

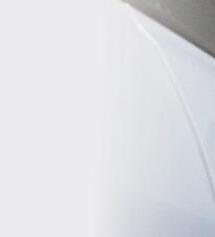
Power sharing & smart load management: Save yourself the significant cost and long wait times of a service upgrade
Simplified and automated billing
No Wi-Fi required
Compatible with any EV charging station
Remote control (mobile application)
Made in Canada
EDITOR
Wayne Karl wayne.karl@nexthome.ca
EXECUTIVE MEDIA CONSULTANTS
Jacky Hill
Michael Rosset
SENIOR VP, SALES NEXTHOME Hope McLarnon 416.708.7987 hope.mclarnon@nexthome.ca
DIRECTOR OF SALES, ONTARIO, NEXTHOME Natalie Chin 416.881.4288, natalie.chin@nexthome.ca
SENIOR MEDIA CONSULTANTS Amanda Bell 1.866.532.2588, amanda.bell@nexthome.ca
Merlyn Minty 204.782.8692 merlyn.minty@nexthome.ca
CEO Kevin Lee DIRECTOR, MARKETING AND COMMUNICATIONS
Natasha Rombough
MANAGER CUSTOMER SALES/SERVICE
Marilyn Watling
SALES & MARKETING COORDINATOR Gary Chilvers
POLICY AND COMMUNICATIONS ANALYST
Emily Fielden
HOME SHOW MANAGER & NEWSPAPER CIRCULATION – GTA Josh Rosset DISTRIBUTION distributionteam@nexthome.ca
ACCOUNTING INQUIRIES accountingteam@nexthome.ca
VP MARKETING — GTA
Leanne Speers
DIRECTOR OF PRINT MEDIA Lauren Reid–Sachs VP PRODUCTION — GTA Lisa Kelly
PRODUCTION MANAGER — GTA Yvonne Poon
GRAPHIC DESIGNER & PRE-PRESS COORDINATOR Hannah Yarkony
COMMUNICATION STRATEGIST
Chloe Perreault
Published 4 times a year by NextHome, on behalf of the Canadian Home Builders’ Association (CHBA), all rights reserved. No part of this publication may be reproduced in any form without written permission. Building Excellence, NextHome, and the Canadian Home Builders’ Association (CHBA) are not responsible for any claims or promises in any advertisement, nor for any unsolicited material sent to the magazine. Canadian Publications Mail Agreement # 40065416
Published by
nexthome.ca
Advertising Call 1.866.532.2588 ext. 1 for rates and information. Fax: 1.888.861.5038
Copyright 2024 All rights reserved. All copyright and other intellectual property rights in the contents hereof are the property of NextHome, and not that of the individual client. The customer has purchased the right of reproduction in NextHome and does not have the right to reproduce the ad or photo in any other place or publication without the previous written consent of NextHome.
Terms and Indemnification Advertisers and contributors: NextHome is not responsible for typographical errors, mistakes, or misprints. By approving your content and/or submitting content for circulation, advertisers and contributors agree to indemnify and hold harmless NextHome and its parent company from any claims, liabilities, losses, and expenses (including legal fees) arising out of or in connection with the content provided, including but not limited to any claims of copyright infringement, unauthorized reproduction, or inaccuracies in the content. Advertisers acknowledge that they have the necessary rights, permissions, and licenses to provide the content for circulation, and they bear full responsibility for the content’s accuracy, legality, and compliance with applicable laws upon approval. Contributors acknowledge NextHome reserves the right to omit and modify their submissions at the publisher’s discretion.
BY MATT MCCURRACH, CHBA PRESIDENT
As the year quickly comes to a close, I’m wrapping up a productive few months of travel. From Penticton to St. John’s, I’m humbled to have had the opportunity to engage with members in important dialogue about your pressing issues and celebrating in your success.
This fall, I made 12 stops at meetings and conferences held by HBAs across the country, including provincial events put on by OHBA, BILD Alberta and CHBA British Columbia, and local events at Simcoe County HBA, CHBA Sea to Sky, and Regina Region HBA, among others. I heard directly from members about how government red tape (at all levels), economic challenges, labour shortages, and supply chain issues continue to hold back the home building process and stifle housing supply. While there are some regional differences, I’m always intrigued to hear that many of the issues we face are the same. And whether it be big or small, I’m captivated by your creative ideas for solutions.
Of course, I always take your on-theground experiences and insights back to our national Association to help inform the next steps of our advocacy efforts.
Most recently, back in October I attended CHBA’s Fall Meetings in Ottawa and shared what I learned on my travels with our national leadership. I was impressed by the collaborative information sharing between members and Executive Officers (EOs), all working towards our common goals. The meetings are an excellent opportunity to hear from the members who sit on CHBA’s National Committees and Councils, who offered some invaluable insights into how they’re navigating a challenging building environment. These leaders spend countless hours giving back to the Association, whether that be through extensive codes meetings, charity work or government advocacy.
I’d like to take this opportunity to thank them, along with all members who dedicate their time to your Association, for their ongoing work. The consistent progress that we’re making in our advocacy work – trying to improve a tough situation in the industry for many right now – is because of members who lend their time and expertise to support the industry as a whole, with the support of our local, provincial and national EOs and staff. We are stronger together, and that mindset is what has helped CHBA thrive for so many years.
As 2024 winds down, we are preparing to celebrate the achievements of our industry this past year. By the time this issue is published, the entry period for the CHBA National Awards for Housing Excellence will be concluding. I hope you took the opportunity to enter this prestigious competition that celebrates the best in Canadian new homes, renovations, community development and residential marketing.
Through the CHBA Association Leadership Awards, we’re celebrating the outstanding work of dedicated volunteer members, as well as the leadership shown by our local and provincial HBAs and their EOs. HBAs and members work hard all year not only to strengthen our Association at all three levels, but also to give back to Canada’s cities, towns and neighbourhoods, and these awards recognize those who are putting in exemplary efforts. The winners will be announced at next year’s CHBA Home Building Week in Victoria, BC – I hope to see you there.
If I’ve learned anything from my time serving in various roles at the Association, it’s that making your voice heard pays off. Hearing your stories has been instrumental in helping the Association, at all levels, secure monumental policy changes on behalf of our sector over the last few years.
So, let’s all encourage more members to get involved. If you’re not currently involved with your local or provincial HBA, I challenge you to find out how you can contribute. Joining a committee or council or attending meetings gets you the most out of your membership. It’s where you’ll learn new insights to help your business, help inform government policy and make valuable business connections, all while doing the work we all care about.
And if you see a younger person who has the makings of a future leader within the association, encourage them to get involved as well. We all know someone who gave us the confidence to push for bigger things – you can be that person for the next generation.
May 11-15, 2025 | Victoria, BC
MAINTAINING PRESSURE ON GOVERNMENTS FOR HOLISTIC CHANGE TO HOMEBUILDING POLICY
BY KEVIN LEE, CHBA CEO
Moreover, homeowners looking to add an accessory dwelling unit (ADU) to their home can now refinance their current mortgage to help construct a secondary suite. Borrowers can access up to 90 per cent of the home’s value, including the value of the extra suite, and amortize the refinanced mortgage over a period of 30 years. To support this, the federal government also increased the mortgage insurance home price limit to $2 million for those refinancing to build a secondary suite.
Over the last couple months, our advocacy feet have been firmly on the gas, and it’s paying off in droves.
In late September, the federal government introduced several measures to support the residential construction sector.
Most notably, the federal government expanded CHBA’s ask on 30-year amortizations for insured mortgages – which was secured for first-time buyers on new construction homes back in April – to include all buyers of new construction homes, and all first-time buyers on any home, new or resale.
To complement this new measure, the federal government also fulfilled another CHBA recommendation by upping the cap on insured mortgages from $1 million to $1.5 million to better reflect the reality of today’s home prices. This will enable homebuyers to qualify for mortgages in Canada’s most expensive markets.
These are huge wins for CHBA members. Better access to mortgages will drive more sales and housing starts and give the industry a chance to build the homes Canada needs to close the supply gap.
CHBA has long called for measures to allow for gentle density, including adding secondary suites or other types of ADUs like laneway homes. This will go a long way to assist homeowners who are looking to achieve that. However, it will be important that more municipalities get on board with zoning and by-law reform to allow for gentle density, a topic that CHBA is consistently engaged on.
