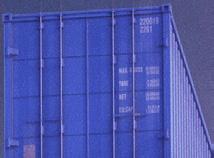
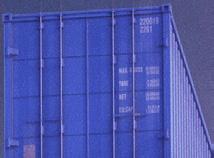
Where It All Falls Into Place
How Virginia helps companies find the right supply chain balance
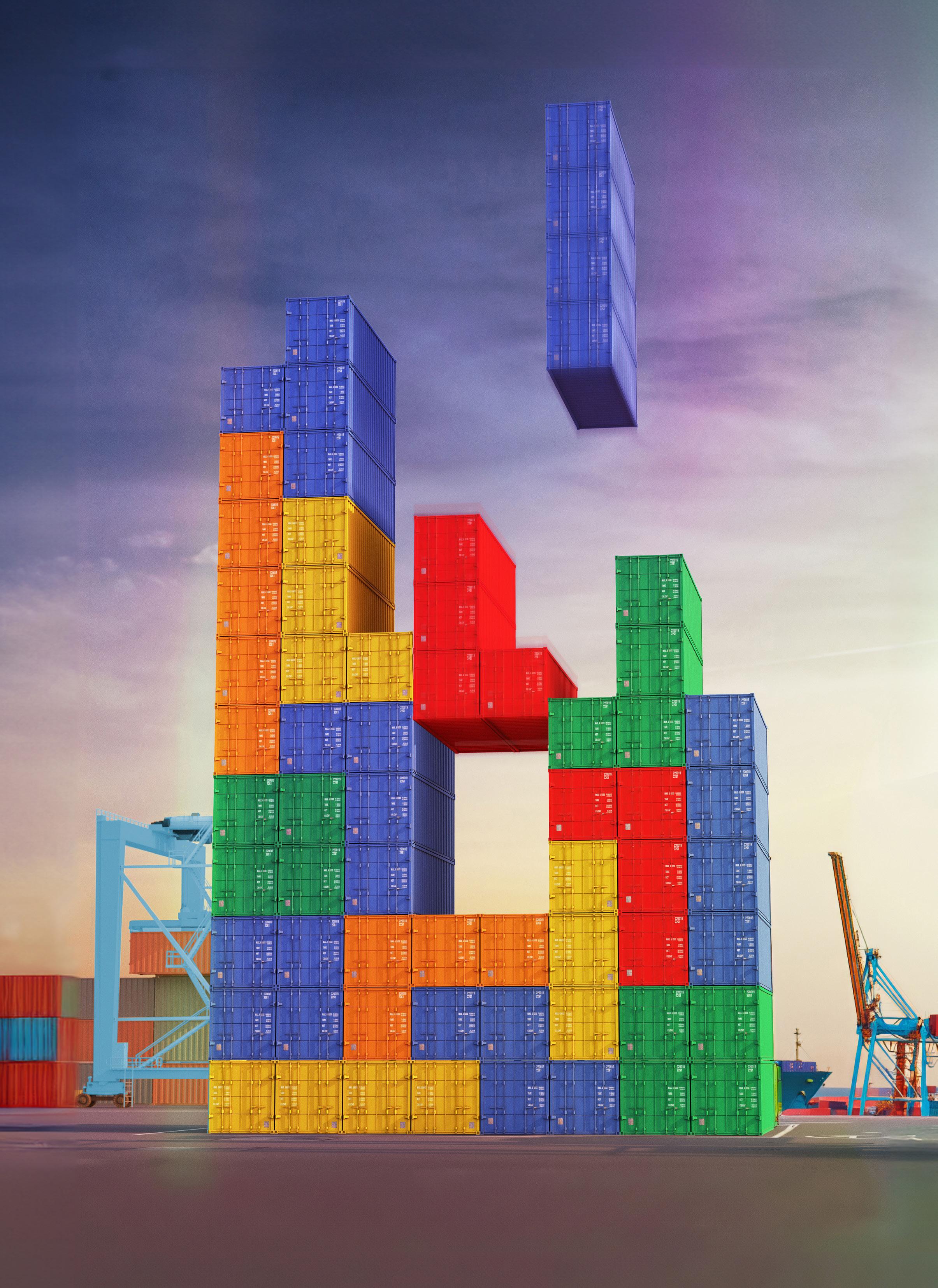
PERSPECTIVES FROM THOUGHT LEADERS
Myra Blanco, Virginia Tech Transportation Institute | Mike Coleman, CV International Ashleigh de la Torre, Amazon | Lance Harcrow, Estes Forwarding Worldwide
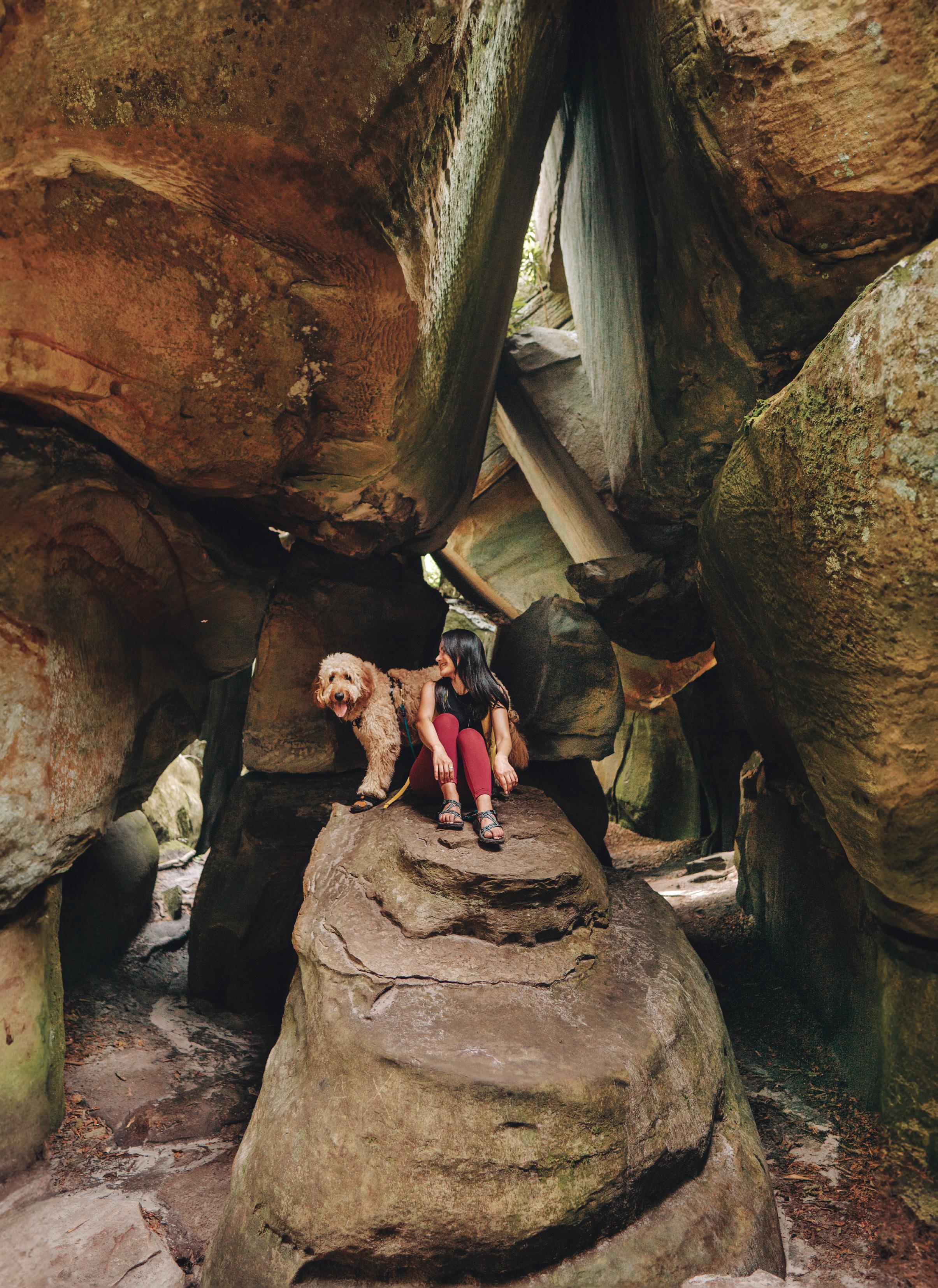
The Channels Natural Area Preserve in Russell and Washington counties derives its name from the Great Channels, a maze-like system of sandstone crevices and boulders that occur near the summit of Clinch Mountain.
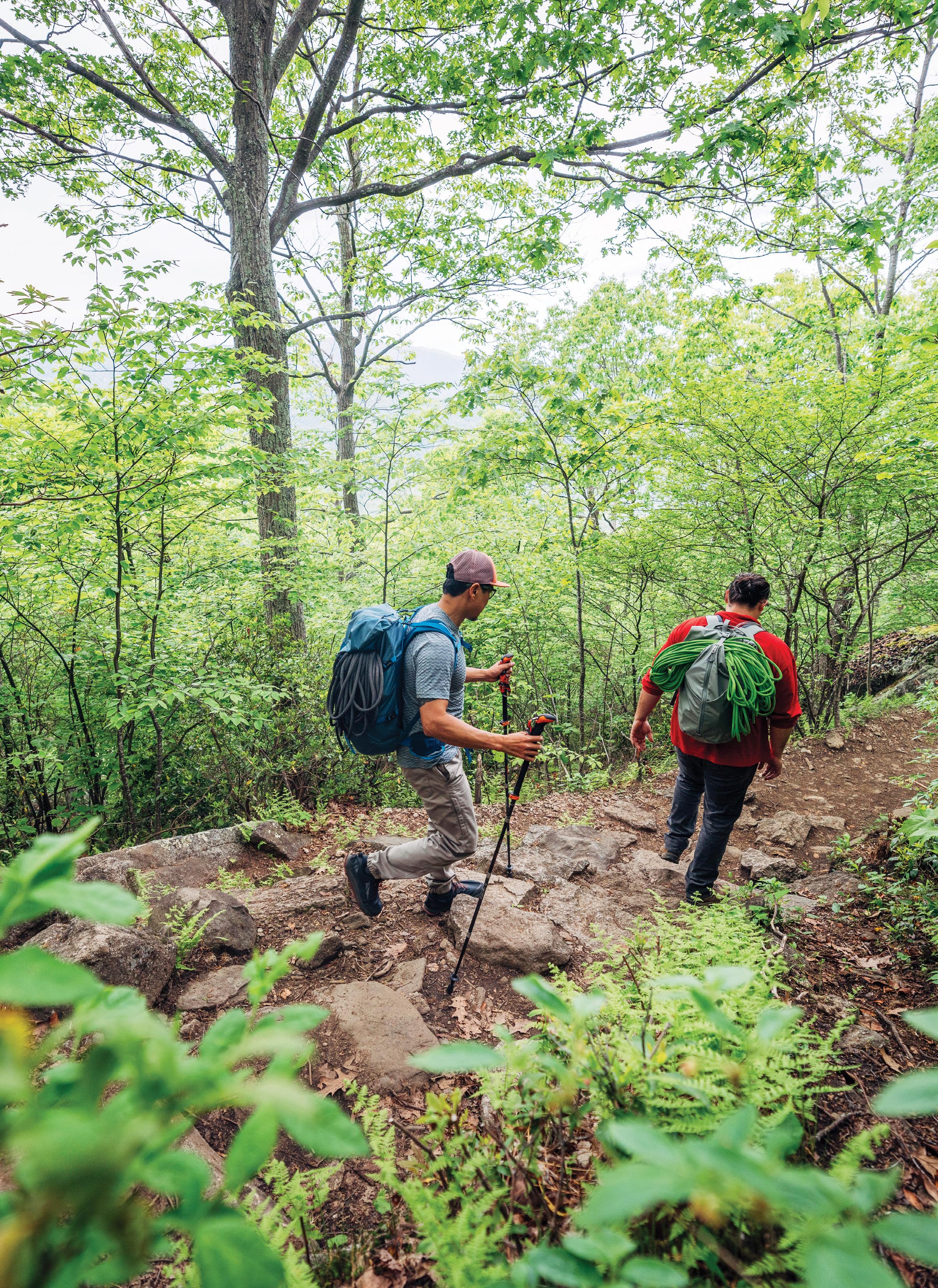
Old Rag Mountain in Madison County is the most popular hiking destination in Shenandoah National Park. The exposed granite summit offers an unusual climbing experience similar to the rocky summits found in California mountains.
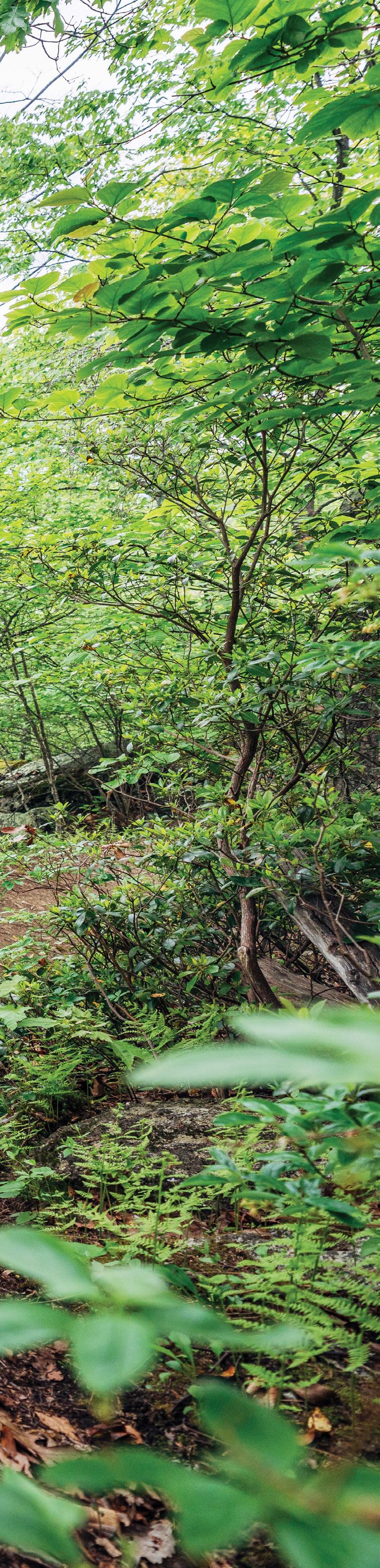
Finding Supply Chain Balance Between Efficiency and Redundancy
FOR SUCH A COMPLICATED TOPIC, the key tension of supply chains is an easy one to express: the balance between efficiency and redundancy. A more intense focus on redundancy helps ensure a more resilient flow of materials and goods but increases expenses, while decreasing redundancies drives costs down but leaves companies more vulnerable to disruption. The COVID-19 pandemic threw this dichotomy into sharp relief, leaving ships waiting off the West Coast, unable to dock for unloading as shipments overwhelmed port facilities. Geopolitical conflicts, climate issues, and unpredictable “black swan” events like the Francis Scott Key Bridge collapse in Baltimore have strained logistics networks even further.
Companies have responded to these disruptions in various ways. Some have rethought their supply chains to shorten shipping times and minimize potential issues. Others are using data and technological advances to optimize operations. Through it all, Virginia has stood ready as a trusted partner in helping companies get materials and products to their destinations. In an industry that strives for reliability and predictability, the Commonwealth and The Port of Virginia have demonstrated dependability time and time again while continuing to enhance the features that make Virginia a reliable place to move product.
In this issue of Virginia Economic Review, we explore the state of the supply chain in an increasingly global, post-pandemic world. Inside are insights into how supply chain considerations drive site selection, including a targeted look at manufacturing issues. We also detail Virginia’s targeted
infrastructure investments, go in depth on Washington Dulles International Airport’s emergence as a key cargo hub, and profile highly targeted logistics workforce development programs at colleges in the Hampton Roads region.
Also inside are discussions with key supply chain thought leaders: Ashleigh de la Torre, vice president of public policy at Amazon; Myra Blanco, chief growth officer at the Virginia Tech Transportation Institute and CEO of the university’s Dock to Door Coalition; Lance Harcrow, chief operating officer at Richmond-based freight forwarder Estes Forwarding Worldwide; and Mike Coleman, president and CEO of Norfolk-based global logistics provider CV International.
We hope you enjoy this look into the systems that help ensure consumers across the country can access the products they need and enjoy. Companies can rest assured that a decision to move supplies and products through Virginia will pay off with reliable service for businesses and consumers through every link in the supply chain.
Jason El Koubi President and CEO, Virginia Economic Development Partnership
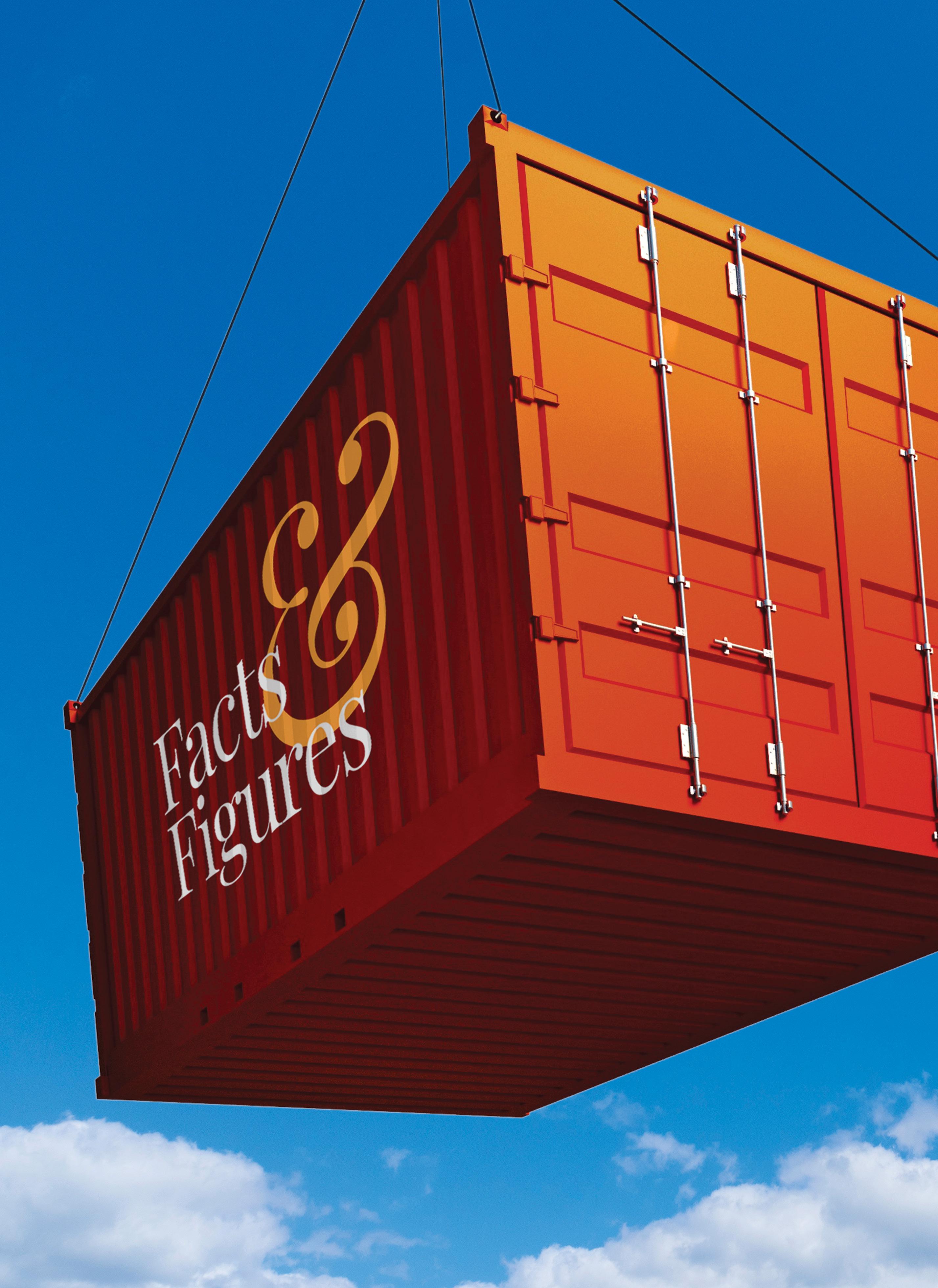

1.8 million (imports) 2.8 million 1 million (exports) +
Twenty-foot equivalent units (TEU) volume at The Port of Virginia, FY22
THE PORT OF VIRGINIA, 2023
100%
Percentage of energy from clean sources
THE PORT OF VIRGINIA, 2024
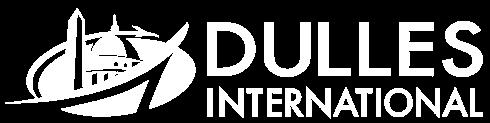
56%
Percentage of U.S. population within an overnight drive
METRO WASHINGTON AIRPORTS AUTHORITY, 2023

#1
Most efficient airport in North America
AIR TRANSPORT RESEARCH SOCIETY, 2023
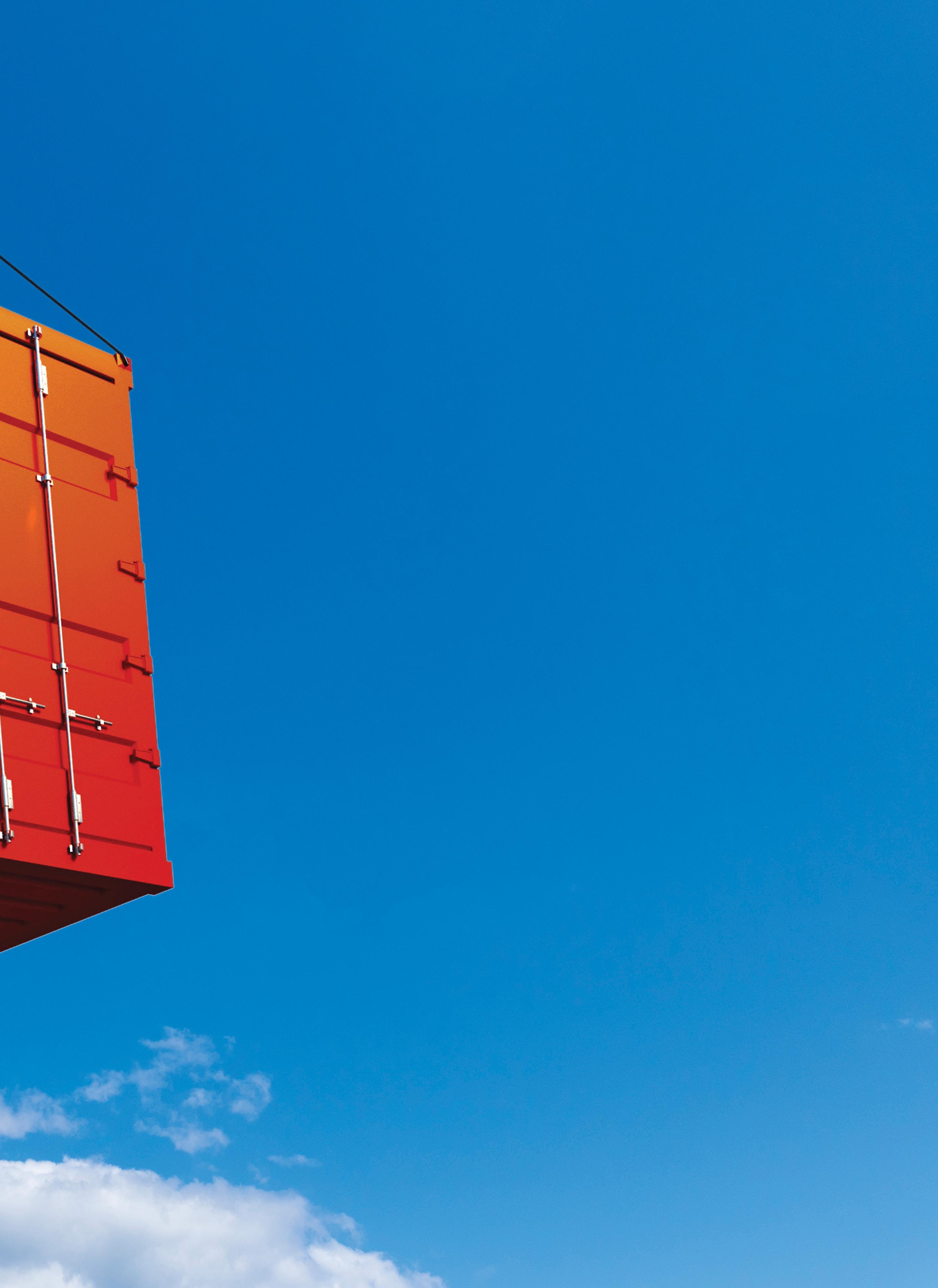
#1
Most efficient large port in North America, 2022
WORLD BANK GROUP, 2023
14%
Year-over-year percentage increase in total cargo activity
METRO WASHINGTON AIRPORTS AUTHORITY, 2023
27%
Year-over-year percentage increase in total cargo activity
RICHMOND INTERNATIONAL AIRPORT, 2023
Selected Virginia Wins
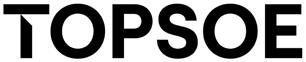
Topsoe, a Danish manufacturer and global leader in carbon emission reduction technologies, will invest more than $400 million to build a factory at Meadowville Technology Park in Chesterfield County. The company will manufacture advanced, energy-efficient solid oxide electrolyzer cells that are essential in the production of clean hydrogen at the facility. Federal tax credits from the U.S. Department of Energy under the Qualifying Advanced Energy Project Credit (Section 48C) will support the construction of the facility, which is Topsoe’s largest U.S. investment. The project will create 150 new jobs.
To support the next generation of innovators, Topsoe also plans to launch the “Topsoe STEM Scholarship” program, which will award five $10,000 one-year scholarships to high school seniors from Chesterfield County high schools. These scholarships will be awarded to eligible high school seniors seeking to continue their education in a STEM major in college, with the first awards given in the spring of 2025 for the next academic year. Topsoe plans to continue this scholarship program in subsequent years.
Support for Topsoe’s job creation will be provided through the Virginia Talent Accelerator Program, a workforce initiative created by VEDP in collaboration with the Virginia Community College System. The program accelerates new facility start-ups through the direct delivery of recruitment and training services that are fully customized to a company’s unique products, processes, equipment, standards, and culture. All program services are provided at no cost to qualified new and expanding companies as an incentive for job creation.
We are thrilled to announce our plans for this new U.S. facility. Through legislation like the Inflation Reduction Act and strong support from individual states like Virginia, the United States is positioning itself as a clean energy leader. With our strong dedication to scientific research and innovation, we will help the U.S. achieve its goals of driving down the cost of clean hydrogen and delivering clean energy jobs.
ROELAND BAAN President and CEO, Topsoe


Selected Virginia Wins
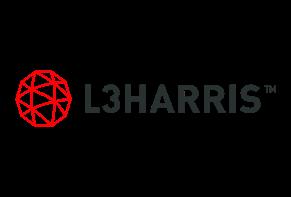
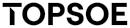
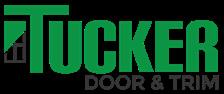
Central Virginia
L3Harris Technologies
Jobs: 80 New Jobs
CapEx: $41.2M
Locality: Orange County
Greater Richmond
Topsoe
Jobs: 150 New Jobs
CapEx: $400M
Locality: Chesterfield County
Tucker Door & Trim
Jobs: 50 New Jobs
CapEx: $10M
Locality: Henrico County
Hampton Roads
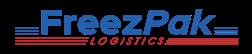
FreezPak Logistics, LLC
Jobs: 80 New Jobs
CapEx: $77.5M
Locality: City of Suffolk
Middle Peninsula


West Point Veneer LLC
Jobs: 92 New Jobs
CapEx: $2.5M
Locality: King William County
New River Valley
ESS Technologies, Inc.
Jobs: 27 New Jobs
CapEx: $1.6M
Locality: Montgomery County

Northern Virginia JDSAT, Inc.
Jobs: 60 New Jobs
CapEx: $630K
Locality: Fairfax County
Shenandoah Valley

Boxer Gifts LLC
Jobs: 15 New Jobs
CapEx: $1.4M
Locality: City of Harrisonburg

Modine
Jobs: 211 New Jobs
CapEx: $18.1M
Locality: Rockbridge County
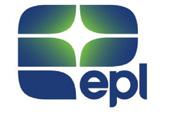
Southern Virginia EPL America
Jobs: 24 New Jobs
CapEx: $37.4M
Locality: City of Danville
Virginia’s
Gateway Region
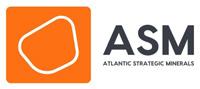
Atlantic Strategic Minerals
Jobs: 71 New Jobs
CapEx: $50M
Locality: Sussex County
Northern Shenandoah Valley
Northern Virginia Shenandoah Valley
Central Virginia
Washington, D.C.
Greater Fredericksburg
Northern Neck
Middle Peninsula
Greater Richmond
Hampton Roads Virginia’s Gateway Region Lynchburg Region
Southern Virginia
South Central Virginia
Eastern Shore

The Quest for Supply Chain Balance
Through disruptive events, companies look to strengthen supply chains while remaining cost-effective
EARLY ON THE MORNING of March 27, a container ship about as tall as the Eiffel Tower left the Port of Baltimore going approximately 9 mph. The ship, named the Dali, was fully loaded with cargo and weighed nearly 100,000 tons. Shortly after leaving the port, it lost power and collided with the Francis Scott Key Bridge. Six workers on the bridge fell to their deaths. The Baltimore icon, a 1970s engineering marvel, folded like wet cardboard, and one of the largest ports on the East Coast shut down instantly.
The accident highlighted the fragile nature of global supply chains, which are still recovering from the COVID-19 pandemic. But it also revealed how supply chain resilience can provide the flexibility manufacturers and shippers need when faced with ongoing disruption.
One node of the vast global web of supply chain infrastructure was ready to step in and support Baltimore through this crisis: The Port of Virginia.
RESILIENCY VS. EFFICIENCY
The Port of Virginia is the sixth-largest port in the United States by container volume. It’s also the most efficient large port in North America, as ranked by the

