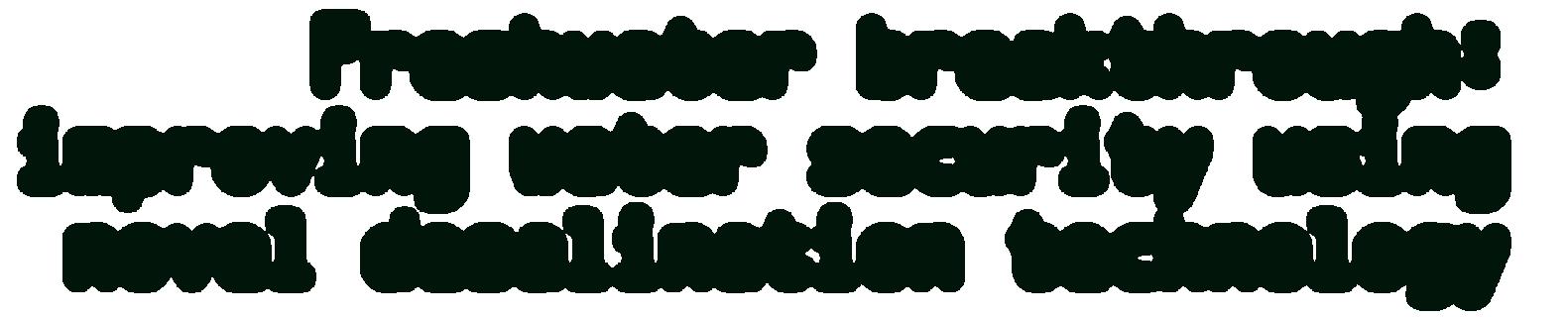
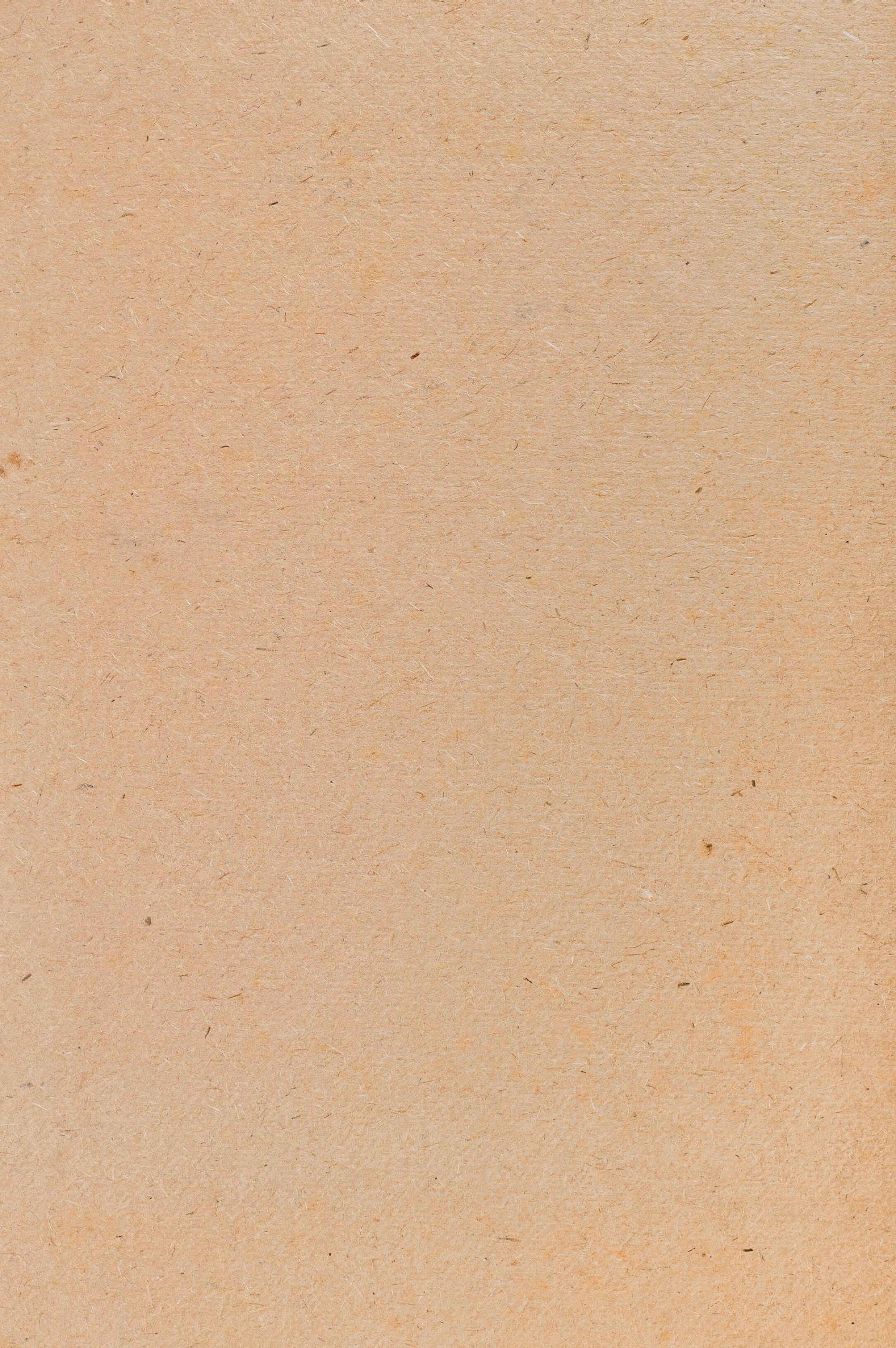
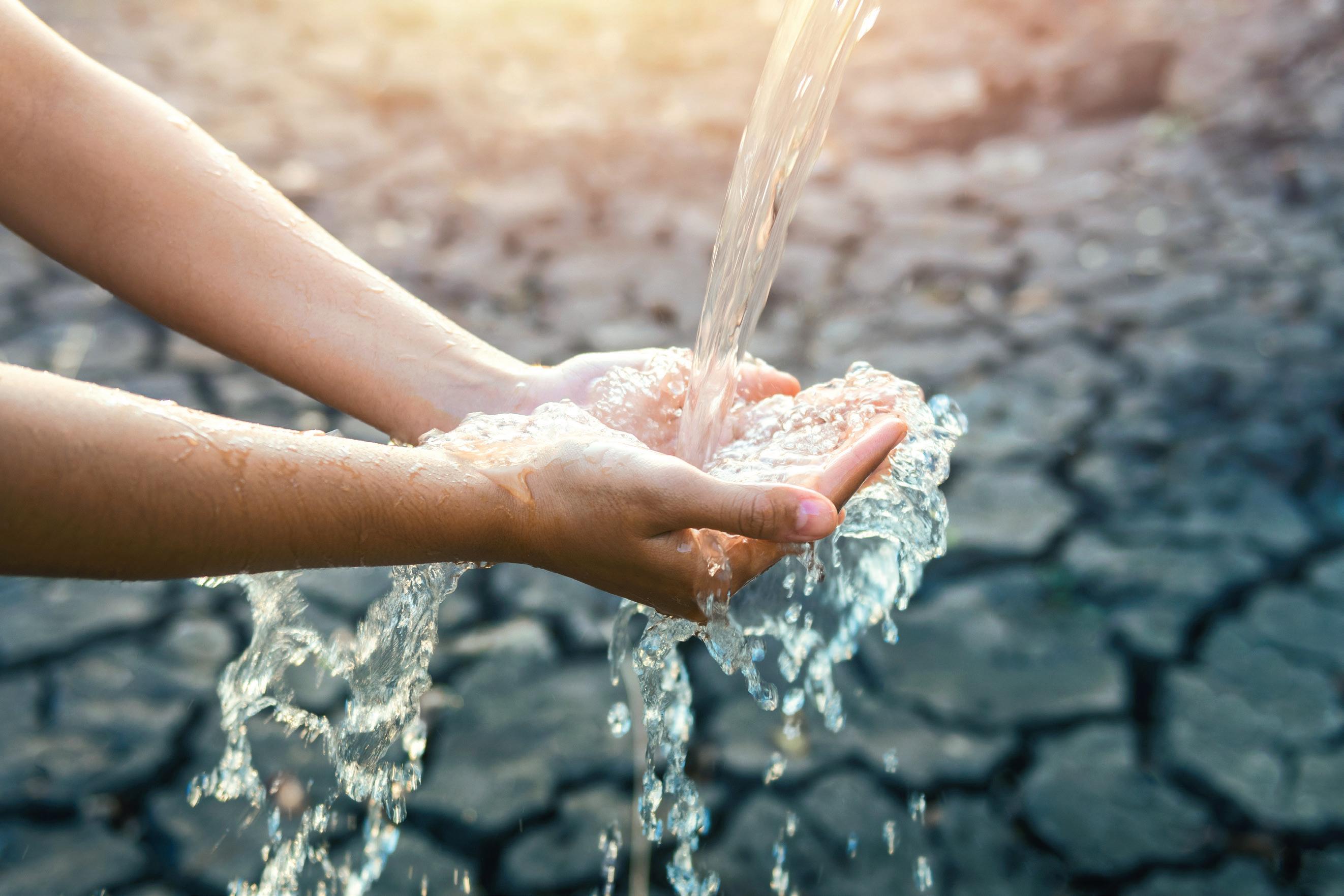
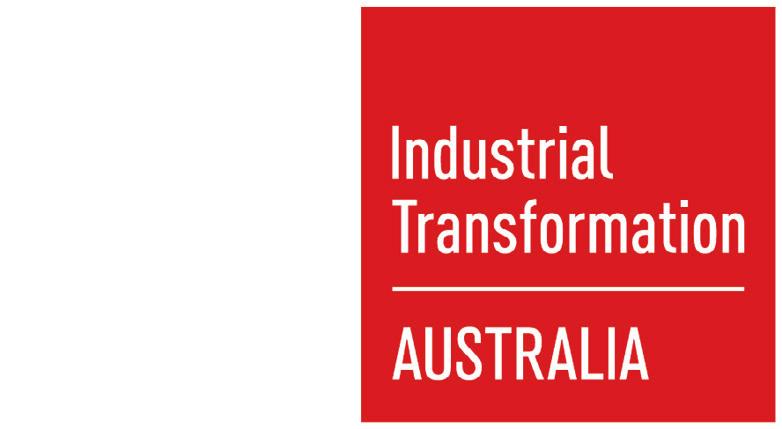
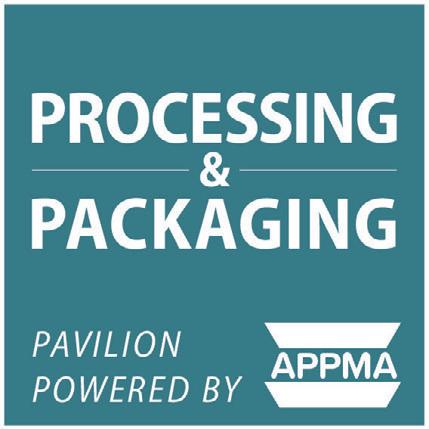
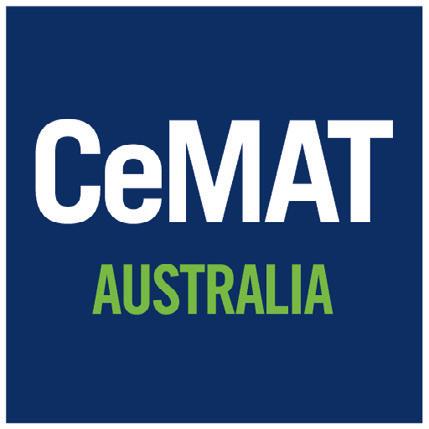
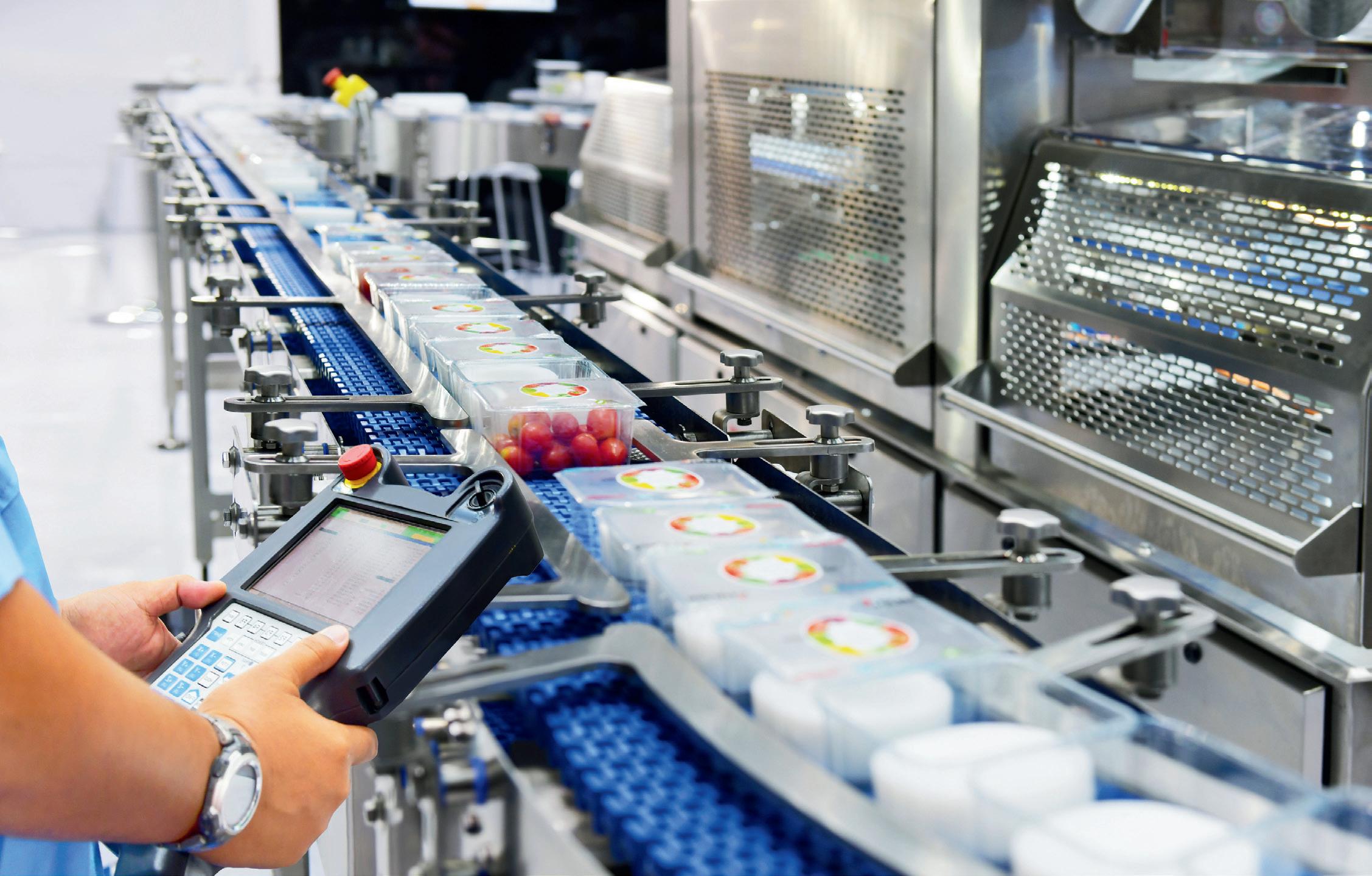
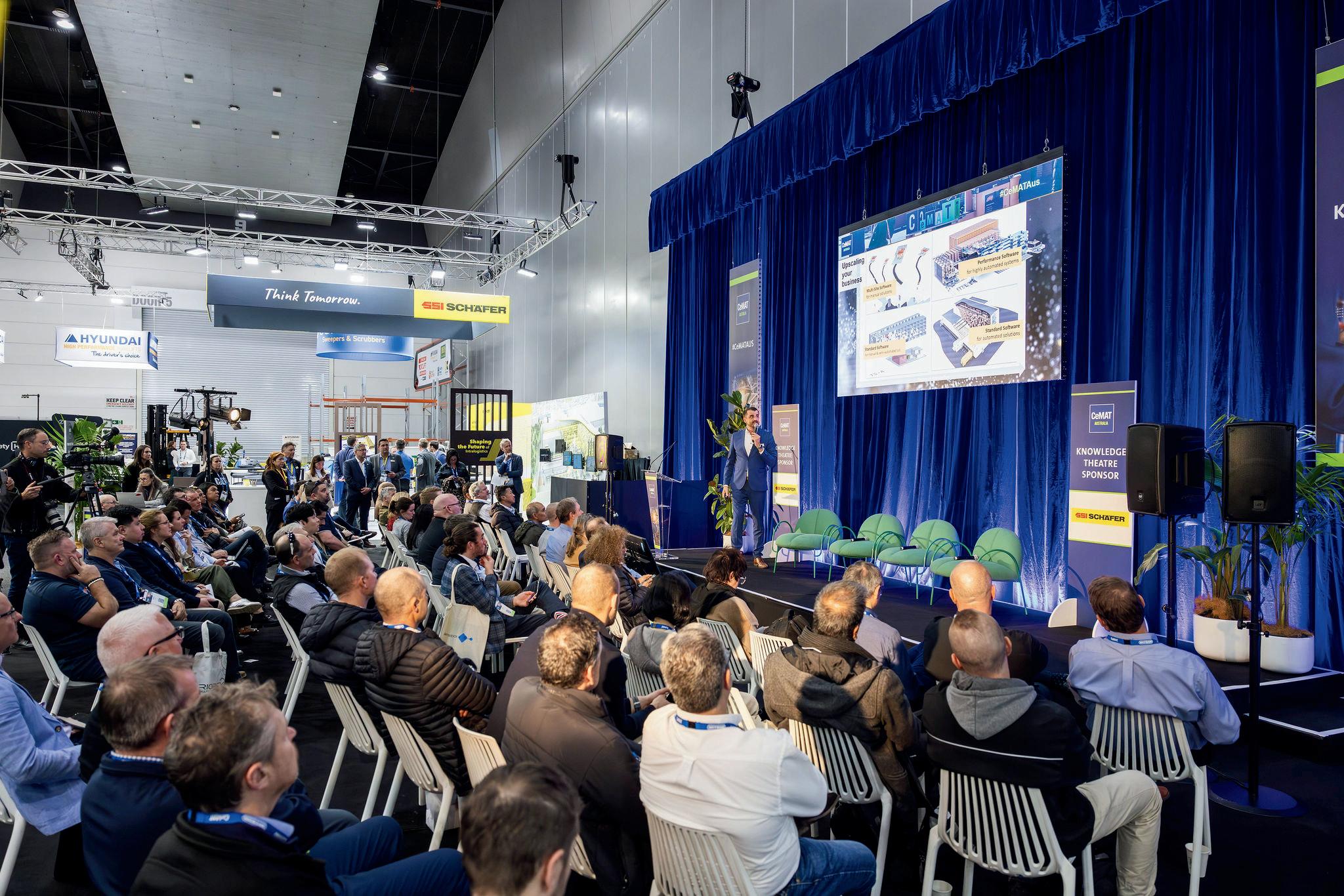
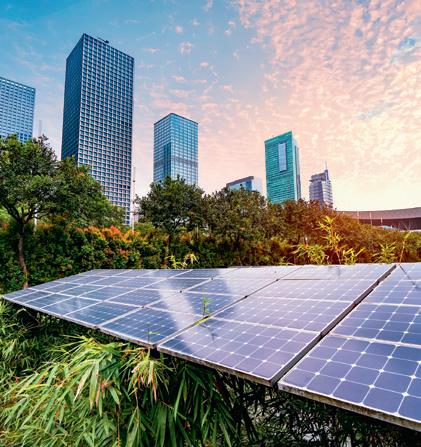

