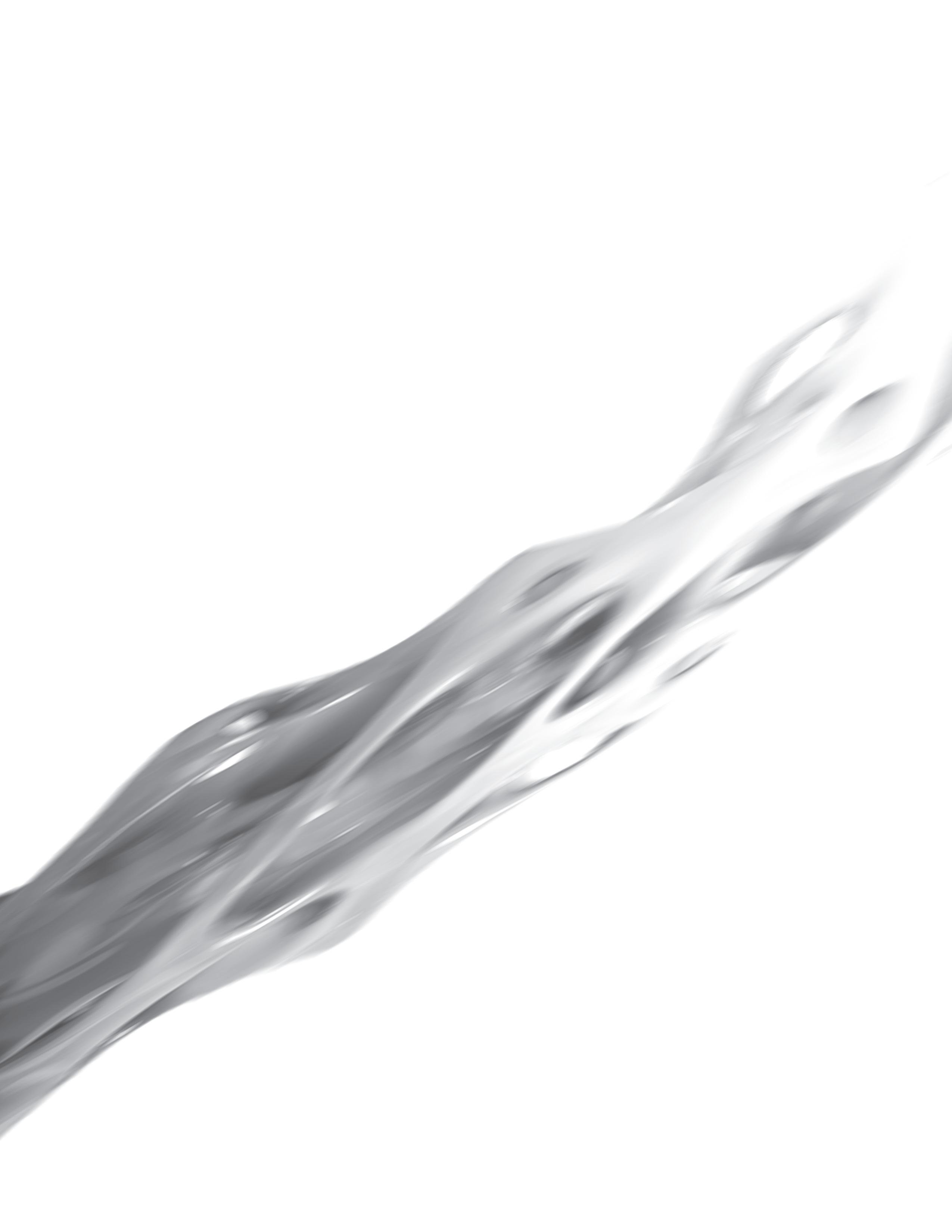
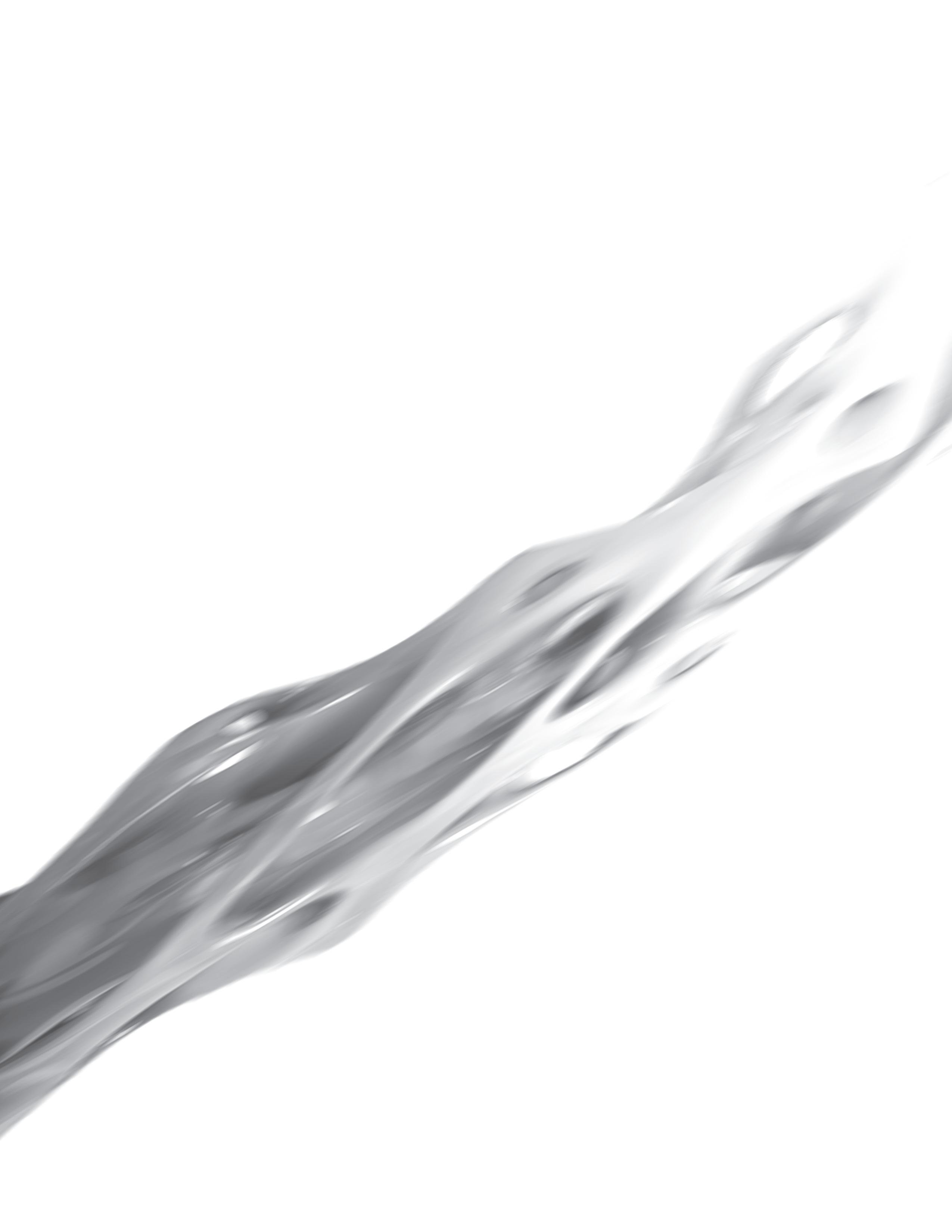
WORK SAMPLE
WEI-CHIEH WANG
wangweichieh821024@gmail.com
https://www.linkedin.com/in/arch-wangweichieh/ (626) 383-9145 Los Angeles, CA 90005
https://issuu.com/wangweichieh/docs/portfolio_wei-chieh_wang
BINHAI BAY OUTLET
PROFESSIONAL PROJECT
PROJECT INFORMATION
Architect: Gianni Ranaulo Design
Type: Shopping Mall (1,156,500 SF)
Location: Dongguan, China
ROLE
Project Designer (Involved in SD and DD)
RESPONSIBILITIES
• Parametric Optimization
• Concept Rendering
• Facade Design
• Technical Drawings
• BIM
PROGRAMS USED
Revit, Rhinoceros, Grasshopper, AutoCAD, Enscape
ROLE ON PROJECT
Gianni Ranaulo Design proposed a shopping mall comprising three distinct areas: “Ring,” “Cluster,” and “Mall,” which together foster a new luxury lifestyle and shopping experience. I joined the project at the latter stage of the SD phase, primarily focusing on developing the five-story “Mall” section, encompassing 788,700 square feet, through to the DD phase. My role involved close collaboration with the LDI to adjust plans and elevations in compliance with building codes, which required meticulously examining structural and mechanical drawings to detail tectonic connections accurately. I also developed scripts to modularize and planarize the curved elements into a feasible design, such as the curtain wall and skylight. Additionally, I proposed several shading canopies at the outdoor junctions to enhance the overall architectural design.
A Floor plans
B Custom Revit family
C Aerial rendering
D-E Design iteration of parametric canopies
