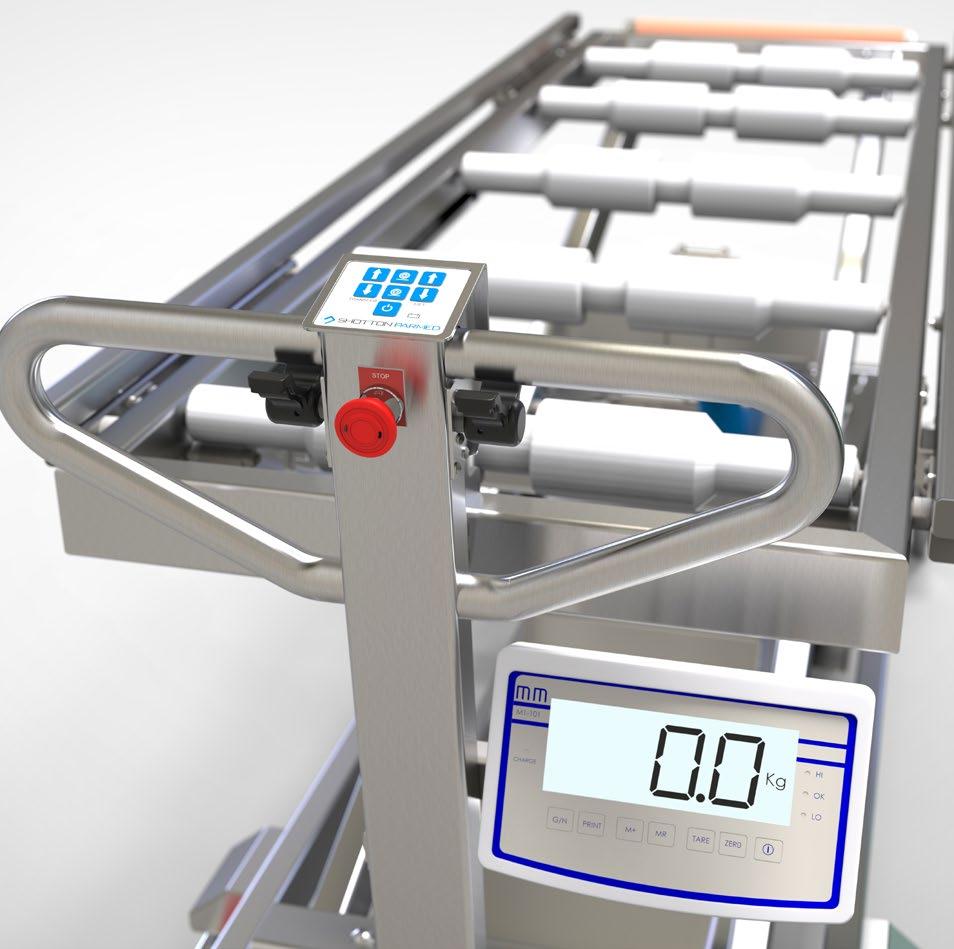
5 minute read
Certification Boosts Shotton Group’s Manufacturing Capabilities
The Shotton Group’s success story started in 1977, when founder Roy Shotton opened his family-owned business with nine employees. Today, the company boasts over 80 staff members, and has continued its strong focus on quality control and continuous improvement in the design, engineering and fabrication of metals. The company works with a range of customers across rail, bus, aviation, architectural, biomedical, forensic, and general infrastructure works. In line with their ongoing professional development, the Shotton Group was recently certified to AS/NZS ISO 3834 and EN 15085, which will help boost their manufacturing capabilities and bring a new list of clients on board.
According to Robert Lamb (Quality Systems and Work Health and Safety Manager, Shotton Group), family values remain at the heart of the company. “It’s still very much focused as a Shotton familybusiness. The company has its roots in the family, but we’re all very much a part of that family from the way that they treat their employees.”
Advertisement
Shotton Group was a pioneer in securing high-level projects, which presented some challenges, but also generated growth and interest in the business from the very start. “They wanted to cater towards the types of work that nobody else was really looking at – jobs that were traditionally deemed ‘too difficult’. We’ve still got a little bit of that occurring today, but the dynamic of the business has changed substantially since its inception,” Lamb said. Forty-four years later, the business has leveraged its expertise and branched out into different areas. “When the business was first conceived, it was merely a fabrication business, working with welding sheet metal. We began working with smaller and
Image: Shotton Group designs and manufactures hydraulic lifters from start to finish. Credit: Shotton Group. medium-sized companies. In the present day, we are an all-inclusive business. We cover design and design support for manufacturing and assembly, which allows us to make a product in a more economical way,” Lamb said.
“We can offer any size solutions. Whether it’s a complete solution, or just elements of what we do combined, we can tailor ourselves to suit our customers and their needs. We’re not scared of anything, which goes back to our founding principles that we’re happy to take on challenging and difficult tasks, because we have the capabilities to deliver where other similar businesses may not,” Lamb said.
The company’s all-in approach has also allowed them to branch into international markets. Today, Shotton exports to the United States, including biomedical sheet metal components manufactured to the Food and Drug Administration’s high standards.
NOTUS Project Saves Lives During COVID-19 The Shotton Group’s expertise was recently enlisted on the NOTUS project – a multinational conglomerate of companies that worked together in a partnership to provide ventilators for COVID-19 patients. Together, the partnership manufactured and delivered 2,100 ventilators across Australia. It was supported by a $31.3 million Federal Government supply contract. Overall, the project created or retained 250 jobs across the broad spectrum of suppliers.
“We rapidly developed the ventilators, got them approved and then went through a series of manufacturing stages through the partners that were involved. It was a pretty quick turnaround, as we were working on a tight schedule,” Lamb explained.
project, as we completed it during a time of great need. It was formed by one of our existing clients who received a government grant to build ventilators under licence.”
