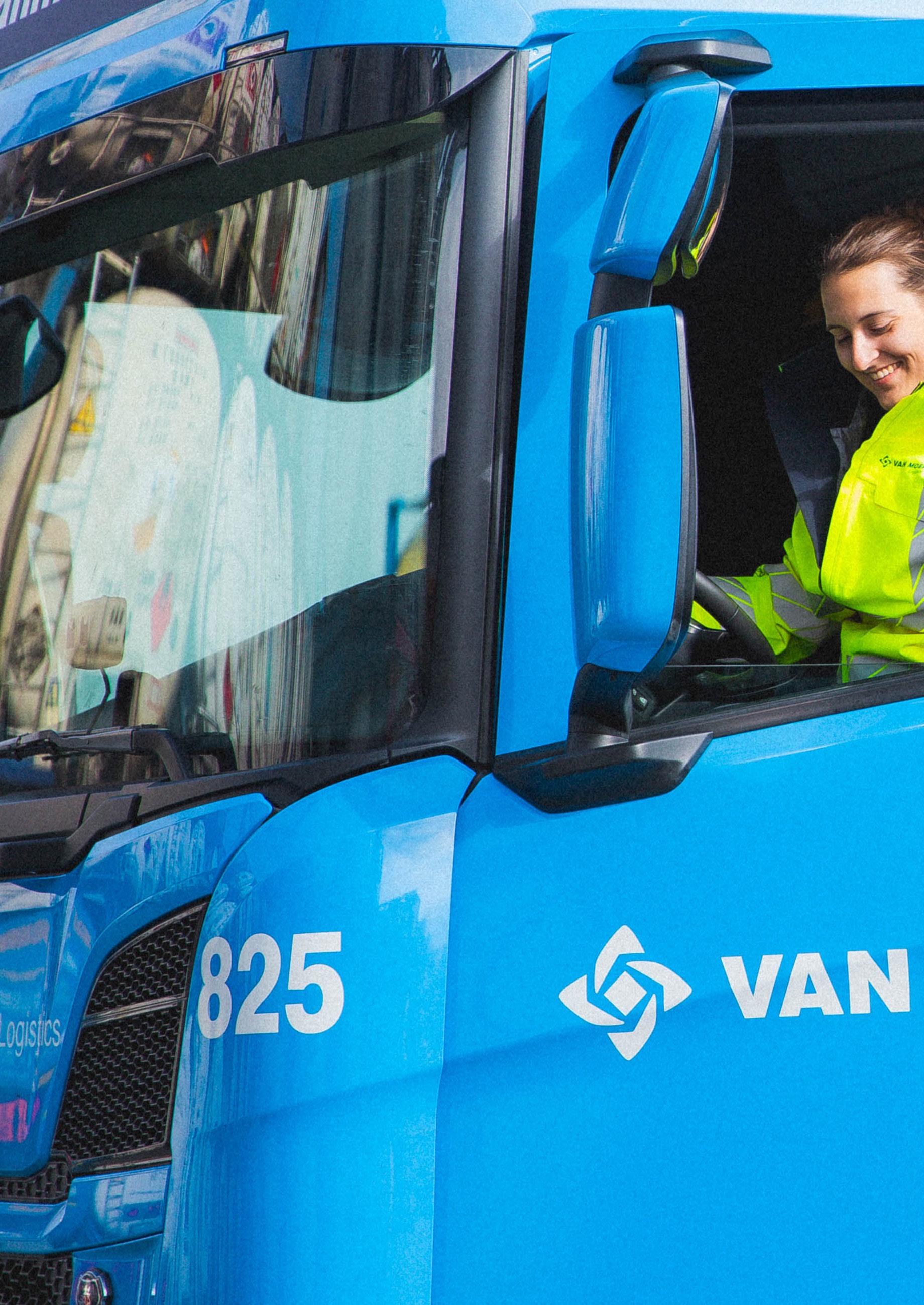
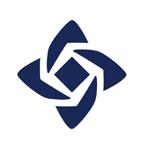
I am a truck driver, but because I always had the best driving reports, I was asked to become an instructor in addition. That way I can teach our Adrianasomething.menLijsters Driver Instructor Van Moer Logistics - 3. Commitment to people and safety
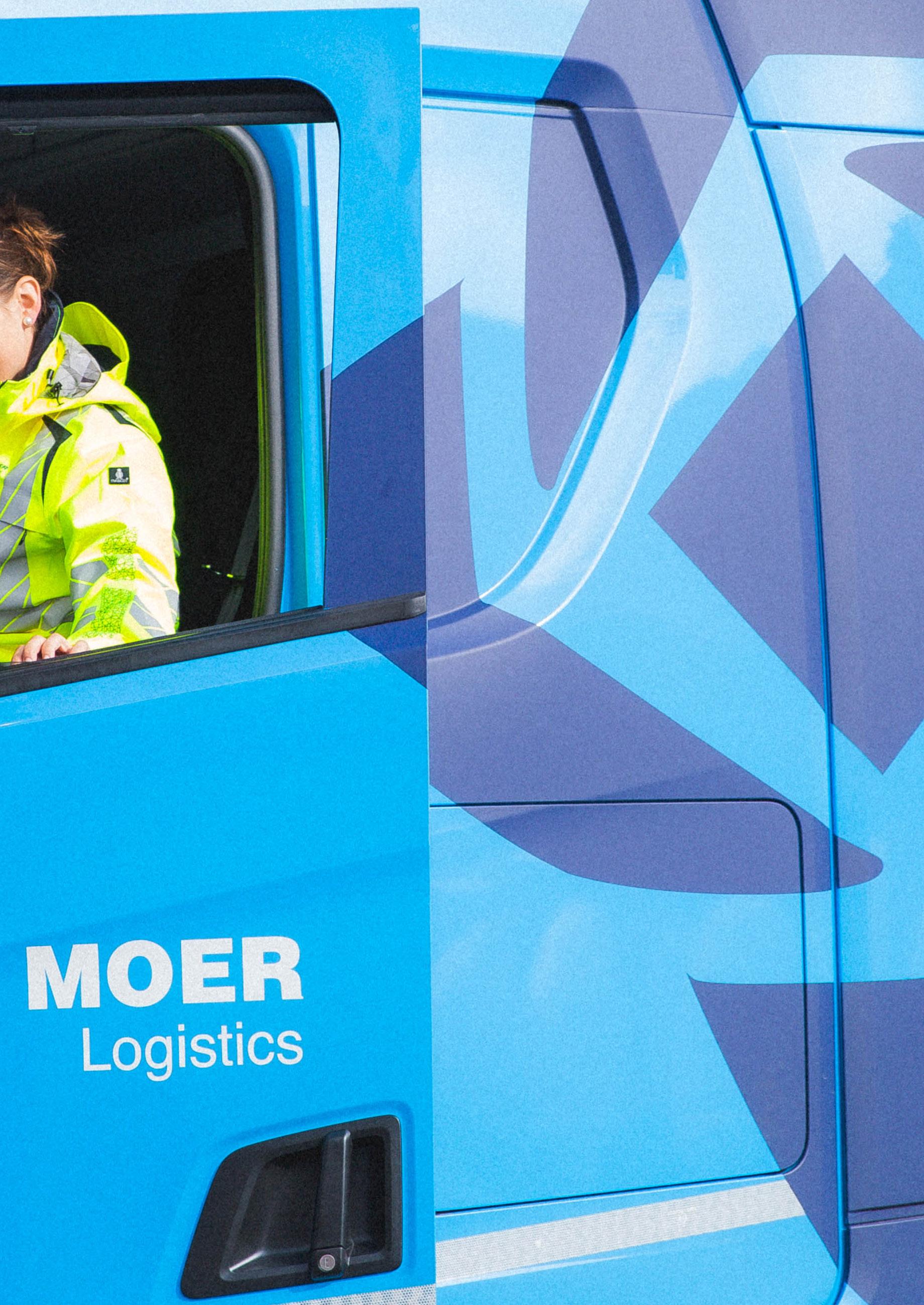

Our goal: We are acutely aware of the great responsibility we bear as a company. We therefore try to live up to our role model in society. Our social responsibility policy is aimed at: DOING BUSINESS ETHICALLY SHOWING INVOLVEMENT
By working long term from a solid value compass, we ensure that everyone feels good about their job and the decisions they have to make. No opportunity without a fair deal. In its policy statements, the management has endorsed several commitments in which we guarantee all stakeholders that we always aim for: and diversified safe and healthy work management safety in all we do employee commitment and involvement and ethical business practice Attention to human rights Privacy and GDPR
• Quality
• Fair
rights • Social
• Behaviour-based
• Sustainability • Ensuring
• Zero tolerance for racism, discrimination, Policyviolencedocuments only have an impact when they are alive. It is our ambition that this vision flows throughout the organisation. The example starts at the top. Through