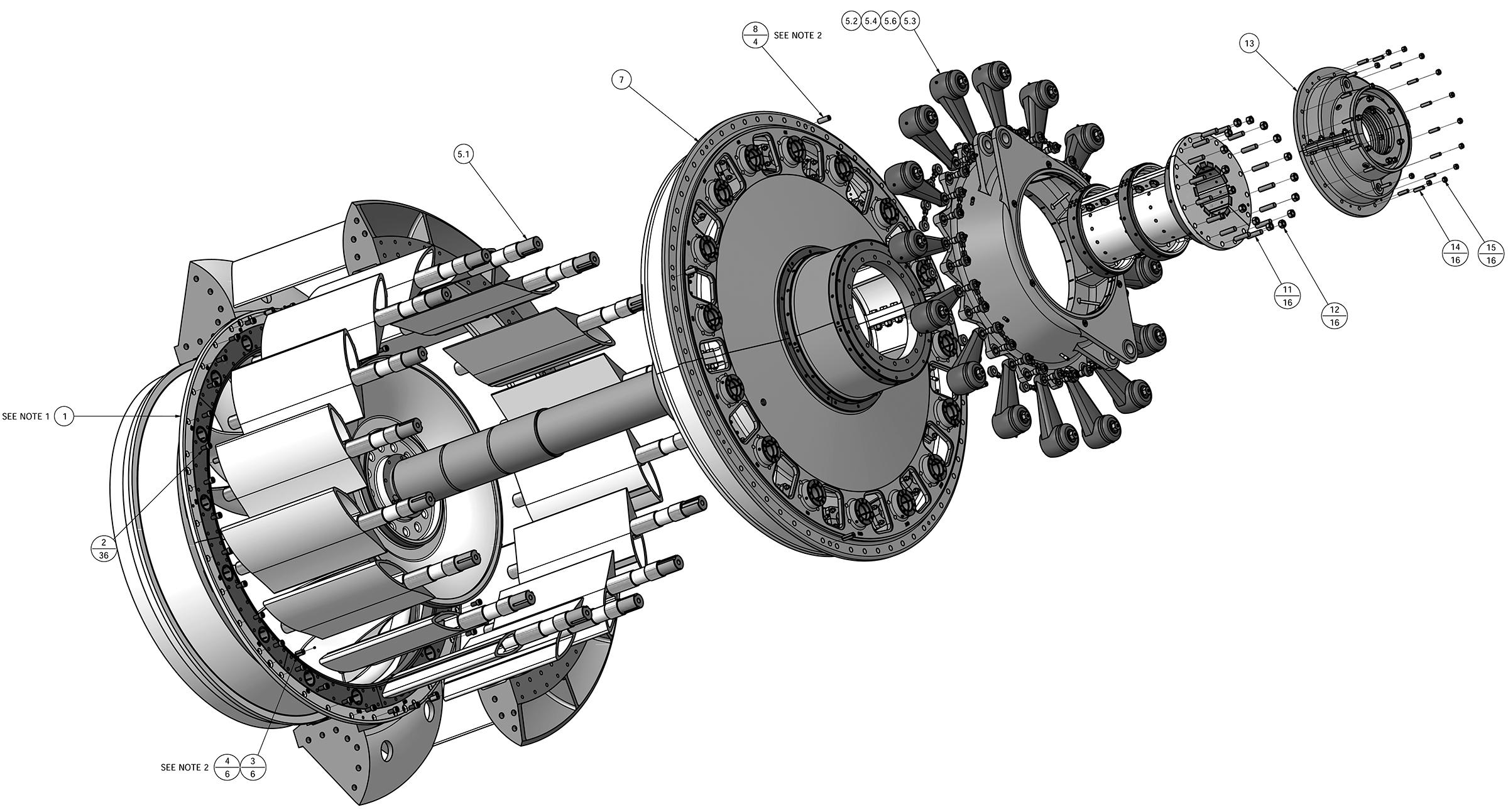
10 minute read
Mike Dupuis of Hydro Tech: From Turbine Overhauls to Bearings
Mike Dupuis of Hydro Tech: From Turbine Overhauls to Bearings

Engineered drawings for a complete Francis turbine located in Maine.
Advertisement
Ontario-based Hydro Tech, Inc., performs turbine and generator overhauls, provides overhauls and bearings for hydropower facilities, and performs a number of other vital services for the hydro industry. In addition to its core mechanical engineering expertise, it also provides both oil- and water-lubricated bearings and is initiating a 3‐year research and development project on bearings with a partner company in South Korea. In this interview, Hydro Tech Founder and President Mike Dupuis tells Hydro Leader about his company’s wide range of products and services.
Hydro Leader: Please tell us about your background and how you came to be in your current position.
