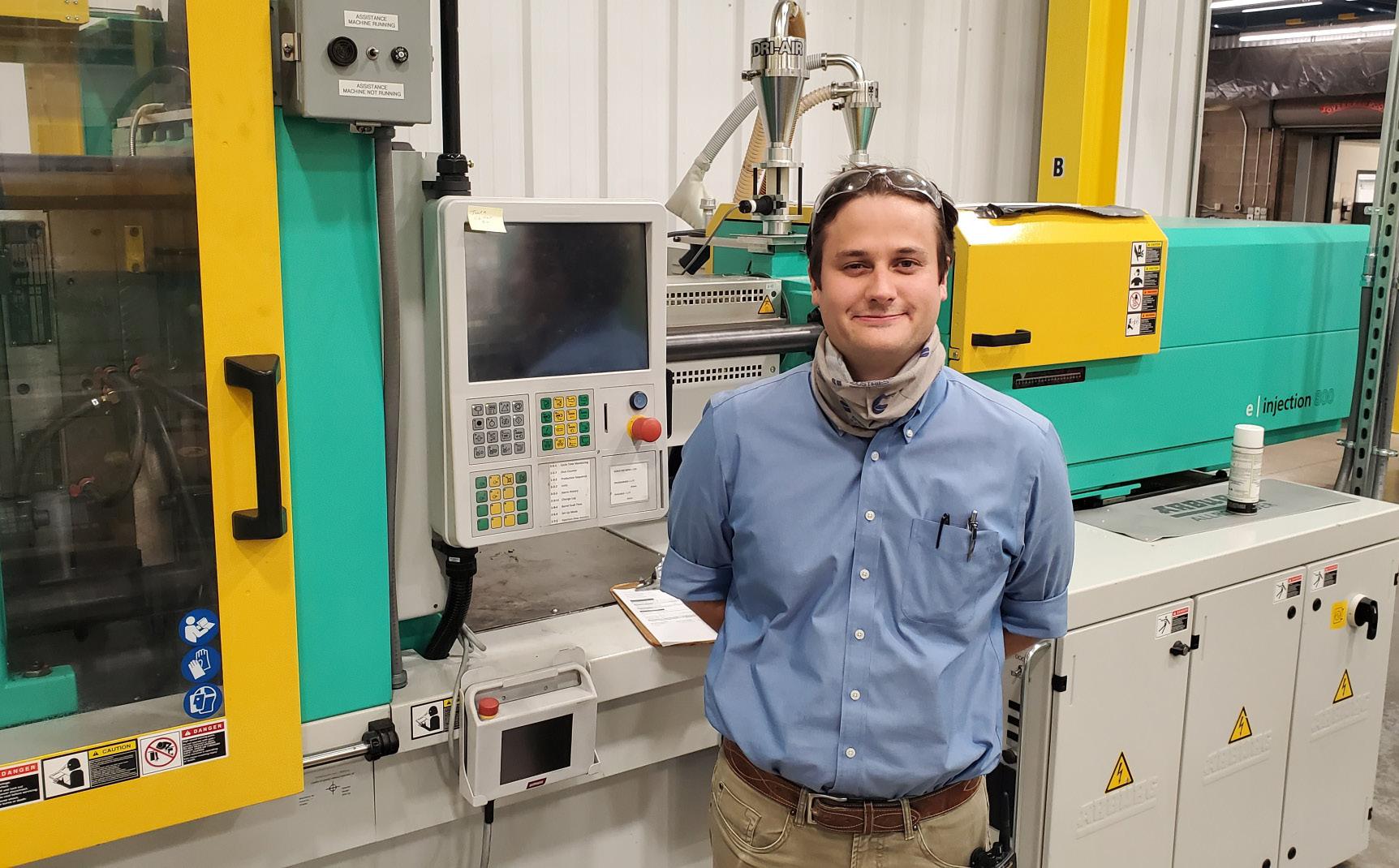
2 minute read
Our Pandemic Heroes
Carlton Radford '08: Supporting Medical Manufacturing
by ADAM BENAVIDES `08
Advertisement
I’ve counted Carlton Radford `08 as a dear friend since we first met sophomore year in the fall of 2005. In the years since, our friendship has never waned (I even had the honor of serving as Best Man at his 2016 wedding), nor has his penchant for being a generous, empathetic and resolute person. So as he finds himself in the midst of a dynamic career playing a vital role in battling the ongoing coronavirus pandemic, I’m certainly a proud friend of over 15 years, albeit not a surprised one.
As Quality Specialist for plastic injection molding company Engineering Industries, Inc. in Verona, Wisconsin, Carlton has spent the last five years ensuring parts are up to customers’ specs and standards. A key component in the supply chain for companies like Sub-Zero Group (home appliances) and Andis Company, Inc. (beauty products), Engineering Industries has become even more vital in supporting a core segment of their customer base: medical device manufacturers. Having long-standing relationships with healthcare companies like GE Healthcare and Mallinckrodt Pharmaceutical, the company is currently helping create the very products being used by healthcare professionals on the frontlines of COVID-19. After being sent home early from a Connecticut conference on March 11, Carlton saw the virus impact his work right away.
“We immediately saw a boost in healthcare projects, along with work from pharmaceutical companies,” he recalls. “We were thankfully able to pivot products intended for other uses to the new needs of healthcare workers across the country.” For example, the company was able to work with a healthcare customer to redirect a product typically reserved for newborn babies with respiratory issues as an alternative treatment for COVID-19 patients suffering from decreased lung function. The company has also been proactive in reevaluating its own internal processes to keep up with the demand from the healthcare industry. “Finding ways to improve our efficiency has helped healthcare customers quickly get their medical devices out to frontline workers,” says Carlton. “We’ve been really proud to help in that way.” To ensure they remain as efficient as possible, Carlton’s team uses realtime data from their ERP software to show which molding presses are performing more efficiently than others. They then use those insights to inform process changes or even to ascertain which machines work better for a given project. While Carlton is grateful his company has been able to avoid the hardships many businesses have been forced to face, he’s mostly grateful his company is in a position to help. “We’ve been really fortunate in how everything has worked out for us but most importantly, we’re able to help those on the frontlines,” he says. “We’ve all been impacted but for our company it has primarily been about doing what you gotta do, gritting it out, and getting back to work. And we’re proud to be able to play any kind of role in getting through this.”