the personal commitment of each manager, the entire company subscribes to these principles. Using targeted actions, we regularly put several focus points back in the light. Our commitments also translate into concrete guidelines for behaviour on the shop floor. And our suppliers and partners commit themselves to follow our standards.
4. SOCIAL RESPONSIBILITY
GOAL 2022-2023
•
• Organisation of 3 types of workshops and toolboxes on sustainability and ESG themes for whitecollar and blue-collar workers
environment • Risk
services • A
•
• Zero infringements of our internal policies
principles • Care
56 DOING BUSINESS ETHICALLY

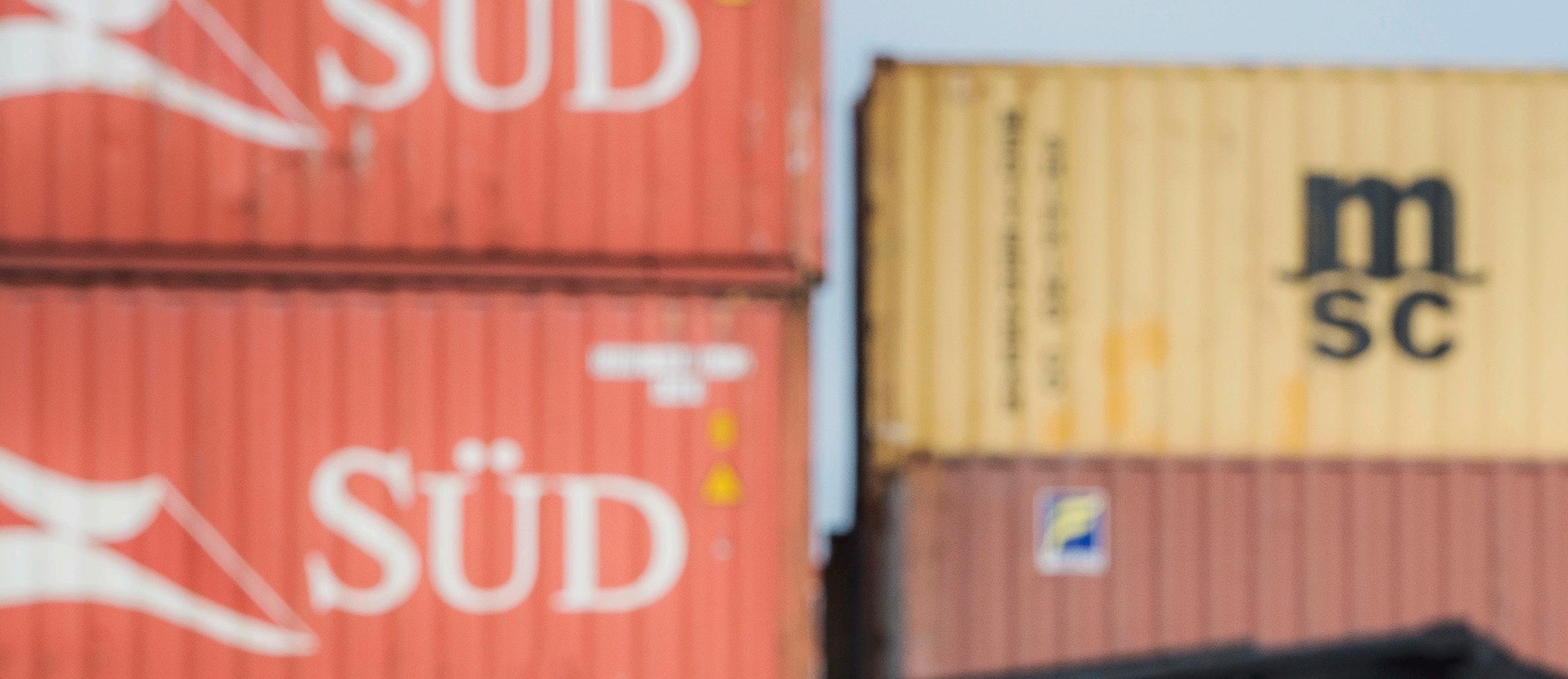


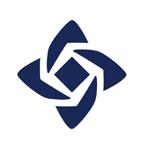
The third pillar, Services, includes a lecture series. The Dennie Lockefeer Chair organises an annual lecture linked to inland navigation. All the expertise of the Chair is brought together and students and young employees are involved and enthused about inland navigation.
SHOWING INVOLVEMENT We are part of our community and take res ponsibility in all areas.
Dennie Lockefeer Van Moer Logistics - 4. Social responsibility
57 Our Ecovadis audits have been excellent. However, there is room for improvement. We are taking to heart the advice to organise hands-on workshops and toolboxes on the ESG theme as well (which stands for Environmental, Social, Governance).