While lower interest rates and other policy steps have been taken by the federal government, many of our members’ challenges persist. CHBA’s Q3 Housing Market Index (HMI) revealed that builders are expecting weak sales with fewer starts moving forward. For the ninth consecutive quarter, both the singleand multi-family HMI showed very negative homebuilder sentiment, and respondents citing issues with access to labour, materials shortages and more.
We know that the housing supply and affordability crisis won’t be fixed overnight. This quarter’s low HMI scores indicate that we can’t stop putting pressure on governments for holistic, housing-supportive policy change.
Bold and decisive action is needed, including at the provincial and municipal
levels, to turn the market around and significantly increase housing starts to address our country’s affordability challenges. That’s why CHBA has been proactive in advocating for change with all federal parties.
CHBA continues to push the current government to use its levers to effect change, and we are also diligently engaging with the Office of the Leader of the Opposition (OLO) regularly to ensure the needs of our industry are top-of-mind in the event of an election.
To indicate CHBA’s impact with the OLO, the Conservative Shadow Minister for Housing, Scott Aitchison, made a surprise appearance at CHBA’s National Fall Meetings in October to speak with local and provincial EOs on a wide variety of topics impacting housing.
And last month, after numerous conversations with CHBA, the Conservatives announced their intention to eliminate the GST on all new homes sold for less than $1 million, should they form government – later pushing the provinces to do the same. This would be a welcome measure, as it addresses a long-standing CHBA ask to fix the GST/HST New Housing Rebate.
Announcements like these reflect continued strong advocacy by the Association, whether that be through CHBA’s Day on the Hill, various parliamentary committee meeting appearances, or ongoing activity by members and national, provincial and local staff. And we’re not stopping now. We encourage CHBA members to stay up to date on our progress by following CHBA’s Industry Highlights, our media aggregator on housing issues with commentary. Subscribe through your website account or email communications@chba.ca.
BY NATASHA ROMBOUGH, DIRECTOR OF MARKETING AND COMMUNICATIONS, CHBA
With nearly 25 years under his belt working to help build a manufactured home business, Frank O’Blenis has seen a lot of changes over the years working as a sales manager for Supreme Homes, a modular homebuilder with a factory in Tracadie, NB. The company serves all of Atlantic Canada, Quebec and Ontario. Frank plans on retiring soon after many years dedicated to the industry, and we took the opportunity to catch up with him and learn more about the family company that he helped grow.
In 1983, Aristide Savoie started a small company in Tracadie, NB, building storage sheds and outdoor garages in the open air. That side of the company grew, and he also began to build stick-built homes. In 1995 he opened a factory with the intention of doing all construction indoors so that the product wasn’t exposed to the weather, and with the
vision of one day expanding the business to building mini homes in the factory. In 1990, his son Robert, who is now the owner-president, began working with the company. As his summer student job in 1996, he was tasked with getting the firm CSA Certified.
In Canada, all buildings, including factory-built ones, must comply with the locally applicable building codes and regulations in effect, and that must be checked, verified and inspected against the requirements in the location they are built in. The CSA A277 certification verifies that factory-constructed buildings comply with local requirements. The certification body oversees the in-plant quality process, including identification of qualified personnel and responsibilities, sign-offs and record-keeping, and conducts annual audits and random inspections.
Supreme Homes received its CSA certification in 1997 and built its first mini home inside the factory, while continuing to make
FAST FACTS
Company Name:
Supreme Homes
Head Office: Tracadie, NB
Areas Served:
NB, NS, Nfld., PEI, Que., Ont.
Full-Time Employees:
More than 200
Retailers: 17
Projects/Homes per year: 250
conventional stick-built homes. Two years later, things were going well, and Aristide Savoie was looking to expand. But his plan to buy out another modular plant in Amherst –three hours away – did not sound appealing to Robert, who was in the process of building a home with his pregnant wife. “Instead, we decided to expand the factory in Tracadie,” Robert says. “We went from 6,000 square feet to 42,000, and hired some of the people who worked at the Amherst business to work in it – Frank was one of them. We never looked back after that, just kept expanding.”
Frank was no stranger to the retailer model, and brought leadership with him to Supreme Homes. He’d worked for years for a door and molding manufacturer called Premdoor, which was based in Ontario and had factories all over Canada, the U.S. and Europe, including a door manufacturing plant in Amherst. Frank worked as a sales manager there before spending a few years working for the home manufacturer in Amherst that Aristide had considered buying out.
Frank truly made a home with Supreme, though, bringing his distribution network with him and developing and maintaining the relationships with retailers that are a main component of factory-built business models. He likens the arrangement to that of car dealerships that procure vehicles for purchasers; the retailers have offices and sometimes lots with showhomes on them, and they are the ones who bring in homebuyers, put in the order and handle the transaction, and arranging for the home to be “installed” onsite.
Supreme Homes continues to grow, and now employs more than 200 full-time employees. In the years that Robert and Frank have been working there, they are happy to note that their workforce has become more diverse. “More women are willing to work in this field now, which is a good thing,” Robert notes. “Twenty years ago, we only had cleaning ladies, but now young women are doing finish carpentry, cabinets, sheathing and more. They have fresh ideas and good attention to detail.”
Aristide retired in 2004, with Robert taking the reins. Since then, the company has been a modular builder exclusively.
Today, the company specializes in single-family custom homes. It prides itself on pushing the boundaries of designs that are compatible with factory-built construction methods, such as models that range from having flat roofs to a 17-ft.-wide high-pitched roof, and styles can be called modern, traditional or Scandinavian. On average, it takes six to nine months to go through the process of conceptualizing a new design and making it available to homebuyers.
“When making a new design, we consider who the buyers will be, what current trends are and what shows well, and what will have lasting appeal. We are inspired by architecture in other countries, but it’s new to modular construction in Canada,” says Robert. “It would be boring to do the same house every day, and our employees like the variation; it’s challenging and fun.”
However, the nature of factory-built homes means the more the company builds a model, the better the return on investment, which is why designing for the future is important. Prospective buyers can see models that are available either on the retailers’ lots, or during open house days that Supreme hosts.
Frank works from home, but often travels to visit retailers and to go into the factory. He’s also very committed to advancing the factory-built industry within Canada. He was on the board and served as president of the Canadian Manufactured Housing Institute (CMHI), and helped navigate the transition of merging CMHI and MHI Canada to create the CHBA Modular Construction Council in 2017. “The work that was being done in the local/provincial associations and at the national level of CHBA was valuable, not just for the industry but also for Supreme Homes,” Frank says of his steady involvement over the years. “The work that gets done
behind the scenes is crucial for moving our industry forward.”
Robert agrees that there’s still work to be done. He says there while it’s improving, there’s still an existing stigma about their products, and it’s frustrating that people still need to be told that their homes built in factories are just as good (or better) than conventional stick-
FEB. 11, 2025
CHBA Day on the Hill Ottawa
built homes, and that the benefits of being built indoors need to be explained. Once people come to the factory and see the product, they’re convinced, but it shouldn’t be necessary.
But the bigger hurdle is with governments, specifically bylaws and zoning challenges. “Governments are asking for more homes and better homes, and modular is the solution for improved efficiency and product,” Robert says.
He feels optimistic about the future. “We have a strong wind in the right direction for factory-built homes.
MARCH 2025
Finalists Announced for the CHBA National Awards for Housing Excellence
MAY 11-15, 2025
CHBA Home Building Week in Canada Victoria, BC
JUNE 9-11, 2025
EOC Professional Development Forum St. John’s, Nfld.
There’s a lack of labour and Canada needs to be more productive. Interest rates are going down, there’s strong demand and growth, and we have a government pushing for investment. General contractors have a lot of work just with commercial projects, so manufacturers can take on residential construction.” He’s already seeing a lot more modular construction locally, and says it’s rare now for an apartment or condo building to be built without some form of panelization. “In five to 10 years, you won’t see any more projects that don’t have boxes built in the factory. Things are changing and modular is the future.”
As for changing the stigma around factory-built homes, “It helps to see governments saying they’re coordinating their efforts with modular construction in mainstream media,” Frank points out.
For its part, Supreme Homes has been developing a new part of its business model that is centred on larger housing contracts with government entities. The company has
completed three projects this year, with housing types ranging from duplexes and townhomes to apartments, all within Part 9 of the building code. Robert points to the government of New Brunswick as an example of things changing, as half of all units to be built were required to be modular.