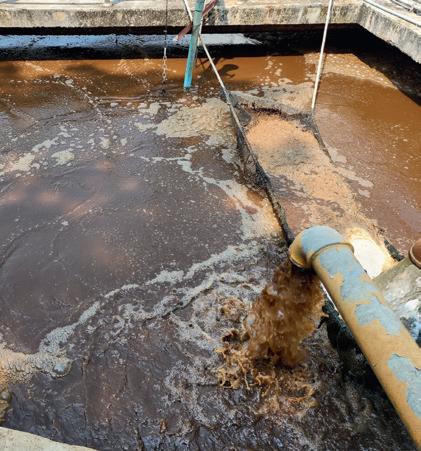
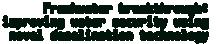
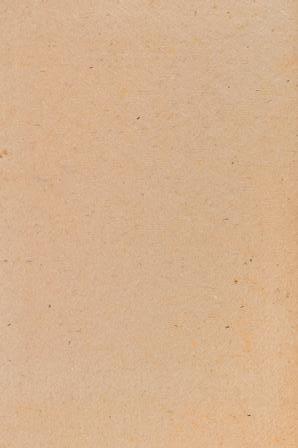
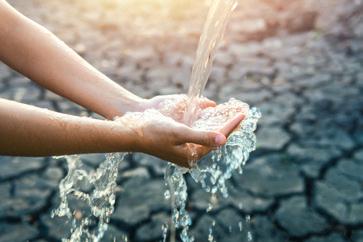
The north-east of Australia is currently recovering from flooding caused by tropical conditions, while most of southern Australia is experiencing the driest weather in decades and a decline in water storage.