Chair Dennie Lockefeer On January 11, 2019, at the mere age of 42, our dear colleague and strongman within the Executive Committee, Dennie Lockefeer, passed away. Dennie was managing director of Port & Intermodal Logistics. It is impossible to forget someone who gave us so much to remember. Dennie was highly regarded in the port community and particularly in the world of inland shipping for his insights and expertise. For example, he often worked with the Port of Antwerp, the Flemish Government, the University of Antwerp and so many other institutions. To honor Dennie’s memory, a chair for fundamental research on intermodal transport has been established at the University of Antwerp. Professor Christa Sys and Marc Van Peel presented the initiative to Jo Van Moer. Jo immediately supported the initiative and managed to obtain a starting amount of € 300,000 from the port community and other companies. The Dennie Lockefeer Chair focuses on three pillars: research, education and services in inland navigation.
Initially, the chair consists of a doctorate in inland navigation. Specifically, the chair will look for ‘future vision for inland navigation’. This falls under the first pillar: Research. In the area of Education, the Dennie Lockefeer Chair annually awards a prize for the best inland navigation thesis and a biennial fee for the Antwerp Inland Navigation School.
GOAL 2022-2023 Structured dialogue on ESG criteria with 10 stakeholders in 2022 and 2023
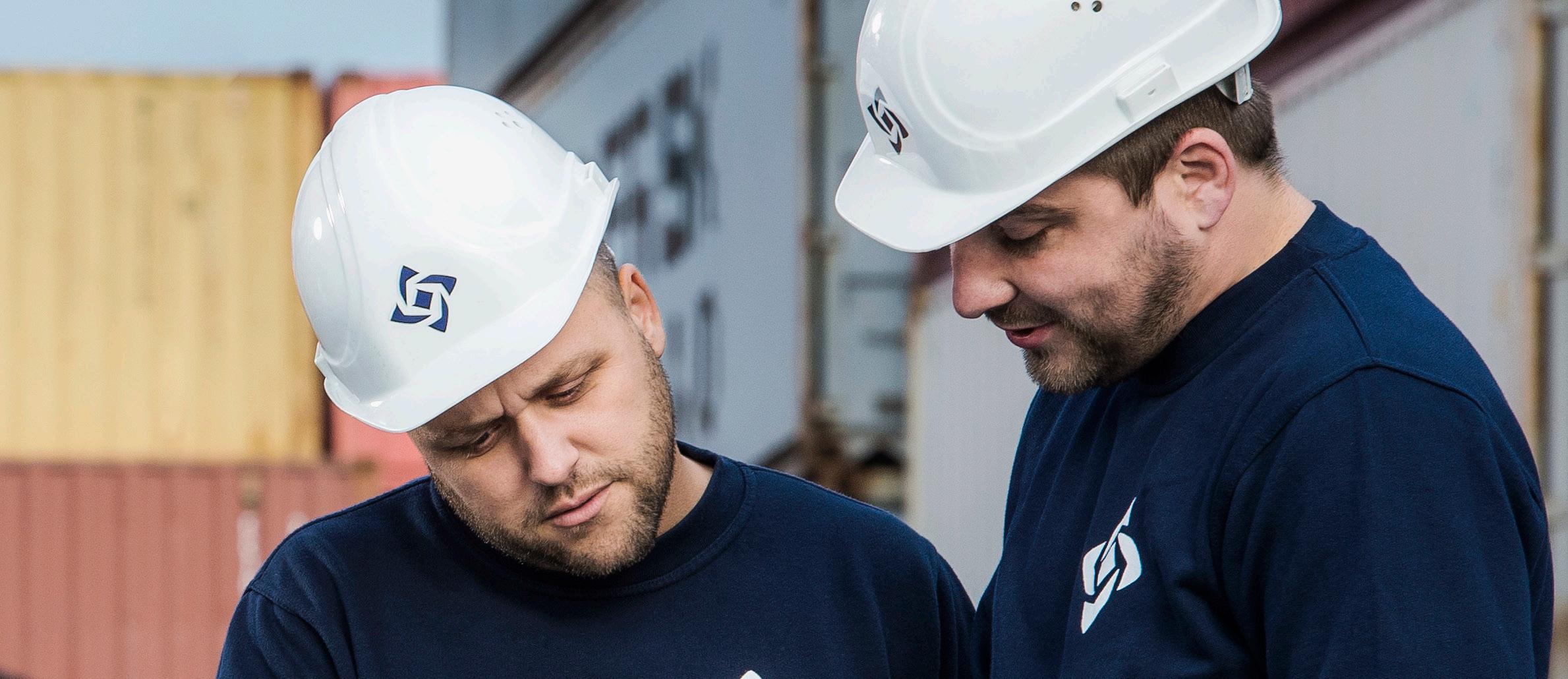
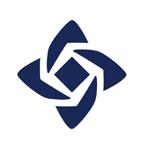
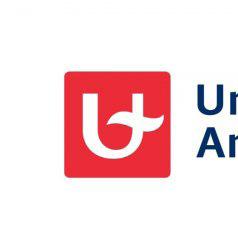
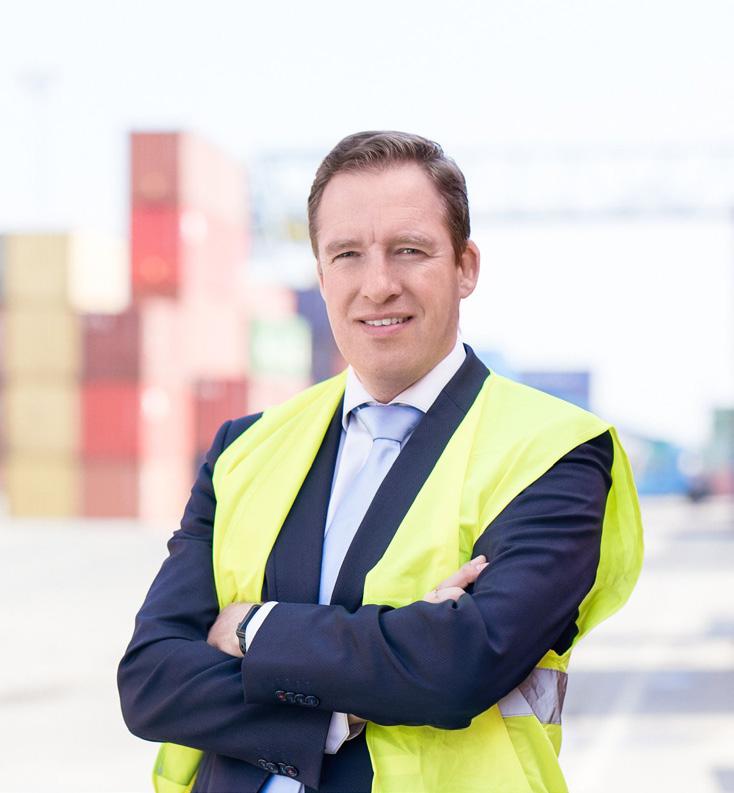
Since January 2022, Jo Van Moer is the new chairman of Waasland Beveren soccer team. He steps into that role at the request of the American owners of the club, and as chairman he will help to ensure the local anchoring of Waasland-Beveren. In the past, our company was already active as a sponsor of what was then SK Beveren. As the chairman of the club and a Beveraar himself, Jo Van Moer has to take care of the local anchoring of WaaslandBeveren. With Van Moer Logistics, we attach importance to that. We employ a lot of people from the region, but we all struggle to find more personnel and we want even more local people to work in our company.