Frank plans to retire in January 2025, but if you ask Robert, he jokes it won’t be until much later. You can tell there is a good history there, the two having spent nearly 25 years working together. Frank credits his longevity with the company to their great working relationships. “Aristide and Robert, and now Robert’s son Yan, who is the third generation working with the company as its chief operations officer, have always treated me as if I was part of their family. They’ve always respected my input and treated me with respect. They’re just a really great family.”
The two have come a long way since first meeting, back when Robert thought Frank was
Italian (Franco Blenis versus Frank O’Blenis) before finally greeting him face to face. “Hiring Frank was a gamechanger for us,” Robert says. “He’s dedicated to his work, and everyone loves him – he’s a great Maritimer with his heart in the right place. He’s always there for anyone, and he’s got a good ear, a good eye and a good soul.”
Frank says that in addition to the Supreme team, he’ll miss the relationships he’s built with retailers over the years. “There have some people I’ve been working with since 1999,” he says. “I can drop in with them outside work hours and they’d always be happy to see me. I’ll also miss the people at the plant that I’ve worked with for a long time.”
But he’s got a lot to look forward to, like more time to dance with his wife (they ballroom dance, waltz and square dance regularly) and to travel. He’ll continue to be proud of how far the industry has come, and where it’s headed.
FRANK LOHMANN, SENIOR DIRECTOR, BUILDING SCIENCE
If it feels like significant building and energy code changes are coming at a fast pace, that’s because they are. The residential construction industry is being inundated with late adoption of 2020 codes and major proposed changes to Canada’s 2025 National Model Construction Codes at the same time. Each proposed change has implications on how homes are built and renovated, and should ideally be evaluated
CHBA’s newly launched Knowledge Centre will help share technical information with members more efficiently. This searchable repository includes building code meeting briefs and summaries of public consultations so that all members can stay informed about new and proposed building code changes and technical information. Find it under at chba.ca under Resources > For Members > Knowledge Centre.
based on its feasibility and impact on affordability. Keeping up with the sheer volume of proposed changes is an extremely difficult task, and it doesn’t look like it will slow down any time soon. The association works with members to provide input into the code system to bring the industry’s
CHBA’s Technical Research Committee (TRC) is comprised of the provincial HBA representatives (which make up the TRC Management Committee) and members representing more than 30 organizations including government research agencies, codes and standards organizations, allied industry associations, colleges, university research networks, home warranty providers and other members at large. Showing the importance of these meetings and the interest members and HBA staff have in content covered at TRC, the last TRC meeting in Ottawa had more than 160 attendees, including observers.
TRC is the CHBA’s forum for all things related to innovation, new technologies, building and energy codes, standards and regulations affecting how homes are constructed. TRC also works to identify technical problems being experienced by the industry, to achieve consensus on their priority, to mobilize private and public R&D resources to resolve these problems and to communicate solutions to members. TRC’s Management Committee occasionally provides policy advice to CHBA’s Board of Directors.
perspectives, concerns and recommendations to the code development process, and to stay on top of the implementation challenges and upcoming changes to best prepare members for the future. Below are some highlights to show the work being done.
Keeping up with all the code changes takes a lot of staff time. So far in 2024, CHBA National staff have spent a combined total of 1085 hours participating in code meetings, reading thousands of pages of code change proposals ahead of meetings, and interpreting the impact these changes will have. This number does not include the invaluable time also spent by members in these meetings, or the staff time collecting and summarizing member feedback to inform the committees and influence the proposals, or for time spent communicating the resulting codes-related information to members and HBA staff across the country.
INNOVATIVE AND STANDARDIZED PRODUCTS
If you have ever found yourself wanting to use a very innovative product that is not in the code and for which no standard exists, you will likely know about the Canadian Construction Material Centre (CCMC). The CCMC issues evaluation reports of innovative building materials and produces listings of standardized products available on the CCMC’s registry. In addition, 277 brand new products are being actively evaluated now. CHBA staff participates as a member of the Canadian Commission of Construction Material Evaluation and makes sure that CCMC continues to improve its service and delivery speed for innovative products being evaluated and brought to market.
26
MAXIMUM
TEMPERATURE REQUIRING COOLING
One Proposed Change Form (PCF) 2061 coming soon to a special public review suggests mandatory mechanical cooling for homes located in regions with maximum July Design Temperature of 26 Celsius or more. CHBA is participating at all levels of code meetings to make sure this fast-paced change, driven by high political priority after the BC heat dome in 2021, can be implemented without difficulty and the costs of this change are being made transparent.
One-hundred and eighty-six of the 1,200 standard references in the national codes are being updated for 2025. Every two to three years, codes are trying to catch up and update all references to the respective newest standards’ edition. Unfortunately, standards committees are not required to conduct cost-benefit analysis. This means that each code’s update of these standard editions adds unknown cost to the construction of homes. CHBA continues to flag this as an issue and to monitor the fast-paced updating to ensure there is no conflict with other parts of codes and that high-cost items are flagged. Many of these standards are still available to the public only at a considerable cost, and CHBA is calling for all codes and standards referenced in the NBC to be available for free.
These two-month public review periods on proposed changes to national construction codes allow CHBA with the guidance of members to submit comments on future code proposal. These comments – whether supportive or not – can have profound impacts on how affordable homes will be in the future and CHBA continues to rely heavily on input from members during each public review.
374
13
All national codes committee structures for the national model code development are changing in January 2025. The current Standing Committees will be dissolved, and new National Model Code Committees will be created. This means there will no longer be a single committee dedicated to Part 9 of the code. CHBA is a working on participating in all committees, but predicts it will be immensely challenging to bring industry input to this new structure.
1•2•3•4•5
Codes Canada’s database of code change requests and proposed changes indicates that there are 374 proposals approved for the four National Model Construction Codes for 2025. CHBA members and staff are involved in the national model codes development, either as committee members or observers.
ENERGY EFFICIENCY PERFORMANCE TIERS IN NATIONAL
The 2020 National Codes have introduced five tiers of progressively ambitious energy efficiency. They are called “Tiers” and go from 1 to 5. According to agreements signed by the provinces, by March 2025 all provinces are to have adopted the national codes and one of these tiers will be the mandatory minimum. So, one number will decide how efficient new homes in your province will be. Tiers 1 and 2 are prescriptive while tier 3, 4 and 5 in the 2020 codes are only available through modeling. The proposals for the 2025 national codes (expected to be adopted in 2027) will offer more prescriptive guidance and a points trade-off method for tiers 3, 4 and 5.
3,042
CHBA has hosted 7 webinars over the last 8 months with more than 3,000 registrations. The webinars inform members about proposed code changes and about the comments that CHBA would likely submit during the respective public reviews. The webinars are still available for members who want to review them to find out what the next building and energy codes may bring. Members can access them at chba.ca/webinars.
J. ZSIROS CONTRACTING IS ON A WINNING STREAK
BY SARAH CARON, CHBA DIRECTOR, RENOVATION SERVICES
J
im Zsiros of J. Zsiros Contracting is no stranger to winning awards. Starting with the 2017 Vancouver Island Building Excellence Award for Best Renovation Under $100K to the most recent 2024 CHBA National Award for Housing Excellence for Best Whole Home Renovation $300-500K, the company has amassed 23 awards at the local, provincial and national level.
Jim Zsiros is the owner and president of J. Zsiros Contracting, a custom homebuilder and
renovator located in Courteney, BC specializing in high-performance, energy-efficient homes. His small team of five full-time employees has been building and renovating homes in the Comox Valley and greater Vancouver Island for more than 25 years.
Zsiros joined the Canadian Home Builders Association – Vancouver Island (CHBA-VI) in 2008 to access the educational benefits offered by CHBA and exchange information on new building techniques and materials with
Company Name: J. Zsiros Contracting
Head Offices: Courtenay, BC
Number of Full-Time Employees:
5
Projects per year: 2-3 per year
Website: zsiroscontracting.ca
other local builders. A life-long dedication to learning and a keen interest in the latest building innovations led the company to build the first Net Zero home in North Vancouver Island in 2018. This passion and dedication for Green building practices is also evident on the renovation side of the business. The renovation process involves educating clients on energy efficient updates and potential rebates that could result in cost savings now and in the future.