According to the Bureau of Meteorology, the rainfall deficiency that began in southern parts of Australia in April 2023 reflects the impacts of climate change.
The Bureau states, “As detailed in the State of the Climate 2024 report, there has been a decline in rainfall from April to October in the south-west and south-east regions of Australia in recent decades. We are seeing more frequent periods of below-average rainfall during these months. Since 1994, cool season rainfall across southern Australia has been 9% below the average recorded from 1900 to 1993. This decline is attributed to a combination of natural variability over decadal timescales and changes in large-scale atmospheric circulation, largely driven by an increase in greenhouse gas emissions.”
To address our continent’s climate variability and the impacts of climate change, effective water management and greenhouse gas emission reduction strategies are essential.
In this issue, we explore how data centres are using water responsibly and a novel approach to desalination. We also examine some promising innovations, such as using rooftops for renewable energy and advancements in energy storage. Additionally, we present some interesting upcycling solutions that transform wind turbine waste into surfboards and utilise carbon dioxide in construction materials.
I hope you enjoy the read!
Carolyn Jackson sm@wfmedia.com.au
Westwick-Farrow Media
A.B.N. 22 152 305 336 www.wfmedia.com.au
Head Office Unit 5, 6-8 Byfield Street, (Locked Bag 2226) North Ryde BC NSW 1670, AUSTRALIA
Ph: +61 2 9168 2500
If you have any queries regarding our privacy policy please email privacy@wfmedia.com.au
Editor
Carolyn Jackson sm@wfmedia.com.au
Assistant Editor
Kylie Baracz
Publishing Director/MD Janice Williams
Art Director/Production Manager
Linda Klobusiak
Art/Production Marija Tutkovska
Circulation
Alex Dalland circulation@wfmedia.com.au
Copy Control
Ashna Mehta copy@wfmedia.com.au
Advertising Sales
Tim Thompson Ph: 0421 623 958 tthompson@wfmedia.com.au Printed and bound by Ive Group Print Post Approved PP 100007399 ISSN No. 1834-917X
All material published in this magazine is published in good faith and every care is taken to accurately relay information provided to us. Readers are advised by the publishers to ensure that all necessary safety devices and precautions are installed and safe working procedures adopted before the use of any equipment found or purchased through the information we provide. Further, all performance criteria was provided by the representative company concerned and any dispute should be referred to them. Information indicating that products are made in Australia or New Zealand is supplied by the source company. Westwick-Farrow Pty Ltd does not quantify the amount of local content or the accuracy of the statement made by the source.
The affordable solution you’ve been waiting for with peace of mind warranty for 5 years*
FULL RANGE OF AIR COMPRESSORS OIL LUBRICATED | OIL FREE | ROTARY SCREW | RECIPROCATING | PORTABLE
Meg Fricke, Partner with EY’s Climate Change and Sustainability Services team
As Australia ushers in a new era of climate-related financial disclosure, many organisations are gearing up for a significant shift in their reporting practices. Since 1 January 2025, the disclosure of Scope 3 greenhouse gas (GHG) emissions transitioned from voluntary to mandatory, marking a crucial step in the country’s commitment to addressing climate change. Scope 3 emissions, which encompass indirect GHG emissions occurring in an entity’s value chain, both upstream and downstream, present unique challenges for reporting entities. These emissions often constitute the largest portion of an organisation’s carbon footprint, making their measurement and reporting critical for understanding and mitigating climate-related risks and opportunities.
As organisations embark on their Scope 3 reporting journey, four key considerations should guide their approach:
• Track progress and set meaningful targets: Design your emissions inventory to accommodate future emission reduction initiatives. For instance, if you plan to work with key suppliers to reduce their emissions, structure your inventory to capture data on an individual supplier basis. This approach allows you to recognise decarbonisation efforts by specific suppliers rather than relying solely on industry-average emission factors.
• Collaborate across internal stakeholders: Scope 3 reporting requires input from various departments within your organisation. Engage with teams from procurement, logistics, sales and other relevant areas to ensure comprehensive coverage of your value chain. This collaborative effort is crucial for identifying the boundary of your Scope 3 inventory, determining which emission sources to include and understanding what data is available for each source.
• Be aware of potential overlaps: In certain sectors, Scope 3 emissions may overlap across different categories. For example, in the oil and gas industry, emissions from fuel combustion reported under “use of sold products” may also be captured in upstream and downstream transport categories. Consult sector-specific guidance to address these nuances and ensure accurate reporting.
• Recognise continuous improvement: Understand that your Scope 3 inventory will become more accurate over time. Initial calculations may rely on high-level estimates, often based on spend data, to identify the most significant indirect emission sources. Use these insights to focus on obtaining primary data for material areas in subsequent years. Document your approach and assumptions to support a repeatable process and facilitate external reporting and assurance.
The measurement of Scope 3 emissions often involves a combination of primary and secondary data. Primary data, obtained directly from specific activities within the entity’s value chain, provides the most accurate picture but requires significant effort to collect. Secondary data, derived from industry averages or proxy sources, is easier to obtain but may not fully reflect an entity’s specific activities or capture decarbonisation efforts by value chain partners. Organisations should prioritise data that is based on direct measurement, specific to their value chain activities, timely and verified. As reporting matures, entities can refine their data collection methods, moving from predominantly secondary data to more primary data for material emission sources.
While not mandatory under Australian Sustainability Reporting Standards (ASRS), setting Scope 3 targets is increasingly important, especially for entities where these emissions represent a significant portion of their total footprint. When setting targets, consider:
• Choosing an appropriate baseline year
• Defining the target boundary (specific categories or entire portfolio)
• Deciding between absolute or intensity targets
• Developing a clear plan to achieve the target Alternative targets related to Scope 3 emissions might include investment in downstream technology, supplier engagement goals, or initiative-oriented targets to improve understanding and measurement of the Scope 3 footprint.
As Scope 3 emissions reporting becomes subject to executive and board approval, it’s crucial to establish a robust controls framework. This includes understanding data sources, review processes, risk management, and oversight committees. Considering baseline assurance before mandatory limited assurance can help identify and address potential issues early.
The transition to mandatory Scope 3 emissions reporting represents a significant step in Australia’s climate action journey. While the process may seem daunting, organisations that start early, document their approach and embrace continuous improvement will be well-positioned to meet these new requirements. Remember, Scope 3 reporting is not just about numbers; it’s a valuable indicator of transition risk and an opportunity to drive meaningful change across your value chain.
As we move towards a more sustainable future, the insights gained from Scope 3 reporting will be instrumental in shaping business strategies, informing investment decisions, and ultimately contributing to global efforts to combat climate change.
Decisions that go into designing a new data centre will stay in place for many years to come. For instance, the cooling solutions often determine how the facility will consume vital resources such as water and energy. Equinix is committed to using water responsibly, which means we include several considerations about the local water context as we design our data centres.
Last year, we were designing a new data centre in an area where the public had concerns about water stress. The facility was originally intended to use evaporative cooling, which relies on evaporating water to cool the building. The benefit of this approach is that it is substantially more energy efficient than cooling systems that don’t use water.
We conducted an in-depth water stress analysis to gain a more comprehensive understanding of the local water context. This analysis included assessing physical water availability, infrastructure and local resiliency planning to understand how prepared the
metro was in case of increased water stress.
Although the metro was well prepared for a drought or other increases in water stress, we decided to switch the building cooling system to use air cooling. Since air cooling consumes substantially less water, we proactively aligned with local concerns about water stress, which reflects our commitment to minimising our impact. However, air cooling also consumes more energy, which is why it isn’t right for every location.
When it comes to balancing the trade-offs between water and energy consumption, getting it right during the design phase is essential, as there are only opportunities for incremental water efficiency improvements after a data centre is operational.
According to the Pacific Institute, a leading research institute focused on water issues, water scarcity refers only to volumetric availability: the ratio of human water consumption to available water supply in an area. In contrast, water stress is a broader, more inclusive concept. Water scarcity is one aspect of water stress, but it also includes other physical factors, such as water quality and environmental flows, and economic factors such as water accessibility.
Understanding the local water context, including water stress levels, is the foundation of our approach to using water responsibly. In 2023, we codified our commitment to avoid using evaporative cooling in areas with high water stress because using evaporative cooling is by far the largest driver of water consumption in data centres.
How does data centre cooling impact water consumption?
IT equipment running in data centres creates heat, and that heat has to go somewhere. Choosing a cooling solution will determine
how a facility consumes water and energy, which are both essential aspects of any data centre operator’s sustainability strategy. However, cooling systems are needed at both the server level and the building level. As servers generate heat, the server-level cooling system moves the heat away from the servers to a heat exchanger, which transfers the heat to the building-level system. The building-level system then rejects the heat from the building. There are different options for both serverlevel cooling and building-level cooling:
• At the server level, air cooling has long been the standard practice, but liquid cooling is becoming more prevalent to support higher server density for AI and other compute-intensive workloads. One misconception about liquid cooling is that it’s the same as evaporative cooling. However, unlike evaporative cooling, liquid cooling doesn’t necessarily increase water consumption because it uses a small amount of water moving continuously in a closed loop, rather than being evaporated.
• At the building level, the two primary methods for rejecting heat from a data
Data centre designers typically choose between air cooling and evaporative cooling based on the unique climate conditions of each specific location.
centre are air cooling (or dry cooling) and evaporative cooling. Evaporative cooling can reject the same amount of heat as air cooling while consuming significantly less energy. However, it also consumes significantly more water via evaporation. Data centre designers typically choose between air cooling and evaporative cooling based on the unique climate conditions of each specific location. To determine the most suitable system they’ll consider the local climate (weather), power availability, water stress and other factors. For instance, evaporative cooling can be particularly effective in managing energy usage in areas with power-constrained grids. In contrast, avoiding evaporative cooling in water-stressed areas minimises water consumption, thus ensuring more water remains available for use in the community.
Balancing this trade-off is at the core of our responsible water strategy. In 2023, we use evaporative cooling at only 40% of our data centres globally. We also take advantage of alternative cooling methods where local conditions allow:
• Geothermal cooling methods such as aquifer thermal energy storage (ATES) and deep lake water cooling (DLWC) utilise natural cooling provided by the Earth’s thermal mass. They draw cold water from large natural sources to circulate through the building-level cooling system, thus causing the water to absorb heat from the heat exchanger. Rather than rejecting it into the atmosphere via evaporating the water, geothermal cooling returns water to its original source. Therefore, the process doesn’t consume water. Similarly, one of our data centres in Toronto uses a DLWC system that pulls cold water from the depths of Lake Ontario. With this approach, we’ve reduced total energy needs for this data centre by 50%, without increasing water consumption.