After an intensive training, a privileged vo lunteer is matched with an underprivileged townsman looking to improve his or her Throughlife. a connection in trust and equality, both buddies discover hidden strengths, and the buddy who is looking for an op portunity builds up his self-confidence. It is a fantastic initiative that we support with great pleasure and enthusiasm.
As a young person, a motivating and inSoudal,toimportantenvironmentstimulatingisverytocontinuegrowasanathlete.TodayIrideforLottobutmyrootsliethecompany’scycling
Chairmanship Waasland Beveren
ArmenTekort Together, we help the buddy work of Ar menTeKort, the association that connects promising and underprivileged people.
Support of local activities
It is with great pleasure that we sponsor lo cal initiatives such as the Beverse festival, the ice rink, the Kruibeke marathon, and many other small activities.
58
Brentteam.VanMoer ProfessionalcyclistLottoSoudal
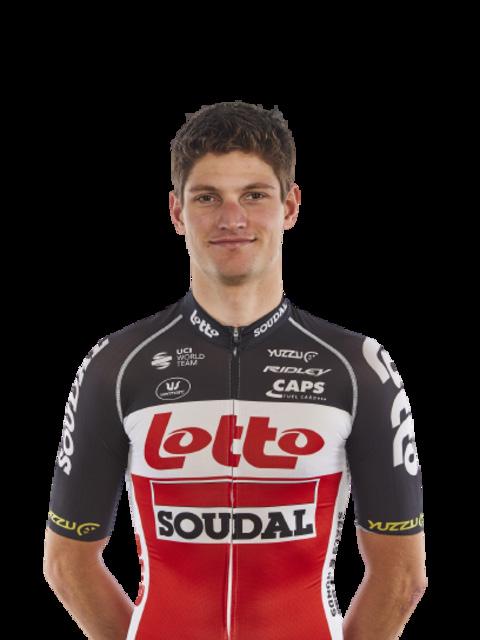
Van Moer Logistics - 4. Social responsibility
Van Moer Logistics Cycling Team We are big fans of cycling and like to offer children and young people the chance to learn about this sport. That is why we sponsor the youth work with full conviction. Since the creation of the Van Moer Logistics Cycling Team, many young cyclists have successfully ridden in the club’s colors. Our team is active in several cycling disciplines: road cycling, track cycling and cyclocross. The team strives for a good balance between performance-oriented sports and fun and social activities in a team. The cyclists are coached by an enthusiastic group of trainers. They are assisted by youth coaches and experienced cyclists. Cycling is possible with the miniemen from the year you turn 8. The final destination of the Van Moer Logistics Cycling Team is the Juniors, after which you can grow into higher categories. The Van Moer Logistics Cycling Team will start the 2022 season with 146 riders. In all categories, we see a substantial increase in the number of members. The girls' team is also a great success. The number of girls in the team rose from 16 to 21.
