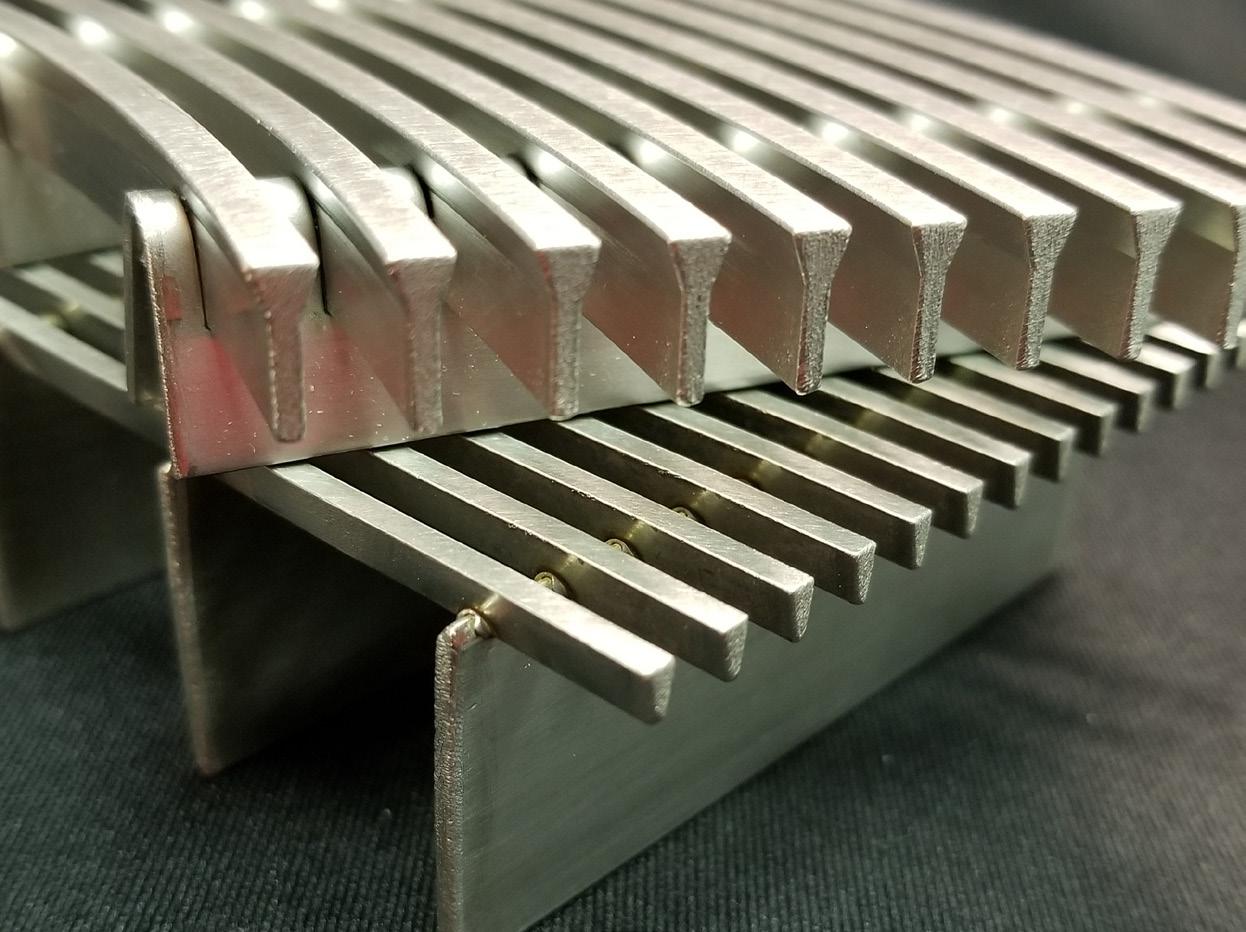
11 minute read
Hendrick Screen Company’s Custom-Tailored Equipment
Hendrick Screen Company’s Custom-Tailored Equipment
Hendrick Screen Company produces fish diversion and water intake screens, airburst cleaning systems, guiderails, bar racks, blank panels, and other equipment of interest to hydro facilities. The company traces its history back more than 140 years and is still family owned today. In this interview, Robert McDole, Hendrick Screen Company’s vice president and general manager, and Cody Veach, the product manager for the water intake and fish diversion markets, tell us about its custombuilt equipment and its commitment to customer service.
Advertisement
Hydro Leader: Please tell us about your background and how you came to be in your current position.
Robert McDole: I started in the metals industry in 1978, so I’ve been in metal-related businesses for approximately 43 years. I have been in executive management for approximately 30 years, managing business units for manufacturers and distribution companies. I started with Hendrick 11 years ago. We manufacture metal screens, primarily made out of stainless steel and other exotic alloys with a heavy emphasis on fabrication. As the company’s vice president and general manager, my responsibilities include profit/loss, sales, production, and all other facets of the business.