World Bank and S&P Global Market Intelligence. The morning of the Key Bridge collapse, Stephen Edwards, CEO of The Port of Virginia, immediately notified his team to expect additional ships diverted from Baltimore.
“I didn’t get a call because it wasn’t our port,” Edwards said. “But when I woke up, there were plenty of texts. I knew straight away it was a major event.”
According to Gary La Point, professor of supply chain practice at the Whitman School of Management at Syracuse University, ensuring supply chain resilience requires balancing efficiency with redundancy in manufacturing and transportation. “One of the big problems with creating a resilient supply chain is that it’s not necessarily an efficient supply chain,” La Point said. In other words, resilience comes at a cost.
Until the COVID-19 pandemic, companies optimized for efficiency over resiliency. “The pandemic woke everybody up because so many were caught completely off guard, and their supply chains suffered,” La Point said. “They had offshored and outsourced many of their [products] to Asia, particularly China.”
The pandemic woke everybody up because so many were caught completely off guard, and their supply chains suffered.
GARY L A POINT Professor of Supply Chain Practice, Syracuse University
James Brucken, a Deloitte Consulting LLP specialist executive who advises government clients on supply chain issues, says increasing complexity has also contributed to supply chain fragility. “Globalization of supply chains over the years has increased risk. More cross-border activity involves more partners in countries, cities, and infrastructures across the world,” he said.
Now, companies are scrambling to change how they manage supply chains. La Point and Brucken say newly available data and advanced analytics can help.
DISRUPTION AS A CONSTANT
According to Edwards, shippers deal with constant disruption.
“As you run through a year, you’re going to have a nor’easter. You’re going to have weather on the Atlantic. You’re going to have ship delays due to hurricane patterns in the summer,” he said. “Judging by looking out my window right now, we’ll probably have to stop operations at some point tonight due to high winds. These things happen in the normal course of business.”
Changes in how consumers purchase goods also play a role in supply chain disruption, like the shift to e-commerce during the COVID-19 pandemic.
E-commerce emphasizes last-mile shipments of small numbers of products
to individual consumers instead of shipping pallets to retailers. This complicates logistics networks and puts downward pressure on revenue. Despite some retailers’ claims to the contrary, “Smaller, more frequent shipments are more expensive,” La Point said. “There’s no free shipping.”
Therein lies one of the challenges of building more resilient supply chains. Greater resilience means more sources of goods and more shipping methods acting as backups. But such redundancy increases costs, and that became abundantly clear during the pandemic.
AN UNPREDICTABLE ENVIRONMENT
The pandemic exacerbated a persistent supply chain problem. “When you’re in the supply chain, you either have too much product or not enough product,” Brucken said. “It’s one or the other.”
During the pandemic, consumer demand radically changed when people stayed home in large numbers. “Spending shifted off of services, vacations, and leisure to hard goods delivered directly to homes,” Brucken said.
The change compounded an existing situation as goods flowed into the country and couldn’t move. “Containers were out of balance to begin with because we import far more than we export,” La Point said. “We had hundreds of ships parked off the coast,
waiting to be unloaded, because we didn’t have any place to put anything. It took years to get rid of all the stuff in the warehouses.”
And the impact of this, according to Brucken, “is still an ongoing oscillation or bull-whip effect today.”
Complicating matters even further during the pandemic, a large container ship ran aground and blocked the Suez Canal for nearly a week, costing the global economy billions of dollars a day in trade. It turned out to be a preview of things to come.
In late 2023, a drought cut the Panama Canal’s capacity from 38 container ships daily to 24. Experts blame normal weather fluctuations, along with an overall warming trend.
CLIMATE DISRUPTIONS
According to the latest U.S. National Climate Assessment, “Climate adaptation and emissions mitigation will require major transformations of supply chain transportation infrastructure and technologies.” The report cited drought, extreme heat, flooding, and more severe weather events.
Given the lingering supply chain headaches of the pandemic and ongoing global disruptions, “Just about every company now has made risk management a priority,” La Point said. “Virtually all have reassessed their supply chain strategies to reduce their risk of disrupting their continuity of supply.”
Companies are also assessing their contribution to global greenhouse gas emissions. Ed Elkins, executive vice president and chief marketing officer at Norfolk Southern Corporation, said rail transport, which is more efficient than other overland shipping modes, can aid companies in meeting their emissions goals.
“Railroads are an essential part of a low-carbon supply chain,” he said.
“Our locomotives can haul one ton of freight over 470 miles on a single gallon of fuel.”
Rail transport, as part of a multimodal transport strategy incorporating maritime, road, and air, serves as a method of balancing competing shipping and inventory considerations. Overreliance on air freight, while efficient, can drive up costs. The ability to flex between different modes of transport helps companies navigate delays and maintain a seamless flow of products.
Virginia’s port facilities enable companies to take advantage of multimodal capabilities. All of the port’s terminals rely on rail access and proximity to major highways to move goods on to their destinations, while the Richmond Marine Terminal’s James River barge service offers a maritime alternative to the port’s terminals in the Norfolk Harbor. Virginia’s mix of public and private investment, including privately held, interstate-adjacent freight processing operations, positions the Commonwealth as a complete gateway through which companies can reach suppliers and customers across the country and the world.
SUFFICIENT AND RESILIENT
Shorter supply chains are more resilient supply chains. La Point cites tool manufacturer Snap-on Incorporated as an example of a company that weathered the pandemic well because of short supply chains made possible by manufacturing goods near consumers. “For example, what they make in China stays in China,” he said. “It doesn’t come back to the United States.”
According to La Point, artificial intelligence (AI) is contributing to more accurate supply chain forecasts.
“In the next couple of years, you’re going to see a dramatic change in the ability of artificial intelligence to be used in supply chain decisionmaking,” he said. “How should things
be routed? Where should we locate our distribution centers? Where do we locate manufacturing operations?”
AI can help supply chain managers with daily operations to prevent delivery delays like unplanned downtime. For example, Norfolk Southern is rolling out AI for automated rail car inspection. Trackside cameras capture hundreds of images per car as trains roll by. “Identified issues are promptly flagged and reviewed by experts at our Network Operations Center, ensuring proactive maintenance and immediate handling of any critical defects,” Elkins said.
READY FOR WHAT’S NEXT
The operating team at The Port of Virginia reacted quickly to the Key Bridge collapse. Crews were unloading cargo originally bound for Baltimore by that evening, according to Edwards.
The supply chain effects of the Key Bridge collapse were temporary. The shipping channel was cleared within a few months of the accident. But other potential hazards will persist, from typical weather-related delays to the longer-term effects of climate change and global conflict. Supply chain managers and port operators will have to continue to adjust.
Virginia’s port facilities stand ready to serve as a partner to shippers, utilizing road, rail, and maritime options to move goods on to the next step in their supply chain journey. The port is investing $1.4 billion to expand its capabilities and efficiency and advance technology throughout the operation. This investment, Edwards said, positions The Port of Virginia for long-term growth and almost any eventuality.
“We found that we can flex capacity quite quickly, and that allows for these disruptive events,” he said. “We’re determined to stay ahead of the curve.”
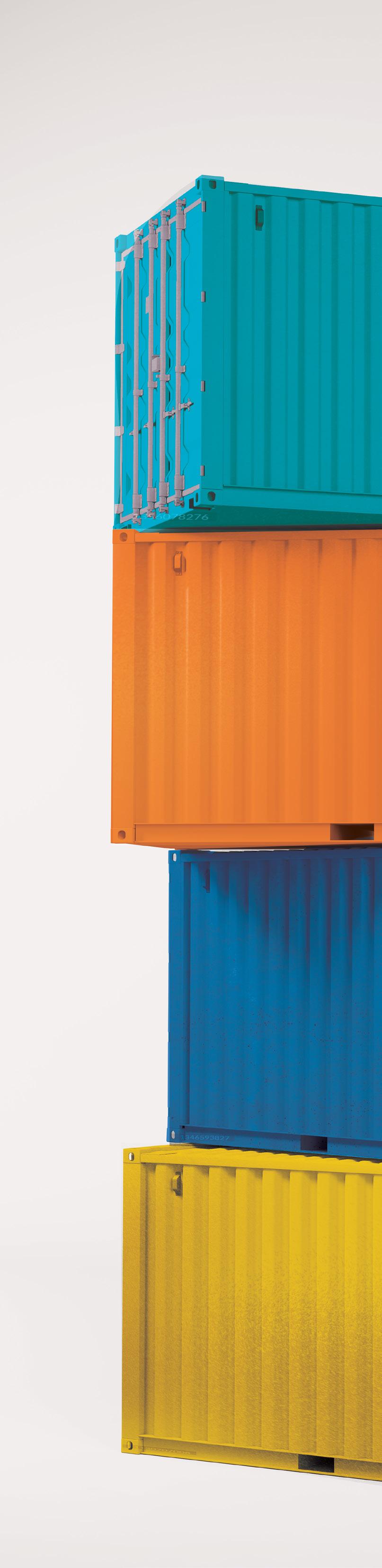
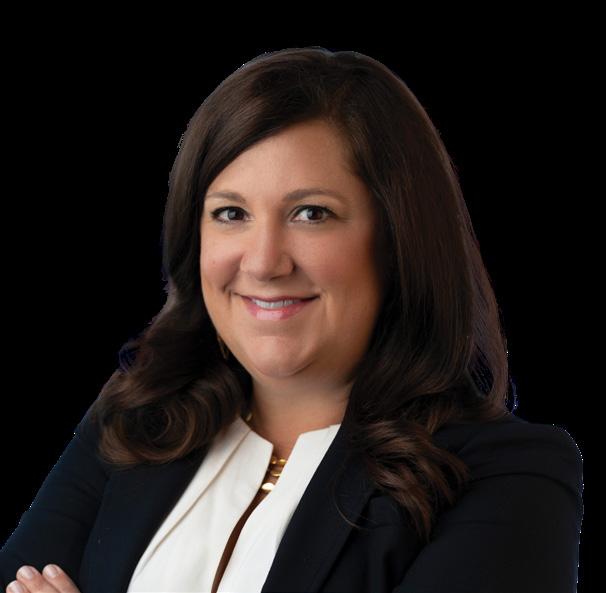
IN TECHNOLOGY AND PEOPLE
A CONVERSATION WITH
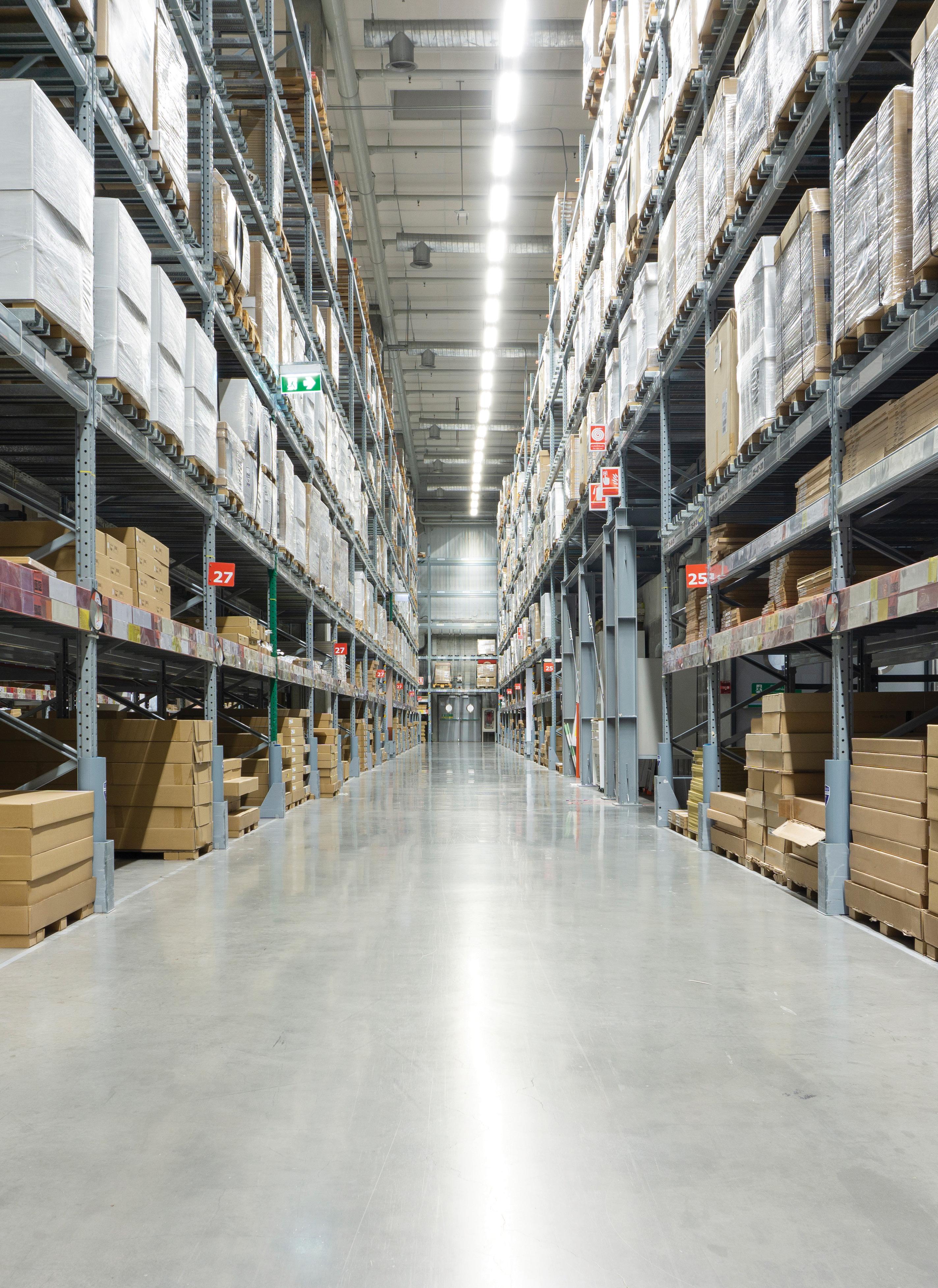
ASHLEIGH de la TORRE
Ashleigh de la Torre is vice president of public policy at Amazon, where she leads the company’s transportation and sustainability initiatives, supporting its operations, logistics, and delivery businesses across land, air, and sea. VEDP President and CEO Jason El Koubi spoke with de la Torre about Amazon’s complex logistics operations and ambitious sustainability goals, as well as how technological advances are transforming the way the company looks across its operations to invest in solutions, its people, and communities.
Jason El Koubi: What are some of the global events, geopolitical and otherwise, having the most pressing effects on Amazon’s supply chain right now, and what are you doing to respond to them?
Ashleigh de la Torre: My team supports the business teams that get goods into and through our fulfillment network and on to our customers in two days or less. We’re now one of the world’s largest package delivery services. Naturally, supply chain issues are super important to our teams. We’re investing in our logistics and supply chain network across our operations. Today, that includes global maritime transportation, middle-mile trucking and aviation, and then last-mile delivery to our customers’ doorstep.
We’ve invested more than $1 trillion across the U.S. since 2010 and now employ over 1 million people. I’m super proud of what we’ve also invested in Virginia, which, as you know, is a great place to do business, and where we are proud to have our second headquarters.
Since 2010, we’ve invested more than $109 billion in Virginia and employ over 39,000 folks. We continue to grow and invest. As I said, my focus is our transportation and delivery network. In order to deliver packages, our logistics network uses all modes of transportation. That includes ships, planes, trains, trucks, vans — even drones and bicycles.
Top of mind to me when you mentioned global issues are continued disruptions in the Red Sea, the Panama Canal
drought and transit restrictions, and the recent tragic collapse of the Francis Scott Key Bridge in Baltimore, all of which have effects on supply chains. We work closely with our ocean carrier partners to pivot operations. That most often means moving volume to the West Coast to address issues with restrictions through the Panama Canal or moving our Baltimore-bound cargo to Newark or Norfolk, where we have ports and terminal operations that will allow us to handle that incremental volume in the meantime.
El Koubi: You mentioned you’ve just crossed the $100 billion number with your investments here in Virginia including, among other things, HQ2. We’re very proud to host you here in Virginia.
Let’s localize this for a minute. At the recent ribbon-cutting for your facility in Henrico County in Virginia, we learned several insights about your demand patterns, how you’re optimizing the network, and how you identified the need for that particular facility. Can you tell us a little bit about that process, the analytics, and how you ultimately come to a decision to invest in a particular facility as part of this global network?
de la Torre: We are proud to have opened our latest fulfillment center, which is what we call our distribution centers, our large warehouses. It’s a 2.7-million-sq.-ft. facility and the Commonwealth’s second Amazon Robotics Fulfillment Center. That means we have over 1,000 employees who are working side by side with our technology to deliver to customers.
Our fulfillment network consists of fulfillment centers, intermediate sorting centers, and then last-mile delivery stations. Previously, we had a nationwide network that was fulfilling orders across the United States, so if someone from Miami ordered something that was across the country, we would find a way to get it to Miami. We realized we might be able to do things more efficiently, make better use of our technology, and help drive down emissions if we restructured the network.
Instead of that national network, we restructured into eight regional networks. What that means now is more customer orders are being fulfilled from the fulfillment centers closer to them.
Before, the percentage of customer orders being fulfilled from the closest region was around 62%. The rest had to come from farther away. Now, with regionalization in place, we are able to fulfill 76% of customer orders from the region in which they’re located, which is a huge efficiency gain. We certainly expect that number to climb.
It also means that delivery speeds have improved because goods are traveling shorter distances and we’re seeing better truck utilization. That’s better for the environment, it’s better for our delivery speeds, and ultimately better for our customers.
El Koubi: You talked about this specific example in Henrico County. That had a lot to do with the particular configuration and demands within Amazon’s supply chain network. How
is the broader supply chain ecosystem learning and adapting based on what you’re doing? How might other companies and industries follow a similar type of approach?
de la Torre: I can share with you a bit of the lessons we’ve learned. I don’t know that it’s particularly any secret sauce, but it has been successful for us.
As I mentioned, we found that fulfilling inventory closer to our customers reduces the distance packages travel, particularly in the middle mile. That’s trucking or aviation, which is the hardest segment to decarbonize, so anywhere we can reduce those stage lengths is a benefit all around. We also found that shorter routes make our network more conducive to introducing electric vehicles and other low-impact transportation modes.
El Koubi: What are you doing to improve supply chain visibility and glean different insights from the data to apply to demand planning, forecasting, and inventory management?
de la Torre: We’ve had to invest in a lot of technology and machine learning to help us determine inventory management so that we have the right stuff available for customers for two-day, and often less than two-day, delivery.
Our supply chain optimization technologies team is responsible for that. They work on some of the world’s most complex supply chain challenges, but at Amazon scale. They’re using data visualization to help understand customer buying patterns, to decide how much inventory to buy, and where to put it.
It’s dynamic, complex, and difficult to do, but the way I simplify it for my own purposes is, for example, stocking cold-weather items, like winter coats, where they’re most likely to be ordered in the northern states. We’re not putting a lot of snow shovels and winter coats
Since we started including robotics in our facilities in 2012, we have created over a million jobs and also deployed more than 520,000 robotic drive units worldwide. It is really a symbiotic relationship where the more we embrace technology, the more we’re able to increase our ability to employ folks.
ASHLEIGH de l A TORRE Vice President of Public Policy, Amazon
in Miami when we know they’re going to be needs in the upper peninsula of Michigan.
It’s a super-simplified way of thinking about it, but that’s how our teams try to anticipate customer needs and place inventory appropriately. I would say, a vast majority of the time, we get it right.
I do, though, have one fun story to share. We were unprepared for a surge in demand that we didn’t anticipate. There’s a famous pop artist who started dating a famous NFL star, and this NFL star’s jersey…
El Koubi: I think I might know who you’re talking about.
de la Torre: …was stocked primarily in the Midwest, where the teams could reasonably expect orders for that jersey to come from. Once the news of their relationship started, we had orders for this jersey surge across the United States. We could have never predicted we would need Mr. Kelce’s jersey in every state in the country. That’s an example of where we certainly did not predict the surge.
El Koubi: What can non-consumerfocused companies glean about the ways you do material handling and physically move goods in a more cost-effective, safe way?
de la Torre: We spend a lot of time thinking about the customer, how we can make sure we’re anticipating their needs, and understanding what is going to remain constant over time. Rather
than chasing trends, we think about what the customer will always want, which is the largest selection, the lowest prices, and the fastest delivery speeds. We continue to focus on that as our North Star and think about how we can make sure we’ve got the goods in place and the services that customers will want to meet those requirements.
El Koubi: How has technology transformed the way employees are working in the supply chain industry, both in terms of what it means for jobs, but also for the nature of the work itself?
de la Torre: Our newest Virginia facility is an Amazon Robotics facility. That means we have our associates working side by side with our robotics. We have found that the more technology we place in our operations, the more individuals we need to employ. Since we started including robotics in our facilities in 2012, we have created over a million jobs and also deployed more than 520,000 robotic drive units worldwide. It is really a symbiotic relationship where the more we embrace technology, the more we’re able to increase our ability to employ folks.
What I’ve also found is we’ve made our facilities safer, more efficient, and collaborative through robotics and advanced technologies like artificial intelligence, machine learning, and computer vision, for example. As we introduce technology and robotics into our operations, we need to train people for new work environments and new types of jobs. That’s one of the reasons
we’ve invested in programs like Amazon Career Choice and our Mechatronics and Robotics Apprenticeship Program. We really do need to train our people in high-demand fields like robotics and software engineering.
El Koubi: How is Amazon using technology — both in a physical sense, but also analytically — to drive sustainability goals?
de la Torre: I’ll start from the beginning. From when a customer clicks “Buy Now” on their app to when their package arrives, we’ve got teams of scientists and engineers working to make that entire process more sustainable without compromising speed, safety, or convenience. That’s not easy to do, but it’s the type of hard challenge our teams really like working on and that we are committed to solving every day.
We’re investing in renewable energy around the world. We’re the largest corporate buyer of renewable energy in the world for the fourth year in a row. Our teams are using machine learning and analytics to analyze routes and distances for where trucks are going. We’re transitioning our fleet to electric last-mile delivery vehicles. We’ve announced the purchase of 100,000 Rivian electric vehicle vans by 2030. We already have around 13,000 on the road today, and that’s all part of our effort to be net-zero carbon by 2040 across our operations, which is 10 years ahead of the Paris Agreement.
Last year, we reduced our overall emissions year over year, even though sales grew, so we know it’s possible. If a company Amazon’s size can do it, I think others can. That’s why we’ve announced our Climate Pledge to be net-zero carbon across our operations and invited other governments and companies to join us.
We don’t yet know how we’re going to get there. These are really hard challenges. I think a lot of the solutions
required don’t yet exist, but we’re investing in new technologies that have that promise. We are looking to governments to partner with us to try to create climate policy that helps to drive decarbonization. We encourage our suppliers and other businesses to join us in helping drive this transition to a cleaner economy.
El Koubi: It’s incredible to watch you and your colleagues lead the way on this and so many other tough challenges facing the world. As a related parting thought, if you could bring about any sort of instant lasting change on one supply chain-related issue — wave the magic wand, if you will — what would it be and why?
de la Torre: I would imagine the best future state and work backward from there. Using that approach here, I think it would be having immediate access to zero-emission fuels and technologies at scale so that all industries could
decarbonize. For not just Amazon, but all industries, all companies, and particularly our suppliers. I think it would go a long way to decarbonizing supply chain, and likely, I would think, helping create a whole new opportunity for companies to deliver faster and cleaner.
El Koubi: Fascinating conversation. Ashleigh, thank you so much for being with us.
de la Torre: It was my pleasure. Thank you. For the full interview, visit www.vedp.org/Podcasts

Virginia’s Exceptional Logistics Infrastructure
Virginia’s extensive network of well-maintained roads, railways, ports, and airports offers efficient logistics and global connectivity.
2nd
3,000 miles
densest roadway and railway networks in the Southeast of railways (anchored by Class I railroads CSX and Norfolk Southern)
6
300K+ tons
major interstates, including major North-South and East-West trucking routes of cargo annually handled by Washington Dulles International Airport
FUTURE FOCUSED
Virginia expands infrastructure capacity through targeted investments in road, rail, and port facilities
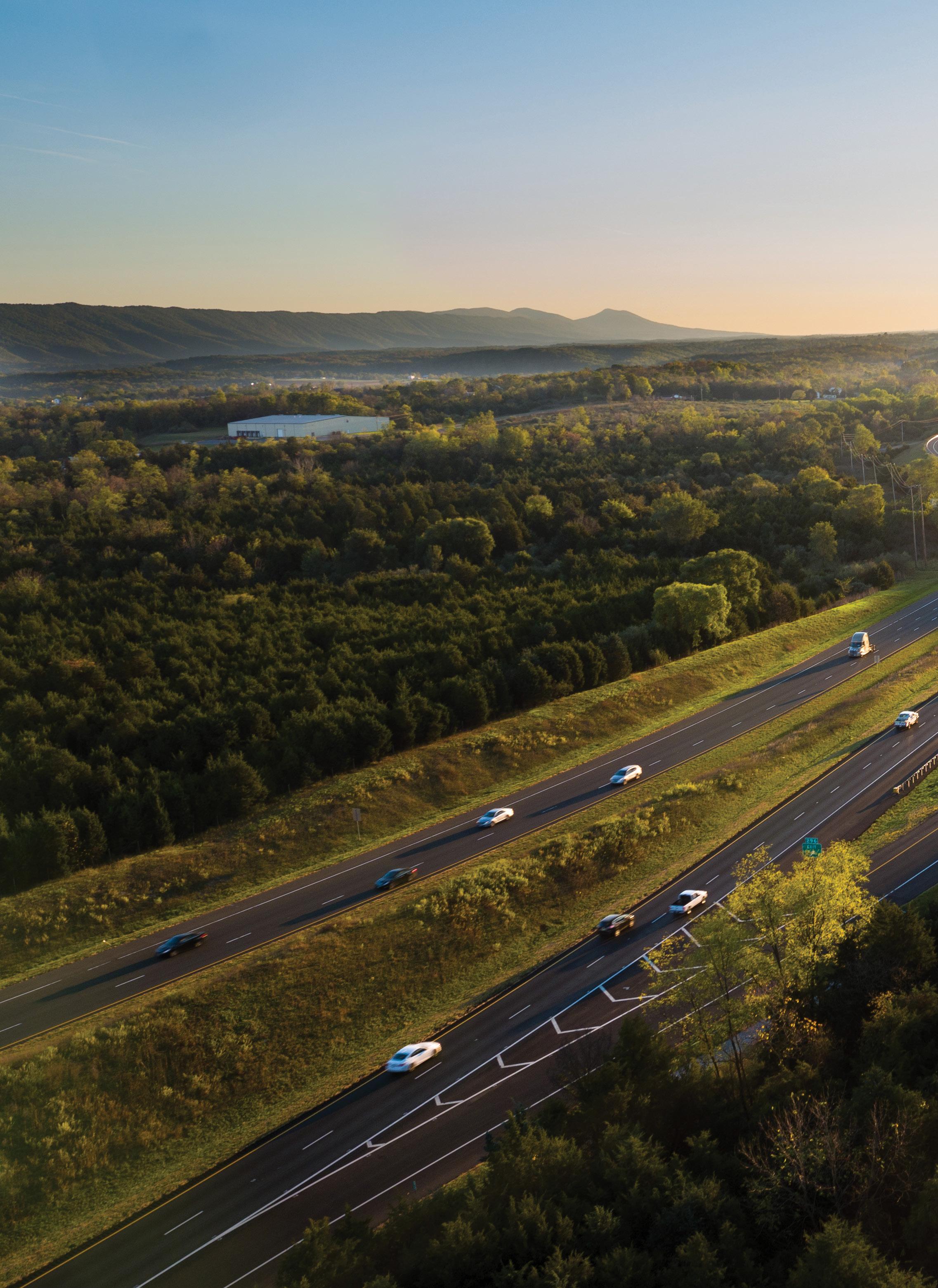
Interstate 81, a crucial North-South backbone of the East Coast freight network, has the highest per capita truck volume of all Virginia’s interstates. This section in Shenandoah County is scheduled to be widened to three lanes in each direction by late 2027.
57,867
Miles of state-maintained highway in Virginia, third-most in the country
6
Interstate highways operating in Virginia, along with auxiliary highways in the Richmond, Roanoke, Hampton Roads, and Northern Virginia areas
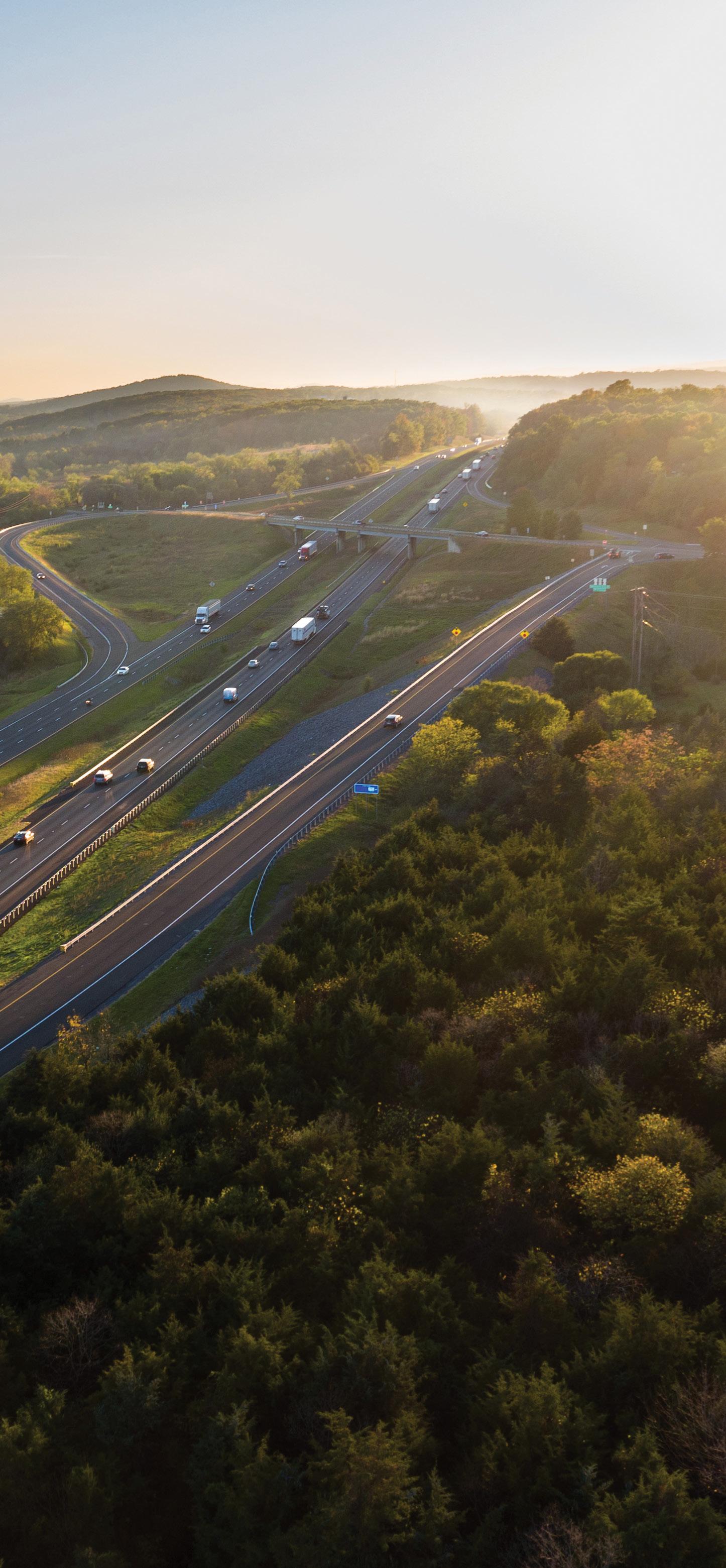
Upgrading Interstate Capacity Along Key Arteries
The Virginia Department of Transportation (VDOT) is in the midst of a $3.9 billion upgrade to the Hampton Roads Bridge-Tunnel, scheduled to be completed in 2027. The project, the largest highway construction effort in Virginia history, will see VDOT widen the current four-lane segments along a 10-mile stretch of Interstate 64 in Hampton and Norfolk and construct new twin tunnels across Norfolk Harbor, doubling the road’s capacity. The boring machine creating the tunnel — named “Mary” after former NASA Langley Research Center engineer Mary Winston Jackson, one of the “Hidden Figures” immortalized in the movie of the same name — completed boring for the first tunnel in April and is currently completing the second, a process expected to take approximately 11 months.
Elsewhere in the Commonwealth, VDOT is in the midst of its I-81 Corridor Improvement Program, aimed at upgrading Virginia’s main freight thoroughfare, which sees 11.7 million trucks move $312 billion in goods each year. VEDP worked with the Commonwealth Transportation Board to approve changes aimed at standardizing data entry across applications.
Miles of Interstate 81 in Virginia, more than any other state
Source: Virginia Department of Transportation
3,141
Miles of freight rail track in Virginia
Source: GoRail.org
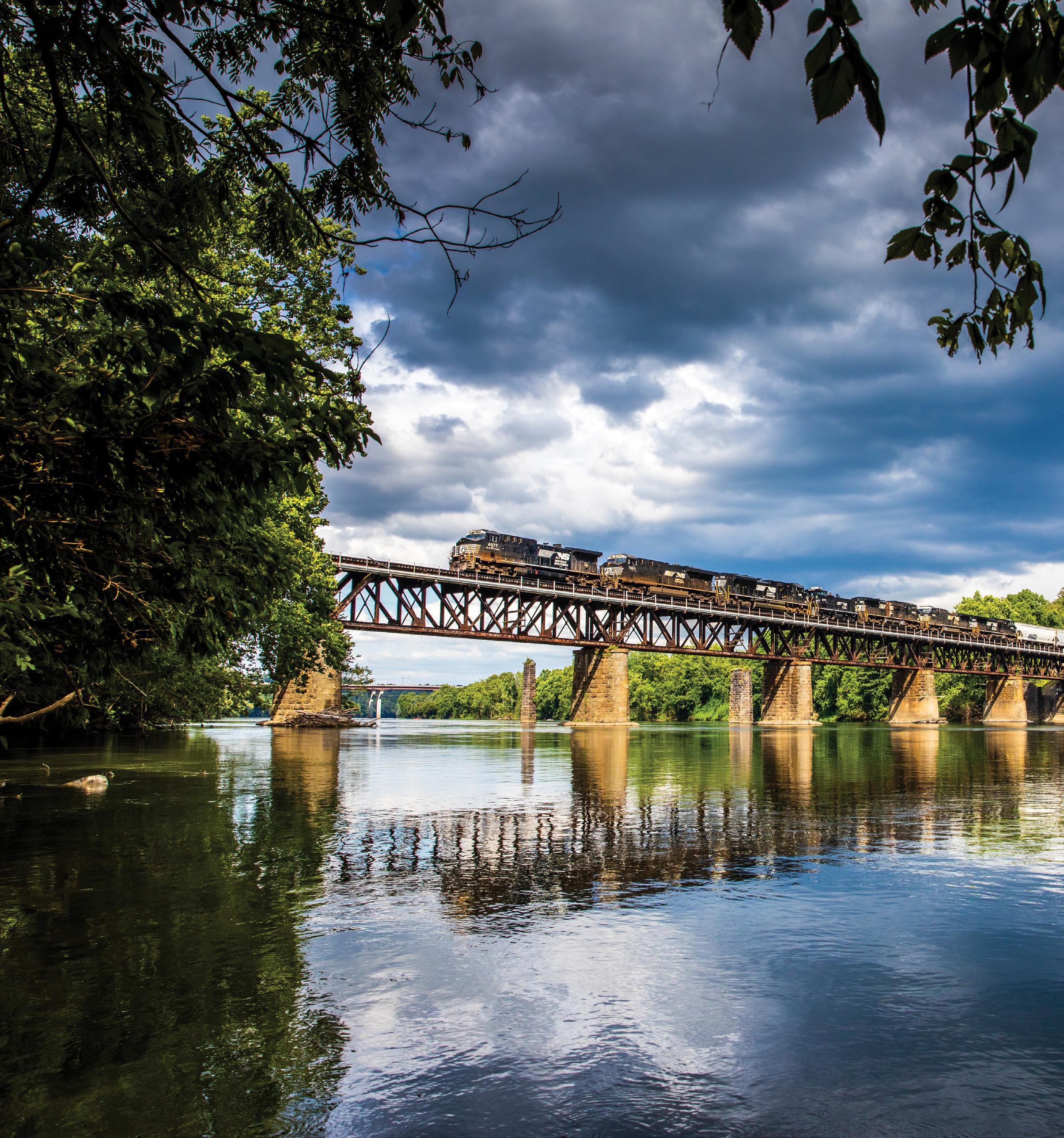
Partnerships
Strengthen Rail Infrastructure
While many of its upgrades are aimed at improving the passenger rail experience in Virginia, the Transforming Rail in Virginia (TRIV) initiative allocates $3.7 billion to improve passenger, commuter, and freight rail in the Commonwealth by expanding Amtrak’s Northeast Corridor line. TRIV consists of several projects aimed at improving railroad infrastructure, adding capacity, and improving reliability of freight and passenger rail. Nine of TRIV’s 15 initial projects are currently in various stages of preliminary engineering.
Freight rail in Virginia is provided by Norfolk Southern, shown here crossing the New River in Radford, and CSX. The two companies operate more than 85% of rail track in Virginia.
7,068
Average 2023 daily entries at WMATA’s Rosslyn station in Arlington County, the system’s busiest outside of Washington, D.C.
Source: Washington Metro Area Transit Authority
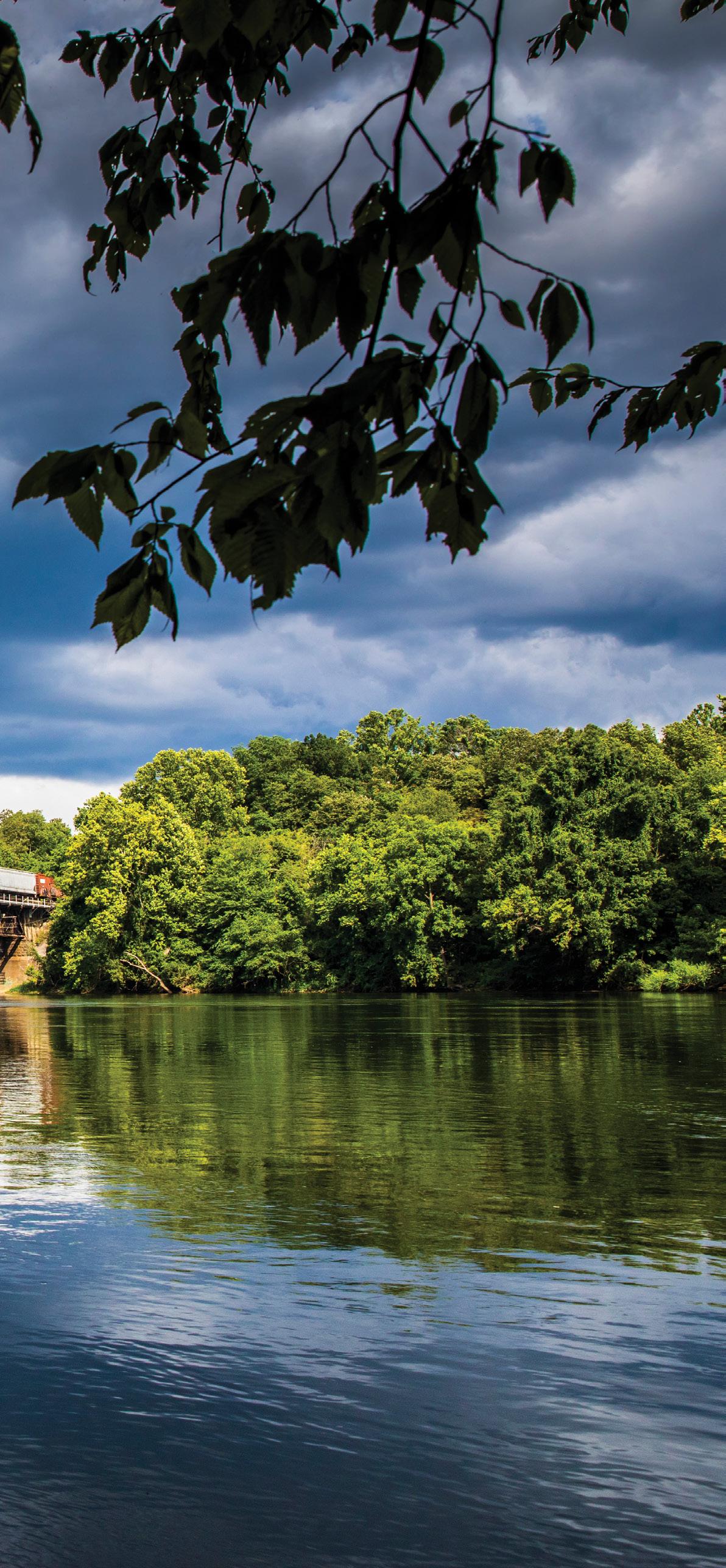
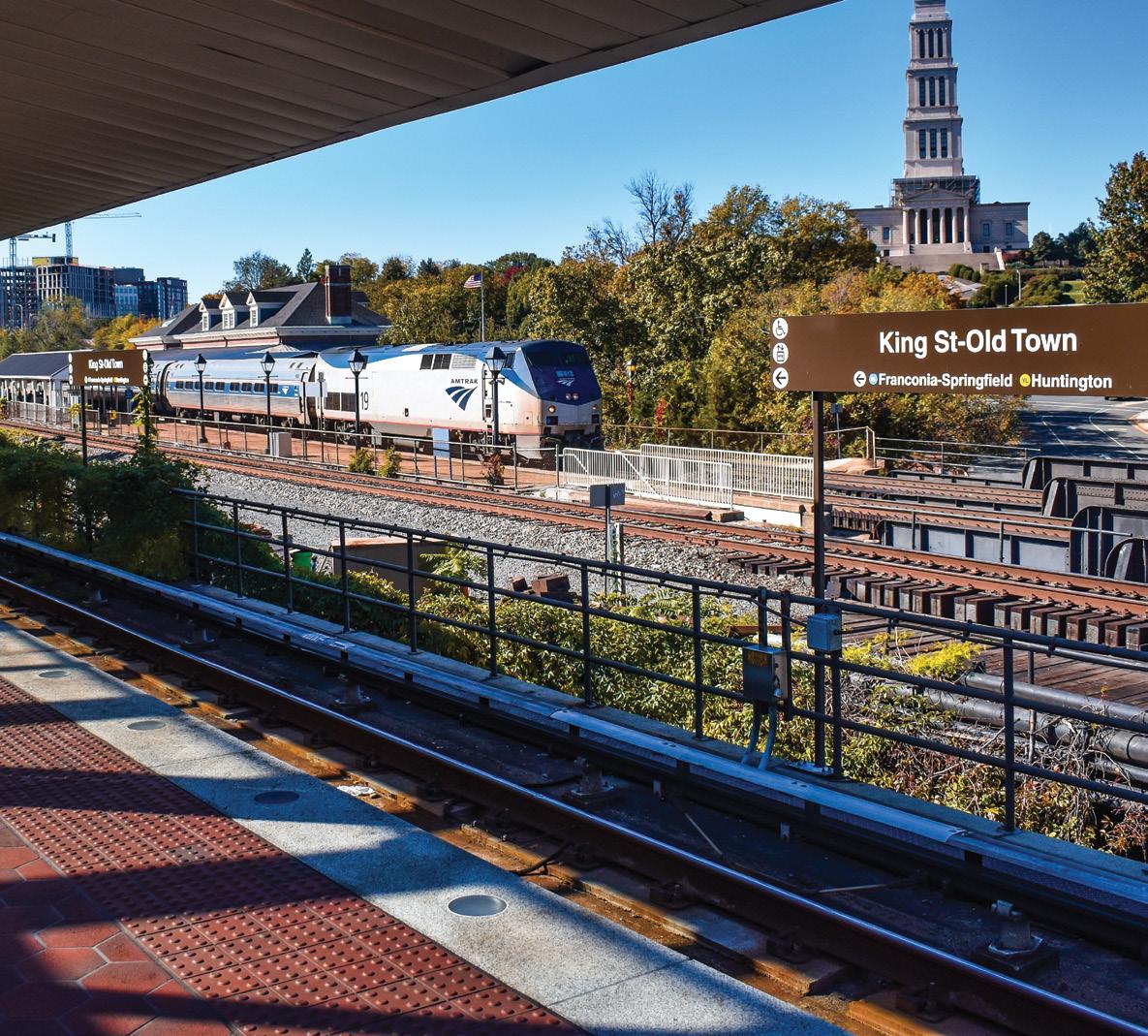
a