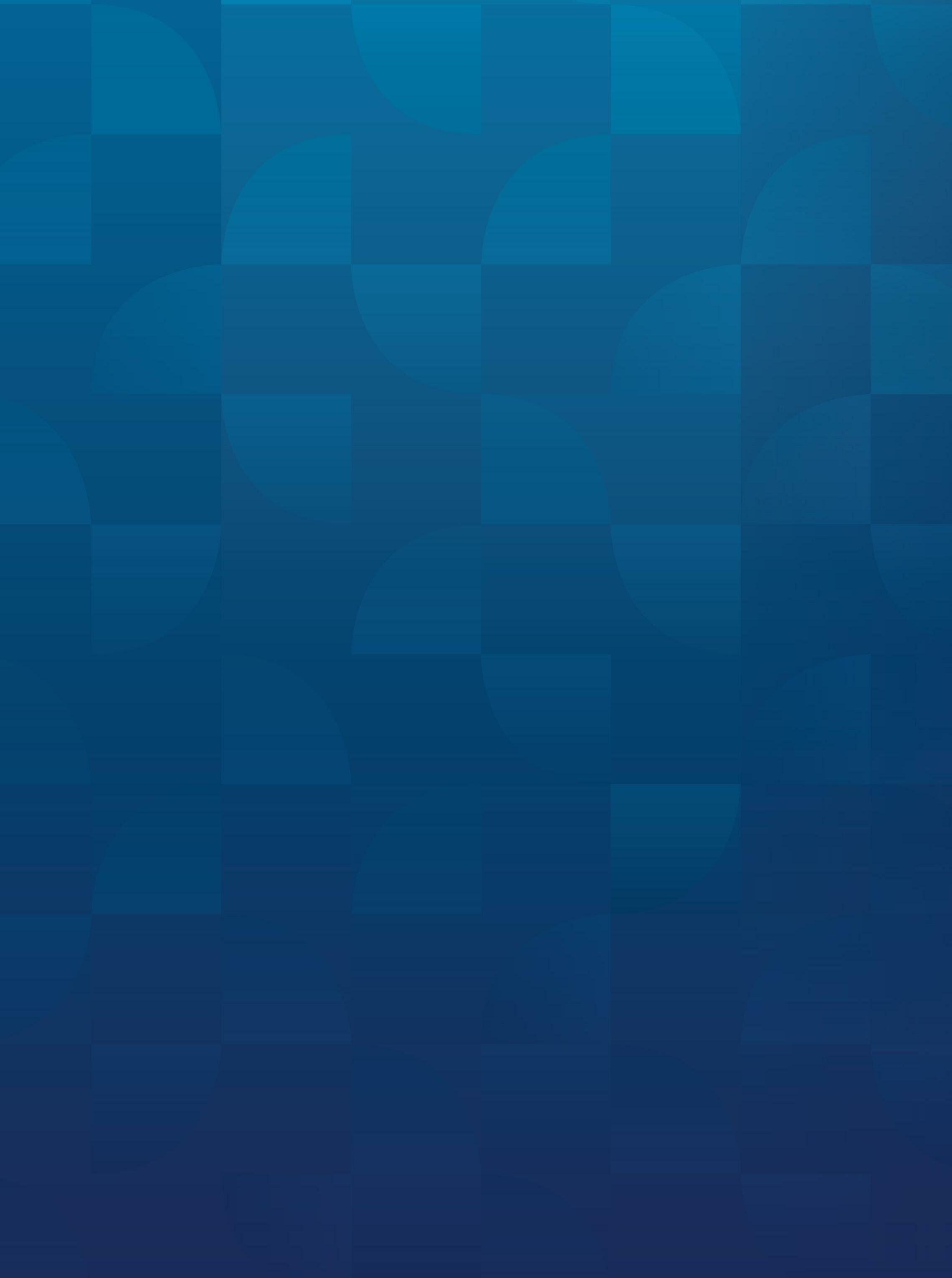
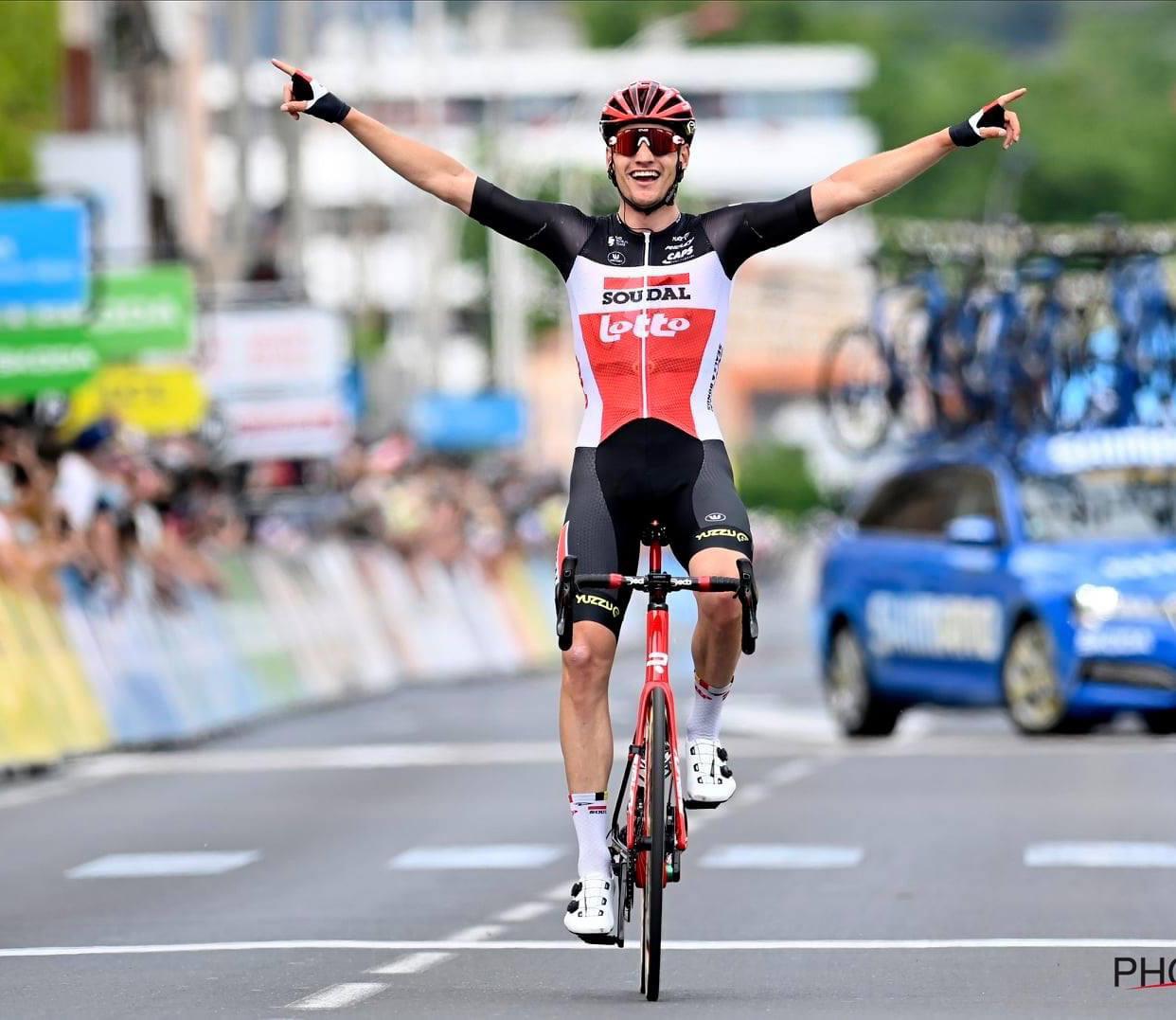
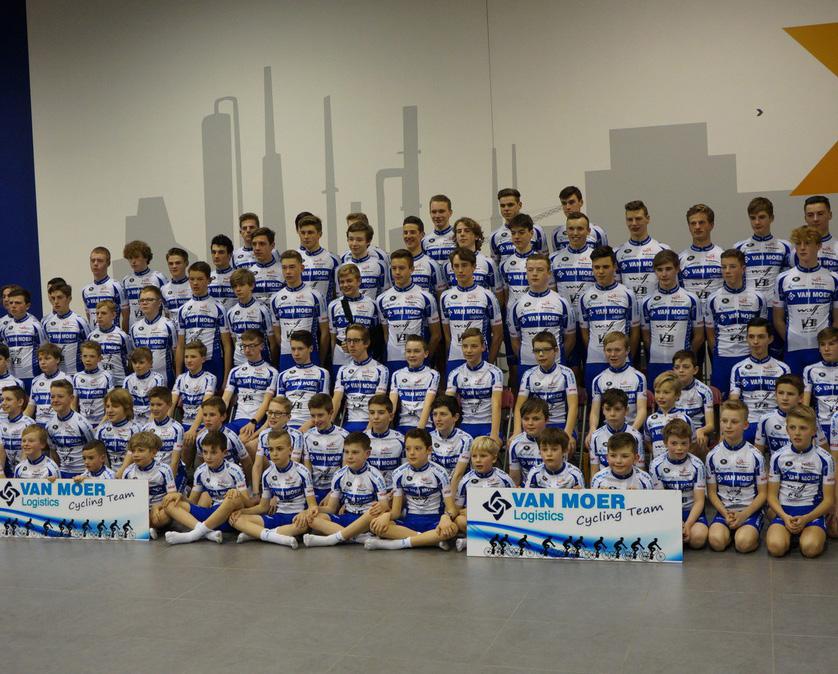
OBJECTIVESEVALUATION
J We achieved 12% reduction! A new environmental management system target, which includes waste, was set. No Continuous improve ment (1) Digitalisation: Van Moer goes paperless: 50% fewer prints companywide per year Not ok Print behaviour fluctuates, but there is no real downward trend. Yes Continuous improve ment (2) Digitalisation: 10 vertical stakeholder integrations by 2025. J In progress 4 projects realised, 4 in progress. Yes Quality Monthly monitoring of all departments through QESSH dashboards
Subject Title Objective Result Comment Continuity solutionsIntermodal1. Increasing multimodal traffic Increase in multimodal transport versus road transport from 50% to 75% by 2025 J In progress This objective has been adjusted. We are aiming for a 50% increase in waterborne transport by 2025 (compared to 2021, expressed in TEU). Yes Circularity 5 circular projects with on-site value-ad ding logistics where we take the lead by 2025 J In progress 1 project completed Yes Green logistics 1 CO2 neutral supply chain in 2022 Not ok One concrete project for a potential customer was not retained. Full CO2 -neutrality without offsetting proved to be infeasible. Therefore, we adjust this target to almost CO2-neutral (= 80% reduction com pared to regular road transport). Yes
Sustainable2. and operationsefficient Reduce CO2 footprint Full CO2 management plan and CO2 reduction plan by 2022 and annual 10% reduction
J Target achieved. Target will be carried over to 2023. Yes
2020-2021
J Target achieved. Another target was set. No Diversity One team! We are all Van Moerianen. Project on understanding and tolerance J In progress Several ad hoc actions are ongoing. For 2022-2023 we will set a more measurable target: 80% of the managers will participate in a training/workshop on inclusive leadership and dealing with other cultures in 2022-2023.