Cody Veach: I started out in fabrication, specifically as a fabricator in the shipbuilding industry. I then moved into the aerospace field, where I was fabricating, machining, and designing heat exchangers. When I came to Hendrick, I spent several years in fabrication and then moved into a sales position in 2014, focusing on the water intake and fish diversion segment.
Hydro Leader: Please tell us about the organization, its history, and its geographic range.
Robert McDole: The Hendrick Company was started in the late 1800s by Eli Hendrick, who was the inventor of the perforating press. His ability to start the new business came with seed money from John D. Rockefeller. The company has maintained the name Hendrick throughout its more than 140 years in business. Today, the company is owned by the Drake family, continuing to be a family-owned business. Hendrick is a worldwide company and ships all over the world, although the majority of our product is sold to customers in North America.
There are three divisions within Hendrick. The two manufacturing divisions are Hendrick Manufacturing, which is the largest family-owned perforator in North America, and Hendrick Screen Company. Hendrick Architectural is supported by both manufacturing divisions and provides products to the architectural market.

Hendrick’s main screen types: above, a profile bar screen; below, a resistance-welded screen.
The company has approximately 200 employees serving over 25 markets, including the architectural, petrochemical, fish diversion, water intake, sound and enclosures, pulp and paper, mining, agriculture, industrial, filtration, original equipment manufacturer, and distribution markets.
Hendrick emphasizes customer service for clients large and small from all over the world. Our motto is, “If you can get it on paper, we can probably do it.” We provide a range of value-added services, including engineering, so that we can be a solutions provider to our customers.
Hydro Leader: How is your business divided up between those different markets?
Robert McDole: Although we consider ourselves a leader in the water intake and fish diversion markets, Hendrick continues to focus heavily on these markets due to demand and growth opportunities. Other target markets include the architectural, food and beverage, industrial, and petrochemical markets.
Hydro Leader: Please tell us about your fish diversion screens and your water intake and treatment items.
Robert McDole: Hendrick offers two basic constructions for our products: resistance welded and a mechanically interlocked screen we refer to as profile bar. Hendrick will work with the customer to provide the best construction method with the best performance for the desired end product.
Cody Veach: When it comes to fish diversion and water intake, there are two types of screens: cylindrical screens and flat panels. We supply a significant amount of each to the marketplace. Additionally, we manufacture a patented halfintake screen, which is like a full circular screen cut in half and is intended for shallow water applications.
Choosing which screen to use really depends on the application. For fish diversion, we may suggest a flat panel for installation in a structure at a dam. Flat panels often have manifolds behind them to facilitate an airburst system used to clean the screens. It’s environmentally friendly and meets practically any criteria. Our screens are 316(b) compliant, which is required by many hydro plants. Hendrick’s screens are always built to order to meet the needs of the end user.
Hydro Leader: Are your systems primarily for hydro facilities and municipal systems?
Robert McDole: They are appropriate for any application: hydro, municipal, or irrigation—anything that’s got water touching it.
Hydro Leader: Where on a hydro facility would these screens be placed?
Cody Veach: Our intake screens are installed at the entry point where water is withdrawn from the water source. Installation locations can vary based on the water source and its environment. For example, if it’s in a reservoir, there may be intake screens at different levels to accommodate water depth variances. If there’s a lot of floating debris, the screens may be lower in the water column, where the water is cleaner, so there’s less debris to deal with. It also depends on how much the water level fluctuates. We install in a variety of water sources, such as rivers, lakes, and oceans; each have their own distinct installation requirements due to the environmental conditions.
Hydro Leader: Once the product is engineered, do your customers install it themselves, or do you go out to install it?
Robert McDole: We provide installation suggestions, but currently, Hendrick does not provide installation services. Our customers manage the installation. However, as a service to our customers, we offer onsite inspections once installation is complete.
Hydro Leader: What’s the largest screen you’ve ever manufactured?
Cody Veach: We have manufactured cylindrical screens of up to 8 feet in diameter and 30 feet in length. Our larger intake screens may include support legs or stands for reinforcement and stability. We’ve built flat screens as large as 12 by 20 feet. In some cases, customers have used multiple flat panels side by side or stacked on top of each other to cover more area.
When an airburst system is used with a flat panel, the screen needs to be installed at a tilt so that air travels through the face of the screen and can remove the debris. If the screen is installed in a completely vertical position, the airburst will not be effective. Some of Hendrick’s flat panels are used in conjunction with mechanical raking systems. In these situations, our engineering group will review each requirement so that we can recommend the best solution. With large flat panels, we can supply an airburst system to clean the screens section by section, with each section of the manifold on a separate valve.
Hydro Leader: What material are your screens made of?
Robert McDole: We build our screens with a variety of alloys, but primarily use stainless steel, including 304L and 316L. We also supply screens and accessories using copper nickel, 2205, carbon steel, and aluminum, depending on the application.
Hydro Leader: Why would a customer prefer a material like copper nickel over aluminum or stainless steel?
