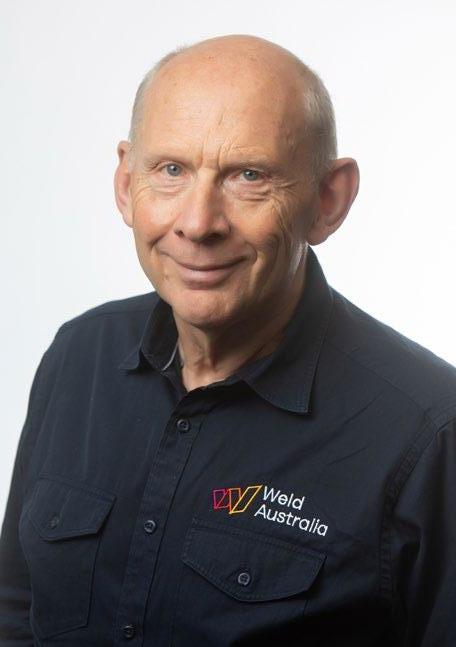
5 minute read
A Message From Weld Australia’s CEO
A Message from Weld Australia’s CEO: Geoff Crittenden
Australia’s jobs-driven COVID-19 recovery must be manufacturing led. Mandating compliance to Australian Standards—whether steel is fabricated in Australia or overseas—is the perfect first step to securing the future of the Australian welding and manufacturing industries. Given a level playing field, Australian welding is internationally price competitive, and of the highest quality. Without regulations that mandate compliance to Australian Standards for the manufacture, fabrication and erection of steel, procurement decisions will continue to focus on the lowest common denominator: cost.
Advertisement
Image: Geoff Crittenden (CEO, Weld Australia).
Now more than ever, it is vital that action is taken to secure the future of Australia’s welding and manufacturing industries.
Recent trade tensions with China illustrate just how important this is to our economy. Over the last 12 months, China has imposed trade strikes on half-adozen key industries including coal, wood, wine and seafood.
Yet, China is still taking every opportunity to export their products to Australia, including fabricated steel. Quite rightly, the Federal Government has not imposed reciprocal tariffs on China. With China’s capacity to inflict economic pain on us much greater than our own, reciprocal tariffs would likely do more harm than good. However, this situation can—and will—cost jobs in what is still quite a fragile industry.
For instance, the jobs of 150 workers in regional south-west Victoria are under threat following the award of the wind turbine towers contract for the $360 million Ryan Corner wind farm to an overseas company.
Danish company Vestas has sent the contract for the manufacture of 52 wind towers offshore. This is despite the fact that Keppel Prince Engineering— the only manufacturer of wind turbines on mainland Australia—is located just 70km away from the project site. As a result, Keppel Prince will likely be forced to make 150 workers redundant. In a regional town with a population of just 10,000 people, the economic fall-out will be severe.
The contract for the Ryan Corner wind farm comprises some 15,000 tonnes of steel. It is simply galling that a contract of this size has been sent offshore. Local manufacturers like Keppel Prince cannot win jobs on their doorstep when multinational companies like Vestas place a premium on price over and above quality and safety.
Nearly all locally manufactured steel used in Australian major projects is certified by the Australasian Certification Authority for Reinforcing and Structural Steels (ACRS). Local fabricators comply to internationally recognised Australian Standards and are certified by the relevant Australian authority. In this way, Government and NonGovernment clients can ensure the quality and safety of projects. Imported steelwork, which does not meet these requirements, is often of inferior quality and may not meet the Australian safety requirements.
Weld Australia has been calling on the Federal Government for the last five years to mandate that all steelwork in Australia—both local and imported— is manufactured and erected according to Australian Standards. The Federal Government must act now to save jobs in regional areas and ensure public safety. The importance of our local manufacturing industry and the development of robust renewable energy sources cannot be underestimated when it
The Federal Government has asserted that job creation is vital to our economic recovery. And yet, it seems unwilling to protect existing jobs. Australia’s jobs-driven COVID-19 recovery must be manufacturing led. Overseas, investment in advanced manufacturing is prioritised by governments. Local industry and populations support manufacturing by buying locally-made goods.
As a result, manufacturing employs millions of people in overseas markets, contributing billions of dollars to their economies. Now is the time to make manufacturing a national priority. Government, at all levels, must support and invest in the manufacturing sector to aid its growth. Mandating compliance to Australian Standards is the perfect first step.
We are not asking for government tariffs on all imported fabricated steel. Instead, we are calling on both sides of government to amend the necessary regulations to mandate compliance to Australian Standards whether fabricated steel is manufactured in Australia or overseas. Given a level playing field, Australian welding is internationally price competitive, and of the highest quality. Over the past three years, the number of companies certified to ISO 3834 has grown exponentially, with over 40 companies achieving certification. The number of ISO 9606 certified welders has grown in tandem. This growth has been largely driven by private clients (such as defence primes, and roads and transport authorities) specifying certification in tender documentation.
Whilst increased certification rates have substantially raised the quality of fabricated products in Australia, it has come at a substantial cost, and it needs to be paid for. It is completely unreasonable for clients to buy cheap, uncertified products from offshore, and not support local fabrication.
It appears that clients are still taking a very narrow view of project costs, allowing ‘cost to buy’ to dominate the procurement process rather than whole of life costs. If this is the case, then they are not delivering value to their shareholders or tax payers— merely concealing the true cost of the project.
Welcome to Weld Australia’s New Team Members Weld Australia has started 2021 in a strong position. We’re working on a range of new projects, with a whole variety of clients. As such, over the last couple of months, we’ve had some changes to our team.
Victor Blain has taken on the role of Engineering Team Manager and Arya Sharifian is now the Qualification and Certification Team Manager. Both Victor and Arya are still reporting to Paolo Corronca, who remains our National Manager Engineering.
We’ve expanded our team, welcoming several new team members: Haider Ali (Welding Engineer), Michele Boatswain (Education and Training Coordinator), Disha Mistry (Graduate Marketing Assistant), Luke Nicholls (Graduate Engineer, Qualification and Certification), Joseph Sandor (Welding Technology Trainer), Laya Pourabdi (Qualification and Certification Coordinator), and Deniz Yalniz (Quality Engineer).
Finally, I’d like to thank Anabel Cantero, our outgoing Qualification and Certification Coordinator, who is retiring after 30 years of dedicated service. We wish Anabel all the very best in her retirement.