Mike Dupuis: I am a mechanical engineering technologist. Prior to founding Hydro Tech, I worked for a regional hydroelectric company for 9 years. I was the group leader for an area covering seven power stations and was responsible for projects and maintenance with a multidisciplinary crew of electricians, programmable logic controller maintenance people, and millwrights. By the time I left that company, I had obtained two trade tickets in the mechanical field, which made me well suited for my position at that company. It was an excellent job, and my boss and coworkers were great, but it wasn’t providing the challenge that I was looking for. I wanted more and left on good terms to start my company.
I founded Hydro Tech in 2001. At that point, it was just me working from my basement as a one-man consulting operation. In 2005, the opportunity arose to start hiring employees for larger, long-term contracts, and things grew from there.
Hydro Leader: How large is the company today?
Mike Dupuis: Our Canadian company, Hydro Tech, Inc., currently has two offices: one in Niagara Falls, Ontario, and our head office in Sault Ste. Marie, Ontario. Our U.S. company, Hydro Tech USA, is located in Brunswick, Maine. In addition, I have a partner, Russell Industries, that I brought on in 2016 to help me grow the company. Between our two companies, we’re about 250 people, and the revenue reflects that.
Hydro Tech is largely technically based, so we have engineers, supervisors, and support staff for those engineers and supervisors. Hydro Tech is a small part of the 250 total employees of the two partner companies. While not a large company, we are a highly skilled team that is always growing.
We have hired four people since January and are always looking for more good candidates. We have been getting some good, qualified applicants recently, which was not always the case when we were a new and relatively unknown company. Now that we are recognized in the industry, people are starting to gravitate toward us. If all goes well, we’ll bring on a few more hires this year and keep going from there.
As a mechanical hydro company, we can take care of just about any kind of overhaul, but if we’re going to be the lead, mechanical engineering should be the main thrust of the project.
Hydro Leader: How did you decide to partner with Russell Industries?
Mike Dupuis: Financing was a big issue for me. When I was on my own, I was forced to turn down some projects. A lot of companies get ahead of themselves by taking on too much work and then find that they can’t finance their projects. From the time one signs a contract to the time one gets paid, one must complete large parts of the project and still meet payroll. In 2015, I was simultaneously doing overhauls in the United States, installing all the generators and turbines at two new plants in northern Ontario, installing some of our biggest gates ever in British Columbia, and doing a few other large projects. I was still financing the business out of my pocket, and I was able to do it, but it was a high-pressure year for me. In 2016, I partnered up with Daniel Russell of Russell Industries. I had already been doing business with Daniel for many years, as he owns some of the manufacturing shops that we were working with, and so we were very familiar with each other. We joined forces, and Russell Industries now provides the financing for our larger projects. It’s also great to have someone like Daniel to discuss business directions and initiatives with.

This four-segment bolted thrust bearing runner plate is 112.5 inches in diameter; the bearing supports over 522 tons of force. This unique design replaced a floating 4-segmented floating runner plate that was causing bearing failure within 3 years. The new upgrades have been in continuous operation since 2009 in Ghana
Hydro Leader: Do you do your own manufacturing?
Mike Dupuis: Russell Industries owns some manufacturing facilities, but for turbine and generator parts we generally use other manufacturers. Some of our projects involve large, heavy turbine and generator components, and it’s more cost effective for us to shop those large pieces out than to manufacture or repair them in house. It’s taken a few years, but we’ve developed some really strong working relationships with a variety of manufacturers. We know the shops that can do rough machining for our generalgrade parts and fine machining for our high-grade parts. Our engineers design the parts, and we provide a stringent quality-control program for those shops to follow.
Hydro Leader: How is your business split between bearing manufacturing overhauls, maintenance gate installations, metrology, and engineering?
Mike Dupuis: A little under 50 percent of it is in turbine and generator overhauls. About one-third of our business is just straight bearings. The last sliver is everything else, which is mostly a mixture of FARO laser tracker metrology and gate work.
Hydro Leader: Please tell us about your bearings.
Mike Dupuis: We’re trying to become a bearing manufacturer that can support whatever bearing is required, but we don’t have anything to do with roller bearings—if we need roller bearings, we buy them from somebody else. Our bearing specialties are either oil-lubricated or water-lubricated. For oil bearings, we use either Babbitt or polytetrafluoroethylene (PTFE), which is basically Teflon. For water bearings, we use many different materials. The one we feel is the best is lignum vitae, which comes from the lignum vitae tree.
Hydro Leader: So lignum vitae is a kind of wood?