As part of the initiative, Amtrak is doubling its service along the Washington-Richmond corridor, increasing service to Roanoke, Newport News, and Norfolk, and extending service to Christiansburg. The Commonwealth has acquired nearly 400 miles of CSX Transportation right-of-way and more than 200 miles of track in rail corridors near Interstates 64, 85, and 95. Outside the Commonwealth, the Washington Metropolitan Area Transit Authority (WMATA) is beginning a three-year, $12.4 billion modernization effort of its system, with upgrades to the Blue Line in Fairfax County and Alexandria scheduled to begin in 2025.
The Washington Metropolitan Area Transit Authority, which operates the passenger rail system colloquially known as the D.C. Metro, is embarking on
$12.4 billion modernization effort that includes Blue Line stations like the King Street-Old Town station in Alexandria.
Among the major users of Norfolk Southern’s rail route through the Middle Peninsula town of West Point include paper and packaging giant WestRock, which runs a plant adjacent to the line.
The Port of Virginia Focuses on Fluidity, Sustainability
The Port of Virginia recently wrapped up $1.4 billion in upgrades to its Hampton Roads facilities, reaching milestones in sustainability and fluidity of operations. The port is the first major East Coast facility to power its entire operation using 100% clean electricity, with commitments to become carbon neutral by 2040. Earlier this year, the port opened a new, wider shipping channel in Norfolk Harbor that allows two-way traffic of ultra-large container vessels (ULCV), saving an estimated 15% of time on berth.
The port continues to work on its dredging initiative, which will deepen the shipping channel to 55 feet and the ocean approach to 59 feet. The $450 million project is expected to finish in 2025 and will give the port the deepest, widest channels on the East Coast.
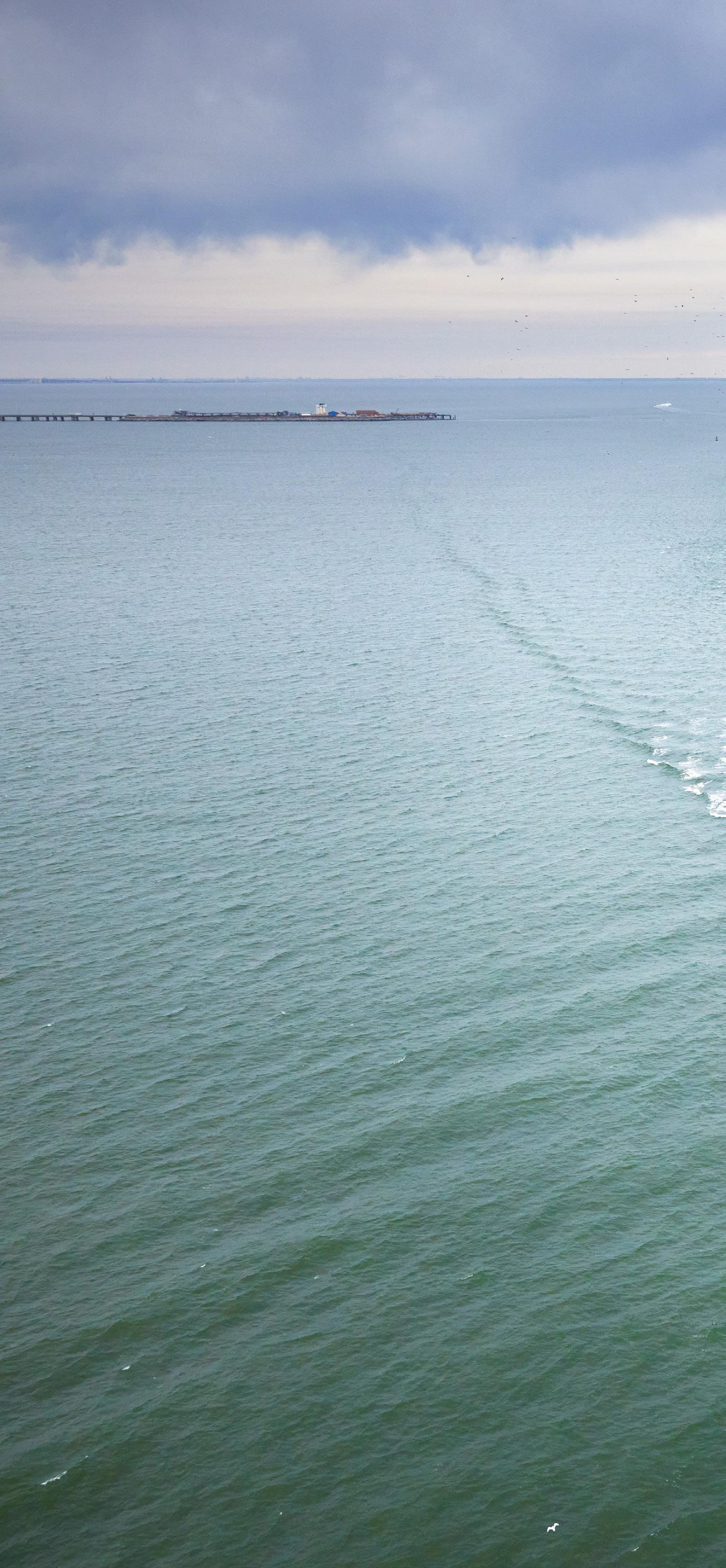
Total employment in Virginia supported by The Port of Virginia 11%
Source: The Port of Virginia, 2023
#1
Most efficient large port in North America, 2022
Source: World Bank Group, 2023
$107M
Total cargo dollar value, The Port of Virginia Norfolk Harbor facilities
Source: The Port of Virginia, 2023

Recently completed dredging operations from The Port of Virginia have created a shipping channel wide enough to accommodate two-way ultra-large container vessel traffic, while ongoing deepening efforts will enable unobstructed access for ships with no height restrictions.
SITE SELECTORS
SEEK SUPPLY CHAIN
PREDICTABILITY
COVID-19 issues drove companies to rethink logistics operations
Real estate developers have dealt with a daunting set of complications in the last few years, from increased borrowing costs to inflation to labor issues. It’s no surprise that developers and site selectors have focused on predictability as they consider supply chain factors in site decisions.
Supply chain predictability is paramount in every step as products travel from their point of origin to the end consumer, said Vincent Burke, senior managing director of development at Matan Companies, which is currently co-developing the Port 460 Logistics Center in Suffolk near The Port of Virginia’s Hampton Roads terminals.
That predictability, he said, must be in everything, “from the highway system to the rail system to the port to the technology used along the way.”
In a post-pandemic world, one thing is crystal clear: Supply chain considerations have emerged as an increasingly powerful driver of site selection. Sometimes it’s all about economies of scale. Sometimes it’s all about how a state responds to businesses’ needs. Sometimes it’s about companies hedging their supply chain bets by choosing more than one port to call home. In every case, however, it’s all about the relentless quest for predictability.
LOCATION, LOCATION, NOT LOCATION
In an unpredictable supply chain world, location isn’t just about where a port is located — but where it’s not located. That’s because, Burke said, the global supply chain basically broke during the height of the pandemic.
Many companies didn’t have enough built-in redundancies, nor were they flexible enough with their shipping and warehousing options. “The West Coast ports got choked and left folks scrambling to fix that,” Burke said.
During the height of the pandemic, warehouses at many West Coast ports were suddenly clogged with inventory as manufacturers and retailers worldwide found themselves facing an unpredictable virus. Last year’s negotiations for a new labor contract for 29 West Coast ports also complicated shipping decisions.
As a result, many companies are seeking more diversified port usage and shifting away from relying only on West Coast ports, according to Katie Lenss, managing director at New York-based developer Rockefeller Group. She said East Coast ports, such as The Port of Virginia, are benefiting from this new dynamic. The Port of Virginia grew container traffic by 32% between 2020 and 2022, ranking second only to Houston in growth rate.
PORT PROXIMITY DRIVES SUPPLY CHAIN INVESTMENTS
The main reason that Matan and Rockefeller partnered to develop the Suffolk site that will host the 540-acre Port 460 Logistics Center is its unique Virginia location, according to Burke. The port sits within a two-day drive of 75% of the entire U.S. population, making it an optimal location for logistics operations — particularly cold storage facilities that serve industries where freshness is paramount.
However, the operators of those facilities can’t rely on location alone to drive business. The average American warehouse is about 43 years old, according to CBRE research, and
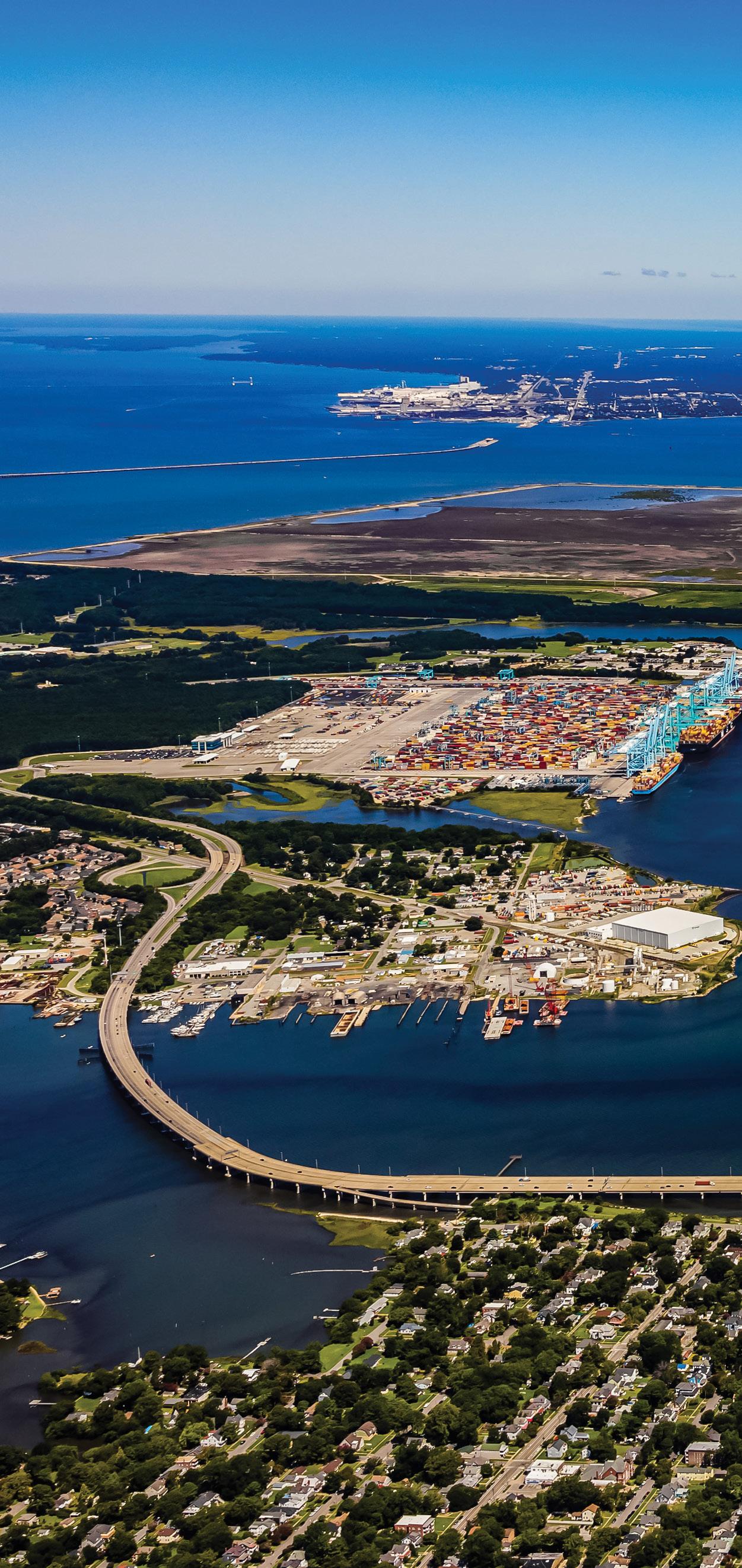
more than 80% of U.S. logistics assets were built before 2000. Many older warehouses were built under a now-adjusted set of best practices that has left owners to deal with lower-than-optimal ceilings, inefficient column spacing, and electricity issues.
Developers also want to operate in as pro-business an environment as possible. Companies are looking for certainty regarding permitting, utilities, and infrastructure. They also want to know how long it might take to get roads, rail, water, power, and sewer so they can confirm everything with their clients.
In addition to those issues, high interest rates and exacting federal regulations have challenged new development. As VEDP Vice President of Real Estate Solutions Michael Dreiling put it, “A major trend has been that the demands of the companies don’t match up with the interest rates and the time needed to deliver sites.”
NEWPORT NEWS MARINE TERMINAL
VIRGINIA INTERNATIONAL GATEWAY
PORTSMOUTH MARINE
TERMINAL/WIND ENERGY
HUB OF THE FUTURE
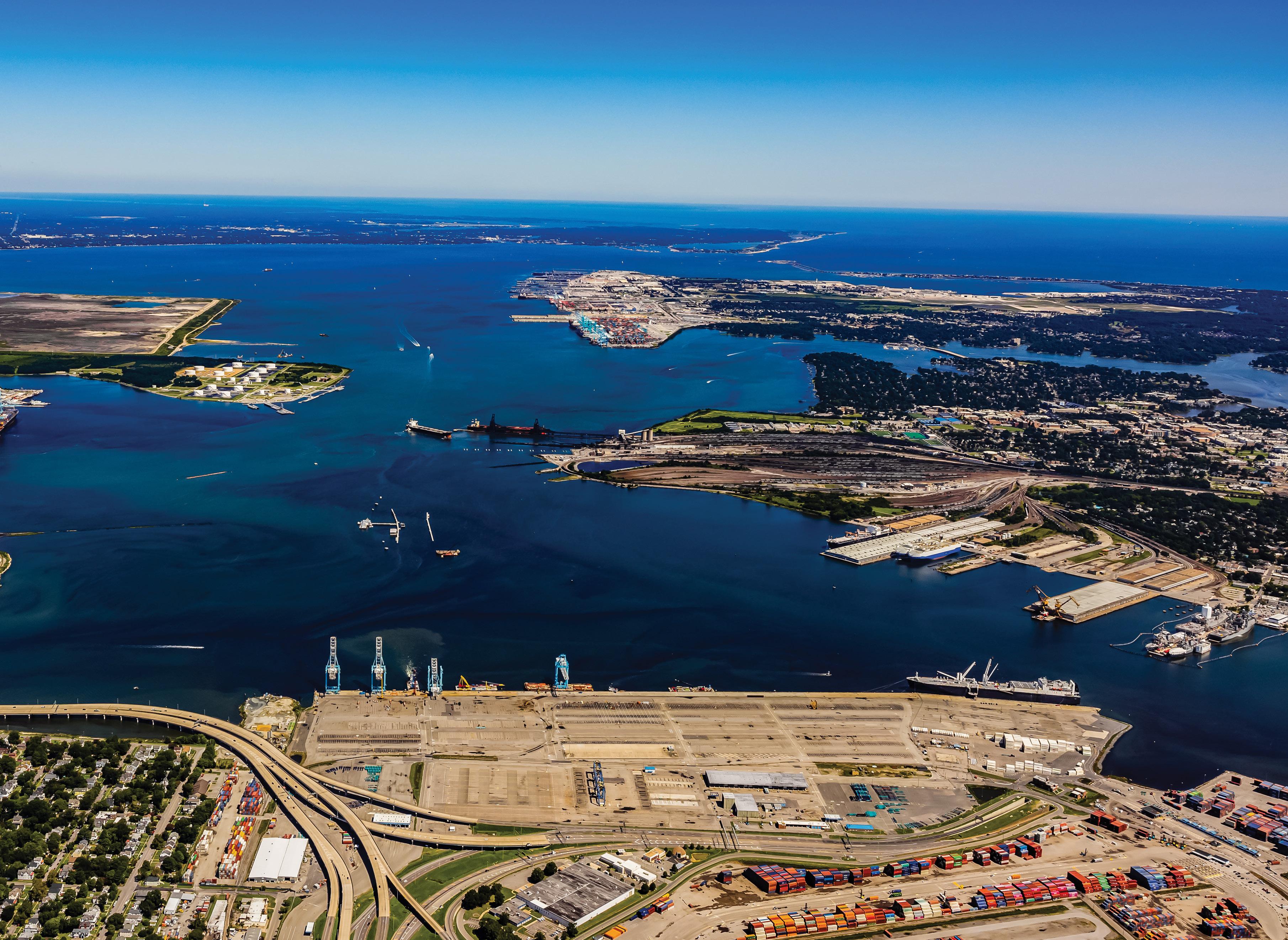
“As interest rates go up, it’s more expensive to keep things in inventory,” said Devon Anders, president of the InterChange Group, which has 20 dry and cold storage industrial warehouses across Virginia. That’s why, he said, companies now need to be able to pivot quickly as an increasing number of geopolitical issues force quick decisions on exports and imports.
“We’re still seeing the impact of manufacturers trying to figure out what inventory they need to maintain,” Anders said. One effect of those adjustments, he said, has been unexpected partnership structures. As he put it, “There’s a lot more collaboration going on where distribution centers are located.”
UPGRADES MAKE THE COMPETITIVE DIFFERENCE
Competing in such an environment requires states and port operators to be proactive with facility upgrades, and Virginia and its port are no exception.
The port recently wrapped up $1.4 billion in upgrades to its Hampton Roads facilities (see page 24), including a new, wider shipping channel that allows two-way traffic of ultra-large container vessels, cutting the amount of time such ships spend on berth by up to 15%.
Upgrading infrastructure isn’t the only way ports distinguish themselves. A swift, efficient customs process can help ports draw investment from foreign shippers that might otherwise look elsewhere.
“Infrastructure is hugely important — not only having quality infrastructure, but the ease of use,” said David MacNamara, a director in KPMG’s Site Selection and Project Development group. “Even if it’s more time on the boat, if you can clear your product quickly and spend fewer days in port, that can be a tipping point.”
Outside the port, the Virginia Department of Transportation (VDOT) is in the process of widening the current four-lane segments along a 10-mile stretch of Interstate 64 in Hampton and Norfolk and constructing new twin tunnels across Norfolk Harbor, doubling the road’s capacity (see page 20).
“If the trucks leave the warehouse and get stuck in traffic, that doesn’t work,” Burke said.
The global supply chain management market exceeded $27 billion in 2022 and is projected to exceed $76 billion by 2032, according to Valuates Reports projections. That helps explain why localities are focused on showing why they rank among the top places to store and ship products. In the end, decisions often come down to which state or locality can be the most predictable.
The Port of Virginia’s Hampton Roads facilities, clustered around a deep harbor, were a major draw in the development of the Port 460 Logistics Center.
NORFOLK INTERNATIONAL TERMINALS
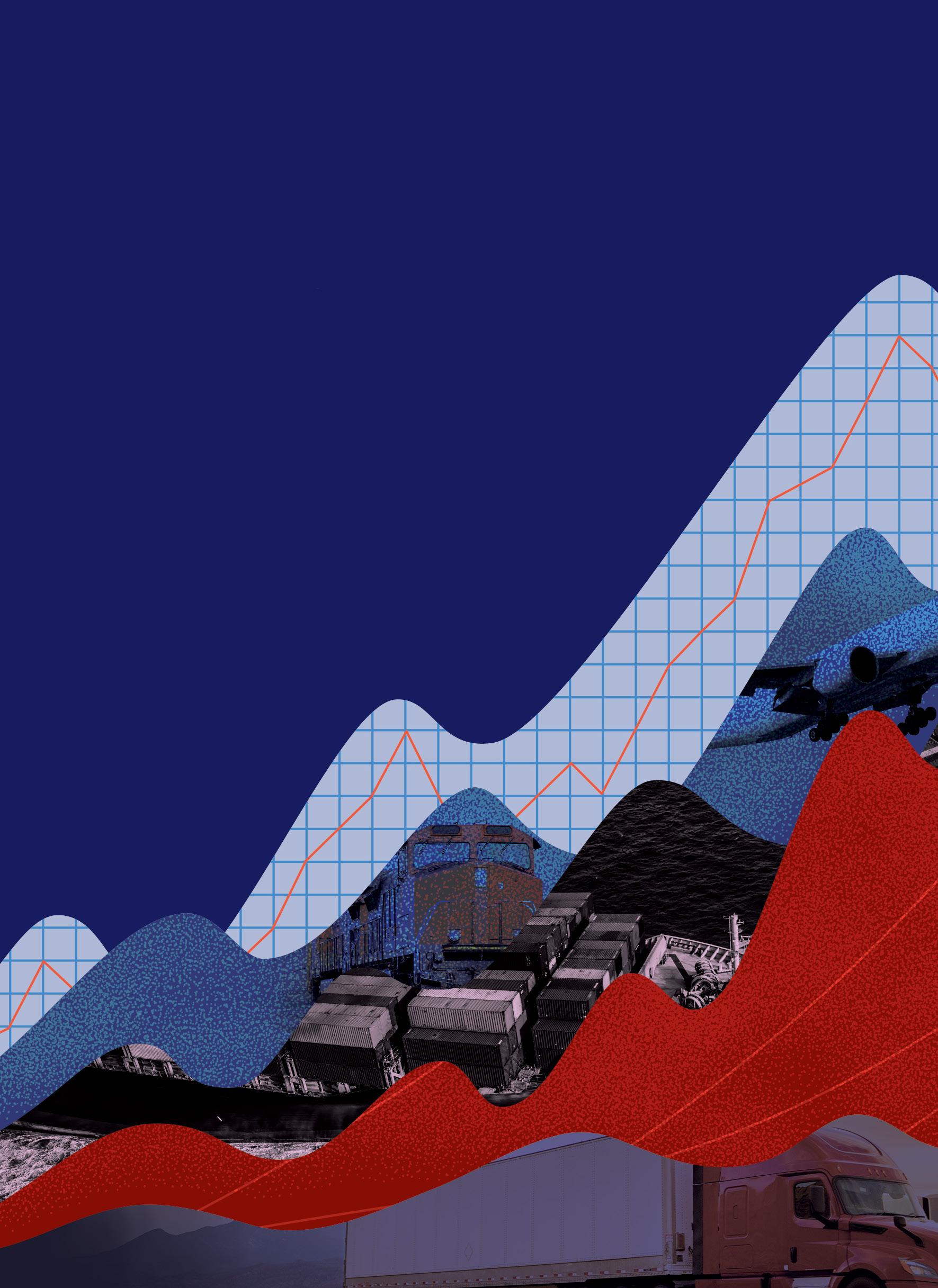
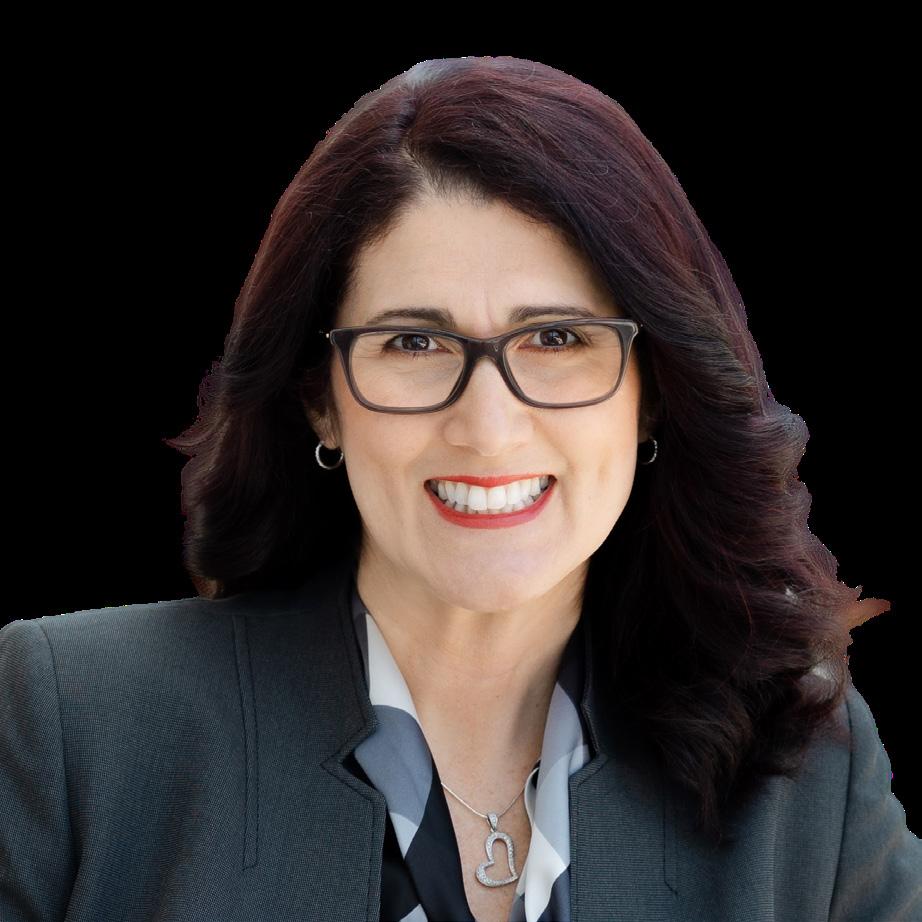
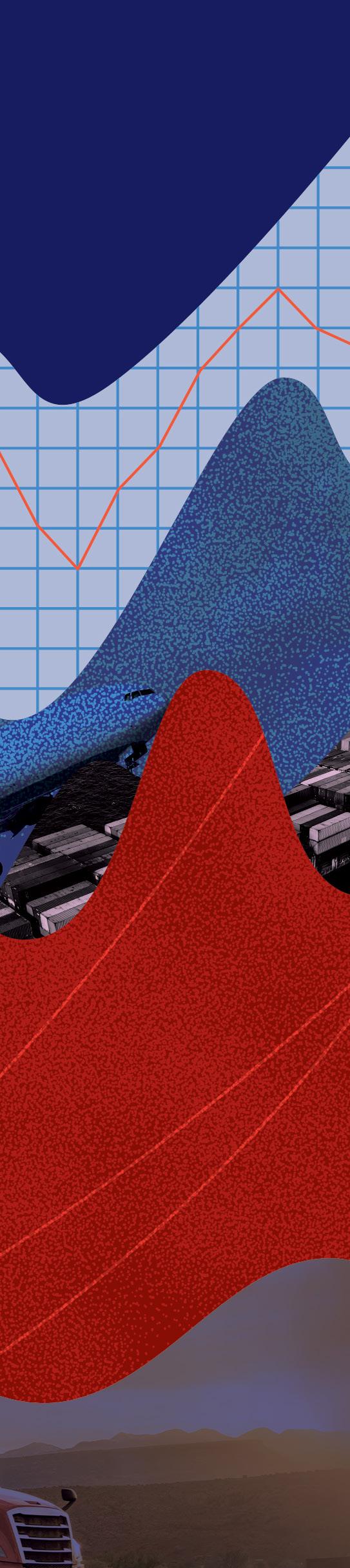
Rethinking the Supply Chain From Dock to Door
A Conversation With Myra Blanco
Dr. Myra Blanco is chief growth officer at the Virginia Tech Transportation Institute (VTTI) and CEO of the university’s Dock to Door Coalition, a partnership of nearly 100 organizations across industry, education, and government that works to develop an integrated approach to modern freight transportation by solving critical supply chain issues. VEDP Vice President of Logistics Eric Jehu spoke to Blanco about the coalition’s goals for transforming the way supply chains are viewed, analyzed, and managed.
Eric Jehu: Could you give us an overview of the Dock to Door Coalition’s mission, vision, and activities?
Myra Blanco: It’s a coalition of many organizations, all very interested in improving our supply chain. This group’s mission is to develop an integrated approach for modern freight transport by galvanizing all those members, from higher education to beneficiary cargo owners to port. Think of all the different links in the supply chain, how we can truly connect them with the vision to create a world where goods are moving seamlessly and reliably from dock to door.
This needs to be resilient. It needs to be connected and environmentally sustainable. But more importantly, it needs to be equitable. We want to ensure we’re growing and supporting small businesses with the practices we develop and the optimization process we’re targeting.
This is under the umbrella of Virginia Tech, allowing us to be that trusted partner and third party overseeing it and ensuring that we’re taking care of all the partners, whether they’re in rural Virginia or toward the coast, or if they’re a bigger organization or a business that’s just getting started.
Jehu: Can you talk us through more of the Dock to Door Coalition’s work focusing on a federated supply chain platform?
Blanco: As we developed the coalition, we also wanted to ensure that we’re documenting what is happening. There’s a lot of information, a lot of literature, but we’re creating a centralized point where we’re looking at the gaps in the supply chain through all those different potential end users of the system.
Four big areas came to be of interest for our members:
◾ More visible and more connected data sharing
◾ Using connected vehicle and automation technology more effectively and efficiently
◾ The importance of carbon-neutral alternatives
◾ Workforce considerations
That data-sharing platform is the one where all our members said, “This is our top priority. We need that visibility. We need to understand what is happening across the supply chain.”
The idea behind the federated data platform is a location where we’re able to see that minimal data set. If two organizations need to communicate effectively, what are the minimal two or three variables they might need? If you go to a different configuration of transport logistics, they might need a
completely different data set.
As we start putting all that information in place and defining it, we’ll understand the information that currently exists, what information is still needed, and how we can all contribute. Each organization will contribute to this platform and be able to safely and securely see others in that minimal data set, to calculate and understand implications for their organization of what they’re doing and how it might affect others.
Jehu: If I’m a buyer of goods and I am working with transportation providers, my goods are coming through the port, ultimately delivering to a warehouse dock, maybe going to another entity to consume or further modify, and then ultimately to an end user. We all want to know, “Where’s my stuff and when am I going to get it?” The answer to that question might be different depending on who owns that link in the supply chain. How they communicate that information to me is going to look different depending on what tools and systems they’re using. With the federated platform, the idea is to come up with a standard where everybody is essentially speaking the same language to answer that question.
Blanco: That’s what standards and professional organizations strive to do, to create those types of operational definitions. That’s how our vehicles right now are designed and certified. So, we as a coalition are taking the first steps to develop that blueprint of what that
minimal set should be and, hopefully, assist organizations that would like to optimize that process and make it a formalized standard.
Jehu: How can technology and initiatives running through VTTI help address these issues in the context of disruption?
Blanco: VTTI is the largest transportation institute under a university umbrella, and we collaborate with a lot of private technology companies. We have been able to understand and use our data for posing questions on how policy can be affected and looking at how to optimize operations. What we’re doing under this particular process is merging all those different components and understanding how to comb through that data quickly and effectively to bring results.
Having information about roadblocks, aspects that need to be considered, information about the humans in the system — all that is going to help with this. We have groups looking at sustainability aspects and doing different models of how to optimize systems to ensure zero emissions is attained.
If you have the right data, you can decide routes and what types of vehicles would be best, and be able to invest on that because you know the impact it would have. You’re able to understand the peak times for specific areas and you start seeing potential delays because certain types of functions might not be effectively deployed in those areas. You
If we have a need for sensor calibration or fixing electric vehicle charging stations, maybe we create a new program through a community college and that becomes a new business model. It becomes a whole new degree we develop by understanding the full ecosystem.
MYRA BLANCO CEO, Dock to Door Coalition
can then bring new businesses to that area and create incentives for that.
Jehu: How can we extend that into regional markets and more rural communities?
Blanco: If we’re able to understand different regions, what they have and what they don’t have, we’re able to service them better. Small businesses that have a product can take advantage of, say, a particular truck that’s not fully loaded and send goods out. They don’t have to own a fleet to do those exports or move them across the Commonwealth. We would have the information and understand that when somebody needs their goods moved in a different direction, we can quickly identify who can assist with that process.
We have in our region, and in many areas in Appalachia, food deserts. If we understand what they need, we can send produce where you might not have a grocery store for miles. We’re able to send medications. We’re able to service those communities and ensure they can remain in rural America, but receive benefits similar to a more urban environment.
Jehu: What are some of the longer-term implications of these efforts, once you’ve established and achieved these clearer deliverables?
Blanco: As we start looking at the data, the technologies, the workforce importance, new potential services that we want to train on, we can potentially develop new businesses that might not exist. In the intersection of all these needs, there might be things we can reinvent. Our transport logistics don’t need to look the same way they look now.
Think of what happens during a natural disaster. I understand where things are and where they need to go. I don’t want to put a human in harm’s way, so I’m able to use that information to guide automated driving vehicles to take water, generators, whatever it is, to that location.
Think of the Key Bridge in Baltimore. We can understand where goods need to be and automatically say, “These are the openings in different ports. This would be the optimal way to move these containers where they need to go. So, let’s move this ship to this location.” Not
because it’s where it’s open, but because it’s prioritized for what you are carrying today and where it needs to go.
Jehu: What workforce preparations should we be making for the future of the supply chain?
Blanco: The idea is that we’re working smarter, not harder. We’re preparing a workforce that is going to understand the implications of decisions, not because they’ve had to work through them for five or 10 years, but because they’re going to be able to forecast.
If we have, for example, a need for sensor calibration or fixing electric vehicle charging stations, maybe we create a new program through a community college and that becomes a new business model, a whole new business. It becomes a whole new degree we develop by understanding the full ecosystem.
It’s a rethinking of what supply chain will be in the future and how we can develop new models that don’t exist today, but will help us have better jobs, better quality of life, and better services tomorrow.
Jehu: Thank you so much, Myra, for your time today.
Blanco: Thank you for your time.
For the full interview, visit www.vedp.org/Podcasts
DULLES BUILDS CARGO REPUTATION ON FLEXIBILITY
Location, stellar service make Northern Virginia an ideal cargo hub for the East Coast and beyond
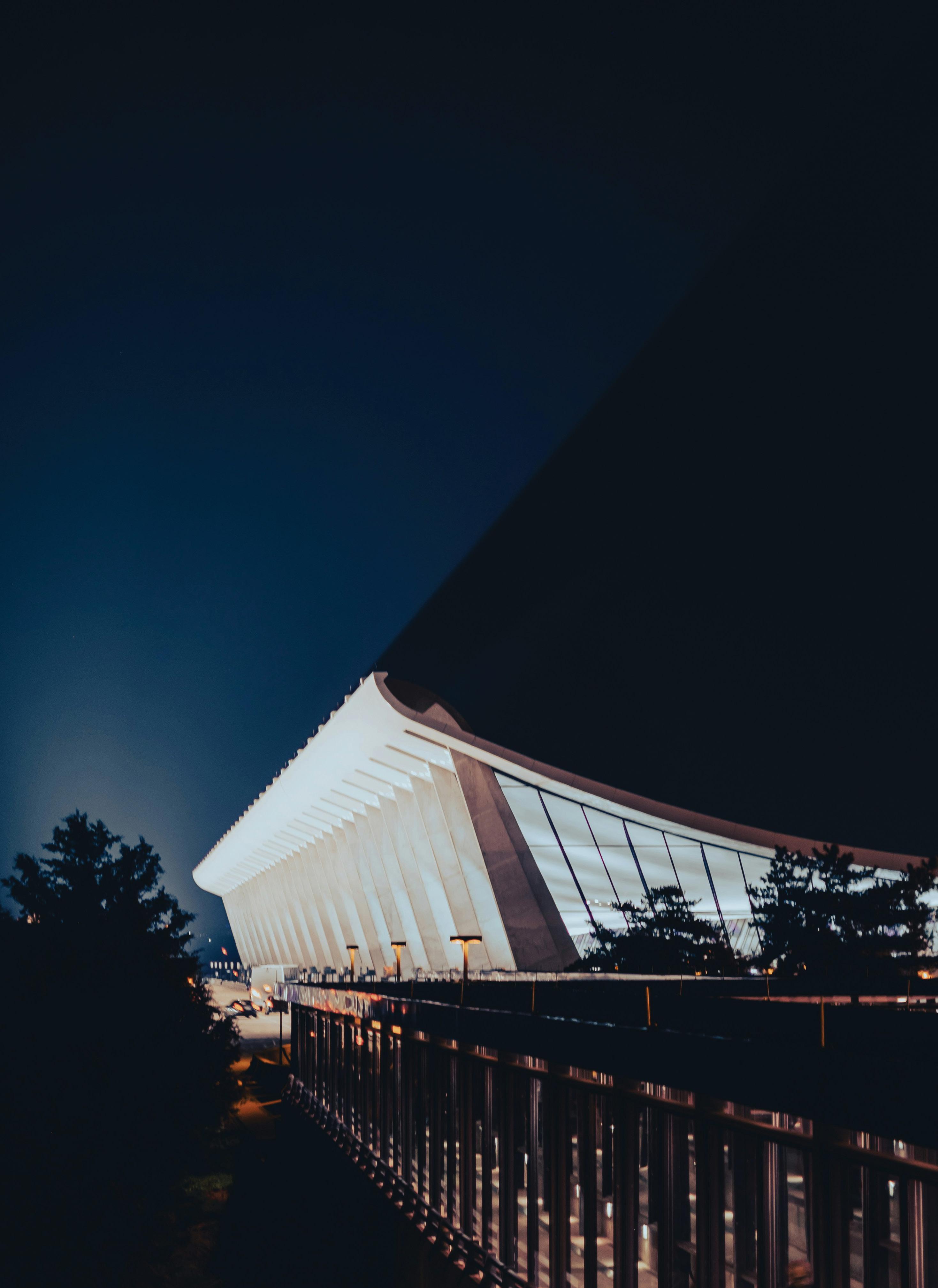
Washington Dulles International Airport
FLEXIBILITY
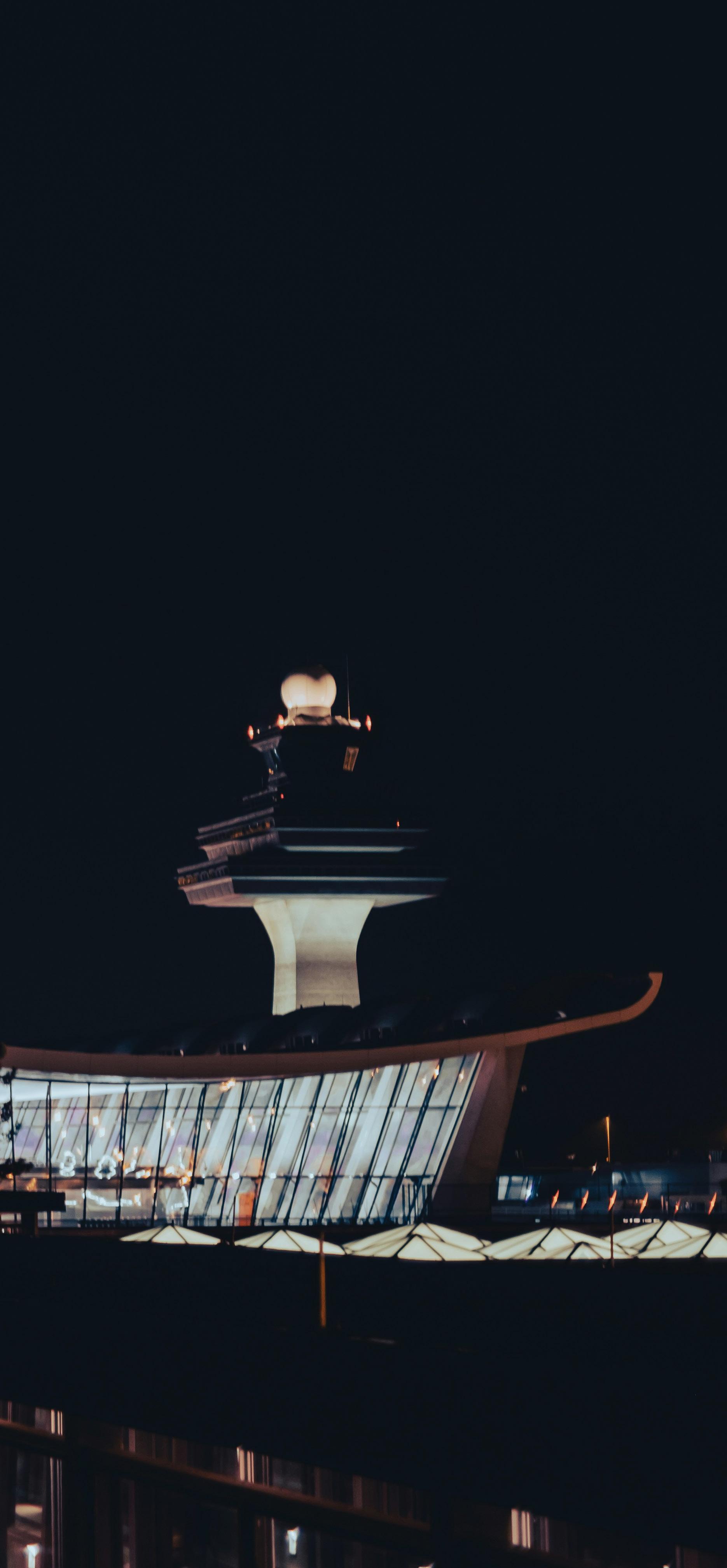
Ask a major importer or exporter what constitutes an optimal air cargo partner for their supply chain, and you’ll hear the usual desired qualities: location, transit time, Foreign Trade Zone incentives, carbon footprint, and even weather.
But dig deeper, listen closer, and carefully unpack the responses.
A clear theme pops out from the gathering word cloud, and it’s flexibility, ranging from first-class conveniences to adapting on the fly.
Washington Dulles International Airport checks that box — and all the others — in a big way.
Part of being a uniquely amenable supply chain asset comes naturally to Dulles, which straddles the border of Loudoun and Fairfax counties in Northern Virginia. Unfolding over 12,000 acres near the Potomac River and Maryland border that once were Civil War battlefields, it’s been able to spread its wings since opening in 1962.
But equally important is how the airport — and the Metropolitan Washington Airports Authority (MWAA), under which it operates — responds to both challenges and opportunities, such as 2020’s manifold obstacles.
“During the pandemic, they [Dulles] were very agile and flexible,” said Marc Barlund, branch manager at Kuehne+Nagel, a Switzerland-based global transport and logistics company that stakes a claim as the No. 1 air and sea freight forwarder.
And, of course, there’s the prime location, which doesn’t necessarily mean the long, impressive list of what lies within close proximity to Dulles, but also who. The Transportation Security Administration (TSA), for example, routinely runs demos at Kuehne+Nagel’s Dulles facilities.
“It’s one of the ways in which we’re able to stay on really good terms and helps us know what trends are coming,” said Barlund, who oversees air logistics in his role. “We’ve found it gives us a leg up.”
Dulles’ ascent from serving 55,000 annual passengers in the early 1960s to guiding 9.3 million through its gates in 2023 was a record number that made it the fastest-growing international gateway airport. This tracks with its growing haul of cargo: more than 300,000 tons annually connecting to 140-plus destinations via 41 airlines.
That’s an abundance of pallets and packages of pharmaceuticals, semiconductors, medical devices, aerospace engineering components, automotive parts, and consumer-facing goods. Some of it is perishable, some temperature-sensitive, and some just sensitive to any jolt, jiggle, or drop, making smooth, timely navigation of the airport’s shipping and handling gauntlet just the start when it comes to supply chain success.
A SUPPLY CHAIN SWEET SPOT
Coordinating supply chain logistics is akin to putting together a 10,000-piece jigsaw puzzle of shape-shifting pieces. They’re vulnerable to variables ranging from planned construction to unplanned detours, as well as pandemics and international affairs affecting everything from fuel prices to tariffs.
It’s part science, part art, a little luck, and a whole lot of adapting to real-time challenges and opportunities.
And Dulles has aced all the questions on the resiliency final exam, thanks in large part to a prime location that’s even stood up to perceived minor threats.
Take traffic, which by perception is a veritable restrictor plate on Northern Virginia commute times. But the reality for Dulles is far from the reputation.
Our customers like the fact that there’s a lot of reliability around bringing anything through Dulles.
JULIAN AMATO
Director of Business Development, Kuehne+Nagel
“Traffic patterns are not a problem in and out of the airport like they are in Northern Virginia,” Barlund said. This is huge for getting a head start on a shipment’s next stop, since 56% of the U.S. population lives within a day’s drive of Dulles.
Because of the airport’s proximity to major thoroughfares — including the Capital Beltway (Interstates 95 and 495), as well as I-270, Route 66, and Route 15 — it’s not just the expected destinations that make sense for those moving cargo through Dulles.
Yes, Norfolk and its key port facilities are only 210 miles south and east of Dulles, with Baltimore (60 miles) and Richmond (120 miles) also relatively quick trips. It’s not a stretch, however, to suggest that Dulles’ effective footprint extends hundreds of miles from the Washington metro area in every direction.
IMPRESSIVE REACH
“We bring cargo to Dulles for surrounding areas, but also for Connecticut, New York, Ohio, Pennsylvania, and the Carolinas,” said Kuehne+Nagel Vice President, Air Logistics Northeast Mario Roldan.
Importers have used Dulles to regularly serve markets as far as Kentucky and even Michigan simply because it’s a better, faster, more reliable solution than the alternatives, Roldan said.
Kuehne+Nagel identified the prime opportunity Dulles provided early on, investing in and building a robust gateway to stage consolidation of goods
for efficient outbound transport.
Other major logistics and freight forwarding companies have taken a similar approach, choosing to build a dedicated facility on the Dulles property.
A representative from one such company said, “Dulles is a really good solution for our customers. Geographically, it’s just an ideal location…you can get up to [key customer locations] quickly.”
The representative said this was especially true for biotech, pharmaceutical, and medical device companies, adding that the airport has a lot of capacity for freight, yet it is right-sized and has proven reliable in handling delicate product quickly.
It’s not just miles and minutes that make Dulles an ideal supply chain partner. It also has to do with having a favorable environment for the product to travel through once it’s loaded into a rail car or 18-wheeler.
“Virginia is an attractive state in general because it doesn’t have the extremes,” said Barlund, mentioning weather as one steadying force. “It’s a safe place with very few disruptions.”
FLEXING AND GROWING
Over six decades, Dulles has evolved from a small operation on the outskirts of the Beltway to play a key role in supply chains for businesses ranging from Fortune 500 stalwarts to startups on the brink of the next big biotech innovation.
Tabbed as Foreign Trade Zone 137 for nearly 40 years, Dulles extends financial incentives including tariff reductions to qualifying businesses located within 60 miles. In addition to laying the groundwork for more costeffective trade, Dulles offers air cargo capabilities and amenities ranging from bonded warehousing to refrigerated and ambient-temperature-controlled storage space. The 24-hour facility can handle
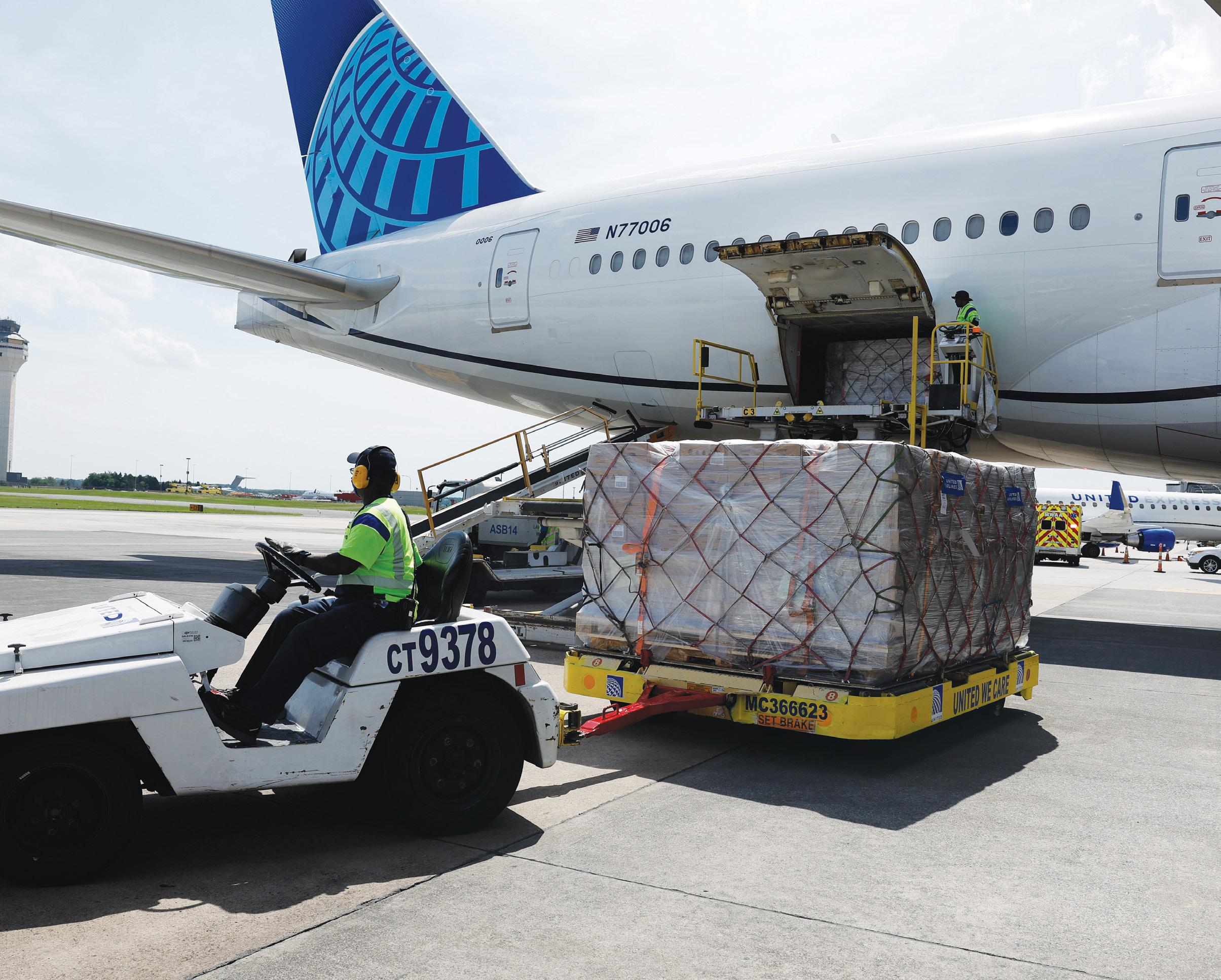
aircraft of any size, and has room to grow.
One vertical taking advantage of being in Dulles’ orbit is data centers. Loudoun County boasts the globe’s largest concentration of the facilities with more than 25 million square feet — an area nicknamed “Data Center Alley.”
“And that continues to grow,” said Julian Amato, director of business development at Kuehne+Nagel. “Our customers like the fact that there’s a lot of reliability around bringing anything through Dulles…If you ask most diagnostic device or drug companies, they agree that they like Dulles.”
Stakeholders see an opportunity for
Dulles to consolidate its market share on tech-sector cargo, with major companies already using the gateway to supply Northern Virginia data centers.
Another way that Dulles drives both growth and flexibility for its cargo customers is the groundswell of support it receives from a wide range of organizations.
“It opens the doors to additional solutions that we or our customers are looking for,” Amato said. “I’ve never seen a chamber of commerce and specific associations, from a supply chain perspective, be so focused on the stakeholders. Having the local connection…we don’t see that in other markets.”
And when it comes to being flexible, it’s not just about reacting to the challenges of today, but planning for the opportunities of tomorrow.
This includes an MWAA collaboration with Dominion Energy to create a 100MW solar project, which is highlighted by a battery energy storage system. Slated for completion in 2026, the project would give Dulles more solar capacity than any other U.S. airport.
“We have an airport authority that’s really willing to invest,” Amato said.
In other words, the future is bright for all those leveraging Dulles in their supply chain — and there’s plenty of open runway ahead.
Washington Dulles International Airport serves as a major East Coast hub for cargo shipments, serving customer needs through a combination of location, infrastructure, and careful consideration and mitigation of factors that can cause delays.
THE VALUE OF DATA
Lance Harcrow is chief operating officer at Estes Forwarding Worldwide (EFW), a subsidiary of Estes Express Lines and a leading domestic and international freight forwarder headquartered in Chesterfield County. VEDP Vice President of Logistics Eric Jehu spoke with Harcrow about the issues EFW sees as a logistics provider and how data analysis can transform the supply chain moving forward.

