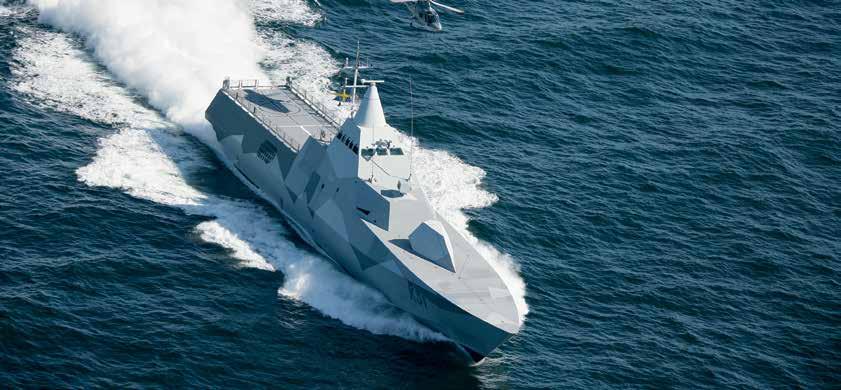
10 minute read
Dubai Airshow
Saab Kockums' Visby corvette is a flexible surface combatant, designed for a wide range of roles, in line with the current multi-mission ship-type design trend
NAVAL DESIGN SWAP
Advertisement
Naval ship design has significantly changed to reflect influencing factors such as lifecycle costs, modularity and energy efficiency.
By Alix Valenti
Over the past couple of decades, technological developments and breakthroughs have been redefining navies’ concepts of operations at a surprising speed. From weapon systems to threat detection and ever-expanding Intelligence, Surveillance and Reconnaissance (ISR), navies have been adapting ship design in a constant bid to keep ahead of the competition.
The more recent return of near-peer competition has further exacerbated this trend, “setting completely new and imperative demands,” Lars Brännström, deputy head and chief marketing officer, Saab’s Business Area Kockums, told Armada International. It brings “new threat vectors, such as unmanned systems above or below water with new weapons that travel faster, while older forms of naval warfare such as mine warfare or the application of electronic warfare (EW) are gaining prominence.”
These trends have had a significant impact on ship design. Constrained by their budgets, navies have been seeking increasingly multi-mission capable ships. These allow for a wide range of missions, but also for more room to accommodate new and emergent technologies, equipment and systems. “This requires very careful provisions of margins for weight, space, power and information to be made” in a bid to contain lifecycle costs without limiting future developments, said Ian Cowper, engineering director Warships at Babcock.
MODULARITY AND LIFECYCLE COSTS
“The need for multi-role capability has largely been driven by the lower number of vessels that each navy can field over recent decades,” Cowper noted. Faced with restricted budgets yet called upon to carry out ever-more complex missions – facing both symmetric and asymmetric threats – the trend has been to acquire ships developed around the concept of mission modularity. These ships feature reconfigurable mission bays housing specific capabilities according to each mission.
However, if modularity has emerged as the solution of choice in such complex geopolitical environments, the reality has revealed that finding the right balance between missions is difficult and will inevitably result in compromise. “The wider consequences of modularity are often neglected or at least underestimated,” Simon Jones, chief naval architect (Ship Delivery) for Defence and Security at BMT, told AI. In particular, requirements for storage, maintenance, personnel training, transportation
BMT’s design for the Royal Norwegian Navy HNoMS Maud Logistics and Support Vessel (LSV), seen here conducting a resupply at sea.
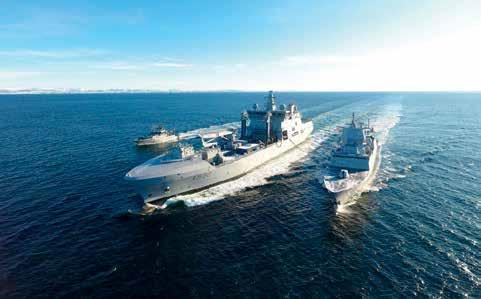
and installation of the modules need to be carefully considered.
