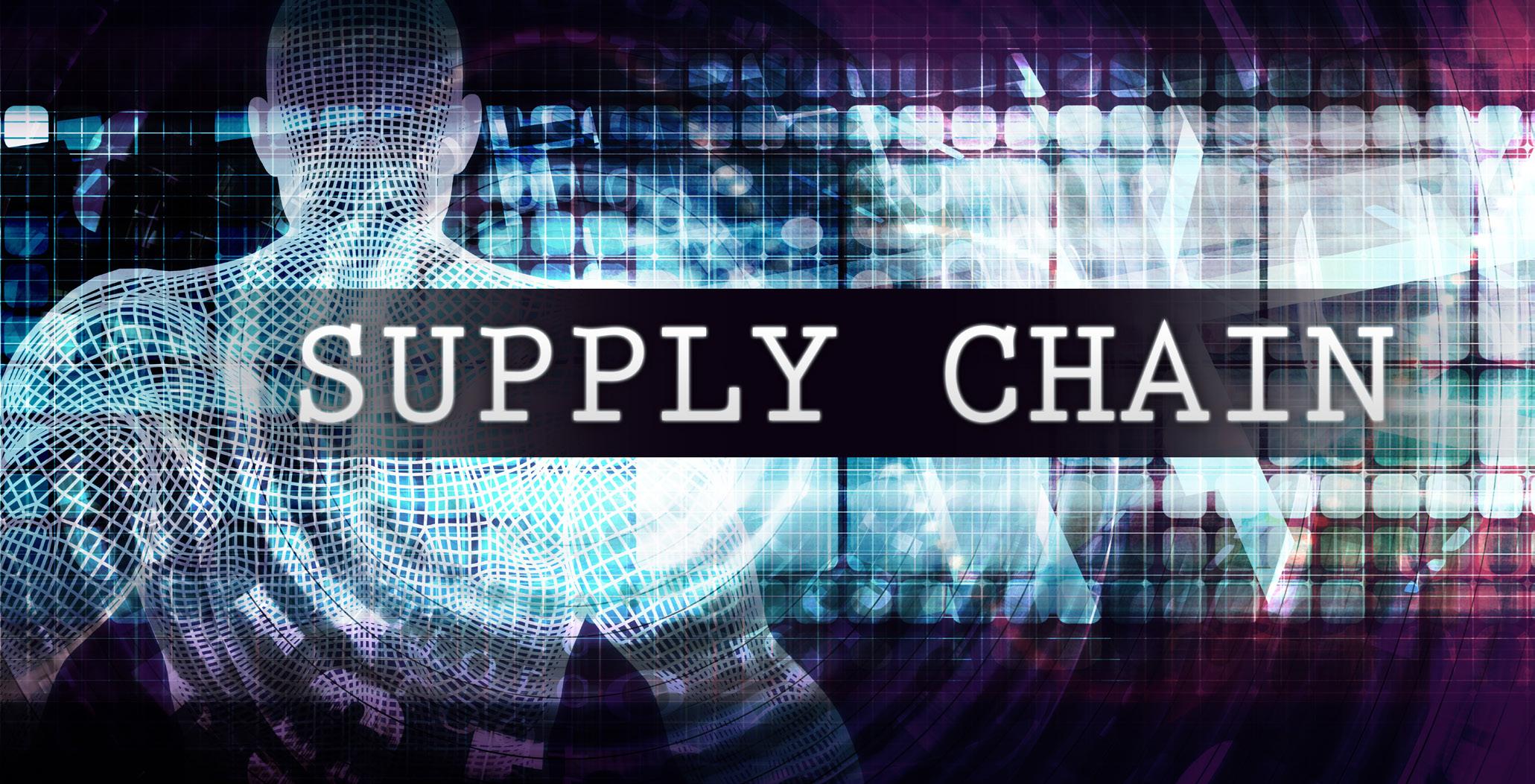
4 minute read
The supply contract in the eyewear sector: the 10 key points
When a company in the eyewear sector purchases from a supplier raw materials or semi-finished products (for example, acetate sheets or optical lens blanks), when it opts for subcontracting a process or parts thereof (for example, the galvanic or welding process of metal eyewear frames) or even when it purchases a finished product (for example, optical frames or uncut lenses) to be placed on the market under its responsibility, it is essential for the parties to define all the information concerning the scope of the supply in order to ensure that the product supplied constantly complies with the customer’s specifications. In addition to being essential for the legal manufacturer of the devices to assure conformity of the products to the regulations in force – both mandatory and technical – this information makes it possible to also define a whole set of aspects, not strictly related to the product, that underlie efficient, stable and long-lasting relations between the parties.
The quality agreement is that part of the supply contract, stipulated by the supplier and the customer, which, in addition to the various commercial and legal clauses, contains specific sections covering the quality requirements of the product and related processes that the parties must adhere to, within their business relations.
Below we have set out the 10 key points of the quality agreement which should always be included in a contract stipulated between customer and supplier.
1. Identify the products covered by the agreement: the agreement between the parties must contain a precise identification of the products covered by the agreement (e.g., model and colour) and, where applicable, an indication of the technical and/or mandatory regulatory framework.
2. The product specifications: the supplier must provide the customer with a product with specific features that must be precisely detailed in the agreement (for example, dimensional and technical specifications).
3. The checks to be performed on the product: if the product must comply with certain specifications, process controls must be scheduled and carried out at different levels, aimed at guaranteeing the specifications at the end of the production flow. The contract specifications precisely detail what checks to carry out, what instruments to use, and what acceptance criteria to consider for a check to be passed or failed.
4. The requirements for approval of the processes and equipment: the suppliers have been selected precisely because they are able to manage a specific process. The requirements for guaranteeing optimal management of the process that is contracted by the company to the supplier must remain over time; that is why they are included in the information that is agreed in writing between the parties.
5. The requirements for personnel qualifications: not just machinery, also human resources. The success of a process depends on multiple factors: the abilities, qualifications, and skills of the personnel are among the most important ones. For the majority of the processes or parts thereof, it is indispensable for those performing them to be appropriately trained.
6. The requirements of the quality management system: whether the critical supplier has a quality management system compliant and/or certified in accordance with one of the reference standards (ISO 13485 and/or ISO 9001), or not, from a documentary point of view there are key aspects that must be defined and agreed between the parties (for example, the procedure for managing deviations).
7. The methods for auditing the supplier’s activities: the parties must define the methods for auditing the activities covered by the agreement. If the customer’s procedures call for specific supplier auditing methods (e.g. second party audit), these must be agreed between the parties.
8. The management of sub-contractors: if the contract covers any sub-contractors (for example, raw material suppliers), it must define the limits, as well as the methods for managing and controlling them by the supplier, in order to guarantee the customer a product that constantly meets the specifications.
9. The clause on changes: the agreement should contain a specific clause that defines the limits and methods of managing changes made by the supplier, which have or may have an impact on the quality and safety of the products (for example, changes to specifications, manufacturing and control procedures, raw materials), as well as the methods for communication and authorisation by the customer.
10.The methods for string and transporting the products: the parties must agree on the storage conditions of the product and agree who will be responsible for transport and therefore for ensuring it takes place in compliance with the specifications.