• Data centre heat export allows a portion of the heat in a data centre to be transferred to a third-party heat network rather than
being rejected into the atmosphere. The heat can then be used for heating homes and businesses. This not only avoids unnecessary water consumption in other buildings’ cooling systems, but also provides a low-carbon heat source for communities. Equinix is pursuing heat export in select locations worldwide. In Paris, heat recovered from our PA10 data centre is transferred to the Plaine Saulnier urban development zone, including a swimming pool used at the recent Paris Summer Olympics.
transparency around water consumption
Recognising that many of our stakeholders want to know more about how we use water and how we’re working to use it more responsibly, we’ve taken steps to increase transparency on our water use.
In 2023, for the first time, we disclosed our water metrics via the CDP water security initiative and included water metrics in our annual sustainability report.
In addition to our water optimisation efforts, our operations team is developing and implementing water efficiency best practices and improving our water metering systems at all existing data centres that use evaporative cooling.
Externally, we are collaborating with our peers and industry working groups to develop measurement frameworks and standards to support water reporting efforts. Earlier this year, we joined the California Water Action Collaborative, a network of diverse stakeholders pursuing collective action projects that improve water security in Equinix’s home state.
We’re also co-funding our first offsite nature project in Finland with Neoen, our local renewable energy partner, to restore 50 hectares of high-value peatland and streams. Since offsite projects like this one often provide both water and biodiversity benefits, we’re sponsoring the development of a framework to account for biodiversity benefits along with water benefits from these kinds of projects.
A novel approach to make seawater evaporate faster than freshwater has been hailed as a significant breakthrough in desalination technology and could help to ease water scarcity.
Seawater desalination is an effective strategy to alleviate the impending water scarcity in some parts of the world, but existing processes consume massive amounts of energy, leaving a large carbon footprint. Considering the global desalination market — which numbers around 17,000 operational plants worldwide — even small declines in desalination performance can result in the loss of tens of millions of tons of clean water.
Researchers from the University of South Australia (UniSA) have already demonstrated the potential of interfacial solar-powered evaporation as an energy-efficient, sustainable alternative to current desalination methods,
but they are still limited by a lower evaporation rate for seawater compared to pure water due to the negative effect of salt ions on water evaporation.
UniSA materials science researcher Professor Haolan Xu has now collaborated with researchers from China on a project to develop a simple yet effective strategy to reverse this limitation.
By introducing inexpensive and common clay minerals into a floating photothermal hydrogel evaporator, the team achieved seawater evaporation rates that were 18.8% higher than pure water. This is a significant breakthrough since previous studies all found seawater evaporation rates were around 8% lower than pure water.
“The key to this breakthrough lies in the ion exchange process at the air–water interface,” Xu said. “The minerals selectively enrich magnesium and calcium ions from seawater to the evaporation surfaces, which boosts the evaporation rate of seawater. This ion exchange process occurs spontaneously during solar evaporation, making it highly convenient and cost-effective.”
The mineral materials used in the process included halloysite nanotubes (HNTs), bentonite (BN), zeolite (ZL) and montmorillonite (MN) in combination with carbon nanotubes (CNTs) and sodium alginate (SA) to form a photothermal hydrogel.
“This new strategy, which could be easily integrated into existing evaporation-based desalination systems, will provide additional access to massive amounts of clean water, benefiting billions of people worldwide,” Xu said.
The researchers say the hydrogel evaporator maintained its performance even after months of immersion in seawater.
The next steps will involve exploring more strategies that can make seawater evaporation faster than pure water evaporation and apply them into practical seawater desalination.
The findings* have been published in the journal Advanced Materials
*'Making Interfacial Solar Evaporation of Seawater Faster than Freshwater' is authored by researchers from the University of South Australia, Shenzhen Institute of Advanced Technology, Jinan University, Tianjin University, University of New South Wales, University of Adelaide, Shanghai Jiao Tong University and Nanjing Forestry University.
The Galltec+Mela Humidity and Temperature sensors with ATEX certification are suitable for use in potentially explosive atmospheres and areas with combustible dust equipment of category 1G, 1/2G and 2D. The sensors consist of a sensor part with a sintered filter (both made of stainless steel) on a robust die-cast aluminium housing (transmitter part). MELA-humidity/temperature sensors in this series are used to measure relative humidity and temperature in air, and other non-aggressive gases in explosion hazardous areas and locations with inflammable dust.
Connection to a non-intrinsically safe electric circuit for humidity (F*C3.Ex/8) and for temperature sensors (T*C3.Ex/8) is achieved with a 1-channel transmitter power supply unit, and for the combined humidity and temperature sensors (K*C3.Ex/8) either with a 2-channel or with two 1-channel transmitter power supply units with galvanic isolation between input-/output circuits and power supply.
These IP65 rating humidity/ temperature sensors provide two analog outputs of 4–20 mA with the accuracy for humidity ± 2 %RH 5...95 %RH at 10 ...40 °C and temperature ± 0.2K at 23°C. The humidity/temperature sensor is mounted on the wall of the hazardous area with class 1 requirements by using assembly kit ZA 40.
Possible applications for these types of sensors include industries like chemical, drying, pharmaceutical, paper & print, environmental, mining and paint shops, etc.
Slentech Pty Ltd www.slentech.com.au
Lauris Technologies (LaurisTech) has announced a leap forward in ultrasonic gas flow measurement technology with the release of the TT-0825 series ultrasonic transducers. Engineered to operate in extreme temperatures ranging from -80 to +250°C, these transducers are designed to set a new standard for gas flow meters.
Flare gas flow measurement, often encountered in industries with process gas temperatures exceeding 150°C, has posed a unique challenge for conventional ultrasonic gas flow meters. Lauris Technologies has addressed this challenge with the TT-0825 series, which is specifically designed for these environments.
AMS Instrumentation & Calibration Pty Ltd www.ams-ic.com.au
ACCIONA has partnered with Australian professional surfer Josh Kerr and his brand Draft Surf, to create surfboards made from a retired wind turbine blade.
The initial range, crafted from a decommissioned blade from ACCIONA’s Waubra wind farm in Victoria, included 10 prototype surfboards as part of the company’s Turbine Made initiative.
The surfboards, hand-crafted on the Gold Coast, feature repurposed turbine blade strips built into the deck for strength and flex control. The fins of the board, made from recycled fibreglass, are said to provide stability, drive and speed, and the outer shell is further strengthened by incorporating recycled turbine blade particulate into the fibreglassing process.
Kerr said, “When ACCIONA approached us about being part of the solution and working together to create these surfboards, we jumped at the opportunity. At its core, our brand is about enabling the best surfing experience with quality products, in a sustainable way — which aligns with ACCIONA’s vision for Turbine Made.”
Launched in February 2025, Turbine Made is an initiative dedicated to exploring ways to transform decommissioned wind turbine blades into new materials and products. It represents the next step in ACCIONA’s efforts to advance circular economy in the renewable energy sector in Australia.
ACCIONA Energia’s global sustainability director Mariola Domenech said, “We know that in the next five to 10 years, countries like Australia will have a large volume of decommissioned wind turbine blades, so we’re acting now to explore new ways to recycle and reuse the material they are built from.
“The creation of a surfboard prototype, developed locally, is an example of how we’re reimagining the materials from decommissioned turbine blades and pushing the envelope of innovation when it comes to the circular economy.”
The Turbine Made initiative builds on ACCIONA’s previous work to repurpose decommissioned wind turbine blades. This includes a collaboration with European fashion brand El Ganso, to create sneakers featuring recycled blade material in their soles and integrating recycled blade materials into the torsion beams of solar trackers at a solar plant in Extremadura, Spain.
The company is also advancing in end-of-life turbine recycling through the development of a blade recycling plant in Navarra, Spain, which is set to become operational in 2026, creating 100 jobs and a processing capacity of 6000 tonnes of material per year.
“Sustainability isn’t just about reducing waste, it’s about product stewardship, ensuring that what we build today doesn’t become tomorrow’s environmental challenge,” Domenech said.
“By working with Australian manufacturers, designers and innovators, we can encourage the creation of practical, high-performance applications that benefit both industry and the environment.” Acciona Australia Energy www.acciona.com.au
Around 359 billion cubic metres of wastewater is produced globally each year.1 In propelling towards sustainability, wastewater treatment providers are facing the challenge of effectively handling a variety of treatment chemicals. Sustainability is driving the use of higher concentration chemicals to minimise transport costs and emissions, as well as reduce the size of dosing systems. High concentration chemicals require a very accurate and repeatable pump to maintain process capability. Peristaltic pumps with low pulsation and no ball valves result in parts per million (ppm) concentrations with very low standard deviations, minimising chemical usage and maximising process quality.
In response to the challenges of disinfection and neutralisation, coagulants and flocculants, and urbanization that demand more powerful pumps with high flow rates and low pulsation to increase efficiency, Watson-Marlow Fluid Technology Solutions has designed pump technology solutions to enable wastewater treatment providers to overcome different process challenges.
After calls from plant managers for more powerful and adaptable pumping equipment that enables accurate, flexible and high capacity dosing, the Qdos H-FLO was designed. The pump is capable of flow rates up to 600 litres per hour and can handle pressures up to 7 bar via a range of interchangeable pump heads. The different pump heads enable the pump to be used in a wide range of wastewater applications and allow plant managers to respond quickly as treatment processing requirements change.
The Qdos H-FLO has a pressure sensor that detects leaks and blockages. The pump stops before the system becomes damaged and alerts the operator with diagnostic feedback. In
addition, all of the chemicals are safety contained within the pump head, preventing operator exposure. If there is a problem, the pump head can just be changed. The twin-tube technology provides extremely low pulsation, with an offset rotor design protecting pipework integrity and providing consistent chemical supply compared with diaphragm pumps delivering similar flow rates. Unlike diaphragm pumps, the Qdos H-FLO has no valves, eliminating the issue of valves becoming stuck or blocked. In addition, the pump has a high accuracy of ±1%, which prevents chemical waste and saves costs.
Wastewater treatment providers face a variety of operating challenges, including handling a wide range of chemicals, meeting high demand, and becoming more sustainable. However, with the correct pumping technology, wastewater plant managers can ensure their operations run efficiently, accurately and safely.
1. https://essd.copernicus.org/articles/13/237/2021/
Watson-Marlow Fluid Technology Solutions www.wmfts.com/en-au
Energy experts present two contrasting viewpoints on the topic of achieving full electrification on a global or regional scale — green electricity or alternative renewable energy sources?