Eric Jehu: Can you explain what your organization is seeing in today’s supply chain and give us an overview of where you’re focusing your energy these days?
Lance Harcrow: The pandemic period clearly demonstrated just how fragile the world’s supply chain is. It’s never been static in my 40 years in the logistics industry. It’s always required contingency planning, flexibility, and change.
So many uncontrollable and unforeseen events impact the supply chain in one form or fashion. The pandemic was one example, but you see impacts consistently based on fluctuating consumer demand, followed by fluctuating capacity levels. You’ve got volatility in the economy and labor markets, natural disasters, geopolitical events, and changes in laws, important export regulations, and tariffs. Since the pandemic, companies have been focused on creating some flexibility and sustainability in their supply chain.
Our energy and focus have really been on evolving quickly to support what we call the elastic supply chain push. The Estes enterprise has a fleet of services that can basically facilitate every link in a customer’s supply chain. So we’ve been dialing those services in, blending them together, and providing a full-service supply chain offering to our customers.
In conjunction, we’re continuing to invest in both our nonasset-based and asset-based expansion. The nonassetbased expansion allows us to increase our operating flexibility and capabilities without heavy investment in fully burdened infrastructure that’s out there. The amount of data and visibility to it is now almost more important than products’ movement.
Jehu: You called out that the pandemic exposed and highlighted some supply chain issues for customers, and globally, that maybe we weren’t aware of. Aside from that, do any other unique post-pandemic challenges come to mind
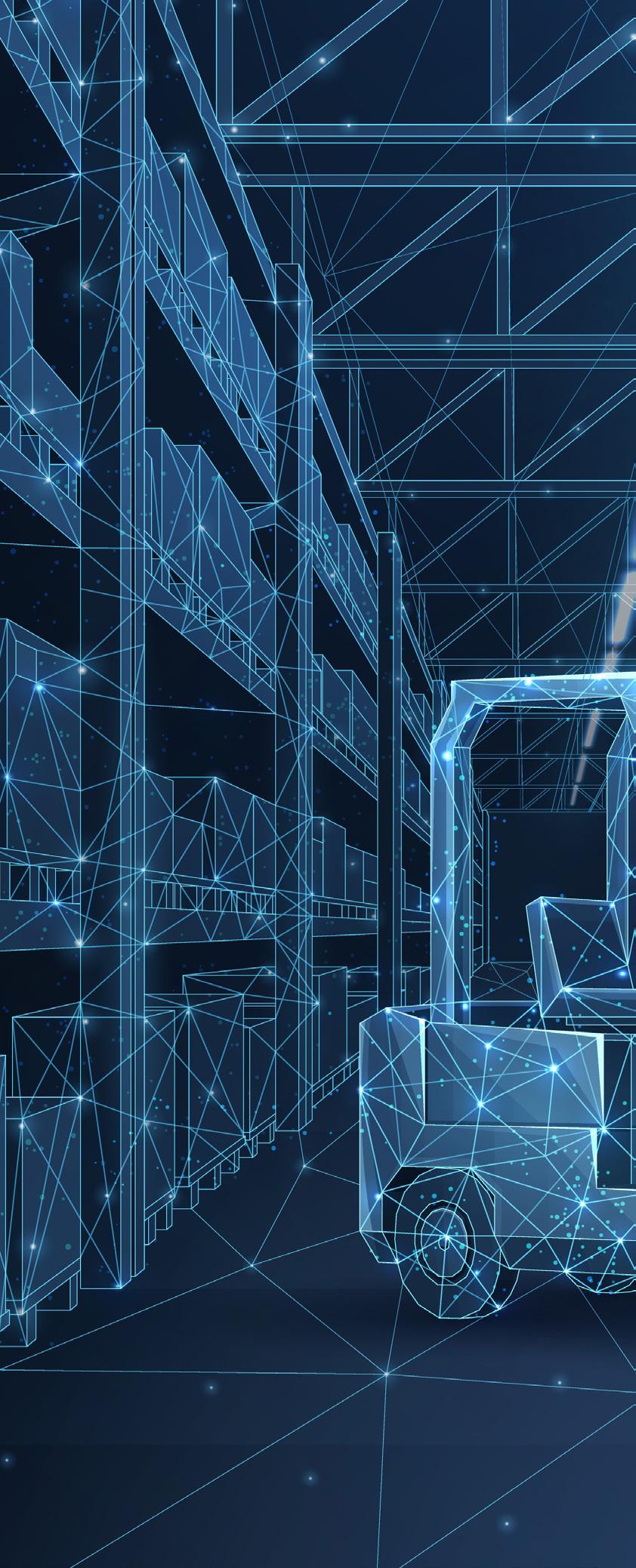
that you hadn’t seen before?
Harcrow: Some cascading changes post-pandemic have become the new norm. Labor is certainly one of those things. Inflation based on the cost of transportation and the cost of space has continued to rise at a fairly quick pace. We saw during the pandemic the cost of ocean freight go higher than ever before because of the lack of capacity. And over the last year, we’ve seen it go lower than probably in 15 or 20 years.
You have push and pull between providers and shippers. Shippers who bore that cost burden during the
A Conversation With Lance Harcrow
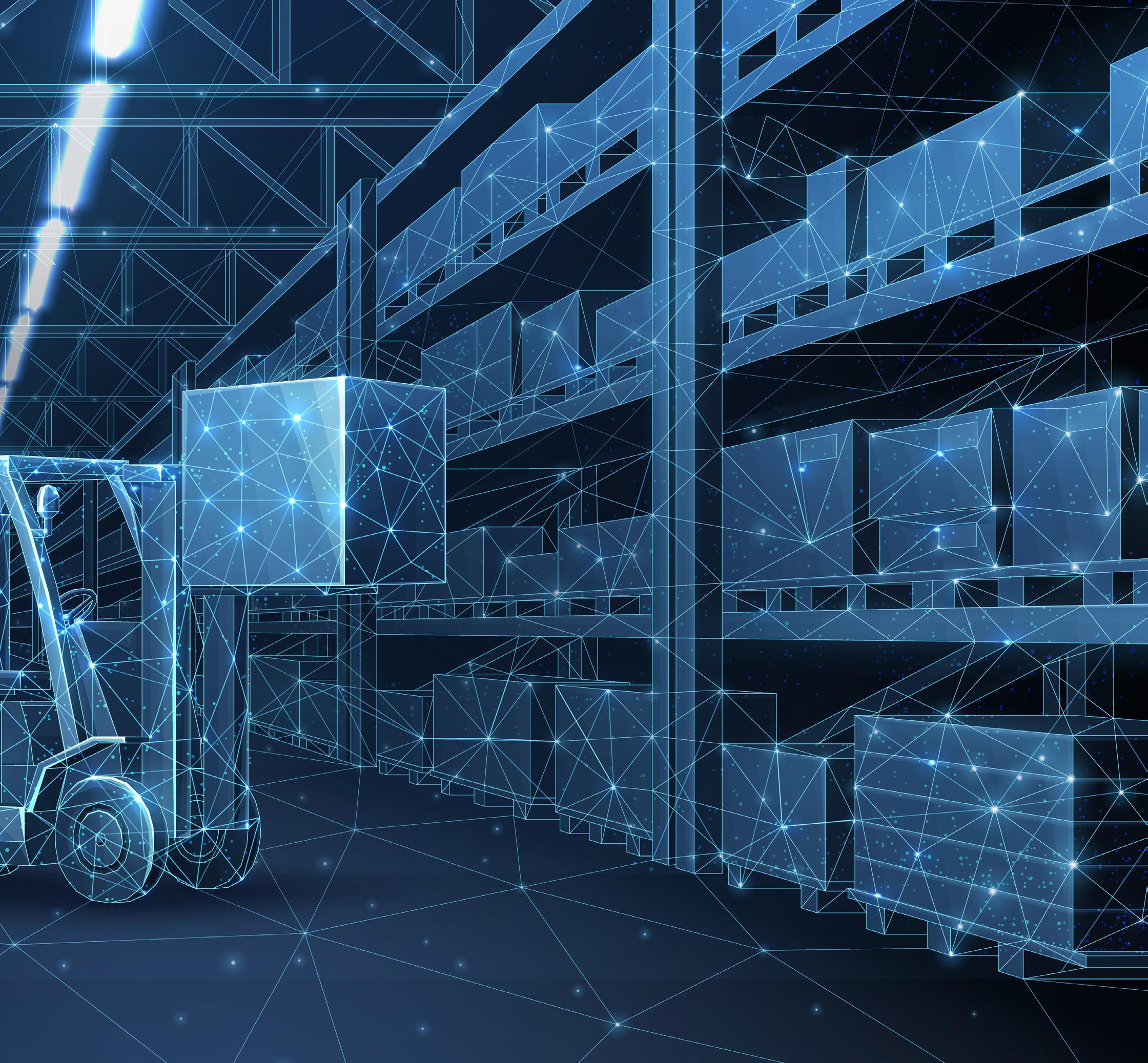
pandemic are looking to reposition and regain some of what they lost due to pandemic rates. We’re updating ocean rates and container rates on a monthto-month basis back to our customers. When you work with customers strategically the way we do, it’s hard because they want as much of a fixed cost analysis on their supply chain as they can get. We’re seeing post-pandemic variables in the entire supply chain that really change rates, again almost month to month or quarter to quarter. One thing I see post-pandemic that is probably the new norm, at least for a period of time, is consistent fluctuation in capacity and rate.
Jehu: You touched on the value of data and information. That operation’s a bit more complex, and answers the question, “Where are my things and when am I going to get them?” and then planning labor around that. You’re also in a position to provide that information to your customers so they can make better decisions. Can you dig a little deeper into that side of the business?
Harcrow: Data integrity is extremely important. You’re trying to create visibility from the time that product hits the port to the time it either gets into the distribution center or to direct-to-consumer or a retailer. Being able to provide that
visibility back to your customer allows them to make good business decisions.
Customers may allow us to be part of their ERP and get into their system and provide, once that product hits our dock, real-time visibility to the status of that product on our dock, so they can make very quick and efficient decisions. At that point, we’re almost operating like a mini-distribution center for them. That gives those customers a lot of flexibility in pushing something to the distribution center or the warehouse or taking it straight to manufacturing or straight to retail. That’s a lot of value to that stream or segment of their business.
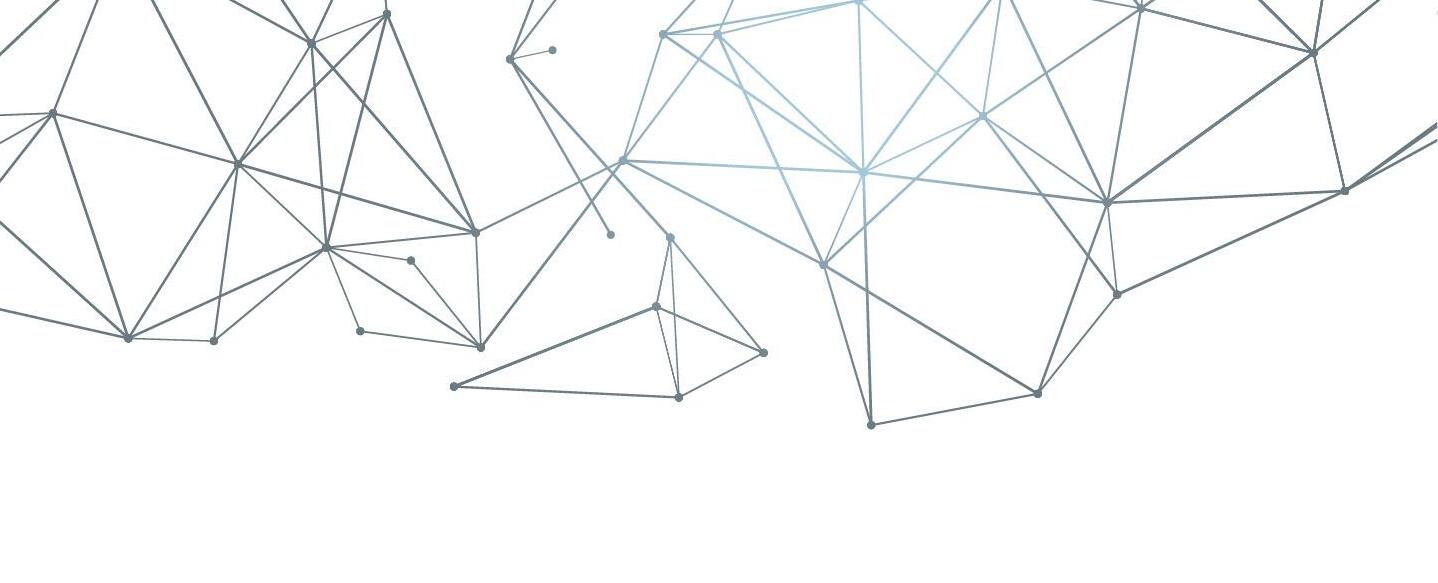
We’re analyzing, based on milestones, what the compression time is between milestones. All these milestones we’re starting to ping and provide visibility back to our customers now allow us, as the provider, to really hone in and become precise in improving our service. If we can logically apply some standard dwell times in between those milestones, then we know immediately when we have something that’s starting to get outside of a service level agreement. That pre-alert to us of something gone awry allows us to jump in and correct it.
Jehu: Early in the conversation, you touched on AI and future-state technology and analytics. Everything you’ve just talked about is massive generation of data and the story that data lake can tell us, with the potential for a future state of an even more predictive environment to optimize and achieve more supply chain stability and balance than we ever have before. Can you talk about your innovation and investment in AI?
Harcrow: I think we have become very good at collecting data, and I think artificial intelligence will help us mine that data better. Cognitive computing will allow us to take mined data and really identify where true trends are. AI should help us identify those things and make them standard parts of our process improvement.
We as an organization, like a lot of organizations, still struggle with how AI is effectively applied to the data or analysis done now. As we run data through our business intelligence tools, how do we apply that final leg of artificial intelligence to become cognitive in our processes and improve them over time?
Jehu: What comes to mind is the disparity between the milestones’ meaning and collection of the data, and the other parties you interact with and what those milestones mean to them, versus what they mean to you and in your operating system. How to get all that into one standard language so data received means the same thing to all parties. Would you agree that’s a massive challenge for the industry? What can we do about it?
Harcrow: It is a massive challenge, and what we’re talking about is just transportation nuts and bolts. You also have the customer experience side of your business that AI needs to continue to evolve and play a significant part in, because customer feedback can tell you where your operational models have gaps and where they’re not engineered properly. If you can capture feedback and mine it effectively, it can tee up corrective action that AI can immediately apply in that environment.
It’s a lot more complex getting everybody together and on the same page as to how this information we’re going to gain, and AI, will apply corrective action to that information across a fragmented logistics and transportation industry and environment.
Jehu: The point you made about customer service feedback, and being able to mine that information in real time, is obvious. How do you get meaningful information? How are you harnessing client feedback to make it actionable?
Harcrow: We recognized the value of customer feedback seven years ago, and our organization made a significant investment in the net promoter system, but it could be any customer feedbacktype structure. The key is your executive team. It has to be part of their DNA. They have to buy into it and cascade it down in the right way.
Jehu: Do you see an opportunity — you mentioned damage — where automation, whether it be autonomous vehicles, robotics, or other types of automation in the warehouse or at the delivery destination, could play a role in the future to further improve that experience?
Harcrow: In our space, humans are going to be around for a while.

In our space, humans are going to be around for a while. Autonomy and vehicles and equipment will continue to advance. As they do, people will learn to manage and interact with them.
LANCE
HARCROW Chief Operating Officer, Estes Forwarding Worldwide
Autonomy and vehicles and equipment will continue to advance. As they do, people will learn to manage and interact with them. If we look 20, 50 years down the road, we’ll see AI and robotics play much greater roles in our lives, whether at home or work.
Autonomous vehicles are on the road today, but most people have never seen them. There are companies like Waymo, which is basically the autonomous Uber operating in places like Arizona. Until we can pull up to an intersection and regularly see autonomous cars there, we’re not likely to see autonomous tractor-trailers.
The dynamics of driving a truck are more complex, certainly in long, open, low-traffic stretches of the interstate. I think that’s where you’ll see impact begin in the trucking industry sooner than later. But I think it’s going to take a while for us to see autonomous trucks regularly moving freight.
I really applaud Estes. They’re looking at how their trailers are loaded and minimizing and mitigating damage. Estes developed and patented the dynamic loading trailer about four years ago. It looks like a web wall, with load bars basically in the trailer’s ceiling that can be pulled down and positioned every six inches from top to bottom. If they load an oddly shaped piece like patio furniture and don’t want anything to stack on top of it, they can lower those load bars to that level, lock them in, and then load above the bars, gaining the efficiency of filling that trailer up without jeopardizing or crushing anything. Innovations like that will really improve damage ratios.
Jehu: Do you have any parting thoughts for us?
Harcrow: I think we’re seeing companies study the strategic changes of their supply chain. It’s all about flexibility. It’s all about elasticity. It’s being able to ride the shifting waves
of raw materials, manufacturing, and capacity and ensuring sustainability. That there is no bottleneck in that supply chain. When you look at the Estes enterprise as a whole, we’re well-positioned to be able to provide that full-service flexibility.
Estes Express is known as an LTL provider, but there are a number of specialized divisions and companies strategically positioned to blend service capabilities and create the worldwide footprint we have. It’s a unique and differentiating hybrid model that allows us to merge robust freight forwarding and contract logistics operations and create the flexibility and elasticity customers need.
Jehu: Lance, I really appreciate you joining us today and for this rich conversation that I’m sure we could continue for another three hours if we had that available to us.
Harcrow: Thank you.