With the increasing costs of construction and land, Zsiros is seeing more clients chose to renovate rather than build new homes. To further bolster their credibility as a renovator, the company joined the RenoMark program in 2020 to “provide clients with the knowledge that the renovations were completed to exacting and warranted standards.” Looking ahead, Zsiros says he believes there is a growing opportunity to regulate the home renovation industry in BC. This is an issue that
“ The RenoMark program adds credibility to the homes we renovate and provides clients with the knowledge that the renovations were completed to exacting and warranted standards. ” – Jim Zsiros
he will continue to advocate for as the current past president of CHBA-VI and a member of the CHBA-BC Renovator’s Council.
This renovation project, which won a CHBA national award in 2024, is a meticulous blend of sustainable innovation and thoughtful design, driven by the clients’ priorities of health, energy efficiency and comfort. The transformation of this 1970s home not only addressed the challenges of modernizing an aging structure but also honored the homeowners’ commitment to an eco-conscious lifestyle.
A reimagined floorplan opened up the interior, creating a more efficient and family-friendly layout. The removal of a bathroom and fireplace allowed for an expanded kitchen that seamlessly integrates with the living area, promoting social interaction. The bathroom was redesigned with an integrated bath/shower, underfloor heating, a heated towel rack and bidet – offering both luxury and practicality.
To meet the client’s sustainability goals, the home underwent substantial energy-efficient upgrades. Existing electric baseboard heaters
were replaced with a ductless heat pump, and a high-efficiency wood stove took the place of the original fireplace. Additionally, all windows were upgraded to triple-glazed, drastically reducing energy consumption. The home’s insulation was also replaced, enhancing R-values for better thermal performance.
All materials used were certified as non-VOC, ensuring a toxin-free environment. Timber frame beams and ceilings were stripped and refinished with natural products, maintaining the home’s original character while promoting environmental responsibility. Materials that could not be reused were donated to Habitat for Humanity, further underscoring the project’s commitment to sustainability.
This renovation tackled significant hurdles, including budget constraints, supply chain disruptions and the need to bring all systems up to current code standards. Sourcing local non-VOC materials proved difficult and costly, but exhaustive research and strategic partnerships helped overcome these barriers. Structural changes were minimized to save on engineering costs, and innovative sourcing kept the project within budget.
BY NATASHA ROMBOUGH, DIRECTOR, MARKETING AND COMMUNICATIONS, CHBA
Questioning the “productivity” of the homebuilding industry – or lack thereof –has been bounced around in the media of late. Statistics Canada published data showing that the construction sector is lagging behind other business sectors when it comes to labour productivity. And while there is a general misunderstanding of the issues around productivity in our sector (which CHBA is working to correct), given Canada’s shortage of both housing supply and skilled workers, stagnant productivity does pose a serious problem.
To increase productivity, we must do more with less. CHBA’s Sector Transition Strategy (STS), which we published in February 2024, presents the challenges and solutions to overcoming Canada’s barriers to doubling housing starts, and some of those opportunities are rooted in the benefits of factory-built homes, including modular construction methods and panelization. The STS garnered widespread interest with both federal politicians and public servants, and Budget 2024 contained several measures taken directly from recommendations in the STS.
While governments are enamoured with modular construction as a solution to the housing shortage, moving to more factorybuilt construction is a complex business proposition. CHBA’s goal with the STS was to explain the substantial barriers to widespread adoption, which include high risks associated with the high capital cost investment required to set up a factory, with high overhead – a particularly risky situation in the boom-bust nature of the housing market. The STS begins by focusing on the policy and regulatory fixes
needed to build more housing in general, and provides a path forward to upscaling the technology involved, which can benefit site-builders as well.
Armed with solutions coming directly from our members, the federal government used the STS to make numerous announcements benefitting modular construction in the Budget. This included a focus on Industrial Strategy and Supporting Innovative Housing Technologies. Part of this strategy is the development of an industrial strategy for homebuilding, which is underway. CHBA CEO Kevin Lee was requested by federal Minister for Innovation, Science and Industry of Canada, François-Philippe Champagne, and Housing Minister Sean Fraser, to be one of five expert members of a consultation panel. On the panel, CHBA was a strong voice for the sector and provided valuable information to policymakers on how to set the stage to enable more factory-built construction.
One of the major barriers to more factorybuilt construction is a lack of understanding of the factory side of the process by building officials, and a resultant duplication of inspections. CHBA has raised this issue and is
therefore glad that the National Research Council (NRC) is being tasked with finding ways to reduce duplication between factory inspections of modular home components and on-site building inspections.
NRC has also been tasked with supporting efforts to address regulatory barriers to help scale up factory-built housing. CHBA is taking advantage of this through an air-tightness testing project supported by NRC, which will help reduce the costs of testing for modular units going to remote locations (more details below).
Budget 2024 also announced two $50-million initiatives to support industry moving to more factory-built solutions. “CHBA was very pleased with the measures announced in the 2024 budget to support modular construction, but our advocacy related to factory-built construction doesn’t stop there,” says Lee.
“The stick-built housing industry in Canada is well adapted to the ebbs and flows of what has historically been a pattern of boom and bust cycles,” he adds. “If we are to transition a large part of the sector to factory-built construction, there are many barriers to overcome. In addition to helping to de-risk the high start-up costs, we need consistent demand to keep the factories moving and people employed, and financial institutions to better understand the business model and offer more helpful financing solutions, which we are starting to make some ground on.”
CHBA continues to call for improved zoning to support gentle densification, including laneway suites and other Accessory Dwelling Units (ADUs), which are often ideal candidates for modular construction, as well as improved financing for factory-built homes. These recommendations have been important pieces of ongoing advocacy work, including CHBA’s annual Day on the Hill.
Our advocacy resulted in the federal government’s October announcement to allow homeowners to refinance their current mortgage and construct a secondary suite, with borrowers able to access up to 90 per cent of the home’s value, including the value of the extra suite. The borrower will be able to amortize the refinanced mortgage over a
period of 30 years. The federal government also said it is increasing the mortgage insurance home price limit to $2 million for those refinancing to build a secondary suite. This will be of value to both our modular and renovation members.
In September, CHBA co-hosted a webinar for members with RBC on getting more buyers into the market. RBC shared their mortgage solutions for through their Construction Mortgage Program. One of the new additions is retail owners purchasing these homes through a Preferred RBC Builder that will continue to reside there now have access to construction draw mortgage financing (as opposed to just purchase single draw transaction previously). This means a modular/ manufactured homebuilder can receive payment in multiple tranches. Members can watch this webinar on demand at chba.ca/webinars.
Shaun Scrupps is general manager of SRI Homes, which has several locations in western Canada, and is under the Champion Canada Modular Ltd. Umbrella, which includes SRI and Moduline. Since SRI was founded in 1978, the company has built more than 45,000 homes. Scrupps says the new RBC financing is already proving helpful to homeowners. “Shelter Home Systems SRI are a preferred manufacturer with the new RBC program, and some of our retailers have gone through the process as well. In the past three months, one retailer identified four sales that were closed under this program that may have been lost previously for financing issues.”
There is still room for improvement when it comes to homeowners receiving comparable financing options for factory-built homes as traditional site-built construction, but things are improving.
We know that factory-built homes can deliver the same – or better – airtightness as site-built homes. However, in addition to required blower-door testing on site, some factories also conduct an additional test in the factory to ensure a quality product. While the
airtightness of manufactured houses is not expected to vary greatly as a result of transport, data is lacking on validating this assumption that would support a code change to allow “in factory” testing for single-section modular units.
CHBA received funding from the National Research Council (NRC), to compare results of in-factory air-tightness testing versus in-place testing. The objective of this project is to understand how the transport of manufactured houses from the factory to their destination affects the measured airtightness performance to inform a code change request for an exemption from on-site testing for single modular units.
Keith Herring, director of modular construction at CHBA, says this project stems from the strategic planning session that members of the CHBA Modular Construction Council participated in last year. “Compiling data to support our recommendations on how to address the challenges that factories face was a big part of our strategic planning session. In
general, Canada needs more empirical data before making building code changes, and this project is exactly the type of investment that needs to be made in order to make factory-built housing more productive and affordable.”
The goal is to get a code change that won’t require on-site airtightness testing for single-section modular homes, which will save time and money for factories, making the end product more affordable to homeowners. It would also benefit homes delivered to very rural and remote areas, where it’s difficult to do on-site testing due to the lack of available Energy Advisors and the high cost of travel and accommodations to bring one to the site.