At the Energy LIVE 2024 conference in Houston, Texas, the path to a net-zero emissions future was a hot topic.
In a session titled ‘The Great Electrification Debate’, energy experts Dr Tej Gidda and Dr Peter Benyon, both from GHD, discussed whether full electrification is possible on a global or regional scale.
Speaking to an audience of industry insiders, policymakers and innovators, Gidda and Benyon presented equally ambitious but contrasting viewpoints. One championed the promise of green electricity while the other advocated for alternative renewable energy sources.
“We are already making significant progress toward electrifying everything. Over the past decade, electricity demand has grown at nearly twice the rate of overall energy demand, and this trend is accelerating rapidly,” he said.
To bolster his argument, Benyon pointed to community-led projects like Electrify 2515, where 500 homes in the city of Wollongong are transitioning from gas to electric appliances.
The case for electrification Benyon, GHD’s Australian Market Leader – Power, opened with a vision of electrification across residential, commercial, industrial and transportation sectors, citing the rapid adoption of renewable energy and advancements in energy efficiency as cornerstones of a clean, sustainable future.
“With net zero objectives in focus, green electricity — produced from abundant resources like wind and solar — stands out as the cleanest and most cost-effective energy source.
“Harnessing these natural resources, coupled with energy storage, makes transitioning to an all-electric system an obvious choice.
“The benefits are clear — cleaner air, lower noise pollution and significant cost savings. Green electricity is not simply better for the environment; it is also healthier and more affordable for communities,” he explained.
He also highlighted progress in Australian states and territories including South Australia, Tasmania and the Australian Capital Territory, which are well on their way to, or have already achieved, net 100% renewable electricity and have advanced electrification initiatives.
Electrification would also be economically beneficial, he said. “Every heat pump and EV we deploy brings tangible savings for households. It is not just about the planet — it is about people’s wallets.
“We’re also seeing breakthroughs in energy storage, including lithium, sodium and vanadium technologies, which will support and stabilise grids and enable deeper electrification.”
In a session titled ‘The Great Electrification Debate’, energy experts Dr Tej Gidda and Dr Peter Benyon, both from GHD, discussed whether full electrification is possible on a global or regional scale.
The case for alternatives
Gidda, GHD’s Global Leader for Future Energy, presented a different perspective, questioning whether electrifying everything is realistic in the short term.
“The power generation required for full electrification is enormous, and in many regions, it is simply not feasible today,” he argued.
Gidda said that affordability was another critical barrier, using North America as an example of a region where consumers and businesses face high costs of transitioning to electric systems even with subsidies.
“We don’t currently have enough power generation to electrify everything. The anticipated increases in demand are already outpacing our ability to generate new power, and we are struggling to meet existing needs,” he said.
“How can we possibly address the additional requirements for full electrification when we’re already behind on capacity for today’s demands?”
However, existing infrastructure in North America still offers untapped potential for decarbonisation, Gidda said.
“We have millions of miles of pipelines that can be repurposed for renewable natural gas and hydrogen. Why abandon these assets when we can use them to reduce emissions today and do so to maintain affordability?”
Gidda cited North American projects converting agricultural waste and landfill gas into biomethane, as well as Toronto’s efforts to displace natural gas with renewable sources created from food waste.
He also underscored the limitations of battery electric vehicles, particularly in heavyduty transport.
“There are not enough lithium reserves globally to electrify all vehicles, and this is a real problem. We need complementary solutions, such as hydrogen and low-carbon fuels.”
Both Gidda and Benyon agreed on the need to advance energy technologies to support the energy transition.
Benyon advocated for diverse energy storage methods, from mechanical processes like compressed air to thermal storage.
“Storage innovation is key to grid reliability and scalability. It is how we will meet growing demand without compromising stability in a renewable electricity grid,” he said.
Gidda made the case for blending hydrogen into existing natural gas systems to decarbonise without costly infrastructure overhauls.
“This approach reduces emissions immediately, with minimal disruption to consumers,” he explained.
When asked what near-term actions are critical for achieving net zero by 2050, Benyon called for aggressive grid decarbonisation and expanded infrastructure, with targeted support for low-income communities to ensure equitable transitions.
Gidda stressed the need for comprehensive national energy policies and public–private partnerships. “This is too big for any one sector to tackle alone. Collaboration is our best shot at success,” he said.
Gidda said that solutions must be tailored to the realities of each region. “There is no single path to net zero,” he said. “For me, I do not believe ‘electrification’ is the answer on its own. It needs to be a combination of electrification and decarbonisation.”
Benyon agreed on the need for diverse approaches, adding, “What matters most is that we act decisively and collaboratively. Every step forward is a step toward a cleaner, greener world.” iStock.com/kynny
New research out of the University of California, Davis and Stanford University has found that storing carbon dioxide in building materials could hugely reduce global greenhouse gas emissions.
The study, conducted by civil engineers and earth systems scientists, has been published in the journal Science . “The potential is pretty large,” said Elisabeth Van Roijen, who led the study as a graduate student at UC Davis.
Van Roijen and her colleagues are presenting this approach as an alternative — more effective — type of carbon sequestration.
Carbon sequestration aims to take carbon dioxide, either from where it is being produced or from the atmosphere, convert it into a stable form and store it away from the atmosphere where it cannot contribute to climate change. Previous proposals have involved injecting carbon underground or storing it in the deep ocean; however, these approaches pose both practical challenges and environmental risks.
“What if, instead, we can leverage materials that we already produce in large quantities to store carbon?” Van Roijen said.
Along with Sabbie Miller, associate professor of civil and environmental engineering at UC Davis, and Steve Davis at Stanford University, Van Roijen worked to calculate the potential for storing carbon in a variety of common building materials including concrete (cement and aggregates), asphalt, plastics, wood and brick.
More than 30 billion tons of conventional versions of these materials are produced worldwide every year.
Some of the techniques the team studied included adding biochar (made by heating waste biomass) into concrete; using
artificial rocks that can be loaded with carbon as concrete and asphalt pavement aggregate; and incorporating biomass fibre into bricks. They also considered the use of plastics and asphalt binders based on biomass rather than fossil petroleum sources.
These technologies are at different stages of readiness, with some still being investigated at a lab or pilot scale and others already available for adoption.
The team found that while bio-based plastics could take up the largest amount of carbon by weight, concrete has by far the largest potential for carbon storage. This is because concrete is the world’s most popular building material, with over 20 billion tons produced every year.
“If feasible, a little bit of storage in concrete could go a long way,” Miller said. If 10% of the world’s concrete aggregate production were carbonateable, it could absorb a gigaton of CO2, according to the researchers’ calculations.
With the feedstocks for these new processes being mostly low-value waste materials such as biomass, Van Roijen said that implementing the new approach would enhance their value, creating economic development and promoting a circular economy.
While some development is needed, particularly in cases where material performance and net-storage potential of individual manufacturing methods must be validated, Miller said many of these technologies are just waiting to be adopted.
Van Roijen is now a researcher at the US Department of Energy National Renewable Energy Laboratory. The work was supported by Miller’s CAREER grant from the National Science Foundation.
Westfalia Fruit has committed to using all parts of the avocado across the supply chain, including the skins and seeds, to make new, sustainable products.
Avocados imported for retail, food service and wholesale customers are carefully inspected and any unsuitable avocados are processed at Westfalia’s facility into products like avocado pulp, smashed avocado and guacamole.
However, the avocado skins and seeds from the process, previously typically used in low-value applications such as anaerobic digesters, are now finding new, higher-value alternative uses.
Having partnered with Efficiency Technologies, the value of the entire by-product channel of avocado skins and stones is assessed to optimise use, with the most recent development being a technology extracting a natural, sustainable dye from avocado stones, with SAGES London.
The process extracts perseorangin (a rare and sought-after natural pigment) from avocado stones collected at Westfalia's UK facility. The pigment offers eight distinct shades ranging from light yellow to rich reddish-brown, creating new opportunities for sustainable colouring solutions across multiple industries.
The specialised extraction method isolates perseorangin, which constitutes approximately 3% of the avocado stone, and processes it into a dried powder form, providing extended shelf life.
“This breakthrough represents a significant step in our journey toward our total crop use strategy,” said Andrew Mitchell, Head of Group Innovation at Westfalia Fruit.
“By transforming what was once considered by-product into a valuable resource, we’re creating sustainable solutions that benefit multiple industries. The ability to produce eight distinct natural shades while maintaining our commitment to use the entire
fruit demonstrates the potential of innovative thinking in sustainable agriculture.”
Besides the dye extraction, remaining materials from the avocado skins and stones are also processed into additional products — for example, starches are directed to paper manufacture as a precursor to packaging production, while ground materials find applications in cosmetics as natural exfoliants, as alternatives to micro-plastics.
The natural dye extraction process represents an advancement in sustainable practices, particularly as industries increasingly seek alternatives to synthetic dyes.
The powder format enables stability and ease of use across various applications, while the range of the eight distinct natural shades provide versatility for different product requirements.
This innovation comes at a time when consumer demand for natural, sustainable products continues to rise across fashion, beauty and packaging sectors. The pigment’s successful showcase at London Fashion Week highlighted its viability in sustainable fashion, while ongoing collaborations with industry leaders in cosmetics and packaging demonstrate its cross-sector appeal.
Plans are underway to understand how the technology could be expanded to additional Westfalia facilities in Europe, where more avocado by-product can be processed using the same techniques.
The company’s integrated operations enable efficient collection and processing of avocado stones and skins from multiple production sites, which will help to maximise the sustainable impact of the initiative and builds upon Westfalia’s commitment to sustainability and circular economy principles.
Westfalia Fruit www.westfaliafruit.com
A pioneer wind turbine tower design is set to be put on trial south of Adelaide in a novel research collaboration between Flinders University and startup company VAWT-X Energy.
Supported by state and federal funding, the research team constructed and tested a 6 KW vertical wind turbine prototype to install at a field site on the Fleurieu Peninsula.
The low-maintenance two-bladed helical vertical axis wind turbine design comprises a rotor with a shaft connected
to a brake and generator. This new design could help to increase the sustainability and energy operating costs of residential, agricultural and light industrial operations close to metropolitan areas, as well as largescale offshore windfarms.
Engineering experts at Flinders University are challenging the trend of using horizontal axis wind turbines by working with VAWT-X Energy’s vertical axis wind turbine (VAWT) design to develop innovative prototypes of large-scale VAWTs, set to be tested in realworld conditions.
