
9 minute read
The Issue of Non-Compliant Imported Rebar Cages and Steel Reinforcing
The issue of non-conforming building products, whether manufactured locally or imported, is an important and complex challenge of national significance. Non-conforming building products impact Australia’s welding, construction, manufacturing and retail sectors—just to name a few. Perhaps most concerning of all, these products can cause a raft of health and safety, economic, legal and social consequences.
Advertisement
With over 140,000 tonnes of steel reinforcement supplied to the Australian market each year from unknown origins, non-conforming materials present a huge risk to the performance of reinforced concrete, which is used in construction on a large-scale, such as in bridges, dams, piers, high-rise buildings and stadiums.
Industry experts believe that a program of education, awareness, training and certification is required. All welding should be undertaken by a JAS-ANZ accredited third party Processor in order to guarantee experienced operators, the use of conforming materials, and weld quality assurance. This due diligence can be relied upon in an unforeseen structural performance issue. Welding should also be carried out by a person qualified in the procedures required by AS/NZS 1554.3 Structural steel welding - Welding of reinforcing steel - Section 4.12.2.

According to research undertaken by the Steel Reinforcement Institute of Australia (SRIA), over 140,000 tonnes of steel reinforcement is supplied to the Australian market each year from unknown origins. This steel may, or may not, conform to Australian Standards.
Scott Munter (Chief Executive Officer, SRIA) explained that the vast majority of builders do not know whether their steel reinforcement complies with Australian Standards.
“When surveying small and medium builders, we found that 63% make the procurement decision about the supply source of reinforcing steel projects. SRIA market research found that 75% of those small and medium builders do not know if their steel reinforcement conforms to Australian Standards,” said Munter.
“Builders made comments like ‘I trust my concreter to do the right thing’ and ‘I’m assuming the retailer they get the steel from is supplying Australian made and quality compliant steel’.”
“Only one in four small and medium builders is confident their steel conforms to Australian Standards,” said Munter. The willingness of the Australian market to use imported steel from unknown origins is a real concern in tandem with the growing reliance on prefabrication.
“Bespoke prefabrication is on the increase, and there are now welding shops offering this service that may not have the required certifications and procedures to guarantee quality supply. These important prequalifications must be verified before procurement,” said Munter.
“Engineers and contractors are more frequently seeking processor made prefabricated cages, under controlled factory conditions, to speed up construction productivity, minimise site congestion, and move workers off-site and into controlled factory environments, thus obtaining more Green Star points through off-site prefabrication. This may even include higher strength steels (up to 750 MPa in fitment confinement regions), which reduces steel intensity.”
“The precast industry is a heavy user of prefabricated elements that must meet tight tolerances to maintain durability when placed in the forms.”
The Industry Experience With over 25 years industry experience, Bob Alesevic (Managing Director, RJB Industries) is no stranger to non-compliant imported rebar cages and steel reinforcing.
“Time and again, manufacturing products that do not comply with the relevant industry Standards are being imported into Australia. I’ve seen countless products that look similar to the products RJB Industries manufacture locally. But, when you look closely at the welding and the steel itself, it’s just not right,” said Alesevic.
“At the end of the day, it all comes down to price. As a local manufacturer, you can do everything right— you can adhere to every Australian Standard— but when competitors import products that are
significantly cheaper, clients just go with the option that’s best for their bottom line,” said Alesevic. “I’ve had companies from China approach me, offering similar products to those I manufacture, with a price tag that would only just cover the cost of my material—let alone labour. And I say no every time. I’m not interested because it’s just too risky. The problem with the plates and reo is, if they’re cast in concrete, you cannot see the problem until it’s too late—until the welds fail and there’s an accident. By then, it’s too late.”
“The last thing I want to hear is that a 16 tonne panel has collapsed and killed someone. I couldn’t live with that.”
