
5 minute read
An Update from Weld Australia’s Hotline
Weld Australia offers a ‘Hotline’ service to all Corporate Members. The purpose of the Hotline is not to provide a solution, but to advise the enquirer on practical next steps. For further advice, Weld Australia’s highly experienced welding consultants can speak to you over the phone or visit your site in person. If you have a Hotline query, complete our online contact form and we will respond as soon as possible: www.weldaustralia.com.au/hotline.
The Weld Australia Hotline recently received a query from a member in relation to AS/NZS 1554.1 and the role of Welding Supervisors and contractors in the overall fabrication process. The member wanted an interpretation from Weld Australia about how the requirements of the Standard aligned with their business practices.
Advertisement
What is AS/NZS 1554.1? AS/NZS 1554.1 was originally published in 1974 and is based on the fundamental principles and practices of the North American AWS D1.1. The Standard refers specifically to structural steel welding, and is crucial for the welding of steel structures made up of several combinations of steel plates, sections, or sheet metals. In practice, welds that are completed under this Standard should be produced at minimal cost, meet compliance levels, and eradicate any rework or post-weld inspection and examinations.
Crucially, the Standard requires the fabricator to maintain a suitable system of quality management to ensure the overall quality of a weld, which falls into two categories: 1. Quality management: fabricators should ensure a well-managed and maintained quality
This Hotline update covers a specific query encountered during the last few months. Whilst accuracy in welding is critical, it is impossible to report in detail the full circumstances of the query. As such, Weld Australia recommends that further technical advice is sought in relation to specific, individual circumstances.
management system that correctly applies the requirements of AS/NZS 1554 is used. 2. Basic welding requirements: personnel should understand the requirements for technical inputs required to control the welding process under this Standard.
Like other Standards, AS/NZS 1554 outlines four fundamental values when conducting a weld: 1. Welds shall be made in accordance with a qualified welding procedure 2. Welds shall be carried out by a welder suitably qualified to carry out such a procedure 3. Welds shall be carried out under the supervision of a Welding Supervisor 4. Welds shall comply with the requirements of the
Standard
In line with the Standard, companies must appoint a Welding Supervisor. The role of a Welding Supervisor is to ensure that the weld process is managed before, during, and after a weld.
A Welding Supervisor may be seen as a job title, or a certain qualification attained by an employee. Therefore, it is critical that organisations specify the qualifications and requirements for their individual needs and services, and are transparent about any particular changes.
Some of the key responsibilities recommended for Welding Supervisors under AS/NZS 1554.1 include: • Working knowledge of AS/NZS 1554 • An understanding of welding safety • Basic cost estimation • Contract review and forward planning • Understanding the selection and care of parent materials • An understanding of welding consumables • Weld process control • An understanding of weld procedures, including the application of essential variables
• An understanding of weld defects and corrective actions • Delegation and supervision of personnel • Basic quality management skills including record keeping and traceability.
Organisations may employ Welding Supervisors with or without formal qualifications; the Standard omits the type of system and the level of accreditation required for Welding Supervisors, as these are considered commercial matters and may vary from organisation-to-organisation.
In some cases, an external contractor may be accepted rather than a full-time Welding Supervisor. This creates gaps within the overall knowledge base of the organisation and their availability, and some questions should be considered: • Who is responsible when the supervisor is not in the workshop? • What happens when business-as-usual changes? • Does the delegated person have a minimum understanding? • Are there opportunities to upskill other staff?
AS/NZS 1554.1 In Practice AS/NZS 1554.1 outlines specific details of the accepted and expected level of qualification for Welding Supervisors, which are outlined in clause 4.12.1 from section ‘a’ to ‘d’. Furthermore, subclause ‘e’ grants the option of a person whose competence is assessed and in line against AS/NZS ISO 14731. Importantly, it is expected that these personnel will have at least the same knowledge as the supervisor, which is defined in AS/NZS 2214 according to their tasks and responsibilities.
According to Weld Australia’s Paolo Corronca (National Manager Engineering), a supervisor assessment through AS/NZS 1554.1 Clause 4.12.1, section ‘e’ is subject to the personal interpretation and knowledge of AS/NZS ISO 14731. This ultimately forms part of the duties for the Welding Supervisor and comes down to the individual examiner. However, variations due to personal interpretation of the examiner can be limited where the fabricator has a clear job description for the supervisor.
Some organisations may find it harder to ensure a high standard of consistency across the board if different individuals are assessing this job function. According to AS/NZS 1554.1 in Clause 4.12.1 section ‘a’ through to ‘d’, a qualification issued by an approved and reputable training organisation ensures stricter compliance for assessing potential candidates and employees.