Designed with quiet operation and adaptability in mind, the large standalone vertical turbines are shaping up to be just as efficient, if not more so, than their horizontal counterparts, said Dr Amir Zanj, head of the Advanced Wind Energy Technology (AWET) research group based at Flinders University’s Tonsley campus.
“Darrieus’ VAWTs can thrive across diverse environments, whether they’re set up as single units, part of urban infrastructure, or scaled up for larger wind farms,” Zanj, from the College of Science and Engineering, said in a recent review article in the journal Energies
“They offer advantages like high power density on wind farms, greater stability for offshore use, and adaptability to urban areas with shifting winds — all while being quieter and more economical to operate.”
VAWT-X Energy founder Gary Andrews said the new wind turbine aims to address some of the longstanding aerodynamic challenges, potentially providing a more sustainable, versatile alternative for renewable production in Australia and elsewhere.
“We believe our VAWTs are not only more efficient but also more accessible for applications like off-grid power and sustainable energy solutions for small businesses and farms,” he said. “The design of these new VAWT-X Energy turbines solves some of the traditional barriers for Darrieus designs.”
Along with private equity funding, research and development will continue with a new grant from the Australian Government. The project is also supported by a $300,000 grant from the Department of State Development in South Australia. Flinders University www.flinders.edu.au
< Members of the Advanced Wind Energy Technology (AWET) group at Tonsley. Left to right: Chun Hin So, Bahar Amani, Abolfazl Abdolahifar, Mohsen Feyzi, Dr Amir Zanj and Mohammad Mahdi Jalilvand with the latest scaled-up version of the 6 KW VAWT-X Energy model assembled at the Tonsley Innovation Precinct on 9 January 2025.
A $17 million upgrade is currently underway at Evoro’s Laverton North liquid and hazardous waste management facility in Melbourne, including new weighbridges and enhanced truck unloading processes.
Coming after a comprehensive five-year planning and approvals process, the upgrade is expected to be completed in late 2025.
“Our forte at Laverton North is handling difficult-to-treat industrial waste, giving it a second life through recycling or preparing it for safe disposal,” said Evoro Victoria General Manager Jenny Barnes.
“It’s a responsibility we conduct with professionalism and pride, knowing that such products could cause havoc if they were misused or illegally dumped, especially in waterways.”
The works are targeted at increasing the facility’s versatility so that it can handle a range of liquid and hazardous waste management services, including:
• neutralising acids and alkaline materials for safe disposal or discharge as stormwater (eg, acids used in galvanising processes to manufacture corrosion-resistant products);
• processing wastewater for safe discharge as stormwater (eg, wastewater resulting from industrial plant washdowns);
• separating and purifying water from oil, such as workshop ‘oily water’ (water mixed with oils and other lubricants), where recovered oil can be reused as an industrial fuel source;
• purifying waste glycol (antifreeze) for reuse;
• processing hard-to-treat liquids such as hydrogen fluoride and waters containing PFAS for safe disposal or reuse.
Evoro Chief Executive Officer Susan McBurney said the investment would incorporate leading global technology and practice.
“This is a sweeping site overhaul enabling us to modernise operations to world-class standard,” she said. “Our clients from multiple industrial sectors will reap the benefits of better efficiency, costeffectiveness and service.
“Much of what we’re doing is a response to client feedback, and in line with strict regulatory requirements.”
The upgrade will bring Evoro closer to reaching maximum treatment capacity, currently at 60 million litres per year. Fulltime employment at the facility is also scheduled to rise, from 34 people to 40 people.
Industrial development specialist LSR Construction Group is completing the works, after being selected via a tender process run by Evoro and Tango Projects.
Evoro
evoro.com.au
A team of scientists at UNSW Chemistry has developed an organic material that is able to store protons, which is being used to create a rechargeable proton battery in the lab.
By using hydrogen ions (protons) instead of traditional lithium, the batteries hold promise for addressing some of the critical challenges in modern energy storage, including resource scarcity, environmental impact, safety and cost. The team’s latest findings, published in the journal Angewandte Chemie , highlight the battery’s ability to store energy quickly, last longer and perform well tunder sub-zero conditions.
The material — tetraamino-benzoquinone — was developed by PhD candidate Sicheng Wu and Professor Chuan Zhao, in collaboration with UNSW Engineering and ANSTO, and has been shown to support rapid proton movement using hydrogen-bond networks.
“We have developed a novel, high-capacity, small-molecule material for proton storage,” Zhao said. “Using this material, we successfully built an all-organic proton battery that is effective at both room temperature and sub-zero freezing temperatures.”
Batteries store chemical energy and convert it to electrical energy through reactions between two electrodes — the anode and cathode. Charge-carrying particles, known as ions, are transferred via the middle component of the battery, known as an electrolyte.
The most common batteries used in household products are lithium-ion batteries. These batteries, which create an electric charge by transferring lithium ions between the anode and cathode, are the most widespread portable energy storage solutions.
Lithium-ion batteries power everyday products such as mobile phones, laptops and smart wearables, as well as newer e-mobility
products such as electric cars, e-bikes and e-scooters. However, they are very difficult to recycle and require huge amounts of water and energy to produce.
“Lithium-ion batteries are already becoming a dominant product in energy storage applications, but they have a lot of limitations,” Wu said.
“Lithium is a finite resource that is not evenly distributed on Earth, so some countries may not have access to low-cost lithium sources. Lithium batteries also have [a] very big challenge regarding fast-charging applications, safety and ... low efficiency in cold temperature.”
Although we currently rely very heavily on lithium-ion batteries, a growing number of alternatives are emerging. In particular, proton batteries are gaining attention as a sustainable alternative in the energy field for energy storage devices.
Protons have the smallest ionic radius and mass of all elements, which allows them to diffuse quickly. Using protons results in batteries with high energy and power density, and protons are relatively inexpensive, produce zero carbon emissions and are fast charging.
“There are many benefits to proton batteries,” Wu said. “But the current electrode materials used for proton batteries, some of which are made from organic materials and others from metals, are heavy and still very high cost.”
While a few organic electrode materials already exist, they also suffer from limited voltage range, and further research is required to make them viable batteries.
Redox potential is a fundamental parameter in electrochemistry. It is related to the flow of electricity, which is important for designing batteries. The range of redox potentials in a battery is important because it affects the battery’s performance. Usually, the redox potentials of cathode materials need to locate in a high range and that of anodes need to locate in a low range to ensure a desirable battery voltage output.
To create their electrode material, the research team started with a small molecule, called tetrachloro-benzoquinone (TCBQ), which includes four chlorine groups. Although TCBQ has been used previously to design electrode materials, the redox potential range of this compound is mediocre — neither low enough to be used as an anode nor high enough to be used as a cathode.
So, to start, the team set out to modify TCBQ to increase its performance as an anode material.
After multiple rounds of modifications of the compound, the researchers settled on replacing the four chloro groups with four amino groups, making it a tetraamino-benzaquinone (TABQ) molecule. By adding amino groups, the researchers significantly improved the material’s ability to store protons and lower its redox potential range.
“If you just look at the TABQ material that we have designed, it’s not necessarily cheap to produce at the moment,” Zhao said. “But because it’s made of abundant light elements, it will be easy and affordable to eventually scale up.”
When the researchers tested the proton battery, the results were promising.
Combined with a TCBQ cathode, the all-organic battery offers a long cycle life (3500 cycles of fully charging and then fully
draining the battery), high capacity and good performance in cold conditions.
“The electrolyte in a lithium-ion battery is made of lithium salt, a solvent which is flammable and therefore is a big concern,” Zhao said. “In our case, we have both electrodes made of organic molecules, and in between we have the water solution, making our prototype battery lightweight, safe and affordable.”
Given the low cost, high safety and the fast charging performance of the proton
battery designed through this collaboration, it has the potential to be used in a variety of situations, including grid-scale energy storage. As noted by Wu, “At the moment, we don’t have any suitable solutions to gridscale energy storage, because we can’t use tons of lithium batteries to do that job due to the price and lack of safety.
"To enhance the usage of renewable energies, we have to develop some more efficient
energy integration technologies and our proton battery design is a promising trial.”
While the potential applications are vast, the researchers are determined to refine and perfect their proton battery.
“We have designed a very good anode material, and future work will move to the cathode side. We will continue designing new organic materials that have higher redox potential range to increase the battery output voltage,” Wu said.
We specialise in Industrial Test & Measurement Sensors/Transducers: Pressure, Temperature, Laser Displacement, Flowmeters, Water Meters, Pneumatic Controls, Joysticks, Rotary Encoders, Accelerometers and LVDTs Instrumentation: Dataloggers, DAQ Systems and Digital Display Units.
As Australia accelerates its push for renewable energy, a major opportunity is being overlooked — commercial rooftops and car parks. From warehouses to factory buildings, these large, unused spaces in urban and industrial areas could be transformed into powerful sources of solar energy.
According to Partners in Performance, a major barrier to renewable energy expansion in Australia is the strong opposition from rural communities who fear the takeover of arable land by solar farms, wind turbines and transmission pylons, all to satisfy the needs of EV-driving city dwellers.
Critics also cite infrastructure costs to connect a myriad of renewable sites to the grid and the inefficiencies that a decentralised system creates — the further electricity travels, the fewer electrons reach the end user.
While some of these concerns are rooted in reality, the truth is Australia needs to find more ways to generate renewable energy closer to consumers and industry, and it has to happen now.
Experts at the company say that an opportunity being overlooked is the vast amount of unused commercial rooftop and car parking space in outer urban areas, at warehouses, freight and logistics hubs, and factories.
August’s 2024 Electricity Statement of Opportunities, the annual 10-year outlook for the National Electricity Market, produced by grid operator AEMO, warned more attention had to be paid to consumer energy resources (CERs).
CERs include residential and commercial rooftop solar and batteries — to ensure power system security is maintained.
Australian Industry Group CEO Innes Willox was reported saying the AEMO report showed there would be serious power shortfalls this decade, and she called for a sustained national effort to speed up plan-
ning, approval and delivery of new energy infrastructure.
To achieve this, we must look beyond the best puff of wind or patch of solar and find places to build more batteries and solar close to readily achievable connections. In some suburbs experiencing a lot of curtailment a step up in storage devices is needed to harness the green energy currently wasted.
Australia is famous for its urban sprawl. There are many large car parking lots and roofs in urban areas — and we can fit them with solar connected to batteries and the grid. This is much more tractable, both in terms of the bite size and the cost per unit of generation capacity.
It would be an efficient use of space, generate revenue for rooftop owners, and cut transmission costs for everyone.