F Modularized and planarized solar panels on a free-form surface using Grasshopper to cut costs
G Interior design
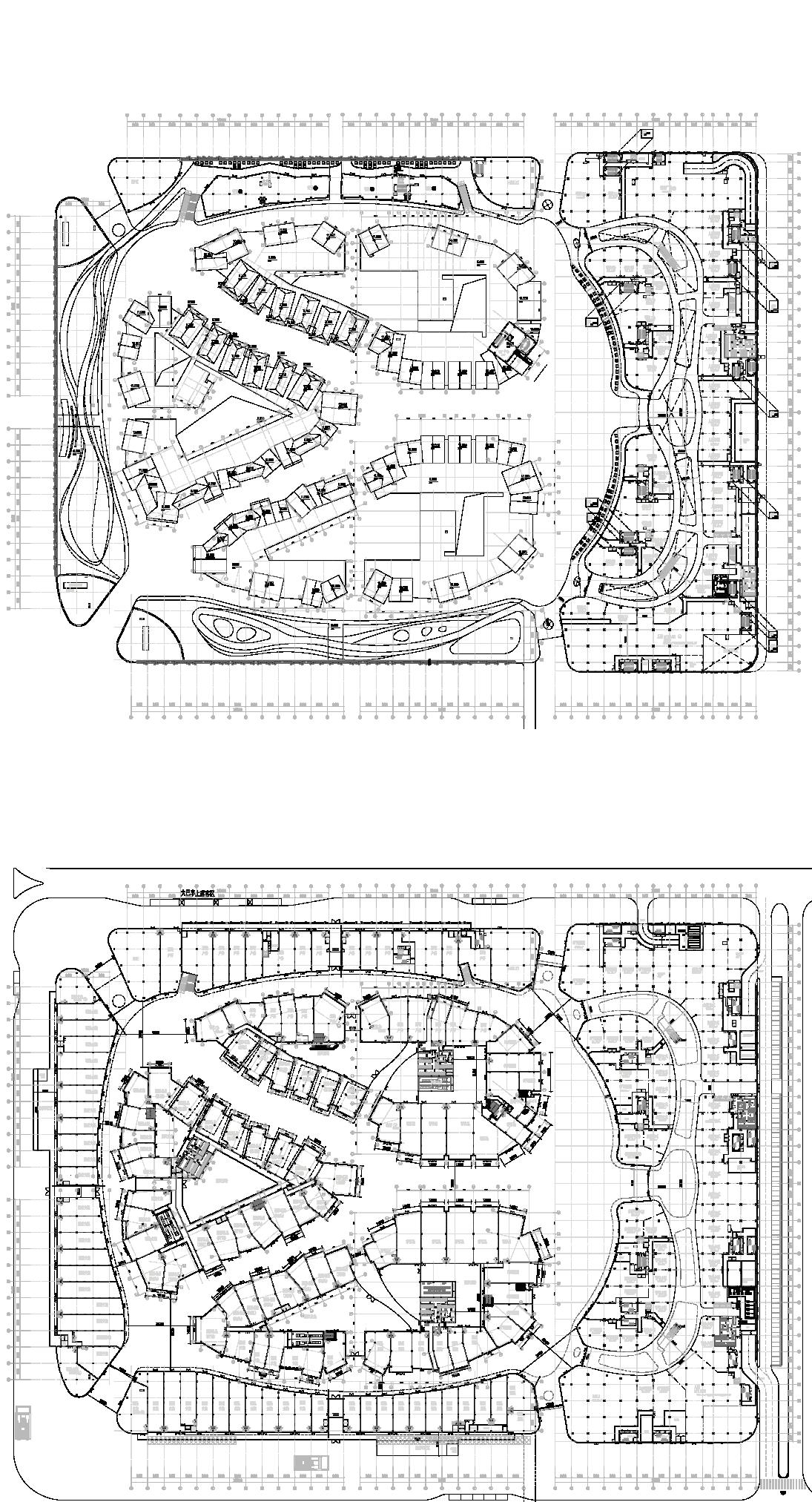
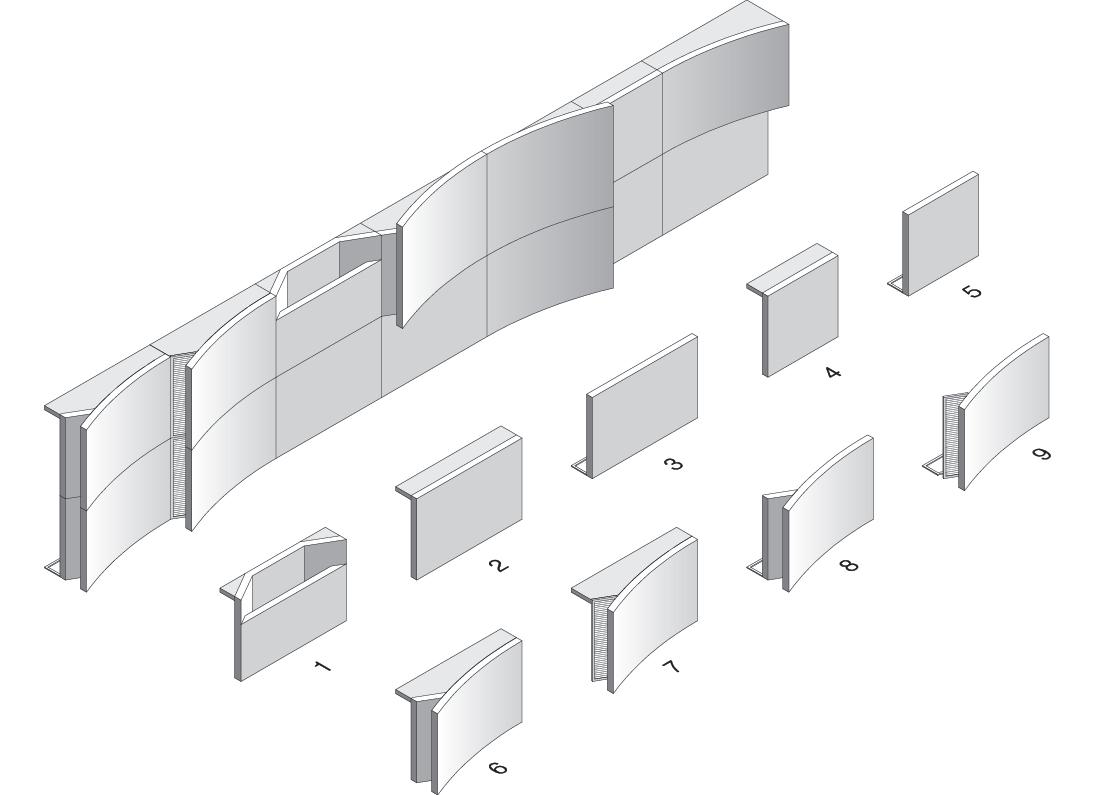
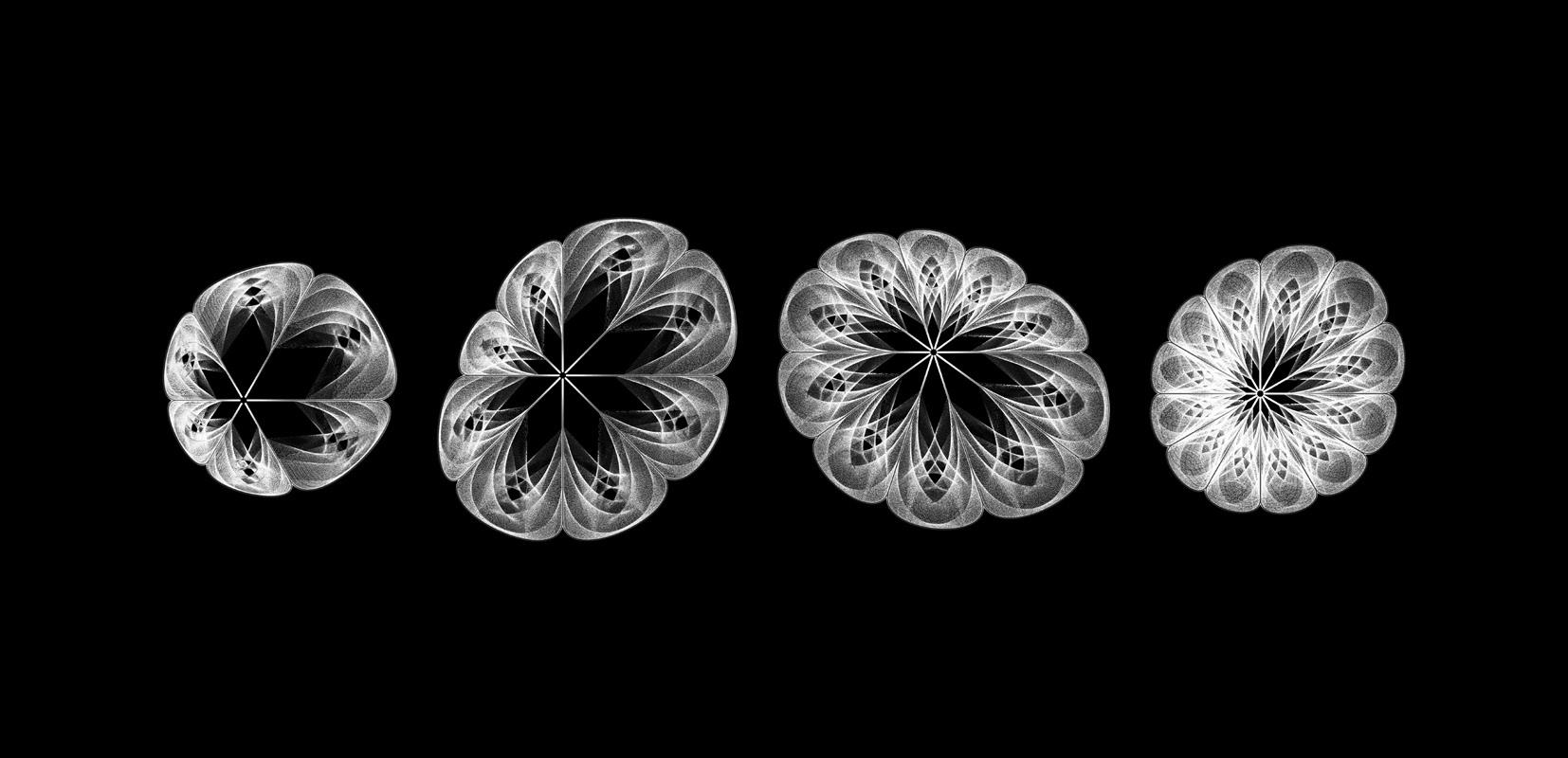
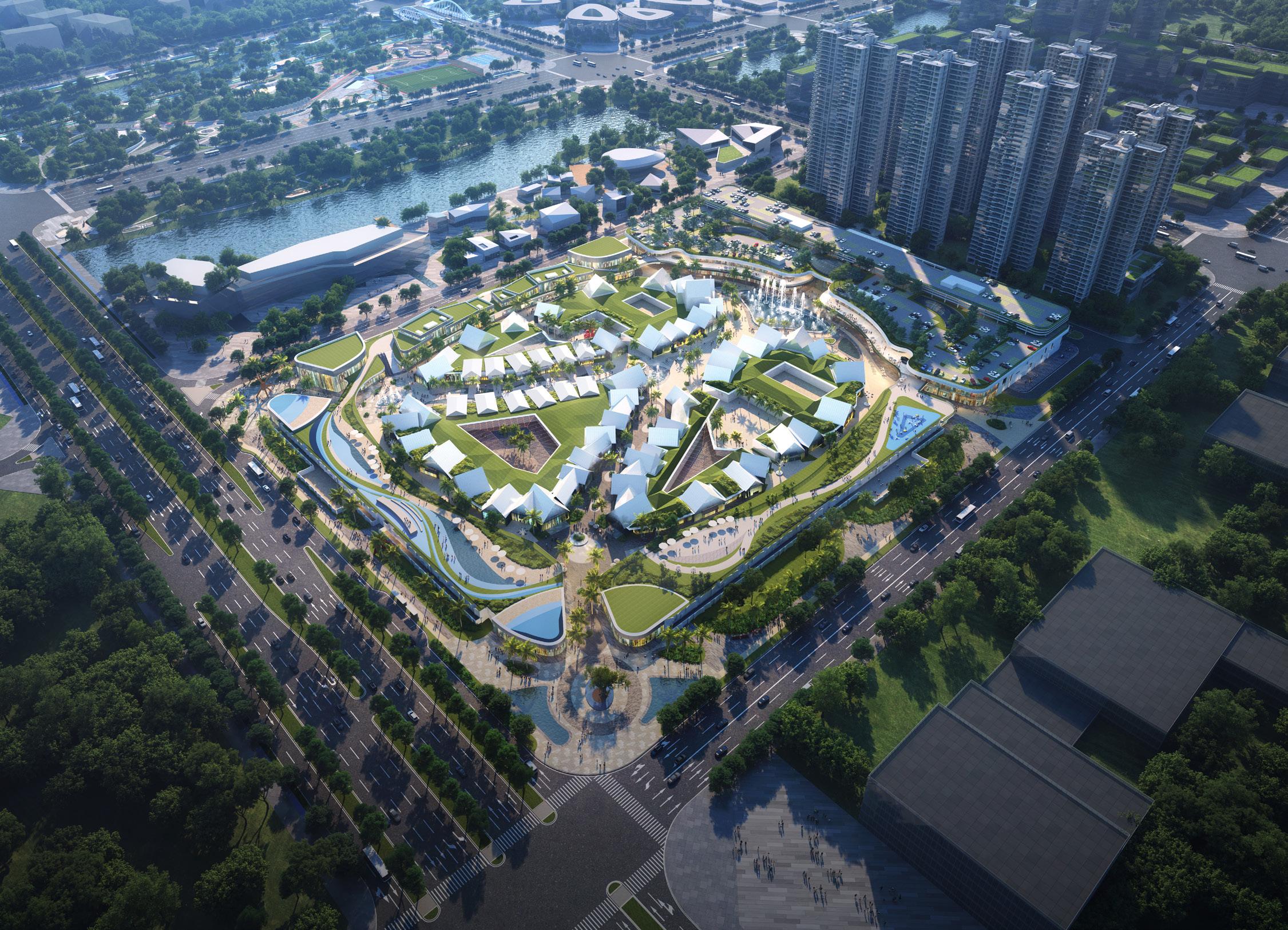
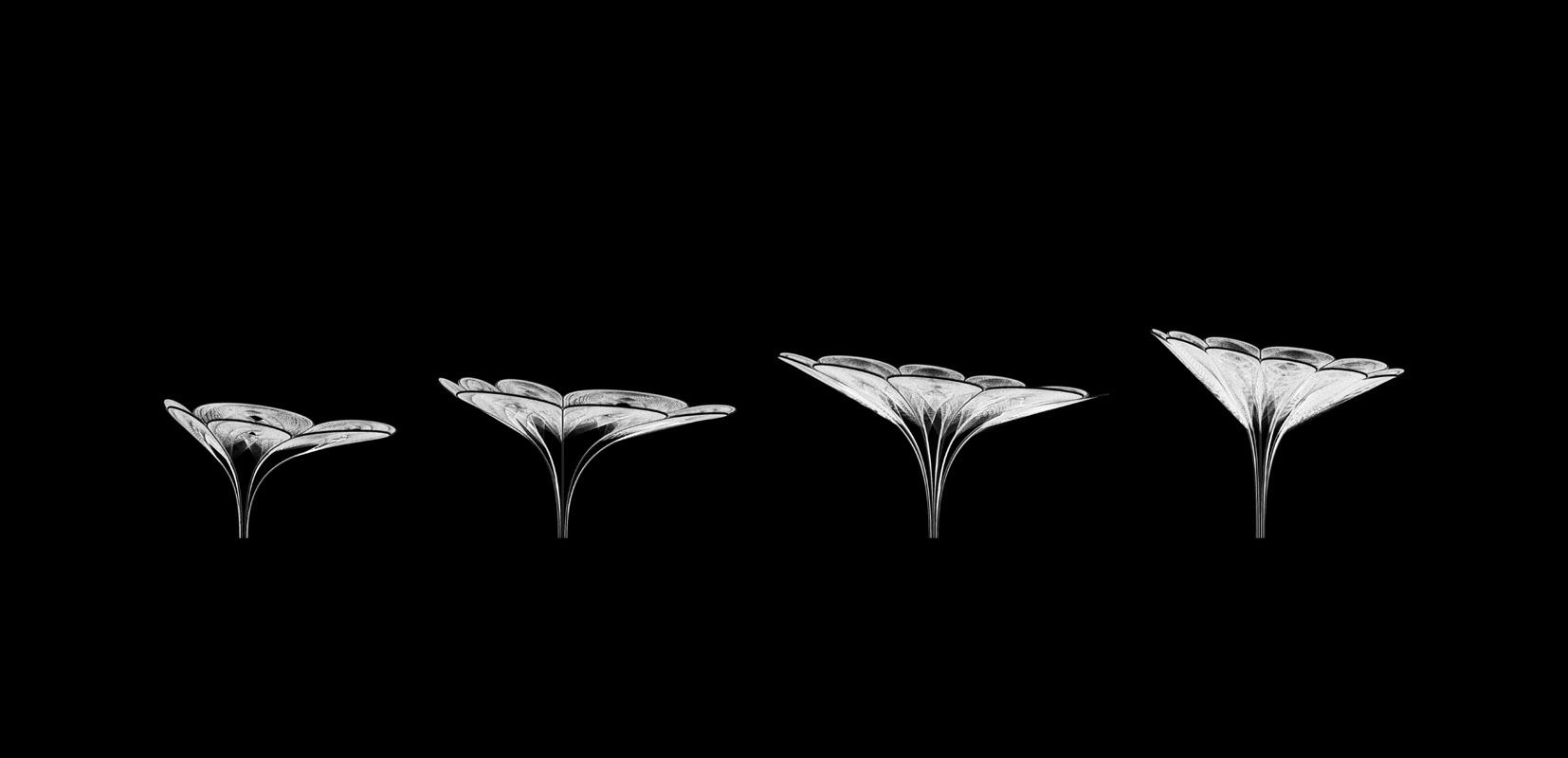


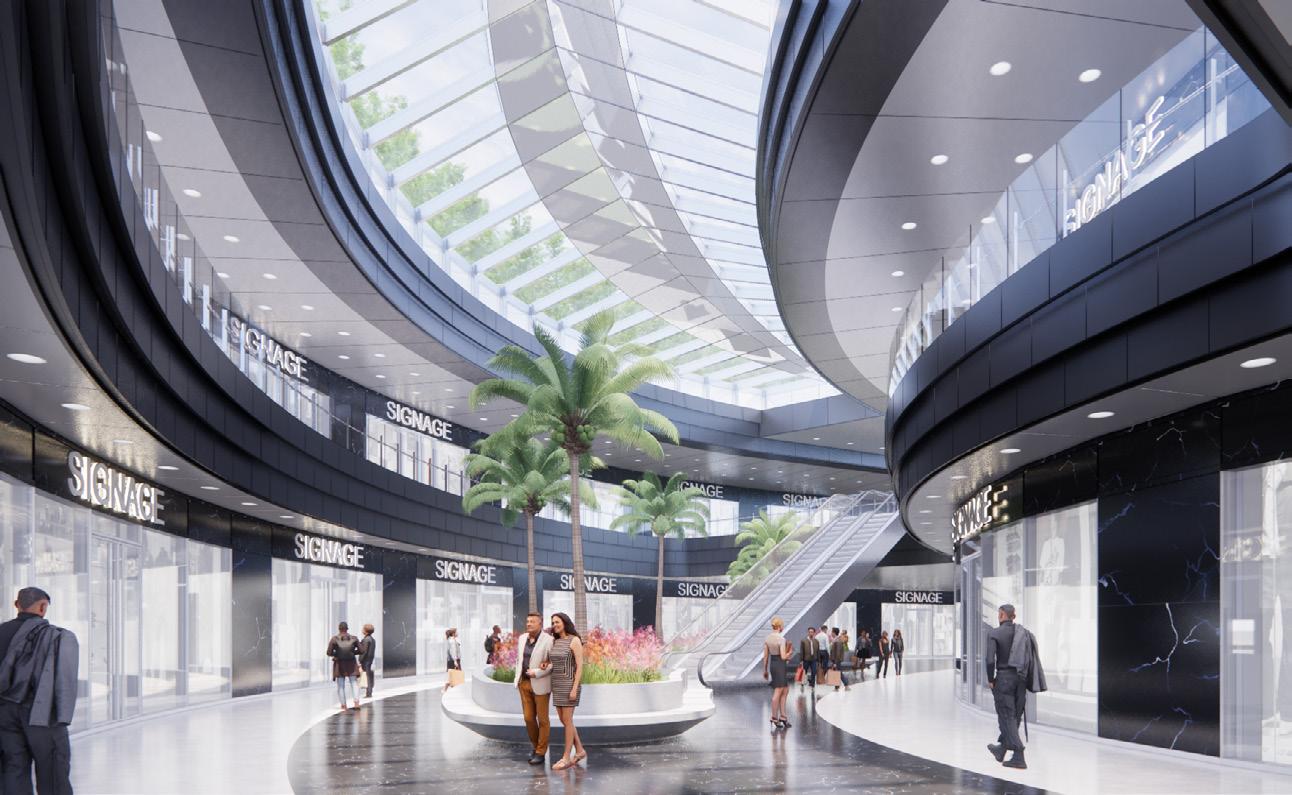
APARTMENTS ON SPRING ST
PROFESSIONAL PROJECT
PROJECT INFORMATION
Architect: Gianni Ranaulo Design
Type: Low-rise Apartments (165 Units)
Location: Los Angeles, CA
ROLE
Project Designer (Involved in SD)
RESPONSIBILITIES
• Massing Study
• Space Planning and Programming
• Facade Design
• Concept Rendering
• Circulation Analysis
ROLE ON PROJECT
Situated in Los Angeles’ Chinatown, this apartment complex serves as a tranquil retreat, offering residents a peaceful living environment far removed from the city’s daily commotion. I was involved in the project from the pre-design phase, beginning with a massing study and transitioning to various unit types’ designs. My role in this project included space planning and programming tailored to the client’s requirements. Concurrently, I crafted a coherent circulation system to efficiently organize the movement of tenants and vehicles across different spaces. After finalizing the spatial layout, I proposed designs for the internal facade and courtyard. Additionally, I contributed to design decisions and assisted in producing presentation materials for client meetings, including site analysis, plans, sections, elevations, area matrices, and renderings.
PROGRAMS USED
Rhinoceros, AutoCAD, Enscape
A Floor plans with unit labels