“I understand that we’re all in business to make money, but the thing is, clients are not comparing apples with apples. There’s nothing wrong with competition – we all need competition. But how do you compete with the cheap imports? If imported products had to comply with Australian Standards and provide all the right documentation, they would likely be dearer than what we can manufacture locally,” said Alesevic.
“If we’re trying to keep work here in Australia, and give the next generation a chance, then we have to do something to shore up the local manufacturing industry. We need to push to have as much made locally as possible. Even in government contracts, a lot of the materials are being imported from overseas, and paid for with our taxes. The government needs to have a look at themselves.”
“We can—and do—make some top products in Australia. Our products are among the best in the world. But, to be able to compete with cheap imports, it’s got to be a fair game. At the moment, it’s not a fair game,” said Alesevic. The Dangers of Non-Compliant Rebar Cages and Reinforcing Steel Non-conforming materials present a significant risk to the performance of reinforced concrete. Most prefabricated cages include non-loadbearing welded joints that should comply with AS/NZS 1554.3 Structural steel welding - Welding of reinforcing steel, Clause 5.6 and Table 6.2 in the case of tack welds, and Section 3.3 for nonloadbearing welds. Either of these weld types can hold the cage during fabrication, transport, erection and concreting. While the welded joint strength does not contribute to the structure, it must not affect the performance of the reinforcement specified in the structural design.
Tack or ‘locational’ welds are generally used to hold parts of a weldment in alignment until the final non-loadbearing AS/NZS 1554.3 Section 3.3 welds (which consume the tack weld) are made. However, this is not necessary if the tack welds comply with the requirements of Clause 5.6 and Table 6.2 of AS/NZS 1554.3, and in particular Notes 6 and 7 to Table 6.2 as follows: • Note 6 requirements ensure there is no loss of cross-sectional area or imperfections • Note 7 (added by Amdt 1 in 2017) addresses the Note 6 requirements by stating: “Nonloadbearing welds shall not reduce the full loadbearing capacity of the structural elements (see Note 6)”
With today’s higher strength reinforcing steels there is a greater likelihood for incorrect or non-complying tack welding to reduce the strength of the steel. If the locational welds are too small they will have insufficient strength when lifted, or adversely change the bar metallurgy underneath. If the weld size does not meet AS/NZS 1554.3 Clause 5.6 and Table
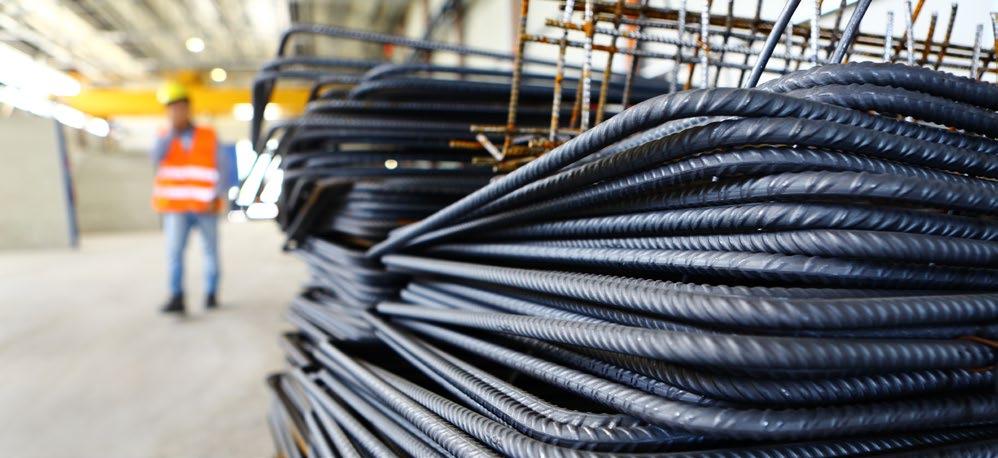
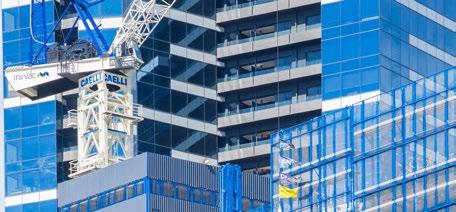
6.2 requirements, their limited heat affect and rapid cooling can lead to cracking, impacting strength and fatigue. Other key factors are unsuitable weld settings that can result in a loss of section and reduced design strength.