The increasing pace of technological developments in the naval domain is also progressively revealing the limits of modularity. Not all technological advances can be turned into modules; some require that ships be designed “to allow upgrade through life as new technologies mature,” Jones added. The introduction of commercial design standards as a viable and cost-effective alternative to some military design standards is further exacerbating this trend. “The balance between the military and commercial aspects will vary depending on the roles that the vessel is intended to carry out,” Cowper explained, “but in essence the aim is to ensure the best possible compromise between the capability required and the budget available.”
Finding the right compromises has meant that an ongoing discussion about ship lifecycle costs between navies and ship designers has now become essential from the start.
Broadly speaking, lifecycle costs include energy efficiency to determine how much fuel the ship will need to operate, personnel needed or available to man the ship, and maintenance throughout the 30 or so years of the ship’s life. In order to restrain a ship’s lifecycle costs, navies and ship designers need to determine how to accommodate future technologies without major alterations to the ship. Doing so requires “margins in the design in terms of Space, Weight, Power and Cooling (SWAP-C), along with flexible infrastructure and open architecture to easily interface any new system that comes along” Jones said. BMT’s design for the Royal Norwegian Navy HNoMS Maud Logistics and Support Vessel (LSV) offers multi-mission capabilities using a mix of mission containers, built-in functions, re-rolable compartments. “We call this ‘in the box’ and ‘out of the box’ modularity, said Jones.
ENERGY EFFICIENCY
The discussion over energy consumption and storage has significantly evolved over the past couple of decades as a result of a number of factors.
First, energy consumption will determine the lifecycle cost of a given ship in terms of fuel expenditure. The more a ship has been designed to optimise energy consumption, the less expensive it will be to operate over its lifespan. There are several ways in which this can be addressed, chiefly amongst which is “in-depth hydrodynamic analysis followed by meticulous model tests to gain maximum efficiency,” stated Shiran Purvin, vice president engineering at Israel Shipyards.
Hull lines have been the centre of attention in this debate from the beginnings of ship design, but increasingly discussions over appendages capable of improving hydrodynamics are taking place. For example, Hull Vane, a company based in the Netherlands, offers the Hull Vane, a partial hydrofoil designed to reduce a displacement or semi-displacement vessel’s resistance. Seeking to reduce resistance and pitching, suppress stern wave, and trim correction, the Hull Vane greatly contributes to reducing fuel consumption. “A side, yet crucial, effect for navies is the fact that a reduced stern wave also greatly reduces noise levels,” Bruno Bouckaert, Hull Vane sales director, told AI. “Reduced resistance has a similar side-effect, because the ship’s engine does not have to work as hard to power the vessel.”
The discussion over energy consumption has also been driven by an increasing trend for navies to comply with commercial standards of cardon dioxide (CO2) emissions reductions. “There are an increasing number of maritime zones in the world today that have become zero carbon areas,” Hervé Boy, business development senior manager at Naval Group revealed. “If ships don’t comply, they will not be able to transit.”
As such, propulsion will shift to completely electric or hybrid architectures, according to Luca Mattei, vice president design and engineering Fincantieri Naval Vessels. Diesel electric has already established itself as a significant trend over the past decades. Yet, as the commercial sector, driven by International Maritime Organisation (IMO) standards, continues to explore new, greener fuels, the naval domain may begin looking in that direction as well, according to Purvin.
However, storage remains a significant challenge to overcome when talking about energy efficiency and greener fuels. “Energy density can be a challenge,” said Jones, especially when looking at hydrogen or batteries, both of which are gaining traction in the maritime sector but require large volumes for installation, and may present additional hazards when used in a naval environment. Electrical power, whether for hybrid or fully electrical, may also raise storage issues, especially as ships are dependent on electricity for their increasing number of sensors onboard and future weapons – such as lasers or electromagnetic guns – according to Boy and Mattei.
“Ultimately, to be able to find the right mix of energy efficiency or new technology to make the ship greener, it is essential to have a full understanding of the concept of operations and assess the trade offs between procurement and through-life costs. Building in adaptability to accept new energy saving technologies or greener fuels as future upgrades will make the vessel more future proof” Jones concluded.
REDUCED MANNING
Over the past decade, a couple of key factors have contributed to a growing number of ships being designed for reduced manning. The primary reason has been the decreasing number of recruits in most Western navies, combined with difficulties in retaining trained personnel. Secondly, and just as importantly, the cost of personnel is a significant part of the lifecycle costs.