For the full interview, visit www.vedp.org/Podcasts
Making Shipping Easier for Manufacturers
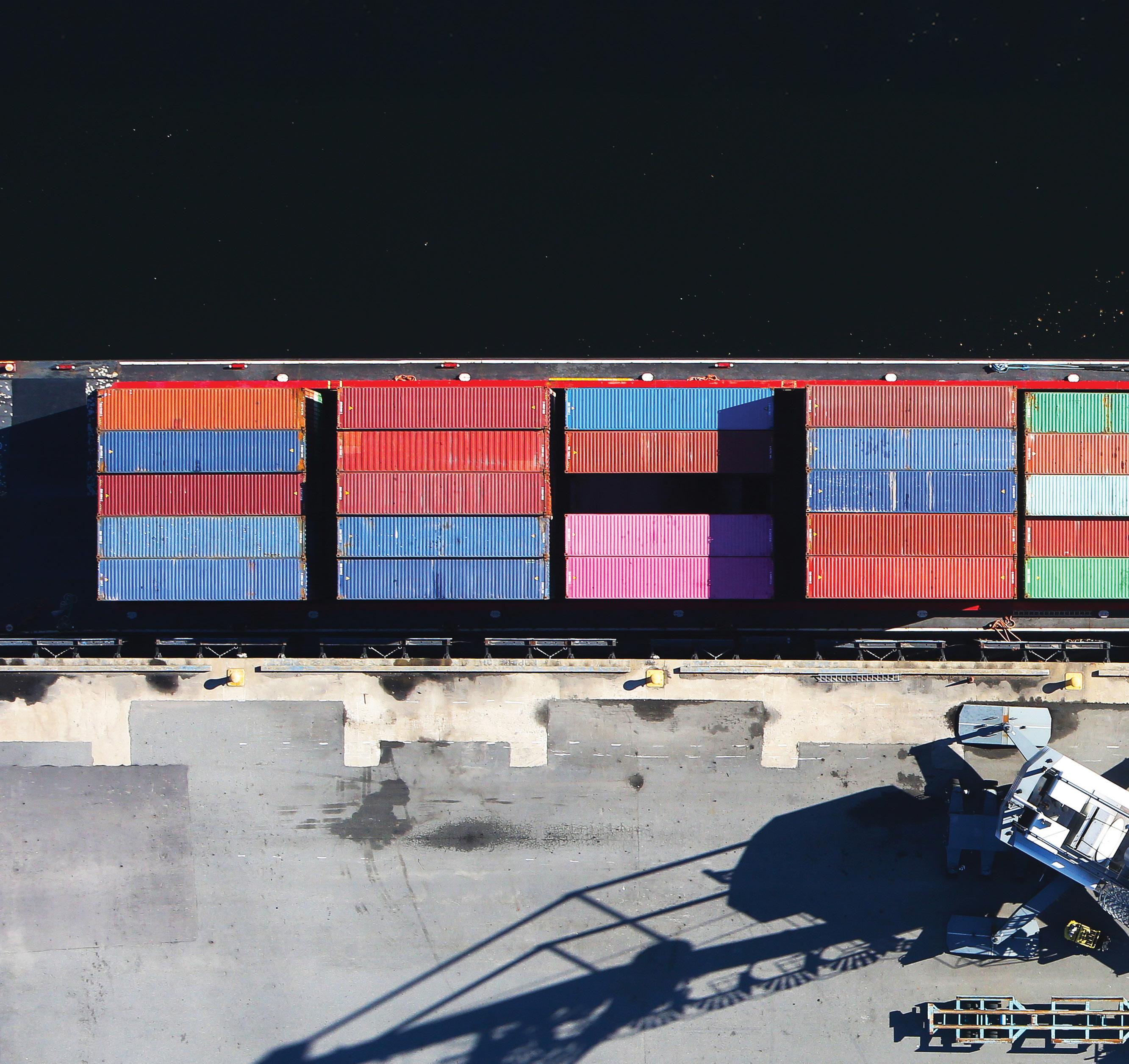
Multimodal focus helps Virginia facilities create value for companies
Supplier and customer accessibility has always played a key role in industrial site selection decisions. But the supply chain shakeups over the last five years have pushed manufacturers to rethink the types of sites that might allow them to best serve their key stakeholders. In the face of global
pandemics and conflicts, tariffs and inflationary pressure, natural disasters and extreme weather events — running alongside consumer demands for greater personalization and faster deliveries — companies are looking for sites with infrastructure in place to help them pivot when transportation challenges arise.
“Given the challenges posed by the COVID-19 pandemic and ongoing geopolitical conflicts, the logistics industry has become increasingly
demanding,” said Julian Amato, director of business development for Kuehne+Nagel, a global logistics provider with nearly 1,300 locations in more than 100 countries. “Customers no longer wish to spend hours waiting on hold for a customer service representative. Instead, they seek localized expertise within their own time zone to provide tailored advice.”
This perspective has driven many global companies to open locations near key Virginia logistics hubs. Kuehne+Nagel’s
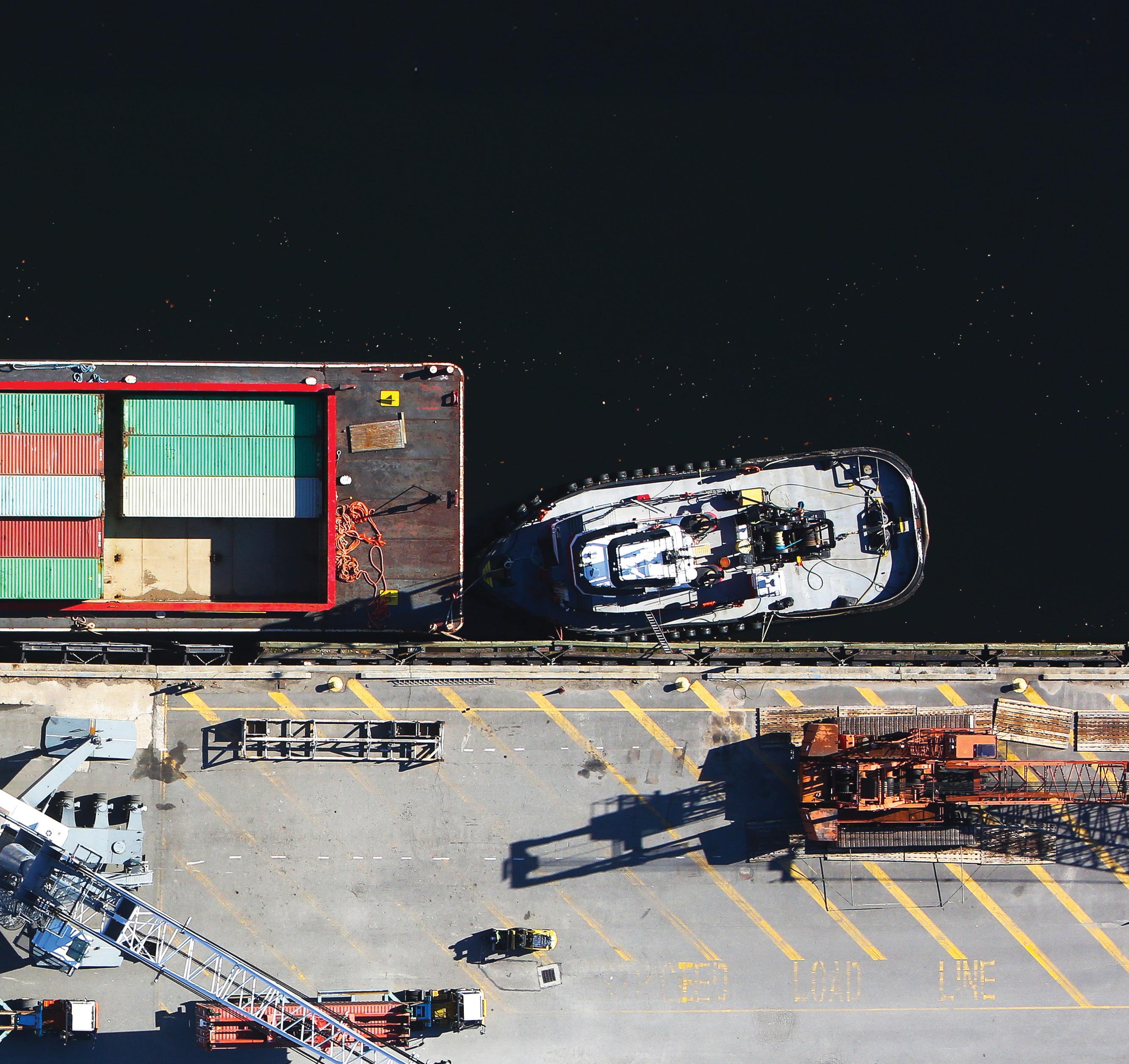
Virginia locations reflect this focus — its Northern Virginia office is adjacent to Washington Dulles International Airport (see page 32). Amato works out of Richmond, where the port’s Richmond Marine Terminal (RMT) helps companies move product along the James River via barge. The company’s Virginia locations provide versatile, multimodal access to customers and suppliers along the East Coast.
“In this high-demand industry, everyone relies on carriers, freight forwarders,
or other logistics service providers,” Amato said. “Having a local presence and providing shippers with an expert to consult are absolutely crucial.”
LOCAL BENEFITS, GLOBAL REACH
Facilities like RMT — currently undergoing a $6.1 million upgrade to allow faster processing for trucks and extended hours for barge loading and unloading — provide non-vessel operating common carriers like Kuehne+Nagel options for moving
goods. This redundancy is proving essential for ensuring speed to market, even in the face of unexpected events.
Both of the Virginia Port Authority’s inland terminals, RMT and the Virginia Inland Port (VIP) in Warren County, are convenient to multiple interstate highways, supplemented by on-site rail service at VIP and the barge service at RMT.
Virginia has also seen an uptick in construction for distribution centers and warehousing, adding to local
The Virginia Port Authority’s Richmond Marine Terminal serves as a multimodal shipping hub for the region, offering road, rail, and maritime services to help shipments reach the rest of the country.
Downtown Richmond serves as a transport hub for the Richmond-Petersburg area and the rest of the Commonwealth, aided by the intersection of Interstates 95 and 64 and abundant cargo and passenger rail infrastructure. Just out of frame at
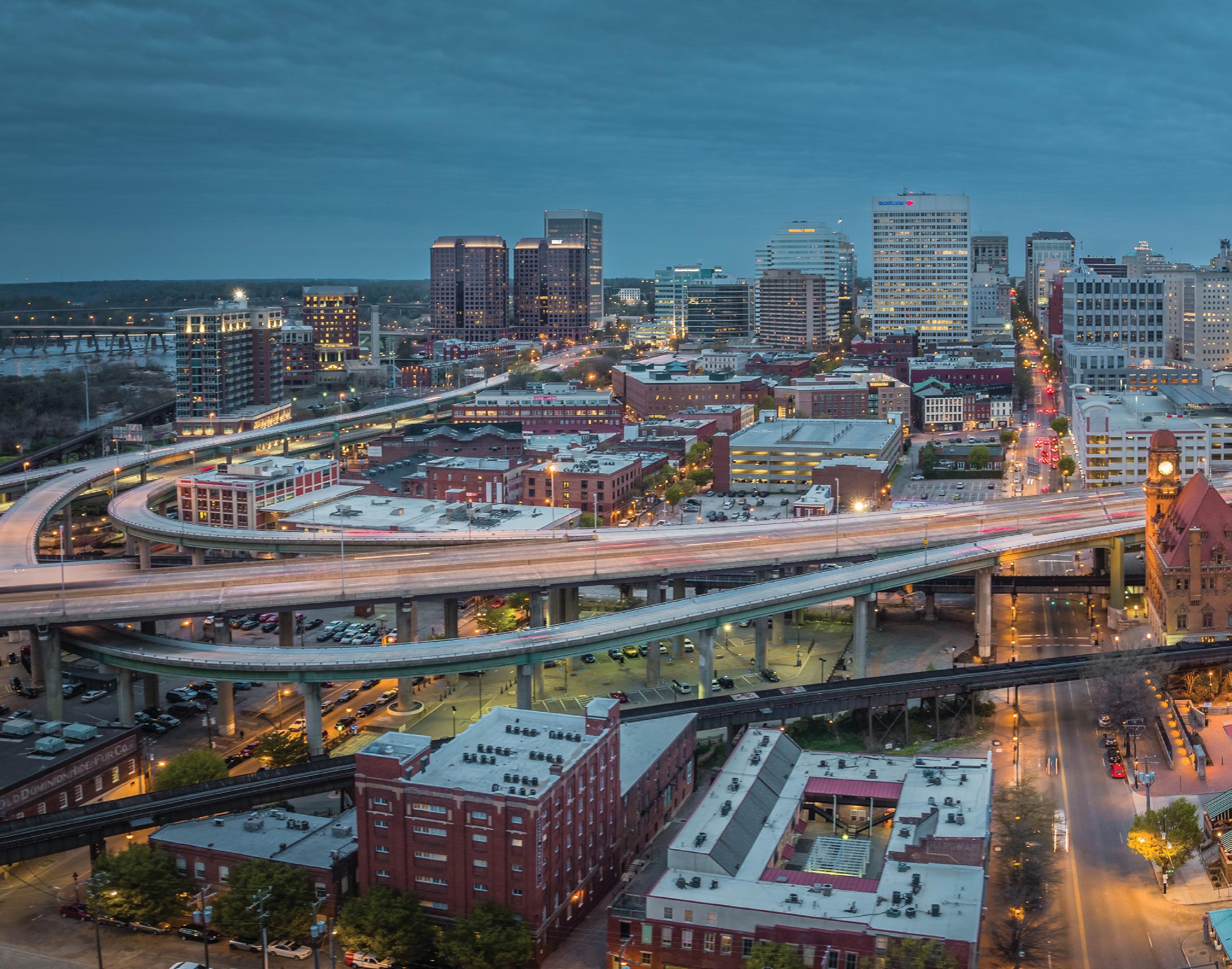
manufacturers’ supply chain efficiency. For Cascades Containerboard Packaging’s Bear Island plant in Ashland, a new three-year contract with several distribution centers across Virginia is a key step that will allow the company to have a more stable raw material supply, according to Jim France, the plant’s logistics director.
Cascades Inc., a Canadian producer of green packaging and paper tissue products, acquired its lightweight recycled containerboard operation in the former Bear Island Paper Mill in 2018. The site was selected in large part due to a location that brought Cascades closer to a number of key suppliers. This new distribution agreement now makes it easier for the plant to manage inventory provided by those suppliers.
In this high-demand industry, everyone relies on carriers, freight forwarders, or other logistics service providers. Having a local presence and providing shippers with an expert to consult are absolutely crucial.
JULIAN AMATO Director of Business Development, Kuehne+Nagel
Upon announcing the site selection decision in 2018, the company noted that the Ashland plant’s geographic positioning would enable Cascades to increase its competitiveness and provide customers a more diversified product offering. France confirmed that has proven true, because the company has been able to expand its recycled linerboard products to include a range of lighter-weight materials as a result of new supplier relationships. While Cascades works to lower packaging weight for a variety of reasons, RMT’s intermodal rail capabilities — the facility offers direct rail service via CSX and connects to Norfolk Southern’s network via a local switch — have proven advantageous in shipping heavy commodities like paperboard across long distances.
the bottom left of this picture is the Triple Crossing, one of two locations in North America where three railroad lines cross at different levels at the same spot.
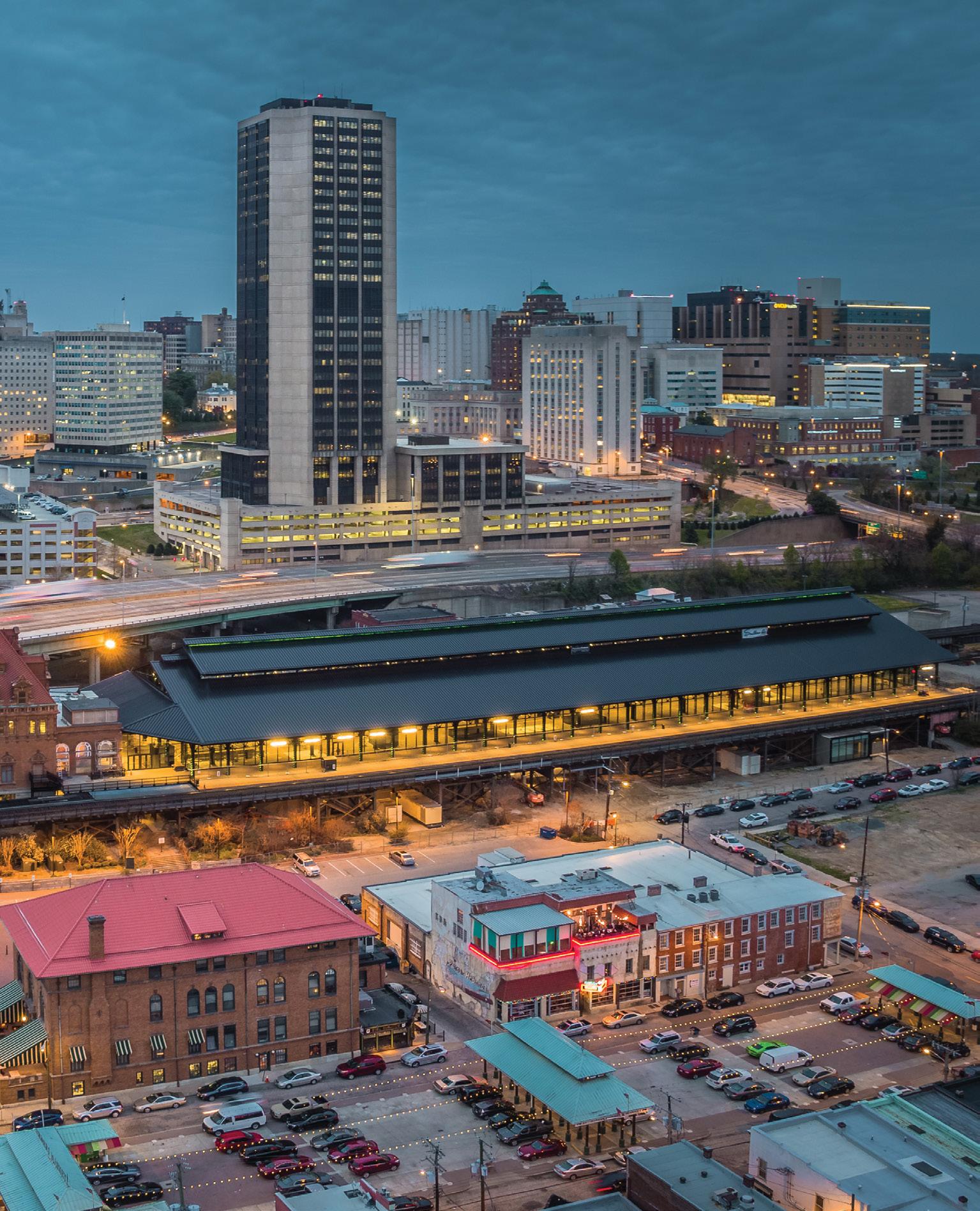
“There are many suppliers within the Mid-Atlantic region, and our location has allowed us to secure several local supplier contracts,” France said. “Most of these suppliers are located along the Interstate 95-Interstate 64 corridor.”
On the customer side, that centralized location also allows the company to more easily reach customers from New York to Georgia. The plant’s reach also extends to the Midwest, as well as Mexico and South America. From the interstates to rail and barge service at RMT, Virginia offers companies like Cascades access to a complete multimodal gateway, and the company’s location in the Richmond-Petersburg area allows it to utilize all modes of transport to move its products on to the rest of the country and the world.
SIMPLIFIED LOGISTICS ELIMINATE HEADACHES
While Kuehne+Nagel has maintained a presence at Dulles for several years supporting unique needs related to humanitarian aid, government shipping, and broader aerospace logistics, the company recently expanded its footprint.
In 2022, the company strategically opened a central Virginia location to better serve clients who were previously assisted by representatives in Baltimore or the Carolinas.
For Kuehne+Nagel, establishing a Richmond office goes beyond mere shipping efficiency — it’s about empowering customers to comprehend and navigate their choices, Amato said. The Port of Virginia’s owner-operator model
inherently simplifies logistics, when compared to other ports that lease terminals to various operators.
“Regardless of the terminal, whether it’s the inland port or barge service, we know exactly who to contact,” Amato said. “This clarity reinforces customers’ understanding that the infrastructure is readily available, offering comparable reach, if not quicker and more efficient service.”
Rather than focusing solely on streamlining shipping processes, Kuehne+Nagel’s Richmond office aims to provide on-the-ground expertise, guiding customers and global colleagues toward Virginia-based solutions for shipping, warehousing, and other critical logistics requirements.
To provide that local touch, companies need to do more than simply open an office — they must actively engage with stakeholders operating local transportation infrastructure. Amato and his team have achieved this by participating in local associations, fostering relationships, and gaining insights into the logistics landscape.
Joining these networks has also connected Amato’s team to a wealth of resources that help shippers and other stakeholders within Virginia’s logistics and transportation network navigate international trade.
As The Port of Virginia and nearby localities continue investing in infrastructure enhancements, collaborative efforts between businesses and local governments demonstrate their commitment to success and customer satisfaction.
“Being in proximity to our customers isn’t just about geography; it’s about forging meaningful connections,” Amato said. “These connections are the bedrock of our strategy, allowing us to build trust, understand customer needs, and deliver exceptional experiences.”
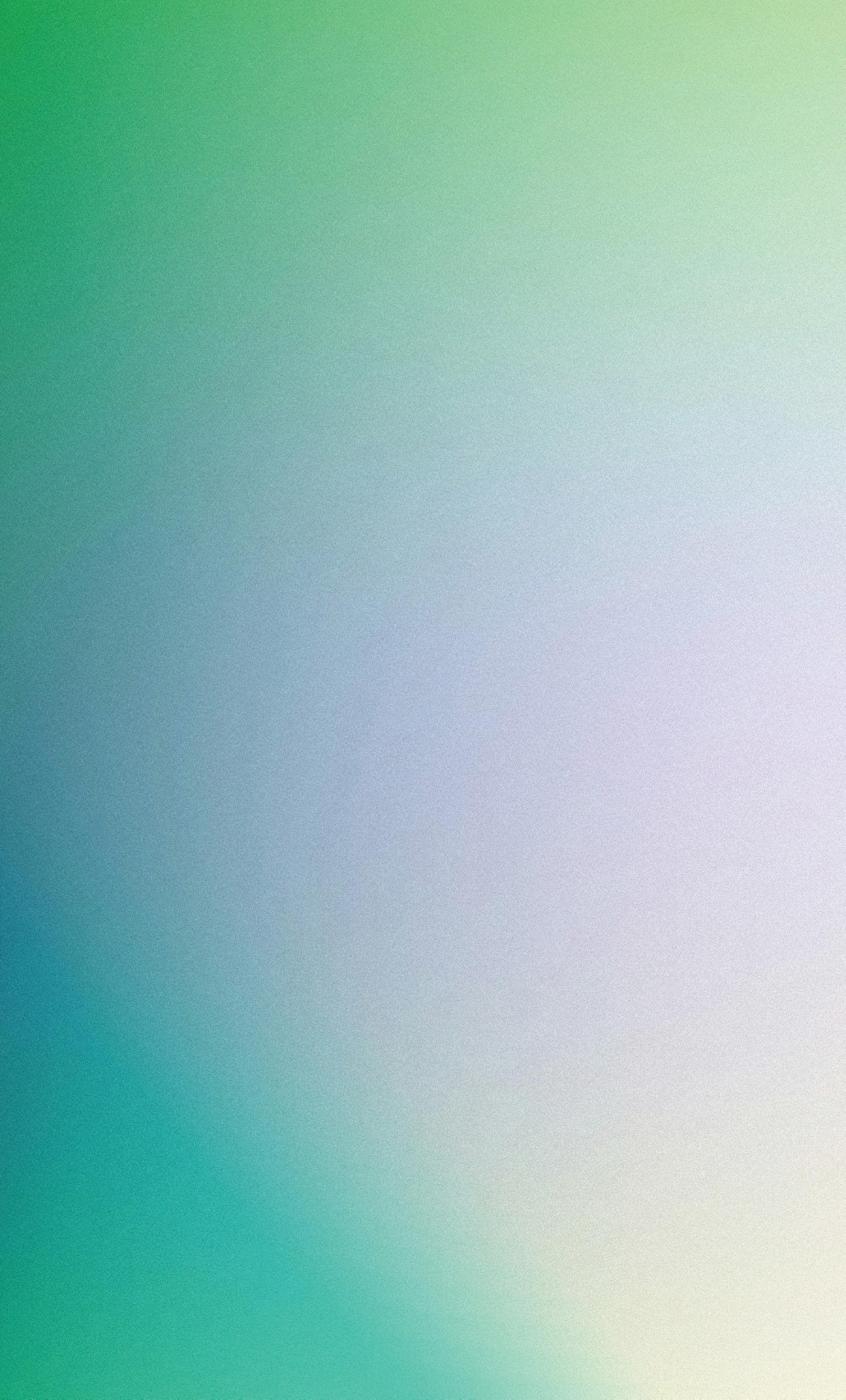
A Partner in Solving Crucial Logistics Issues
A Conversation With Mike Coleman
Mike Coleman is president and CEO of CV International, a Norfolk-based global logistics, freight forwarding, and trade compliance services provider, and Capes Shipping Agencies, a wholly owned subsidiary that provides ship agency, cargo forwarding, and logistics management services to clients. He has served on numerous boards for the logistics industry, including a current appointment to the Virginia Port Authority Board of Commissioners.
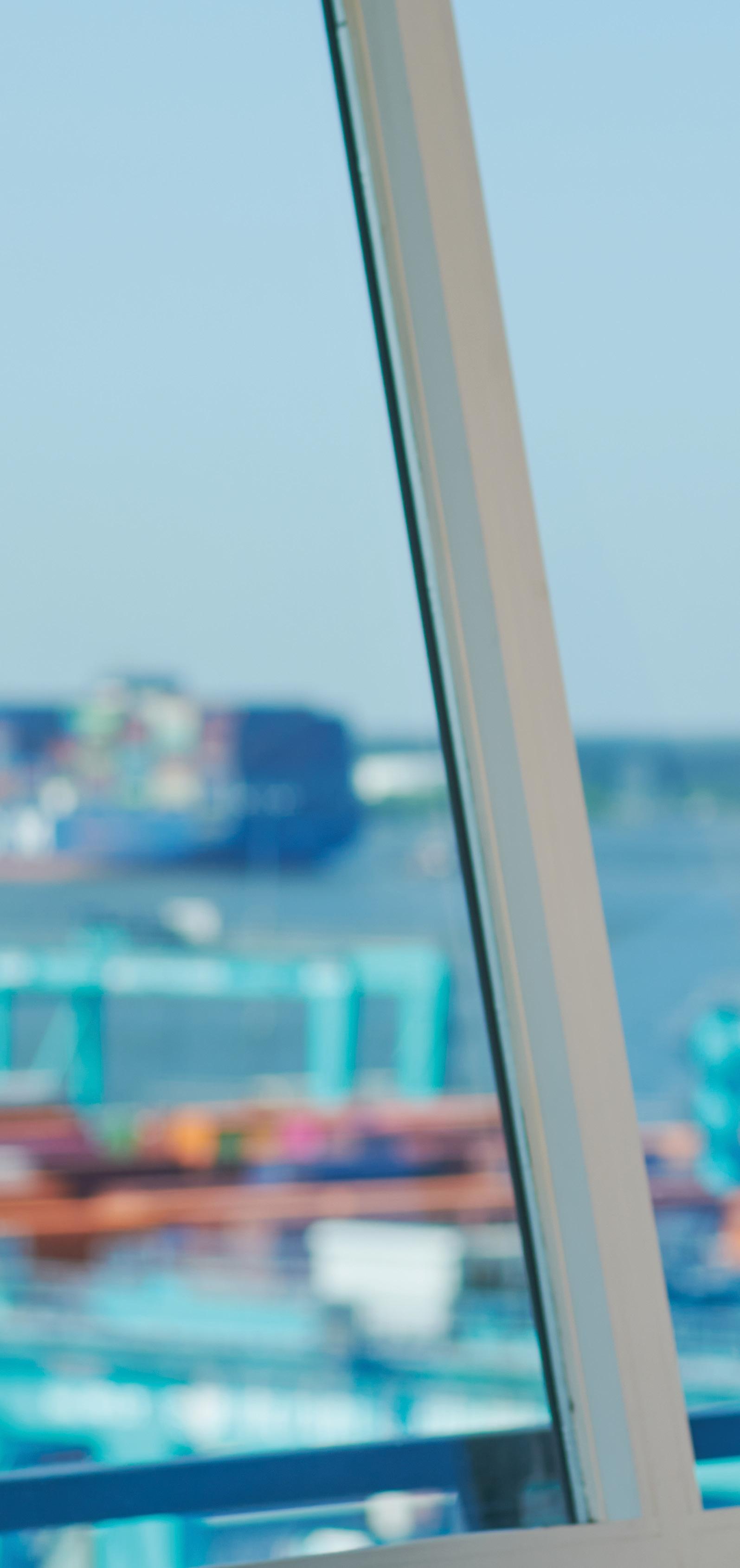
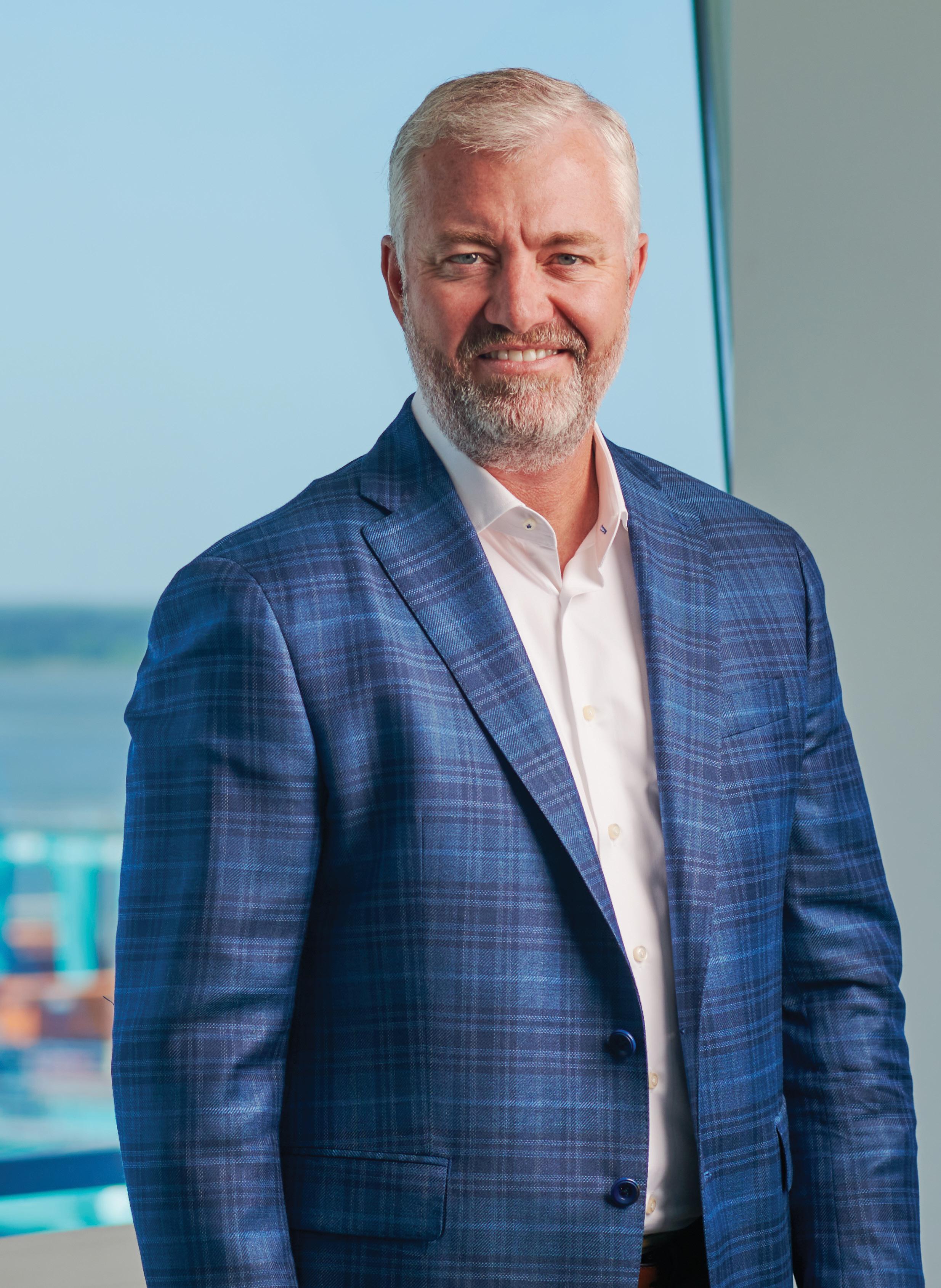
VEDP: Can you give us a high-level overview of CV International’s history and offerings in the third-party logistics space?
Mike Coleman: My father started the company back in 1984. He saw the need for a personalized, high-touch freight forwarding service in Norfolk, and he struck out on his own with the help of my mother and my grandmother. I came back into the family business after graduate school with the task of taking the company to the next level of growth.
We’ve grown steadily since our founding. We’ve expanded our suite of logistic services to include everything from customs brokerage to air freight forwarding to truck brokerage and warehousing to ship agency and bulk shipping under our Capes Shipping Agencies brand — and, most recently, shore-side marine support for the booming offshore wind industry in Virginia.
Our focus really continues to be providing seamless, personalized
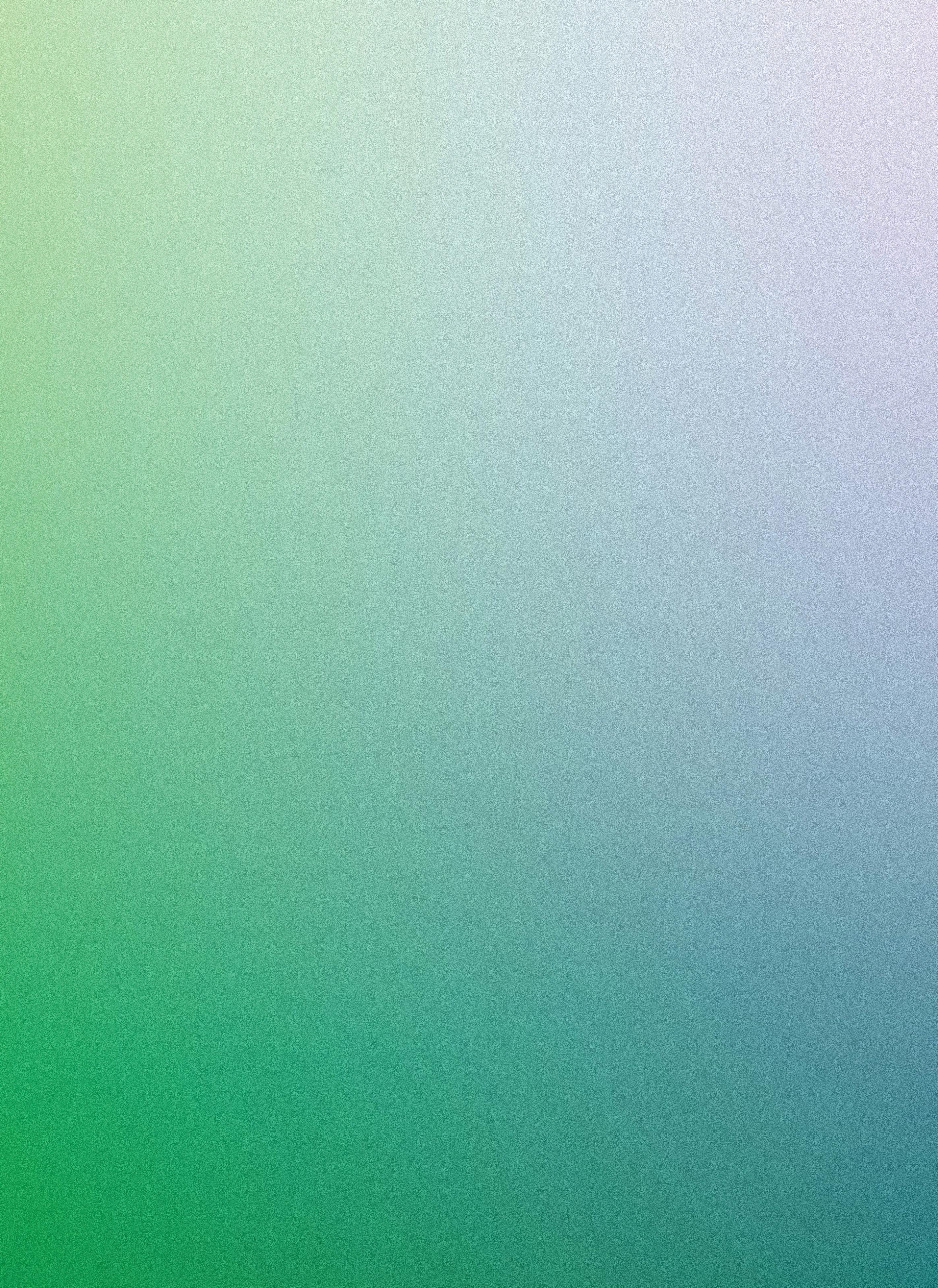
international logistics and compliance solutions for our clients. We operate as if we’re our client’s transportation department or their office in port, as the case may be. We really see ourselves as an extension of our client’s business.
VEDP: You’re intimately familiar with The Port of Virginia as a logistics operator in Hampton Roads and as a member of the port’s Board of Commissioners. What are the main topics this group is concerned with presently?
Coleman: We’re very fortunate to have an incredibly talented leadership team at The Port of Virginia and a best-inclass, very well-run, efficient port. The port recently became the first port on the East Coast to power its terminals 100% by clean energy, and the goal is to have net-zero carbon emissions by 2040. That is a significant accomplishment. We just completed the dredging and opening of the widest shipping channels on the East Coast, allowing for unimpeded two-way traffic in our port. There are also major ongoing investments in port infrastructure,
such as the Gateway Investment Program currently underway and expansions and improvements to our inland terminals in Richmond and Front Royal.
The port has been heavily focused on strategic growth as an economic driver for the Commonwealth. Its efficiency, wide variety of ocean carrier services, and intermodal connectivity make it a significant selling point for companies looking to locate here in Virginia. We’re very fortunate to have this incredible port, this incredible gateway to the world, right in our own backyard. The fact that Virginia continues to invest in its port and its efficiency serves as a tremendous advantage for users.
VEDP: What are you seeing in the supply chain industry from your perspective? Where is your energy focused?
Coleman: I think like most industries, we’re seeing a rapid acceleration of data-driven technologies and the potential for artificial intelligence to
play a massive role in our own space. The problem in our industry is that it has always been fairly slow to adapt, and the source information upon which humans or tech make decisions has been really unreliable or otherwise incomplete.
We’ve been heavily focused on marrying our exceptional service, the human element, with exceptional data and the latest visibility technologies to help our clients make better decisions. Our focus is always going to be on our people and providing them with the resources and technologies that they need in order to deliver a market-leading service to our clients, whether it involves moving a container from Shenzhen to Norfolk or a coal ship loading in the middle of the night in Baltimore.
VEDP: Looking beyond the port, how are other segments of the supply chain responding to the increased focus on resilience and the need to adapt? Are you seeing alternate modes of transport, such as transloading, domestic consolidations, and perhaps even air freight, factoring more into your customers’ overall logistics plans?
Coleman: We’re living in a very volatile world right now, and then you have all these unknowns that come up, like recent events like the Key Bridge collapse in Baltimore and the Red Sea crisis. It underscores the inherent unpredictability in global supply chain and logistics and reinforces the fact that it’s more important than ever right now that companies are building their supply chains to be very resilient and dynamic.
In the years since the COVID-19 pandemic, we’ve seen companies generally fall back on this just-in-time
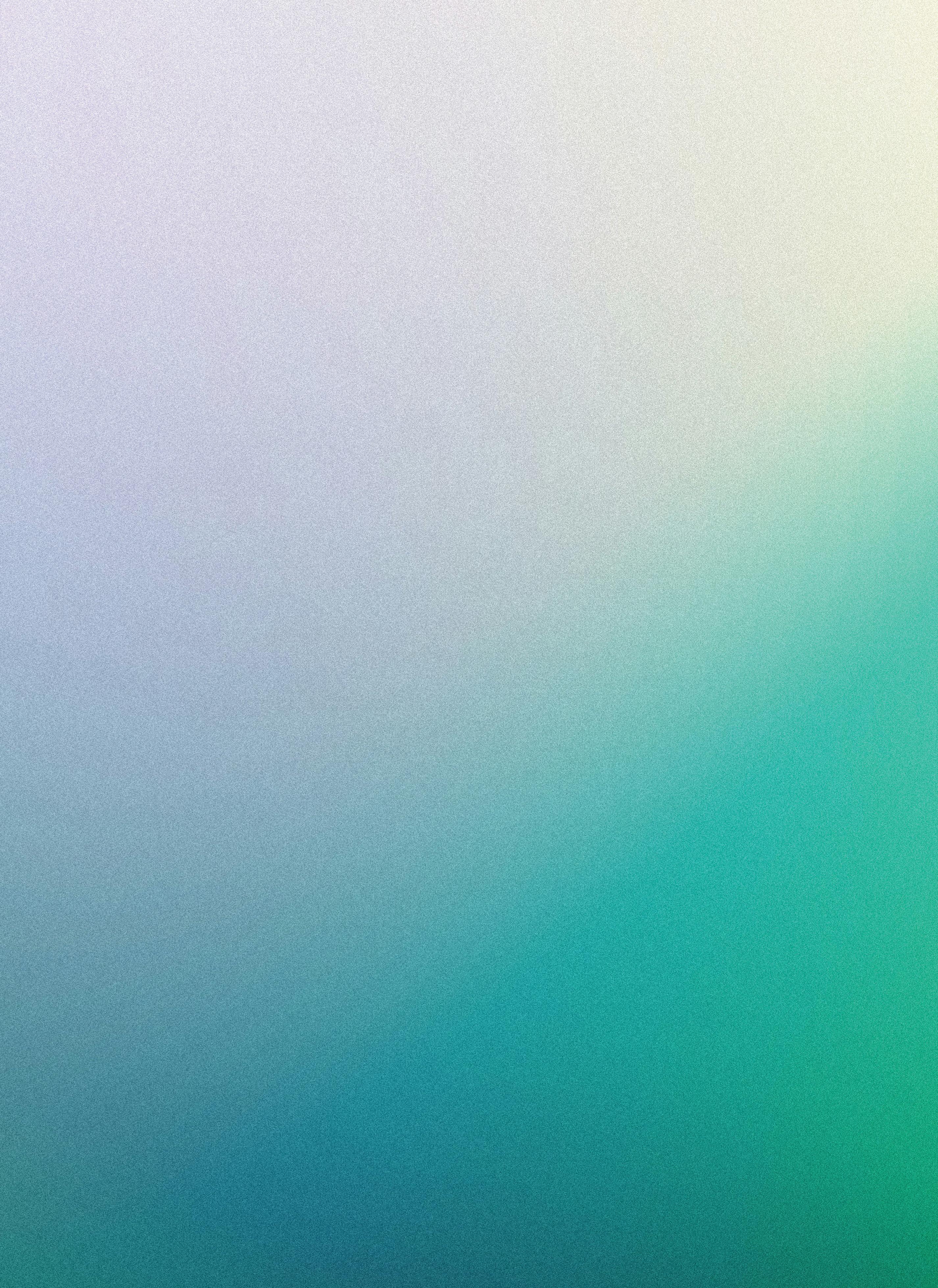
[The
Port of Virginia’s] efficiency, wide variety of ocean carrier services, and intermodal connectivity make it a significant selling point for
companies looking to locate here in Virginia.
MIKE COLEMAN President and CEO,
CV International
inventory methodology. In this environment for global trade, we may not always find that to be sufficient. We frequently urge our customers to use very specific advanced planning in their supply and their supply chains, look ahead for bottlenecks, and then eliminate them or develop contingency plans. It’s more of a just-in-case strategy to help avoid the kind of complications that can disrupt supply chains.
We try to help our clients think three steps ahead and have alternatives available to accommodate for disruptions in the supply chain. Disruptions might come in the form of the Red Sea issues that we’re seeing, or low water in the Panama Canal, but they also might be more specific to a client, like unanticipated shortages of raw materials at a factory.
VEDP: What challenges are CV International’s clients coming to the company to help solve in 2024? Are your clients focused on primarily tactical, near-term behaviors, or have they shifted to longer-term planning and overall supply chain design? How does the
company differentiate itself in a crowded marketplace?
Coleman: Looking forward into the rest of 2024, I think geopolitical problems are going to persist, and companies need to be planning for them. There are also other potential disruptors, such as potential labor actions on the East Coast. Companies need to be thinking about that and just be ready to pivot if things don’t go the way we expect them to.
Our value to our clients this year has really been centered on being dynamic and bringing a lot of logistics options to the table, whether it be multiple ocean lines and services, routings, air and truck freight options, or something totally outside of the box. We, as a freight forwarder, need to be kind of a Swiss Army knife for our client partners, and that’s part of how we differentiate ourselves in our space.
VEDP: Technology and innovation are common points of emphasis these days. Where do you see technology having the most impact from a data perspective?
Coleman: Advancements in AI and data visibility will continue shaping supply chains in the months and years ahead, although I think we’ve yet to see exactly how and what the most appropriate use cases will be for new technologies. As I mentioned earlier, in our industry we have some issues with data quality. The variety of players in the space and the number of links in any supply chain spanning multiple countries and regions mean that there are often a lot of gaps in data.
Currently, shippers, purchasers, and logistics providers often have to use

