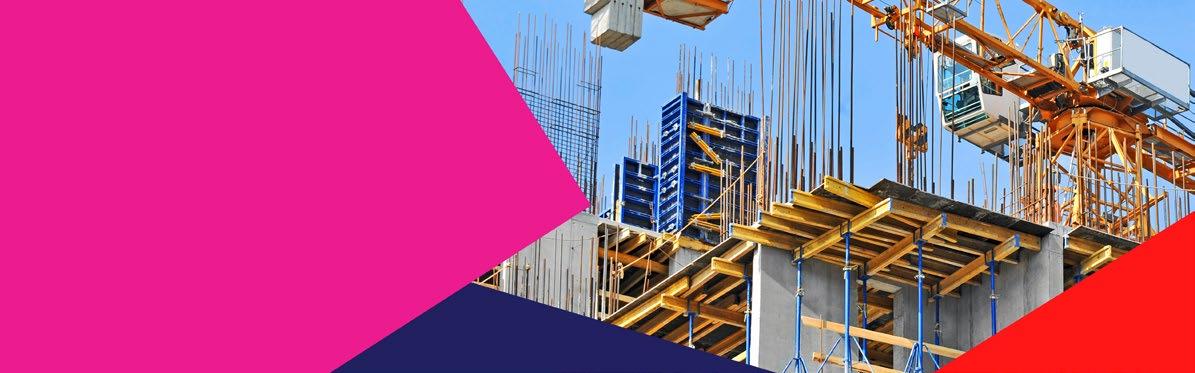
6 minute read
Health & Safety: How to Stay Safe When Laser Welding
Laser beam welding is a highly effective joining technique widely used across the welding and fabrication sector. The practice is underpinned by AS/NZS 2211.1 Laser Safety Part 1: Equipment classification requirements and users guide, which explains the risk categories and safety measures that must be adhered to when completing the practice. Weld Australia has also recently released a Technical Guidance Note to strengthen welder safety and provide practical tips in accordance with the Standard. Together, these safety guidelines and procedures explain the hazards, and the key responsibilities for equipment suppliers and welders who are conducting laser beam welding.
Laser beam welding is a fusion process where two pieces of metal are joined together by a laser. The practice is common across the welding and fabrication sector, but it does pose a range of hazards. However, there are Standards and procedures in place to minimise the risks associated with laser beam welding. The basic approach to nearly all laser safety standards has been to classify lasers according to their hazard potential, which is based on their optical emission.
Advertisement
According to AS/NZS IEC 60825.1 Safety of laser products Part 1: Equipment classification and requirements, laser manufacturers are required to certify that lasers are designated as one of eight risk classes, and labelled accordingly. Additionally, laser users are also responsible for acting in accordance with standardised safety measures to reduce or eliminate accidents. The following is a brief description of the categories of lasers (see also AS/NZS 1336).
Class 1 A Class 1 laser is considered safe according to existing medical knowledge. They do not involve any hazard, and no safety measures are required. There are two subcategories under Class 1 laser systems: • Class 1C: These lasers apply where the beam directly impacts the intended target and engineering controls are applied to prevent leakage at levels higher than that permitted for
Class 1. • Class 1M: Class 1M lasers exceed the emission levels of Class 1 lasers, but the beam divergence does not present a hazard to an unprotected eye. Importantly, if magnifying instruments like binoculars, telescopes, magnifiers, or microscopes are used to view the beam, eye damage can occur. Class 2 Class 2 lasers or laser systems are defined as operating in the visible region between 400-700nm. These lasers are not typically safe, but protection against eye damage can occur through aversion responses like blinking. A very brief exposure, of around 0.25 seconds or less, is not considered hazardous.
Class 2M lasers still operate in the visible region (400-700nm), but at higher power levels than Class 2 lasers. Because of the spread of radiation in laser beam welding, Class 2M lasers afford limited protection against eye damage because of the blink reflex and its response to bright sunlight.
The blink reflex provides little protection, and the beam is considered hazardous if the beam is columnated by optics, or if it is viewed through optical instruments. These instruments may include binoculars, telescopes, magnifiers, or microscopes.
Class 3 Class 3 lasers are medium-powered lasers, which may lead to a potential injury. Laser users who operate under this class may need to follow specific safety precautions, like wearing protective eye wear. However, skin hazards do not typically exist for incidental exposures under this classification. There are two subcategories under Class 3 laser systems: • Class 3R (Restricted): These lasers or laser systems can emit invisible or visible radiation and operate up to five times the power of Class 1 lasers (invisible radiation) or Class 2 lasers (visible radiation). However, they may have higher levels (25 to 50W.m-2) of radiant flux, or power. • Class 3B: Class 3B lasers can emit invisible or visible radiation and can cause eye injury.