J Target achieved. The final target is 65% reduction by 2030. The target was adjusted accordingly and the annual 10% was dropped to look at the overall result. We will show the relative reduction by activity in the future. Yes Reduce environmen tal impact Reduction of non-separated or recyclable commercial waste by 10% per year from 2021 onwards
60
Yes 4. Social respon sibility Doing business ethically (1) 20% higher score on our external sustainability audits through Ecovadis by 2021 J We achieved brilliant scores. No Doing business ethically (2) Zero infringements of our internal policies Not ok 1 infringement Yes Showing involvement (1) Structured dialogue with 10 stakehol ders in 2021 and 202 J In progress 4 meetings to date Yes Showing involvement (2) Sponsorship of 5 socially relevant projects J We will continue to do so. Yes
Commitment3. to people and safety Safe work (1) Evolution to step 4 on the safety ladder in 2022 Not ok At the time of finalising this report, it was not yet achieved. In order to measure this better, this will be broken down by business unit. Yes Safe work (2) Annual improvement of 10% for our safety rates Not ok Target was not achieved. A more detailed target was set for severity and frequency. Yes Open culture and flat structure 5 career paths through internal mobility per year J Target achieved. In addition, we are also looking at the opportunities for employees coming from the new acquisitions. Yes Education and training Launch of Van Moer Academy J Target achieved. Another target was set. No No-nonsense communication Promotion Van Moer Connect App 90% adoption rate 75% of the employees active at least 1x per week 50% of the employees active at least 2x a week
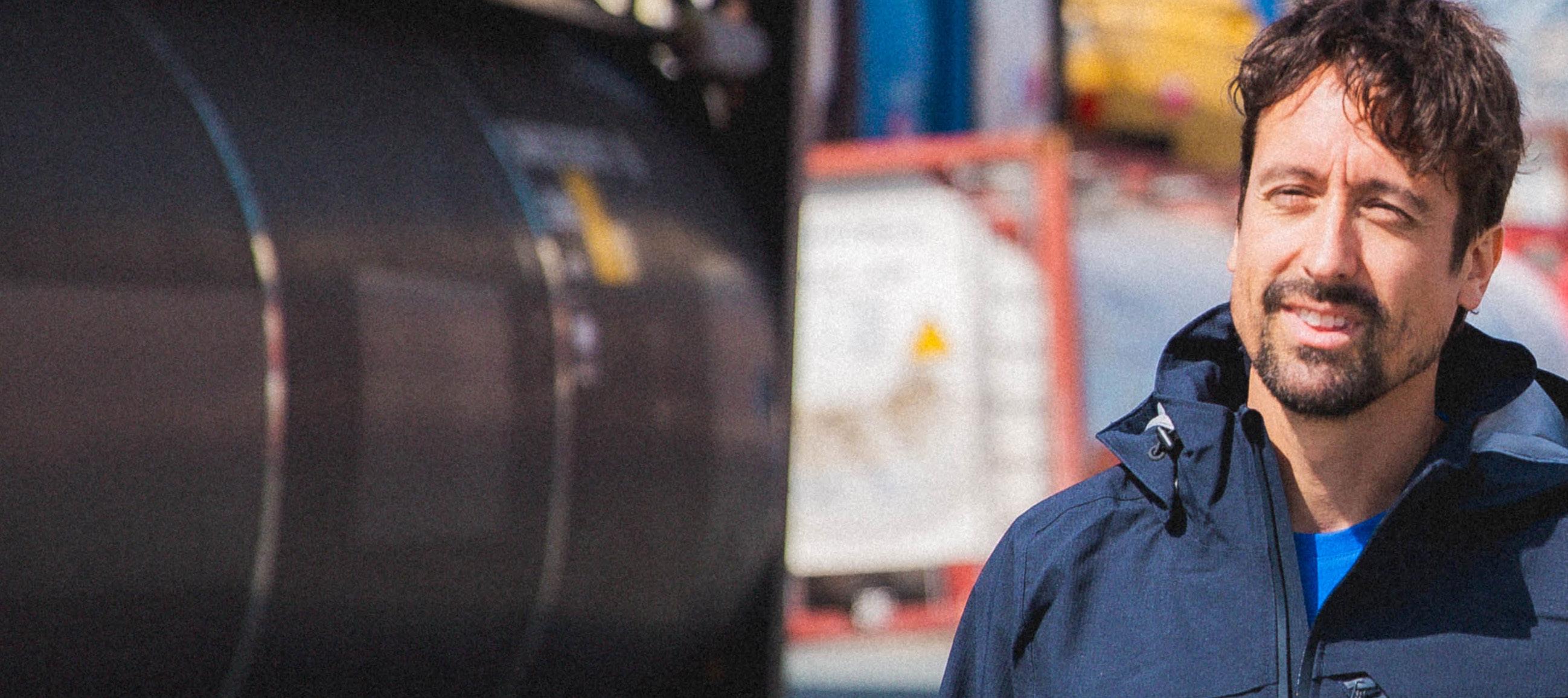
61Van Moer Logistics OVERVIEW TABLES This report was produced in cooperation with the strategy & sustainability consultancy company Sus tacon (www.sustacon.me). For questions regarding our sustainability report, please contact Felien Van Oost at felien@vanmoer.com. Overview table SDGs 1 Intermodal solutions 1.1 Increasing multimodal traffic l l l l l l l l l 1.2 Circularity l l l l l l 1.3 Green logistics l l l l l l 2 Sustainable and efficient operations 2.1 Measure CO2 footprint l l l l 2.2 Reduce CO2 footprint l l l l 2.3 Reduce environmental impact l l l l 2.4 Continuous improvement l l l l 2.5 Quality l l l l 3 Commitment to people and safety 3.1 Safe work l l l 3.2 Open culture and flat structure l l 3.3 Education and training l 3.4 No-nonsense communication l l 3.5 Diversity l l l l 4 Social responsibility 4.1 Doing business ethically l l l 4.2 Showing involvement l l l l l