In prefabrication of cages for columns, beams, piles, walls and boundary elements or even roll-out mats, welding of reinforcing steel usually presents the highest non-conformance risk. Ideally, welding should be undertaken in the processor-controlled facility by qualified welders, but occasionally they are used to fix reinforcing steel placed insitu. AS/ NZS 1554.3 has prequalified welding requirements to ensure quality, but non-standard welding requires a welding procedure which needs to be tested and proven for compliance.
How to Ensure Quality There are three key elements required to ensure the quality of steel reinforcement: • A JAS-ANZ accredited third party Mill Certificate certifying that the stock bar and rod conforms to AS/NZS 4671 Steel for the reinforcement of concrete • A JAS-ANZ accredited third party Processor
Certificate certifying that the processed bar and welded mesh conforms to AS/NZS 4671 and complies with AS 3600 Concrete structures and
AS 5100.5 Bridge design – Concrete • All welding should be undertaken according to
AS/NZS 1554.3 Structural Steel Welding - Part 3: Welding of reinforcing steels in a controlled manner in the ‘processor’ facility. The JAS-ANZ accredited third party Processor Certificate covers the material properties and ensures that any weldability issues are addressed.
“You might assume you’re getting quality steel reinforcement from your supplier… but how do you know for sure?” said Munter. “Builders need to provide a JAS-ANZ accredited third party Processor Certificate (ACRS or equivalent) to the engineer and building certifier to guarantee steel reinforcing quality from the upstream mill supply and after the downstream processing. It’s all about traceability. To fabricate quality reinforcement cages, the weldability of reinforcing steel cannot be determined without knowing the material properties and chemical composition. The mechanical properties of steel reinforcement also change when a bar is bent or straightened from a coil and similarly when bars are welded together to make a sheet of mesh the mechanical properties of the final product have changed.”
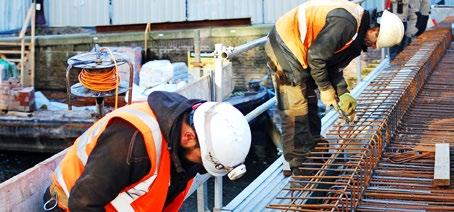
“Buying from an SRIA member, all of whom meet these important requirements guarantees the quality of materials and prefabrication. Once these requirements are met, the client can be confident that the structure is safe and robust, and adheres to the National Construction Code,” said Munter.
“If an SRIA Member is not supplying the prefabrications then the question should be asked… who is? Also, are they able to provide a JAS-ANZ accredited 3rd Party Processor Certificate to guarantee the quality of the reinforcement, and performance of welded connections.”
“When this certification cannot be provided, the procurer has no alternative but to implement a forensic process to verify conforming materials and welding, which will involve rigorous testing and assessment of long-term quality production data. This process will result in construction delays and add significant cost to the project.”
“Reinforcing steels are often seen as a commodity, purely shopped on price, ignoring these important quality requirements,” said Munter.
About the Steel Reinforcement Institute of Australia (SRIA) The Steel Reinforcement Institute of Australia (SRIA) is the leading non-profit national organisation providing high quality technical support and information service to the Australian building industry on the use of reinforcing steel in concrete, primarily reinforcing bar and reinforcing mesh. The organisation actively supports and encourages the use of Australian capability and quality in the processing and use of reinforcing steel in concrete in an increasingly global market. The SRIA was founded in 1988, reflecting the growing demand for technical assistance. For information, visit: sria.com.au.