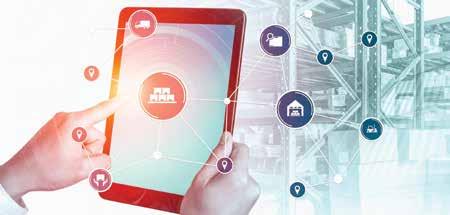
8 minute read
Pharma Consumables Supply Chain Ensuring resilient and reliable in future
Alan S Louie Research Director, Life Sciences IDC Health Insights, USA
Christopher-Paul Milne Director, Research and Research Associate Professor Tufts Center for the Study of Drug Development, US
Advertisement
Douglas Meyer Associate Director, Clinical Drug Supply Biogen, USA
Frank Jaeger Regional Sales Manager, AbbVie, US
Georg C Terstappen Head, Platform Technologies & Science China and PTS Neurosciences TA Portfolio Leader GSK's R&D Centre, Shanghai, China
Kenneth I Kaitin Professor of Medicine and Director Tufts Center for the Study of Drug Development Tufts University School of Medicine, US
Laurence Flint Pediatrician and Independent Consultant Greater New York City
Neil J Campbell Chairman, CEO and Founder Celios Corporation, USA
Phil Kaminsky Professor, Executive Associate Dean, College of Engineering, Ph.D. Northwestern University, Industrial Engineering and the Management Sciences, USA
Rustom Mody Senior Vice President and R&D Head Lupin Ltd., (Biotech Division), India
Sanjoy Ray Director, Scientific Data & Strategy and Chief Scientific Officer, Computer Sciences Merck Sharp & Dohme, US
Stella Stergiopoulos Research Fellow Tufts University School of Medicine, USA
EDITOR
Prasanthi Sadhu Harry Callum
EDITORIAL TEAM
Grace Jones Rohith Nuguri Swetha M
ART DIRECTOR M Abdul Hannan
PRODUCT MANAGER
Jeff Kenney
SENIOR PRODUCT ASSOCIATES
Ben Johnson David Nelson John Milton Peter Thomas Sussane Vincent
PRODUCT ASSOCIATE
Veronica Wilson
CIRCULATION TEAM
Sam Smith
SUBSCRIPTIONS IN-CHARGE
Vijay Kumar Gaddam
HEAD-OPERATIONS
S V Nageswara Rao
Ochre Media Private Limited Media Resource Centre,#9-1-129/1,201, 2nd Floor, Oxford Plaza, S.D Road, Secunderabad - 500003, Telangana, INDIA, Phone: +91 40 4961 4567, Fax: +91 40 4961 4555 Email: info@ochre-media.com
www.pharmafocusasia.com | www.ochre-media.com
© Ochre Media Private Limited. All rights reserved. No part of this publication may be reproduced, stored in a retrieval system or transmitted in any form or by any means, electronic, photocopying or otherwise, without prior permission of the publisher and copyright owner. Whilst every effort has been made to ensure the accuracy of the information in this publication, the publisher accepts no responsibility for errors or omissions. The products and services advertised are not endorsed by or connected with the publisher or its associates. The editorial opinions expressed in this publication are those of individual authors and not necessarily those of the publisher or of its associates. Copies of Pharma Focus Asia can be purchased at the indicated cover prices. For bulk order reprints minimum order required is 500 copies, POA.
Magazine Subscribe LinkedIn
Pharma Consumables Supply Chain
Ensuring resilient and reliable in future
In this article, Ben offers pharma company procurement teams three top tips to finding a trusted consumables supplier to ensure the security and integrity of their supply chain. The author offers advice on questions to ask suppliers, including suppliers of single-use manufacturing equipment, to ensure that they are satisfied that their partners can continue to deliver material when they need it. The author highlights the steps ChargePoint Technology has taken to ensure that they remain a reliable and trusted partner even during these unprecedented times.
Ben Wylie, Senior Product Manager, ChargePoint Technology
How to de-risk the consumables supply chain
For the pharmaceutical industry, managing supply chain risk has never been a higher priority. This is particularly true when it comes to ensuring a reliable supply of consumables - whether ingredients for drug formulation, materials for device and packaging manufacture, or for single-use technology (SUT) for production lines.
The COVID-19 pandemic revealed critical gaps in consumables supply chains and created anxiety as managers scrambled to assure continuity. Learning from the last 24 months is critical if we are to ensure the pharmaceutical supply chain is more resilient and reliable in future.
In this article Ben Wylie, Snr Product Manager at ChargePoint Technology will explore these issues, providing his view on how risk-based approaches to purchasing/specifying consumables relative to product, process and supplier can help de-risk this critical supply chain and help drug programme managers sleep better at night.