what tools and data they have available to them to find workarounds for the anomalies. I think AI is going to help fill in those gaps. But in the end, I still think it’s going to be a tool, and not a silver bullet for these issues. The best solutions — in the near term, anyway — will be combining AI tools with human expertise, particularly in the areas of our business that are highly regulated, such as customs brokerage.
We’re also hearing from many of our customers that sustainability is becoming more and more essential, both internally and from their customers further downstream. The sustainability journey is going to start with data gathering. To know where you’re going, you first need to know where you’re currently standing, and tracking data points like carbon emissions is increasingly becoming more than just a nice-to-have, but a prerequisite for doing business with a lot of our clients.
VEDP: Where should companies focus their own investments, and how should they be collaborating with their partners to navigate today’s complex environment?
Coleman: For anybody shipping globally, there needs to be a very strong focus on resilience and innovation. They’re going to find returns there. Building resilience starts with strategic forecasting, anticipating disruptions and building redundancies in the supply chains, and investing in cybersecurity measures.
On the innovation front, we’re talking
about how automation, data analytics, and AI are becoming game-changers in our business in the way they can optimize efficiency and generate insights that will reshape global trade. In any industry, companies need to be looking toward AI as a way to make their operations more efficient.
Collaboration is going to be key in making this work. Companies should make efforts to share insights with their partners throughout the supply chain. It’s through this sort of collaborative approach that companies are really going to reap the benefits of resilience and innovation. For the upcoming year, building resiliency in your supply chain is going to be critical.
VEDP: Automation in the e-commerce and fulfillment segments of the logistics sector gets significant attention. Tremendous research is going into autonomous vehicle development as well, from individual consumer delivery to autonomous trucking at scale focused on the “middle mile.” How is the logistics industry adapting to these innovations?
Coleman: Well, there’s clearly a lot of potential for automation and autonomous vehicles to really transform the industry. Automation, whether in fulfillment or elsewhere, brings opportunities for tremendous efficiency and cost savings. While the technology isn’t quite there yet, I think it’s clear that the day is going to come when these driverless trucks are going to be part of every supply chain.
There’s been a lot of talk about job displacement, but I don’t think that this
will necessarily be a case of machines replacing workers entirely, but rather an example of collaboration between the two. While there may be large portions of the middle mile that become autonomous and can be navigated successfully, it looks like, at least for the foreseeable future, the skills and judgment unique to human drivers will be necessary for those first and last miles, particularly in cities and more populated areas and even in the ports. We’re a ways off from automated trucks going into and out of our ports and driving in our populated areas, but that middle mile is where I see it potentially having some success.
VEDP: What additional risks around supply chains haven’t we discussed that you see either on the horizon or perhaps remain ever-present? How should companies be looking at mitigating these risks?
Coleman: We’ve experienced sustained economic growth and decades of globalization, but we’re seeing increased pressure due to geopolitical tensions, whether it be the disruptions in the Red Sea, or what’s going on in the Middle East and Europe right now, or even our relationship with China.
Technology has presented many opportunities, but the current market comes with a number of risks. Companies can help mitigate that risk with strategic advanced forecasting — building redundancies in their supply chains and their sourcing strategies and continuing to build strong relationships with their partners in the supply chain. Open communication
While there may be large portions of the middle mile that become autonomous and can be navigated successfully, it looks like, at least for the foreseeable future, the skills and judgment unique to human drivers will be necessary for those first and last miles.
MIKE COLEMAN President and CEO, CV International
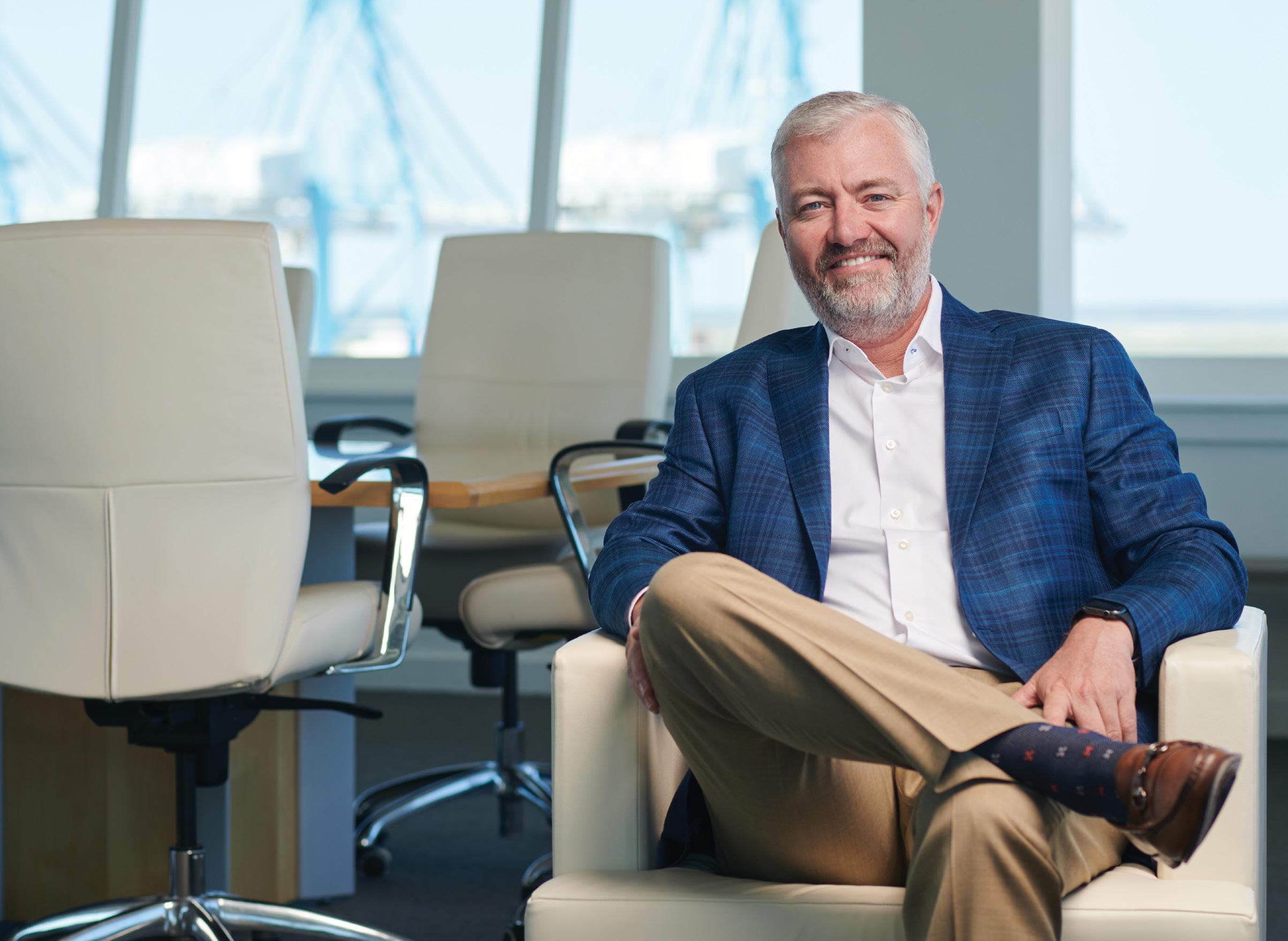
and collaboration allow for quicker responses to disruption. Planning ahead, forecasting, and being prepared for that worst-case scenario allow for quicker responses to disruption. Part of what we’re trying to do for our clients is to be that backup plan for them if things go sideways.
VEDP: On a personal note, do you have any recent discoveries in your leisure time that stand out in the Hampton Roads community? Any favorites elsewhere in Virginia?
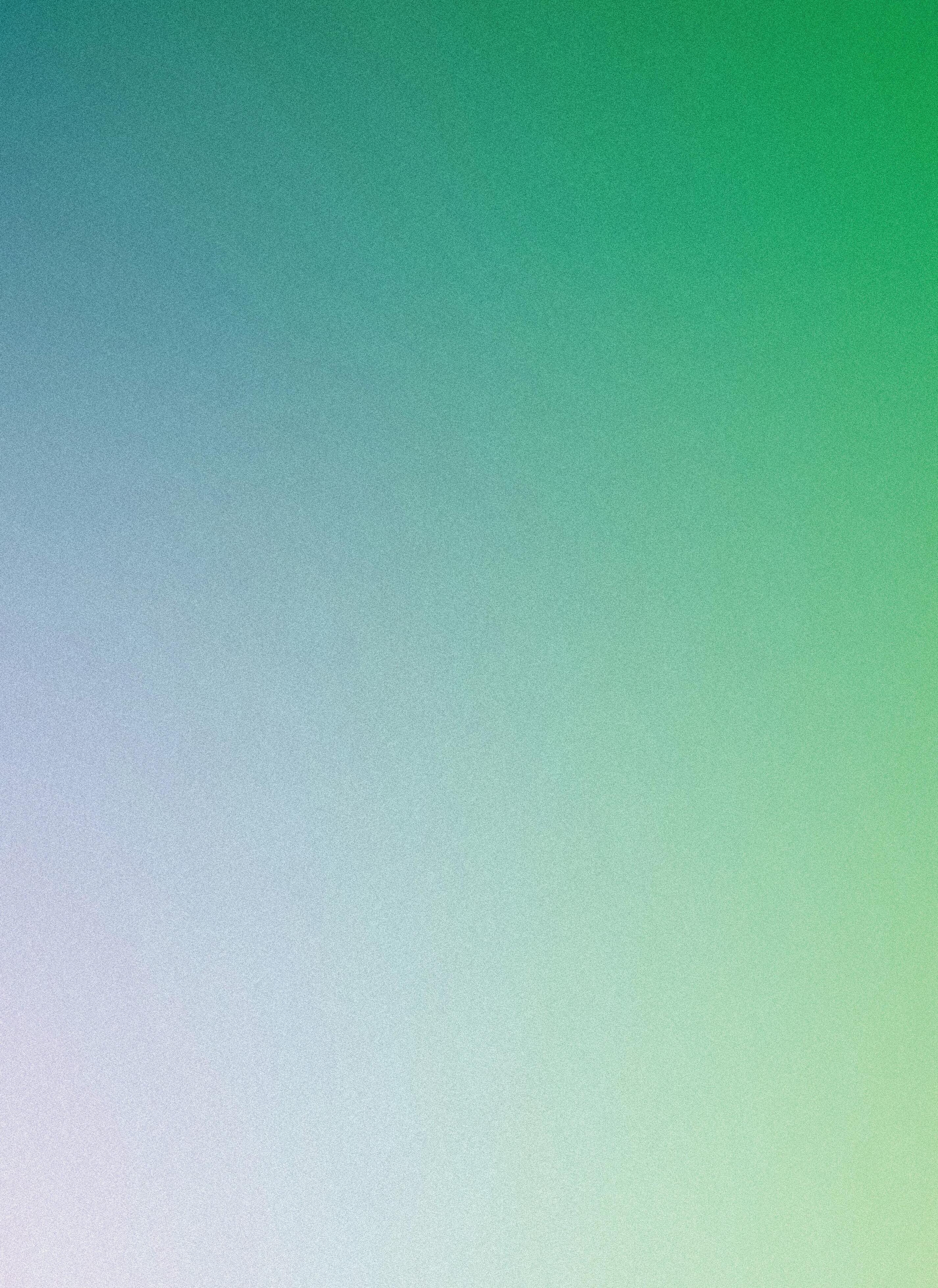
Coleman: The one thing that I love the most about Hampton Roads is the fishing. Unfortunately, I don’t have a lot of free time right now to be fishing, but when things lighten up for me, I’m going to get back out on the water. We’re blessed in Hampton Roads to have a lot of opportunities to target a wide variety of fish, both in the bay and in our inlets and our rivers, as well as offshore. I’m particularly looking forward to cobia fishing this summer in Chesapeake Bay. I’m going to be very intentional about that this year.
Building a Supply Chain Workforce in Hampton Roads
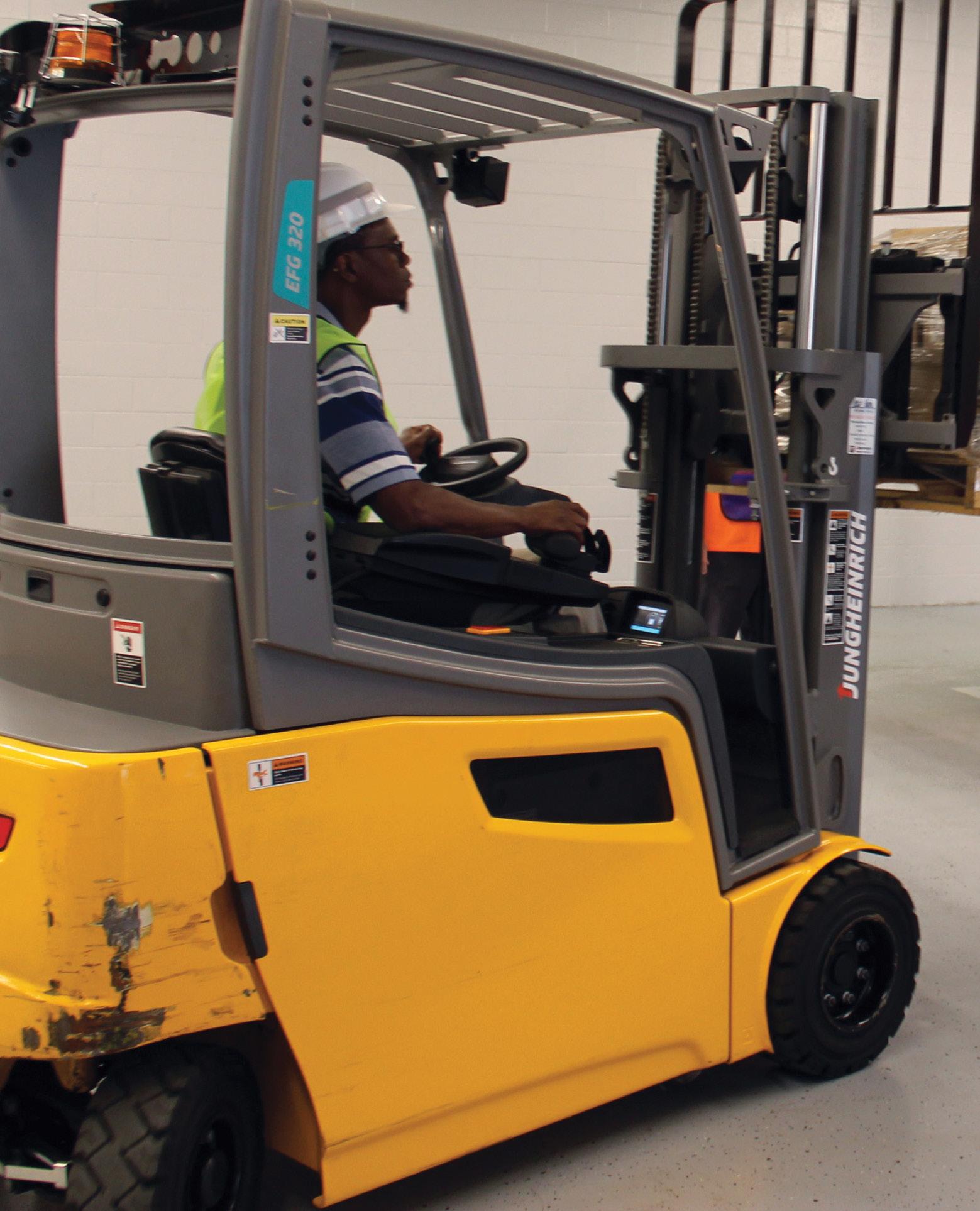
Supply chain management (SCM) and logistics have changed dramatically in the last decade. There’s growing demand for deeper visibility into every step of the supply chain. Automation is playing an ever-larger role in the movement of goods. Delivery times are shrinking even as supply chain hurdles become more complex. With each of these changes, the supply chain workforce is forced to adapt and adopt new skill sets.
In Virginia, where the movement of freight supports more than $350 billion of the annual gross state product,
Paul D. Camp Community College works with employers like Amazon to develop programs that meet industry needs and train students for logistics employment. The college offers industrial automation, robotics, and mechatronics programs along with a Certified Logistics Associate certificate and a Certified Logistics Technician credential.
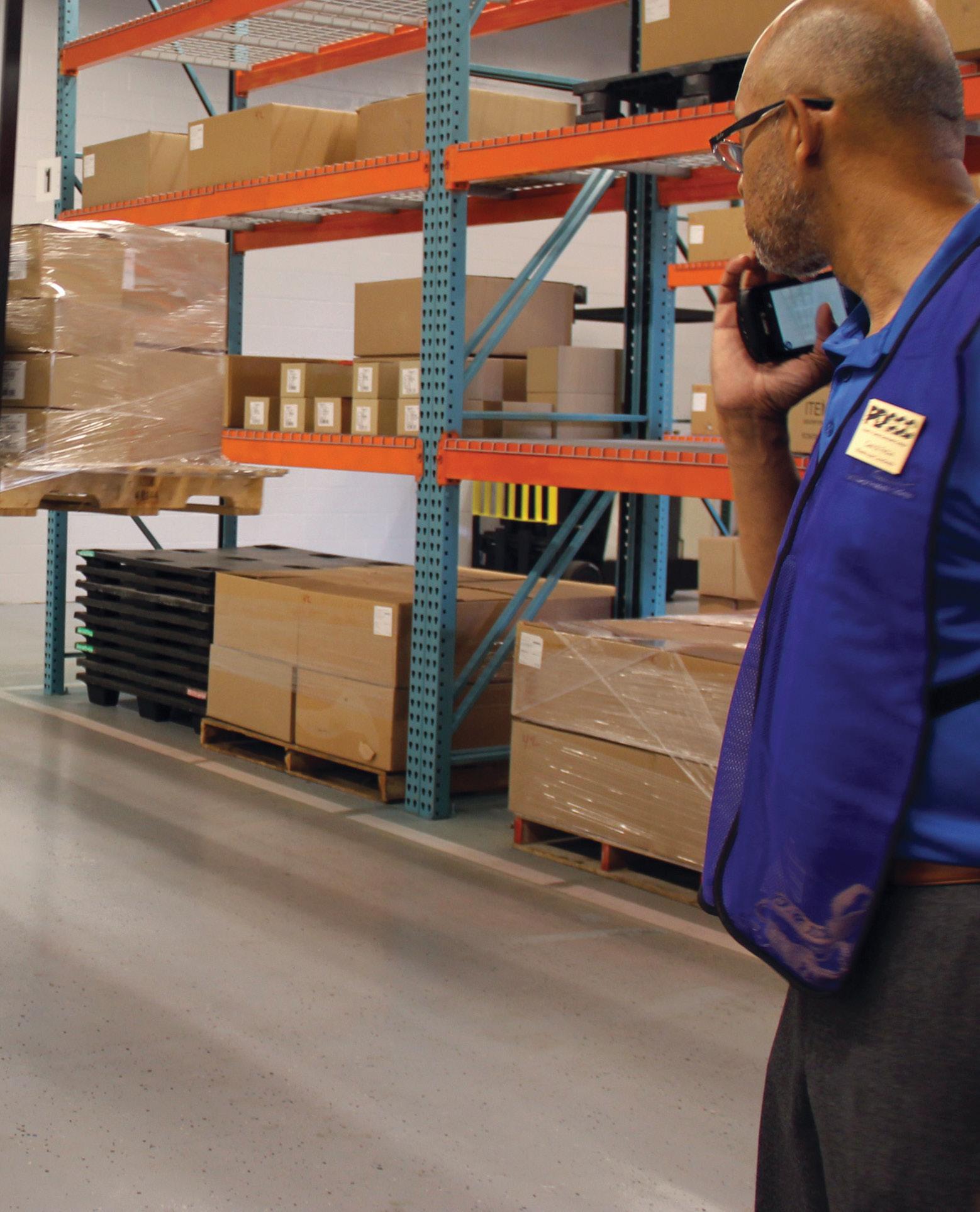
educational institutions are ensuring a workforce is ready to meet the evolving needs of the supply chain industry.
To keep ahead of the industry’s evolving demands, Old Dominion University (ODU) in Norfolk has established a new interdisciplinary School of Supply Chain, Logistics & Maritime Operations. When classes begin in August, the school will be uniquely positioned to connect students with in-demand careers in SCM and logistics and local employers with a trained workforce pipeline.
“It’s a first-of-its-kind offering for this region due to its focus on maritime,” said Elspeth McMahon, associate vice president for maritime initiatives at ODU. “When building this new school and its associated programs, we leveraged the strengths of ODU and its location in the heart of Hampton Roads. Industry was heavily involved to ensure that their needs are met and that we provide the right skills for the future workforce.”
Students at the standalone school will have the option of pursuing a bachelor’s degree in interdisciplinary
We want to drill down and make certain we’re addressing the regional needs. This grant will allow us to engage with our business partners and make sure we have our finger on the pulse of what they actually need in the way of skill sets.
COREY M c CRAY President, Paul D. Camp Community College
studies with a major in supply chain and maritime logistics and a master’s degree in maritime trade and supply chain management. Courses will cover topics as varied as forward and reverse logistics, warehouse and materials management, global sourcing and supply management, buyer-supplier relationships, port operator costing and pricing, and analysis of international shipping. The school also offers previously existing graduate certificates in supply chain management and maritime port and logistics management that provide students with speed and flexibility in advancing their skills.
AN IDEAL LOCATION FOR RELEVANT EXPERIENCE
The school’s location, just minutes away from The Port of Virginia, Naval Station Norfolk, and HII’s Newport News Shipbuilding, sets an ideal stage for on-site experiential learning opportunities, hands-on capstone projects, and local internships in the maritime industry. However, McMahon notes that the school’s curriculum will look well beyond the maritime industry to provide valuable SCM and logistics skills for fields including healthcare, advanced manufacturing, and renewable energy.
The school’s goal of serving myriad industries beyond maritime has attracted support from partners as diverse as sister companies Dollar Tree, Inc. (headquartered in nearby Chesapeake) and Family Dollar Stores, Inc., which manage a vast supply chain and distribution across 48 states and Canada, and warehousing, transportation, and logistics provider Givens Logistics. Ocean carrier Maersk Line, Ltd. and maritime fleet operator McAllister Towing provide a maritime perspective that is rounded out by additional support from the Virginia Maritime Association and the Virginia Ship Repair Association.
While these and other industry partners provide hands-on learning opportunities for students, they also stand to benefit
through ODU’s work as an R1 research institution. The school has set a mission to work closely with industry, government, and other institutions to explore solutions to key supply chain and logistics challenges. “We’re really looking at the future of the industry,” McMahon said.
IDENTIFYING THE SKILLS OF TOMORROW
To the west, Paul D. Camp Community College is preparing students to meet immediate workforce demands for the area’s warehouses and fulfillment centers. The college, which serves students in southeastern Virginia through locations in Franklin, Smithfield, and Suffolk, is working closely with industry leaders to better understand how to position its course offerings to connect students with in-demand skills.
For example, while Amazon’s robotic fulfillment center in Suffolk was under construction, Camp’s president, Dr. Corey McCray, met with partners in Suffolk to identify the skills that would be needed to run a largely automated site. With unmanned forklifts, robotic arms, and conveyor belts moving goods through warehouses and fulfillment centers, McCray found that companies are looking for individuals who can perform maintenance to keep those robotics systems operational.
Camp is working to provide these skills by offering a range of programs that meet students’ needs for flexible education options. Its logistics offerings include industrial automation, robotics, and mechatronics programs, as well as a foundational Certified Logistics Associate certificate and a mid-level Certified Logistics Technician credential.
McCray said the mechanical, electrical, and data science knowledge gained through the school’s mechatronics and related programs has far-reaching applications. To ensure the program is preparing students pursuing these
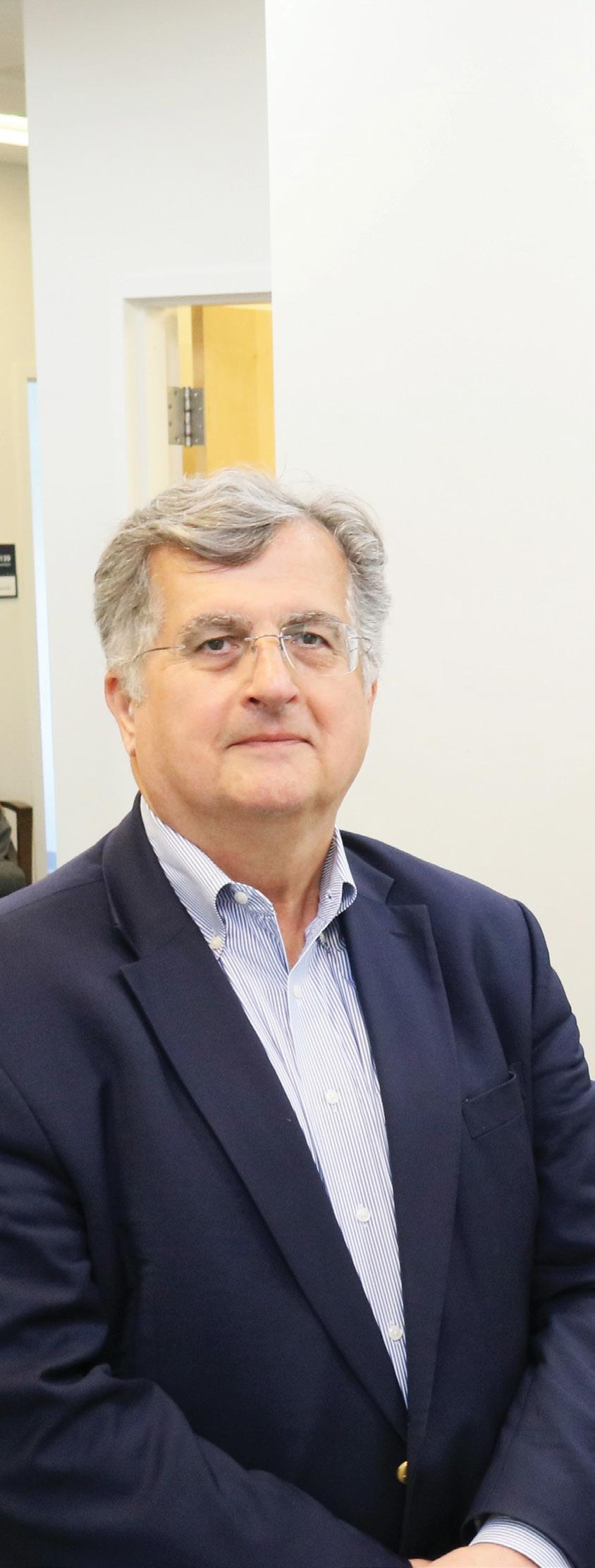
degrees for work in the logistics sector, the school is leveraging a GO Virginia grant to conduct a more expansive survey of the business landscape. With deeper insight into in-demand skill sets, the college will be able to assemble a comprehensive plan to upskill low-wage warehouse workers through its short-term training and degree offerings.
“We want to drill down and make certain we’re addressing the regional needs. This grant will allow us to engage with our business partners and make sure we have our finger on the pulse of
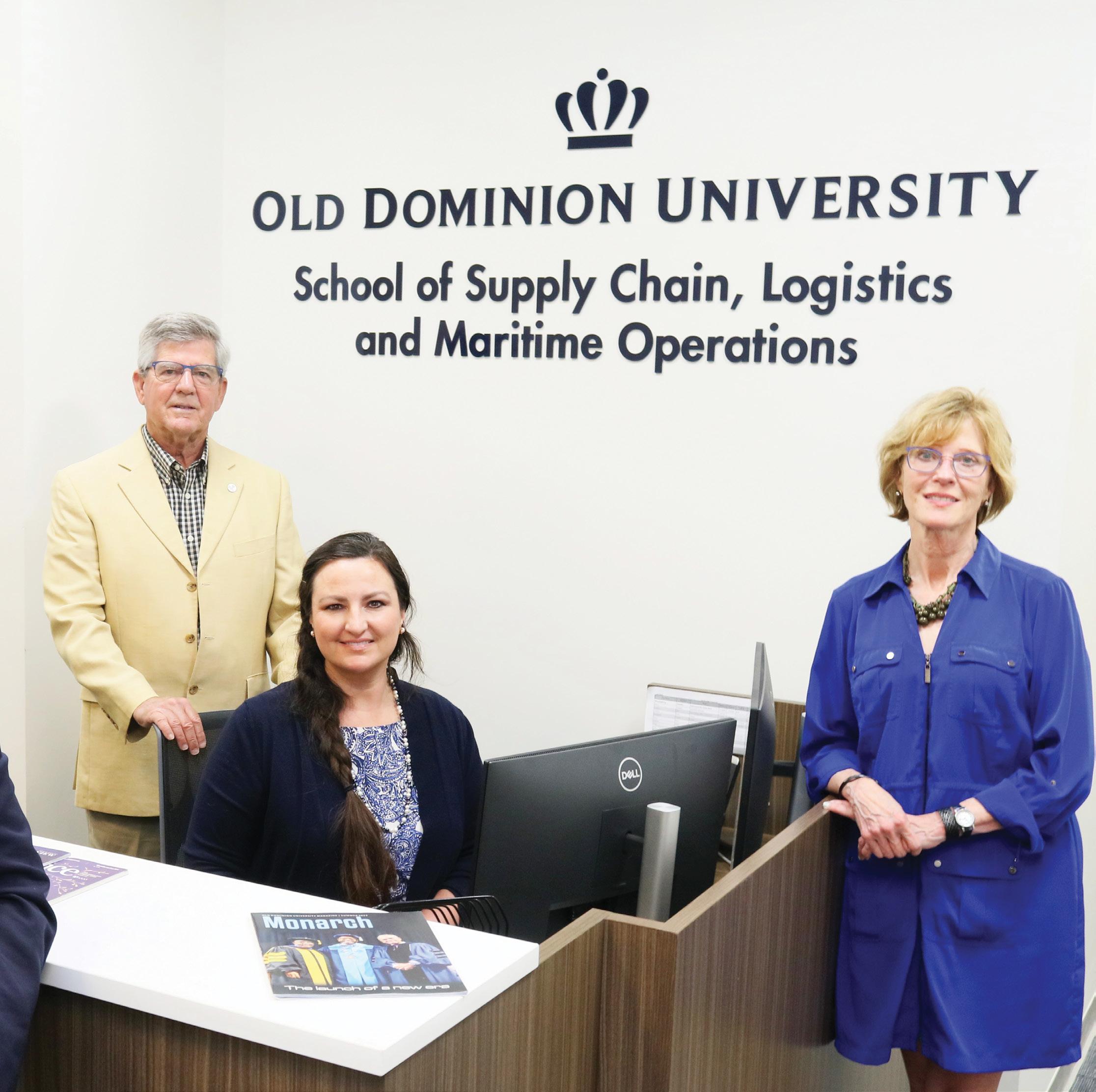
what they actually need in the way of skill sets,” McCray said.
As these schools strengthen their offerings, they’re also working to build community awareness around the value of a career in SCM or logistics.
“People don’t necessarily know about the maritime industry, or have only heard about the supply chain because of the COVID-19 pandemic,” McMahon said. “Not everyone is aware that there are many great, high-paying jobs in the maritime and
supply chain industries right here in Hampton Roads.”
ODU is connecting with alumni and industry partners to develop its strategy to raise awareness around its new school and the opportunities it offers students to stand out in a growing field. Camp, meanwhile, has taken a multi-pronged approach that focuses on meeting a range of student needs.
The college actively engages veterans transitioning out of the military — a large population at ODU, where
roughly 25% of students are militaryaffiliated, and in Hampton Roads, home to 15 military installations and more than 80,000 active-duty service members — and works with employed individuals looking to upskill and local school districts to educate students on their options.
“When [students] understand that this is not about pulling the levers on a forklift but is really robotics, they light up,” McCray said.
Old Dominion University’s School of Supply Chain, Logistics & Maritime Operations will begin official operations in August 2024. Students will be able to pursue a bachelor’s degree in interdisciplinary studies with a major in supply chain and maritime logistics and a master’s degree in maritime trade and supply chain management.