For the project, CHBA will coordinate the in-factory and on-site testing of 75 different homes across Canada in different climate zones. All testing and project administration costs are covered by the NRC funding.
SRI Homes is one of the participating factories, and Scrupps says that there are
several advantages to performing air tightness testing in the factory. “Blower door testing in the factory has allowed us to refine our product quality and guarantee product performance, ensuring passing results in the field which avoids costly interventions and delays. Additionally, it allows us to look ahead to future code requirements over the next 10 years, all the way to net zero efficiency, and it will become a marketing item for our sales teams.”
“The hope is that this will be the first of a multi-phase project that can be expanded to homes with basements or two-section products, followed by multi-section modular homes and eventually multi-unit residential buildings (MURBs),” Herring says.
It’s just one of many changes that can be made to make the business case for incorporating more factory-built homes into Canada’s housing stock. Change has to start somewhere, and CHBA and its members are leading the efforts.
BY EVAN ANDRADE, CHBA ECONOMIST
With many media headlines focused on housing affordability and the increased political action to incent more housing supply, the health of the renovation services industry may not be receiving the attention it should be.
Canada’s existing housing stock consists of 16.7 million homes, including 10.7 million ground-oriented units. That’s an enormous number of dwellings requiring updates, retrofits and general repairs. With the rise in
multi-generational housing arrangements, secondary suites and accessory dwelling units (ADUs), renovators clearly also play a role in expanding the housing stock.
Renovation and repair services are a vital contributor to Canada’s economy, representing $105.5 billion in nominal spending in 2023. CHBA estimates that this translated into 526 thousand jobs supported directly and indirectly and that those jobs collectively paid $36.9 billion in wages across Canadian communities.
So far in 2024, nominal renovation investment (excluding repair), which is the amount of money before factoring in inflation, is trending even stronger than 2023. Between January and August this year, investment totalled nearly $59 billion compared to $52.6 billion last year. This increase in investment was driven by record spending on multi-family building renovations, while spending on single-family renovations remained unchanged. Monthly renovation investment has
reached new record highs in each of the last three months of available data (which Statistics Canada provides starting in 2017) as a result of strong multi-unit investment. The increase is led by Quebec and Ontario, though most other provinces have also seen an increase in multi-unit renovation investment so far this year.
Surprisingly, this nominal investment increase has not translated into real GDP expenditure for renovations in the first two quarters of 2024. Real GDP tracks the “volume” of work by converting nominal values using prices recorded in reference year – 2017 in this case. The chart on the opposite page shows historical real GDP output of the renovation-industry in Canada. Since the 1960s, real renovation output has been fairly stable and consistent – save for the 1990s. In general, real output has grown organically with a larger housing stock and a wealthier population. Although the term may be overused, it is fair to say that the volatility in real output since 2020 is unprecedented. As quickly as the investment rose to its peak level in 2021, it evaporated. This decline has continued in the first two quarters of 2024, despite the increase in nominal investment. The second quarter real GDP for renovations stood at $50.7 billion annualized. If excluding the start of the pandemic, this is a low volume of work last seen in 2013. What could be causing this difference between nominal and real output?
One reason is that materials and labour costs are rising in all parts of the country, so expenditures are up but volume is down. In October, Statistics Canada released its new Residential Renovation Price Index (RRPI) – which CHBA provided input on last year – that records average pre-tax prices charged by renovator contractors over time. The index covers prices charged within 15 cities across Canada and averages across 37 different types of home improvement projects. The RRPI has risen more than 50 per cent nationally since the start of 2020. The chart above shows how renovations and new home construction are facing comparable rises in costs in every province except for Alberta.
Rising costs also lead to a second potential reason, which is that there is likely an unfortunate rise in cash-based work. While nominal investment is derived in part from permit issuance, real GDP likely incorporates other data sources of consumer and business spending. Like the ongoing poor selling conditions for new homes, few households will go ahead with major renovations as the quotes reach above the consumer’s budget. Under pressure to maintain a flow of incoming work, more renovators may be feeling pressure to offer cash prices to compete with fly-by-night contractors. These cash jobs are likely not being recorded in GDP.
The prevalence of cash businesses, and the unfair advantage they have over legitimate
contractors, is one of the reasons why CHBA has renewed its efforts to promote the Association’s consumer-facing RenoMark program. This distinction allows homeowners to easily identify trusted CHBA members that have proven they provide a superior level of service and care.
But there is good news for the future. Real GDP output from renovations could rebound in the second half of 2024, given record investment in nominal terms. Projections from the Bank of Canada anticipate renovation activity to improve in 2025 and 2026, as the broader “housing” sector of the economy will contribute nearly a quarter of all economic growth in these two years. The Bank expects existing home prices to rise on average as their policy rate comes down from restrictive levels while other key barriers to new home supply remain. Both the lower cost to borrow and rising property values will be, in their view, conducive to broadly higher real renovation activity next year.
Earlier this month, CHBA hosted a webinar specific to renovator members about the economic outlook for renovations in 2025. The presentation consists of key near-term opportunities to drive renovator business growth, a summary of CHBA’s federal advocacy that affects renovators, and future policy recommendations. The recording of this insightful webinar can be accessed by members at chba.ca/webinars.
GETTING UPCOMING GENERATIONS INTERESTED IN RESIDENTIAL CONSTRUCTION
BY LEAH NORD, SENIOR DIRECTOR, OPERATIONS, CHBA
Canadians are all too familiar with the country’s housing crisis. The federal government has stated that we need 5.8 million homes built throughout the country between 2022-33 (3.5 million additional homes more than the 2.3 million we would normally build in that time frame) to address the supply shortage and address housing affordability. There are numerous barriers to reaching this goal, and among the most significant is: Who is going to build these homes in the years to come?
BuildForce Canada estimates that to reach this government target of 5.8 million homes, the residential construction workforce needs to grow to more than 1.03 million workers by 2033 – a staggering 83 per cent above our current levels. The most in-demand professions include electricians, trade labourers and helpers, contractors and supervisors, gas fitters,
painters, windows and doors installers, roofers, drywallers and plasterers, insulators, and refrigeration and air conditioning mechanics. This is at a time when 22 per cent of residential construction workers will retire by 2033, with
566,190
40 per cent of the workforce aging to 55 years of age and older.
CHBA has focused on a three-pillar approach to addressing current and future workforce challenges, advocating for a
1,038,150 2033
471,960 (+83%) EMPLOYMENT
combination of increased domestic workforce, changes to the immigration system, and increased sector productivity to help ensure that labour shortages are not a barrier to building the homes that Canada needs to address our housing affordability crisis.
When looking at immigration, CHBA often says that we need new Canadians who not only want to own homes but who can also build them. The same can be said about Canadian youth – among our domestic workforce, we need to do a better job at attracting – alongside retaining – young Canadians into our sector. And, to state the obvious, this is no easy task.
In the first instance, it’s a numbers game. As BuildForce Canada explains in its Residential Scenario Outlook 2024-2033, as our country’s population ages over the next decade, the share of Canadians under 24 years will remain the same, meaning there are fewer youth to replace retiring workers. As a result, sectors and companies will be competing for a relatively
“ Among our domestic workforce, we need to do a better job at attracting – alongside retaining –young Canadians into our sector. ”
smaller percentage of youth, intensifying the talent war for new/entrant workers.
Furthermore, there is a longstanding stigma around entering the skilled trades, which includes the residential construction trades. Statistics Canada has reported that between 2016 and 2021 the number of tradespeople employed in Canada declined, especially among youth (age 15 to 24). And although, for example, overall apprenticeship enrolment has increased in the post pandemic period, completion rates continue to be disconcerting, and are in fact trending downward (from an average of 60 per cent in 2010 to 45 per cent in 2022), with completion rated for women at least 10 per cent lower than their male counterparts since 2017 .
Yet there is some encouraging progress thanks to some great work going on in communities across the country by local and provincial HBAs and their members.
The Guelph & District Home Builders’ Association (GDHBA) in Ontario hosts an annual Residential Construction Day for local high school student to learn more about careers in the skilled trades directly from their members. Nearly 100 students are given hands-on experience with tools and construction techniques, and they tour a variety of homes in a community under construction, allowing them to see the different stages of the homebuilding process. This unique experience helps inform students about what courses to take on the path to apprenticeship, and what they can look forward to in a career within the industry. GDHBA CEO Melissa Jonker says that they created the event because “our members saw the overwhelming need to encourage students to consider careers in the skilled trades. Over the last six years, this event has been a tremendous success with an increase in participants each year. The event allows us to showcase the high-paying, in-demand careers that could be part of the students’ futures.”