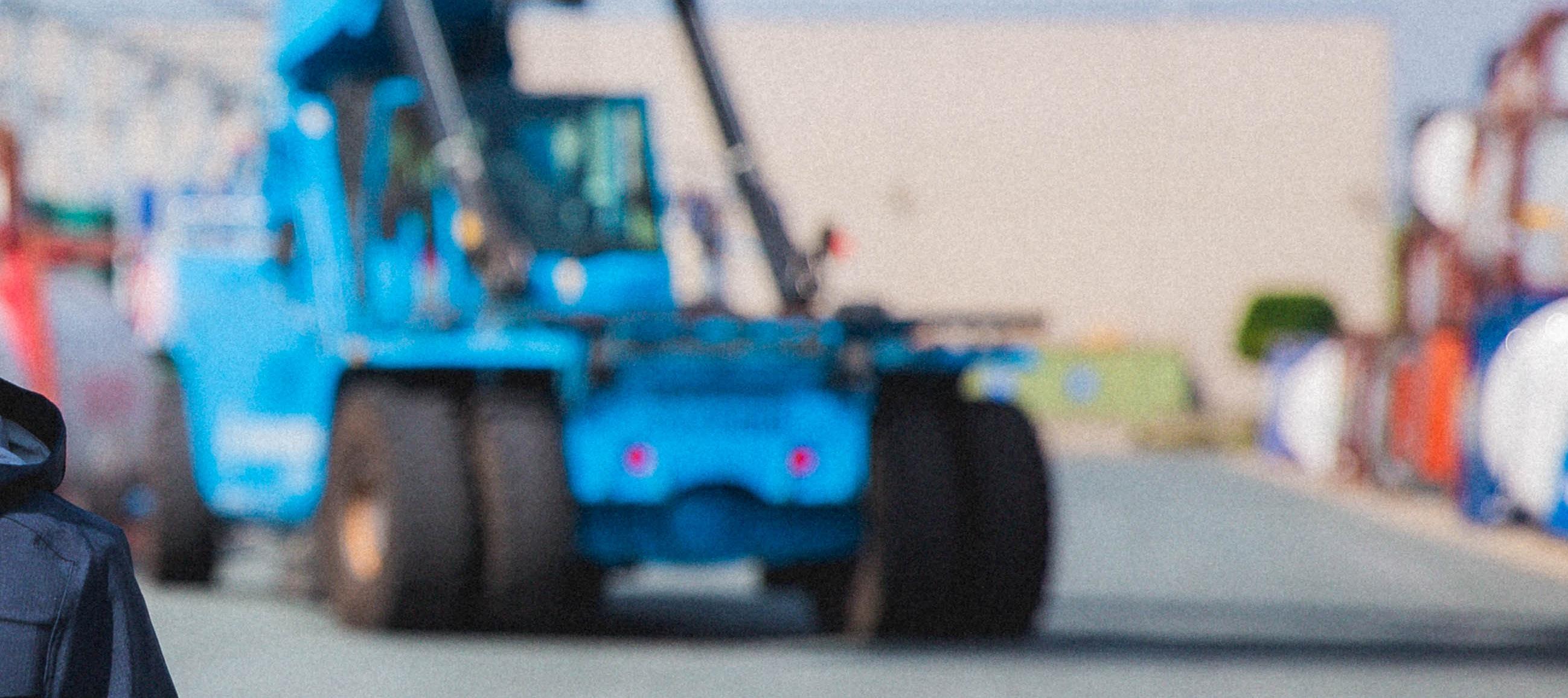












102-14
102-3
102-55
102-56
102-43
102-16
GRI Below we provide the index of this report ac cording to Global Reporting Initiative (GRI), the international standard for sustainability reporting. This report provides information on most of the foundation principles, the core of the general disclosures and a number of GRI Standard Disclosure title Page 102-1 Name of the organisation Certificates (p. 15) 102-2 Activities, brands, products and services Transport and distribution (p. 10) | Bulk & tank container logistics (p. 10) | Warehousing & value adding logistics (p. 11) | Port & intermodal logistics (p. 11) | Supporting services (p. 12) | Certificates (p. 15) Location of headquarters p. 64 103-8 Workforce information Commitment to people and safety (p. 48-55) Statement from senor decision-maker Preface (p. 3-4) Key impacts, risks and opportunities Preface (p. 3-4) | The world is changing (p. 16-19) | Sustainable strategy (p. 20-21) Values, principles, standards and norms of behaviour Preface (p. 3-4) | Open culture and flat structure (p. 56-57) Governance structure Governance (p. 13) 102-22 Composition of the highest governance body and its committees Governance (p. 9) Approach to stakeholder engagement The world is changing (p. 16-19) | Showing involvement (p. 57) Entities included in the consolidated fin. statements Key figures (p. 6) List of material topics The world is changing (p. 18-19 | Sustainable strategy (p. 20-21) Reporting period 2021 2022 (Q1 + Q2) 102-51 Date of most recent report 2022 102-53 Contact point for questions regarding the report Summary tables (p. 61) Claims of reporting in accordance with the GRI standards Summary tables (p. 62-63) GRI content index GRI (p. 62-63) External assurance n.a. 201-1 "Direct economic value generated and distributed" Key figures (p. 5) topic-specific disclosures. We do not claim completeness here, but consider this a first step towards strengthening our reporting pro cess in a targeted manner in the future.