Weld Australia has seen evidence of companies which are using a contractor, particularly for smaller fabrication projects. While contractors may provide some benefits, Corronca believes that consistency is the key to success. Furthermore, he reiterated that having a contractor “on call” only, does not ensure that they would be available when needed, or that the business would avoid the call as much as possible to minimize the production cost. At the cost, this time, of the final product outcome.
“My preference is to have a full time, fully qualified Welding Supervisor – or a part time Welding Supervisor that works contracted, reasonable and scheduled number of hours per week in the fabrication workshop. This person should have a backup, or more knowledgeable person available at all times. The same would apply for workshops that work across multiple shifts,” said Corronca.
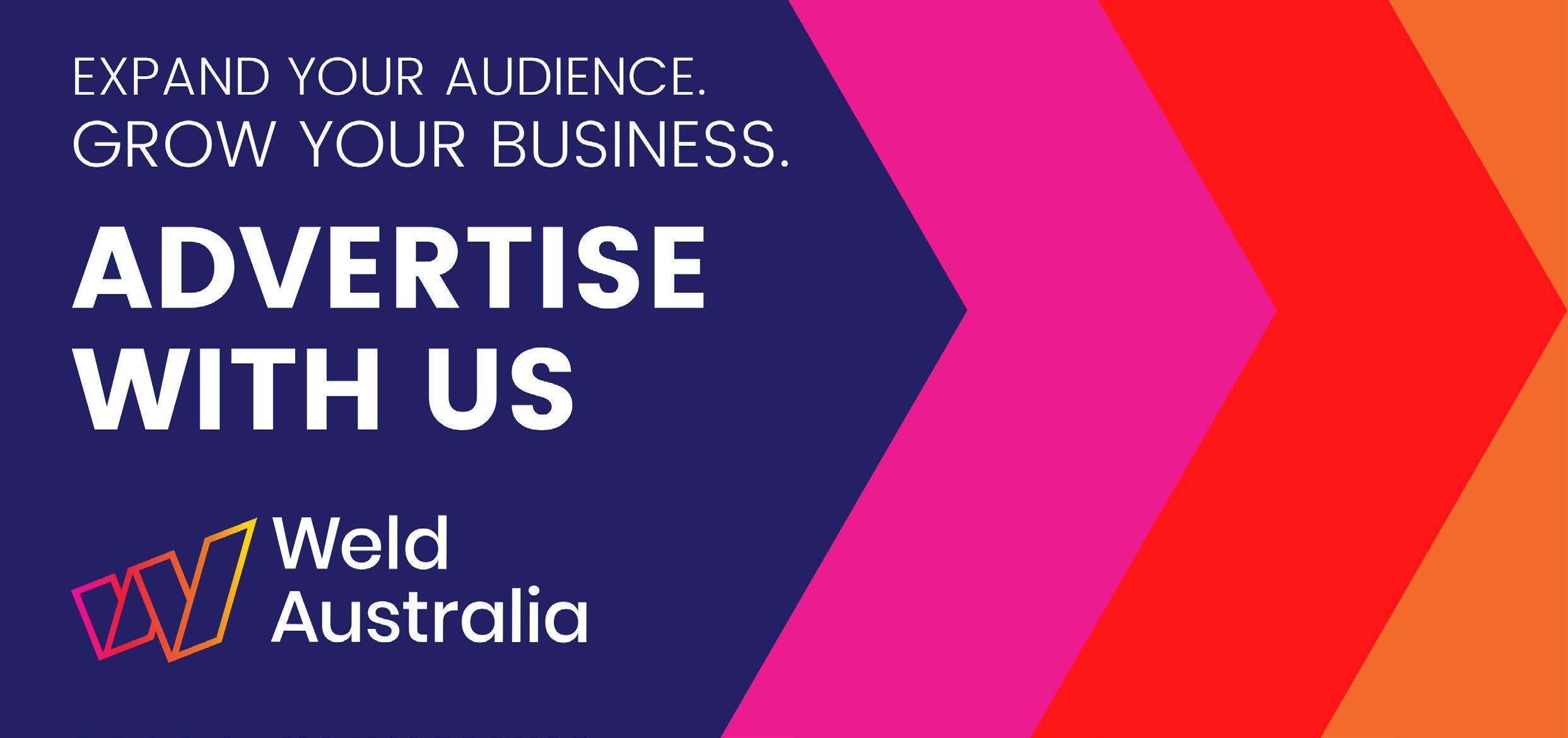