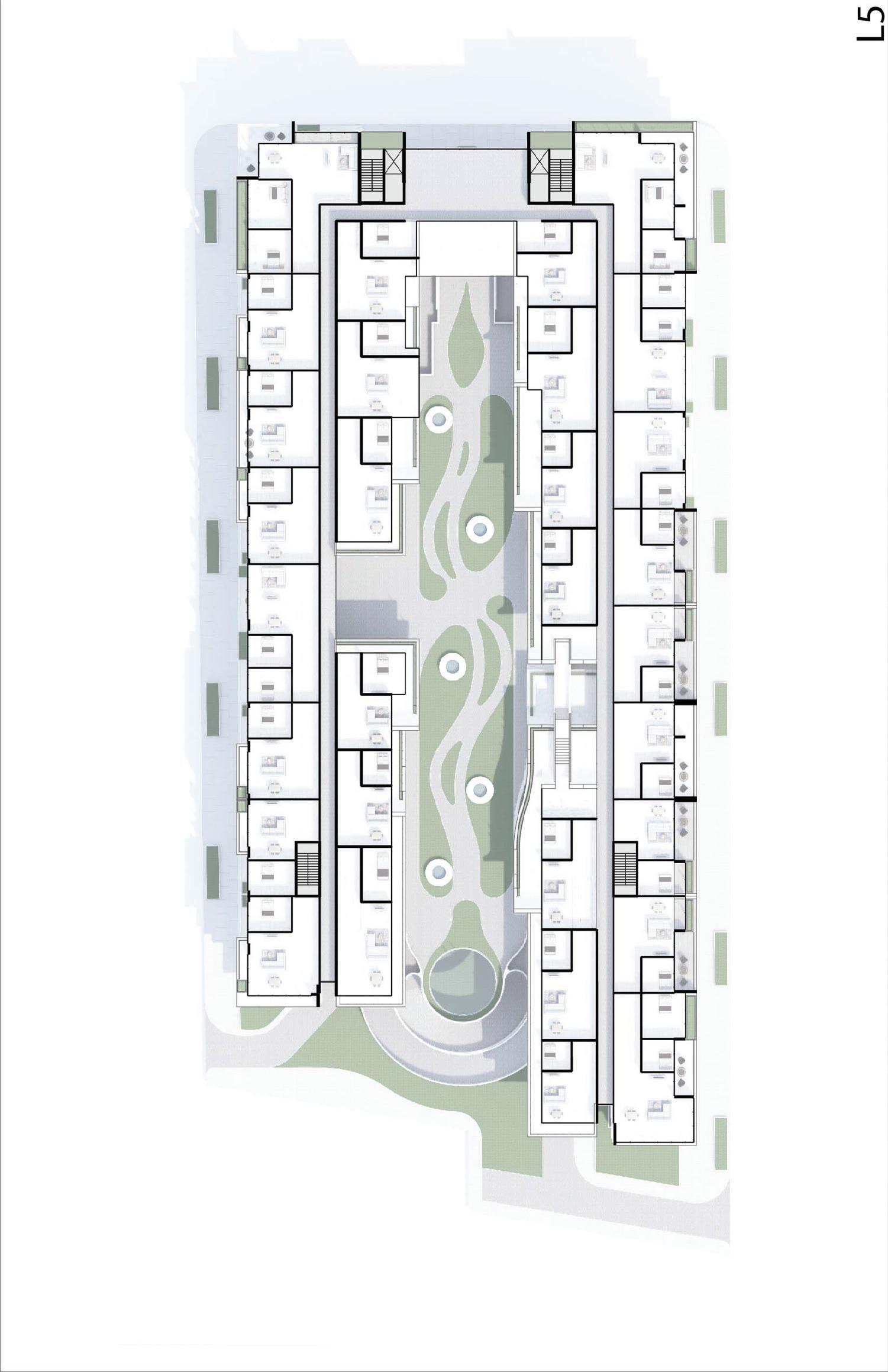
B Car parking layout and circulation design per the Los Angeles Municipal Code
C-D External facade design iteration
E-F Internal facade and courtyard design iteration
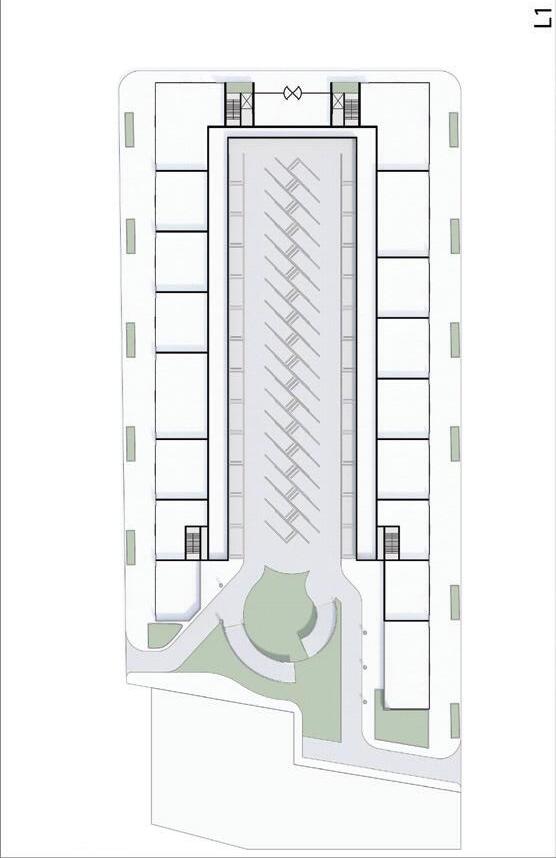
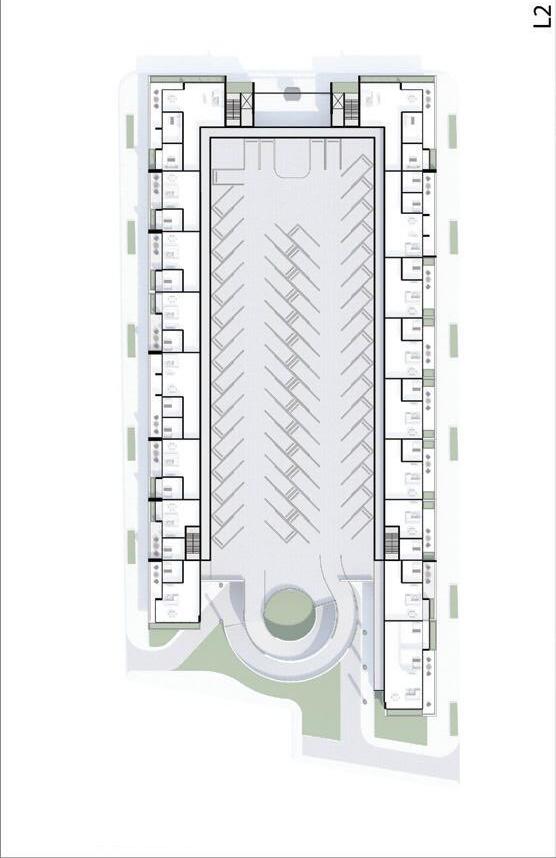
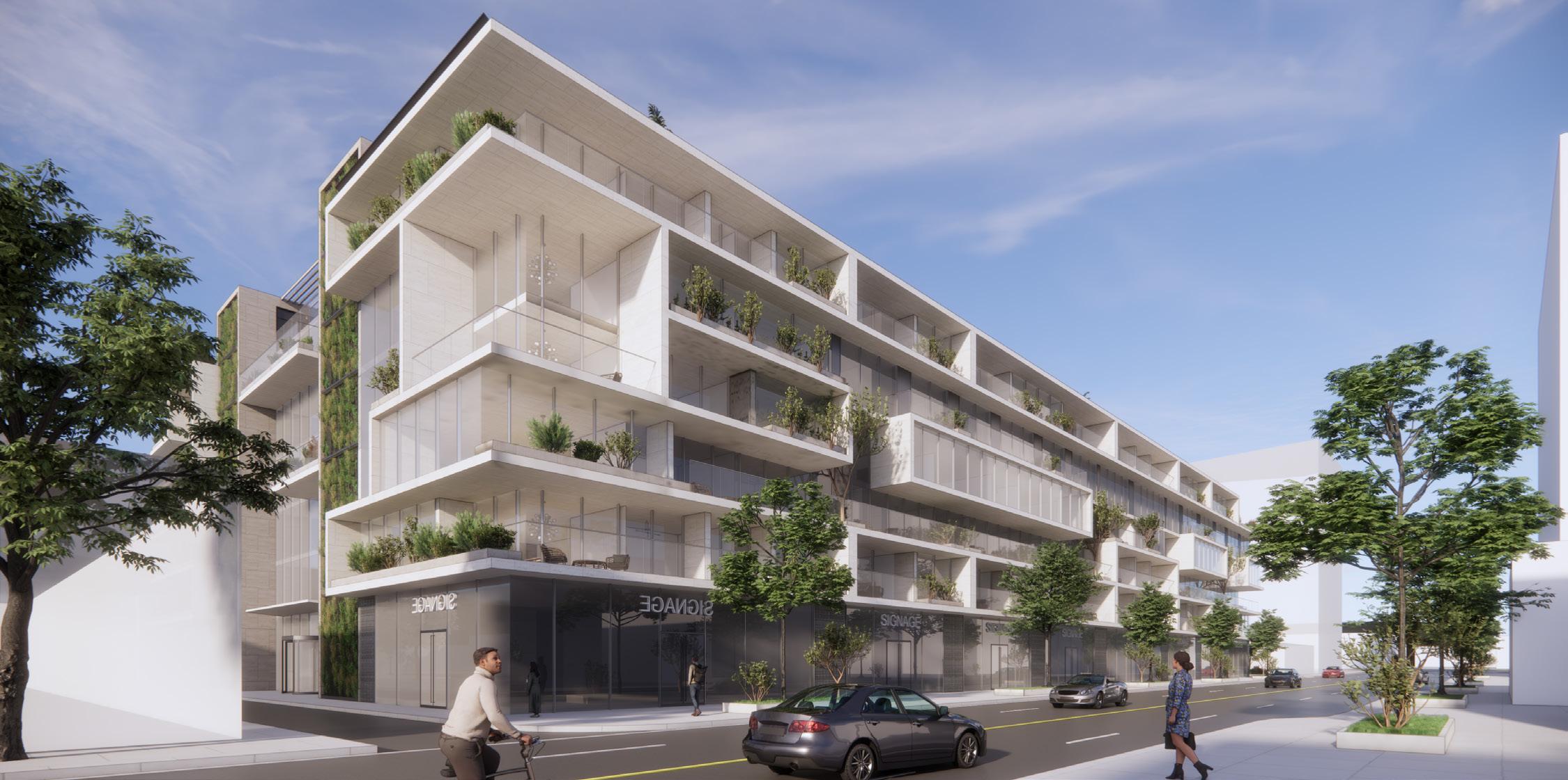
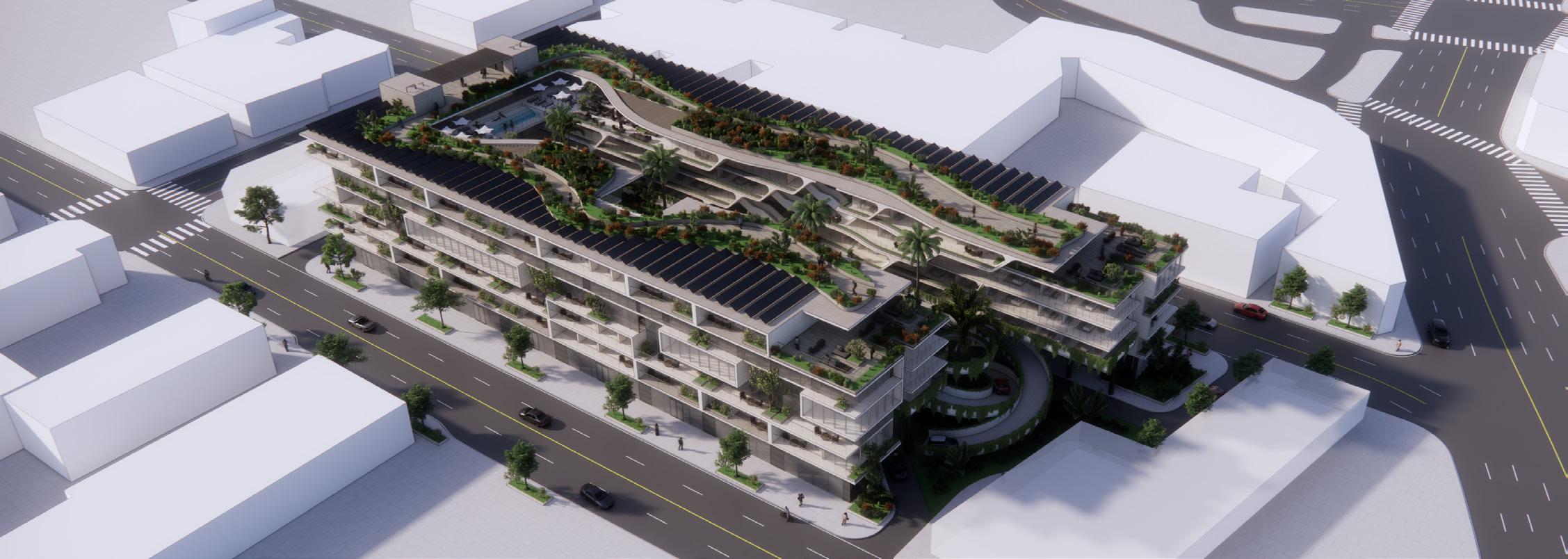
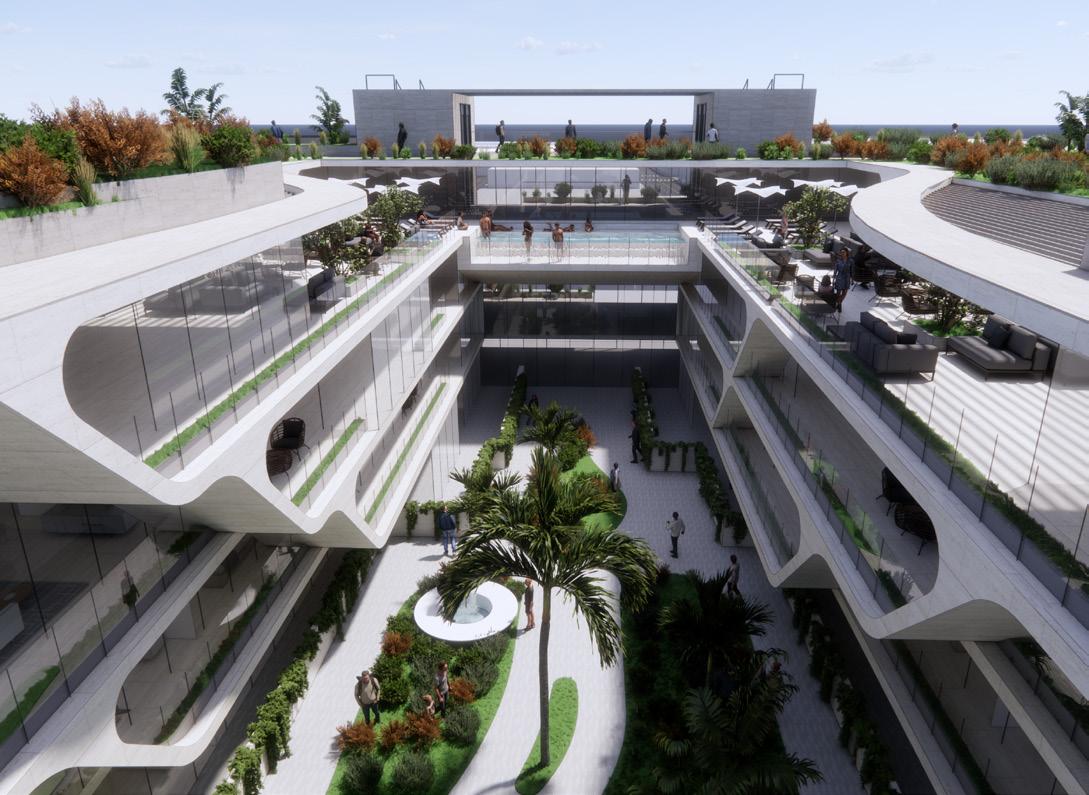
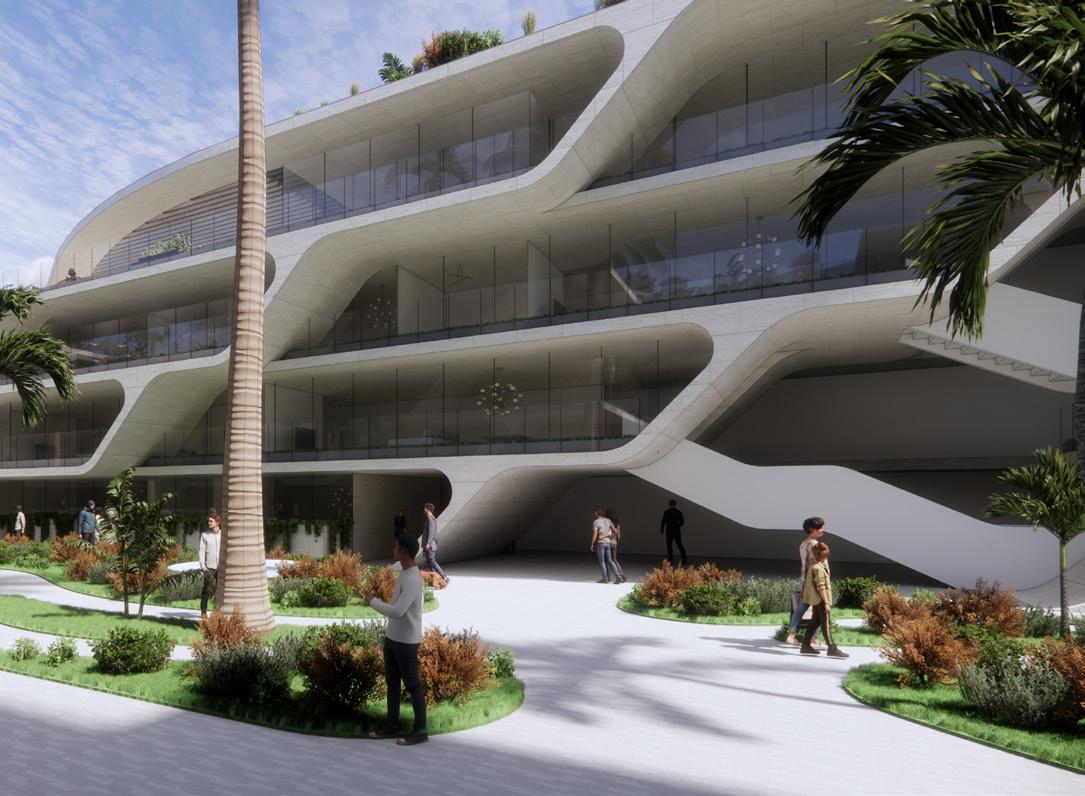
PROFESSIONAL PROJECT
PROJECT INFORMATION
Architect: MHC Architects
Type: Institutional - University (1,250 SF)
Location: Taipei, Taiwan
ROLE
Project Designer (Involved in SD, DD, CD, Bidding, CA)
RESPONSIBILITIES
• Parametric Optimization
• Sustainable Strategies
• Detail Development and Specifications
• Client and Consultation Coordination
• Permit Set and Construction Documents
• Cost Estimation
• Site Observation
ROLE ON PROJECT
The sky bridge connected the north and south halls of the Department of Psychology at National Taiwan University. I was the leading designer working on this project. Therefore, I gained comprehensive exposure to all design phases, rapidly acquiring knowledge of the relevant codes and regulations. Collaborating closely with the principal, I helped transform the project into a feasible proposal. My efforts were focused on enriching the design’s character and tectonic expression to complement the historic campus. Specifically, I scripted the free-form shell, managed the detailed design, conducted area analyses, wrote specifications, estimated construction costs, prepared the permit set and construction documents, and performed site observations.