AT THE SOURCE SUPPLY CHAIN ISSUES SOLVING
ONE IS A TINY COMPANY
with its eyes on the heavens: Micro Harmonics pioneered high-tech designs and components with help from NASA.
The other company is a global leader that does its work beneath the surface: IMPREG builds sustainable liners that seal sewers, and its technology is dominant in Europe.
The companies share this in common: To reach their potential, each Virginia company was selected in 2023 as enrollees in the Supply Chain Optimization Program (SCOP), an initiative run by
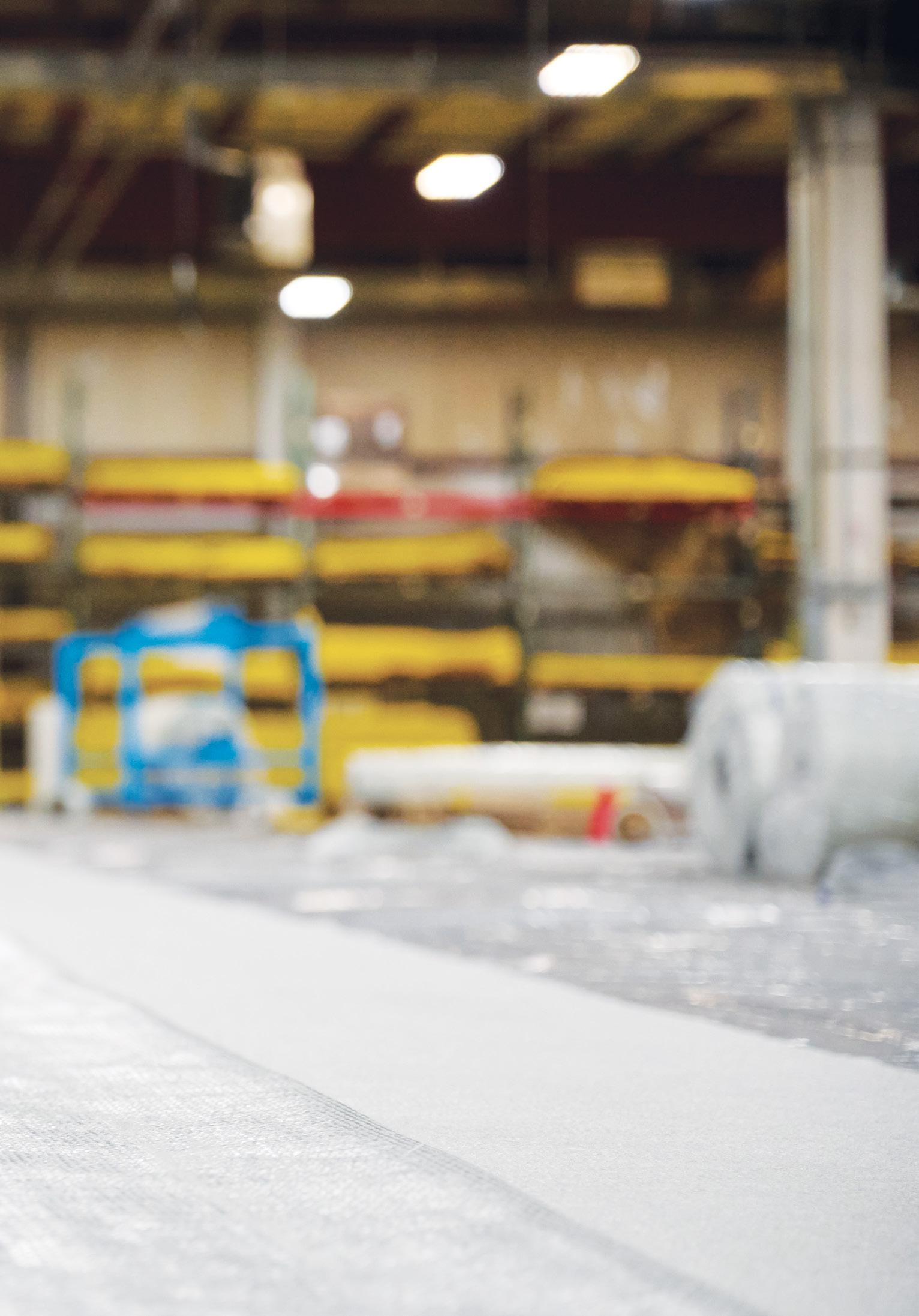
VEDP’s International Trade Division and the first state-led supply chain assistance program in the country.
The International Trade Division, which was recently honored with the U.S. Department of Commerce’s “E Star” Award for the second time, helps Virginia companies expand exports to drive company growth in the Commonwealth. To increase exports, companies must find cost-effective ways to import the materials and components used in the goods they manufacture.
SCOP, launched in September 2021,
selects 20 companies each calendar year to support with funding and expert supply chain guidance. Those companies have employed as many as 750 people and as few as five. But big or small, all benefit.
BIG RESULTS IN A TINY PACKAGE
Representatives from Micro Harmonics, with just 12 employees, first felt out of place when the company joined SCOP in 2023. “I walked in there and thought, I don’t really fit. And then I thought, ‘Wait a minute, we are all trying to do the same thing.’ [The company’s small size] just meant our problems are a little bit
different,” said Micro Harmonics Chief Operating Officer Diane Kees. The SCOP team “was wonderful at pivoting and meeting us right where we were. It had a huge impact on us. We’re set up to be able to grow and grow smoothly.”
That growth has been recognized by others. For a third consecutive year, Micro Harmonics, based in Fincastle, was on the Inc. 5000 Regionals list of fastest-growing private companies.
Micro Harmonics is proof that big possibilities sometimes come in the smallest of packages. Founded in 2008 by Kees’ brother, electrical engineer David Porterfield, the company creates tiny out-of-the-box electromagnetic components that enable high-frequency systems to deliver significantly more data faster than conventional microwaves used in satellites, GPS, and Doppler radar.
That potential, though, comes with challenges. The electromagnetic waves produced are so tiny, the distance between each peak is measured in millimeters. This means the constituent parts must be fabricated with precision to sizes that are so small they can barely be seen with the human eye. These tiny parts must then be aligned at precise angles by highly skilled technicians using powerful microscopes. The final components of competitors might fit into a tissue box; those from Micro Harmonics fit into a matchbox.
Heat is another obstacle. Because the parts are so small and power density is high, localized heating can destroy the tiny parts. To combat that issue, Porterfield invented designs that utilize novel materials, including diamonds grown in a lab, to effectively channel heat away from the tiny parts. The result is that Micro Harmonics components are smaller than other technologies, yet more efficient and able to handle significantly higher power levels.
“We had to come up with a whole different method…something
IMPREG Americas, Chesterfield County
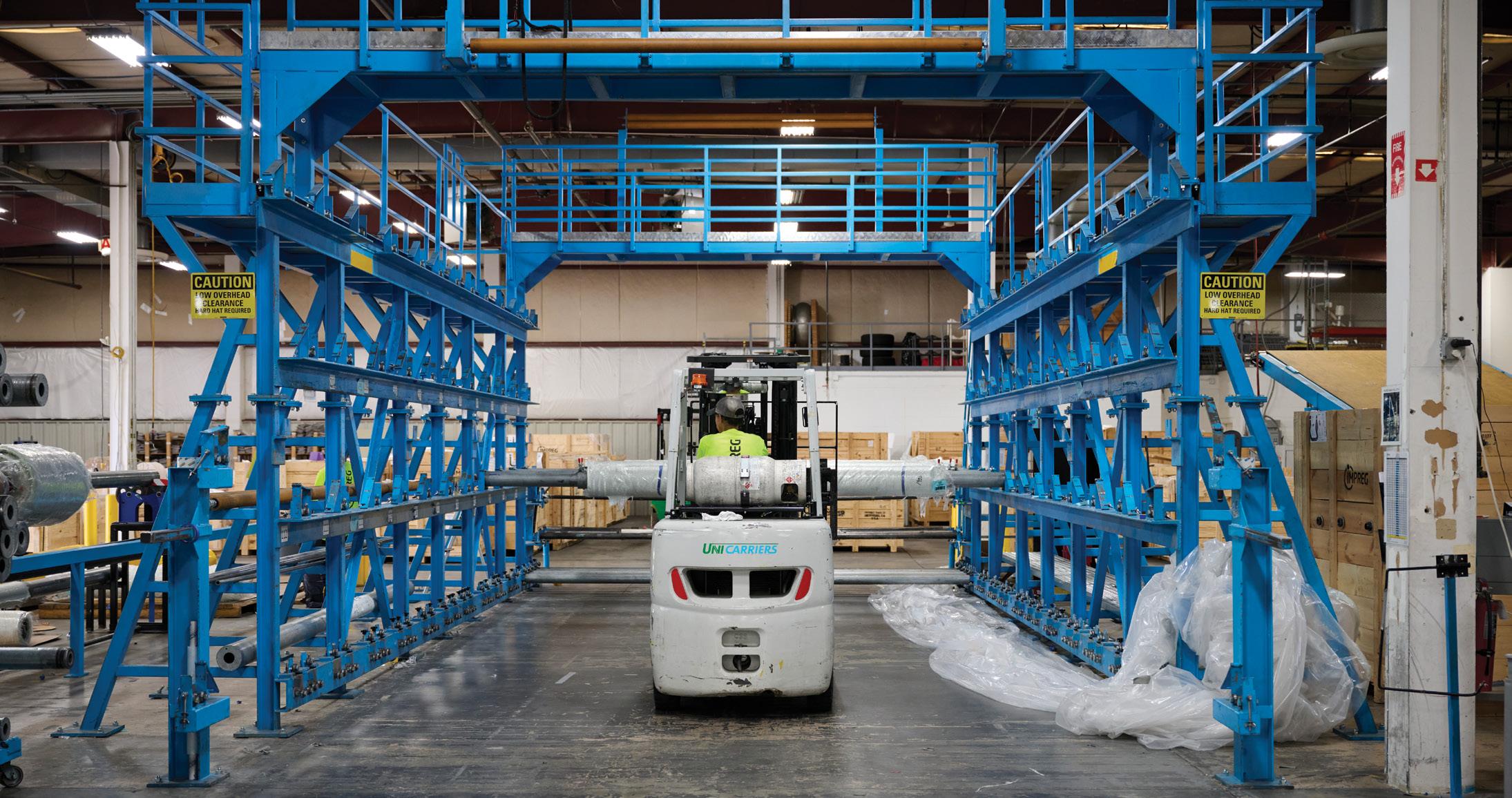
brand new that the world has never had,” said Kees, also an engineer.
Porterfield’s work gained the backing of NASA, which funded his research. But to commercialize, the company needed materials and facilities capable of producing components that would be assembled in Virginia.
HELPING COMPANIES SCALE UP
Domestic producers of lab-grown diamonds couldn’t keep pace, so Micro Harmonics looked overseas for a supplier. Machining proved an obstacle — no existing facility could do work that required such precision on the tiniest of scales.
SCOP and its partners helped the company get beyond sole sourcing and come up with a systemic way to manage vendors and manufacturers. “The program was amazing,” Kees said.
When potential customers want delivery, Micro Harmonics can’t lose time figuring out what must be done. “I’m an engineer. I’m not really a forecaster. Forecasting seems sort of like waving a magic wand, but that step has to be done,” Kees said.
With help from SCOP, Micro Harmonics learned no existing facility could do what it needed after many tried and failed. The company then focused its engineering know-how on finding a new solution. “We had to just come up with a whole different way of doing it that nobody ever thought about before,” Kees explained.
That led to an approach so revolutionary, Micro Harmonics has held off on seeking a patent for fear that doing so might give insight to a potential competitor.
“That sort of insight and action plan is what SCOP delivers,” said VEDP Supply Chain Program Manager Monica Sadie. “Rather than wait for a problem in supplies to emerge, companies are coached to identify vulnerabilities and reduce risks.”
Too many companies sole-source materials or components, so SCOP helps companies diversify suppliers. If one supplier struggles, others pick up the slack.
Such planning requires companies to create a written supply chain operational plan, something many program participants lacked. While
some companies employ a supply chain expert, SCOP encourages them to train multiple managers so the absence of one won’t torpedo the ability to plan smartly and react swiftly.
BESPOKE SUPPORT TO SOLVE SPECIFIC PROBLEMS
Support by SCOP is customized to each company’s needs. “That’s why we only bring 20 companies each year into the program — because we want to have the time and the bandwidth to assist them in an impactful way,” Sadie said.
That customization was crucial for IMPREG, a world-leading manufacturer of fiberglass-reinforced liners for the rehabilitation of sewer and stormwater pipes using environmentally friendly technology.
The company is dominant in Europe and has manufacturing facilities on four continents, but faced challenges sustaining growth in the Americas after locating a manufacturing facility in 2019 in Chesterfield County near Richmond.
“They have taken the time to listen and understand our pain points and have done everything they can to
IMPREG Americas, Chesterfield County
address those,” said Alain Monyette, a spokesperson for IMPREG Americas.
In the United States, when cities repair damaged sewer lines, rather than replace them, most insert liners that are sealed with pressure created by water and heat. But that process pushes harmful resins from the liners into the surrounding groundwater and soil, Monyette said.
IMPREG instead uses ultraviolet (UV) light to seal liners so no resins are released into the environment. That technology has long been the standard in Eastern Europe, where IMPREG and other companies also using UV rehabilitation control about 90% of the market.
“The European Union has a longer history of regulation around environmental protections,” Monyette said.
In the Americas, market share of UV cure is less than 10%, so the potential for growth is massive, but the path is riddled with uncertainty.
“We’re hitting some growing pains, which is why we wanted to start a dialogue with VEDP,” Monyette said. “The decision-makers and the reasons why they choose the IMPREG product are much different here than they are over in central Europe.”
Among the challenges are sourcing raw material quickly so that there aren’t delays in manufacturing liners whose specifications vary for each job. These include not just sizing but strength for load paths, as an example, if the pipe is under a highway or an airport.
IMPREG Americas worked with SCOP to seek local suppliers, said Nur Humayun, the company’s supply chain manager. “That was the first initiative we have done and they are helping us a lot,” he said. To make liners, IMPREG needs seven raw products, including resin
and fiberglass, so tracking those products is crucial. SCOP’s expertise “[helps] us to brainstorm and [gives] us some solutions on how to manage these kinds of inventories,” Humayun said.
HELP WITH SCALING UP
Beyond logistics, IMPREG needed help planning its pace of growth. That’s not a problem in Europe, where the company has operated since 1999. Existing robust sales data accurately projects how much growth to plan each year.
Three months after its manufacturing facility launched in December 2019, the
COVID-19 pandemic hit, stalling plans by IMPREG to use its experts from Germany to help American leadership, as travel restrictions delayed their arrival by 18 months.
But challenges haven’t dampened company plans or the vision to grow quickly on this side of the Atlantic in ways that respect the environment and each community, Monyette said. Just as his company has persevered to bring its facility to Virginia, SCOP continues to work through difficult issues to help companies shore up their supply chains.

Micro Harmonics Corporation, Botetourt County
Northern Shenandoah Valley
A HOTSPOT
FOR NATURAL RESOURCES NEAR THE NATION’S CAPITAL
Anchored by the historic city of Winchester — founded before the American Revolution — the Northern Shenandoah Valley is a fast-growing region on the outskirts of the bustling Washington, D.C. metro area. Winchester and neighboring Frederick County host the Shenandoah Apple Blossom Festival each April — the event celebrated its 100 th anniversary in 2024 — while the area’s abundant orchards support a robust food and beverage processing industry (Kraft Heinz, White House Foods, HP Hood LLC). Other major industries in the region include manufacturing (Thermo Fisher Scientific, Rubbermaid Commercial Products, Continental AG) and wood products (American Woodmark, Trex Company, Inc., Cochran’s Lumber). The region’s most prominent four-year college, Shenandoah University, is home to Shenandoah Conservatory, a performing arts program whose alumni include actors Kate Flannery (“The Office”) and Harold Perrineau (“Lost,” “The Matrix Reloaded”) and Dave Matthews Band drummer Carter Beauford.
THE NORTHERN SHENANDOAH VALLEY OFFERS:
An efficient logistics network including Interstates 81 and 66, freight rail service from CSX and Norfolk Southern, and the Virginia Inland Port, an intermodal container transport facility
The northernmost portion of Shenandoah National Park and the northern terminus of Skyline Drive, described by The Washington Post as “the ultimate fall drive”
A rich array of historical sites owing largely to the region’s prominence in the Civil War — Winchester hosted several battles and changed hands an estimated 72 times during the war
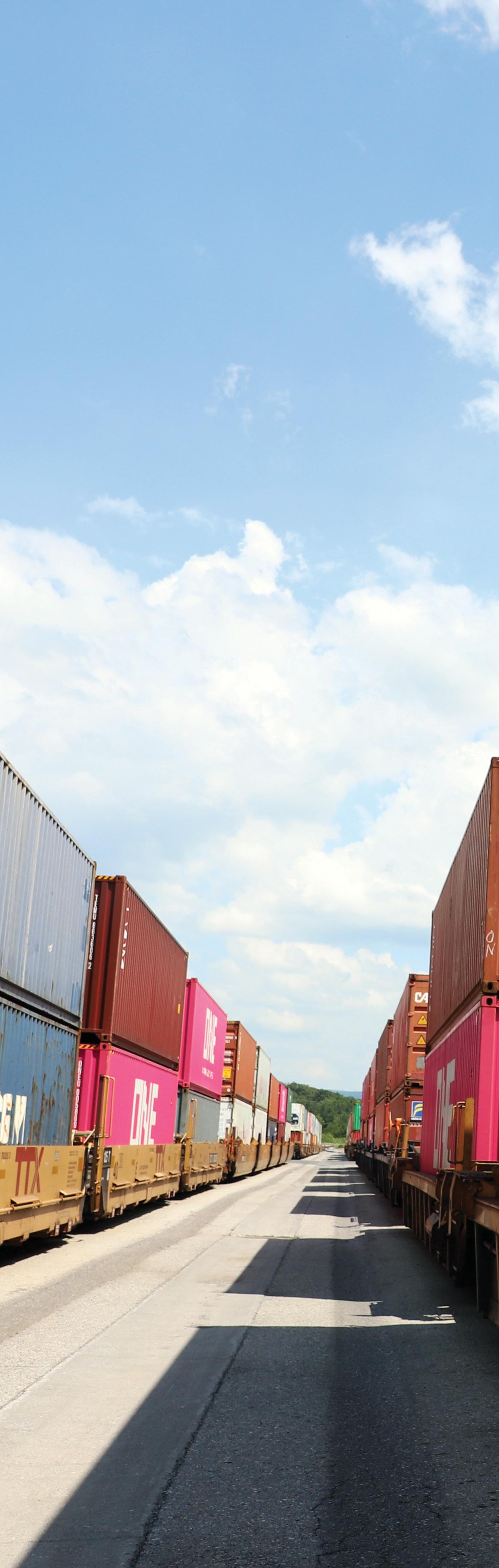
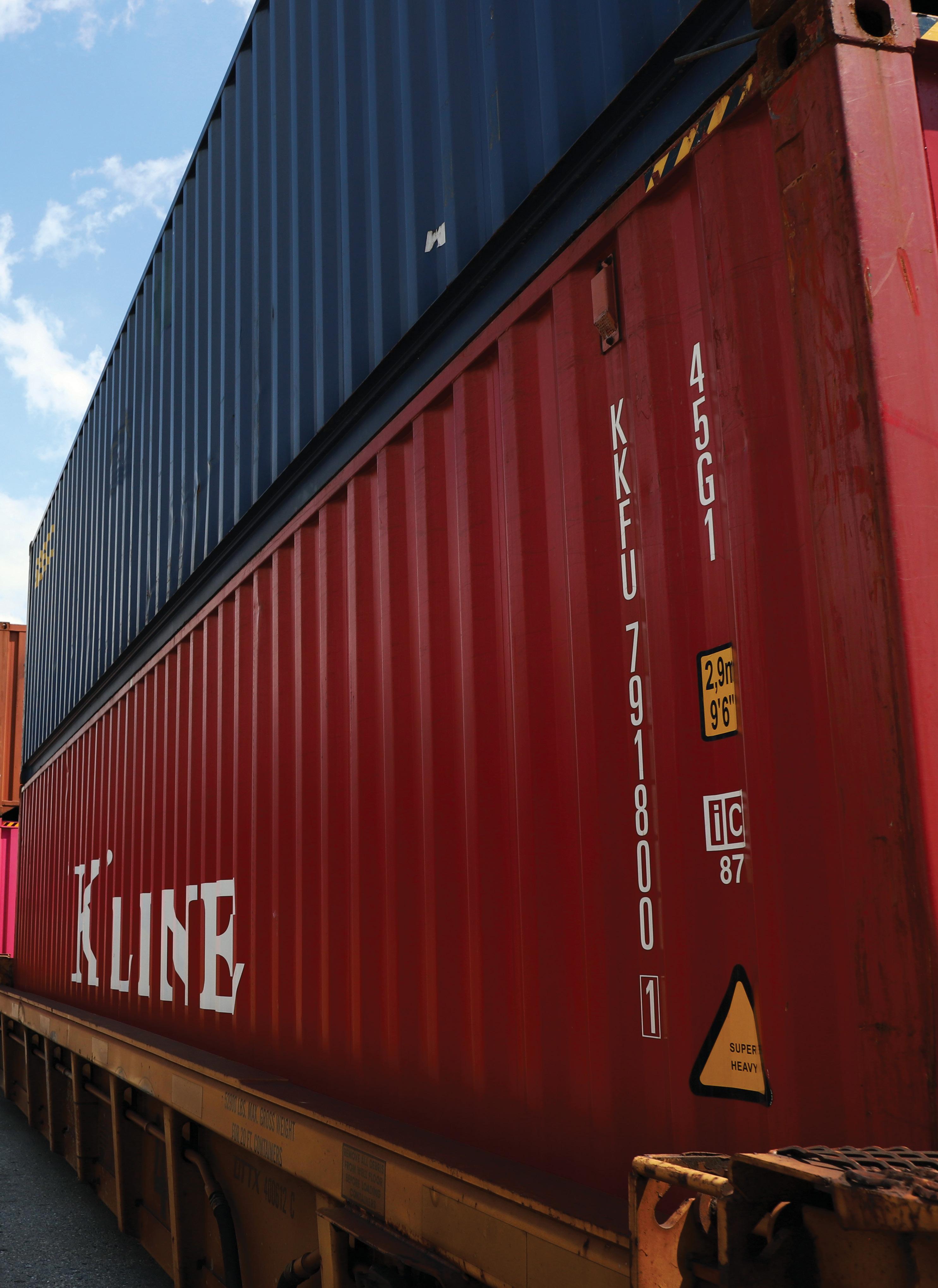
The Virginia Inland Port in Warren County is served by a Norfolk Southern rail line and is convenient to the intersection of Interstates 66 and 81.

Skyline Caverns in Warren County is unusual among publicly open caves in that it was discovered through an examination of surface topography.
Guided tours of the caverns are offered 365 days a year.
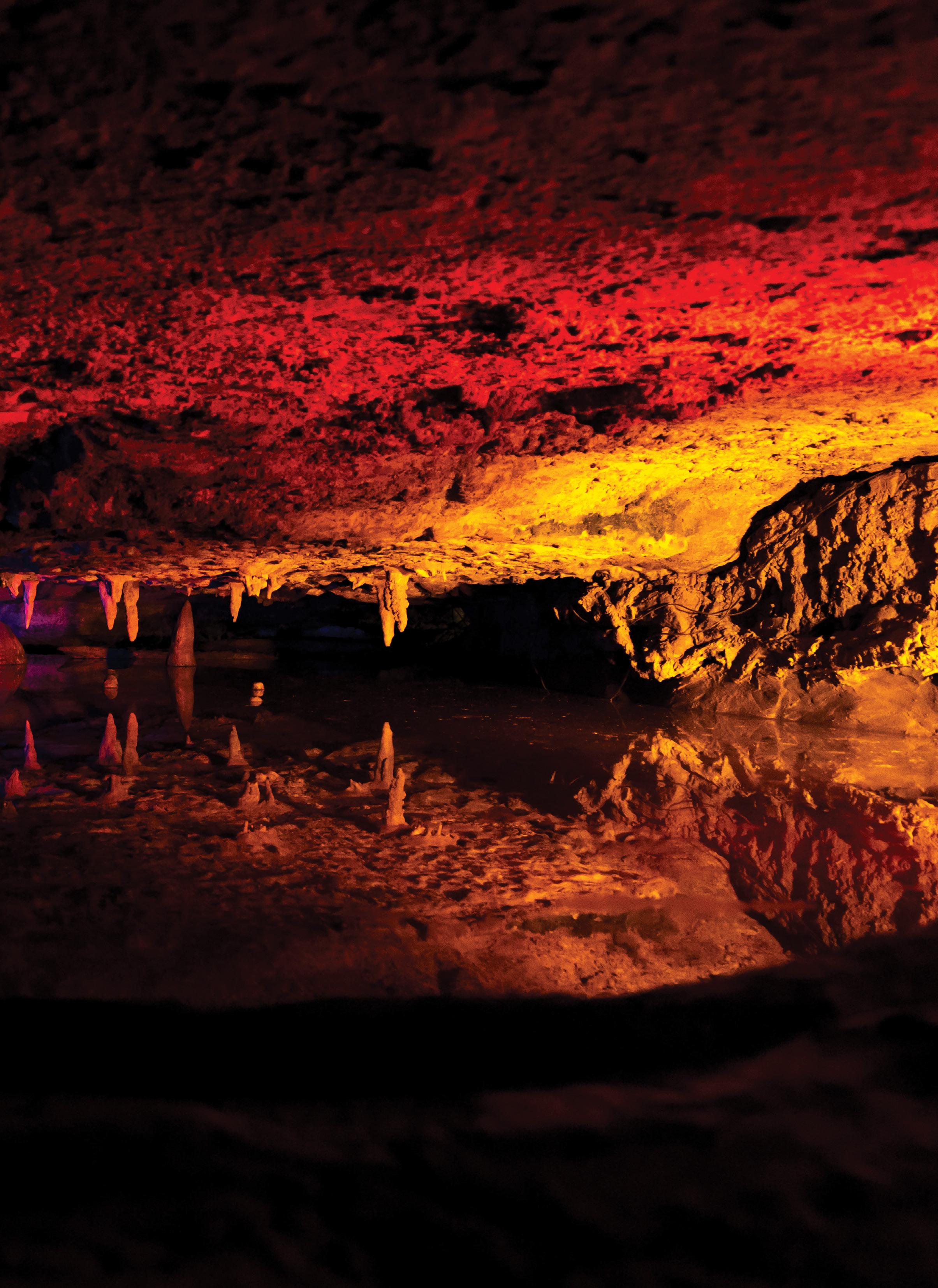
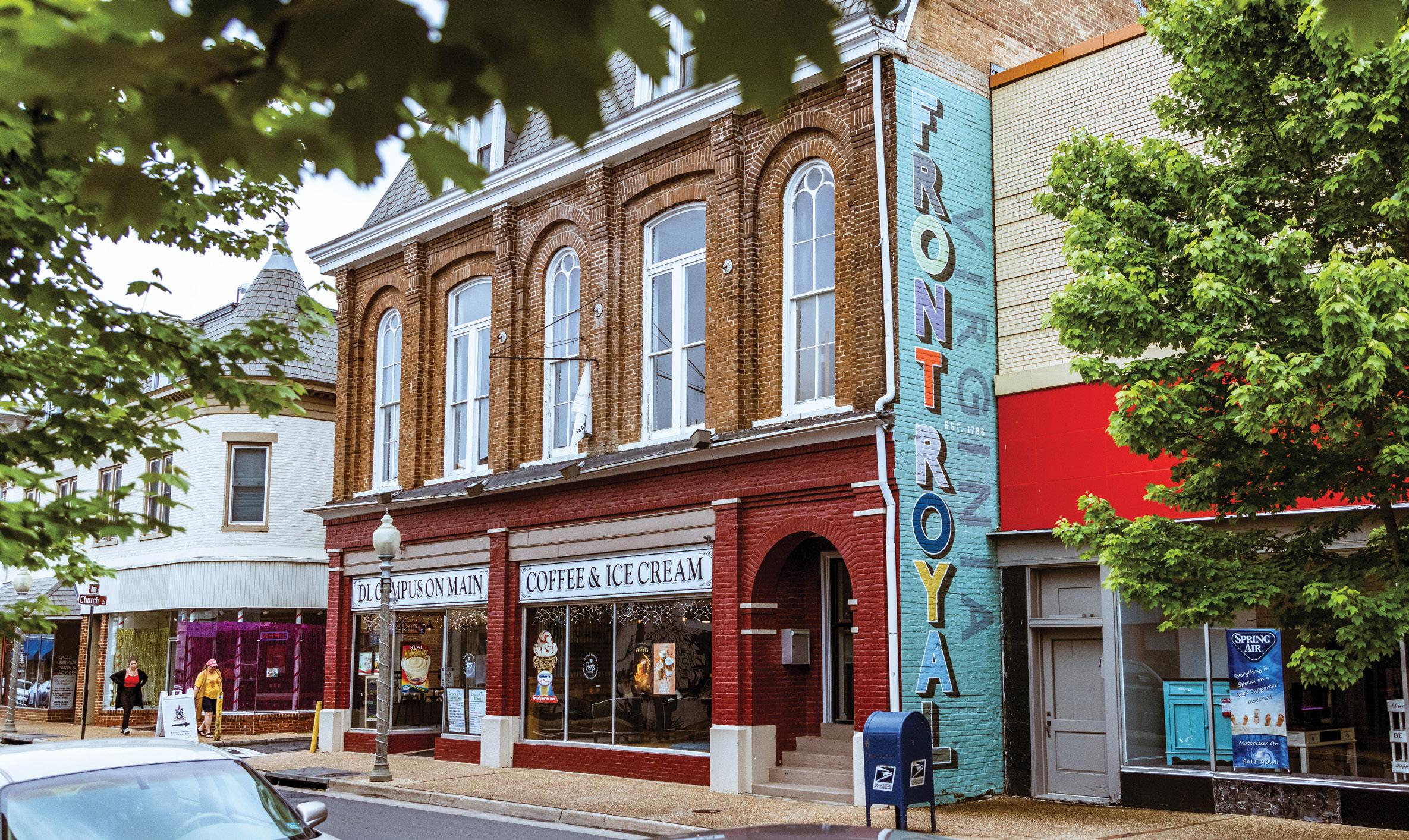
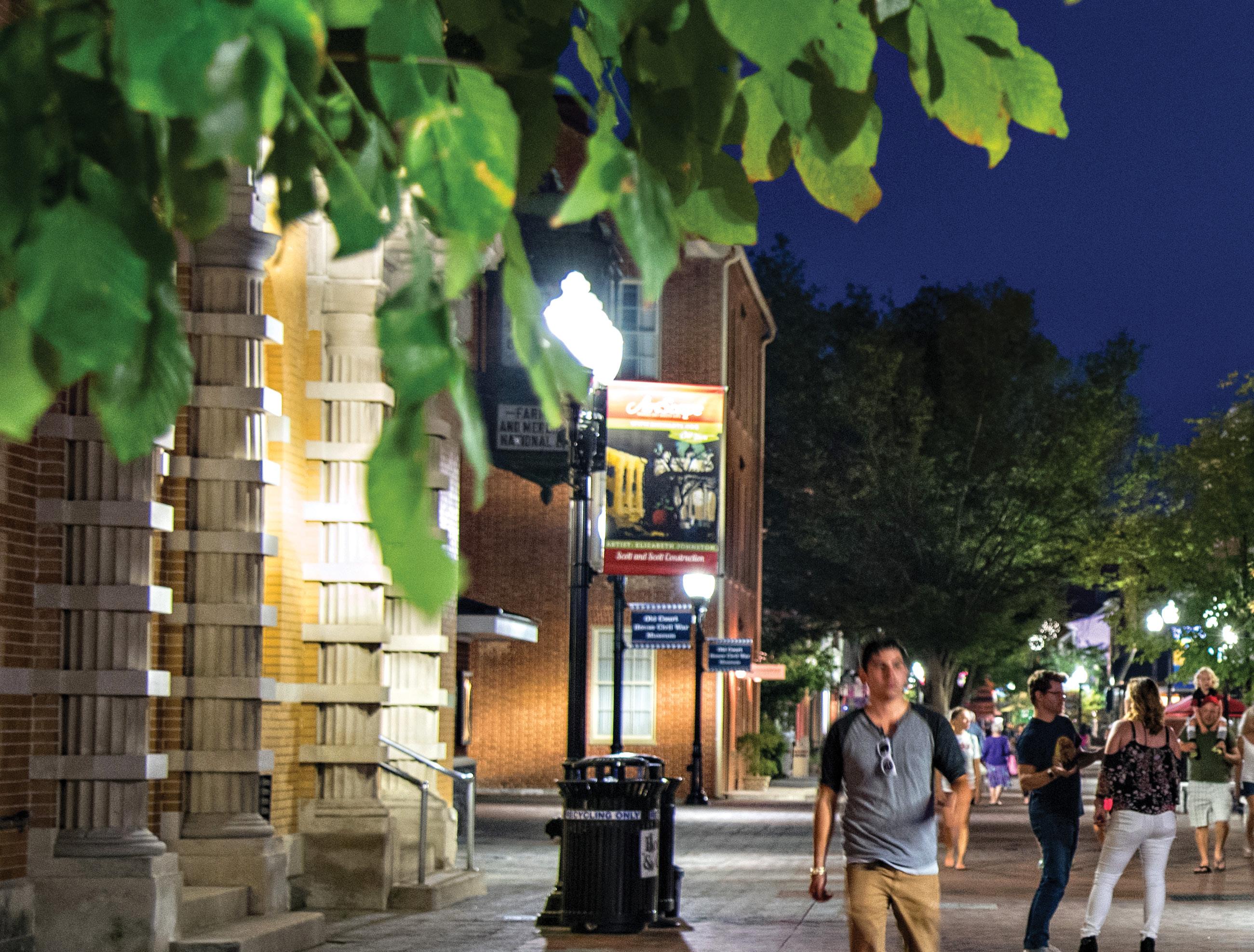
The town of Front Royal in Warren County is the center of an outdoor recreation hotspot that includes Shenandoah National Park, Skyline Drive, Luray Caverns, Skyline Caverns, and the Shenandoah River.
Old Town Winchester has served as a meeting point and commercial center for the Northern Shenandoah Valley for more than 250 years. The district includes a pedestrian mall and numerous restaurants and shops and hosts the Shenandoah Apple Blossom Festival each spring.
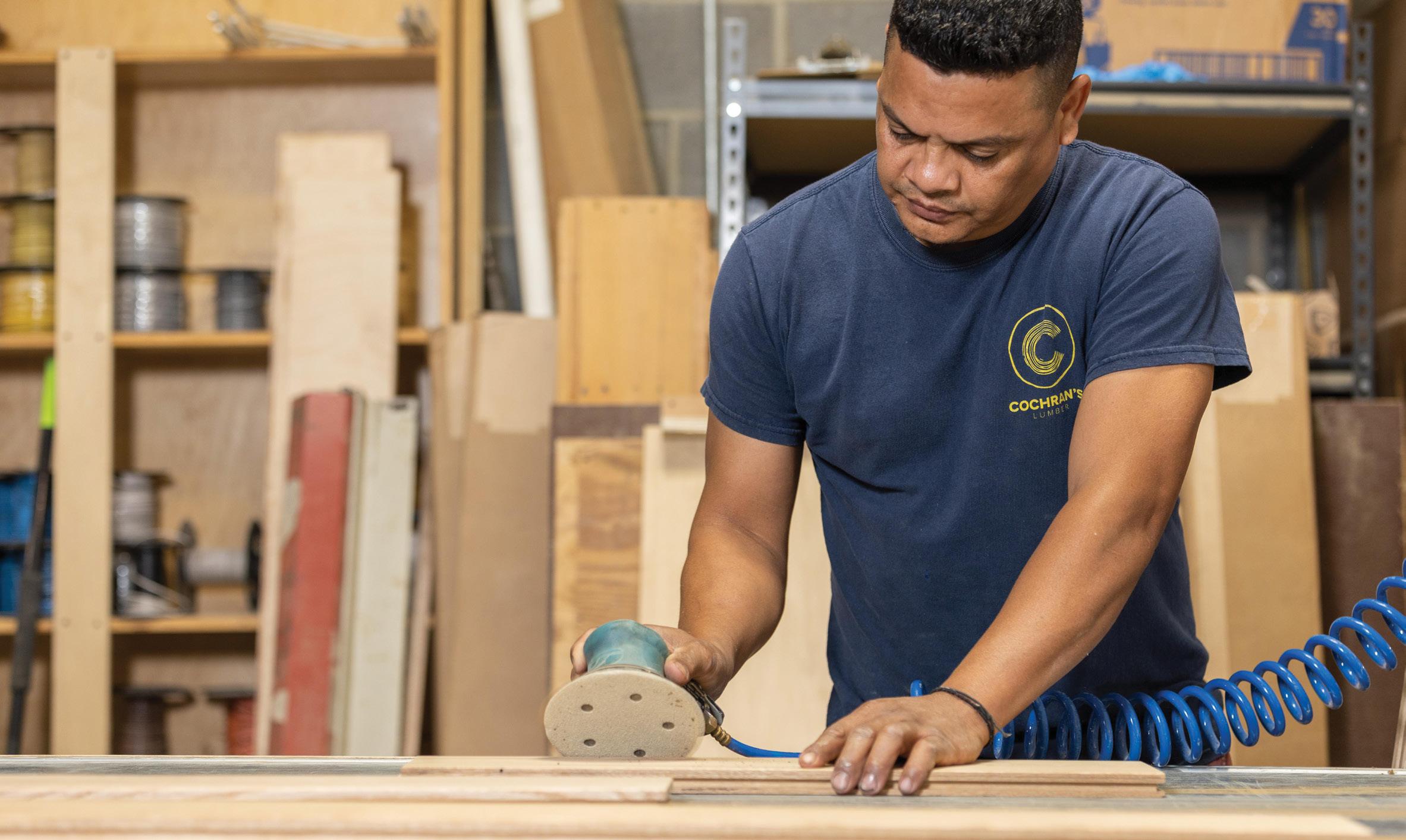
The Northern Shenandoah Valley is home to a thriving wood products industry that includes major companies like American Woodmark and Trex Company, Inc., along with smaller operations like hardwood flooring manufacturer Cochran’s Lumber in Clarke County.
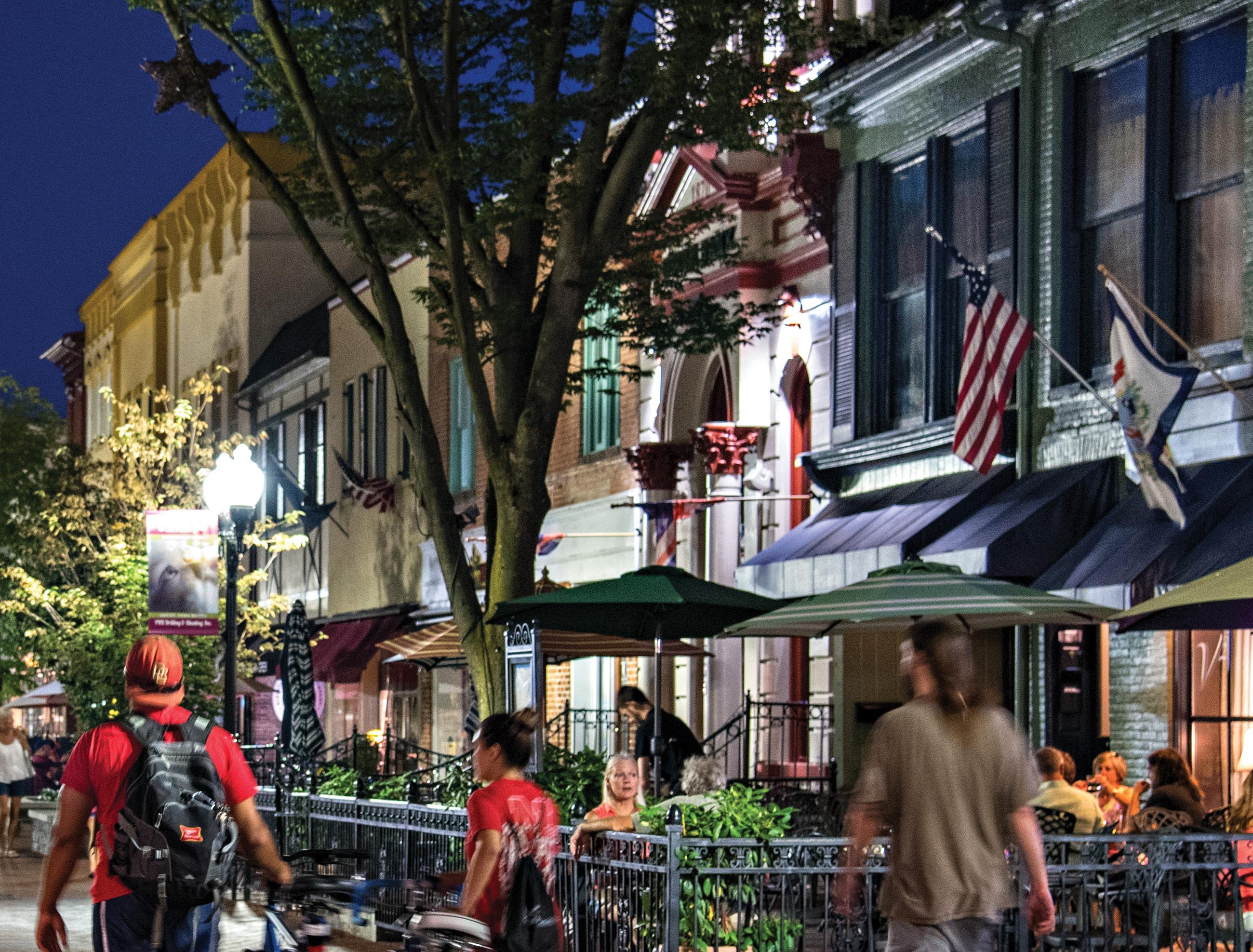
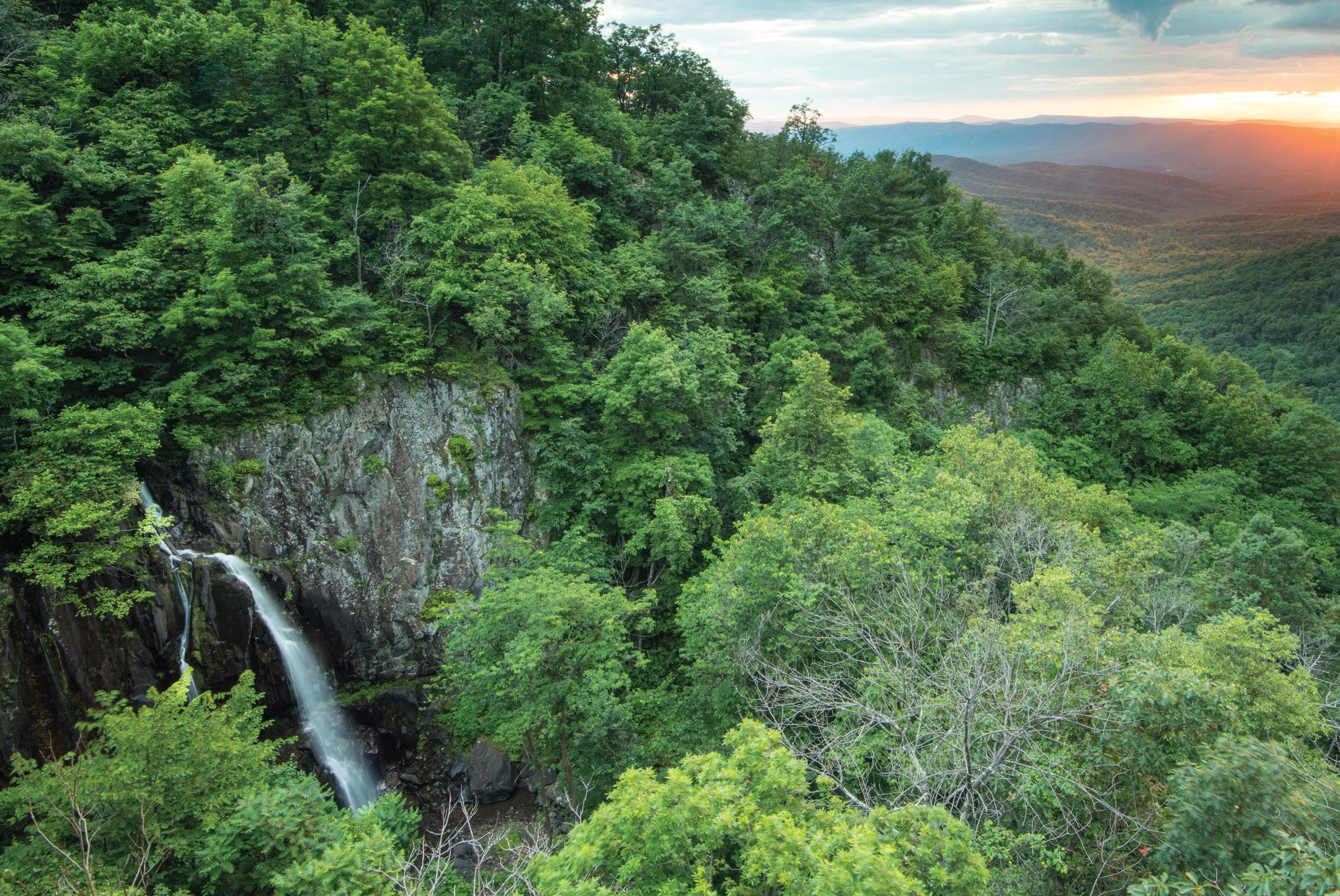
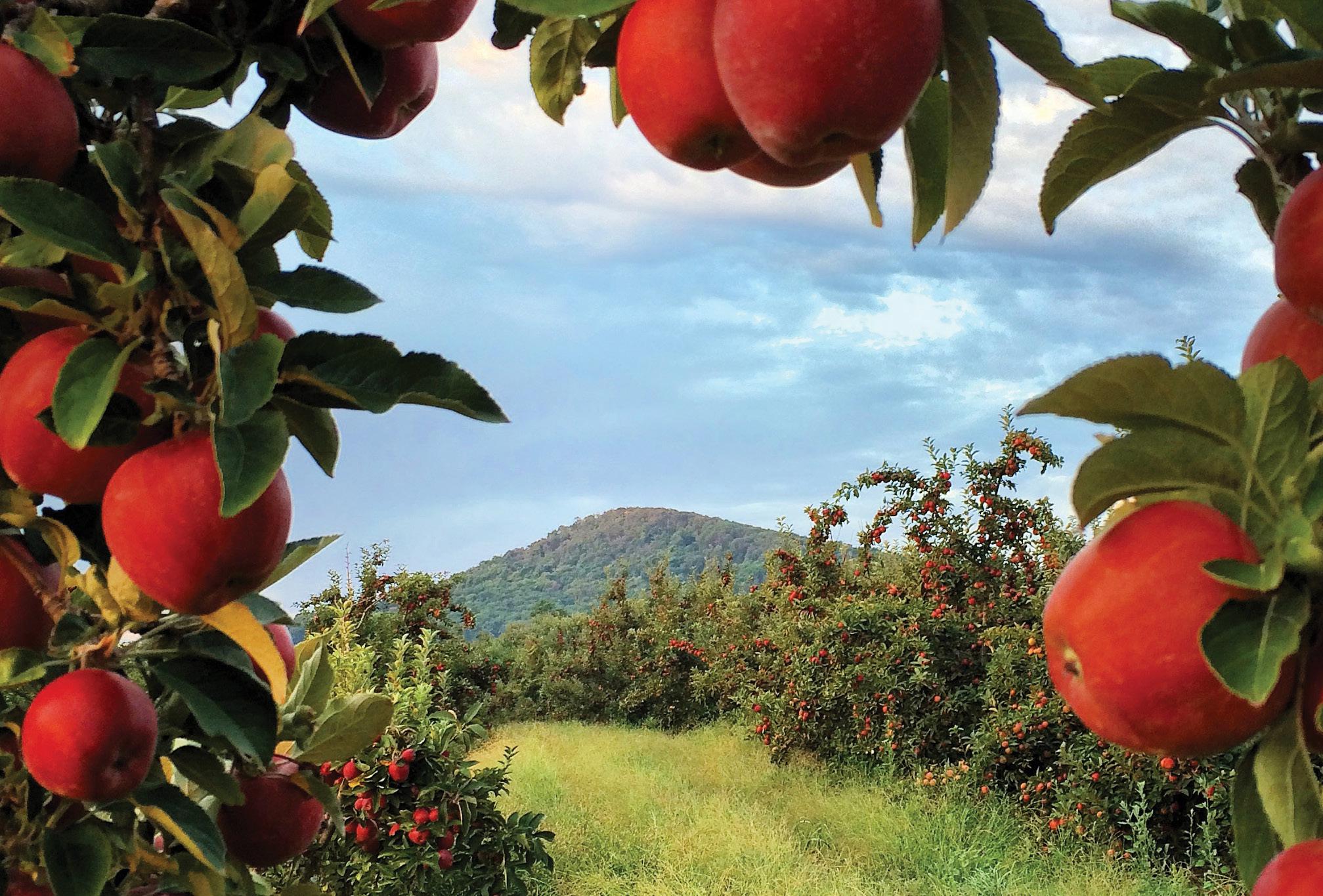
The Northern Shenandoah Valley is known for its abundant apple orchards, with companies like White House Foods and Glaize Apples operating in the region.
Overall Run Falls in Warren County, the highest waterfall in Shenandoah National Park, can be reached via a moderately strenuous hike that takes approximately four hours round-trip.