Understanding the last 24 months
The pharmaceutical industry has undergone considerable upheaval over the last two years due to the COVID19 pandemic, exposing previously unknown vulnerabilities that need to be addressed.
At the height of the first wave of COVID-19 cases in spring 2020, a number of developments caused disruption in the industry. The closure of factories and export restrictions introduced from countries which produce significant portions of the world’s active pharmaceutical ingredients (APIs) and excipients, caused considerable disruption to drug manufacturers across the globe.
In addition, measures designed to control travel to minimise inter-country transmission, combined with a rapid rise in cases in the global freight sector, posed challenges to companies. They resulted in an interruption of essential transport of ingredients, raw materials, as well as consumable production line equipment across the globe. This led to a significant increase in lead times for the supply of essential consumables that impacted on manufacturing productivity,
leading to delays in the delivery of vital medicines around the world.
Some sectors more affected than others
While the events of 2020 demonstrated weaknesses across pharmaceutical supply chains, they also showed that some segments are more susceptible than others. One such is the highly potent active pharmaceutical ingredient (HPAPI) sector, and not simply because of issues sourcing HPAPIs or their ingredients.
HPAPIs, due to their potent nature, require specialist manufacturing processes and production line equipment. This is vital to minimise the risk of operating staff being exposed to hazardous compounds and to prevent crosscontamination between compounds.
Many HPAPI processing lines make use of SUT transfer components, such as single-use Split Butterfly Valves (SBVs) and chargebags, to ensure optimum containment. These offer particular advantages to manufacturers, as they minimise cleaning and washdown requirements, making it possible to minimise contamination risk while enhancing production line efficiency.
The pandemic showed that to ensure a stable and reliable supply of these single-use components during future economic uncertainty, suppliers and pharmaceutical companies need to have effective contingency plans in place to secure their supply chain.
Sterile processing lines are similarly exposed. Manufacturers need to maintain suitable cleanroom environments when processing sterile products, such as parenteral drugs, while also maximising line productivity. To achieve this, many make use of specialist aseptic SBVs and other SUTs due to their combination of optimum aseptic integrity and reduced cleaning and validation requirements.
As with HPAPIs, it is imperative that they are able to source their equipment from reliable suppliers with their own robust supply chains to safeguard against any unforeseen disruption to international trade.
Lessons for the future
While there seems to be light at the end of the tunnel with regards to COVID19, the related economic uncertainty continues, with implications for the pharmaceutical supply chain. As more countries open up, we are seeing demand outstripping supply in the pharmaceutical sector and in other industries, leading to rising prices and extended lead times on new orders of consumables of all stripes. Conflicts are also leading to a rise in energy and commodity prices, which may well have a knock-on effect for manufacturing productivity within the pharmaceutical industry, as well as on global supply chains.
It is no surprise then that many companies across the pharmaceutical industry have taken steps to rethink their consumables supply chains. Not just consumables suppliers, but drug developers and contract development and manufacturing organisations (CDMOs) are exploring how to de-risk in order to further enhance the reliability and quality of the support they provide their customers in the future.
The work of SUT manufacturers to mitigate against supply issues during the first wave of COVID-19 offers a number of important lessons for the rest of the industry as it looks to build a more resilient consumables supply chain capable of handling ongoing uncertainty.
The steps to enhancing the robustness of their consumables supply:
Identify vulnerabilities
A standard pre-COVID-19 supply chain features a number of weak points that can act as a single point of failure. The industry’s reliance on a single global region for much of its API supply, for example, made it vulnerable when factories in that part of the world paused operations due to COVID lockdowns. This is one reason why some national governments have tried to encourage companies to onshore their supplies.
As discussed earlier, a heavy reliance on JIT delivery for many commodities also posed an issue when transport networks were disrupted.
Relying on a single company for an essential supply is also a potential liability highlighted during pandemic. If the company fails and ceases operations, then that can cause considerable delays.
To build a more resilient supply chain in the future, it is important for companies to identify such single points of failure in their own operations, as well as the risk of failure, so they can take steps to address them.
Stock up on essentials
As shown by the experience of many SUT manufacturers, having a ready supply of raw materials or essential components can help mitigate the impact of any delays in new deliveries, enabling them to continue manufacturing and supply customers.
With this in mind, it is recommended to take steps to build an inventory of any essential ingredients or consumable equipment, and explore ways of expanding Where companies are supplying markets overseas, it may be advisable to explore ways of building stocks of finished goods within those markets to ensure they can deliver even when there are international shipping delays.
Diversifying networks
Seeking more than one supplier for essential goods, and working with partners from across the globe can help address the single points of failure identified during the first step. Working with only local partners is not an option for some essential materials or SUTs, as they may not be produced domestically. Nor is it always desirable — it is possible a local market may experience supply shortages.
Creating a global network can ensure access to all of the high-quality consumables as and when they are