PROGRAMS
USED
Rhinoceros, Grasshopper, AutoCAD
A Sections for the permit set
B Building plans based on the design concept and existed building conditions
C Detail development in close coordination with structural engineers and MEP consultants
D-F Photographs of the completed skybridge
G Construction site observation
H Mock-up testing and review during the construction administration phase
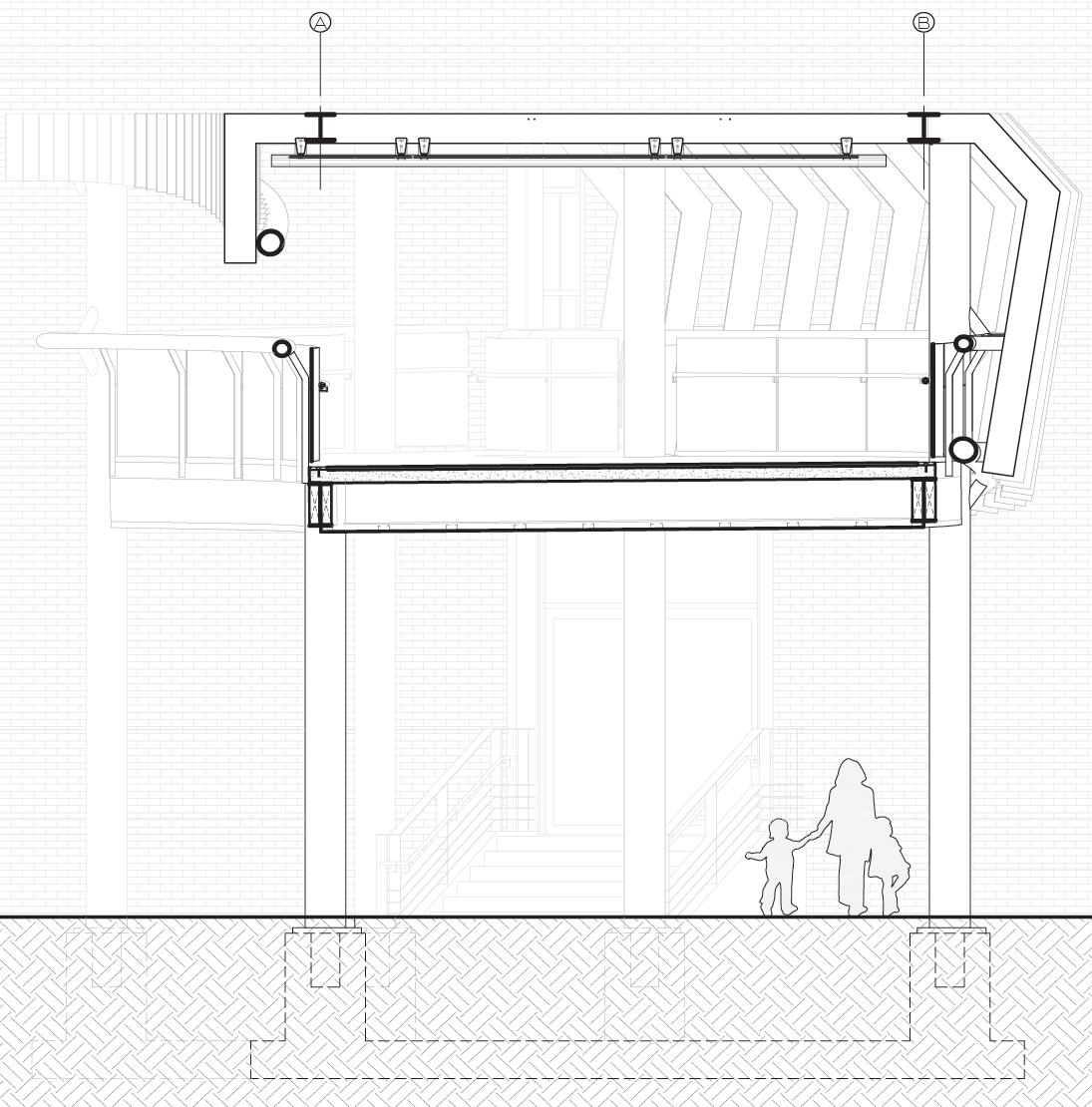
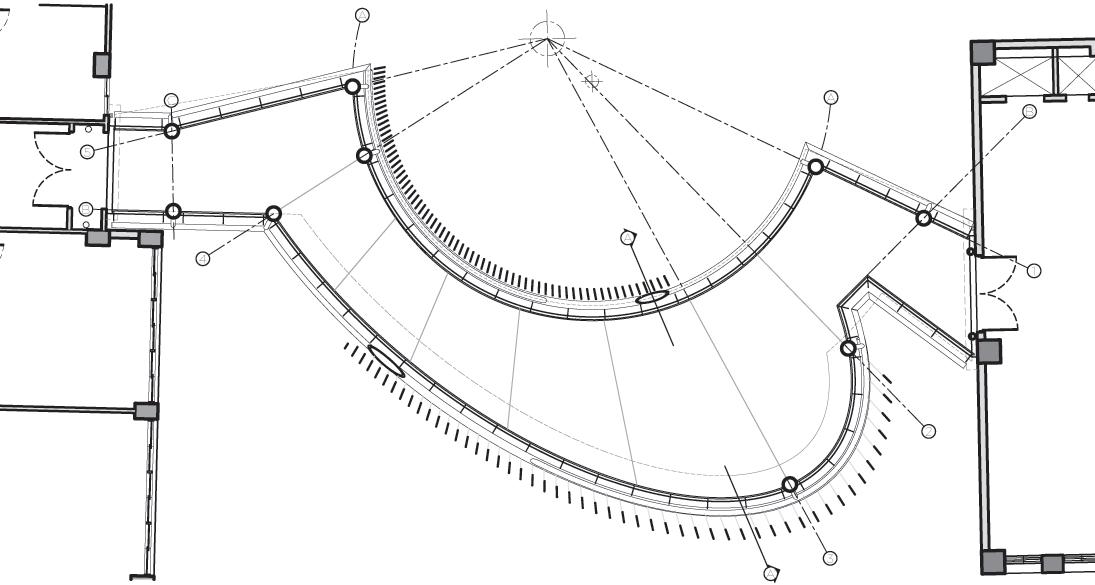
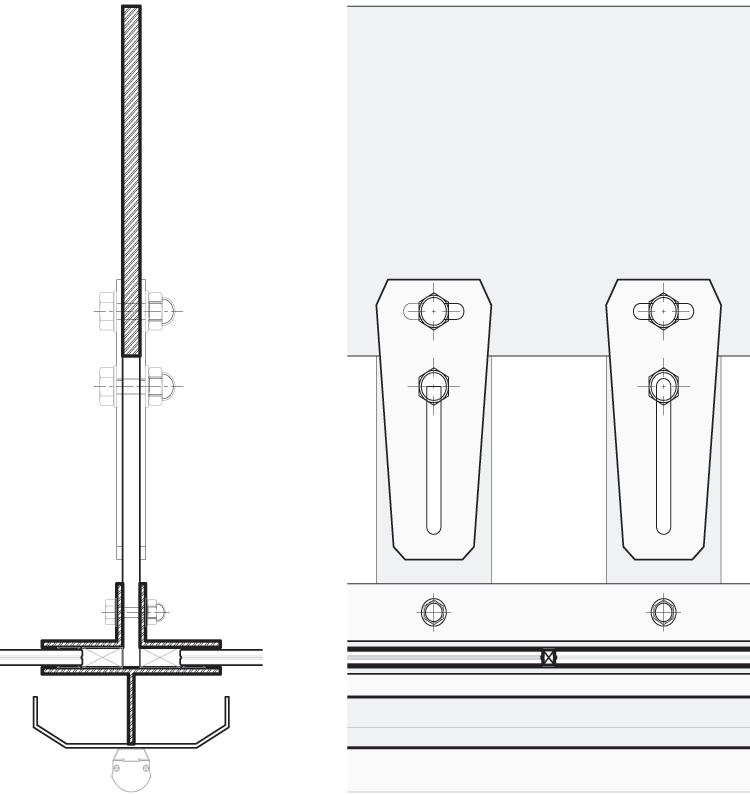
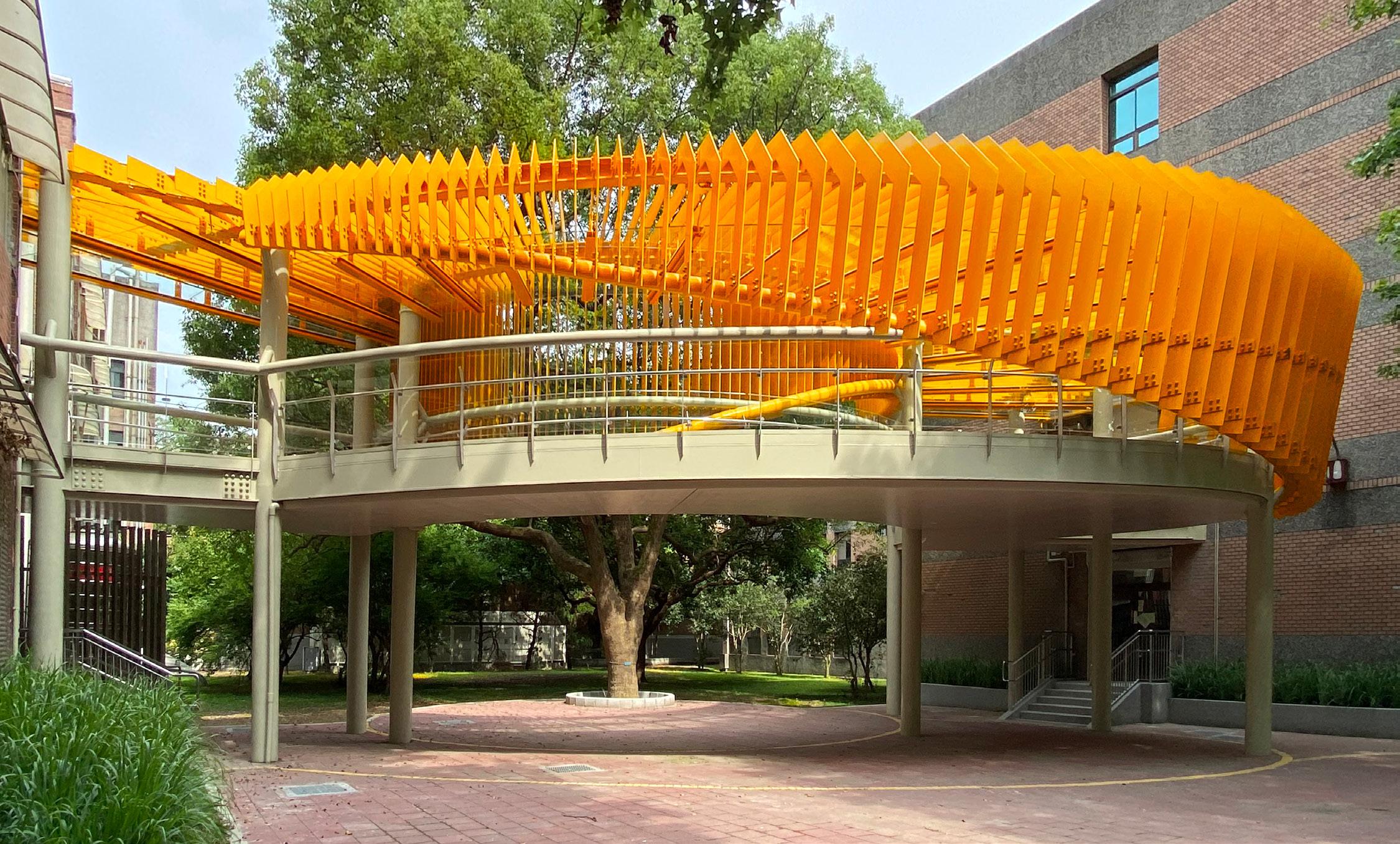
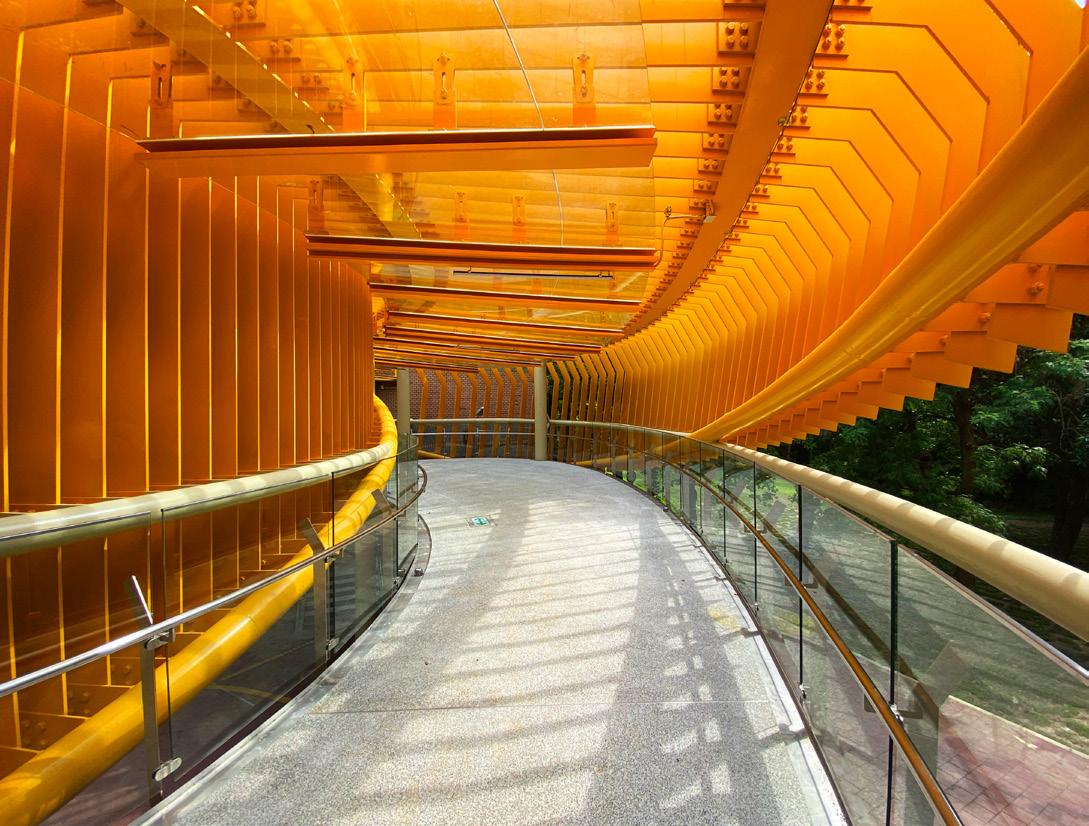
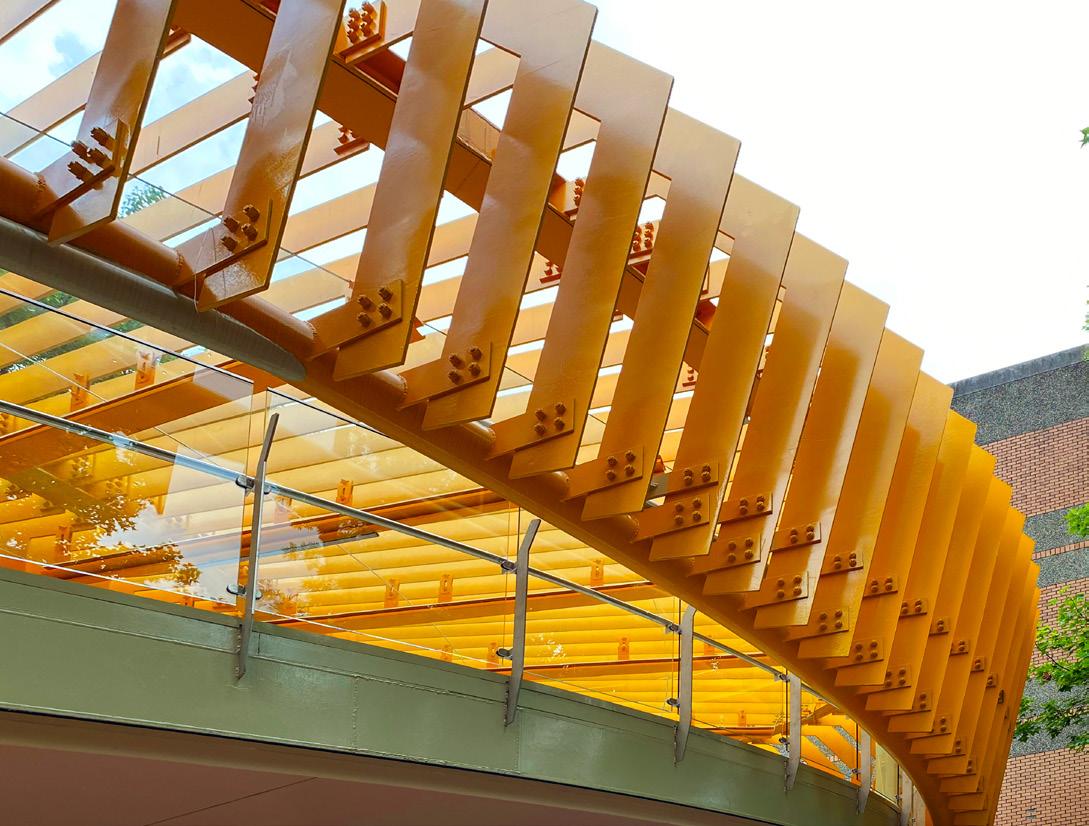
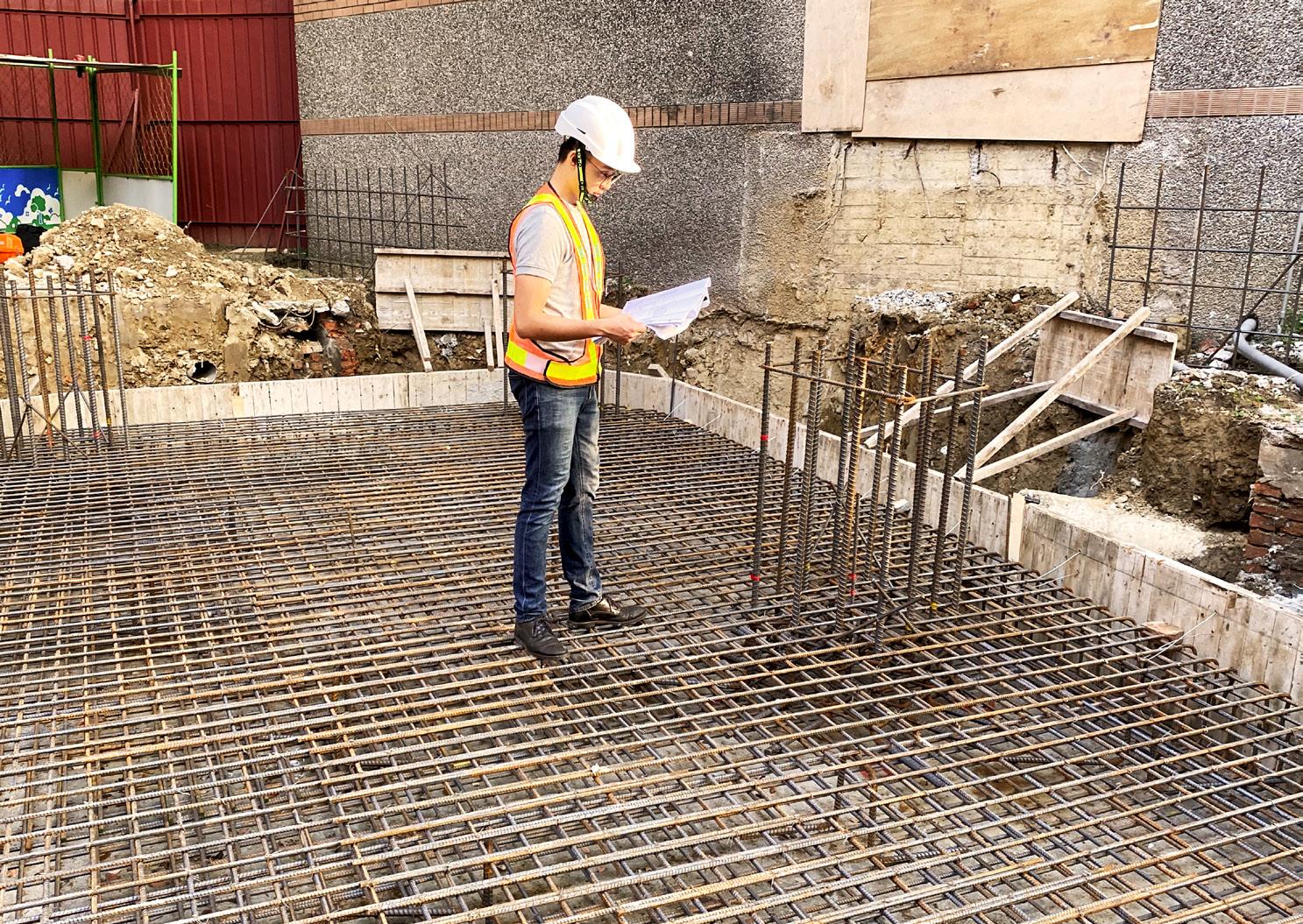
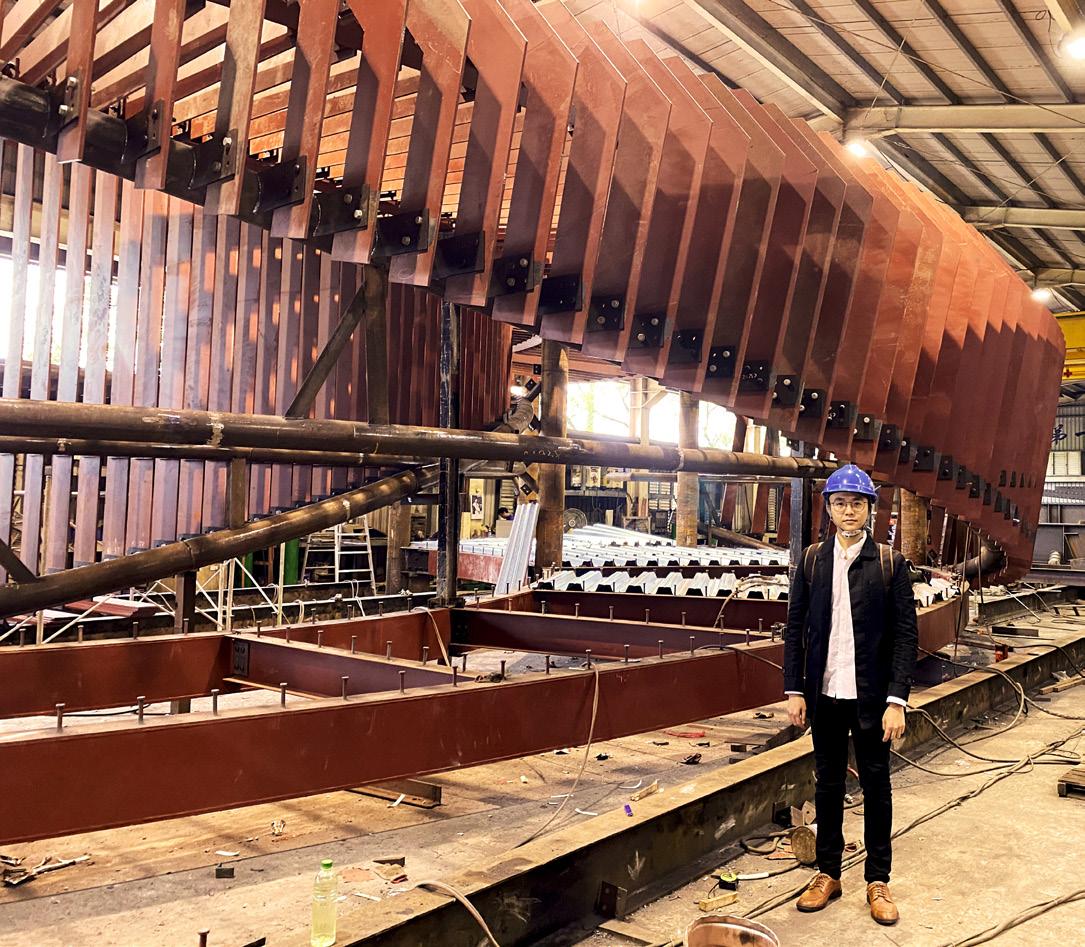
LONG-CI COMMUNITY CENTER
PROFESSIONAL PROJECT
PROJECT INFORMATION
Architect: MHC Architects
Type: Civic - Community (19,950 SF)
Location: Taoyuan, Taiwan
ROLE
Project Designer (Involved in SD, DD, CD)
RESPONSIBILITIES
• BIM Management
• Sustainable Strategies
• Permit Set
• Construction Drawings
• Consultation and Client Coordination
ROLE ON PROJECT
The design goal for the community center was to create a signature public space where citizens could exercise. I joined the project during the pre-design phase to manage the Revit model through to the CD phase. With only myself and a project architect unfamiliar with Revit on this project, I assumed responsibility for documentation and integrating design strategies using Revit. This BIM integration required coordinating with the structural engineer and curtainwall manufacturer to accurately detail the relationships between each sloping roof and curtain wall. To attain EEWH Silver certification, I proposed sustainable strategies focusing on energy efficiency and material selection. For instance, I utilized the roof to exhaust heat to improve climate control. Additionally, I contributed to design decisions and presented our progress in client meetings.