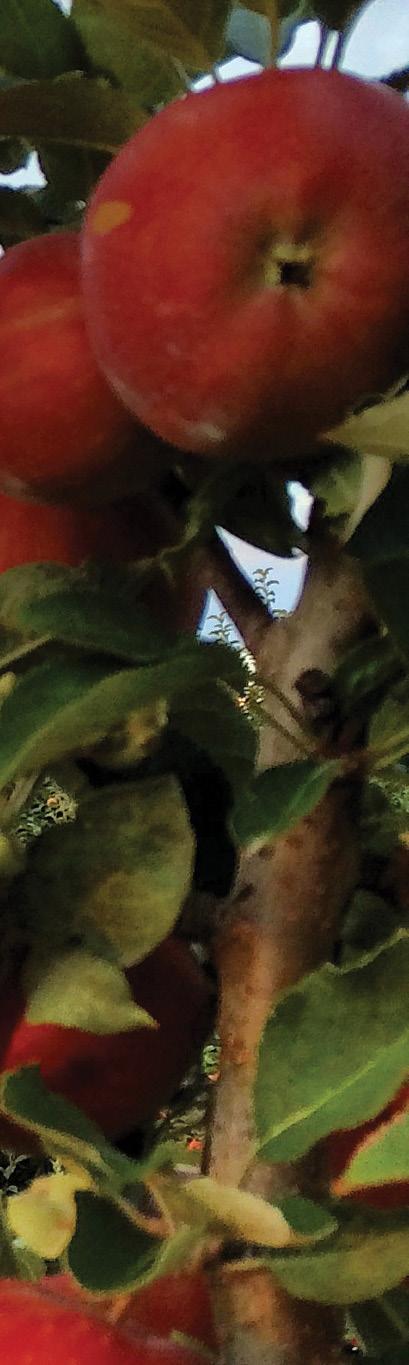
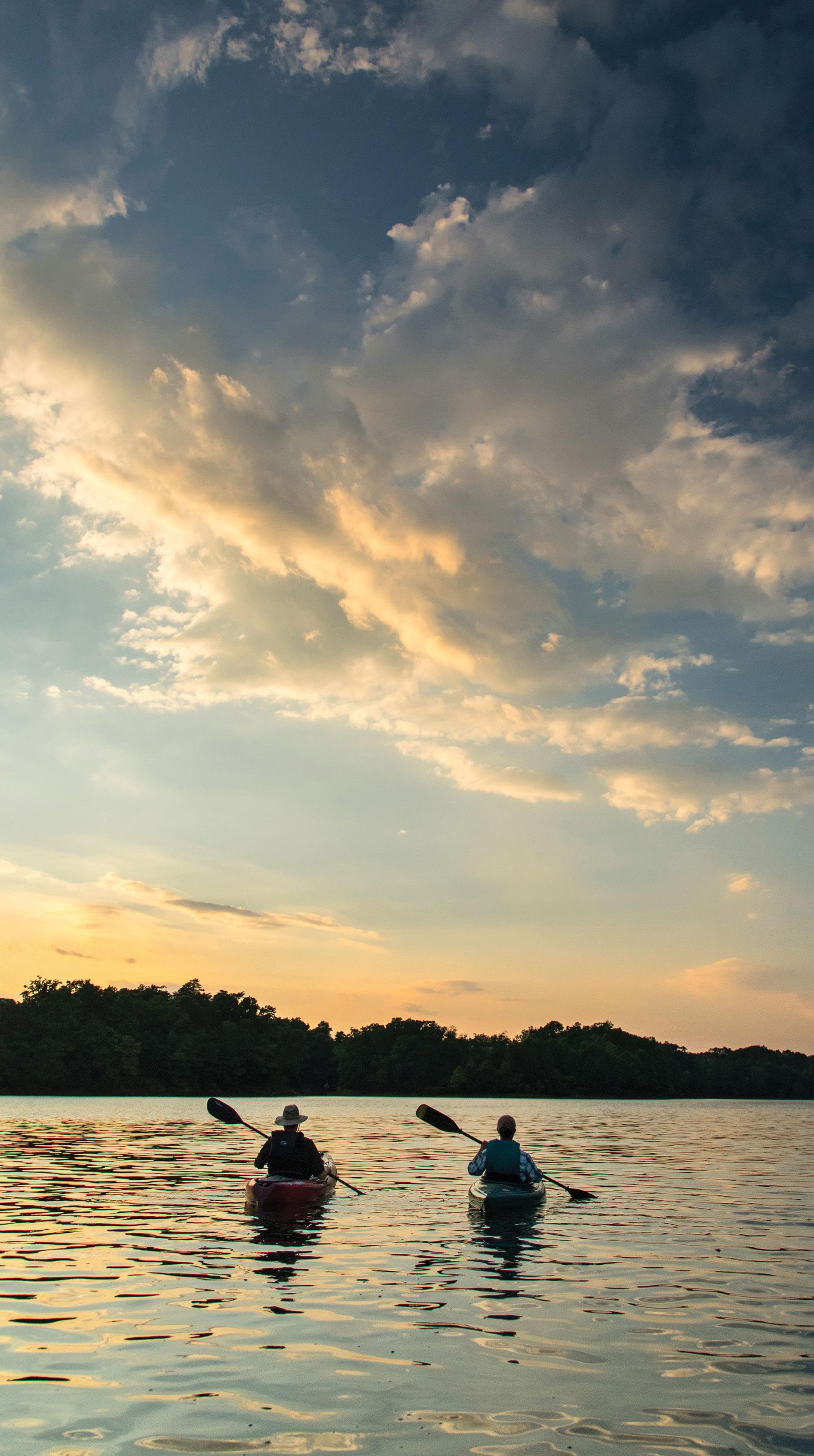
Water recreation areas in the Northern Shenandoah Valley include numerous picturesque lakes and tributaries of the Potomac and Shenandoah rivers. The Cove Campground in Frederick County, shown here, includes three large, spring-fed lakes among its 3,000 acres.
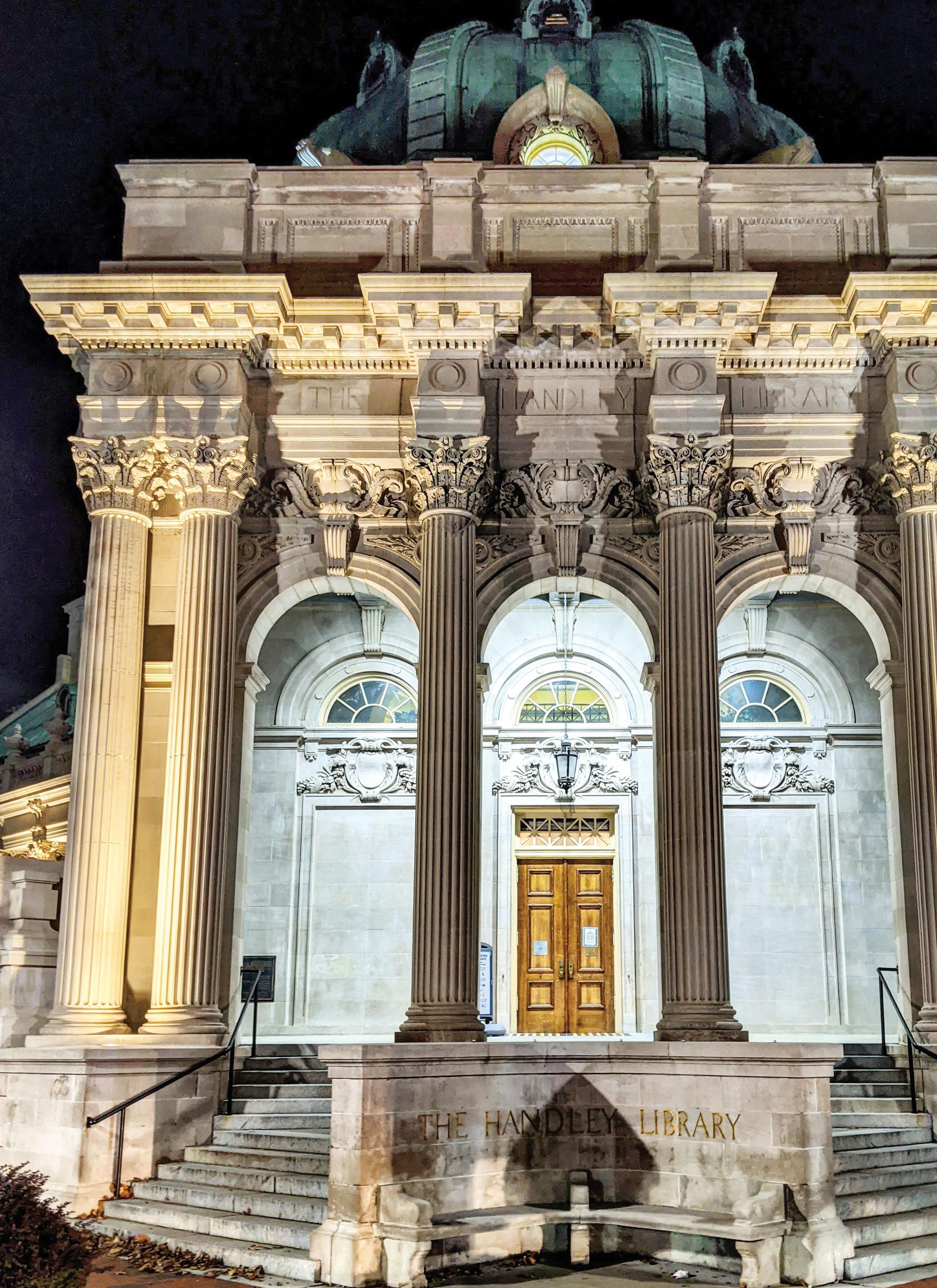
The historic Handley Library in Winchester, designed in Beaux-Arts style to resemble an open book, opened to the public in 1913. Today, the building serves as the main branch for the city’s library system.

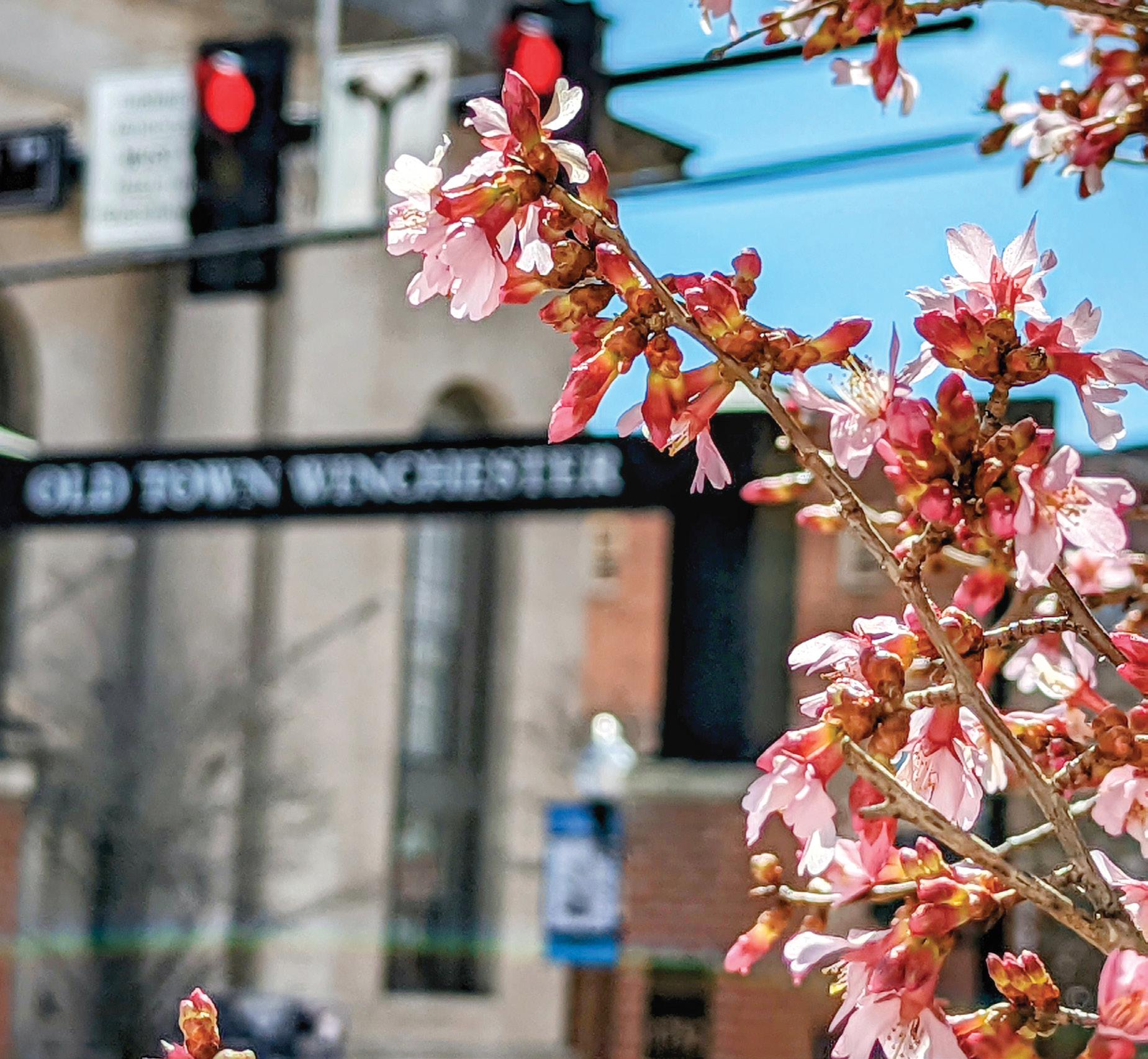
Much like the nearby Washington metropolitan area, the Northern Shenandoah Valley provides some of its best foliage in the spring, like the famous cherry blossoms that draw tourists to the nation’s capital each year.
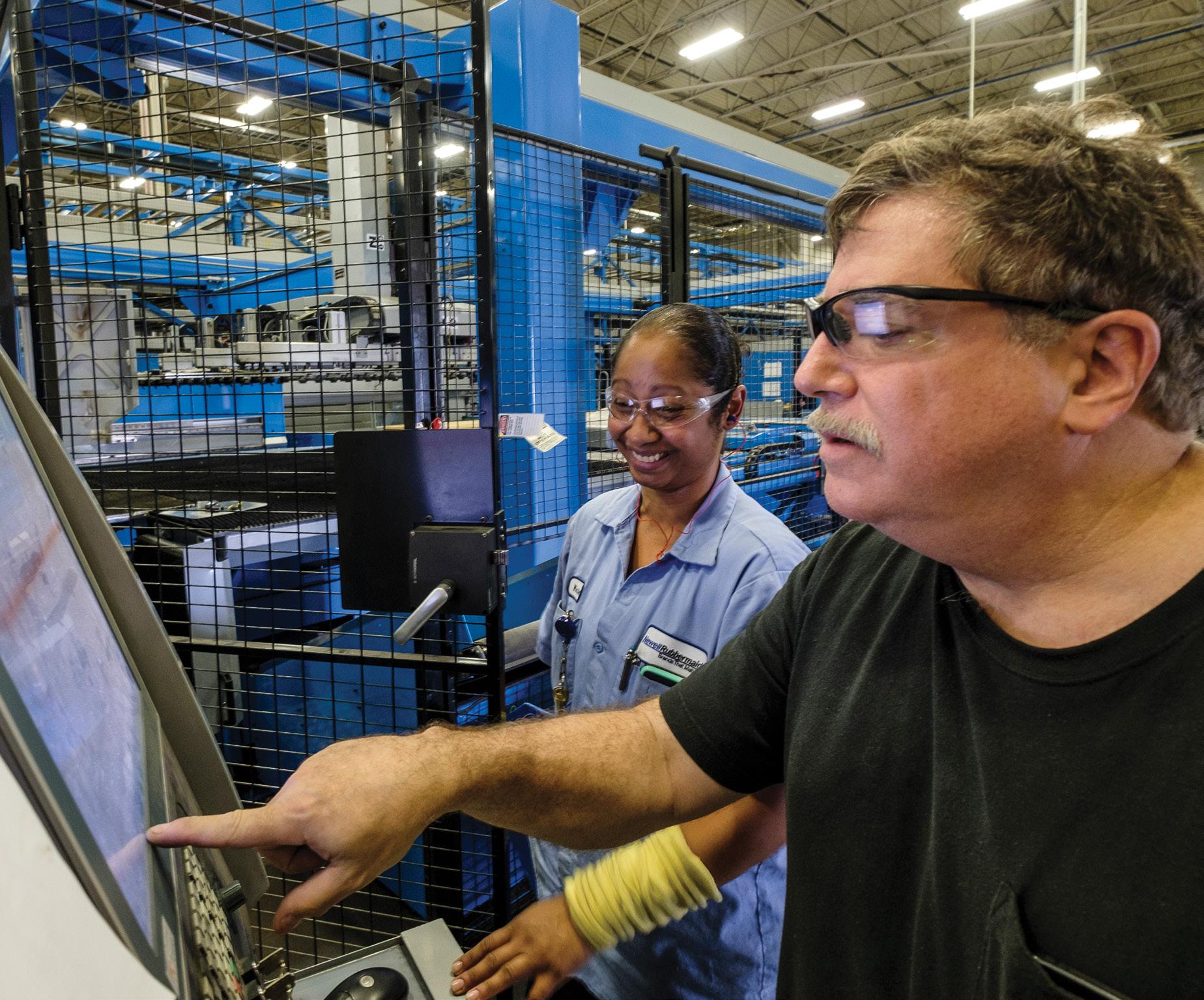
since the company’s founding in 1968.
Rubbermaid Commercial Products has manufactured commercial and institutional products from its Winchester facility
Economic Development Partners in Virginia
VEDP works in close partnership with local and regional economic development organizations. For a full list of local and regional partners, visit www.vedp.org/Regions
In addition, VEDP regularly works with a wide network of statewide partners, including:
State Leadership Partners
Governor
General Assembly
Major Employment and Investment (MEI) Commission
Secretary of Commerce and Trade
Secretary of Finance
Project Delivery Partners Policy and Programmatic Partners
Colleges and universities across the Commonwealth (e.g., UVA, Virginia Tech, William & Mary)
CSX, Norfolk Southern, and short-line railroads
Dominion, AEP, and other electric utilities
The Port of Virginia
Virginia Community College System
Virginia Department of Agriculture and Consumer Services
Virginia Department of Environmental Quality
Virginia Department of Housing and Community Development
Virginia Department of Rail and Public Transit
Virginia Department of Small Business and Supplier Diversity
Virginia Department of Taxation
Virginia Department of Transportation
Virginia Innovation Partnership Corporation
Virginia Tobacco Region Revitalization Commission
Virginia Tourism Corporation
GO Virginia
State Council of Higher Education for Virginia
Virginia Agribusiness Council
Virginia Association of Counties
Virginia Business Council
Virginia Business Higher Education Council
Virginia Cable Telecommunications Association, Virginia Manufacturers Association, Virginia Maritime Association, Virginia Realtors Association, and many other trade associations
Virginia Chamber of Commerce, as well as many local and regional chambers of commerce
Virginia Economic Developers Association
Virginia Farm Bureau
Virginia Municipal League
Virginia Association of Planning District Commissions
Virginia Rural Center
Virginia’s Technology Councils
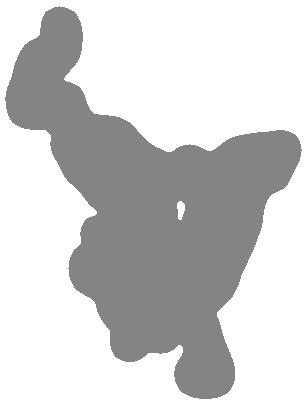
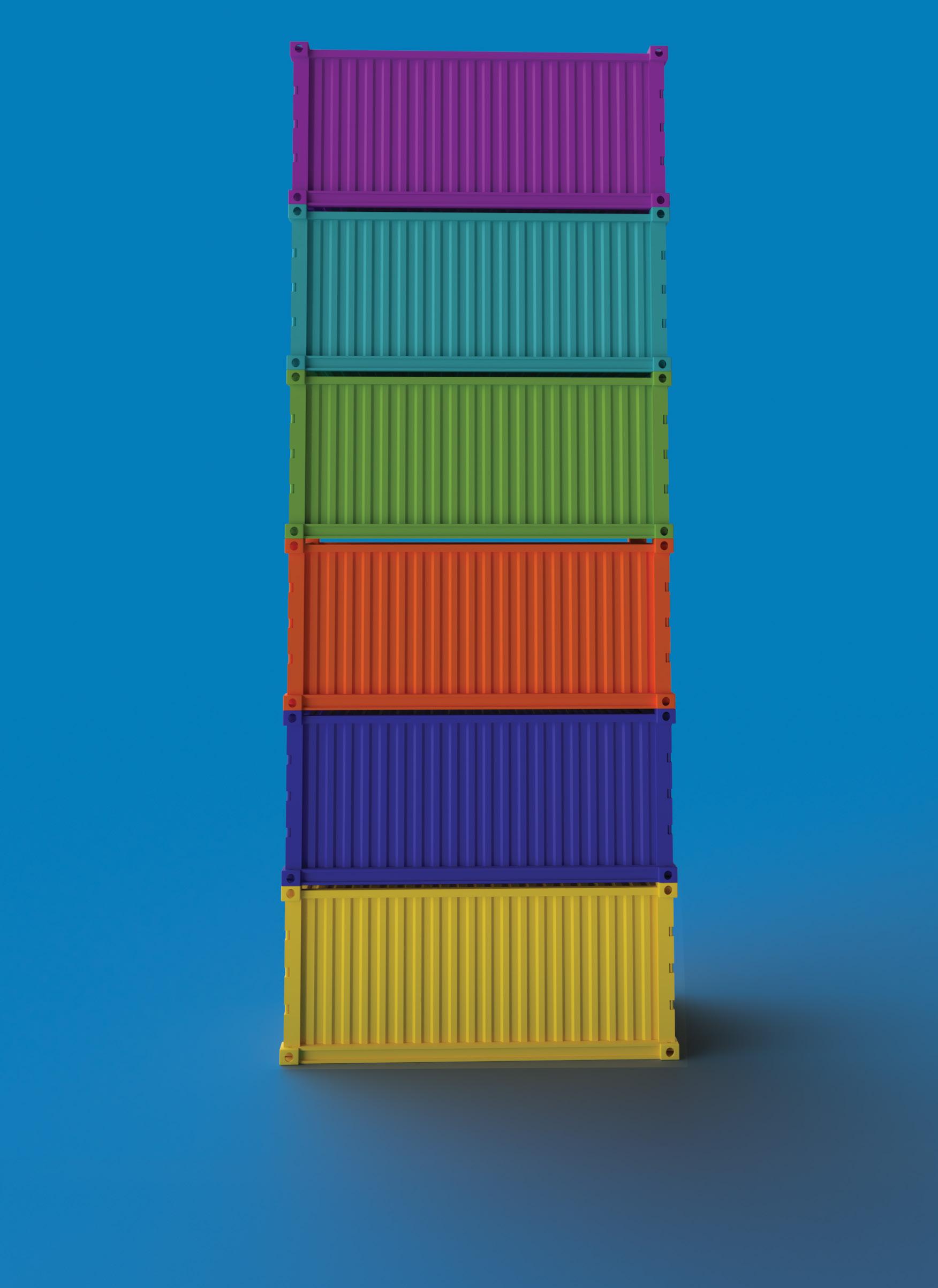
$12.4 billion
$3.9 billion from Washington Metropolitan Area Transit Authority for D.C. Metro system upgrades
$3.7 billion for Hampton Roads Bridge-Tunnel Expansion Project
$2 billion for Transforming Rail in Virginia initiative
$1.4 billion for improvements to Interstate 81 corridor = One great logistics partner for The Port of Virginia facility upgrades
$106 million from Federal Aviation Administration for new concourse at Washington Dulles International Airport