102-18
102-45
102-47
102-50
102-15
102-54

GRI Standard Disclosure title Page Anti-corruption Doing business ethically (p. 56-57)
412
205
404-2
306
403-1 Occupational health and safety management system Safe work (p. 48-50)
307 Environmental compliance Reduce environmental impact (p. 42) | Certifcates (p.15)
302-4 Reduction of energy consumption Measure CO2 footprint (p. 30-34) | Reduce CO2 footprint (p. 35-40)
305 (1-2-3-4) Emissions Measure CO2 footprint (p. 30-34) | Reduce CO2 footprint (p. 35-40) Effluents and waste Reduce environmental impact (p. 42)
302-1 Energy consumption within the organisation Measure CO2 footprint (p. 30-34) | Reduce CO2 footprint (p. 35-40)
301 Materials Reduce environmental impact (p. 42)
303 Water Reduce environmental impact (p. 42)
402 Labor/management relations Doing business ethically (p. 56-57)
406
401 Employment Commitment to people and safety (p. 48-55)
403-2 Hazard identification, risk assessment, and incident investigation Safe work (p. 48-50) 403-9 Work-related injuries Safe work (p. 48-50) Programs for upgrading employee skills and transition assistance programs Education and training (p. 53) Diversity and equal opportunity Diversity (p.54-55) Non-discrimination Diversity (p.54-55) | Doing business ethically (p. 56-57) Human rights Doing business ethically (p. 56-57) Community engagement Showing involvement (p. 57)
413
405
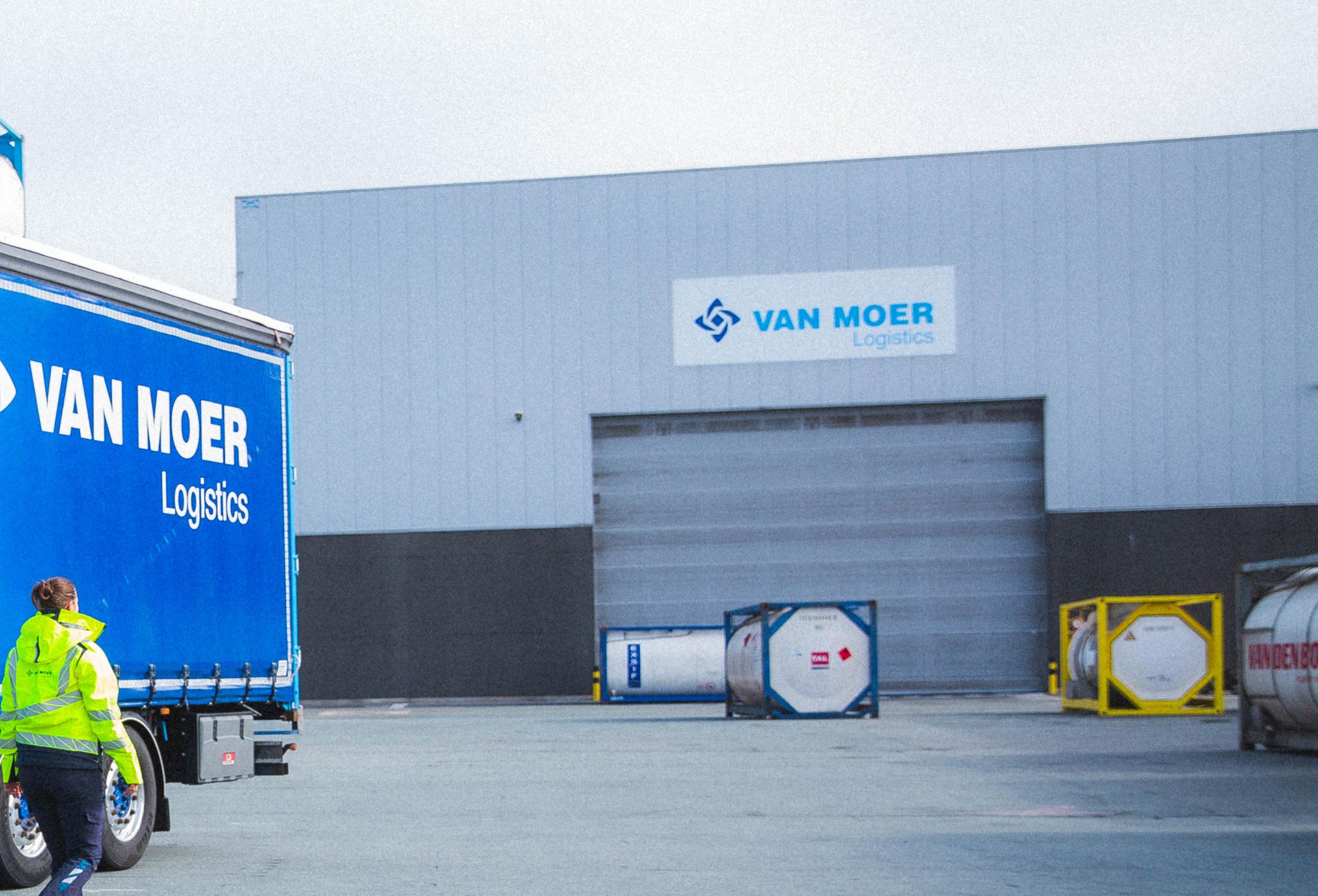
Van Moer Logistics Keetberglaan - Haven 1054 2070 Zwijndrecht +32 3 254 09 www.vanmoer.cominfo@vanmoer.com09 www.sustacon.medesign:&reportingStrategy,world,theAround earth.todown

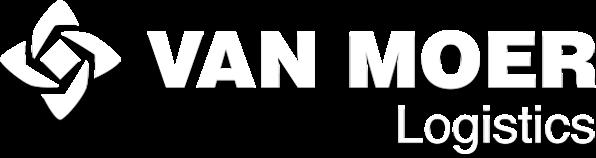
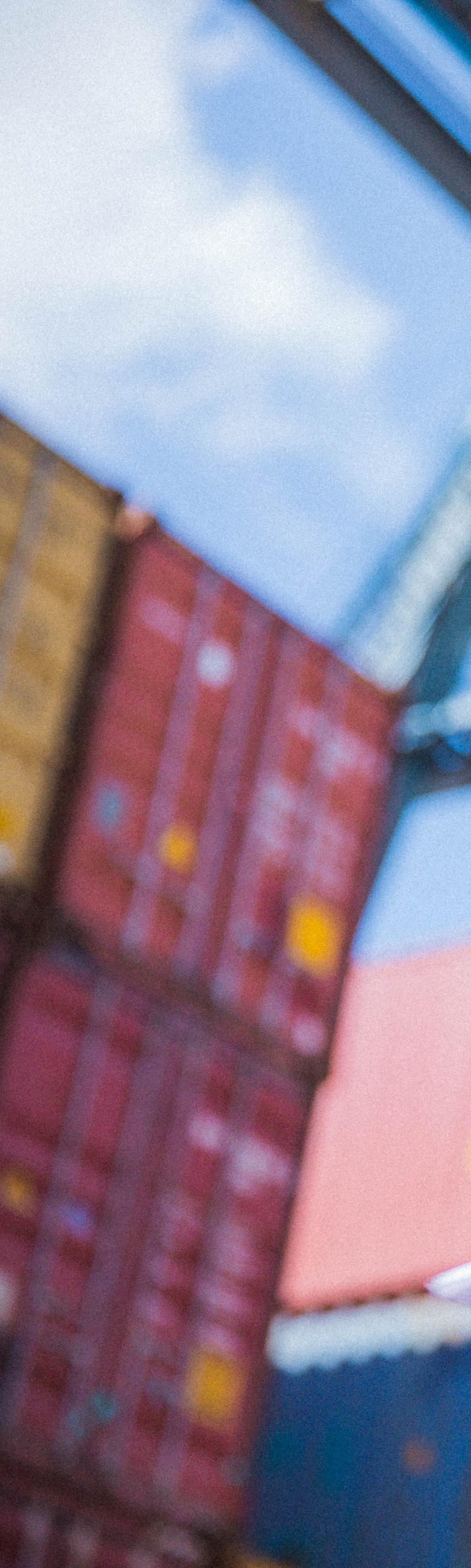
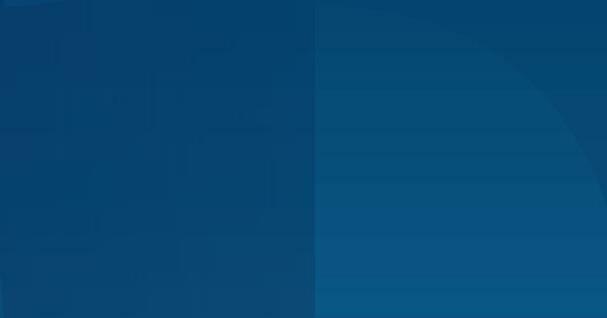