CHBA Central Interior (CHBA CI), based in Kamloops, BC, has partnered with Thompson Rivers University for 35 years to provide first-year students in construction, electrical, plumbing and HVAC with valuable hands-on building experience and access to the latest tools, technologies and industry practices. Students and industry members build a Training House, which is then sold to the YMCA BC for their annual Dream Home Lottery fundraiser. During the build, members provide mentorship, fostering a supportive learning environment that encourages students to pursue careers in residential construction. Matt McCurrach, a builder and developer from Kamloops and the current national President of CHBA, speaks passionately about this initiative: “The Training House is a shining example of how collaboration and hands-on experience can inspire the next generation of tradespeople. It’s initiatives like this that ensure the future of our industry remains bright and innovative.”
In eastern Canada, CHBA Newfoundland and Labrador have partnered with Skills Canada to market their Youth Apprenticeship Summer Program (YASP). The programs allow students in grades 10 and 11 to work for seven weeks in the summer with a Journey Person to try out a trade and see if it is a career path that interests them. The students earn hours towards their apprenticeship if they decide to continue with the trade and some have been kept on by the summer employers after the program concludes. YASP is a pilot project designed by Skills Canada, and CHBA-NL has been helping to connect members with students for the program.
The above are just a few examples among several initiatives taking placing across the country, from scholarships and financial aid to one-the-ground exposure and training programs, to encourage more young people into the skilled trades. Canada needs to invest effort into building up a workforce large enough to build the homes we need and every effort makes a difference.
Professional-grade power tool technology has quickly evolved from battery-powered tools being a distant second to corded tools. Battery-powered tools now dominate the power tool landscape. Hand tools have become more sophisticated ergonomically and in calibration capabilities.
A battery-powered Hilti concrete saw for heavy-duty tasks, the DSH 600-22 gets the same work done as a 60cc gas cut-off saw. It has a longer trigger time and is designed to cut up to 30 per cent more than a full tank of gas with four B 22-255 Nuron batteries and 12-in. SPX univ. A cordless-optimized blades. Reduced running costs with no fuel to buy or mix; less maintenance and up to double the lifespan of a gas saw because of its brushless electric motor. Improved safety features include quieter, lower-vibration cutting and a fast-acting blade brake. Weighs 26.5 lbs, including two B 22-170 batteries and a 12-in. blade. hilti.ca
The DEWALT 60V Max 12-in. double bevel sliding miter saw features regenerative braking technology to extend runtime with virtually every cut. Designed for up to 675 cuts in 3.25 in. MDF base molding or up to 255 cuts in pressure treated four-by-four-in. timber, all on only one DEWALT FlexVolt DCB609 battery. This miter saw has an efficient bevel gear transmission and the ability to capture up to 94 per cent of dust. The blade positioning system provides accurate cut line indication. The saw also features updated controls designed for overall ergonomics compared to previous DEWALT designs. Weighs in at 50.9 lb (tool only). dewalt.ca
The SKIL 4.5 Amp Belt and Disc Combination Sander is a two-in-one sanding station for a variety of lengths and angles. Features a powerful 4.5-amp induction motor to power through the toughest jobs with consistent sanding. Its beveling tabletop allows for sanding from 0 to 45 degrees and the belt angle adjustment allows for 0 to 90-degree sanding. Changing sandpaper grits is easy thanks to a quick tension release lever. A miter gauge guides the workpiece when making crosscuts and a dust port that accepts standard 2.5-inch vacuum hoses minimizes dust in the work area. It includes a 4.5 amp belt and disc combination sander, miter gauge and hex wrench. skil.com
The 80-piece RYOBI Black Oxide Drill and Drive Kit features drill bits with a black-oxide finish that is corrosion-resistant to extend the life of the bits. The kit also features a variety of driving bits. The Steel Drill and Drive Kit includes a hard plastic magnetic storage holder to keep track of pieces on and off the job site. Includes 10 black oxide drill bits and 69 steel driving bits which fit most common fasteners. ryobitools.ca
BRUSHLESS-MOTOR ROUTER FEATURES MICRO ADJUSTMENTS
The DCP580B features a brushless motor for maximum efficiency that helps to maintain speed under load. This brushless planer features a 3.25-in width capacity and ability to adjust depth at 1/256 in adjustments with a rebate capacity of 5/64 in. The planer weighs 6.8 lbs and operates on the DEWALT 20V Max battery system. Lightweight, the planer can be easily transported around the jobsite, and a kickstand allows user to rest it when necessary. Calibrated depth adjustment knob to 1/256 in. on work surface without gouging the material. Precision machined groove-in-front shoe allows for edge chamfering, 5/64 in. maximum depth of cut. dewalt.com
The Makita 40V Max Brushless motor router delivers power equivalent to 2.25-HP corded routers. It is compatible with AWS (auto-start wireless system) for wireless connectivity with compatible dust extraction. The high power brushless XGT motor increases cooling efficiency to achieve power output equivalent to corded routers. Electric brake gently reduces cutter speed, resulting in less damage to the work area. Micro adjustment allows for fine adjustments of the cutting depth. Includes (batteries and charger sold separately) 0.5-in. Collet Cone (763622-4), Collet Cone 0.25-in. (763809-8), Collet Cone 3/8-in. (763810-3), Wrench (781034-9) and Dust Nozzle (P-80023). makita.ca
Cordless miter saw Symmetric SYMC-70 EB-Basic is designed to achieve ideal results more quickly. The SYMMETRIC saw strips twice as fast as with a regular compound miter saw, accurately and without making calculations. Use the bevel to easily obtain interior and exterior angles and transfer them to the symmetrical stop system. Saw exactly along the bisector, with one setting for cutting both strips of a corner with precision. The rollers allow moving the cordless compound miter saw into the correct position quickly and, in combination with the dual battery system, make the saw as mobile as you require. Provides an optimal work process, even in small spaces. Left and right-handed operation; switch and handle are in a central position, so they are just as easy
The Milwaukee M18 fuel Supersawzall reciprocating saw generates the power and performance of a 15A corded reciprocat ing saw. Redlink Plus Intelligence provides overload protection to prevent damage to the tool and battery during heavy applications while still maintaining compatibility across the entire M18 system. Provides 50 per cent more power and runs 50 per cent cooler versus standard RedLithium HD packs. The 1.25-in. stroke length removes more material with each stroke, while the variable speed trigger and five-speed dial provide ultimate speed control. An LED light provides increased accuracy and visibility, and an adjustable shoe extends the life of the blade. Selectable On/Off orbital action provides aggressive cutting in wood and smooth cuts in metal. milwaukeetool.ca
HAND TOOLS TO POWER THROUGH ANY JOB
The Stanley Sweetheart low angle block plane iron is made from extra-thick 1/8-in. A2 steel for excellent edge retention. Features precision-ground ductile cast iron base for accuracy, Norris-type adjuster with lateral locking feature, solid brass hardware for smooth adjustments and 12-degree low-angle bed ideal for cutting end grain. stanleytools.ca
The Jorgensen 33412 12-by-3-3/8 in. Medium Duty E-Z HOLD expandable bar clamp features rapid and easy clamping and can easily be converted to spreader clamps. The contoured comfort grip and quick-release lever make it simple to get a firm grasp, and an exclusive patented feature lets the user join two clamps together to create a clamp with more than double the opening capacity of a single clamp. Deep-reach pads help protect your work. ihlcanada.com
CH Tools’ 13-in. professional laminate flooring cutter comes with CH Tools’ heavy-duty flooring pull bar and floor installation kit for laminate and vinyl flooring. Cuts a variety of materials, including laminate flooring, engineered wood, and vinyl siding. It cuts up to 13 in. wide and 19/32 in. thick and produces clean and burr-free cuts. The built-in table miter gauge allows angled cuts from zero to 45 degrees, ensuring flooring fits seamlessly even in tight corners. Made from steel and alumi num, it’s lightweight, easy to carry and features a long handle for enhanced leverage during cutting. chtools.ca
This set of Fisch Tools decking drills for pure wood constructions consists of four length-adjustable wood spiral drills for centric pre-drilling of bore holes, a chromium alloyed high quality plug-in countersink and an adjustable stopper for adjusting the depth of countersinks. This stopper is made of high-grade plastic and protects the tool surface from scuffs and score marks as the stopper has a bearing and will stop to rotate with the wood spiral drill on encountering resistance. Only one stopper and one countersink for four different drill diameters for more flexibility. Other features include: Clean and tear-free sinkholes through optimized cutting-edge geometry; perfect chip evacuation due to the new groove geometry. alphatools.ca