Higher power lasers in this class may also cause skin burns. However, rapid heating of the skin will typically lead to an aversion response, which will avoid significant skin burns. This may not be the case for wavelengths like those in the ultraviolet region.
Class 4 Class 4 lasers are high-powered lasers, which may lead to serious potential for injury of the eye and skin. As such, users must follow specific safety precautions and wear laser protective equipment. Class 4 laser systems can produce a hazard from direct or specular reflections, and from a diffuse reflection. There are also fire risks linked with the use of such high-powered systems. Only Class 4 lasers are incorporated into systems used for materials processing, like cutting, heat treatment, surfacing and welding. However, a Class 4 laser may also form part of a system designed in a manner that can be considered as Class 1.
Hazards and Safety In materials processing, laser systems may cause injury from either the direct beam, or its specular reflections, or from diffuse reflections. The primary concern for welders and fabricators in laser beam welding is scattered radiation, which may lead to eye and skin damage. Weld Australia’s Technical Guidance Note divides laser hazards into primary and secondary categories. A primary hazard is the laser itself, which may impact humans or objects through radiation, raw beam, focused beam, or directly reflected beam.
Secondary hazards are slightly more complex, as they are subdivided into direct and indirect hazards. A direct hazard is related to the device, and typically includes electrical components, pump radiation, optical components, or laser gases. Indirect secondary hazards are related to the application, like ignition of explosives, fire hazard, secondary radiation, or emitted harmful substances.
Weld Australia has also identified a range of factors that can lead to tissue injury and influence the severity of damage from laser beam exposures, including: • Wavelength of laser radiation • Tissue spectral absorption, reflection, and transmission • Exposure duration • Size of irradiated area • Strength of irradiance of incident laser beam • Pupil size • Location of retinal injury • Laser pulse characteristics
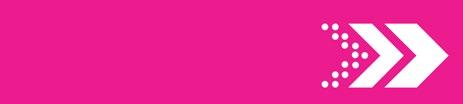
While skin damage is primarily restricted to burns, high-powered lasers can result in permanent damage. When conducting a laser beam weld, the safest prevention strategy is to ensure that the laser beam is encapsulated to minimise human exposure. In the event where a welder is exposed to the beam, the injury will be dependent on the level of exposure.
The level of exposure or irradiance, which determines the border between safe and potentially harmful exposure is known as ‘Maximum Permissible Exposure’ or MPE. Welders who work with a significant risk of exposure to laser radiation more than MPE should consider ongoing eye and skin examinations.
The ‘Nominal Ocular Hazard Area’, (NOHA) is the area around a laser, where the MPEs for the eye may be exceeded. Similarly, the corresponding distance from the laser exit opening is called the Nominal Ocular Hazard Distance (NOHD). Australian Standards contain several samples of NOHD, and other safe calculations for a range of geometries and exposure situations. In addition, the Laser Safety Officer in AS/NZS IEC 60825.14 is an employee who has knowledge about the evaluation and control of laser hazards. The Laser Safety Officer has responsibility for the control of laser hazards and may assist welders who are operating lasers.
To read Weld Australia’s Technical Guidance Note visit: weldaustralia.com.au
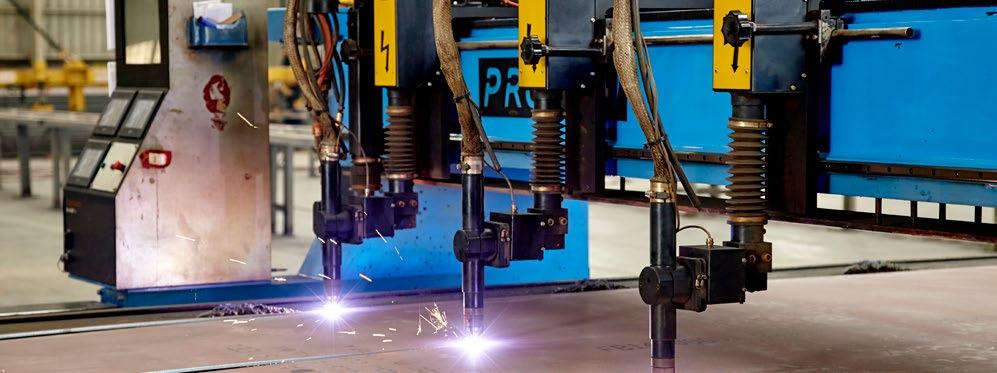