Factories and warehouses typically have large, flat roofs that are ideal for solar panel installations. These roofs are rarely overshadowed by trees and other buildings, making them highly suitable for generating solar energy. Many industrial and logistic sites also have a little bit of spare space where batteries could go. Some batteries of up to 8 MW can now fit into four car spaces (think of a 20 ft container with extra space around it to distribute the weight). And the essential ingredient: connection sizes. Industrial sites have larger connections than homes. This is essential for faster rollout of batteries — in some Australian regions, connection upgrades can take anything from one to three years.
Generating electricity onsite improves energy security by reducing dependence on the grid, and pairing it with batteries can mitigate the impact of power outages or fluctuations as well as reduce energy costs for businesses.
Collectively, rooftop solar is the second largest source of renewable electricity generation in Australia (behind wind energy
generation), and the fourth largest source of electricity generation, making up approximately 11.2% of the country’s installed capacity for power supply.
Last year, the state, territory and federal energy and climate change ministers released the National Consumer Energy Resources Roadmap, reporting that one-third of Australia’s households have installed rooftop solar. Total capacity of rooftop solar across Australia amounted to 22.6 GW in May 2024, more than seven times that of a decade earlier.
Nevertheless, total installed rooftop solar and other distributed solar capacity in the National Electricity Market is required to reach more than 36 GW by 2029–30 under AEMO’s 2024 ISP Step Change Scenario.
Adding to the challenge is the difficulty of predicting how much energy will be required across the entire grid by then.
AEMO’s 2024 Electricity Statement of Opportunities recently cut its forecast for the take-up of electric vehicles by one-third over the next decade, as more motorists buy hybrid cars, reducing pressure on the grid.
The grid operator now expects power usage from the grid to grow by 1.9% per annum over the coming decade, rather than the 3% predicted a year ago.
The increasing size of rooftop household solar systems installed by households helped reduce the forecast.
Energy Users Association of Australia CEO Andrew Richards has reportedly described these forecasts as “a little like astrology”, because it is difficult to predict future demand for Chinese EVs, while anticipated strong growth in demand from data centres and households switching from gas to electricity, further clouds the picture.
Early indications are that businesses are heeding the call and see real value in fitting PVCs to their premises and/or grounds.
According to a 2023 report by fintech company Smart Ease, the commercial solar market is seeing a surge, particularly in the 15–30 kW segment, with a growing preference for smaller commercial systems in the 10–15 kW range.
Queensland and NSW are leading the charge, with the 15–20 and 95–100 kW segments dominating the market, collectively accounting for 55% of recent installations.
30 kW of solar generation can typically fit onto the combined roof space of two average houses (100–250 square metres). A big box warehouse (50,000–100,000 m2) can install more than 8 MW, the equivalent of powering 1500+ homes.
Partners in Performance has assessed renewable assets for over 300 sites. Adding batteries and EV charging to solar can boost savings by 10–50% for some industrial and warehouse owners.
Whatever Australia’s power needs over coming decades, every effort must be made to maximise sources of renewable energy and this means using large areas of vacant space that can be fitted with power generation and storage close to businesses and consumers.
Using large commercial roof space, car parking spaces and existing connections improves business owners’ bottom lines and ESG credentials.
Microbes are microscopic living things found in water, soil, the air and animals’ bodies. There are millions of microbes within the human body. Also known as microorganisms, some microbes make people unwell, while others are important for our health. The most common types are bacteria, viruses and fungi.
While microbes often get a bad rap, they can be beneficial in surprising ways, including by helping to remove harmful carbon monoxide (CO) from the atmosphere.
Over two billion tonnes of the deadly gas are released into the atmosphere globally each year; microbes consume about 250 million tonnes of this, reducing CO to safer levels. Now, Australian researchers have made a significant discovery about the way microbes carry out this important task.
Their study, which was led by Monash University and has been published in Nature Chemical Biology , investigated how microbes consume atmospheric CO at an atomic level. It found that they use a special enzyme, called the CO dehydrogenase, to extract energy from the universally present but highly toxic gas.
Co-first author Ashleigh Kropp, from the Monash Biomedicine Discovery Institute’s (BDI) Greening lab and The University of Melbourne’s Grinter lab, said the study showed for the first time how this enzyme extracts atmospheric CO and powers cells.
“This enzyme is used by trillions of microbes in our soils and waters. These microbes consume CO for their own survival, but in the process inadvertently help us,” Kropp explained.
Co-first author Dr David Gillett, who completed his PhD research in the Greening lab, described the phenomenon as a fantastic example of microbial ‘ingenuity’, demonstrating how life has evolved ways to turn something toxic into something useful.
“These microbes help clean our atmosphere,” Gillett said. “This counteracts air pollution, which kills many millions of people each year, and also reduces global warming given CO is indirectly a greenhouse gas.”
While the team’s discovery is unlikely to be directly used to combat or monitor CO emissions, it deepens our knowledge of how the atmosphere is regulated and how it might respond to future changes.
Professor Chris Greening, co-senior author and head of BDI’s Global Change Program, said the discovery highlighted the broader importance of microbes.
“Microbes play countless roles essential for both human and planetary health. Yet, because they’re invisible and often misunderstood, their contributions frequently go unnoticed,” he said.
Kropp said microbes are a big reason why our air was breathable. “They make half the oxygen we breathe and detoxify various pollutants like CO. It’s crucial we better understand and appreciate how they support our own survival,” she said.
Hydro Innovations was engaged by an engineering consultant to select pumps for Greater Western Water’s WIN project to deliver water to irrigation pivots and also to storage tanks on the north western fringe of Melbourne.
Duty points ranging from 30 to 150 L/s at a constant pressure of 68 m for the pivots and 58 L/s at 43 m up to 115 L/s at 46 m for future flows were required from the same pumps.
Hydro Innovations provided the Gorman Rupp VS6A60S-B pump with 110 kW motors. These pumps are a two-stage, self-priming pump capable of delivering the full flow ranges, either using a single pump or running two pumps in parallel. Although designed by Gorman-Rupp for wastewater handling duties, including raw sewage, the pumps are so efficient and produce high enough pressures for them to be a suitable selection for this application for Greater Western Water.
Greater Western Water was impressed by the simplicity of the solution and the great quality of the Gorman Rupp pump. Hydro Innovations delivered the pump sets coupled to the motors on galvanised steel bases ready to be bolted to the pipework and connected to power.
The pumps run quietly and will deliver the flows required by SCADA reliably and without the need for an operator to be present. As they are above ground, they are easily accessed by maintenance and operations without the need for lifting equipment, confined space entry or a large crew of people.
Floating suction lines mean the pumps can operate across the changing water levels throughout the year without hassle.
The supplied pump is part of Gorman-Rupp’s ‘Ultra V Series’ range of pumps, which are available in single or two-stage configurations, giving them a pressure range between 10 and 95 m. They are available in three sizes (3", 4" and 6"), with flow ranges from 10 L/s through to 100 L/s. Predominantly a wastewater pump, they can also be fitted with Gorman-Rupp’s ‘eradicator solids management system’ to enable the pumps to handle stringy materials such as rags, feathers and wet wipes.
Pumps can operate on suction lifts to 7.6 m, allowing them to be mounted ‘high and dry’ at ground level, allowing easy and safe access for operators to monitor and maintain them.
More information on these pumps may be obtained from Hydro Innovations via email or phone (02) 9898 1800.
Hydro Innovations www.hydroinnovations.com.au
Boral Limited (Boral) has trialled a new recycled sand for concrete using crushed glass from end-of-life and damaged solar panels.
This new concrete trial has been specifically created for Victoria’s North East Link project, a large infrastructure investment in Melbourne’s north-east that will construct 6.5 km of tunnels from Watsonia to Bulleen.
Solar glass sand is an environmentally sustainable replacement product to traditional sand, a natural diminishing resource essential to the building and construction industry.
The innovation was driven by Spark North East Link Design & Construct Joint Venture (Spark), a consortium comprising construction companies and a large Australian road and tunnel operator — which has engaged Boral’s expertise to produce and trial concrete with the solar glass sand. The University of Melbourne has supported Spark with development and testing.
Boral sourced the glass from ElecSome, an Australian solar panel upcycling plant that collects end-of-life or damaged solar panels. The glass was crushed and processed at Elecsome’s recycling facility, then blended with up to 50% natural sand.
A variety of concrete mixes using solar glass sand have been created by Boral. Test loads of concrete were transported from the Tullamarine plant to its recently opened Bulleen Concrete Plant, which supplies concrete to the North East Link project, and a trial concrete slab has been laid onsite.
Boral has conducted an assessment of plastic properties including consistency and finishing and has undertaken hardened property testing for compliance with relevant standards. Results so far have been good.
Dr Ali Nezhad, Head of Sustainability and Innovation at Boral, said, “We’re excited to be leading the development of concrete mixes containing solar glass sand, an innovative new product that will be used in Victoria’s biggest project in history. The success of this sustainable concrete mix in a commercial project provides an effective pathway for recycling of end-of-life solar panels and contributes further to sustainability of the construction and building industry.”
Boral www.boral.com.au
Thirteen regional New South Wales councils have pooled their resources to make the shift to renewable energy via a power purchase agreement (PPA) coordinated by the Hunter Joint Organisation and Mid North Coast Joint Organisation.
The Powering Tomorrow: Regional Councils NSW PPA will secure fixed pricing for the councils up until the end of 2030. Under the agreement, the councils will collectively receive over 390 gigawatt hours of electricity for 163 large council sites and streetlighting.
The participating councils are Bellingen Shire, Berrigan Shire, Edward River, Griffith City, Leeton Shire, Maitland City, MidCoast, Murray River, Murrumbidgee, Muswellbrook Shire, Narrandera Shire, Port Macquarie-Hastings and Upper Hunter Shire.
Over the six years of the agreement, an estimated 83% of the electricity supplied to council sites will be from renewable energy generators in NSW, with nine of the 13 councils opting for 100% renewable energy for the entire term.
The PPA brings various benefits for the participating councils:
Emissions reduction: By opting for renewable energy to power their large sites and streetlighting, the councils will avoid an estimated 185,000 tonnes of carbon dioxide emissions (t/ CO2e) over the duration of the agreement. The procurement of renewable energy though this deal will help the councils to decarbonise their operations and progress towards local, state and national net zero targets.
Cost savings and budget certainty: By purchasing as a group, the councils were able to lock in renewable electricity at a competitive price through to the end of 2030, collectively saving an estimated $5.3m compared to their 2024 electricity rates. The deal also shields councils from volatility in the electricity market that can unexpectedly increase costs, providing long-term budget certainty.
Supporting the local economy: Renewable energy purchased under the deal will come from several of Iberdrola Australia’s NSW-based renewable energy projects: the Capital Wind Farm, Avonlie Solar Farm and Bodangora Wind Farm.