The Klein PowerBox 1 has powerful magnets for attaching to metal job boxes and workbenches. Integrated LED lights brighten up any job box to locate stored tools, batteries and cords. Equipped with four 120V AC outlets, two USB-A ports and one PD-capable USB-C port for fast charging of cell phones, laptops and other compatible devices. Built-in surge protection with LED indicator protects equipment from electrical spikes. Supply power to any metal job box with the five-ft. durable power cord. Available from CF Construction Fasteners and Tools. cf-t.com
Wera’s Zyklop Speed Ratchet With 0.5-in. drive features 72 fine-pitched teeth that enable a low return angle of only five degrees. The ratchet head pivots freely and can be locked into any position by using the slide switch positioned on either side. The user can work conveniently in confined and difficult-to-access areas with enhanced hand clearance. Predefined locking positions at zero-, 15- and 90-degrees, both to the right and left, ensure safe working without any slipping of the ratchet head. The ratchet can be used as a conventional screwdriver in the zero-degree position by attaching an adaptor and a bit. The flywheel design ensures rapid screwdriving. The rotation-symmetric construction of the Kraftform handle and the free-turning sleeve support rapid twisting. tegstools.com
Build it all with one intelligent platform. Procore is a singular solution that drives intelligent risk management across all of your projects, from preconstruction to closeout. Project management: Easy-to-use, mobile project management software that improves efficiency by connecting field and office for real-time visibility. Quality and safety: Mitigate risks and make tough decisions using real-time data from the field. Manage daily logs, inspections and incidents all in one place. Project financials: Manage accurate project budgets with reliable data drawn from the field. See in real-time how your spending decisions affect the profit you’ll have at closeout. Invoice management: Streamline billing across stakeholders so everyone has access to the latest information in one organized platform. Tender management: Save time throughout the tendering process with features that let you distribute information, collect tenders and track coverage all in one place. procore.com
ENHANCING THE HOMEBUYER JOURNEY WITH INNOVATION
BY TIM BAILEY, DIRECTOR OF OPERATIONS, AVID – ECI SOFTWARE SOLUTIONS
I
n today’s competitive housing market, homebuilders face a growing demand for delivering a personalized, transparent, and tech-driven customer experience. Homebuyers are more informed and tech-savvy than ever and expect a seamless, engaging and supportive journey.
Understanding that this journey extends well beyond the closing day is essential.
Some top customer experience trends reshaping the homebuilding industry include:
1| PERSONALIZATION POWERED BY TECHNOLOGY
Personalization has become a major priority in homebuilding, as homebuyers are less interested in cookie-cutter homes. Today’s buyers crave spaces that reflect their unique
tastes and lifestyles. In response, many builders are leveraging cutting-edge technology such as virtual reality (VR), augmented reality (AR) and interactive design platforms to offer immersive and personalized experiences early
in the inspiration and discovery stage of the customer journey.
The digital age has transformed the homebuying experience, particularly upstream in this inspiration and discovery stage. With VR, AR and other technology, homebuyers can virtually tour their potential homes, exploring different layouts, materials and design features. This level of personalization gives buyers a tangible sense of what their dream home could look like, empowering them to make more informed decisions. Feeling a deeper connection to the design process enhances the customer experience early in the journey, making each buyer feel like an active participant in the creation of their dream home.
Clear communication and transparency are essential for a positive customer experience. This is especially important in homebuilding, where timelines can be long, and unexpected delays or changes can occur. Builders are increasingly adopting digital platforms that provide buyers real-time updates on construction progress, timelines and potential issues.
Customer portals and apps allow homebuyers to track their home’s progress, view photos and communicate directly with builders. This
Builder ratings have improved from the initial home buying stages up to the Move-In phase compared to last year. Yet, during the post-occupancy Warranty phase, they have declined to a five-year low.
Correspondingly, the Would Recommend score has also decreased, hitting a five-year low at just 66 per cent.
helps to manage expectations and reduce the uncertainty for buyers. Transparent communication builds trust and trust is currency with today’s homebuyers.
The customer experience doesn’t end when the homeowner takes possession. Unfortunately, data consistently shows that the lowest point in the customer experience occurs after closing.
Leading homebuilders recognize this as an opportunity and are investing in customer service long after move-in.
Many builders now offer technology tools, maintenance packages and customer support programs that provide ongoing assistance for homeowners after move-in. This can include anything from fixing minor post-construction issues to offering guidance and scheduled reminders for home maintenance and repair. AI-powered tools are further enhancing after-sale support, enabling more personalized and immediate assistance.
By staying engaged with homeowners after closing, builders can create advocate customers, ensuring a positive brand reputation to fill the sales pipeline with new prospects and repeat buyers.
Ease and convenience play a crucial role in enhancing the customer experience. This is particularly true in the homebuilding industry, where the process can often feel overwhelming and time-consuming. By streamlining and simplifying various stages of the homebuying and homeownership journey, builders can reduce friction and make the experience more enjoyable.
Top builders recognize that leveraging digital tools allows buyers to manage many aspects of their home purchase and ownership from anywhere, at any time, leading to a smoother, stress-free customer experience.
An outstanding customer experience in homebuilding combines the perfect mix of high-tech and high-touch elements to meet the diverse needs of buyers. Digital tools allow
“ Advanced technologies and personalized customer service create a more engaging and transparent experience that lasts far beyond closing day. ”
customers to take control, enabling them to explore homes, track construction progress and manage homeownership from the comfort of their own devices. These tech-driven elements provide a seamless, convenient experience that caters to the growing demand for speed and autonomy with today’s consumers.
While technology plays a crucial role, high-touch human interactions have become even more important at key “moments that matter.” Personal, expert guidance during critical stages – such as finalizing designs, troubleshooting concerns or addressing post-sale issues – helps to instill confidence and trust.
By layering expert personalized service on top of the digital experience, leading homebuilders are crafting the perfect mix to enhance customer satisfaction and create raving fans.
Build lasting relationships through innovation and personalization
The homebuilding industry is rapidly evolving to meet the changing expectations of today’s buyers. Advanced technologies and personalized customer service create a more engaging and transparent experience that lasts far beyond closing day. The focus on ease and convenience, through digital tools and self-serve platforms, streamlines the process, while high-touch interactions at key moments ensure buyers feel supported.
By embracing technology and prioritizing customer experience, homebuilders can elevate the homebuying journey, foster loyalty and drive long-term success. Builders who adapt to these trends will position themselves as leaders in the market.
BY NICOLE STORESHAW, DIRECTOR, GOVERNMENT RELATIONS, CHBA
Development charges (DCs) or development cost charges (DCCs) are a major contributor to unaffordability in home prices and a resultant lack of supply. All three levels of CHBA have been raising members’ concerns with municipalities and governments for years, explaining that construction and financing costs, including DCs by necessity, get passed on to buyers and warning that if new supply becomes too costly
to develop and people can’t afford the homes, new homes won’t be built. With the current housing affordability crisis, outside-the-box thinking is needed when it comes to how municipalities can pay for growth, rather than on the backs of the buyers of new homes.
DCs (also known as development cost charges, levies, fees and taxes depending on the jurisdiction) are upfront fees charged by
municipalities and paid for by developers for each new unit they build. They are charged to cover infrastructure costs such as new roads, water and sewer connections, but over the years they have grown to pay for much more – too much. The concept of “growth should pay for growth” has long been used as justification for burgeoning DCs. However, it is time to examine the issue of fairness, especial-
“ With the current housing affordability crisis, outside-the-box thinking is needed when it comes to how municipalities can pay for growth. ”
ly when it is new-home buyers (and usually younger) who are the ones being disproportionately impacted by skyrocketing DCs that the previous generation of homebuyers didn’t have to bear.