Mike Dupuis: Yes. It’s strange that despite all of mankind’s scientific advancements, the old wood bearing is still by far the best one out there. Bearings can be made of rubber, plastics, and composite pressed compounds, but lignum vitae is still the best material out there. Hydro Tech is not a sales representative for lignum vitae—we just pick the material for the application, and usually lignum vitae is the best for bearings. It’s a dense wood— if you drop it in a pail of water, it sinks to the bottom. What makes lignum vitae better than any other tree is the unique gum in the wood, which seems to provide better lubrication than anything else. It is the gum that allows the steel shaft to slide over the wood. The gum doesn’t wear away; it just seems to stay there and provide that required slippery surface.
Hydro Leader: Does Hydro Tech sell its products internationally?
Mike Dupuis: When it comes to our hydro-related lines of business, we complete generator and turbine overhauls and gate installations across the United States and Canada. We supply and service bearings around the world, but we do not offer our full range of services internationally, as onsite work is more complicated the farther away from home you get.
Hydro Leader: How are environmental regulations affecting your business?
Mike Dupuis: That’s more of a problem for our clients than it is for us. For example, there are some environmental issues with bearings. Some bearings are oil lubricated, and oil spills can cause environmental damage. Just spilling a gallon of oil is a disaster. We’re in the process of converting some oil bearings to water bearings. This includes plants where turbines are working fine but where there are problems with water flooding the turbine, which can cause oil to be released into the river. If a plant floods after the conversion to water bearings, the environmental risk has been eliminated. We’ve done conversions of this type quite a few times now; it’s becoming more common. Environmental regulations on these types of issues help our business, as we have the ability to solve them.
More generally, hydro is a green energy, so it benefits from green energy requirements. Further, hydroelectric power supports intermittent green energy sources, like wind and solar, as a sort of battery. Since water can be stored behind a dam and used to create power quickly, many power producers use their stored water like a battery. Some utilities have reduced the amount of waterpower they produce in year; they use their hydro sites to balance peak energy consumptions. They get paid to be reliable, not necessarily to generate. As green energy sources of various kinds come online, our hydro turbine maintenance business will increase. We will work to maintain generators and get them in the best reliable state.
Hydro Leader: What are your other top issues today?
Mike Dupuis: We are currently working on two interesting undertakings. We just invented a turbine journal bearing sleeve that can be installed in the field without any major work, and we have a patent pending on it as of last month. The sleeve is intended to restore the diameter of a shaft and can be installed without disassembling the turbine. Normally, you have to take a turbine shaft to a machine shop to repair a journal bearing sleeve.
We always have somebody at Hydro Tech working on research and development, trying to improve our services. Earlier this year, we were awarded a grant from the Canadian and Korean governments to work on the research and development of bearings. We are researching water bearings for cargo ships and hydroelectric turbines. This is a collaboration between a company in South Korea called Movena Korea Co. and Hydro Tech. We will be working together over the next 3 years to finalize designs and create an environmentally friendly, well-working bearing.
Hydro Leader: What other problems are your products trying to address?
Mike Dupuis: Our focus is on efficiency, reliability, and green-powered working products.
Hydro Leader: Have you had issues related to materials and costs?
Mike Dupuis: Costs have recently increased for some of our oil bearings. The Babbitt material has doubled in price over the last 6 months. Everything we need seems to be available, but the prices are fluctuating. These costs are being passed on to our clients, unfortunately. We’re not gouging, but our prices reflect the changes in the market. Some of it seems to be caused by inflation, and some costs appear to be caused by high demand or low supply. To date, we have always been able to get supplies as needed.
Hydro Leader: Please tell us about your acquisition of North American PTFE.
Mike Dupuis: We acquired North American PTFE in 2017. For many years, we had been purchasing our PTFE bearing pads from a Russian company called EnEnergo, and North American PTFE was EnEnergo’s only licensed distributor in North America. PTFE bearing technology was developed in Russia in the 1970s, 30 years before it was ever installed in North America. Hydro Tech would design the bearings and then get the pads from EnEnergo via North American PTFE. When the owner of North American PTFE decided to retire, I bought him out and took over the North American distributorship contract with EnEnergo.
Hydro Leader: What is your company’s vision for the future?
Mike Dupuis: We plan on doing more overhauls for generators and turbines. That’s a big focus for us, and we seem to be getting more work in that field. We’re also making a big push in bearings with the South Korean company, Movena, that I mentioned earlier. Between our companies, we plan on spending about $1.3 million in research and development over the next 3 years. I expect to increase our bearing business from its current level by at least 200 percent. There is a huge amount of growth potential. We are one of the only suppliers that designs both oil and water bearings, so we have the broad capacity to work on any slide bearing a client requires.

Mike Dupuis is the founder and president of Hydro Tech, Inc., and Hydro Tech USA. He can be reached at info@hydrotech-inc.ca or (705) 946‐3182. For more on Hydro Tech, visit www.hydrotech-inc.ca.