PROGRAMS USED
Revit, Lumion
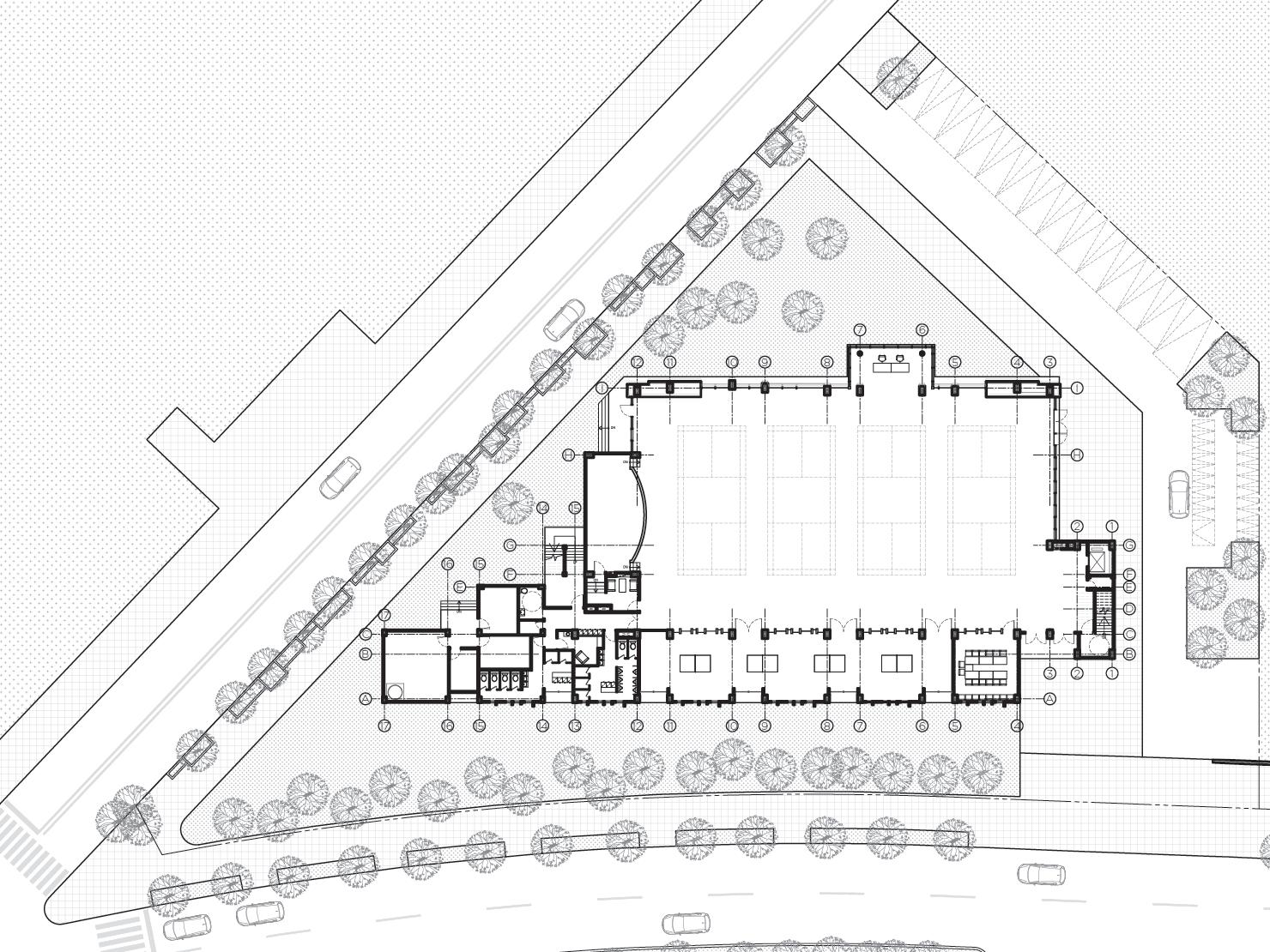
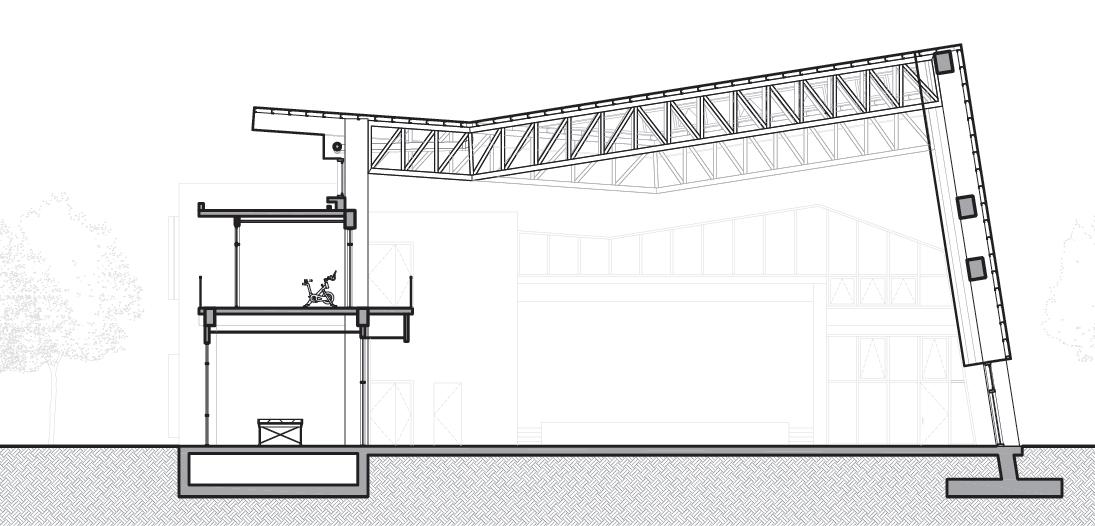
C Sustainable roof detail development in close collaboration with material suppliers, structural engineers, and MEP consultants
D-E Conceptual renderings using Lumion
F Room tags and area schudeules in Revit

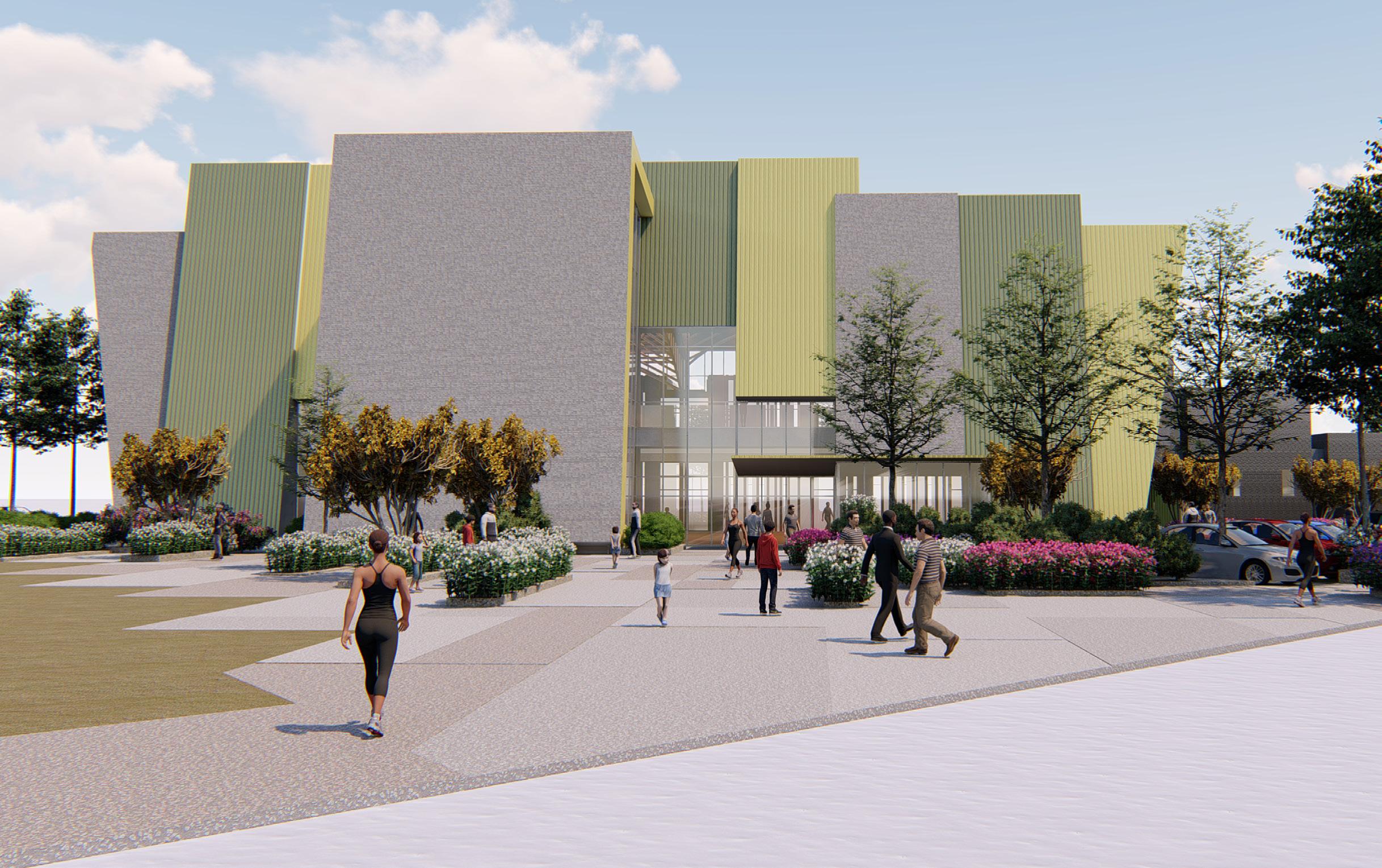
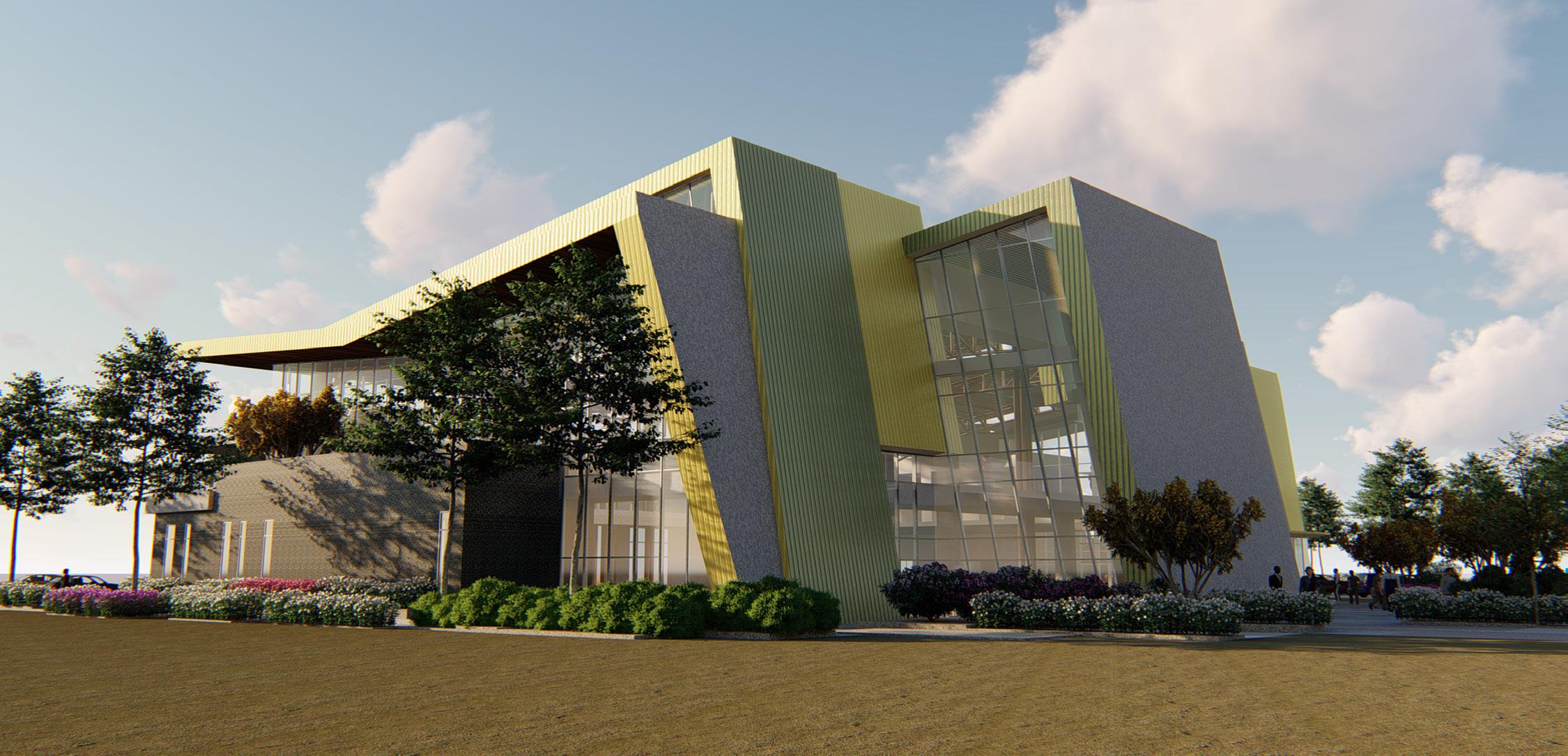
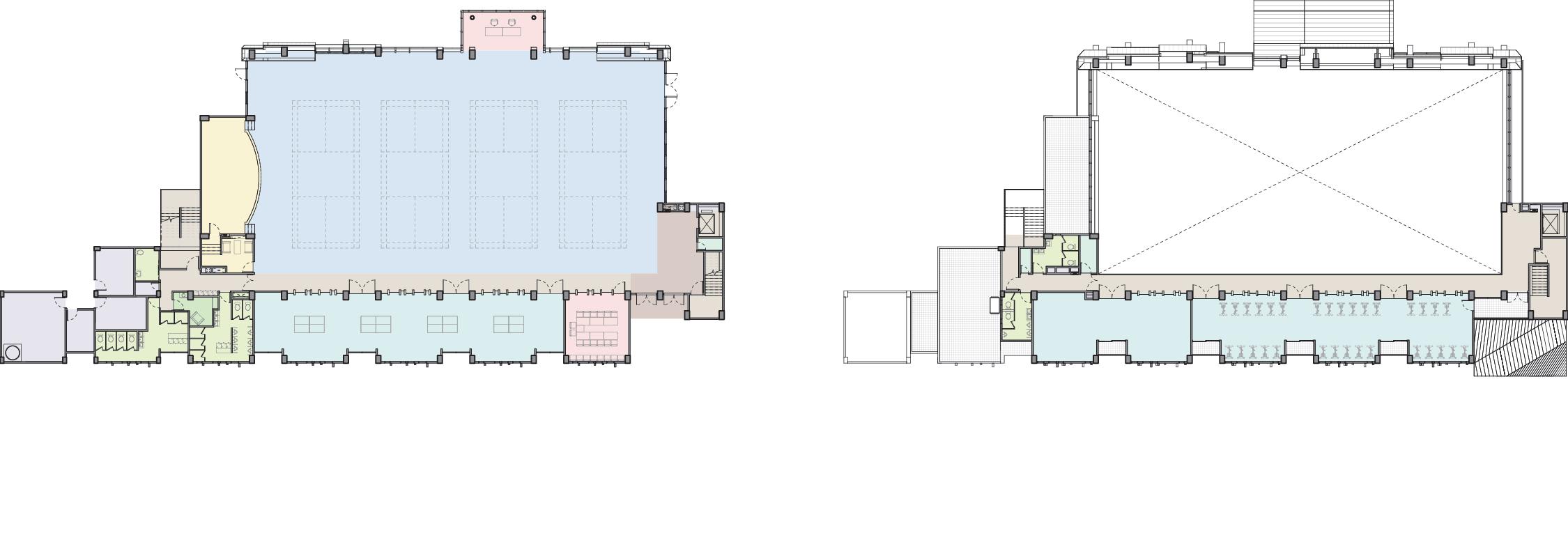
SHOPPING UNIVERSE
ACADEMIC PROJECT
PROJECT INFORMATION
Graduate Thesis Design, SCI-Arc, 2023
Instructor: Elena Manferdini
Partner: Meng-Jung Ho
Location: Los Angeles, CA
DESIGN CONCEPT
We investigated the intricate relationship between consumption and manufacturing, illuminated by globalization. The concealed transportation process behind consumption revealed that most consumers are unaware of a product’s entire lifecycle at the point of purchase. This consumption pattern led to an oversight of the pollution and waste generated throughout the complex manufacturing and transportation chain.
In light of the mall’s contribution to significant waste, we recognized the need to scrutinize the spectacle of consumerism. Hence, our shopping center design integrated three fundamental elements: the production space, the commercial space, and the third place. These areas were seamlessly blended with a pivotal concept: a community-based recycling system, fostering a dynamic and symbiotic environment.
By unveiling the lifecycle of products, our shopping mall design championed environmentally responsible building practices. It introduced a circular production chain that encouraged a symbiotic relationship between production and consumption, aiming for sustainability.