For example, between 2004 and 2024, an analysis of 27 municipalities in Ontario found that all of them increased their development charges for single-detached units more than
the rate of inflation in Canada (which was 54 per cent). Some municipalities increased their charges by as much as 800 per cent. That type of increase makes it particularly difficult for first-time buyers to save enough to buy a home. In Ontario, the tax burden on new housing now accounts for 31 per cent of the purchase price of a new home with development charges adding as much as $184,000 to the purchase price of the average new home in the Greater Toronto Area . The current average municipal DCC rates across Metro Vancouver are $39,199 for a single-family home, with the highest being close to $90,000 for a single-family residence.
A July 2022 Housing Market Insight Report from the Canada Mortgage and Housing Corp.
(CMHC) focused on government charges on residential development stated that there should be policy discussions surrounding ways in which municipalities raise revenue to fund municipal services and capital projects. “Where infrastructure is largely funded through means other than development charges, government fees on residential development tend to be comparatively lower. This may result in new housing being delivered at a lower cost,” the report concluded.
So how should local infrastructure be financed? Municipalities will claim that provincial and federal governments do not provide enough infrastructure money to pay for growth. Local politicians are loathe to increase property taxes.
DCs have become the way to finance these projects without much consideration for how it impacts housing affordability by their constituents.
During CHBA’s Fall Meetings in Ottawa in October, Professor Emeritus Andrew Sancton presented CHBA’s Urban Council with potential alternatives to DCs, which CHBA has been exploring and recommending in its advocacy. Professor Sancton argued, as CHBA does, that as a matter of fairness, everyone should pay for growth, just like we all pay for new hospitals and provincial highways.
One option would be for municipalities to borrow infrastructure money and pay it back over 20 to 30 years. At the moment, buyers of new homes absorb the cost of DCs through their mortgages, at higher rates of interest available to municipalities. This would require changes in municipal financial practices, and possibly provincial legislation. However, it is what is in place in the province of Quebec where development charges are not systematically applied, leading to lower housing prices.
“ At the moment, buyers of new homes absorb the cost of DCs through their mortgages, at higher rates of interest available to municipalities. ”
Another option would be to include new infrastructure costs in user charges for water and wastewater or include costs of new roads in user charges for roads. Both options would require more borrowing, perhaps by new municipally-owned corporations.
A third option would be grants from federal and/or provincial governments for new infrastructure, or the province grants revenue sharing or new taxation powers to its municipalities.
Regardless of the potential alternatives presented, all options would involve everyone paying for new infrastructure in an equitable
fashion, rather than only burdening the buyers of new homes and further eroding affordability.
There is little doubt that reducing or eliminating development charges will be politically difficult. However, the status quo will only further contribute to affordability challenges, especially for younger people. It is also resulting in diminished housing supply. The situation as it stands is not sustainable. Eventually those who hold true to “growth should pay for growth” will see that path leads to no growth at all. Growth can pay for growth, but it can’t pay for everything..
UNLOCK YOUR POTENTIAL WITH THE ULTIMATE HOME BUILDING AND RENOVATION BUNDLE
Renovators’ Manual
Takes a deep dive into applying building science to renovating for a wide variety of circumstances.
EATON’S
Eaton’s spa panel features a reliable protection for spa pumps and hot tubs. They are designed to save time as our panels are prewired, offering ground fault circuit protection device and a disconnect switch in a single simple device.
EATON eatoncanada.ca
No two businesses are alike, so we take the time to get to know yours. With a dedicated Federated agent and risk management team on your side, you always get personalized service, trusted advice, and tailored protection.
At humm, we provide flexible financing for ecommerce and in-store purchases, up to $30,000. Our completely digital financing option brings a unique blend of benefits designed to propel business growth.
HUMM shophumm.com
FEDERATED INSURANCE federated.ca Let’s
Increase your brand exposure, reach, and impressions with Building Excellence
We can highlight your business, product or service. It’s a great way to get your business the valuable exposure it needs!
Call today to be part of our exciting next issue!
Lisa.kelly@nexthome.ca
Embrace the future with JELD-WEN of Canada’s most energy-efficient window. JELD-WEN of Canada proudly presents the innovative JWC8500 series window, meticulously engineered to exceed customer expectations with the perfect blend of style, performance and energy savings.
JELD-WEN jeld-wen.ca
No one can predict the future of the real estate and construction sector, but you can prepare your business for the best possible outcomes, while capitalizing on opportunities. MNP’s proven track record in this industry ensures you get the innovative business strategies, efficient operations and a tax plan that takes you from where you are to where you want to be.
MNP mnp.ca
Canadian Home Builders’ Association (CHBA) members have been building, developing, and renovating Canadian homes for generations. We are sharing the extraordinary contributions CHBA members make in their communities every day through our ongoing #CdnBuilt for Generations campaign. Here are a few recent stories. To read more stories follow our hashtag or visit chba.ca/giving-back.
In an effort to tackle the skilled trades shortage and support the residential construction industry in their region, BILD Edmonton Metro member Homes by Avi made a five-year, $500,000 investment to support students considering post-secondary studies at Northern Alberta Institute of Technology (NAIT)’s School of Construction and Building Sciences. The funding will provide students who have participated in the Homes by Avi Construction Program at M.E. LaZerte, a local high school, with priority access to financial support to enroll in one of 13 eligible skilled trades programs at NAIT. As a result of the contribution, the students have already started to make their mark, building the first floor of a two-storey home that will be sold to an Edmonton homebuyer, with the proceeds funnelled back into the high school to continue this exciting initiative.
Looking to make a meaningful impact in their community, Mattamy Homes, a member of Greater Ottawa Home Builders’ Association, put its building expertise to work for a good cause. A group of volunteers from Mattamy Homes rolled up their sleeves and spent a day building two new tables and a glider, and repaired existing benches to help transform the community courtyard at an Ottawa Community Housing (OCH) complex. OCH is Ottawa’s largest provider of non-market housing, and the space – which needed a little TLC – is a vital gathering place for tenants of the complex to enjoy outdoor events and connect with each other.
In May 2023, Phil and Sue’s lives were turned upside down when wildfires broke out in Upper Tantallon. Like many families affected by the wildfires who were uninsured or underinsured, they lost their home with little hope of financial recovery. Habitat for Humanity Nova Scotia, a member of CHBA Nova Scotia and their Charity of Choice for 2024-25, partnered with the Canadian Red Cross and United Way Maritimes to help them rebuild. After a year and a half of being displaced, Phil and Sue are on track to be in their home just in time for Christmas. With the unwavering support of community partners, generous donors and dedicated volunteers, including other CHBA-NS members Matheson Windows and Doors, Ritchies Flooring, and Ocean Contractors Ltd., Habitat for Humanity Nova Scotia helped this family, along with many others across the province, have a safe place to call home.
DURABLE AND LOW-MAINTENANCE
VINYL AND ALUMINUM CONSTRUCTION
ALUMINUM-CLAD EXTERIOR, OFFERED IN AN ATTRACTIVE SELECTION OF COLOURS
SLEEK, LOW-PROFILE HARDWARE DESIGN
ENERGY-EFFICIENT DUAL-PANE AND TRI-PANE LOW-E GLASS OPTIONS
26% LOWER PROFILE FRAME INCREASES GLASS AREA
UP TO 22% BETTER ENERGY EFFICIENCY
With the unique changes of our Canadian climate, the demand for energy-efficient products that can stand up to the elements is higher than ever. JELD-WEN of Canada proudly introduces the groundbreaking JWC8500 series window —a perfect blend of style, performance, and energy savings, meticulously engineered to exceed expectations. Our newest JELD-WEN® window, the JWC8500 hybrid option exceeds performance, in all regions of Canada, offering an aluminum-clad exterior finish with an exquisite selection of colours to choose from.
Discover the advantages of JELD-WEN of Canada’s most energy-efficient window. Our 8500 series windows are 2030-rated to meet Canada’s U-Factor 0.14 (U.S./I-P) / 0.82 (Metric/SI) or ER 44 building codes, and are designed to significantly reduce energy costs while ensuring year-round comfort in your home.
Tailored to meet the regional needs of homeowners, our windows are the perfect fit when planning a renovation or new home build, seamlessly blending functionality and style to suit any project.
Discover the JWC8500 series window from JELD-WEN of Canada—and experience the future of home comfort and efficiency.
LEARN MORE TODAY jeld-wen.ca
Your business. Your future. Our focus.
No one can predict the future of the real estate and construction sector, but you can prepare your business for the best possible outcomes, while capitalizing on opportunities. MNP’s proven track record in this industry ensures you get the innovative business strategies, efficient operations and a tax plan that takes you from where you are to where you want to be.