To attract and retain personnel, navies have been moving toward ship designs that provide better living conditions. “Crew are at sea for days, weeks, sometimes months at a time,” Purvin told Armada, “so spacious rooms, improved mess areas, recreational spaces and seakeeping, have become crucial.” Israel Shipyards’ latest ship design,
Hull Vane
The Hull Vane, a partial hydrofoil designed to reduce a displacement or semi-displacement vessel’s resistance, seeks to reduce resistance and pitching, suppress stern wave, and trim correction

the OPV-45 multipurpose vessel, included these capabilities. Hull Vane’s Bouckaert noted that one of the important ‘side-effects’ of the Hull Vane technology, and in particular of the Dynamic Hull Vane, is the reduction in pitch motions. “If you reduce this motion, the ship is more stable, even in high sea states, thus improving crew comfort, and the performance of equipment such as radars, weapons systems, sonars,” Bouckaert added.
Concurrently, the lifecycle cost of maintaining trained and skilled personnel has also led to increased automation. “Automation technologies are evolving to help with this challenge partly due to the rapid development of digital remote controlled and autonomous systems,” Jones noted. Furthermore, autonomous systems have the potential to keep crew out of harm’s way, whether for mine countermeasure or ISR missions, but they also provide significant tactical benefits. “Off-board systems in the air, on the surface and underwater can act as force-multipliers for the limited number of ships available and ensure that the sphere of influence of each ship can be increased, offsetting the reduced number of ships,” added Cowper.
Yet, the integration of autonomous systems into ships comes with its own challenges. For instance, space is key and while increased deck space has been the main answer for unmanned aerial vehicles (UAVs) and, to some extent, unmanned underwater vehicles (UUV), it can prove much more complex for unmanned surface vehicles (USV). USVs have become larger over the years, with a number of them designed to deploy UUVs – particularly for mine countermeasure missions – so accommodating them onboard might significantly alter the size of the mothership.
Launch and recovery of unmanned systems, especially USVs, has also proven to be a significant challenge for mothership design. Typically, USVs can be launched when the ship is moving, and can operate at high speed. “There are a number of variables at play that need to be carefully accounted for when designing USV launch and recovery systems,” Jones noted. “From the perspective of the USV – how it finds its way and docks itself in different sea states and weather conditions, how it is affected by the wake of the mothership, and for the motherships, how does the USV and its launch and recovery equipment interface with the ship.” BMT was involved with a Joint Industry Project (JIP) called LAURA for the launch and recovery system for any small navy crafts. Incidentally, Bouckaert noted that the reduction of the wake and the stabilisation of the ship by the Hull Vane can also greatly contribute to addressing some of these challenges.
SMARTER MAINTENANCE
Maintenance costs greatly contribute to increased lifecycle costs. The introduction, over the past decade, of predictive maintenance has made a significant difference in this regard, with onboard sensors collecting data for tools such as digital twins.
Cowper noted that at Babcock, “a digitally enabled In-Service Support Solution is now at the heart of our developments, targeting ship system outputs to provide a data driven understanding of reliability and availability.” This is powered by digital twin technology, a development that has also been at the heart of Naval Group’s maintenance tools.
But this technology also has its impact on ship design, as noted by Boy: “Navies are increasingly looking at gathering as much data as possible to improve the performance of their ships over their lifecycle, and this has meant that at Naval Group we have designed ships with onboard data centres.” It is not just the physical size of the data centres that has been made flexible to continue evolving in tandem with growing data needs; their software architecture has also been designed to accommodate upgrades throughout the ships’ lifecycle. This is the case for the French Navy’s defence and intervention frigates (FDI) for instance.
The introduction of additive manufacturing – more commonly known as 3D printing – is also significantly modifying maintenance costs, particularly in terms of logistics. In February 2021, Naval Group
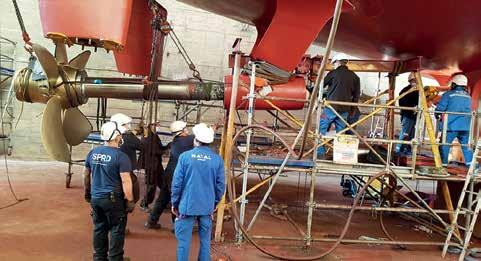