PROGRAMS USED
Rhinoceros, Grasshopper, AutoCAD, Unreal Engine
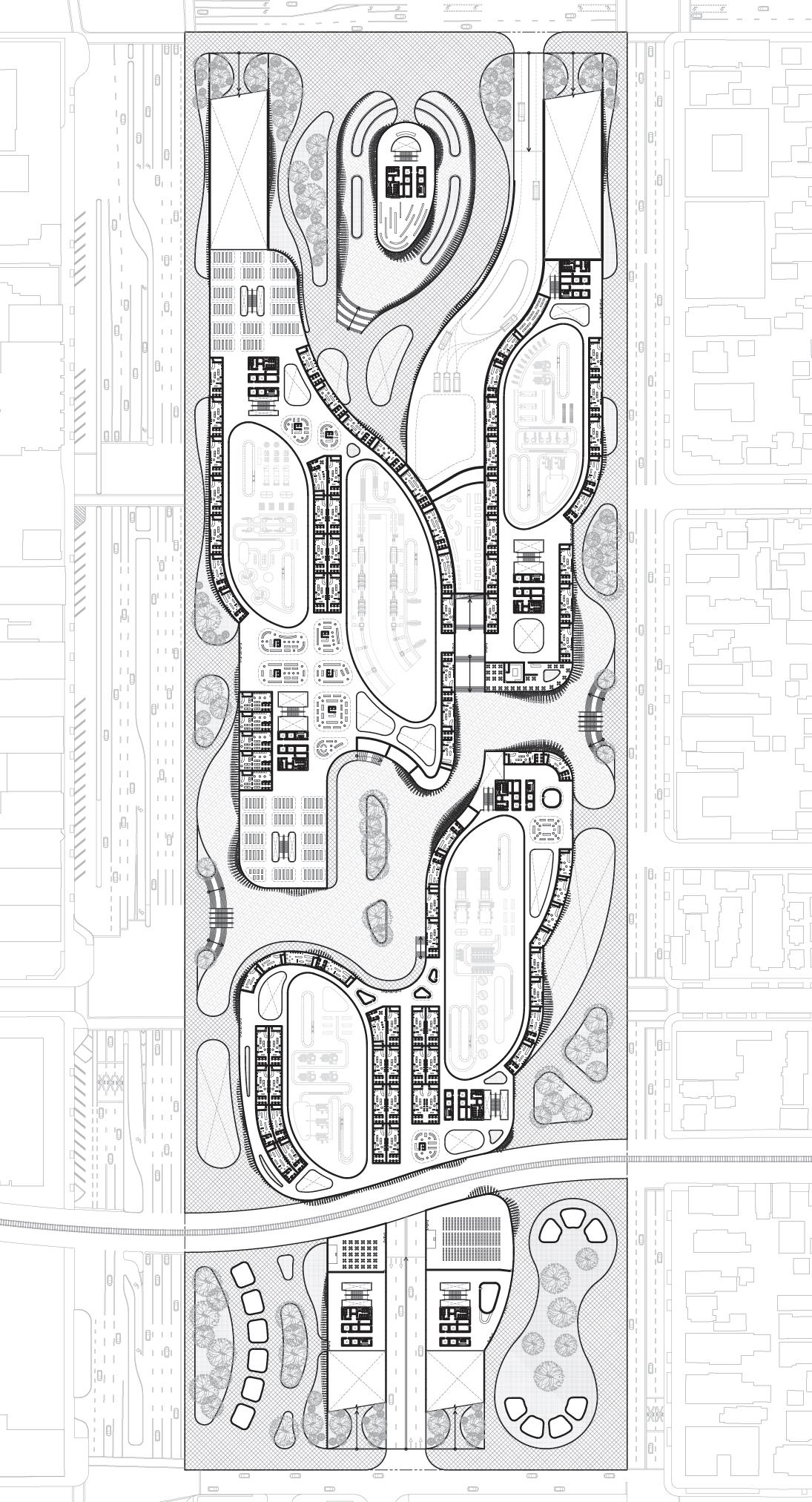
A Ground floor plan highlighted the circulations
B Glass reprocessing facility diagram illustrated the equipment and spatial configuration
C Aerial rendering in Unreal Engine
D Close-up rendering
E Parametric facade comprised of recycled materials
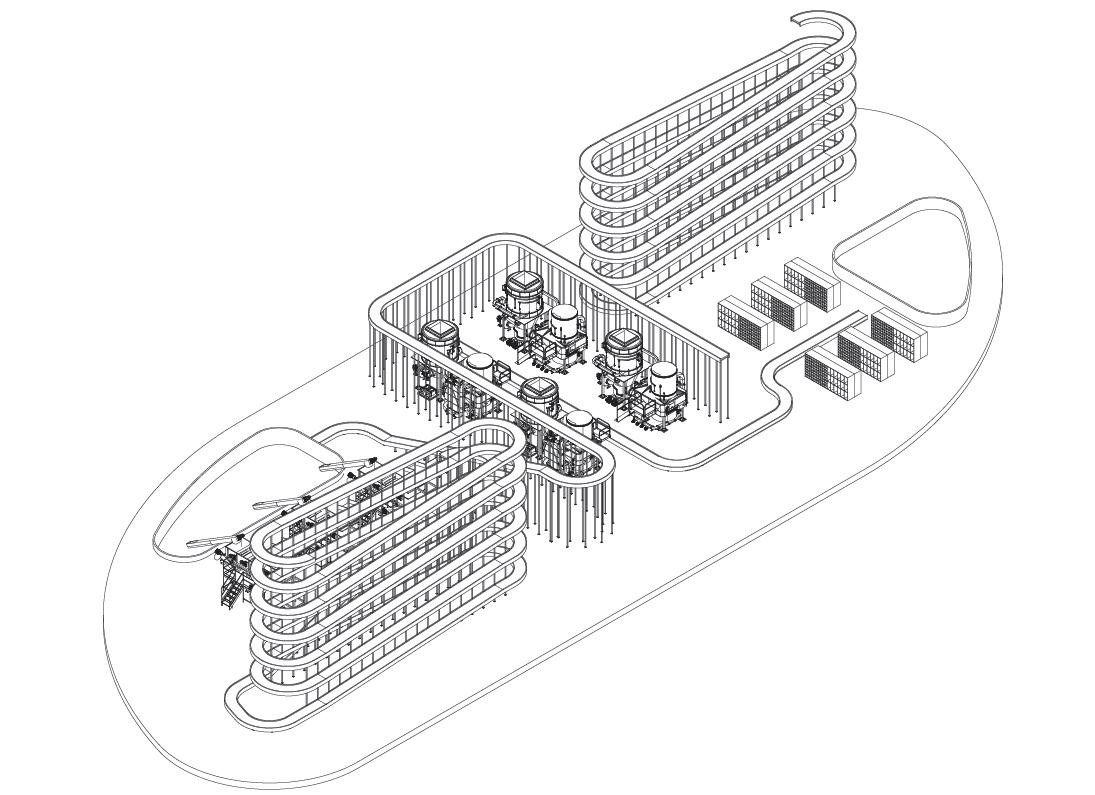
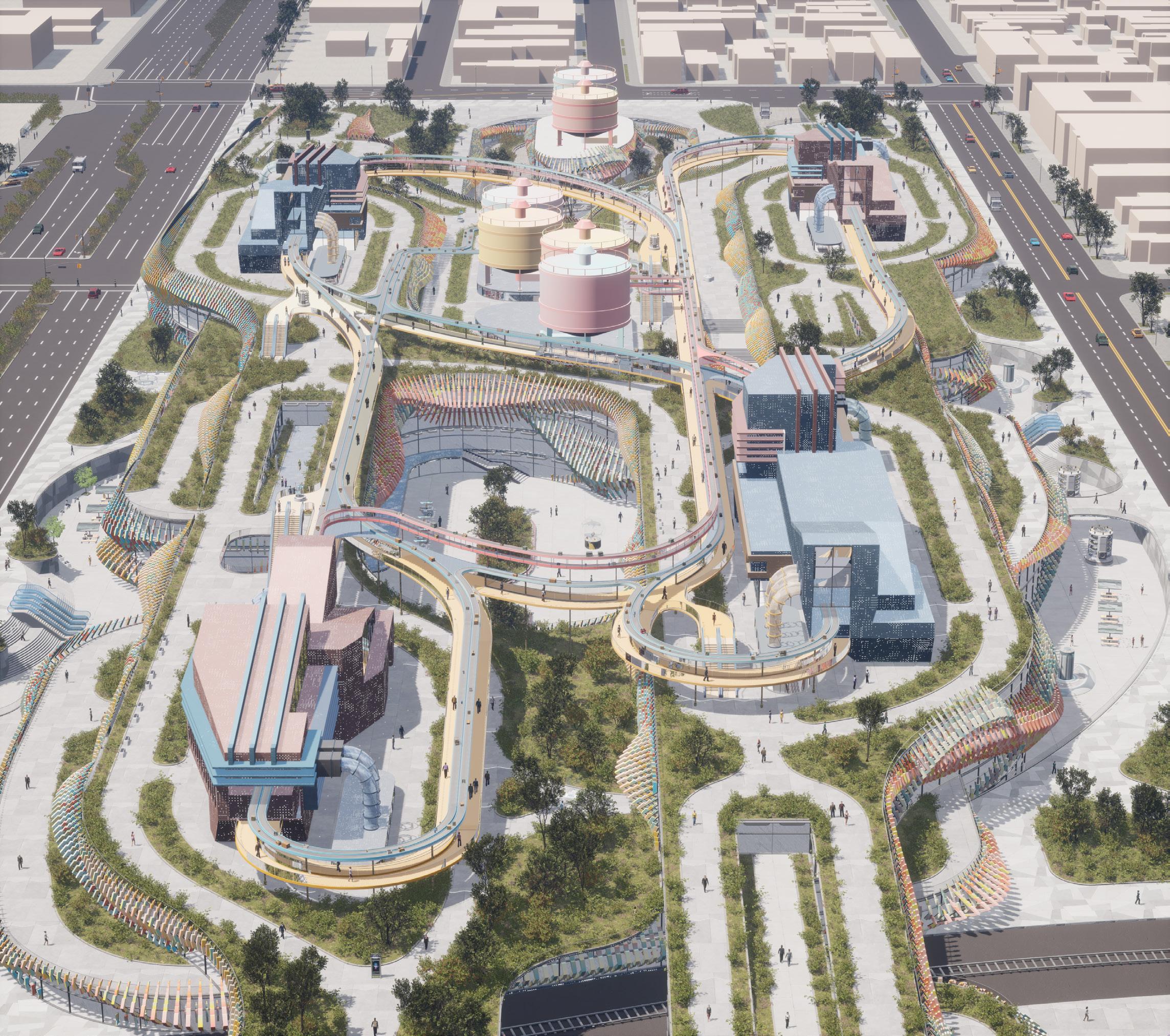
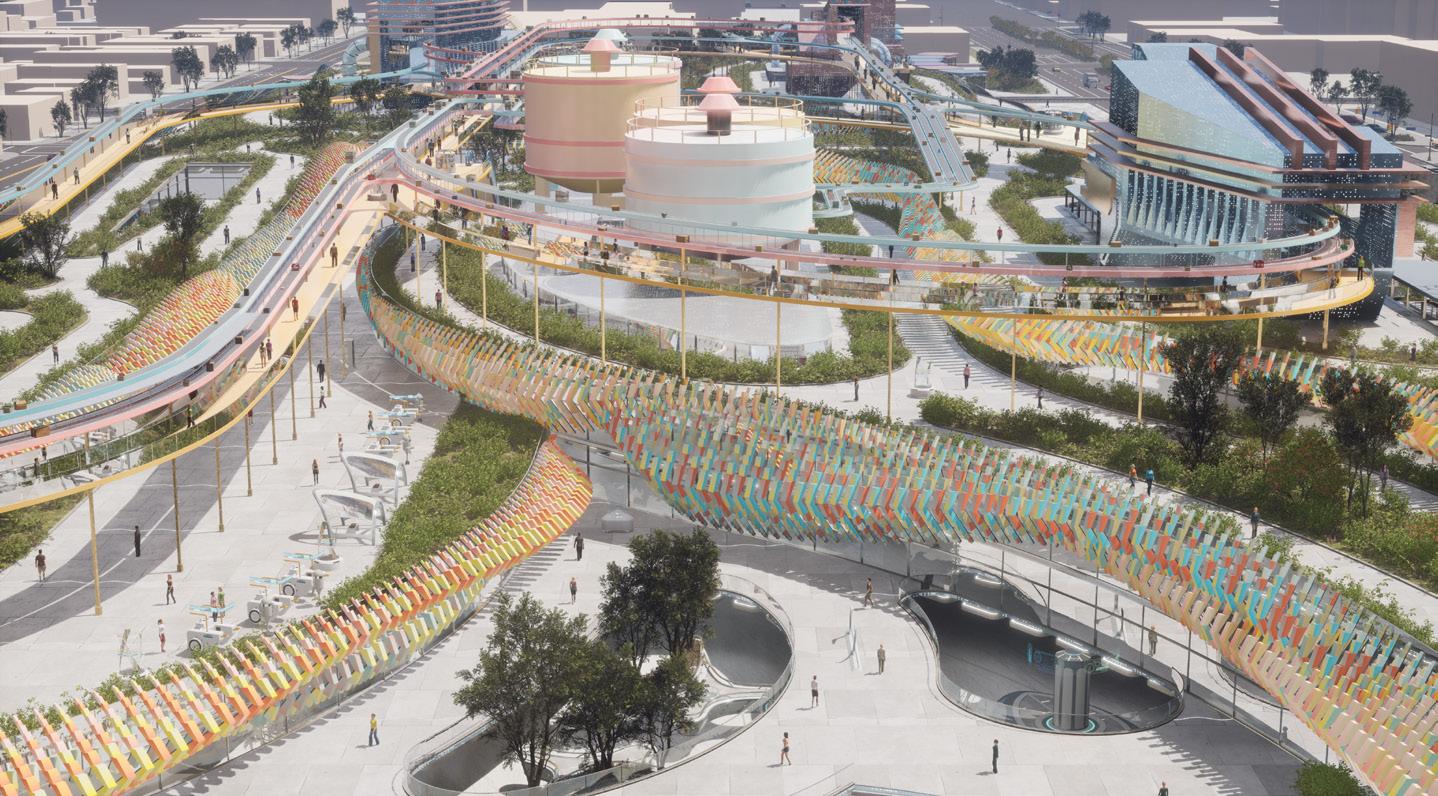
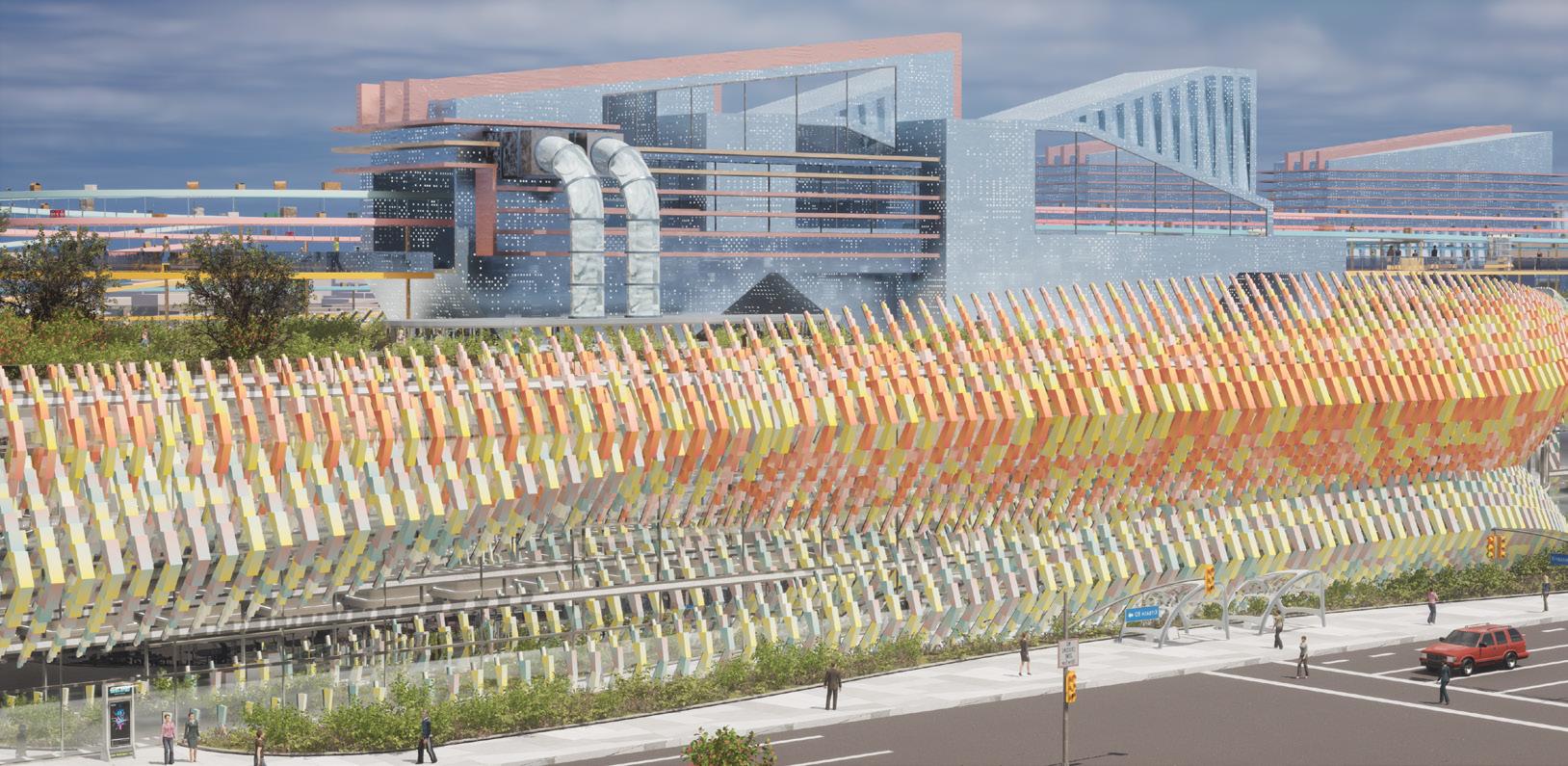
ACADEMIC PROJECT
PROJECT INFORMATION
Advanced Material and Tectonics, SCI-Arc, 2021
Instructor: Randy Jefferson, Dwayne Oyler
Partner: Freeland Livingston, Meng-Jung Ho, Wei-Hung Chen
DESIGN CONCEPT
Tectonics in architecture, blending the science and art of construction, is essential for understanding and shaping the design of complex building envelopes in contemporary architecture. Our project took a deep dive into the Opus by Zaha Hadid Architects, analyzing and documenting the sophisticated tectonics of its subsystems to uncover the nuances of structural and aesthetic design. This exploration provided the foundation for our reinterpretation of these tectonic elements within the Uppsala Concert and Congress Hall by Henning Larsen Architects, integrating technical expertise with an appreciation of the cultural dimensions of facade design.
Our approach expanded the scope of tectonics beyond mere construction techniques, encompassing materials, methods, sequences, and tolerances while embracing architectural expression through geometry and technique. This comprehensive perspective aimed to create a nuanced understanding of tectonics and highlight its role in both the functional and expressive realms of architectural design.