The Shotton Group used their 8,000m2 facility to deliver the project. The company’s head office and manufacturing hub is based in Melbourne, with a further five satellite factories within walking distance, and a warehouse in Queensland.
Their Melbourne facility includes the Amada Combination Laser and Punch, which is unique to the Shotton Group. It offers speed and excellence not matched by other machinery located at similar companies.
“We’ve got a combination machine that does laser cutting, turret punching, and has folding capacity. In that configuration, it is a one-of-a-kind machine in the southern hemisphere. That machine gives us the flexibility to stack up to five different types of materials and then pre-program different jobs to run during the day or night,” Lamb said.
The combination machine delivers a range of capabilities in one machine. It can operate on metal sheets with dimensions of 1,250cm x 2,500cm and boasts accuracy of +/- 0.1mm. In addition, it offers scratch-free processing of sheet metal parts that are complex in nature.
For further information, visit: shottongroup.com.au
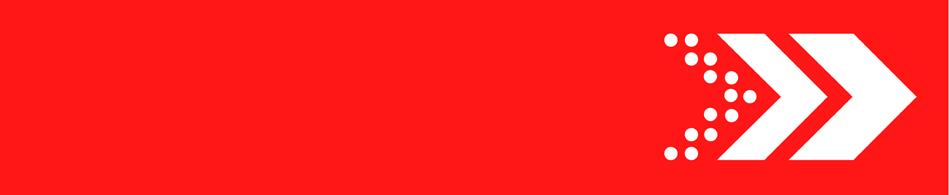
Image: Shotton Group’s Combination Laser and Punch. Credit: Shotton Group.
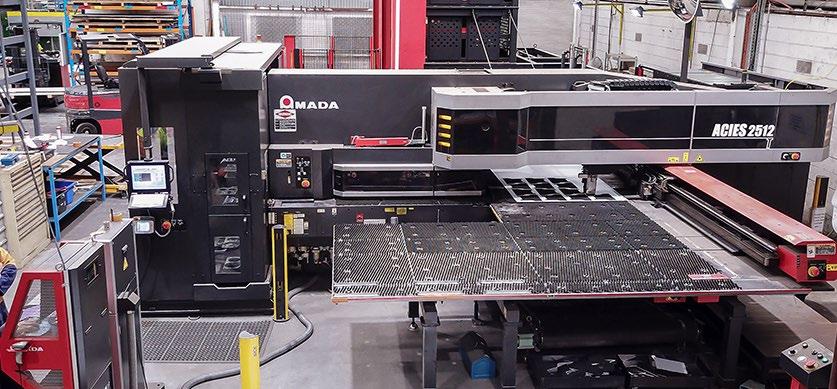
Image: A Shotton Group welder. Credit: Shotton Group. Achieving Certification to AS/NZS ISO 3834 and EN 15085 The Shotton Group recently received two certifications – AS/NZS ISO 3834 and EN 15085 – which will strengthen and add a suite of new opportunities to their business.
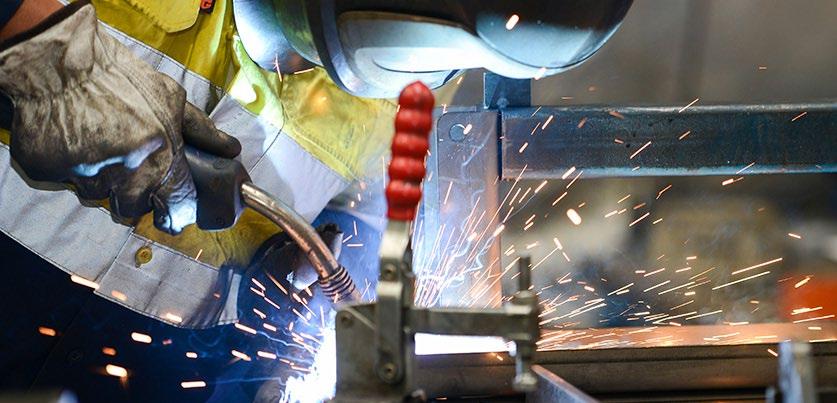
“It came about after a conversation with one of our major customers in the rail industry, who advised us that our welding needed to be lifted to stay in the game. We swiftly embarked on our journey to AS/NZS ISO 3834. Not only has it given us great opportunities with that customer, but it’s also opened the door to other opportunities too,” said Lamb.
AS/NZS ISO 3834 focuses on the minimum quality requirements for fusion welding. It is also a prerequisite for EN 15085, which is crucial for railway vehicles, their components and assembly.
Lamb first heard of EN 15085 three years ago at a seminar hosted by Bombardier, who play a crucial role in the delivery of Victoria’s local train network.
“It’s a mandatory requirement for the rail industry in Australia. Suppliers who supply product into the rail industry need to reach EN 15085, which you are unable to do unless you have AS/NZS ISO 3834, so it really did become a stepping stone for us.”
“I didn’t find the certification processes as hard as I thought, purely because there are so many similarities between AS/NZS ISO 3834 and ISO 9001. The difficulty came with qualifying the welders for the welding process and traceability controls for materials and consumables, and the inspecting and testing requirements,” Lamb said.
Lamb said the two certifications are allowing the Shotton Group to get ahead of the game, as only seven companies and suppliers are certified to EN 15085 in Australia. “We’re getting in early and we’re already seeing potential customers knocking on our door and giving us an opportunity to grow.”
He also offered some advice to other organisations considering the certifications.
“You have to look at the benefits it will have on the business, and the associated costs. It’s not a simple process to go through, and it can be quite costly. You have to go into it with your eyes wide open. It is a long-term commitment,” said Lamb.