Cody Veach: Copper-nickel screens are primarily used in locations where there will be biofouling—the growth of mussels, algae, moss, or anything else that would physically grow on the screen and hinder its performance. We use two different copper-nickel alloys: 90/10, which has a higher copper content and is typically used in freshwater, and 70/30, which has a higher nickel content and is typically used in salt water.
Initially, Hendrick provided a coating on the screen to respond to biofouling issues. Now we provide a coppernickel construction that extends the life of the product, ultimately reducing the total cost. We found that the coating deteriorated over time, which significantly decreased the performance of the screen. Copper-nickel wire, supports, and U-clips provide long-lasting protection from biofouling. Zebra mussels in particular do not like copper.
Hydro Leader: How long does a screen last until it needs to be replaced?
Robert McDole: We’ve never had to replace a profile bar screen due to failure. A lot of companies have used resistance-welded technology for flat panels, which sometimes fail due to water resonance, or light vibration. Hendrick provides a profile bar construction, which is a mechanically interlocking screen. Profile bar is a stronger alternative to resistance-welded technology for flat panels. The costs are basically the same, but it is heavier and lasts longer, especially where flow rates are higher.
Profile bar is a three-piece interlocking construction consisting of a rivet rod, profile wire, and a U-clip. The interlocking design minimizes the need for welding directly on the wire. Also, the unique construction provides additional support and makes the screen stronger than a resistance-welded screen.
Hydro Leader: Are the screens adjustable?
Cody Veach: I wouldn’t say they are adjustable, but having multiple intake levels allows for flexibility. We design for the maximum flow rate required, and the screens perform just fine at any flow rate lower than that. Fish screens are designed to have adequate surface area at the low water level. This allows the screen to use more surface area if the water levels rise, reducing the risk of blinding even more.
Robert McDole: Hendrick builds airburst systems to provide optimal cleaning of the screens. This has been a growth area for our company. It’s an integral part of the screening process, because when somebody buys screens for fish diversion or a water intake application, they generally want a system to clean the surface of the screen. We can provide a customized system to meet the requirements of any given application. These systems can range from a basic manual system with hand-operated valves to a fully automated system with all the accessories.
Hydro Leader: How does the airburst system work?
Cody Veach: The airburst system delivers a blast of air to the screen to remove any debris that has gotten trapped against it. To design the system, we look at the size of the screen, how far the screen is from the compressor system, the size of the air-delivery piping, and the size of the air receiver. We want to ensure that the customer gets the correct amount of air delivered to the screen. Essentially, the system involves a compressor system that charges an air-receiver tank. Typically, they’re set to about 150 pounds per square inch. Once the system charges, a valve releases a blast of air via the air pipe. The air pushes water out of the pipe, providing the initial cleaning; when the air arrives, it blows the debris off and away from the screen; and then the sweep velocity of the water carries the debris downstream, away from the screen.
Hydro Leader: Does the flow need to be stopped during that process?
Cody Veach: It depends. If it’s just gravity-feeding to a wet well with direct connection to the pump and no risk of cavitation, then the water intake can continue, and the air won’t have any effect on it. If it is hooked directly to the pump and there is a risk of cavitation, then we always recommend the pump be shut down. It should only take a couple of minutes. A cleaning cycle usually only lasts about 5–10 seconds, and then there’s just enough time for the air to escape and get away from the screen.
Hydro Leader: How many times per day does the cleaning cycle need to be done?
Cody Veach: It’s project specific. We’ve seen it done anywhere from every 5 minutes to once a month. It can vary based on the time of year as well. During the spring, there may be a lot of high water, causing increased amounts of debris; in the fall, there may be leaves. We look at those questions when we design a system to make sure it can recharge quickly enough to get the cleaning frequency the customer needs.
Hydro Leader: Do you have any other product lines or services that would be of interest for the hydro market?
Robert McDole: Hendrick also provide guiderails, manifolds, baffle plates, blank panels, and bar racks, which are often required on these projects as well.
Hydro Leader: What are your other top issues today?
Robert McDole: The volatility of raw material pricing is certainly an issue when you’re trying to help a customer solve a problem within a budget. Foreign intrusion can be an issue—for example, China provides some of the raw materials that go to the stainless-steel mills around the country.
Hydro Leader: What is the company’s vision for the future?
Robert McDole: We’re a growing company with an emphasis on customer service. Our owners have invested a significant amount of money in both divisions. We want to be seen as the preferred supplier of stainless screens across the world, due to the high level of our quality and service. What has allowed Hendrick to grow over the last 25 years is our ability to service our customers. If there’s a problem, we provide the client with a long-term solution at a reasonable price.

Robert McDole is the vice president and general manager of Hendrick Screen Company. He can be contacted at bmcdole@hendrickcorp.com or (270) 685‐6914.

Cody Veach is the product manager for the water intake and fish diversion markets at Hendrick Screen Company. He can be contacted at cveach@hendrickcorp.com or (270) 685‐6934.