PROGRAMS USED
Rhinoceros, Grasshopper, AutoCAD
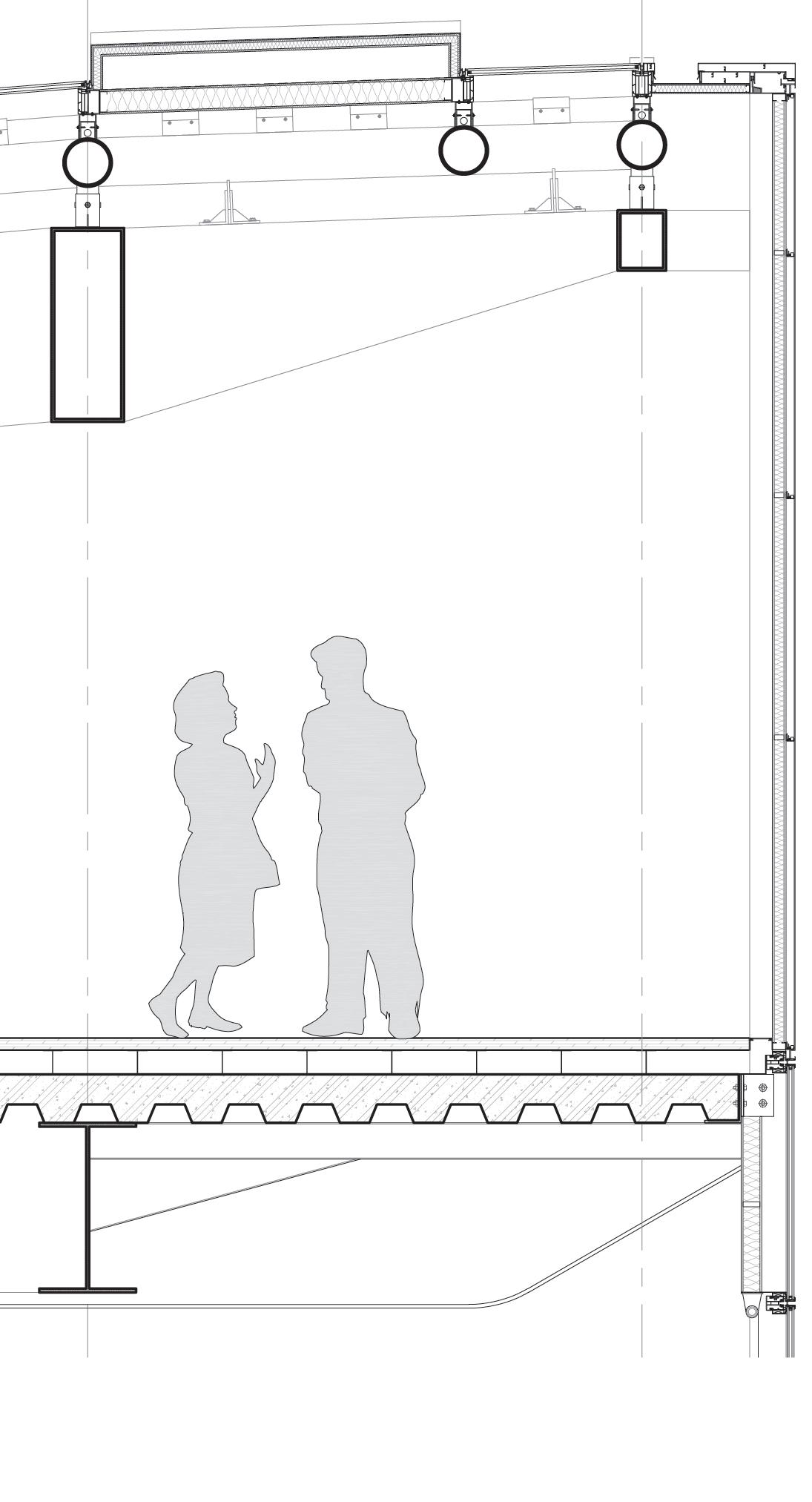
A Wall section development based on the original drawings from online resources and magazines.
B 3D chunk model blended the two projects together in terms of tectonics
C Detail design under consideration of structure, MEP, fireproofing, and waterproofing
D-E Chunk models
F-H Detail models
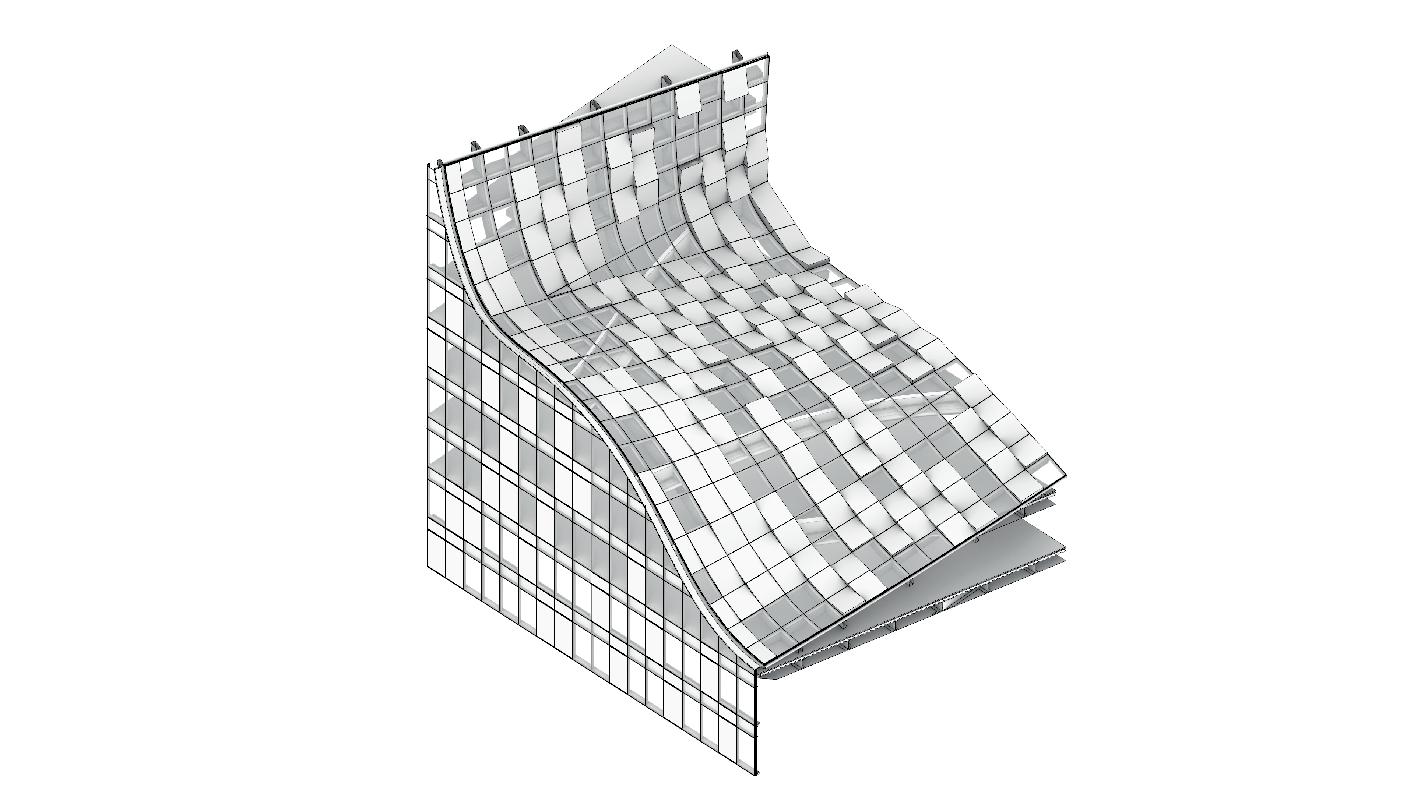
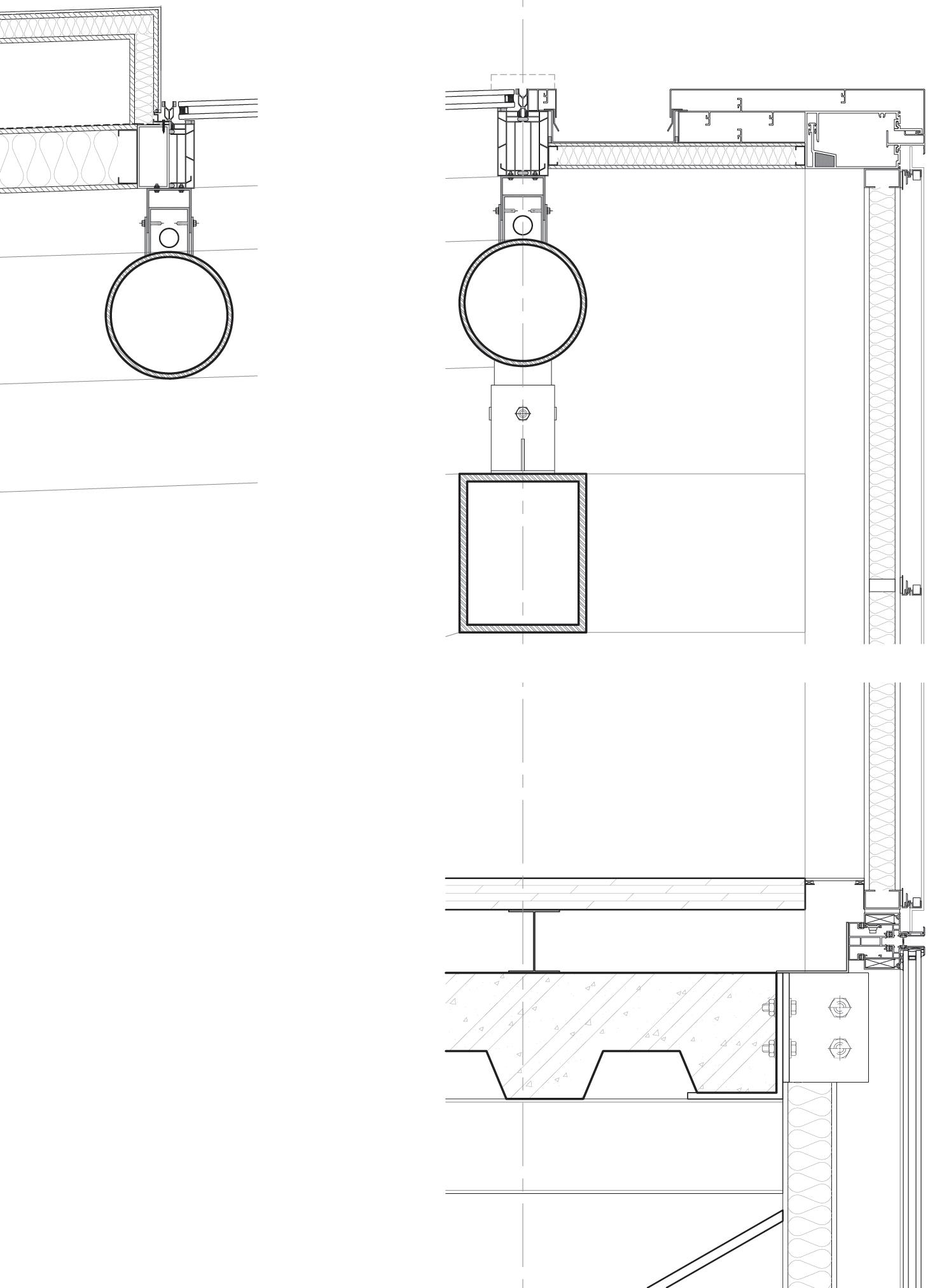
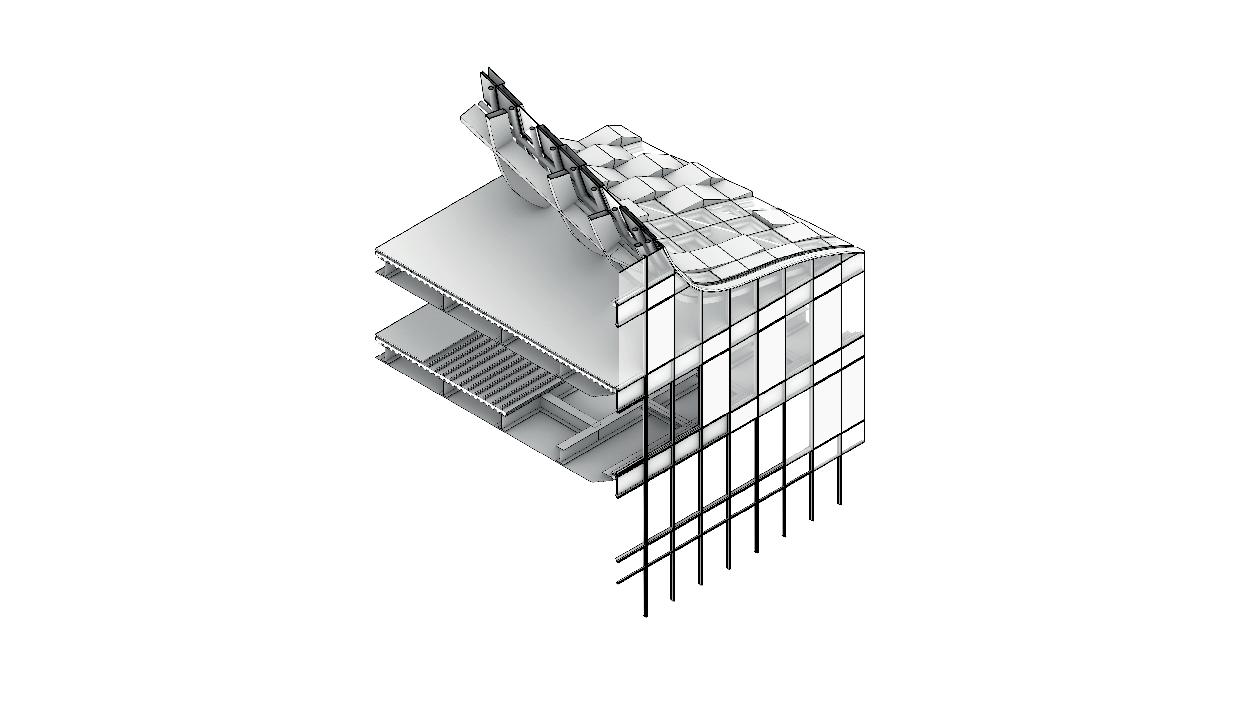

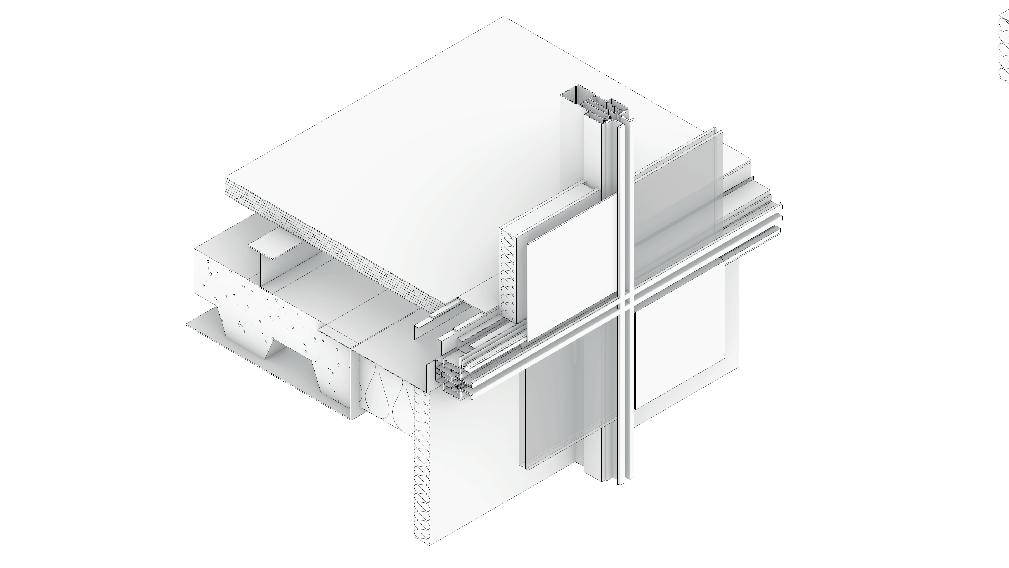
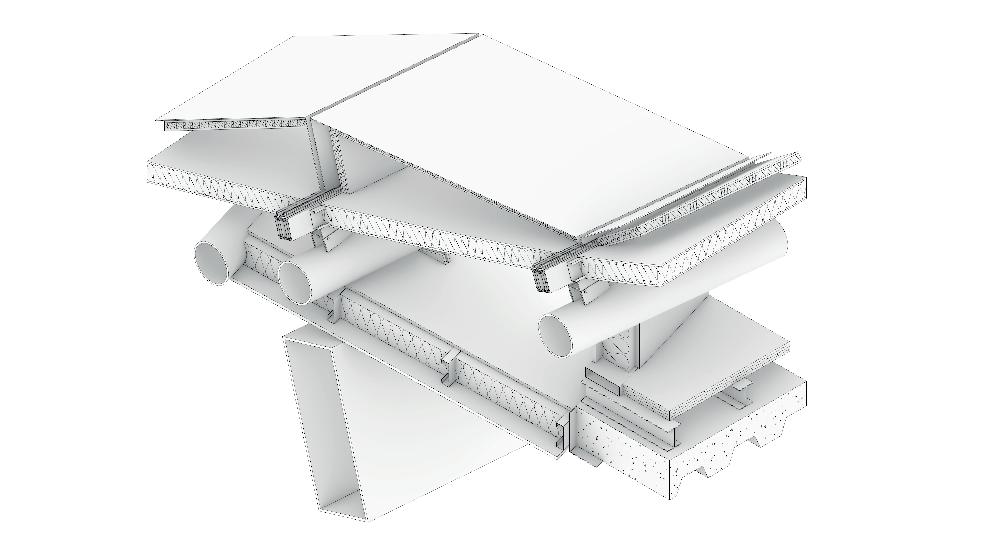
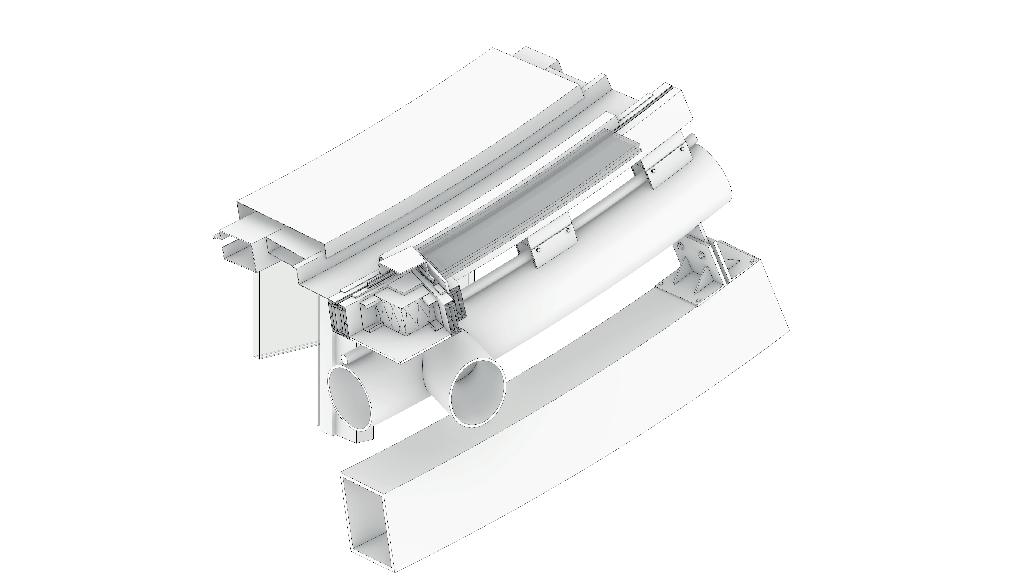
TECTONICS OF FLUIDITY
ACADEMIC PROJECT
PROJECT INFORMATION
Undergraduate Thesis Design, Tamkang University, 2017
Instructor: Ying-Chang Yu
Partner: Individual Work
Location: Taipei, Taiwan
DESIGN CONCEPT
In my research, I delved into fluidity—a concept reflecting the universe’s inherent state of constant change—as it manifests in mechanics, substances, and spaces like water, landscapes, and organic structures. This fluidity is also evident in architecture, transitioning from medieval arches and domes to contemporary free-form designs with concrete shells and curved cladding. Despite its aesthetic appeal, free-form architecture presents significant challenges, particularly in fabricating double curvature panels, which impact cost and quality.