Sydney Water’s newly commissioned mobile PFAS treatment unit at Cascade Water Filtration Plant (WFP) has started to reduce the levels of PFAS during the first month of a new treatment trial.
Recent testing indicated that water processed through the mobile PFAS treatment has reduced PFAS levels below the proposed Australian Drinking Water Guidelines (ADWG).
Sydney Water Managing Director Roch Cheroux said this swift result affirms Sydney Water’s commitment to continue delivering safe and high-quality drinking water across the network.
“Our teams worked around the clock to deliver this important work at Cascade WFP, and to see the results start to shift is a testament to their efforts,” Cheroux said.
The $3.4 million mobile PFAS treatment plant, which treats four megalitres (ML) of water per day, will remain in use for up to three years as part of a strategy to treat water in the Blue Mountains catchment.
Using granular activated carbon (GAC) filters and ion exchange technology, the mobile PFAS treatment plant harnesses the latest technology to remove PFAS from the water.
Prior to the installation of the mobile PFAS treatment plant, the water produced at the Cascade WFP was compliant with the current ADWG. The mobile PFAS treatment plant will ensure compliance with the proposed ADWG.
“We have been testing the treated water from Cascade weekly and publishing the results on our website for the public to view,” Cheroux said.
“With the mobile PFAS treatment plant online, the results have shown a continued decline in PFAS concentrations and Sydney Water is confident the concentration of the PFAS in the water
produced at the Cascade WFP will soon be consistently below the proposed guidelines.
“We will continue testing the treated water at Cascade to provide the Blue Mountains community with confidence in the quality of their drinking water, and to demonstrate Sydney Water’s commitment to delivering water that meets the highest standards,” Cheroux said.
Member for the Blue Mountains Trish Doyle said she is excited to see the mobile PFAS treatment unit in operation.
“I welcome this positive news and the tireless efforts by Sydney Water to assure the Blue Mountains community every effort is being made to deliver safe drinking water of the highest quality,” Doyle said.
The treatment trial is part of Sydney Water’s Long Term Capital and Operational Plan (LTCOP) — an adaptive roadmap designed to deliver essential upgrades and new infrastructure across the network through to 2050.
The LTCOP proposes an investment of more than $30 billion over the next decade to ensure Sydney Water can continue providing safe, sustainable and reliable water services to meet the needs of a rapidly expanding city.
“Our LTCOP prioritises public health, environmental sustainability and economic efficiency to allow us to maintain the highest level of service that our customers expect,” Cheroux said.
The final PFAS guidelines will be published by the National Health and Medical Research Council (NHMRC) in April 2025. Once released, Sydney Water will work closely with NSW Health to implement the guidelines and ensure compliance to any updated regulatory requirements.
Sydney Water Corporation www.sydneywater.com.au
Arnold Kleijn, Sales Director, HRS Heat Exchangers
Over the last couple of years, we have seen increased interest in MVR for evaporation.
Given the turbulent rise and fall of energy markets since 2020 this is understandable, as the electrical energy employed in MVR is normally considerably cheaper than the thermal energy needed for traditional evaporation. However, there are a number of limiting factors and key considerations when using MVR — particularly for very thick and viscous products like digestate and sludges — which can add to the capital cost (and complexity) of an MVR-based evaporation solution. It is therefore very important that all these elements are considered from the outset, so that an accurate investment decision based on both capital (CapEx) and operational (OpEx) costs can be made.
Traditional evaporation techniques use a high-temperature service fluid (such as pressurised steam) to raise the temperature of the product above its boiling point so that water (and other volatile compounds) is driven off, leaving a more concentrated solution. The principal source of energy for this process is therefore the fuel used to heat the water (steam) in the boiler, such as gas or oil. In MVR, the steam which comes off the product in the evaporator is channelled into a compressor which increases the pressure (and therefore the temperature). This steam, which is now above the boiling point of the product, is then used as the service
Due to their thick, viscous nature, digestates and sludges are among the most challenging materials to evaporate efficiently and effectively. However, the benefits in terms of handling, disposal and treatment can be significant. While there is considerable interest in using mechanical vapour recompression (MVR) evaporation techniques, the complex nature of digestate means that MVR may not always be the best choice.
fluid for the evaporator. As the compressor uses an electric motor, the process is driven by electricity rather than thermal energy. Because the compressor reuses/ recycles evaporated steam, a lot of latent heat is recovered. This makes MVR one of the cheapest methods of evaporating water in terms of operational costs.
However, because of the way MVR works, there are some inherent limitations in the process which traditional thermal evaporation does not suffer from. When evaporating at atmospheric pressure, depending on the type of compressor, the temperature rise provided by the compressor is typically between 8 and 15°C. The relatively small temperature difference between the service fluid and the boiling point of the product (~100°C) means that heat transfer between the two is limited and you need a large surface area to achieve it. To put it simply, you need a large heat exchanger.
In contrast, boilers can deliver maximum steam pressure of up to 8 or 10 bar, meaning an effective temperature of 160 or 180°C. Even if general operation is below these levels, the fact is that steam from a boiler will be considerably hotter than from a compressor. The greater temperature difference means that less transfer surface area is required, and you can utilise a much smaller heat exchanger. Because of the thick nature and high fouling potential of many digestates and sludges, in most cases you need a relatively large surface area to achieve sufficient heat transfer. Because of the limitations of compressors in terms of service fluid temperature, the required heat exchangers and pumps can be exceptionally large indeed. Not only does this increase the capital cost significantly, but as you need larger pumps to push the product through the larger heat exchanger, you also require more energy for operation, so the operational cost benefits begin to reduce.
Digestate and sludges often contain suspended solids, which increase the viscosity of the product when evaporated, adding further to the challenges described above. Therefore,
if you want to use MVR evaporation you will need to pre-treat the product to remove as many of these solids as possible, usually via filtration, in order to achieve the necessary rates of heat transfer in the heat exchanger. Again, adding this pre-treatment step adds significant capital costs and reduces potential energy savings during operation.
Digestate also typically contains between 2000 and 3000 ppm of ammonia. Pre-treating the product with acid to reduce the pH can neutralise the ammonia, preventing it from evaporating and reducing the risk of damage to the compressor, but once again this need for acid dosing adds additional cost and operational complexity. You also need to consider the nature of the material and the necessary combination of chemical and physical pre-treatment.
As no two sludges are the same, at HRS we always test the material that any client will be working with in order to determine not only the best heat exchanger solution for the evaporation process, but also what pre-treatment may be necessary.
Evaporating digestate and sludges using MVR is certainly possible and HRS Heat Exchangers has supplied such systems where they are appropriate. However, our experience has shown that careful consideration, including the system modifications which may be required to ensure efficient and effective evaporation of the project, is essential in order to determine the most suitable and most economical technology for each project.
For example, do the high capital costs of an MVR-powered evaporation solution outweigh the reduced operational costs? For many digestate applications, traditional thermalbased evaporation technologies remain the best economic choice, but every situation must be assessed on its own merits.
It is important that the nature of the product is thoroughly assessed and understood, and that all the necessary parts of a complete system are specified and included from the outset, so that an accurate investment decision based on all the necessary information can be made. Otherwise, you could end up with an expensive solution which does not perform as expected.
An innovative tech collaboration is helping to finesse a low-cost rubbish recycling process that relies on the insatiable appetite of black soldier fly larvae.
Biotech company ARC Ento Tech, based on the NSW Central Coast, is helping to process landfill in the state by using the larvae of this common fly to eat the organic waste that’s part of mixed solid waste. Once all the organic waste is eaten, the larvae are recovered and converted into commercial products, including organic fertiliser and a nutrient-rich insect meal for chickens, while the inorganic waste is converted into an industrial reductant that can replace coking coal.
As larvae, black soldier flies will eat almost anything, from food waste to manure, before they become adults and lose their mouths. This makes them a valuable addition to the recycling process. To make its system more efficient, ARC Ento Tech needs more fly larvae to be produced by adult flies in the recycling hatch, but until now, there has been no accurate way to measure black soldier flies’ reproductive behaviour.
This is where a neuromorphic system created by Western Sydney University researchers can help.
“While ARC Ento Tech have created ideal conditions for the black soldier fly larvae to flourish in the recycling hatch, they don’t know the speed at which black soldier flies can breed larvae and the number of larvae they produce,” said Project Lead Dr Alexandre Marcireau from the International Centre for Neuromorphic Systems at Western Sydney University.
“Optimising the breeding of the flies requires precise knowledge of the number of flies that move from the ‘growing area’ where they eat waste, into the ‘breeding room’ where they breed and deposit larvae eggs. If we can count these fast-moving objects, then the recycler can systematically quantify the impact of breeding parameters such as temperature, light intensity and amount of food, and engineer an optimised system with significantly higher yields of larvae.”
It is difficult for conventional cameras and sensors to capture this sort of data due to the high speed and number of flies. The system designed by the Western Sydney University team is based on a neuromorphic camera: technology that uses sensors to collect only useful data, and which has been inspired by biology to accurately observe fast-moving objects, including flies.
The ‘High Speed Counting of Black Soldier Flies’ project utilised the world-leading neuromorphic vision capabilities at Western Sydney University in collaboration with Macquarie University researchers who delivered the hardware that allowed the sensor to operate inside the breeding cages.
“The FlyCount system was developed with neuromorphic vision sensors and a custom spike detection algorithm for real-time,
accurate fly counting, which ensures 95% accuracy in dynamic lighting,” said Professor Subhas Mukhopadhyay from the School of Engineering at Macquarie University.
“By integrating neuromorphic sensing technologies to an IoTenabled system, the system demonstrates the effectiveness and accuracy of the event-based counting system for tracking and analysing the movements of black soldier flies remotely.
“Collaborating with ARC Ento Tech, we have adapted advanced neuromorphic sensing to improve operational efficiency in fly breeding, showcasing how practical innovation can reduce environmental impact and support sustainable agriculture,” Mukhopadhyay said.
The project was funded by the NSW Smart Sensing Network, and its results have been published in IEEE Sensors.
“This is a great example of a genuine collaboration between all parties,” said NSW Smart Sensing Network Environment & Agriculture Theme Lead Dr Tom Hu.
“Western Sydney University had developed their neuromorphic sensing expertise from the space domain, and the mechatronic engineering capability at Macquarie University helped bring this into a new environment. The technology looks to now improve operational efficiencies in breeding flies — aiding ARC Ento Tech,” Hu said.
The solution comes at a time when Greater Sydney is on the brink of a waste crisis due to a lack of landfill space. Almost 70% of the mixed solid waste generated in Australia in 2018 was buried in landfill.
It is hoped the results of the project can be scaled up to help tackle this problem, as well as opening the door to other applications such as beehive monitoring.