Recognizing these challenges, I focused on developing an accurate and efficient method for manufacturing double curvature façades from flat pieces of materials, given their increasing significance in contemporary architecture with the rise of computational design. My work closely intertwined architecture and tectonics, analyzing them through the prism of fluidity and investigating the relationship between materials and geometry from an aesthetic standpoint. I provided detailed insights into the practicalities of producing double curvature panels, supported by a collection of detailed drawings and parameterized construction systems.
PROGRAMS USED
Rhinoceros, Grasshopper, AutoCAD, V-Ray
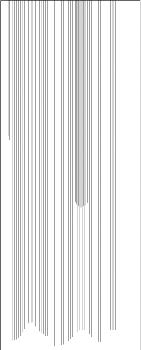
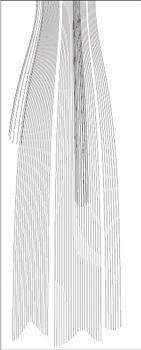
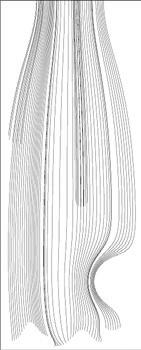
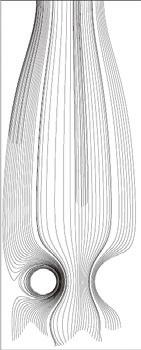
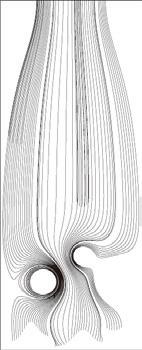
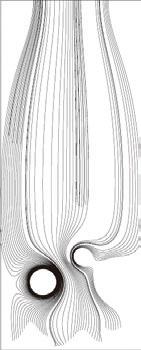
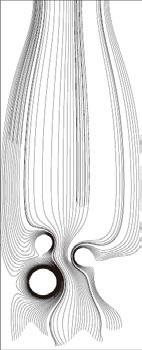
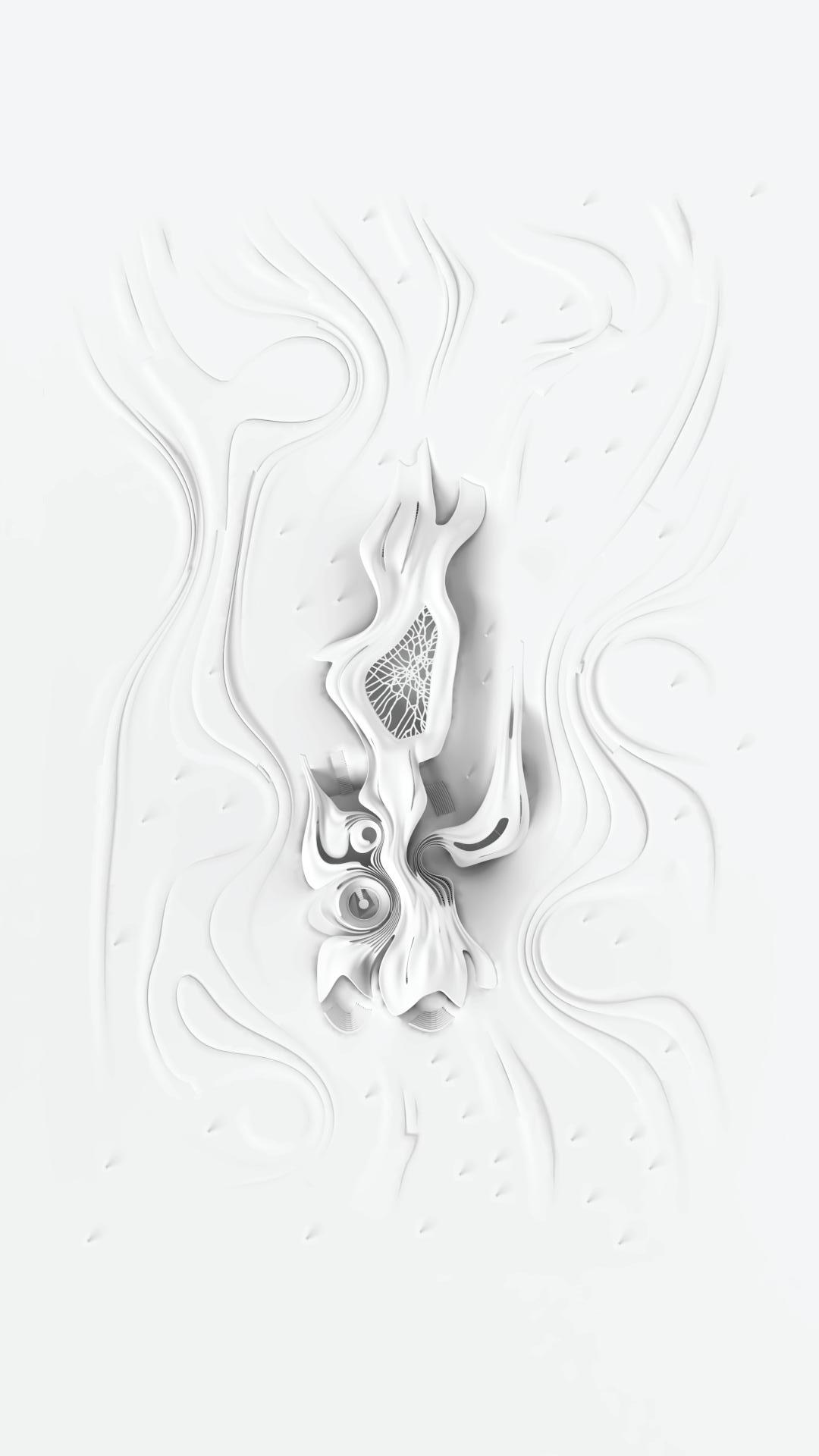
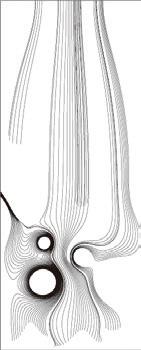
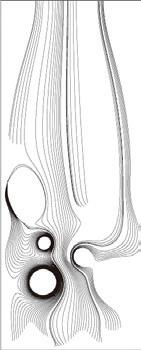
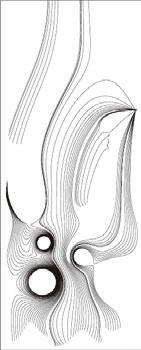
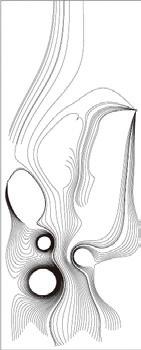
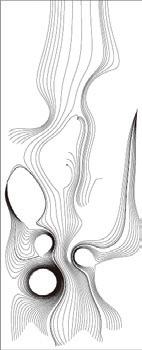
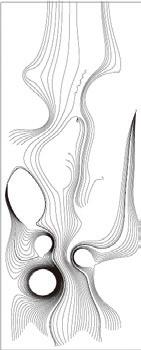

A Fluid simulations in the form-finding process
B Section
C-D Renderings visualized the double curvature panels
E-F Physical models using laser kerf-bending techniques
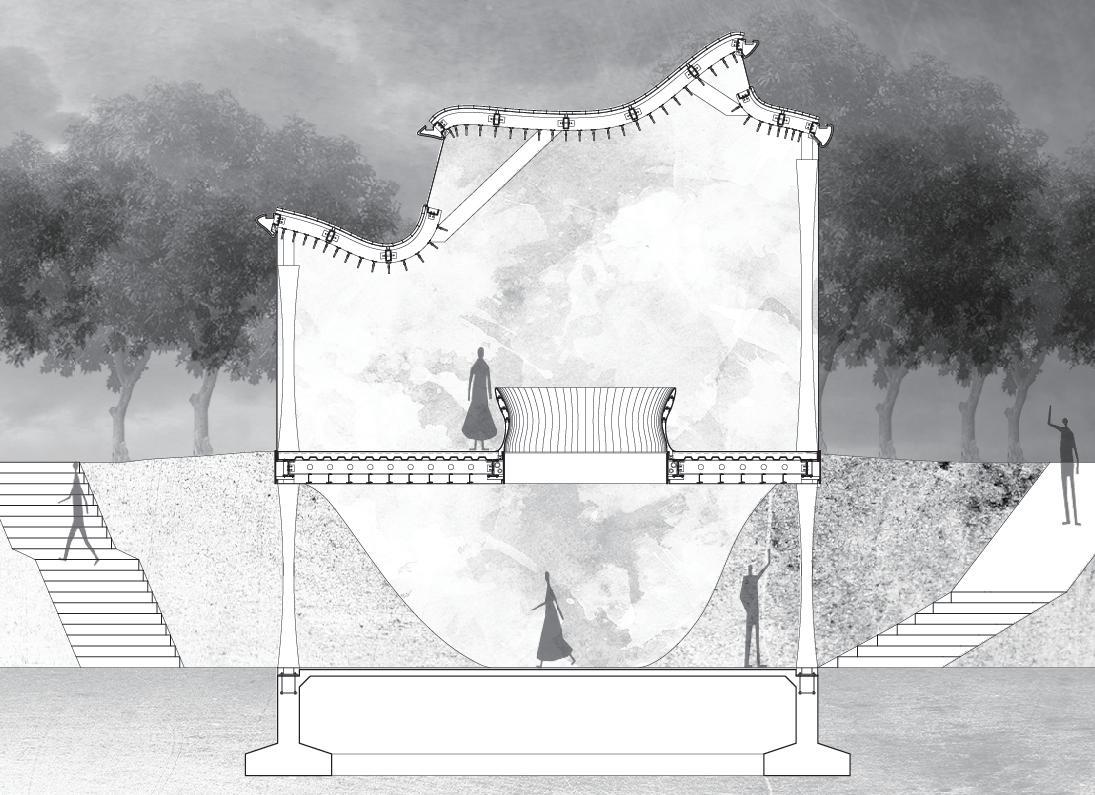
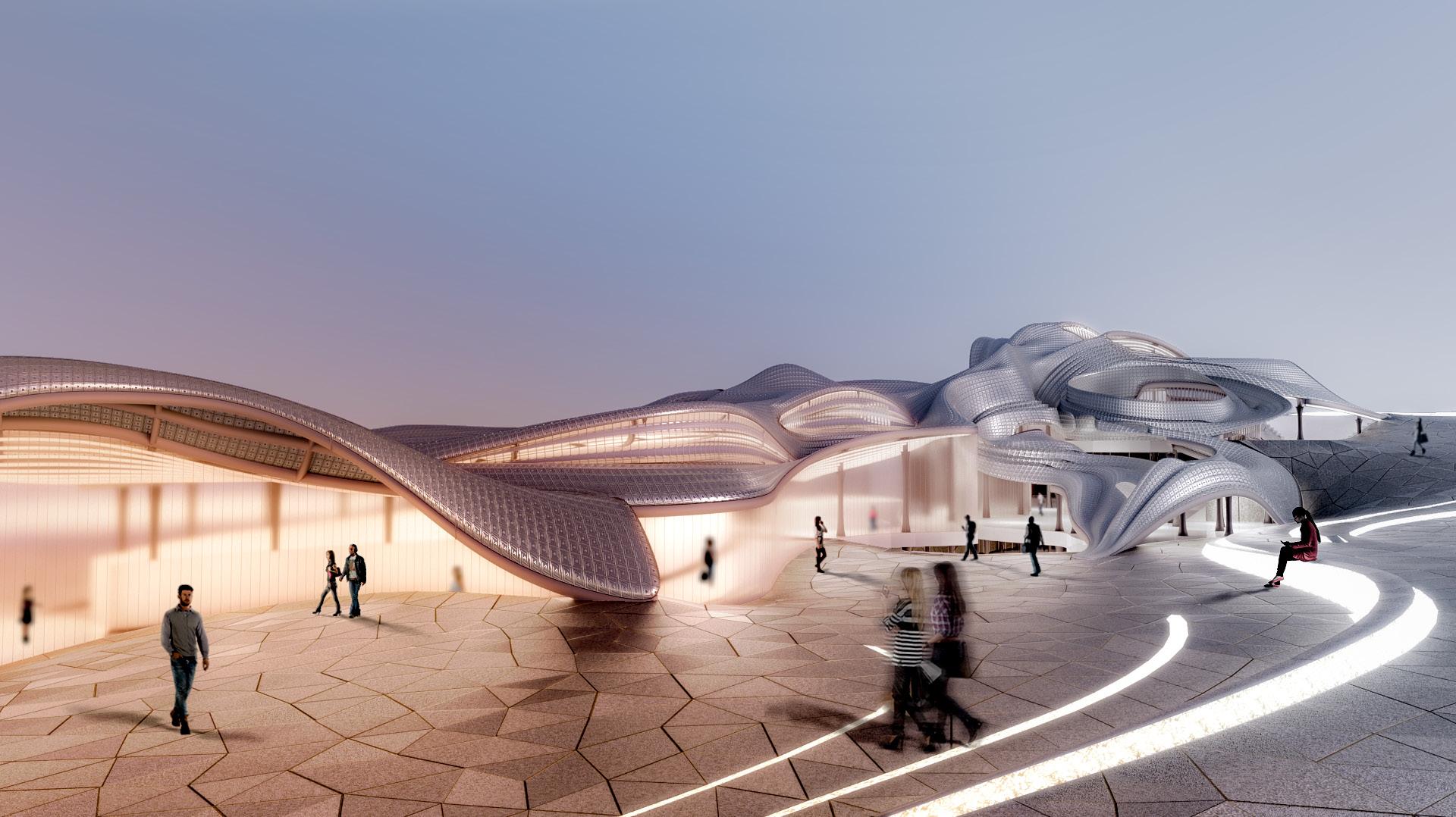
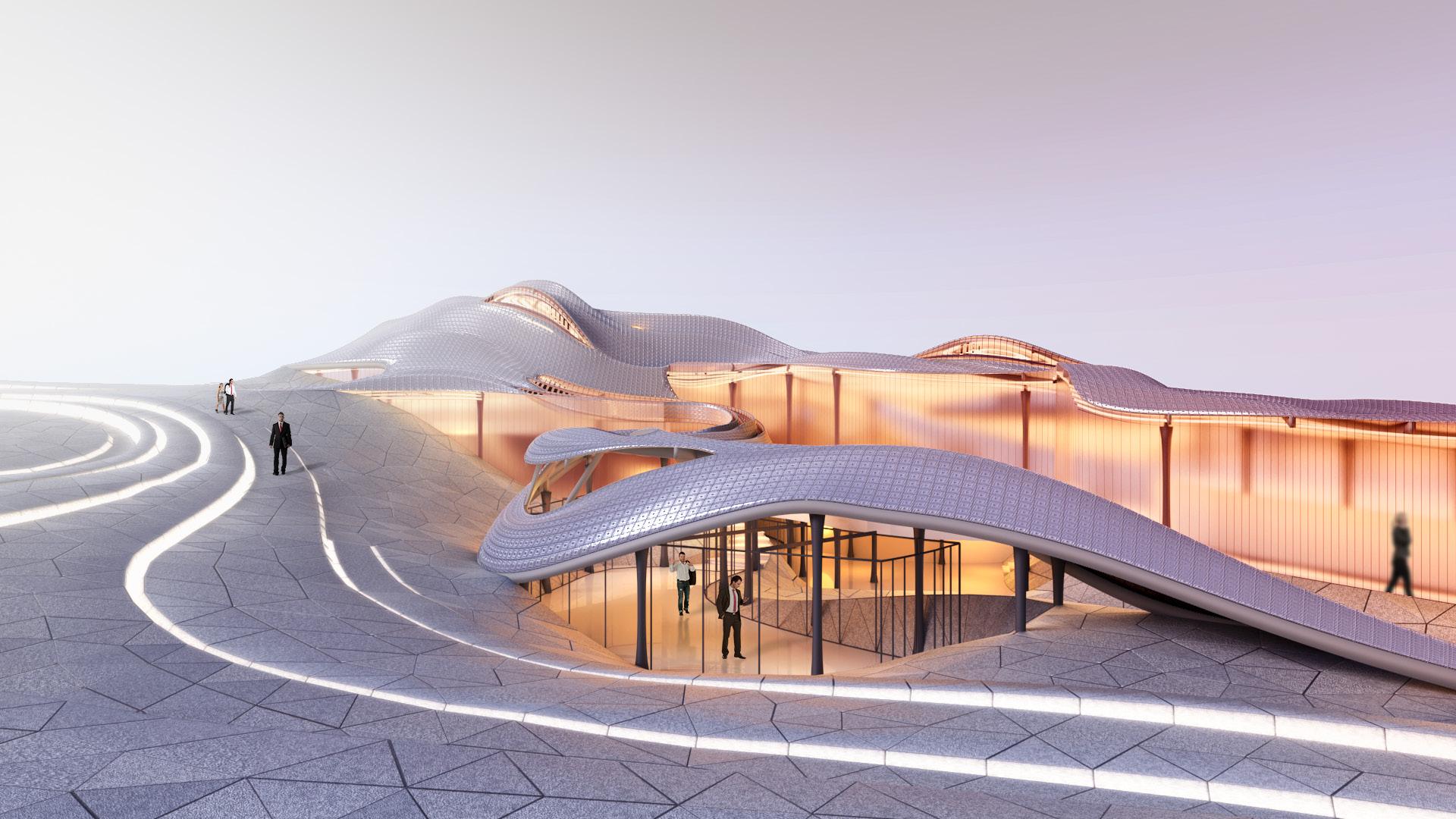

